US Conec MTP Series User manual

Applications Engineering Notes
Copyright 2019 US Conec, Ltd.
Document Title MTP®Loopback Casing Installation
Document Number AEN-1430
Revision Number 1.0
Effective Date August 28, 2019

Document Title: MTP®Loopback Casing Installation
Document Number: AEN-1430, Rev. 1.0
2 of 17 THE USE OF SAFETY GLASSES FOR EYE PROTECTION IS RECOMMENDED
THE USE OF SAFETY GLASSES FOR EYE PROTECTION IS RECOMMENDED
1.0 Introduction
1.1 Purpose
To provide instructions on preparing bare ribbon for terminating one-row and
two-row fiber MTP®hardware in a Loopback Casing.
1.2 Scope
Covers single-mode or multimode bare ribbon, 12-fiber wide or 16-fiber wide,
and one-row or two-row fiber MT ferrules of any grade in an MTP connector and
Loopback Casing. This AEN assumes that the installer already has experience
terminating MTP connectors.
1.3 Description
The MTP Loopback Casing utilizes the novel MTP Push-Pull Tab mechanism to
provide for a simple, elegant method to encapsulate optical fibers in loopback test
assemblies. The interaction of this accessory with US Conec MTP connector
hardware greatly simplifies use of the loopback assembly by eliminating the need
to manually access the release slider during extraction from an MTP port.
Figure 1.3; refer to US Conec customer drawing number C13357
Note: The photos in this document are representative and may not reflect the
exact component color, cable construction, and tool model for your
specific installation. Dimensions shown are not to scale.
Follow the steps in this module in sequential order (e.g. Step 3.0 Step 3.1
Step 3.2 Step 4.0, etc.). Steps that end in “a” or “b” represent an either/or
option. For example, Step 3.1a is for a one-row ferrule, and Step 3.1b is for a two-
row ferrule. Depending on your particular installation (one-row or two-row), you
will follow either Step 3.1a or Step 3.1b. Once Step 3.1a or Step 3.1b is complete,
proceed to the next step.

Document Title: MTP®Loopback Casing Installation
Document Number: AEN-1430, Rev. 1.0
3 of 17 THE USE OF SAFETY GLASSES FOR EYE PROTECTION IS RECOMMENDED
1.4 Tools and Materials
Safety Glasses
Permanent Marker
Metric Ruler
Fiber Optic Side Cutters
Masking Tape
Loctite®4861™, 403™, 4860™, or 411™Prism®Instant Adhesive
WARNING: Refer to the manufacturer’s Safety Data Sheet (SDS) for
proper handling and potential hazards
2.0 Polarity and Loopback
There are several ways that fibers can be mapped to the optical physical layer interface of
a transceiver. When installing a link between two transceivers, the ultimate goal is to
provide an optical path for a transmitter on one end of a channel to the corresponding
receiver on the other end of the channel. When a loopback is in place, an optical path is
formed between a transmitter and receiver in the same transceiver.
Important: In order to assemble a loopback device correctly, it is important to know
the polarity of the transceiver that the loopback device will be used for.
Refer to the transceiver manufacturer’s specifications to determine
polarity.
Note: In this document, it is assumed that the polarity of the transceiver is compatible
with the guidelines in ANSI/TIA-568.3.
Loopback testing is primarily only performed to verify continuity in the fiber optic
infrastructure or troubleshoot transceiver hardware.
Note: A loopback device is not meant to be used to measure channel losses between
transceivers or link losses in the fiber optic infrastructure – use an Optical Loss
Test Set and applicable industry standards for this purpose.

Document Title: MTP®Loopback Casing Installation
Document Number: AEN-1430, Rev. 1.0
4 of 17 THE USE OF SAFETY GLASSES FOR EYE PROTECTION IS RECOMMENDED
2.1 One-row Polarity
Figure 2.1 represents a 12-fiber wide transceiver where the transmitters and
receivers are located in a single row. The loopback device will need to create an
optical path between TX0 and RX0, TX1 and RX1, TX2 and RX2, etc. This
convention would also apply to 16-fiber wide transceivers. This polarity is
compatible with ANSI/TIA-568.3.
Figure 2.1
2.2 Two-row Polarity
Figure 2.2 represents a 12-fiber wide transceiver with two rows. The transmitters
are located in one row, and the receivers are located in the other row. The
loopback device will need to create an optical path between TX0 and RX0, TX1
and RX1, TX2 and RX2, etc. This convention would also apply to 16-fiber wide
transceivers. This polarity is compatible with ANSI/TIA-568.3.
Figure 2.2
3.0 Fiber Ribbon Preparation
This step applies to multimode and single-mode fibers and 12-fiber wide and 16-fiber
wide ribbon. Bend insensitive fiber with minimum bending radius of 7.5mm is
recommended (e.g. ITU-T G.657.A2/B2 for single-mode or bend-insensitive multimode
fiber (BIMMF)). Refer to the transceiver manufacturer’s specifications to select the
appropriate fiber type and MT ferrule for your application. The following steps show
individual loose 250µm fibers. “Peelable” fiber ribbon may also be used, but it is outside
the scope of this document.

Document Title: MTP®Loopback Casing Installation
Document Number: AEN-1430, Rev. 1.0
5 of 17 THE USE OF SAFETY GLASSES FOR EYE PROTECTION IS RECOMMENDED
3.1a One-row Loopback
Polarity shown here is compatible with ANSI/TIA-568.3. For two-row loopback,
follow Step 3.1b.
3.1a.1 For a one-row loopback, you will need six fibers for a 12-fiber wide
ferrule and eight fibers for a 16-fiber wide ferrule. Cut the fibers into
155mm lengths. Use tape to keep the loose fibers together. Mark both ends
of the fibers 40mm from the end.
Figure 3.1a.1
3.1a.2 Load the fibers in a disposable loose fiber ribbonizing tool as shown in
Figure 3.1a.2. Refer to US Conec Document AEN-1414, “Operating
Instructions for the US Conec Disposable Loose Fiber Ribbonizing Tool”
to select the appropriate ribbonizing tool. The order of the fibers must
create the optical paths as described in Section 2.1 to be compatible with
ANSI/TIA-568.3. The 40mm marks made on the fibers in Step 3.1a.1
indicate the starting point for ribbonization. Adjust the fibers in the tool so
that the marks are aligned. Follow the instructions in AEN-1414 to
ribbonize the fibers.
Figure 3.1a.2

Document Title: MTP®Loopback Casing Installation
Document Number: AEN-1430, Rev. 1.0
6 of 17 THE USE OF SAFETY GLASSES FOR EYE PROTECTION IS RECOMMENDED
3.1a.3 Mark the ribbon 12mm from the start of ribbonization.
Figure 3.1a.3
3.1b Two-row Loopback
Polarity shown here is compatible with ANSI/TIA-568.3. For one-row loopback,
follow Step 3.1a.
3.1b.1 For a two-row loopback, you will need 12 fibers for a 12-fiber wide
ferrule and 16 fibers for a 16-fiber wide ferrule. Cut the fibers into 155mm
lengths. Use tape to keep the loose fibers together. Mark both ends of the
fibers 40mm from the end.
Figure 3.1b.1

Document Title: MTP®Loopback Casing Installation
Document Number: AEN-1430, Rev. 1.0
7 of 17 THE USE OF SAFETY GLASSES FOR EYE PROTECTION IS RECOMMENDED
3.1b.2 Load the fibers in a disposable loose fiber ribbonizing tool as shown in
Figure 3.1b.2. Refer to US Conec Document AEN-1414, “Operating
Instructions for the US Conec Disposable Loose Fiber Ribbonizing Tool”
to select the appropriate ribbonizing tool. The 40mm marks made on the
fibers in Step 3.1b.1 indicate the starting point for ribbonization. Adjust
the fibers in the tool so that the marks are aligned. Follow the instructions
in AEN-1414 to ribbonize the fibers on one end of the ribbon.
Figure 3.1b.2
3.1b.3 Load the fibers on the other end of the ribbon in the ribbonizing tool in the
same order as the previous step. Ribbonize the fibers starting at the 40mm
mark.
3.1b.4 Mark the ribbon 12mm from the start of ribbonization at both ends of the
ribbon.
Figure 3.1b.4

Document Title: MTP®Loopback Casing Installation
Document Number: AEN-1430, Rev. 1.0
8 of 17 THE USE OF SAFETY GLASSES FOR EYE PROTECTION IS RECOMMENDED
4.0 Terminating Fibers in MTP Connectors
4.1 MTP Connectors Compatible with Loopback Casing
Refer to the latest US Conec customer drawings listed in Table 4.1 to select from
the connector kit and ferrule options that are compatible with the Loopback
Casing.
Table 4.1
Description
US Conec
Customer Drawing
Termination
AEN
Kit, MTP Connector, Ribbon, for One-row Loopback
C21467
AEN-1403
Kit, MTP Connector, High Spring Force, Ribbon, for
Two-row Loopback
C21490 AEN-1410
Kit, MTP-16™ Connector, Ribbon, for One-row and
Two-row Loopback
C21531 AEN-1424
Assembly, Ferrule and Boot, One-row and Two-row
Loopback
C7593 N/A
Note: The two-piece, round spring push is also compatible with the Loopback Casing.
4.2 MTP Termination AEN
The following steps will refer to the corresponding MTP termination AEN listed
in Table 4.1 for additional instructions, materials, and equipment to strip, cleave,
and terminate the fibers in a ferrule and install the connector hardware.
Note: There is one major deviation from the instructions in the MTP termination
AEN when assembling a loopback device. During normal jumper cable
assembly, the connector hardware is slid onto the fiber ribbon first.
However, for a loopback termination, this is not possible. Therefore, the
spring push, spring, and ferrule boot will be installed after the ribbon has
been stripped and cleaved.
4.3a One-row Loopback
For two-row loopback, follow Step 4.3b.

Document Title: MTP®Loopback Casing Installation
Document Number: AEN-1430, Rev. 1.0
9 of 17 THE USE OF SAFETY GLASSES FOR EYE PROTECTION IS RECOMMENDED
4.3a.1 Insert the ribbon in the ribbon holder. Align the 12mm mark with the edge
of the holder (Figure 4.3a.1-1). Ensure that the loose-fiber portion of the
loopback stays within the ribbon channel of the holder (Figure 4.3a.1-2).
Close the front locking cover of the ribbon holder to secure the ribbon. Do
not close the rear locking cover (Figure 4.3a.1-3).
Figure 4.3a.1-1 Figure 4.3a.1-2
Figure 4.3a.1-3
4.3a.2 Strip and cleave the ribbon according to the appropriate MTP termination
AEN listed in Table 4.1. Remove the ribbon from the holder.

Document Title: MTP®Loopback Casing Installation
Document Number: AEN-1430, Rev. 1.0
10 of 17 THE USE OF SAFETY GLASSES FOR EYE PROTECTION IS RECOMMENDED
4.3a.3 Carefully insert the cleaved ribbon through the spring push until the
ribbonized section of the ribbon is past the spring push latches. The loop
in the ribbon will cause it to back out of the spring push. Use tape around
the fiber loop and spring push to secure the ribbon in position (Figure
4.3a.3-1). An alternate method to secure the ribbon is shown in Figure
4.3a.3-2.
Figure 4.3a.3-1 Figure 4.3a.3-2
4.3b Two-row Loopback
For one-row loopback, follow Step 4.3a.
4.3b.1 Insert the ribbon in the ribbon holder. Align the 12mm mark with the edge
of the holder (Figure 4.3b.1-1). Close the front locking cover of the ribbon
holder to secure the ribbon. Close the rear locking cover (Figure 4.3b.1-2).
Figure 4.3b.1-1 Figure 4.3b.1-2
4.3b.2 Strip and cleave the ribbon according to the appropriate MTP termination
AEN listed in Table 4.1.
Note: In accordance with the MTP termination AEN, when terminating a
two-row ferrule, the bottom row of ribbon will be 2mm longer than
the top row of ribbon. For a loopback termination, this is
accomplished by setting the slider on the bottom of the holder to
the 12mm cleaving position for one end of the ribbon and setting

Document Title: MTP®Loopback Casing Installation
Document Number: AEN-1430, Rev. 1.0
11 of 17 THE USE OF SAFETY GLASSES FOR EYE PROTECTION IS RECOMMENDED
the slider to the 10mm cleaving position for the other end of the
ribbon. It does not matter which end of the ribbon is 2mm longer.
4.3b.3 Remove the ribbon from the holder, and repeat Step 4.3b.1 for the other
end of the ribbon. Strip and cleave the other end of the ribbon. Remove the
ribbon from the holder.
4.3b.4 Hold the coated sections of both ends of the ribbon (i.e. do not hold the
ribbon by the stripped sections of bare fiber), twist the ribbon, and bring
the two ends together. This step will create the optical paths as described
in Section 2.2, which is compatible with ANSI/TIA-568.3.
4.3b.5 Carefully insert both rows of ribbon through the spring push until the
ribbonized sections of the ribbon are past the spring push latches. The loop
in the ribbon will cause it to back out of the spring push. Use tape around
the fiber loop and spring push to secure the ribbon in position.
Figure 4.3b.5
4.3b.6 Align the front coated edge of the ribbon, apply a small amount of instant
adhesive between the two rows near the start of ribbonization (Figure
4.3b.6-1), and affix the two rows together (Figure 4.3b.6-2).
Note: Do not apply so much instant adhesive that it overflows outside of
the two rows of ribbon.
Figure 4.3b.6-1 Figure 4.3b.6-2

Document Title: MTP®Loopback Casing Installation
Document Number: AEN-1430, Rev. 1.0
12 of 17 THE USE OF SAFETY GLASSES FOR EYE PROTECTION IS RECOMMENDED
4.4 The remaining steps apply to both one-row and two-row loopback assemblies.
Carefully slide the spring and ferrule boot onto the ribbon. Refer to the
appropriate MTP termination AEN listed in Table 4.1 to determine the correct
orientation of the ferrule boot relative to the ferrule.
Figure 4.4
4.5 Follow the steps in the appropriate MTP termination AEN listed in Table 4.1 to
terminate and polish the ferrule and install the connector hardware. The complete
MTP connector will look similar to Figure 4.5-3.
Figure 4.5-1 Figure 4.5-2
Figure 4.5-3

Document Title: MTP®Loopback Casing Installation
Document Number: AEN-1430, Rev. 1.0
13 of 17 THE USE OF SAFETY GLASSES FOR EYE PROTECTION IS RECOMMENDED
5.0 Loopback Casing Installation
5.1 Install the MTP connector in the non-handle half of the casing as shown. The
connector can be installed with the key up or key down. Ensure that the lip on the
connector outer housing is in the window of the casing and at the very edge of the
window (Figure 5.1-2); otherwise, the casing may not close properly in Step 5.2.
Figure 5.1-1 Figure 5.1-2
Note: Ensure the fibers do not extended beyond the covered section of the non-
handle half of the casing.
Figure 5.1-3 Figure 5.1-4
5.2 Install the handle half of the casing by interlocking the hooks with the non-handle
half first (Figure 5.2-1) then carefully snapping the two halves together. Ensure all
four side latches are fully engaged (Figure 5.2-2).
Figure 5.2-1 Figure 5.2-2

Document Title: MTP®Loopback Casing Installation
Document Number: AEN-1430, Rev. 1.0
14 of 17 THE USE OF SAFETY GLASSES FOR EYE PROTECTION IS RECOMMENDED
5.3 If a label will be affixed to the loopback assembly, avoid covering the window in
the casing. This will allow the outer housing to move freely within the casing.
Figure 5.3
6.0 Operation
6.1 Inserting Loopback Assembly
Align the loopback assembly and the adapter port with the connector key properly
oriented. Grasp the handle or the body of the casing and gently push into the port
until a “click” is heard. Ensure that the loopback assembly is inserted straight into
the port.
Figure 6.1
6.2 Extracting Loopback Assembly
Grasp the handle or the body of the casing and gently pull away from the port
until the connector disengages. Ensure that the loopback assembly is pulled
straight out of the port.
Figure 6.2

Document Title: MTP®Loopback Casing Installation
Document Number: AEN-1430, Rev. 1.0
15 of 17 THE USE OF SAFETY GLASSES FOR EYE PROTECTION IS RECOMMENDED
Appendix A
Testing
A.1 Endface Geometry
Refer to AEN-1915, “US Conec Recommended MT Ferrule Endface Geometries”.
A.2 Insertion Loss (IL)
The IL measurement procedures in this section reference Figure A.2. This section applies
to both one-row and two-row loopback assemblies.
Note: Make sure all ferrule end faces are inspected and clean. For testing a one-row
loopback, MTP-1, MTP-2, and MTP-4 can be replaced with individual single-
fiber connectors (e.g. LC, SC, etc.).
Figure A.2
A.2.1 It is recommended to use index matching gel between the mated pair MTP-1 and
MTP-2 at Position 1. The index matching gel will minimize potential polishing
anomalies at Position 1.
A.2.2 It is strongly recommended that MTP-3 uses the same grade ferrule as the Device
Under Test (DUT), which is the loopback assembly. Verify Encircled Flux
compliance at MTP-3 at the wavelength under test.
A.2.3 Insert MTP-3 into the Detector and reference. Mate MTP-3 and the DUT at
Position 2. Insert MTP-4 into the Detector at Position 3 to measure the IL of the
DUT at Position 2.
Note: The measured IL of the DUT will be the result of two mated pairs because
of the loopback.

Document Title: MTP®Loopback Casing Installation
Document Number: AEN-1430, Rev. 1.0
16 of 17 THE USE OF SAFETY GLASSES FOR EYE PROTECTION IS RECOMMENDED
A.3 Back Reflection (BR)
The BR measurement procedures in this section reference Figure A.3. This section
applies to both one-row and two-row loopback assemblies. The procedures in this section
assume that BR is measured using an optical continuous-wave reflectometer (OCWR) as
opposed to an optical time-domain reflectometer (OTDR).
Note: Make sure all ferrule end faces are inspected and clean. For testing a one-row
loopback, MTP-1, MTP-2, and MTP-4 can be replaced with individual single-
fiber connectors (e.g. LC, SC, etc.).
Figure A.3
A.3.1 It is recommended to use index matching gel between the mated pair MTP-1 and
MTP-2 at Position 1. The index matching gel will minimize potential polishing
anomalies at Position 1.
A.3.2 It is strongly recommended that MTP-3 uses the same grade ferrule as the Device
Under Test (DUT), which is the loopback assembly.
A.3.3 Terminate MTP-3 in index matching gel or alcohol and reference MTP-3 at
Position 2. Clean MTP-3 to completely remove the gel or alcohol. Mate MTP-3
and the DUT at Position 2.
A.3.4 Terminate MTP-4 in gel or alcohol. Measure the BR of the DUT at Position 2.
Note: The measured BR of the DUT will be the result of two mated pairs
because of the loopback.

Document Title: MTP®Loopback Casing Installation
Document Number: AEN-1430, Rev. 1.0
17 of 17 THE USE OF SAFETY GLASSES FOR EYE PROTECTION IS RECOMMENDED
•MTP®, MTP® PRO, MTP Elite®, MTP-16™, MXC®, MT Elite®, PRIZM®,
LightTurn®, PRIZM® MT, ELiMENT™, IBC™, and Eliminator™ are trademarks
or registered trademarks of US Conec, Ltd., Hickory, NC
•Loctite®, Prism®, 4861™, 411™, 403™, 4860™, 4851™, BIPAX®, TRA-
BOND™, and F113SC™ are trademarks or registered trademarks of Henkel IP &
Holding GmbH, Düsseldorf, Germany
Table of contents
Popular Cables And Connectors manuals by other brands

3M
3M 10350-1230 instructions
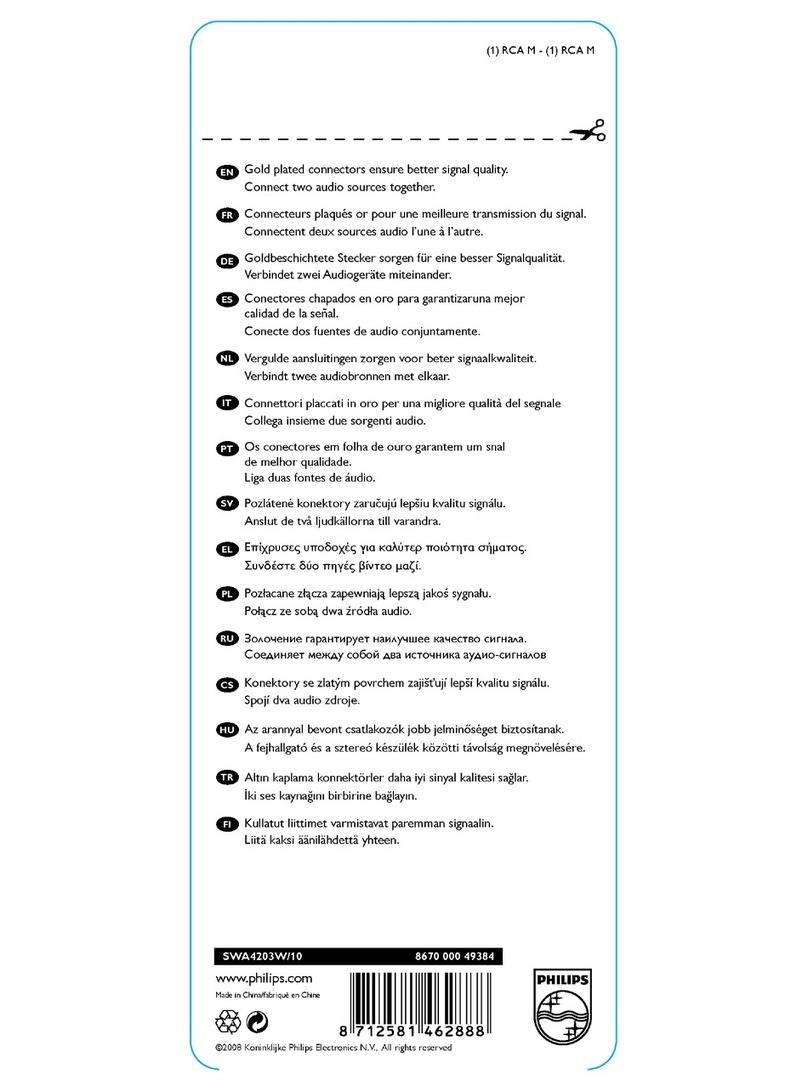
Philips
Philips SWA4203W/10 user manual
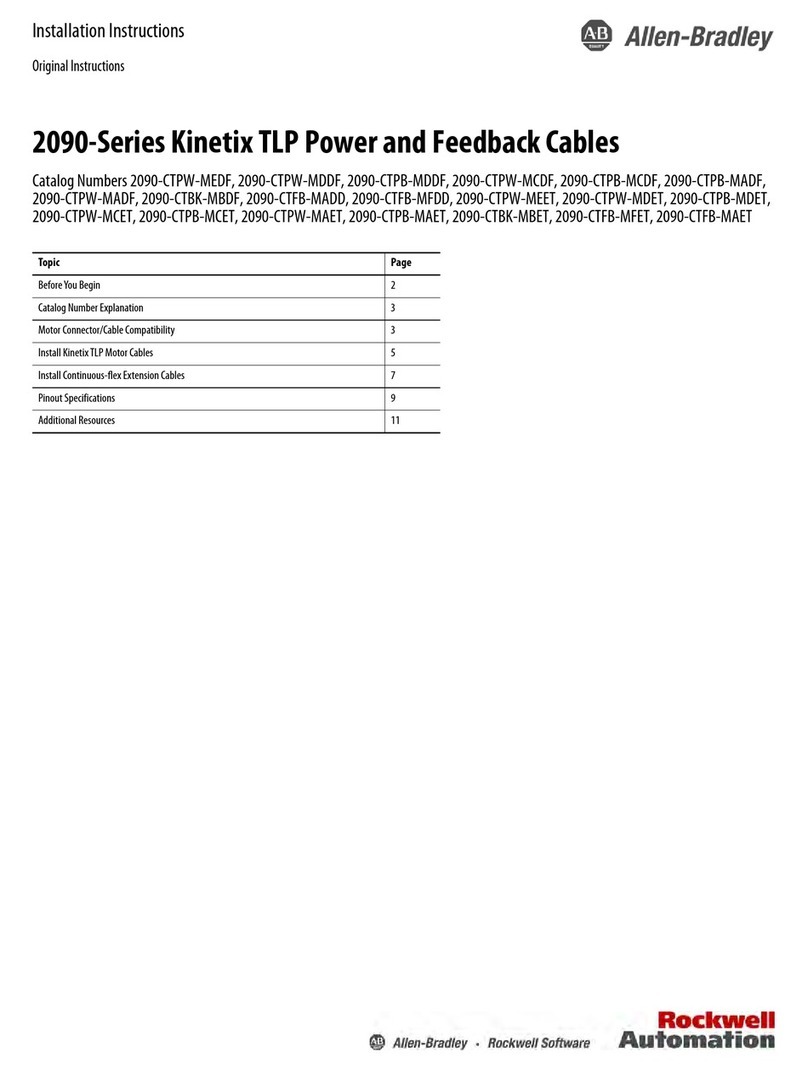
Rockwell Automation
Rockwell Automation Allen-Bradley Kinetix 2090 Series installation instructions
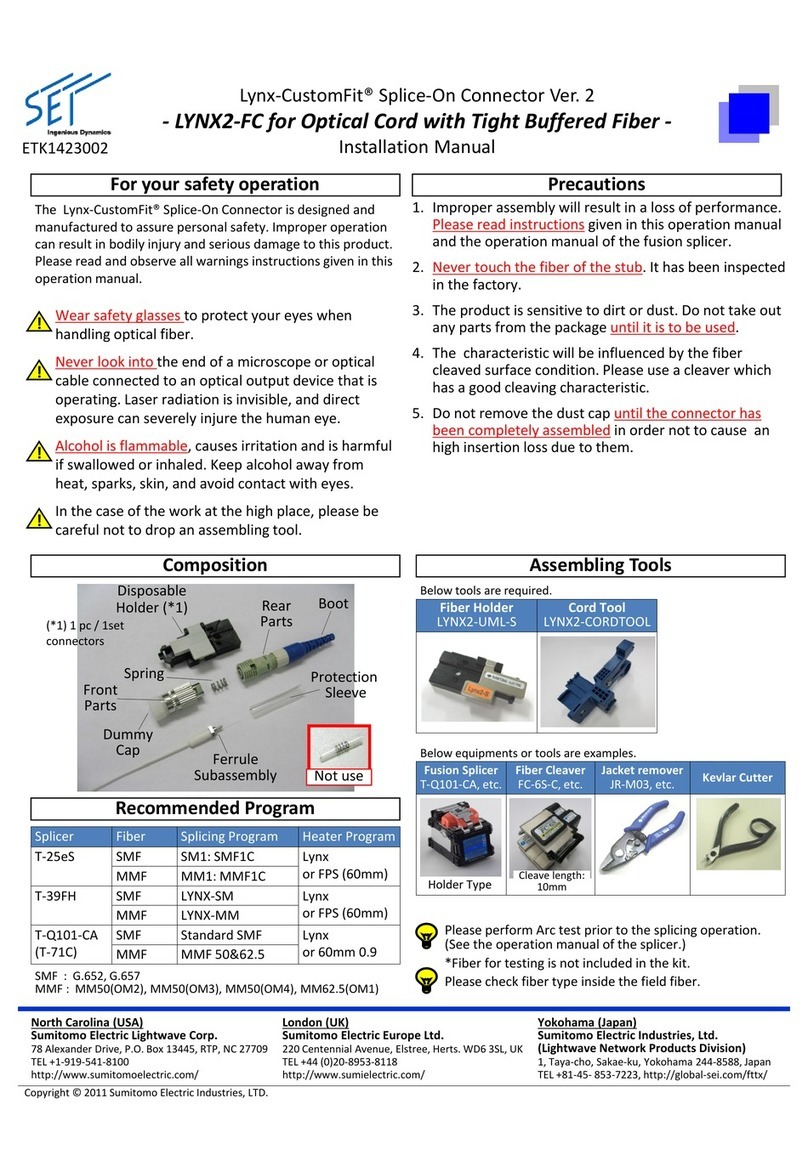
Sumitomo
Sumitomo Lynx-CustomFit LYNX2 installation manual

WolfPack
WolfPack HDTVHDMI-1x2 user manual
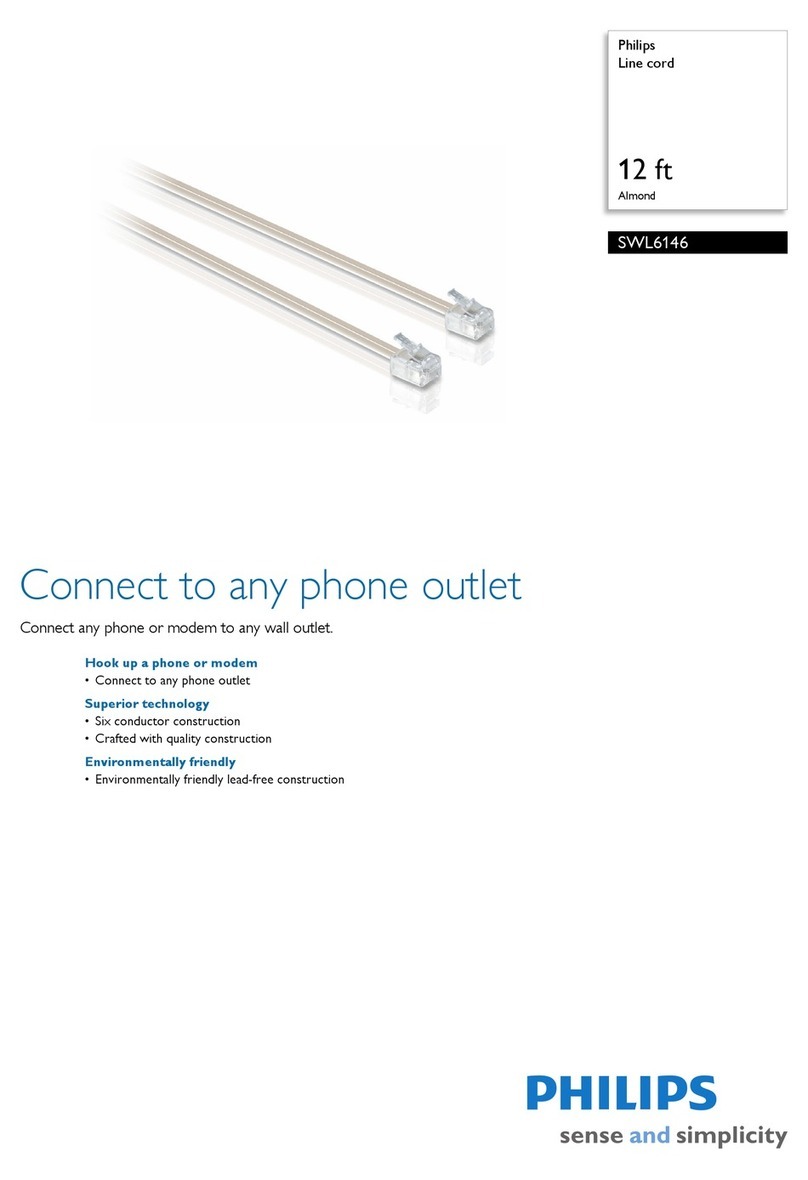
Philips
Philips Line Cord SWL6146 Specifications
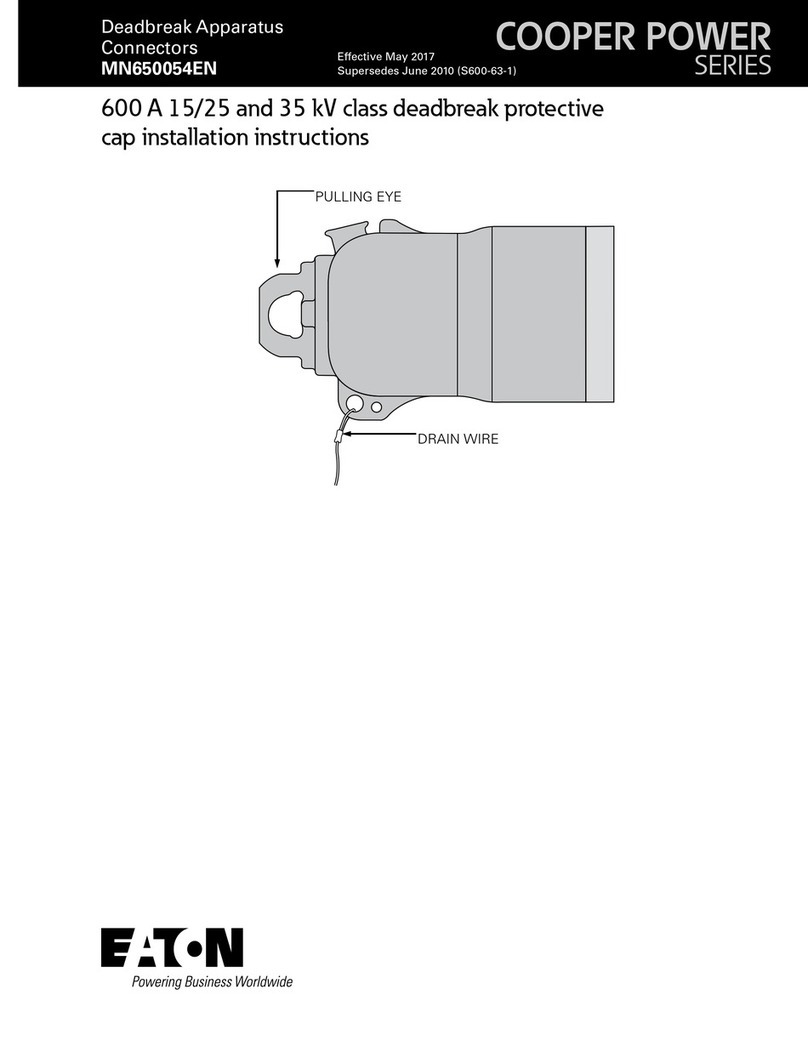
Eaton
Eaton COOPER POWER SERIES installation instructions
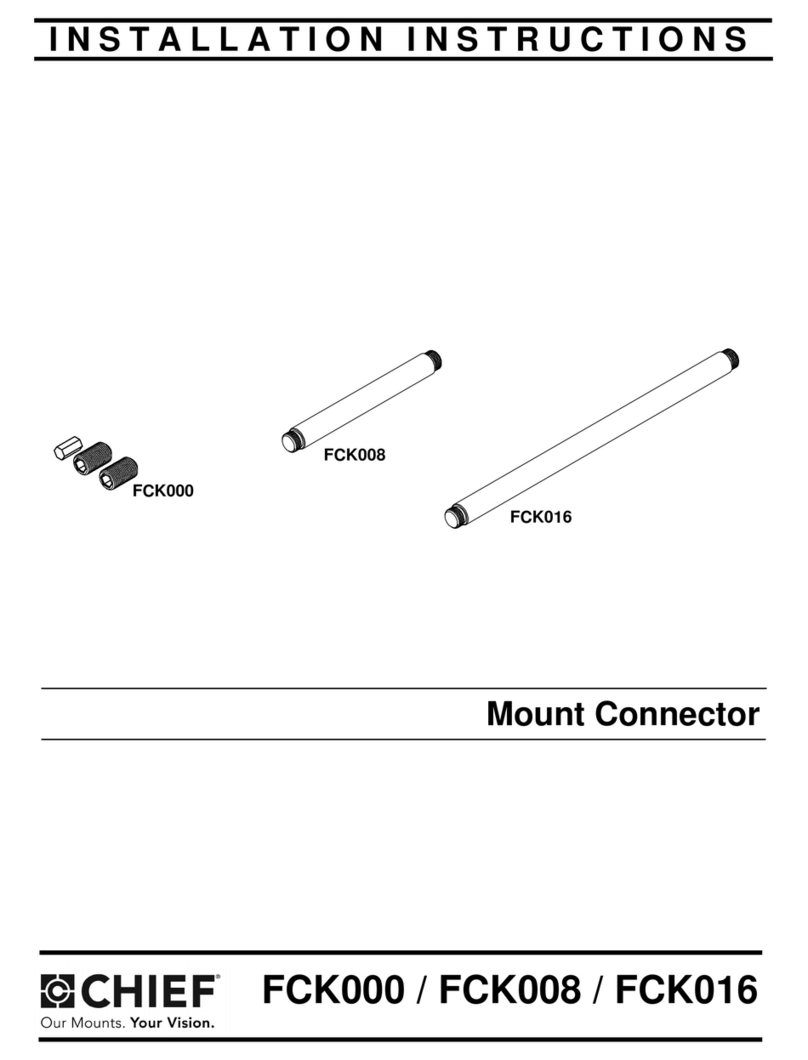
CHIEF
CHIEF Wall Mount PDWP MB 40 L installation guide
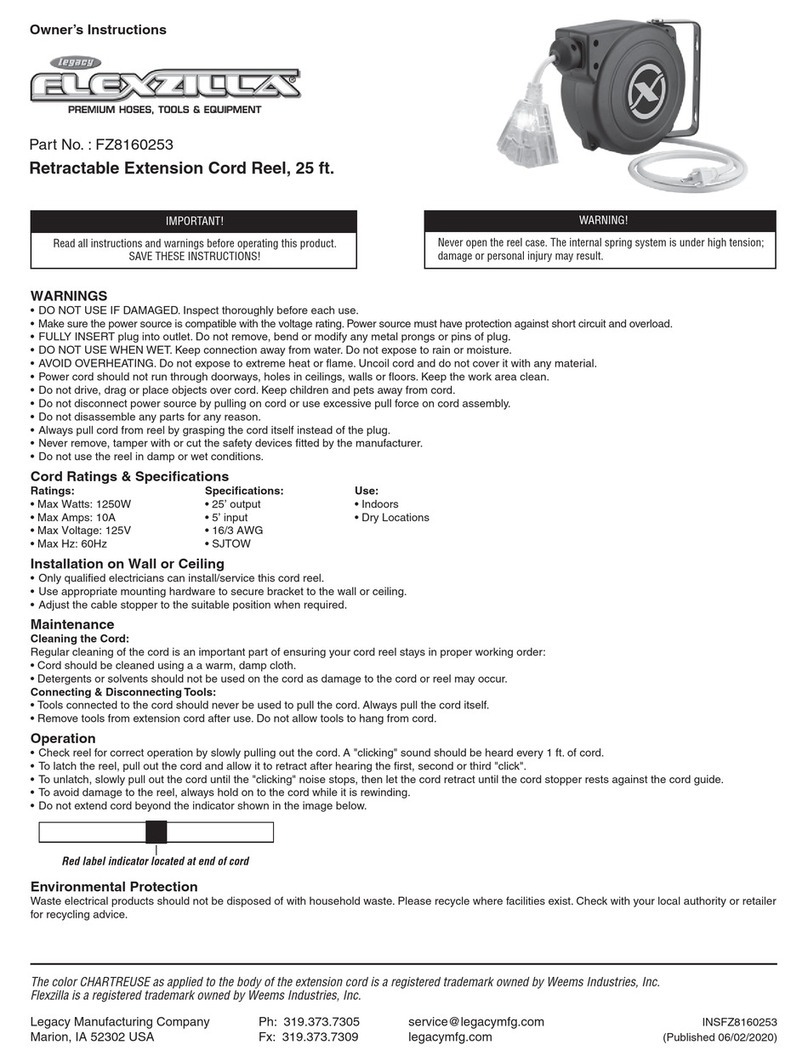
Legacy
Legacy Flexzilla FZ8160253 Owner's instructions

Festo
Festo FBS-SUB-9-GS-2x4POL-B Assembly instructions
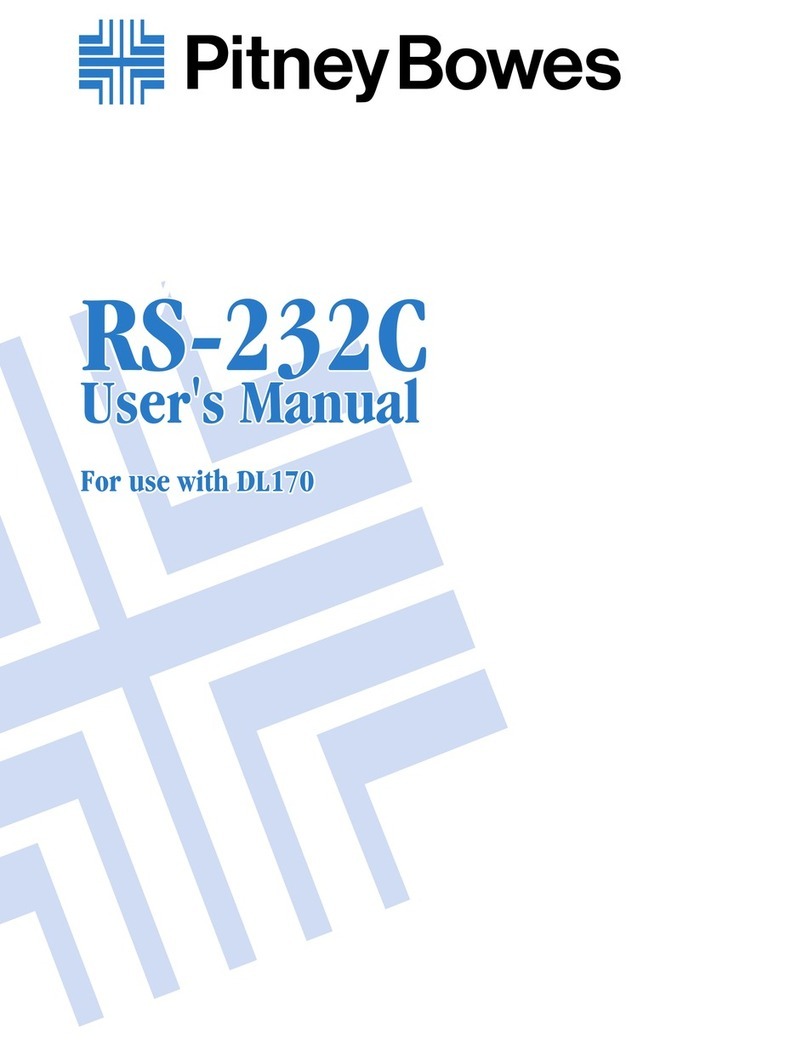
Pitney Bowes
Pitney Bowes Imagistics RS-232C user manual

TE Connectivity
TE Connectivity HVA630-5p manual