Crouzet SMI22 CANopen Operational manual

SMI22 CANopen
C.MO.SAV.00022.FR_V3 Page 1/24
September 3rd, 2018
PRODUCT USER MANUAL
SMI22 CANopen
Important Notes
•This manual is part of the product.
•Read and follow the instructions in this manual.
•Keep this manual in a safe place.
•Give this manual and any other documents relating to the product to anyone that uses the product.
•Read and be sure to comply with all the safety instructions and the section "Before you Begin -
Safety-Related Information" in the document “Safety User Manual”
•Please consult the latest catalogue to find out about the product's technical specifications.
•We reserve the right to make modifications without prior notification.

SMI22 CANopen
C.MO.SAV.00022.FR_V3 Page 2/24
September 3rd, 2018
Table of Contents
1. Introduction................................................................................................................................................5
1.1. Motor Family .....................................................................................................................................5
1.2. Characteristics ..................................................................................................................................5
1.3. Identification Label............................................................................................................................5
1.4. Product Coding .................................................................................................................................6
1.5. Standards and concepts ...................................................................................................................7
2. Options and Accessories...........................................................................................................................8
2.1.1. Holding brake ...........................................................................................................................8
2.1.2. Gearboxes................................................................................................................................8
2.1.3. Other.........................................................................................................................................8
2.1.4. Starter Kit..................................................................................................................................8
3. Precautions for use concerning the mechanics.........................................................................................9
3.1. Data specific to the motor shaft ........................................................................................................9
3.2. USB Connector ...............................................................................................................................10
3.3. Fixings.............................................................................................................................................11
4. Product overview .....................................................................................................................................11
4.1. Description of the Product...............................................................................................................11
4.2. SMI22 CANopen Control Electronics..............................................................................................12
4.3. "DCmind-Soft + CANopen" PC Parameter-Definition Software......................................................13
5. Technical Specifications ..........................................................................................................................14
5.1. Electrical Data.................................................................................................................................14
5.2. Generic Data...................................................................................................................................14
5.3. Logic M16 connector.......................................................................................................................15
5.4. Power Supply M16 connector.........................................................................................................16
5.5. CAN communication M12 connector ..............................................................................................16
6. Motor electrical connection......................................................................................................................18
6.1. Power Connection...........................................................................................................................18
6.1.1. Ballast Circuit..........................................................................................................................18
6.1.2. EMC Protection ......................................................................................................................19
6.1.3. Earth connection.....................................................................................................................19
6.2. Protection........................................................................................................................................20
6.2.1. Voltage Protection..................................................................................................................20
6.2.2. Temperature Protection..........................................................................................................21
6.2.3. Current Limiting......................................................................................................................21
6.3. Input/Output Connection.................................................................................................................22
6.3.1. Equivalent Input Diagram.......................................................................................................22
6.3.2. Equivalent Output Diagram ....................................................................................................23
6.4. Terminology and Abbreviations.......................................................................................................24

SMI22 CANopen
C.MO.SAV.00022.FR_V3 Page 3/24
September 3rd, 2018

SMI22 CANopen
C.MO.SAV.00022.FR_V3 Page 4/24
September 3rd, 2018
About This Manual
This manual applies to SQ75 CANopen brushless products:
•80350,
•80360,
•80370,
And all gearboxes adaptation.
Reference source for manuals
The manuals can be downloaded from our website at the following address:
http://www.crouzet-motors.com/
Units
SI units are the default values.
Risk Categories
In this manual, safety instructions are identified by warning symbols.
Depending on how serious the situation is, the safety instructions are split into 3 risk categories.
DANGER
DANGER indicates a directly dangerous situation which, if the
instructions are not followed, will inevitably lead to a serious or fatal
accident.
WARNING
WARNING indicates a possibly dangerous situation which, if the
instructions are not followed, will in some cases lead to a serious or
fatal accident or cause damage to equipment.
CAUTION
CAUTION indicates a potentially dangerous situation which, if the
instructions are not followed, will in some cases lead to an accident or
cause damage to equipment.

SMI22 CANopen
C.MO.SAV.00022.FR_V3 Page 5/24
September 3rd, 2018
1. INTRODUCTION
1.1.Motor Family
SQ75 brushless motors are brushless DC motors, with a control circuit board integrated in the motor.
1.2.Characteristics
SQ75 brushless motors are intelligent servomotors for speed, position and torque control applications. They
can be configured via a Human-Machine Interface (HMI) with CANopen or USB communication bus.
They are equipped with 3 industrial connectors, 1 for power, 1 for the control signals and 1 for the CANopen
communication.
1.3.Identification Label
The label contains the following data:

SMI22 CANopen
C.MO.SAV.00022.FR_V3 Page 6/24
September 3rd, 2018
1.4.Product Coding
Three
firsts
digits
4th digit 5th digit 6th digit 7th digit 8th digit
803 5 = Rotor 37,5mm
0 : direct motor
IP69
0: with integrated drive
0 à 3: SMi22 CAN (if 6th digit = 0 ou 1)
from 0 to 9
6 = Rotor 50mm D: P72 1: with integrated drive + brake
4 à 6: SMi22 (without CAN) (if 6th digit = 0 ou 1)
7= Rotor 75mm E: P81 4 : hall effects
2: RAD20 5 : Hall effects + brake

SMI22 CANopen
C.MO.SAV.00022.FR_V3 Page 7/24
September 3rd, 2018
1.5.Standards and concepts
The product is ROHS confirmed following European Directive 2011/65/CE. Following this confirmation, the
product is CE marked.
The electrical design follows the IEC 60335-1 and IEC 60950-1 standards.

SMI22 CANopen
C.MO.SAV.00022.FR_V3 Page 8/24
September 3rd, 2018
2. OPTIONS AND ACCESSORIES
The motors can be supplied with options, such as:
•Different gearboxes
•A failsafe holding brake
•Different motor output shaft versions
2.1.1. Holding brake
SQ75 brushless motors can be equipped as standazromechanical brake.
The holding brake is designed to lock the motor shaft in a de-energized state.
The holding brake is not a safety function.
A motor with a holding brake needs a corresponding control logic which releases the holding brake at the
start of the rotation movement, locking the motor shaft in time when the motor stops.
Nota : Outputs are able to drive the electromechanical brake.
Nota : Motor has to be completely stopped before activation of the brake.
2.1.2. Gearboxes
SQ75 brushless motors can be equipped with different types of gearbox.
The gearboxes offered as standard in the catalogue are planetary gearboxes which combine compact size
and robust design, and worm gearboxes that allow a shaft output at right-angles to the motor shaft.
2.1.3. Other
Other types of adaptation are possible on request, please contact the sales department.
2.1.4. Starter Kit
This kit consists of:
- a 2-meter long micro USB B to USB A (MOLEX 68784-0003) connecting cable 27 526 005
- a power cable : this cable can be obtained by ordering part number 79 298 664
- an I/O cable : this cable can be obtained by ordering part number 79 513 106
- a CAN cable M12 M/F : this cable can be obtained by ordering part number 27 358 015
- a bus terminating resistor : this resistor can be obtained by ordering part number 27 358 014
- a D-Sub bus connector 27 358 017
- an USB to CAN converter (PEAK System reference IPEH-002021) 27 358 016
- an USB stick containing the "DCmind Soft + CANopen Interface" parameter-definition software and
installation drivers for this HMI.
- A T (F-M/F) CAN connector 27 358 020
This starter kit can be obtained by ordering part number 79 513 105

SMI22 CANopen
C.MO.SAV.00022.FR_V3 Page 9/24
September 3rd, 2018
3. PRECAUTIONS FOR USE CONCERNING THE MECHANICS
3.1.Data specific to the motor shaft
WARNING
MOTOR MECHANISM
Exceeding the maximum permissible forces on the shaft leads to rapid
bearing wear, a broken shaft or damage to any accessories (encoder,
brake, etc.)
• Never exceed the maximum axial and radial forces.
• Protect the shaft from any impact.
• When press-fitting components, do not exceed the maximum
permissible axial force.
Failure to comply with these precautions can result in death,
serious injury or damage to equipment.
Radial load on the shaft
The application point Xof the radial force Fdepends on the motor size.
This information appears in the motor technical data sheet.
The maximum axial and radial loads must not be applied simultaneously.
F
x

SMI22 CANopen
C.MO.SAV.00022.FR_V3 Page 10/24
September 3rd, 2018
3.2.USB Connector
The motor is equipped with a micro USB connector, which can be accessed by removing the stopper from
the housing.
The stopper prevents penetration of foreign bodies or fluids inside the motor.
The stopper prevents fingers or any inappropriate object making contact with the micro USB connector.
For any other connector, when not used, stoppers have to be mounted.
WARNING
UNEXPECTED MOVEMENT DUE TO ELECTROSTATIC DISCHARGES
Electrostatic discharges (ESD) on the micro USB connector can, in
some cases, lead to deterioration or destruction of some system
components and generate unexpected motor operation.
• Never touch the connector with your fingers or any inappropriate
object.
Failure to comply with these precautions can result in death,
serious injury or damage to equipment.
CAUTION
LOSS OF SEALING
The stopper ensures the motor is sealed.
• Replace it after completing parameter definition.
• Make a visual check to ensure it is in place.
Failure to comply with these precautions can result in injury or
damage to equipment.
Housing
USB stopper

SMI22 CANopen
C.MO.SAV.00022.FR_V3 Page 11/24
September 3rd, 2018
3.3.Fixings
Fixing of the product has to be done by using 4 M6 screws with a screwing torque of 7N.m.
4. PRODUCT OVERVIEW
4.1.Description of the Product
Label
18-pin logic M16 connector
(Inputs/Outputs)
3-pin power supply M16
connector
Output shaft
CAN communication
M12 connector
SMI22 CANopen integrated
electronics
USB-B micro-connector
(Parameter definition via HMI)

SMI22 CANopen
C.MO.SAV.00022.FR_V3 Page 12/24
September 3rd, 2018
4.2.SMI22 CANopen Control Electronics
The SQ75 CANopen electronic control board contains the control electronics for a brushless motor,
integrated in the motor body.
This electronics is used for:
• Power switching of the motor in sine mode (field-oriented control (FOC)) or trapezoidal mode.
• Position-Speed-Torque and Current control algorithms.
• CANopen CiA 301 standard – Application layer and communication profile
• CANopen CiA 402 standard – Drive and motion control device profile
• Use of preconfigured programs which can perform numerous routine applications (DCmind programs).
• Management of different types of operation:
o"Stand-alone" motor without external PLC.
oUse with other motors incorporating SMI22 or SMI21 electronics.
oUse with a programmable controller, with the SMI22 simplifying motor management.
• The interface with parameter-definition software installed on the PC:
oEasy to use, even by a layman, thanks to simplified application programs that are quick to
get up and running.
oWide choice of expert programs covering a wide range of applications.
oCAN connection via a commercially-available standard cable (can be supplied on request).
oUSB connection via a commercially-available standard cable (can be supplied on request).
• Management of 6 inputs,4 outputs and 2 STO inputs (for safety) to control the motor:
o2 inputs that can be configured for 0-10 V 10-bit analog or PWM or digital control
o4 digital inputs
o2 isolated differential STO inputs (4 leads)
o1 output that can be configured as PWM or frequency or digital
o1 output that can be configured as PWM or digital
o2 digital outputs
As standard, the motors have an internal encoder with 4096 points per revolution that can reach high
positioning and control resolutions.
Note : For reset the motor by CANOpen (e.g. when Bootloader mode is required), index 0x2FFF sub index
0x00 has to be set at value=0x64747372.

SMI22 CANopen
C.MO.SAV.00022.FR_V3 Page 13/24
September 3rd, 2018
4.3."DCmind-Soft + CANopen" PC Parameter-Definition Software
This software can be downloaded from the Internet at the following address: http://www.crouzet-motors.com/
It can also be supplied as a kit, see "Starter Kit" section.
This "DCmind-Soft + CANopen" software is needed the first time the motor is used and for debugging if you
don’t have a CANopen master.
It is used for:
• Selecting the motor operating program:
oPosition
oSpeed
oTorque
oHoming
oQuick and easy starting using preprogrammed applications.
oUse of "expert" programs that provide access to all settings.
• The various settings needed for the application to work correctly.
• Updating the "firmware" motor program using the bootloader function.
For more information, see the HMI user manual dedicated for the “DCmind Soft + CANopen”

SMI22 CANopen
C.MO.SAV.00022.FR_V3 Page 14/24
September 3rd, 2018
5. TECHNICAL SPECIFICATIONS
5.1.Electrical Data
Maximum Product Specifications
Parameters
Value
Unit
Supply voltage VDC_MAX
75
V
Maximum current IDC_MAX (2seconds)
75
A
Maximum input voltage VIN_MAX
90
V
Maximum output voltage VOUT_MAX
24
V
Maximum output current IOUT_MAX
10
mA
Operating Specifications
Parameters
Min
Typical
Max
Unit
Supply voltage VDC
9
24 / 32 / 48
75
V
Current IDC
-
15
-
A
Motor consumption when stopped without holding
W0
- 1 - W
Input Specifications
Parameters
Min
Typical
Max
Unit
Input impedance In1 to In4
-
200
-
kΩ
Input impedance AN5 to AN6
-
107.2
-
kΩ
Low logic level on inputs In1 to In4
-90
-
2.4
V
High logic level on inputs In1 to In4
4.5
-
90
V
Low logic level on inputs AN5 to AN6
-90
-
2
V
High logic level on inputs AN5 to AN6
4.6
-
90
V
Low logic level on STO1 & 2
-2
-
4
V
High logic level on STO1 & 2
4.6
-
75
V
CAN Low level
0.5
1.5
2.25
V
CAN High level
2.75
3.5
4.5
V
Output Specifications
Parameters
Min
Typical
Max
Unit
Low logic level on outputs Out1 to Out4 V
OL
RL= 4 K7Ω, VDC = 24 V
- 5 10 mV
High logic level on outputs Out1 to Out4 V
OL
RL= 4 K7Ω, VDC = 24 V = voltage supply added from
eventual rejective voltage
- - 24 V
5.2.Generic Data
General Specifications
Parameters
Value
Unit
Ambient motor temperature
-30 to +70
°C
Insulation class (compliant with directive IEC 60085)
E
/
Ingress protection (excluding output shaft)
IP67 + IP69
/
CANopen compliance
CiA DS 301 and CiA DS 402
/

SMI22 CANopen
C.MO.SAV.00022.FR_V3 Page 15/24
September 3rd, 2018
5.3.Logic M16 connector
It’s a M16 18-pin industrial male connector
Recommended AWG for the associated cable: AWG24 for wires inside a shielded cable.
(See part “Starter Kit” of this document).
With cables more than 3 m long, tests must be performed in situ.

SMI22 CANopen
C.MO.SAV.00022.FR_V3 Page 16/24
September 3rd, 2018
5.4.Power Supply M16 connector
It’s a M16 3-pin industrial male connector.
Recommended AWG for the associated cable: AWG14 for wires inside a shielded cable.
(See part “Starter Kit” of this document).
With cables more than 3 m long, tests must be performed in situ.
5.5.CAN communication M12 connector
It’s a M12 5-pin industrial male connector with standard pinout according to CiA 303-1 recommendations.
Recommended AWG for the associated cable: AWG24 for wires inside a shielded cable.
(See part “Starter Kit” of this document).
Note that the maximum baud rate depends of the cable length.

SMI22 CANopen
C.MO.SAV.00022.FR_V3 Page 17/24
September 3rd, 2018
5.6. Connectors part numbers
MOTOR
CABLE
I/O
connector
Panel
connector
HUMMEL
7.850.000.000
All HUMMEL
M16
AWG24
cable
Insert
HUMMEL
7.003.988.101
HUMMEL
7.003.988.102
Contact HUMMEL
7.010.980.801
HUMMEL
7.010.980.802
Supply
connector
Panel
connector
HUMMEL
7.850.000.000
AWG14
cable
Insert HUMMEL
7.003.983.101
HUMMEL
7.003.983.102
Contact HUMMEL
7.010.982.001
HUMMEL
7.010.982.002
CAN connector MOLEX M12/PG9 1200708205
any compatible connectors
(i.g : Weidmüller SAIL-
M12GM12G-5S3.0U)

SMI22 CANopen
C.MO.SAV.00022.FR_V3 Page 18/24
September 3rd, 2018
6. MOTOR ELECTRICAL CONNECTION
These motors are not intended to be directly connected to the line supply.
It is the responsibility of the installer to define the electrical protections to be implemented according to the
regulations applicable to the end product range of application.
We recommend the use of fuses in accordance with UL248-5 Test 1.3 & 5.
Supply power must be a stabilized power supply with double electrical insulation.
6.1.Power Connection
We recommend grounding the motor housing.
Power connection diagram.
(1) Include capacitors to smooth out inrush currents. Recommended value 1000 µF/A drawn.
6.1.1. Ballast Circuit
When the motor brakes, the kinetic energy stored in the inertias during rotation is returned to the power
supply and generates a voltage surge. This voltage surge can be destructive for the motor or for devices
connected to the power supply.
In the event of frequent braking, an external ballast resistor must be used, all the circuitry is integrated in
the product. Ballast parameters are available through CANopen communication.
For more information, see the HMI user manual dedicated for the “DCmind Soft + CANopen”
It is always necessary to conduct tests to check what size it should be.

SMI22 CANopen
C.MO.SAV.00022.FR_V3 Page 19/24
September 3rd, 2018
6.1.2. EMC Protection
In order to ensure that the product is compatible with EMC standards IEC 61000-6-1, IEC 61000-6-2, IEC
61000-6-3, IEC 61000-6-4, EN55022 Class B we recommend:
- Connecting the motor to ground while limiting length of the grounding strip,
- Adding capacitors on the main power supply.
We recommend 1000 µF per amp drawn.
-
6.1.3. Earth connection
A taped hole on the housing is dedicated to the earth connection. Use M5x6mm screw class 8.8 to connect
product with a screwing torque of 4N.m±15%. Use AWG12 gauge lead for earth connection.

SMI22 CANopen
C.MO.SAV.00022.FR_V3 Page 20/24
September 3rd, 2018
6.2.Protection
DANGER
PROTECTION
The product has internal protection devices that switch off the
motor power supply when activated. As the motor is no longer
controlled, driving loads can decrease.
• The system manufacturer is responsible for complying with all
the applicable safety rules in the event of product failure.
Failure to comply with these precautions will result in
death or serious injury.
6.2.1. Voltage Protection
The product incorporates protection against voltage surges and undervoltages.
Protection against voltage surges:
The voltage surge threshold can be set in the HMI.
When the supply voltage exceeds the threshold, the product automatically switches to ERROR mode. In
ERROR mode the motor is no longer controlled.
To reset the motor:
- The supply voltage must be at least 1 V below the threshold value.
- It is necessary to pass in DISABLE mode then ENABLE mode.
Protection against undervoltages:
The under voltage threshold can be set in the HMI.
When the supply voltage falls below this threshold, the product automatically switches to ERROR mode. In
ERROR mode the motor is no longer controlled.
To reset the motor:
- The supply voltage must be at least 1V higher than the threshold value
- It is necessary to pass in DISABLE mode then ENABLE mode.
This manual suits for next models
7
Table of contents
Other Crouzet Engine manuals
Popular Engine manuals by other brands

Porsche
Porsche 944 Turbo 1988 Workshop manual

Opel
Opel 1973 Service manual
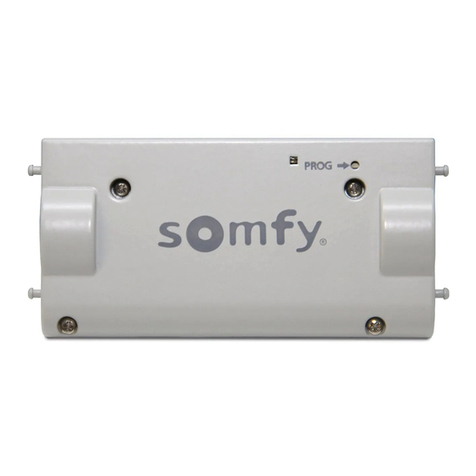
SOMFY
SOMFY Tilt Only 50 RTS Central Pack instructions

Briggs & Stratton
Briggs & Stratton Vanguard 290000 Operating & maintenance instructions

Briggs & Stratton
Briggs & Stratton 290000 Vanguardv Gasoline Operator's manual
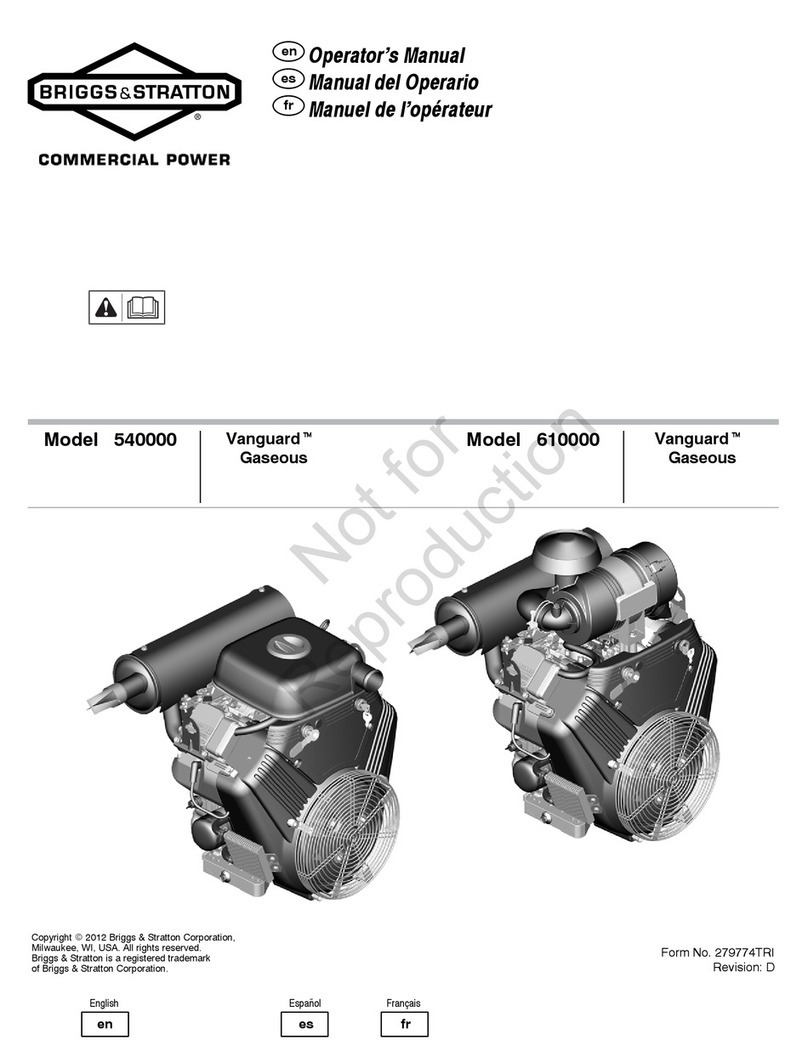
Briggs & Stratton
Briggs & Stratton Vanguard 540000 Series Operator's manual