Eagle Tracker 3000 User manual

Eagle Solutions, ©2008, Tracker Operator Manual Page #1
Tracker 3000
Operator Manual
P.O. Box 350, 100 Eagle Parkway, Adairsville, GA 30103
800.633.0519 or 770.773.3875 Fax 770.773.9903
www.EagleFloorSolutions.com, email - customerservice@eagleoorsolutions.com
Solutions
Model #:
680022,
680267,
680570
ToOrderPartsCall1-888-702-5326-https://monsterfloorequipmentparts.com

Eagle Solutions, ©2008, Tracker Operator Manual Page #2
Eagle Solutions, ©2008, Tracker Operator Manual Page #3
Tracker 3000 deeply strips/scrubs in a 30” path with two 16” counter rotating
brushes removing multiple layers of oor nish easily with its propane
powered engine. No need for high voltage electric cords. Run time is 5 to 6
hours per propane cylinder. Available with your choice of Kawasaki, Robin
or Honda engines. Emissions protected by three-way catalytic mufer on
Kawasaki and Robin engines. Emissions shut down system, two 16” pad
drivers, and solution tank kit are available options.
Machine comes standard with service alert (hour) meter, two gear driven
16” Strata Grit Plus stripping brushes, easy change brush to pad drivers,
transport wheel, adjustable handle, aluminum safety-ll fuel cylinder with
overll prevention device (OPD) (UL and DOT approved), and two year
warranty.
Designed and manufactured in the U.S.A.
Tracker 3900
Production 20,000 sq ft/hour
Engine Speed 3,200 rpm
Cleaning Path 30”
Brush Speed 320 rpm
Brush Size Two 16” counter rotating brushes
Machine Dimensions L 53” x W 30.5” x H 42”
Total Weight 450 lbs
All engines exceed Environmental Protection Agency (EPA) and California Air Resource Board (CARB) regulations for exhaust emissions.
Features:
Tracker 3000
Deep scrub or strip
30” cleaning path
Two 16” gear driven brushes
Low profile 4” deck
No-flat 10” tires
Centrifugal clutch
Gear box driven
EPA & CARB approved
ToOrderPartsCall1-888-702-5326-https://monsterfloorequipmentparts.com

Eagle Solutions, ©2008, Tracker Operator Manual Page #2
Eagle Solutions, ©2008, Tracker Operator Manual Page #3
Table of Contents
What is Propane?..................................................................................5
Emissions...............................................................................................6
Controlling Emissions...........................................................................6
OtherAreas for Safety with Propane..................................................7
Emergency Situations with Propane...................................................8
Reminders..............................................................................................9
Operational Safety................................................................................9
MACHINE OPERATION
Safety Precautions During Machine Use..........................................10
Before Operating the Machine ........................................................................10
While Operating the Machine ..........................................................................10
Machine Storage.............................................................................................10
Servicing the Machine.....................................................................................10
Additional Safety Concerns and Precautions..................................................10
Machine Set-Up & Operation............................................................11
Checking Oil Levels and Filters.......................................................................11
Adjusting Handle.............................................................................................11
Installing the Fuel Cylinder..............................................................................11
Strip Brush Or Pad Driver Installation & Inspection ........................................11
Transport Wheel Installation, Removal............................................................11
Starting Machine .............................................................................................11
Operating Machine..........................................................................................11
Stopping the Machine......................................................................................12
Emergency Stopping.......................................................................................12
Cleaning the Machine......................................................................................12
Storing the Machine ........................................................................................12
Transporting the Machine................................................................................12
Maintenance........................................................................................12
Daily Maintenance - (every four hours of operation) .......................................13
Weekly Maintenance – (every 20 to 50 hours of operation)............................13
Monthly Maintenance – (every 80 hours of operation) ....................................13
Quarterly Maintenance – (every 250 hours of operation)................................13
Propane Fuel System......................................................................................13
Changing the Oil..............................................................................................13
Checking the Oil Level ....................................................................................13
Adjusting Belt Tension.....................................................................................13
Troubleshooting ..................................................................................14
Warranty Information........................................................................15
Instructions and Conditions for Warranty Reimbursement..............................16
Engine Warranty Flat Rate Chart ....................................................................17
Warranty Flat Rate Chart.................................................................................18
ToOrderPartsCall1-888-702-5326-https://monsterfloorequipmentparts.com

Eagle Solutions, ©2008, Tracker Operator Manual Page #4
Eagle Solutions, ©2008, Tracker Operator Manual Page #5
Before We Begin Please Consider
These Important Points!!
• Yoursafetyandthesafetyofthosearoundyouisyourresponsibility!
• Onlycertiedoperatorsshouldbeallowedtooperatepropanepoweredmachines.
• Readandunderstandthis“Operator’sManual.”Makesureeveryoneoperatingthe
machinesreadsandunderstandsitsbasicoperationofyourparticularmachine.
• Plannedmaintenance(PM)istheresponsibilityoftheoperator.
• Regular maintenance by trained service technicians will ensure long life and
satisfactoryperformancefromyourpropanepoweredmachine.Itwillalsohelpto
preventseriousinjurytoyouandothers.
• Onlyatrainedservicetechnicianshouldalteroradjustthefuelsystemorcarburetors
ofapropaneengine.
READ & UNDERSTAND OPERATOR’S
MANUAL BEFORE USING THIS MACHINE
This manual is furnished with each new propane powered machine.It provides
necessaryoperationandmaintenanceinstructions.Readandunderstandtheinformation
inthismanualbeforeoperatingorservicingthismachine.
• Check fuel cylinder for overll before taking it into the building or placing in
storage.
• Install fuelcylinderinawellventilatedarea.
• Beawareofpropanegasleaksifodorispresent.
• Makesurecarburetorairlteriscleanbeforestartingengine.
• Neverrunenginewiththrottleinchokeposition.
• Neverallowwatertocontacthotengine.
• Neverleavethemachineunattendedwhileengineisrunning.
• RemovefuelcylinderandstoreoutsideinanNFPAapprovedcabinet.
• Secure fuel cylinders when being transported.If installed on the machine service
valvemustbeOFF.
• Never store fuel cylinders in your vehicle where they may be exposed to high
temperatures.
• MaintainthemachineasdirectedbyEagleSolutions.
• Onlycertiedoperatorsshouldbeallowedtooperatepropanepoweredmachines.
Thispublicationisdesignedtoprovideaccurateandauthoritativeinformationinregard
tothesubjectmattercovered.Itisprovidedwiththeunderstandingthatthepublisheris
notengagedinrenderinglegalorotherprofessionalservices.
ToOrderPartsCall1-888-702-5326-https://monsterfloorequipmentparts.com

Eagle Solutions, ©2008, Tracker Operator Manual Page #4
Eagle Solutions, ©2008, Tracker Operator Manual Page #5
Propane is a hydrocarbon (C3H8) and is
sometimes referred to as liqueed petroleum gas,
LP-gas or LPG.It is produced from both natural
gas processing and crude oil rening.The major
harmful emissions from propane engines include:
Carbon monoxide (CO), Nitrogen oxides (NOx)
and Hydrocarbons (HC). Propane, like butane or
methane, is odorless.An odorant (usually ethyl
mercaptan) is added to give propane its very
distinctive, pungent smell.The odorant acts as a
warningagentsothatleakscanbedetectedquickly.
Itisnotharmfultobreathe.
Propane is unique because it is a gas at
atmosphericpressureandaliquidwhenstoredunder
pressure.Like any other liquid it expands when
heated, and it expands very rapidly.Compared
to water, propane will expand 17 times more in
volume with an identical increase in temperature.
Thereasonforstoringpropaneunderpressureasa
liquidinsideafueltankistosavespace.Agiven
volume of propane vapor can be compressed into
1/270thofitsvolumewhenliqueed.Conversely,a
givenvolumeofpropaneliquidcanexpandroughly
270 timesifallowed to changebackinto a vapor.
Because of this expansion, propane fuel tanks are
nevercompletely lledwith liquid.Newpropane
cylinders are manufactured with an Overlling
PreventionDevice(OPD) thatshutsoffthelling
processwhenthetankreaches80%ofitscapacity
to allow room for thermal expansion.Fuel tanks
are also equipped with pressure relief valves that
ventpropanevaporifinternaltankpressureexceeds
the preset rating of the valve. The valve closes
automatically when internal pressure is reduced
belowthisstart-to-dischargepressure.Thisallows
forchangesinfuelvolumecausedbytemperature
variationswithout anyreleaseofgasfromthetank.
Liqueedpropanehasaboiling pointof-44oF.
If venting propane from the xed liqueed level
gauge,beawarethattheplumeofgascanfrostbite
youresh.
Propane gas is heavier than air, approximately
1.5 times the specic gravity of air.Therefore,
if propane leaks from the fuel system or cylinder
it will lay close to the oor and seek low places,
like underdoors.Italsodoesn’tpuddlebutinstead
vaporizes and dissipates into the air.Because it
is released from a pressured container as a vapor,
propanecan’tbe ingested like gasolineoralcohol
fuels.Propaneisanon-toxic, non-poisonous fuel
that doesn’tcontaminateaquifersorsoil.
Propane has a narrow range of ammability
when compared with other petroleum products
andhasthelowestammabilityrangeofanyfossil
fuel.Inordertoignite,thepropane/airmixmust
contain from 2.2 percent to 9.6 percent propane
vapor.Ifthemixturecontainslessthan2.2percent
gas,itistooleantoburn.Ifitcontainsmorethan
9.6 percent,itistoorichtoburn.Propanewillnot
ignite when combined with air unless the source
ofignitionreachesbetween920-1020oFandcan
ignitewithoutneedingasparkorame.Incontrast,
gasoline will ignite when the source of ignition
reaches only 430-500oF.The propane ame will
notburnhotterthan3595oF.
Service Tech School
Thisclassincludesdiscussionsonsafeworkenvironmentsandprocedures,machineupdatesand
thefutureoftheindustry and Eagle Solutions. Enjoyhandsontrainingof electrical ignition and,
starting systems,replacingoffuelsystems,emissionstesting,advancedfailureanalysisandteardown
andreassemblyprocedures.You willbegivenaplanttourandmeetthecustomerservicepeopleyou
speakwithregularlyonthephone.ThiscerticationprogramisNOTasmallenginesclass.Although,
you donotneedtobeamechanictoattendyoushouldhaveageneralknowledgeofengines.Call
todayforaclassschedule,800.633.0519.
Benefits of Attending
• CertiedtoworkonEagleSolutionsequipment
• NFPACerticatetoworkonLP-Gasequipment
• UpdatedonmodicationsandnewEagleSolutionsequipmentrepairprocedures
• Arenewedappreciationforsafety
• Certicationcanhelplowerliabilityinsurancecosts
What is Propane?
ToOrderPartsCall1-888-702-5326-https://monsterfloorequipmentparts.com

Eagle Solutions, ©2008, Tracker Operator Manual Page #6
Eagle Solutions, ©2008, Tracker Operator Manual Page #7
United States and European studies show that
propane reduces greenhouse gases.The Propane
Education and Research Council states, “Unlike
fuels such as natural gas, propane vapor is
removed from the atmosphere faster than it takes
forittobecomewell-mixedandimpacttheglobal
climate.Additionally, propane does not have the
contaminants of some other fuels like diesel, and
haslesscriteriapollutantsacrossmanyapplications.
Propane’sportability,storability,andenvironmental
benets also qualify it to serve the unique needs
of several applications,” like oor maintenance
and restoration equipment.Based on the UK
Government’s Standard Assessment Procedure
(SAP) for Energy Rating for Dwellings (2005
edition),CalorGasLtd.concludedthat“electricity
emits80.0%moreCO2thanLPG–propanegas.”
(CO2 being a primary contributor to greenhouse
gas.)Therefore,we can be proud toproduceand
you toownpropanepoweredmachines.However,
therearesomeemissionsfrompropanethatcanbe
dangeroustohumans.
CarbonMonoxideisgeneratedintheexhaustas
theresultofincompletecombustionoffuel.COis
a very toxic, colorless and odorless gas.Propane
emissionsmaycontainconsiderableamountsofCO.
When operating propane powered oor machines
in tightly enclosed spaces carbon monoxide can
accumulatequicklyandreachconcentrationswhich
are dangerous for humans.It causes headaches,
dizziness,lethargyanddeath.
Nitrogenoxidesaregeneratedfromnitrogenand
oxygen under the high temperature and pressure
conditions in the engine cylinder.NOx consists
mostly of nitric oxide (NO) and some nitrogen
dioxide (NO2).Nitrogendioxideisareactivegas
andisverytoxictohumans.AccumulationofNOx
inawarehouseatmospheremaybealsodetrimental
forthestoredgoods.Forexample,onlyafewppm
of NOx in the ambient air can change the color
of paper stock from white to yellowish.NOx
emissionsarealsoaseriousenvironmentalconcern
becauseoftheirozonereactivityandimportantrole
insmogformation.
Hydrocarbons are also a product of incomplete
combustion of fuel.Propane emissions, because
of the composition of fuel, contain only short
chainhydrocarbons.Theyarenotlikelytocontain
toxic components which are found in gasoline
HC emission.Also, the environmental impact of
propane hydrocarbon emissions is much smaller
than that of gasoline.However, hydrocarbon
derivatives are responsible for the characteristic
smell which is often a nuisance when propane
enginesoperateindoors.
Emissions
OSHAhassetaCOPermissibleExposureLevel
(PEL) at 50 parts per million (PPM) over a time
weighted average of eight hours and a ceiling of
200 PPM.TomanagepropaneemissionsinEagle
machines,weinstallathreewaycatalyticmufer
that takes the reactions from CO, HC and NOx
and simultaneously removes nearly all of these
pollutants.Concentrations of pollutants in the
exhaustgasdependonthefuelmixturecomposition.
At lean fuel mixtures, the exhaust gases contain
little carbon monoxide or hydrocarbons but high
concentrations of NOx.Rich mixtures produce
highconcentrationsofCOandHCwithlittleNOx.
Therefore, it is very important to maintain the
engineasrecommended.Somethingsthatassistin
keepingemissionslowfollow.
AirFilters:Theairfuelratiocanbeaffectedby
dirtyairlters,whichcancauseanimbalanceinthe
airmixedwithpropaneandincreasesemissions.It
is imperative that the operator check and correct
dirtyairlterseverytimethemachineisused.
OilLevel:Anotherthingthatcanalteremission
levelsistheoverllingofoil.Whentheoillevelis
toohigh,thevacuumeffectoftheengineoverthe
oilpanpullsoilvaporofftheoilanddistributesit
on thecarburetorairlter.Thisinturncollectsdust
andrestrictsthefreeowofairtothefuelmixture.
Inturn,itincreasestheproductionofCO.Operators
shouldfaithfullychecktheoillevelandkeepitat
the recommended level and not leave machines
idlingformorethanafewminutes.
When checking the oil level, be aware that
different engine manufacturers have different
instructionsforcheckingtheoillevel.Someinstruct
tounscrewthedipstick, wipe itoffand reinsert it
withoutscrewingit in,thenextractingittoreadthe
level.Othersinstructthedipsticktobescrewedin
beforereadingthelevel.Becauseoftheimportance
ofmaintainingthecorrectoillevelalwaysconsult
the engine manufacturer operation manual for the
correctprocedure.Atalltimesthemachineshould
besettinglevelontheoorwhencheckingtheoil.
Controlling Emissions
ToOrderPartsCall1-888-702-5326-https://monsterfloorequipmentparts.com

Eagle Solutions, ©2008, Tracker Operator Manual Page #6
Eagle Solutions, ©2008, Tracker Operator Manual Page #7
Machine Handling:Eagle machines should
never be turned on the carburetor side.This can
causeoiltodrainintothecarburetorand/ortheair
lter and result in oil smoke and increased toxic
emissionswhentheengineisrestarted.Alwaystip
themachineover,ifnecessary,withthecarburetor
on thetopside.
EmissionsShutDownSystems:Propaneengine
fuel systems can be tted with safety devices
and shut-off valves that function automatically
if the emissions become too high or a fuel line
is ruptured.If your machine is equipped with a
shut down device, do not attempt to circumvent
or disconnect it. If you receive a warning of high
emissions,checktheairltersforexcessdustoroil
contamination.Ifneitheroftheseconditionsexist,
havethe machinecheckedbyanauthorizedservice
technician.Donotcontinuetooperatethemachine!
Machinesttedwithelectronic emissions controls
needawarm-upperiodofapproximately12to15
minutesto effectivelydissapateemissions,soitis
recommended the engine be started outside and
allowedtowarmupbeforebringingitinside.
OtherAreas for Safety with Propane
Propane Fuel Cylinders:The National Fire
Protection Association (NFPA) has established
standardsforthestorageandhandlingofliqueed
petroleum gases.This standard is NFPA58 and
is recognized in the United States and Canada as
wellassomeother countries.For other countries
theownermustassurethattherequiredregulations
aremet.
The fuel cylinder supplied with this machine is
aD.O.T.4E240motorfuelcylinder.Cylindersnot
brandedwithD.O.T.4E240onthetopcollarshould
neverbeusedonpropanepoweredequipment.Never
useacylinderfromagasbarbecue,forexample,on
thismachine.Thecapacityofthe4E240cylinder
is20 lbs.,80%ofthetotalliquidcapacity.Never
allow a fuel cylinder to be overlled.Have the
cylinder lled at a reputable propane dealer and
checkitforoverllbeforeacceptingit.
OPD:The supplied cylinder is also tted with
an overll protection device (OPD) that prevents
overllingofapropanecylinder.
Cylinder Filling:Before having a cylinder
relledexaminethecylinderfordamage,including
dents, bulges or cracks on the container surface,
rusting,particularlyonthebottomofthecylinder,
missing cylinder foot ring, collar or valve cover,
manufacture or recertication date, and OPD
valve.Thesearethingsthatcanrenderthecylinder
unusableanddangerous.Cylindersareonlyusable
for12yearsfromthedateofmanufactureandmust
berecertiedevery5years.
Checking a Cylinder for Overll:Always
wear frost proof gloves and a face shield before
attemptingtocheckfuelcylinderforoverll.
1. Take to a safe area outside, away from open
amesandcigarettes.
2. Open the xed liquid level gauge (bleeder
valve).
3. Observethe gasexitingfromthevalve:white
cloud = OVERFILLED; no cloud visible =
SAFE!
4. Ifoverlled,allowtoventuntilvaporisclear.
Do not attempt to repair a damaged propane
cylinder yourself.Return the cylinder to your
propanevendorforauthorizedservice.
Cylinder Storage & Transportation:Propane
fuel cylinders, whether full or empty, should
be stored OUTSIDE the building in a secure,
approved cylinder storage cabinet in accordance
with NFPA58.Do not store cylinders near other
ammableorcombustiblematerials.Thepropane
fuelcylindersthatEaglemachinesusearevertical
cylindersandshouldalwaysremaininthevertical
position, even when being transported or stored.
This position assures the pressure relief valve
and other ttings are in direct contact with the
vaporinthe cylinder andnotthe liquid. Keepthe
safety relief valve pointed away from anything
that escaping propane could come in contact with
possiblycausingareoraccident.Removecylinder
from machine when not in use.Local authorities
mayhaveadditionalrequirementsforfuelcylinder
storage.Alwaysconsultwiththelocalremarshal
forlocalcodes.
NFPA58 Chapter 5 addresses the storage
of portable containers.This standard says,
“Containersinstorageshallbelocatedtominimize
exposure to excessive temperature rise, physical
damage,ortampering.”NFPA585-3detailswhat
isallowedto bestoredinbuildings frequentedby
thepublic.NOTE:Onlycylinderswithamaximum
LP-Gas capacity of no more than 16.8 ounces
shall be permitted to be stored or displayed in
buildingsfrequentlybythepublic.Eaglemachines
use a 20 POUND capacity cylinder and are not
allowed to be stored in buildings frequented by
ToOrderPartsCall1-888-702-5326-https://monsterfloorequipmentparts.com

Eagle Solutions, ©2008, Tracker Operator Manual Page #8
Eagle Solutions, ©2008, Tracker Operator Manual Page #9
the public.In addition, the standard (NFPA 58
5-4.2.1 (b) says “Containers shall be protected
by alockable,ventilatedmetallocker orrackthat
preventstamperingwithvalvesandpilferingofthe
cylinder.”Thestandardalsoincludesthedistance
fromanydoorwayoropeninginthebuilding“shall
beatleast5feet.”
When transporting fuel cylinders it is
recommended that the service valve is closed and
thecylindersare rmly securedinthe vehicle.If
installedonamachinethemachineitselfshouldbe
rmlysecured.Neverallowafuelcylindertoroll
aroundinthebackofapickup,trailerorvehicle.
Formoreinformationonpropanesafety,approved
fuelcylindersandcomponents,transporting,storage
andllingcylinders visitthefollowingweb sites:
www.propane101.com
www.propanesafety.com
www.nfpa.org
www.epa.org
Additional Caution!
In some areas your propane supplier or vendor may offer an “exchange service”
where they set up a security storage cage/rack and exchange lled cylinders for
empty ones or ll them on sight from a delivery truck. If you subscribe to that type of
service be very careful to:
• MakesurethevendorinstallsaVERTICALcylinderrackfor
verticalcylinders.
• Checkeachcylinderforoverll.
• CheckeachexchangedcylindertobeassureditisaVAPOR
DRAWcylinder.
• Checkthemanufacturingdateonthecollartobeassuredithas
notpasseditsrecerticationdate(twelveyears).
Emergency Situations with Propane
PressureReliefValveVents:Coolthecylinderas
quickly aspossibleusingwaterorareextinguisher
on thebody ofthecylinder.Ifthepropanevapor
fromthepressurereliefvalveshouldignitedonot
attempt toextinguishtheame!Itisconsumingthe
propanegasasitisrelieved.Instead,pointthere
extinguisherorwaterhoseonthecylindertocoolit
downandlowerthepressureinthecylinder.The
reliefvalvewillcloseandtherewillgoout.
OperatorHeadache,DizzinessorNauseousness:
Immediately shut down machine and get to fresh
air.These symptoms can be caused by CO and
can lead to serious health risks.To prevent such
situations never operate propane machines in a
closed environment.Maintain ventilation at all
times.Follow machine and engine maintenance
proceduresstrictly.Haveengineemissionschecked
quarterly.
PropaneSmell:Ifyousmelltheodorofpropane,
stop the engine, remove the cylinder and take it
outside for inspection.Check all connections for
leaks.Informyoursupervisor.
Odors Other Than Propane:Potentially toxic
emissions are produced by internal combustion
engines.Properly maintained engines produce
a small amount of these gases including carbon
monoxide.Although carbon monoxide has no
odor,thehydrocarbonsdoandanelevationofodor
may indicate increased CO as well.Inform your
supervisor.
ToOrderPartsCall1-888-702-5326-https://monsterfloorequipmentparts.com

Eagle Solutions, ©2008, Tracker Operator Manual Page #8
Eagle Solutions, ©2008, Tracker Operator Manual Page #9
• Operator must have completed certication
trainingbeforeusingmachine.
• Propermaintenanceistheresponsibilityofthe
operatorbeforeuseofmachine.Thisincludes:
checking the oil level, checking and cleaning
airanddustlters,keepingmachinecleanand
lubricated,inspectfordamaged,wornorloose
parts,cleancarburetorairlters(andasneeded
during operation), clean entire machine after
eachuse.
• Sweepoorandcheckforitemsprotrudingout
oftheoorsurfacebeforeoperatingmachine.
• Do not start engine with the transport wheel
attached,ifapplicable.
• Donotallowthemachinetorununattendedor
betiltedbackwhileitisrunning.
• Exhaustparts areextremely HOT.Becareful
not to allow them to come into contact with
anythingoranyone.
• Do not attempt to change pads or abrasives
whiletheengineisrunning.
• Exercise extreme caution when installing
or changing pads or abrasive material.The
machineisveryheavy!
• Maintainproperroomventilation.
• Donotstandonthemachine.
• Stoptheenginebyclosingtheservicevalveon
thefuelcylinder.
• Removethekeyfromtheswitch,ifapplicable,
topreventunauthorizeduse.
• Removethefuelcylinderfromthemachineand
storeitoutsideinasecureapprovedcabinet.
• Servicingoradjustingthepropanefuelsystem
should only be done by a trained service
technician.Never attempt to adjust the fuel
systemofapropaneengine!Ifequippedwith
an emission monitoring or controlling system
neverattempttodisconnectitorcircumventit!
• Neverattempttobypassordisconnectthekill
switchoranyothersafetydevices.
• Liqueed propane will expand 270 times to
ammable vapor - avoid needless release
of liqueed propane and using overlled
cylinders.
• Propaneisheavierthanair–ifitleaksitwill
spreadinlowplaceslikeunderdoorswhereit
maybeignitedandcausedamage.
• Only use 4E240 cylinders that are approved
bytheDOT-neverusecylindersdesignedfor
otherserviceslikebarbecues.
• The low boiling point of propane can cause
serious frostbite – always wear frost proof
gloves and a face shield before attempting to
checkforfuelcylinderoverll.
• Incaseofare,keepthefuelcylindercoldwith
anextinguisherorwaterhose.
• Store fuel cylinders vertically in an outside
lockable,ventilatedstoragelocker.
• Beawareofthesymptomsofcarbonmonoxide
poisoning and take appropriate actions if
necessary.
• Always maintain engine and machine as
specied for superior performance, long life
andsafety.
Reminders
Operational Safety
ToOrderPartsCall1-888-702-5326-https://monsterfloorequipmentparts.com

Eagle Solutions, ©2008, Tracker Operator Manual Page #10
Eagle Solutions, ©2008, Tracker Operator Manual Page #11
This propane fueled machine is intended for
commercial use only.Do not use the machine
other than described din this Operator’s Manual.
All operators must read, understand and practice
thesafetyprecautionsinthismanual.Onlytrained
and authorized operators should operate propane
poweredoormachines.Checkfuelcylindersfor
overllbeforetakingthemintothebuildingoryour
vehicle.
Before Operating the Machine
• Checkoillevel.
• Checkcarburetorairlter.
• Checkpadandpadholder.
• Adjusthandleheight.
• Installfuelcylinderinawellventilatedarea.
While Operating the Machine
• Eagle Solutions recommends wearing hearing
protection while operating any internal
combustionengineinanenclosedarea.
• If you smell the odor of propane, stop the
engine,removethecylinderandtakeitoutside
forinspection.
• Be aware of odors other than propane. Toxic
emissionsareproducedbyinternalcombustion
engines.Properlymaintainedenginesproduce
asmallamountofthesegasesincludingcarbon
monoxide.Althoughcarbonmonoxidehasno
odor,thehydrocarbonsdoandanelevationof
odormayindicateincreasedCOaswell.
• Donotallowthemachinetorununattended.
• Exhaustparts areextremely HOT.Becareful
not to allow them to come into contact with
anythingoranyone.
• Donotattempttochangebrushesorpadswhile
theengineisrunning.
Machine Storage
• Stoptheenginebyclosingtheservicevalveon
thefuelcylinder.
• Removethekeyfromtheswitch,ifapplicable.
• Removethefuelcylinderfromthemachineand
storeitoutsideinasecure,approvedcabinet.
• Cleanandinspectairanddustlters.
Servicing the Machine
Planned maintenance is the responsibility of the
operator.Itincludes:
• Checkingoillevel.
• Checkingandcleaningairanddustlters.
• Keepingmachinecleanandlubricated.
• Reporting any damaged or worn parts to
supervisor
• SeeMaintenancesectionforservicingintervals
andinstructions.
• Servicingoradjustingthepropanefuelsystem
should only be done by a trained service
technician.
• Never attempt to adjust the fuel system of a
propaneengine! Ifequippedwith anemission
monitoringorcontrollingsystemneverattempt
todisconnectitorcircumventit!
Additional Safety Concerns
and Precautions
• Operatormusthavecompletedtrainingbefore
usingmachine.*
• Sweepoorandcheckforitemsprotrudingout
oftheoorsurfacebeforestarting.
• Nevertiltthemachinebackwhileitisrunning.
• Do not start engine with the transport wheel
attached.
• Exercise extreme caution when installing or
changingbrushesorpads.Themachineisvery
heavy!
• Checkforlooseboltsandnutsdaily.
• Clean carburetor air lters after four hours
running and clean or replace daily before
operation.
• Cleanentiremachineafter each use including
underthegeardriveassembly.
• Because of the length of time these machines
may operate continuously it is very important
tobeassuredofproperventilation.
• Neverattempttobypassordisconnectthekill
switchoranyothersafetydevices.
*To arrange for operation and safety training
contactEagleSolutionsbyphoneat770.773.3875,
email customerservice@eagleoorsolutions.com
or mail request to P.O. Box 350, Adairsville, GA
30103.
Machine Operation
Safety Precautions During Machine Use
ToOrderPartsCall1-888-702-5326-https://monsterfloorequipmentparts.com

Eagle Solutions, ©2008, Tracker Operator Manual Page #10
Eagle Solutions, ©2008, Tracker Operator Manual Page #11
Checking Oil Levels and Filters
Checkoillevelspriortostartingengine.Refer
toengineowner’smanualfortheproperprocedure.
DONOTOVERFILL OIL LEVEL; todosomay
cause damage to the engine and may elevate
harmfulemissions.Use10W30oil.Alwayscheck
oil daily before using the machine (see “Daily
Maintenance”).
Be sure the carburetor air lter is free of dust,
oil,etc.Dirtyltersarethemostfrequentcauseof
elevatedtoxicemissions.
Check recoil dust lter.Clean or replace if
necessary.See the instructions in the engine
owner’smanual.
Adjusting Handle
Your machine is equipped with an adjustable
handleforcomfortanduse.Mostnditnecessary
to adjust the handle to “belt height” for optimum
control.A9/16wrenchisusedtoloosenandtighten
thepivotpoints.
The handle folds over the engine to facilitate a
compact transport space.However, leaving the
handle loose when operating, allows the operator
tofoldthehandlewhileusingtheTrackerintight
spaces.
Installing the Fuel Cylinder
1. Takemachinetowellventilatedarea.
2. Checkcylinderforoverll.
3. Placecylinderonthemachineintankholding
areaandsecurethestrap.
4. Connectfuelcylindertothemachineusingthe
“Rego”connection.Tightenhandtight.Donot
useawrenchorpliersorcrossthreadtheRego
connection.
5. Opentheservicevalveslowly.Bealertforthe
odorofpropanethatmayindicatealeak.
6. Toremovethecylinder,reversetheprocedure.
Strip Brush Or Pad Driver
Installation & Inspection
1. Place transport wheel on Tracker & install
safetychain.
2. Lying on oor, grip strip brush or pad driver
withbothhands.Firmlytwistinalefttoright
rapidmotion.
3. Removeandinspect.
4. Reinstallinsimilarmotion.
5. Removetransportwheel.
Transport Wheel Installation,
Removal
1. Position one operator at Tracker handle,
pressingdowntoliftfrontendofmachine.
2. Second operator removes or installs transport
wheel.
3. When installing transport wheel, position
so that the chain on the transport wheel that
holdsthesecurepinisinthefront,awayfrom
the Tracker.This assures that the wheel is
positionedproperly,allowingeaseofmovement
whenpushingtheTrackertostorage.
Starting Machine
1. Check fuel cylinder for overll and install
cylinderonmachine.
2. Installbothstripbrushesorpaddedpaddrivers
ontomachine.
3. Remove transport wheel.Store in a secure
location.
4. Place machine on level surface and check for
correctoillevel.
5. Lowersplashguardskirttooorlevel.
6. Slowly open the service valve on the fuel
cylinder.NOTE: Opening the service valve too
quickly may cause the excess ow valve to stop
the ow of propane. If this occurs, close the
valve, wait a few seconds and re-open the valve
SLOWLY!
7. Chokeengineandengagestarterwiththrottlein
‘slow’position.
5. When engine starts, ease the throttle back to
running position.NOTE: Do not run engine
with the throttle in the choke position! Excessive
harmful emissions will be produced putting you
in harm’s way!
7. Increasethrottle.Centrifugalclutchwillengage
and brushes will begin turning.Continue
increasingthrottleto100%positionasmachine
movesforward.
Operating Machine
WARNING! Be careful not to allow the machine to
come in contact with loose tiles or other obstructions
on the oor. If objects are hit by the revolving pad
they could become dangerous projectiles.
1. Clearareaofalldisplays.Removeanydustand
stickersfromoor.
2. Prepare stripping solutions according to
instructionsonthechemicallabel.
3. Apply solution to the oor using a mop or
solutionspreader.KEEPFLOORWETWITH
SOLUTION!
Machine Set-Up & Operation
ToOrderPartsCall1-888-702-5326-https://monsterfloorequipmentparts.com

Eagle Solutions, ©2008, Tracker Operator Manual Page #12
Eagle Solutions, ©2008, Tracker Operator Manual Page #13
4. Allow stripper solution to penetrate as
directed.
5. Begin stripping with the machine (one pass
is generally all that is needed).Move at a
deliberate,steadypace.
6. Keepmachinemoving.Runninginoneplace
formorethan afewseconds maydamagethe
oor.
7. Do not leave machine unattended while the
engineisrunning.ATTENTION: It is possible
to damage the engine by allowing it to idle
for long periods of time by affecting proper
lubrication. WARNING! Exhaust emissions
contain harmful toxic gases; the worst being
carbon monoxide. Always make certain that
adequate ventilation is available. Do not
operate the machine in conned areas.
8. When stripping against walls, it is best to
generallykeep thewallto theoperator’sright
handside.Mosthandedgingmaybeeliminated
or at least minimized by moving slowly with
theTrackeralongwalls.
9. Removesludgewith vacuumrecoverysystem
or auto scrubber.Damp mop oor- rinse
thoroughly.
10. Uponcompletion,followshutdownprocedures
as instructed in operation manual and allow
enginetocometoacompletestop.
11. Raisesplashguardskirtandtighten.
12. Install transport wheel, positioning chain of
transportwheeltowardsfrontofmachine.
13. Turnkeyswitchtooff,ifsoequipped,andplace
keyinsecurelocation.
14. Removestripbrushesorpaddrivers.
Stopping the Machine
1. Putmachineinidlemode.
2. Close the service valve on the fuel cylinder
while the engine is running.This serves to
“purge”thefuelsystemofallammablegas.
3. Ifequipped,turnthekeyswitchtoOFF.
Emergency Stopping
Incaseofemergency,themachinecanbebrought
toaninstantstopbythefollowingmethods:
»Release “KILL SWITCH” (if installed).
»Turn key switch to “off” position (if installed).
»Position throttle to “off position.
»Close control valve on fuel cylinder.
Cleaning the Machine
Afteruse,theunderneathoftheTrackermaybe
hoseddownforcleaningbystandingthemachinein
anuprightposition.
1. Removethepropanecylinder.
2. Twooperatorsshouldrmlygripthefrontofthe
Trackerandliftuntilthemachineisupright.
3. Thestrippingbrushesorpaddriversmaythen
be easily removed and the under belly of the
Trackermaybecleaned.
4. Care should be taken when lowering the
machine;twoorthreeoperatorsmaybeneeded
(it is heavy!).NOTE: An operator should be
stationed by the side of the Tracker when it is
in an upright position to prevent it accidentally
being knocked over. It should never be left
unattended in the upright position.
Storing the Machine
1. RemovethefuelcylinderandstoreinaNFPA
approved propane storage cage outside as
directedbyyourlocalgovernment.
2. After the engine has cooled completely, clean
machinethoroughly.
3. Performalldailymaintenancerequirements.
4. Storemachineinacool,dry,secureareawhere
itwillnotbedamagedbyothertrafc.
Transporting the Machine
Whentransporting themachinefromonejob to
another,securethemachinewiththefuelcylinder
installed and the service valve OFF!Allow the
enginetocooldownbeforeloadingit.
Maintenance
WARNING: Before attempting any maintenance
procedures on the machine, close the service valve
on the fuel cylinder and stop the engine.
Repairsandadjustmentstothefuelsystemmust
be performed by an authorized, properly trained
service technician. To keep the machine in good
workingcondition,simplyfollowthedaily,weekly
andmonthlymaintenanceprocedures.
Keeping the machine clean and free from
accumulateddust,lintandoil allowsfreeair ow
acrosstheengineandpropercooling.Alwaysuse
cleanrecoildustlters.Thesecan be cleaned by
washing them in owing water and shaking them
dry.Extra lters may be ordered from Eagle
Solutions at 800.633.0519.Keep a log book of
maintenanceand/orrepairs.
ToOrderPartsCall1-888-702-5326-https://monsterfloorequipmentparts.com

Eagle Solutions, ©2008, Tracker Operator Manual Page #12
Eagle Solutions, ©2008, Tracker Operator Manual Page #13
Daily Maintenance - (every four
hours of operation)
• Check oil level (use 10W30 or SAE30 oil
only).
• Checkandcleanrecoildustlter.
• Checkandcleancarburetorairlter.
• Check belt tension by pinching belt together.
Beltshoulddeectonly½”(13mm).
• Make sure all components (pad holder, fuel
cylinder,etc.)aresecureandtight.
• Check pad holder and pad daily (clean or
replace).
• Cleanmachine.Ifcompressedairisavailable,
blow dust from machine and engine,
concentratingontheinsideofengineshrouds.
Wash undercarriage.CAUTION: Care should
be taken to make sure engine is cool before
water is used to prevent warping and other
damage.
Weekly Maintenance – (every
20 to 50 hours of operation)
• AllDailyMaintenanceservices.
• Changeoilandoilltersat50hoursofservice.
Use10W30orSAE30motoroil.Useofnon-
recommendedoilmayvoidtheenginewarranty
(seeengineowner’smanual).
• Check for loose nuts and/or bolts on entire
machine.
• Examineallpropanefuelcomponentsforleaks
orwear.Replaceifnecessary.
• Grease wheels.Use one pump only of white
lithiumgrease.Moregreasethanrecommended
maypushthesealsanddustcoversout,allowing
dustandotherforeignmaterialstopenetratethe
bearings, thus shortening their life, as well as
allowinggreasetodropfromthewheelstothe
oor.
Monthly Maintenance – (every
80 hours of operation)
• Perform all Daily and Weekly Maintenance
services.
• Consult engine owner’s manual for the
following:
»Torque head bolts.
»Check valve clearance.
»Torque valve cover bolts.
»Inspect spark plugs. Replace if necessary.
»Remove engine shroud and clean cooling
ns.
Quarterly Maintenance – (every
250 hours of operation)
• Performallmonthlymaintenanceitems.
• HaveenginecheckedbyanAuthorizedService
Center-includingemissionscheck.
Propane Fuel System
Repairs and adjustments to the fuel system can
onlybemadebyanauthorized,properlytrainedand
certiedservicetechnician.Improperadjustments
will cause increased toxic emissions of carbon
monoxide andmayresultincarbonmonoxide
Changing the Oil
1. Theenginemanufacturerrecommends10W30
or SAE30 motor oil.ATTENTION: Do not
over ll oil and never run engine with low oil
level.
2. Runengineforveminutestowarmtheoil.
3. Makesuremachineisonalevelsurface,with
padrestingontheoor.Placeacontainerunder
thedrainandopentheoildrainvalve.Allowoil
todraincompletely.
4. Close drain valve and add 1 quart of 10W30
or SAE30 motor oil.Check level and add if
necessary.
5. Replace oil-ll cap assembly.Hand tighten
only.
Checking the Oil Level
Whencheckingoil,removedipstick,wipeclean,
and then reinsert the dip stick into the engine.
Do not screw in for Kawasaki or Robin engines.
Removedipstickandobserveoillevelasindicated
on thedip stick.
Adjusting Belt Tension
Toolsrequired:
»9/16” (19 mm) open end wrench
»15/16” (24 mm) deep-well socket
1. Loosenmountingbolt ontopsideof machine
deckwhileholdingadjustingnutonunderside
of deck.NOTE: The mounting bolt must be
loosened before adjustment can be made.
2. Rotate adjusting nut counter clockwise with
sockettoapplytensiontobelt.
3. While holding the tension on the adjusting
nut,tightenthemountingboltonthetopofthe
deck.
4. Check belt tension by pinching belt together.
Beltshoulddepressonly½”(12mm).
ToOrderPartsCall1-888-702-5326-https://monsterfloorequipmentparts.com

Eagle Solutions, ©2008, Tracker Operator Manual Page #14
Eagle Solutions, ©2008, Tracker Operator Manual Page #15
Problem Cause Solution
Will not start No fuel
Dirt in fuel line
Blown head gasket
Engine overload
Dirty air cleaner
Faulty spark plug
Fuel system out of adjustment
Defective ignition
See engine owners manual for
servicing
NOTE: Only properly trained
Service Technicians should
adjust or repair fuel systems!
Hard to start No fuel
Dirt in fuel line
Engine overloaded
Dirty air cleaner
Faulty spark plug
Spark plug or head bolts loose
Blown head gasket
Timing, coil or valves need adjusting
Regulator needs adjustment
Insufcient vacuum
See engine owners manual for
servicing
NOTE: Only properly trained
Service Technicians should
adjust or repair fuel systems!
Lacks power Improper valve clearance
Dirt in fuel line
Faulty spark plug
Incorrect oil level
Worn rings
See engine owners manual for
servicing
NOTE: Only properly trained
Service Technicians should
adjust or repair fuel systems!
Odor of burned
rubber Belt out of adjustment See “Adjusting Belt Tension”
Engine overheats Incorrect oil level
Engine overloaded
Build up of dirt inside engine shroud
See engine owners manual for
servicing
High fuel
consumption Faulty spark plug
Dirty air cleaners
Improper fuel system adjustment
Clean, adjust/replace spark plug
See engine owners manual for
servicing
NOTE: Only properly trained
Service Technicians should
adjust or repair fuel systems!
Engine stops
suddenly Out of fuel
Faulty spark plug
Pad not centered on pad driver
Incorrect pad size
Low oil
Change fuel cylinders
Clean, adjust/replace spark plug
Center pad on pad holder
Replace with proper pad
Add oil (see Changing Oil notes)
Excessive vibration Loose bolts on engine or deck
Pad not centered or damaged pad
Incorrect oil level
Engine overloaded
Dirty lters
Faulty spark plug
Inspect and tighten all bolts
Center or replace pad(s), tighten
Check and adjust oil level
See engine owners manual for
servicing
Clean or replace lters
Check adjust/replace spark plug
Troubleshooting
ToOrderPartsCall1-888-702-5326-https://monsterfloorequipmentparts.com

Eagle Solutions, ©2008, Tracker Operator Manual Page #14
Eagle Solutions, ©2008, Tracker Operator Manual Page #15
Subjecttotheconditionsandexpectationsstated
inthiswarranty,wewarrantourproductstobefree
from defects in material and workmanship, under
normal use and service, for the periods listed,
warrantedtotheoriginalpurchaser.Atanytime
withintheperiodslisted,thecompanywillfurnish
Eagleproductreplacementparts.Suchreplacement
parts will be furnished to the original owner
and charged, including transportation charges,
through an authorized Eagle distributor or service
organization, FOB the factory (Georgia).ONLY
whentheoriginalpartisreturnedwithin30daysand
isfoundtobedefective,willtheownerbecredited
forthecostofthereplacementpartand/orlabor(as
speciedintheWarranty Flat Rate Schedule) and
normal transportation charges.Parts replaced or
repaired under the warranty are fully guaranteed
for the remainder of the original warranty period.
Any implied warranty granted under State Law,
including warranties or merchantability or tness
for a particular purpose are limited to duration
to the express warranty granted hereunder.The
manufacturer or manufacturer’s authorized
representativeinnoeventshallbeliablefordirect,
indirect, incidental or consequential damage.
Abuseandfailuretoproperlymaintainenginewill
voidwarranty.Properenginemaintenanceincludes
lter and oil changes as described in the engine
manufacturer’s operator manual.See information
on thePlannedMaintenanceKitattheendofthe
manual.Somestatesdonotallowlimitationsonhow
longanimpliedwarrantylastsand/ordonotallow
the exclusion or limitation of incidental damages,
so the above limitations and exclusions may not
apply to you.“THIS WARRANTY IS IN LIEU
OFANY OTHER WARRANTIES, EXPRESSED
OR IMPLIED, INCLUDING ANY IMPLIED
WARRANTY OF MERCHANTABILITY,
FITNESS FORA PARTICULAR PURPOSE, OR
OTHERWISE.UNDER NO CIRCUMSTANCES
WILLTHESELLERBELIABLEFORANYLOSS,
DAMAGE, EXPENSE, OR CONSEQUENTIAL
DAMAGE ARISING IN CONNECTION WITH
USE, OR INABILITY TO USE, SELLER’S
PRODUCTS.”
We reserve the right to make changes and
improvementsto ourequipmentwithoutnotice.
Pleasemakesuretorecordthisinformation.This
informationwillbe necessarytoretrieve warranty
informationinthefuture.
Datepurchased:_______________________
ModelNumber:_______________________
SerialNumber:_______________________
90 days 1 Year 2 Years 3 Years
Belts, Brushes, Choke Cables, Clutches, Electrical Components X
Filters, Hand Grips, Hoses, Pad Drivers, Starters, Switches X
Throttle Cables, Wheels X
Emissions Shutdowns, Gearboxes, Hydraulic Motors X
Lockoffs, Mufers, Fuel Valves X
Engines: (Warranty covers Manufacturer’s defects only) X
Robin EH65 22hp X
Kawasaki KH541 17 hp X
Kawasaki FH381 13 hp X
Honda GXV390 13 hp X
Frames, Handles, Pulleys, Regulators X
Tanks (LP) X
Tank Valve X
Warranty Information
ToOrderPartsCall1-888-702-5326-https://monsterfloorequipmentparts.com

Eagle Solutions, ©2008, Tracker Operator Manual Page #16
Eagle Solutions, ©2008, Tracker Operator Manual Page #17
Service Pre-Approved by Eagle
1. CallEagleCustomerServicetoleaclaim.For
warrantyrequestsonequipmentyouwillneed
toprovidetheEngineSerialNumber,Machine
Serial Number, Model Number, and Proof of
Purchase(i.e.invoice).
2. You willbedirectedtotheappropriateservice
organization based on where your business is
located.
3. The service organization will arrange an on
site visit or specify the location to bring your
equipmentforrepair.
4. You mayberequiredtopaytravelchargesand
servicefeesinadvanceofanonsitevisit.The
amount of these charges may vary depending
upon the service organization and your
geographiclocation.
5. The service technician will perform the
necessary diagnostic and repair work and
contact Eagle Solutions to determine if the
defective component(s), travel charges, and
service fees will be covered under the Eagle
SolutionsWarrantyPolicy.
6. The service technician will contact Eagle
Solutionstoacquirethenecessaryreplacement
partsandanRGAnumberforthereturnofthe
defective components.A copy of this RGA
form will be faxed to you. (The RGA form
will specify the carrier to use for parts to be
returned).
7. EagleSolutionswillshipthereplacementparts
toyouortheservicerep.andinvoiceyouatfull
valuealongwithrelatedfreightcharges.
8. Uponreceiptofthereturnedgoodsyouwillbe
creditedforthereplacementpartsinvoiceifthe
itemsarestillunderwarranty.Pleaseincludea
copyoftheRGAformwiththereturneditems.
9. Advance payment of travel and service fees
determined to be covered under the Eagle
SolutionsWarrantypolicywillbereimbursedby
theserviceorganizationinvolved.Ifwarranty
doesnotapply,chargeswillnotbereimbursed.
Service NOT Pre-Approved by
Eagle
1. CallEagleCustomerServicetoleaclaim.For
warrantyrequestsonequipmentyouwillneed
toprovidetheEngineSerialNumber,Machine
Serial Number, Model Number, and Proof of
Purchase(i.e.invoice).
2. You will also need to provide documentation
forallrepairrelatedcharges.
3. Yourclaimwillbereviewedtodetermineifit
iscoveredbyourwarrantypolicy.Ifapproved,
aReturnGoodsAuthorization (RGA) number
willbeissuedfordefectivepartsandanRGA
form will be faxed to you. (The RGA form
will specify the carrier to use for parts to be
returned).
4. We recommend that you place an order for
the replacement parts that are needed.These
willbeinvoicedtoyouatfullvaluealongwith
relatedfreightcharges.
5. Ifyourwarrantyclaimhasbeenapprovedand
an RGA number has been provided to you,
youwillbe credited forthereplacement parts
invoice upon receipt of the defective parts.
If the defective parts are not covered under
warrantynocreditwillbeissued.
6. Approvedtravelandservicecharges will also
becreditedtoyouuponreceiptofthedefective
parts.
Warranty Conditions
1. Approved warranty return items must be
receivedbyEagleSolutionswithin30daysof
theRGAdateinordertoreceivecredit.
2. A copy of the RGA form should be included
withtheitemsreturned.
3. Replacement parts orders will be shipped via
UPSorFedexGround.You willberesponsible
foranyupgradedorexpediteddeliverycharges.
These additional charges will not be covered
underwarranty.
4. Warrantytravelislimitedto60milesandapplies
onlytoclaimsmadewithin30daysofthedate
ofpurchase.Ourmileagereimbursementrateis
$0.35permile.(Rateissubjecttochange).
5. LaborhoursaresubjecttotheEagleSolutions
Warranty Flat Rate Chart.(Rates are subject
tochange).
6. Warrantytravelandservicefeesmaybedenied
ifnotpre-approvedandperformedbyanEagle
SolutionsAuthorizedServiceOrganization.
Warranty Contacts
CustomerService800.633.0519oremail:
customerservice@eagleoorsolutions.com.
Instructions and Conditions for Warranty Reimbursement
ToOrderPartsCall1-888-702-5326-https://monsterfloorequipmentparts.com

Eagle Solutions, ©2008, Tracker Operator Manual Page #16
Eagle Solutions, ©2008, Tracker Operator Manual Page #17
Job Description Labor
Hours
Allowed
Job Description Labor
Hours
Allowed
TUNE UP & ADJUSTMENT PISTON & CRANKSHAFT
COMPRESSION MEASUREMENT (ALL) 0.4 PISTON OR RING SET (1 CYCL) 2.1
VALVE CLEARANCE ADJUSTMENT (ALL) 0.6 PISTON OR RING SETS (ALL) 2.9
VALVE CLEARANCE ADJUSTMENT (1 CYL) 0.3 CRANKSHAFT 3.3
GOVERNOR ADJ (Includes low idle & high speed adj) (ALL) 0.3 CONNECTING ROD (1CYL) 2.1
LOW IDLE & HIGH SPEED ADJUSTMENT (ALL) 0.2 CONNECTING RODS (ALL) 2.9
CARB CLEANING (ALL) 0.7 CRANK/OR CAMSHAFT OIL SEAL (PTO SIDE) 0.9
CYLINDER HEADS, VALVES & CAMSHAFT CRANK/CAMSHAFT OIL SEAL (FLYWHEEL SIDE) 0.8
CYLINDER HEAD COVER OR GASKET (1 CYL) 0.2 RECOIL STARTER & GOVERNOR
CYLINDER HEAD COVERS OR GASKETS (ALL) 0.3 RECOIL STARTER ASSY 0.1
CYLINDER HEAD (1 CYL) 1.7 REEL, SPRING OR ROPE 0.3
CYLINDER HEADS (ALL) 2.2 GOVERNOR ASSY OR SLEEVE 1
CYLINDER HEAD GASKET (1 CYL) 1.3 GOVERNOR SHAFT OR OIL SEAL 0.9
CYLINDER HEAD GASKETS (ALL) 1.8 GOVERNOR ARM 0.3
VALVE AND/OR SPRING (1 VALVE OR SPRING) 1.5 CONTROL PANEL ASSY 0.3
VALVE AND/OR SPRINGS (2 VALVES OR SPRINGS) (1 CYL) 1.6 CARB, FUEL PUMP AND FUEL TANK
VALVES AND/OR SPRINGS (ALL) 2.2 CARBURETOR 0.5
VALVE LAPPING OR VALVE GUIDE (1 VALVE, 1 CYL) 1.6 CARB HOLDER OR INTAKE MANIFOLD 0.6
VALVE LAPPING (2 VALVES, 1 CYL) 1.8 CHOKE VALVE(S)/THROTTLE VALVE(S) (INCLUDES
CARB R&R) 0.6
VALVE LAPPING OR VALVE GUIDES (ALL) 2.6 MAIN JET(S) FLOAT OR VALVE (INCLUDES CARB R&R) 0.6
CAMSHAFT 1.3 FLOAT CHAMBER GASKET 0.3
ROCKER ARM OR PUSH ROD (1 ARM OR ROD) 0.4 SOLENOID VALVE OR FUEL CUT VALVE 0.3
ROCKER ARMS OR PUSH RODS (ALL) 0.6 FUEL TUBE (TO CARB) 0.2
CYLINDER/CRANKCASE & OIL PUMP DIAPHRAGM FUEL PUMP 0.2
CYLINDER BORING & HONING (1 CYL) 4.8 FUEL FILTER 0.1
CYLINDER BORING & HONING (ALL) 5.3 IGNITION, COOLING & STARTER MOTOR
CRANKCASE OR MAIN BALL BEARINGS 4.1 ENGINE FLYWHEEL 0.7
BREATHER, BREATHER COVER OR REED VALVES 1CHARGING COIL OR STARTER 0.9
CRANKCASE COVER 1.2 IGNITION COIL (1) 0.5
CRANKCASE COVER GASKET 0.8 IGNITION COILS (ALL) 0.7
OIL FILTER (CARTRIDGE) OR OIL DRAIN PLUG 0.1 SPARK PLUG (1) 0.1
OIL PUMP 1.1 SPARK PLUGS (ALL) 0.2
OIL PRESSURE RELIEF VALVE 1VOLTAGE REGULATOR (REGULATOR/RECTIFIER) 0.2
OIL FILTER SCREEN (INTERNAL) 0.9 COOLING FAN 0.3
OIL DRAIN PLUG OR GASKET, OR OIL FILTER/
OIL LEVEL DIPSTICK TUBE 0.1 COOLING FAN HOUSING 0.2
OIL PRESSURE SWITCH 0.2 UPPER ENGINE SHROUD 0.2
AIR CLEANER/MUFFLER LOWER ENGINE SHROUD 0.2
AIR CLEANER CASE 0.2 STARTER MOTOR ASSY 0.3
AIR CLEANER ELEMENT OR COVER 0.1 STARTER BRUSH(ES) (INCLUDES STARTER (R&R)) 0.5
MUFFLER OR HEAT COVERS 0.2 MISC
EXHAUST PIPE(S) OR GASKET(S) 0.3 DIAGNOSIS 0.5
Engine Warranty Flat Rate Chart
ToOrderPartsCall1-888-702-5326-https://monsterfloorequipmentparts.com

Eagle Solutions, ©2008, Tracker Operator Manual Page #18
Eagle Solutions, ©2008, Tracker Operator Manual Page #19
Job Description Labor
Hours
Allowed
Job Description Labor
Hours
Allowed
MISC FUEL SYSTEMS
DIAGNOSIS 0.5 CHOKE CABLE/THROTTLE CABLE 0.25
CLAMPS 0.1 FUEL HOSE 0.25
FRAME REGULATOR/LOCKOFF 0.5
DC BRUSH SKIRT 0.25 ENGINE
DECK 1.5 REPLACEMENT 1.5
FLEXIWALL SHIELD 0.25 *See Engine Warranty Flat Rate Chart
FLEXIWALL SHIELD MOUNT 0.5 EXHAUST SYSTEM
HANDLE 0.5 MANIFOLD 0.5
ELECTRICAL SYSTEM MUFFLER / MOUNTING BRACKET 0.25
BATTERIES/BATTERY BOXES 0.25 DRIVE SYSTEM
KEY SWITCH 0.25 BELTS 0.25
WIRING HARNESS 0.5 CLUTCHES 0.5
PAD DRIVERS/STRIP BRUSHES 0.25
PULLEYS 0.25
TENSIONERS 0.25
Warranty Flat Rate Chart
ToOrderPartsCall1-888-702-5326-https://monsterfloorequipmentparts.com

Eagle Solutions, ©2008, Tracker Operator Manual Page #18
Eagle Solutions, ©2008, Tracker Operator Manual Page #19
ToOrderPartsCall1-888-702-5326-https://monsterfloorequipmentparts.com

Eagle Solutions, ©2008, Tracker Operator Manual Page #20
Keep your engine running smooth
Easy engine starting
Extends life of engine
Complete kit for maintenance
Planned Maintenance Kits from Eagle will help your engine run longer and cleaner.
Without proper maintenance you run the risk of increased emissions and loss of
warranty. Don’t let that happen to you. Give your machines some fresh breath by
replacing the recoil dust lter, the carburetor air lter element, carburetor foam pre-
lter and clean oil and lter today.
Kit includes:
2 quarts of oil
1 oil lter
1 recoil dust lter
1 carburetor air lter element
1 carburetor foam pre-lter
Engine PM Kit Part #
Honda 680426
Robin 680508
Kawasaki - 13hp 680713
Kawasaki - 17hp 680428
Features:
Planned
Maintenance Kit
Don’t
Forget
P.O. Box 350, 100 Eagle Parkway
Adairsville, GA 30103
800.633.0519 or 770.773.3875
Fax 770.773.9903
www.EagleFloorSolutions.com
email - customerservice@
eagleoorsolutions.com
Solutions
ToOrderPartsCall1-888-702-5326-https://monsterfloorequipmentparts.com
This manual suits for next models
3
Table of contents
Popular Scrubber manuals by other brands
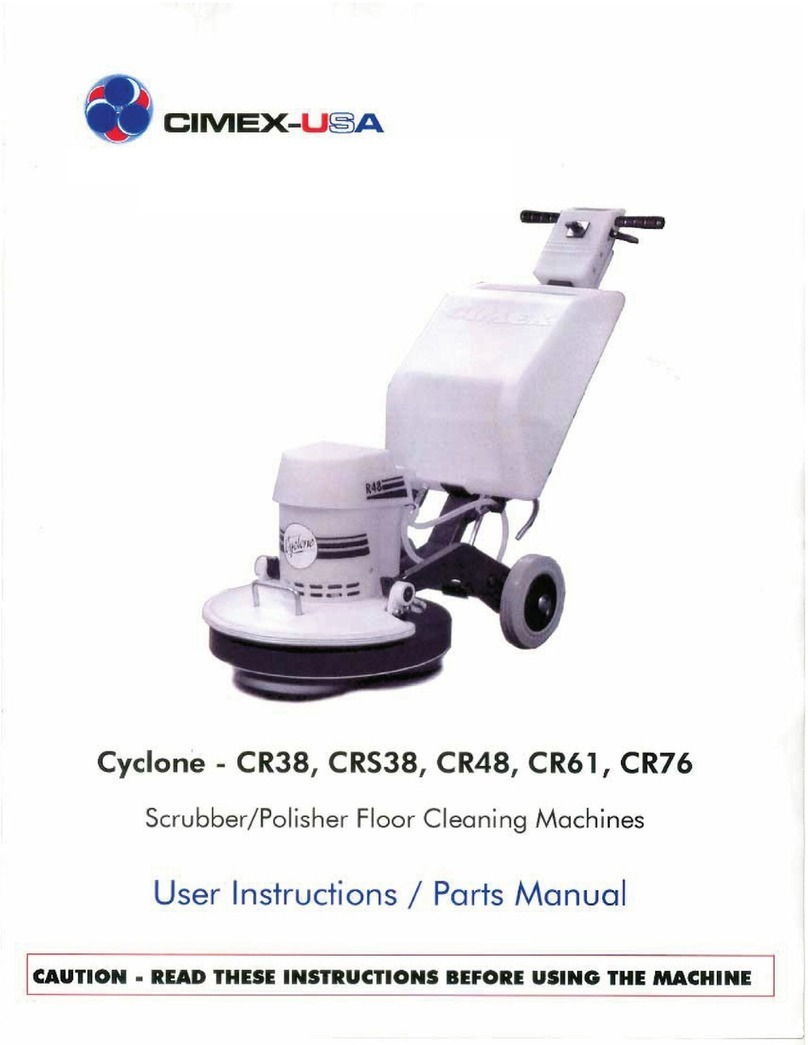
cimex
cimex Cyclone CR38 User instructions
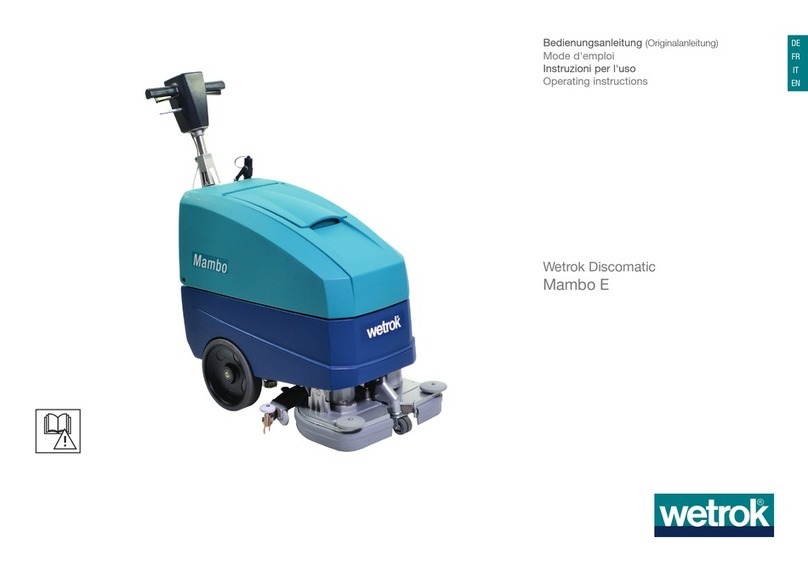
Wetrok
Wetrok DISCOMATIC MAMBO E operating instructions

Clemas & Co
Clemas & Co TENNANT T500 Operator's manual
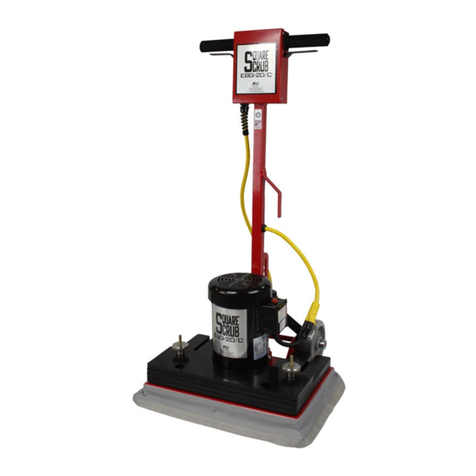
Square Scrub
Square Scrub Versality 2 EBG Series owner's manual

Miele
Miele DAD 4840 Operating and installation instructions
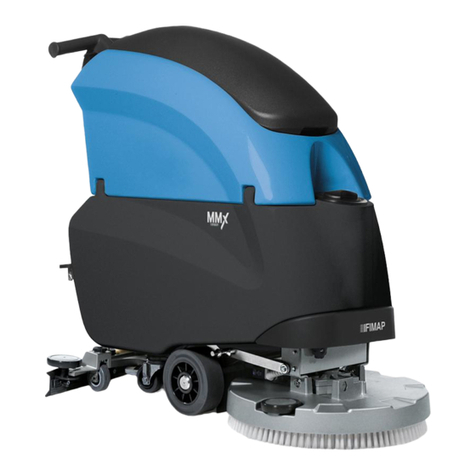
Fimap
Fimap MMX 43B Use and maintenance manual