FireFlex Systems Inc. Integrated Compressed Air Foam System Installation guide

Operation &
Maintenance Manual
FM-0723-0-02 A

Integrated Compressed Air Foam System
with Electric Release
Owner's Operation and Maintenance Manual
FM-0723-0-04 A

OWNER'S OPERATION & MAINTENANCE MANUAL
ICAF - Integrated Compressed Air Foam System
FM-0723-0-04 A
FireFlex Systems Inc.
1935 Lionel-Bertrand Blvd
Boisbriand, QC (Canada) J7H 1N8
Tel: (450) 437-3473 Toll free: (866) 347-3353
Fax: (450) 437-1930

OWNER'S OPERATION & MAINTENANCE MANUAL
ICAF - Integrated Compressed Air Foam System
FM-0723-0-04 A
Table of contents
ICAF COMPRESSED AIR FOAM SYSTEM WITH ELECTRIC RELEASE
AND FIREFLEX ARC-1 CONTROL PANEL
Description Form No
General .......................................................................................................................................FM-0723-0-07
1. Applicable standards
2. Listings & Approvals
3. Environment
4. General description
5. Features
Configuration Description
Release systems
Installation
Preliminary inspection before placing the system in service
Placing the system in service
Important settings
Mechanical trim section
1. System operation
Post discharge instructions
Inspection, tests and maintenance
Controls Section ........................................................................................................................FM-0723-0-17
User Interface
1. System status lamps
2. Keyboard – System main control keys
3. Keyboard – Menu navigation keys
4. Keyboard – User defined keys
5. Local alphanumeric display
System sequence of operation
System wiring details
ICAF System Trim Schematic ..................................................................................................FM-0723-0-09
1. Description
2. Normal condition
Trim schematic
Trim components
Continued on next page…

OWNER'S OPERATION & MAINTENANCE MANUAL
ICAF - Integrated Compressed Air Foam System
FM-0723-0-04 A
Table of contents (cont'd)
Air Supply Section.....................................................................................................................FM-0723-0-12
1. Design & selection
2. Interconnection piping to ICAF system
3. Operation
4. Recharge cylinders
5. Maintenance and Inspection
Foam Supply Section ................................................................................................................FM-0723-0-13
1. Foam storage tank
2. Foam concentrate
3. Foam tank design and selection
4. Interconnection piping to ICAF system
5. Operation
6. Filling procedure
7. Maintenance and Inspection
System Characteristics Section ..............................................................................................FM-0723-0-14
Mounting & installation details
Dimensional data
User Notes .................................................................................................................................FM-0723-0-16
Limited Warranty

OWNER'S OPERATION & MAINTENANCE MANUAL
ICAF - Integrated Compressed Air Foam System
FM-0723-0-04 A
Copyright © 2004 FireFlex Systems Inc.
All Rights Reserved
Reproduction or use, without express written permission from FireFlex Systems Inc, of any portion of this manual is prohibited.
While all reasonable efforts have been taken in the preparation of this manual to assure its accuracy, FireFlex Systems Inc
assumes no liability resulting from any errors or omissions in this manual, or from the use of the information contained herein.
ICAF ® is a registered trademark of FireFlex Systems Inc.
FireFlex Systems Inc. reserves the right to make changes to this manual and the data sheets herewith at any time, without prior
notification.

OWNER'S OPERATION & MAINTENANCE MANUAL
ICAF - Integrated Compressed Air Foam System
FM-0723-0-04 A

Page 1 of 10
ICAF - Integrated Compressed Air Foam System
General Section
FM-0723-0-07 C
General
1. Applicable Standards
Design and installation of CAF (Compressed Air Foam)
systems are covered by NFPA 11, via TIA (Tentative Interim
Amendment) #05-1. Complete design and installation shall
be prepared in full accordance with FireFlex's Design Manual
(FM-090M-0-01).
Working plans shall be prepared only by persons fully
experienced and qualified in the design of fixed Compressed
Air Foam systems. Working plans shall be reviewed by
FireFlex's engineering department prior to installation. No
deviation from these documents shall be made without prior
permission from FireFlex Systems Inc.
Before the installation, the contractor installing the system
shall be familiar with the following documents and standards:
-NFPA 11, Standard for Low-, Medium- and High-
Expansion Foam
-NFPA 13, Standard for the Installation of Sprinkler
Systems;
-NFPA 72, National Fire Alarm Code;
-Applicable Local & State Building Codes;
-Any additional requirements of the Local Authority
Having Jurisdiction.
2. Listings and Approvals
In addition to being fabricated under strict ISO-9001
manufacturing and quality control procedures, your ICAF
System has also been tested and approved by Factory
Mutual Research <FM> under the heading: "Integrated
Compressed Air Foam Extinguishing System for Fixed Piping
Networks, Class 5135" when installed with specific
components.
CAUTION ! Any unauthorized modification or addition
made on-site to a factory built Approved system will void
this Approval. Such modifications or additions may also
void the system's warranty as well. Consult FireFlex
Systems Inc. Engineering Department before proceeding
with any such modifications or additions.
3. Environment
All ICAF Systems shall be installed in a dry and clean
location. Verify that all equipment is properly heated and
protected to prevent freezing and physical damage.
The system and its components must be kept free of foreign
matter, freezing conditions, corrosive atmospheres,
contaminated water supplies, and any condition that could
impair its operation or damage the components.
The frequency of the inspections and maintenance will vary
depending on these environmental conditions. The owner is
responsible for maintaining the fire protection system and
devices in proper operating condition.
4. General Description
Compressed Air Foam (CAF) is formed by combining air
under pressure, water and foam concentrate in the right
proportions, and then sending it through piping for distribution
on the protected area.
Integrated Compressed Air Foam (ICAF) Systems for fixed
piping networks consist of a complete system including the
compressed air supply equipment, the water control valve,
the foam tank and a mixing chamber, all pre-assembled, pre-
wired and factory tested. All electrical and mechanical
components of the system are contained in single or multiple
units and ready to be connected to a fixed piping network.
The CAF is carried using standard piping network as used for
conventional sprinkler or foam systems. To distribute the
CAF over the hazard area, nozzles specially developed for
CAF are used. These nozzles are offered in different types
for various applications. The nozzles are rotary type and
insure uniform CAF distribution over the protected area.
A detection network is used in parallel with the open type
nozzles. This network may be pneumatic or electric and may
be actuated by manual, fixed temperature, rate-of-rise
temperature, smoke or other means. When the detection
system operates, it gives an alarm and activates the ICAF
System. Because ICAF Systems are often used in extra-
hazard occupancies, electrical and pneumatic detection
systems are by far the most common.
The connections required for installation are the water supply
inlet, the compressed air and the foam concentrate
interconnection with the system trim, CAF discharge outlet,
open type main drain, electrical connections with air cylinders
pressure transducer and the electrical detection and alarm
connections. The discharge outlet is connected to a fixed
piping system of open nozzles.
The ICAF system is supervised in order to monitor its
integrity. The electrical detectors and associated wiring are
also supervised.
Note: Each ICAF System mixing chamber is identified with
its unique Serial Number. This number is located on a
sticker on the mixing chamber inside the cabinet and is
used to maintain a record in our computerized data base.
Have these Serial Numbers handy when calling for
information on your unit (format is MIX-XXXXX).
5. Features
Your ICAF System is superior to many other products
available on the market now and has been manufactured by
the company that has introduced and developed the concept
of integrated fire protection systems on the market.
Main features are:
-Very efficient suppression capability using a minimal
amount of water
-Trouble free design for safe and easy application
-Available in different sizes and configuration to suit
hazards requirements

Page 2 of 10
ICAF - Integrated Compressed Air Foam System
General Section
FM-0723-0-07 C
-Very dependable stainless steel pressure vessel type
foam tank, without bladder
-Air supply cylinders bank factory assembled and tested
-User-friendly standardized owner's manual with every
unit
-Unique serial number on every mixing chamber
-Trim fully assembled and tested at the factory
-Grooved end water supply and drain connections on
both sides of the cabinet
-Sturdy 14 Gauge steel cabinet painted fire red with oven
baked polyester powder on phosphate base (powder
coated)
-Textured rust proof finish
-Neoprene gasket on all doors to eliminate vibrations
-Easily removable doors for ease of access
-Key-alike locks on all cabinet doors
-Manufactured under ISO-9001 quality control
procedures.
Configuration Description
An ICAF System is a fixed deluge-type fire suppression
system which totally floods an area or hazard with
compressed air foam through a piping system of open
nozzles. The system piping is empty until the system is
activated by a pneumatic, electric or manual release system.
Single zone configuration can be used to protect smaller
hazards whereas multiple zones and multiple mixing
chambers configurations can be used to protect larger
hazards or a combination of smaller independent hazards.
System requires a reliable and automatic water supply. Air
supply is provided by compressed air cylinders mounted on a
skid and includes an air pressure regulator. Foam
concentrate is contained inside a stainless steel tank. Upon
system activation, the foam concentrate tank is pressurized
and water, air and foam concentrate are injected and mixed
together inside a mixing chamber. Compressed Air Foam is
then generated and moves inside the piping network toward
the distribution nozzles.
ICAF Systems trims including water, air and foam controls,
CAF mixing chamber and release system are factory
assembled in cabinets and available in self-contained,
remote controlled and extension unit configurations to suit
project's requirements. A description of the available units
follows:
Self-Contained Unit
This unit includes all the mechanical controls & trims,
CAF mixing chamber(s) and is provided with the ARC-1
releasing control panel.
Components size and quantity of mixing chambers are
determined by the system's flow and configuration
required to supply the nozzles in the hazard(s).
Remote Controlled Unit
This unit is used when an additional zone is required to
be protected by the same system. This unit includes all
the mechanical controls, trims and CAF mixing
chamber(s) and is provided with a field wiring junction box
in lieu of the releasing control panel enclosure. This
should then be connected to the control panel of the self-
contained unit.
Components size and quantity of mixing chambers are
determined by the system's flow and configuration
required to supply the nozzles in the hazards.
Extension Unit
This unit is used when additional mixing chambers are
required to supply a single zone with a larger amount of
nozzles. This unit includes the CAF mixing chamber(s)
without any controls or releasing control panel. It should
be used in parallel with a self-contained unit or a remote
controlled unit.
Water Supply
CAF technology offers an important reduction in the water
supply requirements compared to standard sprinklers or
foam systems. The system can operate with a water
pressure in the range of 50 to 175 psi (345 to 1206 kPa).
The ICAF System is dependable, automatic and capable of
providing the required flow and pressure for the required
duration.
ICAF System uses pneumatically actuated globe valves for
¾" (20 mm) diameter or Listed fire protection flow control
valves for 1½" (40 mm) diameters and up.
All the valves are rated up to a maximum of 175 psi WWP
(1206 kPa) and are available in the following diameters:
¾" (20 mm) 1½" (40 mm)
2" (50 mm) 3" (80 mm)
When water pumps are required for system operation, they
shall be designed and installed in accordance with NFPA 20,
Standard for the Installation of Centrifugal Fire Pumps.
The water system shall be designed and installed in
accordance with NFPA 24, Standard for the Installation of
Private Fire Service Mains and their Appurtenances. A
strainer shall be provided on water supplies containing solids
likely to clog orifices. Such strainers shall be provided with a
cleanout port and shall be arranged to facilitate inspection,
maintenance and replacement.
Air Supply
CAF is 90% compressed air. Air is provided by cylinders
bank as described in the Air Supply Section.
The connection is used to supply compressed air between
the cylinders bank and the ICAF System. The piping is
factory prepared according to installation arrangement and is
supplied with the system. The system can be configured for:
Single air interconnection line (circled item 4).
Multiple air interconnection lines (circled item 4).

Page 3 of 10
ICAF - Integrated Compressed Air Foam System
General Section
FM-0723-0-07 C
Foam Supply
Foam concentrate is stored inside a stainless steel pressure
vessel type tank as described in the Foam Supply Section.
There are two interconnection lines provided on all foam
storage tanks. One connection is used to pressurize the
foam storage tank with compressed air (circled item 3) on
alarm condition, the other to provide foam concentrate to the
mixing chamber (circled item 2). Piping between the foam
storage tank and the ICAF System is factory prepared
according to the installation arrangement and is supplied with
the system.
System Supervision
The ARC-1 release control panel supervises the air and
water supplies to insure system's reliability at all times.
A high pressure transducer (C7) is provided to supervise
cylinder bank pressure. The intent of this device is to provide
a supervisory signal if the cylinder bank pressure goes under
the minimum pressure required to provide air supply for the
specified discharge time. A cylinder bank pressure under
2200 psi (15,158 kPa) will cause the controller to go in a
supervisory alarm mode.
An alarm pressure switch (B15) is provided with an alarm test
valve (B5) and a drain valve (B6). The alarm pressure switch
is operated through the system's water alarm line when the
system is discharged. System actuation, manual or
automatic, will cause the control panel to go under alarm and
flow confirmation modes.
The main control valve (B10) is supervised from abnormal
position by an integrated supervisory switch. The
supervisory switch supervises the valve in an open position
and will cause the controller to go in a supervisory alarm
mode in case the main control valve is not in a completely
open position.
Release Systems
The system can be activated manually, electrically using
solenoid valves or pneumatically using a pilot line. When
electrically activated, the solenoid valves are controlled by
FireFlex's ARC-1 release controller listed for releasing and
compatible with the solenoid valves.
Electric Fail Safe Release:
Electrically controlled ICAF Systems require an electric
Solenoid Valve (R2) controlled by the Approved ARC-1
Control Panel with compatible detection devices (if
provided with this system, see Controls Section for
details). The Failsafe mode maintains the system
activated in case of total power failure (AC and DC) of the
release control panel. An emergency release valve (R1)
is provided for manual override in case of a malfunction of
the release control panel.
In fire condition, when the detection condition is satisfied
the ARC-1 Control Panel energizes the Solenoid
Valve (R2) open, the pneumatic control line is then
pressurized causing the water, air and foam
pneumatically activated control valves (A1, B9 &F1) to
open simultaneously and generate the CAF through a
piping system into the discharge devices and to be
discharged over the area served by the discharge
devices.
Electric Release:
Electrically controlled ICAF Systems require an electric
Solenoid Valve (R2) controlled by the Approved ARC-1
Control Panel with compatible detection devices (if
provided with this system - see Controls Section for
details). An emergency release valve (R1) is provided for
manual override in case of a malfunction of the release
control panel.
In fire condition, when the detection condition is satisfied
the ARC-1 Control Panel energizes the Solenoid
Valve (R2) open, the pneumatic control line is then
pressurized causing the water, air and foam
pneumatically activated control valves (A1, B9 &F1) to
open simultaneously and generate the CAF through a
piping system into the discharge devices and to discharge
over the area served by the discharge devices.
Pneumatic Release:
Pneumatically controlled ICAF Systems require a
pneumatic release system, equipped with fixed
temperature releases, and/or pilot heads. An emergency
release valve (R1) is provided for manual override in case
of a malfunction of the release line.
Release trim, for pneumatically controlled ICAF Systems
utilizes a Pneumatic Actuator (R5) normally held closed
by pressure maintained in the pneumatic release system.
The air supply for the pneumatic release piping system is
provided by the cylinders bank installed as part of the
ICAF System unit. It is recommended to provide
Inspectors Test Connections on the release system.
In fire condition, the low pressure resulting in the
operation of the pneumatic release system causes the
Pneumatic Actuator (R5) to open, the pneumatic control
line is then pressurized causing the water, air and foam
pneumatically operated control valves (A1, B9 &F1) to
open simultaneously and generate the CAF through a
piping system into the discharge devices and to discharge
over the area served by the discharge devices.
Manual Release.
Manually actuated ICAF Systems provide a manual
means for the user to actuate the system. Manual
actuation is accomplished by turning the manual release
valve (R1) in the open position (identified "Emergency
Release" on the front of the unit).
In fire condition, by turning the "Emergency Release"
valve in the open position the user will cause the
pneumatic control line to pressurize, causing the water,
air and foam pneumatically operated control valves (A1,
B9 &F1) to open simultaneously and generate the CAF
through a piping system into the discharge devices and to
discharge over the area served by the discharge devices.

Page 4 of 10
ICAF - Integrated Compressed Air Foam System
General Section
FM-0723-0-07 C
Installation
ICAF Systems shall be located, installed, or suitably
protected so as to not be subjected to mechanical, chemical,
or other damage that could render them inoperative. Foam
concentrates are subject to freezing or deterioration from
prolonged storage at high temperatures, the system shall
therefore be located in a room with ambient temperature
between 40°F to 110°F (4°C to 43°C).
Although it is preferable to locate the system outside the
protected area, in the case where there is no other
alternative, provisions should be made to ensure that the
system is not going to be exposed to fire or mechanical
damage in a manner that would affect its operation.
Systems shall also be installed so that inspection, testing,
recharging, and other maintenance are facilitated and
interruption to protection is held to a minimum.
1. Install the ICAF System unit, cylinders bank and foam
concentrate tank according to the technical data
supplied.
Note: The drain collector shall be connected to an open
drain. Do not restrict or reduce drain piping.
2. Install the open nozzles piping network in accordance
with the ICAF System's Design Manual (FM-090M-0-01).
3. Install the releasing piping (if applicable), detection and
signaling circuits in accordance with applicable NFPA
standards.
4. Conform to local municipal or other codes regarding
installations of fire protection systems.
5. Perform preliminary inspection outlined below prior to
putting system in service.
6. Put the system into operation as outlined below.
7. Perform the annual inspection sequence and test each
detector and alarm unit.
8. If the system does not operate as it should, make the
necessary corrections according to manuals issued or
consult your distributor or FireFlex Systems Inc.
9. Make sure that the building owner or a delegated
representative has received instructions regarding the
operation of the system.
Preliminary inspection before placing the
system in service
(Refer to TRIM SCHEMATIC section)
1. Open door to mechanical section. Main Water Supply
Control Valve (B10) should be CLOSED. Priming
valve (B1) must be CLOSED. Air supply must be
CLOSED (see AIR SUPPLY SECTION). Flow Test
Valve (B6) and main drain valve (B16) must be
CLOSED. Alarm test valve (B5) must be CLOSED.
Emergency Release valve (R1) is CLOSED. System
flushing valve (A3) and foam injector flushing valve (F5)
must be CLOSED. All gauges (B11, B12, B17 and F4)
should show 0 psi pressure.
2. Connect all detection and alarm audible devices
(provided by others) according to electrical schematics
(see field wiring diagrams in SYSTEM WIRING section).
3. Connect the AC power for the control panel on a
separate circuit breaker in the electric distribution panel
(see TBA field wiring diagram in SYSTEM WIRING
section).
Note: Do not use these circuit breakers for other parallel
applications. If necessary, equip each circuit breaker with
a security seal in order to avoid accidental closing.
4. After the system is set, operation of the system will
require the pressurization of the actuation line to open
the pneumatically operated control valves. This may be
by automatic or manual operation of one of the release
systems described above. For specific trim
arrangement, refer to TRIM SCHEMATIC section.
Note: Electric Release: Solenoid valves, system control
panels and electrical detectors must be compatible.
Consult ARC-1 Installation & Operation Manual
FM-072Z-0-01 for devices compatibility charts.
Placing the system in service:
(Refer to TRIM SCHEMATIC section)
1. Verify the following:
a) The system Main Water Supply Control Valve (B10)
is CLOSED.
b) The system has been properly drained.
c) Flow Test Valve (B6) is OPEN.
d) The Emergency Release Valve (R1) is CLOSED.
e) The system water supply piping is pressurized up to
the CLOSED Main Water Supply Valve (B10) and
the priming line is pressurized up to the CLOSED
Priming Valve (B1).
f) The system flushing valve(s) (A3) is(are) CLOSED.
g) The foam injector flushing valve (F5) is CLOSED.
2. Verify that all releasing devices are set and that auxiliary
drain valves are CLOSED.
a) OPEN Priming Valve (B1).
3. OPEN Main Drain Valve(s) (B16).
4. PARTIALLY OPEN Main Water Supply Control
Valve (B10).
5. When full flow develops from the Flow Test Valve (B6),
CLOSE the Flow Test Valve.
a) Verify that there is no flow from the open Main Drain
Valve (B16).
6. CLOSE Main Drain Valve(s) (B16).
7. FULLY OPEN and secure the Main Water Supply
Control Valve (B10).
8. Verify that the Alarm Test Valve (B5) is CLOSED and
that all other valves are in their "normal" operating
position.

Page 5 of 10
ICAF - Integrated Compressed Air Foam System
General Section
FM-0723-0-07 C
9. Depress the plunger of the Drip Check Valve (B7). No
water should flow from the Drip Check when the plunger
is pushed.
10. Open air supply, (Refer to AIR SUPPLY section for
details).
11. Place the foam supply in SET condition, (Refer to FOAM
SUPPLY section for details).
12. Check and repair any leaks.
13. On new installations, systems that have been placed out
of service, or where new equipment has been installed,
trip test system to verify that all equipment functions
properly. Refer to INSPECTION & MAINTENANCE –
ANNUALLY section for instructions.
CAUTION ! Performing a trip test results in operation of the
ICAF System. CAF will flow into the distribution piping.
Take necessary precautions to prevent any damage.
14. After completing the trip test, perform instructions in
INPECTION & MAINTENANCE – SEMI-ANNUALLY
section.
Note: When a valve has been removed from service and is
subject to freezing or will be out of service for an
extended period of time, all water must be removed
from the priming chamber, trim piping, water supply
piping and any other trapped areas.
15. Notify the Authority Having Jurisdiction, remote station
alarm monitors, and those in the affected area that the
system is in service.
Mechanical trim section
(Refer to TRIM SCHEMATIC section)
1. System Operation
In the SET condition:
System water supply pressure enters the priming
chamber of the Flow Control Valve (B14) through the
priming line which includes a normally open priming
valve (B1), strainer (B2), restricted orifice (B3) and spring
loaded check valve (B4).
System air supply pressurizes the normally closed air
pneumatically operated control valve (A1), and the
pneumatic control lines.
Electric Fail Safe Release: In the SET condition, water
supply pressure is trapped in the priming chamber by a
spring loaded check valve (B4) and the normally closed
Water pneumatically actuated control valve (B9). The
pressure in the priming chamber holds the Flow Control
Valve (B14) clapper closed, keeping the outlet chamber
and system piping dry.
System air supply pressurizes the normally closed air
pneumatically actuated control valve (A1) and the
normally closed Solenoid Valve (R2) prevents the air to fill
up the pneumatic control lines, keeping the system
closed. The control line vent Solenoid Valve is
closed (R4).
Electric Release: In the SET condition, water supply
pressure is trapped in the priming chamber by a spring
loaded check valve (B4) and the normally closed water
pneumatically actuated control valve (B9). The pressure
in the priming chamber holds the Flow Control Valve
(B14) clapper closed, keeping the outlet chamber and
system piping dry.
System air supply pressurizes the normally closed air
pneumatically actuated control valve (A1) and the
normally closed Solenoid Valve (R2) prevents the air to fill
up the pneumatic control lines, keeping the system
closed.
Pneumatic Release: In the SET condition, water supply
pressure is trapped in the priming chamber by a spring
loaded check valve (B4) and the normally closed water
pneumatically actuated control valve (B9). The pressure
in the priming chamber holds the Flow Control
Valve (B14) clapper closed, keeping the outlet chamber
and system piping dry.
System air supply pressurizes the normally closed air
pneumatically actuated control valve (A1) and the
pneumatic release system. The Pneumatic Actuator (R5)
is held closed by pressure maintained in the pneumatic
release system, preventing the air to fill up the pneumatic
control lines, keeping the system closed.
Manual Release: In the SET condition, water supply
pressure is trapped in the priming chamber by a spring
loaded check valve (B4) and the normally closed water
pneumatically actuated control valve (B9). The pressure
in the priming chamber holds the Flow Control
Valve (B14) clapper closed, keeping the outlet chamber
and system piping dry.
System air supply pressurizes the normally closed air
pneumatically actuated control valve (A1). The normally
closed Emergency Release Valve (R1) prevents the air to
fill up the pneumatic control lines, keeping the system
closed.
In a FIRE condition:
Electric Fail Safe Release: When the detection system
operates, system Control Panel activates an alarm and
energizes normally closed Solenoid valve (R2) to open.
Electric Release System: When the detection system
operates, system Control Panel activates an alarm and
energizes normally closed three way Solenoid valve (R2)
to open.
Pneumatic Release System: When a releasing device
operates, pressure in the pneumatic release system
escapes, causing the Pneumatic Actuator (R5) to open.
Manual Release: When the Emergency Release
Valve (R1) is opened, the pressure control line is
pressurized and the pneumatically actuated control
valves for water (B9), air (A1) and foam (F1) are all
opened simultaneously.

Page 6 of 10
ICAF - Integrated Compressed Air Foam System
General Section
FM-0723-0-07 C
Pressure is released from the priming chamber to the
open drain manifold faster than it is supplied through the
restricted orifice (B3). The Flow Control Valve (B14)
clapper opens to allow water to flow into the system
piping and alarm devices, causing the water flow alarm
connected to the Alarm Pressure Switch (B15) to activate.
The foam pneumatically actuated control valve (F1)
opens, pressurizing the foam concentrate tank with air
and expelling the foam concentrate in the foam injection
line through the dip tube. Water, air and foam
concentrate being supplied at the mixing chamber,
Compressed Air Foam (CAF) is then generated and
moves inside the piping network toward the distribution
nozzles.
When the discharge time has elapsed:
Electric Fail Safe Release: The Control Panel de-
energizes the normally closed Solenoid valve (R2),
allowing it to close, the normally closed solenoid (R4) is
energized allowing the pressure control line to vent and
close the pneumatically actuated control valves for
water (B9), air (A1) and foam (F1). The Flow Control
Valve (B14) re-primes and closes, stopping the flow of
water through the piping system.
Electric Release System: The Control Panel de-energizes
the normally closed three way Solenoid valve (R2),
allowing it to close. The pressure control line is then
vented allowing the pneumatically actuated control valves
for water (B9), air (A1) and foam (F1) to close. The Flow
Control Valve (B14) re-primes and closes, stopping the
flow of water through the piping system
Emergency Shut-off instructions
(Refer to TRIM SCHEMATIC section)
1. Press and hold the F3 function key labelled: "System
Shut-Off" on the keypad of the ARC-1 panel until its
adjacent red lamp is turned ON.
2. Close the system main water supply control valve (B10)
inside the ICAF cabinet. The red lamp labelled
"Discharge suspended" will turn ON.
Note: This special function is not intended to be used prior
to the CAF discharge.
Post Discharge Instructions
(Refer to TRIM SCHEMATIC section)
To take the system Out of Service:
Warning ! Placing the control valves or detection system
out of service may eliminate the fire protection capabilities
of the system. Prior to proceeding, notify all Authorities
Having Jurisdiction. Consideration should be given to
employ a fire patrol in the affected areas.
ICAF Systems that have been exposed to a fire must be
returned to service as soon as possible. The entire system
must be inspected for damage, and repaired or replaced as
necessary.
1. Close Water Supply Control Valve (B10).
2. Open system Main Drain Valve(s) (B16).
3. Open the System Flushing Valve (A3) to flush the piping
network.
4. Open the Foam Injectors Flushing Valve (F5) to flush the
foam injectors.
5. Silence alarms (if provided; refer to CONTROL PANEL
section for additional details).
Note: Electric alarms controlled by a pressure switch
installed in the ½" (15mm) NPT connection for a Non-
interruptible Alarm Pressure Switch cannot be shut-off
until the Flow Control Valve (B14) is reset or taken out of
service.
6. For Pneumatic Release Systems, shut-off the air supply
(refer to TRIM SCHEMATIC section).
7. Close Priming Valve (B1) (optional).
8. Close Air Supply (Refer to AIR SUPPLY for details).
9. Replace any detectors, pilot heads or other release
device that have operated.
10. Replace any nozzle that have been damaged or
exposed to fire conditions. Obstructed nozzles may be
cleaned and re-installed.
11. Perform all maintenance procedures recommended in
MAINTENANCE, describing individual components of
the system that has operated.
Placing the system back in service after
operation
(Refer to TRIM SCHEMATIC section)
IMPORTANT: After a fire, make sure it is completely
extinguished. If necessary, place a fire patrol in the zone
covered by the system. ICAF Systems that have been
subjected to fire must be returned to service as soon as
possible. The entire system must be inspected for
damage, and repaired or replaced as necessary.
1. Verify that the system has been properly drained. Main
Water Supply Control Valve (B10) and priming valve
(B1) must be CLOSED. Flow Test Valve (B6) and main
drain valves (B16) should be OPEN.
2. Open the System Flushing Valve(s) (A3) to flush the
piping network.
3. Open the Foam Injectors Flushing Valve (F5) to flush the
foam injectors.
4. Air supply must be CLOSED (see AIR SUPPLY
SECTION). Verify that the Emergency Release
valve (R1) is CLOSED. System flushing valve (A3) and
foam injector flushing valve (F5) must both be CLOSED.
All gauges (B11, B12, B17 and F4) should show 0 psi
pressure.
5. Refill the foam concentrate tank (T1) according to the
procedure described in the FOAM SUPPLY section.

Page 7 of 10
ICAF - Integrated Compressed Air Foam System
General Section
FM-0723-0-07 C
6. Refill the compressed air cylinders bank (C2) according
to the procedure described in the AIR SUPPLY section.
NOTICE: Empty cylinders must be recharged by FireFlex or
its trained authorized agent. Contact FireFlex After Sales
Support Department for information about the nearest
authorized agent to your location.
7. Reset the System Control Panel (refer to CONTROL
PANEL section).
8. Open priming valve (B1).
9. Open Flow Test Valve (B6).
10. Partially open Main Water Supply Valve (B10), when full
flow develops from Flow Test Valve (B6), close the Flow
Test Valve. Verify that there is no flow from the System
Main Drain Valves (B16).
11. Close the System Main Drain Valve(s) (B16).
12. Fully open and secure the Main Water Supply Control
Valve (B10).
13. Verify that the Alarm Test Valve (B5) and all other valves
are at their NORMAL operating position.
14. Depress the plunger of Drip Check (B7). No water
should flow from the Drip Check when the plunger is
pushed.
15. Open air supply (refer to AIR SUPPLY section for
details).
16. Place the foam supply in NORMAL condition (refer to
FOAM SUPPLY for details).
17. Reset the System Control Panel.
18. Notify the Authority Having Jurisdiction, remote station
alarm monitors, and those in the affected area that the
system is in service.

Page 8 of 10
ICAF - Integrated Compressed Air Foam System
Inspection & Maintenance Section
FM-0723-0-07 C
Inspections, test & maintenance
Regular inspections, tests, and maintenance should be
performed at intervals specified in this document to verify that
the ICAF System is in good operating condition and that it
functions as intended. Components shall be restored to full
operational condition following inspection and testing.
The frequency of the inspections may vary due to
contaminated water supplies, corrosive or humid
atmospheres as well as the condition of the air supply to the
system. In addition to the instructions herewith, local
Authority Having Jurisdiction may have additional
maintenance, testing and inspection requirements which
must be followed.
Warning ! Any system maintenance which involves placing
a control valve or detection system out of service may
eliminate the fire protection capabilities of that system.
Prior to proceeding, notify all Authorities Having
Jurisdiction. Consideration should be given to the
employment of a fire patrol in the affected areas.
RESPONSIBILITY of the Owner.
1. The responsibility for properly maintaining the
compressed air foam system shall be that of the owner
of the property.
2. Inspection, testing, and maintenance shall be
implemented in accordance with procedures meeting or
exceeding those established in this document.
3. These tasks shall be performed by FireFlex's authorized
personnel who have developed competence through
training and experience.
4. It is the responsibility of the owner to promptly correct or
repair deficiencies, damaged parts, or impairments
found while performing the inspection, test, and
maintenance requirements of this document.
5. Corrections and repairs shall be performed by qualified
FireFlex's authorized personnel.
6. The building owner shall not make changes in the
occupancy, the use or process, or the materials used or
stored in the building without evaluation of the fire
protection systems for their capability to protect the new
occupancy, use, or materials.
7. Where changes are identified, the owner shall promptly
take steps to evaluate the adequacy of the installed
system in order to protect the building or hazard in
question. Where the evaluation reveals a deficiency
causing a threat to life or property, the owner shall make
appropriate corrections.
Records.
1. Records of inspections, tests, and maintenance of the
system and its components shall be maintained by the
owner and made available to the Authority Having
Jurisdiction upon request.
2. Records shall indicate the procedure performed (e.g.,
inspection, test, or maintenance), the organization that
performed the work, the results, and the date.
3. Original records shall be retained for the life of the
system.
4. Test results shall be compared with those of the original
acceptance test (if available) and with the most recent
test results.

Page 9 of 10
ICAF - Integrated Compressed Air Foam System
Inspection & Maintenance Section
FM-0723-0-07 C
The following requirements are based upon NFPA-25:
Monthly:
INSPECTION:
ICAF Discharge Nozzles:
ICAF discharge nozzles shall be inspected visually and
maintained to ensure that they are in place, continue to be
aimed or pointed in the direction intended in the system
design, and are free from external loading and corrosion.
Misaligned discharge nozzles shall be adjusted (aimed) by
visual means, and the discharge patterns shall be checked at
the next scheduled flow test.
Only ICAF Discharge nozzles are approved and shall be
used with ICAF System. Inspection shall verify that unlisted
combinations of discharge nozzles have not been
substituted.
Control Valves:
The valve inspection shall verify that the valves are in the
following condition:
1. In the normal open or closed position
2. Properly sealed, locked, or supervised
3. Accessible
4. Provided with appropriate wrenches
5. Free from external leaks
Flow Control Valves:
Valve enclosure heating equipment for ICAF Systems subject
to freezing shall be inspected during cold weather for its
ability to maintain a minimum temperature of at least 4°C
(40°F).
The gauge on the supply side of the flow control valve shall
indicate that the normal supply water pressure is being
maintained.
The gauge monitoring the ICAF system air pressure shall be
inspected monthly to verify that it indicates that normal
pressure is being maintained.
The flow control valve shall be externally inspected to verify
the following:
1. The valve is free from physical damage.
2. All trim valves are in the appropriate open or closed
position.
3. The valve seat is not leaking.
4. Electrical components are in service.
Quarterly:
INSPECTION:
Drainage:
The area beneath and surrounding a ICAF System shall be
inspected to ensure that drainage facilities, such as trap
sumps and drainage trenches, are not blocked and retention
embankments or dikes are in good repair.
System Piping and Fittings:
System piping and fittings shall be inspected for the
following:
1. Mechanical damage (e.g., broken piping or cracked
fittings)
2. External conditions (e.g., missing or damaged paint or
coatings, rust, and corrosion)
3. Misalignment or trapped sections
4. Low point drains (automatic or manual)
5. Location and condition of rubber-gasketed fittings
Hangers and Supports:
Hangers and supports shall be inspected for the following
and repaired as necessary:
1. Condition (e.g., missing or damaged paint or coating,
rust, and corrosion)
2. Secure attachment to structural supports and piping
3. Damaged or missing hangers
TEST:
Water-Flow Alarm:
All water-flow alarms shall be tested in accordance with the
manufacturer’s instructions.
Semiannually:
TEST:
Supervisory Switches:
A distinctive signal shall indicate movement from the valve’s
normal position during either the first two revolutions of a
hand wheel or when the stem of the valve has moved one-
fifth of the distance from its normal position.
The signal shall not be restored at any valve position except
the normal position.

Page 10 of 10
ICAF - Integrated Compressed Air Foam System
Inspection & Maintenance Section
FM-0723-0-07 C
Annually:
TEST:
Control Valve:
Each control valve shall be operated through its full range
and returned to its normal position.
Main Drain:
A main drain test shall be conducted to determine whether
there has been a change in the condition of the water supply
piping and control valves.
Operational Test:
Operational tests shall be conducted to ensure that the ICAF
System responds as designed, both automatically and
manually.
The test procedures shall simulate anticipated emergency
events so the response of the ICAF System can be
evaluated.
Protection shall be provided for any devices or equipment
subject to damage by system discharge during tests.
Where the nature of the protected property is such that CAF
cannot be discharged for test purposes, the trip test shall be
conducted in a manner that does not necessitate discharge
in the protected area.
Where the nature of the protected property is such that CAF
cannot be discharged unless protected equipment is shut
down (e.g., energized electrical equipment), a full flow
system test shall be conducted at the next scheduled
shutdown. In all cases, the test frequency shall not exceed 3
years.
Where discharge from the system discharge devices would
create a hazardous condition or conflict with local
requirements, an approved alternate method to achieve full
flow conditions shall be permitted.
Response Time:
Under test conditions, the automatic fire detection systems,
when exposed to a test source, shall operate within the
requirements of NFPA 72, National Fire Alarm Code, for the
type of detector provided and the response time shall be
recorded.
Discharge Time:
The time lapse between operation of detection systems and
water delivery time to the protected area shall be recorded
for open discharge devices.
Discharge Patterns:
The discharge patterns from all of the nozzles shall be
observed to ensure that patterns are not impeded by plugged
nozzles and to ensure that nozzles are correctly positioned
and that obstructions do not prevent discharge patterns from
covering surfaces to be protected.
Where obstructions occur, the piping and nozzles shall be
cleaned and the system retested.
Pressure Readings:
Pressure readings shall be recorded at the main control valve
and the CAF outlet.
Readings shall be compared to the design pressures to
ensure the original system design requirements are met.
Multiple Systems:
The maximum number of systems expected to operate in
case of fire shall be tested simultaneously to check the
adequacy of the water supply.
Manual Operation:
Manual actuation devices shall be tested.
Return to Service:
After the full flow test, the system shall be returned to service
in accordance with the instructions described in this manual.
Low points in the ICAF System shall be drained after each
operation.
Records indicating the date the ICAF System was last tripped
and the tripping time as well as the individual and
organization conducting the test shall be maintained at a
location or in a manner readily available for review by the
Authority Having Jurisdiction.
MAINTENANCE:
Strainers:
Priming line strainer (basket or screen) shall be removed,
cleaned and inspected.
Every 5 years:
TEST:
Gauges:
Gauges shall be tested every 5 years by comparison with a
calibrated gauge. Gauges not accurate to within 3 percent of
the full scale shall be recalibrated or replaced.
INSPECTION:
Flow Control Valve:
The interior of the flow control valve shall be inspected to
verify that all components operate properly. Internal
components shall be cleaned, repaired, or replaced as
necessary.

Page 1 of 8
ICAF - Integrated Compressed Air Foam System
Controls Section
FM-0723-0-17 B
User Interface
F1
F2
F3
Audibles
Silence
Ground Fault System
Reset
Partial
Disable
AC Power Alarm
Supervisory
Trouble
Alpha-Numeric Display
System Status LEDs
and Operation Keys
Menu
Navigation Keys
Function
Keys
System LED
Indicators Alarm Silence
/ Activate
Release
Acknowledge
Discharge
Enter
Menu / Exit
System
Shut-off
Inspection
Log
Shut-Off Key
Activated
Section visible
through
the door window
Left
Right
Up / Previous
Down / Next
Contrast Adjustment
FM-072C-0-275 A
Log
Activated
Discharge
Suspended
Not Used
1. System Status Lamps
Alarm, Trouble and Supervisory lamps will flash for their
respective events until acknowledged, at which point the
lamp will illuminate steadily. The local Alphanumeric Display
will provide additional details for every event (refer to screen
details in the text).
- "AC POWER": A green lamp that illuminates steadily to
indicate the presence of AC power and flashes when
system is on battery power only.
- "AUDIBLES SILENCE": A yellow lamp that illuminates
steadily when the ALARM SILENCE switch has been
depressed after an alarm. Lamp will begin flashing upon
subsequent alarm.
- "GROUND FAULT": A yellow lamp that illuminates steadily
during a ground fault condition.
- "PARTIAL DISABLE": A yellow lamp that illuminates
steadily when any input or output circuit is disabled by the
user.
- "RELEASE": A red lamp that illuminates steadily when
solenoid(s) is (are) activated and release occurs. This
lamp will flash when discharge is stopped (cycling type
systems only).
- "DISCHARGE": A red lamp that illuminates steadily when
the actual water flow has occurred.
- "ALARM": Red lamp that flashes when an alarm occurs
and becomes steady after event have been acknowledged.
- "SUPERVISORY": A yellow lamp that flashes upon
activation of a supervisory device (such as a tamper switch
and air pressure switch or sensor) and becomes steady
after event have been acknowledged.
- "TROUBLE": A yellow lamp that flashes for any trouble
condition and becomes steady after event have been
acknowledged. System internal routines trouble will
activate the trouble signals continuously.
- "OPTION LAMPS": The three (3) option lamps (factory-
defined and identified Led1, Led2 & Led3) are used for
various special functions.
Contrast Adjustment: A small potentiometer is provided on
the circuit board to adjust the LCD contrast level. This
potentiometer (shown above) can be accessed from the
bottom of the LCD module when the cabinet door is open
and adjusted with a small flat screwdriver.

Page 2 of 8
ICAF - Integrated Compressed Air Foam System
Controls Section
FM-0723-0-17 B
2. Keyboard - System Main Control Keys
Panel is provided with a membrane type keyboard as shown
on the previous page. Local sounder will beep once every
time a valid control key is depressed. Sounder will beep
twice anytime an invalid entry is made or user is scrolling too
fast with the navigation keys. Various system main control
keys are described below:
ACKNOWLEDGE: Every new event must be
acknowledged. Depressing this key will acknowledge
alarms, supervisory and troubles while in their respective
events screen. The panel has alarm and trouble resound
with lamp flash on subsequent events with alphanumeric
annunciation. The flashing lamp turns steady and the local
sounder is silenced once all events have been
acknowledged.
As shown above, before any event is acknowledged, the
Alphanumeric Display shows the three letter code 'NAK' in
front of the event description. Once acknowledged by the
user, this code changes to 'ACK'.
By default, each event has to be acknowledged
independently. The user can define in the TECHNICAL
SETUP - PARAMETERS menu that holding the key for 2
seconds will acknowledge all the current category of events
at once. When this feature is enabled, a second beep will
confirm the command has been executed and all events will
display the code 'ACK'.
ALARM SILENCE / ACTIVATE: When alarms are
sounding, pressing once on this key will turn off all
the audible devices connected to the silenceable Notification
Appliance Circuits (but not the Releasing Circuits). The
AUDIBLES SILENCE lamp will illuminate.
When alarms are not sounding, pressing and holding the key
for 2 seconds will activate the Alarm Condition, the
Notification Appliance Circuits and the System Alarm Relays
but not the Releasing Circuit(s). The ALARM ACTIVATE
function of the key is always available and both functions are
latching, so will require a SYSTEM RESET to clear.
SYSTEM RESET: The SYSTEM RESET key will
only operate while the system is either displaying a
normal operating screen for lamp test or once all events in
the System Event Screens have been acknowledged. Trying
to reset the system while any event is still not acknowledged
will silence the system buzzer momentarily, then make it
beep twice and finally continuously again. Once all events
are duly acknowledged, a full reset sequence should take
only a few seconds to complete.
Under normal conditions, pressing on the SYSTEM RESET
key make the local sounder beep once and will also perform
a LAMP TEST function.
Under alarm, supervisory or trouble conditions, once all
events have been acknowledged and cleared, pressing once
on this key resets the system and breaks power to all
initiating device circuits, 4-wire smoke power and option
boards. It will also clear any activated output circuits.
Should any alarm or trouble still exists after the reset, they
will automatically re-activate the panel (subsequent alarm
function).
3. Keyboard - Menu Navigation Keys
UP / PREVIOUS: Pressing on this key once will scroll
up the highlight to the PREVIOUS line on the
Alphanumeric Display or increase the value of a digit.
Pressing and holding the key will scroll fast up through the
values of a digit.
DOWN / NEXT: Pressing on this key once will scroll
down the highlight through the NEXT line on the
Alphanumeric Display or decrease the value of a digit.
Pressing and holding the key will scroll fast down through the
values of a digit.
LEFT ARROW: Pressing on this key once will scroll
the cursor (underscore) sideways to highlight the
PREVIOUS digit or field on the Alphanumeric Display.
RIGHT ARROW: Pressing on this key once will scroll
the cursor (underscore) sideways to highlight the
NEXT digit or field on the Alphanumeric Display.
Every time a valid navigation key is depressed, the local
sounder will beep once. Holding the UP or DOWN key
depressed for 2 seconds will return the cursor (highlight on
the active item) directly up to the first or last item or field of
any list, depending on the key selected.
The UP or DOWN keys will also scroll up or down a full page
in a list of items, thus accelerating navigation when used the
same way.
Depressing the same key again when already at the
beginning or the end of a list will make the local sounder
beep twice to indicate an invalid entry. Any invalid entry will
also make the sounder beep twice.
ENTER: This key is used to make and confirm
choices in the various user menus. It is also used to
validate an entry or select an option.
While within the System Normal or System Event screens,
pressing and holding the ENTER key for 2 seconds will give
access to specific system data screens.
First screen displays the SENSORS LIST / TEMPERATURE
as shown below, where up to 6 sensors pressures can be
displayed. The cursor also highlights the screen name being
accessed in the first line as shown below:

Page 3 of 8
ICAF - Integrated Compressed Air Foam System
Controls Section
FM-0723-0-17 B
System Temperature is displayed in the lower part of this
screen. Trouble signal will be activated on high or low
temperature indications (levels are factory defined). This
value is used for system performance analysis and should
not be used as a thermometer.
While in this screen, pressing on the RIGHT or LEFT keys
will scroll to display the BATTERY INFO. / GROUND FAULT
status screen or the TIMER STATUS screen as shown
below.
In the BATTERY INFO screen the upper portion of the
screen displays the actual battery voltage, current and size.
A minus sign in the Battery Current indication shows battery
load when the system is powered by the batteries:
- BATTERY SIZE is displaying the value entered initially at
the factory or by the user. Refer to MENUS – BASIC
SETUP for additional details. CHARGING MODE is also
displayed in this section as per the current status of
batteries:
- TRICKLE indicates a fully loaded battery on low charge
mode.
- CHARGING indicates a low battery condition on high
charge mode and will also display a timer showing how
long the condition has been active.
- DISABLE is displayed whenever the charger is turned off.
This condition appears when system is in alarm state,
when a battery fault has occurred or when AC power is off.
- TEST indicates that the batteries are in the system's
Automatic Battery Test mode (after a cold start or 30 days
after last test). This mode also displays a timer showing
how long the condition has been active. If a bad condition
of battery is detected, system will go on trouble condition.
The bottom section's GROUND FAULT STATUS indication is
for technician use and displays factory codes on Ground
Fault condition for troubleshooting purposes. Refer to
TROUBLESHOOTING section for additional details.
In the TIMER STATUS screen, all the set values of the
various timers are displayed as shown in the example below
(actual screen may differ depending on system
configuration):
Pressing on the MENU/EXIT key will exit the display
altogether and return to the default screen.
Note: Next time the user will access this display, system will
automatically return to the last screen it was displaying
before exiting, making a quick return to the same data
much easier.
MENU / EXIT: Pressing and holding this key for 2
seconds activates the user menu screen on the
Alphanumeric Display and when pressed once within
a menu item, is used to exit from this menu item. To exit
from the menu entirely, press and hold the key for 2 seconds.
Typically, the display will automatically return to its default
mode if no key activity is detected for a period of about 5
minutes.
Once modifications have been done in a menu section,
exiting the menu will save all the new data for the entire
section in the system's memory. Individual items don't need
to be saved individually.
4. Keyboard -
Function Keys
These three keys are configured for
special functions adapted to the ICAF
system mode, but their programming is
not accessible to the user and is made at the factory. The
keys functions are only available to the user when in the
Normal Screen and while navigating through the System
Events Screen.
Note: The keys usage is also contextual – depending on the
menu or utility, they can be used to perform other systems
related functions.
- F1: INSPECTION LOG is used in conjunction with the
ARC-1 PC Interface software. It is used at the factory for
testing complex sequence of operations with the help of a
PC connected to the system, by setting up a flag in the
sequence of operation. Once the sequence of operation is
activated, the PC will display all the events that occurred
between the activation and the de-activation of this flag,
making complex sequences verification easier. The log
can also be printed for archiving.
F1 F2 F3
This manual suits for next models
1
Table of contents
Popular Control Unit manuals by other brands
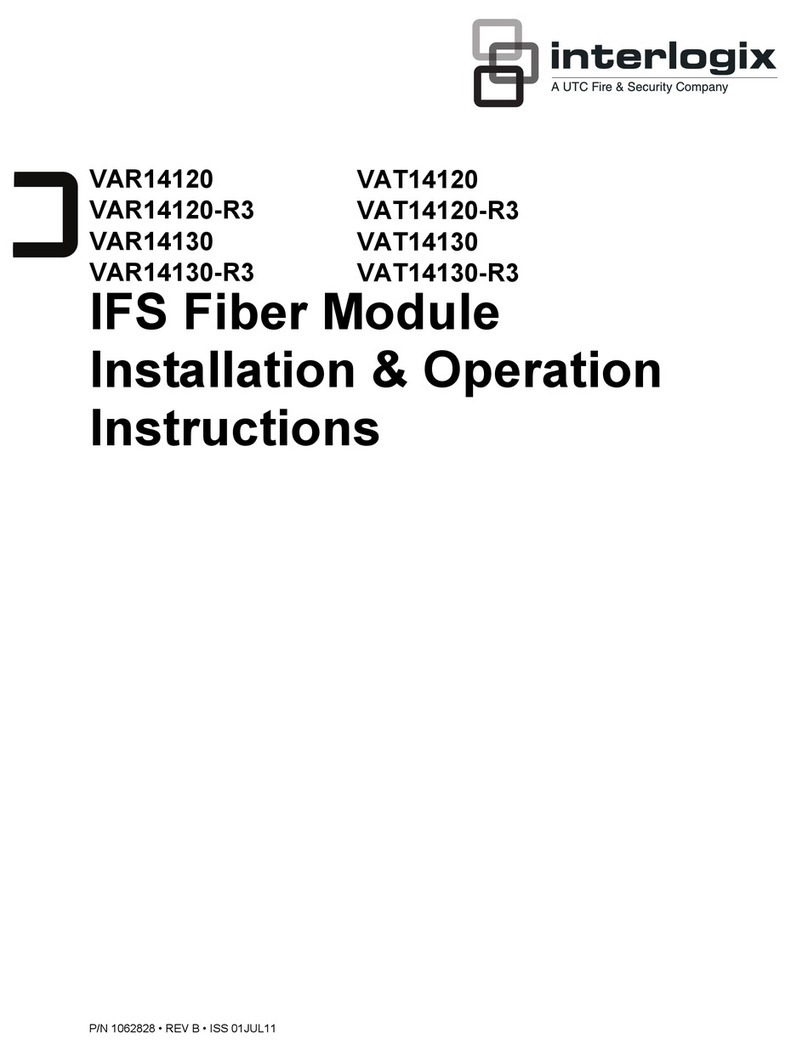
UTC Fire and Security
UTC Fire and Security interlogix VAR14120 Installation & operation instructions

Satel
Satel DT-1 Quick installation guide

Edwards
Edwards LCPV16EKA instruction manual
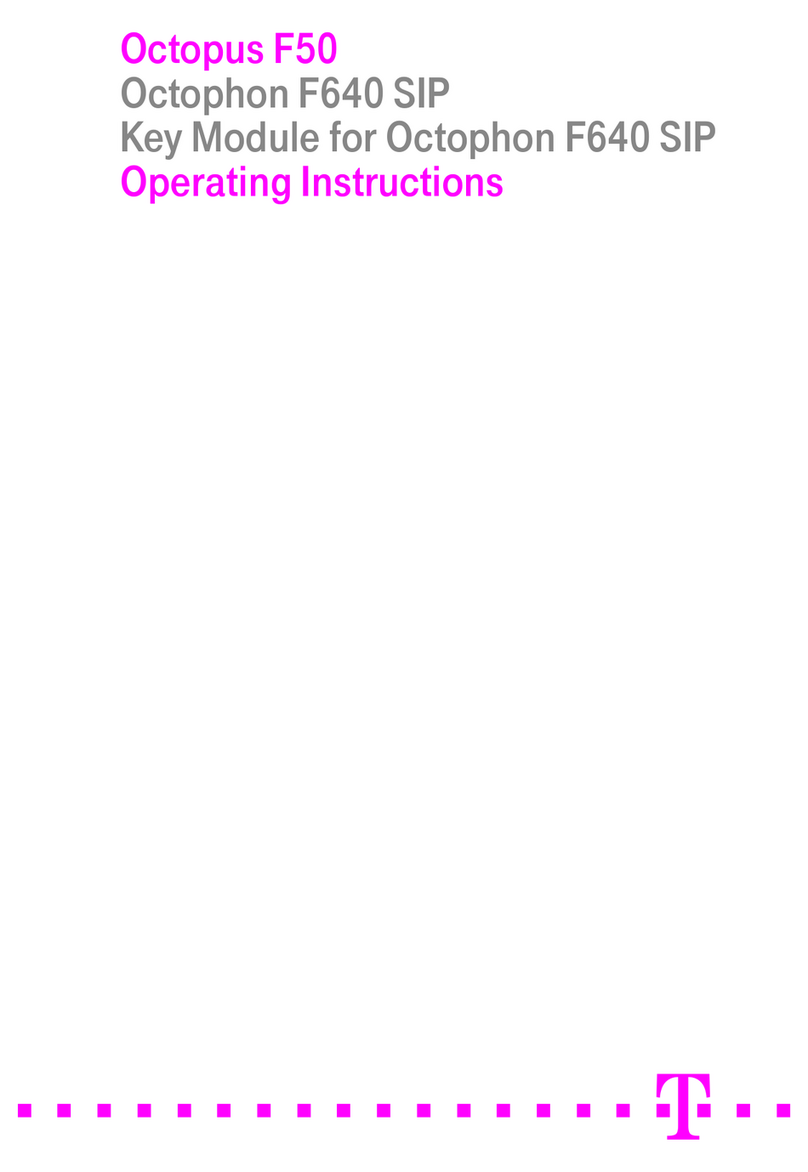
Telecom
Telecom Octopus F50 operating instructions

Kohler
Kohler K-528-K1 Installation and care guide
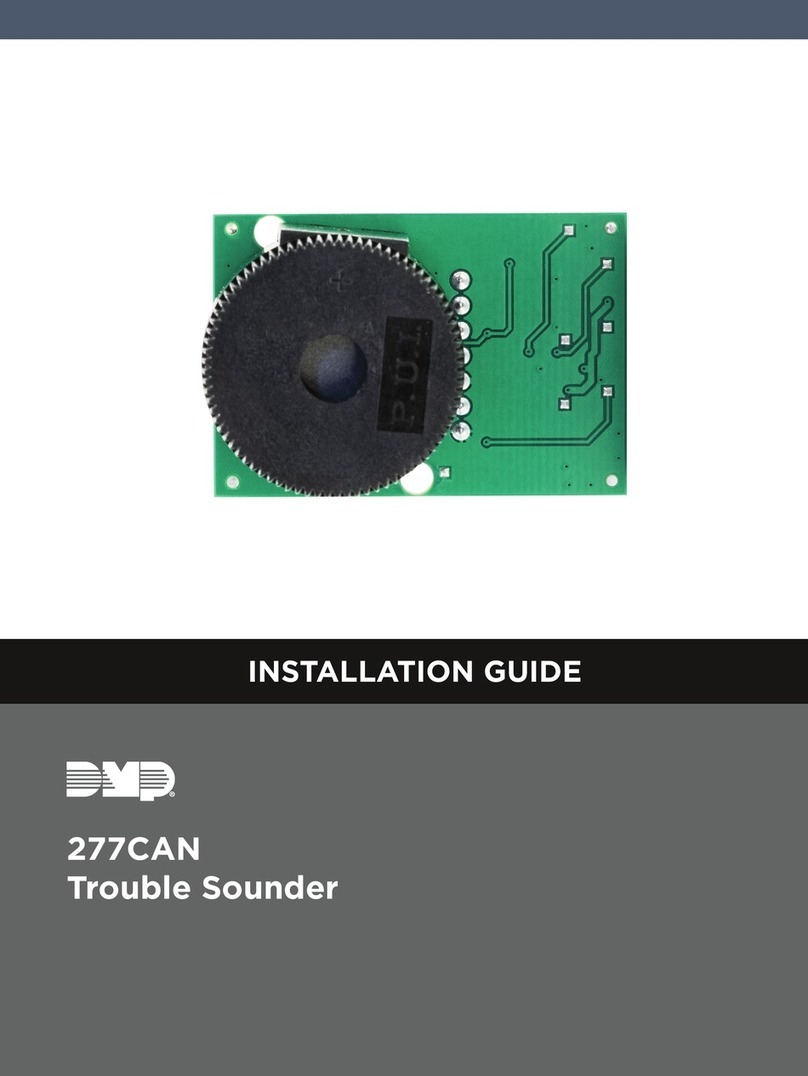
DMP Electronics
DMP Electronics 277CAN installation guide
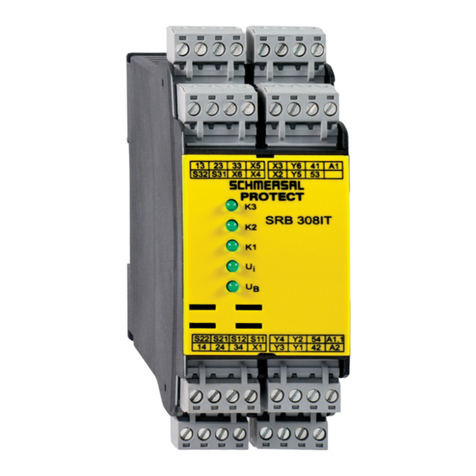
schmersal
schmersal SRB 308IT operating instructions

ETAS
ETAS ES585.1 user guide
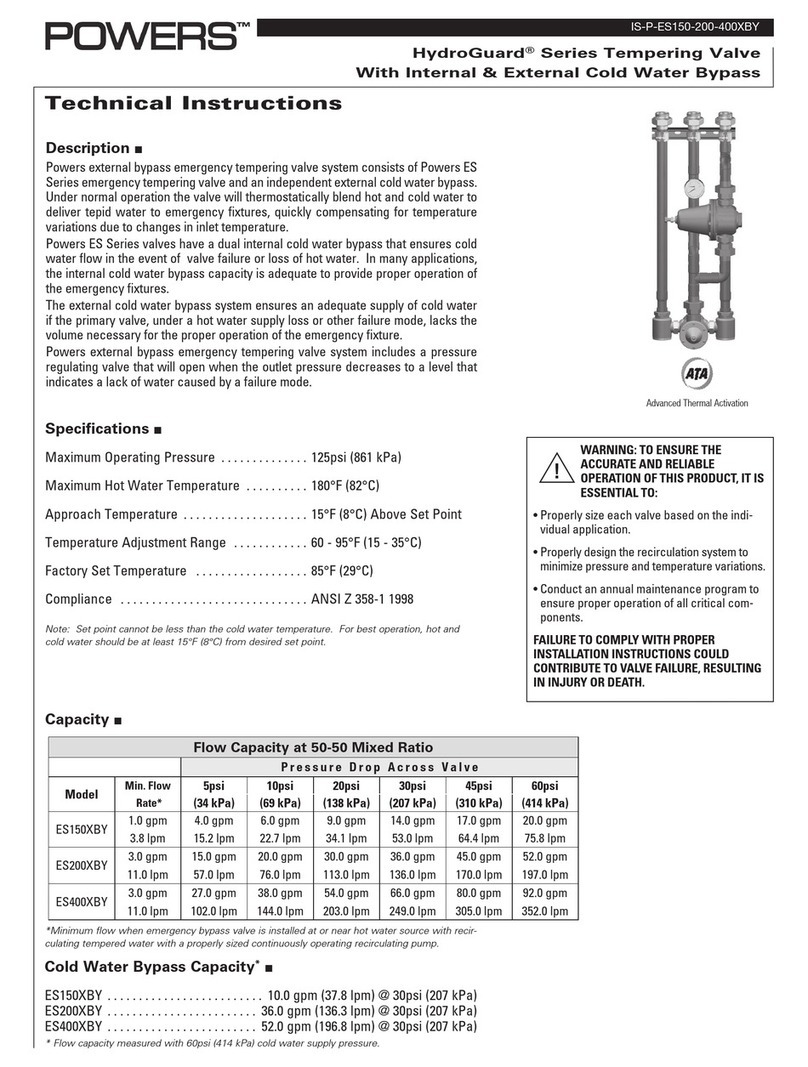
Powers
Powers HydroGuard ES150XBY Technical instructions
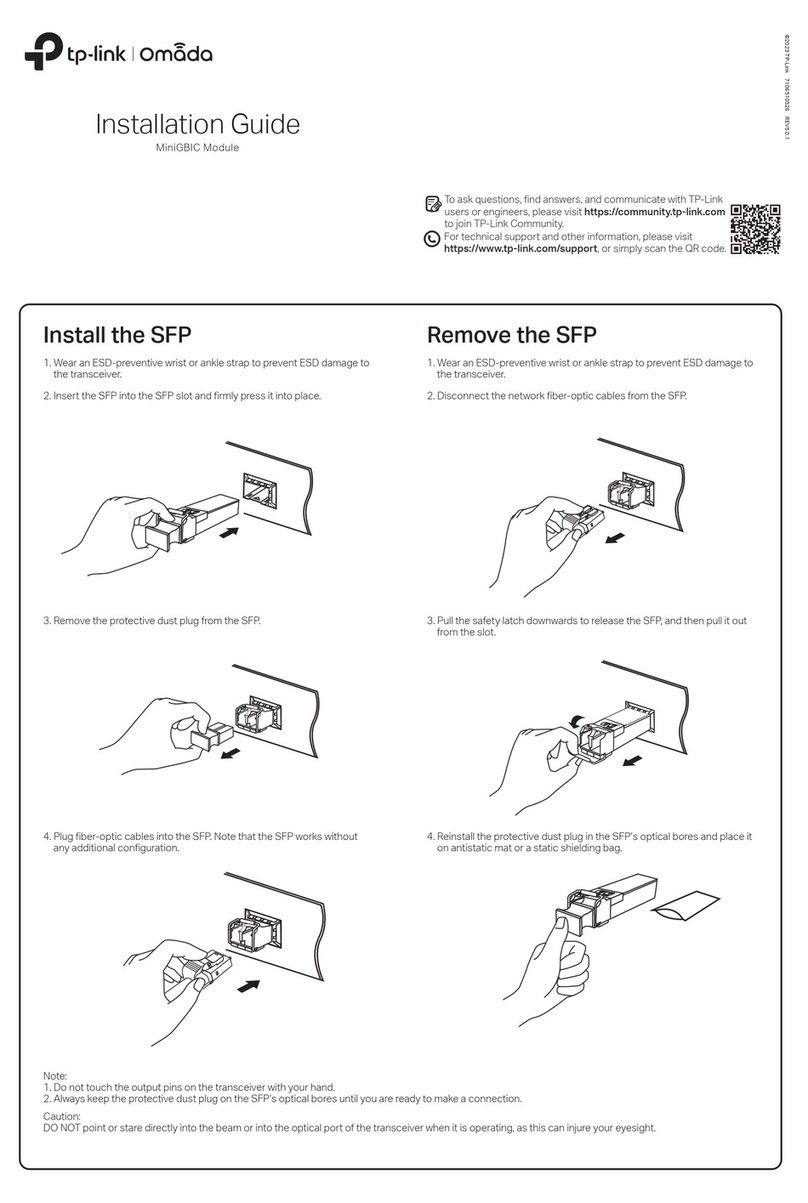
TP-Link
TP-Link Omada SM311LS V5 installation guide
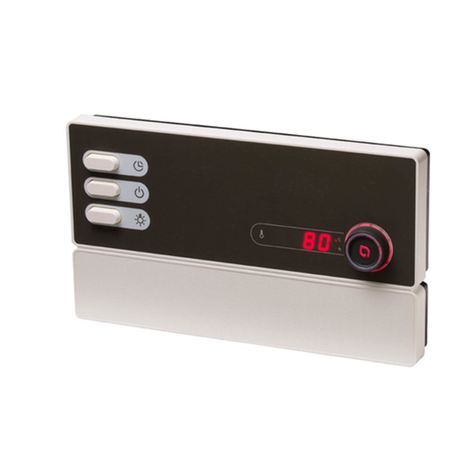
Sentiotec
Sentiotec Pro B2 Instructions for installation and use
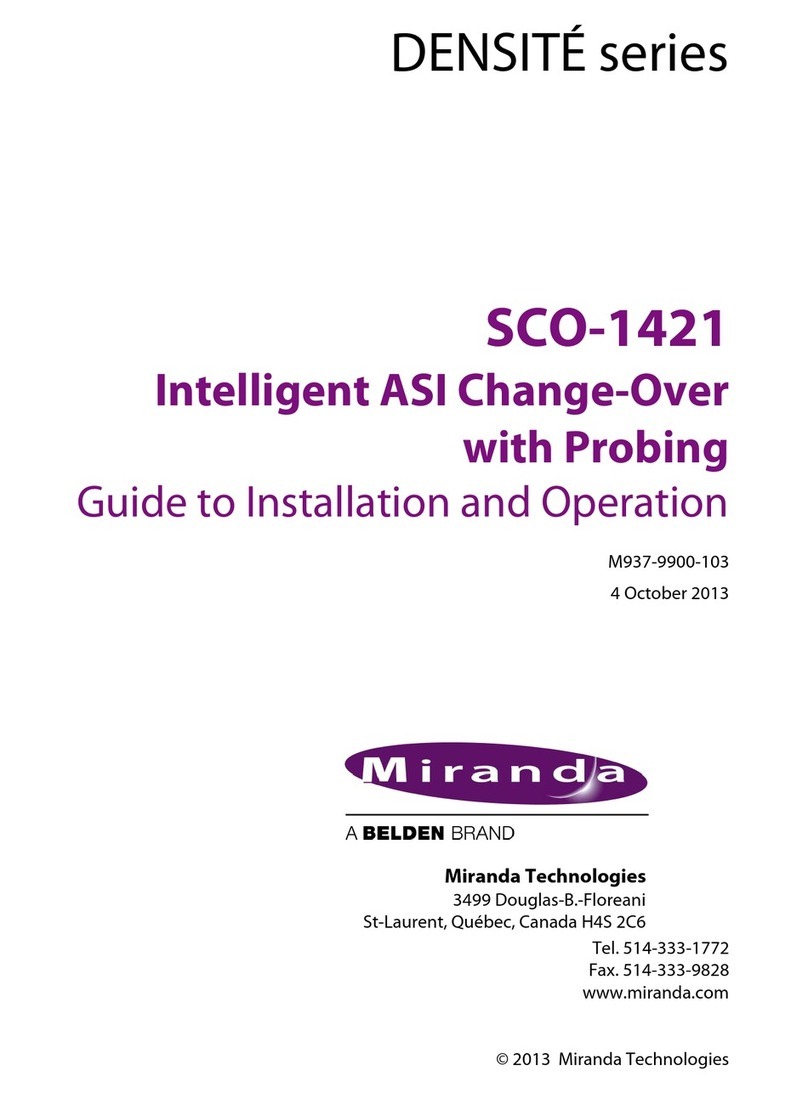
Belden
Belden Miranda DENSITE Series Guide to installation and operation