BPS Signal R2 User manual

Signal R2 User Manual
Use with Signal R2, running SignalSoft
1.5.6, with R2 hardware.
This document will explain what’s in the kit, step-by-step instructions for assembly, and some
tips and tricks to improve Signal R2’s performance! For more details and resources, you can
visit http://bps.space/build-signal-r2
1. Signal R2 Parts
1. 29mm motor mount
2. TVC servos
3. TVC extension
cables
4. BPS stickers!
5. Signal R2 flight
computer
6. 9v battery
connector
7. Flight computer
mounting brackets
8. TVC inner gimbal
9. TVC outer gimbal
10. M3.5 long screws
11. M3.5 short screws
12. M2 screws
13. Linkage stoppers
14. 1.5mm hex wrench
15. TVC pushrods
Copyright © 2019 Barnard Propulsion Systems, LLC Version 1.8, Jan 1, 2019
www.bps.space

2. Pre-assembly notes
When building your rocket, pick one direction or orientation to define as the ‘front’ or ‘forward
facing side’. Most of the 3d printed parts have at least one star on them. The stars should
ALWAYS face forward; if your rocket were see-through, you would be able to see all the stars
from the front. For Signal to keep your rocket on course, the stars must literally align :)
3. Flight computer assembly
1. The two included brackets go
on the top and bottom of the
flight computer. Paying
attention to the stars and
orientation of the text, place
these on the top and bottom of
the flight computer. The stars,
black terminal blocks, and
“Signal” text should all face the
same direction. The fit should
be very snug.
2. Use 4 of the M3.5 long screws
to secure the flight computer in
place, they should go all the
way through the center beam
of the mounting bracket.
Copyright © 2019 Barnard Propulsion Systems, LLC Version 1.8, Jan 1, 2019
www.bps.space

4. Flight computer power
To power Signal R2, you’ll need a power source of at least 7v connected to the “Bat” power
terminals; 9v batteries or 11.1v Lithium Polymer batteries are ideal.
1. Attach the correct + and - leads of the battery connector to the Bat terminal block. Be
careful to not reverse the polarity of the computer’s power.
2. Connect the leads of the battery to the battery connector, and flip the power switch on
Signal R2 to the On position. The computer should boot up after a second and start
making noise. You can turn it off now, we’ll set that up next.
a. If the computer doesn’t start up, make sure the battery is wired correctly and try
again. If it still doesn’t turn on, head to the troubleshooting section at the bottom
of this document.
3. Secure the battery to the flight computer or mounting brackets. Several rubber bands
wrapped around the whole computer and battery work well. They can also be used to
keep the SD card from falling out.
a. Be sure to cover up any exposed metal or leads on the battery or cables;
masking tape works well for this. Unexpected metal contact with parts of Signal
R2 may damage the computer.
Copyright © 2019 Barnard Propulsion Systems, LLC Version 1.8, Jan 1, 2019
www.bps.space

5. Flight computer setup
The flight computer needs is a Micro SD card to function properly.
1. Place a Micro SD card into the slot
on the back of the computer, and
turn it on again. The computer
should boot through it’s startup
sequence for a few seconds and
into the pad-idle mode.
2. Once the green light is on and the
computer is beeps once per
second, your computer is ready for
flight! Well, not quite yet, but green
lights and constant beeps indicate
the computer has passed all
startup checks and is ready to go.
3. Using your iPhone or Android
device, go to the app store and
download the “Signal - BPS.space”
app. This application will talk with
the Signal computer over Bluetooth!
4. With the flight computer turned on and beeping, open the Signal app and tap on “Signal
R2” in the flight computer list. If you don’t see your flight computer there, hit refresh a few
times and try booting up Signal again.
5. You’re in! Now you can view live sensor data, change flight settings, etc. Feel free to get
familiar with the app, we’ll be using it a bit more before the first flight.
6. TVC mount assembly
6a. Motor mount
The motor mount comes in the bag with the servos
and TVC extension cables. You’ll also need the
tiny silver linkage stopper.
1. Screw the linkage stopper into the motor
mount. It should be quite snug, completely
screwed in, and somewhat hard to turn with
just your fingers.
a. You can insert the straighter
pushrod here too, don’t worry about
tightening the linkage stopper to
lock in the pushrod yet, we’ll take
care of that later.
Copyright © 2019 Barnard Propulsion Systems, LLC Version 1.8, Jan 1, 2019
www.bps.space

2. Cut a small (10cm or so) length of 29mm cardboard motor mount tube to use as a liner
for your motors. Wrap it several times in tape(masking tape works well) until it fits snug
inside the 3d printed motor mount.
3. If you have one, insert a spent 29mm motor into the mount. The 3d printed part flexes
quite a bit without it, but can hold its structure well once a motor is inserted
6b. Inner gimbal
Next, let’s attach the inner gimbal to the motor mount.
1. Remove the large pieces of 3d printed support material. This should be fairly easy with a
pair of pliers. Use a smaller drill bit or long rod to remove the support material inside the
screw holes of the part.
2. Slide the inner gimbal over the motor tube. Make sure the star on the inner gimbal faces
the same direction that the pushrod points.
3. Screw into place using two of the M3.5 short
screws. It should be a tight fit.
4. Grab one of the included servos. Count 3 holes
from the attachment point of the servo horn,
and insert the bent end of pushrod.
Copyright © 2019 Barnard Propulsion Systems, LLC Version 1.8, Jan 1, 2019
www.bps.space

5. Attach the servo to the inner gimbal using two of the M2 screws. The servo horn should
be pointing down, away from the center of the TVC mount, along with cable coming out
of the servo housing. It should be slightly hard to screw in, but the screws will hold the
servo very tightly in place during flight.
6. Finally, use the 1.5mm hex wrench to unscrew the linkage stopper a bit. Align the servo
horn to its center position (pointing straight down), move the motor mount to its center,
so that it’s parallel with the servo, and tighten the linkage stopper. The mount doesn’t
need to be exactly centered, we’ll take care of that later, but do your best. Make sure it’s
very tight, we don’t want this coming loose!
Copyright © 2019 Barnard Propulsion Systems, LLC Version 1.8, Jan 1, 2019
www.bps.space

6c. Outer gimbal
This is the last major piece of the TVC mount!
1. Just like the inner gimbal, remove the large pieces of support material, then the smaller
pieces inside the M3.5 screw holes.
2. Make sure the stars are aligned,
facing forward, and slide the outer
gimbal into place. The outer gimbal
should snap into place, since it’s
another slightly tight fit. Screw the
outer gimbal into the inner gimbal with
two M3.5 short screws.
3. Grab one of the the more bent
pushrods, and insert it into the very
top hole of the inner gimbal. This is
tricky to do, and may require some
force or pliers. Be careful not to
damage the inner gimbal stem in the
process.
4. Count 3 holes from the
attachment point of the servo
horn, and insert the other side
as shown here. The servo and
inner gimbal should now be
attached.
Copyright © 2019 Barnard Propulsion Systems, LLC Version 1.8, Jan 1, 2019
www.bps.space

5. Use the two M2 screws to
attach the servo to the outer
gimbal, this time with the
cable and servo horn
pointing up. Make sure the
servo cable is threaded in
toward the motor mount, not
away from it. If this isn’t done
correctly, the cable may
interfere with the rocket’s
airframe during integration.
This should be a tight fit - the
bottom screw (closest to the
center of the TVC mount)
may be a little hard to get
into place.
6d. TVC extension cabling
The TVC mount is almost finished! To complete the build, we’ll need to take care of some
wiring.
1. Thread the TVC Y servo (labeled on the mount) cable up in between the X servo
pushrod and the motor mount.
2. Use a marker directly on the black plastic headers of the servos, and label them
appropriately according to
their markers on the TVC
mount. With the mount
standing upright, Y should
be the bottom servo, X
should be the top.
3. Do the same for the TVC
extension cables - label
one X on both ends, and
the other Y. It’s worth being
thorough on this, accidental
reversal of the leads will
result in an in-flight abort.
Copyright © 2019 Barnard Propulsion Systems, LLC Version 1.8, Jan 1, 2019
www.bps.space

4. Connect the TVC extension cables to their respective servos, and make sure they are
connected tight! The two cable colors should correspond. Orange to white, red to red,
and black to black.
5. Fold the TVC X servo cable
around the extension cable/servo
cable joint, and wrap a good deal
of masking tape around the
assembly. With the tape wrapped
around the wire joint, both cables
should have little or no slack when
pulled by their extensions.
6. If you were to stretch out the TVC
extension cables, they should now
be equal length at the end, since
the slack in the X cable was
wrapped in tape. This is important,
slack in the X cable could result in
a TVC jam.
6e. Final TVC hardware steps
The TVC mount is built and wired up! Time to get it powered on and tested.
1. Plug the correct TVC extension cables into the flight computer. The white wire of the
TVC extension cable should be at the top, and the black wire on the bottom.
2. Turn on the Signal flight computer, let it boot up into the green pad-idle mode again
3. Open up the Signal app on your iPhone or Android device, and go to System
Preferences
Copyright © 2019 Barnard Propulsion Systems, LLC Version 1.8, Jan 1, 2019
www.bps.space

4. Let’s see how the mount works! Tap and hold the TVC Test button. The mount should
swivel back and forth on each axis slowly. If either axis seems stuck, this is a good time
to check for stuck wires or tight screws.
5. Next, let’s get things lined up. Exit System Preferences, tap on “Thrust Vectoring”, then
on “Advanced”
a. Use the + and - buttons under “TVC Servo Alignment” on each axis to get the
motor mount centered. Don’t worry if it’s not perfect. Each time you hit + or -, the
computer will change where the center point of the TVC mount is
6. If you’re eager to see the whole system in action, head down to section 9b to simulate a
full flight.
7. Once that’s done, your flight hardware is ready to go in a rocket! But first, we must build
the rocket...
7. Using the drill/cut guides
Signal R2 comes with drill and cut guides for the vectoring mount and flight computer. These
guides will be wrapped around the airframe of your rocket to ensure you place the holes and
cutouts in the correct place. If you’ve already used your provided cutout guide, they can be
downloaded and printed on a regular 8.5x11 inch US letter paper, just make sure they’re printed
at 100% scaling. Head to the Build Signal R2 web page for those files.
You’ll want to start out with a brand new body tube for this to work well, though a pre painted
one can work too.
1. Wrap the TVC cutout guide around the airframe, pulling it tight. Ensure that “Line 1” can
be seen through directly beneath the three tics by the number 4. This is to simply make
sure you’re using the correct guide on the correct airframe.
a. I recommend lining up the bottom edge of the paper labeled “dirt” with the bottom
of your airframe for most ~10 cm long motors. You can move it up or down
slightly depending on the length of the motor you use. For instance, the Aerotech
G8 motor is 15 cm long, and requires about 5cm more clearance if you don’t
want it to stick out from the bottom of the rocket. It’s helpful to hold the loaded
thrust vectoring mount up next to TVC guide on the airframe to get an idea of
where things will sit once you make the cuts.
2. Carefully hold the paper against the airframe and unwrap it enough to apply tape on the
edge indicated, “Tape to vehicle here”.
3. Once again, wrap the guide around the airframe, this time taping down the other edge of
the paper, so the rocket remains covered when you let go.
4. Apply small pieces of tape on the top and bottom of the TVC guide to help secure it a bit
more.
5. Follow the same application process with the flight computer drill/cut guide. The most
important part here is to line up the small blue numbers between the two guides. 1, 2, 3,
and 4 should match up as closely as possible between the papers. You can mount the
Copyright © 2019 Barnard Propulsion Systems, LLC Version 1.8, Jan 1, 2019
www.bps.space

computer anywhere on the vehicle so long as these numbers are exactly in line with
each other.
6. Make your drills on both guides first - these are all for the M3.5 screws. Drill directly in
the center of each red dot, through the airframe. If you’re using a cardboard or a
somewhat flexible airframe, I recommend drilling holes at 2.5 or 3mm, so that the hole
taps itself when the screw is inserted. Otherwise, do not drill larger than 3.5 mm.
7. Cut on the red lines with a sharp hobby knife.
a. On the TVC guide, red lines outline the minimum required cut out area, mostly for
the TVC servos and pushrods.
b. On the flight computer guide, these are simply suggested cut out areas, and are
not completely needed. The cutouts allow you to insert and remove the Micro SD
card, turn the computer on and off, and observe the LED clearly without removing
the computer from the rocket. If you prefer not having a hole in the side of your
rocket, you can cover this up by making a removable door.
8. If you’re building a vehicle with multiple airframe sections, it can be useful to label each
“side” on the inside of the airframe; 1, 2, 34. This can help you line up the different
sections during assembly, and is vital if the computer and TVC mount are in different
sections.
9. That’s it! Your rocket is now ready for assembly!
8. Assembly notes
Before putting all these parts together, there are a few things to note.
● By nature, in comparison with traditional model rockets, TVC rockets will be heavy for
their thrust. This means they’ll have a more energetic impact on landing, which could
damage some parts of the rocket. Because of this, I recommend reinforcing the airframe
around the TVC mount/bottom of the rocket.
○ To do this, you can use an extra body tube. Cut out sections of the tube to fit
around the outside of the bottom of the vehicle. Very generously use epoxy, CA,
or a strong hobby glue to secure this tubing to the outside of the airframe.
Contrary to most cases, the more glue - the better!
● You are welcome to cover up the TVC servos with your own 3d printed or handmade
parts! So long as you are careful not to restrict any of their motion, placing objects or
covers over them is just fine.
● The same goes for the flight computer cutouts. The barometer just needs to sense the
outside air-pressure. So long as your rocket has a few holes to ensure that happens,
covering up the flight computer access hatch is no problem.
● You can paint the TVC mount - if you’re painting your rocket and want to disguise your
the TVC cutouts, you can paint the rocket while the TVC mount is inside. The paint will
have little or no effect on its ability to gimbal the motor.
● You cannot paint the flight computer - doing so will cover up the state indication LED,
and may damage some of the sensors or screw terminals.
Copyright © 2019 Barnard Propulsion Systems, LLC Version 1.8, Jan 1, 2019
www.bps.space

9a. Rocket integration
If your airframe segments are longer than the TVC extension cables, you may need to insert the
flight computer first. If that is the case, start from step 3, follow through to the end, then
complete steps 1 and 2.
1. First, you’ll need to attach the TVC mount. With the airframe and TVC mount upside
down, cables first, lower the TVC mount into the rocket.You may need to wiggle the
mount around or have it actuate a bit, but it should otherwise fit quite well.
2. Once mounted, screw the TVC mount in place from the outside of the airframe. Use the
M3.5 long screws
3. Plug both TVC extension cables into the flight computer. The cables should be sticking
out the top of the airframe section. Once again, the white wires of the extension cables
should be on top, with the black wires on the bottom.
4. While the flight computer is still outside the rocket, thread all available slack in the TVC
extension cables up through the flight computer mounting brackets. Use a rubber band
or cable tie to keep the slack in the cable minimal.
5. Slide the flight computer down through the top of the airframe section. This is a good
time to ensure that all the stars between the TVC mount and flight computer are aligned
and facing “forward”.
a. As the computer slides through the tube, keep pulling the TVC extension cable
tight to remove slack.
b. Be sure the TVC cables do not become unplugged from the flight computer.
6. Attach the flight computer to the rocket airframe using 8 of the M3.5 short screws
7. Once more, make sure the TVC extension cables are pulled tight and cannot fall back
through the airframe.
a. This part is critical for a good flight. If the TVC cables have slack, they may end
up jamming the TVC mount during flight.
9b. Testing
1. Turn the rocket on! When the computer boots up, keep an eye on the TVC mount. If
you’ve aligned everything correctly, the TVC mount will briefly actuate forward and to the
right, with the rocket upright, facing “forward”. It will hold this position for several
seconds, then move to center. At the end of startup the TVC mount will actuate positive
and negative on each axis to the PID limit, then return to center.
2. After startup the computer will load into “pad-idle” mode.
3. Simulate a launch by lifting your rocket straight up quickly! Keep the rocket very close to
upright, simulating a successfully stabilized flight.
Copyright © 2019 Barnard Propulsion Systems, LLC Version 1.8, Jan 1, 2019
www.bps.space

4. Signal R2 is now in the “powered flight mode”. The vectoring mount is actively working to
correct the orientation of the rocket. Place a finger on the mount to ensure it’s working in
both axes.
5. Now simulate motor burnout by quickly jolting your rocket downward, the exact opposite
of simulating launch.
6. The TVC mount will lock up to center, recognizing burnout and shutting down TVC to
conserve power. The LED will turn white briefly before turning yellow, this indicates
apogee detection. Apogee is detected when no upward trend is found in barometer
readings.
7. After several more seconds, the LED will turn red and Signal will begin beeping again.
Signal has now recognized a sustained altitude of less than 5 meters for a few seconds,
which it classifies as having landed. The red LED and beeping indicates that flight data
is being transferred to the Micro SD card into a .CSV file. It’s very important to not
remove or wiggle the SD card during this period, as it may compromise the transfer of
data.
a. Depending on how long your flight lasted, this process can take several minutes.
8. The LED may turn purple for a bit, this indicates that Signal is clearing the Flash memory
chip, and should only last a few seconds.
9. When the data has been transferred to the Micro SD card, Signal will start beeping while
the LED alternates between blue and green. After this begins, the computer can safely
be shut off, and the SD card can be removed.
10. Try simulating another launch! This time, right at “launch”, pitch the vehicle over about
30-40 degrees, simulating a poor flight. The in-flight abort system should kick in, turning
on the buzzer for just a second(but not firing any pyro channels, all pyros are restricted
below 4 meters above ground level). The detected abort will also show up in the flight
data.
11. Jolt the vehicle down again to simulate burnout, then wait for Signal to log all the flight
data before shutting the computer down.
If Signal R2 moves through all these steps smoothly, congratulations! Your thrust vectoring
system is working just fine. If not, head down to the troubleshooting section to diagnose the
problem.
9c. TVC fine calibration
Now it’s time to really dial things in on the TVC mount. The goal here is to get the center
position of the mount entirely in-line with the rest of the vehicle. The better your TVC alignment
is, the more stable the rocket’s flight will be.
1. Slide a motor, preferably spent or inert, into the TVC mount
2. Grab a long length of motor mount tube and slide it over the motor - it should be sticking
far out of the bottom of the rocket now. Ideally 1-2 feet of tubing should be sticking out.
3. Lay the rocket down sideways, turn Signal R2 on, and open up the Signal app on your
iPhone or Android device
Copyright © 2019 Barnard Propulsion Systems, LLC Version 1.8, Jan 1, 2019
www.bps.space

4. Connect to the flight computer, tap “Thrust Vectoring”, then “Advanced”
5. Get your head close to the top of the rocket on one axis(in line with a TVC servo, X or Y)
and look down the length of the rocket to the bottom. The motor tube sticking out might
not be perfectly centered.
a. If there’s a bit of play or slack in the mount’s position, that’s okay in small
amounts. Gently push the mount back and forth to estimate where the center of
the slack is, and use that position to judge the alignment of the mount.
6. Use the + and - buttons on your iPhone or Android device to move both the X and Y axis
to their center positions
7. Once everything is centered, the long motor tube should look like a straight extension
from the airframe.
8. Remove the long motor tube, and you’re all set!
10. Parachutes and pyros
Your rocket still needs parachutes, and a way to get them out of the vehicle in time. You can’t
use a motor ejection change, so you’ll need to wire up those pyro channels to black powder
charges. If you’re unfamiliar with how to build a piston based parachute deployment system, or
the required ejection charges, check out this part of the “Build Signal Alpha” series.
11. Tuning
Before you launch your newly built rocket, you’ll need to tune it for flight. This involves finding
the inertia of the vehicle and running it through a flight sim to generate safe P, I, and D gains.
The methods used here are the same used by NASA to tune many of their experimental aircraft!
The Signal app has the steps and tips for tuning your rocket. You can click the “?” button in the
tuning section. That said, it’s easier to follow along on a computer, and the steps are all here:
https://bps.space/tuning
12. Flight tips
With your tuned PID values loaded into Signal R2, you’re ready to fly! Here are a few tips to
help the first flight work well.
● Because thrust vectoring keeps the rocket stable, you do not need to launch from a rail
or rod. If you want, you can build your own launch pad without them. That said,
launching from a short rail is usually best to ensure the vehicle stays upright before
launch.
● Do not use a launch rod, use a launch rail.
○ Because the rocket can roll around the launch rod, any type of correction
maneuver in the TVC will induce roll on the vehicle while it is still connected to
the rod. Launch rods are also a bit more flexible, and may whip the rocket around
as it leaves the rail, which can be bad for stability
Copyright © 2019 Barnard Propulsion Systems, LLC Version 1.8, Jan 1, 2019
www.bps.space

○ A launch rail solves this - by nature, the rocket cannot roll around the rail. Small
corrections are no problem as long as the rocket can move along the rail without
jamming.
● Always fully charge your batteries before flight!
○ You can double check the voltage of your battery in the “Sensors” section of the
Signal app on your iPhone or Android device - it should be at least 1 or 2 volts
above 7v, where the computer is at risk of shutting down.
● Fly in low wind.
○ Though weather cocking isn’t an issue with TVC rockets, Signal R2 cannot
correct for horizontal drift while under power. It may stay upright, but can still drift
laterally from the pad.
● Do not launch the rocket at more than 30 degrees from vertical.
○ This is identical to the NAR Model Rocket Safety Code. Especially with TVC
rockets, launching at a steep angle puts the rocket at risk of falling back to the
ground because of insufficient vertical force against gravity.
● Check TVC manually
○ Before each flight, with Signal R2 powered off, use your hand to move the TVC
mount back and forth on each axis. If you feel any obstruction or potential jam, do
not fly the rocket until the jam has been removed or fixed.
● Watch TVC during startup
○ When Signal R2 moves through startup, pay attention to the TVC mount. With
the rocket upright, and facing you, the mount should ALWAYS actuate the bottom
of the motor toward you and to the right right for a few seconds. If it doesn’t move
in this way, you may have reversed the TVC wiring, and should not fly the rocket
until it is fixed.
● Every two or three flights, it’s a good idea to perform some maintenance and tests on
your rocket, just to be safe.
○ Re-check TVC calibration. Especially after a hard impact, the mount can lose
alignment by a bit, or become loose. If it’s loose, head to the troubleshooting
section for fixes.
○ Double check the slack in the TVC extension cables - make sure there’s little or
no slack in order to avoid a TVC jam.
12. Viewing flight data
You’ve flown your rocket, and you got it back! Now it’s time to look at the data to see how things
went.
1. Remove the Micro SD card from Signal R2 and plug it into your desktop or laptop
computer
2. Copy the most recent flight log file to the computer
3. The .CSV file can be used in most spreadsheet programs or data viewers. Google
Sheets is a great option - if you have an account with Google, go to
www.docs.google.com/spreadsheets
Copyright © 2019 Barnard Propulsion Systems, LLC Version 1.8, Jan 1, 2019
www.bps.space

a. Create a new spreadsheet
b. Go to File > Import > Upload. Drag your .CSV flight log file in, and Google Sheets
will import all the data
c. Sheets should automatically recognize this, but if it doesn’t, select Comma as the
separator character.
d. From here, you can view or edit any of your flight data
e. If you want to view it as a plot, select the data you want to view, then go to Insert
> Chart
f. Any data you view should also include the “Flight Time (sec)” column. Once the
chart is created, check the box beside “Use column B as labels”
4. If you don’t have a Google account(though they’re quite easy to create), there are
several account-free data viewers as well. https://plot.ly/create/ is a fast online
alternative.
Troubleshooting
If you experience an error or anomaly when using the Signal R2 kit, you can likely diagnose it
with this table of problems and solutions. If you experience a problem not listed here, or none of
the solutions work, please contact BPS at [email protected].
Problems
Causes/solutions
Signal won’t turn on at all with the power connected
● Check polarity of power input
● Check voltage of power input - must be above
7v
● Check for a possible short circuit on servo
outputs
● Ensure all nearby metal objects make no
contact with exposed contacts on the PCB
Signal turns on, flashes the LEDs once, waits 2-3
seconds, then plays the 2-tone buzzer indication
● Signal is missing an SD card, or it is not
connected well - remove and re-insert the SD
card
● This can also be a file formatting error on the
SD card, sometimes it occurs with cards above
32gb in capacity. Try using a smaller card, or
reformatting it as FAT32.
Signal turns on, flashes all LEDs once, and immediately
plays the 2-tone buzzer indication
● Signal cannot find the configuration file on the
SD card, or did not read it correctly. Remove
the SD card and delete the CONFIG.TXT.
Place it back in Signal and boot it up again
Signal boots up successfully, but does not enter
pad-idle mode, instead going straight to powered-flight
mode, with the red and blue LEDs flashing
● The launch detection threshold is too low in
the configuration file. Anything less than 9.85
will likely cause this.
Near the end of startup, Signal halts the process and
● Reboot the computer. Signal may have
Copyright © 2019 Barnard Propulsion Systems, LLC Version 1.8, Jan 1, 2019
www.bps.space

plays the 2-tone buzzer indication
detected an issue with one of the sensors. If it
persists over multiple startups, please contact
BPS.
At the end of startup, Signal halts the process with a
purple light and plays the 2-tone buzzer indication
● The IMU or barometer has failed self-test
function, this can happen because of too much
movement during startup. Reboot the
computer.
After cycling through all LEDs in startup, the red light
flashes and starts beeping once a second.
● This is not a bug! Signal has detected
significant data on the flash memory card,
likely from a previous flight, or long pad-idle
period. This process is usually executed at the
end of a flight, but since your data wasn’t
transferred to an SD card before shutting
down, it is being saved now. Reboot the
computer only after the blue and green LEDs
start flashing slowly.
The TVC servos don’t move at all when Signal is
powered on, and can be moved easily with a finger.
● The TVC servos are plugged in backwards.
○ Reseat the TVC extension cables so
the white wire is on top, closest to the
X or Y label, with the black wire on
the bottom, closest to the ‘-’ symbol
○ If this doesn’t work, double check the
connection between the servo cables
and extension cables. Black, red, and
orange/white wires should all match
up.
One of the TVC servos does not work function
● Repeat the above steps for the individual
servo.
● If everything is wired correctly, you may have a
faulty or damaged servo. Please contact BPS
One of the TVC servos seems to move slowly when
used in the mount.
● You may have a faulty or damaged servo, see
above.
● The TVC mount may be jammed - check for
loose debris or wiring near the joints
The TVC mount seems to move slowly, the joints
between parts do not move without considerable force
● The TVC mount may be jammed, see above
● The TVC mount may not be worn in, use a drill
or screwdriver to over tighten the M3.5 short
screws by a few turns to loosen it up
The TVC mount has a lot of ‘play’ - it’s able to wiggle
back and forth in one or both axis while not moving the
servos. A small amount of this will always be present,
but 1.5+ degrees will start to affect the quality of flights
● The TVC actuation points(screw holes) are too
loose
● Long term solutions
○ Contact BPS for replacement parts or
print files
● Short term solutions
○ Coat the M3.5 screws in a layer of
epoxy, CA, or another strong type of
glue to make them larger. Wait for the
glue to fully dry, and replace them in
the mount.
○ Wrap a piece of paper around the
screws as they enter the screw holes,
for the same effect as the glue.
Copyright © 2019 Barnard Propulsion Systems, LLC Version 1.8, Jan 1, 2019
www.bps.space

One of the pyro channels isn’t working
● Use a voltmeter to check if power is sent to the
channel while ground testing the channel using
the Signal app
● If the problem persists, please contact BPS
After a long time in pad-idle, the OnTime(sec) column of
data starts counting from 0 again
● This is a known bug, and will not affect any of
the other readings or functions of the flight
computer. After about an hour of idling on the
launch pad, the computer has to reset the
pad-idle time variable.
Something in the SD card data looks odd or out of
place. Examples might be columns filled with zeros,
large spikes in certain columns, far-from-nominal
battery voltage, etc.
● Try removing the CONFIG.TXT file and
rebooting the computer. Poor formatting can
cause odd errors in the data.
● Contact BPS with the flight or test data you’re
seeing
User Requirements
The following constitute the guidelines that you agree to follow when using the Signal R2 kit. If
you do not follow these, you void any guarantees or warranties for Signal R2, and neither
Joe Barnard nor BPS.space have any liability.
● I will use and fly Signal R2 only during high visibility conditions
● I will not use or fly Signal R2 under the influence of drugs or alcohol
● I will alert all persons in the general vicinity of the rocket before I launch
● I will ensure an audible countdown to ignition is conducted from at least 5 seconds
● I will never use or launch Signal R2 in the direction of people, property, or anything other
than open space
● I will never launch Signal R2 with the intent to harm
● I will only launch Signal R2 in accordance with FAR 101 by the FAA, the NAR’s MRSC,
and the Tripoli Safety Code.
Copyright © 2019 Barnard Propulsion Systems, LLC Version 1.8, Jan 1, 2019
www.bps.space
Other manuals for Signal R2
1
Table of contents
Other BPS Toy manuals
Popular Toy manuals by other brands
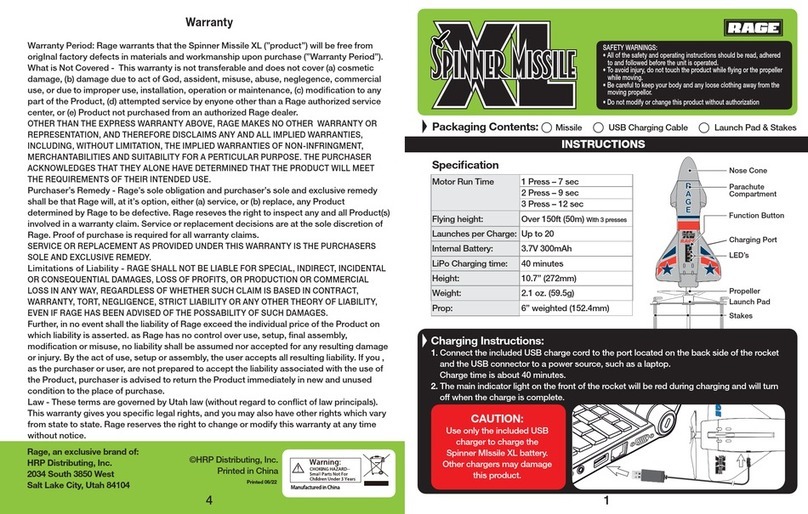
Rage
Rage SPINNER MISSILE XL instructions

TufFlight
TufFlight Big Bouncer Assembly instruction
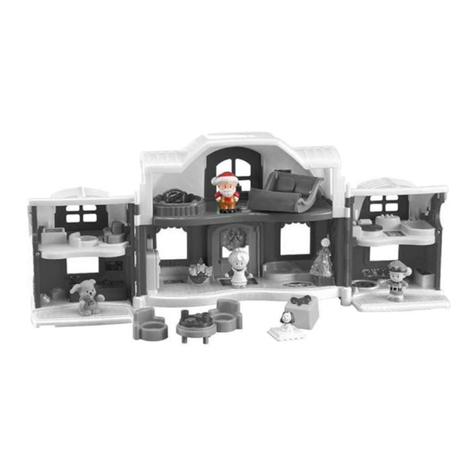
Fisher-Price
Fisher-Price BLV78 quick start guide
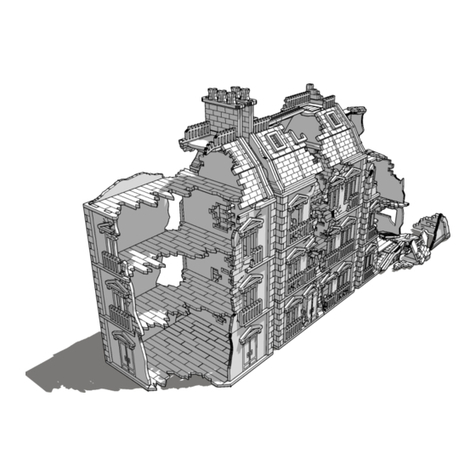
Tabletop Scenics
Tabletop Scenics TTSC-WAR-083 instruction manual
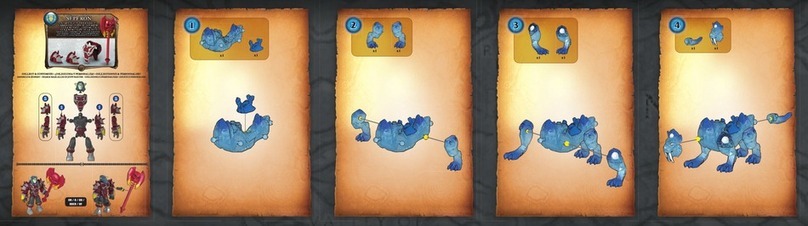
Mega Bloks
Mega Bloks World of Warcraft quick start guide

Jamara
Jamara Small City 460668 Instruction
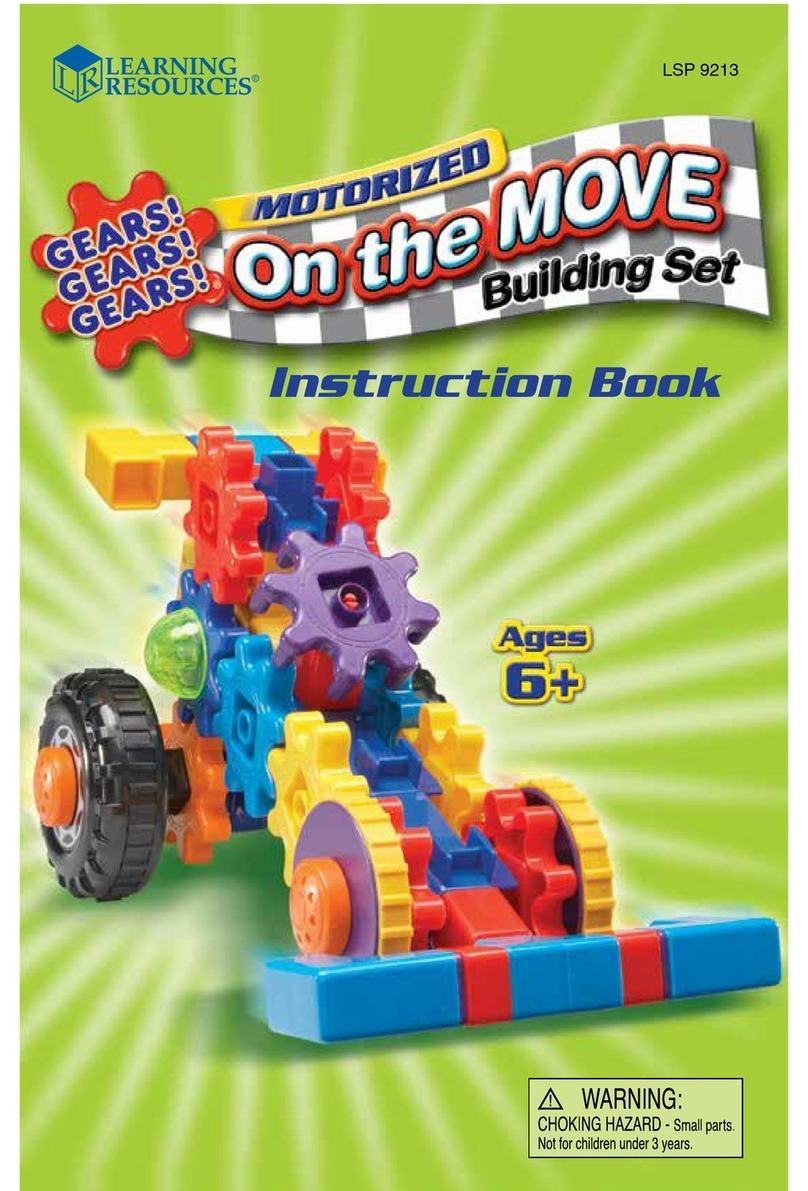
Learning Resources
Learning Resources Gears on the Move LSP 9213 Instruction book
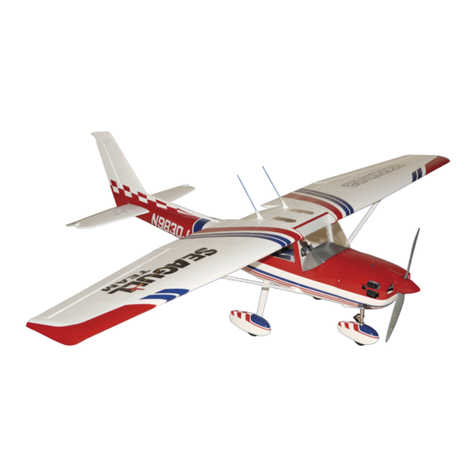
Seagull Models
Seagull Models CESSNA 152 Assembly manual

LEGO
LEGO Ninjago Zane 4618490 Assembly instructions
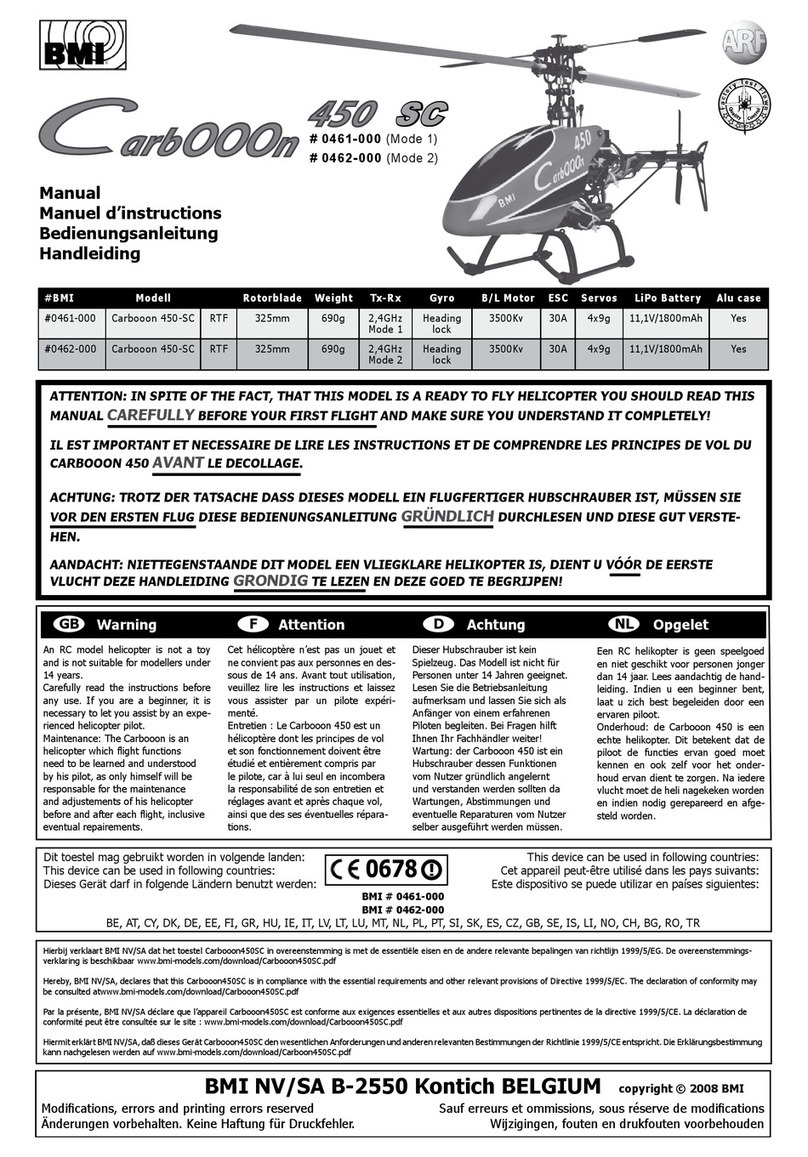
BMI
BMI Carbooon 450-SC 0461-000 manual

Eduard
Eduard Yak-38 interior Assembly instructions
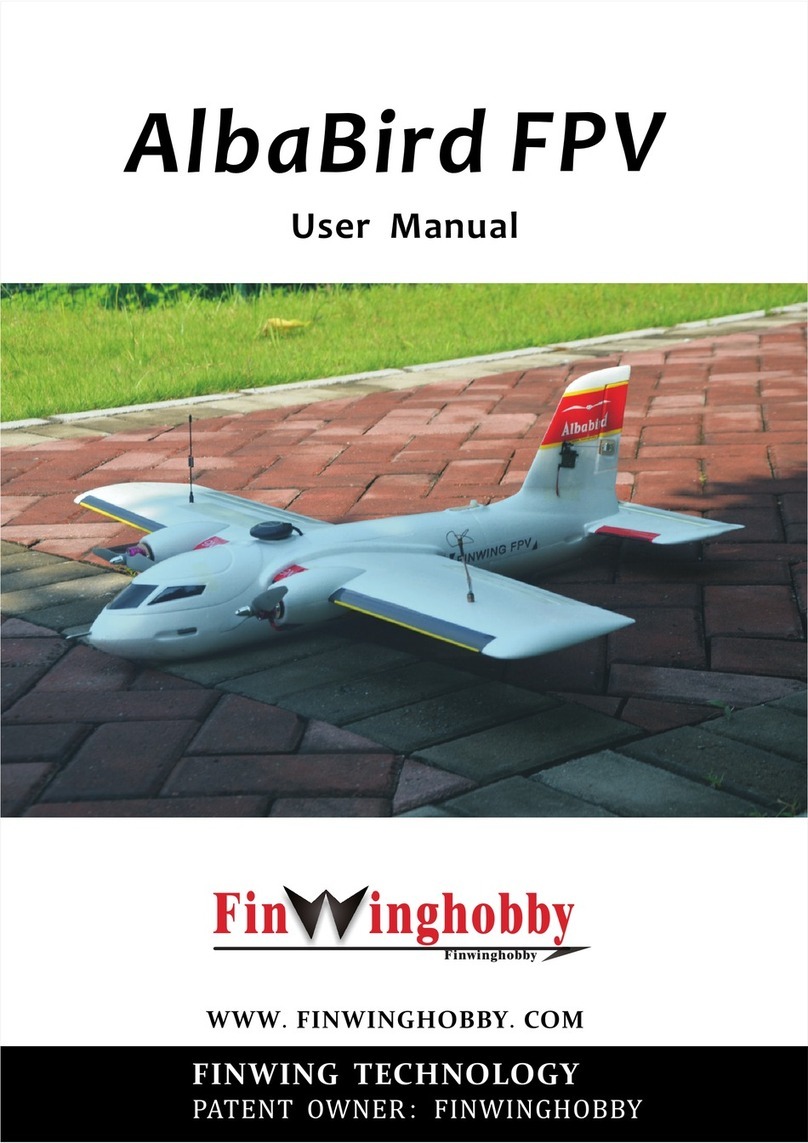
Finwinghobby
Finwinghobby AlbaBird FPV user manual