Absolute Measurement ACDF-3 User manual

Transducer Instruction
Manual
Range: Advance
Type: ACDF –3
Revision: V1.0

_____________________________________________________________________________________________________________________
Absolute Measurement Ltd. (T/A CMC Controls)
t: (0) 1732 763278 | e: sales@absolutemeasurement.co.uk | w: absolutemeasurement.co.uk
Unit 19 | Silver Birches Business Park | Aston Road | Bromsgrove | B60 3EU
1
Transducer Instruction Manual
Range: Advance
Type: ACDF –3
Revision: V1.0
Contents
Contents........................................................................................................................................................1
1. Principle of Transducer Operation........................................................................................................2
2. Installation ............................................................................................................................................2
2.1 Selection of Transducer Mounting Location.................................................................................2
2.2 Installation Precautions ................................................................................................................3
2.3 Mounting Surface Preparation .....................................................................................................3
2.4 Bearing Lubrication.......................................................................................................................3
2.5 Sensing Roller Balance ..................................................................................................................3
2.6 Transducer and Sensing Roller Installation...................................................................................4
2.7 Temperature Compensation and Shaft Expansion .......................................................................4
2.8 Hazardous Area Installation - Intrinsic Safety...............................................................................5
2.9 Single Transducer Operation ........................................................................................................5
2.10 Transducer Electrical Connections................................................................................................5
3. Transducer Force (MWF) Calculation ...................................................................................................6
4. Troubleshooting....................................................................................................................................6
4.1 High Output Signal With No Tension ............................................................................................6
4.2 Low Output Signal With Maximum Tension .................................................................................7
4.3 Wrong Polarity of Output Signal...................................................................................................7
4.4 Output Signal Not Linear, Zero Shifts During Operation...............................................................7
4.5 Transducer Strain Gauge Resistance.............................................................................................7

_____________________________________________________________________________________________________________________
Absolute Measurement Ltd. (T/A CMC Controls)
t: (0) 1732 763278 | e: sales@absolutemeasurement.co.uk | w: absolutemeasurement.co.uk
Unit 19 | Silver Birches Business Park | Aston Road | Bromsgrove | B60 3EU
2
Transducer Instruction Manual
Range: Advance
Type: ACDF –3
Revision: V1.0
1. Principle of Transducer Operation
ACDF web tension transducers are annular force transducers supplied with double row self-aligning ball
bearing cartridges for rotating shaft applications. Normally a pair of transducers would be used,
supporting the ends of the tension sensing roller shaft. The tension force applied to the sensing roller
must pass freely through to the transducer, which converts this force into an electrical signal.
This signal is a combination of tension force and sensing roller dead weight. The dead weight is zeroed
out electrically in the indicator or controller leaving the tension force signal only to be amplified to give a
true display of measured tension.
2. Installation
2.1 Selection of Transducer Mounting Location
The transducer must be mounted in a clean, dry location, see below for hazardous area installation.
When selecting a transducer mounting location, please remember that the tension sensing roller must
NOT be mounted where the web wrap angle can vary. Any change in the wrap angle will be sensed by
the transducer as a change in tension, and indicated as such on the tension meter or display.

_____________________________________________________________________________________________________________________
Absolute Measurement Ltd. (T/A CMC Controls)
t: (0) 1732 763278 | e: sales@absolutemeasurement.co.uk | w: absolutemeasurement.co.uk
Unit 19 | Silver Birches Business Park | Aston Road | Bromsgrove | B60 3EU
3
Transducer Instruction Manual
Range: Advance
Type: ACDF –3
Revision: V1.0
2.2 Installation Precautions
To ensure proper installation and operation of the tension system, the following steps should be
performed in sequence - always install, orientate and firmly bolt down the transducer BEFORE installing
the tension sensing roller.
Welding. Unplug the cable connector from the transducer before any electric welding is undertaken on
the machine.
Transport. It is recommended that the tension sensing roller is removed from the transducer before the
machine is transported to prevent excessive shock being transmitted through to the transducer.
Failure to carry out these precautions could seriously damage the transducer and invalidate the warranty.
2.3 Mounting Surface Preparation
Precision machined surfaces are necessary as the transducer is located in the machine frame by the
close tolerance mounting spigot. The close concentricity of this mounting spigot to the bearing diameter
allows parallel path rollers and thus avoids web tracking problems. No appreciable force should be
transmitted through the four fixing bolts. See the Transducer Dimensions drawing for full details.
2.4 Bearing Lubrication
The bearing normally fitted by CMC Controls is without seals and has only the bearing manufacturers
preservative. The bearing will require lubrication by the user prior to use according to the service and
environment. When the transducer is for use in vacuum the bearing will need to be removed from the
transducer, degreased and suitably lubricated by the user before refitting into the transducer. To lubricate
the bearing remove side plate "A" only. Periodic inspection of the lubricant is advised in all cases.
2.5 Sensing Roller Balance
The tension sensing roller should be dynamically balanced when the roller speed exceeds 300 RPM as
excessive vibration can damage the transducer. Any out of balance force should not exceed 10% of the
maximum working force (MWF) of the transducer. The sensing roller must not be driven or have any force
applied to it except by the web. Even with a balanced roller, a vibration can be set up at the critical roller
speed. To ensure that this problem is avoided, the critical roller speed should be at least 20% above that
attained at maximum web speed. Consult the roller manufacturer for advice.

_____________________________________________________________________________________________________________________
Absolute Measurement Ltd. (T/A CMC Controls)
t: (0) 1732 763278 | e: sales@absolutemeasurement.co.uk | w: absolutemeasurement.co.uk
Unit 19 | Silver Birches Business Park | Aston Road | Bromsgrove | B60 3EU
4
Transducer Instruction Manual
Range: Advance
Type: ACDF –3
Revision: V1.0
2.6 Transducer and Sensing Roller Installation
The transducer should be mounted so that the Measurement Direction is in the direction of the resultant
tension force. The cable connector is at right angles to the Measurement Direction.
One end of the sensing roller should be held in the bearing of one transducer, as at 'A' above; the other
end of the roller must be free to move or "float" axially in the other transducer bearing, as at 'B' above.
This float must allow the overall distance between transducers to be reduced by at least 8mm to permit
the transducers and roller assembly to fit inside the machine frames for installation. The transducers may
also be fitted on the outside faces of the frames to allow full use of the machine width. Alternatively
provision must be made to fit the complete transducers and roller as an assembly into the machine
axially. The bearing is retained in the transducer by circlips. It is recommended that only the plain side
plate "A" of the transducer be removed for bearing access, see the Transducer Dimension drawing for
details.
2.7 Temperature Compensation and Shaft Expansion
The transducer is supplied with a temperature compensation network which is in series with Pin D, the
output signal lead. The compensation circuit will operate correctly only when used with a tension indicator
or controller supplied by CMC Controls. The transducer can accommodate sensing roller shaft expansion
due to normal temperature changes. The transducer, sensing roller and machine structure should all
therefore be at normal room temperature during installation

_____________________________________________________________________________________________________________________
Absolute Measurement Ltd. (T/A CMC Controls)
t: (0) 1732 763278 | e: sales@absolutemeasurement.co.uk | w: absolutemeasurement.co.uk
Unit 19 | Silver Birches Business Park | Aston Road | Bromsgrove | B60 3EU
5
Transducer Instruction Manual
Range: Advance
Type: ACDF –3
Revision: V1.0
2.8 Hazardous Area Installation - Intrinsic Safety
CMC Controls tension transducers can be located in a hazardous area to provide an Intrinsically Safe
installation to EN 50039 when a proprietary Zener Barrier module, Part Number 4503, is used. Tension
transducers are passive components and are classified as simple apparatus by EN 50014. Strain gauge
transducers (load cells) will be damaged if subjected to the 500 volt insulation test required by EN 50020.
To comply with Intrinsic Safety regulations the body of the transducer must be bonded to the IS earth
using 4 square millimetre green/yellow insulated cable. Consult CMC Controls for more information.
NOTE It is the responsibility of the user to ensure that all relevant safety regulations are complied with.
The integrity of all connections particularly the earth should form part of any maintenance procedure.
2.9 Single Transducer Operation
Most web tension installations require two transducers, each supporting one end of the sensing roller
shaft and the transducer output signals are summed to give a measurement of Total tension. For those
installations where only one transducer is required a Dummy Transducer, Part Number 4431, may be
needed to complete the full Wheatstone bridge. For single transducer installations the MWF calculation,
see below, should be derated by a factor of 1.5, consult CMC Controls for more information.
2.10 Transducer Electrical Connections
The signal wiring between the transducer and the indicator or controller must be by screened cable
routed well away from any power wiring or other sources of interference.
The RED SPOT on the transducer specifies the output signal polarity in relation to the applied load
direction. Depending on the installation the transducer output signal can be positive or negative for
increasing load. Ensure the yellow and green output leads are connected to the indicator or controller
terminals correctly, so that they add to, rather than cancel each other. In most installations, one
transducer will give a positive signal the other a negative signal.
To confirm the connections to the indicator, switch on, unplug any one of the transducer connectors,
adjust the indicator zero control until the meter or display reads approximately zero. Apply a load to the
tension sensing roller in the same direction as the resultant web tension, the display should move
positive. If the display decreases or moves negative, reverse the appropriate yellow and green transducer
leads at the indicator terminals. Repeat for the other transducer.
When completed, reconnect both transducers.

_____________________________________________________________________________________________________________________
Absolute Measurement Ltd. (T/A CMC Controls)
t: (0) 1732 763278 | e: sales@absolutemeasurement.co.uk | w: absolutemeasurement.co.uk
Unit 19 | Silver Birches Business Park | Aston Road | Bromsgrove | B60 3EU
6
Transducer Instruction Manual
Range: Advance
Type: ACDF –3
Revision: V1.0
3. Transducer Force (MWF) Calculation
The formula for calculation of the transducer maximum working force (MWF) or force rating allows a
100% overload for tension transients or a tight edge to the web.
Remember to use the correct units.
To convert W in Kg to Newtons - N multiply by 10, the exact factor is 9.81
MWF = 2 Tmax Sin(A/2) + (W/2) Sin(B) MWF = 2 Tmax Sin(A/2) - (W/2) Sin(B)
MWF MUST BE GREATER THAN SENSING ROLLER WEIGHT W
ANGLE 'A' IS 30 DEGREES MINIMUM
4. Troubleshooting
There are no user replaceable or serviceable parts in the transducer. Tampering or damage caused
during installation will invalidate the warranty.
The signal output from the transducer with the recommended 5.6V DC excitation is 250mV (nominal)
when the transducer is loaded to its maximum working force - MWF.
The transducer has built in mechanical overload stops which operate at approximately 125% of the MWF.
Forces above 150% of MWF particularly transients or tension snatches may cause permanent damage.
The ultimate overload capability before breakage is 300%, bearing damage may occur before this.
4.1 High Output Signal With No Tension
[1] Check for correct wiring to the transducer.
[2] Check cables and connectors for good continuity with an ohm meter, do NOT use a 'megger'.
[3] The transducer may have too low a MWF, replace with a higher MWF transducer or reduce the
web wrap angle.
[4] The transducer excitation voltage may be too high - this will cause permanent damage and may
invalidate the warranty.
[5] There may be a high degree of misalignment of the transducers causing a severe pre-load.
[6] The sensing roller weight may be too heavy, this should not exceed the MWF of the transducer.

_____________________________________________________________________________________________________________________
Absolute Measurement Ltd. (T/A CMC Controls)
t: (0) 1732 763278 | e: sales@absolutemeasurement.co.uk | w: absolutemeasurement.co.uk
Unit 19 | Silver Birches Business Park | Aston Road | Bromsgrove | B60 3EU
7
Transducer Instruction Manual
Range: Advance
Type: ACDF –3
Revision: V1.0
4.2 Low Output Signal With Maximum Tension
[1] Check for correct wiring to the transducer.
[2] Check cables and connectors for good continuity with an ohm meter, do NOT use a 'megger'.
[3] The transducer may have too high a MWF, replace with a lower MWF transducer or increase the
web wrap angle.
[4] The transducer excitation voltage may be too low.
4.3 Wrong Polarity of Output Signal
[1] Check that the web path is correct.
[2] The transducer may be incorrectly orientated, rotate 180to correct this. If rotation is not possible,
interchange the transducer excitation supply or output signal leads at the indicator or controller
terminals.
4.4 Output Signal Not Linear, Zero Shifts During Operation
[1] Check that there is no dirt or foreign matter interfering with the transducer mounting and that the
mounting hole diameter in the machine frame is correct.
[2] Check that the four fixing bolts are secure.
[3] Check that the bearing is completely free to rotate and align.
[4] Check that one end of the tension sensing roller is free to float axially in the transducer bearing.
4.5 Transducer Strain Gauge Resistance
The transducer has four foil strain gauges in a Wheatstone bridge. The nominal resistance is 350 ohms.
Table of contents
Popular Range manuals by other brands
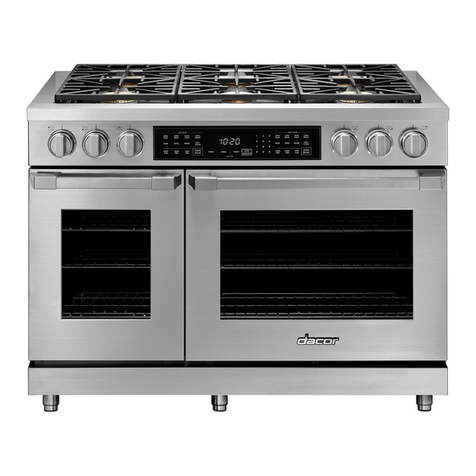
Dacor
Dacor Epicure ERD36 Planning guide
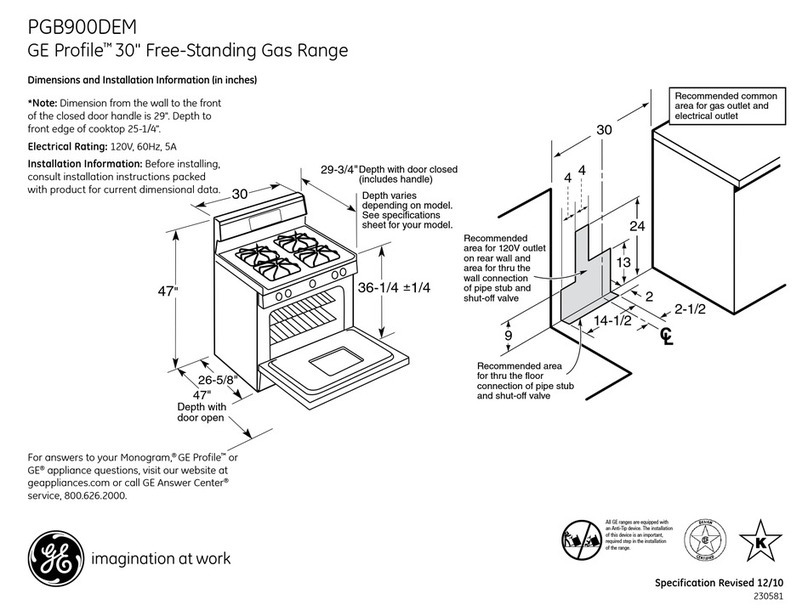
GE
GE PGB900DEMWW - Profile 30 in. Gas Ran Dimensions and installation information
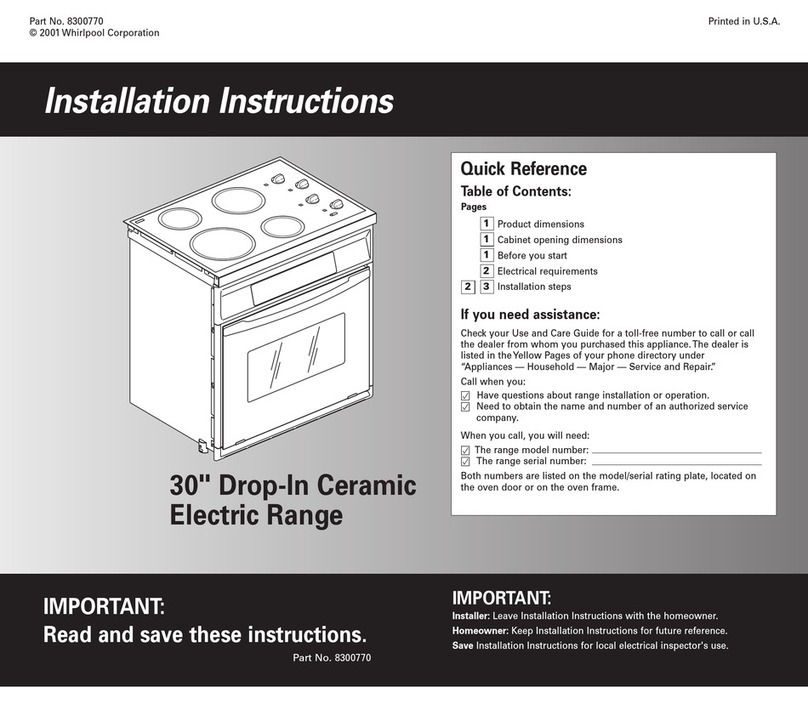
Whirlpool
Whirlpool 8300770 installation instructions
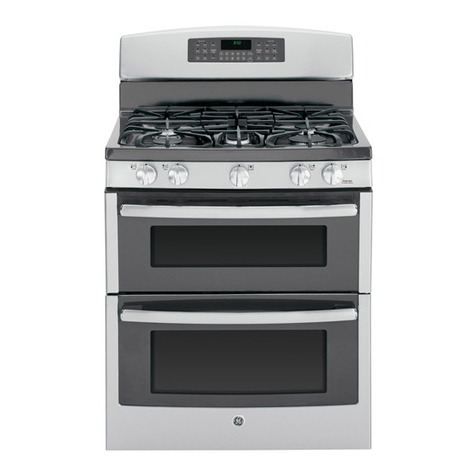
GE
GE JGB850SEFSS owner's manual
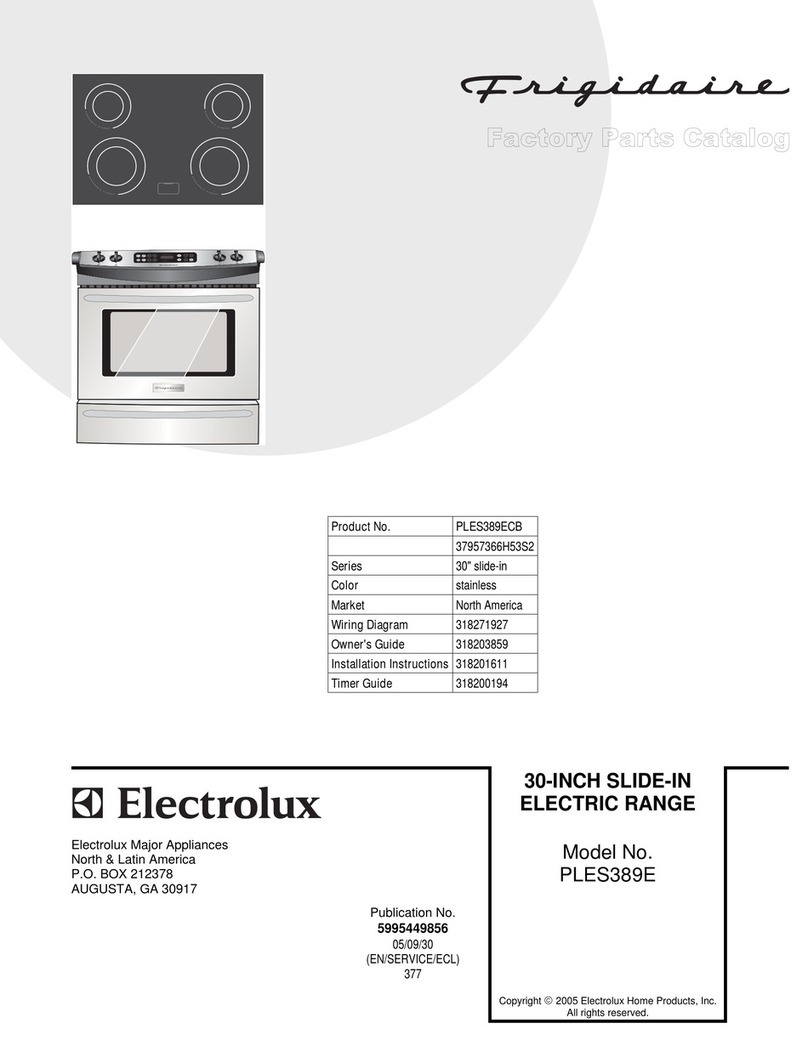
Frigidaire
Frigidaire PLES389E Factory parts catalog

Frigidaire
Frigidaire CFGS379DC2 installation instructions

Kenmore
Kenmore 790.7802 Series Use & care guide

Bartscher
Bartscher SNACK 115157 Instructions for installation, operation and maintenance
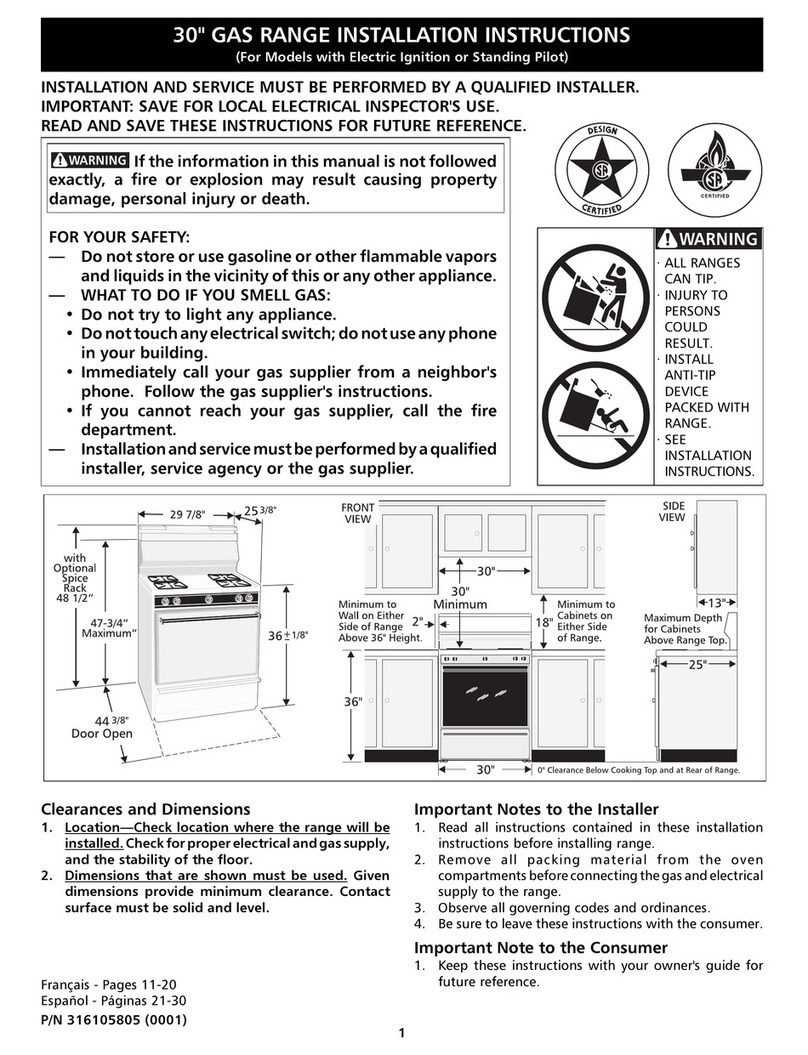
Frigidaire
Frigidaire FGF345BHWC installation instructions

LG
LG LRG30855ST user guide

Frigidaire
Frigidaire CGEF3055MW Use & care manual

Heartland
Heartland 6210 48" Installation and operating instructions