RTP 3236 User manual

Technical Manual
3236 and 3237
16-Channel
Analog Output Cards

2
© 2002 - 2018 RTP Corporation
Specifications, information and graphics are subject to change without notice. Contact
RTP’s corporate office for specifics regarding any changes.
Not for reproduction in any printed or electronic media without express written consent
from RTP Corp.
All information, data, graphics and statements in this document are proprietary
intellectual property of RTP Corp. unless otherwise indicated and are to be considered
RTP Corp. confidential. This intellectual property is made available solely for the direct
use of potential or licensed RTP Corp. customers in their application of RTP Corp.
products, and any other use or distribution is expressly prohibited. If you have received
this publication in error, immediately delete, discard or return all copies to RTP Corp.
RTP Corporation
2832 Center Port Circle
Pompano Beach, FL 33064
Phone: (954) 597-5333
Internet: http://www.rtpcorp.com
Last Updated: 4/4/2018

3
TABLE OF CONTENTS
INTRODUCTION........................................................................................4
SPECIFICATIONS.....................................................................................5
CABLING...................................................................................................8
FAILURE RATES IN ACCORDANCE TO IEC 61508 .............................10
SOFTWARE CONFIGURATION .............................................................11
NetArrays Configuration...............................................................................11
Watchdog Timer.....................................................................................12
Integer Error Detection...........................................................................12
Integer Channel Error Status..................................................................13
Integer Card Revision.............................................................................13
Integer Cal Date.....................................................................................13
Integer Cal Serial Number......................................................................13
Channel .................................................................................................13
I/O Tag...................................................................................................13
Readback Tag........................................................................................14
Type.......................................................................................................14
Comment...............................................................................................14
Default (3100/Non safety system only)..................................................14
Default On (3100/Non safety system only)............................................14
COMPLIANCE WITH CE MARK .............................................................15
ENVIRONMENTAL CONDITIONS ..........................................................17
REFERENCED COMPANIES..................................................................18
DEFINITIONS...........................................................................................18

4
Introduction
The 16-Channel Analog Output Cards provide high-precision analog output signals. This card
can be purchased factory-configured to generate 4 mA to 20 mA outputs for the current option; or
0V to +10V outputs or –10V to +10V outputs for the voltage option. All channels are isolated from
RTP chassis ground.
The 16-Channel Analog Output card’s model number determines the channel output options as
follows:
3236 Current Output Channels (4 to 20 mA)
3237 Voltage Output Channels (0 V to +10 V or –10 V to +10 V)
Each channel consists of a digital-to-analog converter. Individual D/A converters generate the
sixteen outputs. No field adjustments are necessary after the initial factory setup.
I/O bus checking diagnostics, card address tests, and configuration tests are performed each
time the controller accesses the card. All data and control transfers are performed twice, once
using the actual data and then using the data inverted. Both versions of the data are compared
to verify that all I/O bus data bits are functioning properly. The configuration code from the card is
compared to the I/O configuration to check that the correct card is installed in the rack. I/O Bus
slot address and control signal contention tests also are performed. Any fault detected sets
status bits in an error detection variable returned to the user application program.
Watchdog timers on the card can open all of the output channels in the event backplane
communication errors persist.

5
An indicator LED, located near the top of the front panel, indicates the overall health status of the
card. If this LED is on, the card is functioning normally; if it is off, the card is offline. If this LED is
on, but the card is shown in red on the NetArrays IOC screen and cannot be enabled, indicates
an error in the cards calibration data.
Specifications
Module Safety Integrity Level: NI
Address: Determined by the slot of the controller backplane
Number of channels: 16
Isolation: 500 VDC Channel to RTP System
Type of protection: Digital isolators (magnetic)
Type of Loads: Grounded
Common Points between Channels: All channels share an isolated common ground
Monotonicity with no missing codes: Yes
Resolution: 16 bits
Output Response: Outputs are in a high-impedance state at power-up. Outputs
drive to commanded levels when initialized by software.
Outputs are in a high-impedance state when powered-down.
Watchdog Timers:
Programmable 3.278msec to 13.4 seconds in steps of 3.278msec
Fixed 0.6 to 1.5 seconds
Power Requirements:
+5 VDC 300 mA
+24 (±10%) VDC 350 mA (from RTP backplane external voltage)
3236:
Output Signal Range: 4 mA to 20 mA Current Outputs
Full Scale Value: 20 mA
Analog output error:
Maximum error at 25 °C: ±0.1600% of Full Scale Current (±32 µA)
Temperature Coefficient: ±0.0120% of Full Scale Current/ ºC (±2.4 µA/ºC)
Maximum error (-20 to 60 °C):±0.5800% of Full Scale Current (±116 µA)
Note: To insure the stated Analog I/O specifications, you need five minutes of warm-up
time in a stable temperature environment.
Value of LSB: 366 nA
Settling Time: Less than 1msec for full range change
Typical Slew Rate: 0.04 mA/sec
Load Resistance: 100 minimum to 600 maximum
Crosstalk between Channels: -71 dB at D.C., A.C. (50 Hz & 60 Hz)
Non-Linearity: ±0.160% of Full Scale Value
Repeatability: ±0.160% of Full Scale Value at fixed temperature

6
Readback Latency 1 scan cycle maximum
Diagnostic Testing: No testing
3237:
Output Signal Range: 0 V to +10 V Voltage Outputs
–10 V to +10 V Voltage Outputs
Output Impedance: Less than 1.15 when outputs turned on
Full Scale Value: 10 V
Analog output error:
Maximum error at 25 °C: ±0.065% of Full Scale Value (±6.5 mV)
Temperature Coefficient: ±0.0030% of Full Scale Value/ ºC (±0.300 µV/ ºC)
Maximum error (-20 to 60 °C):±0.1700% of Full Scale Value (±17.5 mV)
Note: Accuracy measured using 5-foot cable and 4.75KΩ load
Note: To insure the stated Analog I/O specifications, you need five minutes of warm-up
time in a stable temperature environment.
Value of LSB: 335 V
Settling Time: Less than 1msec for full range change
Typical Slew Rate: 0.02 V/s (resistive load)
Load Resistance: 2000 minimum reference to Signal Return
Maximum Capacitive Load: 0.01 µF
Maximum Inductive Load: 50 mH
Crosstalk between Channels: -72 dB at D.C., A.C. (50 Hz & 60)
Non-Linearity: ±0.065% of Full Scale Value
Repeatability: ±0.065% of Full Scale Value at fixed temperature
Readback Latency 1 scan cycle
Diagnostic Testing: No testing
Termination Module Connectors: 37 pin D-Sub connector for use with the 3056/00 Digital
Cables. These cables have a diameter of 0.5 inches (1.27
centimeters) with a minimum bend radius of 4.6 inches
(11.69 centimeters).
Termination Module: 3099/60-100 Single Termination Module 16 Channel AO
Voltage (used with 3237 card)
3099/22-100 Single Termination Module - 16 Channel AO
Current (used with 3236 card)
Effect of Incorrect Field Wiring: Outputs can be shorted to ground indefinitely. Connections
may be left open indefinitely. Reversed terminal connections
results in reversed polarity output applied to load.
Termination Module Dimensions: All Termination Modules are 4.38 inches (11.1 centimeters)
in height and have 3.75 inches (9.5 centimeters) of depth.
The width for each termination module and the compatible
field wiring size is tabulated as following:

7
Model #
Description
Width
(")
Width
(cm)
Minimum
AWG
Maximum
AWG
3099/60-100
Single Termination Module - 16 channel isolated analog
output - Voltage
2.17
5.5
28
16
3099/22-100
Single Termination Module - 16 channel isolated analog
output - Current
3.64
9.2
28
16
Module dimension values are ± 0.05 inches or ± 0.127 centimeters!

8
Cabling
Adhere to the specified insulation strip length of 0.26 inches (6.5 mm) when you connect field
wiring to the terminal modules; excessive insulation strip lengths can cause an electrical hazard.
Do not exceed the specified torque when you secure the wires into the terminal module;
maximum torque is 2.2 inch-pounds (0.25 N-m).
Standard cables to termination modules are minimum 5 feet in length.
You must disable (offline) an I/O card before you can hot-swap it. After you replace an I/O card,
you must enable it to return it to operation. While NetArrays is operating in Debug mode, use the
I/O Configuration Form to disable or enable I/O cards. To hot swap an I/O card, first display the
card’s icon in the I/O Configuration Form. If the I/O card’s icon is red, you can remove it. If the
I/O card’s icon is yellow or green, select the icon and disable it before you remove the card. After
you replace the I/O card, select the card’s icon and re-enable it. The color of the icon changes to
green to indicate the card is online.
Warning! Never remove the card from the chassis with the termination cables
connected and the field power applied. Always disconnect the field power and cables
before removing the card from the chassis. Always insert the card into the chassis with
the cables and field power disconnected.
Pin
Signal
1 Top
Channel 0+
1 Middle
Channel 0-
1 Bottom
Channel 0 Shield
2 Top
Channel 1+
2 Middle
Channel 1-
2 Bottom
Channel 1 Shield
3 Top
Channel 2+
3 Middle
Channel 2-
3 Bottom
Channel 2 Shield
4 Top
Channel 3+
4 Middle
Channel 3-
4 Bottom
Channel 3 Shield
5 Top
Channel 4+
5 Middle
Channel 4-
5 Bottom
Channel 4 Shield
6 Top
Channel 5+
6 Middle
Channel 5-
6 Bottom
Channel 5 Shield
7 Top
Channel 6+
7 Middle
Channel 6-
7 Bottom
Channel 6 Shield
8 Top
Channel 7+
8 Middle
Channel 7-
8 Bottom
Channel 7 Shield
9 Top
Channel 8+
9 Middle
Channel 8-
9 Bottom
Channel 8 Shield
10 Top
Channel 9+
10 Middle
Channel 9-
10 Bottom
Channel 9 Shield
11 Top
Channel 10+
11 Middle
Channel 10-
11 Bottom
Channel 10 Shield
12 Top
Channel 11+
12 Middle
Channel 11-
12 Bottom
Channel 11 Shield
13 Top
Channel 12+
13 Middle
Channel 12-
13 Bottom
Channel 12 Shield
14 Top
Channel 13+
14 Middle
Channel 13-
14 Bottom
Channel 13 Shield
15 Top
Channel 14+
15 Middle
Channel 14-
15 Bottom
Channel 14 Shield
16 Top
Channel 15+
16 Middle
Channel 15-
16 Bottom
Channel 15 Shield
Figure 1: Field connections on the 3099/60-100 Termination Module.
Load
Ground
Load
Ground
Load
Load

Pin
Signal
TB1 Pin 1
Channel 0+
TB1 Pin 2
Channel 0-
TB1 Pin 3
Channel 0 Shield
TB1 Pin 4
Channel 1+
TB1 Pin 5
Channel 1-
TB1 Pin 6
Channel 1 Shield
TB1 Pin 7
Channel 2+
TB1 Pin 8
Channel 2-
TB1 Pin 9
Channel 2 Shield
TB1 Pin 10
Channel 3+
TB1 Pin 11
Channel 3-
TB1 Pin 12
Channel 3 Shield
TB1 Pin 13
Channel 4+
TB1 Pin 14
Channel 4-
TB1 Pin 15
Channel 4 Shield
TB1 Pin 16
Channel 5+
TB1 Pin 17
Channel 5-
TB1 Pin 18
Channel 5 Shield
TB2 Pin 1
Channel 6+
TB2 Pin 2
Channel 6-
TB2 Pin 3
Channel 6 Shield
TB2 Pin 4
Channel 7+
TB2 Pin 5
Channel 7-
TB2 Pin 6
Channel 7 Shield
TB2 Pin 7
Channel 8+
TB2 Pin 8
Channel 8-
TB2 Pin 9
Channel 8 Shield
TB2 Pin 10
Channel 9+
TB2 Pin 11
Channel 9-
TB2 Pin 12
Channel 9 Shield
TB2 Pin 13
Channel 10+
TB2 Pin 14
Channel 10-
TB2 Pin 15
Channel 10 Shield
TB2 Pin 16
Channel 11+
TB2 Pin 17
Channel 11-
TB2 Pin 18
Channel 11 Shield
TB3 Pin 1
Channel 12+
TB3 Pin 2
Channel 12-
TB3 Pin 3
Channel 12 Shield
TB3 Pin 4
Channel 13+
TB3 Pin 5
Channel 13-
TB3 Pin 6
Channel 13 Shield
TB3 Pin 7
Channel 14+
TB3 Pin 8
Channel 14-
TB3 Pin 9
Channel 14 Shield
TB3 Pin 10
Channel 15+
TB3 Pin 11
Channel 15-
TB3 Pin 12
Channel 15 Shield
TB3 Pin 13
No Connection
TB3 Pin 14
No Connection
TB3 Pin 15
No Connection
TB3 Pin 16
No Connection
TB3 Pin 17
No Connection
TB3 Pin 18
No Connection
Figure 2: Field connections on the 3099/22-100 Termination Module.
Ground
Load
Load

10
Failure Rates in Accordance to IEC 61508
The 3236 and 3237 analog output cards cannot be used for safety-critical functions. However, the
module is non-interfering with other safety-critical modules and therefore can be used for non-
safety related functions.

11
Software Configuration
NetArrays Configuration
Each output point is controlled by a Floating-point Variable object with the corresponding Tag. A
Floating-point readback can be read to compare the actual output from the card. NetArrays also
returns an error detection status word for the card. This card includes a Watchdog Timer, which
can disable the outputs if the processor fails to access the card within the allotted time.
NOTE: Properties for the 3236 and 3237 cards are the same

12
Card Properties
Watchdog Timer
When enabled, the Watchdog Timer will disable the outputs if the card is not accessed by the
controller within 150 ms. When disabled, the Watchdog Timer has no effect on the card's
operation.
Integer Error Detection
The Error Detection input is an Int Variable that can be used to detect an I/O card failure.
NetArrays assigns a default Tag to this variable when the card is added to the I/O configuration.
A Card Timeout Error (Bit 0) will set the Error Latch bit (Bit14), which will remain set until this bit is
cleared to zero by an operator. While the Error Latch is set, the card will be offline and the target
node will not attempt to communicate with it. Note that most cards do not use all the status bits
shown. Any unused bits will always equal zero.
15
14
13
12
11
10
9
8
7
6
5
4
3
2
1
0
ERR
LTCH
DATA
ERR
DATA
INV
CARD
ID
CARD
ERR
CBL
ERR
LOOP
BACK
CH
FAIL
TIME
OUT
Bit 14 Card Error Latch
This status bit indicates that a Card Timeout Error occurred on the I/O card, and that it
has been taken offline. The card will not be initialized or placed online until this bit is
cleared in the project program or operator intervention.
If this bit is set, it must be cleared to return the card to operation. The correct way to
clear this bit is to select the card’s icon in the I/O configuration Form while NetArrays is
operating in Debug mode and answer “Yes” to the prompt. See I/O Card Status and
Control. (It is also possible to change the value of this variable by forcing an Integer Bit
Variable object, with Bit 14 selected in the object's properties, to zero. Do not clear the
entire Error Detection Integer Variable to zero.)
Bit 9 Backplane Bus Data Error
This status bit is applicable only to I/O cards with Backplane Bus data checking
capability. It indicates that a data error was detected in a data or command transfer to or
from an I/O card.
Bit 8 Data Invalid
This status bit indicates that the I/O card is not ready to send valid data.
Bit 7 Card ID Does Not Match I/O Configuration
This bit indicates that the ID code read from the I/O card does not match the card type
specified in the NetArrays I/O configuration.
Bit 6 Card Error
This bit indicates that a hardware timeout is reported by PLD.
Bit 5 Cable Detect Error
This bit indicates that one or more of the cables are not connected to the I/O card or
between the I/O card and the termination block.
Bit 4 Loopback Error
This bit indicates that the card has failed a loopback test. The actual output from the card
does not equal the expected output.

13
Bit 1 Channel Failure
This bit indicates that the card has a failure on one or more of its channels. Examine the
channel error status variable to determine the failed channel.
Bit 0 Card Timeout Error
This bit indicates that there was no response from the I/O card. The card is not returning
a ready test signal, is offline, or has been removed from the chassis. This bit sets the
Card Error Latch (Bit 14).
Integer Channel Error Status
The bits of this Int input represent the last analog output states written to the card. A 1 indicates
that the channel has readback or fault error. NetArrays assigns a default Tag to this variable
when the card is added to the I/O configuration.
15
14
13
12
11
10
9
8
7
6
5
4
3
2
1
0
Chan
15
Chan
14
Chan
13
Chan
12
Chan
11
Chan
10
Chan
9
Chan
8
Chan
7
Chan
6
Chan
5
Chan
4
Chan
3
Chan
2
Chan
1
Chan
0
Integer Card Revision
The card revision is an integer value, which equals to the revision number of the PLD code.
NetArrays assigns a default Tag to this variable when the card is added to the I/O configuration.
Reassign this Tag as required to access this card revision in the project program.
Integer Cal Date
This is an encoded date when the card was calibrated in the format YYDDD where YY is the last
2 digits of the year and DDD is the day within the year.
Integer Cal Serial Number
This is a serial number recorded when the card was calibrated.
I/O Channel Properties
Channel
Each channel may be configured as a Float output Disabled. For the 3236 (current) card, this
value represents the output current in mA. For the 3237 (voltage) card, this value represents the
output voltage in V. For example, if the 3236 card is used, a value of “10” should generate a 10
mA output in current mode. The Type selection specifies the outputs high and low limits, so even
if the value is greater than themaximum output or less than the minimum output, the output will
be appropriately limited. Example: When the type is set to 4 –20 mA, a zero value will still
generate a 4 mA output.
If "Disabled" is selected, the channel is disabled. You can disable any unused channel to avoid
scanning unconnected outputs.
I/O Tag
Each Float channel is controlled by a Float Variable object. NetArrays assigns a Tag to each
channel when the card is added to the I/O configuration.
Note! All unused un-terminated I/O points must be disabled in IO Configuration.

14
Readback Tag
The Readback Tag column specifies the Tag assigned to the readback input of the channel. The
Readback input can be enabled or disabled by checking or un-checking the box in this column. If
the channel is Disabled, this column entry is disabled. NetArrays assigns a default Tag to this
variable when the card is added to the I/O configuration.
Type
For the 3236 (current) card, select a type of current 4-20mA. For the 3237 (voltage) card, select a
type of voltage 0-10V, or voltage +/-10V.
Comment
Enter up to 255 characters for comments associated with the corresponding tag. The comments
are informational only and are not required by any RTP NetSuite application.
Default (3100/Non safety system only)
Note! This property is available only if output card is used in non safety 3100 Node.
Specifies channel behavior when chassis to node communication is lost:
On - the output will be equal to the value configured in "Default On" property
Off - the output will be off
Freeze - output value will be frozen at last value
Default On (3100/Non safety system only)
Note! This property is available only if the output card is used in non safety 3100 Node and
Default property is set to On.
The channel is set to a value configured in this property during a period of no communication with
the Node Processor.

15
Compliance with CE Mark
This section describes how to install and operate RTP equipment for use in the European Union
(EU) to comply with the requirements of the CE Mark and its referenced standards. The
procedures in this section apply also to other environments where provisions of the EU’s EMC
and Low Voltage Directives are either required or desirable.
RTP Corporation has successfully tested and reviewed its products to the stringent requirements
of the European Union’s EMC Directives (2004/108/EC) and Low Voltage Directive (2006/95/EC).
In order for the equipment to meet the requirements of these directives, the equipment
must be installed and operated in accordance with these instructions.
These tests and reviews are in accordance to EN 61131-2:2007 as listed in the next section.
Information on the tests performed and the standards involved is available from RTP Corporation.
To comply with the requirements of the CE Mark and its referenced standards, the system
integrator, installer, and end user must store, integrate, install, and operate this equipment in
accordance with the following guidelines.
1. Compliance with all product specific instructions (including but not limited to storage
instructions, installation instructions, operating instructions, maintenance instructions,
disposal instructions, and specifications) is required.
2. RTP equipment is rated for use in Installation Category (Overvoltage Category) II and
Pollution Degree 2 environments in accordance with standard IEC 664.
3. To assure that an Operator is not exposed to electrical hazards, all equipment capable of
electrical hazards must be housed in a grounded enclosure (equipment cabinet/rack) that
limits access to the equipment only to Service Personnel. Limited access may include
enclosure doors and side panels, which are locked or require a tool to open. To assure
compliance with the EMC requirements, the equipment must be housed in an enclosure
(equipment cabinet/rack) that provides EMC shielding. Compliance testing was
performed in a shielded equipment rack provided by Hoffman Concept® Wall Mounted
Enclosure model number CSD242420. To assure compliance, the equipment must be
installed in this style cabinet, or one with similar or greater RF attenuation characteristics.
The cabinet should be outfitted with continuous copper finger gasketing and copper foil
along all seams and joints.
4. The Service Personnel must be trained to operate the equipment and must be aware of
the potential of electrical hazards of the equipment and of the field I/O signals connected
to the equipment.
5. Hazardous voltage warning labels must be applied to the enclosure doors adjacent to the
locking mechanisms to warn the Service Personnel that hazardous voltages are
contained within the enclosure, if modules carrying 120 V and above are used.
6. Hazardous voltage warning labels also must be applied to the termination modules
(which carry 120 V and above), adjacent to the external connectors, to warn the Service
Personnel that hazardous voltages are present at the module's terminal blocks.
7. To assure compliance with the EMC requirements, the equipment must have all
communications, power, and field signal cabling exiting the enclosure enclosed in metal
conduits or shielded wireways. These conduits must provide EMI/RFI shielding and must
be terminated at the enclosure shell. There must be no uncovered openings in the
cabinet. Connections between the cabinet and conduit must be made with conduit
connectors making good (low impedance) electrical contact to the enclosure. Input
mains power to the enclosure and mains power fed to switching digital output I/O cards
and modules must be filtered by AC mains filters with attenuation characteristics of

16
Corcom VR series filters or with similar filters with equal or greater attenuation
characteristics.
8. DC input mains power to the enclosure and mains power must be filtered by a DC mains
filters with attenuation characteristics of Corcom 6EH1 series filters or with similar filters
with equal or greater attenuation characteristics.
9. Insulation strip length of 0.26 inches (6.5 mm) is required on all field wirings to the I/O
card termination modules.
10. The disposal of any electronic products must be in accordance with local regulations (e.g.
Directive 2002/96/EC of the European Parliament and of the Council on waste electrical
and electronic equipment). Some RTP Corporation products contain materials that may
be detrimental to the environment. These materials may include, but are not limited to
lead (in solder) and lithium (in batteries).
11. Prior to storage or shipping, the equipment must be packaged in accordance with the
following guidelines:
●Inventory all items and inspect all components for damage.
●Verify that all fasteners are properly tightened and that the chassis I/O module
retaining bar is properly installed.
●Wrap the chassis assembly in plastic bubble wrap.
●Select a suitable shipping box that provides at least 1½ inches of space between the
equipment and all sides of the box. This space shall be tightly packed with packing
peanuts or bubble wrap to protect the equipment during storage or shipping.
●Close and secure the box with suitable packing tape.
●Do not stack boxes more than three high. Store the boxes in a protected, dry
environment. Do not expose the boxes to rain or environmental conditions beyond
the ranges specified for the equipment in this document.

17
Environmental Conditions
The modules are rated for the following environmental conditions:
Specification Type
Recommended Range
Test Specification
Operating Temperature
-20 ºC to 60 ºC
IEC 60068-2-30, Db
RTP Type Testing
Operating Temperature Change
10 ºC/minute
IEC 60068-2-14 Test Nb
Operating Humidity
10% to 95% non-condensing
IEC 60068-2-30, Db
Storage Temperature
-40 ºC to 85 ºC
IEC 60068-2-1 Tests Ab, Ad
IEC 60068-2-2 Tests Bb, Bd
RTP Type Testing
Storage Temperature Change
10 ºC/minute
IEC 60068-2-14 Test Na
Storage Humidity
0% to 100% condensing
IEC 60068-2-30, Db
Vibration
9 Hz to 150 Hz at 1 g
IEC 60068-2-6, Fc
Mechanical Shock
15 g for 11 milliseconds
IEC 60068-2-27, Ea
Electrostatic Discharge Immunity
±6 kV contact
IEC 61000-4-2
Radiated E-Field Immunity
80 MHz to 1 GHz at 20 V/m
1 GHz to 2.1 GHz at 10 V/m
2.1 GHz to 2.5 GHz at 5 V/m
2.5 GHz to 2.7 GHz at 1 V/m
IEC 61000-4-3
Pulsed Magnetic Field
300 A/m
IEC 61000-4-9
Modules can be ordered with optional HumiSeal© conformal coating. In this case, the modules
can be installed in G3 harsh environmental conditions as defined in standard ISA–S71.04–1985.
This equipment has been tested and found to comply with the limits for a Class A digital device,
pursuant to Part 15 of FCC Rules. These limits are designed to provide reasonable protection
against harmful interference when the equipment is operated in a commercial environment. This
equipment generates, uses, and can radiate radio frequency energy and, if not installed and used
in accordance with the instruction manual, may cause harmful interference to radio
communications. Operation of this equipment in a residential area is likely to cause interference
in which case the user will be required to correct the interference at his own expense.
This Class A digital apparatus complies with Canadian ICES-003.
Cet appareil numérique de la Classe A est conforme à la norme NMB-003 du Canada.

18
Referenced Companies
Corcom Inc.; Libertyville, Illinois, USA; 708-680-7400
Hoffman; Anoka, Minnesota, USA; 763-422-2178
Definitions
OPERATOR is any personnel other than SERVICE PERSONNEL. Requirements
assume that the OPERATOR is oblivious to electrical hazards, but does not act
intentionally in creating a hazard.
SERVICE PERSONNEL are assumed reasonably careful in dealing with obvious
hazards.
CE Conformité Européenne
EMC Electro-Magnetic Compatibility
EMI Electro-Magnetic Interference
EC European Community
EN European Norm
ESD Electro-Static Discharge
EU European Union
IEC International Electrotechnical Commission
MPU Main Processing Unit
MTTR Mean Time to Restoration
RF Radio Frequency
RFI Radio Frequency Interference
This manual suits for next models
1
Table of contents
Other RTP Network Card manuals
Popular Network Card manuals by other brands
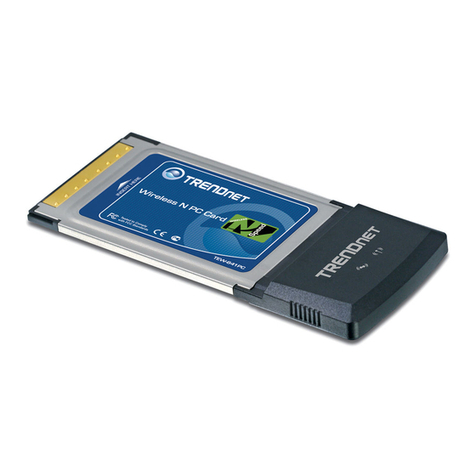
TRENDnet
TRENDnet TEW-641PC Quick installation guide

SUNRICH TECHNOLOGY
SUNRICH TECHNOLOGY N-460 user manual
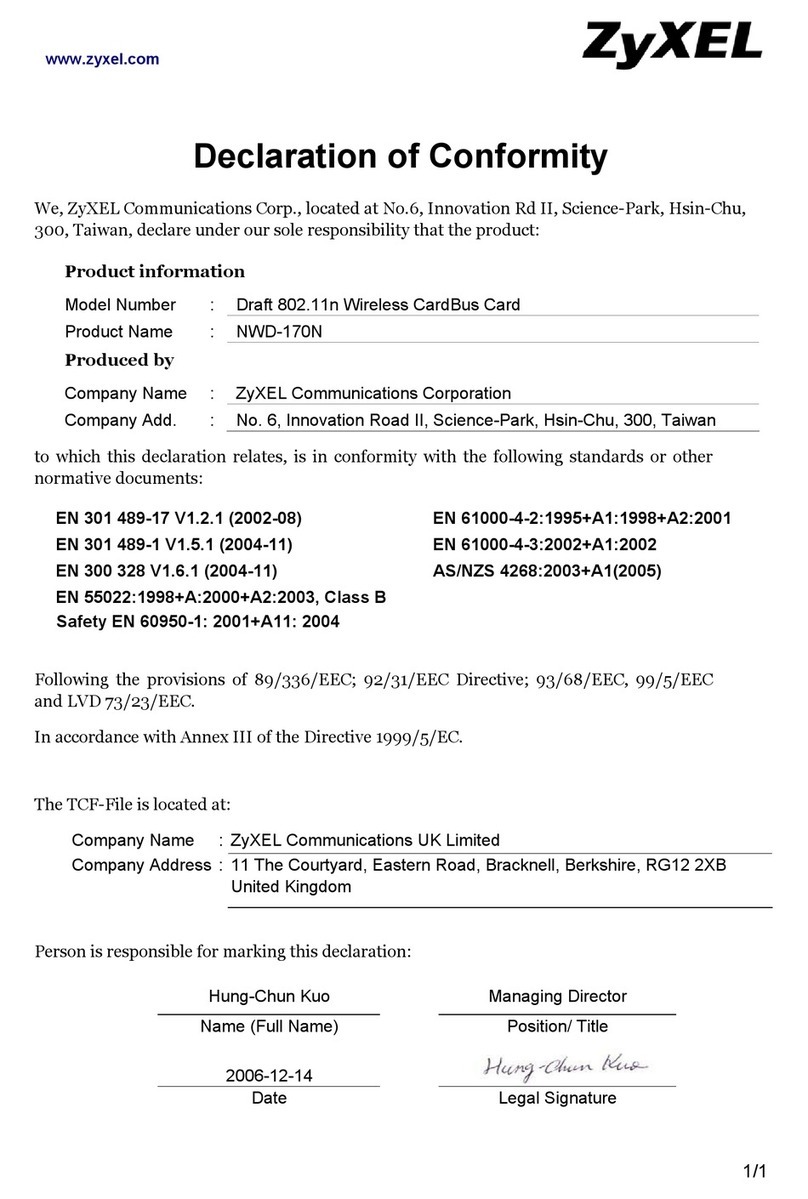
ZyXEL Communications
ZyXEL Communications NWD-170N Declaration of conformity
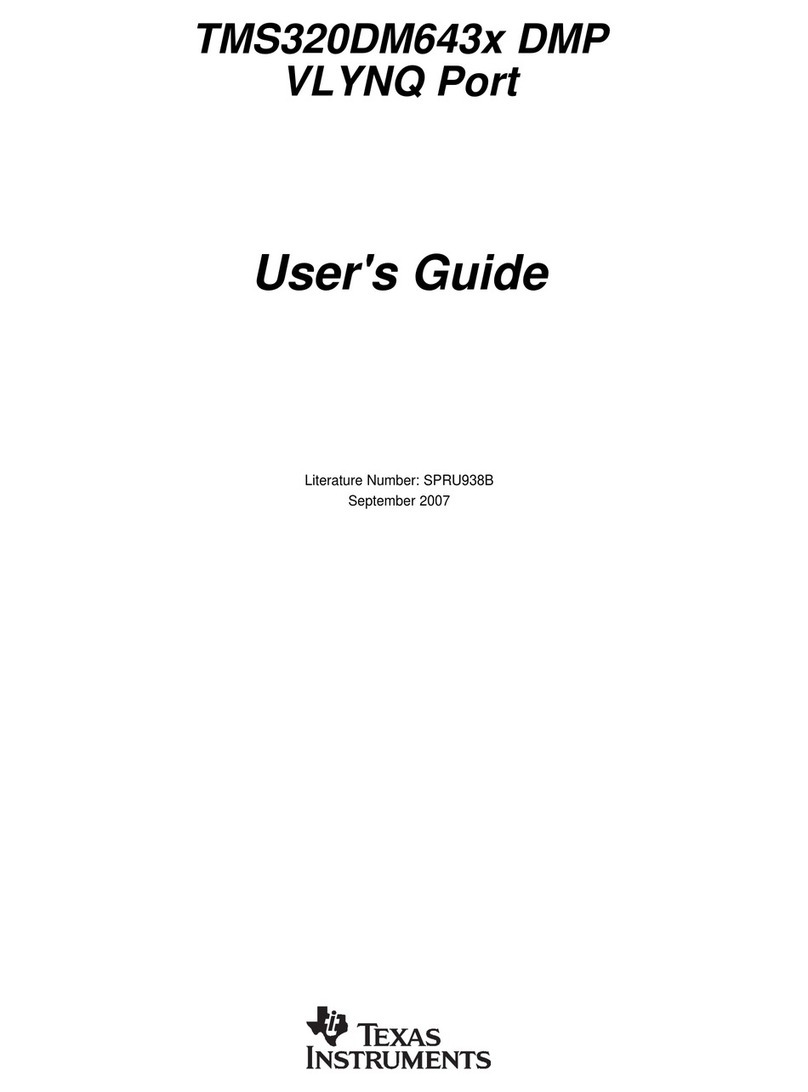
Texas Instruments
Texas Instruments SPRU938B user guide
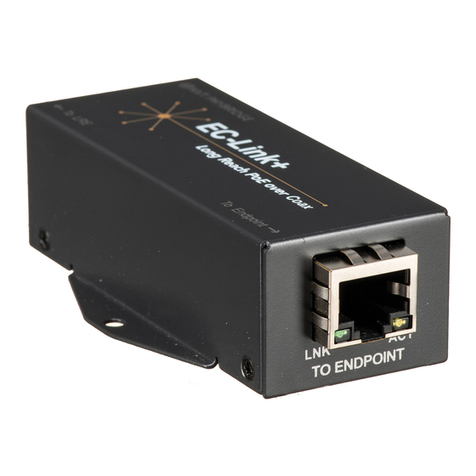
NVT Phybridge
NVT Phybridge EC-Link+ Quick install guide
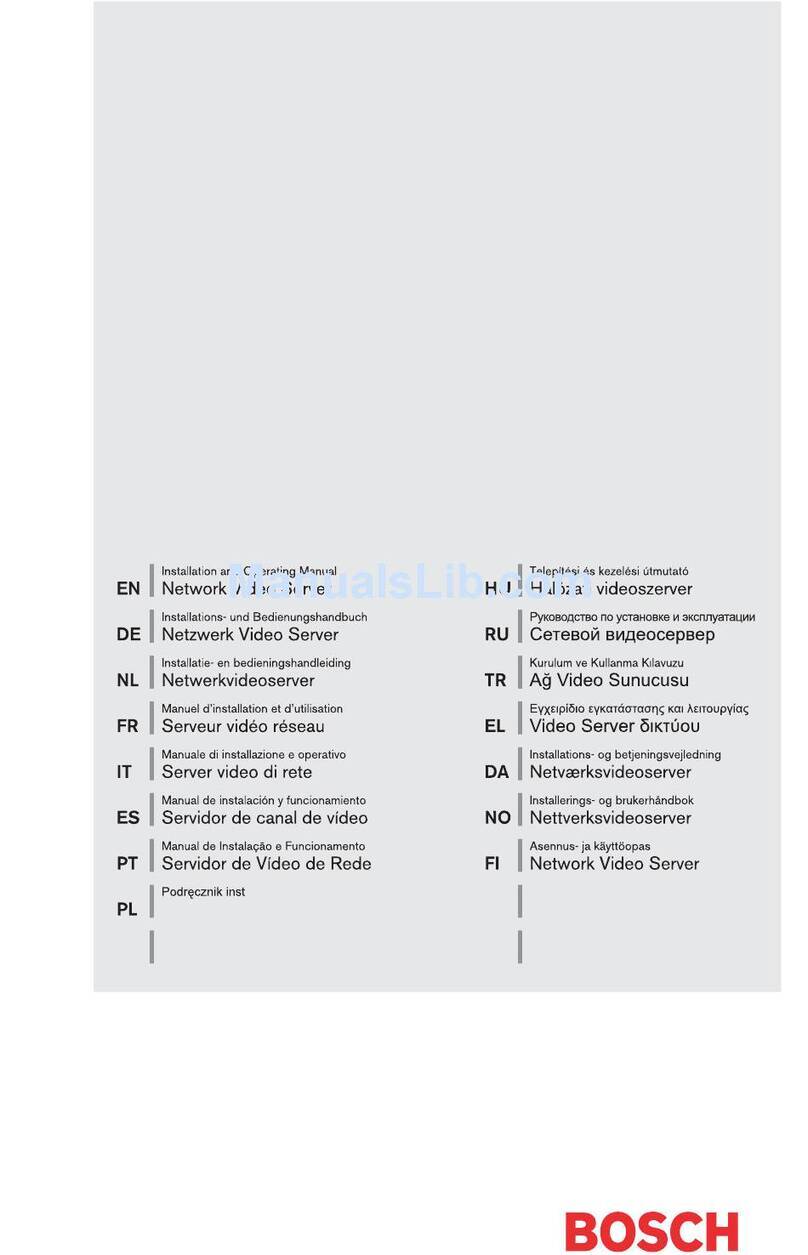
Bosch
Bosch VIP XD Installation and user guide