RayTek LineScanner MP150 User manual

MP150
Linescanner
Operating Instructions
Rev. E3 07/2013
58501


Contacts
Raytek Corporation
Worldwide Headquarters
Santa Cruz, CA USA
Tel: +1 800 227 – 8074 (USA and Canada only)
+1 831 458 – 3900
Fax: +1 831 458 – 1239
solutio[email protected]om
European Headquarters
Berlin, Germany
Tel: +49 30 4 78 00 80
raytek@raytek.de
France
United Kingdom
ukinfo@raytek.com
China Headquarters
Beijing, China
Tel: +86 10 6438 4691
Internet: http://www.raytek.com/
Thank you for purchasing this Raytek product. Register today at www.raytek.com/register to receive
the latest updates, enhancements and software upgrades!
© Raytek Corporation.
Raytek and the Raytek Logo are registered trademarks of Raytek Corporation.
All rights reserved. Specifications subject to change
without notice.

WARRANTY
The manufacturer warrants this instrument to be free from defects in material and workmanship under normal
use and service for the period of two years from date of purchase. This warranty extends only to the original
purchaser. This warranty shall not apply to fuses, batteries, or any product which has been subject to misuse,
neglect, accident, or abnormal conditions of operation.
In the event of failure of a product covered by this warranty, the manufacturer will repair the instrument when it
is returned by the purchaser, freight prepaid, to an authorized Service Facility within the applicable warranty
period, provided manufacturer’s examination discloses to its satisfaction that the product was defective. The
manufacturer may, at its option, replace the product in lieu of repair. With regard to any covered product
returned within the applicable warranty period, repairs or replacement will be made without charge and with
return freight paid by the manufacturer, unless the failure was caused by misuse, neglect, accident, or abnormal
conditions of operation or storage, in which case repairs will be billed at a reasonable cost. In such a case, an
estimate will be submitted before work is started, if requested.
THE FOREGOING WARRANTY IS IN LIEU OF ALL OTHER WARRANTIES, EXPRESSED OR IMPLIED,
INCLUDING BUT NOT LIMITED TO ANY IMPLIED WARRANTY OF MERCHANTABILITY, FITNESS, OR
ADEQUACY FOR ANY PARTICULAR PURPOSE OR USE. THE MANUFACTURER SHALL NOT BE LIABLE
FOR ANY SPECIAL, INCIDENTAL OR CONSEQUENTIAL DAMAGES, WHETHER IN CONTRACT, TORT,
OR OTHERWISE.
SOFTWARE WARRANTY
The manufacturer does not warrant that the software described herein will function properly in every hardware
and software environment. This software may not work in combination with modified or emulated versions of
Windows operating environments, memory-resident software, or on computers with inadequate memory. The
manufacturer warrants that the program disk is free from defects in material and workmanship, assuming
normal use, for a period of one year. Except for this warranty, the manufacturer makes no warranty or
representation, either expressed or implied, with respect to this software or documentation, including its quality,
performance, merchantability, or fitness for a particular purpose. As a result, this software and documentation
are licensed “as is,” and the licensee (i.e., the User) assumes the entire risk as to its quality and performance. The
liability of the manufacturer under this warranty shall be limited to the amount paid by the User. In no event
shall the manufacturer be liable for any costs including but not limited to those incurred as a result of lost profits
or revenue, loss of use of the computer software, loss of data, the cost of substitute software, claims by third
parties, or for other similar costs. The manufacturer’s software and documentation are copyrighted with all rights
reserved. It is illegal to make copies for another person.
Specifications subject to change without notice.
The device complies with the requirements of the European Directives.
EC – Directive 2004/108/EC (EMC)

Content
1 SAFETY INSTRUCTIONS..............................................................................................................................7
2 TECHNICAL DATA.........................................................................................................................................8
2.1 MEASUREMENT SPECIFICATIONS .................................................................................................................8
2.2 OPTICAL SPECIFICATIONS ............................................................................................................................9
2.2.1 Standard Focus....................................................................................................................................11
2.2.2 Far Focus.............................................................................................................................................12
2.3 ELECTRICAL SPECIFICATIONS.....................................................................................................................13
2.4 GENERAL SPECIFICATIONS .........................................................................................................................13
2.5 DIMENSIONS ...............................................................................................................................................14
2.6 SCOPE OF DELIVERY....................................................................................................................................15
3 BASICS .............................................................................................................................................................16
3.1 MEASUREMENT OF INFRARED TEMPERATURES .........................................................................................16
3.2 EMISSIVITY OF TARGET OBJECT ..................................................................................................................16
4 SYSTEM OVERVIEW ....................................................................................................................................17
5 INSTALLATION ............................................................................................................................................18
5.1 AMBIENT TEMPERATURES ..........................................................................................................................18
5.2 ENVIRONMENT ...........................................................................................................................................18
5.3 ELECTRICAL INTERFERENCE .......................................................................................................................18
5.4 GEOMETRY ..................................................................................................................................................18
5.5 MOUNTING .................................................................................................................................................19
5.6 COMMUNICATION INTERFACES .................................................................................................................20
5.6.1 Ethernet Wiring ..................................................................................................................................20
5.6.2 Ethernet Settings.................................................................................................................................21
5.6.3 Changing the Ethernet Settings for the PC.........................................................................................22
5.6.4 Changing the Ethernet Settings for the Scanner.................................................................................24
5.7 POWER SUPPLY CABLE ...............................................................................................................................25
5.8 WARM-UP TIME ..........................................................................................................................................25
5.9 WATER COOLING........................................................................................................................................26
5.9.1 Avoiding Condensation.......................................................................................................................26
5.10 AIR PURGE COLLAR...................................................................................................................................28
5.11 INPUT AND OUTPUT CONNECTORS .........................................................................................................29
5.12 LASER ........................................................................................................................................................31
6 OPERATION ...................................................................................................................................................32
6.1 SCAN RATE AND TARGET VIEWING TIME..................................................................................................32
6.2 SECTORS ......................................................................................................................................................33
6.3 DATA TRANSFER MODES............................................................................................................................34
6.4 SCANNER AS STAND-ALONE DEVICE ........................................................................................................34
7 ACCESSORIES................................................................................................................................................35
7.1 OVERVIEW...................................................................................................................................................35
7.2 MOUNTING PLATE......................................................................................................................................36
7.3 ADJUSTABLE MOUNTING BASE ..................................................................................................................36
7.4 TUBE FITTINGS ............................................................................................................................................37
7.4.1 Installation of the Tube Fittings..........................................................................................................37

7.4.2 Reassembly of the Tube Fittings ......................................................................................................... 37
7.5 THERMOSTAT ............................................................................................................................................. 38
7.6 SPARE WINDOWS ....................................................................................................................................... 40
7.7 INDUSTRIAL POWER SUPPLY ...................................................................................................................... 41
7.8 RS485 INTERFACE KIT................................................................................................................................ 41
7.8.1 RS485 Cable Extension ...................................................................................................................... 43
7.9 OUTPUT MODULES..................................................................................................................................... 44
7.9.1 General Specification .......................................................................................................................... 44
7.9.2 Dimensions......................................................................................................................................... 45
7.9.3 Wiring ................................................................................................................................................ 46
7.9.4 RS232/485 Converter 7520 ................................................................................................................ 47
7.9.5 Output Module 7024, analog ............................................................................................................. 48
7.9.6 Output Module 7042, digital ............................................................................................................. 48
7.9.7 Output Module 7043, digital ............................................................................................................. 49
7.9.8 Output Module 7045, digital ............................................................................................................. 49
7.9.9 Output Module 7067, Relay............................................................................................................... 50
7.10 ALARM MODULE...................................................................................................................................... 51
8 MAINTENANCE............................................................................................................................................ 52
8.1 CLEANING THE WINDOW .......................................................................................................................... 52
8.2 REPLACING THE WINDOW......................................................................................................................... 52
9 TROUBLESHOOTING ................................................................................................................................. 54
10 APPENDIX..................................................................................................................................................... 57
10.1 DETERMINATION OF EMISSIVITY.............................................................................................................. 57
10.2 TYPICAL EMISSIVITY VALUES................................................................................................................... 57
INDEX

Safety Instructions
MP150 Rev. E3 07/20137
1Safety Instructions
This document contains important information, which should be kept at all times with the instrument
during its operational life. Other users of this instrument should be given these instructions with the
instrument. Updates to this information must be added to the original document. The instrument can
only be operated by trained personnel in accordance with these instructions and local safety
regulations.
Acceptable Operation
This instrument is intended only for temperature measurement and is appropriate for continuous use.
The instrument operates reliably in demanding conditions, such as in high environmental
temperatures, as long as the documented specifications are adhered to. Compliance with the operating
instructions is necessary to ensure the expected results.
Unacceptable Operation
The instrument should not be used for medical diagnosis.
Replacement Parts and Accessories
Use only original parts and accessories approved by the manufacturer. The use of other products can
compromise the operational safety and functionality of the instrument.
Instrument Disposal
Do not dispose of this product as unsorted municipal waste. Go to Fluke’s website for
recycling information.
Operating Instructions
The following symbols are used to highlight essential safety information in the operation instructions:
Helpful information regarding the optimal use of the instrument.
Risk of danger. Important information.
Incorrect use of 110 / 230 V electrical systems can result in electrical hazards and personal
injury. All instrument parts supplied with electricity must be covered to prevent physical
contact and other hazards at all times.
The instrument is equipped with a Class 2 laser. Class 2 lasers shine only within the
visible spectrum at an intensity of 1 mW. Looking directly into the laser beam can produce
a slight, temporary blinding effect, but does not result in physical injury or damage to the
eyes, even when the beam is magnified by
optical aids. At any rate, closing the eye lids is
encouraged when eye contact is made with the laser beam. Pay attention to possible
reflections of the laser beam. The laser functions only to locate and mark surface
measurement targets. Do not aim the laser at people or animals.

Technical Data
8 Rev. E3 07/2013MP150
2Technical Data
2.1 Measurement Specifications
Temperature Range
LT 20 to 350°C (68 to 662°F)
MT 100 to 800°C (212 to 1472°F)
HR 100 to 650°C (212 to 1202°F)
G5 100 to 950°C (212 to 1742°F)
P3 30 to 250°C (86 to 482°F) – for P30
100 to 350°C (212 to 662°F) – for P31
2M 400 to 950°C (752 to 1742°F)
1M 600 to 1200°C (1112 to 2192°F)
Spectral Response
LT 3 to 5 µm
MT 3.9 µm
HR 3.5 to 4 µm
G5 5 µm
P3 3.43 µm
2M 1.6 µm
1M 1 µm
Detectors
LT, MT, HR, G5, P3 MCT
2M InGaAs
1M Si
System Accuracy1
LT ± 2°C (± 4°F)
MT ± 0.5% of reading or ± 3°C (6°F), whichever is greater
HR ± 0.5% of reading or ± 3°C (6°F), whichever is greater
G5 ± 0.5% of reading or ± 3°C (6°F), whichever is greater
P3 ± 3°C (± 6°F)
1M, 2M ± 0.5% of reading or ± 3°C (6°F), whichever is greater
Repeatability2
LT ± 1°C (± 2°F)
MT ± 1°C (± 2°F)
HR ± 1°C (± 2°F)
G5 ± 1°C (± 2°F)
P3 ± 1°C (± 2°F)
1M, 2M ± 2°C (± 4°F)
1at 0 - 50°C (32 - 122°F) ambient temperature
2at 0 - 50°C (32 - 122°F) ambient temperature

Technical Data
MP150 Rev. E3 07/20139
Temperature Resolution
digital interface 0.1 K
analog output 16 bit
Scan Rate
All models 150 Hz
Measured Points per Line1
All models 256 pixel @ 150 Hz scan rate
512 pixel @ 76 Hz scan rate
1024 pixel @ 36 Hz scan rate – model as option
Scan Angle (FOV)
All models 90°
2.2 Optical Specifications
Standard Focal Distance
All models 1.52 m / 69 in. (standard focus)
special focal distances available
minimal focal distance: 500 mm (20 in)
HR ∞ (far focus)
Optical Resolution D:S 2
Measurement Resolution (90% energy)
LT, MT, HR, G5 170 : 1 (IFOV = 5.9 mrad)
P3 33 : 1 – for P30 (IFOV = 30 mrad)
75 : 1 – for P31 (IFOV = 13.3 mrad)
1M 200 : 1 (IFOV = 5 mrad)
2M 200 : 1 (IFOV = 5 mrad)
Hot Spot Detection (50% energy)
LT, MT, HR, G5 510 : 1 (IFOV = 2 mrad)
P3 100 : 1 – for P30 (IFOV = 10 mrad)
225 : 1 – for P31 (IFOV = 4.5 mrad)
1M 600 : 1 (IFOV = 1.7 mrad)
2M 600 : 1 (IFOV = 1.7 mrad)
1at 90° scan angle
2measured as slit response at 20 Hz scan rate, per pixel at focus distance

Technical Data
MP150 Rev. E3 07/201313
2.3 Electrical Specifications
Communications
Ethernet TCP/IP protocol 10/100 MBit/s, electrically isolated,
auto-negotiation
RS485 full-duplex, not addressable
9.6, 57.6, 115.2, 230.4 kBaud
Outputs
Analog 3 active current outputs, each adjustable 0/4 ... 20 mA,
maximum load: 500 Ω, minimal load: 47 Ω
common ground connection for all current outputs, electrically
isolated to the GND ground
Alarm potential-free relay contacts: 30 V / 1 A
normally open / normally closed
Inputs
Trigger + 5 to 24 VDC pulse, high/low active
Functional Input max. + 5 VDC
function depends on the specific MP150 based system
Signal Processing
Stand-alone unit Max, Min, Average, Peak/Valley Hold, Alarm setpoints
further signal processing function through software
Power Supply 24 VDC ± 25%, 1 A
2.4 General Specifications
Mechanical Scanning System 40,000 h (about 4.5 years) meantime between failures (MTBF)
for the mechanical scanning system at 48 Hz scan rate
Environment Rating IP65 (NEMA 4) in accordance to IEC 60529
Ambient Temperatures 0 to 50°C (32 to 122°F) – without water cooling
max. 180°C (356°F) – with water cooling
down to –40°C (–40°F) – only for scanner with internal heating
element (optional) and still air (e.g. by using a protective
housing)
Storage Temperatures -25 to 65°C (-13 to 149°F)
Water Cooling max. pressure 15 bar (218 PSI)
Air Purge Collar max. pressure 3 bar (43 psig)
Warm-up Time 30 min.
Relative Humidity 10 to 90%, non-condensing,
for operating and non-operating temperature range
Vibration IEC 60068-2-6, 3 axes, 10 to 150 Hz, operating 2 g above 20 Hz
Shock IEC 60068-2-27, 3 axes, operating: 5 g at 11 ms, 15 g at 6 ms
Dimensions 200 x 180 x 190 mm (7.8 x 7.02 x 7.41 in)

Technical Data
14 Rev. E3 07/2013MP150
Weight (incl. air purge) 7 kg (15.4 lbs)
2.5 Dimensions
Figure 5: Linescanner mounting locations and dimensions
Note: The mounting dimensions are the same for top and bottom view!
All mounting threads are
4x M6
8 mm (0.31) deep
(front side, upside, below)
Air purge connections
ISO 228 G⅛“
∅outer 5 mm (.2 in)
∅
inner 3 mm (.12 in)
Water connections
∅outer 6 mm (.24
in)
∅inner 4 mm (.16
in)
Water connections
∅outer 6 mm (.24
in)
∅inner 4 mm (.16
in)

Technical Data
MP150 Rev. E3 07/201315
2.6 Scope of Delivery
The linescanner package includes the following:
•MP150 Linescanner
•Operating Instructions (also included as PDF file on the CD-ROM)
•Software CD with DataTemp DP (Windows 2000, XP, Vista, Win7)
•Protocol Manual only as PDF file on the CD-ROM
•Ethernet cable: 1x 7.5 m (24.6 ft), max. ambient temperature: 180°C (356°F)
•Power Supply cable: 1x 7.5 m (26.4 ft), max. ambient temperature: 180°C (356°F)
(power supply XXXSYSPS should be ordered separately)
•1x spare window for MP150
•Tools: 1x hex key wrench 2.5 mm
1x hex key wrench 5 mm
1x connector (female) 6-pin for inputs/outputs
1x connector (female) 4-pin for analog current outputs

Basics
16 Rev. E3 07/2013MP150
3Basics
3.1 Measurement of Infrared Temperatures
Every object emits an amount of infrared radiation (IR) according to its surface temperature. The
intensity of the infrared radiation changes with the temperature of the object. Depending on the
material and surface properties, the emitted radiation lies in a wavelength spectrum of approximately
1 to 20 µm. The intensity of the infrared radiation (”heat radiation”) is dependent on the material. For
many substances this material-dependent constant is known. It is referred to as ”emissivity value”, see
appendix 10.2 Typical Emissivity Values on page 57.
Infrared thermometers are optical-electronic sensors. These sensors are able to detect ”radiation of
heat”. Infrared thermometers are consist of a lens, a spectral filter, a sensor, and an electronic signal
processing unit. The task of the spectral filter is to select the wavelength spectrum of interest. The
sensor converts the infrared radiation into an electrical signal. The connected electronics process this
signal for further analysis. The intensity of the emitted infrared radiation is thereby used to determine
the temperature of the target. Since the intensity of the infrared radiation is dependent on the material,
the appropriate emissivity can be selected on the sensor.
The biggest advantage of the infrared thermometer is its ability to measure temperature without the
need to be in contact with the target. Consequently, surface temperatures of moving or hard to reach
objects can be easily measured.
3.2 Emissivity of Target Object
For accurate temperature readings, the sensor must be set to the appropriate emissivity value for the
target material. Determine the emissivity of the target object as described in appendix 10.1
Determination of Emissivity on page 57.
When measuring materials with low emissivity, the results could be effected by interfering infrared
radiation from background objects (such as heating systems, flames, fireclay bricks, etc. near to or
behind the target object). This type of problem can occur when measuring reflective surfaces and very
thin materials such as plastic films and glass. This error can be reduced to a minimum if particular
care is taken during installation, and the linescanner is shielded from reflected infrared radiation.

System Overview
MP150 Rev. E3 07/201317
4System Overview
The following figure shows the principal structure of the system. It shows a solution with one scanner,
one Digital Output Module and one Analog Output Module. The system can be expanded by adding
more Output Modules to the RS485 network, see section 7.9 Output Modules, page 44.
Figure 6: Principal structure of the system
Instead of outputting the temperature data by means of output modules also an OPC server capability
or a serial communication port can be used for forwarding the data to other control systems, e.g. a
PLC.
Ethernet
Network
Adapter
PC
Scanner
Control room
C
OM
-
Port
RS485
Converter*
RS232
RS232
RS485
D0
.
.
D15
Digital Output
Module*
D0
.
.
D3
Analog Output
Module*
Signals to the
process
24VDC Power
Process area
*optional

Installation
18 Rev. E3 07/2013MP150
5Installation
Linescanners are able to measure temperature values along a line through the use of a rotating mirror.
For 25% of its revolution, the linescanner scans the field of view (FOV). This corresponds to a scan
angle of 90°. The remaining 75% of its revolution is used for the internal operation of the sensor. The
rotating mirror views the scene and reflects the infrared energy striking it onto a system of lenses
which focuses the radiation onto a thermoelectrically cooled detector. The incoming signal is scanned,
digitized, and then converted to temperature values by the internal microprocessor. For every
revolution of the mirror, up to 1024 measured values will be internally collected. An air purge system
keeps the scanner’s window free of dust, debris, and condensation.
5.1 Ambient Temperatures
Without water cooling, the linescanner is designed for ambient operating temperatures between 0°C
and 50°C (32°F and 122°F). With water cooling, it can be used in environments of up to 180°C (356°F),
see section 5.9 Water Cooling, page 26. The internal temperature is the determining factor for proper
operation of the linescanner. It is displayed in the DataTemp software. The difference between the
external ambient temperature and the temperature inside the housing also depends on the thermal
contact of the linescanner and its mounting hardware.
The temperature inside the housing must be between 0°C to 60°C (32°F to 140°F) during
operation and never more then 65°C (150°F) at any time, including non-operation!
5.2 Environment
The linescanner complies with class IP65 and is therefore dust and splash resistant. The linescanner’s
window is made of a material that is resistant to thermal stresses and it is equipped with an integrated
air purge system which protects the window against contamination. Air supply for the air purge
should be oil free, clean “instrument“ air.
5.3 Electrical Interference
To minimize electrical or electromagnetic interference, follow these precautions:
•Mount the sensor as far away as possible from possible sources of interference such as
motorized equipment producing large step load changes!
•Ensure a fully insulated installation of the sensor (avoid ground loops!).
•Make sure the shield wire in the sensor cable is earth grounded at one location!
•To avoid potential differences use a single power circuit to power both the linescanner and the
PC running the software!
5.4 Geometry
The smallest possible object which can be measured depends on two conditions:
1. The area measured must be no less than 90% (90% energy response).
2. Hot spots must be clearly detected, when in front of a cold background (50% energy response).
Remark: The measured area for 50% energy response is approximately ⅓ of the area size of the
measured spot for 90% energy response.

Installation
MP150 Rev. E3 07/201319
Refer to section 2.2 Optical Specifications, page 9, for basic versions of optical resolution values for the
various models.
Figure 7: Relationship between scan line width and distance to target
The relationship between the scan line width (L) and the distance (D) to the front side of the
linescanner housing is defined as described above. For long distances, the scan line width is about
twice the measurement distance (90° FOV).
5.5 Mounting
The linescanner can be installed as follows:
•on a tripod with a standard 1/4-20 UNC (photo equipment) thread. This type of setup requires
the optional tripod mounting plate (XXXTMP50ACCC) and is recommended if the linescanner
is to be used only for temporary or mobile measurements.
•with the mounting holes of the linescanner housing. This type of setup is recommended for
permanent installations where higher stability is desired.
Prevent all contact between heat sources and the linescanner to protect the linescanner from
overheating.
L = Scan line width
D
= Distance to target (measured from front
surface of housing)
90° FOV:
D = L/2

Installation
20 Rev. E3 07/2013MP150
5.6 Communication Interfaces
The MP150 can communicate via Ethernet interface or RS485. During system configuration the user
selects either Ethernet or RS485. You cannot use Ethernet and RS485 communications for the data
transfer at the same time!
The Ethernet connection between linescanner and the PC has a maximum speed of 100 MBit/s and
permits real-time data transfer for all temperature pixels. For multi-scanner systems you can use a
standard Ethernet Switch to connect to the PC network adapter.
5.6.1 Ethernet Wiring
The linescanner is shipped with an Ethernet cable specified to NEMA WC-63.1 Category 5e, UL
verified to Category 5e, Ethernet/IP Compliant. This standard cable is 7.5 m (24.6 ft.) long, free from
Halogen, and withstands ambient temperatures up to 180°C (356°F).
The connector on one cable end (scanner wiring) is an M12 plug-in connector, 4 pin D-coded, suited
for industrial Ethernet with IP67 protection rate with a screw retention feature.
The connector on the other cable end (field/PC wiring) is an RJ45 connector.
Figure 8: Ethernet Cable with M12 Plug and RJ45 Connector
Figure 9: M12 Connector Socket at the Scanner (left) and the Corresponding Plug (right)
Figure 10: RJ45 Connector
M12-Pin
RJ45-Pin
1
1
TX+
2
3
RX+
3
2
TX-
4
6
RX-
Other manuals for LineScanner MP150
2
Table of contents
Other RayTek Scanner manuals
Popular Scanner manuals by other brands

Fujitsu
Fujitsu FI-4120C2 - Document Scanner Getting started
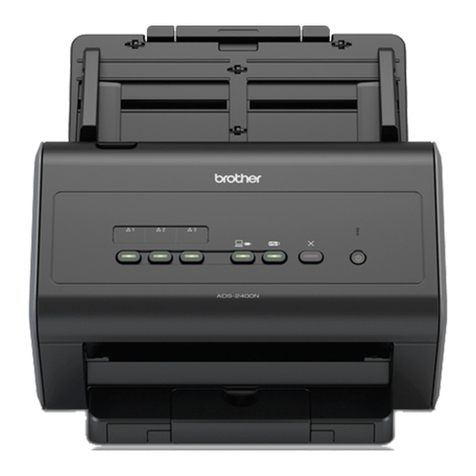
Brother
Brother ImageCenter ADS-3000N Service manual

Colortrac
Colortrac SmartLF SG Series Assembly instructions
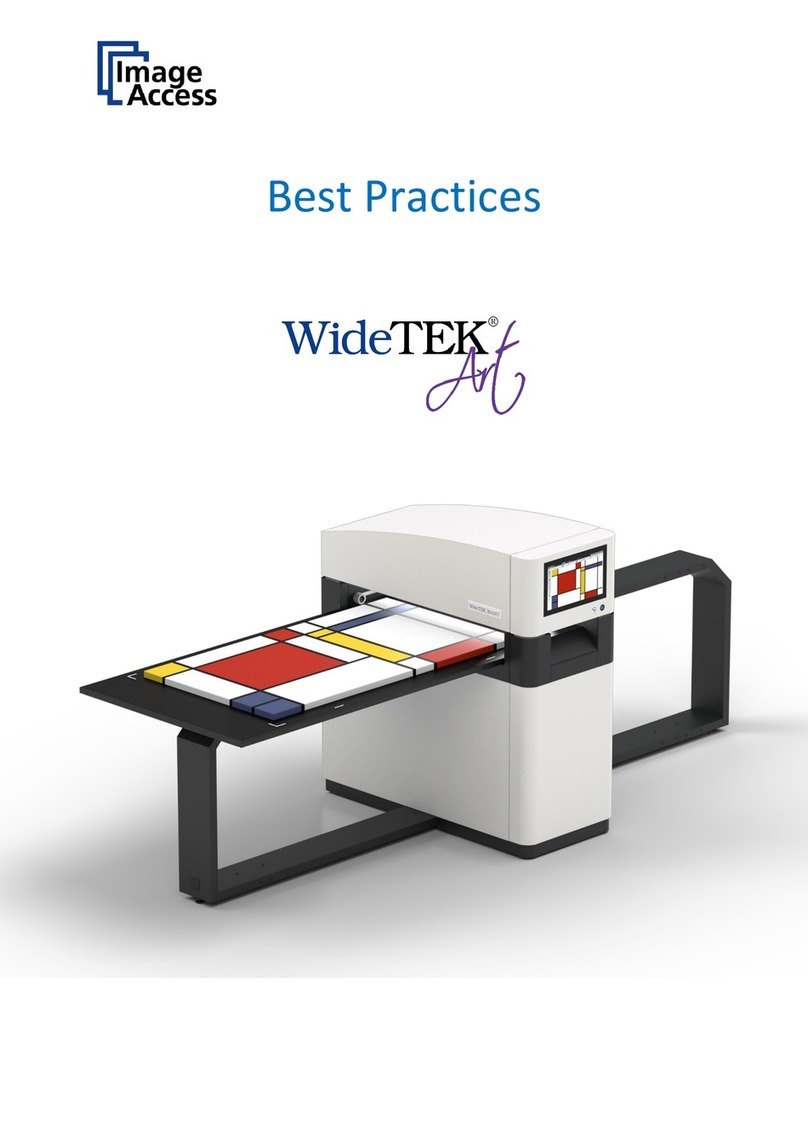
Image Access
Image Access WideTEK Art Best practices manual
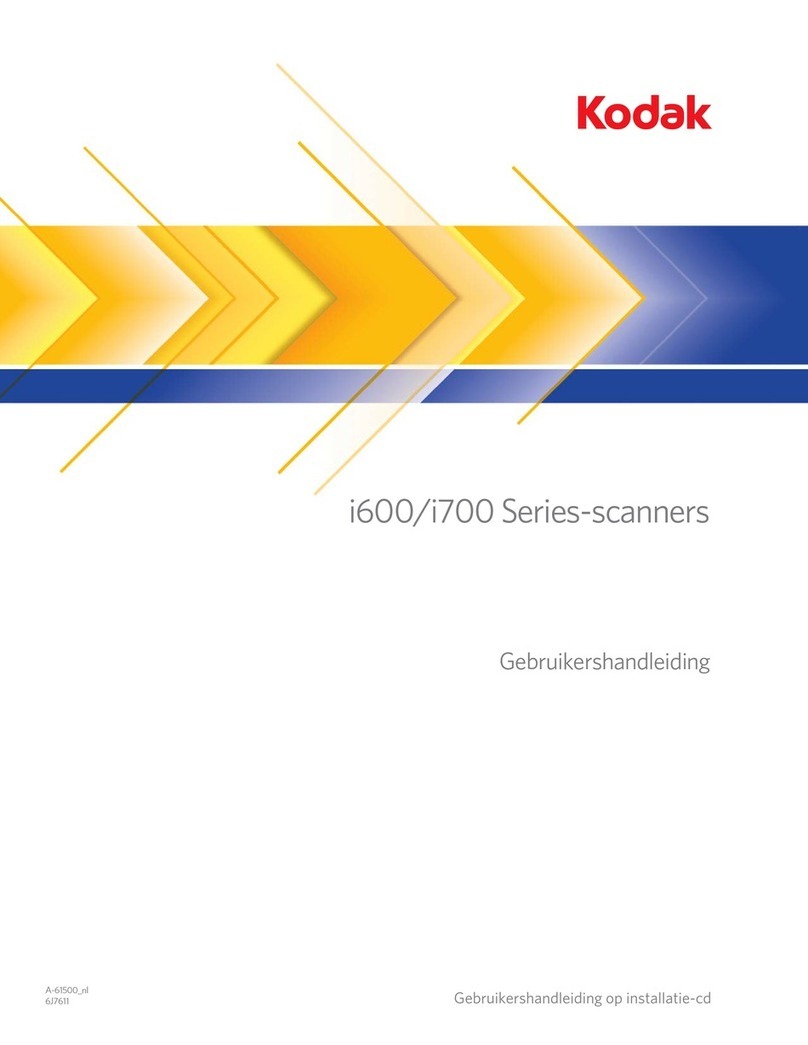
Kodak
Kodak i700 Series Gebruikershandleiding
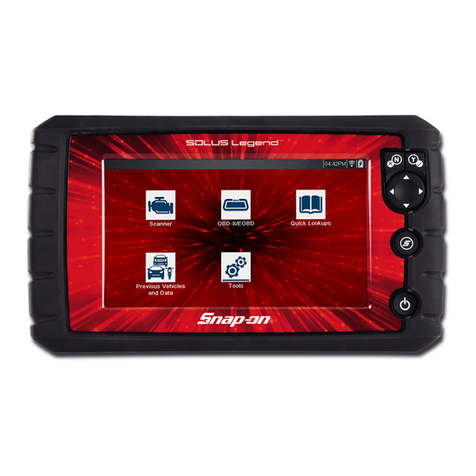
Snap-On
Snap-On Solus Legend user manual