Datum MobileTrak5 User manual

Page 1
MobileTrak5 Installation Instructions
PLEASE OPEN ALL BOXES & CHECK TO MAKE
SURE YOU HAVE ALL PIECES REQUIRED
READ ALL INSTRUCTIONS BEFORE STARTING
INST0111REV1NFW5/8/06
Tools Required for Assembly
7/16, 1/2 Wrench Phillips Head
Screwdriver Rubber Mallet
1/8, 5/32, 1/4"
Allen Wrenches
Mortar Trowel
(Optional) Tape Measure
Not Shown but required: Transit, Laser
Level or Water Level; Electric Drill; 2'
Bubble Level; 9" Bubble Level
Optional Equipment: Mortar Mixing
Equipment

A
Figure A
Figure B
MobileTrak5 Rail Installation Instructions
Page 2
STEEL PIN
5/16-18 x 1/4"
SET SCREWS
RAIL
TAG
TAG
TAG
TAG
DECKING
USE DECKING SECTIONS TO
CORRECTLY SET THE SPACING
BETWEEN THE RAILS
ALTERNATE DIRECTION OF RAILS. POSITION
FIRST RAIL WITH TAGS TO THE LEFT. NEXT
RAIL TAGS TO THE RIGHT. THEN ALTERNATE
FOR EACH ADDITIONAL RAIL.
LAYING RAILS
1. The number of rails and their size
depends on the size of the system. Refer
to floor plan for system dimensions. The
direction of each complete rail should be
reversed on each run of rail. This can be
done by positioning the first rails with all
tags to the left, the second rail with all
tags to the right, then alternate each
additional rail. Rail sections are connected
together with 1/4" steel pins and are
secured with (4) 5/16-18 x 1/4" long set
screws (see Figure A). Make sure rail
sections are butted tightly together before
tightening set screws.
2. Position all of the rail sections on the floor in the approximate location where they will be used.
Use decking sections to correctly set the spacing between rails (see Figure B). Refer to decking
layout sheet for rail sizes, decking placements and locations.
3. IMPORTANT! Verify the rail locations by measuring the centerline distance (see Figure C). The
rail location can also be checked by placing a carriage on the rails and assuring that the wheels are
centered on the rails and that the flanged wheels are approximately 1/16" to 1/8" from the rail
sides.

Figure C
Figure D
Figure E
Page 3
MobileTrak5 Rail Installation Instructions
VERIFY RAIL DISTANCE BEFORE CONTINUING INSTALLATION
CORRECT SPACING REQUIRED TO ENSURE SMOOTH OPERATION OF SYSTEM
RAIL
LEVELING SCREW
GROUT
FLOOR LINE
1/2"
MINIMUM
LEVELING RAILS
GROUTED: Using a water level, laser level, or transit (NOT BUBBLE LEVEL), locate the highest point
on the rail/floor. Leveling screws (see Figure D) should be installed approximately 24" apart. Do not
install screws in every threaded insert or you will not have enough screws for leveling the entire
system (Optional: Shims can be used in place of leveling screws). Begin leveling the rails working out
from the highest point. Use leveling screws or shims to position rails. There must be at least 1/2"
between the floor and the bottom of the rail (see Figure E). Rails must be level from left to right ,
front to back, and from rail to rail. NOTE: Height of rails should not vary more than 1/16" across
entire system. With rails leveled and in the correct position the rails should be screwed in place to the
floor. Use fasteners that are correctly suited for the flooring. This will keep the rails in place while
grouting. Mix grout (as per the instructions supplied with the grout) keeping in mind not to mix more
than can be used in a short time period. Work with a small (4 to 6 foot) section of track at a time.
Pack grout under the rail making sure not to leave any voids or air pockets (see Figure E). Pack grout
until it starts to come out the other side of rail. Using trowel, remove grout from under rail flanges
(see Figure E). Grout can be mixed with different amounts of water; more water makes it thinner and
easier to pack but takes longer to set up; less water makes a thicker consistency that sets up faster,
but is harder to prevent voids from forming under the rail. Mix to a consistency that you are
comfortable with. Complete the installation of the grout and let it set up for at least 12 hours before
going on to the next step.
ADJUSTABLE RAIL SYSTEM: Adjustable rails require the use of galvanized floor channels (see Figure
D). Rails sit on floor channels, which provide sturdy surfaces for the leveling screws to sit on. Using a
water level, laser level, or transit (NOT BUBBLE LEVEL), locate the highest point on the rail/floor.
Install leveling screws into the threaded inserts located in the rails (threaded inserts are spaced 6"
apart). Begin leveling the rails working out from the highest point. Rails must be level from the left to
the right, front to back, and from rail to rail. NOTE: Height of rails should not vary more than 1/16"
across entire system.
FLOOR CHANNEL
FOR CARRIAGES SHORTER THAN 72", DIMENSION EQUALS CARRIAGE LENGTH MINUS 12"
FOR CARRIAGES LONGER THAN 72", DIMENSION EQUALS CARRIAGE LENGTH MINUS 24"
DO NOT PACK GROUT UNDER
THESE FLANGES AS IT WILL
PREVENT DECKING
INSTALLATION.

Figure F
DECKING
DECKING
DECKING
DECKING
Figure G
#10 x 1" SELF
TAPPING SCREW
SPLICE PLATE
RAIL
DECK END TRIM
DECKING
#10 x 3/4" PARTICLE
BOARD SCREW
FLANGE OF
END TRIM
Page 4
MobileTrak5 Decking Installation Instructions
INSTALLING DECKING
Check to make sure that the decking has 1/4-20 T-nuts installed on the bottom. Use the decking
layout sheet supplied with each job as a guide. Install the decking sections from left to right, making
sure to install (3) splice plates between each section of decking (see Figure F). After all sections of
decking are laid out, it must be secured to the rails. To secure: Drill pilot holes through the pre-drilled
holes in the decking into the flange of the rail (space approximately 12" apart). Then use #10 x 1"
long self tapping screws to secure decking to rails. Make sure that rails do not move while attaching
decking (see Figure C. To make decking more rigid and eliminate "bounce", install 1/4-20 x 1 1/4" long
leveling screws through the T-nuts in decking until they contact floor and level with a 2' bubble level
(NOTE: try not to put weight on the decking while this is being done). Repeat for the remaining
decking sections. (NOTE: If the system is equipped with side ramps, skip to the section on installing
side ramps before attaching decking to system).
INSTALLING DECK END TRIM
(OPTIONAL)
Deck end trim is used in some cases to
cover the exposed end of a system (see
Figure G). Deck end trim is supplied in
standard sizes. In most cases these pieces
need to be cut in the field to fit. Deck end
trim is to cover decking only. Do not cover
the ends of the rails. After measuring and
cutting pieces to length, attach to decking
with the flange sitting on top of the
decking with #10 x 3/4" pan head Phillips
screws.

Figure H
Figure K
Figure J
NOTE: BE SURE TO USE DECK SPLICE PLATES BETWEEN SECTIONS OF RAMP
Figure I
RAIL
RAMP
RAIL
FILLER
METAL SECTION
#10 x 3/4" PARTICLE BOARD SCREW WOOD SECTION
#10 x 1 1/4" FLAT HEAD
PHILLIPS TEK SCREW
RAIL
BRACKET
#10 x 3/4" PARTICLE
BOARD SCREW 2 SHIMS
DECKING
1/4" CLEARANCE BETWEEN
DECKING & INSIDE OF BRACKET
MobileTrak5 Ramp Installation Instructions
Page 5
INSTALLING RAMP
The ramp installs with the flange of the ramp
resting on the lip of the front rails (see Figure H).
The ramp does not need to be secured to rail but
can be if necessary. To secure: Drill pilot holes
(approximately 48" apart) through the ramp into
the flange of the rail. Then using #10 x 1" long
self-tapping screws, secure the ramp to rails.
NOTE: Ramp runs entire length of system
including under the stationary units.
INSTALLING A.D.A. COMPLIANT RAMP (OPTIONAL)
Attach the metal ramp section to the wood ramp section using #10 x 3/4" particle board screws (see
Figure J). Lay the assembled section of the ramp on to the front most rail and attach using #10 x 1
1/4" flat head Phillips Tek screws. Repeat step for additional sections of ramp. Be sure to use deck
splice places between ramp sections.
INSTALLING SIDE RAMP (OPTIONAL)
In some cases, side ramps are installed on exposed
ends of systems (see Figure I). Use #10 x 3/4"
particle board screws to attach angle and shims to
bottom side of decking board before installing
decking board on system. The front ramp and the
side ramp will need to be miter cut in the field.
Refer to the customer layout for location of the
ramps.
INSTALLING FILLER (OPTIONAL)
Track filler is used to fill the gaps
between the anti-tip channel and the
rail. It is placed in the rail over the
adjuster screws (see Figure K). Two
different sizes of track filler are used
(see page 06).

Figure L Figure M
MobileTrak5 Filler Installation Instructions
Page 6
SHORT FILLER
RAIL
SET SCREWS
FLANGED
WHEEL
SET SCREWS
RAIL
NO FLANGE
WHEEL
TALL FILLER
Tall track filler is used in all gaps except where the flanged part of a wheel is located (see Figure L).
In cases where the flanged part of a wheel sits, a short track filler is used (see Figure M).

THIS PAGE
INTENTIONALLY
LEFT BLANK
Page 7
MobileTrak5 Installation Instructions

Figure N
Figure O
MobileTrak5 Carriage Assembly Instructions
Page 8
DRIVE SHAFT
5/16-18 x 3/4
HEX BOLTS
CARRIAGE HALF
5/16-18
NYLOCK NUTS
1/4-20 x 3/8
SET SCREW
CONNECTOR ASSEMBLY
CARRIAGE HALF
DRIVE SHAFT COUPLER
CARRIAGE HALF
SPLICE PLATE
5/16-18 x 3/4
HEX BOLT
5/16-18 x 3/4
NYLOCK NUT
WOODRUFF KEY
Carriages 108" long and shorter will be shipped in one piece. Carriages longer than 108" long will be
shipped in sections. To reconnect sections, bolt a connector plate to the end of one carriage section
(NOTE: The connector plate may be shipped already attached to one end of the carriage) using
5/16-18 x 3/4" hex head bolts and Nylock nuts. Do not tighten at this time. On manual and stationary,
slide next section on to connector and bolt into position using 5/16-18 x 3/4 hex head bolts and Nylock
nuts (see Figure N). Tighten all screws. On Mechanical Assist carriages, slide next section onto
connector assembly. To connect drive shafts, place a woodruff key in the slot in the drive shaft and
slide into coupler (see Figure N). Tighten coupler set screws to secure drive shaft. Bolt carriage
sections together using 5/16-18 x 3/4" hex head bolts and Nylock nuts (see Figure O). Tighten all
screws. Check drive shafts for binding. Repeat entire step for additional carriages.

DETAIL P
Figure Q
Figure P
P
WHEEL
CHANNEL
LOCATE SHELF SUPPORTS UNDER
EACH SHELVING UPRIGHT AS
LONG AS THERE IS NO
WHEEL CHANNEL UNDER
THE UPRIGHT.
SHELF
SUPPORT
SHELF
UPRIGHTS
MobileTrak5 Carriage Shelf Support Assembly
Instructions
Page 9
CARRIAGE FRAME
SHELF SUPPORT
5/16-18
NYLOCK NUT
5/16-18 x 3/4 BOLT
Measure location of shelving uprights on
shelving that is being used (see Figure Q).
Locate holes in carriage that will place the
shelving supports under the uprights of the
shelving being used. Insert 5/16-18 x 3/4 hex
head bolts and 5/16 Nylock nuts in carriage and
tighten most of the way (see Figure P). Slide
shelf supports over bolts and finish tightening.
NOTE: Laying carriage on its side or upside
down will make installation easier.

Figure R Figure S
MobileTrak5 Anti-Tip Installation Instructions
Page 10
5/16-18 X 1/2"
HEX HEAD BOLT
LOCK WASHER
FLAT WASHER
ANTI-TIP
BRACKET
WHEEL CHANNEL
ANTI-TIP BRACKET
RAIL
ANTI-TIP
CHANNEL
Four anti-tip brackets per carriage must be installed for anti-tip system to work properly. With
carriages on track, slide one anti-tip bracket under carriage making sure that anti-tip bracket stays
hooked under anti-tip channel. Attach bracket to wheel channel flange on underside of carriage using
two 5/16-18 x 1/2" hex head bolts, lock washers and flat washers (see Figure R). Tighten screws
making sure that bracket does not bind or scrape against anti-tip channel (see Figure S). Repeat for
remaining anti-tip brackets. Anti-tip brackets are attached to outer most wheel channels.

Figure U
METHOD 2
METHOD 1
Figure T
Page 11
MobileTrak5 Stationary Carriage Installation
Instructions
CROSSMEMBER
STATIONARY CARRIAGE
MOUNTING
BRACKET
STATIONARY CARRIAGE
GLIDE
CROSSMEMBER
5/16-18 FLANGE NUT
Use a movable carriage to align stationary carriage before screwing carriage to decking. Stationary
platforms can be mounted two ways (which way depends on the type of installation being done).
Method 1 (Figure T): Stationary carriage sits on
floor. Glides must be mounted to each
crossmember on the underside of the stationary
carriage (four glides per crossmember).
Method 2 (Figure U): Stationary
carriage is mounted directly to top
of decking. Attach two stationary
mounting brackets to each
crossmember on the stationary
carriage with two 5/16-18 x 1/2"
hex head bolts per mounting
bracket. After installing mounting
brackets attach stationary
carriage(s) to decking using #10 x
3/4" Phillips pan head wood screws
(4 screws per bracket).
Optional: Systems may have
shelving sitting directly on floor
adjacent to the movable carriages
and act as end stops for the
system. If this method is used,
shelving must be anchored to floor
(anchoring fasteners must be
supplied by the installer).

Figure V
Figure W
Figure X
MobileTrak5 End Stop Installation Instructions
Page 12
RAIL
END STOP
5/16-18 x 3/4 ALLEN
BUTTON HEAD SCREW
RUBBER BUMPER
1/4-20 x 3/8
PAN HEAD
5/16-18 x 3/4
ALLEN CAP SCREW
END STOP
RUBBER BUMPER
1/4-20 x 3/8
PAN HEAD
5/16-18
NYLOCK NUT MARK & DRILL USING
21/64" DRILL BIT
#10 x 1/2" PHILIPS
PARTICLE BOARD SCREW
LOCK PLATE
SYSTEM LOCK
5/16-18 x 3/4"BUTTON
HEAD ALLEN CAP SCREW
COVER
#8 x 3/8 TEK SCREW
End stops must be installed if:
1. System has no stationary carriages.
2. System has only one stationary carriage.
3. System has stationary carriages, but they are not secured
to floor or top of decking.
ANGLE END STOP BRACKET
Using two 5/16-18 x 3/4 allen button head screws, fasten end
stop on top of rail (see Figure V). Attach rubber bumper to
bracket with 1/4-20 x 3/8" pan head Phillips screw.
ALUMINUM END STOP BRACKET
Using two 5/16-18 allen cap screws, attach end stop bracketon
top of rail with rubber bumper facing mobile carriages.
INSTALLING CARRIAGE
SYSTEM LOCK (OPTIONAL)
Remove cover from system lock.
Place system lock in desired
location on side of carriage.
Using the system lock as a
template, mark the mounting
holes and drill using a 21/64" bit.
Attach the lock using the 5/16-18
x 3/4" button head allen cap
screw.

Figure Y
MobileTrak5 Carriage Cover Plate Installation
Instructions
Page 13
CHAIN TENSIONER
BEFORE CONTINUING, MAKE SURE THAT THE CHAIN
TENSION AND TENSIONER ARE TIGHT!
CARRIAGE
#10 x 1/2" PAN HEAD
PHILLIPS TEK SCREW
CARRIAGE
COVER PLATES
INSTALLING CARRIAGE COVER
PLATES (OPTIONAL)
Typically a carriage cover plate is used
where the shelving is not as large as the
carriage it's attached to. Center the
carriage cover plate on the appropriate
carriage and secure using #10 x 1/2"
long pan head Phillips Tek screws.
CHAIN

MobileTrak5 Shelving Installation Instructions
Page 14
Assemble shelving on carriage following shelving manufacturers assembly
instructions. NOTE: Shelving must be secured to the carriage to eliminate
the possibility of shelving falling over or off the carriage. USE CAUTION
when drilling or screwing into carriage. Drilling or screwing into
carriage wheels will cause carriages to be difficult, if not
impossible to move.
When racks or shelving units are mounted back
to back on carriages, it is required that they be
bolted together back to back and side to side
using hardware supplied by installer.

Figure Z
Figure 1B
Figure 1A
MobileTrak5 Drive Tower Installation Instructions
Page 15
TOWER BRACKET
24 TOOTH SPROCKET
5/16-18 x 3/4 HEX BOLT
DRIVE TOWER
CHAIN
DRIVE
BOX
0.25
Install the drive tower into top of tower bracket on
carriage (see Figure Z). Fasten tower to tower
bracket using 5/16-18 x 3/4" hex head bolts.
Place woodruff key in drive shaft. Slide sprocket
over drive shaft, aligning woodruff key with
sprocket. Slide sprocket so that front is 1/4" from
the front of the driveshaft (see Figure 1A). Place
blue locktite on 1/4-20 set screw and tighten.
Route chain on drive tower as shown in Figure 1B. Connect
ends of chain together using master link. Adjust chain
tensioner so that chain is tight. Do not put too much tension
on the chain or it will cause poor operation. Test chain
tension by turning handle shaft.

Figure 1C
SHOWN WITHOUT END PANELS OR
DRIVE BOX COVER.
Figure 1D
MobileTrak5 Drive Tower Cover Installation
Instructions
Page 16
PLACE HOLE
TANGENT WITH
BRACKET
PLACE LOCK CAM IN
VERTICAL POSITION
FOR SMOOTH
INSTALLATION
T-HANDLE (SHOWN
WITH OPTIONAL LOCK)
Before installing drive tower cover or mechanincal end
panel, the chain lock bar and T-handle need to be
aligned. Slide the lock bar so that the hole in the chain
lock bar is tangent with the right side of the mounting
bracket (see Figure 1C). Turn T-handle so that the lock
cam is in the vertical position, which will allow it to slide
in the lock bar.
CHAIN LOCK BAR
MOUNTING
BRACKET
If using drive tower cover, place cover over
drive tower. Secure in place using (4) #8 x
3/8" Tek screws (see Figure 1D). Check to
make sure that the T-handle engages lock
bar by turning handle to locked position and
ensuring the carriage is locked in position.
Continue to page 23 for handle installation.
If system includes fully enclosed end panels,
skip to page 19.
#8 x 3/8"
TEK SCREW
1/4-20 x 1 1/4"
HEX HEAD BOLT
DRIVE TOWER COVER
SEE ABOVE
FOR REQUIRED
LOCK ALIGNMENT

Figure 1E
Figure 1F
1G
Detail 1G
MobileTrak5 Upright Installation Instructions
Page 17
Mount end panel uprights using (4) 1/4-20 x 3/4" hex
bolts (see figure 1E). Do not fully tighten at this time.
Place top spacer bracket over studs on top of uprights.
Finger tighten (4) #10 - 24 flange nuts on studs.
Making sure that uprights are square, and top spacer's
flange is against top of shelving; tighten 1/4-20 bolts
and #10-24 flange nuts.
Screw #8 x 1/2" Tek screws into top of shelving on
carriage through holes in top spacer bracket (see
Figure 1F).
Attach female end panel clips to uprights using (2) #8
x 1/2 sheet metal screws per clip (see Detail 1G). The
clip opening should be facing away from shelving. If
using 3 piece end panels, clips will be used on all sets
of holes in uprights. If using a 1 piece end panel, clips
will be used in bottom holes, top holes, and the fourth
set of holes from the bottom.
TOP SPACER
BRACKET
#10 FLANGE NUT
1/4-20 x 3/4"
HEX HEAD BOLT END PANEL UPRIGHT
TOP SPACER
#8 x 1/2"
TEK SCREW
SHELVING
UPRIGHT
#8 x 1/2" SHEET
METAL SCREW
END PANEL CLIP
(FEMALE HALF)

MobileTrak5 Installation Instructions
THIS PAGE
INTENTIONALLY
LEFT BLANK
Page 18

Figure 1H Figure 1I
Figure 1J
MobileTrak5 End Panel Installation Instructions
Page 19
1 PIECE
END PANEL
END PANEL CLIP
(MALE HALF)
#8 x 1/2
SCREW
TOP 3 PIECE
END PANEL
MIDDLE
3 PIECE
END PANEL
BOTTOM
3 PIECE
END PANEL
#8 x 1/2
SCREW
END PANEL CLIP
(MALE HALF)
Install male end panel clips to end panels using (2) #8 x 1/2 sheet metal screws per clip. Place flat side
of male clip towards outside of end panel (see Figure 1J) Install 6 clips per one piece panel (see Figure
1H). Install 4 clips per panel on 3 piece end panels, making 12 clips in total (see Figure 1I).
PLACE FLAT PORTION
OF CLIP TOWARDS
SIDE OF PANEL
END PANEL

Figure 1M
Figure 1K
Figure 1L
MobileTrak5 Mechanical End Panel Installation
Instructions
Page 20
SEE PAGE 18
FOR PROPER
HANDLE
ALIGNMENT
UPPER 3 PIECE
END PANEL
LOWER 3 PIECE
END PANEL
1/4-20 x 1
HEX HEAD BOLT
3 PIECE WOOD END PANEL SHOWN
1 PIECE & STEEL ARE SIMILAR
T-HANDLE
3/8-24
JAM NUT
CHAIN LOCK CAM
#8-32 MACHINE SCREW
END PANEL
T-HANDLE
LOCK CAM
INSTALLING T-HANDLE
Install T-handle to end panel by inserting threaded portion through hole in end panel (see Figure 1K).
On 3 piece end panels, handle hole is located on bottom panel. On 1 piece end panels handle hole is
lower hole on panel. Attach to wood panel with #8-32 x 7/8" machine screw. Attach to steel end
panel with #8-32 x 3/8" machine screws. Screw first 3/8 jam nut on to T-handle. Place lock cam on
handle shaft as shown in Figure 1J. Finger tighten second jam nut onto handle shaft. Distance cam
1/8" from end of handle shaft (see Figure 1L). Fully tighten jam nuts.
INSTALLING END PANELS
If using steel end panels, attach steel panel spacers to drive tower using (4) #8 x 3/8 Tek screws
(see Figure 1M). On all panels, align T-handle and chain lock bar according to instructions on Page
18. Align male clips on end panel with female clips on uprights. Using smooth, firm pressure, press
end panels onto uprights. Tighten (2) 1/4-20 x 1" hex bolts through holes next to crank shaft.
UNLOCKED
POSITION LOCKED
POSITION
0.125
#8 x 3/8 TEK SCREW
STEEL PANEL SPACER
Popular Fan manuals by other brands

Hunter
Hunter 23898 Installation and operation guide
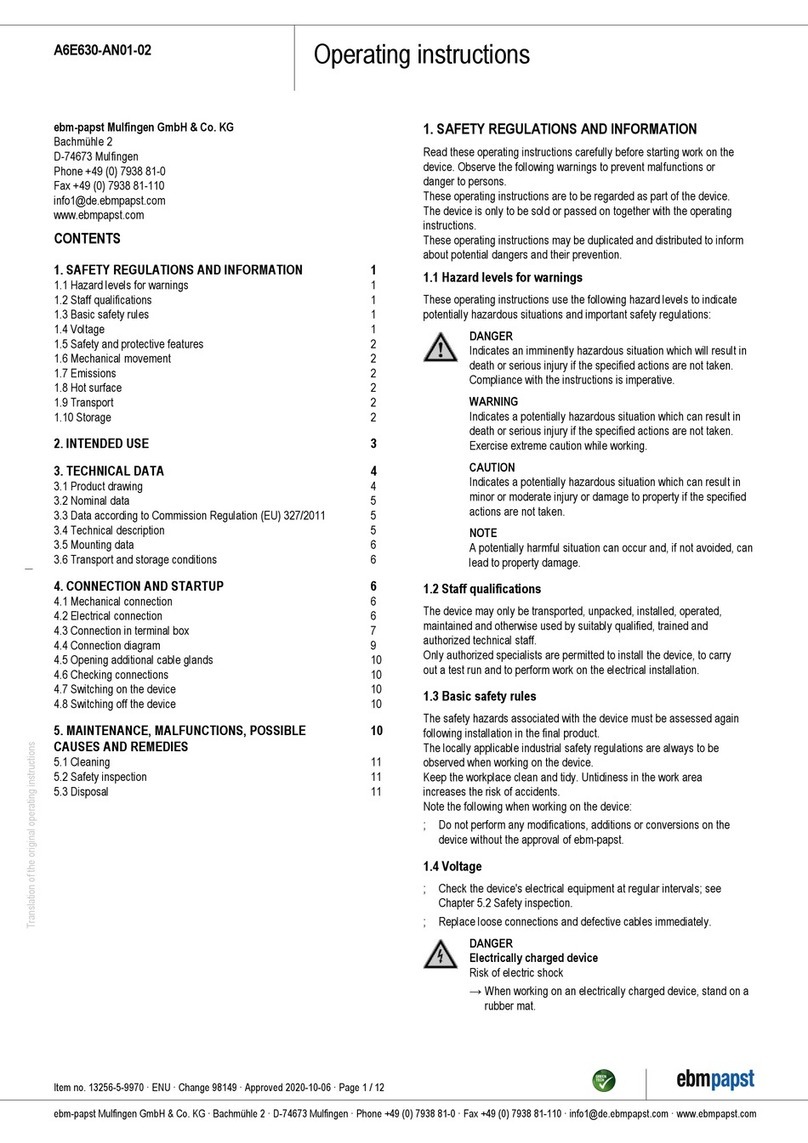
Ebmpapst
Ebmpapst A6E630-AN01-02 operating instructions
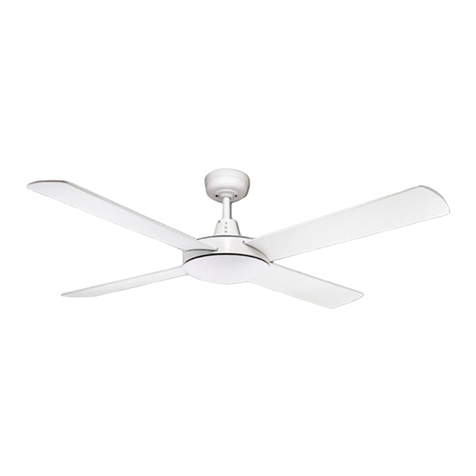
Fanco
Fanco Urban 2 Series Instruction book
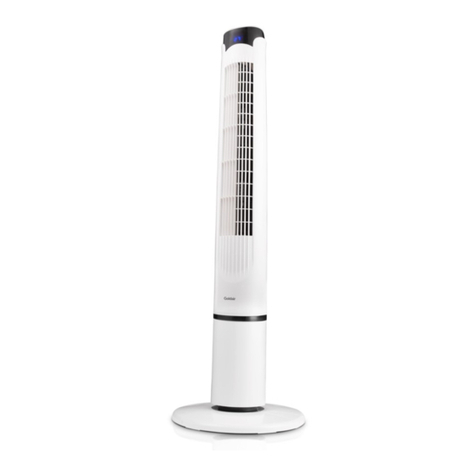
Goldair
Goldair GCTF370 operating instructions
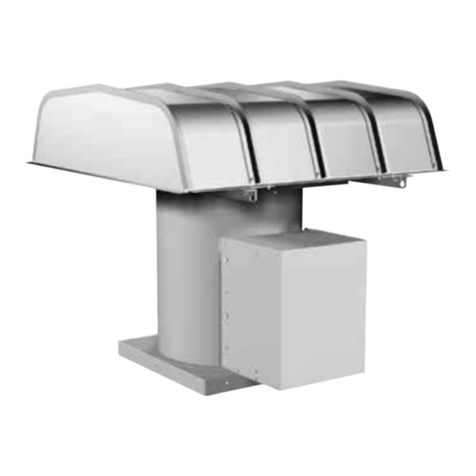
Greenheck
Greenheck TCB Series Installation, operation and maintenance manual

RP LIGHTING
RP LIGHTING 1070W installation guide