a2b ACCORRONI MEC MIX C Series Manual

1
TECHNICAL INFORMATIONMEC MIX C - MEC MIX F
Axial and centrifugal condensation hanging hot air generators
with pre-mixed modulating gas burner
MEC MIX C
modulating condensation
MEC MIX F
xed power
HIGH
PERFORMANCE 104%
CERTIFICATED
COMBUSTION
ROOM IN
STAINLESS STEEL
CONDENSATION
SYSTEM
CONDENSING
PREMIXED BURNER
REMOTE
OF SERIES
MADE
IN ITALY

2
INDEX
1. GENERAL WARNINGS ........................................................................................................................... 4
2. SAFETY WARNINGS .............................................................................................................................. 4
2.1 Qualication of the installer ...................................................................................................................... 4
2.2 Power supply ........................................................................................................................................... 4
2.3 Fuel .......................................................................................................................................................... 4
2.4 Gas leaks ................................................................................................................................................. 4
2.5 Use ........................................................................................................................................................... 4
2.6 Transportation and handling .................................................................................................................... 4
3. MAIN CHARACTERISTICS ..................................................................................................................... 5
3.1 Functional description .............................................................................................................................. 5
3.2 Constructive features ............................................... ............................................................................... 5
3.3 Table of MEC MIX C axial condensation technical data .......................................................................... 6
3.4 Technical data table MEC MIX F axial ..................................................................................................... 6
3.5 Centrifugal condensing MEC MIX C technical data table ...................................................................... 7
3.6 Table of MEC MIX F centrifugal technical data .......................................... ............................................ 7
3.7 Dimensions and dimensions MEC MIX C condensing 20/35 - 20/45 with centrifugal fans ................... 8
Dimensions and dimensions MEC MIX F 20/35 - 20/45 with centrifugal fans ....................................... 8
HOT AIR GENERATORS PRE-MIXED WALL UNITS
MEC MIX C CONDENSING SERIES
AXIALS AND CENTRIFUGES
MODELS 20/35 - 20/45 - 20/70 - 20/90
SERIES MEC MIX F AXIAL AND CENTRIFUGAL
MODELS 35 - 50 - 70 - 100
Technical information
This manual is separated into ve sections:
- SECTION A - GENERAL INFORMATION
It contains all the news related to the description of the generators and their technical characteristics
- SECTION B - TECHNICAL NEWS FOR THE INSTALLER
It collects all the indications and the instructions that the installation technician must observe for the realization
of an optimal system
- SECTION C - HYDRAULIC INSTALLER
- SECTION D - ELECTRIC INSTALLER
- SECTION E - ASSISTANCE AND MAINTENANCE
Important notes for consultation:
1 -For the purpose of the correct and safe use of the appliance, the designer, the installer, the user and the
maintenance technician, for their respective competences, must scrupulously observe what is indicated
in this manual. It must be kept for possible consultation and must accompany the appliance throughout its
life, including the case of transfer to third parties.
2 - With the wording ATTENTION! they follow information that, due to their importance, must be scrupulously
observed and whose non-compliance can cause damage to the appliance and / or jeopardize its safe use.
The paragraphs highlighted in bold contain information, warnings or important advice that is recommended
to evaluate carefully.
3 - The A2B Accorroni E.G. Srl declines any responsibility for any damage caused by improper use
of the appliance, from a different use to the intended use and from an incomplete or approximate
application of the instructions contained in this manual.
4 - The technical data, the aesthetic characteristics, the components and the accessories shown in this
manual are not binding.
The A2B Accorroni E.G. Srl reserves the right to make changes at any time deemed necessary for the
improvement of its product.
5 - References to laws, regulations or technical rules cited in this manual are intended for information
purposes only and referred to the date of printing of the same, shown on the last page. The entry into force
of new provisions or changes to those in force will not constitute a reason for any obligation of A2B
Accorroni E.G. S.r. towards third parties.
6 - The A2B Accorroni E.G. Srl is responsible for the conformity of its product with the laws, directives and
construction standards in force at the time of marketing. The knowledge and observance of the laws
and regulations concerning the design of the systems, installation, operation and maintenance are the sole
responsibility, for the respective skills, of the designer, installer and user.

3
3.8 Dimensions and dimensions MEC MIX C with condensation 20/35 - 20/45 with axial fans .................. 9
Dimensions and dimensions MEC MIX F 35 - 50 with axial fans ........................................................... 9
3.9 Dimensions and dimensions MEC MIX C condensation 20/70 - 20/90 with centrifugal fans ................ 10
Dimensions and dimensions MEC MIX F 70 - 100 with centrifugal fans ............................................... 10
3.10 Dimensions and dimensions MEC MIX C condensing 20/70 - 20/90 with axial fans ............................. 11
Dimensions and dimensions MEC MIX F 70 - 100 with axial fans ........................................................ 11
3.11 Wiring diagram - MEC MIX C / F series .................................................................................................. 12
4. CONTROL AND SECURITY BODIES .................................................................................................... 13
4.1 Description ............................................................................................................................................... 13
4.2 General features ...................................................................................................................................... 13
4.3 Logical data technical data ...................................................................................................................... 13
4.4 Checks on commissioning ...................................................................................................................... 14
5. KRONOS GA11 CHRONOTHERMOSTAT ............................................................................................ 15
5.1 Weekly-programming digital chronothermostat for the remote control of hot air generators through.... 15
5.2 General technical data ............................................................................................................................ 15
5.3 Technical data of the chronothermostat................................................................................................. 15
5.4 Instructions for use .................................................................................................................................. 19
5.5 Base function rst leve............................................................................................................................. 19
5.6 Corrispondence between icons and operation modes ........................................................................... 17
5.7 Management chronothermostat setting menu ........................................................................................ 19
5.8 Management system parameters menu ................................................................................................. 21
6. SPECIFIC FUNCTIONS KRONOS GA11 ............................................................................................. 22
6.1 Internal energy store and use of batteries............................................................................................... 22
6.2 Warnings about the backlight.................................................................................................................. 22
6.3 Installation instructionst........................................................................................................................... 22
6.4 Installing the chrothermostat on the wall................................................................................................. 23
6.5 Dimensions xings................................................................................................................................... 23
6.6 Wiring diagram for brahma equipment type TC340P.............................................................................. 24
6.7 Connection diagram for cascade connections more devices through Open Therm.............................. 25
6.8 Types 0f connection................................................................................................................................. 26
7. INSTALLATION ....................................................................................................................................... 27
7.1 General rules for installing the appliance ................................................................................................ 27
7.2 Installation sequence .............................................................................................................................. 28
7.3 Dimensioning of air tubes comburente / fumes discharge ..................................................................... 29
7.4 Calculation example ................................................................................................................................ 30
7.5 Conduct evacuation ................................................................................................................................ 34
8. INSTALLATION ............................................... ...................................................................................... 35
8.1 How to connect the generator to the electric line ................................................................................... 35
8.2 Digital chronothermostat installation ....................................................................................................... 35
9. ASSISTANCE AND MAINTENANCE ..................................................................................................... 36
9.1 First switching on of the appliance .......................................................................................................... 36
9.2 How to adjust the gas valve .................................................................................................................... 36
9.3 How to change gas ................................................................................................................................. 38
9.4 Maintenance ............................................................................................................................................ 38
10. TECHNICAL DATA TABLES ERP ........................................................................................................... 39
10.1 Technical data table ERP - MEC MIX C 20/35 - 20/70 axial ................................................................... 39
10.2 Table of ERP technical data - MEC MIX C 20/35 - 20/70 centrifuges .................................................... 40
10.3 Technical data table ERP - MEC MIX C 20/45 - 20/90 axial .................................................................. 41
10.4 Table of technical data ERP - MEC MIX C 20/45 - 20/90 centrifuges .................................................... 42
10.5 Technical data table ERP - MEC MIX F 35 - 70 axial ............................................................................. 43
10.6 Table of technical data ERP - MEC MIX F 35 - 70 centrifuges ............................................................... 44
10.7 Technical data table ERP - MEC MIX F 50 - 100 axial ........................................................................... 45
10.8 Technical data table ERP - MEC MIX F 50 - 100 centrifuges ................................................................. 46
11. MAIN REQUIREMENTS OF HOT AIR GENERATORS ......................................................................... 47
11.1 Table of main requirements - MEC MIX C 20/35 - 20/70 axial ............................................................... 47
11.2 Table of main requirements - MEC MIX C 20/35 - 20/70 centrifuges ..................................................... 47
11.3 Table of main requirements - MEC MIX C 20/45 - 20/90 axial ............................................................... 48
11.4 Table of main requirements - MEC MIX C 20/45 - 20/90 centrifuges ..................................................... 48
11.5 Table of main requirements - MEC MIX F 35 - 70 axial .......................................................................... 49
11.6 Table of main requirements - MEC MIX F 35 - 70 centrifuges ................................................................ 49
11.7 Table of main requirements - MEC MIX F 50 - 100 axial ........................................................................ 50
11.8 Table of main requirements - MEC MIX F 50 - 100 centrifuges .............................................................. 50

4
1. GENERAL WARNINGS
This manual is an integral part of the product, it should
not be separated from it and must be kept carefully for
any future use or consultation.
Failure to comply with the indications in this manual
will result in the forfeiture of the warranty conditions.
Should the appliance be sold or transferred to
another owner, make sure that the manual always
accompanies the appliance. This appliance must only
be used for the purpose for which it was built.
All uses not expressly indicated in this manual are
considered improper and therefore dangerous.
2. SAFETY WARNINGS
2.1 QUALIFICATION OF THE INSTALLER
Installation and maintenance must only be carried out
by specialized and specially qualied personnel.
2.2 POWER SUPPLY
The MEC MIX series hot air generator must be
correctly connected to an efcient grounding system.
The connection to the power supply must be performed
according to the current national plant standards.
2.3 COMBUSTIBLE
Before starting the MEC MIX verify that:
- the data of the gas supply networks are compatible
with those shown on the plate;
- the combustion air intake grill is not obstructed
(even partially);
- the generator is powered by the same type of
fuel for which it is prepared;
- the system is sized for this capacity and is equipped
with all safety and control devices caught
by applicable rules
- internal cleaning of the gas pipes and channels
air distribution for ductable generators has been
performed correctly
- the fuel ow rate setting is adequate to the power
required by the generator
- the fuel supply pressure is included in the values
shown on the plate.
2.4 GAS LEAKS
If you feel a gas smell:
- do not operate electric switches, the telephone e
any other item or device that can cause sparks;
- open doors and windows immediately;
- request the immediate intervention of qualied and
specialized personnel.
2.5 USE
The use of the appliance should not be allowed to
children, inexperienced persons and unassisted
disabled persons.
The following indications must be observed:
- do not touch the appliance with parts of the body
wet or humid and / or barefoot;
- do not insert tools, paper or anything else penetrate
through the protection grids of the fans;
- do not open the access panels to the internal parts
unit. These operations have been re-established
exclusively to specialized personnel;
- do not clean the external parts without having rst
removed it the power supply from the main switch;
- do not touch the hot parts of the generator such as
example the smoke exhaust duct;
- do not wet the generator with water or other liquids;
- do not use gas pipes as grounding electrical devices;
- do not leave the appliance exposed to agents weather;
- do not place objects on top of the appliance;
- do not touch the moving parts of the generator.
2.6 TRANSPORTATION AND HANDLING
The appliance is shipped on wooden pallets, covered
with a suitably secured cardboard box.
The appliance can only be moved by suitably equipped
personnel and with equipment suitable for the weight
of the product, such as a forklift truck or transpallet,
taking care to distribute the weight on the supports.
WARNING! During transport and handling the
appliance must only be kept in a vertical position.
Upon delivery, check that no visible damage has
occurred during transport on the packaging and / or
on the appliance.
In case of damage assessment, immediately expose
a formal complaint to the forwarder.
Do not install damaged devices during transport.
It is forbidden to dispose parts of the packaging
in the environment, or leave it within reach of
children as a potential source of danger.
Any storage of the generator must take place in a
suitable place, protected from atmospheric agents
and from excessive humidity, for the shortest possible
time.
SEZIONE A - INFORMAZIONI GENERALI

5
3. MAIN FEATURES
3.1 FUNCTIONAL DESCRIPTION
The MEC MIX series hot air generator is an independent
heating device of type atin circuit.
The appliance belonging to the II2H3P category
according to the EN 1020 standard, can be adapted
to operation with natural gas (G20) and G.P.L. (G31).
It was designed to be installed inside the room to be
heated.
The combustion circuit is watertight compared to the
heated environment and meets the requirements
of the EN 1020 and EN 1196 standards for type C
appliances: the combustion air extraction and the
fumes discharge take place outside and are insured
from the operation of a blower inserted in the circuit of
combustion.
The operation of the generator is controlled by the
room thermostat integrated in the chronothermostat.
When the hot card is hot, after a pre-wash time of about
40 seconds, provides for the ignition of the burner.
The detection electrode checks that the ignition has
occurred.
In the event of a ame failure, the control board blocks
the device.
The combustion products internally cross the heat
exchangers that are invested externally from the air
ow produced by the fan giving rise to the circulation
of hot air in the environment.
The airow direction is adjustable by means of the
horizontal ns of the mobile grate.
The fan is automatically activated only by hot heat
exchangers (when the temperature of 40 °C is
reached on the exchangers probe), in order to avoid
the introduction of cold air into the environment, and it
will switch off with cold exchangers.
In case of overheating of the heat exchangers, due
to anomalous functioning, the probe of temperature
removes voltage from the gas valve by supplying
the blower and the fan at maximum speed; if the
temperature should increase further, the limit
thermostat intervenes which causes the generator to
switch off.
The reset of the generator in block due to intervention
of the limit thermostat is manual and takes place via
the remote control.
WARNING!
The reset of the generator in block due to
intervention of the limit thermostat is the
responsibility of the personnel professionally
qualied, after having identied the cause of
overheating.
Upstream of the burner a blower provides for the air-
gas mixing and for the forced expulsion of the fumes
derived from combustion.
In the case of obstruction of the intake or exhaust duct,
or in the event of malfunction of the blower,
the electronics respond automatically, causing
generator modulation.
In the event of obstructions or malfunctions beyond
the permitted temperature, a ue gas thermostat will
then cause the gas valve to stop and the generator to
shut down.
Winter operation of the generator can be automatic
or manual: for further information see paragraph
WINTER OPERATION (HEATING).
During the summer it is possible to operate the fan
only, in automatic or manual mode, to order to have a
pleasant movement of the ambient air.
3.2 CONSTRUCTION CHARACTERISTICS
The MEC MIX series hot air generator is supplied
complete with:
- premixed stainless steel burner
- high prevalence blower, with modulation of the
rotation speed
- stainless steel combustion chamber
- heat exchangers, made of stainless steel, with a
very high heat exchange capacity.
- external paneling made of painted steel with epoxy
powders.
- high air ow axial fans, with variation of the rotation
speed.
The generator is also supplied with the following
components control and security:
- electronic management board, with microprocessor
and anti-noise lter: provides for burner ignition
functions, surveillance and ame modulation;
command and control of the burner fan speed,
command fan speed; temperature control of the
exchanger by means of a probe;
- Supply voltage: 230 V - 50 Hz
- Security time: 5 seconds
- Prewash time: 40 seconds
- Model: BRAHMA TC3 40 with transformer ignition
BRAHMA AR1
- 90 °C limit thermostat against overheating of heat
exchangers.
- ue gas thermostat: in case the duct of aspiration /
exhaust fumes or the duct internal condensate
evacuation were blocked, the appliance is stopped.
- gas solenoid valve: if a device intervenes of safety
(limit thermostat, thermostat of safety, etc.) the gas
valve is de-energized electrically with the consequent
interruption of inow of gas to the burner.
- Supply voltage: 230 V - 50 Hz
- Operating temperature: 0 ° C up to + 60 ° C.
- Model: SIT 848 SIGMA

6
3.3 Technical data table MEC MIX C axial
DESCRIPTION
Equipment category
Type of device
Gas supplies
Rated heating capacity
Heat capacity min
Nominal heat output
Thermal power min
Condensation produced maximum
Gas ow rate maximum power
15 °C - 1.013 mbar
Gas ow rate minimum power
15 °C - 1.013 mbar
Nominal yield at maximum ow
Nominal yield at minimum ow
Class of NOx emission
Diameter gas supply
Diameter air supply pipe
Diameter exhaust fumes pipe
Electrical Supply
Air ow max
Air ow min
Rpm air fans
Launching
Jump thermal power max
Jump thermal power min
Sound level (5 meters)
Electrical power
Fuse
Net weight
Methane 20 mbar
Propane 37 mbar
Methane 20 mbar
Propane 37 mbar
MEC MIX C 20/35 A
34,9
19,8
34,2
20,8
3,9
3,69
2,71
2,10
1,55
98,0
105,1
4
3600
2100
1210
27
28,4
29,6
48
365
6,3
84
MEC MIX C 20/45 A
45,0
20,0
43,4
20,9
4,3
4,76
3,49
2,12
1,55
96,5
104,5
3
3600
2100
1210
27
36,1
29,8
48
365
6,3
84
G 1/2
60
60
230V/1/50Hz
II2H3P
B23 - C13 - C33 - C63 - C53
Gas Naturale - G.P.L.
2 x G 1/2
2 x 60
2 x 60
MEC MIX C 20/70 A
69,8
39,6
68,4
41,6
7,8
7,40
5,40
4,20
3,10
98,0
105,1
4
7200
4200
1210
27
28,4
29,6
51
730
2 x 6,3
160
MEC MIX C 20/90 A
90,0
40,0
86,9
41,8
8,6
9,50
7,00
4,20
3,10
96,5
104,5
3
7200
4200
1210
27
36,1
29,8
51
730
2 x 6,3
160
U.M.
kW
kW
kW
kW
l/h
m3/h
kg/h
m3/h
kg/h
%
%
”
mm
mm
m3/h
m3/h
n.
m
°C
°C
dB(A)
W
A
kg
3.4 Technical data table MEC MIX F axial
DESCRIPTION
equipment category
Type of device
Gas supplies
Rated heating capacity
Heat capacity min
Gas ow
15°C-1.013 mbar
Nominal yield at maximum ow
Nominal yield at minimum ow
pressure feeding LPG 31
Class of NOx emission
Diameter gas supply
Diameter air supply pipe
Diameter exhaust fumes pipe
Air ow max
Air ow min
Rpm air fans
launching
Jump thermal power max
Jump thermal power min
Sound level (5 meters)
electrical power
fuse
net Weight
Methane
Propane
MEC MIX F 35 A
34,9
33,9
3,69
2,71
97,0
4
3600
2100
1120
27
28,1
48
365
6,3
84
MEC MIX F 50 A
50,1
47,9
5,30
3,89
95,6
2
3600
2100
1120
27
39,8
48
365
6,3
84
G 1/2
60
60
230V/1/50Hz
20
37
II2H3P
B23 - C13 - C33 - C63 - C53
Gas Naturale - G.P.L.
2 x G 1/2
2 x 60
2 x 60
MEC MIX F 70 A
69,8
67,7
7,39
5,42
97,0
4
7200
4200
1210
27
28,1
51
730
2 x 6,3
160
MEC MIX F 100 A
100,2
95,8
10,60
7,78
95,6
2
7200
4200
1210
27
39,8
51
730
2 x 6,3
160
U.M.
kW
kW
m3/h
kg/h
%
mbar
mbar
”
mm
mm
m3/h
m3/h
n.
m
°C
dB(A)
W
A
kg

7
3.5 Technical data table MEC MIX C centrifuge
DESCRIPTION
equipment category
Type of device
Gas supplies
Rated heating capacity
Heat capacity min
Nominal heat output
Thermal power min
Condensation produced maximum
Gas ow rate maximum power
15 °C - 1.013 mbar
Gas ow rate minimum power
15 °C - 1.013 mbar
Nominal yield at maximum ow
Nominal yield at minimum ow
Class of NOx emission
Diameter gas supply
Diameter air supply pipe
Diameter exhaust fumes pipe
Electrical Supply
Pressure ventilation
Air ow max
Air ow min
Jump thermal power max
Jump thermal power min
Sound level (5 meters)
Electrical power
Fuse
Net Weight
Methane 20 mbar
Propane 37 mbar
Methane 20 mbar
Propane 37 mbar
MEC MIX C 20/35 C
34,9
19,8
34,2
20,8
3,9
3,69
2,71
2,10
1,55
98,0
105,1
4
3700
2200
27,7
28,3
52
1050
10
93
MEC MIX C 20/45 C
45,0
20,0
43,4
20,9
4,3
4,76
3,49
2,12
1,55
96,5
104,5
3
3750
2200
34,7
28,4
52
1050
10
94
G 1/2
60
60
230V/1/50Hz
100
II2H3P
B23 - C13 - C33 - C63 - C53
Natural Gas - G.P.L.
2 x G 1/2
2 x 60
2 x 60
MEC MIX C 20/70 C
69,8
39,6
68,4
41,6
7,8
7,40
5,42
4,19
3,10
98,0
105,1
4
7400
4400
27,7
28,3
54
2100
2 x 10
185
MEC MIX C 20/90 C
90,0
40,0
86,9
41,8
8,6
9,50
6,99
4,24
3,11
96,5
104,5
3
7500
4400
34,7
28,4
54
2100
2 x 10
188
U.M.
kW
kW
kW
kW
l/h
m3/h
kg/h
m3/h
kg/h
%
%
”
mm
mm
Pa
m3/h
m3/h
°C
°C
dB(A)
W
A
kg
3.6 Technical data table MEC MIX F centrifuge
DESCRIPTION
equipment category
Type of device
Gas supplies
Rated heating capacity
Heat capacity min
Gas ow
15°C-1.013 mbar
Nominal yield at maximum ow
Nominal yield at minimum ow
pressure feeding LPG 31
Class of NOx emission
Diameter gas supply
Diameter air supply pipe
Diameter exhaust fumes pipe
Electrical power
Air ow max
Air ow min
Jump thermal power max
Sound level (5 meters)
electrical power
fuse
net Weight
Methane
Propane
MEC MIX F 35 C
34,9
33,8
3,69
2,71
96,8
4
3700
2200
27,3
52
1050
10
93
MEC MIX F 50 C
50,1
47,9
5,30
3,89
95,6
2
3750
2200
38,2
52
1050
10
94
G 1/2
60
60
230V/1/50Hz
100
20
37
II2H3P
B23 - C13 - C33 - C63 - C53
Natural Gas - G.P.L.
2 x G 1/2
2 x 60
2 x 60
MEC MIX F 70 C
69,8
67,6
7,39
5,42
96,8
4
7400
4400
27,3
54
2100
2 x 10
185
MEC MIX F 100 C
100,2
95,8
10,60
7,78
95,6
2
7500
4400
38,2
54
2100
2 x 10
188
U.M.
kW
kW
m3/h
kg/h
%
mbar
mbar
”
mm
mm
Pa
m3/h
m3/h
°C
dB(A)
W
A
kg

8
3.7 DIMENSIONS AND DIMENSIONS
Series MEC MIX C condensing models 20/35 - 20/45 with centrifugal fans
MEC MIX F series models 35 - 50 with centrifugal fans
Values expressed in mm
* The drain siphon is only available in the condensing MEC MIX C series
747
120
view from above
gas
connection
air intake exhaust exhaust*

9
3.8 DIMENSIONS AND DIMENSIONS
Series MEC MIX C condensing models 20/35 - 20/45 with axial fans
MEC MIX F series models 35 - 50 with axial fans
Values expressed in mm
* The drain siphon is only available in the condensing MEC MIX C series
view from above
gas
connection
air intake exhaust exhaust*

10
3.9 DIMENSIONS AND DIMENSIONS
Series MEC MIX C condensing models 20/70 - 20/90 with centrifugal fans
Series MEC MIX F models 70 - 100 with centrifugal fans
Values expressed in mm
combustion
air intake
combustion
air intake
gas
connection
gas
connection
exhaust
fumes
exhaust
fumes

11
3.10 DIMENSIONS AND DIMENSIONS
MEC MIX C series condensing models 20/70 - 20/90 with axial fans
MEC MIX F series 70 - 100 models with axial fans
Values expressed in mm
combustion
air intake
combustion
air intake
gas
connection
gas
connection
exhaust
fumes
exhaust
fumes

12
3.11 ELECTRICAL DIAGRAM - MEC MIX C / F Series
LEGEND
ACC1 Remote ignition transformer
C1 Capacitor 1 (5μF)
C2 Capacitor 2 (5μF)
EA Ignition electrode
EF Burner fan motor
EV1 First valve stage
EX Connection for equipment
in cascade
F1 Fuse 1 (6.3A)
F2 Fuse 2 (6.3A)
FAN1 Fan motor 1 treated air
FAN2 Fan motor 2 treated air
GA1 Programmable thermostat
ION Detection electrode
M1 Terminal block 1
RESET Release button
SA Room sensor (optional)
SL LED light signaling
SR FAN and LIMIT regulation sensor
STF Fire damper (optional)

13
4. CONTROL AND SECURITY BODIES
In this section you will nd all the necessary
information to make it work properly MEC MIX
series generators.
The functioning of the MEC MIX series generator is
controlled by the BRAHMA digital thermoregulation
system mod. TC340.
The digital thermoregulation system performs
the dual function of room thermostat and clock
programmer as well as to diagnose any operating
errors.
The following are all the necessary instructions
for the correct use of the thermoregulation system
digital.
4.1 DESCRIPTION
This device is expressly designed for the control
of the safety cycle and for the thermoregulation in
the hot air generators using gas burners sealed
chamber with automatic ignition and pre-mixed
modulating burners.
4.2 GENERAL CHARACTERISTICS
Important device requirements are:
- compliance with EN 298: 2003-09 (European
standard for automatic programming systems
and verication of the presence of ame for
burners gas);
- CE certication in accordance with the Directive
Gas 90/396 / EEC and subsequent amendments
(Directive 93/68 / EEC);
- piloting and regulation by phase cutting of the
treated air convector fan (FAN);
- piloting and regulation of the fan
burner by phase cutting (applications with burners
forced draft gas) or via PWM signal (applications
with type gas burners premixed using type fans
brushless with integrated management
electronics);
- two independent safety contacts for the piloting
of the main gas solenoid valve EV1;
- exit for driving a transformer auxiliary electronic
ignition;
- regulation of the burner power via PWM signal
(for type applications premix);
- interfacing with a digital chronothermostat GA1
type via communication protocol OpenTherm ™;
- summer ventilation function (requires connection
to BRAHMA chronothermostat type GA1);
- management of a double NTC probe type ST16
for the control of the delivery temperature
air for regulation and safety functions;
- management of a double NTC probe type ST08
for the control of the delivery temperature
air for regulation functions;
- possibility of managing a thermostat safety;
- provision for the management of a probe ad
NTC type ST07 with room probe function or
external probe (g 3);
- possibility of connecting a damper contact
re barrier (optional);
- possibility of use in applications with regulation
by analogue 0¸10V signal (ex. PLC);
- manual reset button on the board;
- reporting of the operating status and of any
anomalies by means of two-colored LEDs;
- RS-232 communication interface for diagnostic
and setup functions;
- integrated EMI noise lter;
- two fuses with a suitable extractor for the power
line protection on both potentials;
- connections for integrated security lands on
card.
4.3 TECHNICAL DATA LOGIC CARD
Internal fuses: 6.3 A delayed type
for TC340P: 3.15 A delayed type
External fuses (recommended): 6.3 A quick type 1
for TC340P: 3.15 A rapid type 1
EC type examination certicate:
CE0051-PIN0051BU3887
Times:
Pre-ventilation time (TP): 0...60 s
Safety time (TS): 3 ... 120 s
Intervention time in case of shutdown
ame: <1 s
Post-ventilation times
- on the burner fan
EF (tPOST): 0 ... 1200 s
- on treated air fan
FAN (tFS): 20 ... 1200 s
Delay time at power up
of the FAN fan (tFA): 2 0 ... 1200 s14
Waiting time or ventilation: 1 ... 240 s
Waiting time for entry
in modulation (tRP1): 1 ... 240 s
Block delay for parasitic
ame (option Knn): 0 ... 60 s
Block for air lack
(option Qnn) 3: 3 ... 120 s
SECTION B - USER

14
Pre-ignition time (option Jnn): 1 ... 60 s
Cycle repetition attempt
(option Ynn): 1 ... 10
Maximum cable length of external
components: OpenTherm ™
interfaces: 50 m
Flame control
The ame detection device uses the righting
property of the ame.
As an important safety aspect, it should be noted
that the control device is more sensitive to ame at
start-up or during waiting / pre-purge time (negative
differential switching).
Minimum ionization current: 0.5 μA
System temperature probes
- Regulation probe (SR)
The control probe is designed to detect the
temperature of the heat exchanger and is mainly
used by the NTC dual-sensor FAN heating function
(version standard):
in this case the probe has a double function as it
avoids the use of the safety thermostat.
It will therefore be used both for temperature control
functions and for safety functions ( safety shutdown
due to excessive system temperature).
For this purpose it is necessary to use the BRAHMA
probe type ST16 (g.3).
Ambiance sensor (SA)
The room probe (optional) can be used if the remote
temperature control (BRAHMA chrono thermostat
type ENCRONO GA1) is not in the area where you
want to implement thermoregulation or in cases
where it is necessary to relate the latter to the
temperature of the environment external.
For more details about the functions in which this
probe is used, refer to the section
“OPERATION”
For this purpose it is necessary to use the BRAHMA
probe type ST07 (for the detection of the local
ambient temperature) or the BRAHMA probe type
SSE (for the detection of the external ambient
temperature).
Fire damper (STF)
Through this input (option S) it is possible to check
the contact status of the re damper: in case this
consent was open (fault condition) the ignition cycle
it is interrupted by bringing the device into the
waiting position, signaling the error by means of
LEDs.
On request, the behavior of the equipment in case
of opening of the contact can be modied according
to customer specications.
4.4 CHECKS STARTING UP
Carry out a check of the device when it is put into
operation for the rst time, after each revision and
after the system has been inactive for a long time.
Before any ignition operation, check that the
combustion chamber is free from gas, therefore
check that:
- if the start-up attempt is implemented without
gas injection occurs a blocking stop at the end of
the security time;
- interrupting the ow of gas with the appliance in
the operating position, voltage is removed within
1s to the gas solenoid valves and, after a
repetition of cycle (or more cycle repetitions up to
a maximum of 10, depending on the settings),
the device make a block stop;
- the times and the cycle comply with those
declared for the type of device used;
- the ame signal level is sufcient high (see Fig.4);
- the ignition electrodes are adjusted
stably for a discharge distance in air between
2 and 4 mm;
- the intervention of limiters or safety devices
cause the safety lock or shutdown of the appliance
according to the type of application and the
procedures laid down.
Connection of the double NTC probe
Brown
black
blue
Fig. 3
Fig. 4
Measurement of the ame signal
Microampere

15
5. KRONOS GA11
5.1 WEEKLY-PROGRAMMING DIGITAL
CHRONOTHERMOSTAT FOR THE REMOTE
CONTROL OF HOT AIR GENERATORS
THROUGH INTERFACE BOARD
The digital chronothermostat Brahma Kronos series
integrates the functions of room temperature control
and remote control of hot air generators in a single
interface, specially designed to make available all its
functionalities in intuitive mode.
Control of the heating system is complete, allowing to
manage the parameters of more air generators, with
the related control boards connected in cascade, and
the eventual unlock.
It is possible to choose beetween different modes of
thermoregulation, even using an external probe
(connected to the hot air generator) for climatic
compensation.
Weekly programmation is particularly versatile
because it provides 4 temperature levels settable and
no restriction number of time slots per day, consisting
of individual intervals equal to a quarter of an hour
and can be viewed on the appropriate graph of the
daily program.
The communication between the chronothermostat
(master) and the control board (slave) of hot air
generators takes place by means of a two-wire cable.
Particulary, the data, between the chronothermostat
and the control board of the rst generator, are
exchanged with the communication protocol
compatible OpenTherm ™ v3.0 Smart Power Mode
- Medium Power.
5.2 GENERAL TECHNICAL DATA
- Brahma design
- graphic LCD 128x64 pixel
- backlight timer 20 seconds
- LED for diagnostics/signaling
- 7 variable function keys
- weekly programming
- 4 temperature levels (T0, T1, T2, T3)
- resolution (0,5°C temperature set)
- resolution (0,1°C temperature read)
- minimum interval programming: 15 minutes
- SELV insulation (Safety Extra Low Voltage)
- bipolar connection, non-polarized
- protocol v3.0 Smart Power Mode – Medium Power
5.3 TECHNICAL DATA OF THE
CHRONOTHERMOSTAT
Operating temperature: 0°C +50°C
Humidity: 95% maximum at 40°C
Power supply: low voltage (3V), obtained from
communication with the hot air generator control board
Protection degree: IP30
Dimensions: 140x90x32 mm
Compliance: directive 2004/108/CE (EMC), directive
2006/95/CE (LVD).
Description of the remote control unit
graphic display (LCD)
buttons to select
or change the
function
parameters
buttons to
increase and
decrease
temperatures and
parameters
hole for
access to the
reset button
multifunction button with LED
function buttons
(il comando attivo è indicato, di volta in volta, sul display graco) Fig. 5

16
5.4 INSTRUCTION FOR USE
The Kronos GA11 provides the user with a graphic LCD
dot-matrix, a series of buttons in silicon rubber, and an
LED indicator located below a button plastic transparent
to display the parameters and interact with the heating
system. Figure 5.
The buttons have any versatile utilization depending on
the selected menu.
The use of buttons is facilitated by the indications with
text, icons and other graphics that appear on the display.
The vertical buttons on the left of the display are typically
used to navigate the setup menu or to select the
parameters.
The vertical buttons on the right of the display are used
to vary temperature and the classical function increase /
decrease (+ / -).
To facilitate the change of set values, the long press of
these buttons accelerates the increase or decrease.
The horizontal buttons at the bottom serve to conrm or
cancel the settings, or to enter and exit the submenus.
The center button to used for special functions as the
unlock of the boiler.
Under the center button there is an LED:
- LED with color red continuous: error or no
communication with the hot air generators;
- LED with color red intermittent: hot air generators
lockout;
- LED with color yellow intermittent: anomaly;
LED with color green continuous: the
chronothermostat is resuming work after a power
failure.
The most frequently used functions by the user are
available in the main menu.
It is possible to quickly browse through the pages to set,
for example, room temperature or the maximum power
of the hot air generators.
The rst time or after a reset of the Kronos, appears the
language menu, as shown in the gure below.
Pushing buttton OK, you conrm the selection.
5.5 BASE FUNCTION
FIRST LEVEL MENU
When the chronothermostat is connected to a
hermoregulation board, the following screen appears on
the display.
If the thermoregulation board is not compatible, you will
receive an error message.
Then the current time can be entered.
Also in this case the buttons to the left allow you to select
the various menu items, while the right buttons are used
to change the values, the OK button stores the settings
while the ESC button allows you to continue without
changing the data time.
If you press ESC, the subsequent reconnection of the
cronothermostat (for example power down) you will
again be prompted to select the language and set the
current time.
In the gure the main screen.
Above are shown the day of the week and the current
time, these indications are intermittent if they are not
updated.
Below there is an indication of the temperature measured
(measurement every 10 seconds);
Beside, an icon indicates the function of thermoregulation
currently active: in this case the image of a clock
indicating the automatic mode.

17
The buttons on the right, marked with + and -, allow
to vary the temperatures required for the automatic
program (T0, T1, T2, T3). Instead, in “manual mode”
(icon ) allow to vary the set point room temperature.
Pushing the buttons on the left, marked with arrows, you
can browse the pages of rst level menu.
Pushing the button▼, the following display appears.
Pushing the buttons +/- you can vary the temperature
and pushing the button OK you activate the “manual
mode”.
Pushing again button ▼, you can activate the “summer
mode”, which is not active environment thermoregulation.
The management of the cronothermostat by the user is
much simplied. The functions are not distinct between
the functions relating to hot air generators and functions
relating to thermoregulation.
If you select the “summer mode”, you can turn summer
ventilation through the function key [Vent.].
Once activated ventilation, a key mark becomes [V.OFF],
and it is possible to stop the fan using the same key.
5.6 CORRISPONDENCE BETWEEN ICONS AND
OPERATION MODES:
Automatic
Temperature control
environment according to the
weekly program set by the
user. Program seen as
a graph of the current day.
Temperature control
environment in accordance
with a user-selected
temperature (thermostat
function).
Manual
Sandby Temperature control
environment disable.
Temperature control
environment disable.
Summer ventilation can be
activated manually.
Summer
In “automatic mode”, the cronothermostat performs the
temperature control program was set for the current day,
the graph is visible at the bottom of the display.
The graph is divided into time intervals of 15 minutes,
corresponding to a pixel horizontally, and in the four
programmable temperature levels.
Near the icon of the operation mode other icons may
appear.
If the hot air generators is turned on appears ame
symbol, different sizes depending on the modulation
level of the ame ( ) ).
If it present a lockout or a fault appear symbols
( , ! ) respectively and if it is not present the
connection icon appears symbol ( ?).
No icon appears in the visualization if the hot air
generators is in stand-by and has no problem.
Under the indication of the room temperature may
be present, in addition, a line of text that provides
information to the user in special cases, such as the
presence of error or the status of additional Here there
are the messages that may appear, alongside with their
meanings:
____________________________________________________________________
Starting… Kronos is in the process of connection to the hot
air generators.
____________________________________________________________________
Ambient probe error Room temperature sensor on Kronos damaged.
____________________________________________________________________
Fault code xxx There is an anomaly or a lockout on the hot air
generators. Code xxx .
____________________________________________________________________
Comm. error Communication error between Kronos and hot air
generators.
____________________________________________________________________
Error ID xx The Kronos fails to correctly interpret of
information sent from the hot air generators.
____________________________________________________________________
Note: Please refer to the thermoregulation board’s documentation for
detailed description of the fault codes and error codes.

18
Pushing again button ▼ you switch to another option:
In this scren, it is possible to limit the power level required
by the chronothermostat to generators, for heating the
environment.
For more details see the next section, in particular the
description of the submenu “Thermoregulation”.
Pushing again button ▼ is proposed the submenu
“PARAMETERS MENU”
The submenu “PARAMETERS MENU” (described in
the relevant section) allows you to see the parameters
of the hot air generators and allows you to manage
advanced functions, such as transparent parameters
(TSP) and unlock.
If you press ▼, you will see the control panel of the
heating system.
In the rst row are displays the icons that illustrate
the status of thermoregulation and generators with at
the side, the number of generators (or control boards
“slave”) connected.
In the central row are displays additional information
about the status of generators or anomalies.
In the third line, if available, is shown the value of outdoor
temperature or errors related to thermoregulation
environment.
This menu has a frame xed.
The options previously seen remain displayed for 20
seconds, then the display returns to the main screen,
which depends on the chosen operation mode. (manual,
automatic, summer, off).
In this option, however, if the user does not push ESC or
not push ▼ or ▲, the crhonothermostat continues to
show the control panel with the relevant information.
Pushing again the button ▼ you return to the rst option.
This option allows you to turn off the system (temperature
control environment and ventilation are disabled).
The rst level menu is circular, all the screens described
above are accessible by pushing the reverse button ▲.
Pushing again button ▼ is proposed the sub-menu
“SETTING MENU”
In “SETTING MENU” are set the calendar, the mode of
thermoregulation and a weekly schedule. The “SETTING
MENU” is described in a separate paragraph below.
Pushing again button ▼ you enter the menu for setting
maximum power.

19
To select the temperature level is necessary to push the
buttons ↓ e ↑, instead to vary the temperature value it is
necessary to push + e –.
On the right side of the screen is shown the relative
position of the current setpoint temperature value with
respect to minimum values (5 °C) and maximum value
(30 °C).
The higher temperature is associated with T3 and the
lowest temperature with T0, the chronothermostat
meets the following constraint: T0 ≤ T1 ≤ T2 ≤ T3 and
automatically resizes the temperatures.
Choosing the option “Day program” you enter in the
following screen.
At the top of the screen you select the day, and at the
bottom of the screen displays the day program.
Pressing the + and - buttons you can select the day.
For example, suppose you want to program the day
“Monday”, pressing OK button you enter the scheduling
of time slots.
The time slots are programmed in three steps: initial
time, temperature and nal time.
In the rst step is set the starting time by pushing the +
and - buttons at intervals of at least 15 minutes and you
conrm pushing OK.
However, if you want to quit the programming of the
selected day, push ESC.
In case it is already active the automatic mode, it is
indifferent push NO or OK.
5.7 MANAGEMENT CHRONOTHERMOSTAT
SETTING MENU
This section describes the submenu “SETTING MENU”
This submenu allows you to manage temperature
control environment, the weekly program, the time
setting and the language choosing.
Selecting the option “Programming” you enter in weekly
program dedicated submenu.
Choosing the option “Temperature” you enter in the
screen setting of the four temperature levels T0, T1, T2
and T3.

20
In the second step, pushing the ◄ and ► you select
which of the four programmed temperatures will be
associated to the time slot.
Pushing OK you conrm the level of temperature and
pushing ESC you return in the rst step.
In the third step you select the ending time.
The nal time can not be less than initial time, selecting
two coincident values for initial time and nal time, the
daily schedule is not changed.
The last item on the “Programming” menu allows you to
copy the program day to another day.
At the top you select the source day in the lower you
select the destination day, You can also copy a program
of the day all week and have the same program every
day, to do this select as target the “ALL”.
When you press OK, a message conrms your copy of
the program.
Completed the description of the “Programming menu”,
we return to describe the sub menu “SETTING MENU”.
The “Time setting” submenu on the “SETTING MENU”
allows adjustment of the current time and day of the
week.
Pushing the ↓ and ↑ buttons you select the item you
want to change, while pushing the + and - buttons you
change the value.
Pushing the OK button, you conrm the changes.
The “Language” submenu on the “SETTING MENU”
allows set the language of texts on the chronothermostat.
As seen above, this setting is required when you rst
start or after a reset of the chronothermostat, then it can
be changed at will.
The last item, “Heating Control” of the “SETTING MENU”,
concerns the method used by the chrothermostat for
controlling room temperature.
In this screen you can set the differential, which can
vary between 0.2 º C and 5.0 º C (default value: 2.0 ºC).
dis the thermal differential, Max is the maximum rate,
Ti and Ta are the room temperature set and the room
temperature measured.
The required percentage P is calculated as follows:
if Ta ≤ Ti - d then P = Max
if Ti – d < Ta < Ti then P = ( Max / d ) x ( Ti – Ta )
if Ta ≥ Ti then P = 0
Example 1:
Ti = 20,0 ºC
Max = 100%
d = 0,5 ºC
If Ta ≤ 19,5 ºC then P = 100%;
If 19,5 ºC < Ta < 20,0 ºC then P = (100 / 0,5) x (20 – Ta) %;
if Ta ≥ 20 ºC then P = 0.
On the same page you can enter the hysteresis value
(asymmetric) in order to avoid frequent restart of
generators.
Hysteresis may vary in steps of 0.1 ºC between 0.1 ºC
and 50% of the set differential value.
After reaching the set temperature Ti, the chrothermostat
controls the switching off of the generators, the following
restart will take place only if the temperature falls
under the set temperature decreased hysteresis (Ti-
hysteresis). The default hysteresis is 0.1 ºC.
This manual suits for next models
17
Table of contents
Popular Portable Generator manuals by other brands

Jet
Jet JGE3100 Operation manual
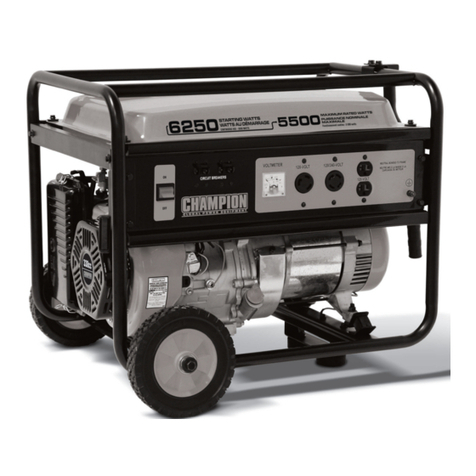
Champion
Champion 41154 Owner's manual & operating instructions
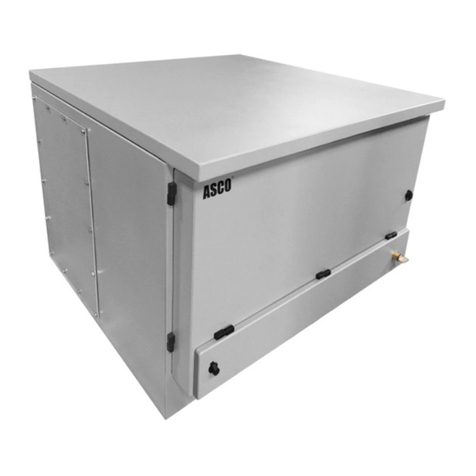
ASCO POWER TECHNOLOGIES
ASCO POWER TECHNOLOGIES Series 300 installation manual
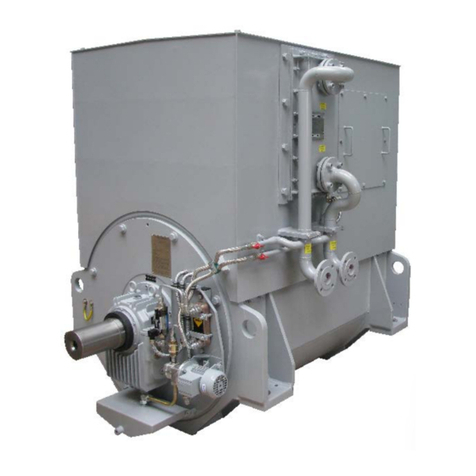
Siemens
Siemens 1D Series operating manual
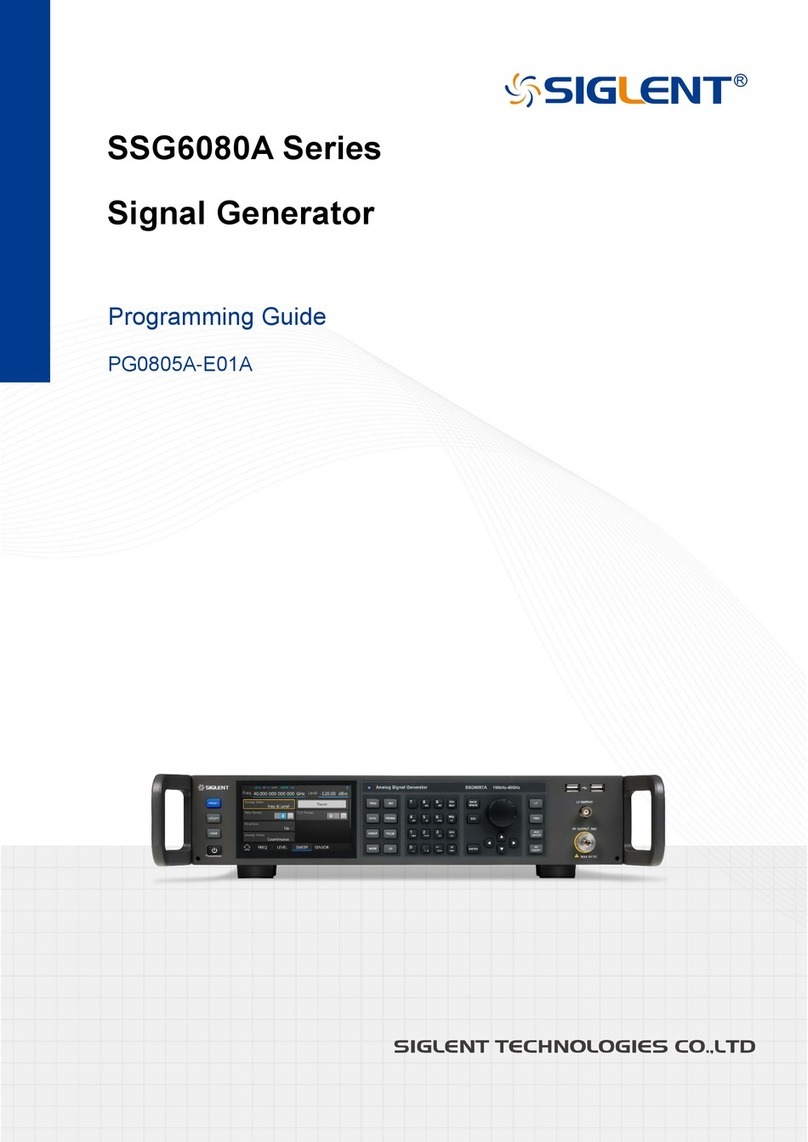
SIGLENT
SIGLENT SSG6080A Series Programming guide
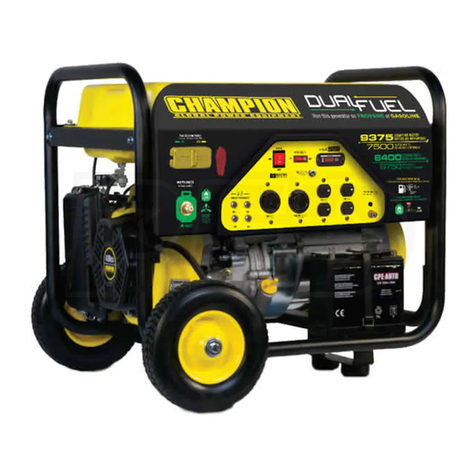
Champion Power Equipment
Champion Power Equipment 71531 Owner's manual & operating instructions