CTI 2572-B Operating instructions

CTI 2572-B / 2500C-2572-B
ETHERNET TCP/IP MODULE
INSTALLATION AND OPERATION GUIDE
Version 2.2

ii
CTI 2572-B Installation and Operation Guide
Copyright 2016 Control Technology Inc.
All rights reserved
This manual is published by Control Technology Inc. (CTI) 5734 Middlebrook Pike, Knoxville, TN 37921. This
manual contains references to brand and product names which are tradenames, trademarks, and/or
registered trademarks of Control Technology Inc. Siemens®, SIMATIC®, and Series 505®, and 505® are
registered trademarks of Siemens AG. Other references to brand and product names are tradenames,
trademarks, and/or registered trademarks of their respective holders.
DOCUMENT DISCLAIMER STATEMENT
Every effort has been made to ensure the accuracy of this document; however, errors do occasionally occur.
CTI provides this document on an “as is” basis and assumes no responsibility for direct or consequential
damages resulting from the use of this document. This document is provided without express or implied
warranty of any kind, including but not limited to the warranties of merchantability or fitness for a particular
purpose. This document and the products it references are subject to change without notice. If you have a
comment or discover an error, please call us toll-free at 1-800-537-8398 or email us at
sales@controltechnology.com.
REVISION HISTORY
1.0
7/12/2016
Initial Release
2.0
9/20/2016
Added 2500C-2572-B module information
Added PWR bit to WX/WY Quick Reference diagram
2.1
10/11/16
Revised Document Title
2.2
11/8/2016
Corrected the label for the illustration of the 2500C-2572-B PC board

i
CTI 2572-B Installation and Operation Guide
PREFACE
This Installation and Operation Guide provides reference information for the CTI 2572-B Ethernet TCP/IP
Module. The information in this manual is directed to individuals who will be installing and/or using the
module, developing PLC logic to control or monitor the product operation, or maintaining the product.
We assume you are familiar with the installation and operation of:
1) CTI 2500® Series and/or Siemens SIMATIC® 505 programmable controllers,
2) Ethernet local area networks,
3) Transmission Control Protocol/Internet Protocol (TCP/IP).
Please refer to the appropriate user documentation for specific information on programmable controllers and
I/O modules.

ii
CTI 2572-B Installation and Operation Guide
USAGE CONVENTIONS
NOTE:
Notes alert the user to special features or procedures.
CAUTION:
Cautions alert the user to procedures that could damage equipment.
WARNING:
Warnings alert the user to procedures that could damage equipment and endanger the user.

i
CTI 2572-B Installation and Operation Guide
TABLE OF CONTENTS
CHAPTER 1. PRODUCT OVERVIEW ...........................................................................1
1.1. Introduction.............................................................................................................1
1.2. Compatibility ...........................................................................................................2
CHAPTER 2. INSTALLATION.......................................................................................3
2.1. Installation Planning................................................................................................3
2.2. Unpacking the Module ............................................................................................6
2.3. Setting the 2572-B Option Switches........................................................................6
2.4. Physical Installation.................................................................................................9
2.5. Connecting the Ethernet Cable ...............................................................................9
2.6. Initial Power On.......................................................................................................9
2.7. Entering the Module into the PLC I/O Configuration................................................9
2.8. Storing Network Parameters in Flash.....................................................................10
2.9. Module Checkout..................................................................................................11
CHAPTER 3. MODULE OPERATION.......................................................................... 13
3.1. Front Panel Features.............................................................................................13
3.2. Module Startup......................................................................................................14
3.3. Normal Operation..................................................................................................15
CHAPTER 4. CAMP SERVER..................................................................................... 17
4.1. Overview...............................................................................................................17
4.2. Operation..............................................................................................................17
4.3. Connections..........................................................................................................17
4.4. Error Processing ...................................................................................................17
CHAPTER 5. MODBUS TCP SERVER........................................................................ 19
5.1. Overview...............................................................................................................19
5.2. Variable Mapping..................................................................................................19
5.3. Address Translation ..............................................................................................19
5.4. Supported Modbus Function Codes (FC)..............................................................20
5.5. Modbus Exception Codes......................................................................................20
5.6. Diagnostic Statistics..............................................................................................20
CHAPTER 6. ETHERNET/IP SERVER........................................................................ 21
6.1. Overview...............................................................................................................21
6.2. Tag Types Supported............................................................................................22
6.3. 2572-B Configuration ............................................................................................22
6.4. Application Example..............................................................................................22
CHAPTER 7. PLC COMMAND INTERFACE OVERVIEW........................................... 27
7.1. Module WX/WY Words.........................................................................................27
7.2. Command Blocks..................................................................................................28
7.3. WX/WY Command Block Interaction.....................................................................29
CHAPTER 8. START NETWORK SERVICES COMMAND......................................... 31
CHAPTER 9. CAMP CLIENT COMMANDS ................................................................ 37
9.1. Overview...............................................................................................................37
9.2. CAMP IP Multicast Operation................................................................................37

ii
CTI 2572-B Installation and Operation Guide
9.3. Create Socket Command ......................................................................................38
9.4. Close Socket Command........................................................................................40
9.5. Memory Transfer Commands ................................................................................40
9.6. Application Examples............................................................................................48
CHAPTER 10. TROUBLESHOOTING ......................................................................... 59
10.1. Troubleshooting Aids...........................................................................................59
10.2. General Troubleshooting Techniques..................................................................60
10.3. Module Startup Problems....................................................................................60
10.4. Communications Problems .................................................................................62
10.5. Performance Problems........................................................................................63
10.6. PLC Logic Problems...........................................................................................64
10.7. Development and Debugging Tips ......................................................................65
CHAPTER 11. FIRMWARE UPDATE..........................................................................69
11.1. Overview.............................................................................................................69
11.2. Obtaining New Firmware .....................................................................................69
Updating 2572-B Firmware .......................................................................................... 69
APPENDIX A. ERROR CODES ................................................................................... 71
2572-B System Error Codes.........................................................................................71
General Memory Transfer Error Codes .........................................................................73
Start Network Services Error Codes..............................................................................78
CAMP Server Error Codes............................................................................................79
PLC CAMP Client Error Codes.....................................................................................81
APPENDIX B. PLC COMMAND INTERFACE.............................................................87
General Description......................................................................................................87
WX/WY Description .....................................................................................................89
Command Timing Diagrams.........................................................................................96
APPENDIX C. IP ADDRESS INFORMATION ...........................................................103
IP Address Nomenclature ..........................................................................................103
Using the Subnet Mask..............................................................................................104
Converting between CIDR and Dotted Decimal Notation.............................................106
Selecting an IP Address.............................................................................................106
Selecting a Multicast Address ....................................................................................107
HARDWARE SPECIFICATIONS................................................................................ 109
LIMITED PRODUCT WARRANTY.............................................................................110
REPAIR POLICY........................................................................................................112

CTI 2572-B / 2500C-2572-B Installation and Operation Manual 1
CHAPTER 1. PRODUCT OVERVIEW
1.1. Introduction
The 2572-B Ethernet TCP/IP module provides network services for CTI 2500 Series®
Classic controllers and Siemens SIMATIC 505® programmable logic controllers. The
2572-B module is designed to install in a CTI 2500 Series classic base or a Siemens
Series 505® base. Employing a new microprocessor and related components, the
2572-B module is a direct replacement for the 2572-A Ethernet TCP/IP module.
The 2500C-2572-B Ethernet TCP/IP module provides network services for CTI 2500
Series® Compact Controllers. The 2500C-2572-B module installs in a CTI 2500 Series
compact base.
Both modules are Special Function modules, which communicate with the PLC using
the SFIO (Special Function I/O) protocol. Network workstations and control devices
can use the services of these modules to read data from the PLC, write data to the
PLC, program the PLC, and exercise supervisory control over the PLC operation. In
addition, PLC logic can use the facilities of the CTI 2572-B and 2500C-2572-B
modules to access data in other CTI 2500 Series® controllers or Siemens SIMATIC
505® PLCs.
The modules support the following communications protocols:
•Camp Server: Allows a client to access PLC data and control PLC operation
using the CTI CAMP or the Siemens Task Code protocols.
•Modbus Server: Allows a client to access PLC data using the Modbus TCP
(Open Modbus) protocol.
•EtherNet/IP Server: Allows Allen Bradley Logix® controllers to read and
write PLC data stored in V memory.
•Camp Client: Allows the PLC to read and write data stored in V memory on other PLCs.
They connect to an Ethernet network via a CAT 5e RJ-45 connector. The network port supports
10Mb or 100Mb Ethernet data link (half or full duplex operation). The firmware includes a full
function TCP/IP stack that supports both TCP and UDP protocols.
The module provides extensive diagnostic facilities, accessible via an embedded web browser, to
aid in the detection and correction of network problems. In addition, the web browser can be
used to configure module operating parameters and to initiate firmware update.

CTI 2572-B / 2500C-2572-B Installation and Operation Manual 2
1.2. Compatibility
2572-B
The 2572-B mode is designed to be a direct application replacement for the CTI 2572-A module.
•The module uses the same PLC command interface as the CTI 2572 and 2572-A modules, allowing
existing PLC logic to control the operation of the module.
•The CAMP server is compatible with existing CAMP and task code drivers.
•The Modbus Server and EtherNet/IP server functionality is identical to the corresponding 2572-A
protocol managers.
Some features of the 2572-A module that are unrelated to the product application are not supported:
•The TFTP method used by the 2572-A module has been replaced by a method initiated by the
embedded web browser;
•The serial port, which provided an alternate means to set the IP parameters address on the 2572-A, is
not present;
•The Module ID switches, used to generate a DHCP client ID, are not present;
•The SYSLOG client capability is no longer supported.
2500C-2572-B
Except for the smaller form factor, the 2500C-2572-B module is functionally equivalent to the 2572-B module.
It uses the same command interface as the 2572, 2572-A, and 2572-B modules. Consequently, user logic
designed to control these modules will also work with the 2500C-2572-B module. HMI and SCADA workstation
drivers that can access data in CTI 2500 Series Classic controllers via the 2572-A or 2572-B also work with the
2500C-2572-B Module to access data in CTI 2500 Series Compact controllers.

CTI 2572-B / 2500C-2572-B Installation and Operation Manual 3
CHAPTER 2. INSTALLATION
The installation of the Model 2572-B Ethernet TCP/IP Adapter Module consists of the following steps:
1) Planning the installation,
2) Unpacking and configuring the module,
3) Physical installation,
4) Setting IP information,
5) Connecting cables,
6) Checking the module operation.
2.1. Installation Planning
Choosing Ethernet Media
The 2572-B module attaches directly to 10BaseT or 100Base TX media (Shielded or Unshielded Twisted Pair)
via the RJ-45 connector. Ensure that the cables you use for Ethernet communications meet the appropriate
IEEE 802.3 specifications and are appropriate for the environment in which you are operating. CTI
recommends you use cables rated Category 5e or better.
Selecting an IP Address and Other Network Parameters
Before proceeding, you must determine what IP address you will assign to the module, the subnet mask to
use, and the IP address of the default gateway/router. If you are connecting to an existing network, your
network administrator should provide this information. If you are installing a stand-alone network, you should
choose from within the set of “private” IP addresses specified in RFC 1597. See APPENDIX D. IP ADDRESS
INFORMATION for a description of the IP Address numbering conventions.
Choosing a Module Startup Method
Before the 2572-B will communicate using TCP/IP, the IP address and related parameters must be set and the
module network server must be started. There are two startup options, described below.
AutoStart
If you choose this method, the module will automatically start the network server using IP parameters stored
in flash memory. The primary advantage of this approach is that it eliminates the need for additional PLC logic
to initiate startup. See Section 2.8. Storing Network Parameters in Flash.
The disadvantage of this method is that, when installing or replacing modules, you must manually configure
the IP parameters of the replacement module. In addition, if you arbitrarily swap 2572-B modules between
PLCs, the IP address will move with the module. The effect of inadvertently swapping IP addresses could
cause process problems, since communications directed at one PLC would actually be going to another PLC.

CTI 2572-B / 2500C-2572-B Installation and Operation Manual 4
PLC Start
Using this method, PLC logic is used to set the IP address of the module during startup. The Start Network
Services command, triggered by PLC logic, sets the IP parameters based on data stored in V memory. Once the
IP parameters are successfully set, the network TCP/IP services are started
An important advantage to this method is that it eliminates the need to manually configure the module during
the initial installation or during a replacement operation. In addition, since the network parameters are stored
in PLC memory, the module IP address remains associated with the PLC even when modules are swapped. The
primary disadvantage is that it requires a small amount of additional ladder logic. In addition, if the PLC is not
in run mode (not executing logic) the module will not start up. The PLC logic to perform this function is
described in CHAPTER 8. START NETWORK SERVICES COMMAND.
Choosing between TCP and UDP Protocols
Many HMI drivers and OPC servers will allow you to select either TCP (Transmission Control Protocol) or UDP
(User Datagram Protocol) for delivering messages. The 2572-B client functions also allow you to choose
between the two. The following information is provided to help you determine which is right for your
situation.
UDP Protocol
The UDP protocol allows you to send a message to another node without previously establishing a logical
connection to the other node. This method, called connectionless delivery, uses less network bandwidth,
consumes fewer module resources, and usually results in faster response times. Although the delivery of UDP
messages is not acknowledged by TCP/IP, higher level protocols, such as CAMP, confirm that the message was
received and that the requested service performed.
NOTE:
In most installations, UDP is the preferred protocol for HMI applications that continuously read data
from the PLC.
TCP Protocol
The TCP protocol requires that a logical connection be established between two points before messages can
be sent. This method, called connection-oriented services, provides delivery acknowledgement and message
flow control within the TCP/IP protocol. If a message is not delivered correctly, the TCP protocol will cause the
message to be re-transmitted.
Although TCP may be slightly slower than UDP because additional acknowledgement messages must be
transmitted and evaluated, there are several instances in which it should be used:
1. If you have a network whose quality requires a significant amount of message re-transmission, TCP can
provide better overall performance because the TCP is quicker at delivery acknowledgement and retry
than the application level, which typically relies on a message timeout measured in seconds.
2. If you are using the Internet to access the module, you may want to consider TCP. When traversing the
Internet, some gateways may break a packet up into smaller chunks, a process called fragmentation. The
smaller packets may be sent via different paths and could arrive out of order. TCP will ensure that the
fragmented packets will be re-assembled in the correct order, while UDP will not.

CTI 2572-B / 2500C-2572-B Installation and Operation Manual 5
Maximizing Performance
For best performance, you should place the module in a local rack (the one containing the PLC). Using a
Special Function module such as the 2572-B in a Remote I/O rack imposes significant additional
communications overhead and noticeably increases the scan time of the PLC. This effect is especially
noticeable when transferring large blocks of data.
NOTE:
The 2572-B will not work in a remote rack using the Profibus Remote Base Controller (RBC).
Profibus does not support Special Function modules.
The module is allowed to access to the PLC only once during a scan cycle. Ensure that the task codes per scan
setting of the PLC is set to eight (8). This allows the maximum number of PLC access requests to be processed
in a single scan. Set the PLC to the shortest acceptable scan time or use the variable scan time setting.
Excessive broadcast and/or multicast traffic can degrade performance. If you experience excessive
broadcast/multicast traffic, you will need to segment your network into separate Ethernet broadcast domains
or IP subnets.
Security Considerations
Since the 2572-B module communicates on a TCP/IP network, you should take precautions to prevent
someone from inadvertently or maliciously interrupting the operation of the module. Some actions you can
take include:
Use a dedicated network that does not connect to other networks. By eliminating external physical
connections, you limit access to only those on the network segment.
Use a router with firewall capability to connect to other networks. If isolating the network from other
networks is not practical, you can use “firewall” techniques to limit access from the outside.
Disable routing for the 2572-B modules. If you want to prevent access to the 2572-B modules from replying
to requests outside the local network segment but you want to allow your PC workstations
to access the corporate network, disable routing on the 2572-B module. You can accomplish
this by setting the Default Gateway/Router IP address to 0.0.0.0.
Use password protection or switch setting that limit access to module functions that could interrupt
service. Password protection is available for the Module Configuration and Firmware
Download functions. Switch settings can be used to prevent firmware update or
configuration changes.
Use hardware lockout protection to prevent configuration changes or firmware download. Switches on the
board can be used to disable these functions (see section 2.3. Setting the 2572-B Option
Switches).
Power Requirements
The CTI 2572-B module consumes a maximum of 2.8 watts of +5 VDC power from the backplane.

CTI 2572-B / 2500C-2572-B Installation and Operation Manual 6
2.2. Unpacking the Module
Open the shipping carton and remove the special anti-static bag that contains the module.
After discharging any static build-up, remove the module from the static bag. Do not discard the static bag.
Always use this bag for protection against static damage when the module is not inserted into the I/O base.
CAUTION:
The components on the 2572-B module printed circuit card can be damaged by static
electricity discharge. To prevent this damage, the module is shipped in a special anti-static
bag. Static control precautions should be followed when removing the module from the bag
and when handling the printed circuit card during configuration.
2.3. Setting the 2572-B Option Switches
Using the option switches on the 2572-B circuit board, you can designate how the module will operate. The
following illustration indicates the location of the switchblocks on both products.
2572-B 2500C-2572-B
Figure 1. Switchblock Locations

CTI 2572-B / 2500C-2572-B Installation and Operation Manual 7
The function of the switches is described below.
Figure 2. Option Switches
SW1, SW2: These switches are unused and may be set to any position with no effect.
SW3: This switch position is reserved for future use. It should be set to the open position to prevent a future
use from unintentionally affecting the module operation.
SW4: Startup Option: This switch selects how the 2572-B module will start network services.
Startup
Option
Position
SW4
AutoStart
Closed
PLC Start
Open
In the AUTOSTART position, the module will automatically start up using parameters stored in non-volatile
(flash) memory.
In the PLC START position, the module will start up in a limited function mode, using the parameters stored in
flash. It will then wait for PLC logic to trigger the START NETWORK SERVICES command before starting the network
services that allow access to the PLC. CHAPTER 4. describes the PLC logic required. When the command is
successfully completed, the IP parameters obtained from the PLC will be written to non-volatile (flash)
memory.
NOTE:
When using the PLC Start Option, the PLC must be in run mode before the module will start up in
full function mode.

CTI 2572-B / 2500C-2572-B Installation and Operation Manual 8
SW5: Configuration Lock. This switch allows you to prevent changes to the module IP parameters via the
Ethernet network. If the PLC Start option is selected, PLC logic will still be able to change the module IP
parameters.
Configuration Lock
Position
SW5
Locked
Closed
Unlocked
Open
When set to the LOCKED position, changes to the module IP parameters via the embedded web server Module
Configuration page will be prevented. In the UnlOCKED position changes will be allowed.
SW6: Firmware Update. This switch allows you to prevent updates to the module firmware. When set to the
CLOSED position, this switch prevents the user from the initiating firmware update using the embedded web
server Update Firmware page.
Firmware Update
Position
SW6
Disabled
Closed
Enabled
Open
SW7: Password Bypass. When set to the CLOSED position, this switch bypasses all password checks in the web
server. This is typically used to allow the password to be changed when the current password is unknown or
to eliminate the password check when password protection is not required.
Password Bypass
Position
SW7
Bypass
Closed
Not Bypassed
Open
SW8 – SW10: These switches are reserved for future use. They should be set to the open position to prevent
a future use from unintentionally affecting the module operation.
SW11: PLC Interface Mode. This switch allows you to select a PLC interface that is compatible with the CTI
2572 module and other Special Function I/O modules. By default, the 2572-B module uses a high
performance interface mode that increases the amount of data per scan that can be transferred to and from
the PLC and sets the task codes per scan to 8. In most cases, you should use the high performance mode.
However, in instances where minimizing PLC scan time is required, you may wish to use compatibility mode.
This is especially true when the 2572-B module is installed in a remote base where high performance mode
can significantly increase the PLC scan time.
Interface Mode
Position
SW11
Compatibility
Closed
High Performance
Open

CTI 2572-B / 2500C-2572-B Installation and Operation Manual 9
When this switch is set to the CLOSED position, the Special Function Interface will use the compatibility mode.
When the switch set to the OPEN position, the module will use a high performance interface mode.
SW12: This switch is reserved for future use. It should be set to the open position to prevent a future use
from unintentionally affecting the module operation
NOTE
The Option switches are read only at module startup. If you change the switch position after
startup, you must restart the module before the setting will take effect.
2.4. Physical Installation
Figure 3. Ethernet Connection
To insert the module into the I/O base, hold the top and bottom of the bezel and slide the module carefully
into the slot, pushing it all the way into the base. If you have inserted the module correctly, you will feel a
slight increase in resistance as the module mates with the base backplane connector. Once the module is fully
seated in the slot, tighten the captive screws at the top and bottom to hold the module in place. To remove
the module from the I/O base, loosen the captive screws, and then slide the module out of the base. Take
care not to damage the connector at the back of the module when inserting or removing the module.
2.5. Connecting the Ethernet Cable
Insert the 8 pin (RJ-45) plug on your unshielded twisted pair cable into the RJ-45 jack on the 2572. Push the
plug into the jack until the plug clicks into place. Attach the other end of the cable to an Ethernet switch.
2.6. Initial Power On
Apply power to the base. The module should begin a power-up sequence during which the LEDs and the
Multi-Segment Display will change state. See CHAPTER 3. MODULE OPERATION for a description of the
possible LED states. Early in the startup procedure, all LEDs and Multi-Segment Display (MSD) segments will be
turned on approximately 1 second.
2.7. Entering the Module into the PLC I/O Configuration
To enter the module into the PLC I/O configuration, you will need to use your PLC programming application.
The 2572-B is configured as a Special Function module with 2 WX and 6 WY words. In the following example,
the 2572-B module is installed into slot 1 on I/O base 0 and will be logged in starting at address 1. Your
configuration may differ.

CTI 2572-B / 2500C-2572-B Installation and Operation Manual 10
Figure 4. Example I/O Configuration
After you read the I/O base, if the number of WX and WY words are the same as those shown in the example
above and Special function = YES, then the PLC can recognize the module. Change the address as required by
your application and save the result. If the line is blank or erroneous, re-check the module to ensure that it is
firmly seated in the I/O base slot. Generate the PLC I/O configuration chart again by reading the I/O base. If
the problem persists, contact your distributor or contact CTI.
NOTE:
The module must be configured in the I/O table before you can use PLC logic to start the module or
control the module operation from the PLC.
2.8. Storing Network Parameters in Flash
If you have selected the AutoStart option, you will need to manually set the IP parameters to correspond to
your networking requirements.
The 2572-B IP Parameters can be set using the embedded web server. Point your browser to the main Product
Information page by entering the IP address of the 2572-B module in the browser URL field. From the list of
pages on the left hand side of the page, select the MODULE CONFIGURATION page. Unless you have bypassed
password protection, you will be asked for a User ID and Password. When the configuration page is
displayed, enter the new IP address information in the appropriate fields and press the Update Module
button.
The 2572-B is shipped from CTI with the IP address set to 169.254.1.1 and the subnet mask set to 255.255.0.0.
To connect to the module, you must ensure that your PC has an IP address that is on the same IP network and
is not the same as the module IP address.
One method of providing your PC with compatible IP address is to use Windows Control Panel (or Windows
Settings in Windows 10) to configure a static IP address. In this case, the first two octets of the PC IP address
must be 169.254, the last two octets of the PC IP address must not be 1.1, and the PC subnet mask must be set
to 255.255.0.0 . For example, an IP address of 169.254.1.2 will work.

CTI 2572-B / 2500C-2572-B Installation and Operation Manual 11
Instead of manually setting a static address, you can cause your PC to generate a compatible address, if your
PC is using DHCP (Dynamic Host Configuration Protocol) to obtain an IP address.
The IP address 169.254.1.1 is a link local IP address, which is used only to communicate on the local network.
When a Windows PC is unable to obtain an IP address from DHCP, it automatically generates a link local
address using a feature called Automatic Private IP Addressing. To cause the PC to generate a compatible
address, do the following:
•Connect an Ethernet cable directly between your PC and the 2572-B module,
•Reboot the PC.
NOTE: It may take several minutes before the PC will stop trying to contact a DHCP server and generate the Link
Local address. You can display the IP parameters being used by the PC by opening the Command Prompt
window and entering IPCONFIG at the prompt. Once the link local IP address is generated, you can connect by
typing http://169.254.1.1 in your browser’s URL box.
2.9. Module Checkout
If functioning properly, the 2572-B will respond to an ICMP Echo Request message known as a ping. Using a PC
on the local network, open the Command Prompt window and type the following: PING IPaddress
where IPaddress is the IP address of the module in dotted decimal format. If the module does not reply,
refer to CHAPTER 8. TROUBLESHOOTING.


CTI 2572-B / 2500C-2572-B Installation and Operation Manual 13
CHAPTER 3. MODULE OPERATION
3.1. Front Panel Features
Status LED Indicators
The following table describes the module LED indicators.
LED Name
Purpose
Function
MS: Module Status
Indicates the
operational state of
the module.
Off: Application Firmware not started
Steady Green: Module Operational
NS: Network Status
Indicates the status
of the network
interface.
Off: Network Interface not started
Flashing Green: The module is waiting on
PLC logic to start network services (PLC
Start option).
Flashing Red: The module is waiting on
the PLC logic to start network services.
The IP address initially read from flash is a
duplicate of another IP host on the
network.
Steady Green: The network interface is
operational.
Steady Red: The network interface is
operational. The module IP address is a
duplicate of another IP host with the same
IP address is on the network.
ACT: Ethernet Activity
Indicates activity on
the Ethernet Link.
Off: No Ethernet activity detected.
Flashing: Ethernet frames are being
received and/or transmitted.
LS: Link Status
Indicates status of
Physical Link.
Off: Ethernet link not operational.
On: Ethernet Link is operational.
FDX: Full Duplex
Indicates Ethernet
link duplex mode.
Off: Operating in half duplex mode or not
connected to network.
Steady Green: Operating in full duplex
mode.
100: Ethernet Speed
Indicates the
Ethernet baud rate.
Off: Operating at 10Mb or not connected
to a network.
On:Operating at 100Mb.

CTI 2572-B / 2500C-2572-B Installation and Operation Manual 14
Multi-Segment Display (MSD)
The Multi-Segment Display (MSD) is located below the status LEDs. During normal operation the MSD will
display certain status information and the TCP/IP address of the module and the subnet mask in CIDR format.
CIDR format is a compact way of displaying the network mask. See APPENDIX C. IP ADDRESS INFORMATION
for more information regarding CIDR format.
Reset Button
Some module functions, such as reading module switch settings or using new IP parameters stored in flash,
are performed only at startup. The Reset Button is a momentary contact switch that allows you to restart the
module without having to cycle power to the base. It is recessed to prevent inadvertent use. To reset the
module, use a small object such as the tip of a ball point pen to depress and hold the switch for approximately
one second. When the switch is released, the module will begin the startup sequence.
NOTE:
To reset the parameters stored in flash memory to factory default values, hold the reset button
down for 10 seconds or more.
Ethernet Port
The 2572-B provides a Category 5e RJ-45 connector which attaches directly to Unshielded Twisted Pair (UTP)
or Shielded Twisted Pair (STP) Ethernet cabling. The port complies with the IEEE 802.3 specifications for
10BaseT and 100Base TX and will operate in either half or full duplex mode. The speed and mode are
automatically negotiated by the module in accordance with IEEE 802.3u specifications. When attaching to a
hub or switch that does not support auto-negotiation, the port will default to 10Mb half-duplex.
3.2. Module Startup
After power is applied to the 2572-B module, when the Reset button is pressed, or when the module is
restarted by software or the reset switch, the module will begin the startup procedure. After the application
firmware is running, all LEDs and MSD segments will be illuminated for approximately one second (multicolor
LEDs will be red for ½ second and green for ½ second), and then will be turned off. This serves a display test
and as an indication that module startup is in process.
AutoStart Mode
If the AUTOSTART option is selected (via SW4), the module will start up using the IP address stored in flash. If
the startup is successful, all module network services, including the embedded web server, CAMP Server,
Modbus TCP Server, and the Ethernet IP server, will be enabled. After startup, the MS LED should be STEADY
GREEN and the Multi-Segment Display (MSD) should display the module IP address and subnet mask (in CIDR
format). The NS LED should be either STEADY RED if a duplicate IP has been detected (indicating the module IP
address is the same as another IP Host on the network) or STEADY GREEN if no duplicate has been detected.
PLC Start Mode
If the PLC START option is selected, the module will start up in a limited function mode using the IP address
stored in flash, enabling only the embedded web server. Then it will wait on the PLC logic to set the IP address
and enable the application servers using the Start Network Services command. While the module is waiting
This manual suits for next models
1
Table of contents
Popular Network Card manuals by other brands
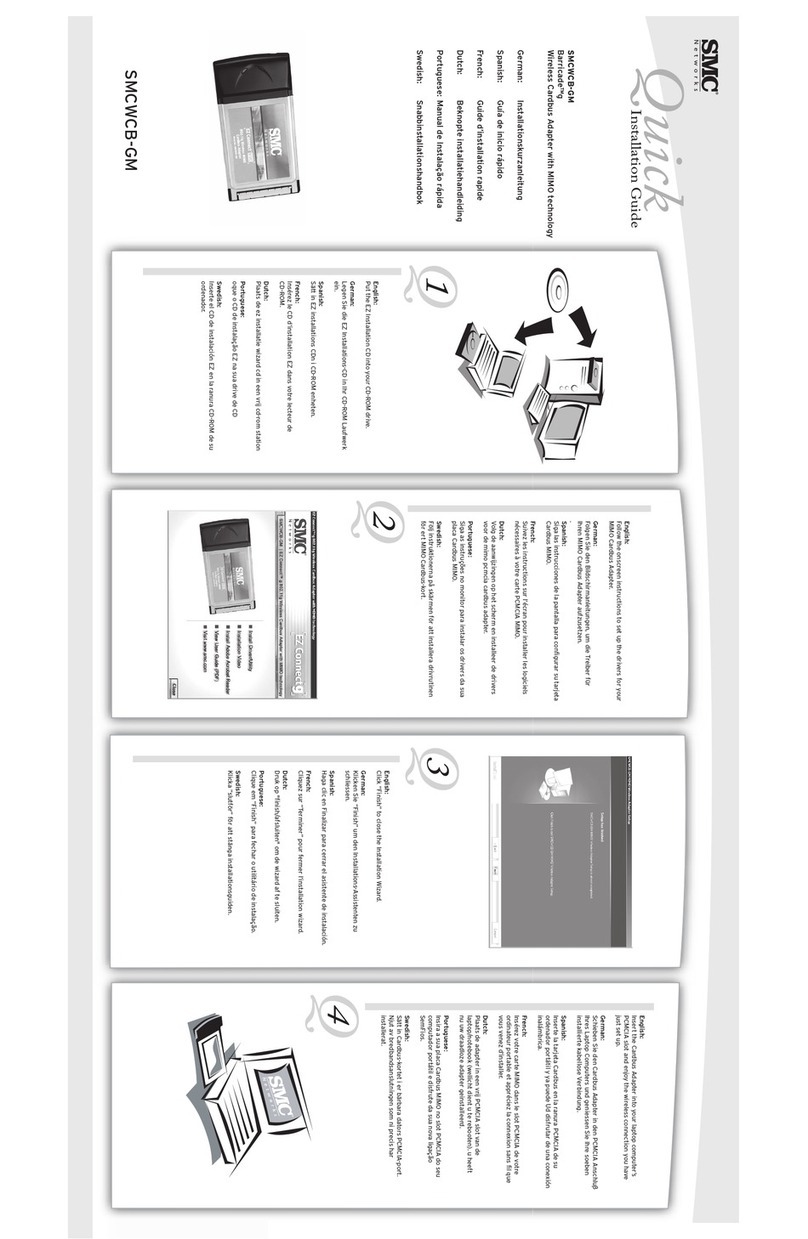
SMC Networks
SMC Networks Barricade SMCWCB-GM manual
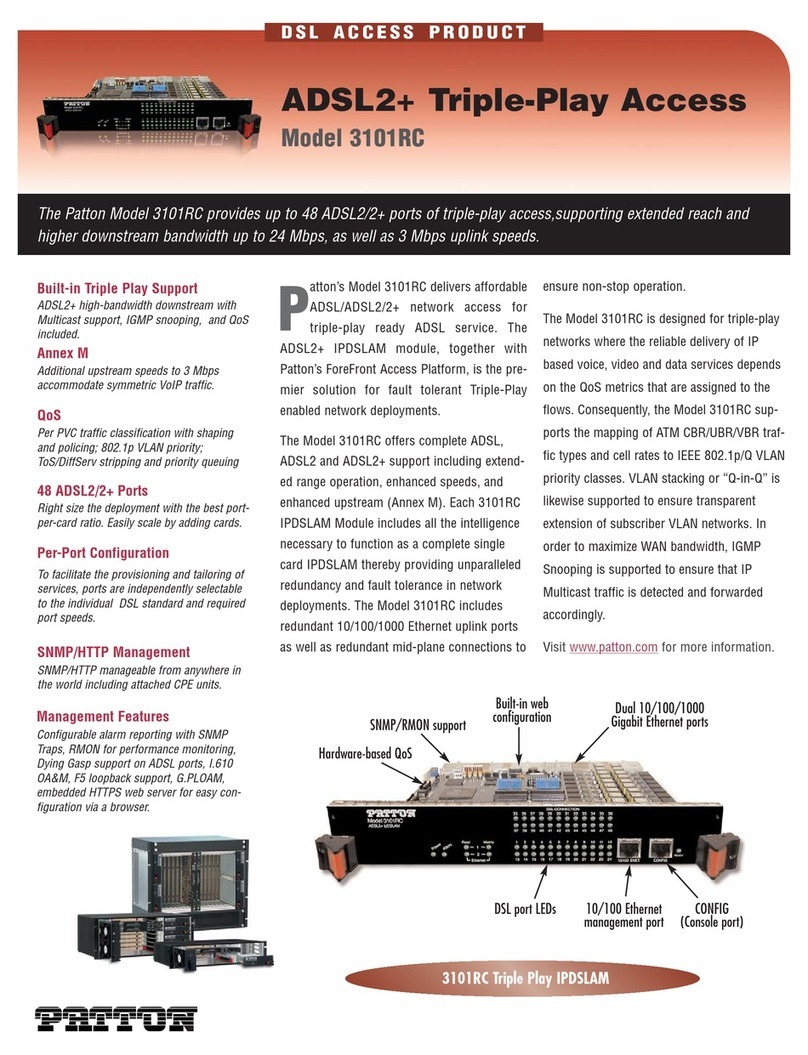
Patton electronics
Patton electronics 3101RC Specifications
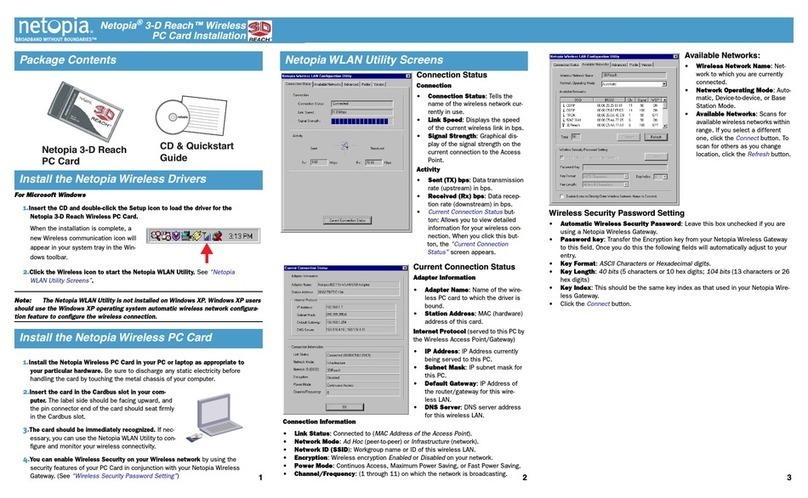
Netopia
Netopia Network Card user manual
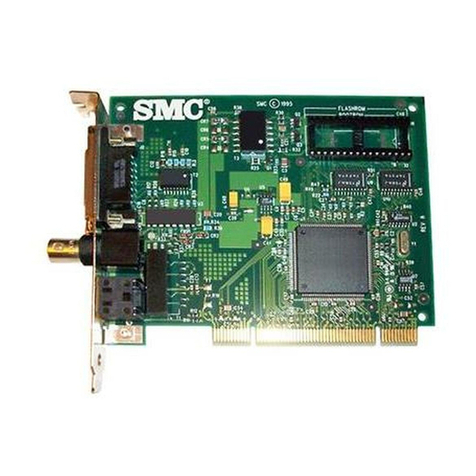
SMC Networks
SMC Networks SMC9432BTX user guide
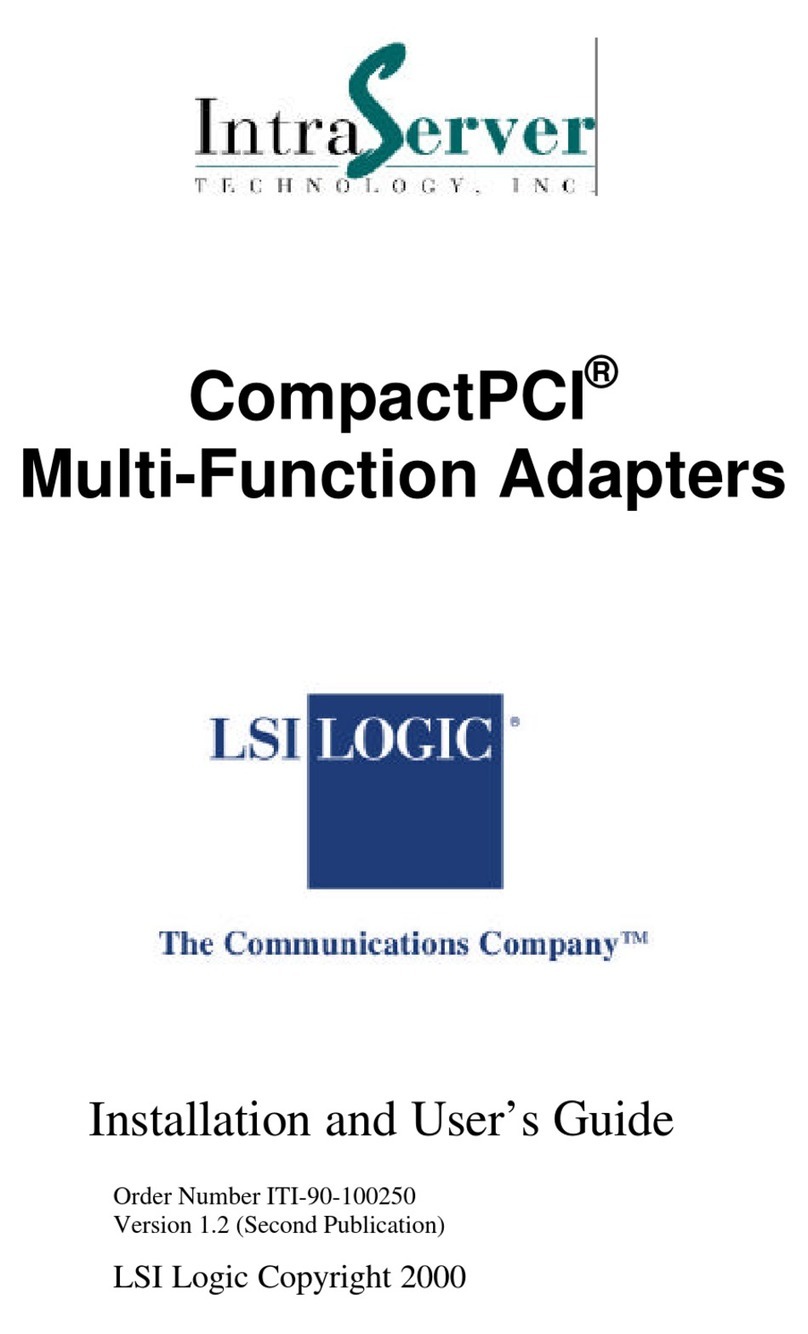
IntraServer Technology
IntraServer Technology ITI-90-100250 Installation and user guide
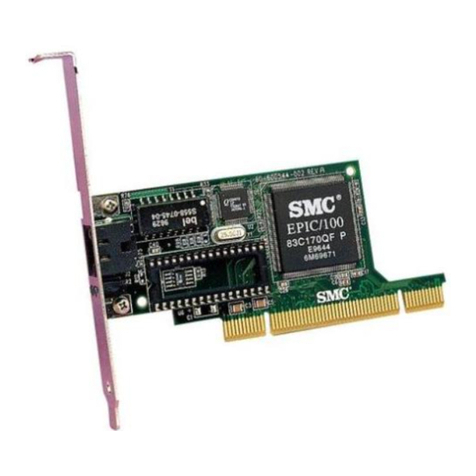
SMC Networks
SMC Networks SMC9432TX user guide