Fairport PP46 Guide

PLATE COMPACTOR
MODEL PP46
OPERATION, SPARE PARTS
AND SERVICE MANUAL
FAIRPORT
CONSTRUCTION EQUIPMENT LIMITED
Blagden Street
Sheffield
S2 5QS
ENGLAND
Tel: +44 (0) 114 276 7921
Fax: +44 (0) 114 272 0965
Email: [email protected]
Web: www.fairport.uk.com

CONTENTS PAGE
1. SAFETY ………………………………………………………………………… 2
1.1 SAFETY PICTOGRAMS USED ON FAIRPORT EQUIPMENT ………….. 3
1.2 SAFETY DECAL POSITIONS………………………………………………… 4
2. TECHNICAL DATA ……………………………………………………………. 5
3. USING THE MACHINE FOR THE FIRST TIME……………………………. 5
4. ROUTINE MAINTENANCE …………………………………………………… 6
5. STARTING THE ENGINE ……………………………………………………. 6
6. OPERATOR INSTRUCTIONS ……………………………………………….. 6
7. LUBRICATION…………………………………………………………………... 7
8. VEE BELT ADJUSTMENT ……………………………………………………. 7
9. WARRANTY CONDITIONS AND CLAIMS PROCEDURE ……………….. 7
CONDITIONS …………………………………………………………………... 7
CLAIMS PROCEDURE ………………………………………………………... 8
10. REPAIRS AND ESTIMATES ………………………………………………….. 8
11. ENVIRONMENT…………………………………………………………………. 9
11. PARTS LIST ……………....……………………………………………………. 9
BEDPLATE AND DRIVE SYSTEM…………………………………… 10
HANDLE ……………………………………………………………….. 11
BASEPLATE AND VIBRATOR……………………………………… 12
BLOCK COMPACTING MAT KIT ……………………………………. 13
WATER SPRINKLER KIT………………………………………………. 14
12 DECLARATION OF CONFORMITY…………………………..………………. 15

1. SAFETY
DO NOT operate this machine unless all guards are in position and secure.
DO NOT smoke when refuelling.
DO NOT refuel with engine running.
Wipe up spilt fuel.
DO NOT overfill.
Dispose of fuel contaminated wipes safely
DO NOT run engine in enclosed areas without adequate ventilation.
DO NOT run engine in an area that has a hazardous or explosive atmosphere.
Disconnect H.T. lead from spark plug on petrol engines before carrying out any
maintenance.
Turn off fuel when not using machine.
Wear protective footwear, ear defenders and gloves.
Comply with site safety regulations.
Check condition and tightness of anti-vibration mounts between engine plate and
base plate before lifting.
1.1 SAFETY PICTOGRAMS USED ON FAIRPORT EQUIPMENT

1.2 SAFETY DECAL POSITIONS

2. TECHNICAL DATA
MODEL ENGINE
MANUFACTURER ENGINE
MODEL POWER
(HP/kW)
PP46 Honda GX160 5.5/4.0
MODEL HEIGHT- H
(mm) LENGTH – L
(mm) WIDTH – W
(mm) CONTACT
AREA (sq. m) WEIGHT
(kg)
PP46 928 910 460 0.161 77
PERFORMANCE
MODEL CENTRIFUGAL
FORCE (kN) COMPACTION
RATIO (kg/m²)
PP46 12 328
NOISE AND VIBRATION EMMISSIONS
The Guaranteed Sound Power level (LWA) tested according to ISO3744 and the
Machinery Directive is 108dB(A).
*The 3-Axis Hand Arm Vibration Value tested in accordance with BS 500-4 on
uncompacted granular sub base materials is 13.8 m/s2.

3. USING THE MACHINE FOR THE FIRST TIME
When the machine is delivered from Fairport it will have no oil in the engine. Please
refer to the Engine Manufacturers Manual issued with the machine for instructions on
filling the engine with the correct type and quantity of oil.
4. ROUTING MAINTENANCE
(See Also The Engine Manufacturers Manual issued with the machine)
Daily: Check engine oil level twice daily.
Check tightness of all fastenings after first days use, thereafter check
monthly.
Check belt tension after the first days use, thereafter check monthly.
Clean air filter daily if working in dusty conditions.
Clean base plate throroughly if compacting black-top or lean concrete.
Weekly: Clean air filter (see “daily”).
Monthly: Check tightness of fastenings.
Check condition and tightness of anti-vibration mounts. Poor condition
of vibration mountings can lead to a deterioration of the product
vibration levels.
Check belt tension.
5. STARING THE ENGINE
Check oil level.
Turn fuel tap on.
Put speed control lever to tick-over.
If engine is cold, close the choke (petrol engines only).
Turn engine switch to ON(1) position.
Pull the starter rope toggle lightly until resistance is felt, then pull briskly using quick
short pull. Do not pull rope to its full extent or allow toggle to snap back against
engine. Return gently to avoid damage.
When the engine is warm, open choke.
Position engine speed control lever to give required engine speed (usually full
speed).
Commence vibration – the compactor is self – travelling.
To stop the engine, postion the engine speed control to slow and turn the engine
switch to off(0).
Turn the fuel valve off.
6. OPERATING INSTRUCTIONS
Read section (1) - Safety.
NOTE: Drive between engine and vibrator is through a centrifugal clutch. Vibration
will commence as engine speed is increased.

Position the engine speed control lever to give required speed (usually full speed).
Commence compaction. The compactor is self-travelling. Its speed of travel and the
number of passes required to achieve optimum compaction depends on the type and
condition of material being compacted and the layer depth.
Uniformly graded granular material compacts far more efficiently than wet cohesive
material.
When Compacting block paving always use a rubber attachment mat, contact your
agent for details.
When compacting blacktop always use a water spray, contact your agent for details.
Do not run the machine on solid surfaces, as this is likely to cause damage.
7. LUBRICATION
The vibrator pack is a ‘lubricated for life’ unit. It will only need relubricating if there is
a need to replace the seal and/or bearings. Replenish the housing with 150ml of
engine oil Grade 10W/30 or 15W/40.
8. VEE BELT ADJUSTMENT
It is important to note that belt tension in this application is much less than is
generally accepted as normal. Too high a belt tension may lead to engine damage,
excessive vibration in the handle, short belt life and short vibrator shaft bearing life
due to excessive transmission of vibration through the belt. Correct adjustment is
achieved by moving the engine back to take the slack out of the belt. With light finger
pressure on top of the belt and at the centre of the span, a deflection of between
5mm and 10mm is expected.
9. WARRANTY CONDITIONS AND CLAIMS PROCEDURE
All products supplied by Fairport Construction Equipment Ltd (hereafter referred to as
FCE) are warranted to be free of defects due to faulty materials or workmanship for a
period of 12 months from the date of original despatch from FCE or 3 months for all
spare parts used in repairs carried out by FCE or an authorised dealer or repairer.
If the goods have been purchased through a stockist the above warranty periods also
apply from receipt of the goods by the user of the equipment up to a total of a further
6 months from date of despatch from FCE whichever is earlier.
Filter elements, gauges and oils are specifically excluded from this warranty.
FCE shall at their option repair or replace, during normal working hours, goods
accepted as faulty free of charge to the user.
For proprietary items such as engines, the original manufacturer’s warranty and
conditions shall apply.
CONDITIONS
The goods shall be returned at the purchaser’s expense to FCE or to a destination
FCE may reasonably direct. Carriage costs will be refunded if warranty is accepted.
Warranty claims will not be considered where there is evidence that failure has been
caused by carelessness, improper use, negligence, inadequate servicing, incorrect

engine speeds, fair wear and tear or non-compliance with instructions issued by the
manufacturer.
To the extent permitted by law, the liability of FCE under this section is confined only
to providing a remedy for defective goods and does not extend to any consequential
loss, loss of profit, injury or damage suffered.
Warranty will not be accepted on dismantled goods unless dismantling was carried
out with the written permission of FCE.
No claim shall be considered if other than genuine parts supplied by FCE have been
used.
Products are only covered by this warranty in the country to where they were
supplied by FCE.
Warranty on products applies only to the original user of the equipment.
This warranty shall not apply if the serial number or other identifying numbers or
marks applied by FCE have been removed, defaced or are otherwise illegible.
CLAIMS PROCEDURE
Check that the goods are still under warranty before returning them to FCE (see
above for warranty periods).
Return the goods to FCE with an order number for the work to proceed. If warranty
is accepted no charge will be made. If warranty is not accepted a quotation will be
given for the repair and the conditions under the section headed REPAIRS AND
ESTIMATES will apply.
In the customer’s interest, goods must be accompanied by documentation detailing
the nature of the fault or its symptoms. Phrases such as ‘Faulty’ are unacceptable
and will result in delays and possible charges to defray costs incurred in identifying
the fault.
In the case of hydraulic breakers and power packs, both the breaker and the pack
should be returned.
10. REPAIRS AND ESTIMATES
When returning a machine, or an assembly for repair, always include an Advice Note
quoting model and serial number of the machine.
An official order must also be forwarded to FCE giving detailed instructions. No
repair work can be carried out unless covered by an official order.
An estimate will be submitted before proceeding with any repair. To partly cover the
cost in dismantling, cleaning and inspection, a small charge will be made; this
however will be waived upon receipt of your official instructions to proceed with the
repair.
In the event of the estimate not being accepted, a further charge will be made to
defray the rebuilding of the machine.
Estimates must be treated as approximate only as it may be found necessary to use
additional parts on further examination.

11. ENVIRONMENT
This machine contains materials that can be recycled. We recommend that when the
machine is disposed off it is done safely and in a way that protects the environment.
Part Description Materials
Engine Aluminium and steel
Baseplate Steel
Engine Frame Steel
Engine Bedplate Steel
Belt Cover Steel
Handle Steel
Ant vibration Mounts Steel and rubber
Block Paving Kit (if fitted) Steel and Polyurethane
Water Bottle Kit (if fitted) Steel and Medium Density Polyethylene

12. PARTS LIST – BEDPLATE AND DRIVE SYSTEM
Parts List Part Code Description Qty Required
1 W81731 Honda GX160 1
2 W14681 Engine Spacer 1
3 W14815 Belt Guard Back Plate 1
4 W406/5/12 5/16 UNF x ¾” Hex Setscrew 4
5 W14562 Clutch Spacer 1
6 W87287 Vee Belt 1
7 W87060 Clutch 1
8 P80120 Retaining Washer 1
9 W432/6 M6 Spring Washer 1
10 P80167 1/4 UNF x 1” Setscrew (FPC320) 1
11 W14816 Belt Guard 1
12 W437/8/16 M8 x 16 Hex Setscrew 4
13 W432/8 M8 Spring Lock Washer 4
14 W418/8 M8 Washer 4
15 W88920 Buffer Mount 2
16 W440/10 M10 Nut 2
17 W418/10 M10 Washer 2
18 W432/10 M10 Spring Lock Washer 2
19 WPC080-005 Engine Fixing Plate 2
20 W418/8 M8 Washer 8
21 W432/8 M8 Spring Lock Washer 8
22 W440/8 M8 Nut 4
23 WPC080-007 Engine Bedplate 1

12. PARTS LIST - HANDLE
Parts List Part Code Part Description Qty Required
1 W14814 Handle 1
2 W14683 Handle Pivot Bolt 2
3 W88912 Handle Bush 2
4 W480/12 M12 Nyloc Nut 2

12. PARTS LIST – BASEPLATE AND VIBRATOR ASSEMBLY
Parts List Part Code Description Qty Required
1 WPC080-001 Base 1
2 WPC080-B12 Vibrator Housing 1
3 P85034 Sealing Washer 1
4 W68574 Filler Plug 1
5 W81019 Bearing 2
6 WPC080-B09 Gasket 2
7 W81249 Oil Seal 1
8 W14819 End Plate (Pulley Side) 1
9 W14818 End Plate 1
10 W437/8/25 M8 x 25 Hex Setscrew 12
11 W14820 M8 Fibre Washer 1
12 W432/8 M8 Spring Lock Washer 11
13 W418/8 M8 Washer 11
14 P120-4012-01 M12 x 40 Hex Setscrew 6
15 W440/8 M12 Spring Lock Washer 6
16 W418/12 M12 Washer 6
17 W88919 AV Mount 4
18 W418/10 M10 Washer 8
19 W432/10 M10 Spring Lock Washer 8
20 W440/10 M10 Plain Nut 8
21 WPC080-B11 Vibrator Shaft 1
22 W87288 Drive Key 1
23 W14561 Pulley 1
24 W14593 Collar 1
25 W440/8 M12 Spring Lock Washer 1
26 W437/12/30 M12 x 30 Hex Setscrew 1

12. PARTS LIST AND FITTING INSTRUCTIONS – BLOCK COMPACTING MAT
Parts List Part Code Description Qty Required
C W14557 Rear clamp strip 1
B W14558 Centre clamp strip 1
A W14559 Front clamp strip 1
D W14560 Block compacting mat 1
-- W469/8/25 M8 csk screw x 25 2
-- W437/8/40 M8 hex screw x 40 5
-- W439/8 M8 Shakeproof 5
92991 Complete kit, includes all above parts
1. Locate Rear Clamp Strip, C, part no. W14557 behind anti-vibration mount
bracket on plate compactor with welded-on spacer facing upward. The Rear Clamp
Strip is the one with threaded holes
2. Fasten Centre Clamp Strip, B, part no. W14558 to Rear Clamp Strip with the
two M8 countersunk screws provided. The Centre Clamp Strip is the one with the
two countersunk holes.
3. Place Front Clamp Strip, A,part no W14559 onto Block Compacting Mat, D,
part no W14560 and push five M8 hexagon screws through holes in both strip and
mat after first placing Shakeproof washers under heads of screws.
4. Offer Clamp Strip, Mat and screws up to Clamp Strips fastened to compactor.
Locate screws into holes and tighten.

12. PARTS LIST – WATER SPRINKLER KIT
Part No Description Qty
W14595 Strap (Honda) 1
W14608 Strap (Briggs & Stratton) 1
W14594 Tank bracket (Honda) 1
W14607 Tank bracket (Briggs & St) 1
W80528 Clip 4
W80568 Tank 1
W80588 Tap 1
W51675 Hose tail 1
W80589 3/8” BSP nipple nut 1
W523/8 ½” fibre washer 1
W80045 Feed pipe, ¼” x 3/8” State length required
W14596 Sprinkler bar 1
W14598 Clamp plate 2
W87859 ¼” BSPT Socket Plug 2
W435/6/55 M6 x 55 Hex Bolt 4
W480/6 M6 Nyloc nut 4
W435/8/35 M8 x 35 Hex Bolt 4
W480/8 M8 Nyloc nut 4
W439/8 M8 star washer 8
93052 Complete kit for Honda, includes all above parts.

13. EC DECLARATION OF CONFORMITY
WE, FAIRPORT CONSTRUCTION EQUIPMENT LTD, BLAGDEN ST, SHEFFIELD,
SOUTH YORKSHIRE, S2 5QS
DECLARES THAT THE PRODUCT:
PP46; FITTED WITH A HONDA GX160 ENGINE
ENGINE POWER; 5.5HP/4.0kW at 3600RPM
SERIAL No.
………………………………
CONFORMS TO THE FOLLOWING DIRECTIVE:
89/336/EEC, 89/392/EEC, 91/368/EEC, 2000/14/EC
NOTIFIED BODY; AV Technology Ltd, AVTECH House, Arkle Avenue, Stanley
Green Trading Estate, Handforth, Cheshire. SK9 3RW.
USES THE FOLLOWING STANDARDS:
BS EN 292-1, BS EN 292-2, BS EN 294, BS EN 500-4
CONFORMS TO THE FOLLOWING STATUTORY INSTRUMENTS
THE SUPPLY OF MACHINERY (SAFETY) REGULATIONS 1992 &
AMMENDMENTS
COMPLIES WITH THE RELEVANT ESSENTIAL HEALTH & SAFETY
REQUIREMENTS OF THE MACHINERY DIRECTIVE
DECLARATION
I certify that on completion of manufacture of the machine detailed above that a
full conformity has been completed and relevant Health and Safety
Requirements complied with.
NAME: IAN MORRIS
STATUS WITHIN COMPANY: TECHNICAL MANAGER
SIGNATURE:
Table of contents
Other Fairport Power Tools manuals
Popular Power Tools manuals by other brands
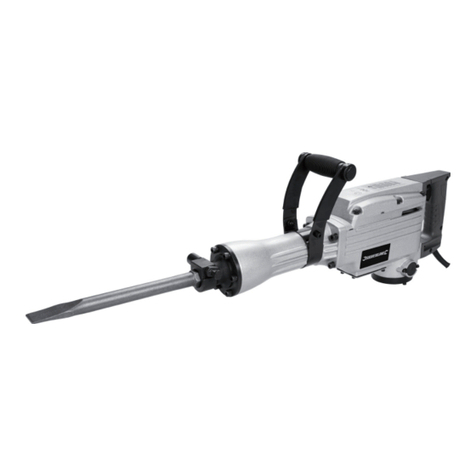
Silverline
Silverline 263570 Original instructions
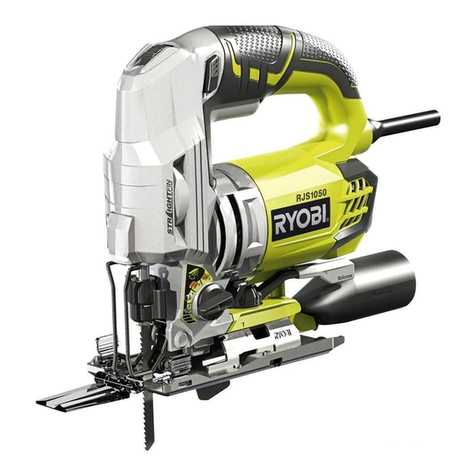
Ryobi
Ryobi RJS1050K Original instructions

Facom
Facom DM.J instruction manual
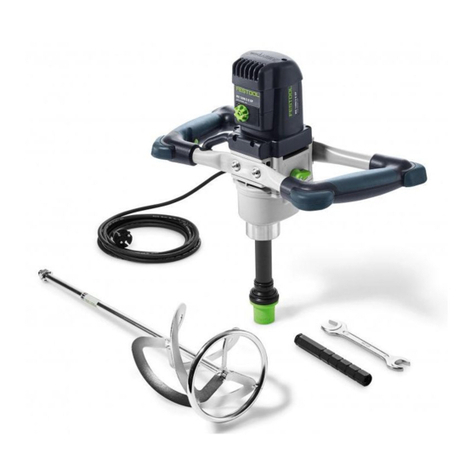
Festool
Festool MX 1200/2 E EF Original operating manual
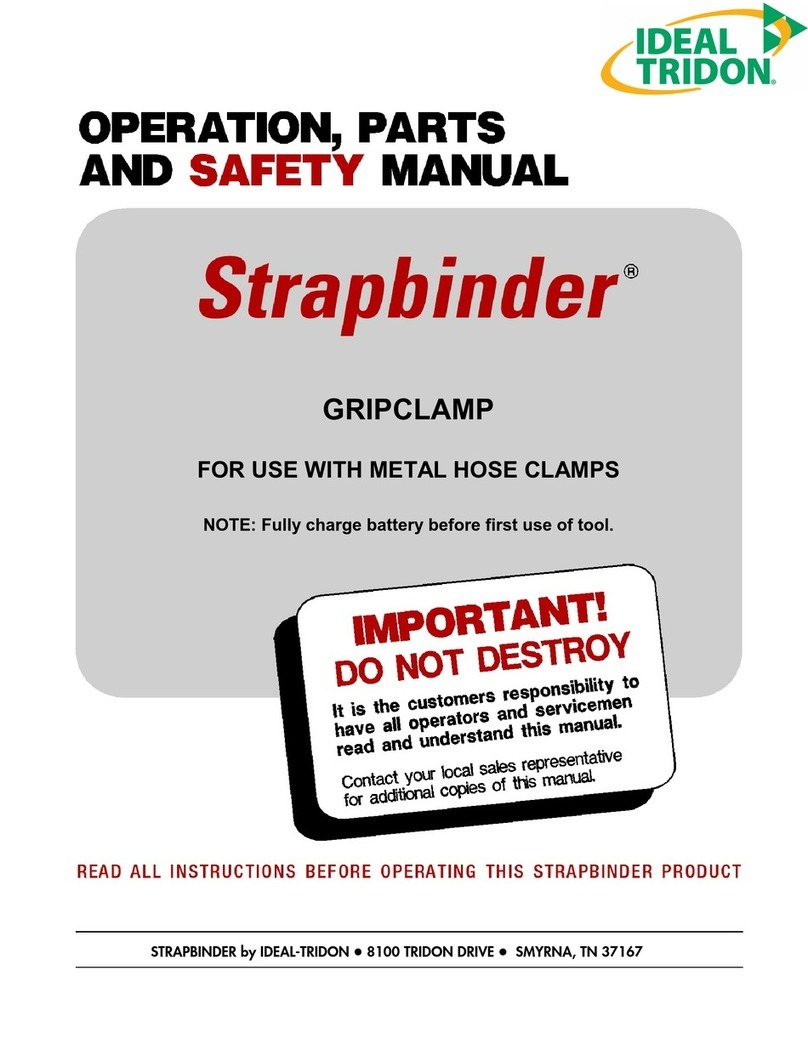
Ideal-Tridon
Ideal-Tridon Strapbinder Operation, parts and safety manual
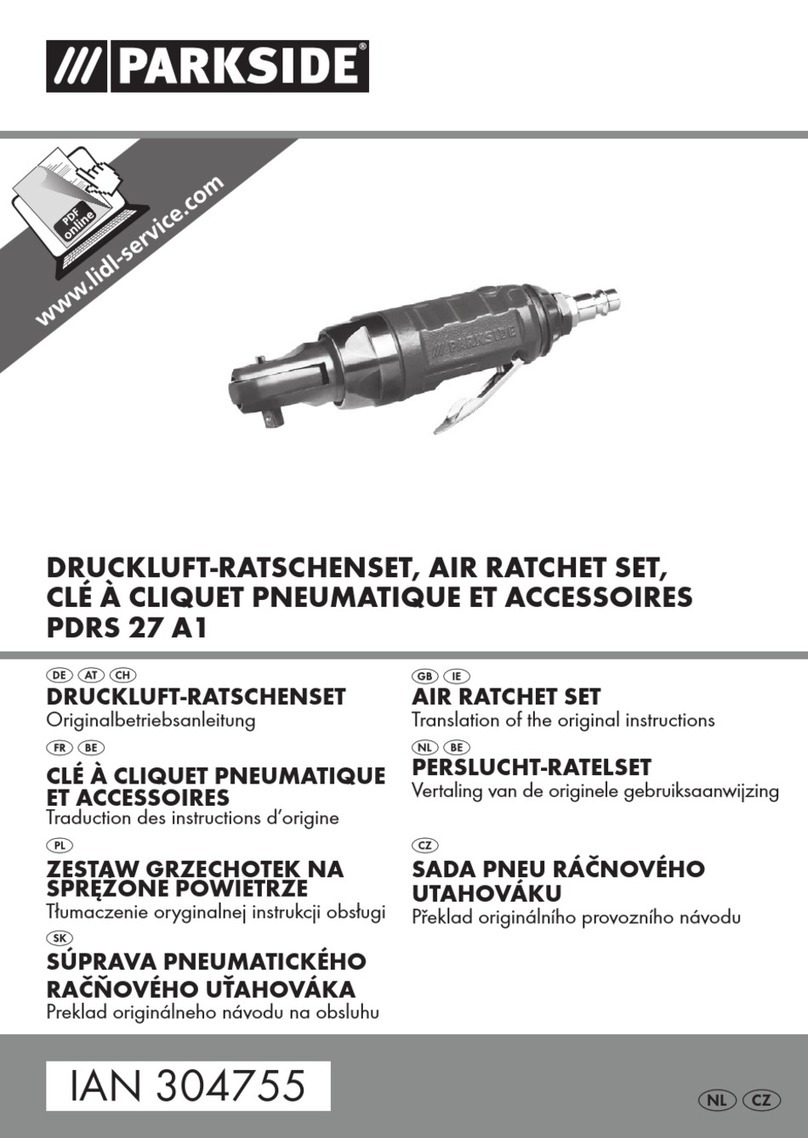
Parkside
Parkside PDRS 27 A1 Translation of the original instructions