Baileigh Industrial EW-30 User manual

OPERATOR’S MANUAL
ENGLISH WHEEL
MODEL: EW-30 (B8870)
© 2016 Baileigh Industrial, Inc.
Rev. 12/2016

Table of Contents
INTRODUCTION............................................................................................................. 1
GENERAL NOTES.......................................................................................................... 1
SAFETY INSTRUCTIONS .............................................................................................. 2
SAFETY PRECAUTIONS ............................................................................................... 4
Dear Valued Customer:................................................................................................... 4
TECHNICAL SPECIFICATIONS ..................................................................................... 6
UNPACKING AND CHECKING CONTENTS.................................................................. 7
Cleaning ...................................................................................................................... 7
TRANSPORTING AND LIFTING .................................................................................... 8
INSTALLATION............................................................................................................... 9
Anchoring the Machine.............................................................................................. 10
GETTING TO KNOW YOUR MACHINE ....................................................................... 10
MATERIAL SELECTION............................................................................................... 11
OPERATION................................................................................................................. 11
ROLLING TIPS ............................................................................................................. 12
Selecting Lower Wheels ............................................................................................ 16
MACHINE ADJUSTMENTS .......................................................................................... 17
Wheel Replacement .................................................................................................. 17
LUBRICATION AND MAINTENANCE .......................................................................... 18
TROUBLESHOOTING .................................................................................................. 18
FRAME ASSEMBLY ..................................................................................................... 19
WHEEL ASSEMBLY ..................................................................................................... 20
ADJUSTER ASSEMBLY............................................................................................... 21
Parts List ................................................................................................................... 22

1
1
INTRODUCTION
The quality and reliability of the components assembled on a Baileigh Industrial machine
guarantee near perfect functioning, free from problems, even under the most demanding working
conditions. However if a situation arises, refer to the manual first. If a solution cannot be found,
contact the distributor where you purchased our product. Make sure you have the serial number
and production year of the machine (stamped on the nameplate). For replacement parts refer to
the assembly numbers on the parts list drawings.
Our technical staff will do their best to help you get your machine back in working order.
In this manual you will find: (when applicable)
•Safety procedures
•Correct installation guidelines
•Description of the functional parts of the machine
•Capacity charts
•Set-up and start-up instructions
•Machine operation
•Scheduled maintenance
•Parts lists
GENERAL NOTES
After receiving your equipment remove the protective container. Do a complete visual
inspection, and if damage is noted, photograph it for insurance claims and contact your
carrier at once, requesting inspection. Also contact your distributor and inform them of the
unexpected occurrence. Temporarily suspend installation.
Take necessary precautions while loading / unloading or moving the machine to avoid any
injuries.
Your machine is designed and manufactured to work smoothly and efficiently. Following proper
maintenance instructions will help ensure this. Try and use original spare parts, whenever
possible, and most importantly; DO NOT overload the machine or make any unauthorized
modifications.

2
2
Note: This symbol refers to useful information throughout the manual.
LEARN TO RECOGNIZE SAFETY INFORMATION
This is the safety alert symbol. When you see this symbol on
your machine or in this manual, BE ALERT TO THE
POTENTIAL FOR PERSONAL INJURY!
Follow recommended precautions and safe operating
practices.
UNDERSTAND SIGNAL WORDS
A signal word – DANGER, WARNING, or CAUTION
is used with the safety alert symbol. DANGER
identifies a hazard or unsafe practice that will result in
severe Injury or Death.
Safety signs with signal word DANGER or WARNING are
typically near specific hazards.
General precautions are listed on CAUTION safety signs.
CAUTION also calls attention to safety messages in this
manual.
IMPORTANT
PLEASE READ THIS OPERATORS MANUAL CAREFULLY
It contains important safety information, instructions, and necessary operating
procedures. The continual observance of these procedures will help increase your
production and extend the life of the equipment.
SAFETY INSTRUCTIONS

3
3
SAVE THESE INSTRUCTIONS.
Refer to them often and use them to instruct others.
PROTECT EYES
Wear safety glasses or suitable eye protection
when working on or around machinery.
PROTECT AGAINST NOISE
Prolonged exposure to loud noise can cause impairment or loss of
hearing. Wear suitable hearing protective devices such as ear muffs or
earplugs to protect against objectionable or uncomfortable loud noises.
BEWARE OF CRUSH HAZARD
NEVER place your hands, fingers, or any part of your body in the die
area of this machine.
BEWARE OF PINCH POINTS
Keep hands and fingers away from the rolls when the machine is in
operation.
ENTANGLEMENT HAZARD – ROTATING SPINDLE
Contain long hair, DO NOT wear jewelry or loose fitting clothing.

4
4
SAFETY PRECAUTIONS
Metal working can be dangerous if safe and proper operating procedures are not followed. As
with all machinery, there are certain hazards involved with the operation of the product. Using
the machine with respect and caution will considerably lessen the possibility of personal injury.
However, if normal safety precautions are overlooked or ignored, personal injury to the operator
may result.
Safety equipment such as guards, hold-downs, safety glasses, dust masks and hearing
protection can reduce your potential for injury. But even the best guard won’t make up for poor
judgment, carelessness or inattention. Always use common sense and exercise caution in
the workshop. If a procedure feels dangerous, don’t try it.
REMEMBER: Your personal safety is your responsibility.
Dear Valued Customer:
•All Baileigh machines should be used only for their intended use.
•Baileigh does not recommend or endorse making any modifications or alterations to a
Baileigh machine. Modifications or alterations to a machine may pose a substantial risk of
injury to the operator or others and may do substantial damage to the machine.
•Any modifications or alterations to a Baileigh machine will invalidate the machine's warranty.
PLEASE ENJOY YOUR BAILEIGH MACHINE!....PLEASE ENJOY IT SAFELY!
1. FOR YOUR OWN SAFETY, READ INSTRUCTION MANUAL BEFORE OPERATING THE
MACHINE. Learn the machine’s application and limitations as well as the specific hazards.
2. Only trained and qualified personnel can operate this machine.
3. Make sure guards are in place and in proper working order before operating
machinery.
4. Remove any adjusting tools. Before operating the machine, make sure any adjusting tools
have been removed.
5. Keep work area clean. Cluttered areas invite injuries.
6. Overloading machine. By overloading the machine you may cause injury from flying parts.
DO NOT exceed the specified machine capacities.
WARNING: FAILURE TO FOLLOW THESE RULES MAY RESULT IN
SERIOUS PERSONAL INJURY

5
5
7. Dressing material edges. Always chamfer and deburr all sharp edges.
8. Do not force tool. Your machine will do a better and safer job if used as intended. DO NOT
use inappropriate attachments in an attempt to exceed the machines rated capacity.
9. Use the right tool for the job. DO NOT attempt to force a small tool or attachment to do the
work of a large industrial tool. DO NOT use a tool for a purpose for which it was not
intended.
10.Dress appropriate. DO NOT wear loose fitting clothing or jewelry as they can be caught in
moving machine parts. Protective clothing and steel toe shoes are recommended when
using machinery. Wear a restrictive hair covering to contain long hair.
11.Use eye and ear protection. Always wear ISO approved impact safety goggles. Wear a full-
face shield if you are producing metal filings.
12.Do not overreach. Maintain proper footing and balance at all times. DO NOT reach over or
across a running machine.
13.Stay alert. Watch what you are doing and use common sense. DO NOT operate any tool or
machine when you are tired.
14.Check for damaged parts. Before using any tool or machine, carefully check any part that
appears damaged. Check for alignment and binding of moving parts that may affect proper
machine operation.
15.Observe work area conditions. DO NOT use machines or power tools in damp or wet
locations. Do not expose to rain. Keep work area well lighted.
16.Keep children away. Children must never be allowed in the work area. DO NOT let them
handle machines, tools, or extension cords.
17.Store idle equipment. When not in use, tools must be stored in a dry location to inhibit rust.
Always lock up tools and keep them out of reach of children.
18.DO NOT operate machine if under the influence of alcohol or drugs. Read warning
labels on prescriptions. If there is any doubt, DO NOT operate the machine.
19.Keep visitors a safe distance from the work area.

6
6
TECHNICAL SPECIFICATIONS
Mild Steel Capacity
14ga. (1.897mm)
Aluminum Capacity (Soft)
.125” (3.175mm)
Throat Depth
30" (762mm)
Top Wheel Dimensions
10" x 3” (254 x 76.2mm)
Lower Die Edge Radius
Flat, 36”, 24”, 12”, 8”, 6”, 4”, and 2”
(Flat, 914, 610, 305, 203, 152, 102, and 51mm)
Power
Manual
Shipping Dimensions
48" x 48" x 84" (1220 x 1220 x 2134mm)
Shipping Weight
900lbs. (409kg)
Note: The photos and illustrations used in this manual are representative only and
may not depict the actual color, labeling or accessories and may be intended to illustrate
technique only.
Note: The specifications and dimensions presented here are subject to change
without prior notice due to improvements of our products.

7
7
UNPACKING AND CHECKING CONTENTS
Your Baileigh machine is shipped complete in one crate. Separate all parts from the packing
material and check each item carefully. Make certain all items are accounted for before
discarding any packing material.
Cleaning
Your machine may be shipped with a rustproof waxy coating and/or grease on the exposed
unpainted metal surfaces. Fully and completely remove this protective coating using a
degreaser or solvent cleaner. Moving items will need to be moved along their travel path to
allow for cleaning the entire surface. For a more thorough cleaning, some parts will occasionally
have to be removed. DO NOT USE acetone or brake cleaner as they may damage painted
surfaces.
Follow manufacturer’s label instructions when using any type of cleaning product. After cleaning,
wipe unpainted metal surfaces with a light coating of quality oil or grease for protection.
Important: This waxy coating is NOT a lubricant and will cause the machine to
stick and lose performance as the coating continues to dry
WARNING:
SUFFOCATION HAZARD! Immediately discard any plastic
bags and packing materials to eliminate choking and suffocation hazards to children
and animals.
If any parts are missing, do not plug in the power cable, or turn the power switch on
until the missing parts are obtained and installed correctly.
WARNING: DO NOT USE gasoline or other petroleum products to clean
the machine. They have low flash points and can explode or cause fire.
CAUTION: When using cleaning solvents work in a well-ventilated area.
Many cleaning solvents are toxic if inhaled.
GAS

8
8
TRANSPORTING AND LIFTING
IMPORTANT: Lifting and carrying operations should be carried out by skilled workers,
such as a truck operator, crane operator, etc. If a crane is used to lift the machine, attach the
lifting chain carefully, making sure the machine is well balanced.
Follow these guidelines when lifting with truck or trolley:
•The lift truck must be able to lift at least 1.5 – 2 times the machines gross weight.
•Make sure the machine is balanced. While transporting, avoid rough or jerky motion, and
maintain a safe clearance zone around the transport area.
•Use a fork lift with sufficient lifting capacity and forks that are long enough to reach the
complete width of the machine.
•Remove the securing bolts that attach the machine to the pallet.
•Approaching the machine from the side, lift the machine on the frame taking care that there
are no cables or pipes in the area of the forks.
•Move the machine to the required position and lower gently to the floor.
•Level the machine so that all the supporting feet are taking the weight of the machine and no
rocking is taking place.
Follow these guidelines when lifting crane or hoist:
•Always lift and carry the machine with the lifting holes provided at the top of the machine.
•Use lift equipment such as straps, chains, capable of lifting 1.5 to 2 times the weight of the
machine.
•Take proper precautions for handling and lifting.
•Check if the load is properly balanced by lifting it an inch or two.
•Lift the machine, avoiding sudden accelerations or quick changes of direction.
•Locate the machine where it is to be installed, and lower slowly until it touches the floor.

9
9
INSTALLATION
IMPORTANT:
Consider the following when looking for a suitable location to place the machine:
•Overall weight of the machine.
•Weight of material being processed.
•Sizes of material to be processed through the machine.
•Space needed for auxiliary stands, work tables, or other machinery.
•Clearance from walls and other obstacles.
•Maintain an adequate working area around the machine for safety.
•Have the work area well illuminated with proper lighting.
•Keep the floor free of oil and make sure it is not slippery.
•Remove scrap and waste materials regularly, and make sure the work area is free from
obstructing objects.
•If long lengths of material are to be fed into the machine, make sure that they will not extend
into any aisles.
•LEVELING: The machine should be sited on a level, concrete floor. Provisions for securing it
should be in position prior to placing the machine. The accuracy of any machine depends on
the precise placement of it to the mounting surface.
•FLOOR: This tool distributes a large amount of weight over a small area. Make certain that
the floor is capable of supporting the weight of the machine, work stock, and the operator.
The floor should also be a level surface. If the unit wobbles or rocks once in place, be sure to
eliminate by using shims.
•WORKING CLEARANCES: Take into consideration the size of the material to be
processed. Make sure that you allow enough space for you to operate the machine freely.

10
10
Anchoring the Machine
•Once positioned, anchor the machine to the floor, as shown in
the diagram. Use bolts and expansion plugs or sunken tie rods
that connect through and are sized for the holes in the base of
the stand.
•This machine requires a solid floor such as concrete at a
minimum of 4” (102mm) thick. 6” (153mm) minimum is preferred.
GETTING TO KNOW YOUR MACHINE
The English wheel stretches metal
workpieces thinner and longer as
they are rolled between the upper
wheel and lower wheel.
Simultaneously, a track is pressed
into the metal, creating a convex
curve in the workpiece. By varying
the amount and pattern of the
tracks, a wide variety of contours
can be produced.
The English wheel can be used to
produce curves in mild steel up to
10ga. (3.416mm) and aluminum up
to .125” (3.175mm).
Note: Stock photo.
Item
Description
A
Kick Wheel
B
Lower Wheel Assembly
C
Quick Release Lever
D
Lower Wheel Bracket
A
B
C
G
K
H
F
D
I
E
J
L
.31"
(7.87mm)
.50"
(12.7mm)

11
11
E
Lower Wheel Axle
F
Lower Wheel
G
Upper Wheel
H
Upper Axle Latch
I
Upper Wheel Axle
J
Upper Wheel Bracket
K
Frame
L
Mounting Plates
Wheel Storage Bracket (Opposite side)
MATERIAL SELECTION
When selecting materials keep these instructions in mind:
•Material must be clean and dry. (without oil)
•Material should have a smooth surface so it processes easily.
•Dimensional properties of material must be consistent and not exceed the machine capacity
values.
•Chemical structure of material must be consistent.
•Buy certificated steel from the same vendor when possible.
OPERATION
1. Clean the workpiece and wheels thoroughly, making sure any abrasive particles are
removed. Grit or dirt will mar your workpiece and even damage the wheels.
2. Dull sharp edges with a deburring tool arid put on a pair of leather gloves to prevent Injury to
your hands.
CAUTION: It must be determined by the customer that materials being
processed through the machine are NOT
potentially hazardous to operator or
personnel working nearby.
CAUTION: Always wear proper eye protection with side shields, safety
footwear, and leather gloves to protect from burrs and sharp edges.
Keep hands and fingers clear of the rollers.
When handling large heavy sheets make sure they are properly supported.

12
12
3. Turn the upper wheel knob clockwise to raise the upper wheel bracket against the frame
bracket.
Note: Make sure the upper wheel bracket and frame bracket edges are parallel so
they slide past each other when raising the upper wheel bracket. If not, they may bind.
4. Check the distance between the bottom of the upper wheel and top of the lower wheel.
They should be about an inch apart. To adjust the distance, rotate the kick wheel to lower or
raise the lower wheel.
5. Engage the quick release lever to raise the lower wheel to the operating position. The button
head cap screw on the cam should rest against the bottom of the lower wheel bracket.
6. Insert the workpiece between the wheels.
7. Rotate the kick wheel counterclockwise until there is light pressure on the workpiece.
8. Roll the workpiece up to an edge, rotate it slightly, then pull it back.
9. Turn the kick wheel counterclockwise to increase pressure on the workpiece; turn the kick
wheel clockwise to decrease pressure.
To reinsert a workpiece or insert another workpiece of the same thickness, use the quick
release lever.
ROLLING TIPS
PRACTICE AND PATIENCE. An English wheel is a simple tool that is easy to start to use
however, it is the type of tool that requires experience to master.
When an operator keeps in mind a few safety considerations as noted in the front of the manual
they can create and form metal to almost any shape.
They can use the following tips to learn to operate the English wheel more successfully:
•Clean the workpiece and wheels; making sure all grit is removed.
•Start rolling slowly and increase your speed.
•Try rolling the wheels up to, but not past the workpiece edge.
CAUTION: Always wear proper eye protection with side shields, safety
footwear, and leather gloves to protect from burrs and sharp edges.
Keep hands and fingers clear of the rollers.
When handling large heavy sheets make sure they are properly supported.

13
13
•Mark the workpiece with a non-permanent marker to make it easier to follow tracking
patterns or contour the metal.
•Try using the lightest wheel pressure possible to shape the workpiece. Too much pressure
will crease or ruin the metal.
•Light pressure is best for smoothing; higher pressure is best for rough shaping.
•Consistent patterns and movements generally return consistent results.
Tracking Patterns
As metal passes between the upper and lower wheels, a "track" or shiny line is pressed into the
metal. Various tracking patterns can be used to shape workpieces depending upon their shape
or size.
Zigzag Pattern
This pattern uses closely-spaced tracks to move from
one end of the material to the other. It can be used for
a variety of workpiece shapes.
1. Insert the workpiece between the wheels at point A,
and start rolling it along the edge. Left edge shown.
2. Push the workpiece forward to the stop point.
3. Turn the workpiece counterclockwise slightly.
4. Pull the workpiece back until it reaches the next
point near the far edge.
5. Turn the workpiece clockwise slightly.
6. Continue feeding the workpiece to the other side in
the same manner, following the pattern as shown.
Note: Try keeping the tracks close to
each other.

14
14
7. When the wheels reach point B, feed the workpiece in the opposite direction and return to
point A.
Star Pattern
The star pattern is useful for shaping round
workpieces.
Note: Avoid rolling directly over the
center of the workpiece, as too many passes could
overstretch the metal.

15
15
Staggered Stop Pattern
With this pattern, the track alternates randomly
between three different sets of lines.
Note: Marking the workpiece with a non-
permanent marker so you can see the outside, middle
and inside lines more clearly. Clean the wheels and
workpiece when you are finished.
1. From the starting point, roll the workpiece from the
outside line on one side to the outside line on the
opposite side.
2. Roll the workpiece from the middle line on one side
to the middle line on the opposite side.
3. Roll the workpiece from the inside line on one side
to the inside line on the opposite side.
4. Repeat Steps 1-3, as you move across the
workpiece, randomly alternating between outside,
middle, and inside lines.
Crisscrossing Tracks
Crisscrossing tracks can help produce smoother curves
in your workpiece using the zigzag or staggered stop
pattern.
After running tracks along one length of the workpiece,
turn the metal sheet 90° and run tracks along the
opposite length so the workpiece is equally covered by
both sets of tracks.

16
16
Selecting Lower Wheels
Choose a lower wheel that will produce the contour you desire.
Flat lower wheels are good for adding gentle curves to large metal panels; these wheels have
wide flat surfaces profiles
Domed lower wheels create tighter curves. The flat areas range from 1/8” to 3/4" (3.175 to
19.05mm). The wider the flat area, the wider the track produced on the workpiece.
Roll a workpiece between a grooved lower wheel and a ridged upper wheel to emboss metal.
The step roller can be used with the flat upper wheel to add a small crease in a metal panel.

17
17
MACHINE ADJUSTMENTS
Wheel Replacement
A flat upper and lower wheel are preinstalled on the English wheel. The lower wheel can be
replaced with any of the other lower wheel wheels.
Important: Hold an upper wheel securely when installing or removing it or it may
fall causing injury or damage! Wear steel toe foot-wear to protect your feet.
Upper Wheel Replacement
1. Raise the lower wheel until the top lightly touches the bottom of the upper wheel. This help to
supply some support to the upper wheel.
2. Remove the cotter pin from the inside of the upper wheel axle.
3. Hold the upper wheel firmly to prevent dropping and remove the upper wheel axle.
4. Carefully remove the upper wheel and set it on the upper wheel rack using a bracket
mounting shaft.
5. Place a different upper wheel into the upper wheel bracket.
Note: Adjust the lower wheel height as needed to allow the upper wheel to fit into
the upper wheel bracket.
6. Align the bracket and wheel bearing holes, insert the axle, and rotate the latch to secure the
wheel.
Lower Wheel Replacement
1. Use a wrench to disengage the quick release cam and lower the lower wheel bracket until it
stops.
2. Remove the lower wheel and replace it with another one.
3. Engage the quick release lever and raise the lower wheel to the operating position.

18
18
LUBRICATION AND MAINTENANCE
•Check daily for any unsafe conditions and fix immediately.
•Check that all nuts and bolts are properly tightened.
•On a weekly basis clean the machine and the area around it.
•Lubricate threaded components and sliding devices.
•Apply rust inhibitive lubricant to all non-painted surfaces.
Note: Proper maintenance can increase the life expectancy of your machine.
TROUBLESHOOTING
Symptom
Possible Cause
Possible Solution
Quick release lever will
not engage, or has
trouble engaging.
1. Lower wheel bracket and
cams bind.
2. Setscrews on cams loose and
not contacting quick release
lever flats.
1. Lubricate top of cams where
they contact the bracket
2. Align setscrews over lever flats
and tighten
Upper wheel swivels. 1.
Upper wheel is not secured by
frame bracket.
1. Turn upper wheel knob
clockwise to raise upper wheel
bracket so it is snug against frame
bracket.
Wheel does not shape
workpiece.
1. Workpiece is too thick.
2. Crown is too low.
3. Incorrect pressure.
1. Use sheet metal of appropriate
thickness.
2. Use a lower wheel with a higher
crown.
3. Increase pressure on workpiece.
Upper wheel bracket
will not seat against
frame.
1. Upper wheel bracket catches
on frame bracket; surfaces are
not parallel.
1. Align upper wheel and upper
frame bracket surfaces and raise
upper wheel bracket up to frame.
Wheels form too high a
crown in workpiece.
1. Using lower wheel with too
small a flat area.
1. Use a lower wheel with a larger
flat.
Wheels form too low a
crown in workpiece.
1. Lower wheel flat is too large.
1. Use a lower wheel with a smaller
flat area.
WARNING:Maintenance should be performed on a regular
basis by
qualified personnel.
Always follow proper safety precautions when working on or around any machinery.
This manual suits for next models
1
Table of contents
Other Baileigh Industrial Sander manuals

Baileigh Industrial
Baileigh Industrial OS-1414 User manual

Baileigh Industrial
Baileigh Industrial ES-6100 User manual

Baileigh Industrial
Baileigh Industrial DBG-106 User manual

Baileigh Industrial
Baileigh Industrial DM-10 User manual
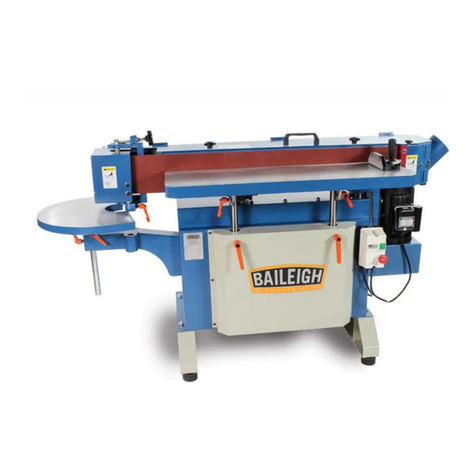
Baileigh Industrial
Baileigh Industrial ES-6108 User manual

Baileigh Industrial
Baileigh Industrial ES-9138 User manual
Popular Sander manuals by other brands

Shop fox
Shop fox W1689 instruction manual
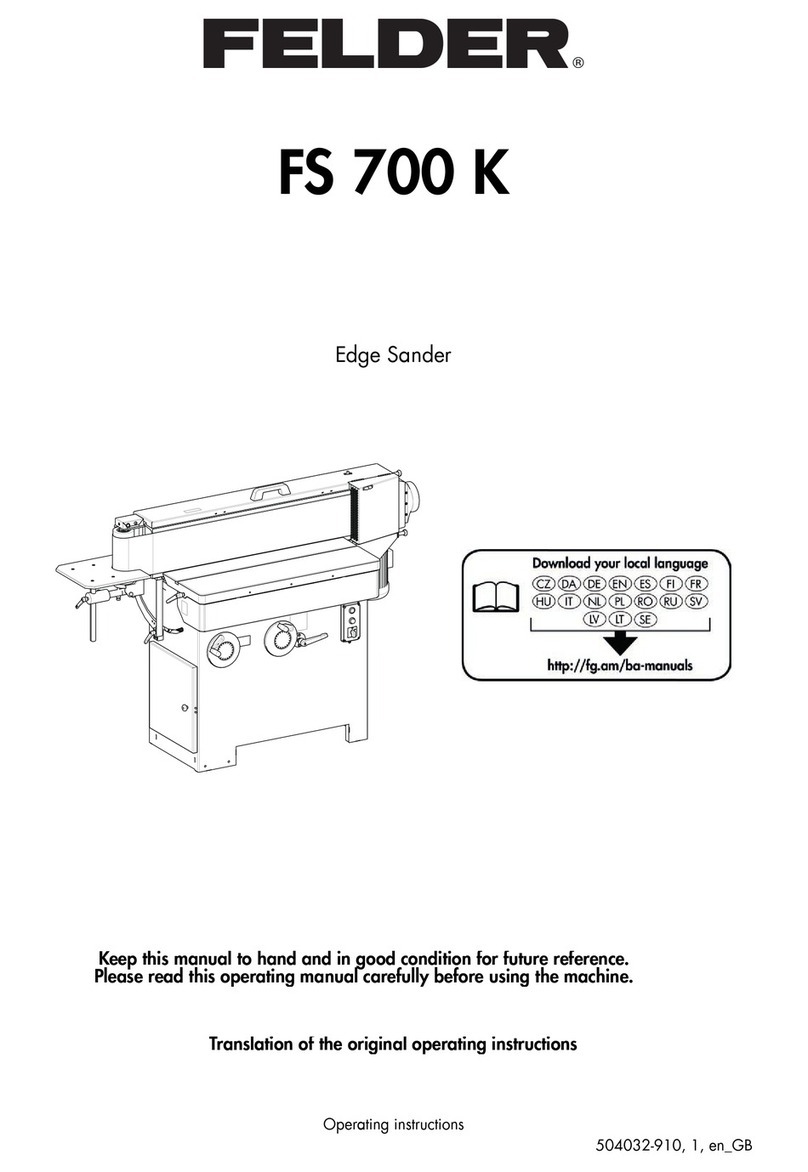
Felder
Felder FS 700 K Translation of the original operating instructions
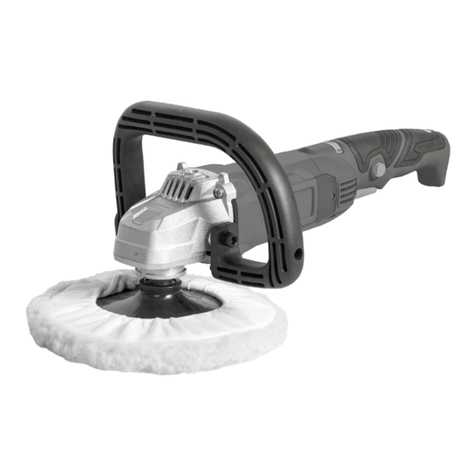
Bort
Bort 93728076 user manual
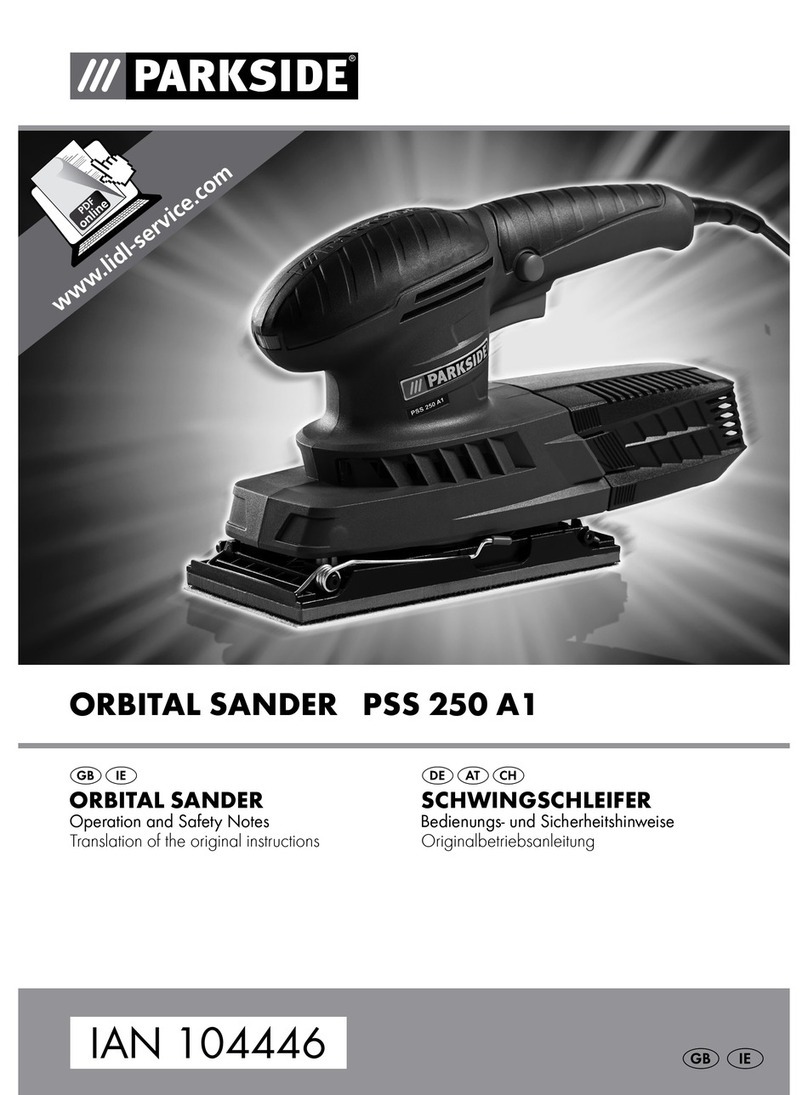
Parkside
Parkside PSS 250 A1 Operation and safety notes
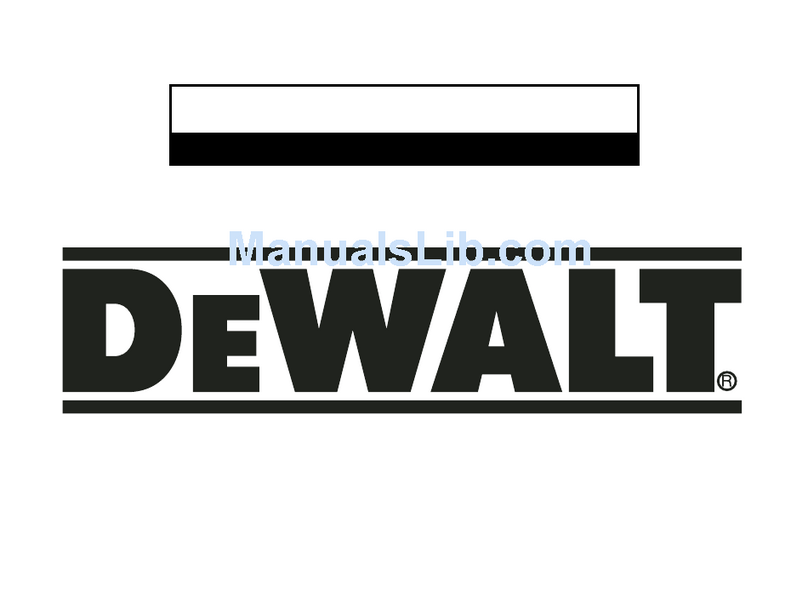
DeWalt
DeWalt DW441 instruction manual
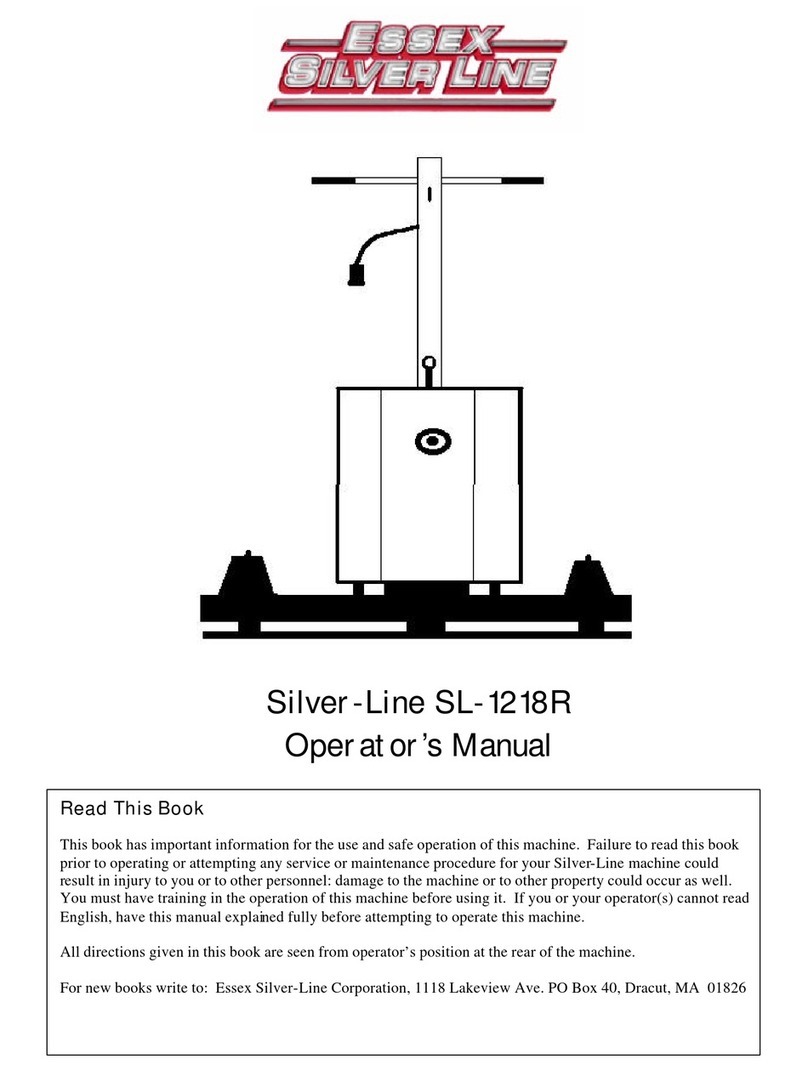
Essex Electronics
Essex Electronics Silver-Line SL-1218R Operator's manual