Bartington PA1 User manual

Operation Manual for
PA1 Power Amplifier
www.bartingtondefenceandspace.com www.bartingtondefenceandspace.com

BARTINGTON DEFENCE & SPACE
Page 2 of 19
OM3225/1
Table of Contents
1. About this Manual 3
1.1. Symbols Glossary 3
2. Safe Use 3
3. Introduction 4
3.1 PA1 Power Amplifier Features 5
3.1.1. PA1 Power Amplifier Front View 5
3.1.2. PA1 Power Amplifier Rear View 6
4. PA1 Power Amplifier Installation 7
4.1. Test Assembly Location and Ventilation Requirements 7
4.2. Connecting to the HCS1 System 7
4.3. Connecting to the HC1 or HC2 Helmholtz Coils 7
4.4. Connecting to the CU1 Control Unit 8
4.4.1. Pin-Outs 8
4.5. PA1 Power Amplifier Power 9
4.6. Amplifier O/P Circuit Breakers 9
4.7. Cooling 10
4.8. Static Field Compensation 10
4.8.1. Method 11
5. Coil Calibration and Alignment Adjustment 11
5.1. Calibration Process 12
5.1.1. X Trim, Y Trim & Z Trim 12
5.1.2. X Mon, Y Mon & Z Mon 12
5.1.3. Alignment trim 13
6. Air Intake Filter Cleaning and Replacement 14
7. Absolute Maximum Voltages and Ratings 15
8. Troubleshooting, Care and Maintenance 15
9. Storage and Transport 15
10. Disposal 15
10.1. Waste Electrical and Electronic Equipment (WEEE) Regulations 16
Appendix A: Connecting the Components of the HCS1 Helmholtz Coil System 17
Appendix B: Guidance for Connection to Mains Supply 18

BARTINGTON DEFENCE & SPACE
Page 3 of 19
OM3225/1
1. About this Manual
This manual provides the information necessary to help customers install and operate the PA1
Power Amplifier. The PA1 Power Amplifier is one component of Bartington Defence & Space’
One, Two or Three-Axis Helmholtz Coil Control System. This manual should therefore be read in
conjunction with:
• OM3226 HC1 Helmholtz Coil or OM3342 HC2 Helmholtz Coil
• OM3224 CU1 Control Unit.
Both are available via the Helmholtz Coil System product page at www.
bartingtondefenceandspace.com.
This manual should also be read in conjunction with the product brochure (DS2613) and outline
drawings which can also be found on the product page.
Photographs of key components are included, labelled with numbers. A number in the text in
square brackets [ ] refers to that label.
Bartington Defence & Space cannot advise on the integration of this equipment with any third
party products.
1.1. Symbols Glossary
The following symbols used within this manual call your attention to specific types of
information:
WARNING: Indicates a situation in which serious bodily injury or death could result if the
warning is ignored.
Caution: Indicates a situation in which bodily injury or damage to your instrument, or both,
could result if the caution is ignored.
Identifies items that must be disposed of safely to prevent unnecessary damage to the
environment.
Note: A paragraph in this format provides useful supporting information on how to make
better use of your purchase.
2. Safe Use
WARNING: The PA1 Power Amplifier is powered by mains electricity and contains
uninsulated parts. Ensure that the unit is properly earthed at all times. Do not open the
casing or have contact with any internal parts except where following a procedure precisely

BARTINGTON DEFENCE & SPACE
Page 4 of 19
OM3225/1
as described in this manual. Safety protection will be impaired if the unit is used in a
manner not specified in this manual.
WARNING: The electromagnetic field from this product may interfere with the operation
of pacemakers and other medical devices. Consult your device’s manufacturer before
operation.
WARNING: These products are not qualified for use in explosive atmospheres or life
support systems. Consult Bartington Defence & Space for advice.
WARNING: Personal injury may result from lifting the PA1 Power Amplifier. Use more than
one person to move this device. It should be carried by each of the four lower corners.
CAUTION: When operated at full power for extended periods of time, thermal cut-out may
be activated to protect the equipment from overheating. Should this occurs, the power
will to the PA1 will be cut. In such event, it is advised to allow the unit to cool down before
restarting it. To prevent the thermal cut-out from activating, the equipment should be used
in a cooled temperature controlled environment (refer to Cooling)
3. Introduction
The PA1 Power Amplifier is the power amplifier for the HCS1 Helmholtz Coil Control System. The
full HCS system consists of:
• HC1 or HC2 Helmholtz Coils: an assembly of up to three Helmholtz coils. See OM3226 (HC1)
or OM3342 (HC2).
• PA1 Power Amplifier.
• CU1 Control Unit: the control unit for the system which enables it to interface with a PC-
based test, measurement and control system. See OM3224.
A diagram showing the connection of these separate items into one system is given in Appendix
A.
The PA1 Power Amplifier is available in a number of variants to match the coil assembly it is
being used with:
• PA1-1X, PA-1Y, and PA1-1Z Single Axis versions
• PA1-2XY, PA1-2YZ, and PA1-2XZ Two Axes versions
• PA1-3 Three Axes version

BARTINGTON DEFENCE & SPACE
Page 5 of 19
OM3225/1
Key
1. Upper front panel
2. Current control input (takes input from signal generator)
3. Calibration controls, behind transparent plastic cover
4. Current monitor output
5. Static field offset controls
6. Fastening screws
7. Rocker switch
8. Lower front panel
9. Centre front panel (grille)
10. Amplifier O/P circuit breakers
51
8 79
2 4
6
6
3
10
51
8 79
2 4
6
6
3

BARTINGTON DEFENCE & SPACE
Page 6 of 19
OM3225/1
Key
11. Blank ventilation panel
12. Fastening screws
13. Coil drive output to the HC1 or HC2 Helmholtz Coils
14. Lower rear panel
15. Circuit breaker
16. Mains power input socket
14
11
16 13
15
12
12

BARTINGTON DEFENCE & SPACE
Page 7 of 19
OM3225/1
The PA1 amplifier must be positioned such that the front, sides and rear ventilation panels
are not obstructed to allow free movement of cooling air. The CU1 has no forced ventilation
requirements and can be sited close to the PA1.
Note: The HCS1 coil system should be positioned around 3m away from the amplifier to
reduce noise pick up from the amplifier.
Note: For optimum results the ambient temperature should not exceed the maximum
specified in the data sheet DS2613.
4.2. Connecting to the HCS1 System
The PA1 Power Amplifier connects to the HC1 or HC2 Helmholtz Coils and the CU1 Control Unit.
The HC1 or HC2 Helmholtz Coil connection to the PA1 Power Amplifier is to power the coils only.
See Connecting to the CU1 Control Unit for connecting to the CU1 Control Unit.
4.3. Connecting to the HC1 or HC2 Helmholtz Coils
The HC1 or HC2 Helmholtz Coils are fitted with a cable with a plug for connection to the PA1
Power Amplifier.
The PA1 Power Amplifier and the HC1 or HC2 must be connected before the amplifier power is
turned on. The supplied cable is plugged into the coil drive output socket on the rear of the PA1
Power Amplifier [13].
13

BARTINGTON DEFENCE & SPACE
Page 8 of 19
OM3225/1
Caution: The coil drive output socket is reserved for the cable connecting the HC1 or HC2
and the PA1 Power Amplifier. No other connection should be made to this socket.
Note: The amplifier and any other control or measuring equipment must be at least 3m
away from the coil assembly.
Note: The PA1 Power Amplifier varies for Helmholtz Coils with different numbers of axes.
One, two, and three axis PA1 versions are available. If an HC1 has a greater number of axes
than the PA1 then only the number of axes corresponding to the PA1 can be used.
4.4. Connecting to the CU1 Control Unit
The PA1 Power Amplifier is connected to the CU1 Control Unit via the current control input [2].
The current monitor output [4], located on the upper front panel of the PA1 Power Amplifier, is
also connected to the CU1.
Note: A diagram showing the interconnection of components of the HCS1 System is given
in Appendix A.
In order to achieve a good noise rejection, the input and current monitor output are differential/
balanced signals. Single ended/unbalanced sources may be used by connecting the input
negative signals to the source ground. The output may be connected to a single-ended input by
using the positive signal and leaving the negative output disconnected; however the output signal
will be reduced to half the specified value.
WARNING: Do not connect either positive or negative outputs to ground.
4.4.1. Pin-Outs
Pin-out information for the current control input and the current monitor output can be found on
the PA1 Outline Drawing DR3047 available from the product page on our website.
4
2

BARTINGTON DEFENCE & SPACE
Page 9 of 19
OM3225/1
Details of suitable power supply for the PA1 Power Amplifier are provided in the product
brochure, with the supply beeing earthed/grounded. The supply from a standard wall outlet
should be suitable in most countries. A compatible mains cable supplied with a UK 13A
connector, an EU connector or bare ends can be specified at the time of ordering.
A 16A circuit breaker is situated on the rear panel [15] which is suitable for the supply stated in
the product brochure. Contact Bartington Defence & Space for advice if a lower voltage is to be
used.
Each amplifier o/p is fitted with a resettable 20A circuit breaker [10], which protects both the
amplifiers and the coil assembly in the event of a fault. The breakers are normally in the reset
position. If a breaker trips, it can be reset by pressing in the appropriate button on the front
panel. Repeated tripping may be an indication of a system fault.
15

BARTINGTON DEFENCE & SPACE
Page 10 of 19
OM3225/1
4.7. Cooling
The amplifier is fan-cooled so needs an unimpeded airflow from front to rear. A self-resetting
thermal shut-down mechanism will prevent damage through overheating.
Caution: If used on full power ensure that the equipment is placed in a cool, controlled
environment to prevent activation of the thermal cut-out.
Caution: The air filter in the front panel [9] should be inspected regularly, and cleaned or
replaced when necessary. See Air Intake Filter Cleaning and Replacement.
The static field is offset by introducing a DC offset into the amplifier input. Lockable controls for
static field offset [5] are available on the amplifier upper front panel to set this compensation.
The static field compensation should be set individually for each axis to obtain a minimum field
in the centre of the coil. This should be measured by a magnetometer placed in the coil centre.
Bartington Defence & Space can provide a suitable magnetometer.
9
5
17
18

BARTINGTON DEFENCE & SPACE
Page 11 of 19
OM3225/1
4.8.1. Method
The controls are locked by the outer hexagonal lock [17] which should be loosened with a
spanner. The compensation is adjusted by turning the central shaft [18] with a screwdriver.
A static field of below 100nT should be easily attained. The control should then be locked by
tightening down the outer hexagonal lock whilst holding the centre shaft with the screwdriver.
Once complete, recheck the offset of each axis.
Note: The compensation current will appear as part of the field current measured by the
field monitor. This adjustment should be checked regularly and will certainly need setting
on installation, or should the coil or metalwork in the vicinity of the coil be moved, or
should other sources of magnetic fields be introduced into the surroundings.
5. Coil Calibration and Alignment Adjustment
The calibration controls are mounted on the upper front panel of the PA1 Power Amplifier behind
a transparent cover [19]. To gain access to the controls, the cover must be carefully removed by
unscrewing the two screws. Adjustments are made with a small screwdriver.
Note: On PA1 Power Amplifiers intended for use with one or two axis Helmholtz coils,
either one or two axis controls will be missing from the front panel. In this case ignore
references to missing axes when reading this manual.
20 21 22
23
27
26
24
25
28
31
29
30
19

BARTINGTON DEFENCE & SPACE
Page 12 of 19
OM3225/1
The identities and functions of the calibration controls are as follows.
Image label Control label Function
[20] X Trim X axis gain adjust
[21] X->Y X axis alignment trim in Y axis
[22] X->Z X axis alignment trim in Z axis
[23] Y Trim Y axis gain adjust
[24] Y->X Y axis alignment trim in X axis
[25] Y->Z Y axis alignment trim in Z axis
[26] Z Trim Z axis gain adjust
[27] Z->X Z axis alignment trim in X axis
[28] Z->Y Z axis alignment trim in Y axis
[29] X Mon X axis current monitor gain adjust
[30] Y Mon Y axis current monitor gain adjust
[31] Z Mon Z axis current monitor gain adjust
5.1. Calibration Process
Calibration should be carried out using an AC signal, away from 50 or 60Hz and their harmonics,
and away from DC and slowly varying interferences. We use for example a 35Hz signal. The
use of a true RMS reading voltmeters will enable the user to measure only the AC component
of a signal. For HC1, a 1Vrms input signal on the PA1 will correspond to a 100μTrms field. The
output of the magnetometer may also be monitored on an oscilloscope to ensure that there is no
distortion of the waveform.
Note: In the event of a single or two axis Helmholtz Coil being used, discard calibration
instructions related to an axis that is not present on the system being used.
Note: Further information can be found in the detailed calibration document available on
request. Please contact Bartington Defence & Space.
5.1.1. X Trim, Y Trim & Z Trim
Feed a signal from the signal generator into each axis in turn. Adjust the axis gains until the
magnitude of the measured field matches the magnitude expected from the input signal level.
5.1.2. X Mon, Y Mon & Z Mon
Feed a signal from the signal generator into each axis in turn. Adjust the monitor gains until the
magnitude of the output matches the magnitude of the measured field.

BARTINGTON DEFENCE & SPACE
Page 13 of 19
OM3225/1
5.1.3. Alignment trim
In order to compensate for any small alignment inaccuracy in the test magnetometer, two
measurements are made, in each axis, with the magnetometer being rotated about the
measurement axis by 180 degrees and the average of the two voltages taken. When working with
an AC field, the axis alignment trim control is adjusted until the reading is the same each time
the test magnetometer is rotated about the axis being aligned.
X axis alignment trim in Y axis
Feed a signal from the signal generator into the X axis. Monitor the Y axis output of the
calibration magnetometer. Initially adjust the trim control until a minimum is obtained. Then
rotate the test magnetometer through 180° about the Y axis. If a signal is found then adjust the
trim control until the same level is observed when the magnetometer is in the normal position
and rotated position.
X axis alignment trim in Z axis
Feed a signal from the signal generator into the X axis. Monitor the Z axis output of the
calibration magnetometer. Initially adjust the trim control until a minimum is obtained. Then
rotate the test magnetometer through 180° about the Z axis. If a signal is found then adjust the
trim control until the same level is observed when the magnetometer is in the normal position
and rotated position.
Y axis alignment trim in X axis
Feed a signal from the signal generator into the Y axis. Monitor the X axis output of the
calibration magnetometer. Initially adjust the trim control until a minimum is obtained. Then
rotate the test magnetometer through 180° about the X axis. If a signal is found then adjust the
trim control until the same level is observed when the magnetometer is in the normal position
and rotated position.
Y axis alignment trim in Z axis
Feed a signal from the signal generator into the Y axis. Monitor the Z axis output of the
calibration magnetometer. Initially adjust the trim control until a minimum is obtained. Then
rotate the test magnetometer through 180° about the Z axis. If a signal is found then adjust the
trim control until the same level is observed when the magnetometer is in the normal position
and rotated position.
Z axis alignment trim in X axis
Feed a signal from the signal generator into the Z axis. Monitor the X axis output of the
calibration magnetometer. Initially adjust the trim control until a minimum is obtained. Then
rotate the test magnetometer through 180° about the X axis. If a signal is found then adjust the
trim control until the same level is observed when the magnetometer is in the normal position
and rotated position.

BARTINGTON DEFENCE & SPACE
Page 14 of 19
OM3225/1
Z axis alignment trim in Y axis
Feed a signal from the signal generator into the Z axis. Monitor the Y axis output of the
calibration magnetometer. Initially adjust the trim control until a minimum is obtained. Then
rotate the test magnetometer through 180° about the Y axis. If a signal is found then adjust the
trim control until the same level is observed when the magnetometer is in the normal position
and rotated position.
The air filter consists a 440x85mm (approx.) foam pad [32] fitted behind the centre front panel of
the PA1 Power Amplifier. It should be cleaned or replaced when necessary.
WARNING: Disconnect mains supply before removing filter panel. The earth bonding
connector can then be disconnected if required. Fan filter maintenance must be performed
by suitably trained personnel only.
Remove the power connector from the lower rear panel before removing the centre front panel.
The centre front panel can be removed by loosening the four large screws in the corners [33].
The filter may be cleaned by brushing off any dust from the front and blowing through from the
inside surface.
Caution: Air should be blown with a low pressure air line. Use appropriate personal
protective equipment (PPE).
Should the filter need replacing, the old filter can be removed by taking out the six screws [34]
holding the filter retaining bracket. Replace the filters with appropriate flame retardant filter
material (contact Bartington Defence & Space for details). Replace the filter retention bracket
and screws.
When filter maintenance is complete, replace the earth bonding wire connector (if disconnected),
before replacing the centre front panel.
33 33
32
34
34

BARTINGTON DEFENCE & SPACE
Page 15 of 19
OM3225/1
WARNING: Ensure the earth bonding wire is firmly re-attached to the panel before
refitting.
See the product brochure for the maximum voltages that may be applied to the PA1 Power
Amplifier control input, current monitor output and coil drive output
Refer to the product brochure for this product’s maximum environmental, electrical and
mechanical ratings.
Caution: Exceeding the maximum environmental ratings may cause irreparable damage to
the equipment.
Caution: If these voltages are exceeded, this may cause damage to the equipment.
Caution: Do not make any other connection to these ports.
8. Troubleshooting, Care and Maintenance
In the event of any apparent malfunction, email: service@bartingtondefenceandspace.com or
telephone the Bartington Defence & Space service team on: +44 (0)1993 706565.
9. Storage and Transport
The PA1 Power Amplifier is a precision electronic instrument and should be treated as such.
Bartington Defence & Space has supplied this product in appropriate packaging for
transportation. This packaging should be used for any future transport.
Due to the weight of the equipment it should be moved by at least two people and carried by each
of the four lower corners.
10. Disposal
This product should not be disposed of in domestic or municipal waste. For information about
disposing of this product safely, check local regulations for disposal of electrical / electronic products.

BARTINGTON DEFENCE & SPACE
Page 16 of 19
OM3225/1
This product complies fully with Restriction of the Use of Certain Hazardous Substances in
Electrical and Electronic Equipment (RoHS) and WEEE Regulations current at the time of
printing.

BARTINGTON DEFENCE & SPACE
Page 17 of 19
OM3225/1
Appendix A: Connecting the Components of the HCS1 Helmholtz Coil System
PXI CHASSIS
CU1
PA1
DAQ DAQ
Connector 0 Connector 1
Current
Control
Output
Aux
Input
Current
Monitor
Input
Device
Test
Input
Current
Control
Input
Current
Monitor
Output
DUT
Sensor
Optional
aux sensor
if required
HC1
Current
Output to
HC1/HC2

BARTINGTON DEFENCE & SPACE
Page 18 of 19
OM3225/1
1. Ensure that the mains feed is from a clean AC supply with the following characteristics:-
Voltage Range 100V to 240V AC
Frequency 50/60Hz
It is highly recommended that this mains feed is via an appropriate Residual Current Circuit
Breaker, rated at 30mA trip current. This must comply with local regulations.
2. The mains input connectors are as follows:-
Device Input Connector Mating Cable Connector
Power Amplifier PA1 IEC C20 IEC C19
Control Unit CU1 IEC C14 IEC C13
These cables are available in specific versions for most countries.
3. If an un-terminated IEC connector lead is supplied with the equipment, the wires must be
wired accordingly:-
BROWN LIVE
BLUE NEUTRAL
GREEN/YELLOW EARTH
4. It is essential that the control unit CU1 and the Power Amplifier PA1 are properly earthed at all
times.
5. It is recommended that the mains to each unit is supplied via an appropriate mains fuse:-
Power Amplifier PA1 13A
Control Unit CU1 13A
This is appropriate for the use over the whole supply voltage range.
6. This installation MUST be carried out by a trained, competent person.
7. Before initial switch-on, an appropriate earth bonding test should be performed to ensure a
robust earth connection.
8. To disconnect mains power, the mains supply cord must be removed from the rear panel
mains input connector.

Bartington Defence & Space Ltd
5, 8, 10, 11 & 12 Thorney Leys Business Park
Witney, Oxford, OX28 4GE. England
T: +44 1993 706565
F: +44 1993 774813
E: sales@bartingtondefenceandspace.com
W: www.bartingtondefenceandspace.com
www.bartingtondefenceandspace.com
OM3225/1
The copyright of this document is the property of Bartington Defence and Space Ltd.
Bartington® is a registered trade mark of Bartington Instruments Limited in the following
countries: United Kingdom, Australia, Brazil, Canada, China, European Union, India, Japan,
Norway and the United States of America.
Other manuals for PA1
1
Table of contents
Other Bartington Amplifier manuals
Popular Amplifier manuals by other brands
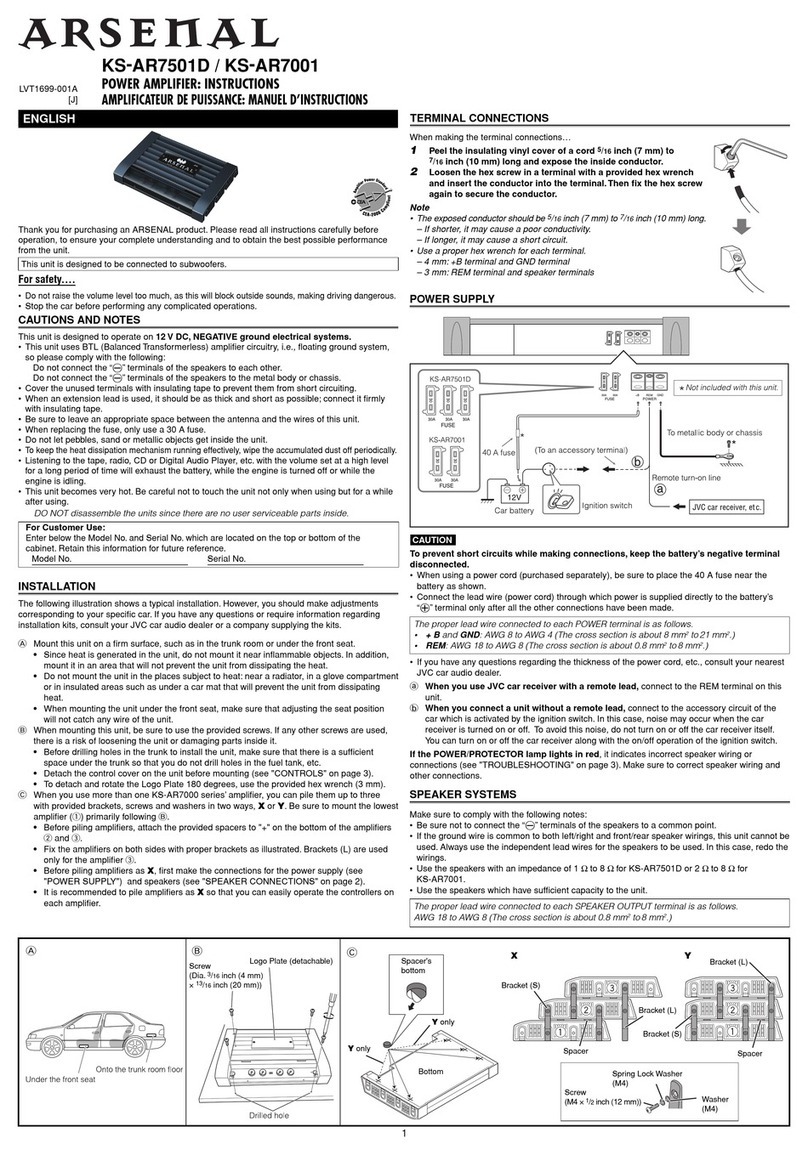
Arsenal
Arsenal KS-AR7501D - Class D Mono Amplifier 1200... instructions
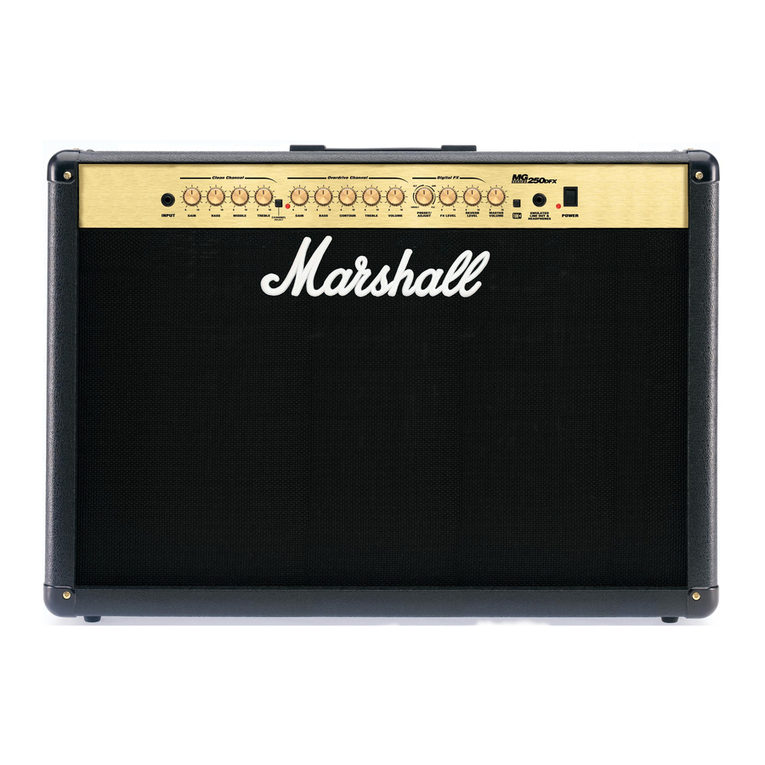
Marshall Amplification
Marshall Amplification MG250DFX owner's manual

Pure Resonance Audio
Pure Resonance Audio DA2240 Installation and operation manual
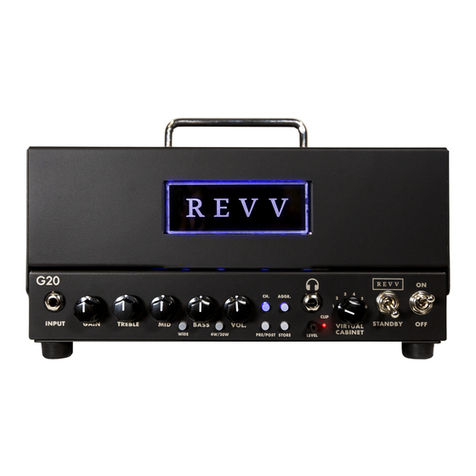
REVV
REVV G20 manual
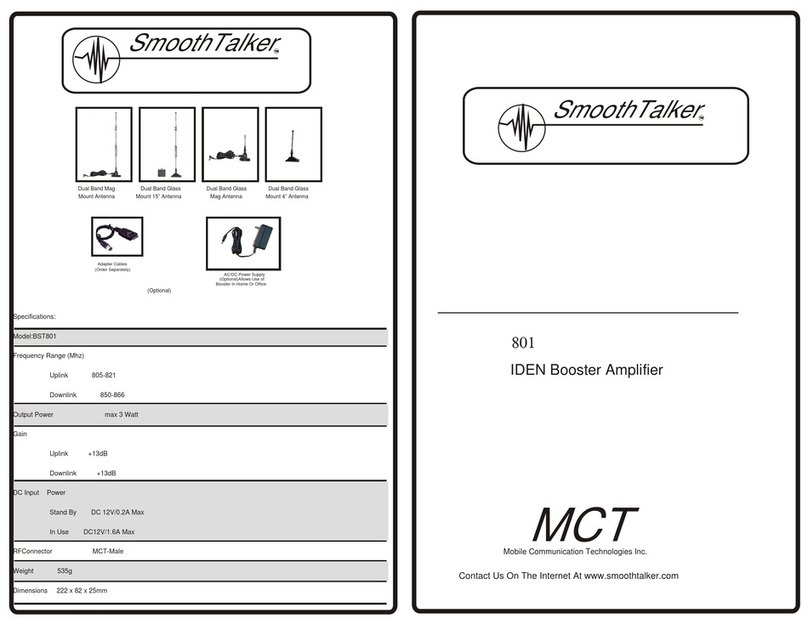
SmoothTalker
SmoothTalker BST801 quick start guide
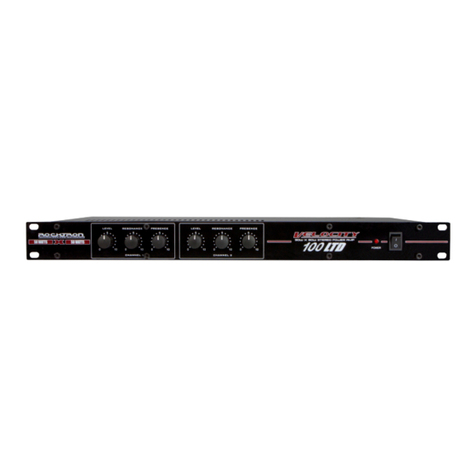
Rocktron
Rocktron Velocity 100LTD user manual