Comtherm PHC Series Instruction Manual

+44 (0) 1905 775 783 www.comtherm.co.uk sales@comtherm.co.uk
Installation & Maintenance Manual
PH Burner
Burners, Heaters & Combustion Systems

PH Burner Instruction Manual
Page.1 .............................................GeneralSpecification
Page.2 .............................................GeneralDescription
Page.3 .............................................Installation
Page.4 .............................................Installation
Page.5 .............................................Installation
Page.6 .............................................Initial Light Up (Commissioning guidance)
Page.7 .............................................Initial Light Up (Commissioning guidance)
Page.8 .............................................Initial Light Up (Commissioning guidance)
Page.9 .............................................Initial Light Up (Commissioning guidance)
Page.10 ...........................................Fault Finding Guide
Page.11 ............................................Fault Finding Guide
Page.12 ............................................Fault Finding Guide
Page.13 ............................................Fault Finding Guide
Page.14 ............................................Fault Finding Guide
Page.15 ............................................Fault Finding Guide (Indirect Heaters)
Page.16 ............................................ Parts List (Key)
Page.17 ............................................Suggested Service Program
Page.18 ............................................SuggestedService Program
Page.19 ............................................BurnerService program
Page.20 ............................................Burner Commissioning Record
Additional Commissioning Notes
Index
Comtherm Ltd
Installation & Maintenance Manual
Burners, Heaters & Combustion Systems

The Comtherm and PHC' series of gas burners are designed to fire applications were
fresh or recirculated air is to be heated up to plant requirements. The burners can be installed
in air systems were it is not possible to construct a combustion chamber and install a
conventional type of burner assembly. The burners can be supplied for gap firing or flange
mounted in-line combustion head.
All the air required for combustion can be supplied by an integral combustion air fan mounted
on the burner head or provided that the process air has sufficient oxygen by developing
sufficient pressuredrop through profile plates on an design.
Typical applications; Industrial Dryers, Preheaters, Industrial Spray Booths, Direct Fired ARP
and AHU, Drying and Curing Rooms
The PH and PHC burner is modular with each 300mm section rated at 300kW whilst the PHC
is rated at 600 kW per 300mm section.
The burners are available in and sections which enable the burner to be
constructed to suit the appliance layout and in theory limitless in maximum output.
Typical Flame Lengths at Maximum Duty - 600mm
All valve assemblies on the burners are sized to suit an inlet gas pressure of 17.5 mbar
(natural gas) or 30mbar (LP gases) unless otherwise specified. Burners can be supplied to suit
other gastypes and supply pressures.
Combustion air PressureDrop across burner air wings;
PH 200 Pascals
PHC 300 Pascals
The nozzle mix design of the burner and the progressive air mixing feature of the combustion
head ensure that burners can operate with high turn down capability; turndown ratios up to
40:1 arepossible dependingon burner applicationsand selection.
The PH burner range is designed to always operate with approximately 30% excess
combustion air.
For high - low and modulating gas only burnerswith fixed combustion air.
The PH burner is not availablewith modulating gas and air control.
General Specification
Comtherm Ltd
Installation & Maintenance Manual
Page 01
Burners, Heaters & Combustion Systems

The burner consists of a gas manifold assembly having fuel and air jets designed to produce
effective mixing of the fuel and combustion air hence providing good flame stability.
The manifold assembly is fitted with integral ignition and flame sensor facilities.
The unit comes complete with all the valves and controls required; forming a fully packed, safe
burner assembly.
The valves and controls are pre-piped and mounted on the burner side plate, as illustrated
diagrammatically in document M4. Pressure test points are fitted between valves where
necessary.
The physical arrangement of the burner is shown in diagram form in document M3 (where
applicable).
All the electrical equipment on the unit is pre-wired to a terminal enclosure on the assembly,
as detailed in the burner wiring diagram in document M5.
The electrical operation of the burner is as follows:
When the electrical supply is switched on to the burner and all the control circuits are closed,
the burner light up sequence is initiated.
The burner flame safety sequence control unit (unit A1) receives the electrical start signal and
begins to cycle through an air pre-purgeand light up sequence.
The air pre-purge is for a specified, preset time and allows for dilution of any fuel leakage; to
safeguard against the possibility of explosive fuel/air mixture being present in the burner duct
when the ignition is energized.
After the completion of the pre-purge,the ignition and flame proving period take place.
When the flame signal is proven, the burner sequence control remains in the operating
position until any of the control circuit interlocks are broken or a flame failure (lockout)
condition occurs.
Complete details of the burner light-up sequence including the flame safety control unit (item
A1) will be found in the component data sheet, enclosed. For details on installation and
commissioning, referto pages 3-9.
NOTE: - See pages 16 for key to items referred to throughout this manual. Refer to documents
M!, M3, M4, M5, M9 sent with your contract for specific component manufacturers used on
this equipment.
General Description
Comtherm Ltd
Installation & Maintenance Manual Page 02
Burners, Heaters & Combustion Systems

Before proceeding with the installation of the burner, inspect the burner for any physical
damage that may have occurred during transit, storage or off-loading. Any damage should
be reportedimmediately.
The pipe work or gas valves on the burner should not be used for lifting under any
circumstances, as this tends to pull fittings loose or damage valves, causing leaks during later
operation.
Mount the burner in the firing position, making sure that adequate space is allowed around
the burner for ventilation and that the combustion air inlet is not blocked. Ensure that an
adequate fresh air supply is available for combustion and generalventilation.
Situations where gas from valve and pipe work leaks can collect and form pockets of
combustible gas/air must be avoided.
Ensure that adequate space is allowed around the burner for easy access to all burner
components, pressureswitches, control operatorsetc.
The burner should be securely fixed and the transmission of vibration and heat should be
minimised.
GAS SUPPLY:
Gas piping to the burner should be of sufficient size to provide the correct gas pressure at the
burner valve assembly inlet (see specificationon pageM1).
If in any doubt concerning the size and design of the gas supply pipe work, consult the gas
supply company.
The pressure loss in the gas supply pipe work should be such that the following pipeline
velocities are not exceeded:
Unfiltered supply 20M/s (65.6ft.sec)
Filtered supply (250microns) 45M/s (148ft.sec)
The above stated velocities are based on the avoidance of excessive noise pollution and
erosion.
For low-pressure supplies up to 25 mbar (10 w.c), the pressure drop between the meter and
the burner inlet should normally not exceed 1mbar (0.4 w.c). For high-pressure supplies, this
pressuredropshould not exceed 10%of the available gaspressure.
Installation
Comtherm Ltd
Installation & Maintenance Manual
Page 03
Burners, Heaters & Combustion Systems

A manual shut off valve followed by a union or flangedjoint should beincorporatedin the
Gas supply pipe adjacent to the burner, this valve permits isolation of the supply and removal
of the burner assembly for maintenance purposes.
The manual shut off valve should be easily accessible.
Do not use the burner valve assembly to support the gas supply pipe work. Suitable brackets
or hangersshould be used for this purpose.
Before connecting the gas supply check that the available gas pressure is correct (see
specification in document M1).
Check that the gas supply system has been designed and installed to ensure that during fault
conditions, pressuresin excess of the maximum designratingof the equipmentcan not be
reached.
If the burneris installed in aconfined spaceconsiderationshould be taken forthe fitting of a
vent pipe to the breatherholes of governors.
Vents from governorsmust not be manifoldedand should terminate in a safe place,preferably
above roof level.
Any additional vent pipes that are requiredwill be shown in document M4.
The gas supply pipe will be full of air andwill require purging.
This purging should only be carried out by a suitably qualified gas engineer.
With regardto the soundness (leak) testing and purgingof the supply pipework ensure that a
certificate exists stating that this work has been completed in accordancewith technical
publications EN 746-2.
After completion of the installationwork, the procedurefor testing for gasleaks on the burner
detailed in the manual section pages 10-15, should be completed and any leaks repaired.
The burnershould be left with the manual shut off valve (item V1) in the closed position until
the plant is commissioned by a suitably qualified gas engineer.
Installation (Continued)
Comtherm Ltd
Installation & Maintenance Manual Page 04
Burners, Heaters & Combustion Systems

ELECTRICAL SUPPLY:
Burners can be supplied to suit almost all types of electrical power supply; including all
common industrial three phase (50 or 60Hz) power supplies and with 110/120v or
220/240v control circuits. Burners to suit other electrical supply voltages can be supplied
specially to suit specific application requirements.
All wiring on the burner should comply with the requirements of the local electrical codes of
practice.
All conduits should be kept clearof heat zones.
Local means of electrical isolation should be installed close to the burner.
Ensure that the electrical voltage does not vary from the specified by morethan 6%.
High temperaturewire (tri-rated or better) should beused for all electrical connections.
The electrical connections to the burner shown on diagram M5 should be strictly adheredto.
Gas pipe work should not be used as an electrical earth.
Installation (Continued)
Comtherm Ltd
Installation & Maintenance Manual
Page 05
Burners, Heaters & Combustion Systems

PLEASE NOTE:
Without exception, burners should only be commissioned by suitably qualified
personnel. The following notes are intended as guidance and in no way negate the
need for the equipment to be commissioned by suitably qualified personnel.
1. Examine the burner for physicaldamage.
2. Close all manual fuel valves.
3. Check that the electrical supply is switched off.
4. Check all electrical connections to ensure that the combustion air pressure switch (item P1)
and the safety shut off valve (item S1) are wired to the correct terminals in the burner
safety control unit (see electrical diagram in document M5)
5. Check the incoming gas pressure (at V1) and verify that the inlet gas pressure is as
specified (see document M1).Generally speaking, the inlet gas pressure, without the
burner operating,will be somewhat higher than when the burner is in operation.
6. Ensure that the burner on/off switch is in the position.
7. Switch the electrical supply on.
8. Check for gasleaks on the burneras follows:
(a) Close the manual valve V1 and pilot manual valve V6.
(b) Vent burner pipe work downstream of V1 by opening a suitably positioned test
nipple.
(c) Use a manometer test pressure downstream of V1 for 1.5 minutes. If no pressure
buildsup, valve V1 is not leaking.
(d) Open valve V1.
(e) Check for external leakage using a soap solution or gasdetector on
pipe work and valves, rectifying any leaks before proceeding.
(f) Put temporary electrical supply onto valve S1.This will pressurise the space
between S1 and S2. Open the test point downstream of S2 and connect the
manometer (valve V2 must be closed); if no pressure builds up within 1.5 minutes then
valve S2 is sound.
Initial Light Up (Commissioning)
Comtherm Ltd
Installation & Maintenance Manual Page 06
Burners, Heaters & Combustion Systems

(g) Disconnect the electrical supply to valve S1 and vent the space
between valve S1 and S2, using the pressuretest nipple. Using the
manometer, check that no pressure builds up between the two valves; if no pressure
is detected then valve S1 is sound
(h) Open pilot manual valve V6 and check by using the test nipple downstream of V1
that there is no pressure drop at this point. If no pressure drop is detected in 1.5
minutes then valve S3 is not leaking.
(i) Finally, check downstream of V2 and V3 with soap solution or gas detector (with
burner running).
In cases where burners are fitted with main multi-block / combination safety valve units, the
above procedure will vary; the valve should be energized to check for downstream pipe
leakages and de-energised followed by venting of downstream pipe space to check for valve
seat leakages.
9. Release the spring pressure on the gas governor (item G2).
10.Set the combustion air pressure switch (item P1) 25% below the specified air pressure
required.
11. Start the fan supplying the combustion air and ensure that the fan rotation direction is
correct.
Check the running current of the motor and crosscheck this with the data on the Motor label.
Ensure that the motor overload protection is correctly set.
12.Ensure that valves V2 and V6 areclosed.
13.Check that all pressure switches associated with the burner are in the correct position.
Note that the burner combustion air pressure switch (item P1) should be in the
position and should only switch over after the combustion air fan has started
14. Check that all pressure switches associated with the burner arein the position calling
for and switch the burner on.It may be necessary to reset the burnerlockout fault button.
Initial Light Up (Commissioning)
Comtherm Ltd
Installation & Maintenance Manual
Page 07
Burners, Heaters & Combustion Systems

15.Allow the flame safety control unit (item A1) to cycle through the start up sequence; check
that the pressure switch (P1) has changed over from the `no to the air proved position.
If it adjust the combustion air supply so as to provide satisfactory burner air
pressure. Check that the ignition and pilot solenoid valves are electrically energised at the
correct time and in the correct sequence. The burner flame safety control unit should then
lockout.
16.Open the manual pilot valve (item V6)
17.Fit Micro-ammeter into circuit with the flame sensor.
18.Reset the burner lockout button; the burner will cycle and the pilot flame should light. It
maybe necessary to start the light up sequence (reset) several times so as to remove air
from the pilot line and to adjust the pilot flame to the correct size. Check the pilot flame
signal on the micro-ammeter.
19.Note that the burner will go to lockout after each attempt to light the pilot.
20.Half open the manual test valve (item V2). Reset the burner lockout button. The burner
should cycle and light up onto the main flame.
21.Slowly open up the manual test valve (item V2) to the full position and adjust the main gas
governor (item G2) to produce the required flame size. With the burner on full fire
(temperature control calling heat) check that the gas pressure at the nozzle is as specified
for the required thermal/fuel rating, this will be indicated on the burner data label and
can also be established from the nozzle flow graph included with this manual.
22.Check the main flame signal on the micro-ammeter.
23.Turn the combustion air pressure switch (item P1) upwards so that the burner shuts down.
Note the adjustments in air pressureand reduce the switch setting by 25%.
24.Whilst the burner is operating remove the electrical connections from the flame sensor.
Check that the burner flame safety control locks out immediately and that the gas supply is
automatically shut off.
25. Whilst the burner is operating, block the combustion air supply so that the pressure switch
P1 switches to the position, checking that the burner shuts down.
Initial Light Up (Commissioning)
Comtherm Ltd
Installation & Maintenance Manual Page 08
Burners, Heaters & Combustion Systems

26. Check the operationof all control and safety devices in the burner control circuits.
In addition ensure that the burner operates correctly. Make a note of all control
settings.
27. The low fire setting of the burner should be made in line with the process
requirements whilst still maintaining a steady flame signal.
NOTE;-
Once correctly commissioned the burner settings should only be altered by suitably
qualified personnel, and only when changes to the process requirements deem it
necessary. At no point should the settings of any safety device be altered to overcome
changes in process conditions without the burner again being fully commissioned in line
with those process conditions.
Initial Light Up (Commissioning)
Comtherm Ltd
Installation & Maintenance Manual
Page 09
Burners, Heaters & Combustion Systems

FIND FAULT
POSSIBLE CAUSES
SOLUTION
Burner light up
sequence does not
start
No electrical supply Check electrical supplyat
local isolator.
Check the control fuse
Burner electrical control
condition
Check controls and switches
in control circuit
Check all pressure switches
and micro-switches
Airflow pressureswitch not
made Check setting on switch, if this is
correctcheck airflow
Low gas pressure switch
not made Check setting on switch
if this is correctcheck the gas
pressure
Start cycle begins but
the burner locks out or
shuts down before
initiating the ignition
sequence
Low combustion air
pressuredifferential Reset burnerpressureswitch
(P1)
If pressureswitch P1 is set
correctly open the air damper
on the combustion air fan
Check that the combustion air
fan motor is rotatingin the
correctdirection
Check that the combustion air
fan is running,if not check the
overload or circuit breakers
Fault Finding Guide
Comtherm Ltd
Installation & Maintenance Manual Page 10
Burners, Heaters & Combustion Systems

FIND FAULT
POSSIBLE CAUSES
SOLUTION
Pilot does not light No spark Check electricalsupply to
ignition transformer
Check electrical connection
to spark plug
Check operationof ignition
transformer
Check condition of spark
plug and clean, reset or
replace
No pilot gas Check manualvalve is open
Check that pilot solenoid
valve opens
Ensure gasis available at
burner
Not enough pilot gas Check pilot gas flow adjuster
and pilot gas regulator
Pilot blown out Reduce process air flow if
possible
Increase pilot gas rate
Pilot lights but locks
out when ignition de-
energised
Pilot gas rate too low Adjust pilot gas rate
Pilot lights but the
burner locks out before
the main valves are
energised
Flame sensor not detecting
the flame
Or
Faulty sensor
Check sensor for damageor
moisture
Clean flame sensor
Check flame sensor
installation and position
Replacesensor
Fault Finding Guide
Comtherm Ltd
Installation & Maintenance Manual
Page 11
Burners, Heaters & Combustion Systems

FIND FAULT
POSSIBLE CAUSES
SOLUTION
Main flame does not
light and burner locks
out at the end of the
pilot phase
Faulty main shut off valve Check electricalsupply to
valve
Check conditionof the valve,
if faulty, replaces
No main gas Check manualvalve open
Check the adjustment of the
gas control valve
Ensure gasis available at
burner
Not enough main gas Check main gas flow adjuster
and main gas regulator
Main flame lights but
shuts down after a short
periodof time
Pilot gas rate too high Adjust pilot gas rate
Control circuit operating Check control circuit, over
temperature
limits etc.
Burner gas or air ports
blocked Check and Clean
Identify source of blockage
and rectify
Flame sensor not detecting
the
flame
Over firing andflame is
firing rate
Check flame sensor
installation and position
Check the main gas pressure
governor
Fault Finding Guide
Comtherm Ltd
Installation & Maintenance Manual Page 12
Burners, Heaters & Combustion Systems

FIND FAULT
POSSIBLE CAUSES
SOLUTION
Flame failure (lockout)
during normal main
flame operation
Faulty main shut off valve Check electricalsupply to
valve
Check conditionof the valve
if faulty, replace
No main gas Check manualvalve is open
Check the adjustment of the
gas control valve
Ensure gasis available at
burner
Not enough main gas Check main gas flow adjuster
and main gas regulator
Low fire set too low Check and adjust
Control circuit operating Check control circuit, over
temperature
limits etc.
Burner gas or air ports
blocked Check and Clean
Identify source of blockage
and rectify
Flame sensor not detecting
the flame
Combustion air failure
Over firing andflame is
firing rate
Check flame sensor
installation and position
Inspect combustion air fan for
damage
Check fan overloads
Check air filter (if fitted) and
clean if necessary
Fault Finding Guide
Comtherm Ltd
Installation & Maintenance Manual
Page 13
Burners, Heaters & Combustion Systems

FIND FAULT
POSSIBLE CAUSES
SOLUTION
Flame failure (lockout)
at low fire Faulty low fire bypass valve
(high low burners only) Low fireflame set too low
Check electrical supply to
valve
Check condition ofthe valve
if faulty, replace
Low fireflame set too low Check the adjustment of the
gas control valve
Ensure gas is available at
burner
Too much air Check and reset air at high and
low fire
Low fire air set too low
(modulating gas and air
burnersonly)
Check and adjust
Control circuit operating
due to Check control circuit, over
temperaturelimits and low fire
settings
Flame sensor not detecting
Flame Check flame sensor installation
and position
Main flame too long Too much gas
Check main gas pressure and
reset
Check gas control valve and
reset
Check fuel type
Combustion air set too low Check air dampers,linkages
and air filter (where fitted)
Fault Finding Guide
Comtherm Ltd
Installation & Maintenance Manual Page 14
Burners, Heaters & Combustion Systems

FIND FAULT
POSSIBLE CAUSES
SOLUTION
Red
.
Low process airflow.
Reset air.
Main flame too long.
Check the adjustment of the gas
control valve.
Combustion airset too low.
Check air dampers,linkages and
air filter (where fitted).
Unit will not achieve
temperature.
Too much process air.
Check and reset air.
Burner input setting too low.
Check and reset Burner.
Leakage of cold air into
system.
Source and rectify.
Burner shuts down (see
also sheets M8.1 to
M8.4b).
Control circuit operating.
Check control circuit, process
airflow switch, over temperature
limits and low firesettings.
Flame sensor not detecting
the flame.
Check flame sensor installation
and position.
Too much pressurein
chamber.
Check Flue.
Unit Produces
condensation.
Burner turned down too
low.
Check the adjustment of the gas
control valve.
Low processair volume.
Check and reset air.
Fault Finding Guide
(Indirect Heaters)
Burners, Heaters & Combustion Systems
Page 15 Comtherm Ltd
Installation & Maintenance Manual

Parts List (Key)
A1: Flame control unit
A2: Flame electrode
A3: U.V. flame sensor
A4: Valveproving unit
B1: Burner combustionhead
B2: Peep sight
B3: Viewing window
B4: Inspection plate
C1: Burner fancontactor/overload
C2: Processair fan contactor/overload
E1: Ignition transformer
E2: Ignition plug
E3: Burner on-off switch
E4: Low fire position microswitch
E5: High fire position microswitch
E6: Closed positionindicator switch
E7: Isolator
E8: Terminal box
E9: Purgetimer
ET: 24v Control transformer
EB: Alarm Bell
EFS: Exhaust flow switch
FC: Control circuit fuse
FB: Burner control fuse
F1: Burner motor fuse
F2: Process air fan fuse
G1: Primary gas regulator (high pressure)
G2: Main gas governor
G3: Primary pilot gas governor (high pressure)
G5: Over pressureslam shut valve
G6: Pressurereliefvalve
K1: Push button burner start
K2: Push button burner stop
K3: Push button lockout reset
K4: Push button fault reset
K5: Push button alarm mute
K6: Push button valve provingfault reset
K7: Push button Flame signal test
L1: Indication light burner lockout
L2: Indicationlight burner run
L3: Indicationlight valve fault
L4: Indicationlight power on
L5: Indicationlight instruments on
L6: Indication light burner fan failure
L7: Indicationlight burner fan run
L9: indicationlight processfan run
L10: indicationlight exhaust fan run
MF: Burner fan
M1: Burner fan motor
M2: Burner fan impellor
P1: Burner fanpressureswitch
P2: Process air pressureswitch
P3: Low gas pressureswitch
P4: High gas pressureswitch
P5: Valve proving pressureswitch
P8: Gas pressuregauge
P9: Air pressuregauge
R: Electrical relay
S1: First safety shut off valve
S2: Second safety shut off valve
S3: First pilot/start gas solenoidvalve
S4: Second pilot/start gas solenoidvalve
S5: Vent valve (normal open)
S6: Threeway solenoid valve -burner air
SM: Solenoid/governor multi-bloc valve
TC: Control instrument
TL: High limit thermostat or sensor
T3: Valve positioner
T4: Valve actuator
T5: Control supply transformer
V1: Manual inlet valve
V2: Manual test valve
V3: Gas filter
V4: Vent cock
V5: Gas control valve
V6: Pilot manual gas valve
V7: Pilot gas adjustment
V8: Gauge cock
V9: Air flow control valve
V10: Gas flow adjustment
V11: Air flow adjustment
V12: Air filter
V13: Oil filter
V14: Oil control valve
V15: Gas orifice plate
Inclusion of this list does not imply that all items are included in the particular equipment to which this refers: refer to sheets M3 (if
applicable), M4 and M5 for details. Refer to recommended spares list for actual complete parts specification.
Burners, Heaters & Combustion Systems
Page 16

The exact timing of service work to the burners can only be determined based on the
ambient working environment of each specific installation; as a minimum however we would
suggest that the following service points are covered at least on a half yearly basis and should
only becarried out by a suitably qualifiedor experienced person;
1. Remove spark electrode, clean with wire brush and check plug gap setting of 2.5 to
3mm. Inspect plug ceramic for any cracks or damage.
2. a. Remove flame sensing electrode, clean electrode with emery paper and inspect
plug ceramic for any cracksor damage.
Or
b. Remove U.V. cell and clean bulb with clean cloth; taking care to not touch the bulb
itself.
3. Remove combustion fan motor and impellor, clear impellor blades of any blockage or
build-up of materialdrawnin by the fan.
4. Clear fan inlet guard of any blockage or restriction, if the combustion air is ducted to
the fan assembly then the duct should be removed to check for anyblockage.
5. Clear burner body of any dirt or debris which has been drawn in by the combustion
fan.
6. Condition of the burner air wings can be accessed from inside the combustion
chamber /duct, if access to the inside of the oven or combustion chamber is restricted
then the burner should be removed from its fixings to inspect for serious damage to the
burner air wings, small cracks and fishers or very slight distortion in the air wings
would not be detrimental to the operationof the burner.
7. In the event that the burner air wings are found to be severely damaged then the
burner head will need to be completely broken down to fit replacements.
Suggested Service Program
Burners, Heaters & Combustion Systems
Page 17 Comtherm Ltd
Installation & Maintenance Manual

8. All pressure switch impulse lines should be removed and checked for any
blockage.
9. This down time with the burner should also be used to check the integrity
and correct operation of safety pressureswitches and solenoids.
10. The burner valve assembly should also be checked at this time for gas leaks.
11. Finally all burner gas and air settings should be checked against the last
recorded commissioning or service settings. The burner should not be put back into
operation until test firing has been carried out by the engineerperformingthe service.
Under no circumstances should the settings of any safety devices be changed from those
recorded in the last commissioning data unless this is being carried out as a complete re-
commissioning of the burner to facilitate changes in process requirements; the re-
commissioning of the burner should only be carried out by suitably qualified personnel.
If the ambient conditions are particularly dirty then we would suggest carrying out a full
service on a quarterlybasis.
Suggested Service Program
Burners, Heaters & Combustion Systems
Page 18
Comtherm Ltd
Installation & Maintenance Manual
This manual suits for next models
1
Table of contents
Other Comtherm Burner manuals
Popular Burner manuals by other brands
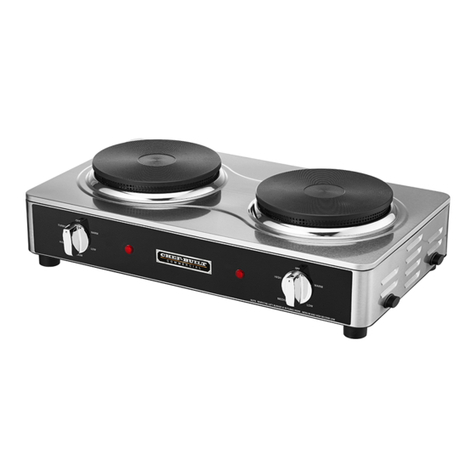
CHEF-BUILT
CHEF-BUILT CHP-80 instruction manual
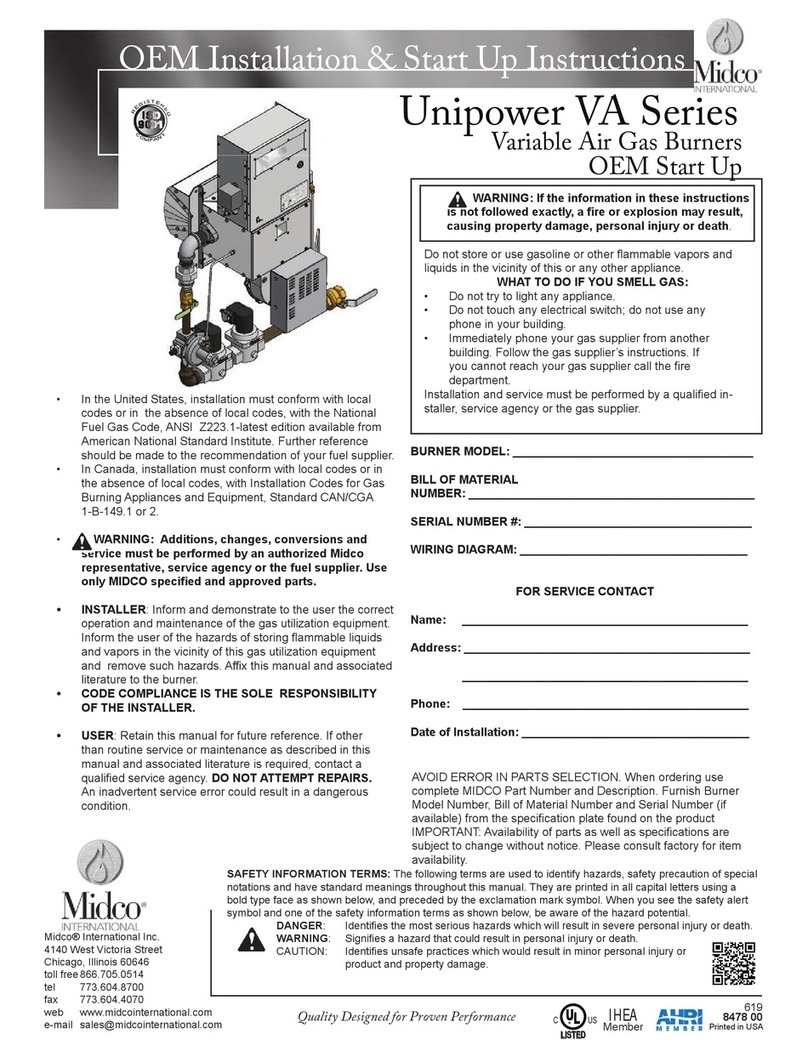
Midco
Midco Unipower VA Series OEM Installation & Start Up Instructions
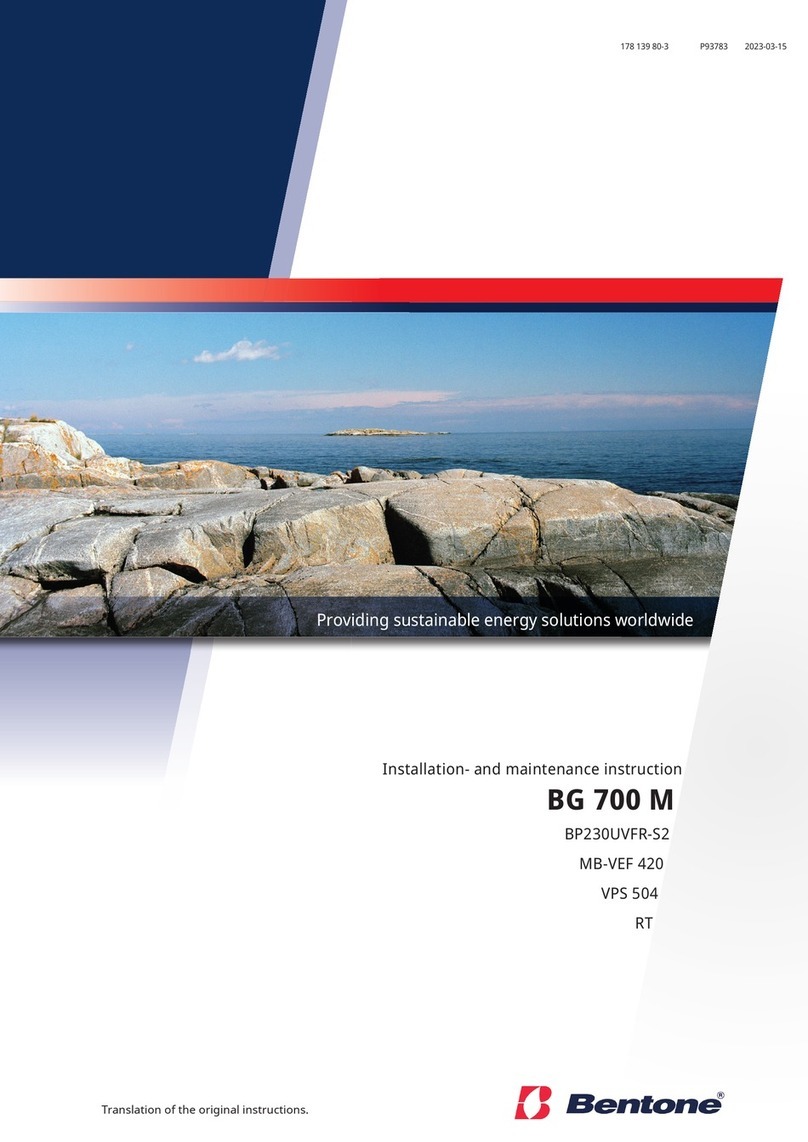
Bentone
Bentone BG 700 M Installation and maintenance instruction
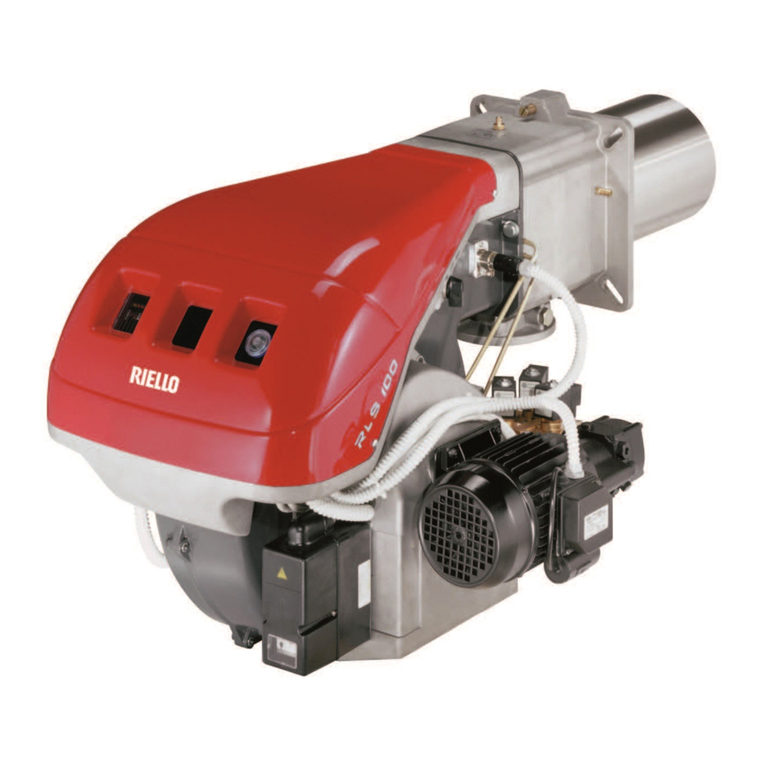
Riello
Riello RLS 70/M Installation, use and maintenance instructions
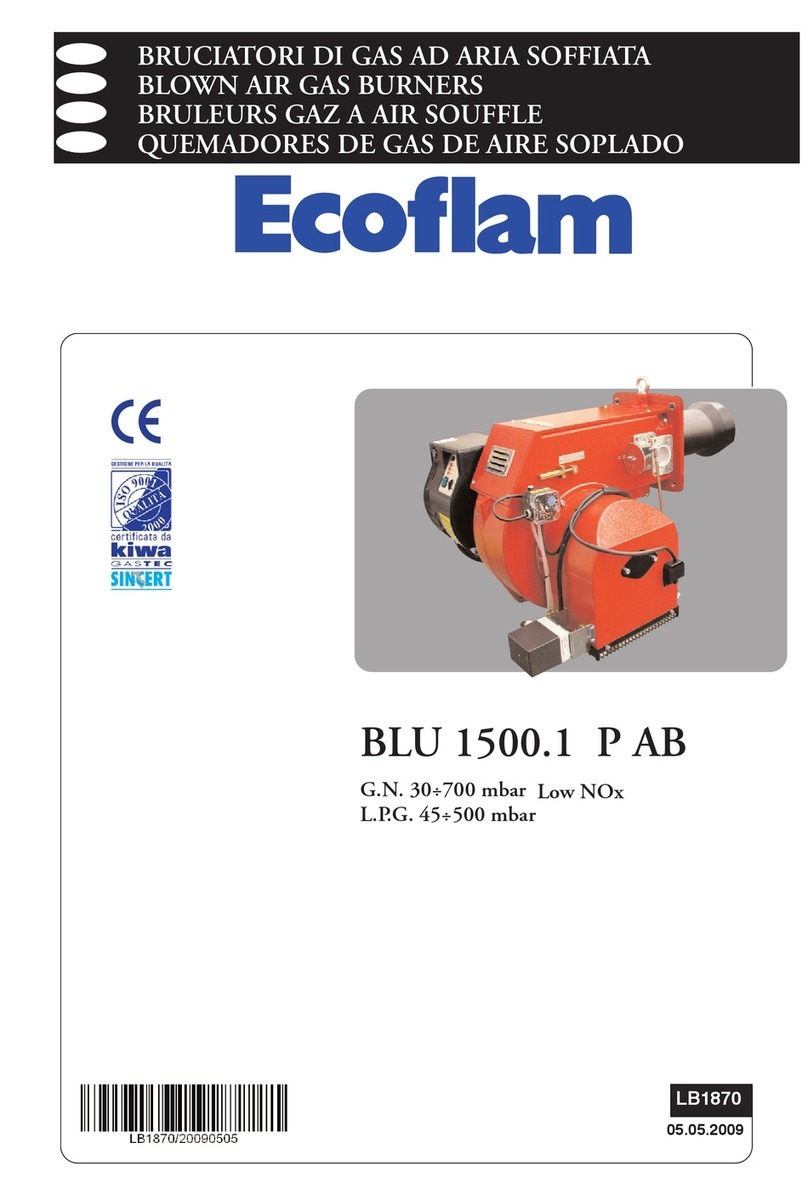
Ecoflam
Ecoflam BLU 1500.1 PAB manual
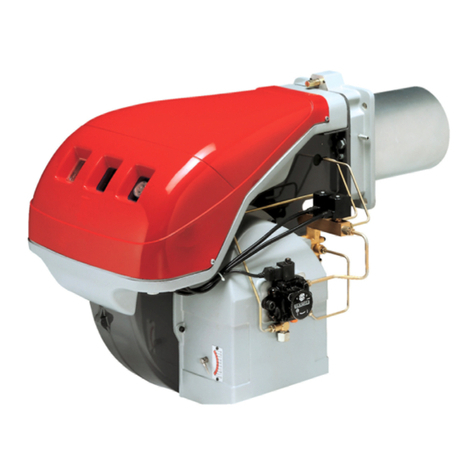
Baxi
Baxi TECNO 70-L Installation, use and maintenance instructions
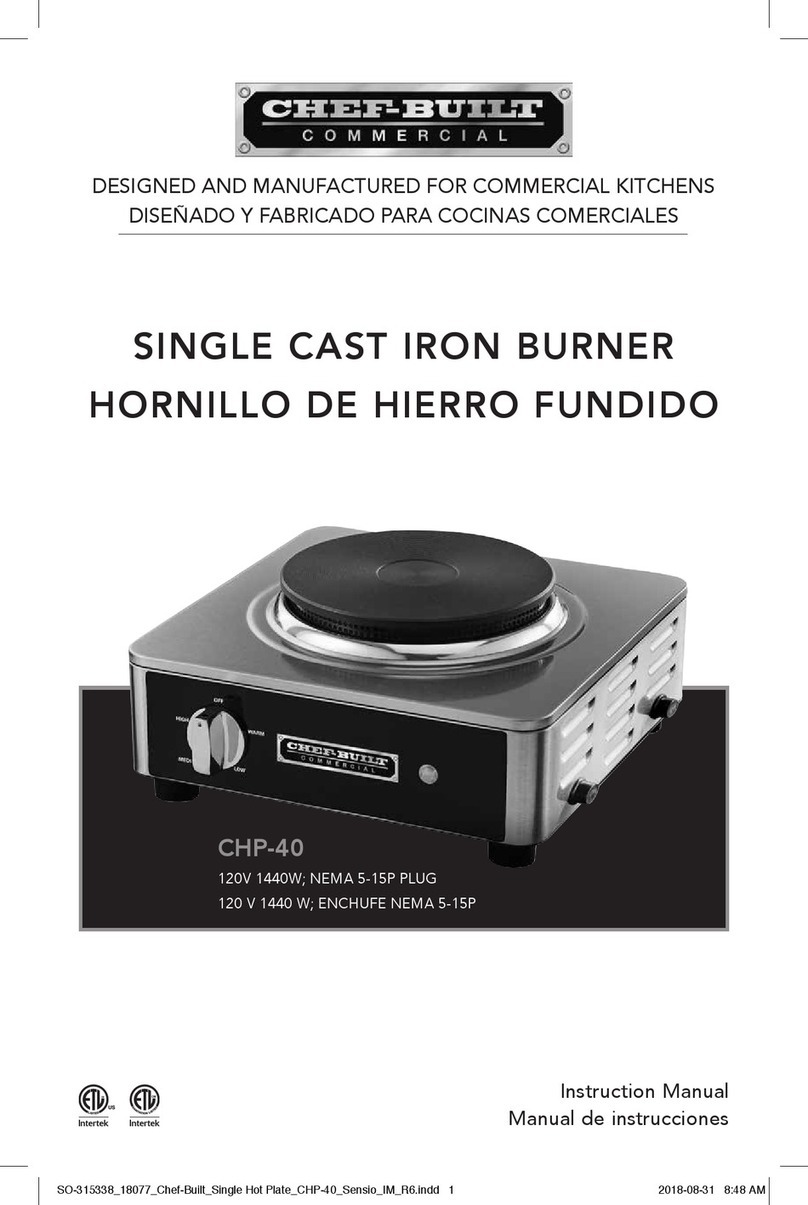
CHEF-BUILT
CHEF-BUILT CHP-40 instruction manual
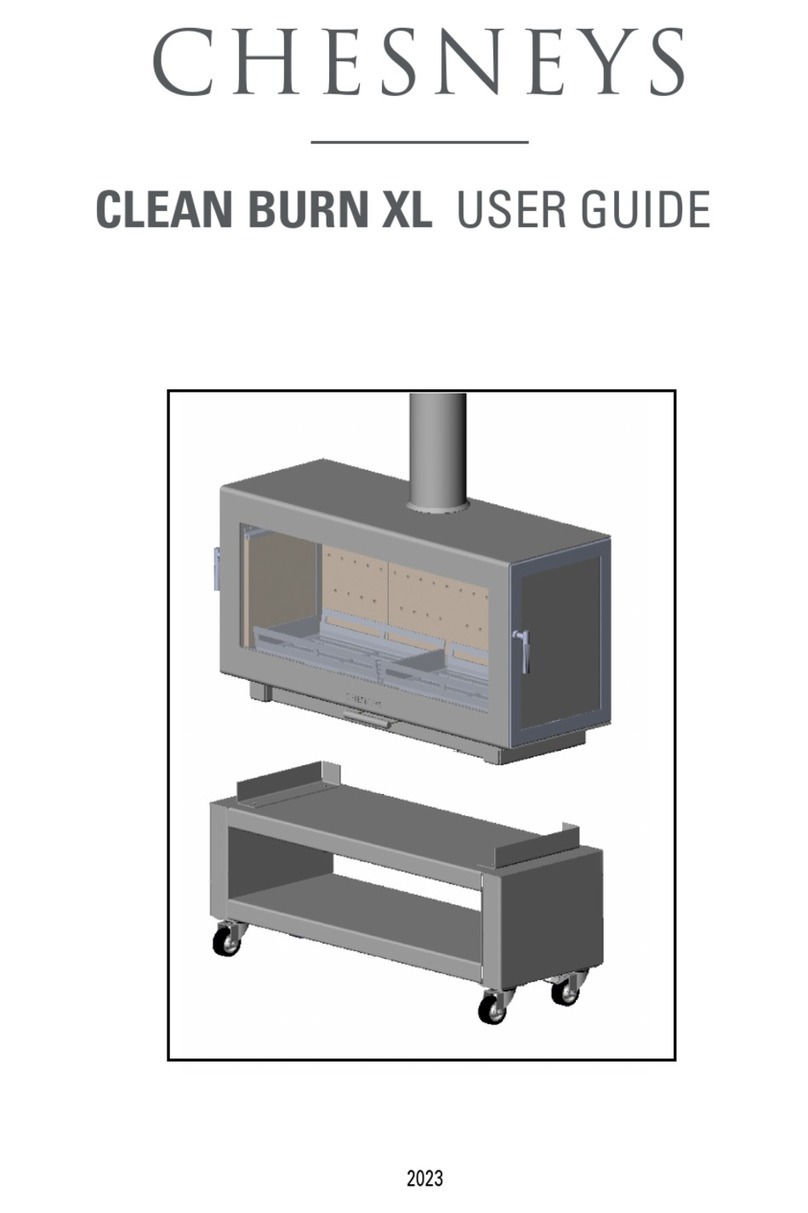
Chesney's
Chesney's CLEAN BURN XL user guide

elco
elco VE 2.100 D operating instructions
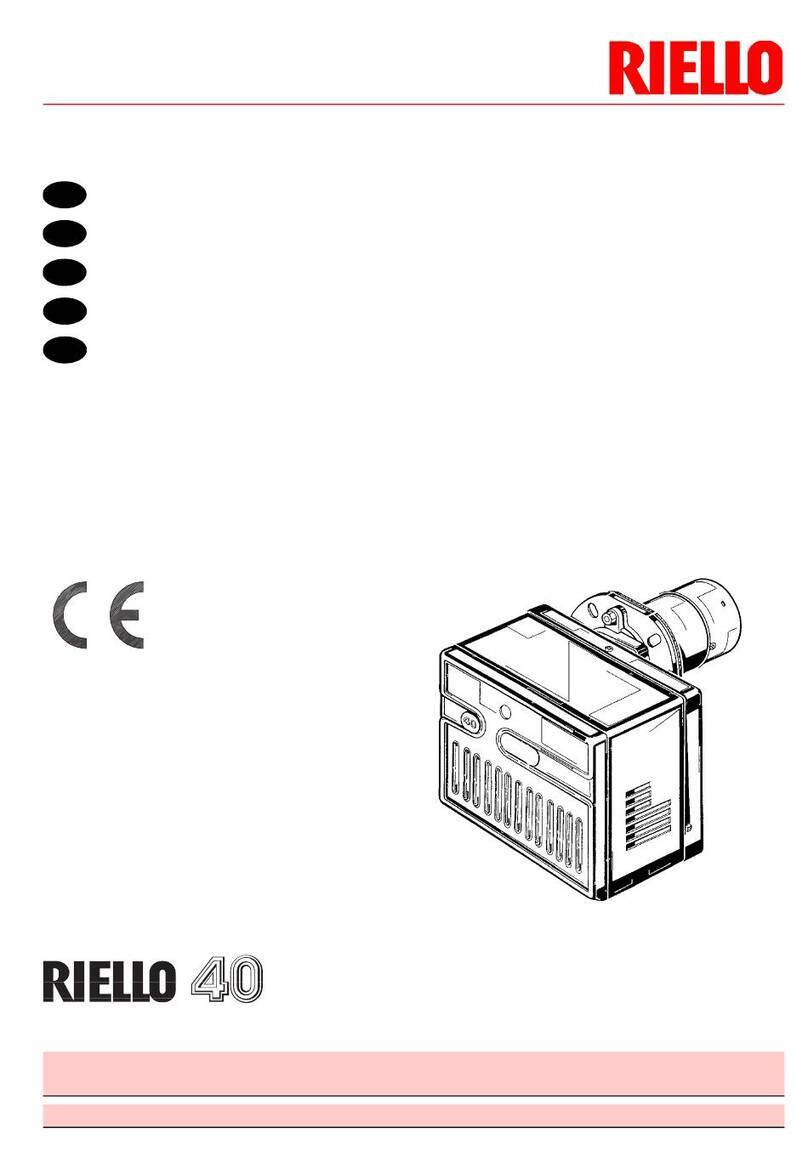
Riello
Riello 462T58 Installation, use and maintenance instructions
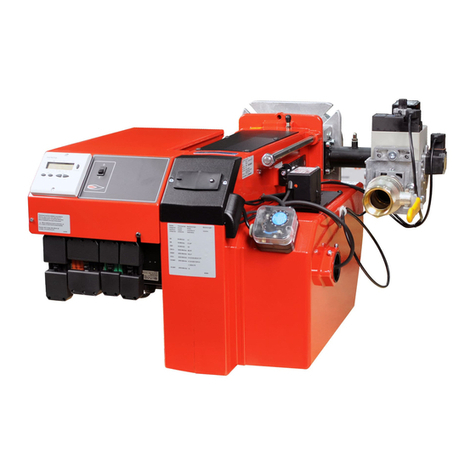
Bentone
Bentone BG 650 Installation and maintenance instruction
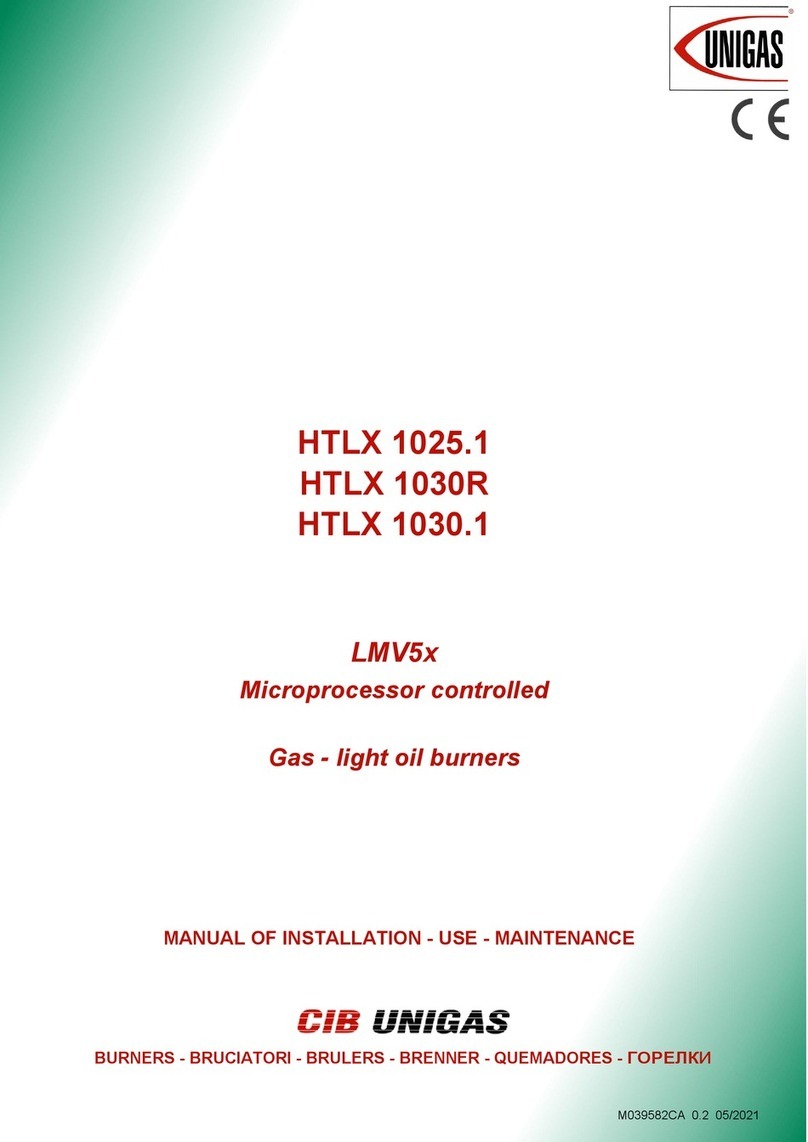
Unigas
Unigas HTLX 1025.1 installation manual