Zellabox Cubb User manual

1
Zellabox
Installation Manual

1Introduction
2Safety Instructions
2.1 Overview
3Power Connection
3.1 Power supply requirements
3.2 Switchboard operation & START UP PROCEDURE
Reference for electrician
3.3 Switchboard Electrical Diagram – 12U Cubb
3.7 Switchboard Front and Rear layout – 25U, 30U & 38U Cubb & CubbDuo
4Access Control
4.1 Metal key Pad Access Control codes
4.2 Biometric Access Control
4.3 Digital Key Pad Control and Card
5 Single Cooling & Dual Cooling System Commissioning
Reference for air conditioning contractor
5.1 Condenser
5.2 Commissioning
5.3 Wiring
5.4 Copper Piping
5.5 Start up – Single Cooling
5.6 Start up – Dual Cooling
6. Online Access – PDView Access
Option 1 - To access the Zellabox PDU using a smart device
Option 2 - To access the Zellabox PDU using LAN connections
Option 3 - To access the Zellabox PDU through a network / switch or something similar
7 Pyrorack
7.1 Preparation Step 1
7.2 Preparation Step 2
7.3 Commissioning
7.4 Decommissioning
7.5 Print and Laminate pages
7.6 Canister replacement procedure
7.7 Important Tips
8 Start up and ready for population
2
Zellabox
Table of Contents

3
The micro data centre is a self-contained facility designed to house
your critical networking & IT equipment and to provide the infrastructure
of a conventional server facility in a portable and robust environment.
The Micro Data Centre eliminates the need for a server room.
Our micro data centres offer a robust and dependable answer to the
question of housing and securing your networking and data storage
equipment. The facility, in the form of a cabinet, has a host of built-in
features, which ensure that your server is secure, accessible and fully
portable.
The Micro Data Centre can accommodate your requirements based
on a plug-and-play operation of any of the following components:
The Micro Data Centre is available in two models namely; Cubb®and
Cubb®Duo. The Cubb is a single cooling unit and the CubbDuo is a
dual cooling unit.
This guide needs to be followed according to the steps of installation
to ensure the most effective installation is achieved.
Zellabox
Introduction
1Introduction

This manual contains instructions relating to safety, installation,
operation, maintenance and warranty of this product and its
components.
Please keep this manual in a safe place for future references.
Handling Safety
Do not lift heavy loads without assistance.
Zellabox
Safety Instructions
2Safety Instructions
2.1 Overview Important safety note
•
Caution needs to be taken when removing the side panels of the
Micro Data Centre, in particular when dealing with the 38U as
they are heavy. We recommend a 2 man lift when removing and
re-installing the side panels.
•
ALWAYS ENSURE the bottom brackets are locked in and that the
top pins are COMPLETELY slotted in.
VERY IMPORTANT SAFETY NOTE
Do not plug in the cooling system/s into the switchboard until the
condenser/s has been hardwired as per installation manual.
This process to be undertaken by a qualified air conditioner contractor.
4

5
Important note
DEPENDING ON SIZE AND MODEL. Power
consumption can vary from less than 10 amps
and up to 60 amps depending on load. When
arranging the on premise power supply with the
landlord or power company make sure you
structure your energy bill based on power used
and not based on a fixed power supply.
For security purposes we recommend a
hardwired connection directly into power source
rather than a plug.
Max power supply to Zellabox can either be 10,
32 & 60 amps
(220v – 240v / 50/60hz) depending on the model
WE RECOMMEND THAT INSTALLATION
SHOULD ONLY BE CARRIED OUT BY
SUITABLY QUALIFIED ELECTRICAL
CONTRACTOR
WITH THE NECESSARY TRAINING.
Zellabox
Safety Instructions
3.1 Power Supply requirements
!
Zellabox
3.2 Switchboard Operation
Following the connection to mains power
DEPENDING ON MODEL (CUBB & CUBBDUO) THE SWITCHBOARD
LAYOUT AND CONFIGURATION IS DIFFERENT. (SEE LAYOUT
DIAGRAMS – pages 6-9)
Start Up Procedure
! Switch Mains Isolator switch to the ON position
! Very Important - Leave the Cooling System circuit breaker in
the OFF position – Electrical Hazard
! Please Note: If hardwiring 6 or 8KVA UPS – LEAVE IN OFF
POSITION until UPS and switchboard have been connected by
electrician – Electrical Hazard. (See UPS Manual)
•
Switch UPS to the ON position once connected
! Important - (Leave the RCD cooling and Cooling system for the air
conditioner contractor – Electrical Hazard)
3Power connection

6
Zellabox
Safety Instructions
3Power connection
!
3.3 Power Supply diagram to PDU switchboard – 12U Cubb only
Cooling system
RCD
Mains power
Cooling system
UPS Power
Non-monitored
sockets

7
Zellabox
Safety Instructions
3Power connection
!
3.4 Switchboard layout – 25U,30U & 38U models
Front View
Rear View
CLIENT:
DESIGN APPROVED BY:
APPROVAL DATE:
CLIENT JOB / P.O. No:
ZELLABOX
B
8819_FRONT PANEL
ZELLABOX
FRONT PANEL
2 UNIT PROTOTYPE
FRONT LAYOUT
NTS
8819
A
09/03/16
ISSUED FOR APPROVAL
AM
LM
PM
B
14/06/16
AM
LM
PM
FRONT VIEW
ISOLATOR
MAIN
3KVA
UPS
6KVA
UPS
AVAILABLE
POWER
P
R
O
TE
C
T
I
ON
NO
RC
D
DIVERTER
SURGE
38
T
O
T
A
L
C
U
T
OU
T
47 TOTAL CUT OUT
485 (NOMINAL 19-INCH RACK CASE)
10
7
18
18
18
18
HANDLE
2
R
U
=
88
NO
M
I
NA
L
H
E
I
GH
T
RCD
COOLING
36
ISSUED FOR REVIEW
REVIEW
1 2 3 4 5 6
7
8 9
10 11
12
A
B
C
D
E
F
G
H
1 2 3
4
5 6
7
8 9
10 11 12
A
B
C
D
E
F
G
H
SHEET SIZE:
DRAWING No:
SCALE:
DATE
REV No:
REVISION DESCRIPTION
DRAWN
APPR
CHKD
REFERENCE DESCRIPTION
REFERENCE DOCUMENT No.
REV No.
TECHWORX JOB No:
EC009337
ALL DIMENSIONS IN MILLIMETRES
www.techworxaust.com.au
Tel: (08) 9418 2900
1/6 Bushland Ridge, Bibra Lake WA 6163
ABN 59 077 882 869
A1
CLIENT:
DESIGN APPROVED BY:
APPROVAL DATE:
CLIENT JOB / P.O. No:
ZELLABOX
B
ZELLABOX
2 UNIT PROTOTYPE
NTS
8819
A
ISSUED FOR APPROVAL
AM
LM
PM
B
REAR VIEW
MAINS
POWER
6 kVA UPS
NO RCD
PROTECTION
3 kVA UPS
NO RCD
PROTECTION
430
DUAL
COOLING
RCD
PROTECTION
01/04/2016
2
R
U
=
80
NO
M
I
NA
L
H
E
I
GH
T
TOP/BOTTOM PANELS CUT OUT
8819_TB_PANEL_CUTOUT
14/06/16
ISSUED FOR REVIEW
AM
LM
PM
REVIEW
1 2 3 4 5 6
7
8 9
10 11
12
A
B
C
D
E
F
G
H
1 2 3
4
5 6
7
8 9
10 11 12
A
B
C
D
E
F
G
H
SHEET SIZE:
DRAWING No:
SCALE:
DATE
REV No:
REVISION DESCRIPTION
DRAWN
APPR
CHKD
REFERENCE DESCRIPTION
REFERENCE DOCUMENT No.
REV No.
TECHWORX JOB No:
EC009337
ALL DIMENSIONS IN MILLIMETRES
www.techworxaust.com.au
Tel: (08) 9418 2900
1/6 Bushland Ridge, Bibra Lake WA 6163
ABN 59 077 882 869
A1

4.1 Metal Key Pad Operation
The default code for the doors are pre-set in
the factory as follows:
•
Front door - 2580
•
Back door – push button
FOR FURTHER INSTRUCTION TO
PROGRAM DOOR CODES. SEE USER
MANUAL
4.2 Biometric / Card Reader
The Zellabox is supplied with a default card
which will open the front door. The rear door
is opened by the push button located inside
the Zellabox.
See user manual for programming options.
Use card reader until you are ready for
biometric access mode.
4.3 L.E.D. Key Pad Operation
The default code for the doors are pre-set in
the factory as follows:
•
Front door – 2580#
•
Back door – push button
FOR FURTHER INSTRUCTION TO
PROGRAM DOOR CODES. SEE USER
MANUAL
Zellabox
Technical data
4 Access control
Front panel description
Card reader
Fingerprint
reader
Card reader
Key Pad
8
Push button to
open back door

9
Important Safety Warning
PLEASE NOTE COOLING SYSTEM HAS BEEN
UNPLUGGED FROM BACK OF SWITCHBOARD
(Leave for cooling contactor to insert into switchboard).
Do not try plug cooling system plug into
switchboard until cooling system has been
commissioned by qualified air con contractor
PLEASE ENSURE THERE IS POWER TO
THE ZELLABOX (SWITCHBOARD) BEFORE
COMMISSIONING THE COOLING SYSTEM
5.1 Condenser
Depending on the model and cooling capacity
the condenser maximum distance can vary between 20
and 30 meters. The Zellabox is supplied with relevant
cable length (3 core orange output to condenser & 4 core
grey cable. The condenser draws its power from the
Zellabox. The condenser size and weight can also vary
depending on model and cooling capacity.
The condenser will be positioned either on
the outer wall of the building or on the roof.
5.2 Commissioning
Once the Zellabox has been positioned in its
proposed location and connected to power
the air conditioning contractor can commission
the cooling system.
Only once the air conditioning contactor has
Connected wires to the condenser and plugged the
grey and orange cable into the Zellabox, can the
cooling be turned on.
ENSURE THE COOLING SYSTEM PLUG IS
PLUGGED INTO THE CORRECT POWER
SOCKET ON THE SWITCHBOARD
5.3 Wiring
The Zellabox is supplied with all the cables (orange and grey)
which is pre-coiled and ready to be run with the
copper piping during the commissioning process.
The pre-coiled condenser cables are located inside the Zellabox.
CONTRACTORS TO ENSURE BOTH ORANGE AND GREY
CABLES ARE LOCKED BY TURNING THE YELLOW DISK ON THE
SIDE OF THE CABLE PLUGS WITH A SCREW DRIVER.
THE COOLING / AIR CONDITIONING CONTRACTOR MUST
SUPPLY COPPER PIPING.
!
Zellabox
Safety Instructions
!
!
!
!
!
!
!
!5 Single & Dual cooling system commissioning steps:
Wiring table (White Cable)
1- Live Red / Brown
2 - Neutral Blue / Black
3 - Signal White
Green / yellow Earth / Ground

!
FTK(X)S-L Series
- Cooling Only / Heat Pump -
ED041204
Zellabox
Safety Instructions
!
!
!
!
!
!
!
!
!
!
!
Orange cable termination in condenser
(3 core cable)
L – Red / Brown
N – Blue
– Green / Earth
Grey cable termination in condenser
(4 core cable)
1 – Red / Brown
2 – Blue
3 – White
- Green / Earth
5.3 Wiring cont.
Electrical Hazard – Ensure cooling system is in the OFF
position on Zellabox base mounted switchboard and
orange cooling system plug is unplugged from rear of
switchboard
5 Single & Dual cooling system commissioning steps:
10

!
5.3 Wiring cont.
Zellabox
Safety Instructions
!
!
!
!
!
!
!
!
!
5 Single & Dual cooling system commissioning steps:
PLEASE&NOTE:&WHEN&PLUGGING&THE&CABLE&CONNECTORS,&YOU&SHOULD&HEAR&A&CLICK&TO&CONFIRM&CONTACT.&
AFTER&INSERTING&THE&PLUG&&ENSURE&BOTH&ORANGE&AND&GREY&CABLES&ARE&LOCKED&BY&TURNING&THE&YELLOW&
DISK&ON&THE&SIDE&OF&THE&CABLE&CONNECTOR&WITH&A&SCREW&DRIVER.!!!
11

.
!
5.4 Copper Piping (see hand out in Zellabox)
1. Cut the pipe ends with a pipe cutter
2. Remove burrs with the cut surface facing downwards so
that the chips do not enter the pipe
3. Put the flare nuts on pipe
4. Flare the pipe
5. Check that the flaring is properly made
6. Never use old or pre-used pipes
!
Zellabox
Safety Instructions
!
!
!
!
!
!
!
!
!
7. Do not use mineral oil on flared part
8. Incomplete flaring may cause gas leakage
9. Use flare nut fixed to unit
10. Use torque wrenches when tightening the flare nuts
11. Protect ends from dust
12. Use pipe bender
10. NEVER use pipes thinner than 0.8mm even when it is
available on the market.
Refrigerant Piping Work
1. Flaring the pipe end.
1) Cut the pipe end with a pipe cutter.
2) Remove burrs with the cut surface facing
downward so that the chips do not enter the pipe.
3) Put the flare nut on the pipe.
4) Flare the pipe.
5) Check that the flaring is properly made.
1) Do not use mineral oil on flared part.
2) Prevent mineral oil from getting into the system as this would reduce the unit life.
3)
Never use piping which has been used for previous installations. Only use parts which are provided with the unit.
4) Do never install a refrigerant drier to this unit.
5) The drying material may dissolve and damage the system.
6) Incomplete or improper flaring may cause refrigerant gas leakage.
WARNING
2. Refrigerant piping.
1) Use the flare nut fixed to the main unit. (To prevent cracking of the flare nut by aged deterioration.)
2)
To prevent gas leakage, apply refrigeration oil only to the inner surface of the flare. (Use refrigeration oil for R410A.)
3)
Use torque wrenches when tightening the flare nuts to prevent damage to the flare nuts and gas leakage.
CAUTION
Align the centers of both flares and tighten the flare nuts 3 or 4 turns by hand. Then tighten them fully with the torque wrenches.
2-1. Caution on piping handling
1) Protect the open end of the pipe against dust and moisture.
2) All pipe bends should be as gentle as possible.
Use a pipe bender for bending.
2-2. Selection of copper and heat insulation materials
• When using commercial copper pipes and fittings, observe the following:
1) Insulation material: Polyethylene foam
Heat transfer rate: 0.041 to 0.052 W/mK (0.024 to 0.030 Btu/fth˚F (0.035 to 0.045kcal/mh˚C))
Refrigerant gas pipe’s surface temperature reaches 230˚F (110˚C) max.
Choose heat insulation materials that will withstand this temperature.
2) Be sure to insulate both the gas and liquid piping and to provide
insulation dimensions as below.
3) Use separate thermal insulation pipes for gas and liquid refrigerant pipes.
Flare nut tightening torque
Gas side Liquid side
1/2 inch 5/8 inch 1/4 inch
36.5- 44.5ft • Ibf
(49.5-60.3N • m)
45.6- 55.6ft • Ibf
(61.8-75.4N • m)
10.4 -12.7ft • Ibf
(14.2-17.2N • m)
Gas side Liquid side
15/18/24 class
O.D. 1/4 inch (6.4mm)
Gas pipe thermal insulation
Thickness 0.393 inch (8mm) Min.
Thickness 0.031 inch
(0.8mm) (C1220T-O)
Thickness 0.039 inch
(1.0mm) (C1220T-O)
Thickness 0.031 inch
(0.8mm) (C1220T-O)
1-9/16 inch (40mm) or more
1-15/16 inch (50mm) or more
1-3/16 inch (30mm) or more
Minimum bend radius
24 class
O.D. 5/8 inch (15.9mm)
15/18 class
I.D. 0.551-0.630 inch
(14-16mm)
24 class
I.D. 0.630-0.709 inch
(16-20mm)
Liquid pipe thermal insulation
15/18 class
O.D. 1/2 inch (12.7mm)
15/18/24 class
I.D. 0.315-0.393 inch
(8-10mm)
(Cut exactly at
right angles.) Remove burrs
Check
Flare’s inner
surface must
be flaw-free.
The pipe end must
be evenly flared in
a perfect circle.
Make sure that the
flare nut is fitted.
Set exactly at the position shown below.
A
Flaring
Die A
0-0.020 inch (0-0.5mm)
Clutch-type
Flare tool for R410A
0.039-0.059 inch (1.0-1.5mm)
Clutch-type (Rigid-type)
0.059-0.079 inch (1.5-2.0mm)
Wing-nut type (Imperial-type)
Conventional flare tool
Do not apply refrigeration
oil to the outer surface.
Flare nut
Apply refrigeration
oil to the inner
surface of the flare.
Do not apply refrigeration
oil to the flare nut avoid
tightening with over torque.
[Apply oil]
Torque wrench
Piping union
Flare nut
Spanner
[Tighten]
Wall
If no flare cap is
available, cover the
flare mouth with
tape to keep dirt or
water out.
Be sure to
place a cap.
Rain
Gas pipe
Liquid pipe
Gas pipe
insulation
Liquid pipe
insulation
Finishing tape Drain hose
Inter-unit wiring
Refrigerant Piping Work
1. Flaring the pipe end.
1) Cut the pipe end with a pipe cutter.
2) Remove burrs with the cut surface facing
downward so that the chips do not enter the pipe.
3) Put the flare nut on the pipe.
4) Flare the pipe.
5) Check that the flaring is properly made.
1) Do not use mineral oil on flared part.
2) Prevent mineral oil from getting into the system as this would reduce the unit life.
3)
Never use piping which has been used for previous installations. Only use parts which are provided with the unit.
4) Do never install a refrigerant drier to this unit.
5) The drying material may dissolve and damage the system.
6) Incomplete or improper flaring may cause refrigerant gas leakage.
WARNING
2. Refrigerant piping.
1) Use the flare nut fixed to the main unit. (To prevent cracking of the flare nut by aged deterioration.)
2)
To prevent gas leakage, apply refrigeration oil only to the inner surface of the flare. (Use refrigeration oil for R410A.)
3)
Use torque wrenches when tightening the flare nuts to prevent damage to the flare nuts and gas leakage.
CAUTION
Align the centers of both flares and tighten the flare nuts 3 or 4 turns by hand. Then tighten them fully with the torque wrenches.
2-1. Caution on piping handling
1) Protect the open end of the pipe against dust and moisture.
2) All pipe bends should be as gentle as possible.
Use a pipe bender for bending.
2-2. Selection of copper and heat insulation materials
• When using commercial copper pipes and fittings, observe the following:
1) Insulation material: Polyethylene foam
Heat transfer rate: 0.041 to 0.052 W/mK (0.024 to 0.030 Btu/fth˚F (0.035 to 0.045kcal/mh˚C))
Refrigerant gas pipe’s surface temperature reaches 230˚F (110˚C) max.
Choose heat insulation materials that will withstand this temperature.
2) Be sure to insulate both the gas and liquid piping and to provide
insulation dimensions as below.
3) Use separate thermal insulation pipes for gas and liquid refrigerant pipes.
Flare nut tightening torque
Gas side Liquid side
1/2 inch 5/8 inch 1/4 inch
36.5- 44.5ft • Ibf
(49.5-60.3N • m)
45.6- 55.6ft • Ibf
(61.8-75.4N • m)
10.4 -12.7ft • Ibf
(14.2-17.2N • m)
Gas side Liquid side
15/18/24 class
O.D. 1/4 inch (6.4mm)
Gas pipe thermal insulation
Thickness 0.393 inch (8mm) Min.
Thickness 0.031 inch
(0.8mm) (C1220T-O)
Thickness 0.039 inch
(1.0mm) (C1220T-O)
Thickness 0.031 inch
(0.8mm) (C1220T-O)
1-9/16 inch (40mm) or more
1-15/16 inch (50mm) or more
1-3/16 inch (30mm) or more
Minimum bend radius
24 class
O.D. 5/8 inch (15.9mm)
15/18 class
I.D. 0.551-0.630 inch
(14-16mm)
24 class
I.D. 0.630-0.709 inch
(16-20mm)
Liquid pipe thermal insulation
15/18 class
O.D. 1/2 inch (12.7mm)
15/18/24 class
I.D. 0.315-0.393 inch
(8-10mm)
(Cut exactly at
right angles.) Remove burrs
Check
Flare’s inner
surface must
be flaw-free.
The pipe end must
be evenly flared in
a perfect circle.
Make sure that the
flare nut is fitted.
Set exactly at the position shown below.
A
Flaring
Die A
0-0.020 inch (0-0.5mm)
Clutch-type
Flare tool for R410A
0.039-0.059 inch (1.0-1.5mm)
Clutch-type (Rigid-type)
0.059-0.079 inch (1.5-2.0mm)
Wing-nut type (Imperial-type)
Conventional flare tool
Do not apply refrigeration
oil to the outer surface.
Flare nut
Apply refrigeration
oil to the inner
surface of the flare.
Do not apply refrigeration
oil to the flare nut avoid
tightening with over torque.
[Apply oil]
Torque wrench
Piping union
Flare nut
Spanner
[Tighten]
Wall
If no flare cap is
available, cover the
flare mouth with
tape to keep dirt or
water out.
Be sure to
place a cap.
Rain
Gas pipe
Liquid pipe
Gas pipe
insulation
Liquid pipe
insulation
Finishing tape Drain hose
Inter-unit wiring
Please note: Pipe size is 9.5mm for cooling capacity 2kw up to 3.5kw (See enclosed
manual with condenser)
5 Single & Dual cooling system commissioning steps:
12

5.5 Start up Procedure – Single Cooling ( Cubb)
1. ONLY once the condenser has been hardwired and copper piping
connected can the cooling system be turned on.
2. Insert cooling system IEC plug (orange cable) into the cooling system
socket at the rear of switchboard labelled (Cooling system).
3. Ensure switchboard is powered and both the Cooling System RCD
and Cooling System are in the ON position
4. Start-up cooling system on remote located at the back door on
left hand side.
5. Press the START button on the cooling system remote.
6. Ensure temperature is set to 23° on cooling mode and FAN
STRENGTH is on HIGH.
7. Installation complete
5.6 Start up Procedure – Dual Cooling ( Cubb)
1. ONLY once the condensers have been hardwired and copper piping
been connected can the cooling system be turned on.
2. Insert cooling system (IEC) plugs (Orange cable) into:
3. Plug Orange Cable (Labelled – Cooling system 1) into Permanent
supply 1
4. Plug Orange Cable (Labelled – Cooling system 2) into Permanent
supply 2
5. Ensure switchboard is powered and both the Cooling System RCD
and Cooling System are in the ON position
6. Start-up cooling system on remote located at the back door on
left hand side.
7. Press the START button on the cooling system remote.
8. Ensure temperature is set to 23° on cooling mode and FAN
STRENGTH is on HIGH.
9. Run both system together for 5 minutes – ensure both systems are
operating.
10. Pull out both plugs without turning cooling system off from the
permanent supply and plug into Cooling systems 1 & 2 outlets.
11. One system will be operation following this step.
12. Installation complete
!
!
!
Zellabox
Safety Instructions
!
!
!
!
!
!
!
!
!
!
!
!
Name of Parts
Remote Controller
Signal transmitter
"#$#%&#'
()*+,#*-.#*'#/)-#*$)0-')11#'2*3%/*-.#*4*
-'30,/%--#'*3-*-.#*%05))'*+0%-6*78*-.#'#*
%,*309-.%0:*-)*;1)$<*,%:031,*;#-=##0*
-.#*+0%-*305*-.#*'#/)-#*$)0-')11#'2*
,+$.*3,*3*$+'-3%02*-.#*+0%-*=%11*0)-*
)>#'3-#6
?)*0)-*5')>*-.#*'#/)-#*$)0-')11#'6*?)*4*
0)-*:#-*%-*=#-6
(.#*/3@%/+/*5%,-30$#*8)'*4*
$)//+0%$3-%)0*%,*3>>')@6*!/6
FAN setting button
7-*,#1#$-,*-.#*3%'*)=*'3-#*,#--%0:6*4*
**A3:#*BC
POWERFUL button
ADEF"GHI*)>#'3-%)06*4* *A3:#*B!
Display (LCD)
7-*5%,>139,*-.#*$+''#0-*,#--%0:,64*
J70*-.%,*%11+,-'3-%)02*#3$.*,#$-%)0*%,*
,.)=0*=%-.*311*%-,*5%,>139,*)0*8)'*-.#*
>+'>),#*)8*#@>1303-%)06K
TEMPERATURE
adjustment buttons
7-*$.30:#,*-.#*-#/>#'3-+'#*,#--%0:64*
**A3:#*BL
ON/OFF button
A'#,,*-.%,*;+--)0*)0$#*-)*,-3'-*4*
)>#'3-%)06
A'#,,*)0$#*3:3%0*-)*,-)>*%-6* *A3:#*BB
Front cover
D>#0*-.#*8')0-*$)&#'6*4* *A3:#*M
NFO(*AHPA*/)5#1 O"QCRLOC
QDDI7ST*DSIU*/)5#1 O"QCRLOBV
01_EN_3P291209-1.indd 701_EN_3P291209-1.indd 7 12/8/2011 9:18:00 PM12/8/2011 9:18:00 PM
Mechanical Diagram
Model Number: PX3-5092R-F84
Cooling Remote
Cooling System 1
Cooling System 2
Permanent Supply 1
Permanent Supply 2
5 Single & Dual cooling system commissioning steps:
13

14
!
Zellabox
Safety Instructions
!
!
!
!
!
!
!6 PDView Access:
Default IP address is 192.168.0.192
Zellabox PDU Configuration Guide
OPTION 1: To access the Zellabox PDU using an smart device (iPhone, iPod, iPad, andriod devise etc.) follow these steps:
1. Download the following App (Raritan PDView) from the Apple App Store,
2. Connect the Apple device with the app installed into the Zellabox PDU/door access portal,
3. Use the following to access:
a) Login: admin
b) Password: z3ll@box (lower case ‘Z’, numeral ‘3’, lower case ‘L’, @ sign, lower case ‘B’, lower case ‘O’ and lower case ‘X’)
c) Accept the terms of use check box. d) Once connected to the PDU the following similar image should appear:
4. Access the ‘network’ icon located at the bottom of the screen. If you cannot see the icon simply click on the nearest icon to
the right of the screen and more options will show.
5. At this point you will be able to locate the IP address for the unit. If you would like to change the default IP address
(192.168.0.1) you can do so at this stage.
6. Change the IP address status to ‘static’.
7. Change the IP address as desired.
8. Remember to save/apply changes at bottom of screen.

15
!
Zellabox
Safety Instructions
!
!
!
!
!
!
!
!
!!!!!!! 6 PDView Access:
OPTION 2: To access the Zellabox PDU using LAN connections follow these steps:
"
Plug a CAT cable directly into the PDU and your computer,
Access a web browser,
Type the IP address allocated to the PDU into the web browser. At this stage if you do not know the IP address go
back to ‘OPTION 1’.
Press ‘enter’,
Use the following to access:
Login: admin
Password: z3ll@box
Accept the terms of use check box.
"
OPTION 3: To access the Zellabox PDU through a network / switch or something similar follow these steps:
"
Assign the desired IP address to the PDU by referring to ‘OPTION 1’ above,
Plug network cable / switch directly into the PDU,
Access a web browser,
Type the IP address allocated to the PDU into the web browser,
Press ‘enter’,
Use the following to access:
Login: admin
Password: z3ll@box
Accept the terms of use check box.

16
!
Zellabox
Safety Instructions
!
!
!
!
!
!
!
!
!
!
!6 PDView Access:
OPTION 4: To access the Zellabox PDU through a network / switch or something similar using DHCP follow these
steps:
"
Assign the desired IP address to the PDU by referring to ‘OPTION 1’ above,
Plug network cable / switch directly into the PDU,
Access the PDU through local Display,
If you have any questions please contact Zellabox:
"
Australia: 1300 117 644
International: + 61 8 6311 2814
"
ONCE YOU HAVE ACCESSED THE PDU VIA WEB BROWSER THIS IS WHAT YOU SHOULD SEE:

Zellabox
Safety Instructions
!
!
!
!
!
!
!
!
!
!
!7 Pyrorack commissioning & user guide:
IMPORTANT#
For effective and safe installation follow the steps
in the next few slides.#
#
Please note: Accidental discharge will occur if this
guide is not followed step by step
#
For effective and safe installation follow the steps
below#
#
Please note: Accidental discharge will occur if this
guide is not followed step by step
Please print, laminate & stick near
your Zellabox for all to see the next 2
slides.
!
17

18
IMPORTANT#
#
For effective and safe installation follow the steps in the
next few slides.#
#
Please note: Accidental discharge will occur if this guide
is not followed step by step
For effective and safe commissioning follow the steps
below
Please note: Accidental discharge will occur if this guide
is not followed step by step
COMMISSIONING STEPS:
7.1 Preparation 1
Before mounting the Pyrorack into the Zellabox. Make sure
you have the following ready:
1. Supplied fuses are ready (a pack of fuses should have
arrived with MDC)
2. Ensure keys are in slot at the front of the Pyrorack
3. Star (Phillips screw driver) ( to connect Pyrogen canister)
7.2 Preparation 2
1. Before mounting the Pyrorack, place the Pyrorack upside
down on a table.
2. Remove the four screws in the middle – surrounding the
string.
3. Remove the Pyrogen canister from the Pyrorack
4. Connect the Pyrogen canister to the Pyrorack by
inserting the plug and tightening the washer
5. Reinsert the canister back into the Pyroack
6. Place the Pyrorack into position top of the Zellabox
!
7.3 Commissioning Steps
1. Fit the Mains fuse F5 (far right hand side)
2. Insert mains supply cable (C13)
3. Wait 5 seconds
4. Fit the Battery Fuse F4 (middle fuse)
5. Wait 5 seconds
6. Fit the Extinguishing Agent Release Fuse F3. Wait 5
seconds, the extinguishing agent fault LED goes off
7. Press and hold Test Button and confirm all LEDs are
functioning
8. Ensure Key switch is in automatic mode
9. Pyrorack is successfully replaced into service
7.4 Decommissioning Steps
1. Remove Mag fuse F3 from the rear of the Pyrorack (far
left)
2. Wait 5 seconds
3. Remove the main fuse F4 (middle fuse)
4. Wait 5 seconds
5. Remove the mains cable
6. Remove the battery fuse F5. The unit shall be powered
down at this stage.
7. Remove the Pyrorack from the server cabinet.
7.5 Please print, laminate & stick the next 2
slides near your Zellabox for all to see.
Zellabox
Safety Instructions
!
!
!
!
!
!
!
!
!
!
!7 Pyrorack commissioning & user guide:

Warning #
Fire Suppression System
Information
! Before working within the Zellabox ALWAYS ensure you follow
these steps:
1. Turn key switch to manual
2. Isolate both zones 1 and 2 by pressing the isolate zones buttons
located on the front panel
3. A beeping sound will continue intermittently as a reminder
4. Once you have completed work within the MDC and you are ready to
close the doors press the isolate buttons 1 and 2 once more
5. Turn the key switch back to the automatic position
6. The Pyrorack should return to normal status
19

Warning #
Fire Suppression System
Information
20
Other manuals for Cubb
1
This manual suits for next models
1
Table of contents
Popular Storage manuals by other brands

Western Digital
Western Digital Raptor WD1500ADFD Specifications
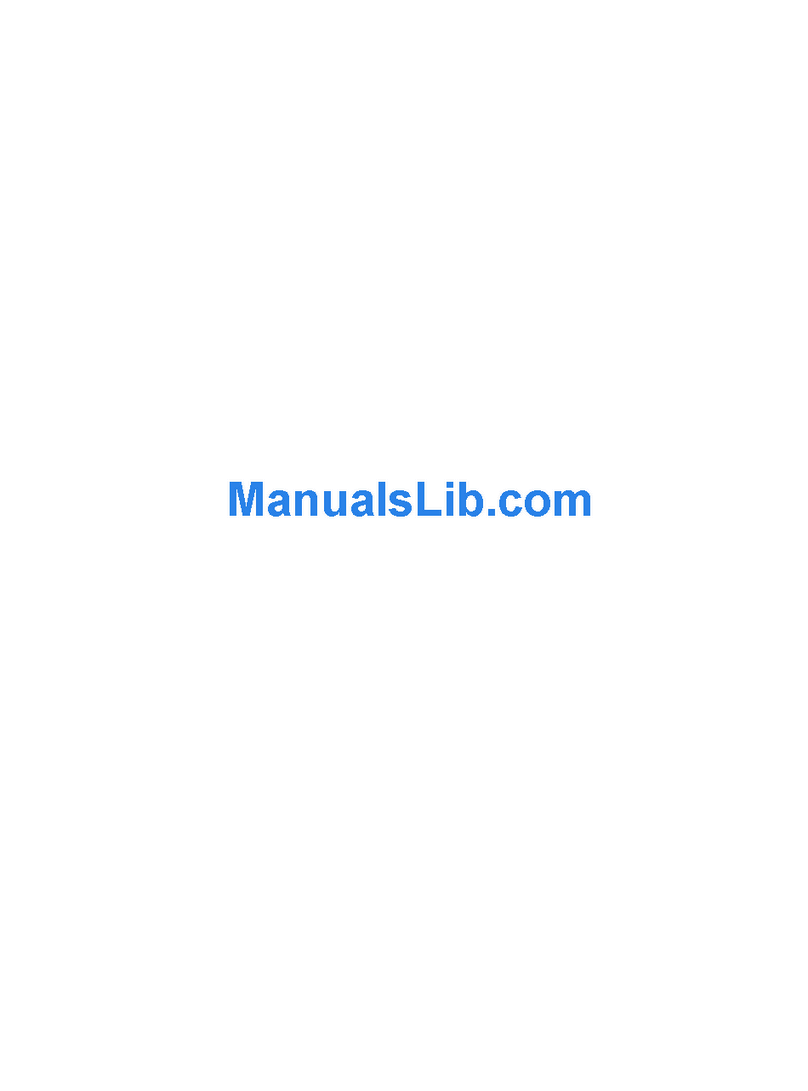
Quantum
Quantum DLT 1 install guide
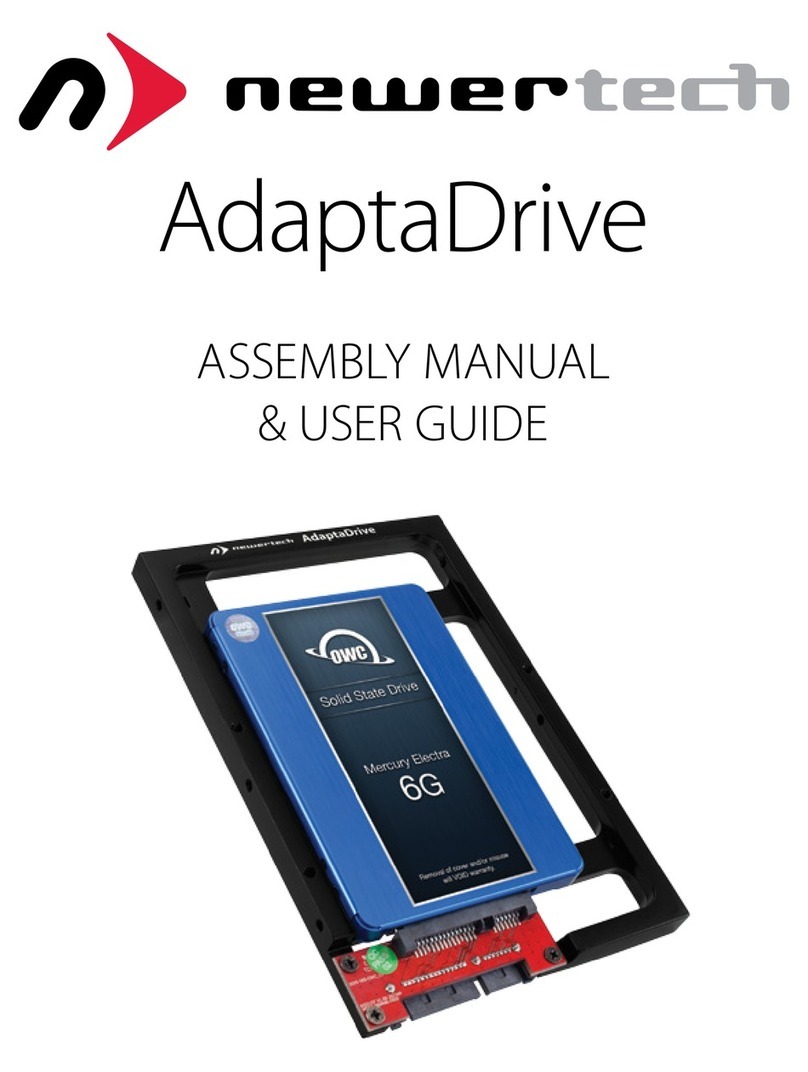
NewerTech
NewerTech AdaptaDrive Assembly manual & user guide
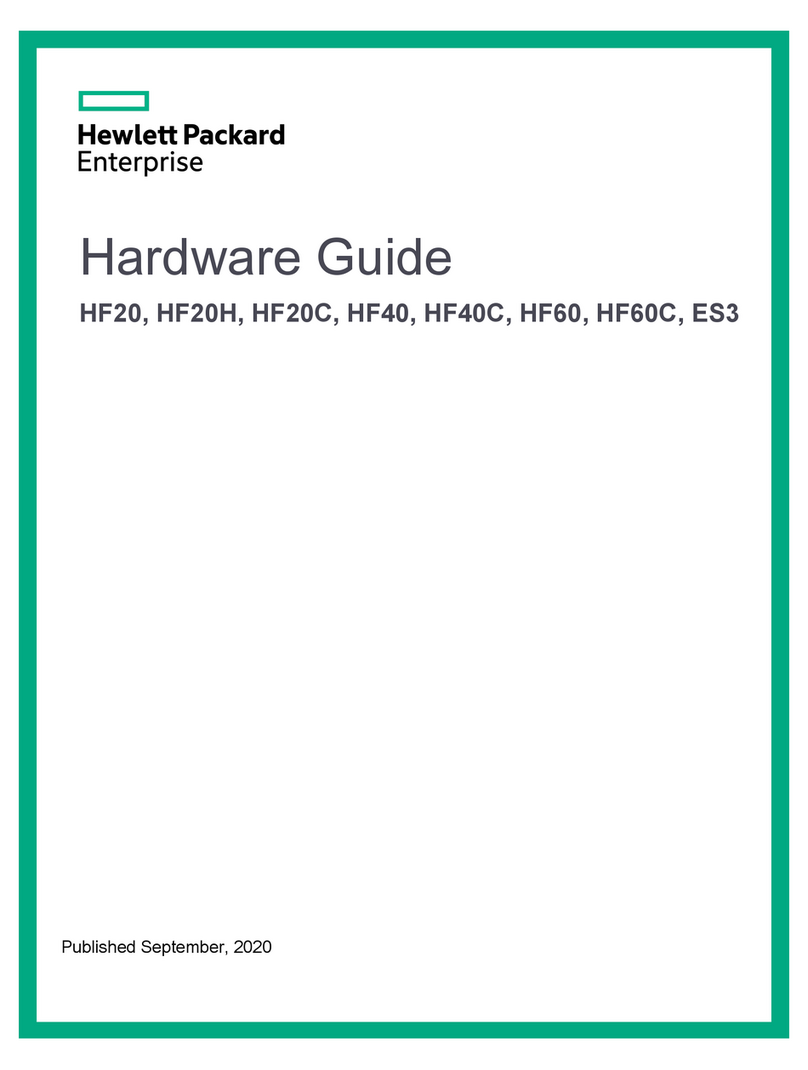
Hewlett Packard Enterprise
Hewlett Packard Enterprise HF20 Hardware guide
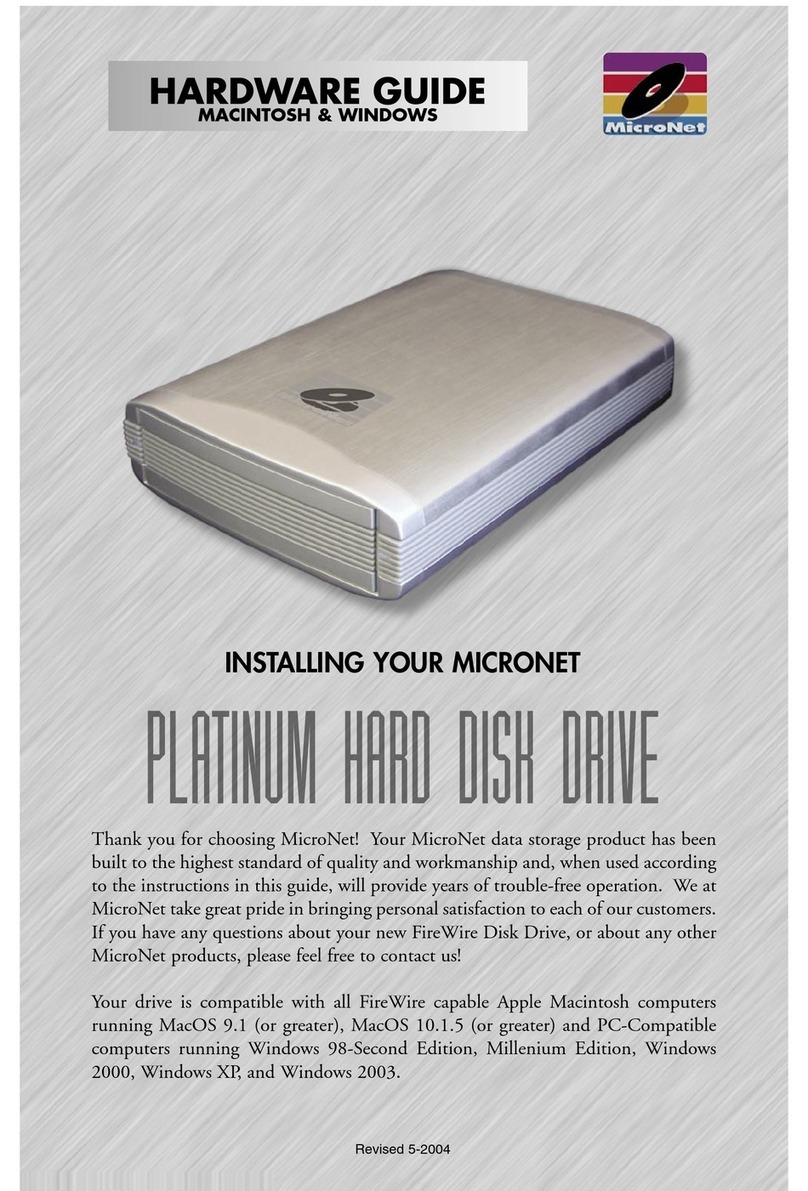
MicroNet
MicroNet apple Hardware guide
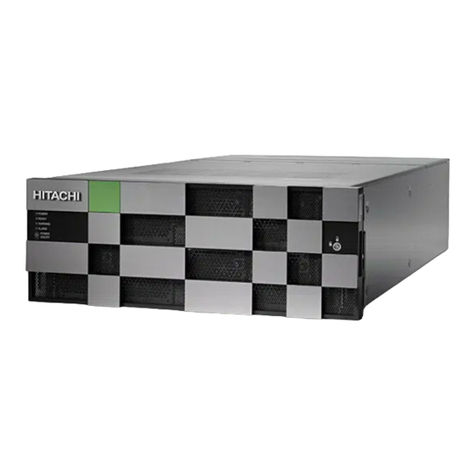
Hitachi
Hitachi 88-06-0x Hardware reference guide