electrogas MB User manual

elektrogas.com
MB
MZ
Servomotors
for butterfly valves VF, VFH
E
E
1
5
7
-1209

ELEKTROGAS – MANUALE TECNICO
2-10
MB
MZ
Servomotors
Contents
Description ………………………………………….. 2
Features ……..……………………………..……….. 2
Application .……..........................…………………. 3
Technical specifications .………………….……….. 4
Operation MB ........................................................ 5
Operation MZ ........................................................ 5
Manual mode
...................................................
6
Automatic mode
7
DIP chart
x
Operating states
x
Ordering information …..…………………………… x
Standards and approvals ………………………….. x
Description
Servomotors MB/MZ are designed to operate VF and VFH butterfly valves, used in three-stage
control (MB) or with electronic positioning control (MZ), of gas and air flow in combustion
processes.
Features
DC motor with multi-stage spur gearbox.
Status LEDs and position indicator of the motor visible externally.
Provided with four cams with double adjusting screw (adjustment tool included in the housing).
Two switches for manual adjustment of the position.
Two switches to memorize minimum and maximum position (MZ).
Analogue input and output signals for electronic positioning (MZ).
Very high positioning precision.
The same unit is suitable for 230-110-24V.
Adjustable opening time from 7 up to 60s.
Provided with connection for external programming terminal (MZ).
Its sturdy and functional design allows a fast and easy installation, and it is practically free of
maintenance.
WARNING
This control must be installed in compliance with the rules in force.

ELEKTROGAS – MANUALE TECNICO
3-10
Functioning and
application
- In case of combustion process being
regulated by combustive air
modulation, VF valves with servomotor
can be used, coupled to another
butterfly valve manually operated
(available graduated scale and locking
screw) to setup high-fire rate of the
burner.
- In case of combustion process with
excess of air or gas, VF butterfly valve
can be used, coupled to a Lambda
sensor for ratio correction.
- In case of combustion process with
pre-heated air, VFH butterfly valve can
be used MZ servomotor.
WARNING
Location and mode of installation must be in compliance with local rules in force.
VF
.
.
MZ
Fig. 1
Fig. 2
Fig. 3
VF..MZ
VFH..MZ
VF..MB

ELEKTROGAS – MANUALE TECNICO
4-10
Technical
specification
Tab. 1
Actuator type MB basic adjusting position operated by cams
MZ advanced adjusting position by analogue signals
Overall dimensions See fig. 4
Weight 2 Kg
Rotation angle 0 / 90°
Precision of positioning ±0.25°
Ambient temperature -15°C / +60°C
Voltage rating 230VAC 50/60Hz
110VAC 50/60Hz
24V AC/DC
Voltage tolerance -15% / +10%
Power consumption 5 W
Enclosure IP65 (EN 60529)
Cable gland 2x ISO 20 (EN 50262)
Torque
(=Holding torque) 5 Nm
Operating time
(0 - 90°) From 7s up to 60s
(adjustable)
Outputs (MB) Potentiometer 2,5 KΩ
ΩΩ
Ω
Analogue inputs (MZ) Signal type
Overload max.
Load impedance
0-10V
11Vdc
100KΩ
ΩΩ
Ω
0-20mA
22mA
250Ω
ΩΩ
Ω
4-20mA
22mA
250Ω
ΩΩ
Ω
Analogue outputs (MZ) Signal type
Load max.
Output impedance
0-10V
5mA
0,1Ω
ΩΩ
Ω
0-20mA
500Ω
ΩΩ
Ω
1MΩ
ΩΩ
Ω
4-20mA
500Ω
ΩΩ
Ω
1MΩ
ΩΩ
Ω
Fig.4

ELEKTROGAS – MANUALE TECNICO
5-10
Operation
MZ
This unit is designed for all applications that require high precision control of rotary movement
between 0° and 90°. Inside the compact servo drive housing there is a DC electric motor, a
gearbox and a control unit with a 16-bit microcontroller.
Fig.5
A Main terminal board J Warning LED2 (red)
B Analogue signals K Status LED3 (green)
C DIP switch L MIN push button (B4)
D Cams (C1..C4) M Hysteresis control
E Closing push button (B1) N Terminal (T1)
F Automatic/ Manual switch (S1) O Direct motor driving
G Opening push button (B2) P Position indicator
H Manual operation LED1 (green) Q Cams adjustment tool
I MAX push button (B3) R DC motor
The shaft rotation angle can be controlled via analogue signals and any angle of rotation can be
freely selected within the defined operating range. The current position can be monitored via
output analogue signals. The hysteresis can be adjusted with a potentiometer in order to
suppress interferences in the input signal.
MZ servomotor is provided with buttons for manual adjustment of the position and for
memorization of minimum/maximum limits. Some LEDs visible even externally, show the current
status of the unit (e.g. manual operation, memorization, errors, etc.).
The most of settings can be made with a DIP switch on board (e.g. selection of analogue
signals, sense of rotation, behaviour in the event of cable break, two-point operation). In the
back side is also available a connection for the external programming terminal. It is useful to set
advanced features of the unit, to monitor some parameters (e.g. temperature, errors) or to
upload new software releases.
On the back side is located a socket to connect a 12VDC power supply and perform direct
motor driving, by-passing the control unit (e.g. if control unit does not work and the valve must
be operated anyway).
The servomotor is also provided with four cams continuously adjustable: two cams are used to
define the limits of the operating range and safeguarded the unit; the others are available for
controlling external devices.

ELEKTROGAS – MANUALE TECNICO
6-10
Fig.6
Manual mode
For a simplified commissioning, the actuator can be operated manually. The manual mode is
useful to determine the operating positions for the process, such as the High/Low fire positions.
To enter in the manual mode press the switch S1 downwards (LED1 lights up). Now it's possible
to move the valve toward the MAX. position (counter clockwise rotation seen from the top), by
pressing the push button B2, and to move the valve toward the MIN. position (clockwise rotation
seen from the top), by pressing the push button B1 (factory setting provides the cams C1 and
C2 at 0°and 90°). The initial rotating speed is 0. 25 RPM, this lets operator perform an accurate
adjustment of position. If the button is pressed for more than 3 seconds the rotating speed shifts
to 1 RPM.
Setting of the MIN and MAX positions
In manual mode it's possible to memorize current position as MIN (MAX) by pressing button B4
(B3) for more than 3 seconds (shorter pressing are not considered). When the position is
memorized, LED2 lights up and the button may be released.
MAX position can not be lower than MIN position memorized (and vice versa). In this case the
position won't be memorized and an alarm will go up (see "Alarms Chart") until a new proper
position is memorized.
Running time setting (continuous)
With a proper software configuration made by terminal T1, running time can be chosen also on
field. By means of terminal T1, changing the parameter
RUN_MODE
from 1 to 5 as follows:
RUN_MODE
1 Running time according to RUN_TIME parameter (default)
5 Running time may be adjust freely (manual mode)
Press both B3 and B4 buttons at the same time, for the time required (LED3 lights up). Running
time must be included between 7 s and 60 s, otherwise its value won't be memorized and an
alarm will go up (see "Alarms Chart") until a new proper time is memorized. A proper running
time is operative in automatic mode only.
Opening (B2)
Automatic
/
Manual (S1)
Closing (B1)
Setpoint
Output
0
N
230-
110V
COM
MIN
MAX
24V
N
Direct motor
driving
Terminal (T1)
Hysteresis
MIN (B4)
MAX (B3)
LED1
LED3
LED2

ELEKTROGAS – MANUALE TECNICO
7-10
Automatic mode
In the automatic mode the angular position corresponds to the input analogue signal provided
by a setpoint device. Factory setting allows full range of operation (0-90°) but, as above
described, MIN and MAX position can be set within this range in manual mode.
An output analogue signal proportional to angular position is also provided.
Both input and output signals can be chosen between 0-10V, 0(4)-20mA setting the proper DIP
switch configuration (see "DIP Chart").
Behaviour without input signal (4-20mA)
In the event of cable break or any other situation that a missing of input signal can happen,
servomotor has to move in a defined mode. It's possible to set three different behaviour modes
by the DIP switch: open position, closed position and stop (see "DIP Chart").
2-point control
The servomotor can work as 2-point device by means of an external relay, setting the proper
DIP switch configuration (see "DIP Chart"). Main power supply must be also provided.
Fig.7
If an input signal V is applied to relay terminals, the actuator opens. If no input signal is applied
to relay terminals, the actuator closes.
Hysteresis and Filtration
The input analogue signal is processed internally with a resolution of 12 bit (corresponding to
0.025%). This allows, with a 4-20mA input signal for example, to detect a change of 0.005 mA
(hysteresis).
If the input signal fluctuations are too greatly (e.g. due to noise), use of high resolution causes
constant corrections of the position. In this case the hysteresis may be increased up to 0.5 mA
(resolution is reduced down to 2.5%).
The analogue input is sampled every 1 ms (sampling rate) and a mean value is generated over
0.1 s. This filtering can be prolonged by the terminal T1 up to 1 s, but this also prolongs the
response time to a change at the analogue input.
Running time setting
Factory setting for running time is 30 s. However, it can be modified in the same unit by means
of terminal T1, changing the parameter
RUN_TIME
as follows:
RUN_TIME Time to run 0-90°
0 7 s
1 15 s
2 30 s (default)
3 60 s
Moreover the parameter
RUN_MODE
must be set as follows:
RUN_MODE
1 Running time according to RUN_TIME parameter (default)
5 Running time may be adjust freely (manual mode)
Remote Control Unit

ELEKTROGAS – MANUALE TECNICO
8-10
DIP chart
Input analogue signal
1 2 3 4 5 6 7 8 9 10
ON
OFF
0-10V
1 2 3 4 5 6 7 8 9 10
ON
OFF
0-20mA
1 2 3 4 5 6 7 8 9 10
ON
OFF
4-20mA
Output analogue signal
1 2 3 4 5 6 7 8 9 10
ON
OFF
0-10V
1 2 3 4 5 6 7 8 9 10
ON
OFF
4-20mA
(0-20mA) programmable by means of T1
Behaviour without input
signal (4-20mA)
1 2 3 4 5 6 7 8 9 10
ON
OFF
Open position
1 2 3 4 5 6 7 8 9 10
ON
OFF
Closed position
1 2 3 4 5 6 7 8 9 10
ON
OFF
Stop
Sense of rotation
1 2 3 4 5 6 7 8 9 10
ON
OFF
Right
1 2 3 4 5 6 7 8 9 10
ON
OFF
Inverted
2-point control
1 2 3 4 5 6 7 8 9 10
ON
OFF
2-point control activated

ELEKTROGAS – MANUALE TECNICO
9-10
Operating state
Normal operation
Tab.x
Nr. Status LED3
GREEN Warning LED2
RED State description
1
Fast flashing OFF Automatic mode
2
Slow flashing OFF Manual mode
3
Slow flashing Lighted up when
position has been
memorized
Setting of the MIN and MAX positions
(Manual mode)
4 Slow flashing Permanent light
while buttons are
pressed
Running time setting
(Manual mode)
Fast flashing: 4 times per second Slow flashing: 1 time per second
Alarms chart Tab.x
Error
Nr. Status LED3
GREEN Warning LED2
RED Alarm type Description Cause
1 1 Flashing Permanent light Warning Input signal is missing
(4-20mA) Cable break
2 2 Flashings Permanent light Warning Invalid position Operator has attempted to
memorize an invalid position
(e.g. MIN>MAX)
3 3 Flashings Permanent light Warning Invalid running time Operator has attempted to
memorize an invalid running time
(out of 7-60 s range)
4 4 Flashings Permanent light Warning Too many changes
of direction Hysteresis is too small
5 5 Flashings
Permanent light Warning Motor overload Valve is blocked, direction of
rotation is wrong
6 Permanent light
Permanent light Fault Unit defective Control unit defective, motor
defective, internal error
n-Flashing (2 per second) followed by a longer pause (2 seconds)

ELEKTROGAS – MANUALE TECNICO
10-10
Product
identification
Tab.2
M Z
(*)
MB MZ
Model
Type
B= basis
Z= advanced
Running time
7 s
15 s
30 s
60 s
7...60 s continuous
Voltage
A= 230VAC 50/60Hz
B= 110VAC 50/60Hz
C= 24VAC/DC
Inputs
0-10 V
0-20 mA
4-20 mA
Outputs
Feedback potentiometer
0-10 V
0-20 mA
4-20 mA
For more information about butterfly valves
see their technical sheets.
Standard
Optional
Programmable (T1)
Not available
(*) Specification is omitted if does not match any requirement
Manufacturer reserves the right to update or make technical changes without prior notice.
Standards and
approvals
The actuators meet current European approval requirements regarding electrical safety:
- Electromagnetic Compatibility (2004/108/CE)
- Low Voltage Directive (2006/95/CE)
Quality Management System is certified according to UNI EN ISO 9001 and the monitoring is
carried out by the notified body:
Kiwa Gastec Italia Spa.
Via Treviso, 32/34
I- 31020 San Vendemiano (TV)
This manual suits for next models
1
Table of contents
Popular Servo Drive manuals by other brands
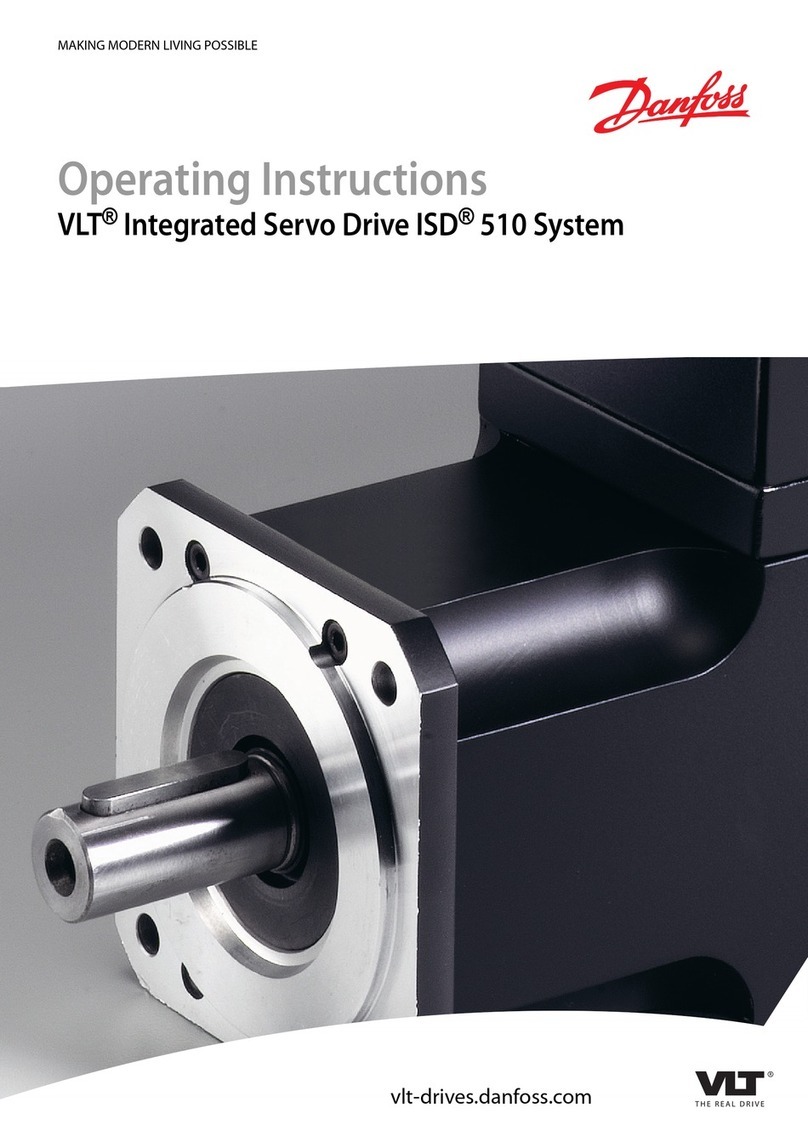
Danfoss
Danfoss VLT Integrated Servo Drive ISD 510 System operating instructions
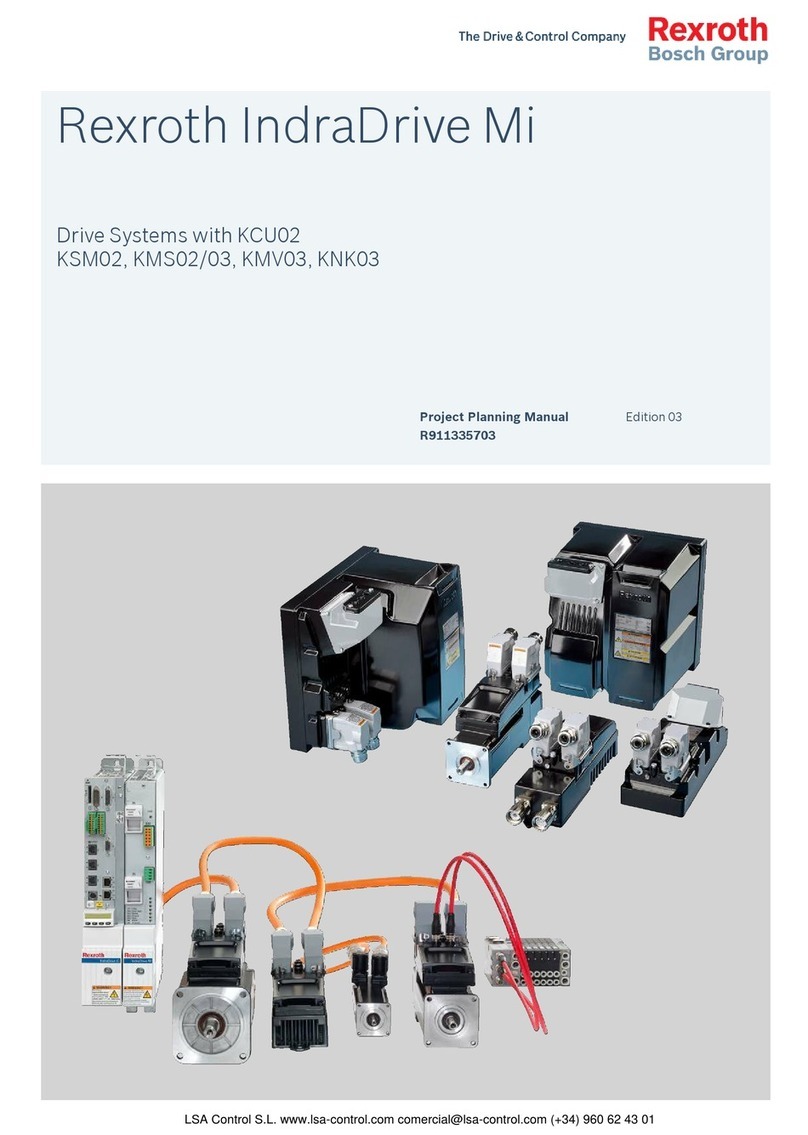
Bosch
Bosch Rexroth IndraDrive Mi Project planning manual
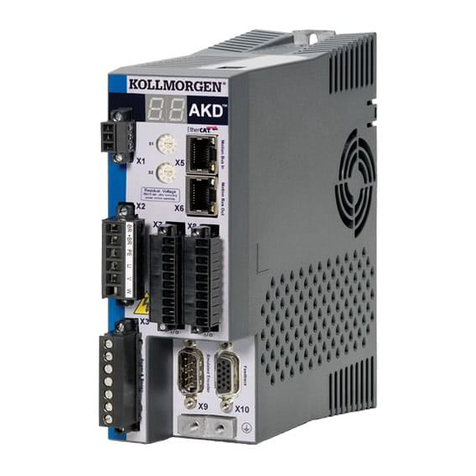
Kollmorgen
Kollmorgen AKD-CC installation manual
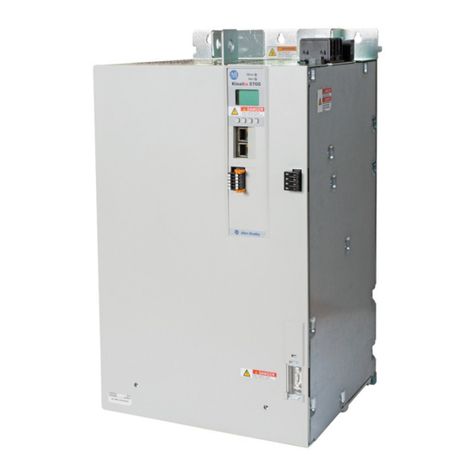
Rockwell Automation
Rockwell Automation Allen-Bradley Kinetix 5700 Series user manual
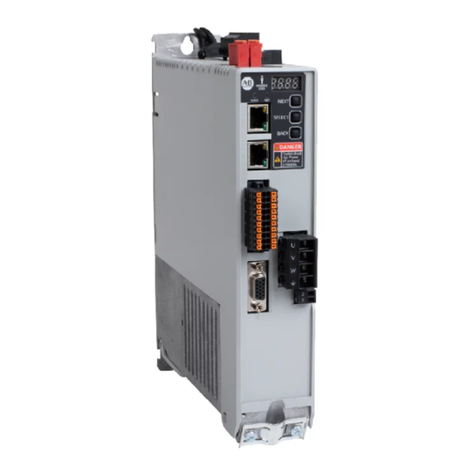
Rockwell Automation
Rockwell Automation Allen-Bradley Kinetix 5300 user manual
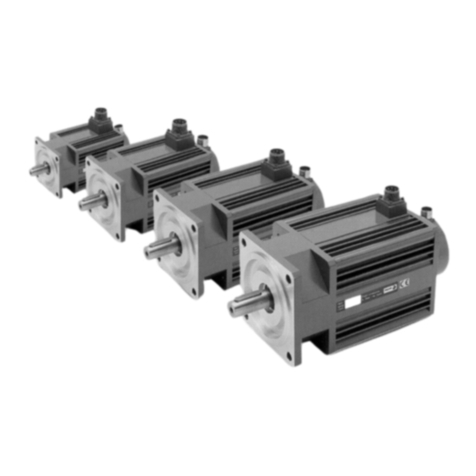
Fagor
Fagor ACS Series manual