Wild Hare R/C Edge 540T User manual

Wild Hare R/C
Edge 540T 28%
Extra 300LX and Extra 300 Special 28%
Assembly Manual
For assistance contact Wild Hare R/C
8608 Doral Court, Flower Mound Texas 75022
817-430-0107 Fax 817-490-1279
Copyright © 2004 by Wild Hare Hobbies, Inc. All rights reserved.
Preliminary edition rev. 1.08 June 25, 2004

Warranty Information
Wild Hare R/C, division of Wild Hare Hobbies, Inc. guarantees this kit
to be free of defects in both material and workmanship at the time of
purchase. This warranty does not cover any components damaged by
use or modification. In no case shall Wild Hare Hobbies, Inc. liabil-
ity exceed the original cost of the purchased kit. Further Wild Hare
Hobbies Inc, reserves the right to change or modify this warranty with-
out notice.
In that Wild Hare has no control over final assembly or materials used
in final assembly, no liability shall be assumed or accepted for any
damage resulting from the use by user of the final user assembled prod-
uct. By the act of using the user assembled product, the user accepts all
resulting liability.
If the buyer is not prepared to accept the liability associated with the
use of this product, the buyer is advised to return this kit immediately in
new and unused condition to the place of purchase.
While this kit has been flight tested to exceed normal use, if the plane
will be used for extremely high stress flying such as racing or extreme
aerobatics the modeler is responsible for taking steps to reinforce the
high stress points.
Read through this manual before starting construction. It
contains important warnings and instructions concerning
the assembly and use of this model.
Warning. This is not a toy. If not properly con-
trolled it can cause injury or death and property
damage..

Specifications
Wingspan 84 inches
Length 76 inches
Wing Area 1350 sq. inches
Weight 16-18 lbs .
Recommended engine 50 to 62 cc gasoline engine
Additional equipment required
Computer Radio with at least 8 channels
2 Elevator servos minimum 100 oz/in. of torque each
2 aileron servos, total torque required not less than 120 oz./in. per wing.
Rudder servo(s) at least 180 oz./in. (see text)
Throttle servo
Radio operated engine kill switch or servo operated choke strongly suggested
Single or dual radio battery packs at least 1650 mah total
Switch[es] for receiver batteries
Miscellaneous servo extensions.
High strength pushrods, carbon fiber reinforced suggested.
Gasoline resistant fuel tank and lines with filler system.
3.5 inch wheels for main landing gear, 1.5 inch tail wheel.
3/16 inch axles for main landing gear
3.5” spinner
Rocket city #69D or similar control horn set (3 sets required)
Please remember, this is a big airplane with high stresses on the controls. You
must use high performance servos, pushrods, linkages, horns, etc. Flexing in
linkage or loose hinges can and will cause flutter of the control surfaces
which will destroy the airplane in just a few seconds. Metal gear servos are
required. Proper installation of hinges is critical.

Optional Accessories
Wild Hare R/C makes available several accessories that can enhance the Edge
540T. These are;
Hardware kit. The hardware kit includes all the things you need to assemble the
Edge except for engine, spinner, glue, prop, and electronics. Specifically it con-
tains;
2 sets Rocket City #69d control horns (2 per set)
1 set Dubro #866 HD control horns
6 Dubro HD safety Kwik links
Carbon fiber pushrod materials to make pushrods as explained in this manual.
Your choice of 1 Dubro pull-pull setup or extra pushrod materials for rudder
3 1/2” Dubro wheels and 3/16” axles.
24 oz. gas tank, either Dubro or Great Planes, plus tygon line, tee, and fuel dot
Many miscellaneous small parts such as nuts, washers, horns, springs, etc.
Spinner. The Edge requires a 3 1/2” spinner. Wild Hare normally keeps Dave
Brown Vortec spinners in stock, they are cut to fit a large prop such as a 22-10
Menz, and may be available drilled for a DA-50 or ZDZ-50.
Switches. The Edge has holes laser cut in the fuse sides to accept the Maxx prod-
ucts charge-jack switch, a very nice way to switch your receiver and ignition bat-
teries.
Servos. Wild Hare sells servos from Hitec and JR. We have flown the planes with
servos ranging from the economical Hitec 645 to the JR 8611. We have found that
better servos really do make a plane fly better, and we recommend that you use
the best servos that you can afford.

Table of Contents
Steps Subject
1Open and inspect everything
2Mount the engine
3Hinge the control surfaces
4Mount the hatch and canopy
5Mount the horizontal stabilizers
6Install the control horns
7Install the servos
8Install the landing gear
9Install a fuel tank and fuel system**
10 Mount the radio equipment**
11 Hook up the engine control linkage**
12 Mount the wings
13 Check and adjust balance
14 Control throw adjustment
Appendix: Quick Start Guide and tips for the very experienced builder
** These Items require user supplied materials and creativity. These steps as-
sume that the user will be installing mounts, retainers, and other assemblies to
suit his particular building style. For example no servo mount is supplied for
the throttle, we have no way of knowing what type of engine you will use or
what is the best location for the throttle servo.
we’ll be happy to try to try to answer your questions.

28% Edge 540T Assembly Manual
Step 1. Open and inspect everything
This section should be fairly self explanatory.
In the large box you should have a fuselage with hatch., wing tube and dual stab tubes, the
elevator/stab assemblies, the rudder, cowl, wheel pants, canopy, and a package with the land-
ing gear, tail wheel bracket and miscellaneous nuts and bolts. Use some acetone on a rag to
clean the glue off the tubes. Under all of this is a false floor, and under that you will find the
wings with ailerons attached. The hinges are installed in the elevators and ailerons, but they
are not glued, you have to do that. The hinges for the rudder are in the hardware pack. We
have had good luck with Pro-bond Ultimate and Gorilla glue, both of which are glues that
expand as they dry cure and fill the voids in the hinges and their sockets. The wings and ai-
lerons are made of sheeted foam, so be sure not to use any type of glue which might dissolve
the foam.
Check everything for shipping damage and/or manufacturing defects. If there is a problem,
report it to us NOW, not after you start building the plane.
Read the quick start guide
at the end of this manual
first. It has helpful hints
and any errata correc-
tions that may be avail-
able.
Before proceeding to any assembly,
now is a good time to go over the
whole plane and fix any cosmetic
flaws. Some cosmetic flaws are to be
expected, this fact is reflected in the
price.

Known issues and improvements
There are a few areas where, at this unassembled stage, you can improve the final results of
your assembly project. There are many items that cannot be addressed on the assembly line
due to cost and possibly because not every improvement would be welcomed by every
builder. Here are a few items that have come up over time.
Go over the covering with a heat gun or iron. The covering tends to get loose over time
and with changes in temperature and humidity. It may have come out of the box with wrin-
kles, I can assure you it did not go into the box that way.
Clean out the hinge holes. Without removing any wood, use a very sharp X-acto knife and
remove any covering that may have been pushed into the hinge holes. It is very important
that the glue sticks to the wood and not to the covering.
Composite landing gear. We now have available a composite landing gear for the 28% Ex-
tra and Edge. This gear will save about 4 oz. weight over the stock aluminum gear. More im-
portantly it is very resilient. It can flex on a hard landing and return to it’s shape without per-
manently deforming. It is available painted (red for Extras, yellow for Edge) or unpainted. If
you fly off rough ground or are prone to hard landings this may be a useful addition.
Hardening holes. The fuselage sides on this plane are made of balsa which in certain areas
is doubled by lite ply.
Using wood screws in balsa is difficult because balsa is very soft. It’s a good idea whenever
you drill a hole that must accept a wood screw to put a drop of thin CA into the hole and
then if necessary re-drill the hole. The CA will wick into the wood and harden it, adding
strength in that area.
Rudder servo tray. The rear rudder servo tray is not supported properly at the rear edge,
which causes rudder deflection to be less positive than it could be. This can be corrected by
adding a support across the bottom of the tray (1/8” x 3/4” balsa should do it) that attaches to
the fuselage sides.

28% Edge 540T Assembly Manual
Step 2. Engine mounting
The first thing to do, before anything else goes in the fuselage, is to get the engine mounted
and aligned with the cowl. Here’s how I have done it. This is the hardest and most time con-
suming step in building this plane. If you can do this everything else should be easy. Do this
first before you hinge the rudder.
Note that the firewall already has a proper amount of right thrust built in, do not use any
other offsets. When you shim the engine out from the firewall use shims of equal thickness
on all 4 corners so that you do not introduce any other thrust angles.
This plane is designed around an engine of 3 to 4 1/2 pounds. If you plan to use a heavier
engine (some people plan to use 70-75cc, even though that is way overpowered and over-
weight) it’s a good idea to double the firewall. Cut a piece of 1/4” aircraft ply the same size
as the inside of the motorbox and epoxy it to the back of the pre-installed firewall. Reinforce
it with 1/2” triangle stock on all 4 sides. Drill out the center hole so the next step will still
work.
With no cowl or hatch on the fuse find a place in your workshop where you can stand the
fuselage up on its tail so that the motor mount is pointing at the ceiling. Secure the fuse so it
stands like that and wont fall over. I wrap masking tape around it and tape it to the side of
the workbench.
Note that the firewall already has a proper amount of right thrust built in, do not use any
other offsets.
Set the engine on it’s rear radial mount (assuming it has one) on the motor mount firewall so
the crankshaft is pointing up at the ceiling. Some single cylinder engines will sit nicely on
their motor mount plate on the firewall, others have too much weight in the cylinder and will
fall over. If yours falls you will need some method of keeping the engine sitting on its
mounting lugs without falling over. Here’s how I did this:
Temporarily mount the engine to a piece of wood about 1/2” thick, any old piece of plywood
will do. If the engine has a rear carb you may need to open up the firewall for the carb to go
through, but I find it easier to remove the carb during this fitting stage, then when the exact
engine location is found you can cut the firewall to clear the carb and then remount it. If you
do that, be sure to seal the engine inlet so you don’t get sawdust and debris in the engine.
Cut a strip of 1/4” ply about 3” long, and drill it in the center so that you can put a sheet
metal screw through it. The idea is to sandwich the firewall between the wood spacer and the

small piece of ply through the large hole in the firewall to allow the engine to move around to
position it. Put the screw through this wood piece, through the large hole in the firewall, and
into the engine spacer so that the wood spacer is snug against the firewall but will still slide
around.
Now mount the cowl using the supplied
screws and washers. If you are using a
single cylinder engine it will be neces-
sary to cut out the cowling to clear the
cylinder to mount the cowl. Cut a little
bit at a time rechecking clearance until
the cowl will fit over and mount on the
cowl.
Mount the cowl using the supplied
screws and washers. Place your spinner
back plate over the crankshaft or prop
bolt so that it is centered. You can now
just move the engine around by hand
(reach in from behind the engine) to get
the spinner back plate centered on the
cowl face.
Once the spinner back plate and engine
are in the right position, remove the
cowl and remove the engine from the
wood block/spacer which should remain
in place. You can now drill straight
through the holes from the wood screws
to drill the engine’s actual mounting
holes in the firewall.
The final step is to install blind nuts be-
hind the firewall and fine adjust the en-
Note these
pictures show
this technique
on another
plane, please
do not attempt
to mount a 3w
106 twin on
this plane.

gine spacing so that the spinner back plate fits per-
fectly. Remember that the firewall is already set
with proper thrust angles, any drilling must be
square to the firewall and not parallel with the fuse-
lage line.
Like I said, the rest is very easy.

Hinging is a very simple matter. We recommend that you hinge all the control surfaces in
two steps allowing the glue to dry between steps. These photos show our 35% Extra, but
the technique is identical.
There’s an important
note about hinging the
ailerons at the end of
this section.
Before you start gluing
anything, test fit each
control surface. Aileron
to wing, elevator to sta-
bilizer, rudder to fin/
fuse, with the hinges in
place. Make sure the
hinges go in the holes
smoothly and that there
is ample room for the
hinge “knuckle” so
there is no large gap
between surfaces. The
hinge lines are beveled.
The point of the bevel
should be at the center of the hinge pin, this as-
sures that the hinges are aligned and centered
on the hinge line.
Once you are certain that they all go together
smoothly, take one surface and remove the
hinges. Glue the hinges into the holes securely
using the glue you prefer. Many people prefer
epoxy for this, I have had good success with
Pro-bond polyurethane (not the pro-bond yel-
low furniture glue) because when drying it
foams up slightly and fills the gaps between the
hinge and the mounting hole. Check hinge op-
Step 3. Hinging the control surfaces
28% Edge 540T Assembly Manual

eration every few minutes as the glues sets wipe off any excess that oozes from the glue
joint.
It’s also a good idea to put some lite oil (like WD40) on a rag, and to wipe the edges of the
hinging surfaces with this rag. The oily residue will keep spilled glue from sticking to the
covering.
Whatever you use, put a drop of light oil (like 3-in-1) on the hinge knuckle after gluing. Be
careful that no oil get on the shaft of the hinge prior to gluing.
Make sure the hinges can be worked, and that the bent hinge is perpendicular to the edge
(see picture).
When the glue is dry, do the same thing with the mating surface, glue the hinge legs into the
holes provided. Work the surface back and forth to be sure it moves smoothly. Do this every
few minutes as the glue sets to be sure you haven’t glued the hinge solid, but be careful not
to pull the hinges loose. Keep the surfaces as close together as possible to minimize gaps.
When completed it’s a good idea to seal the hinge gaps by ironing a piece of Ultracoat cov-
ering material into the groove between the surfaces.
Repeat this on both elevators and both ailerons. For the rudder you may wish to wait until
later to do the final installation of the rudder, it makes it easier to handle the airplane.
To make the rudder removable, it is possible to remove the hinge pin from each hinge (grind
off the recessed end and push the pivot out) and one or two piece of wire as the pivot on all
the hinges. Use the largest wire that will fit through the hinge holes. Then to remove the
rudder you just remove the wire, but be sure the wire can’t fall out in flight. I have used a
very small wheel collar to retain the hinge wire.
Important note about hinging the ailerons. The beveled balsa strips at the back of the
wing are glued to the inner foam core. The foam is not very strong, so be sure that the
hinge is glued to the balsa all the way up to the surface. Glue the hinges into the wing
first, then glue the ailerons on later. Be very careful that the glue goes all the way down
and all the way up to the top of the hole and that it is contacting the hinge and the wood
all the way around. If you just glue the hinge to the inner foam eventually it will come
loose. Trim away any covering that is protruding into the hole, but don’t remove any
wood if you can help it. Don’t drill the holes bigger either.

The hatch mounts to the fuselage by two tabs on each side that are attached at the rear of the
hatch.
Set the hatch on the fuse and mark the fuselage so
you can see where the fore and aft edges of the
mounting tabs are. Find the center between these
two marks and measure down 1/2 inch from the
fuse top edge and make a mark. With the hatch in
place drill a 1/8” hole at the mark you made
through the fuse side and the hatch tab. Don’t
push real hard when drilling the hatch tab, it can
be broken by excessive force.
Once the hole is drilled you may want to harden the wood around the hole in the fuse side by
putting some thin CA into the hole.
Install a 4-40 blind nut in the backside of the tab. Use a 1” long 4-40 screw (I like allen bolts
because if a screwdriver slips it will usually poke a hole in the covering) through the fuse
into the retaining tabs to secure the hatch to the fuse.
Trim the canopy to fit the hatch. Leave a small lip in the front, it makes the attachment more
secure.
Attach the canopy with whatever is your favorite method. Some people use tape, some glue
the canopy down, some use small screws. This is up to you. If you use small screws add
some hard wood such as 1/16” ply to back up the balsa wood of the hatch.
The picture above is not of the Edge, but the technique is exactly the same.
Step 4. Mounting the hatch and canopy
28% Edge 540T Assembly Manual

28% Edge 540T Assembly Manual
Step 5. Install horizontal stabilizer
This step is easy.
Trim the covering around the holes in the fuse for the stab spar tube and the two retaining
bolt holes on each side. You should also cut away the covering over the holes for the eleva-
tor servos, but don’t cut out the rudder servo covering yet.
Slide the spar through the fuse, and slide the stabilizers onto the tubes from each side.
Retain the stab to the fuse with two 4mm bolts, washers and lock washers. I advise you to
use washers and lock washers or a little blue loctite on the threads. Don’t use a lot, and don’t
use red loctite, or you won’t be able to get the screws out without tearing out the blind nut.
The assembled h-stab with controls is shown below.

28% Edge 540T Assembly Manual
Step 6. Install control horns on all surfaces
We recommend Rocket City or similar control horns with a 8-32 screw used for the horn.
Rocket city #69D is the one I prefer because of the snap-together assembly. Each package
has hardware so that you get either 2 control horns or 1 rudder tiller. There will be hardware
left over no matter what you do.
There are a couple ways to do this. You should decide whether you care if the screw head
shows on the upper surface. The hard points are already pilot drilled, but need to be made
larger for the 8-32 stud. I have found that grinding a small flat on one side of the tip of the 8-
32 stud makes it thread into the hard point more easily.
IMPORTANT NOTE: Do not drill the hardpoints larger than 9/64. The screws must
thread snugly into the hardpoints. If you drill it larger the screw can wobble in the hole
and allow the control surface to flutter with disastrous results.
If you don’t care about the screw head showing, drill all the way through the hard point in
the aileron and elevator with a 9/64 drill. Also drill the upper hard point in the rudder with
the 9/64 drill, save the lower one for later. Countersink the drilled holes in elevators and ai-
lerons on the top.
On ailerons and elevators install the 8-32 stud from the top, screw it all the way in until it is
snug. Install the rest of the horn assembly from the bottom.
Or;
Another way to do it does not allow anything to show on top. Very carefully and slowly
drill from the bottom side with a 9/64 drill, following the pilot hole so you don’t change the
angle. I use a hex drive quick change bit and put it in my power screwdriver which turns
slowly and is easy to handle. Pull the bit out every 1/8” or so and blow out the shavings.
While drilling observe the top surface of the hardpoint visually. When the drill reaches the
covering on top you should be able to see it bulge before the covering is pierced. As soon as
you see it, stop drilling and withdraw the drill, blow out all the shavings.
Now take your 8-32 stud and thread it into the hole from the bottom. Screw it in by hand or
with a power screwdriver, again observing the other end, until you can see the tip of the
screw through the covering.

Now, cut off the head of the stud/screw and thread the rest of the hardware onto the screw.
Here’s a tip. When you cut the head off with your Dremel, it will be hot. Don’t let it fall on
your legs or on the surface or it will burn through the covering (or your skin or pants).
Rudder tiller;
After the upper hardpoint has been drilled through with a 9/64 drill, install the tiller bar so
that it is showing the same amount of threads on each side of the rudder. Once the stud is
installed cut the head off with your Dremel.
After the tiller bar is installed, if you need to adjust the position you can do this without
damaging it by double-nutting two 8-32 nuts and use a wrench to turn the stud into the hard-
point.
Now install the horns exactly the same distance from the rudder surface. If using the DuBro
horn set for this you should re-drill the horn with a 1/8” bit in a location that is even with the
hinge center line/ Both horns should be drilled at the same point. Then trim the excess from
the horn leaving at least 1/8” of material at the end.

28% Edge 540T Assembly Manual
Step 7. Installing the servos
1. Elevator servos.
Trim away the covering from the rear sides of the fuselage to expose the two servo trays. At-
tach a servo extension to the servo cord long enough to reach the receiver, and tie this servo
connector together with dental floss or whatever you prefer.
Slide the extension through the servo hole and fish the end through the fuse with a piece of
wire with a hook or whatever you want to use. Servos should be secured with all screws.
There are two fuselage formers that have lightening holes in them. If you run the extensions
through these holes it keeps the wires from flopping around in flight.
2. Aileron servos.
There is a servo wire tunnel through the wing that touches the servo tray. You can use a
piece of wire with a hook to fish through the hole and pull the servo pigtail through. Be sure
the extension is long enough to reach the receiver. Also be sure the servo extension is se-
curely attached to the servo lead. If you bought our hardware kit there are small plastic re-
tainer clips included for this purpose.
3. Rudder servo.
Do this last, after everything else is done and the plane is otherwise ready to fly.
Balance the plane and determine if weight is needed in the tail.
If tail weight is required, mount two servos in the tail below the elevator servos in the same
manner as the elevator servos.
If tail weight is not needed, I suggest that you mount a single powerful digital servo such as
a JR 8611 or Hitec 5945 in the servo tray and use pull-pull cables to actuate the rudder. If
necessary there is a second servo cutout which can be used to gang two servos for the rudder
and still use pull-pull.

Throttle and (optional) choke servo installation.
We recommend that a small servo be used to operate the choke as well as the throttle. This
provides an extra level of safety by acting as a secondary engine kill mechanism in case of
failure in the throttle control system.
It is impossible for us to anticipate every potential throttle layout for every engine, so I have
included photos of two
typical installations. The
one above is for a DA 50
with rear carb, but pre-
sumably could apply to
any rear carb engine. No-
tice that all we did is add
two lite ply supports be-
hind the motor box.
Another installation is
shown below, this is a
G62 which has a side carb
setup. This photo does not
show the choke installa-
tion, it required removal
of the factory installed
arm and installation of a new one in the proper orientation.

28% Edge 540T Assembly Manual
Step 8. Install the landing gear
There should be drilled holes in the landing gear plate under the covering, these should
match up with the holes in the landing gear. Unfortunately the holes are not always there. To
assure perfect alignment use the following procedure. If the holes are not there center the
gear so the holes align with the aluminum
bracket inside. The front edge of the gear
should be back about 1/2 to 3/4 inch from the
front fuselage former edge. Drill one of these
holes through the aluminum bracket and mount
the landing gear with 4mm screws and lock-
nuts. Then use the landing gear as a template
and drill the remaining holes as well and use
4mm screws and locknuts there also. Keep the
front edge of the gear parallel with the front
former.
To mount the wheel pants you simply drill
through the back of the landing gear and through the wood backing plate. Install a 4-40
blind nut in that wood backing plate.
The tail wheel
bracket attaches to
the hardwood plate at
the bottom of the tail
using two wood
screws. Use springs
from the tailwheel
tiller for controlling
the tailwheel. See the
accompanying photo.

28% Edge 540T Assembly Manual
Steps 9, 10, 11. Installation of fuel system, radio and con-
trol linkages
These 3 subjects are combined on one page because this is the part where you get to do
things your way. We have only done a few things to get you started.
1. There are holes cut in both fuse sides that will fit any of the popular integrated switch/
charge jack assemblies. These are available from
Maxx Products, Cermark, JR, and probably several
other vendors. Some trimming may be required.
Since the fuse sides are balsa new holes are easily
cut with a razor knife if you need to mount your
switch in a different location. The location shown
in the picture is convenient and will just clear the
wing when it is installed. If you do cut into the
fuse side for any reason do not cut the 1/4” balsa
stringers at the top and bottom of each side.
2. The fuel tank can be mounted on the tray beneath the wing tube. Putting it there mini-
mizes changes in balance as the engine burns off fuel.
3. There are two trays which are meant to hold the receiver, battery pack(s), and one or two
rudder servos if a pull-pull is chosen.
4. IN case you need to add weight in the front of the plane for balancing, the sides of the
motor box at the front are a
good place to mount the re-
ceiver packs. Be sure to
range check your radio to be
sure no interference is being
caused by the batteries being
in close proximity to the en-
gine’s ignition system.
This manual suits for next models
2
Other Wild Hare R/C Toy manuals
Popular Toy manuals by other brands
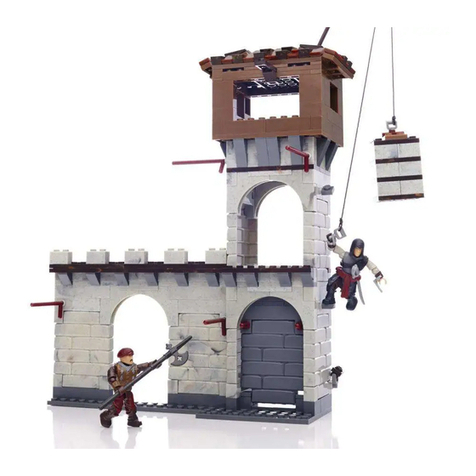
Mega Bloks
Mega Bloks Collector Series manual
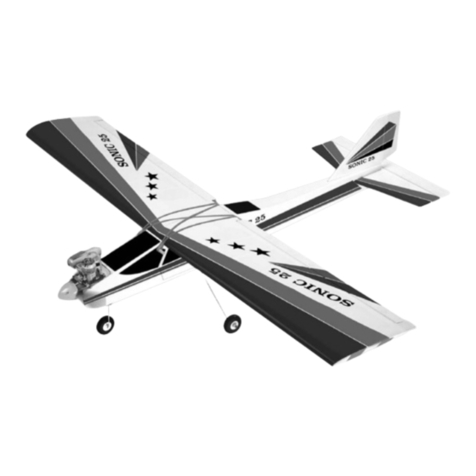
Phoenix Model
Phoenix Model SONIC 25 instruction manual
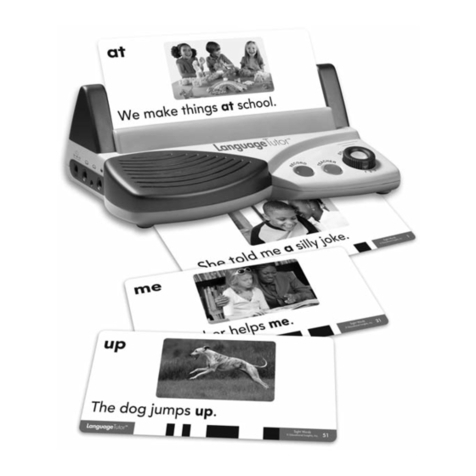
Educational Insights
Educational Insights EI-2306 Language Tutor Instructions for use
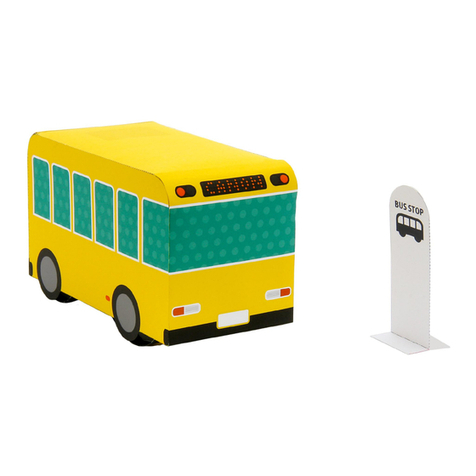
Canon
Canon Creative Park Elastic-powered Bus Aassembly Instructions

Chicco
Chicco SINGING ANIMALS PLAYMAT manual
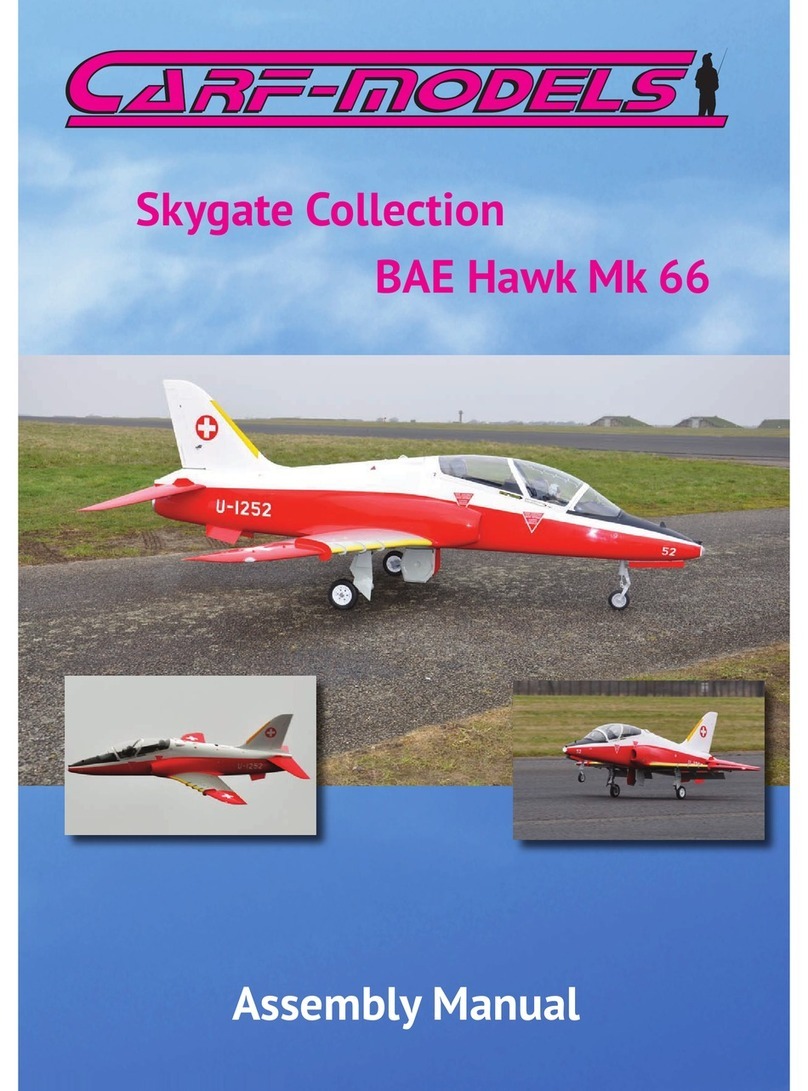
Carf-Models
Carf-Models BAE Hawk Mk 66 Assembly manual