Cygnus 1 User manual

CYGNUS 1
Digital Ultrasonic
Thickness Gauge
CYGNUS
INSTRUMENTS
Ultrasonic NDT Equipment
OPERATION MANUAL
ROV-MOUNTABLE
SYSTEM

CYGNUS 1 ROV ULTRASONIC
THICKNESS GAUGE
ROV-MOUNTABLE SYSTEM

V6.21A - Jul 06 S.074 / Issue 2
2
QUALITY POLICY STATEMENT
“It is the policy of Cygnus Instruments to provide all customers with products and
services of a quality that complies in all respects with the requirements contained in
their orders and specifications.
“It is our firm belief that excellence can only be achieved and maintained by
continual appraisal. The organisation, methods, and procedures adopted by the
company aim to both fulfil this policy and ensure adherence to it.”
Cygnus is an ISO-9001 accredited company.
The scope of our accreditation covers all our products and services.
abcde

Content
3
CYGNUS 1 ROV
ULTRASONIC THICKNESS GAUGE
OPERATION MANUAL
INTRODUCTION 5
Cygnus 1 ROV Ultrasonic Thickness Gauge 6
Cygnus Instruments 7
The Multiple-Echo Method 8
Cygnus 1 ROV Specification – Deep-Water Gauge 9
Cygnus 1 ROV Specification – Shallow-Water Gauge 10
Cygnus 1 ROV Specification – Mini-ROV Lightweight Gauge 11
Selection of Ultrasonic Probes 12
Serial Data Format 13
INSTALLING THE UNDERWATER GAUGE 15
Cygnus 1 ROV Kit Contents – Deep-Water & Shallow-Water Gauge 16
Cygnus 1 ROV Kit Contents – Mini-ROV Lightweight Gauge 17
Gauge Assembly & Disassembly 18
Underwater Cable Connector 18
Probe/Knurled Ring Assembly 20
Data & Power Connections 21
VIEWING MEASUREMENTS ON THE PC 23
Computer Connection Options 24
Installing the CygLink Program 25
Installing the USB-to-Serial Adaptor Drivers 26
Connecting the System Together 27
Using the CygLink Remote Display Program 31

Content
4
MEASURING WITH THE GAUGE 34
Controls 35
Calibrating the Gauge 35
Measurement 38
Probe Usage 39
Troubleshooting 40
General Points on Thickness Gauging 42
A Guide to Sound Velocities 43
Table of Sound Velocities 44
WORKING WITH LOG-FILES 45
About Log-Files 46
Viewing Log-Files 47
Creating a Report File 48
Printing Files Using CygLink 50
File Format 51
CREATING TEMPLATE-FILES USING CYGLINK 52
About Template-Files 53
Creating a Single-Record File 54
Creating a Multi-Record File 55
Creating a Key-Point File 56
Creating a Grid-Point File 61
REMOTE-LOGGING 63
Using Remote-Logging 64
Quick Logging 65
Remote-Logging to Datalogger Files 68
Logging to a Single-Record File 69
Logging to a Multi-Record File 71
Logging to a Key-Point File 72
Logging to a Grid-Point File 74
CARE AND SERVICING 80
Care of the Cygnus 1 ROV Gauge 81
Servicing 82
Recycling & Disposal 83
RoHS Directive 83

Introduction
5
INTRODUCTION
Cygnus 1 ROV Ultrasonic Thickness Gauge
Cygnus Instruments
The Multiple-Echo Method
Cygnus 1 ROV Specification – Deep-Water Gauge
Cygnus 1 ROV Specification – Shallow-Water Gauge
Cygnus 1 ROV Specification – Mini-ROV Lightweight Gauge
Selection of Ultrasonic Probes
Serial Data Format

Introduction
6
CYGNUS 1 ROV ULTRASONIC THICKNESS GAUGE
The Cygnus 1 ROV Multiple-Echo Ultrasonic Thickness Gauge is designed for high-
reliability thickness measurement using the multiple-echo technique.
The Gauge is designed to be mounted onto most types of work-class ROV with or without a
manipulator facility. There is also a lightweight version of the Gauge for use with smaller
ROVs.
All versions of the Gauge are fully-waterproof, and can be used both underwater and in air -
Cygnus manufactures the Cygnus 1 ROV Thickness Gauge in three system options :
¾Deep-Water Version :
pressure-tested down to 3000 metres
¾Shallow-Water Version :
pressure-tested down to 1000 metres
¾Mini-ROV Lightweight Version :
pressure-tested down to 500 metres
All versions of the Gauge are supplied with dedicated PC-software for displaying and
logging the thickness readings at the surface.
The Gauge is supplied with one Ultrasonic Probe – the Probe-type must be specified at the
time of purchase of the Gauge. Probes are not freely interchangeable – please consult with
Cygnus if you wish to use a different Probe with the Gauge.
The Cygnus 1 ROV Ultrasonic Thickness Gauge is a solid-state electronic instrument
which, under normal operating conditions, will give many years of active service.
Although designed for ease of operation, the first time user should carefully read this manual
to familiarise themselves with the features of the instrument.

Introduction
CYGNUS INSTRUMENTS
Cygnus Instruments Limited, founded in 1983, were pioneers in the development of the
Ultrasonic Multiple-Echo Technique used for measurement through coatings. This has long
been the standard required to ensure that accurate measurements are taken without the need
to first zero the Gauge or remove coatings.
Our philosophy is to work closely with each of our customers to provide a range of products
specifically for each application. Cygnus Ultrasonic Thickness Gauges are designed to be
simple to use and to withstand the harsh environments that they are intended for. We have
built up an enviable reputation with our customers in over 45 countries around the world.
website : www.cygnus-instruments.com
CYGNUS Instruments Limited CYGNUS Instruments Inc.
Cygnus House 1993 Moreland Parkway
30 Prince of Wales Road Suite 202
Dorchester Annapolis
Dorset DT1 1PW Maryland 21401
England USA
Tel: 00 44 (0) 1305 265533 Tel: 00 1 410 267 9771
Fax: 00 44 (0) 1305 269960 Fax: 00 1 410 268 2013
7

Introduction
THE MULTIPLE-ECHO METHOD
The Cygnus 1 ROV Ultrasonic Thickness Gauge works on the pulse-echo principle. The
Probe is made to vibrate for a very short period, creating a pulse of ultrasound which enters
the test piece. The Probe waits for returned echos and acting as a receiver, converts them
into electrical signals which are processed to produce timings in digital form.
The multiple-echo beam travel is depicted above, spread out for time, to illustrate the timing
method. The beam path is in fact straight, at 90 degrees to the surface and the ultrasonic
energy reverberates up and down within the metal (as shown in the small sketch above -
left). Each time the echo is reflected back down, a small portion of the energy comes up
through the coatings, striking the Probe which now acts as a receiver.
The delay between echoes at the Probe-face is exactly equal to the time taken to pass
through the metal twice, therefore coatings such as paint are ignored and the measurement
displayed is of the metal thickness only.
8

Introduction
9
CYGNUS 1 ROV SPECIFICATION – DEEP-WATER GAUGE
Materials
Sound Velocity from 1000 m/s to 9995 m/s
[0.0400 in/uS to 03998 in/uS]
Range
Typical Measurable Range in Steel :
with 2¼ MHz Probe : 3mm to 250mm [0.120 in. to 10.0 in.]
with 3½ MHz Probe : 2mm to 150mm [0.080 in. to 6.0 in.]
Resolution
0.1 mm [0.005 in.] or
0.05 mm [0.002in.]
Accuracy
± 0.1 mm [± 0.005 in.] or
± 0.05 mm [± 0.002 in.]
Probes
Single-Crystal, Soft-face Compression Probes :
¾2¼ MHz : 13mm [0.5 in.]
¾2¼ MHz : 19mm [0.75 in.]
¾3½ MHz : 13mm [0.5 in.]
Operating
Temperature
Recommended :
-10°C to +50°C [14°F to 122°F]
Power Supply
Power Supply Requirement :
7.5 – 30 Vdc @ 100mA typical, 150mA maximum
Data-link
RS-422 Communication, differential pair, single direction
Display
Software
Computer Requirement :
Windows®-compatible PC or Laptop (486 minimum) with 45
MB free hard disk space
One free Serial COM-port, or a USB connection
Size
Gauge-Body dimensions, excluding cabling :
Length 237 mm x Diameter 70 mm [9.3 in. x 2.8 in.]
Probe-Cable length : 5 metre [16 ft. 5 in.]
Weight in Air
With Remote Probe – 4.0 Kg [141 ounce]
Water Depth
Fully Waterproof :
Pressure tested to a depth of 3000 m [9842 ft.]

Introduction
10
CYGNUS 1 ROV SPECIFICATION – SHALLOW-WATER GAUGE
Materials
Sound Velocity from 1000 m/s to 9995 m/s
[0.0400 in/uS to 03998 in/uS]
Range
Typical Measurable Range in Steel :
with 2¼ MHz Probe : 3mm to 250mm [0.120 in. to 10.0 in.]
with 3½ MHz Probe : 2mm to 150mm [0.080 in. to 6.0 in.]
Resolution
0.1 mm [0.005 in.] or
0.05 mm [0.002in.]
Accuracy
± 0.1 mm [± 0.005 in.] or
± 0.05 mm [± 0.002 in.]
Probes
Single-Crystal, Soft-face Compression Probes :
¾2¼ MHz : 13mm [0.5 in.]
¾2¼ MHz : 19mm [0.75 in.]
¾3½ MHz : 13mm [0.5 in.]
Operating
Temperature
Recommended :
-10°C to +50°C [14°F to 122°F]
Power Supply
Power Supply Requirement :
7.5 – 30 Vdc @ 100mA typical, 150mA maximum
Data-link
RS-422 Communication, differential pair, single direction
Display
Software
Computer Requirement :
Windows®-compatible PC or Laptop (486 minimum) with 45
MB free hard disk space
One free Serial COM-port, or a USB connection
Size
Gauge-Body dimensions, excluding cabling :
Length 237 mm x Diameter 70 mm [9.3 in. x 2.8 in.]
Probe-Cable length : 5 metre [16 ft. 5 in.]
Weight in Air
With Remote Probe – 1.25 Kg [44 ounce]
Water Depth
Fully Waterproof :
Pressure tested to a depth of 1000 m [3281 ft.]

Introduction
11
CYGNUS 1 ROV SPECIFICATION – LIGHTWEIGHT GAUGE
Materials
Sound Velocity from 1000 m/s to 9995 m/s
[0.0400 in/uS to 03998 in/uS]
Range
Typical Measurable Range in Steel :
with 2¼ MHz Probe : 3mm to 250mm [0.120 in. to 10.0 in.]
with 3½ MHz Probe : 2mm to 150mm [0.080 in. to 6.0 in.]
Resolution
0.1 mm [0.005 in.] or
0.05 mm [0.002in.]
Accuracy
± 0.1 mm [± 0.005 in.] or
± 0.05 mm [± 0.002 in.]
Probes
Single-Crystal, Soft-face Compression Probes :
¾2¼ MHz : 13mm [0.5 in.]
¾2¼ MHz : 19mm [0.75 in.]
¾3½ MHz : 13mm [0.5 in.]
Operating
Temperature
Recommended :
-10°C to +50°C [14°F to 122°F]
Power Supply
Power Supply Requirement :
7.5 – 30 Vdc @ 100mA typical, 150mA maximum
Data-link
RS-422 Communication, differential pair, single direction
Display
Software
Computer Requirement :
Windows®-compatible PC or Laptop (486 minimum) with 45
MB free hard disk space
One free Serial COM-port, or a USB connection
Size
Gauge-Body dimensions, excluding cabling :
Length 160 mm x Diameter 62 mm [6.3 in. x 2.4 in.]
Probe-Cable length : 100 mm [3.9 in.]
Weight in Air
With Remote Probe - 550 gm [19.4 ounce]
Water Depth
Fully Waterproof :
Pressure tested to a depth of 500 m [1640 ft.]

Introduction
12
SELECTION OF ULTRASONIC PROBES
The Cygnus 1 ROV Gauge is supplied with a single heavy-duty Ultrasonic Probe, which
comes in a waterproof assembly with the Probe fixed to a cable which connects to the
removable nose-cone of the Gauge.
UProbe-assemblies are not freely interchangeable – the Gauge is preset for optimum
performance with the supplied Probe
Cygnus offers a selection of different Probe-types – the table below shows which Probe to
choose, depending on the application.
LThe Deep-Water and Shallow-Water versions of the Gauge are normally supplied with a
5 metre Probe-cable assembly, and the Mini-ROV Lightweight version is normally
supplied with a 0.1 metre cable – other cable-lengths are available on request.
CRYSTAL
DIAMETER
FREQUENCY
MEASUREMENT
RANGE
APPLICATION
13 mm
½ inch
2¼ MHz
Red face
3.0 – 250 mm
0.12 – 10 inch
This is the standard probe –
suitable for most applications
19 mm
¾ inch
2¼ MHz
Red face
3.0 – 250 mm
0.12 – 10 inch
Use with castings and other
attenuative materials if the
13mm probe is inadequate –
the larger diameter gives
greater penetration power on
badly corroded or heavily
coated steel. Some metallic
coatings are also highly
attenuative.
13 mm
½ inch
3½ MHz
Orange face
2.0 – 150 mm
0.08 – 6 inch
Suitable for measurement on
thinner sections where
surfaces are relatively rough

Introduction
13
SERIAL DATA FORMAT
CygLink program is provided to automatically decode the measurement data sent from the
Gauge, and to provide a calibrated display of the results
For users who want to display and log the data using their own software : this describes the
arrangement of the data sent from the Gauge
Data Communication Format
¾Data Output Standard
ÖDifferential RS-422 line drivers [TX+, TX-]
ÖUnidirectional - Gauge is transmit only
¾Data-byte Format
Ö8 Data bits, 1 Start bit, 1 Stop bit, No Parity; 2400 baud
¾Data-Packet Arrangement
Ö4 packets per second
ÖValid-Reading packet-length : 7 bytes
ÖNo-Reading packet-length : 3 bytes
Interpreting the Reading sent from the Gauge
¾Scaling
ÖThe Gauge takes measurements using an accurate fixed-rate crystal oscillator
ÖReadings are scaled for an equivalent Velocity of Sound of 6400 m/s
ÖDisplayed readings have to be scaled by multiplying by the Velocity of Sound (in
m/s) for the Material-under-Test, and then dividing by 6400
ÖDecimal Point position is implied from the combination of Range, Resolution, and
Units bits in the Status byte of each Reading [see table below]
¾Range
ÖThe Gauge returns all Readings in a 4-byte decimal string
ÖReadings which require 5-bytes [eg 100.00+mm, or 10.000+inch] are autoranged to
the 4 most significant bytes
ÖRange bit for every Reading must be read from the Status-byte
¾Resolution
ÖThe Gauge has a default Hi-Resolution setting : 0.05 mm, or 0.002 inch
ÖLo-Resolution setting is not normally used : 0.1 mm, or 0.005 inch
ÖResolution bit must be read from the Status-byte
¾Units
ÖThe Gauge has a default Metric Units-setting
ÖUnits bit must be read from the Status-byte

Introduction
14
Valid-Reading packet arrangement
7 byte sequence :
1. SOH [hex 01]
2. Status-byte
3. Data-byte 0
4. Data-byte 1
5. Data-byte 2
6. Data-byte 3
7. ETB [hex 17]
No-Reading packet arrangement
3 byte sequence :
1. SOH (hex 01)
2. Status Byte
3. ETB (hex17)
Status-byte structure
decodes into bit-fields :
¾bit 7 - ms Cygnus Gauge type HI = Mark2+ [default]
[LO = Mark1 – not used]
¾bit 6 Reading Resolution HI = Hi-Resolution [default]
¾bit 5 Measurement Units LO=Metric [default]
HI=Imperial
¾bit 4 Reading Range HI = Hi-Range
¾bits 3, 2 Echo Count 0 to 3 Echoes found
¾bit 1 Calibration HI = Remote [default]
LO=Local
¾bit 0 - ls No-Reading flag HI = No-Reading
LO=Valid-Reading
Data-bytes arrangement
¾The four data bytes are ASCII-encoded, decimal thickness value
¾Data byte 0 is most-significant
¾Leading-zeroes are replaced by ascii Space [hex 20]
¾Decimal points are implied from the Status-byte – Units, Resolution and Range bits :
Reading-type Hi-Range Lo-Range
ÖImperial, Lo-Resolution x x . x x x . x x x
ÖMetric, Lo-Resolution x x x . x x x x . x
ÖImperial, Hi-Resolution x x . x x x . x x x
ÖMetric, Hi-Resolution x x x . x x x . x x

Installing the Gauge
15
INSTALLING THE GAUGE
Cygnus 1 ROV Kit Contents – Deep-Water Gauge & Shallow-Water Gauge
Cygnus 1 ROV Kit Contents – Mini-ROV Lightweight Gauge
Underwater Cable Connector
Gauge Assembly & Disassembly
Probe/Knurled Ring Assembly
Data & Power Connection

Installing the Gauge
CYGNUS 1 ROV KIT CONTENTS
DEEP-WATER GAUGE & SHALLOW-WATER GAUGE
Deep-Water Gauge and Shallow-Water Gauge – Kit Contents
•Instrument Body
•Blanking-Plug
•Heavy Duty Remote Probe
•Bottle of Membrane Oil, and Packet of Membranes [not shown]
•O-Rings, type A and B
•Nose Cone Torque Bar
•Locking Ring Key
•Steel Test Block
•Molykote
•4-way Impulse Connector with flylead [not shown]
•9-way D-connector [not shown]
•Surface Test Cable [not shown]
•KKE/K3 RS422-to-RS232 Adaptor
•RS232-to-USB Adapator [not shown]
•CygLink Remote Display Software CD
16

Installing the Gauge
CYGNUS 1 ROV KIT CONTENTS
MINI-ROV LIGHTWEIGHT GAUGE
Mini-ROV Lightweight Gauge – Kit Contents
•Instrument Body
•Blanking-Plug
•Heavy Duty Remote Probe
•Bottle of Membrane Oil, and Packet of Membranes [not shown]
•O-Rings, type A and B
•Nose Cone Torque Bar
•Locking Ring Key
•Steel Test Block
•Molykote
•4-way Impulse Connector with flylead [not shown]
•9-way D-connector [not shown]
•Surface Test Cable [not shown]
•KKE/K3 RS422-to-RS232 Adaptor
•RS232-to-USB Adapator [not shown]
•CygLink Remote Display Software CD
17

Installing the Gauge
GAUGE ASSEMBLY & DISASSEMBLY
Fitting the Probe-module
Fit the two O-Rings, A and B, then attach the Probe-module to the Gauge-body :
ÖCover both O-Rings with a light coating of Dow Corning Molykote, then fit as shown in
the diagram below
¾Ais fitted into the O-Ring groove in the Nose-cone housing
¾Bis to be fitted in the O-Ring groove at the front of the instrument
ÖEnsure that the O-Rings are properly located
There is no need to stretch or force the O-Rings into their locations
ÖScrew the Probe-module onto the Gauge-body, hand tight.
Do not use the Nose-cone torque bar to tighten.
LOnly use the torque bar to undo the Nose-cone after a dive : both O-Rings should be
discarded after each dive.
UBoth O-Rings must be replaced after every dive
See : Care of the Cygnus 1 ROV Underwater Gauge section on page 81
UAll parts are designed to ensure a good water-tight fit : incorrect fitting will result in
the instrument leaking.
18

Installing the Gauge
UNDERWATER CABLE CONNECTION
The Cygnus 1 ROV Underwater Gauge is provided with a fully-waterproof external cable
connection. To maintain the integrity of the electrical operation and watertight-seal it is
essential that these precautions are observed :
ÖCable connection should only ever be made in dry ambient conditions at the surface
Connections must never be made, or broken, underwater
ÖBoth the male Underwater Cable connector and the Blanking-plug should have
Molykote smeared on the pins before inserting into the Gauge
ÖThe male plug-connector should be pushed fully into the female socket-connector, and
then the rubber retaining-loop should be pushed into the groove on the male-connector,
to complete the fully-waterproof connection
LA Blanking-plug is supplied for use - for safety we recommend that the Blanking Plug is
fitted at all times that there is no cable attached to the Gauge body
19
Table of contents
Other Cygnus Measuring Instrument manuals
Popular Measuring Instrument manuals by other brands
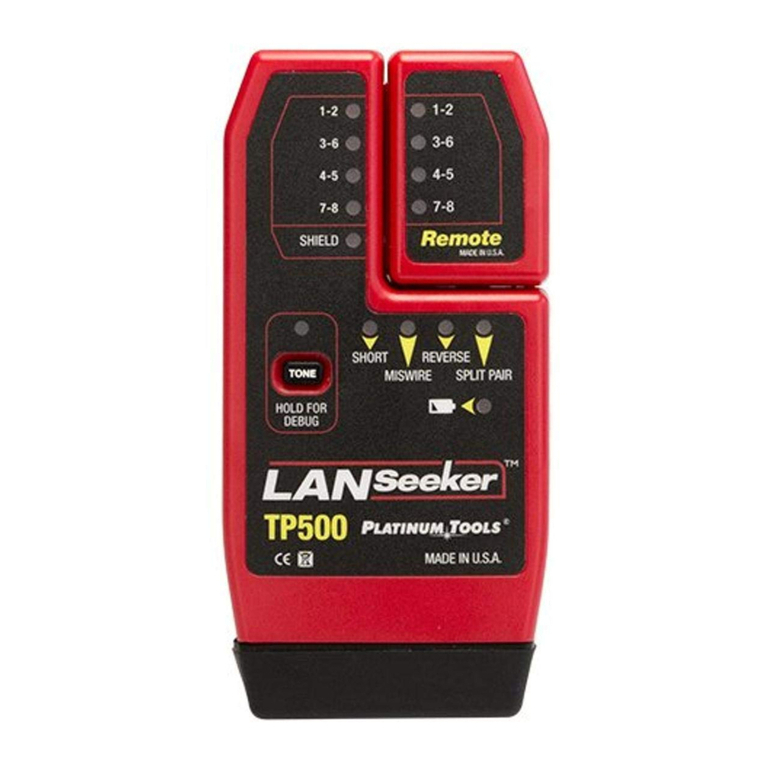
Platinum Tools
Platinum Tools LANSeeker TP500 user manual

PCB Piezotronics
PCB Piezotronics ICP 337A31 Installation and operating manual
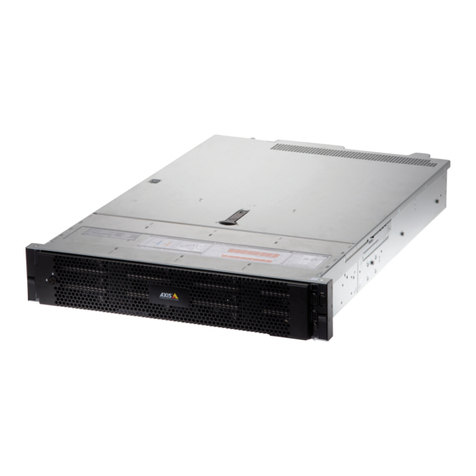
Axis
Axis S1148 installation guide
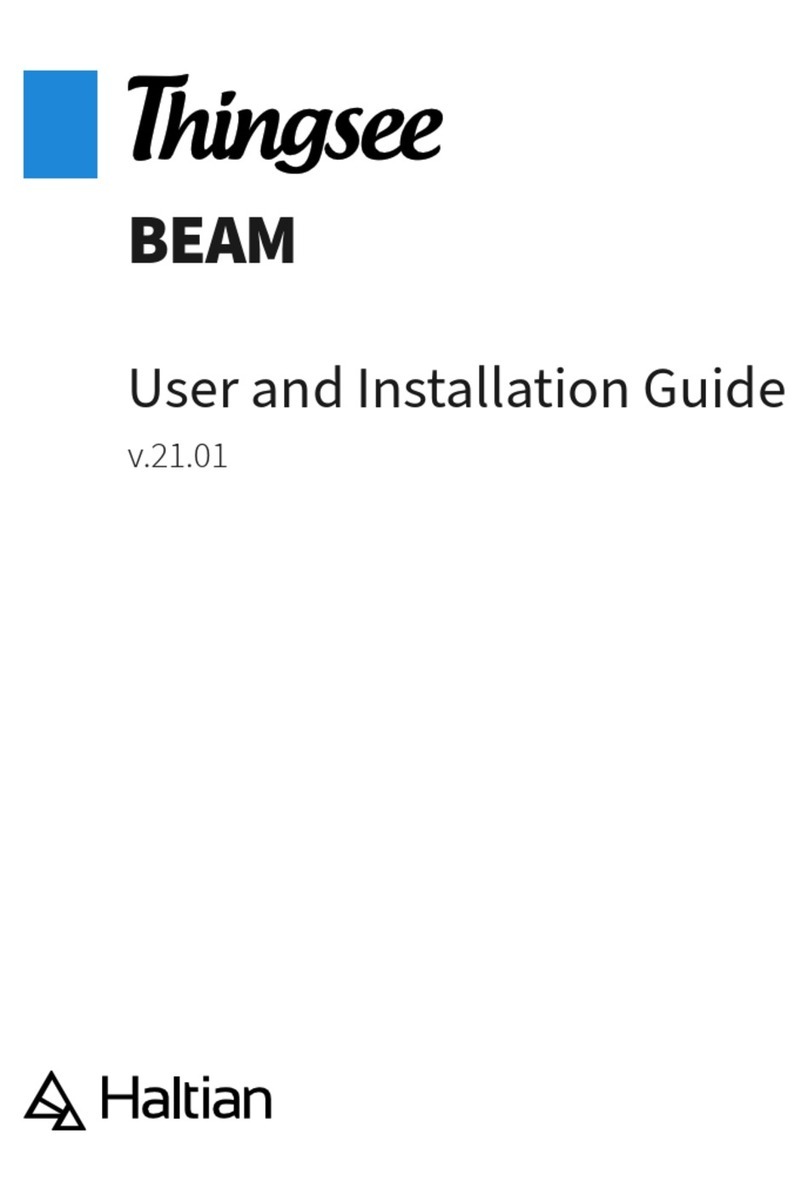
Haltian
Haltian Thingsee BEAM User and installation guide
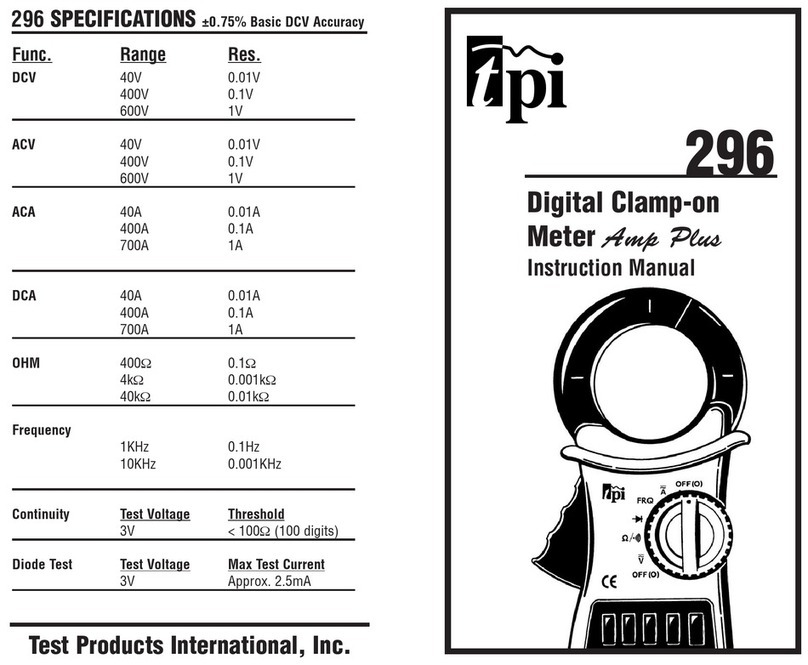
TPI
TPI Amp Plus instruction manual
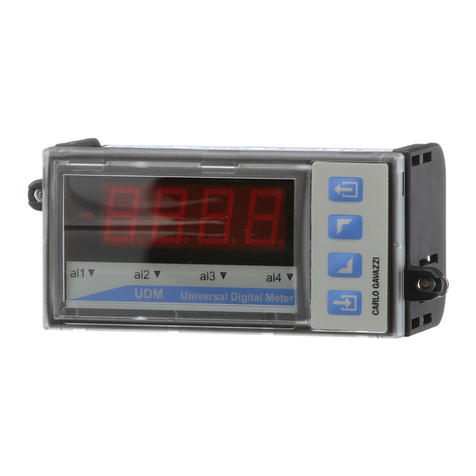
CARLO GAVAZZI
CARLO GAVAZZI UDM 35 - PROGRAMMING Programming guide