BSD BSD-1000 User manual

®
OPERATION AND MAINTENANCE MANUAL
LOW VOLTAGE
METAL ASSEMBLY SCREW DRIVER
WWW.KILEWS.COM.CN
KILEWS ELECTRIC TOOLS(SHANGHAI)CO., LTD.
No.367, 2nd Xinjian Road, Xuhang Town, Jiading District, Shanghai 201808 China
Tel: 86-21-59556022 Fax: 86-21-59553779
OSH-D10E
BSD-1000
BSD-1200

BSD-1200 Series
Metal Assembly Screwdrivers are designed for installing threaded fasteners in light
industrial and appliance manufacturing applications.
KILEWS is not responsible for customer modification of tools for applications on which
KILEWS was not consulted.
Important safety information enclosed.
Read all these instructions before placing tool in service or operation this tool and save
these instructions. It is the responsibility of the employer to place the information in this
manual into the hands of the operator. Failure to observe the following warnings could
result in injury. When using electric tools, Basic safety precautions should always be
followed to reduce the risk of fire, electric shock and personal injury, including the
following:
1.General Safety Rules
2.Operations Cautions
3.Specifications
4.Description Of Operation
5.Torque Adjustment Operation
6.Accessories
7.Servicing
NOTICE
WARNING

BSD-1200 Series
WARNING! Read all instructions Failure to follow all instructions listed below may result
in electric shock fire and/or serious injure. The term “power tool” in all of the warning listed
below refer to your mains operated (corded) power tool or battery operated (cordless)
power tool.
SAVE THESE INSTRUCTIONS
1) Electrical Safety
a) Keep work area clean and well lit. Cluttered and dark areas invite accidents.
b) Do not operate power tools in explosive atmosphere, such as in the presence of
flammable liquids, gases or dust. Power tools creat sparks which may ignite the dust
of fumes..
c) Keep children, and bystanders away while operating a power tool. Distractions can
cause you to lose control.
2) Electrical Safety
a) Power tool plugs must match the outlet. Never modify the plug in any way. Do not
use any adapter plugs with earthed (grounded) power tools. Unmodified plugs and
matching outlets will reduce risk of electric shock.
b) Avoid body contact with earthed or grounded surfaces such as pipes, radiators,
ranges and refrigerators. There is an increased risk of electric shock if your body is
earthed or grounded.
c) Don’t expose power tools to rain or wet conditions. Water entering a power tool will
increase the risk of electric shock.
d) Do not abuse the cord. Never use the cord to carrying, pulling or unplugging the
power tool. Keep cord away from heat, oil, sharp edges or moving parts. Damaged
or entangled cords increase the risk of electric shock.
e) When operating a power tool outdoors, use an extension cord suitable for
outdoor use.Use of cord suitable for outdoor use reduces the risk of electric shock .
3) Personal Safety
a) Stay alert, watch what you are doing and use common sense when operating a
power tool. Do not use power tool while you are tired or under the influence of
drugs, alcohol, or medication. A moment of inattention while operating power tools
may result in serious personal injury.
b) Use safety equipment. Always wear eye protection. Safety equipment such as dust
mask, non-skid safety shoes, hard hat, or hearing protection used for appropriate
conditions will reduce personal injuries.
c) Avoid accidental starting. Ensure the switch is in the off position before plugging
in. Carrying power tools with your finger on the switch or plugging in power tools that
have the switch on invites accidents.
d) Remove any adjusting keys or wrench before turning the power tool on. A wrench
or a key that is left attached to a rotating part of the power tool may result in personal
injury.
e) Do not overreach. Keep proper footing and balance at all times. This enables better
control of the power tool in unexpected situations.
f) Dress properly. Do not wear loose clothing or jewellery. Keep your hair,clothing,
and gloves away from moving parts. Loose clothes, jewellery, or long hair can be
caught in moving parts
1. General Safety Rules

BSD-1200 Series
g) If devices are provided for the connection of dust extraction and collection
facilitys, ensure these are connected and properly used. Use of these devices can
reduce dust related hazards.
4) Power tool Use and Care
a) Do not force the power tool. Use the correct power tool for your application. The
correct power tool will do the job better and safer at the rate for which it was designed.
b) Do not use power tool if switch does not turn it on or off. Any power tool that
cannot be controlled with the switch is dangerous and must be repaired.
c) Disconnect the plug from the power source before making any adjustments,
changing accessories, or storing the power tools. Such preventive safety measures
reduce the risk of starting the power tool accidentally.
d) Store idle power tools out of reach of children and do not allow persons
unfamiliar with the power tool or these instructions to operate the power tool.
Power tools are dangerous in the hands of untrained users.
e) Maintain power tools. Check for misalignment or binding of moving parts,
breakage of parts and any other condition that may affect the power tools
operation. If damaged, have the power tool repaired before use. Many accidents are
cause by poorly maintained power tools.
f) Keep cutting tools sharp and clean, Properly maintained cutting tools with sharp
cutting edges are less likely to bind and are easier to control.
g) Use the power tools, accessories and tool bits ect., in accordance with these
instructions and in the manner intended for the particular type of power tool,
taking into account the working conditions and the work to be performed. Use of
the power tool for operations different from intended could result in a hazardous
situation.
5) SERVICE
a) Have your power tool serviced by qualified repair person using only indentical
replacement parts, This will ensure that the safety of the power tool is maintained.
Additional information shall be provide
a) Instruction for putting into use
1. Setting-up or fixing power tool in a stable position as appropriate for power tools which
can be mounted on a support.
2. Assembly
3. Connection to power supply, cabling, fusing, socket type and earthing requirements.
4. Illustrated description of functions.
5. Limitations on ambient conditions.
6. List of contents.
b) Operating Instructions.
1. Setting and testing.
2. Tool changing.
3. Clamping of work.
4. Limits on size of work piece.
5. General instructions for use.
c) Maintenance and servicing.
1. Regular cleaning, maintenance, and lubrication.
2. Servicing by manufacture or agent, list of addresses.
3. List of user-replaceable parts.
4. Special tools which may be required.

BSD-1200 Series
1) Whenever changing a bit, make certain the Power Switch is in the “ OFF “ position and
tool is unplugged.
2) Do not allow chemicals such as acetone, benzene, thinner, trichloroethylene ketone, or
other similar chemicals to come in contact with the screwdriver housing as damage
will result.
3) Do not drop or abuse the screwdriver.
4) Do not adjust the torque setting higher than 8 on the torque scale.
5) There should be a tool rest interval when cycles three seconds or longer. This tool is
intended for a duty cycle of 0.8 sec on, 2.4 sec off.
6) Do not use this screwdriver for tightening wood screws. This is “ Metal Assembly
Screw Driver ”
7) Do not operate the Forward / Reverse Switch the motor is running.
8) Whenever a tool is not being used, move the Power Switch to the “OFF” position and
unplug the screwdriver.
●Do not drop or abuse the tool.
●Whenever a tool is not being used, position the Power Switch to the “OFF” position
and unplug the power cord.
2. Operations Cautions
CAUTION

BSD-1200 Series
MODEL BSD-1000 BSD-1200
Input voltage(DC) 32VDC
Rated input 48W
Bit torque
Kgf.cm 0.5-7 2-15
Lbf.in 0.44-6.10 1.68-13.01
N.m 0.05-0.69 0.19-1.47
Torque Adjustment Step less
Unloaded Rotation Speed
(R.p.m) ±10% 1000 1000
Metal assembly
screw
Machine
screw(mm) 1.4~2.6 2.0-4.0
Tapping
screw(mm) 1.4~2.0 2.0-3.0
Weight (g) 480
Length (mm) 230
Model of Torque Fixing Ring KC-3
Model of Suspension Rack KH-4(KC&KH-2)
Power controller BSD-32P
Bit Type Ø4mm ,Ø5mm
* 1N.m=10.2Kgf.cm 1N.m=8.85Lbf.in
3. Specifications

BSD-1200 Series
Attaching / detaching bit and bit type
Push up the holder clamp by finger tip, and it will be unlocked. Thus, the bit can be freely
attached and detached (single finger notion type) select such a bit whose shank is equal
to the size shown below.
■Insert the power plug into a receptacle and set the changeover switch to “F”position.
■Apply the bit to the screw head and press the lever or push main body to, then the
switch will be turned ON to start the motor running.
■When the screw is tighten and reach the torque that you had set, The tool will stopped
automatically.
■To reset the tool by releasing the lever to the original position or releasing the bit From
the screw head.
■To return the screw, set the changeover switch to “R” position.
To adjust the torque on these screwdrivers. Proceed as follows:
1. Determine the torque output of the tool by checking
a tightened Fastener with a torque wrench.
2. Increase or decrease the torque by rotating the
Spring Adjusting Ring. Rotating the Ring clockwise to
a higher number on the torque Scale increase torque
output while rotating the Ring counterclockwise to a
lower number decreases the torque output.
3. Check the adjustment with a torque wrench. A
number of factors will affect torque output from one
job to another. Final torque adjustment should be
made at the job through a of series of gradual
increase. Always start below the desired torque and
work upward.
4. Adjust the bit torque by changing the driving in
length of the adjust ring at the end.
5. The relationship between torque scale and bit torque
is as shown Ring, in the torque diagram. The figures
of torque scale do not indicate bit torque values.
However, the clamping torque of screw itself is
different form type, size, material of the screw and
the material of its mating part. Use it as standard to
obtain an appropriate clamping torque.
6. The (Return torque method) in which once-clamped screw is returned with torque
wrench or the like is available as one of torque control methods however, note that the
measured values by the return torque method generally appear in 10%~30% lower
than the actually clamping torque.
7. The torque checker measures the torque of screwdriver. The clamping torque of screw
itself is different from the clamped conditions. Understand the correlation between
clamping torque values and the torque checker values perform the torque control
properly.
4. Description of Operation
5. Torque Adjustment Operation

BSD-1200 Series
1. Also in reverse rotation, the clutch is turned off in such manner as in normal rotation,
stopping the motor running. Accordingly, when the screw tightened at a large torque,
set it to a higher torque scale.
2. The number from zero to eight on the Torque Scale are reference number only and not
an indication of actual torque output.
1. BIT Type :No. 00 ....Bit use in dia 1.3~1.8mm screw
No. 0.....Bit use in dia 1.6~2.0mm screw
No. 1.....Bit use in dia 2.0~2.6mm screw
No. 2.....Bit use in dia 3.0~4.0mm screw
BSD-1000 withBIT 1#&2# 1Pce.Each
BSD-1200 withBIT 1#&2# 1Pce.Each
2. Suspension rack and Torque fixing ring acceptable for use with the tool are available from
KILEWS catalogue.
6. Accessories
CAUTION

BSD-1200 Series
Maintenance and Inspection:
1. The screw driver must be operated in top condition. one day working hour must be not
more than eight hours.
2. Periodically check for wear of motor carbon brush, one day for eight hours use is
normal, replace it after every five to six months.
3. Please note don’t let the motor get over heated, every minute use 10~15 screws to
operate.
4. The frequency use of this electric screw driver is over than eight hours a day, still it
needs periodically testing and treatment. Every 5-6 months.
5. Inspect tool cords periodically and if damaged, have them repaired by an authorized
service facility. Inspect extension cords periodically and replace if damaged.
6. Do not remove any labels. Replace any damaged label.
1. The use of other than genuine KILEWS replacement parts may Result in decreased
tool performance and increased maintenance, and may invalidate all warranties.
2. All repairs and maintenance of this tool and its word must be performed by an
authorized service center.
3. KILEWS is not responsible for customer modification of tools for applications on which
KILEWS was not consulted.
4. Repairs should by made only by authorized, trained personnel. Consult your nearest
KILEWS authorized service center.
5. It is the responsibility of the employer to place the information in this manual into the
hands of the operator.
DO NOT ATTEMPT TO REPAIR THIS
ELECTRIC SCREW DRIVER
SAVE THESE INSTRUCTIONS
DO NOT DESTROY
7. Servicing
CAUTION
CAUTION


NO PARTS NO PARTS NAME-E Q'ty NO PARTS NO PARTS NAME-E Q'ty
1 AA50001-2 CORD 1 26 GH20241 GEAR PLANET 8
2 CJ20011 SUSPENSION RING 1 27 GG20271 GEAR SEAT 2
3 CB15021 HOUSING-UNDERSIDE 1 28 G20101 GEAR OF CENTER 1
4 CA15101 HOUSING-UPSIDE 1 29 GA30311-5 GEAR CASE 1
5 CC20031-3 TRIGGER 1 30 GN30321 MAIN BEARING 1
6 CK20051 TRIGGER SPRING 1 31 GC20301 CAM 1
7 HB50073 START SWITCH 1 32 GP30351 STEEL BALL-4MM 2
8 HA20091-4 CHANGEOVER SWITCH 1 33 GD30381A SHAFT A-TYPE 1
9 CI30212 SWITCH CAP FOR 1000 1 GD20321-3 SHAFT B-TYPE 1
CI30211 SWITCH CAP FOR 1200 1 GD20321-2 SHAFT C-TYPE 1
10 CH20102F SCREW 3 GD20321 SHAFT AD-TYPE 1
11 MO15121-1 MOTOR ASSEMBLY 1 34 GP20331 STEEL BALLS FOR "A&AD" TYPE 2
12 EB33610-2 CERAMICS CAPACITOR 1 GP21291B STEEL BALLS FOR "B&C" TYPE 2
13 EF51431 CAPACITOR 1 35 GF20341 WARRING PLATE FOR A,C,AD TYPE 1
14 MD20151 BRUSH CAP 2 GF20341B WARRING PLATE FOR B TYPE 1
15 MC71411-1 CARBON BRUSH 2 36 GE20351-1 WARRING SPRING FOR 1000L 1
16 M10308 MOTOR TOP COVER 1 GE20351 WARRING SPRING FOR 1200L 1
17 ME20181 ARMATURE BEARING 2 37 GY30421 WARRING SPRING BASE FOR A,C,AD 1
18 MH15191 ARMATURE 1 GY30421B WARRING SPRING BASE FOR B TYPE 1
19 MJ15631-1 MOTOR YOKE ASSEMBLY 1 38 GK20231B C-RING FOR B TYPE 1
20 MB20221 MOTOR END COVER 1 39 GB30441-10 CLUTCH CASE FOR A,C,AD TYPE 1
21 MA20211B ASSEMBLING SPRING 2 GB30441-7A CLUTCH CASE FOR B TYPE 1
22 MK20131-1 FUN 1 40 GO20391 BIT SPRING FOR A,C,AD TYPE 1
23 GZ22141-1A CLUTCH ASSY 1000LA 1 GO20391B BIT SPRING FOR B TYPE 1
GZ22141-1B CLUTCH ASSY 1000LB 1 41 GJ30461 BIT SLEEVE FOR A,C,AD TYPE 1
GZ22141-1C CLUTCH ASSY 1000LC 1 GJ3046B BIT SLEEVE FOR B TYPE 1
GZ22141-1AD CLUTCH ASSY 1000LAD 1 42 GQ30471 “C” RING FOR A,C,AD TYPE 1
GZ22141-2A CLUTCH ASSY 1200LA 1 GQ21361 “C” RING FOR B TYPE 1
GZ22141-2B CLUTCH ASSY 1200LB 1 43 GL30481-5 TORQUE ADJ PINS 4
GZ22141-2C CLUTCH ASSY 1200LC 1 44 GM20431-1 TORQUE ADJ RING 1
GZ22141-2AD CLUTCH ASSY 1200LAD 1 45 GS30501 “C” RING FOR GM21381 1
24 GK20231 “C” RING 146 GN30435 MAIN BEARING 1
25 GI20251-1 IRON WASHER 1 47 CD20111 COUPLER 1
48 ML50571-2F MOTOR TOP COVER ASSEMBLY 1
BSD-1000LA/B/C/AD , BSD-1200LA/B/C/AD


NO PARTS NO PARTS NAME-E Q'ty NO PARTS NO PARTS NAME-E Q'ty
1 AA50001-2 CORD 1 24 GK20231 “C” RING 1
2 CJ20011 SUSPENSION RING 1 25 GI20251-1 IRON WASHER 1
3 CB15021 HOUSING-UNDERSIDE 1 26 GH20241 GEAR PLANET 8
4 CA15101 HOUSING-UPSIDE 1 27 GG20271-G GEAR SEAT 1
5 CC20031-3 TRIGGER 1 28 GG20261-G GEAR SEAT 1
6 CK20051 TRIGGER SPRING 1 29 GA30311-5-G GEAR CASE 1
7 HB50073 START SWITCH 1 30 GN30321 MAIN BEARING 1
8 HA20091-4 CHANGEOVER SWITCH 1 31 GC20301-G CAM 1
9 CI30212 SWITCH CAP FOR 1000 1 32 GP30351 STEEL BALL-4MM 2
CI30211 SWITCH CAP FOR 1200 1 33 GD20321-1-G SHAFT D-TYPE 1
10 CH20102F SCREW 3 34 GP20331 STEEL BALLS FOR "D" TYPE 2
11 MO15121-1 MOTOR ASSEMBLY 1 35 GF20341-G WARRING PLATE FOR D TYPE 1
12 EB33610-2 CERAMICS CAPACITOR 1 36 GE20351-1 WARRING SPRING FOR 1000L 1
13 EF51431 CAPACITOR 1 GE20351 WARRING SPRING FOR 1200L 1
14 MD20151 BRUSH CAP 2 37 GY30421-G WARRING SPRING BASE FOR D 1
15 MC71411-1 CARBON BRUSH 2 38 GB30441-10-G CLUTCH CASE FOR D TYPE 1
16 M10308 MOTOR TOP COVER 1 39 GO20391 BIT SPRING FOR D TYPE 1
17 ME20181 ARMATURE BEARING 2 40 GJ30461-G BIT SLEEVE FOR D TYPE 1
18 MH15191 ARMATURE 1 41 GQ30471 “C” RING FOR D TYPE 1
19 MJ15631-1 MOTOR YOKE ASSEMBLY 1 42 GL30481-5 TORQUE ADJ PINS 4
20 MB20221 MOTOR END COVER 1 43 GM20431-1-G TORQUE ADJ RING 1
21 MA20211B ASSEMBLING SPRING 2 44 GS30501 “C” RING FOR GM21381 1
22 MK20131-1 FUN 1 45 GN30435 MAIN BEARING 1
23 GZ22141-1D CLUTCH ASSY 1000LD 146 CD20111 COUPLER 1
GZ22141-2D CLUTCH ASSY 1200LD 147 ML50571-2F MOTOR TOP COVER ASSEMBLY 1
BSD-1000LD , BSD-1200LD

®
BSD-32P
No. PARTS No. PARTS NAME. Q.TY
1 P11013 HOUSING 32V 40W FOR BSD-32P 1
2 EG50101-14 PCB POWER SUPPILY FOR BSD-32P 1
3 A10105-3 CORD 2C× 1.5m 1

This manual suits for next models
4
Table of contents
Other BSD Power Tools manuals
Popular Power Tools manuals by other brands
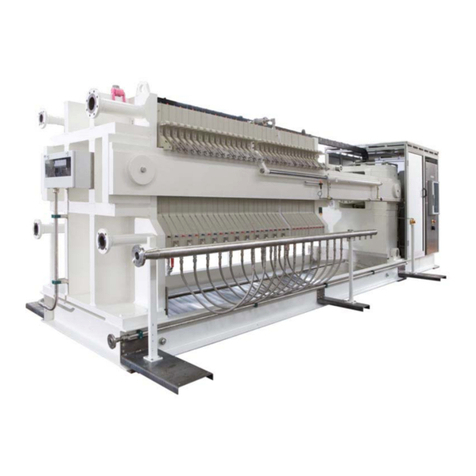
Putsch
Putsch PKF 100 NG-2 operating instructions

Chicago Pneumatic
Chicago Pneumatic Quiet CP7830Q Operator's manual
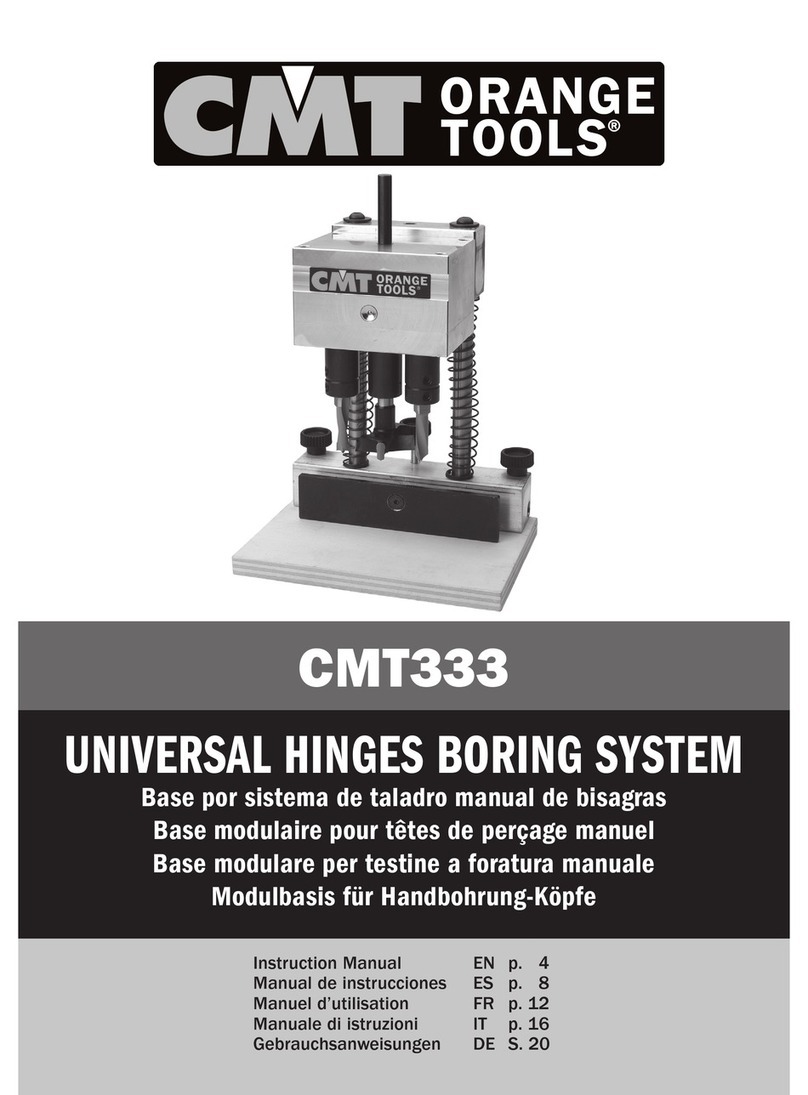
CMT ORANGE TOOLS
CMT ORANGE TOOLS CMT333 instruction manual

Cornwell Tools
Cornwell Tools CAT1000MRRG quick start guide
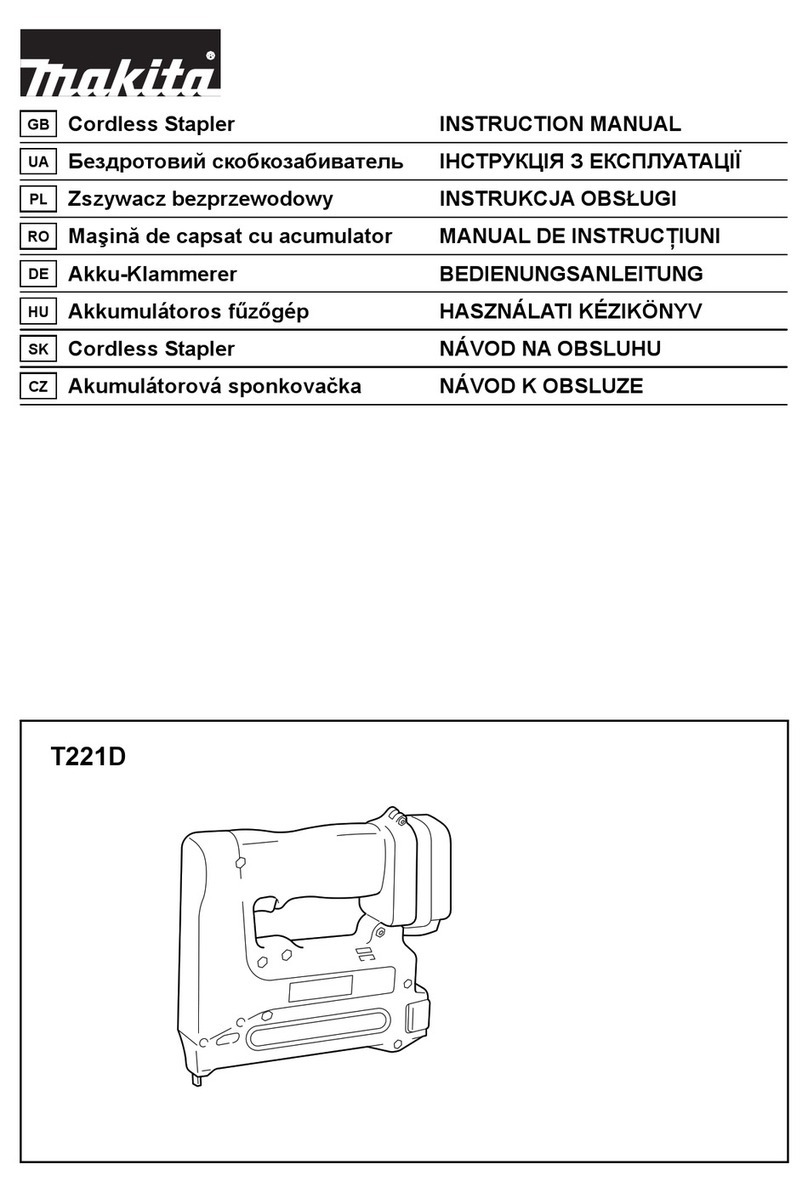
Makita
Makita T221D instruction manual
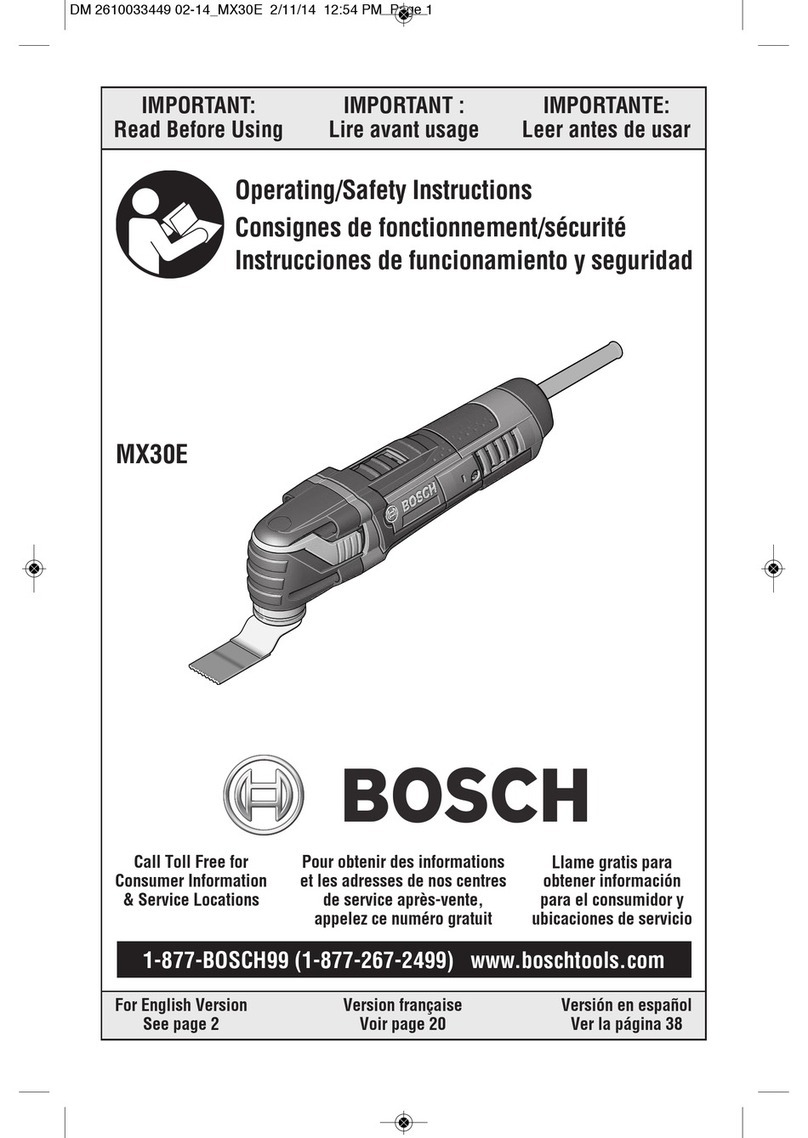
Bosch
Bosch MX30E Operating/safety instructions