SGS SAT101 User manual

FOR YOUR SAFETY
PLEASE READ THESE INSTRUCTIONS CAREFULLY
AND RETAIN THEM FOR FUTURE USE.
OWNER’S MANUAL
SAT101
IMPACT WRENCH

PAGE 3
PAGE 2
RISK OF EYE OR HEAD INJURY
WHAT COULD HAPPEN HOW TO PREVENT IT
Air powered equipment and power tools
are capable of propelling materials such as
fasteners, metal chips, sawdust and other
debris at high speed which could result in
serious eye injury.
Always wear approved safety glasses with
side shields.
Disconnect air hose when tool is not in use.
Compressed air can be hazardous.
The air system can cause injury to soft
tissue areas such as eyes and ear. Particles
or objects propelled by the air stream can
cause injury.
For additional protection use an approved
face shield in addition to safety glasses.
Tool attachments can become loose or
break and fly apart, propelling articles at
the operator and others in the work area.
Make sure that any attachments are securely
assembled.
RISK OF FIRE OR EXPLOSION
WHAT COULD HAPPEN HOW TO PREVENT IT
Abrasive tools such as sanders and grinders,
rotating tools such as drills and impact tools
such as nailers, staplers, wrenches, hammers
and reciprocating saws are capable of gen-
erating sparks which could result in ignition
of flammable materials.
Never operate tools near flammable sub-
stances such as petrol, naphtha, cleaning
solvents etc.
Work in a clean, well-ventilated area free of
combustible materials.
Never use oxygen, carbon dioxide or other
bottled gases as a power source for air tools.
Exceeding the maximum pressure rating of
tools or accessories could cause an explo-
sion resulting in serious injury.
Use compressed air regulated to a maximum
pressure at or below the rated pressure of
any attachments.
Never connect to an air source that is capa-
ble of exceeding 200 psi.
Always verify prior to using the tools that the
air source has been adjusted to the rated air
pressure range.
SPECIFICATION
TOOL MODEL SAT101
CAPACITY 1/2 IN.
FREE SPEED 7000 RPM
MAX TORQUE 600 FT-LB / 880 Nm
AVERAGE AIR CONSUMPTION 6.5 SCFM
WORKING PRESSURE 90 PSI / 6.3 BAR
AIR INLET 1/4 IN.
AIR HOSE 3/8 IN.
LENGTH x HEIGHT 205 x 200 MM
WEIGHT 2.8 KGS
SAFETY GUIDELINES
Please read and fully understand the manual for information relating to protecting
YOUR SAFETY and PREVENTING EQUIPMENT PROBLEMS.
Indicates an immediately hazardous situation which if not
avoided will result in death or serious injury.
DANGER
WARNING
NOTE
Indicates a potentially hazardous situation which if not
avoided could result in death or serious injury.
Alerts the operator to useful information.
SAFETY INSTRUCTIONS
WARNING
DANGER
WWW.SGS-ENGINEERING.COM

PAGE 5
PAGE 4
SAFETY INSTRUCTIONS
RISK OF LOSS OF HEARING
WHAT COULD HAPPEN HOW TO PREVENT IT
Long term exposure to noise produced
from the operation of air tools can lead to
permanent hearing loss.
Always wear hearing protection.
INHALATION HAZARD
WHAT COULD HAPPEN HOW TO PREVENT IT
Abrasive tools such as grinders, sanders and
cut-off tools generate dust and abrasive
materials which can be harmful to the lungs
and respiratory system.
Always wear a properly fitting facemask or
respirator when using such tools.
Some materials such as adhesives and tar
contain chemicals whose vapours could
cause serious injury with exposure.
Always work in a clean, dry, well-ventilated
area.
RISK OF ELECTRIC SHOCK
WHAT COULD HAPPEN HOW TO PREVENT IT
Using air tools to attach electrical wiring can
result in electrocution or death.
Never use nail/staplers to attach electrical
wiring while energized
This tool is not provided with an insulated
gripping surface. Contact with a “live” wire
will also make exposed metal parts of the
tool “live” and can result in electrocution.
Avoid body contact with grounded surfaces
such as pipes, radiators and refrigerators.
There is an increased risk of electric shock if
your body is grounded.
Fasteners coming in contact with hidden
electrical wiring could cause electrocution
or death.
Thoroughly investigate the work piece for
possible hidden wiring before performing
work.
WARNING
WARNING
RISK OF CUT OR BURNS
WHAT COULD HAPPEN HOW TO PREVENT IT
Tools that cut, shear, drill, staple, punch &
chisel are capable of causing serious injury.
Keep the working part of the tool away
from hands and body.
DANGER
DANGER
SAFETY INSTRUCTIONS
RISK OF INJURY
WHAT COULD HAPPEN HOW TO PREVENT IT
A tool left unattended or with the air hose
attached can be activated by unauthorized
persons leading to injury.
Remove air hose when tool is not in use
and store tool in secure location away from
reach of children and untrained users.
Air tools can inadvertently propel fasteners
or other materials in work area.
Use only parts, fasteners and accessories
recommended by SGS Engineering.
Keep work area clean and free of clutter.
Keep children and others away from tool
while it is in operation.
Keep work area well lit.
A wrench or a key that is left attached to a
rotating part of the tool increases the risk of
personal injury.
Remove adjusting keys and wrenches be-
fore turning the tool on.
Using inflator nozzles for duster applications
can cause serious injury.
DO NOT use inflator nozzles for duster ap-
plications.
Air tools can become activated by accident
during maintenance or tool changes.
Remove air hose to lubricate or add grind-
ing attachments, sanding discs, drills, etc.
to the tool.
Never carry the tool by the hose.
Avoid unintentional starting. Don’t carry the
tool with a finger on the trigger.
Only an authorised service representative
should perform repair servicing.
Air tools can cause the work piece to move
upon contact, leading to injury.
Use clamps or other devices to prevent
movement.
Loss of control of the tool can lead to injury
to self or others.
Never use tool while using drugs or alcohol.
Don’t over-reach. Keep proper footing and
balance. Keep handles dry, clean and free
from oil/grease. Stay alert. Watch what
you are doing. Use common sense. Do not
operate the tool when you are tired.
Poor quality, improper or damaged tools
such as grinding wheels, chisels, sockets,
drills, nailers, staplers, etc. can fly apart dur-
ing operation, propelling particles through-
out the work area causing serious injury.
Always use tool attachments rated for the
speed of the power tool. Never use tools
which have been dropped, impacted or
damaged by use. Use only impact grade
sockets on an impact wrench. Do not apply
excessive force to the tool; let the tool
perform the work.
WARNING
WWW.SGS-ENGINEERING.COM

PAGE 7
PAGE 6
SAFETY INSTRUCTIONS
RISK OF INJURY
WHAT COULD HAPPEN HOW TO PREVENT IT
Fasteners could ricochet or be propelled
causing serious injury or property damage.
Never point or discharge tool at self or oth-
ers. Do not pull trigger unless tool contact
safety device is against work surface.
Never attempt to drive fasteners into hard
surfaces such as steel, concrete, or tile.
Avoid driving a fastener on top of another
fastener. Position tool carefully so that
fasteners will be delivered to the proper
location.
Improperly maintained tools and accesso-
ries can cause serious injury.
Maintain the tool with care.
Keep a cutting tool sharp and clean. A
properly maintained tool, with sharp cutting
edges, reduces the risk of binding and is
easier to control.
There is a risk of bursting if the tool is dam-
aged.
Check for misalignment or binding of mov-
ing parts, breakage of parts and any other
condition that affects the tool’s operation.
If damaged, have the tool serviced and
repaired before use.
Use only accessories identified by SGS
Engineering as suitable for use with specific
tools.
Use of an accessory not intended for a
specific tool increases the risk of injury to
persons.
WARNING
RISK OF ENTANGLEMENT
WHAT COULD HAPPEN HOW TO PREVENT IT
Tools which contain moving elements, or
drive other moving parts, such as grinding
wheels, sockets, sanding discs, etc. can be-
come entangled in hair, clothing, jewellery
and other loose objects resulting in severe
injury.
Never wear loose fitting clothes or apparel
that contains loose straps or ties which
could become entangled in moving parts of
the tools. Remove any jewellery, watches,
identifications, bracelets or necklaces which
might become caught by the tool.
Keep hands away from moving parts. Tie
up or cover long hair. Always wear proper
fitting clothing and other safety equipment
when using the tool.
SAFETY GUIDELINES
1. Make sure that the air compressor being used for the air tool operation sup-
plies the correct output (CFM).
2. Have the tool in the “off” position when connecting the tool to the air supply.
3. Use normal 90 PSI (or ranging from 6.0 to 8.0kg) air pressure while running the
tool. High pressure and unclean air will shorten the tool’s life due to faster wear
and may also create a hazardous situation.
4. Drain water from air compressor tank daily as well as any condensation in the air
lines. Water in the air line may enter the tool and damage the tool mechanisms
at operation.
5. Clean the air inlet filter cartridge weekly. The recommended hook-up procedure
can be viewed in the diagram below.
6. Line pressure should be increased accordingly to make up for extra long air
hoses (usually over 8 metres). The minimum hose diameter should be 1/4” I.D.
and the fittings should have the same inside dimensions. But usually a 3/8”
I.D. air hose is recommended for air supply to get the best function of air tool
operation.
7. Use proper hoses and fittings. We do not suggest connecting quick change
couplings directly to the tool since they may cause failure due to vibration.
Instead, add a leader hose and connect coupling between air supply and hose
whip.
8. Check hoses for wear before individual use. Make certain that all connections
are securely fastened.
DANGER
1
WWW.SGS-ENGINEERING.COM

PAGE 9
PAGE 8
CARE & MAINTENANCE
The tool should be lubricated daily (or before each use) with air tool oil (not in-
cluded). Air tool oil is available from SGS Engineering. Do not use detergent oil.
During continuous operation, the tool should be oiled every 1 to 2 hours. This may
be done using an in-line oiler or manually. If done manually, proceed as follows:
1. Disconnect the tool from air supply. (See Figure 6)
2. Place a few drops of air tool oil into the air inlet. (See Figure 7) Avoid the misuse
of thicker oil which may lead to the reduced performance or malfunction.
3. Connect the tool to the air supply. Run the tool without load for a few seconds
to distribute the oil through the tool. Any excess oil may be propelled from the air
exhaust area so point the tool in a safe direction.
4. After operating the tool and before storing the tool, disconnect the air hose and
place 4 or 5 drops of air tool oil into the air inlet, then re-connect the air hose and
run the tool to evenly distribute the oil throughout the tool for approximately 30
seconds. This will prolong the tool life.
5. Avoid storing the tool in a humid environment which promotes rusting of internal
mechanisms. Always oil the tool before storage.
OPERATING INSTRUCTIONS
1. How to install/tighten threaded fasteners
Push the F/R valve knob (D) backward. Press the trigger (C).
Then the tool anvil (B) runs clockwise. (See Figure 1-a)
2. How to remove/loosen threaded fasteners
Push the F/R valve knob (D) forward. Press the trigger (C).
Then the tool anvil (B) runs counter-clockwise. (See Figure 2-a)
This tool features a power regulator valve. Rotate the F/R valve knob (D) until
desired output is achieved. The settings 1, 2, 3 are only for reference and do
not denote a specific power output. “Setting 1” is the least amount of power
while “Setting 3” is the most amount of power. Rotate the F/R valve knob (D)
either clockwiseor counter-clockwise having the triangle mark or hollow line on
the knob (D) pointing at any setting to get the desired power. (See Figure 3-a
& Figure 3-b)
FIGURE 1 FIGURE 2 FIGURE 3
FIGURE 6FIGURE 5FIGURE 4
FIGURE 1-a FIGURE 2-a FIGURE 3-a
FIGURE 3-b
WWW.SGS-ENGINEERING.COM

PAGE 11
PAGE 10
TROUBLESHOOTING
SERVICE AND REPAIRS
All quality tools will eventually require servicing or replacement of parts due to wear
from normal use. These operations should ONLY be performed by a licensed profes-
sional technician. Never try to repair the tool by yourself.
Disconnect tool from air supply before performing any
service procedure.
WARNING
SYMPTOM PROBLEM SOLUTION
Tool runs slowly or
will not operate
1. Grit or gum in tool.
2. No oil in tool.
3. Low air pressure.
4. Air hose leaks.
5. Pressure drops.
6. Worn rotor blade.
7. Moisture blowing out
of tool exhaust.
1. Flush the tool with air-tool oil or
gum solvent.
2. Lubricate the tool according to the
lubrication instructions in this manual.
3. Adjust the regulator on the tool
to maximum setting. Adjust the
compressor regulator to tool
maximum of 90 PSI.
4. Tighten and seal hose fittings if
leaks are found. Use sealing tape.
5. Be sure the hose is the proper
size. Long hose or tools using large
volumes of air may require a hose with
an I.D. of 1/2 in. or larger depending
on the total length of the hoses. Do
not use a multiple number of hoses
connected together with quick-
connect fittings. This causes additional
pressure drops and reduces the tool
power. Directly connect the hoses
together.
6. Replace rotor blade.
7. Water in tank: drain tank. (See air
compressor manual). Oil tool and run
until no water is evident. Oil tool again
and run 1-2 seconds.
Abnormal vibration
and/or excessive
heat develops in
the tool.
Improper lubrication. Follow proper lubrication procedures
in this manual.
PARTS DIAGRAM
WWW.SGS-ENGINEERING.COM

PARTS LIST
PART DESCRIPTION QTY
01
02
03
04
05
06
07
08
09
10
11
12
13
14
15
16
17
18
19
20
21
22
23
24
Main housing
Trigger sleeve
Trigger
Bolt
Screw
Regulat. knob (1)
Protect. grip (1)
Protect. grip (2)
Valve sleeve
O-ring
Valve stem
Spring
Steel ball
Regulat. knob (2)
Seal ring
Tilt valve
Spring
Muffler
Gasket
Air inlet
Greasecap screw
O-ring
O-ring
Middle casing
1
1
1
1
2
1
1
1
1
2
1
1
1
1
1
1
1
1
1
1
1
1
1
1
PART DESCRIPTION QTY
25
26
27
28
29
30
31
32
33
34
35
36
37
38
39
40
41
42
43
44
45
46
47
48
Bolt
Gasket
E-clip
Bearing
Rear plate
Cylinder
Rotor
Rotor blade
Front plate
Bearing
Hammer dog
Hammer case
Bolt
Anvil
O-ring
Retainer
Bushing
Spacer
V-cushion
Gasker
Front housing
Spacer
Set screw
Screw
1
1
1
1
1
1
1
6
1
1
2
1
2
1
1
1
1
1
1
1
1
4
4
4
EC Declaration of Conformity
This is an important document and should be retained
MANUFACTURER’S NAME:
TYPE OF EQUIPMENT:
PART NUMBER:
I, the undersigned, hereby declare that the equipment specied above con-
forms to the above European Communities Directive(s) and Standard(s).
PLACE:
DATE: (Signature)
Robert Wyatt
Company Secretary
Derby, UK
24th JUNE 2017
SGS Engineering (UK) Ltd
SGS Engineering (UK) Ltd
West Side Park
Raynesway
Derby, DE21 7AZ
Impact Wrench
SAT101
2006/42/EC Machinery Directive
2004/108/EC Electromagnetic Compatibility Directive
APPLICATION OF EC COUNCIL DIRECTIVES / STANDARD:
FOR YOUR SAFETY
PLEASE READ THESE INSTRUCTIONS CAREFULLY
AND RETAIN THEM FOR FUTURE USE.
Table of contents
Other SGS Impact Driver manuals
Popular Impact Driver manuals by other brands

Chicago Pneumatic
Chicago Pneumatic CP724H series Operator's manual
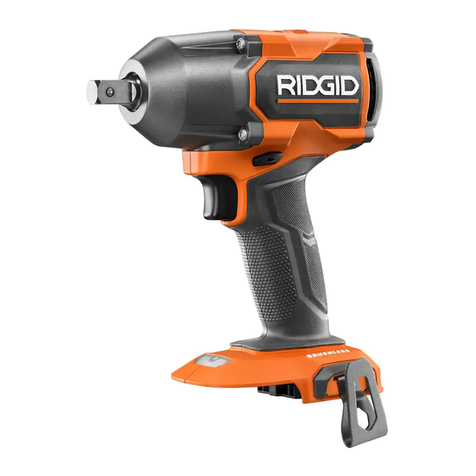
RIDGID
RIDGID R86012PD Operator's manual

Florida Pneumatic
Florida Pneumatic Universal Tool UT8350C General Safety Information & Replacement Parts
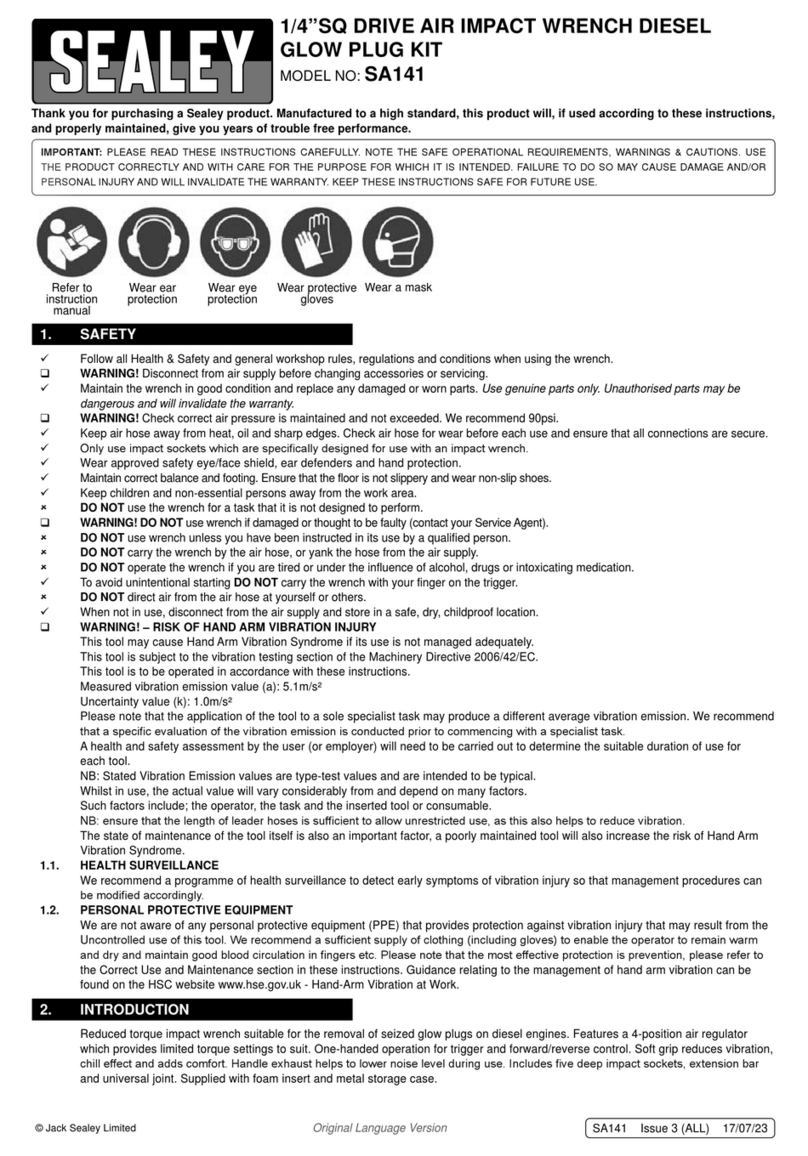
Sealey
Sealey SA141 manual

Makita
Makita BTP141Z technical information
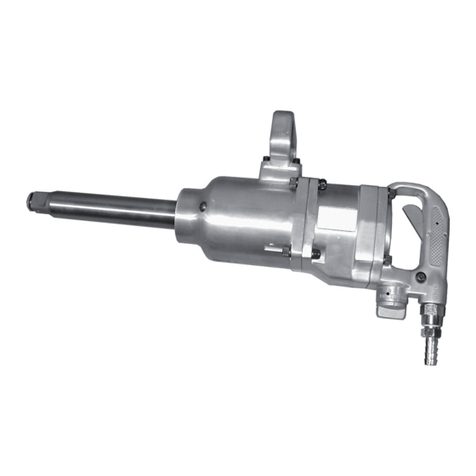
Central Pneumatic
Central Pneumatic 92622 Assembly and operating instructions
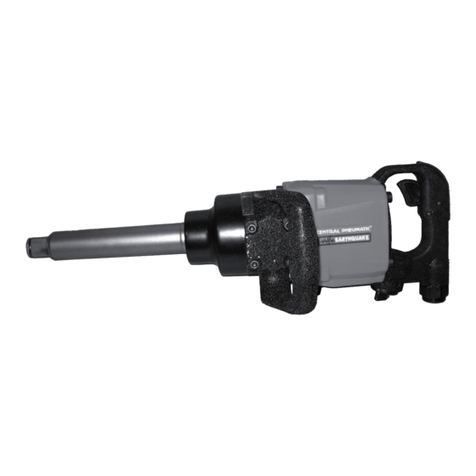
Central Pneumatic
Central Pneumatic Earthquake 92421 Assembly and operating instructions

Central Pneumatic
Central Pneumatic 95141 Set up and operating instructions

Central Pneumatic
Central Pneumatic 60629 owner's manual

Makita
Makita XDT08 instruction manual
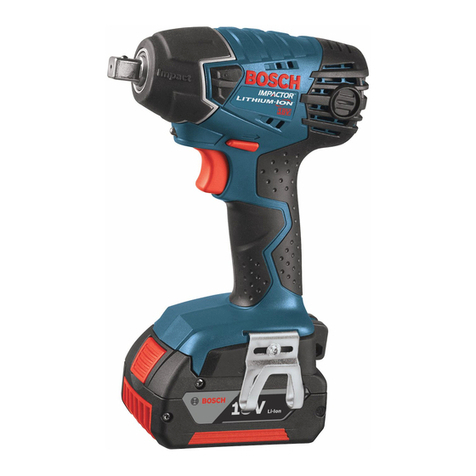
Bosch
Bosch 24618 Operating/safety instructions
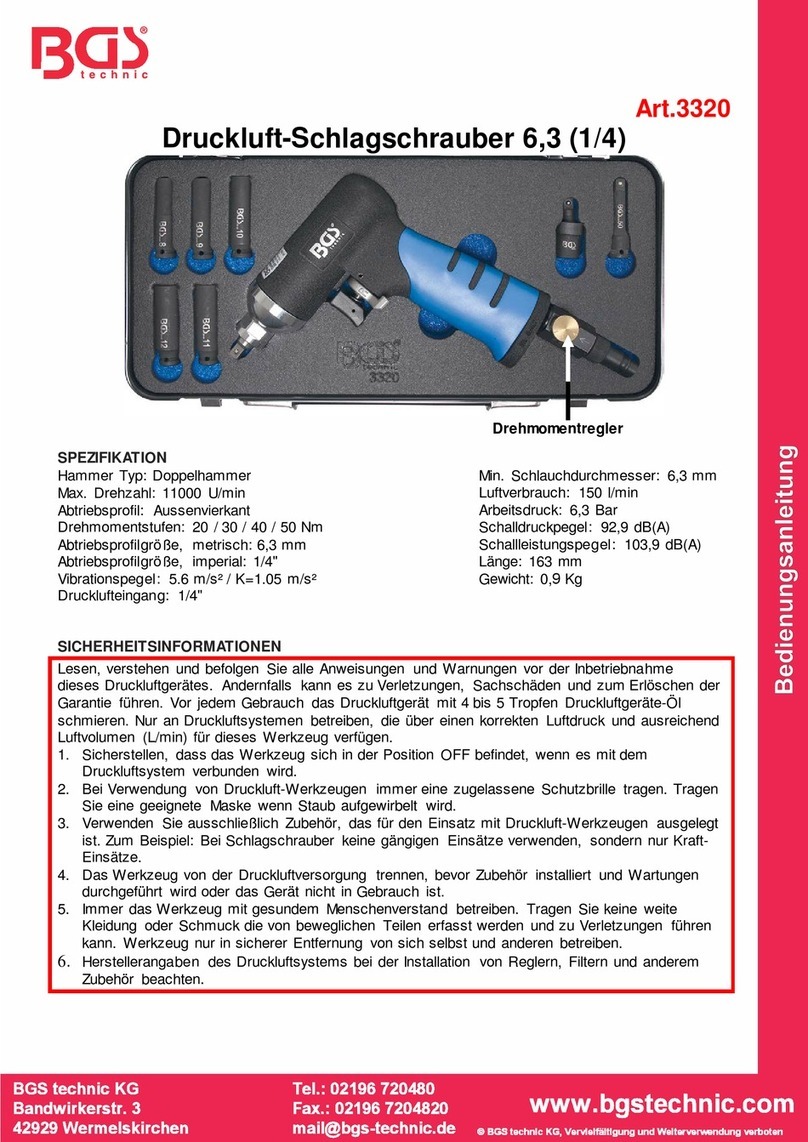
BGS technic
BGS technic BGS 3320 instruction manual