Elmo SSA Series Installation instructions

1
SSA - Rev 6/98
Rev 6/98

2
SSA - Rev 6/98
SSA - SAFETY INSTRUCTIONS
Read this page carefully before installation and use of the instrument, and
follow all instructions in section 6 of Installation Procedures for safe
installation of this product.
INTRODUCTION
The following clauses contain information, cautions and warnings which must be
followed to ensure safe operation and to retain the instrument in a safe
condition.
As this product is intended for incorporation into a machine or end-product,
the end product must comply with all safety aspects of the relevant requirements
of the European Safety of Machinery Directive 89/392/EEC as amended, and with
those of the most recent versions of standards EN60204-1 and EN292-2 at least.
Installation, adjustment, maintenance and repair of the instrument shall be
carried out only by qualified personnel.
WARNINGS
Any removal from the structure or removal of parts, except those to which
access is permitted, is likely to expose live parts and accessible terminals
which can be dangerous to live. If afterwards any adjustment, maintenance or
repair of the opened instrument under voltage is inevitable, it shall be carried
out only by a qualified person who is aware of the hazard involved.
The instrument shall be disconnected from all voltage sources before it is
opened (for service method).
Any interruption of the protective earth conductors inside the instrument, is
likely to make the instrument dangerous.
Components which are important for the safety of the instrument, may only be
renewed by components obtained through Elmo service organization.
Before switching on, ensure that the instrument has been installed in
accordance with the Installation Instructions.
Maximum DC supply according the types described in the operating manual.

3
SSA - Rev 6/98
How to use this manual - Flow Chart
The SSA amplifier is designed for OEM applications. It enables the user to
adjust the amplifier for various types of motors and to save valuable adjusting
time in repetitive applications.
Use the following flow chart in order to determine the chapters that you should
read. If you are a new user of the SSA, you should read chapters 1-4 which will
familiarize you with the product.
Read chapter 5.1
Read chapter 6 - Installation
Read chapter 7.1 - Start-Up
Read chapters
1,2,3,4
Familiar with the SSA ? no
no
Read
7.3
Brush Tacho ?
Read
7.2
Read chapter 8 - Adjustments
Read chapter 9 - Summaries
no
Using SIB-SSA interface ?
Terminals
Read chapters 5.1+5.2 Terminals
Armature voltage feedback ? no
(Current mode)

4
SSA - Rev 6/98
TABLE OF CONTENTS
1. DESCRIPTION..........................................................................................................................7
2. TYPE DESIGNATION...............................................................................................................8
3. TECHNICAL SPECIFICATIONS...............................................................................................8
4. OPERATION OF THE SERVO CONTROL.............................................................................10
4.1 Inputs ..............................................................................................................................................................................10
4.2 Velocity mode..................................................................................................................................................................11
4.2.1 Velocity control using armature voltage feedback.......................................................................................................12
4.3 Current mode..................................................................................................................................................................12
4.4 Current loop....................................................................................................................................................................12
4.5 Current limits .................................................................................................................................................................12
4.5.1 Time dependent peak current limit.............................................................................................................................13
4.6 Protective functions.........................................................................................................................................................14
4.6.1 Short circuit protection ..............................................................................................................................................14
4.6.2 Under/Over voltage protection ...................................................................................................................................14
4.6.3 Temperature protection..............................................................................................................................................14
5. TERMINAL DESCRIPTION ....................................................................................................17
5.1 Terminals of the basic SSA.............................................................................................................................................17
5.2 Terminals for SIB-SSA...................................................................................................................................................19
6. INSTALLATION PROCEDURES............................................................................................20
6.1 Mounting.........................................................................................................................................................................20
6.2 Wiring.............................................................................................................................................................................20

5
SSA - Rev 6/98
6.3 Load inductance..............................................................................................................................................................21
6.4 DC power supply ............................................................................................................................................................21
6.5 Wiring diagrams.............................................................................................................................................................23
7. START - UP PROCEDURES ..................................................................................................28
7.1 Common procedures for all amplifiers types.................................................................................................................28
7.1.1 Inhibit logic...............................................................................................................................................................28
7.1.2 Velocity mode............................................................................................................................................................30
7.1.3 Current mode.............................................................................................................................................................30
7.1.4 Static current limits ...................................................................................................................................................31
7.2 Velocity control using tachogenerator feedback............................................................................................................32
7.3 Velocity control using armature voltage feedback.........................................................................................................32
8. AMPLIFIER ADJUSTMENT AND DIAGNOSTICS..................................................................34
8.1 Balance adjustment ........................................................................................................................................................34
8.2 Verifying the static current limits..................................................................................................................................34
8.3 External Current Limit (ECL) adjustment....................................................................................................................35
8.4 Adjustment of the IxR compensation.............................................................................................................................35
8.5 Response adjustment (Velocity mode only)....................................................................................................................36
9. TABLES AND SUMMARIES ...................................................................................................38
9.1 Adjusting trimmers.........................................................................................................................................................38
9.2 LED diagnostics..............................................................................................................................................................38
APPENDIX A - RESPONSE ADJUSTMENT - CURRENT LOOP................................................39
SERVICE CENTERS AND WARRANTY......................................................................................44

6
SSA - Rev 6/98
1
1
1.
.
.
D
D
De
e
es
s
sc
c
cr
r
ri
i
ip
p
pt
t
ti
i
io
o
on
n
n
The SSA is a miniature PWM servo amplifier designed for DC servo motors. It
utilizes power MOSFETs which contribute to its high efficiency and compact
design. The SSA is constructed from two PCBs mounted on a heat sink plate. The
lower board contains the power switching transistors which drive the motor,
terminals for the power stage, the switch mode power supply and the protection
logic. The upper PCB contains the control logic, terminals for the control stage,
adjusting trimmers and indication LED's.
Standard features
* Four quadrant operation allows motor acceleration and deceleration under power
in both CW and CCW directions.
* Internal DC to DC converter allows for operation from a single supply.
* Zero deadband.
* Excellent linearity.
* 2 inputs.
* Motor current monitor.
* Inhibit/fault indication (open collector).
* Remote control functions: Inhibit and CW/CCW disable.
* Adjustable compensation.
* Continuous and peak current limits.
* Input balance (offset) adjustment.
* External current limit adjustment.
* Operation in two velocity modes (Tacho or armature voltage feedback) or current
mode.
* LED diagnostics.
* Removable terminals for easy installation and service.
The amplifiers are fully protected against the following faults:
* Under/over voltage.
* Shorts between: outputs, output to ground.
* Excess temperature.

7
SSA - Rev 6/98
SIB-SSA
The SIB-SSA is an interface board for the SSA that is used to convert the SSA
flat ribbon connector to spring type Phoenix terminals. This board has the same
size as the SSA board and it can be assembled as an add-on card on top of any SSA
amplifier or as a separate panel mount unit.
The SIB-SSA is connected to the SBA amplifier via a 16 wires ribbon cable.
2
2
2.
.
.
T
T
Ty
y
yp
p
pe
e
e
d
d
de
e
es
s
si
i
ig
g
gn
n
na
a
at
t
ti
i
io
o
on
n
n
SSA - 12 / 55 - 4
SSA amplifier
Rated current
Maximum rated voltage
Switching frequency
20KHz when not specified
4=40KHz, 6=60KHZ
3
3
3.
.
.
T
T
Te
e
ec
c
ch
h
hn
n
ni
i
ic
c
ca
a
al
l
l
s
s
sp
p
pe
e
ec
c
ci
i
if
f
fi
i
ic
c
ca
a
at
t
ti
i
io
o
on
n
ns
s
s
Type
DC Supply
Min-Max(V) *
*
*
Current limits
Cont/Peak(A)
Size
(mm)
Weight
Kg
SSA-12/55 10-55 12/30 100x65x30 0.2
SSA-6/100 20-100 6/15 100x65x30 0.2
SSA-8/100 20-100 8/20 100x65x30 0.2
SSA-5/200 40-195 5/10 100X65X30 0.2
* DC output voltage is 90% of DC input voltage.
* 20KHz, 40KHz or 60KHz switching frequency.
* 2KHz current loop response (minimum)
*
*
*These are the absolute minimum-maximum DC supply voltages under any condition.

8
SSA - Rev 6/98
* Outputs voltages of +13V, (15mA each) for external use.
* Efficiency at rated current - 97%.
* Drift: 10µV/°C (referred to input)
* Operating temperature: 0-50°C.
* Storage temperature: -10 - +70°C.

9
SSA - Rev 6/98
4
4
4.
.
.
O
O
Op
p
pe
e
er
r
ra
a
at
t
ti
i
io
o
on
n
n
o
o
of
f
f
t
t
th
h
he
e
e
s
s
se
e
er
r
rv
v
vo
o
o
c
c
co
o
on
n
nt
t
tr
r
ro
o
ol
l
l
4
4
4.
.
.1
1
1
I
IIn
n
np
p
pu
u
ut
t
ts
s
s
The SSA has 2 inputs: A single ended input (no.1) at terminal 1 and a
differential input (no.2) at terminals 3,4.
The current gain of input 1 (current mode) is given by:
66 x Ic
Gc = ----------- (Amp/Volt), R1 in Kohm
100 + R1
Ic - amplifier rated continuous current
The current gain of the differential input for R6=R7 (current mode) is given by:
6.66xIc
Gcd= --------- (Amp/Volt)
R7
R7 in Kohm
The current gain in velocity mode is given by (place the appropriate Gc for
each input):
50 x Gc
Gv = ---------- (Amp/Volt),
R11
R11 in Kohm
The maximum input voltage at terminal 1 is calculated by:
V1max= 8 + 0.08R1 (Volts), R1 in Kohm
The maximum input voltage at terminal 3,4 is calculated by:
Vdmax= 8 + 0.8R6 (Volts), R6=R7 in Kohm

10
SSA - Rev 6/98
4
4
4.
.
.2
2
2
V
V
Ve
e
el
l
lo
o
oc
c
ci
i
it
t
ty
y
y
m
m
mo
o
od
d
de
e
e
In this mode op amp U1/2 is employed as a high gain error amplifier. The
amplifier sums velocity command and the tachogenerator feedback signal, and
provides the necessary servo compensation and gain adjustments, resulting in
stable, optimum servo operation. This op amp is configured with two feedback
paths:
One, in the form of a resistive T network, controls the DC gain of this
amplifier. The equivalent value of a T network is given by:
1010
Rf = ------
R11
Resistor R11 (30 ohm) is mounted in solderless terminals so it can be changed
easily whenever the DC gain of the error amplifier is to be changed.
The second feedback path controls the AC gain by C3 (0.022 µF), R12 (475 Kohm)
and T1. Maximum AC gain is obtained with T1 set fully CW. Setting T1 fully CCW
removes AC gain and no lag in response occurs. R12 and C3 are mounted in
solderless terminals and can be easily replaced in cases when T1 range is not
enough to get optimum response (See 8.5 for details).
The output of the error amplifier is:
1 + SxC3xR12
Vo=(V1Gv1+V2Gv2)x[ ---------------------- ]
1 + SxC3xR12(1 + RfxK1/R12)
V1,V2, - Input signals
Gv1,Gv2- Gain of inputs.
K1 = Position factor of the wiper of T1.
Full CW = 1
Full CCW = 0.01

11
SSA - Rev 6/98
The feedback element must be connected for negative feedback.
The polarity of the SSA servo amplifiers is such that a positive input signal
results in a negative voltage at terminal M1 with respect to terminal M2.
4
4
4.
.
.2
2
2.
.
.1
1
1
V
V
Ve
e
el
l
lo
o
oc
c
ci
i
it
t
ty
y
y
c
c
co
o
on
n
nt
t
tr
r
ro
o
ol
l
l
u
u
us
s
si
i
in
n
ng
g
g
a
a
ar
r
rm
m
ma
a
at
t
tu
u
ur
r
re
e
e
v
v
vo
o
ol
l
lt
t
ta
a
ag
g
ge
e
e
f
f
fe
e
ee
e
ed
d
db
b
ba
a
ac
c
ck
k
k
Using the differential input amplifier to adjust its value, the armature
voltage can be used as velocity feedback in all cases when low regulation ratio
and low speed accuracy are acceptable.
4
4
4.
.
.3
3
3
C
C
Cu
u
ur
r
rr
r
re
e
en
n
nt
t
t
m
m
mo
o
od
d
de
e
e
In order to operate the servo amplifier as a current amplifier, the velocity
loop should be disabled. This is done by converting the error amplifier into a
low gain DC amplifier which has a flat response beyond the desired current
bandwidth. In this mode, R11 and C3 have to be removed from the circuit.
4
4
4.
.
.4
4
4
C
C
Cu
u
ur
r
rr
r
re
e
en
n
nt
t
t
l
l
lo
o
oo
o
op
p
p
Current loop control is obtained by op amp U1/3 (Current amplifier) and R20,
C11 which form a lag-lead network for current loop. The standard amp is equipped
with R20 (100Kohm) and C11 (0.01µF) to get optimum current response for an
average motor in this power range. These components are mounted in solderless
terminals.
4
4
4.
.
.5
5
5
C
C
Cu
u
ur
r
rr
r
re
e
en
n
nt
t
t
l
l
li
i
im
m
mi
i
it
t
ts
s
s
The servo amplifier can operate in the following voltage-current plane:
-Ip -Ic
+V
Ic Ip
Intermittent
zone
Continuous
zone -V
Ic - Continuous current Ip - Peak current
Fig. 4.1: Voltage-Current plane

12
SSA - Rev 6/98
Each amplifier is factory calibrated to have this shape of voltage-current
operating area with rated values of continuous and peak current limits. To adjust
other values of current limits, the user has to calculate and insert two
resistors (one for the continuous limit and one for the peak limit). In addition
to these "static" current limits, there are two analog inputs for "dynamic"
control of the current limits. By applying 0-3V to the continuous current limit
input and/or 0-7V for the peak current limit input, the user can scale down the
static current limits from the preset values down to zero.
4
4
4.
.
.5
5
5.
.
.1
1
1
T
T
Ti
i
im
m
me
e
e
d
d
de
e
ep
p
pe
e
en
n
nd
d
de
e
en
n
nt
t
t
p
p
pe
e
ea
a
ak
k
k
c
c
cu
u
ur
r
rr
r
re
e
en
n
nt
t
t
l
l
li
i
im
m
mi
i
it
t
t
The peak current is so designed that its duration is a function of the peak
amplitude and the motor actual operating current before the peak demand. The
maximum peak current is available for 2 second. The duration of Ip is given by:
Ip - Iop
Tp = 2.2ln ----------
Ip - Ic
Ic - Amplifier continuous current rating.
Ip - Peak demanded (not amplifier Ip)
Iop - Actual operating current before the peak demand.
Example:
A motor is driven by an SSA-12/55 amplifier at constant speed and constant
current of 5A. What is the maximum possible duration of a 20A peak ?
20 - 5
Tp = 2.2ln -------- = 1.38 seconds
20 - 12

13
SSA - Rev 6/98
4
4
4.
.
.6
6
6
P
P
Pr
r
ro
o
ot
t
te
e
ec
c
ct
t
ti
i
iv
v
ve
e
e
f
f
fu
u
un
n
nc
c
ct
t
ti
i
io
o
on
n
ns
s
s
All the protective functions activate internal inhibit. If the cause of the
inhibit disappears, the amplifier will restart automatically. The user can
monitor this function by checking terminal 12.
4
4
4.
.
.6
6
6.
.
.1
1
1
S
S
Sh
h
ho
o
or
r
rt
t
t
c
c
ci
i
ir
r
rc
c
cu
u
ui
i
it
t
t
p
p
pr
r
ro
o
ot
t
te
e
ec
c
ct
t
ti
i
io
o
on
n
n
The short circuit protection uses the capability of the power MOSFET to
tolerate high energy peaks for short periods of time. This protection is realized
by sensing current in the DC line. Every current peak above a certain value will
inhibit the amplifier for a period of approx. 30mS.
If a short circuit condition still exists, the cycle will repeat endlessly
while turning on the Inhibit LED (Inh) to indicate short circuit condition. The
amplifier is protected against shorts between outputs, and either output to
ground.
4
4
4.
.
.6
6
6.
.
.2
2
2
U
U
Un
n
nd
d
de
e
er
r
r/
/
/O
O
Ov
v
ve
e
er
r
r
v
v
vo
o
ol
l
lt
t
ta
a
ag
g
ge
e
e
p
p
pr
r
ro
o
ot
t
te
e
ec
c
ct
t
ti
i
io
o
on
n
n
Whenever the DC bus voltage is under or over the limits indicated in the
technical specifications, the amplifier will be inhibited.
4
4
4.
.
.6
6
6.
.
.3
3
3
T
T
Te
e
em
m
mp
p
pe
e
er
r
ra
a
at
t
tu
u
ur
r
re
e
e
p
p
pr
r
ro
o
ot
t
te
e
ec
c
ct
t
ti
i
io
o
on
n
n
Temperature sensor is mounted on the heatsink. If, for any reason, the
temperature exceeds 90°C the amplifier will be inhibited. The amplifier will
restart when the temperature drops below 85 °C.

14
SSA - Rev 6/98
R11
T2
+13
-13
10M
R12
100K
4700PF
100K
C3
10K
1000PF
R20
100K C11
.01MF
CURRENT
FEEDBACK
10K
IxR
R61
100K
100K
10K
4700PF
C41
.01MF
1
2
R1
3
4
10K C12
.01MF
R6
R7
R40
IC
IP
R42
CURRENT
LIMITS POWER
STAGE
M1
M2
G
VS
5
6
EXTERNAL IC LIMIT CONTROL (ECL IC)
EXTERNAL IP LIMIT CONTROL (ECL IP)
7
11
12
CURRENT MONITOR
INHIBIT OUTPUT
PROTECTIONS 16
15
EXT. INH. LED
EXT. Ic LED
8910
CCWCW
INHIBIT INPUT
13
14
-13V+13V
NOTE:
1. ALL COMPONENTS DENOTED BY
ARE MOUNTED IN SOLDERLESS PINS.
PWM
CONVERTER
U1B U1C

15
SSA - Rev 6/98
SSA -CONTROL BOARD
U10
U7 U8
J1
1
U1
U6
C3
C11
C12
C41
R40
R12
R1
R42
R7
R6
R11
U11
J3
J2
1
Q1
R20
R61
U2
U9
U4
U3
T2
T1
ICVS
U5
INH.

16
SSA - Rev 6/98
5
5
5.
.
.
T
T
Te
e
er
r
rm
m
mi
i
in
n
na
a
al
l
l
D
D
De
e
es
s
sc
c
cr
r
ri
i
ip
p
pt
t
ti
i
io
o
on
n
n
5
5
5.
.
.1
1
1
T
T
Te
e
er
r
rm
m
mi
i
in
n
na
a
al
l
ls
s
s
o
o
of
f
f
t
t
th
h
he
e
e
b
b
ba
a
as
s
si
i
ic
c
c
S
S
SS
S
SA
A
A
Power Stage
Terminal Function Remark
Vs Power input
positive
M1 Armature
output
This output will be negative when a positive signal is
fed to one of the inputs.
M2 Armature
output
This output will be positive when a positive signal is
fed to one of the inputs.
GPower input
common
Control stage
Terminal Function Remark
1 Reference input For more details see chapter 4.1.
2 Circuit common
3Differential input
(negative)
For more details see chapter 4.1.
4Differential input
(positive)
For more details see chapter 4.1.
5External continuous
current limit
For more details see chapter 4.5.
6External peak current
limit
For more details see chapter 4.5.
7 Current monitor The scale is 3/Ic (V/A)
8 CW disable Low level input voltage *
*
*will disable half
of the power bridge and rotation in one
direction.
*
*
*-1V < Vil < 1V ; 2V < Vih < 30V
Source sink capability - 2mA min.

17
SSA - Rev 6/98
Control stage - Cont.
Terminal Function Remark
9 CCW disable Low level input voltage *
*
*will disable half
of the power bridge and rotation in one
direction.
10 Inhibit input Low level input voltage* will disable the
power bridge. See 7.1.1 for details
11 Circuit common
12 Inhibit indication
output
Whenever the amplifier is inhibited, whether
by an internal or external cause, this open
collector output goes low state (Max sink
current 10mA).
13 -13V 15mA external load.
14 +13V 15mA external load.
15 Output for external Ic
LED
16 Output for external
Inhibit LED
SSA WITHOUT SIB CARD
CONNECTORS
15 1
216
VSM1
M2
G
*
*
*-1V < Vil < 1V ; 2V < Vih < 30V
Source sink capability - 2mA min.

18
SSA - Rev 6/98
5
5
5.
.
.2
2
2
T
T
Te
e
er
r
rm
m
mi
i
in
n
na
a
al
l
ls
s
s
f
f
fo
o
or
r
r
S
S
SI
IIB
B
B-
-
-S
S
SS
S
SA
A
A
The numbering of the SIB-SSA terminals (1-16) is identical to the numbering of
the SSA control board connector.
SSA WITH SIB-SSA CARD
CONNECTORS
VSM1
M2
G
16 1

19
SSA - Rev 6/98
6
6
6.
.
.
I
IIn
n
ns
s
st
t
ta
a
al
l
ll
l
la
a
at
t
ti
i
io
o
on
n
n
p
p
pr
r
ro
o
oc
c
ce
e
ed
d
du
u
ur
r
re
e
es
s
s
6
6
6.
.
.1
1
1
M
M
Mo
o
ou
u
un
n
nt
t
ti
i
in
n
ng
g
g
As there are hazardous voltages in some models, and all models require
protection against environmental effects/elements, and each may be required to
provide adequate earth, these models must be adequately enclosed in accordance
with electric shock protection and earth requirements and Enclosure Degrees of
Protection requirements in accordance with the most recent version of standard
EN60204-1.
The SSA series dissipates its heat by natural convection up to loads of 400W.
For higher output load the amplifier should be mounted on an additional heatsink
or cooled by fan.
6
6
6.
.
.2
2
2
W
W
Wi
i
ir
r
ri
i
in
n
ng
g
g
Warning! As the units (some of the models) are used with hazardous voltages
(>60vdc), and there is no electrical isolation provided, adequate electrical
separation in accordance with the requirements of EN60204-1 (latest version) must
be provided at their outputs, and to the supplies.
Proper wiring, grounding and shielding techniques are important in obtaining
proper servo operation and performance. Incorrect wiring, grounding or shielding
can cause erratic servo performance or even a complete lack of operation.
a) Keep motor wires as far as possible from the signal level wiring (feedback
signals, control signals, etc.).
b) If additional inductors (chokes) are required, keep the wires between the
amplifier and the chokes as short as possible.
c) Minimize lead lengths as much as is practical. The DC power supply should be
mounted as closed as possible to the amplifier.
d) Use a shielded flat ribbon cable for connecting the signals. Avoid running
this ribbon in close proximity to power leads or other sources of EMI noise.
If you use the SIB-SSA interface, use twisted and shielded wires for
connecting all signals (command and feedback).
e) Use a 4 wires twisted and shielded cable for the motor connection.
f) Shield must be connected at one end only to avoid ground loops.
g) All grounded components should be tied together at a single point (star
connection). This point should then be tied with a single conductor to an
earth ground point.

20
SSA - Rev 6/98
h) After wiring is completed, carefully inspect all conditions to ensure
tightness, good solder joints etc.
A reliable connection with the spring type connectors (on the SIB-SSA) is achieved
with wires of 0.5mm2(AWG 20) stripped to a length of 11mm (.043").
6
6
6.
.
.3
3
3
L
L
Lo
o
oa
a
ad
d
d
i
i
in
n
nd
d
du
u
uc
c
ct
t
ta
a
an
n
nc
c
ce
e
e
The total load inductance must be sufficient to keep the current ripple within
the limits (10%-20% of rated current is recommended). The current ripple (Ir) can
be calculated by using the following equation:
0.5 x Vs
Ir = ---------- (A)
f x L
L - load inductance in mH.
Vs - Voltage of the DC supply in Volts.
f - Frequency in KHz.
If motor inductance does not exceed this value, a choke should be added (on the
motor branch) summing together the required inductance
Lch = L - Larm
Lch - Choke inductance
Larm - Armature inductance
6
6
6.
.
.4
4
4
D
D
DC
C
C
p
p
po
o
ow
w
we
e
er
r
r
s
s
su
u
up
p
pp
p
pl
l
ly
y
y
DC power supply can be at any voltage in the range defined within the technical
specifications (chapter 3). The supply source must comply with the safety aspects
of the relevant requirements in accordance with the most recent version of the
standard EN60950 or equivalent Low Voltage Directive Standard, all according to
the applicable Overvoltage Category. If the power source to the power supply is
the AC line (through a transformer), safety margins have to be considered to
avoid activating the under/over voltage protection due to line variations and/or
voltage drop under load.
The nominal DC bus voltage should be in the following range:
This manual suits for next models
4
Table of contents
Other Elmo Amplifier manuals
Popular Amplifier manuals by other brands
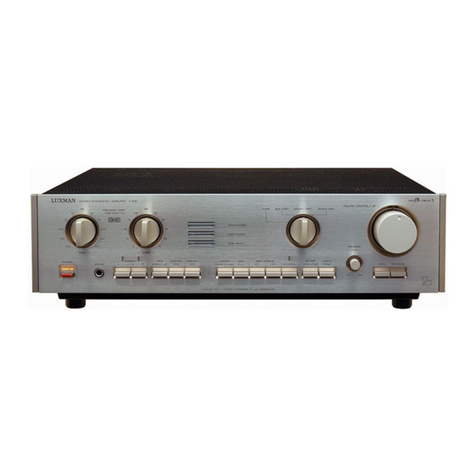
Luxman
Luxman L-430 owner's manual
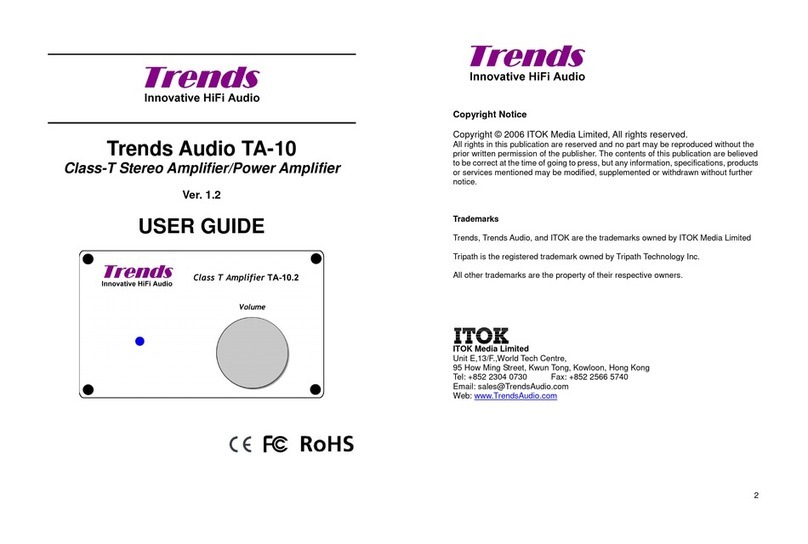
Trends Audio
Trends Audio Trends Audio TA-10 user guide
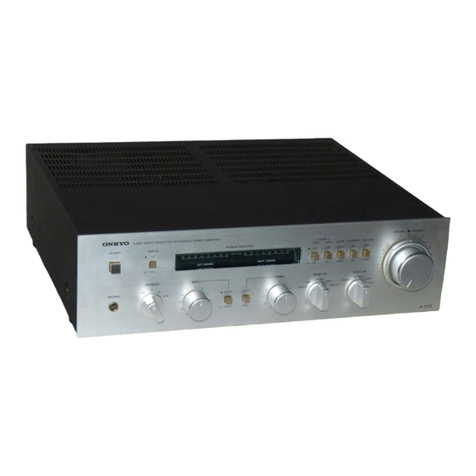
Onkyo
Onkyo A-7070 Service manual

Hogtunes
Hogtunes REV 200SG KIT-RM installation manual

Applied Research and Technology’s
Applied Research and Technology’s AV Direct Artcessories user manual
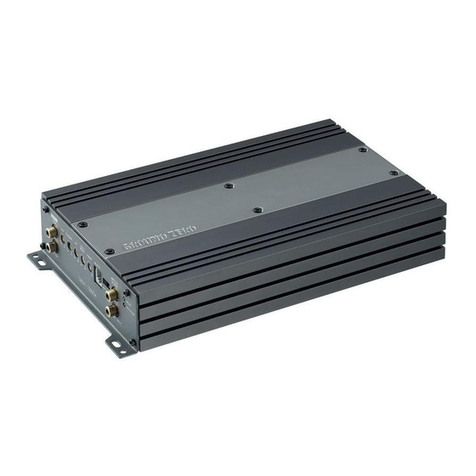
Ground Zero
Ground Zero Uranium GZUA 1.1000DX owner's manual