Cygnus ROV UTM User manual

Cygnus ROV UTM
Ultrasonic Thickness Gauge
Operating Manual
Covers Instrument Model: M5-ROV-ASCAN
with SD2D-DCW Probe
Doc No. Cygnus ROV UTM Operation Manual (Issue 7).docx
June 2022

Cygnus ROV UTM - Operating Manual
Page 2 of 60
Contents
1. Introduction......................................................................5
Cygnus ROV UTM...................................................................5
Register your Gauge ..............................................................6
Kit Contents..........................................................................7
Optional Items ......................................................................7
2. System Overview ..............................................................8
Subsea Instrument ................................................................8
Ultrasonic Probe ....................................................................8
P50 Probe Handler ...............................................................10
3. Connecting the System Together ....................................13
Subsea Instrument ..............................................................13
Power and Comms ............................................................13
Connecting the Ultrasonic Probe..........................................14
Securing the Cables ..........................................................15
Connecting Topside..............................................................16
4. System Operation ...........................................................17
On the deck before launching the ROV ....................................17
Taking Thickness Measurements Subsea .................................18
Surface Preparation...........................................................18
Zeroing the Probe .............................................................18
Probe Alignment ...............................................................18
Start CygLink Topside........................................................19
Taking Measurements........................................................20
Logging Measurements ......................................................23
Manual Gain Control ..........................................................24
Using the Cursors to make Direct Measurements ...................24
Using the Display Freeze....................................................25
5. Measurement Modes .......................................................27
Single Echo Mode (SE) .........................................................27
Echo-Echo Mode (EE) ...........................................................28
Multiple Echo Mode (ME).......................................................28
Auto EE/SE/ME Mode ...........................................................29
6. Measurement Settings in CygLink ...................................30
Units...............................................................................30
Measure Mode ..................................................................30

Cygnus ROV UTM - Operating Manual
Page 3 of 60
Manual Gain.....................................................................31
Velocity of Sound and Material List ......................................31
Measurement range for A-Scan Range..................................31
7. Calibration and Zero .......................................................33
Why should I Calibrate?........................................................33
Calibrating to a Known Thickness ...........................................34
Zeroing the Probe................................................................35
8. CygLink ...........................................................................37
Installing CygLink ................................................................37
Requirements...................................................................37
Upgrading........................................................................37
Installing .........................................................................37
COM Port Numbers ..............................................................38
Setting the COM Port Manually............................................38
Finding your COM Port Number ...........................................38
Connecting to the Instrument................................................39
First time USB Connection..................................................39
Connecting the Instrument to CygLink for the First Time.........40
Connecting to the Instrument Afterwards .............................41
Disconnecting from the Gauge ............................................42
Manual Connection Settings................................................42
CygLink Surveys and Data Logging.........................................43
Editing the Survey Details ..................................................44
Editing the Survey Group Details.........................................45
Producing a Survey Report Document ..................................45
Logging Measurements Directly in CygLink ..............................46
Reference and Minimum Thickness Criteria ...........................46
Pre-Set Measurement Comments List...................................46
Adding Comments or Notes to a Measurement ......................47
To Change the COM Port number assigned by Windows®...........48
Opening Device Manager....................................................48
CygLink Trouble Shooting .....................................................49
Connection Problems –USB Drivers.....................................49
Wiring Problems ...............................................................50
9. Care and Servicing ..........................................................51
Cleaning the Instrument .......................................................51
Environmental.....................................................................51
Repairs ..............................................................................51
Returning the Gauge for Servicing..........................................51

Cygnus ROV UTM - Operating Manual
Page 4 of 60
10. Technical Specifications ..................................................52
11. Table of Sound Velocities ................................................54
Reading Conversions .........................................................55
12. Recycling and Disposal (EC Countries)............................56
13. Electrical Connections.....................................................57
Power & Comms Port (Bulkhead plug).....................................57
Probe Port (Bulkhead) ..........................................................57
14. Cygnus Instruments .......................................................58
15. Warranty Information.....................................................59
16. Index ..............................................................................60
Revision History.
Issue
Date
Changes
Issue 3
06-Jun-19
SE Mode Measurement Range increased to 55mm, on
page 49.
Issue 4
17-Jul-19
Revised depth rating to 3000m (300bar)
Issue 5
04-Oct-19
Included Maximum Surface Contact Temperature to Probe
Specifications
Issue 6
03-Nov-20
Updated for change in Probe Connector (CRE).
Updated for Serial Interface (RS-232).
Issue 7
06-Jun-22
Change of product name to “Cygnus ROV UTM”
Added product registration info.

Cygnus ROV UTM - Operating Manual
Page 5 of 60
1. Introduction
Cygnus ROV UTM
The Cygnus ROV UTM –ROV Mountable Thickness Gauges are
rugged, compact instruments designed for reliable ultrasonic
thickness measurements.
The instrument is pressure rated to a maximum depth of 3000
meters sea water (300 bar). The instrument takes its power from
the ROV craft and output thickness measurement data as serial
data in RS232 format. The thickness measurement data is viewed
top-side using CygLink which can also be used to provide Data
Logging facilities and report generation.
Measurements can be displayed in Metric (mm) or Imperial (inch)
units; measurement resolution is set to 0.1mm (0.005 inch).
Crystal-controlled Calibration provides stability and accuracy. The
thickness measurement can easily be calibrated to a known
thickness or to a known Velocity of Sound.
The instruments are able to operate accurately in adverse
environmental conditions both underwater and above the sea.
The system is a solid-state electronic instrument which,
under normal operating conditions, will give many years of
active service.
Although designed for ease of operation first time users
should carefully read this manual to familiarise themselves
with the features of the instrument

Cygnus ROV UTM - Operating Manual
Page 6 of 60
Register your Gauge
Register your gauge to receive updates on gauge firmware and to
register your 3-year warranty.
Registration is quick and easy, go to this web address;
https://cygnus-instruments.com/service/product-registration/
Product Registration Link QR

Cygnus ROV UTM - Operating Manual
Page 7 of 60
Kit Contents
The Cygnus ROV UTM system is supplied as a complete kit in a
transportation case
1
Cygnus ROV UTM
Subsea Instrumentation
Unit
2
SD2C-DAW 2.25 MHz
Single Element Delay
Line Probe with cable
and connector. Fitted in
P50 Probe Handler.
3
Patch cable for wiring the Cygnus ROV UTM to the ROV,
0.6m
4
Test Lead –RS-232 to USB
5
Test Block 15mm thick in 1080 Mild Steel
6
USB Flash Drive with CygLink Software and
Documentation
7
A Calibration Certificate
8
Silicon grease for lubricating connectors and O-rings
Optional Items
1. Fish tail or T-bar manipulator handle.

Cygnus ROV UTM - Operating Manual
Page 8 of 60
2. System Overview
Subsea Instrument
The system is supplied ready to use. All that is required is to make
the necessary electrical connections between the subsea unit and
the ROV Craft and the top side computer.
There are no controls or display on the subsea instrument unit,
operation and calibration is performed at the surface using
CygLink software.
Cygnus ROV UTM Subsea Instrument Unit.
Ultrasonic Probe
The Ultrasonic Probe (model number SD2C-DCW) has a 2.25 MHz
ø13mm single element piezo-composite crystal, bonded to a
30mm long Rexolite delay line. The delay line face is ø16mm. The
delay line is bonded directly to the active element of the probe and
cannot be replaced.
The probe is fully encapsulated internally, double O-Rings seal the
delay line in the probe body.

Cygnus ROV UTM - Operating Manual
Page 9 of 60
SD2C-DCW Ultrasonic Probe.
The probe is supplied with 5m of cable, protected by an outer
reinforced air hose. Each end has a stainless steel bracket which is
attached by M5 screws and nuts.
Ultrasonic Probe Cable Mounting Bracket - P50 Probe Handler End.
Ultrasonic Probe Cable Mounting Bracket - Connector End

Cygnus ROV UTM - Operating Manual
Page 10 of 60
Connection to the subsea unit is by a multi-pin connector secured
by a brass threaded collar.
The instrument is designed only to be used with ultrasonic
probes supplied by Cygnus Instruments.
P50 Probe Handler
The ‘P50’ probe handler is designed to align the ultrasonic probe
on to straight pipes from 50mm in diameter up to flat surfaces.
The spring-loaded probe and V shaped block allow the probe to be
positioned correctly on a straight pipe and move to accommodate
different pipe diameters.
A gimbal allows the probe to move to align on to the straight pipe
surface when used with a ROV manipulator arm.
The probe handler can be fitted with a choice of manipulator
handles; T Bar or Fishtail.

Cygnus ROV UTM - Operating Manual
Page 11 of 60
Ultrasonic Probe and P50 Probe Handler.
P50 Probe Handler on ø130mm Pipe.

Cygnus ROV UTM - Operating Manual
Page 12 of 60
Ultrasonic Probe Alignment on ø130mm Pipe Surface.
Ultrasonic Probe Cable Fitted to the P50 Probe Handler.

Cygnus ROV UTM - Operating Manual
Page 13 of 60
3. Connecting the System Together
Subsea Instrument
There are two connectors on
the subsea instrument,
marked
•POWER COMMS
•PROBE
Power and Comms
On the subsea instrument power and comms are connected via the
6-way SubConn©MCBH6M connector marked ‘POWER COMMS’.
Power must be connected to a clean DC Power Supply on the ROV,
typically 12 to 24V DC is used.
The Comms link is connected to a channel on the ROV multiplexer.
This must be configured for RS-232, 115200 Baud, 8 Data Bits.
The MCBH6M (mates with MCIL6F).
The picture below is shown looking into the bulkead connector.

Cygnus ROV UTM - Operating Manual
Page 14 of 60
Pin No.
Colour
Description
Pinout
1
Black
Ground
2
White
12-24V DC Input
3
Red
RS-232 TXD
4
Green
RS-232 RXD
5
Orange
No connect
6
Blue
No connect
Connecting the Ultrasonic Probe
The ultrasonic probe is connected to the subsea instrument using
the threaded connector marked ‘PROBE’. There is a slot to ensure
correct alignment before the connector can be mated.
Ultrasonic Probe Connectors, Mated.
Ensure the brass knurled Screw Collar is tight, and
the connector is fully mated.
There should be no movement between the
connector parts when correctly mated.

Cygnus ROV UTM - Operating Manual
Page 15 of 60
Securing the Cables
The system is supplied with a Cable Support Cage which is used to
secure the probe cable bracket and cable-tie the power and
comms cable. The cable support cage is bolted to the top of the
subsea enclosure using four M5 cap-head screws.
There are two alignment marks on the top of the subsea enclosure
and cable support cage to ensure it is fitted in the right position.
Alignment Marks (arrowed)
Cable Support Cage with Cables Fitted and Secured.

Cygnus ROV UTM - Operating Manual
Page 16 of 60
Connecting Topside
At the surface, the RS-232 Comms link should be wired from the
multiplexer port to the RS-232 to USB converter lead. There are
three connections; TXD, RXD and Ground. You must connect the
ground.
The RS-232 to USB converter is then plugged into the computer
that will run the CygLink program.

Cygnus ROV UTM - Operating Manual
Page 17 of 60
4. System Operation
On the deck before launching the ROV
Before launching the ROV, test the system is operating and you
can take a thickness measurement using the 15mm Test Block
from the kit. Hold the test block against the probe face and use
couplant gel to ultrasonically couple the test block to the probe.
If necessary, Calibrate the system so the measurement is correct.
Otherwise set the velocity of sound to 5920m/s for steel.
See Calibrating to a Known Thickness on page 34
When operating the system with the probe out of water
you will get a standing reading of around 9.7mm in SE
Mode. This is normal and will disappear once the ultrasonic
probe is submerged in water.
Delay Line Reflections when Probe in Air.

Cygnus ROV UTM - Operating Manual
Page 18 of 60
Taking Thickness Measurements Subsea
Surface Preparation
Water jetting the surface to SA1 is recommended.
The instrument will not measure through barnacles or similar hard
encrustations. You must therefore remove any hard marine growth
before attempting a thickness measurement.
Thin layers of green algae over paint don’t need to be removed.
If there is loose rust (rusticles) or de-lamination of the metal
surface you will need to remove these loose outer layers with a
scraping tool.
Zeroing the Probe
As the pressure increases with depth the delay line will compress
and this will shift the interface echo (zero point) as the length of
the delay line decreases. To compensate for this, before
attempting measurements perform a Probe Zero measurement.
Always perform a Probe Zero before attempting thickness
measurements.
See Zeroing the Probe on page 35.
Probe Alignment
To have any chance of getting a good measurement the ultrasonic
probe must be positioned correctly on the surface of the object
being surveyed.

Cygnus ROV UTM - Operating Manual
Page 19 of 60
The probe MUST BE perpendicular to the surface in both
axes, otherwise the ultrasound will not reflect back to the
probe.
The P50 Probe Handler will assist in aligning the probe with the
surface but the ROV’s position and the manipulator arm position
are critical in helping to align the probe correctly.
The Probe Must Be Aligned Perpendicular in Both Axes.
Start CygLink Topside
Run the Cygnus CygLink program from its desktop shortcut. To
Connect to the Subsea Instrument, from the menu select;
Connect -> Connect to Gauge
See Connecting to the on page 39.

Cygnus ROV UTM - Operating Manual
Page 20 of 60
Taking Measurements
For best results set the Measuring Mode to Auto SE/EE/ME, see
Measure Mode on page 30. This will let the instrument decide the
best measurement to make.
The ROV operator should position the ultrasonic probe on the
measurement surface, when CygLink is running it will continuously
update the screen with the A-Scan and display a measurement if it
can get one.
The probe handler should be moved/re-positioned until an
acceptable measurement has been obtained.
No Measurement.
The screens shown below show a valid measurement of 12.0mm
and the A-Scan graph shows a signal marked with a single yellow
diamond to indicate the SE measurement point.
This manual suits for next models
2
Table of contents
Other Cygnus Measuring Instrument manuals
Popular Measuring Instrument manuals by other brands
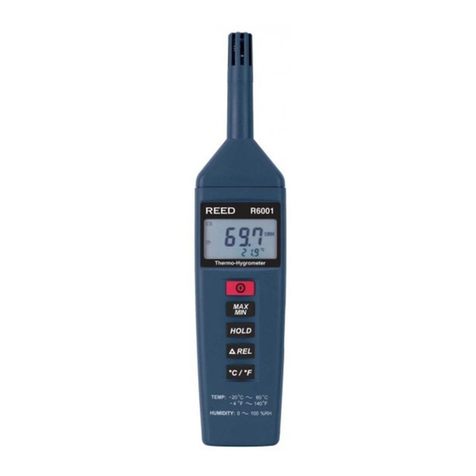
REED
REED R6001 instruction manual
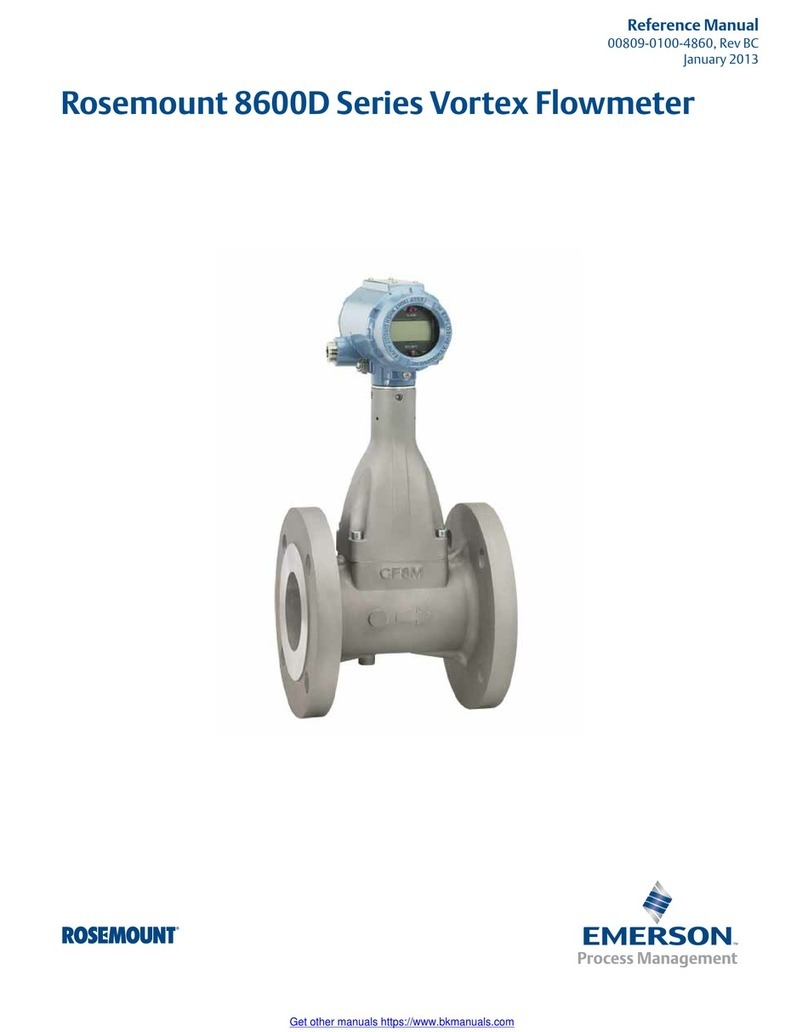
Emerson
Emerson Rosemount 8600D Series Reference manual
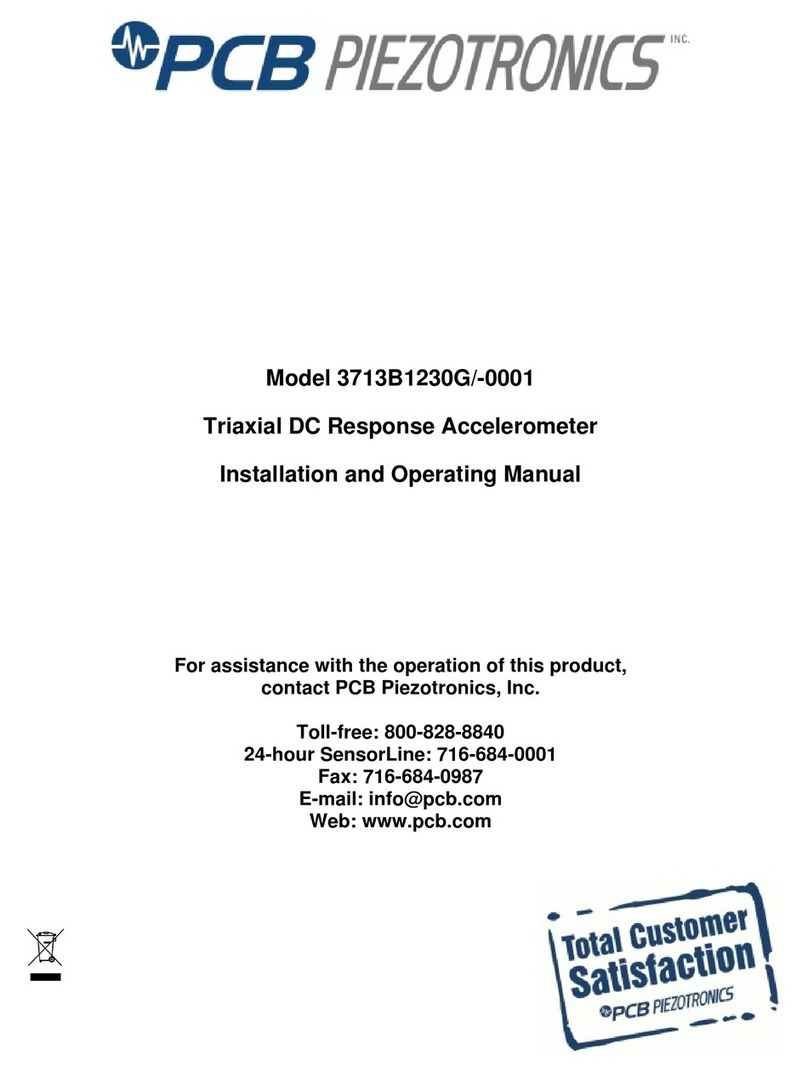
PCB Piezotronics
PCB Piezotronics 3713B1230G/-0001 Installation and operating manual
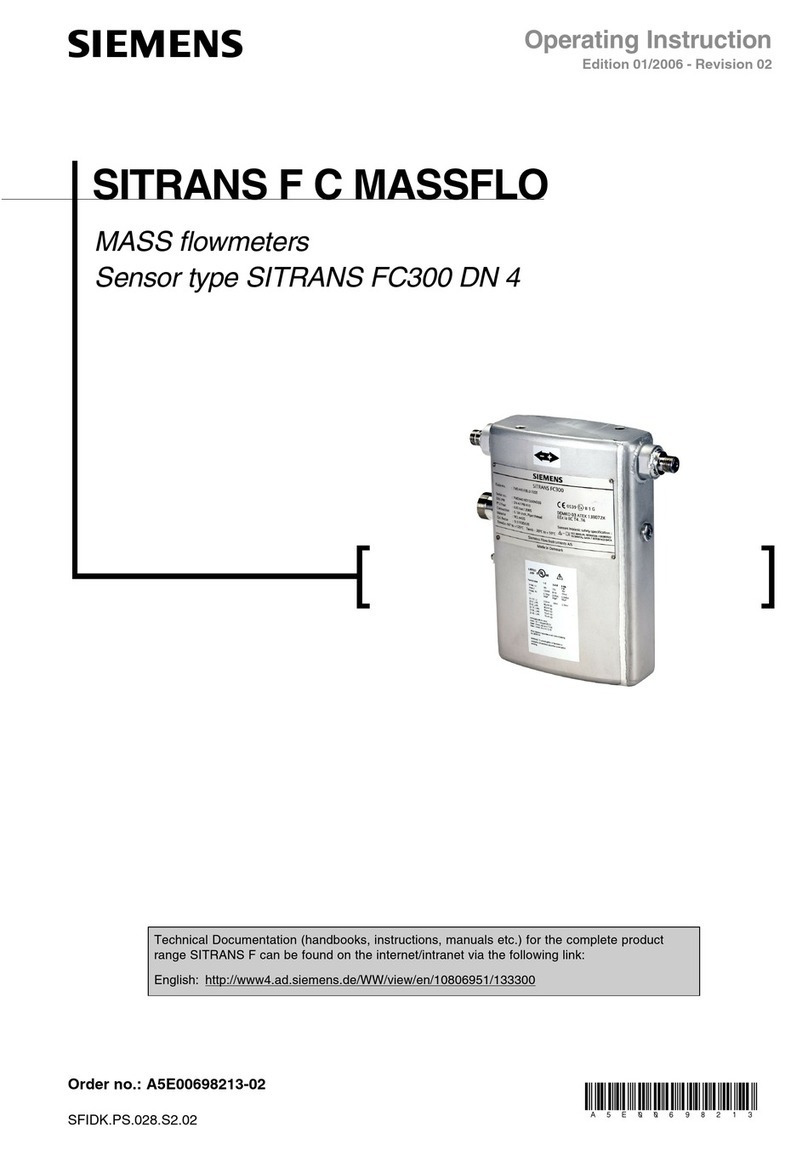
Siemens
Siemens SITRANS F C MASSFLO Operating instruction
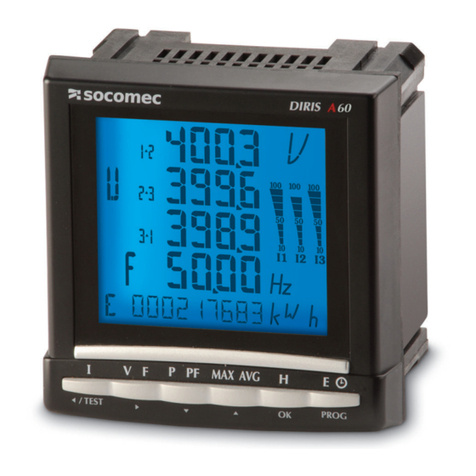
socomec
socomec DIRIS A60 Quick start up guide
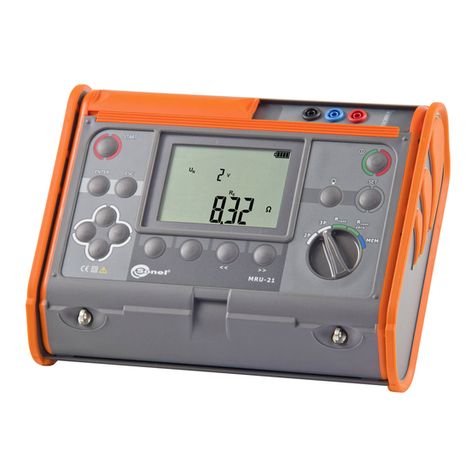
Sonel
Sonel MRU-21 user manual