FireFlex DUAL Installation guide

FM-0860-0-31F
Integrated Fire Protection System
®DUAL
Owner's Operation and Maintenance Manual
Double Interlocked Preaction
NOVEC 1230
Remote Controlled

Page ii of 28 ®DUAL
Integrated Fire Protection System
OWNER'S OPERATION &MAINTENANCE MANUAL
FM-0860-0-31F
Copyright©2009-2016
FIREFLEX Systems Inc
.
All Rights Reserved
Reproduction or use, without express written permission from FIREFLEX Systems Inc, of any portion of this manual is prohibited.
While all reasonable efforts have been taken in the preparation of this manual to assure its accuracy, FIREFLEX Systems Inc
assumes no liability resulting from any errors or omissions in this manual, or from the use of the information contained herein.
FIREFLEX®DUAL is a registered trademark of FIREFLEX Systems Inc.
FIREFLEX Systems Inc. reserves the right to make changes to this manual and the data sheets herewith at any time, without prior
notification.

®DUAL Page iii of 28
Integrated Fire Protection System
OWNER'S OPERATION &MAINTENANCE MANUAL
FM-0860-0-31F
Table of Contents
1. GENERAL.................................................................................................................................................................1
1.1 APPLICABLE STANDARDS.............................................................................................................................................. 1
1.2 LISTINGS & APPROVALS................................................................................................................................................. 1
1.3 ENVIRONMENT ................................................................................................................................................................ 1
1.4 GENERAL DESCRIPTION ................................................................................................................................................ 1
1.5 FEATURES........................................................................................................................................................................ 2
1.6 CONFIGURATION............................................................................................................................................................. 2
1.7 RELEASING ...................................................................................................................................................................... 2
2. CLEAN EXTINGUISHING AGENT...........................................................................................................................3
2.1 AGENT............................................................................................................................................................................... 3
2.2 DESCRIPTION .................................................................................................................................................................. 3
2.3 ENVIRONMENTAL............................................................................................................................................................ 3
2.4 SAFETY CONSIDERATIONS............................................................................................................................................ 3
3. PREACTION SYSTEM .............................................................................................................................................4
3.1 DESCRIPTION .................................................................................................................................................................. 4
3.2 CONFIGURATION............................................................................................................................................................. 4
3.3 RELEASE .......................................................................................................................................................................... 4
4. INSTALLATION, OPERATION & MAINTENANCE INSTRUCTIONS......................................................................5
4.1 INSTALLATION ................................................................................................................................................................. 5
4.2 PRELIMINARY INSPECTION............................................................................................................................................ 5
4.3 PLACING SYSTEM IN SERVICE...................................................................................................................................... 6
4.4 SEQUENCE OF OPERATION........................................................................................................................................... 7
4.5 EMERGENCY INSTRUCTIONS........................................................................................................................................ 8
4.6 PLACING THE SYSTEM BACK IN SERVICE AFTER OPERATION................................................................................. 9
4.7 ELECTRIC ACTUATOR..................................................................................................................................................... 9
4.8 INSPECTIONS & TESTS................................................................................................................................................. 10
4.9 MAINTENANCE............................................................................................................................................................... 11
4.10 OPTIONAL SHUT-OFF VALVE AND SIGHT GLASS.................................................................................................... 15
4.11 OPTIONAL SEMI-FLANGED INLET/OUTLET............................................................................................................... 15
5. PREACTION AIR SUPPLIES .................................................................................................................................16
5.1 AIR SUPPLY DESIGN AND SELECTION ....................................................................................................................... 16
5.3 OPERATION.................................................................................................................................................................... 17
5.4 MAINTENANCE AND INSPECTION................................................................................................................................ 18
5.5 DEHYDRATOR OPTION................................................................................................................................................. 22

Page iv of 28 ®DUAL
Integrated Fire Protection System
OWNER'S OPERATION &MAINTENANCE MANUAL
FM-0860-0-31F
6. CONTROLS............................................................................................................................................................23
6.1 PRODUCT DESCRIPTION.............................................................................................................................................. 23
6.2 REMOTE CONTROLED FIREFLEX®DUAL....................................................................................................................... 23
7. WIRING DIAGRAMS .............................................................................................................................................24
7.1 REMOTE CONTROLLED FIREFLEX®DUAL..................................................................................................................... 24
8. CABINET.................................................................................................................................................................25
9. LIMITED WARRANTY............................................................................................................................................28

®DUAL Page 1 of 28
Integrated Fire Protection System
OWNER'S OPERATION &MAINTENANCE MANUAL
FM-0860-0-31F
1. GENERAL
The new FIREFLEX®DUAL integrated system consists of a
remotely controlled integrated preaction automatic sprinkler
system combined with a cleanagent fire extinguishing system,
factory-assembled in a single cabinet. All the components
necessary for both extinguishing systems are integrated.
The FIREFLEX®DUAL system uses 3M™ NOVEC™ 1230 fire
protection fluid combined with the Viking preaction system.
1.1 APPLICABLE STANDARDS
In addition to being fabricated under stringent ISO-9001
manufacturing and quality control procedures, your
FIREFLEX®DUAL complies with the following standards:
NFPA-13 Sprinkler Systems
NFPA-70 National Electrical Code
NFPA-72 Fire Alarm Systems
NFPA-2001 Clean agent fire extinguishing system
Before the installation, the contractor installing the unit shall
also be familiar with the following documents and standards:
Applicable Local & State Building Codes
Any additional requirements of the Local Authority Having
Jurisdiction
1.2 LISTINGS & APPROVALS
- Approbation Factory Mutual: FIREFLEX®1230 systems
are FM Approved under the heading: "FIXED
EXTINGUISHING SYSTEMS, CLEAN AGENT FIRE
EXTINGUISHING SYSTEMS".
- Underwriters Laboratories Inc. (UL): FIREFLEX®1230
Systems are UL Listed under "Clean Agent Extinguishing
System Unit” Category # GAQF-EX6174 and Category
# GAQFC-EX6174 (ULC).
Warning ! Any unauthorized modification or addition made
on-site to a factory built Listed Unit will void this Listing.
Such modifications or additions may void the unit's
warranty as well. Consult your nearest FIREFLEX
Systems Authorized Distributor before proceeding with
such modifications or additions.
1.3 ENVIRONMENT
FIREFLEX®DUAL unit shall be installed in a dry and clean
location. Verify that all equipment are properly heated and
protected to prevent freezing and physical damage.
The unit and its components must be kept free of foreign
matter, freezing conditions, corrosive atmospheres,
contaminated water supplies, and any condition that could
impair its operation or damage the components.
The frequency of the inspections and maintenance will vary
depending on the environmental conditions as well as the
condition of the air supply to the system.
THE OWNER IS RESPONSIBLE FOR MAINTAINING THE
FIRE PROTECTION SYSTEM AND DEVICES IN PROPER
OPERATING CONDITION (REFER TO SECTION 4).
1.4 GENERAL DESCRIPTION
The FIREFLEX®DUAL system uses SEVO®cylinder
designed fora high volume discharge rate in order to meet
the rapid discharge requirements specified in the
NFPA-2001 Standard. Discharge valve is of brass
construction and is designed as per the pressure
differential concept. The valve is equipped with a
pressure-indicating gauge and an electric actuator. The
cylinder is also provided with an integrated pressure safety
device.
The FIREFLEX®DUAL system integrates the same type of
preaction automatic sprinklers system as found in the
renowned FIREFLEX Systems TOTALPAC3, using top quality
Viking Corporation components and the deluge valve
model F-1. FIREFLEX®DUAL system is provided with an
integrated 2 or 3-inch diameter deluge valve.
The clean agent section of the FIREFLEX®DUAL system
is engineered by FIREFLEX Systems Inc. (or an authorized
contractor) to meet the specific protection requirements of
the application for which it is being installed.
Detection is shared by both the preaction automatic
sprinkler system and the clean agent fire extinguishing
system.
All systems are designed per NFPA-2001 Standard and in
compliance with instructions found in the following
manufacturer design manuals:
•SEVO Design Manual: SE 1230 500 ENG (latest rev.)
•Viking Corp. Form No F_070889 / Data Sheet 319,
(latest rev.)
The cylinder is filled with the extinguishing agent and then
pressurized to 500 Psi at 70°F (34.5 bar at 21.1°C) with
Nitrogen allowing maximum flexibility at the time of
installation. Each cylinder is fabricated, tested and
stamped according to D.O.T. 4BA500 or 4BW500 or TPED
specifications depending on its size and capacity.
The FIREFLEX®DUAL cabinet is of the free-standing type
and is made of robust 14 gauge steel with a rustproof fire
red paint finish, polyester powder coated and oven baked
on a phosphate base. Each cabinet is provided with two
frontal locked doors,reducing space requirements for ease
of installation and maintenance. Furthermore, all doors
are provided with a neoprene gasket to reduce vibrations
and can be removed without special tools for easier
access.
Table 1.1 - FIREFLEX®DUAL capacity of cabinet
(cylinder quantity)
Cabinet
width Size of cylinder (lbs)
40 76 164 322 601 850
36"
1 1 1 n/a n/a n/a
46" n/a n/a n/a 1 1 n/a
54" n/a n/a n/a n/a n/a 1

Page 2 of 28 ®DUAL
Integrated Fire Protection System
OWNER'S OPERATION &MAINTENANCE MANUAL
FM-0860-0-31F
1.5 FEATURES
FIREFLEX®DUAL main features are:
•Trouble-free design for safe and easy application
•Available in 3 cabinet sizes
•Uses the Viking deluge valve
•Trim is fully assembled and tested at the factory
•All trims are galvanized steel, Listed and Approved for
250 psi (17.2 bar) service maximum
•Quick connections to water supply and drain on left side,
and sprinkler riser on top of unit, all available with grooved
end or flanged fittings
•No open drain cup inside unit
•Separate unlocked access hatch to emergency manual
release
•Compact, aesthetic and easy to move
•User-friendly standardized owner's manual with every unit
•Unique serial number on every unit
•Uses UL, ULC and/or FM Approved components
•Designed in accordance with NFPA Standards
•Sturdy 14 gauge steel cabinet painted fire red with oven
baked polyester powder on phosphate base
•Textured rust proof finish
•Neoprene gasket on all doors to eliminate vibrations
•Key-alike locks on all cabinet doors
•Manufactured under ISO-9001 quality control procedures
1.6 CONFIGURATION
Configuration for FIREFLEX®DUAL:
•Engineered NOVEC 1230 single cylinder with electric
release
•Double interlocked preaction with electric / pneumatic
release
1.7 RELEASING
1.7.1 Electric releasing conditions
The electric releasing condition is needed by an approved
releasing control panel in order to operate the electric
actuator (C) of the NOVEC 1230 and the solenoid
valve (F1)of the preaction system. It can be achieved as
the following:
a) Single zone detection activated by either Zone 1 or
Zone 2.
b) Cross zone detection activated by both Zone 1 and
Zone 2.
c) Manual pull station activated.
1.7.2NOVEC 1230 electric release
Electric release is achieved with an electric actuator (C)
installed on the discharge valve (B) of the cylinder (A).
When the releasing conditions are fulfilled, a 24Vdc source
is applied to the electric actuator (C) thereby venting the
pressure on top of the discharge valve (B) thus allowing
the extinguishing agent NOVEC 1230 to be discharged
through the piping and nozzles.
1.7.3Double interlocked preaction electric release
Release trim for the double interlocked preaction system
with electric / pneumatic release utilizes a normally closed
solenoid valve (F1) controlled by control panel listed for
releasing with a compatible detection system, and a
pneumatic actuator (F3) normally held closed by
supervisory air pressure maintained in the sprinkler piping.
In fire condition, when the detection condition is fulfilled,
the control panel energizes the solenoid valve (F1) and an
open sprinkler releases the supervisory air pressure from
the sprinkler piping. Both the electric detection condition
and supervisory pressure relieved fromthesprinklerpiping
are necessary before the deluge valve (A1) will open and
fill the sprinkler piping with water. Water will flow from any
opened sprinklers in the system piping.

®DUAL Page 3 of 28
Integrated Fire Protection System
OWNER'S OPERATION &MAINTENANCE MANUAL
FM-0860-0-31F
2. CLEAN EXTINGUISHING AGENT
2.1 AGENT
The clean extinguishing agent used in FIREFLEX®DUAL total
flooding system is NOVEC 1230.
Note: The term NOVEC 1230 employed throughout this
manual refers to the extinguishing agent Dodecafluoro-2-
methylpentan-3-one known as SEVO 1230 Fire
Protection Fluid (also known as FK-5-1-12, 3M™
NOVEC™ 1230 Fire Protection Fluid, C6-F-ketone)
produced by 3M™.
2.2 DESCRIPTION
NOVEC 1230 is a colorless fluid. It is stored as a pressurized
liquid and injected into a room, area, or compartment that has
the structural integrity to retain the agent that has been
discharged.
NOVEC 1230 is dispensed as an odorless, electrically non-
conductive vapor. It leaves no residue.
NOVEC 1230 is a clean, efficient fire-extinguishing agent that
can be used on Class A, B, or C fires. It is a very stable, inert
and electrically non-conductive gas. Its primary use is for
energized electric equipment fire containment and preventing
reigniting.
2.3 ENVIRONMENTAL
NOVEC 1230 does not contribute to depletion of the
stratospheric ozone layer. NOVEC 1230 has an atmospheric
lifetime of 0.014 years. Its global warming potential is 1.
2.4 SAFETY CONSIDERATIONS
2.4.1 TOXICITY
The table 2.1 identifies the toxicological data on
NOVEC 1230 and compares this with HALON 1301.
Table 2.1 - Toxicological data
NOVEC 1230 HALON 1301
No Observed
Adverse Effect Level
(NOAEL) 10% 5.0%
Low Observed
Adverse Effect Level
(LOAEL) 10% 7.5%
Acute Exposure
LC50 (4 hour rate -
ppm) 100,000 800,000
Design Concentration
(minimum)
4.2% 4.3%
2.4.2 NOISE
Discharge of a NOVEC 1230 system can cause noise loud
enough to be startling but ordinarily insufficient to cause
traumatic injury.
2.4.3 TURBULENCE
High velocity discharge from nozzles may be sufficient to
dislodge substantial objects directly in the path of the
discharge. General turbulence in the enclosure may be
sufficient to move light objects, unsecured paper, etc.
Ceiling tiles in the vicinity of the nozzles should be clipped
in place to prevent them from being dislodged during the
discharge.
2.4.4 COOLING
Direct contact with vaporizing liquid NOVEC 1230 will have
a strong chilling effect on objects and can cause frostbite
burns to the skin. The liquid phase vaporizes rapidly when
mixed with air and thus limits the hazard to the immediate
vicinity of the discharge nozzle.
2.4.5 VISIBILITY
Upon discharge reduced visibility will be evident,
especially in humid atmospheres, as a result of the
condensations of vapor. The period of reduced visibility will
normally be brief.
2.4.6 PRESSURE
The discharge nozzle is between
73 Psi and 290 Psi (5 bar and 20 bar).

Page 4 of 28 ®DUAL
Integrated Fire Protection System
OWNER'S OPERATION &MAINTENANCE MANUAL
FM-0860-0-31F
3. PREACTION SYSTEM
3.1 DESCRIPTION
The preaction system in the FIREFLEX®DUAL integrated fire
protection system by FIREFLEX Systems Inc. consists of a
preaction system trim totally pre-assembled, pre-wired and
factory tested. All electrical and mechanical components of
the system are contained in one single unit.
The only connections required for installation are the water
supply inlet, water discharge outlet, main drain, the electrical
devices and alarm connections to an approved releasing
control panel. The discharge outlet is connected to a fixed
piping system of automatic sprinklers. Water is the
extinguishing agent.
The sprinklers network is supervised with compressed air or
gas. If the sprinklers piping or sprinkler is broken, the deluge
valve will not open.
3.2 CONFIGURATION
The FIREFLEX®DUAL preaction system is built around the
Viking trim using deluge valve model F-1.
The valve is rated up to a maximum of 250 psi (17.2 bar)
working water pressure max. and is available in the following
diameters:
•2" (50 mm)
•3" (80 mm)
FIREFLEX®DUAL preaction system is supplied with flange–
groove deluge valve.
3.3 RELEASE
Release trim for the electric / pneumatic operated double
interlocked preaction system utilizes a normally closed
solenoid valve (F1) controlled by an approved release
control panel with a compatible detection system, and a
pneumatic actuator (F3) normally held closed by
supervisory air pressure maintained in the sprinkler piping.
The FIREFLEX®DUAL system utilizes a detection system,
the same as clean agent.
In fire condition, the release control panel energizes the
solenoid valve (F1) and an open sprinkler releases the
supervisory air pressure from the sprinkler piping. Both
the electric detection condition and supervisory pressure
relieved from the sprinkler piping are necessary before the
deluge valve (A1) will open and fill the sprinkler piping with
water. Water will flow from any opened sprinklers in the
system piping.
Note: If the detection system does not operate
properly, the deluge valve (A1) will not open.
To prevent false discharge, if the detection system
operates alone due to fire, damage or malfunction, the
deluge valve (A1) will not open. If the sprinkler piping is
damaged or a sprinkler is broken or fused, the deluge
valve (A1) will not open either.

®DUAL Page 5 of 28
Integrated Fire Protection System
OWNER'S OPERATION &MAINTENANCE MANUAL
FM-0860-0-31F
4. INSTALLATION, OPERATION & MAINTENANCE INSTRUCTIONS
4.1 INSTALLATION
IMPORTANT ! The FIREFLEX®DUAL unit IS NOT
designed to be installed in area subject to freezing
conditions. Refer to section 1.3 for additional details.
1. Install the FIREFLEX®DUAL cabinet (refer to section 8).
IMPORTANT ! THE CABINET MUST BE FIRMLY
ANCHORED TO THE FLOOR USING ALL FOUR (4)
ANCHORING HOLES.
2. Install the automatic sprinkler piping and clean agent
releasing piping, detection and signaling circuits (if
applicable) in accordance with applicable standards.
3. Connect all devices and alarm devices to the remote
releasing control panel, where applicable, according to
electrical schematics (refer to section 7).
4. Connect the AC power for the remote releasing control
panel and for the optional air compressor on two
separate breakers in the electric distribution panel (refer
to section 7).
5. Conform to local municipal or other codes regarding
installations of fire protection systems.
6. Place the FIREFLEX®DUAL system in service (refer to
chapters 4.2 & 4.3).
7. If the system does not operate as it should, make the
necessary corrections according to manuals issued or
consult your distributor or FIREFLEX Systems Inc.
8. Make sure that building owner or a delegated
representative has received instructions regarding the
operation of the system.
4.2 PRELIMINARY INSPECTION
See figures 4.5 & 4.6 at the end of the current section.
1. FIREFLEX®DUAL cabinet shall be firmly anchored
to the floor.
2. Open door to mechanical section.
3. Cylinder (A) shall be solidly fixed with brackets (F).
4. Check the pressure of the cylinder with pressure
gauge (D) according to table 4.1. If the cylinder
shows a loss in pressure of more than 10%, it shall
be refilled or replaced.
5. Check that piping supports have been installed at the
correct intervals and are adequate for the purpose.
6. The piping distribution system shall be inspected to
determine that it is in compliance with the design and
installation documents.
7. Nozzles and pipe size shall be in accordance with
system drawings. Means of pipe size reduction and
attitudes of tees shall be checked for conformance to
the design.
8. Check that all nozzles are fitted in accordance with
the design requirements and are aimed in the correct
alignment away from obstructions or barriers that
could prevent adequate distribution/mixing of the
gas.
9. Protected area Integrity test shall be considered to
locate and then effectively seal any significant air
leaks that could result in a failure of the enclosure to
hold the specified agent concentration level for the
specified holding period. The currently preferred
method is using a blower door fan unit and smoke
pencil.
10. Main water supply control valve (D1) should be
closed.
11. Priming valve (B1) must be closed.
12. Air supply must be CLOSED (refer to section 5).
13. Drain test valve (B6) and main drain valve (D3) must
be closed.
14. Alarm test valve (B5) must be closed.
15. All gauges (B11, B12 and E3) should read 0 psi.
16. Using the built-in contractor's hydrostatic test ports
(see figure 4.5), fill sprinklers network with water and
maintain pressure as per NFPA-13 requirements.
WARNING ! Do not subject the air pressure gauges to
hydrostatic pressures above 250 psi (17.2 bar). Close
gauge valves before proceeding with hydrostatic test.
17. Correct leaks if any before completing test. OPEN
main drain valve (D3) to completely drain the
sprinklers network.

Page 6 of 28 ®DUAL
Integrated Fire Protection System
OWNER'S OPERATION &MAINTENANCE MANUAL
FM-0860-0-31F
4.3 PLACING SYSTEM IN SERVICE
1. Check all connections to the remote releasing control
panel.
2. Check all local audible devices.
3. Check all releasing conditions.
4. Check if NOVEC 1230 electric actuator (C) operates
after preset time delay.
5. Simulate a low cylinder pressure by shorting low cylinder
pressure switch (D) terminals.
6. Verify the active installation supervision switch on the
electric actuator (C).
CAUTION ! Activate the releasing circuit disable switch
before doing any tests on the system (see figure 6.2).
7. Verify that the system has been properly drained. Main
water supply control valve (D1) is CLOSED. Main drain
valve (D3) is OPEN. Emergency release valve (B10) is
CLOSED.
8. CLOSE main drain valve (D3).
9. OPEN priming valve (B1).
10. Reset the release control panel.
11. Restore supervisory pressure to sprinkler piping.
Note: On systems provided with an air pressure
maintenance device (air option style "B"), verify that the
½" by-pass valve (E8) in the air pressure maintenance
device trim is CLOSED and that both ¼" valves (E6 & E7)
are OPEN.
12. OPEN drain test valve (B6).
13. PARTIALLY OPEN main water supply control
valve (D1).
14. When full flow develops from the drain test valve (B6),
CLOSE the drain test valve and verify that there is no
flow from the drip check valve (B7) when the plunger is
pushed.
15. FULLY OPEN the main water supply control valve (D1).
16. Verify that the alarm test valve (B5) is CLOSED and that
all other valves are in their "normal" operating position.
17. Depress the plunger of the drip check valve (B7). No
water should flow when the plunger is pushed.
18. Check and repair all leaks.
19. Perform sequence of operation (refer to chapter 4.4).
20. Reset the remote releasing control panel.
Table 4.1- Cylinder pressure versus temperature
Cylinder pressure Temperature
413 psi
(28.4 bar)
0°F
(-17.8°C)
425 psi
(29.3 bar)
10°F
(-12.2°C)
438 psi
(30.1 bar)
20°F
(-6.67°C)
450 psi
(31 bar)
32°F
(0°C)
463 psi
(31.9 bar)
40°F
(4.4°C)
475 psi
(32.7 bar)
50°F
(10°C)
488 psi
(33.6 bar)
60°F
(15.6°C)
500 psi
(34.5 bar)
70°F
(21.2°C)
513 psi
(35.3 bar)
80°F
(26.7°C)
525 psi
(36.2 bar)
90°F
(32.2°C)
538 psi
(37 bar)
100°F
(37.8°C)
550 psi
(37.9 bar)
110°F
(43.3°C)
563 psi
(38.8 bar)
120°F
(48.9°C)

®DUAL Page 7 of 28
Integrated Fire Protection System
OWNER'S OPERATION &MAINTENANCE MANUAL
FM-0860-0-31F
4.4 SEQUENCE OF OPERATION
The remote releasing control panel shall be configured for the
following operation.
4.4.1 Automatic release
1. Actuation of a detector from one detection zone:
a) “ZONE 1” (or “ZONE 2”) activates.
b) "ALARM" audible devices activate.
c) “ALARM” contacts activate.
d) Preaction solenoid valve (F3)activates.
Note: Preaction piping network will not yet be filled with
water.
2. Actuation of a detector from the other detection zone (for
crossed zones configuration):
a) “ZONE 2” (or "ZONE 1”) activates.
3. Discharge sequence occurs:
a) “PRE-DISCHARGE NOVEC 1230” contacts activate.
b) Pre-discharge delay starts (not exceeding 60 sec).
c) "SECOND STAGE ALARM" audible devices activate.
Note: The abort station from the remote releasing control
panel will prevent the NOVEC 1230 discharge as long as
being maintained if activated during the pre-discharge
delay.
4. After pre-discharge delay is completed:
a) NOVEC 1230 electric actuator (C) activates.
If NOVEC 1230 discharge switch option is selected:
b) “DISCHARGE NOVEC 1230” contact activates.
5. After a preaction sprinkler head fuses:
a) Deluge valve (A1) opens; water will flow into sprinkler
piping network and out of sprinklers and any openings
on the system.
b) “WATERFLOW PREACTION” contact activates.
4.4.2 Manual release
1. Actuation of a manual release pull station within the
system:
a) "ALARM" audible devices activate.
b) “ALARM” contacts activate.
c) Preaction solenoid valve (A1) activates.
Note: Preaction piping network will not yet be filled with
water.
d) “PRE-DISCHARGE NOVEC 1230” contacts activate.
e) Pre-discharge delay starts (not exceeding 30 sec).
f) "SECOND STAGE ALARM" audible devices
activate.
2. After pre-discharge delay is completed:
a) NOVEC 1230 electric actuator (C) activates.
If NOVEC 1230 discharge switch option is selected:
b) “DISCHARGE NOVEC 1230” contact activates.
3. After a preaction sprinkler head fuses:
a) Deluge valve (A1)opens; water will flow into
sprinkler piping network and out of sprinklers and any
openings on the system.
b) “WATERFLOW PREACTION” contact activates.
Note: At any time, if the optional mechanical
activator (J) is activated, the NOVEC 1230 will be
released.
At any time, if the emergency release valve (B10) is
activated, the preaction piping network will be filled
with water. Only the "ALARM" audible devices will
activate.
4.4.3 Abort Station
1. Actuation of an abort station within the system:
a) "TROUBLE” contact activates.
When abort release switch is activated, pre-discharge
timer will continue to count down until it reaches
10 seconds and then wait. Releasing the abort release
switch will allow the pre-discharge to continue its count
down from 10 seconds. If the abort release switch is again
activated before the pre-discharge timer reaches zero, the
timer will reset to 10 seconds and wait.
4.4.4System supervisory
1. Actuation of a supervisory device such as low pressure
switch or valve in wrong position within the system:
a) "SUPERVISORY” contact activates.

Page 8 of 28 ®DUAL
Integrated Fire Protection System
OWNER'S OPERATION &MAINTENANCE MANUAL
FM-0860-0-31F
4.5 EMERGENCY INSTRUCTIONS
To take system out of service:
WARNING ! Placing a system out of service mayeliminate
the fire protection capabilities of the system. Prior to
proceeding, notify all Authorities Having Jurisdiction.
Consideration should be given to employ a fire patrol in
the affected areas.
After placing the system out ofservice hasbeen authorized by
the appropriate Authority Having Jurisdiction:
1. Turn the releasing circuit disable switch to
DISABLED before doing any tests on the system (see
figure 6.2).
2. Close main water supply control valve (D1).
3. Open system main drain valve (D3).
4. Silence alarms at the remote releasing control panel
(refer to section 6).
Note: Electric alarms controlled by a pressure switch
installed in the ½" (15mm) NPT connection (C2) for a
non-interruptible alarm pressure switch cannot be shut-
off until the deluge valve (A1) is reset or taken out of
service.
5. Shut-off the air supply (refer to section 5).
6. Open drain test valve (B6).
7. Close priming valve (B1).
8. Sprinklers network thathas been subjected to a fire must
be returned to service as soon as possible. The entire
system must be inspected for damage, and repaired or
replaced as necessary.
9. Replace any sprinklers that have opened, been
damaged, or have been exposed to fire conditions.
10. Replace any detectors that have been damaged.
11. Return the system to service as soon as possible.
Perform steps 5 through 18 of chapter 4.3.
12. Turn the releasing circuit disable switch to NORMAL
(see figure 6.2).

®DUAL Page 9 of 28
Integrated Fire Protection System
OWNER'S OPERATION &MAINTENANCE MANUAL
FM-0860-0-31F
4.6 PLACING THE SYSTEM BACK IN SERVICE AFTER
OPERATION
See figures 4.5 & 4.6 at the end of the current section.
1. Remove the electric actuator (C) from the cylinder (A).
2. Remove cylinder (A) and send it to an authorized agent
for filling.
3. Reinstall the cylinder (A) inside the cabinet.
4. Reset the electric actuator (C) (refer to chapter 4.7).
5. Install the electric actuator (C) on the cylinder (A).
6. Check that the piping and nozzles have not been altered.
WARNING ! the optional mechanical release (J) SHALL
be in NORMAL position, handle upwards and safety pin
installed BEFORE installing it on the cylinder valve (B).
7. Verify that the system has been properly drained. Main
water supply control valve (D1) is CLOSED. Main drain
valve (D3) is OPEN. Emergency release valve (B10) is
CLOSED.
8. CLOSE main drain valve (D3).
9. OPEN priming valve (B1).
10. Restore supervisory pressure to sprinkler piping.
Note: On systems provided with an air pressure
maintenance device (air option style "B"), verify that the
½" by-pass valve (E8) in the air pressure maintenance
device trim is CLOSED and that both ¼" valves (E6 & E7)
are OPEN.
11. Reset the release control panel. Solenoid valve (F1)
should close.
12. OPEN drain test valve (B6).
13. PARTIALLY OPEN main water supply control
valve (D1).
14. When full flow develops from the drain test valve (B6),
CLOSE the drain test valve.
15. Verify that there is no flowfrom the drip check valve (B7)
when the plunger is pushed.
16. FULLY OPEN the main water supply control valve (D1).
17. Verify that the alarm test valve (B5) is CLOSED and that
all other valves are in their "normal" operating position.
18. Depress the plunger of the drip check valve (B7). No
water should flow from the drip check when the plunger
is pushed.
19. Check and repair all leaks.
20. Notify the Authority Having Jurisdiction, remote station
alarm monitors, and those in the affected area that the
system is back in service.
4.7 ELECTRIC ACTUATOR
When the electric actuator (C) gets energized, it stays in
the activated position (see figure 4.1).
Figure 4.1
Reset the actuator (C) to normal position by turning or
pushing the resetting tool (see figures 4.2 & 4.3).
Figure 4.2
Figure 4.3
Activated position
Resetting tool
Normal position

Page 10 of 28 ®DUAL
Integrated Fire Protection System
OWNER'S OPERATION &MAINTENANCE MANUAL
FM-0860-0-31F
4.8 INSPECTIONS & TESTS
NOTICE:THE OWNER IS RESPONSIBLE FOR
MAINTAINING THE FIRE PROTECTION SYSTEM AND
DEVICES IN PROPER OPERATING CONDITION.
The purpose of the periodic inspection and tests is to insure
that the system is operating satisfactory and to identify
problems that could adversely affect the performance of the
system. Inspection and tests of the system shall be
accomplished in accordance with NFPA-25, NFPA-72 and
NFPA-2001. At least annually, the system shall be thoroughly
inspected and tested for proper operation by competent
personnel. In addition, the Authority Having Jurisdiction may
have additional maintenance, testing, and inspection
requirements that must be followed.
WARNING ! Any system maintenance that involves
placing the system out of service may eliminate the fire
protection capabilities of that system. Prior to proceeding,
notify all Authorities Having Jurisdiction.
Records
Records of inspections, tests, and maintenance of the system
and its components shall be made available to the Authority
Having Jurisdictionupon request. Typical records include, but
are not limited to, detection system, NOVEC 1230 cylinder
inspections, valve inspections, trip tests of preaction valve.
Acceptance test records should be retained for the life of the
system. Subsequent test records should be retained for a
period of 1 year after the next test. The comparison
determines deterioration of system performance or condition
and the need for further testing or maintenance.
4.8.1 Preaction low air pressure supervisory test
To test preaction system “low air” supervisory:
Note: To prevent operation of the deluge valve (A1) and
filling of the sprinkler piping with water during the test,
CLOSE main water supply control valve (D1) and OPEN
drain test drain (B6).
1. Slowly open the Inspectors test valve or the main drain
valve (D3).
2. Verify that low air supervisory operate within pressure
setting from table 5.3.
3. Close the Inspectors test valve or the main drain
valve (D3).
4. Establish recommended air pressure.
5. Reset the remote releasing control panel.
When testing is complete, return the system to
service:
1. Verify that the pressure indicated on pressure
gauge (B11) indicates that the priming chamber is
pressurized with system water supply pressure
indicated on pressure gauge (B12).
2. OPEN drain test valve (B6).
3. PARTIALLY OPEN main water supply control
valve (D1).
4. When full flow develops from flow test valve, CLOSE
the drain test valve (B6).
5. FULLY OPEN and secure the main water supply
control valve (D1).
6. Verify that the alarm test valve (B5) is CLOSED and
that all other valves are in their "normal" operating
position (see figure 4.5).
7. Verify that there is no flow from the drip check
valve (B7) when the plunger is pushed.
4.8.2 Preaction full flow trip test
Performance of a trip test is recommended annually during
warm weather. Consider coordinating this test with
operation testing of the releasing devices.
Caution ! Performance of this test will cause the
deluge valve (A1) to open and the sprinkler system to
fill with water.
To trip test the preaction system:
1. Notify the Authority Having Jurisdiction and those in
the area affected by the test.
2. To trip the deluge valve (A1):
♦Fulfill the electric releasing condition (refer to
chapter 1.7.1).
♦Open the sprinkler system inspectors test valve
or the main drain valve (D3).
♦OR Open the door of emergency release (B10)
and pull the handle.
3. The deluge valve (A1) should open, filling the
sprinkler system with water. Water flow alarms
should operate.
4. Verify adequate flow from the sprinkler system
inspectors test valve within an acceptable time
period.
When trip testing is complete:
Perform steps 5 through 7 of chapter 4.5.
Perform steps 7 through 20 of chapter 4.6.
Notify the Authority Having Jurisdiction and those in the
affected area that testing is complete.

®DUAL Page 11 of 28
Integrated Fire Protection System
OWNER'S OPERATION &MAINTENANCE MANUAL
FM-0860-0-31F
4.8.3 Main drain test
A main drain test shall be conducted to determine whether
there has been a change in the condition of the water supply
piping and control valves (as per NFPA25).
1. Record the water supply pressure indicated by the
pressure gauge (B12).
2. FULLY OPEN the drain test valve (B6).
3. Record residual water supply pressure indicated by the
pressure gauge (B12).
4. SLOWLY CLOSE the drain test valve (B6).
5. Record the water supply pressure indicated by the
pressure gauge (B12).
6. Readings shall be compared with those made at the time
of the original acceptance tests or with those made at the
time of the last test to determine whether there has been
any deterioration of the water supply.
Note: A main drain test shall be conducted any time the
water supply control valve (D1) is closed and reopened
at the system.
4.8.4 Monthly inspection
1. Gauges on preaction system shall be inspected to
ensure that normal air and water pressures are being
maintained.
2. Verify that the control valves are in the following
condition:
(1) In the normal open or closed position.
(2) Properly supervised.
(3) Accessible.
(4) Free from external leaks.
3. The deluge valve (A1) and associated components shall
be externally inspected to verify the following:
(1) The valve is free from physical damage.
(2) All trim valves are in the appropriate open or closed
position.
(3) The valve seat is not leaking.
(4) Electrical components are in service.
4. Check alarm device (C1) switch by opening the alarm
test valve (B5).
5. Conduct low air pressure supervisory test (refer to
chapter 4.8.1).
6. Visually inspect all NOVEC 1230 system components
and cylinder pressure.
7. Refer any noted problems or deficiencies to authorized
service personnel for correction.
4.8.5 Semi-annual inspection
1. Check main water supply control valve (D1) switch upon
movement of the hand wheel.
2. Check alarm device (C1) switch by opening the alarm
test valve (B5).
3. Check the sprinklers piping for corrosion and damage.
4. Check all piping supports to insure they are tight and
properly secured.
5. Check the discharge nozzle orifice(s) to see if they
are clear with no obstructions.
6. Check to insure that the nozzles are positioned
correctly.
7. Check the quantity of liquid and pressure in the
cylinder (A). If a loss in net weight of more than 5%
or a loss in pressure of more than 10% (refer to
table 4.1), it shall be refilled or replaced.
8. Perform functional test of all components of the
system.
WARNING ! Prior to any functional tests, the
actuator (C) must be removed to prevent cylinder (A)
discharge.
4.8.6 Annual inspection
1. Perform semi-annual inspection.
2. Check all detectors at the remote releasing control
panel.
3. Check all releasing conditions.
4. Check all audible & visual devices at the remote
releasing control panel.
5. Check all HVAC shut down, etc. from the remote
releasing control panel.
6. Check if extinguishment electric actuator (C)
operates after pre-discharge delay.
7. Simulate a low pressure of cylinder (A) by shorting
low cylinder pressure switch (D) terminals.
8. Perform sequence of operation (refer to chapter 4.4).
9. Perform manual emergency release test of the
preaction system.
10. Perform full trip test.
11. Perform drain test.
4.8.7 Long term inspection
1. Alarm valves and their associated strainers, filters,
and restriction orifices shall be inspected internally
every 5 years unless tests indicate a greater
frequency is necessary.
2. Riser check (D2) shall be inspected internally every
5 years unless tests indicate a greater frequency is
necessary.
3. Test on gauge (gauge precision required: less than
3% of the full scale).
4.9 MAINTENANCE
The system shall be maintained in full operation condition
at all times.
All troubles or impairments shall be corrected promptly
consistent with the hazard being protected.
Any penetration made through the enclosure protected by
the clean agent shall be sealed immediately. The method
of sealing shall restore the original fire resistance rating of
the enclosure.

Page 12 of 28 ®DUAL
Integrated Fire Protection System
OWNER'S OPERATION &MAINTENANCE MANUAL
FM-0860-0-31F
Figure 4.4 - FIREFLEX®DUAL (shown without doors)
See figures 4.5 & 4.6 for additional details.
FM-076Z-0-5D-3
Agent storage cylinder
Air compressor
Junction box
TBA & TBB
Air compressor
Isolation switch
Water inlet
Drain outlet
Preaction assembly
Preaction outlet
Clean agent outlet
Releasing circuit
disable switch

®DUAL Page 13 of 28
Integrated Fire Protection System
OWNER'S OPERATION &MAINTENANCE MANUAL
FM-0860-0-31F
Figure 4.5 - FIREFLEX®DUAL - Double interlocked preaction trim
Components:
A1 Deluge valve
B1 Priming valve
B2 Strainer
B3 1/16" Restricted orifice
B4 Spring loaded check valve
B5 Alarm test valve
B6 Drain test valve
B7 Drip check valve
B8 Drain check valve
B9 Pressure operated relief valve (PORV)
B10 Emergency release valve
B11 Prime pressure water gauge & valve
B12 Water supply pressure gauge & valve
B13 Clapper check valve
C1 Alarm pressure switch
C2 Connection to water motor gong (strainer
supplied by contractor)
D1 Water supply control valve
D2 Riser check valve
D3 Main drain valve
F1 N.C solenoid valve (24Vdc)
F3 Pneumatic actuator
D1
D2
A1
B13
F
IRE
F
LEX
DUAL base
(shown without enclosure)
Field connection
to open drain
Field connection
to water supply
Field connection
to sprinklers piping
Hydrostatic test port
(water supply side)
3
From air
supply trim
C1
C1
FM-076Z-0-14C-1
F3
From air
supply trim
1B5
B10
B9
B3
B4
B2
Hydrostatic test port
(system side)
D3
B11
B12
C2
B7
F1
B8
B1
B6

Page 14 of 28 ®DUAL
Integrated Fire Protection System
OWNER'S OPERATION &MAINTENANCE MANUAL
FM-0860-0-31F
Figure 4.6 - FIREFLEX®DUAL - NOVEC 1230 trim
Components:
A Cylinder
B Cylinder valve
C Electric actuator
D Pressure gauge c/w Low cylinder pressure switch
E Liquid level indicator
F Bracket
G Discharge pressure switch (optional)
H Mechanical actuator (optional)
FM-076Z-0-16B-2
FIREFLEX DUAL base
(shown without enclosure)
F
A
F
E
G
C
D
B
H
Field connection
to NOVEC 1230 piping

®DUAL Page 15 of 28
Integrated Fire Protection System
OWNER'S OPERATION &MAINTENANCE MANUAL
FM-0860-0-31F
4.10 OPTIONAL SHUT-OFF VALVE AND SIGHT GLASS
The shut-off valve & sight glass option is intended to be used
for applications where testing of the system operation without
filling the sprinkler piping network is desirable and where it is
critical that all functions of the preaction system be tested
under actual discharge conditions.
Operation of the shut-off valve
Inspection of the system can be implemented without filling the
sprinkler piping system with water.
1. CLOSE the shut-off valve (D4).
2. OPEN the main drain valve (D3).
3. Simulate the operation of the system to open the deluge
valve (A1) (refer to chapter 4.8.6). Verify that water
flows through the sight glass assembly (D5).
4. Once tests are completed, make sure the main drain
valve (D3) is completely CLOSED. Reset the system
(refer to chapter 4.6).
5. FULLY OPEN the system shut-off valve (D4). Reset the
remote releasing control panel.
Figure 4.7 - Shut-off valve option
4.11 OPTIONAL SEMI-FLANGED INLET/OUTLET
When required by the user, FIREFLEX®DUAL unit can be
provided in a semi-flanged configuration.
The semi flanged option provides flanged fittings only on
the water inlet pipe (left side) and on the system riser
outlet. The drain manifold is provided with a threaded
connection (left side). The rest of the fittings are the same
as usual with the main components being provided in the
standard flanged / grooved configuration.
Figure 4.8 - Semi-flange option
Vanne de drain
principal (D3)
Vanne deluge (A1) ou
de contrôle de débit (A2)
Vannes d'essais (D4)
Verre de visée (D5)
Clapet
anti-retour (D2)
Pointer lampe
de poche ici
Vanne principale
d'entrée d'eau (D1)
FM-061H-1-64A
Raccord bridé
à l'extérieur du cabinet
Raccord bridé
à l'extérieur du cabinet
Connection vers
alimentation d'eau
(spécifier le côté)
Bout fileté
Connection vers drain
ouvert (spécifier le côté)
FM-061H-1-66A

Page 16 of 28 ®DUAL
Integrated Fire Protection System
OWNER'S OPERATION &MAINTENANCE MANUAL
FM-0860-0-31F
5. PREACTION AIR SUPPLIES
The sprinklers network of the preaction system uses air
pressure for supervisory purposes. The air supply can be
provided with either internal or external supervised air
supplies.
Two (2) styles of air supplies are available for the
FIREFLEX®DUAL unit depending on needs or
configurations. These air supplies are all factory assembled,
mounted in the cabinet and pressure tested. They are all
located in the top part of the cabinet, hung on mounting rails
above the valve trim. Here is the description of those
options:
♦Air supply Style "A"
See figure 5.3.
Used only for the sprinkler piping network of the preaction
system. Air supply Style "A" includes the air compressor
mounted inside the FIREFLEX®DUAL cabinet with its
supervisory trim and options. Compressor is factory piped
to the sprinkler piping system riser. It is available in three (3)
sizes:
1/6HP
1/3HP
1/2HP
All the above air compressors are oiless piston type without
reservoir and have open, single phase motor with internal
thermal protection and supply voltage of 120Vac, 60Hz or
220Vac, 50/60Hz.
♦Air supply Style "B"
See figure 5.4.
Used only for the sprinkler piping network of the preaction
system, when an external air supply is provided by others
(either a compressor, plant air or dry nitrogen cylinders) and
piped to the air inlet port of the unit. Air supply Style "B"
provides an air pressure maintenance device (APMD) (E5)
trim, factory mounted in the FIREFLEX®DUAL cabinet.
Note: When air supplies Style "B" is selected, the air
supply should be provided andinstalled by the sprinkler
contractor OUTSIDE of the FIREFLEX®DUAL cabinet.
It IS NOT provided with the unit.
5.1 AIR SUPPLY DESIGN AND SELECTION
The air supply compressor should be sized to automatically
establish the total required air pressure in 30 minutes.
External air supply should be provided with an air pressure
maintenance device (air supply Style "B") to regulate and
restrict the flow of supervisory air into the sprinkler system
piping.
WARNING ! Pressures other than the factory pressure
settings may affect the operation of the system.
Note: Selection of the proper air compressor size is the
responsibility of the installing contractor.
Table 5.1 - Compressor selection
Compressor
size
CFM
@
40 psi
120VAC
System
capacity
to pump 40psi
in 30 minutes
220VAC
System
capacity
to pump 40psi
in 30 minutes
1/6 HP 1.33
CFM 110 gallons 90 gallons
1/3 HP 2.61
CFM 215 gallons 170 gallons
1/2 HP 4.06
CFM 335 gallons 270 gallons
5.2 Air compressor AC power connection
(Air supply Style "A" only)
The motor must be protected against short circuit, overload
and excessive temperature rise. Fuses, motor protective
switches and thermal protective switches provide the
necessary protection in these circumstances.
Fuses only serve as a short circuit protection of the motor
(wiring fault), not as protection against overload. Those are
provided and wired by the electrical contractor.
An isolation switch (E15) is also provided in the
FIREFLEX®DUAL cabinet (see figure 6.2) and is factory
wired, allowing powering off the air compressor while some
maintenance work on the unit is done, without disturbing the
rest of the system.
Connect non-energized AC power to the air compressor
input circuit (see figure 5.1).
Figure 5.1 - Wiring of power source
Table 5.1 - Compressor Amp rating
Compressor
size
Amp rating @
120VAC, 60Hz
Amp rating @
220VAC, 50/60Hz
1/6 HP 6.6 A 3.3 A
1/3 HP 6.6 A 3.3 A
1/2 HP 8 A 4 A
NEUTRAL
GROUND
LINE
AC POWER SOURCE INPUT
4
3
2
1
TBB
AIR COMPRESSOR
120 / 220VAC
1/2 HP MAX
FM-076Z-0-7A
This manual suits for next models
2
Table of contents
Other FireFlex Firefighting Equipment manuals
Popular Firefighting Equipment manuals by other brands
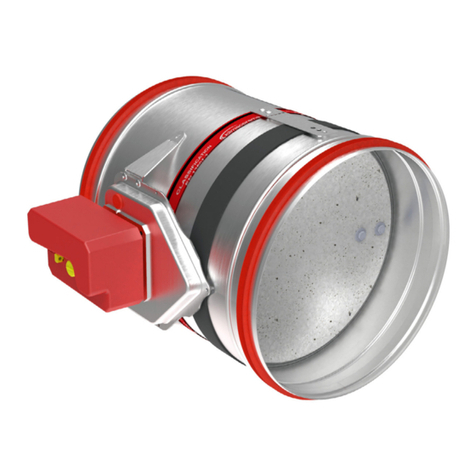
klimaoprema
klimaoprema FDC25 Series product manual

Siemens
Siemens FC361-ZZ Installation
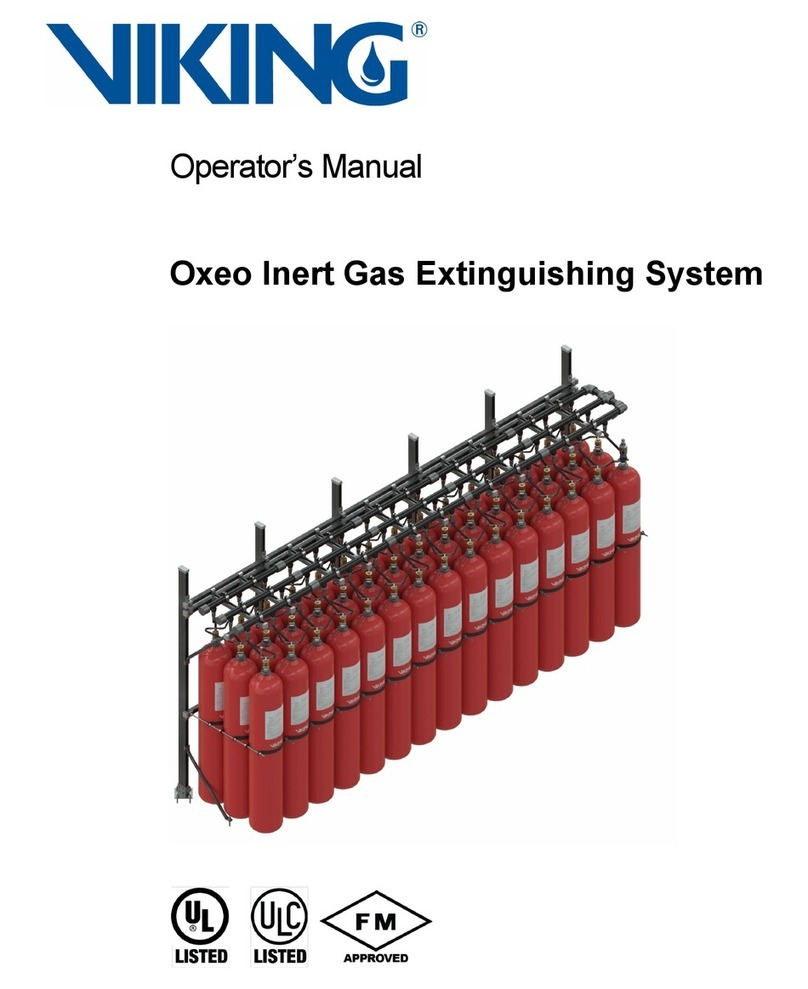
Viking
Viking Oxeo PR LCP Operator's manual
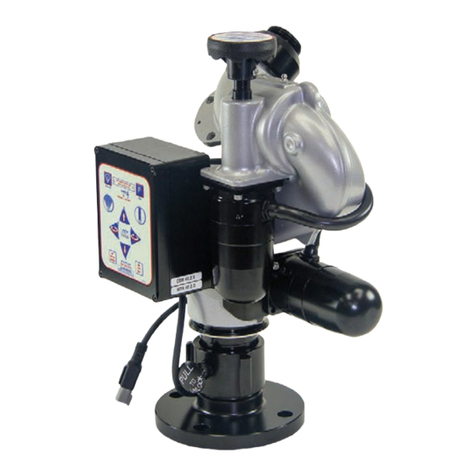
TFT
TFT Tornado Series Instructions for installation, operation and maintenance

Projoy Electric
Projoy Electric PEFS-24V-CN Series installation guide
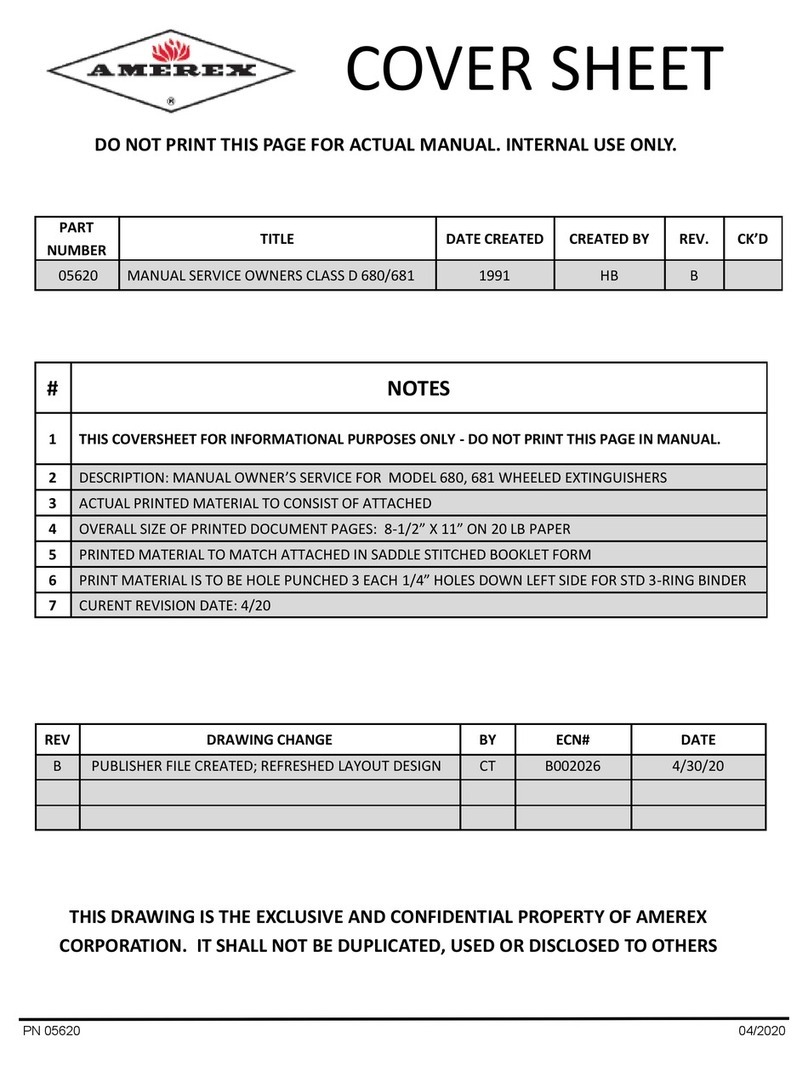
Amerex
Amerex 680 Installation, operating & servicing instructions