Comet Models LCP13 User manual

This pack contains sideframes, brake gear, wheel balance weights, cylinders, coupling and connecting rods,
valve gear, crossheads and pony truck to produce a detailed chassis of the correct scale dimensions and
appearance which can be used as a substitute for a kit or RTR chassis. A separate fret of 00 spacers is
included, which can be exchanged for EM (LS10) or P4 (LS60) by returning them to us in a stamped, self-
addressed envelope. We recommend the Mashima MH1624 motor with our gearbox GB1 for this model, and
can supply the latter together with Markits wheels if required.
As supplied the chassis is suitable for the Bachmann RTR model. It can be modified to fit the former Lima
RTR model or the DJH and SE Finecast kits as suggested below. This should be undertaken with care and
good pre-planning, especially as regards body fixings and ride height.
DJH: This is almost a direct fit. For 00 the height of the upper section of the frames may need to be reduced
in order to clear the underside of the boiler. Slots will be required across the underside of the cast running
plate where the boiler curve intrudes in order to allow the top of the cross frame assemblies to fit.
SE Finecast (original): The frames need to be shortened by 2.5mm at the front and 1mm at the rear. The
brace across the body just behind the cylinder position must be removed and the underside of the running
plate smoothed off. The small steps on the front under curve should be filed away.
Lima: The frames need to be shortened as for the Finecast body above. The dragbeam should be cut away
allowing the rear of the frames to pass through. A new dragbeam can be fashioned from brass and soldered
across the back of the frames.
In 1931/2 five of the class were modified with Lentz rotary cam poppet valve gear. In 1953 they were again
modified, this time with the Reidinger version of the rotary cam gear. The modified engines were
13118/22/4/5/9, later becoming (4)2818/22/4/5/9. Parts for both versions are included.
Etched parts list
Please note that part numbers 15,19,20,26-36 and 38-42 apply only to the Walschaerts valve gear version
and are not present in this kit. A chassis kit for this version is available as LCP14.
Fret 1 Frames and brake gear
1Frames x2 7Brake hanger overlays, front x2
2Spring overlays x6 8Brake pull rods, front x2
3Running plate support brackets 00/EM/P4 x6 9Brake pull rods, rear x2
4Brake hangers, centre and rear x4 10 Brake pivot brackets, intermediate x2
5Brake hangers, front x2 11 Brake pivot brackets, front x2
6Brake hanger overlays, centre and rear x4 Balance weights, front and rear x4
Fret 2 Frame parts and pony truck
14 Spur gearbox bracket 55 Pony truck 'A' frame 00
16 Slidebar support bracket 56 Pony truck 'A' frame EM/P4
17 'D' brackets x2 57 Pony truck sides x2
18 Return crank gearbox steady rod bracket 58 Pony truck side overlays x2
21 Return crank gearbox steady rod bracket 59 Full thickness washers x4
reinforcements 00/EM/P4 x2 60 Half thickness washers x2
Fret 3 Rods and slidebars
12 Coupling rods x2 24 Connecting rods x2
13 Coupling rod overlays x2 25 Connecting rod overlays x2
22 Slidebars x2 37 Return cranks x2
23 Slidebar steps x2
Fret 4 Cylinders and motion details
43 Spur gearbox support shelf 50rd Cylinder cover plate, round (Reidinger) x2
44 Lubricator drive bracket 51 Cylinder cam box cover x2
45 Cylinder front 52 Lubricator drive crank
46 Cylinder rear 53F Cylinder front cover plate x2
47 Return crank gearbox steady rod links x2 53R Cylinder rear cover plate x2
48 Return crank gearbox mounting plate x2 54 Return crank gearbox steady rods x2
49 Return crank gearbox cover plate x2 Balance weights, centre x2
50lz Cylinder cover plate, square (Lentz) x2
Whitemetal castings
Cylinder sides x2 Return crank gearbox x2
Sandboxes, front x2 Bevel gearbox x2
Sandboxes, centre x2 Universal joints x6
Sandboxes, rear x2 Steam pipes x2
Reversing rod support bracket Vacuum release valves x2
Lost wax brass castings
Spur gear box Crossheads x2
Turnings
Universal joint shrouds x6
Please note that all bends should be made with the half-etched lines to the inside (unless stated otherwise)
and reinforced with a fillet of solder. The kit is designed to be built up as a set of sub-assemblies and finally
brought together as a running chassis. At several points in the process you are strongly advised to check for
fit and function before proceeding. All references to Left and Right hand are given as from the cab looking
forward.
Assembly Instructions
Chassis
1. The frames may be assembled rigid, or with sprung axles using our hornblocks and springs code
LS55. If you wish to spring the chassis cut through the spring hangers using a piercing saw and
remove them together with the centre portion of etch within the hornway. The sides of the hornways
are etched at approximately 5.85mm apart to ensure that any slight variations in the width of the
machined grooves in the hornblocks do not result in any one of them having a loose fit within the
hornway. Each hornway must be carefully dressed with a file to achieve a good sliding fit to each
hornblock, which should then be marked up or placed into a labelled bag to ensure it is assembled
only into the hornway to which it has been precisely matched. Take time and care over this stage,
removing material slowly and from each face equally. The hornblock must drop in freely under gravity
but must not show any fore and aft play which might cause the coupling rods to bind. This might
sound daunting, but the patient builder will be rewarded with a chassis having superior ride, track
holding and traction compared to an unsprung chassis.
2. For rigid axle assembly, carefully open out the axle bearing holes in the frames until the bearings are
a close fit, ensuring the bearing flanges fit snugly against the frames. This is best done using a five
sided broach. If you are using our chassis jigs (see below), DO NOT solder the bearings in place at
this stage. Open out the holes for the brake cross-shafts to 0.75mm.
3. Recommended fixing points for the Bachmann body are under the smokebox and the underside of
the firebox backhead, as indicated in sketch 1. The backhead should be permanently fixed with
cyanoacrylate glue before attempting to mount the body on the chassis. The frames are supplied with
the forward extension over the pony truck. For this conversion the front section should be cut off as
indicated on the fret and in sketch 1.
4. If you are springing the chassis drill out the holes at each side of the hornways and those in the
separate spring etches to 0.5mm as shown in sketch 2. The suggested layout for the frame spacers
is shown in sketch 1. Those spacers which are used for attaching sub-assemblies should have the
nuts soldered to them as shown before fixing them to the frames. For the cross frame assemblies
ensure that the spacers are soldered slightly below the designated positions, then insert packing to
Components recommended to construct a
complete chassis
6 Markits 5'6" driving wheels (WH205B)
3 axles, 6 crankpins and washers (RM2)
1 set 3'6" 10 spoke bogie wheels (WH33)
Mashima MH1624 motor and GB1/20
gearbox
LCP13 Chassis pack for LMS
Hughes/Fowler Crab 2-6-0
(Rotary Cam valve gear)

give the exact height required. Temporarily fit the driving wheels to check the ride height. You might
need to remove some material from inside the rear splashers under the cab if the wheels have
overscale flanges. Solder the spacers to one side of the chassis then assemble by clamping the
other side to the first using the wheelsets to check the alignment before soldering the second side
frame. This crucial stage of the assembly can be achieved more easily and with greater accuracy by
using our frame assembly jigs (code LS16 for 00, LS17 for EM and LS61 for P4); full instructions are
provided with them. If you are springing the chassis please note that you will need a set of four
turnings code LS59 which are intended to locate in the hornways during this stage in the assembly
5. For a sprung chassis insert the springs and hornblocks, ensuring that they are placed into their
correct hornways only. Note that the grooves in the hornblock are not on the centre line. This allows
you to choose a greater or lesser amount of sideplay on each axle. Use 0.45mm wire to locate the
spring detail and solder in place using a minimum of flux. This captures the hornblock and the
protruding centre shackle should ensure that the bottom of the hornblock is slightly above the bottom
edge of the chassis giving approximately 1.0mm of movement only. Do not be tempted to file too
much material from the top of the centre shackle. Greater travel should not be necessary and there is
then a risk that the spring could become dislodged if there is too much downward travel.
6. Fold up and solder in place the intermediate (10 L/R) and rear (11 L/R) brake pivot brackets (sketch
3), then solder lengths of 0.7mm wire through the brake hanger holes. Solder the brake overlays to
the brake rear etches (sketch 4) then thread on and solder in place. Their alignment is made easier if
something of suitable thickness is used to space out the brake shoe from the frame, with a wheelset
fitted to ensure correct spacing relative to the wheel treads.
7. Lengths of 0.7mm wire are next threaded through the bottom brake hanger holes on one side of the
chassis, through both sets of brake pull rods (8 front and 9 rear), ensuring that they are the correct
way round, and then through the second set of brake hangers. Solder the wire to the brake hangers,
then slide the pull rods outwards to line up with the inner edges of the frames and solder them to the
wire. If you prefer greater prototype accuracy at the expense of greater strength you can decide to
solder the two pull rods together and fix this assembly along the chassis centreline so that the lever
at the rear end aligns itself inside the brake pivot brackets. However, as well as being more fragile,
this will also make it more difficult to arrange pick up from the underside of the chassis.
8. Select the appropriate set of running plate support brackets (3 00, EM, or P4) and solder them into
the six indicated slots in the frames as shown in sketch 1. Ensure that they are at right angles and
level across the top. Solder in the lubricator pivot bracket (44) in line with the outer end of the running
plate supports. Check the fit of the chassis in the body.
For all the cross frame assemblies it is important to ensure that they do not foul the underside of the running
plate when fitted into the body. It is better that they start low and are packed up on final assembly. They
should fit snugly under the body without causing it to rock. This should be checked constantly during the
assembly process.
9. See sketch 5. Dependent on your chosen gauge remove the break off sections of the spur gearbox
mounting bracket (14) as shown. Ensure that the narrower section will pass between the frames. The
wider section fits into the slots in the top of the frames. Carefully fold over the two sections with the
half-etch to the outside. Ensure that they line up and pinch them closed. Fold out the mounting tab to
right angles then run a bead of solder around the edges and file smooth. Slot the unit into the frames
and check for fit in the body. Note that the mounting tab for this sub-assembly will not be in contact
with its spacer. See step 11.
10. See sketch 6. Drill out to 1.0mm the holes in the slidebar support bracket (16) for the spigot on the
bevel gearbox. Remove the break off sections, fold up and solder as in step 9 above. Solder in the
two 'D' brackets (17) [these served no function on the RC engines but were left in place when the
engines were modified]. Ensure the slots in the outer part of the bracket and the bevel gearbox spigot
hole are clear of solder. Check the fit as above but leave it in place.
11. With the slidebar support bracket in place refit the spur gearbox mounting bracket and secure them
both to the frame spacer with an M2 screw. Check the fit to the body. The two units should be level
with the running plate and, ideally just short of contact with it. When satisfied tack solder the
mounting tabs to each other (but not to the spacer) remove the assembly and complete the joint.
12. Fold up the spur gearbox support shelf (43), shape the tang to follow the edge of the left hand side of
the bracket and solder it on with the upper edge of the triangular section level with the bottom of the
outer edge of the bracket. Carefully file away the excess from each side of the tang until it is the
same width as the thickness of the bracket itself. Fix the bevel gearboxes into both sides of the
slidebar support bracket then fix the spur gearbox to its support with its lower rear facing extension
against the front of the bevel gearbox.
13. See sketch 7. Remove the break off sections of the return crank gearbox steady rod bracket (18) as
in step 9 above. Fold the two sections together with the half-etched line to the outside ensuring that
they are aligned. Fold out the mounting tab to 90º then fold back the front and rear facing extensions.
Run solder around all the edges and clean up with files. Solder in the reinforcements (21 00, EM or
P4). Solder on the steady rod bracket overlays (47R/L) on the outside of the extensions ensuring
they are aligned along the edges. File down the upper projection until the bracket fits snugly under
the running plate.
14. See sketch 8. Open up the piston rod holes in the cylinder rear section (46) so that the piston rod on
the lost wax brass crosshead will pass through. Solder the rear end cover plates (53R) onto the rear
face using the half-etched line as a guide and aligning the holes in each part. Drill out the holes to
0.75mm. Solder the front end cover plates (53F) onto the front section (45). Drill out the wire locating
holes in both sections to 0.5mm. Fold up, then pass 0.45mm wire through both sections and solder
them together. Cut off the excess wire and clean up the assembly. With the side castings temporarily
in place check the fit to the body. There should be a slight gap between the top front of the sides and
the running plate.
The frames do not need to be handled again until final assembly so they can now be painted and set aside to
harden.
15. See sketch 9. Fold up the slidebars (22R/L) as shown and solder the two halves together. Fit the
steps (23R/L) using 0.45mm wire through the holes to locate them. [Photos show that the RC
engines had plate slidebar steps but if a particular engine is to be modelled this feature should be
checked]. Leaving the tiebar at the back end in place for now, thoroughly clean the slidebars of
excess solder. This is important for smooth operation of the crossheads. Remove the tiebar at the
front end and insert the projections at the front of the slidebar assembly through the square holes in
the rear of the cylinders and solder in place. Ensure that the hole on the extreme edge of the rear
face just above the slidebars is clear of solder.
16. Carefully remove the tiebar at the rear of the slidebar assembly. Reduce the length of the piston rod
to 21mm between the pivot and the end of the rod. Open up the slots in the crosshead until it will run
smoothly in the slidebars without opening the gap between them. Laminate the two halves of the
connecting rods (24R/L and 25R/L) and drill out the small end to take the pin and the large end for
the crankpin (1.1mm). See sketch 10. Fit the connecting rods into the hollow at the back of the
crosshead, pass the pin through from the back and solder in place on the front.
17. See sketch 11. File smooth one face of the return crank gearbox castings then remove the front oil
pot. Drill out the hole in front 0.75mm to a depth of about 2mm. Solder the castings to the support
plates (48). With the half-etch on the tang to the outside, roll the half-etched section over the top of
the gearbox then fold the triangular tag at the top to the vertical. Drill out the hole in this tab to
0.5mm. Fit the access plate (49) in the centre of the gearbox.
At this point all the sub assemblies are complete and the chassis can now be fully assembled.
18. See sketch 12. Fit the balance weights (F front, M middle and R rear) to the wheels. Fit the
crankpins. Laminate the coupling rods (12R/L and 13R/L). It is recommended that the rods are split
rather than rigid as this aids in setting up the chassis and gives greater freedom when running. There
is the option to assemble them to pivot on the knuckle joint or on the crank pin. See sketch 13. Fit the
wheels to the chassis and then the coupling rods. The rods can be held in place on the crank pins
with short lengths of plastic insulation cut from electrical wire. Check that the chassis is free running.
With split rods the process can be carried out as two separate sets of four-coupled wheels. When
satisfied the motor and gearbox can be fitted and the chassis checked out under power. Check again
the fit to the body. When thoroughly satisfied, retain the rods on the front and rear crankpins with
their washers. Do not trim back the right hand rear crank pin as it will carry the lubricator drive crank
–see step 23.
19. Bolt the two support bracket assemblies to the chassis. Fit the crossheads into the slidebars then
slide the ends of the slidebars and the connecting rods through the slidebar support bracket, seat the
cylinders in place and bolt them down. Fit the large end of the connecting rod over the middle axle
crank pin with, if working in 00, a spacing washer between it and the coupling rod. Retain the
connecting rod with plastic insulation and check the chassis for free running and a final fit to the
body. Remove the small end boss from the return cranks (37) and use them to retain the connecting
rods. These will serve to keep the return crank gearbox away from the connecting rod. There should
be no 'lead' so that the free end is in line with the centre of the axle.

Parts are provided for both the Lentz and Reidinger versions The Lentz gear had shrouded universal joints
which are the turned brass double coned items. The Reidinger engines had unshrouded universal joints
which are provided for as castings. These latter should be drilled through 0.75mm.
20. See sketch 14. For the cam drive shafts cut two 50mm lengths of 0.7mm brass wire and fix one end
of each into the holes drilled in the return crank gearboxes. Thread one of the appropriate universal
joint parts down against the gearbox ensuring that it is the correct way round and fix in place. Thread
a second part down the wire then pass the wire through the slot in the slidebar support bracket.
Thread on a third part the other side of the bracket then pass the front end of the wire through the
hole located on the extreme outside of the cylinder rear just above the slidebars. Align the centre of
the gearbox over the centre of the axle then fix the wire in place in the support bracket with the
universals each side hard up against it. There should be no need to fix the front end of the wire to the
cylinders but it should be cut off just inside. Drill out the hole in the rounded end of the return crank
gearbox steady rod (54). Locate it over the triangular tab on the box itself with a short length of
0.45mm wire. Pivot the loose end over the hanging link on the steady rod support bracket overlay, fix
both ends in place then cut off the excess length.
21. See sketch 6. Thread a 15mm length of 0.7mm wire through the hole in the top of the left hand
cylinder rear until it is touching the forward facing extension on the spur gearbox and solder in place
inside the cylinder. Repeat for the other side with a 25mm length of wire but this time locate it on the
centre of the bevel gearbox. There should be no need to fix these rods to the gearboxes as this will
then allow the cylinders to be removed without disturbing the rest of the motion.
22. See sketch 8. Add the details to the cylinder sides. Note that these will become handed when
completed. Drill through the forward dimple 1.5mm. Fix the access plate over the rear dimple using
part 50lz for the Lentz and 50rd for the Reidinger versions. Fix the cam box cover (51) over the upper
boss with the projection vertical. File a slight groove in the inside face of the castings to clear the end
of the drive shaft. Attach the cylinder sides to the cylinder assembly ensuring that they are fully
against the edges of the front and rear plates.
23. Solder the lubricator drive crank at the extreme end of the right hand rear crank pin so that it is
aligned with the axle centre i.e. with no 'lead'. Form a length of 0.45mm wire as shown in sketch 15
and hook the ends into the crank and the lubricator drive support bracket and squeeze the ends over
to retain the wire.
24. See sketch 16. Select the appropriate pony truck ‘A’ frame (55 for 00, 56 for EM and P4). Fold the
strengtheners and the box section to right angles and reinforce with solder. Fit the sides (57) to the
box section by means of the locating slots and tabs and solder in place. Solder on the overlays (58R/
L) ensuring that they are aligned with the sides. Check that the pony wheel axle will drop into the slot
and fettle if necessary to achieve an easy fit. Sufficient sideplay has been allowed for variations
according to the wheel sets chosen and a selection of half and full depth washers is provided (59 and
60). For fixed wheelsets these should be soldered over the slot and the bottom filed away to enable
the axle to drop in. Solder a washer over the oval hole at the back of the ‘A’ frame and adjust it until
the wheels are in the correct position with reference to the wheel arch on the body. Retain the wheel
set in place with 0.45mm wire through the holes in the bottom of the box section and fix with a spot of
solder. Shape the guard irons to align with the wheel treads. If desired, a piece of phosphor bronze
strip formed into a V shaped spring can be attached to the tab, and the holes in the top of the box
section can be used to locate side control wires.
Modifications to the loco body.
25. Remove both lubricators by drilling 0.75mm through the two pegs under each of them and carefully
lever them off. Retain them, as they will be re-used. Remove the square section reversing rod and
discard it. There are two holes to be drilled in the body for the new reversing rod. As they are difficult
to get to and are subject to some adjustment they should be drilled oversize and at an angle to avoid
damage to the body. It is best to start with a small pilot hole, 0.75mm maximum, then open them out
to 1.2mm for clearance and alignment of the rod in its proper position.
26. Refer to sketch 17. Drill the casing on the left hand side of the cab 2mm down from the top and 1mm
from the side. Drill the running plate 1mm under the upper running plate and 1.5mm in. Drill out the
hole in the top of the reversing rod support 1mm. Cut a 70mm length of 0.7mm brass wire and pass it
through the hole in the running plate. Thread on the reversing rod support with the top pointing away
from the body then pass the wire through the hole drilled in the cab casing.
27. See sketches 6 and 17. Temporarily refit the chassis, allowing the rod to pass into the slot in the top
of the slidebar support bracket. The rod should now be approximately in line with the angled rearward
extension on the spur gear box. The position may be adjusted if required by further opening up the
holes. The reversing rod support should be centred on the joint between the boiler and firebox. If in
this position the rod has an upward curve, some of the mounting plate on the bottom of the support
can be filed away. When satisfied, fix the support to the running plate and fix the ends of the rod in
the running plate and the casing. Shorten the section under the running plate so that it is just in
contact with the spur gearbox extension.
28. See sketch 17. Fix the vacuum relief valves to the back of the steam pipes and fill in the hole at the
front. Any gaps left by the oversized holes for the reversing rod and the lubricator peg holes can be
filled now as well. Fit the steam pipes to the running plate alongside the smokebox as shown. Refit
the lubricators on the right hand side of the running plate but with the 'operating wheel' facing
outwards.
29. Fit the sandboxes to the underside of the running plate with reference to the fillers on the top,
ensuring that they do not interfere with either the removal or running of the chassis. Note that the rear
sand box filler is off centre towards the front of the engine.
Our preference is for wiper pick-ups made from 28swg phosphor bronze wire as per sketch 18. The wire is
soldered to PCB strip which is bolted to a frame spacer. We recommend that, if possible, you arrange for the
pick-up to be “bolt-on:” since this allows for easy removal and adjustment of the wire wipers. Pack LS23
provides all the parts.
Comet Models is part of Wizard Models Limited, PO Box 70, Barton upon Humber DN18 5XY
Tel 01652 635885, web www.wizardmodels.co.uk, e-mail andrew@modelsignals.com
© Wizard Models Limited 2020

Spacer A 10mm x 10mm
Spacer B 10mm X 6mm
Spacer C 6mm X 6mm
Spacer D 6mm X 3mm
GB1
gearbox
Mashima
MH1624
motor
A
BB
C
C
D
D
7
SKETCH 1
SKETCH 6
SKETCH 4
SKETCH 3
SKETCH 2
SKETCH 5
8
Brake hanger holes
Intermediate brake pivot bracket (10). RH
side shown viewed from outside the frame
Rear brake pivot bracket (11). RH side
shown viewed from inside the frame
Spur gearbox
support bracket
Slidebar support
bracket
Tongue for Bachmann
front body fixing
Return crank
gearbox support
bracket
Lubricator drive
mounting bracket
(other side only)
Front brake
pivot bracket
Rear brake
pivot bracket
Running plate
supports
14
P4 width
inside frames.
Break off for
EM and 00
Part 14 formed and
placed onto spacer
in the frames
14
To front
of engine
To front
of engine
14
43
Spur gearbox
support shelf
43
Mounting tabs
overlapped
To cylinder
Bevel
gearbox
‘D’ bracket
17
Spur gearbox
To reverser Front
sandbox
16
Ensure holes and
slots are clear after
folding and soldering Top of triangle
to line up here
Fold 180°
Then fold 90°
Fold 180°with half
etch to the outside
of the fold
Then fold 90° with
half etch to the
inside of the fold
2
8
10
11
9
Spacer for
Bachmann rear
body fixing
Cut off front end
of frames for
Bachmann body
4.5

SKETCH 10
SKETCH 12
SKETCH 11
SKETCH 7
18
To front
of engine
21
47
18
25R/L
48
49
Drill for
drive shaft
FRM
Fold 180°with half
etch to the outside
of the fold
5
SKETCH 9
Front
tiebar
Rear
tiebar
Rod steps from
0.45mm wire
SKETCH 8 53R
53F
46
45
50rd
50lz
51
1.5mm
drill
Plan
Side elevation

SKETCH 17
SKETCH 14
SKETCH 16
SKETCH 15
SKETCH 18
SKETCH 13
Front half
Front half
Rear half
Rear half
A
A
Outer rod
Backing rod.
B
B
To split the rods over the centre crankpin
cut the backing rod at A-A, solder to the
corresponding halves of the outer rods and
connect both halves at the centre crank-
pin.
To split the rods on the knuckle joint first
drill through the half etched centres on the
knuckle and cut the backing rod at B-B.
Solder the inner and outer halves together
then join the front and back halves of the
rods using a pin or rivet (not supplied) so
that the rods are articulated behind the
centre crankpin.
Cylinder
Shrouded
universal
joints on
Lentz gear
Steady rod
link 47
Slidebar
support
bracket
Steady rod
54
Exposed universal joints
on Reidinger gear
4.5
27
58
57
55 or 56
59
59 or 60
Spur gearbox
Slidebar
support
bracket Reversing rod
support bracket
Drill hole 1.0mm
down and 1.5mm
in from edge
Drill hole 2.0mm down
from top and 1.0mm in
from edge of casing
Running plate
support brackets
Lubricator drive
bracket
Rear sandbox
Centre sandbox
Front sandbox
Steam pipeVacuum relief
valve
6mm
Lubricator from
LH side
Lubricator turned around
and replaced in original
position
Other Comet Models Chassis manuals
Popular Chassis manuals by other brands
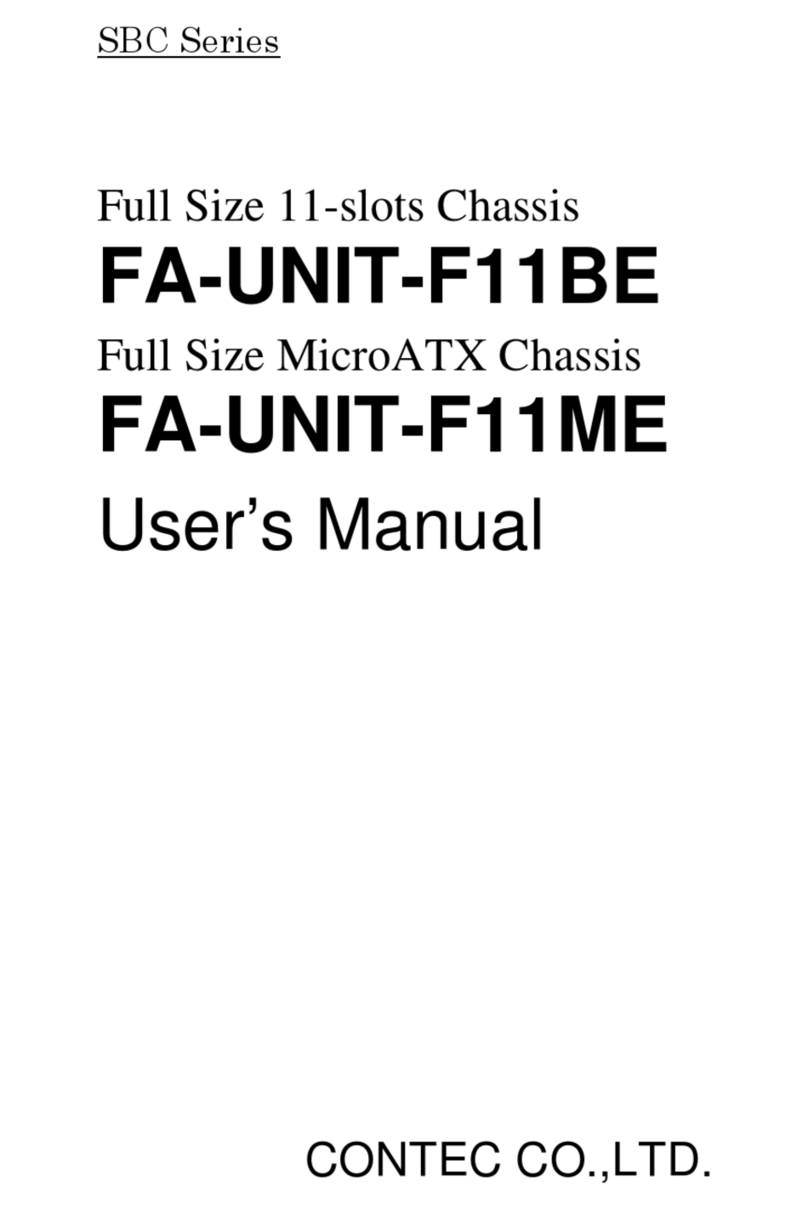
Contec
Contec FA-UNIT-F11BE user manual
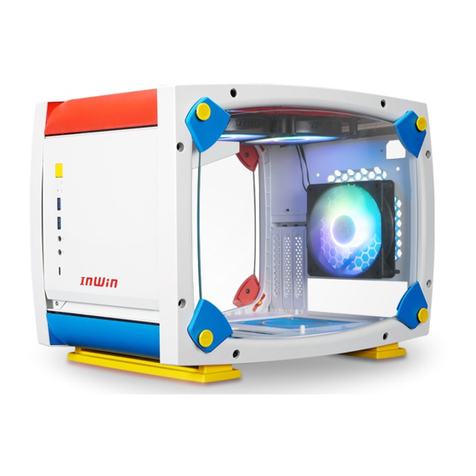
InWin
InWin Explorer user manual
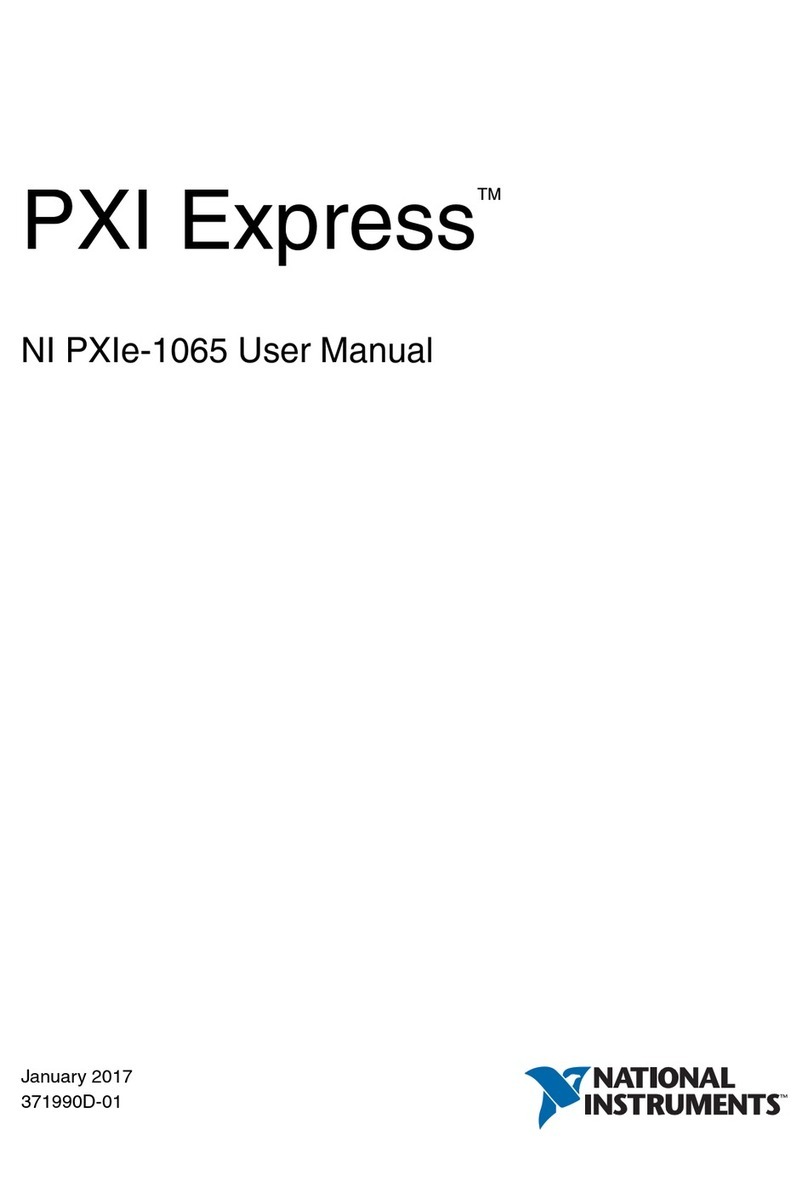
National Instruments
National Instruments PXI Express NI PXIe-1065 user manual
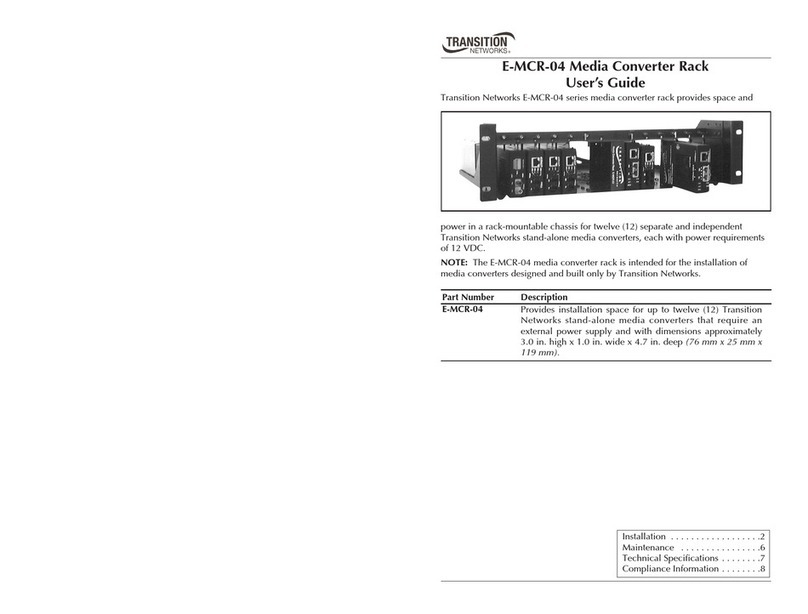
Transition Networks
Transition Networks E-MCR-04 user guide
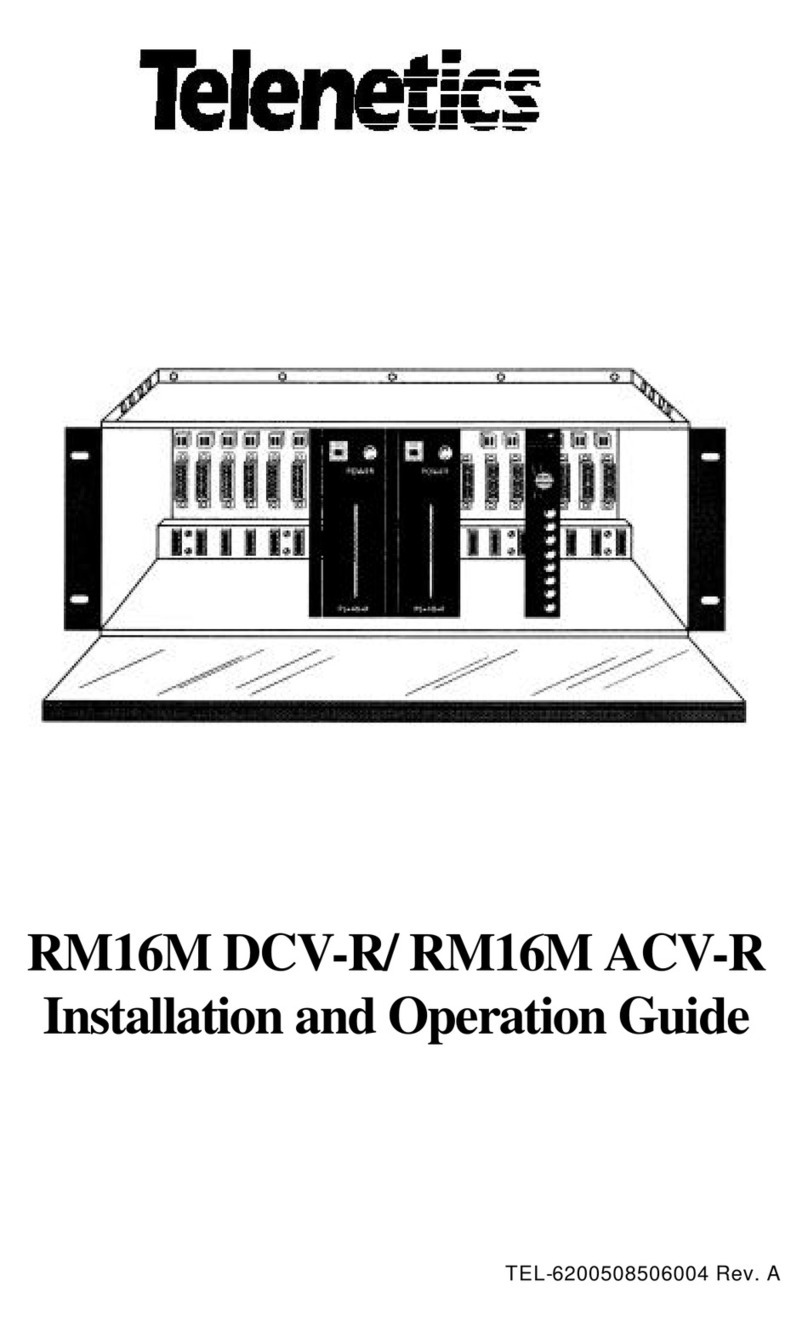
Telenetics
Telenetics RM16M - Versatile Rack Mounting Chassis Installation and operation guide
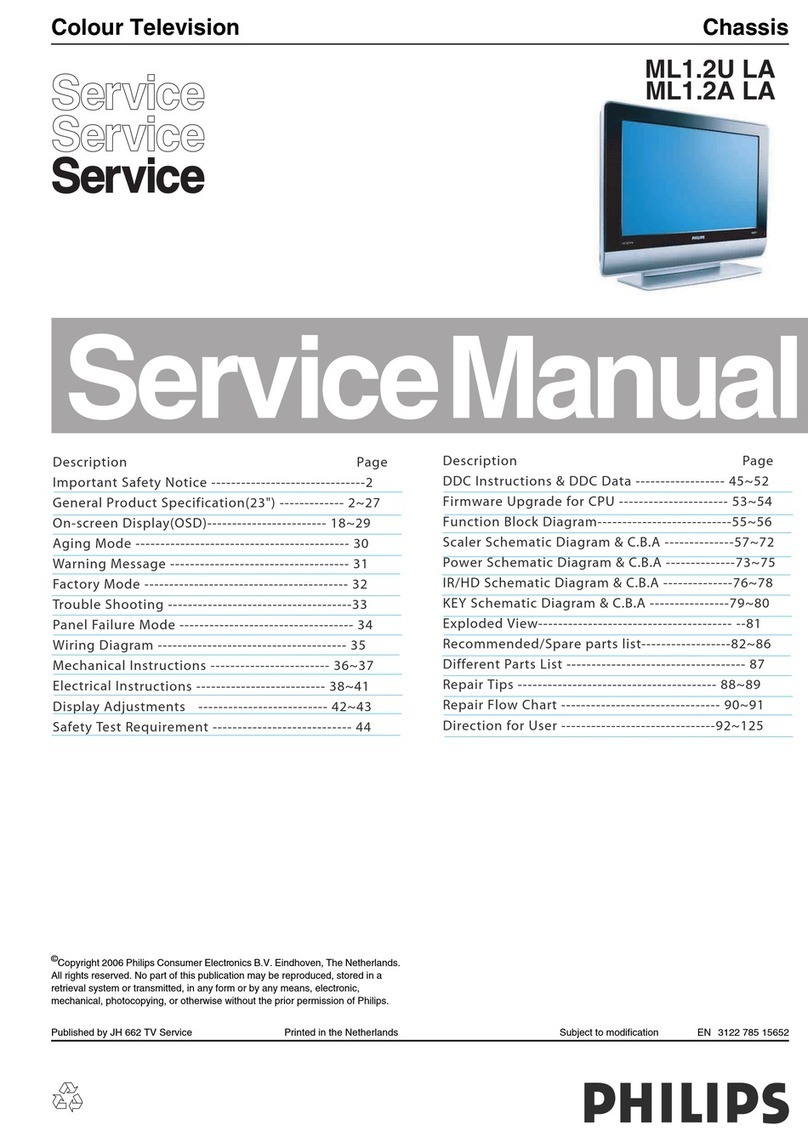
Philips
Philips ML1.2U LA Service manual