Daihatsu MD-SX User manual

JULY. 2015
INB000044D
OIL MIST DETECTOR
INSTRUCTION MANUAL
MD-SX
(Sensor type)
Original content from www.daihatsu.cc
Issued to HORIZON TANKERS LIMITED S.A.

Safety Precautions on Operation of Oil Mist Detector
This Manual describes cautionary items for installation and operation of the oil mist
detector for sake of safe use.
Please operate the equipment adequately while following the cautionary items.
The degree of hazard and damage likely to result from wrong use, neglecting the indicated
cautions, is explained in this Manual using symbol marks shown below.
The symbol marks mean as follows.
·········· CAUTION
State likely to cause damage of light or middle degree is
indicated, unless the state is avoided or prevented.
1. Caution for electric shock
(1) Voltage is left in the internal terminal block, even if the body POWER
turned OFF.
Please switch off the controller every time when sensor is replaced or
disconnected from sensor connector, otherwise, it may cause not only the
electric shock but the breakdown of the equipments.
(2) Especially, when 100 V AC is used for signal output contacts, please be
careful for electric shock from the terminal block.
2. Caution against current leakage
(1) To prevent electric leakage, please be sure to ground the equipment.
* The specification may be changed for improvement with no advance notice.
!
!
!
Original content from www.daihatsu.cc
Issued to HORIZON TANKERS LIMITED S.A.

CONTENTS
1. OVERVIEW......................................................................................................................... 1
2. FEATURES .......................................................................................................................... 1
3. CONSTITUTION................................................................................................................. 2
4. OUTLINE............................................................................................................................. 4
5. SPECIFICATIONS.............................................................................................................. 8
5.1 Sensor unit ........................................................................................................................ 8
5.2 Controller.......................................................................................................................... 9
6. DISPLAY AND FUNCTIONS OF SENSOR UNIT ...................................................... 10
6.1 Description of function................................................................................................... 10
6.2 “POWER” LED.............................................................................................................. 10
6.3 “ALARM” LED.............................................................................................................. 10
6.4 “FAILURE” LED ........................................................................................................... 10
7. DISPLAY AND FUNCTIONS OF CONTROLLER..................................................... 11
7.1 Mist indicator.................................................................................................................. 11
7.2 “RUN” LED.................................................................................................................... 11
7.3 “SYSTEM FAILURE” LED........................................................................................... 12
7.4 “PRE ALARM” and “HIGH ALARM” LEDs............................................................... 12
7.5 [STEP] keys and [ENTER] key...................................................................................... 13
7.6 [INITIAL SET] key switch............................................................................................. 13
7.7 [TEST] key switch.......................................................................................................... 13
7.8 [MODE] key switch........................................................................................................ 14
8. INSTALLATION.............................................................................................................. 15
8.1 Sensor unit........................................................................................................................... 15
8.2 Controller ............................................................................................................................ 18
9. WIRING............................................................................................................................. 19
9.1 CABLE ........................................................................................................................... 20
9.2 Wiring of the sensor........................................................................................................ 22
・9.3 Wiring of the controller ............................................................................................ 23
9.4 Setting of resistance for detecting disconnection............................................................ 26
9.5 Wiring of the gland type sensors .................................................................................... 27
9.6 Cautions in wiring........................................................................................................... 27
10. INITIAL SETUP............................................................................................................... 29
10.1 Initial setup of sensor units............................................................................................. 29
10.2 Initial setup of controller................................................................................................. 30
11. OPERATION.................................................................................................................... 31
11.1 Checks before turning the power on............................................................................... 31
11.2 Steps from the first power ON to practical operation..................................................... 31
11.3 Full load (mist density level) setting............................................................................... 33
11.4 Initial reset ...................................................................................................................... 34
11.5 Alarm operation check.................................................................................................... 34
12. TEST METHOD AND OPERATION CHECK (FOR IACS M10.13) ........................ 36
13. APPROXIMATE VALUE OF MIST DENSITY........................................................... 37
14. MAINTENANCE.............................................................................................................. 38
15. TROUBLESHOOTING................................................................................................... 40
15.1 TROUBLESHOOTING by controller indicate................................................................. 40
15.2 Sensor fail code at LCD on the controller....................................................................... 43
15.3 Sensor clean code at LCD on the controller ................................................................... 43
15.4TROUBLESHOOTING by sensor unit indicate................................................................ 44
16. APPENDIX........................................................................................................................ 45
16.1 Parts list........................................................................................................................... 45
16.2 Anti-vibration bracket mounting drawing (OPTION) .................................................... 48
16.3 Sensor cleaning procedure.............................................................................................. 48
16.4 Attention of using LOOP wiring for sensor cable routing.............................................. 53
Original content from www.daihatsu.cc
Issued to HORIZON TANKERS LIMITED S.A.

1
1. OVERVIEW
This equipment consists of “sensor units” that are directly mounted through the wall on the crankcase side of a
diesel engine or gas engine (or EGR system : option) that collectively controls the units by communication
means and “controller”.
This equipment was developed by applying new techniques and ideas based on our long-term accumulated
techniques related to detection of oil mist density. For detection of mist by the sensor units, the equipment uses
a natural diffusion system that does not require mechanically moving parts, such as a suction mechanism,
driving air or piping. Compact design, improved reliability and easy maintenance are realized by the use of the
light scattering system for detection of mist density.
The maximum number of detection points is 16. Except for the ship engine with classifications approved, this
system can use the sensor for the 8 cylinders (max.) on two engines. The system is very flexible for controller
layout and installations.
Since the controller has key switches and an LCD, the operability is improved, and the conditions of the whole
equipment including the sensor units can be monitored by the self-diagnostic function.
The oil mist density in the crankcase is constantly monitored. When the oil mist density exceeds the setting
owing to overheated bearings, an alarm will be given, and a signal will be output to the outside. Not only on
low-speed engines, but also on middle- to high-speed engines, serious failures can be found early or predicted.
2. FEATURES
(1) For mist detection by the sensor units, a natural diffusion system is used.
This eliminates the necessity of such fan suction mechanism, piping and driving air that the conventional
systems required.
(2) The mist detection section consists of a light emitting element (LED) and a light receiving element (PD:
photodiode). The use of the light scattering detecting technique reduced the equipment size and realized
high-sensitivity detection excelling in stability.
(3) The sensor units do not have mechanically moving parts. They are light and excel in durability and
vibration resistance.
(4) Output variations due to changes in temperature are automatically corrected.
In addition any adjustment is not necessary for the sensitivity deterioration by contamination. It can be used for
the long term by cleaning sensor hood.
(Please refer to 16.3 sensor cleaning procedure)
(5) The use of a single-chip microcomputer ensures high-performance stable detection.
(6) The use of data communication techniques realizes daisy chain wiring-saved connection for power supply
lines and communication lines between sensor units and between the controller and each sensor unit.
(7) The mist indicator on the controller consists of 16 LEDs in three colors and is clear. For alarm detection, a
two-stage system (pre-alarm and high-alarm) is used.
(8) The controller is provided with key switches and an LCD to improve the operability.
(9) It is possible to connect an external output unit for an external monitor. (Option)
(10) Since the connector is used for wiring connection of the sensors, wiring work is easy.
(Connector type)
Original content from www.daihatsu.cc
Issued to HORIZON TANKERS LIMITED S.A.

2
3. CONSTITUTION
It is possible to install MD-SX oil mist detection system for ONE engine or TWO engines.
(1) In case of install MD-SX system for one engine. (For ship: refer to IACS UR M10.12)
Fig. 1 Install MD-SX system on one engine
(2) In case of install MD-SX system for two engines. (For land or ship use without classification approved)
Fig. 2 Install MD-SX system on two engines
MD-SX SENOSR
JUNCTION BOX
MD-SX CONTROLLER
24Vdc POWER SUPPLY
RELAY OUTPUTS(to Alarm
Monitoring System)
MD-SX
special cables
Marine cable
(shielded)
DIESEL ENGINE
MD-SX SENOSR
JUNCTION BOX
MD-SX CONTROLLER
24Vdc POWER SUPPLY
RELAY OUTPUTS(to Alarm
Monitoring System)
Marine cable
(shielded)
DIESEL ENGINE
MD-SX SENOSR
JUNCTION BOX
DIESEL ENGINE
MD-SX
special cables
Original content from www.daihatsu.cc
Issued to HORIZON TANKERS LIMITED S.A.

3
16 sensors can be installed for one engine at the maximum.
16 sensors can be installed in total at the maximum for two engines, 8 sensors each for an engine.*
Wire the sensors in daisy chain system (connection-in-a-row system) for each engine.
Limit the total length of the telecommunication cable from the sensor of an end to a controller is less than
150 m (for use of Daihatsu option cables). In case of the total wire length exceed 150 m, please ask the wiring
method to Daihatsu.
The wiring between sensors and controller shall be used Daihatsu option cables (the cable with connectors).
(Note: When installing a junction box between a controller and sensors, a general cable for ships can be used
between the controller and the junction box.)
Mount the sensor directly on the engine frame.
Use the specified rubber cushions to isolate the controller from vibration if it is directly mounted on the
engine body.
Before using the mounting method described above, please contact us.
For ship use, it may be limited by the shipping classification society with one oil mist detector system 1
formula per engine. Please follow the rule of each shipping classification society.
For sensor wiring method, The loop wiring also applicable other than daisy chain method
(Please refer to 16.4 Attention of using LOOP wiring for sensor cable routing)
Original content from www.daihatsu.cc
Issued to HORIZON TANKERS LIMITED S.A.

4
4. OUTLINE
(1) DOWN WARD SENSOR UNIT
STANDARD TYPE (CONNECTOR TYPE)
CABLE GLAND TYPE
FLYING-LEAD TYPE
Fig. 3 MD-SX OUTLINE OF DOWN WARD SENSOR UNIT
Original content from www.daihatsu.cc
Issued to HORIZON TANKERS LIMITED S.A.

5
(2)HORIZONTAL CABLE SENSOR UNIT
STANDARD TYPE (CONNECTOR TYPE)
FLYING-LEAD TYPE
Fig. 4 OUTLINE OF HORIZONTALCABLE SENSOR UNIT.
Original content from www.daihatsu.cc
Issued to HORIZON TANKERS LIMITED S.A.

6
(2) CONTROLLER
Wall mount type(with cable gland)
Wall mount type(with cable comb)
Fig. 5 Controller outside
Original content from www.daihatsu.cc
Issued to HORIZON TANKERS LIMITED S.A.

7
Flush mount type
Fig. 6 Controller outside
PANEL CUT
Original content from www.daihatsu.cc
Issued to HORIZON TANKERS LIMITED S.A.

8
5. SPECIFICATIONS
5.1 Sensor unit
No. MODEL MD-SX SENSOR UNIT
(1) Function Oil mist concentration detection
Mist level signal conversion and output
(2) Detection point 1 point/1 unit
(3) Mist detection Natural diffusion system
(4) Detection concentration 0 - 2.0 mg/L (0 - 0.5 mg/L : for EGR system)
(5) Detection system Optical system (Optical dispersion system)
(6) Detection interval Continuous
(7) Display
3 LEDs
“POWER” (Green) : Power status (Lighting)
“ALARM” (Red) : PRE ALARM (Blink)
HIGH ALARM (Lighting)
“FAILURE” (Yellow) : Comm. and Sensor failure (Lighting)
(8) Data communications Serial interface: RS-485 (Half Duplex) conformity (Sensor unit - controller)
(9) Initial-setting operation Rotary switch: Communication node (16CH) “0” - “F”
Dip switch : Terminator “ON”/“OFF
(10) External connection
(Sensor unit - Controller)
Sensor line : MD-SX option cables (Daisy chain)
Total length: 150 m max.
Connection method : Connector (Standard type)
Clamp-type terminal (Cable gland type)
(11) Power supply 24 V DC (+30% to 25%) (supply from controller)
(12) Power consumption 60 mA (max.)/1 unit
(13) Outline dimensions 80 W124 H168 Dmm (Standard: connector type)
80 W120 H168 Dmm (Cable gland type)
(14) Installation
Screw size: G 3/4 (with a seal washer)
Vertical direction : Level or less than 15of facing down
Rotation direction : Less than 5
(15) Protection against dust
and waterproofing Protection class: IP 55
(16) Weight Approx. 450 g (Standard connector type, Cable gland type)
Approx. 500 g (Fling - lead type)
(17) Paint color Munsell N1.0 (Black) (Case part)
(18) Environmental conditions
Ambient temperature:
(For operation) 5 - 55C
5 - 80C (Engine insertion part)
(For storage) 20 - 80C
Humidity : Max. 80%RH (without dew condensation)
Atmosphere : No corrosive gas
Vibration : Amplitude: 1.6 mm or less (2 to 25 Hz), 4 G or less (25 to 2 kHz)
Original content from www.daihatsu.cc
Issued to HORIZON TANKERS LIMITED S.A.

9
5.2 Controller
No. MODEL MD-SX CONTROLLER
(1) Function Mist level indication and alarm monitoring
(2) Number of sensor unit connection 16 units (max.) (16 units/1 engine or each 8 units 2 engines)
(3) Detection time Continuous (Response time: 1 sec or less/16 points)
(4) Detection concentration 0 - 2.0 mg/L
(5) Operation Key switch input
(6) Display
1) Mist level: 3-color bar-graph indication (16 LEDs)
2) 4 LEDs
“RUN” (Green) : Detection (Lighting)/Mode set up (Blink)
“PRE ALARM” (Red) : (On at mist level LED: “(10)” and over)
“HIGH ALARM” (Red) : (On at mist level LED: “(15)”)
“SYSTEM FAILURE” (Orange)
3) LCD: 60 22 mm
20 letters 4 lines (with back light)
(7) Contact outputs 1) Alarm (2 contacts for each engines) “PRE ALARM”,“HIGH ALARM”
2) Failure output (1 contact) “SYSTEM FAILURE”
(8) Contact specification Relay contact output (1 form C)
Contact capacity: 125 V AC 0.4 A / 30 V DC 2 A (Resistance load)
(9) Data communications Serial interface: RS-485 (Half Duplex) conformity
(Sensor units and external unit)
(10) External connection
Sensor line : Daihatsu option cables or specified cable for ships (To install a
junction box: AWG15 4 cables)
Contact output line : Cable outer dia. = 18 mm or less (for one engine)
Cable outer dia. = 18 mm or less (for two engines)
Power line : Cable outer dia. = 13 mm or less
Connection method : Clamp-type terminal connection
(11) Power supply 24 V DC (+30% to 25%)
(12) Power consumption 1.5A (max.) (Internal: 0.5A, Sensor units supply: 1.0A)
(13) Outline dimensions 360 W 200 H 100 D mm (Wall mount type)
370 W 260 H 100 D mm (Flush mount type)
(14) Protection against dust and
waterproofing Protection class: IP 55
(15) Weight Approx. 5.0 kg (Wall mount type with cable gland)
Approx. 5.6 kg (Wall mount type with cable comb)
Approx. 5.8 kg (Flush mount type)
(16) Paint color Munsell N1.0 (Black)
(17) Environmental conditions
Ambient temperature:
(For operation) 5 - 55C
(For storage) 20 - 80C
Humidity : Max.80%RH (Without dew condensation)
Atmosphere : No corrosive gas
Vibration : 1 G or less (If vibration is more than 1 G, adopt a vibration-proof device.)
Original content from www.daihatsu.cc
Issued to HORIZON TANKERS LIMITED S.A.

10
6. DISPLAY AND FUNCTIONS OF SENSOR UNIT
Fig. 7 Sensor unit
Each sensor unit has three status indicating lamps (LEDs); POWER (green), ALARM (red), and FAILURE
(yellow).
6.1 Description of function
The light emitted from the LED of the sensor unit is diffused and reflected by the oil mist in the sensor hood,
and then received by the photo receiver diode (PD). After amplification and A-D conversion, the output from
the photo receiver is input to the CPU for arithmetic operation, and then transferred to the controller as the oil
mist density data.
6.2 “POWER” LED
This lamp is located on the left of the surface of the sensor unit case. When the green LED is on, this means that
power is being supplied from the controller and the CPU is working normally.
6.3 “ALARM” LED
The controller detects the alarm status based on the oil mist density detected by the sensor unit.
There are two alarm statuses, “PRE ALARM” and “HIGH ALARM”. Upon occurrence of any alarm, the red
LED in the center of the case surface flashes (PRE ALARM) or lights (HIGH ALARM) according to the signal
from the controller.
6.4 “FAILURE” LED
The sensor unit has a self-diagnosis function. If any trouble is found, the yellow LED on the right of the case
surface will turn on.
Upon occurrence of a light receiving or emitting element output trouble, a CPU trouble, a thermistor trouble or a
circuit trouble, the LED lights.
In addition, when the controller is set in the test mode, the LED of all sensor units becomes blinking.
“FAILURE”DISPLAY
“ALARM” DISPLAY
“POWER”DISPLAY
Connector ground
Slide cover
Fixed Screw of slide cover
“FAILURE”DISPLAY
“ALARM” DISPLAY
“POWER”DISPLAY
Connector ground
Slide cover
Screw of cover
Original content from www.daihatsu.cc
Issued to HORIZON TANKERS LIMITED S.A.

11
7. DISPLAY AND FUNCTIONS OF CONTROLLER
Fig. 8 Controller face of a board
The controller has not only operation key switches and an LCD indicator for displaying the status, but also
16-ch mist indicators that show the oil mist density level with 16 LEDs in three colors, green, orange and red.
It has also lamps (LEDs), “RUN” (green) and “SYSTEM FAILURE” (red), that indicate the system operation
status and alarm indicating lamps (LEDs), “PRE ALARM” (orange) and “HIGH ALARM” (red). These devices
have the following functions.
7.1 Mist indicator
The controller transfers oil mist density data with the sensor units (up to 16 units can be connected) and
indicates the oil mist density levels based on the data with 16-level bar graph LEDs in three colors, green (No.0
to No.7), orange (No.8 to No.10) and red (No.11 to No.15).
When only the mist indicator LED No.0 (green) is flashing, this means that the controller has not been
initialized (Full-load setting) as specified.
Initialize the controller as stated in [10.2 Initial setup of controller] or [11 Operation].
7.2 “RUN” LED
When this LED is on, the power supply is normal, and the controller CPU is working normally. If the controller
has not been initialized as specified or is not in the normal mode, the LED is flashing.
Usually, when key operation does not have 10 minutes or more in the modes other than the mode, it usually
returns to the mode automatically.
“
PRE ALARM
”
DISPLAY
(LED)
“
HIGH ALARM
”
DISPLAY
(LED)
MIST
INDICATOR
(LED)
“
RUN
”
DISPLAY
(LED)
“
SYSTEM FAILURE
”
DISPLAY
(LED)
[ENTER]
KEY
[STEP]
KEY
[TEST]
KEY
[MODE]
KEY
LCD DISPLAY
Fastener
[INITIAL SET]
KEY
Cable gland
Original content from www.daihatsu.cc
Issued to HORIZON TANKERS LIMITED S.A.

12
7.3 “SYSTEM FAILURE” LED
When a controller CPU trouble occurs, a hardware trouble is detected by the self-diagnostic function of any
sensor unit or a communication trouble between the controller and a sensor, the LED will be turn on, and the
“SYSTEM FAILURE” output relay will be activated.
(1) After receiving a sensor unit trouble signal, the controller will turn off the LED Nos. 1 to 7 (green) of the
mist indicator for the relevant sensor and make the LED Nos. 8 to 10 (orange) flash. Then, you can identify
the defective sensor unit.
The defective sensor unit will be automatically excluded from the calculation of deviation (mean value).
(2) When a cable is disconnected, a communication trouble will be detected on the sensor units in the
downstream of the disconnected point. In this case, mist indicator LED Nos. 0 to 7 (green) will go out, and
the LED Nos. 8 to 10 (orange) will flash. Then, you can identify the cable disconnection point.
(3) After the communication recovers normally, “SYSTEM FAILURE” will be automatically restored.
Even after recovery, the error message will be continuously displayed on the LCD until the system is reset
by the ENTER key.
System failures other than communication troubles are self-held. Turn off power with the power switch in
the controller, and remove the cause of the trouble.
After recovery from the trouble, turn on the power switch in the controller to reset.
(4) When a CPU trouble occurs, “SYSTEM FAILURE” will be output.
As for the details, see Section [15.Troubleshooting].
7.4 “PRE ALARM” and “HIGH ALARM” LEDs
There are two alarm statuses, “PRE ALARM” and “HIGH ALARM”. Upon occurrence of an alarm, the
indicating lamp (LED) and the output relay function.
The status message is displayed on the indicating LCD.
The mist indicator lamps are in the following conditions when an alarm occurs and when the alarm is cleared.
Operation point Restoration point
“PRE ALARM”
No. 10 or above
or
At the time of deviation
unusual generating
No. 8 or below
or
At the time of a deviation
unusual return
“HIGH ALARM” No. 15
(self-holding)
After mist density decreases
Press the ENTER key
for restoration.
Any deviation of the sensor level indicates the deviation alarm message of “PRE ALARM” when the level of
the sensor in question deviates by more than 4 levels from the average level of all the sensors indicated on the
mist indicator.
The “PRE ALARM” message is not continuously indicated, but automatically reset when the oil mist density
level goes down.
The message indicator is automatically reset when the deviation goes below the level 4 from the average level.
“HIGH ALARM” is self-held, and all lamps (up to No.15) of the mist indicator are kept on.
When the mist density is lowered to the normal range, press the ENTER key to reset the “HIGH ALARM”.
As for the specifications for external output of the output relay, see Section [9.3 Wiring of the controller].
Original content from www.daihatsu.cc
Issued to HORIZON TANKERS LIMITED S.A.

13
7.5 [STEP] keys and [ENTER] key
Use the arrow keys to move the cursor on the LCD or to increase or decrease the set values.
Use the ENTER key to reset the alarm to the normal mode.
In the setting status of each mode, also use the ENTER key to determine the set data at the cursor position.
7.6 [INITIAL SET] key switch
The [INITIAL SET] key switch is to (store the mist density data under the maximum load in the controller)
when setting the full load. You can display the setting change screen by pressing the key long (for more than 3
seconds).
7.7 [TEST] key switch
You can select the test mode by pressing the [TEST] key switch.
The “FAILURE” message blinks for each of the sensor units as communication is disconnected between the
sensor units and the controller when the test mode is selected. The “RUN” message on the controller also blinks.
The test mode has the following functions:
1. Alarm operation check
2. Function check
1) LED/LCD ALL ON : To check that the LCD screen and LED lamps properly operate by turning
all of them on.
2) SWITCH CHECK : To check that the key switches properly operate
3) OUTPUT CHECK : To forcibly turn the contacts on and off to check the function.
The 「1. ALARM OPERATION CHECK」is to detect mist in the sensor and to check if the system properly
operates. You can check the proper operation of the system by temporarily lowering the alarm setting-off level
of one sensor unit to detect the “PRE ALARM” and “HIGH ALARM” set off at the density level of oil mist
generated during the engine in operation. See the [11.5 ALARM OPERATION CHECK] for the detailed
procedure.
The 「2. FUNCTION CHECK」is to check if the individual displays and switches properly function.
The alarm output relays (external output) are operational in the test mode.
But avoid checking the functions in the test mode during the engine in operation. If there is no
other way than to check in the test mode, take necessary actions such as disconnecting the wire
for the external output or grounding the external output circuit.
(Always reconnect the wire after it is disconnected.)
!
Original content from www.daihatsu.cc
Issued to HORIZON TANKERS LIMITED S.A.

14
7.8 [MODE] key switch
You can select the mode change screen for the modes of 「1. STATUS」,「2. INITIAL RESET」, and 「3.
CONFFIGURE」by pressing the [MODE] key switch.
1. STATUS
1) CONTROLLER : To display the controller data on the LCD screen in a batch
2) SENSOR : To display the current status of the connected sensor
3) MIST/ALARM LEVEL : To digitally display the set mist quantity(full-scale 0-1023)
(mg corresponding value and temperature of sensor can be displayed.)
4) SOFTWARE VER. : To display the version of the software currently set in the system
5) WORKING MODE : To display that the oil mist detector version is now used.
6) ALARM HISTORY : To display that the history of the generated alarm is displayed.
(History is deleted in power supply OFF.)
2. INTIAL RESET
3. CONFIGURE (A password must be input for the change.)
1) CONTROLLER : To change the basic settings for controller display and
communication, etc.
2) SET ENG/SENSOR : To set the number of the engines and sensors
3) ISOLATE SENSOR : To temporarily disconnect and connect a sensor when the sensor fails
4) EXCEPTED FROM AVE. : To set a specific item to be excluded from the average computing
5) INITIAL VALUE SET : To manually set the alarm setting-off level
The 「1. STATUS」mode is to display the current status of the system, but does not change the setting.
The 「2. INITIAL RESET」is to reset the initial setting (for the engine and sensor quantity and the exclusion
from the average computing). The resetting procedure is in the same sequence as for the initial setting and in the
interactive manner.
The 「3. CONFIGURE」mode is to change the detailed setting for individual functions. A password “9999”
must be input for the change. Do not make the password public to prevent changing by anyone. Do not change
the settings unless definitely necessary.
Original content from www.daihatsu.cc
Issued to HORIZON TANKERS LIMITED S.A.

15
8. INSTALLATION
8.1 Sensor unit
(1) Use the sensor unit under environmental conditions meeting the following specifications
When mounting the sensor unit, select a place where vibration can be 4 G or less (2 Hz to 2 kHz).
When selecting the sensor mounting place, also check that the mist suction port of the sensor hood
cannot be continuously blocked by a large quantity of oil.
By rotatory direction of a crankshaft and structure of the engine inside, the heavy splash of lubrication oil
occurs, and there may be the case that the oil mist is hard to come in to a detecting element.
Please install it by a recommended method.
The recommended installation position of the MD-SX sensors is upper place from clank shaft and side of
figure below.
Fig. 9 Recommended attachment position of the sensor unit
MD-SX sensor
mounting position
[Example. 2]
MD-SX sensor
mounting position
[Example. 4]
2-strokes engine
MD-SX sensor
mounting position
[Example. 1]
MD-SX sensor
mounting position
[Example. 3]
4-stroke in-line engine 4-stroke V-engine
MD-SX sensor
mounting position
[Example. 1]
MD-SX sensor
mounting position
[Example. 2]
MD-SX sensor
mounting position
[Example. 2] MD-SX sensor
mounting position
[Example. 1]
Original content from www.daihatsu.cc
Issued to HORIZON TANKERS LIMITED S.A.

16
(2) Mounting conditions
1) Horizontal or downward (front declined) within 15°
Fig. 10 Tilt tolerance for horizontal direction
2) Rotation direction within ±5°
Fig. 11 Tilt tolerance for the rotation direction
(3) Insert the hood of the sensor unit into the crankcase through the threaded portion (thread size: G3/4) of
the engine frame, screw in the hood to the specified length (threaded portion length of 15 mm: 10 turns
or more) after winding a sealing tape, and secure the hood with the lock nut through the supplied
sealing washer.
Note:・If the screw part is not rolled up by seal tape, Oil leak will be occurred from screw part to engine
outside.
・If you use the special sealing washer (optional), it is not necessary to wind the sealing tape. If
you need this special sealing washer, please contact us
(4) Although the threaded portion is made of stainless steel and has sufficient strength, the case and the
front hood are made of plastics. When handling them, take care not to give undue force to them.
(5) Please do not install an obstacle to a radius of less than 100 mm from an installation hole of a sensor.
On sensor installation work, a sensor hits the obstacle, and there is the case that cannot screw.
Original content from www.daihatsu.cc
Issued to HORIZON TANKERS LIMITED S.A.

17
(6) When MD-SX sensor unit install on engine with the following condition, MD-SX sensor should be avoided to
install on these place.
- Oil comes from upper part like a waterfall continuously.
- Oil comes from lower part like a fountain continuously.
- Oil comes from the inside structure to reflect oil heavily.
- There is the structure like oil pool, and the sensor hood sinks.
In case the sensor is installed such a place, mist inlet holes of the hood may be blocked by oil and MD-SX may
not detect mist density surely. Then, oil comes into mist detection area in hood from the mist inlet holes.As a
result it may cause sensitivity abnormal or miss-alarms (HIGH and/or PRE-ALARM).
When MD-SX sensor unit can not install on the recommended place by the limit of engine design, Daihatsu
recommend using the cover structure or the protection pipe to cover the hood part of MD-SX sensor from heavy
scattering oil. Please refer to the below drawings for protection method or ask Daihatsu in the details.
Fig.12 (Sample 1) Protection pipe
Outline of Cover
Fig.13 (Sample 2) Cover structure
(7)In case of fitting sensor to a gear case except the engine crankcase, a chain case, the part of fuel oil supply unit,
please measure the vibration value of the sensor fitting part up to frequency 2KHz beforehand, then please fit
the sensor after confirmed the specification is satisfied.
In case of exceeding the vibration value from the specified value of sensor, please fit the sensor after executed
the anti-vibration measures.
If the sensor is fitted to the place the vibration value is large, or the space the engine outside is narrow where the
external force seems to suffer from the sensor connector,
Please adopt the flying lead type sensor or the ground type sensor.
When the connection is not enough between the sensor connector and cable connector by the large
Vibration or external force to the sensor, it may cause communication abnormal and/or the breakdown of
sensors. Please fix the cable within 200mm from a sensor connection to avoid the above troubles.
Original content from www.daihatsu.cc
Issued to HORIZON TANKERS LIMITED S.A.
Table of contents
Popular Security Sensor manuals by other brands
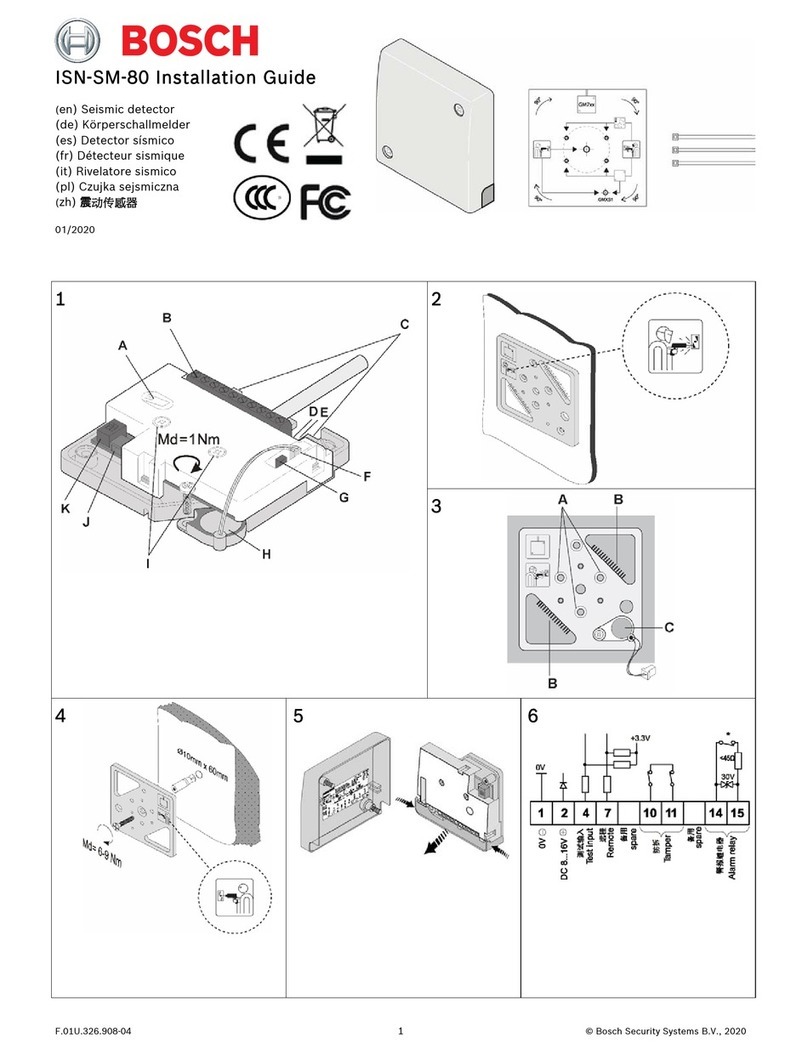
Bosch
Bosch ISN?SM?80 installation guide
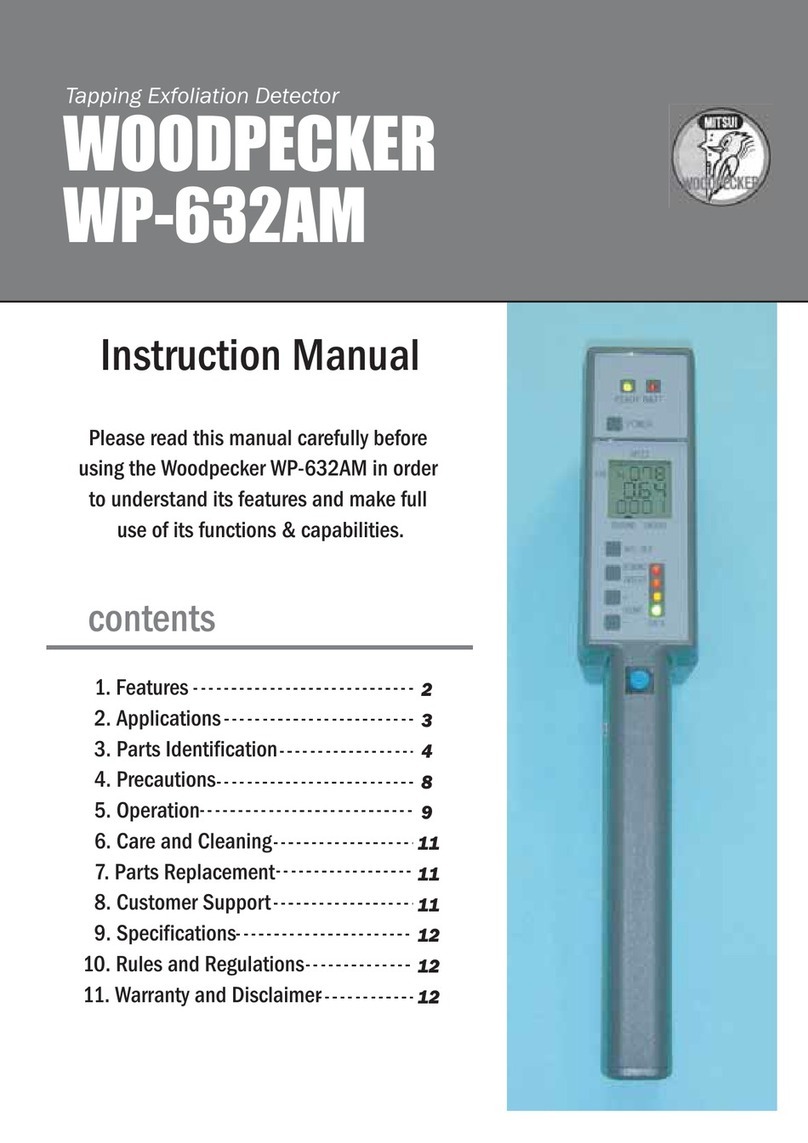
Woodpecker
Woodpecker WP-632AM instruction manual
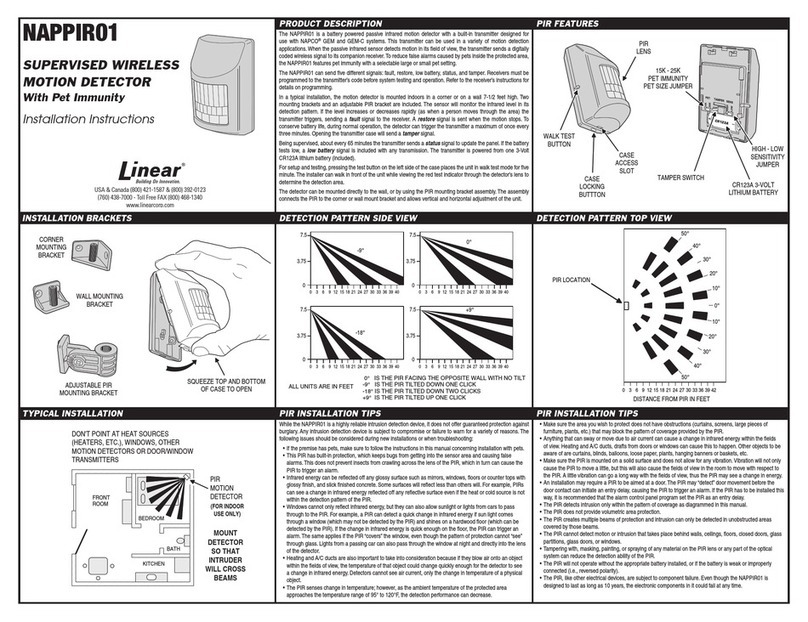
Linear
Linear NAPPIR01 installation instructions
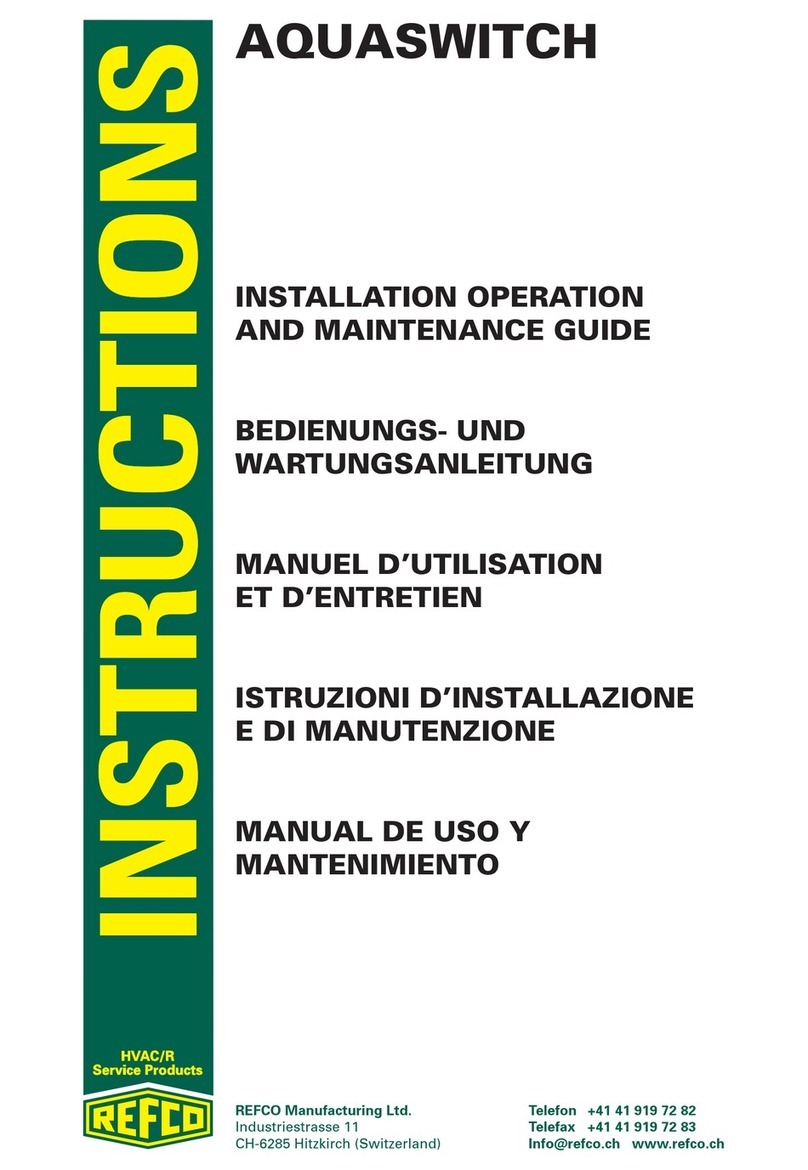
Refco
Refco AQUASWITCH Installation, operation and maintenance guide
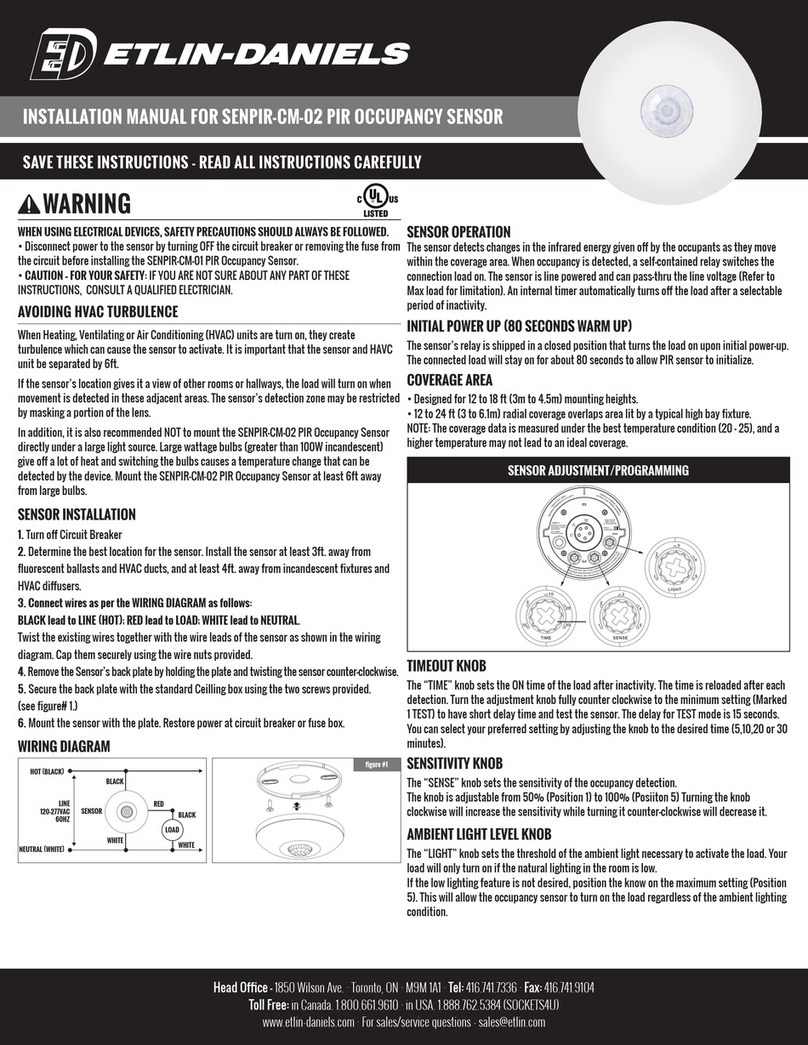
Etlin-Daniels
Etlin-Daniels SENPIR-CM-02 installation manual

Optex
Optex DX-40 installation instructions