FRIULAIR CWE Series Operating instructions

CWE CHILLERS
Air Coooled Liquid Chillers
Water Chillers/Heat Pumps
USER AND MAINTENANCE MANUAL
CWE CHILLERS
BY FRIULAIR

Editions Record
Code
Revision
Edition
Changes
7425MUM541
11
04/2018
Original instructions: ITALIAN
EN Translation of the original instructions

Dear Customer,
Thank you for the trust you have placed in us. Please read this manual carefully to obtain the best
performance from our product.
In order to avoid incorrect operating conditions and danger for the operators, it is essential that you
follow the instructions meticulously as well as the current accident -prevention laws in the country of
use.
Every chiller/heat pump in the CWE/HWE series is tested thoroughly before being packed.
At this stage, checks are made to verify that there are no manufacturing defects and that the machine
performs correctly the functions for which it was designed.
This manual must be kept for future reference and is an integral part of the chille r you have
purchased.
Due to continuous technical development, we reserve the right to make the necessary modifications
without any obligation to give advance notice.
Do not hesitate to contact us if you have any problems or need more information.
The product identification plate, located on the side of the chiller, contains all essential information
about the machine.
You will have to give this data to the manufacturer, or reseller, whenever you request information,
spare parts, etc., during the warranty period.
Removing or tampering with the identification plate will void the warranty.
Warranty conditions:
For 12 months from the commissioning date, and no more than 14 months from the shipping date, any
parts that were originally defective will be repaired or replaced at no charge. Expenses for transport
and travel, room and board for our technicians are excluded.
The warranty excludes any liability for direct or indirect damage to persons, animals and/or property
that are caused by incorrect use or inadequate maintenance and is exclusively limited to
manufacturing defects.
The right to service under the warranty is secondary to your faultless observance of the installation,
use and maintenance instructions in this manual.
The warranty will be voided immediately if the chiller is modified or tampered with, even slightly.
When requesting warranty service, you must provide the data on the product's identification plate.


CONTENTS
1SAFETY RULES ..................................................................................................................1
1.1 DEFINITIONS OF THE SYMBOLS USED ...........................................................................................................1
1.2 WARNINGS ............................................................................................................................................2
1.3 PROPER USE OF THE CHILLER .....................................................................................................................2
1.4 INSTRUCTIONS FOR USING EQUIPMENT UNDER PRESSURE CONFORMING TO PED DIRECTIVE 2014/68/EU............3
2OPERATION AND MAIN COMPONENTS.............................................................................4
2.1 REFRIGERANT CIRCUIT..............................................................................................................................4
2.2 WATER CIRCUIT ......................................................................................................................................5
2.3 FANS.....................................................................................................................................................5
2.4 CONDENSATION CONTROL ........................................................................................................................5
2.5 CONTROL OF THE WATER TEMPERATURE .....................................................................................................5
2.6 PROTECTING THE INTEGRITY OF THE MACHINE..............................................................................................5
2.7 CWE/HWE UNITS:IDENTIFICATION OF THE MAIN COMPONENTS....................................................................6
2.7.1 TANF –Non ferrous atmospheric water circuit ............................................................................................ 6
2.7.2 TP P3 - Pressurized water tank with single P3 pump .................................................................................... 6
2.8 SPARE PARTS ..........................................................................................................................................7
3INSTALLATION .................................................................................................................8
3.1 TRANSPORT............................................................................................................................................8
3.1.1 Handling the unit with a forklift truck or pallet jack ..................................................................................... 8
3.1.2 Lifting with belts and tubes........................................................................................................................... 8
3.2 STORAGE ...............................................................................................................................................8
3.3 PLACE OF INSTALLATION ...........................................................................................................................9
3.3.1 Installation spaces......................................................................................................................................... 9
3.4 WATER CONNECTIONS ...........................................................................................................................10
3.4.1 Recommended water system ..................................................................................................................... 11
3.4.2 Use of ethylene glycol as a winter anti-freeze............................................................................................ 11
3.4.3 Charging the water circuit........................................................................................................................... 11
3.5 ELECTRICAL CONNECTIONS......................................................................................................................12
3.5.1 Connecting a remote on/off switch and a remote alarm indicator light .................................................... 12
4PRELIMINARY CHECKS AND START-UP............................................................................ 13
4.1 PRELIMINARY CHECKS AND PREPARATION FOR THE FIRST START-UP ................................................................13
4.2 START-UP ............................................................................................................................................13
4.2.1 Start-up under critical conditions ............................................................................................................... 14
4.3 TURNING OFF THE UNIT ..........................................................................................................................14
5ELECTRONIC CONTROLLER.............................................................................................. 15
5.1 MAIN FUNCTIONS OF THE ELECTRONIC CONTROLLER BUTTONS AND MEANINGS OF THE ICONS ............................15
5.2 SWITCHING ON/OFF ..............................................................................................................................16
5.3 CONTROLLING WATER TEMPERATURE .......................................................................................................16
5.4 CHANGING THE COOLING SET POINT .........................................................................................................17
5.5 CHANGING THE HEATING SET POINT..........................................................................................................18
5.6 DISPLAY OF INPUTS AND OUTPUTS............................................................................................................18
5.7 ALARMS ..............................................................................................................................................18
5.7.1 Displaying and resetting alarms.................................................................................................................. 18
5.7.2 Table of alarm codes................................................................................................................................... 19

5.7.3 Displaying alarm history.............................................................................................................................. 19
5.8 PARAMETERS CHANGING ........................................................................................................................20
5.9 SETTING THE DATE AND TIME ..................................................................................................................20
5.10 LOW WATER TEMPERATURES (<32°F//0°C)..............................................................................................20
6SAFETY DEVICES............................................................................................................. 21
6.1 CALIBRATION OF THE SAFETY DEVICES AND TYPE OF REARM ..........................................................................21
6.2 REARMING THE HIGH-PRESSURE PRESSURE SWITCH .....................................................................................22
7OPERATING LIMITS ........................................................................................................ 23
7.1 MINIMUM WATER FLOW ........................................................................................................................24
8SEPR - SEASONAL ENERGY PERFORMANCE RATIO According to Commission Regulation (EU)
2016/2281 ....................................................................................................................... 25
9MAINTENANCE, INSPECTIONS AND PERIODIC CHECKS .................................................... 26
10 TROUBLESHOOTING....................................................................................................... 27
11 DISMANTLING THE CHILLER............................................................................................ 30
12 WATER DIAGRAMS ........................................................................................................ 31
13 REFRIGERANT DIAGRAMS .............................................................................................. 34
14 DIMENSIONAL DRAWINGS ............................................................................................. 36

1
7425MUM541 Model: CWE/HWE - Use and Maintenance Manual Rev. 11
1
SAFETY RULES
1.1 DEFINITIONS OF THE SYMBOLS USED
Read this use and maintenance manual carefully before performing any repairs on the
chiller.
Warnings of a general character; risk of danger or possibility of damaging the machine,
pay particular attention to the phrase following this symbol.
Risk of electrical danger; the phrase highlights conditions that could be fatal. Follow the
instructions provided meticulously.
Risk of danger; component or system under pressure.
Risk of danger; component or system that can reach high temperatures during operation.
Risk of danger; it is absolutely forbidden to use water to extinguish fires near or on the
chiller.
Risk of danger; it is absolutely forbidden to operate the machine with the panel
open.
Service that can be performed by the machine’s operator, if qualified (1).
Water input connection point.
Water output connection point.
Dispose of each type of material in accordance with the requirements of the country of
use.
NOTE
Phrases to be emphasized that do not contain safety rules.

2
7425MUM541 Model: CWE/HWE - Use and Maintenance Manual Rev. 11
This chiller has been carefully designed and constructed to be environmentally
friendly:
Refrigerants without CFC;
Expanded foam insulation without CFC;
Energy-saving techniques;
Reduced noise;
The chiller and its packing materials are recyclable.
In order not to hinder our efforts, the user is required to obey the simple ecological
warnings indicated by this symbol.
(1) These are persons with the experience, technical preparation and knowledge of standards and
regulations who are qualified to perform the necessary actions and able to recognize and avoid
possible dangers while handling, installing, using and maintaining the machine.
1.2 WARNINGS
Only qualified persons may use and maintain electrically-powered equipment.
Before commencing maintenance operations ensure no parts of the machine are
live and it cannot be re-connected to the electrical power supply.
These chillers contain R410A refrigerant fluids. Service of the refrigerant circuit must be
performed by specialized personnel using proper tools.
Any modifications to the machine or related operating parameters not previously
verified and authorized by the Manufacturer may be hazardous and will invalidate
the guarantee.
Do not use water to extinguish fires near or on the chiller.
1.3 PROPER USE OF THE CHILLER
CWE/HWE units are monobloc water chillers/heat pumps with air-condensation.
They are intended for use in industrial process or air-conditioning systems requiring chilled water.
Any other use is considered improper.
The manufacturer is not liable for damage resulting from inappropriate use; in all cases, the user is
liable for any resulting hazards.
Proper use requires conforming to the installation conditions and, in particular:
Power voltage and frequency;
Pressure, temperature and flow-capacity of the incoming water;
Surrounding temperature.
The chiller has been tested and completely assembled. The user must only make the connections to
other systems, as described in the chapters that follow.

3
7425MUM541 Model: CWE/HWE - Use and Maintenance Manual Rev. 11
1.4 INSTRUCTIONS FOR USING EQUIPMENT UNDER PRESSURE CONFORMING TO
PED DIRECTIVE 2014/68/EU
The proper use of equipment under pressure is an essential prerequisite for ensuring safety.
To this end, the user must proceed as follows:
Use the equipment within the temperature range outlined in the operating limits on the
manufacturer's plate;
Do not solder on the exchangers or refrigerant fluid pipes;
Do not install the equipment in insufficiently ventilated rooms, areas expo sed to sources of
heat or near inflammable substances;
During operation, the equipment must not be subjected to vibrations that could cause fatigue
failures;
Keep the documentation attached to the equipment (user manual, declaration of conformity,
etc.) for future reference;
The maximum operating pressure shown on the manufacturer's plate must not be exceeded.
The user is responsible for fitting appropriate safety/control devices.

4
7425MUM541 Model: CWE/HWE - Use and Maintenance Manual Rev. 11
2
OPERATION AND MAIN COMPONENTS
2.1 REFRIGERANT CIRCUIT
Operation of the CWE/HWE chillers/heat pumps is based on a vapour compression cycle implemented
within the chiller circuit and made up of the following components - evaporator, compressor,
condenser and thermostatic expansion valve.
Evaporator: this is a braze-welded plate exchanger that exchanges heat between water and a
refrigerant fluid without their coming into contact with each other. It consists of corrugated stainless
steel plates braze-welded to each other with copper. The evaporator is protected against a lack of
water by a differential pressure-switch and against the formation of ice by an anti-freeze system
managed by the chiller's electronic controller.
Compressor: this compresses the vapours coming from the evaporator and sends them to the
condenser at a higher pressure. The CWE/HWE series has scroll compressors which are characterized
by low noise and vibration levels. They are protected by thermal magnetic circuit breakers and a
temperature sensor inside the motor windings.
Condenser: heat exchanger with copper pipes and aluminum fins which enables heat exchange
between the refrigerant and the air. It condenses the refrigerant gas by transferring condensation heat
from the refrigerant gas to the air (which flows to the outside). As a result high pressure liquid
refrigerant is produced.
Thermostatic expansion valve: this reduces the pressure of the refrigerant liquid coming from the
condenser and sends it to the evaporator. This valve modulates the flow of refrigerant in such a way
as to maintain the constancy of the superheating of the gas exiting to the evaporator under its various
working conditions and, thus ensures that the flow of gas entering the compressor contains no liquid.
Thanks to these components, the vapour-compression cycle works as follows: the refrigerant liquid
evaporates in the evaporator, chilling the water; the refrigerant vapours are then aspirated from the
compressor, which compresses them and sends them to the condenser under high pressure; here,
thanks to a flow of forced air from the fans, the high-pressure refrigerant gas is cooled, making it
condensed and undercooled.
The flow of refrigerant liquid then passes through the lamination valve (thermostatic expansion
valve), which drastically reduces its pressure: the refrigerant liquid retu rns to the evaporator at a
reduced pressure where it again evaporates, taking heat from the water.
Heat pump operation: In addition to cooling water the heat pump models (HWE) also heat water.
This is made possible via a switchover valve which intercepts the hot high pressure gas produced by
the compressor and sends it to the plate exchanger (which the water flows through). Condensing the
refrigerant heats the water. The flow of condensed refrigerant then passes through the thermal
expansion valve, which reduces the pressure drastically - the reduced pressure liquid refrigerant enters
the finned tube exchanger (which the air flows through) where it can evaporate by drawing heat from
the outside air. The switchover valve intercepts the evaporated refrigerant and sends it for compressor
suction.
De-icing: When the heat pump is operating condensation may freeze on the external finned tube
exchanger (which acts as an evaporator in the heat pump mode) as a result of certain external air
conditions (e.g. high level of humidity). This layer of ice impedes heat exchange and must be
removed, therefore the machine switches operation mode from heat pump to chiller for a few minutes
when appropriate, sending the hot refrigerant to the external finned tube exchanger. The heat from the
hot refrigerant melts the ice. During this de-icing phase the water drained from the exchanger is
collected in the relevant tank and drained out of the machine.

5
7425MUM541 Model: CWE/HWE - Use and Maintenance Manual Rev. 11
2.2 WATER CIRCUIT
The water circuit mainly consists of: pump, evaporator, tank, and expansion vessel.
The water flows first into the evaporator, where it is chilled, and then to the tank; afterwards it is
aspirated by the pump, which sends it to the system.
A differential pressure switch on the evaporator checks that the flow of water is sufficient and stops
the compressors if the flow-capacity of the water does not ensure the good functioning of the
exchanger.
An automatic vent valve removes any air bubbles in the circuit.
A fine mesh metal filter at the entrance to the evaporator catches any solid residues that could damage
the evaporator.
Units can be equipped with pumps with different head values (see equipment with pumps P2, P3 or
P5).
A manometer and safety valve complete the unit's water circuit.
2.3 FANS
The fans force air through the condenser’s fins to remove the heat from the condensation of the
refrigerant gas, thus limiting the pressure inside the condenser.
CWE/HWE chillers use external-rotor axial fans with thermal protection inside the motor winding.
2.4 CONDENSATION CONTROL
When the ambient air temperature decreases air flow cooling capacity increases considerably,
lowering the pressure within the condenser. The fans are switched off (or slowed down) to reduce air
flow and prevent the condensation pressure going below the acceptable limits for correct chiller
circuit operation.
The fans are actually managed electronically by the condensation pressure, enabling correct machine
operation even when the external air temperature is very low (see section 8 Operating limits).
2.5 CONTROL OF THE WATER TEMPERATURE
The purpose of the chiller is to maintain the temperature of the water produced within a desired
interval as the load on the system varies; this is handled by an electronic controller and a temperature
probe that turn the compressor on and off appropriately (also see paragraph 6 Temperature
regulation).
2.6 PROTECTING THE INTEGRITY OF THE MACHINE
In addition to controlling the temperature, the electronic controller uses pressure switches, thermostats
and timers to prevent and handle situations that could compromise the integrity of the machine (also
see Chapter 7 Safety Devices).

6
7425MUM541 Model: CWE/HWE - Use and Maintenance Manual Rev. 11
2.7 CWE/HWE UNITS:IDENTIFICATION OF THE MAIN COMPONENTS
2.7.1 TANF –Non ferrous atmospheric water circuit
2.7.2 TP P3 - Pressurized water tank with single P3 pump
04 High pressure switch
06 Compressor
08 Condenser
09 Fan
10 Filter
14 Water filter
17 Electronic controller
18 Evaporator
20 Liquid ricever
22 Disconnector switch
23 High pressure manometer
24 Low pressure manometer
31 Safety valve
34 Sight glass
35 Thermostatic valve
37 Pressure transducer
45 Water manometer
46 Four-way valve
47 Vent valve
48 Expansion vessel
61 Power input
68 On/off light
69-B Selector Local/0/Remote
69-A Heat/Cold selector
83 Pressure plug
85 Solenoid valve
90 Pump
91 Tank
94 Water filler
95 Water inlet
96 Water outlet
97 Drain

7
7425MUM541 Model: CWE/HWE - Use and Maintenance Manual Rev. 11
2.8 SPARE PARTS
Spare parts list is printed on a dedicated sticker applied inside the chiller. On this sticker each spare
part is identified with its ID Number and related Spare Part Number. Here below the cross reference
table between ID Number and exploded drawings Ref. With their description and quantity installed
inside chillers.
NOTE To order the suggested spare parts or any other part, it is necessary to quote the data
reported on the identification plate.

8
7425MUM541 Model: CWE/HWE - Use and Maintenance Manual Rev. 11
3
INSTALLATION
3.1 TRANSPORT
The units are provided with protective corner sections in cardboard and transparent film.
After checking that the packing is undamaged, position the unit near the installation site and unpack
it. The units can be handled using tubes and belts or a forklift truck.
Always keep the chiller vertical: turning it upside down can irreparably damage several parts
of the unit.
Handle with care. Violent falls can cause irreparable damage.
3.1.1 Handling the unit with a forklift truck or pallet jack
The centre of the machine is approximately its centre of gravity. In any case, when handling
the machine with a forklift truck or pallet jack, always check its stabi lity before lifting.
3.1.2 Lifting with belts and tubes
Base supports that can accommodate bars to raise the units are provided.
Use steel tubes with a diameter of 1¼” and at least 0,12 in//3 mm thick and long enough to project at
least 9.85÷11,81 in//250÷300 mm from both sides of the machine's profile.
Lock the belts so that they won't slip off during lifting (see figure).
3.2 STORAGE
Protect the machine from bad weather, even if packed.
Always keep the chiller vertical, even when in storage. Turning it upside down can irreparably
damage several parts of the unit.
If not used, the chiller can be stored packed in an enclosed place, free of dust, with a maximum
temperature of 50 °C/122°F and specific humidity of no higher than 90%.
The packing material is recyclable.
Dispose of each type of material in accordance with the requirements in the country
of use.

9
7425MUM541 Model: CWE/HWE - Use and Maintenance Manual Rev. 11
3.3 PLACE OF INSTALLATION
The CWE/HWE unit can be installed either inside or outside.
To determine the best place to install the unit, it is important to consider the following aspects:
The dimensions and source of the water pipes;
The location of the electricity;
The solidity of the support surface;
Avoid any obstacles to the flow of the fan which could cause the recirculation of air t o the
condenser;
Avoid the possible reflection of sound waves: (do not install in narrow or tight spaces);
Provide access for maintenance or repair (see paragraph 3.3.1 Installation spaces);
The air temperatures in the area selected for installation (see Chapter 8 Operating Limits).
Attention! If the machine is installed outside, it could find itself at a temperature lower than
32°F//0°C, when stopped; the formation of ice could damage the evaporator. If
you do not intend to drain the machine during the winter, you must add anti-
freeze to the water circuit (see paragraph 3.4.2 Use of ethylene glycol as a
winter anti-freeze).
3.3.1 Installation spaces
To ensure the good functioning of the unit and access for maintenance, you must respect the minimum
installation space shown in the figure in this paragraph.
The exit of air from the fans must not be obstructed.
In any case, avoid all situations in which hot air can circulate between the output of the fans and the
intake of the machine.
The left or right side of the units can be placed against a wall (*).

10
7425MUM541 Model: CWE/HWE - Use and Maintenance Manual Rev. 11
3.4 WATER CONNECTIONS
Connect the machine to the water pipes following the instructions located near its water fittings (see
figures).
Water input to the
machine
Water exit from the
machine
NOTE It is a good rule that the diameters of the arriving and departing pipes be not less than the
water fittings.
We recommend an extraordinary cleaning of the mechanical water filter after the machine
has been running for the first week (also see Chapter 9 Maintenance, inspections and
periodic inspections).
With heat pump models it is advisable to collect
the water produced from de-icing by connecting
the condensation collection pipe of the unit to an
appropriate drain.
Diameters of the in/out water fittings
CWE/HWE models
013 ÷ 026
036 ÷ 068
075 ÷ 140
50 Hz version
1” GAS FM
1½ ” GAS FM
2” VIC
60 Hz version
1” NPT FF
1½ ” NPT FF
2” VIC

11
7425MUM541 Model: CWE/HWE - Use and Maintenance Manual Rev. 11
3.4.1 Recommended water system
The CWE/HWE units can be provided with a pump tank, expansion vessel, safety valve, filter
(standard), and automatic venting valve, however it is advisable to also equip the water circuit with:
A mechanical filter and a check valve upstream from the charging tap;
An air vent at the highest point of the system;
A drain tap in the lowest point of the system;
Manometers and thermometers at the machine’s water input and output to check its
functioning;
Vibration damping joints on the pipes to avoid the transmission of vibration to the system.
In the case of water circuits with considerable capacity, we recommend checking whether it is
necessary to supplement the expansion vessel possibly on the unit with another additional one.
Attention! Never work with an open flame near or inside the unit when making connections
to the water system.
Important! If the machine is stopped during the winter, you must empty the system (or just
the chiller) to avoid frost damage; any water remaining in the pump must be
drained using the screw on the lower part of the pump housing (see figure).
3.4.2 Use of ethylene glycol as a winter anti-freeze
Instead of emptying the system in winter, you can charge the system with a mixture of water and a
suitable percentage of ethylene glycol, chosen as a function of the lowest expected temperature of the
outside air.
Percentages of ethylene glycol recommended as a function of the expected temperature of the outside air
Outside air temperature [°C]
0
-5
-10
-12
-15
-20
Outside air temperature [°F]
32
23
14
10.4
5
-4
Percentage of ethylene glycol [%]
10
15
20
25
30
40
Attention! Maximum concentration of ethylene glycol allowed: 40%.
3.4.3 Charging the water circuit
Check that the drain taps are turned off;
Open all the system’s vent valves;
Turn on the system's shut-off devices;
Start filling by slowly turning on the system's water-charging tap;
When water starts coming out of the vent valves, close them and continue charging until the
manometer shows at least 1 bar;
Bleed the pump using the venting screw on the Archimedes screw;
Check the system level again;
Check for any leaks by looking at the manometer and inspecting the circuit.
Pump drain screw
Pump venting screws

12
7425MUM541 Model: CWE/HWE - Use and Maintenance Manual Rev. 11
3.5 ELECTRICAL CONNECTIONS
The machine must be connected to the electricity following the electrical diagram and
conforming to the current laws and regulations in the place of installation.
The voltage, frequency and number of phases must conform to the data shown on the
machine's identification plate;
The power supply voltage must not vary by more than ±10% from its nominal value ;
The frequency must not vary by more than ±1% from its nominal value (±2% for brief
periods);
The imbalance between power phases must be <2%;
Upstream from the electrical panel, install a differential switch (IDn=0,03A) (main power
switch) and slow-blow fuses with the specifications shown on the electrical diagram;
Use wires of the section shown on the electrical diagram.
Attention! Never change the internal electrical connections, as the warranty will be
immediately voided.
Important! Screw the wires solidly to the terminal strip of the cut-off switch and lock the
wire with a cable-gland.
Important! Make the cable entering the machine enters the cable-gland from below: this
prevents rain from dripping inside the machine.
Important! The earth connection is mandatory: connect the earth wire to the terminal
provided in the electrical panel.
The ground wire must be longer than the other wires so that it will be the last one to be pulled if the
device holding the cable loosens.
3.5.1 Connecting a remote on/off switch and a remote alarm indicator light
A remote on/off switch can be connected to terminals in the electrical panel: there are 24V between
these two terminals.
To enable a remote switch, move the I/O/REM switch to REM.
An alarm indicator light can be connected to terminals (clean contact) in the electrical panel.
Consult the electrical diagram.

13
7425MUM541 Model: CWE/HWE - Use and Maintenance Manual Rev. 11
4
PRELIMINARY CHECKS AND START-UP
4.1 PRELIMINARY CHECKS AND PREPARATION FOR THE FIRST START-UP
Before starting up the unit, it is a good idea to do the following:
Check that the water shut-off valves are open;
Check that the pressure shown on the manometer with the pumps stopped is at least 1 bar (for
closed water systems);
Check that the surrounding temperature is in the range for the machine to function (see
Chapter 8 Operating Limits);
Check that the cut-off on the electrical panel of the machine is open (0 position);
Check that the run/stop switch (I/O/REM) in the electrical panel is in the 0 position;
Check that the mains voltage matches the voltage on the machine's identification plate with a
tolerance of ±10%;
Close the main power supply switch;
Close the cut-off switch on the machine's electrical panel (I position).
This puts the machine under voltage without starting it up.
Attention! Apply voltage to the machine at least two hours before start-up to give the
heating elements in the compressor housing time to heat the oil inside.
Our company reserves the right of not recognizing the warranty in case of premature
breaking down of the compressor, if it is established that this operation is not normally
executed by the installer / user of the plant.
The heating elements limit the quantity of refrigerant dissolved in the oil and prevent the oil from
migrating when the compressors start.
Before start-up, check that the temperature of the lower part of the compressors is at least 50-59°F
[10-15°C] higher than the surrounding temperature.
4.2 START-UP
To proceed to start-up:
1. Move the remote on/off switch (I/O/REM) on the door of the electrical control panel to position 1;
2. Press key for 4 seconds. The led will flash and turn off, the chiller will switch on;
Electronic controller
3. Check that the alarm symbol does not light up on the electronic controller;
Attention! At the first start-up there could be an alarm for an incorrect sequence of the R-S-T
phases, indicated by the initials AC21.
This safety system prevents the compressor from turning in the wrong direction.

14
7425MUM541 Model: CWE/HWE - Use and Maintenance Manual Rev. 11
In this case, turn on the main power supply switch upstream from the machine
and reverse the two phases immediately downstream from the main switch.
Attention! Never reverse the wires downstream from the main switch on the
electrical panel because doing so risks changing the correct sequence
of other devices, such as, for example, the pump and fans.
Repeat the steps from point 1.
4. Check that the pump has started (the pump icon lights up) and check the water pressures upstream
and downstream from the machine on the manometers previously installed;
5. Wait for the electronic controller to verify that the water flow is constant through the signal from
the differential pressure-switch; if the differential pressure-switch intervenes (alarm code AL03),
vent the system, check that the shut-off taps and the functioning of the pump are turned on;
6. Wait for the compressors to start.
4.2.1 Start-up under critical conditions
The consequence of starting up under critical conditions could be the intervention of the high -pressure
pressure switch (to rearm the high-pressure pressure switch, see paragraph 6.2 Rearming the high-
pressure pressure switch).
To overcome this problem, you will have to reduce the thermal load on the machine by shutting off
some of the uses or, if this is not possible, by reducing the flow of water into the evaporator: partially
close the output tap from the chiller and restart the machine.
Operate the chiller under these conditions until the water temperature gradually returns within
operating limits; then, you can turn on the tap completely.
4.3 TURNING OFF THE UNIT
For turn off the controller, press key for 4 seconds The led will flash and turn on, the chiller will
switch off or move the run/stop I/O/REM switch to the O position (see paragraph 5.2 Switching on/off).
Attention! It is important not to turn the unit off using the main power supply switch or the
cut-off on the machine's electrical panel because this would not provide for the
delayed power-off of the pump regarding the power-off of the compressors, with
the risk of damaging the evaporator; in addition, it would prevent the func tioning
of the heating element in the compressor housing.
Other manuals for CWE Series
1
This manual suits for next models
39
Table of contents
Other FRIULAIR Chiller manuals
Popular Chiller manuals by other brands
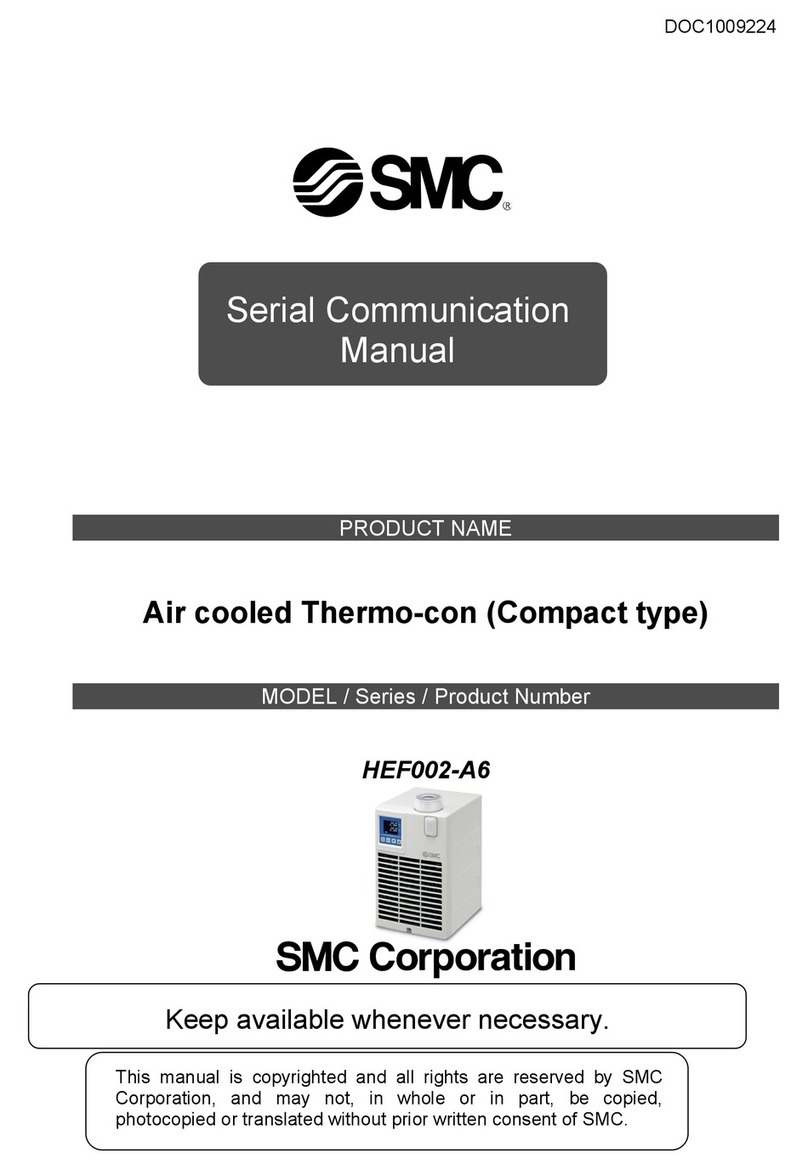
SMC Networks
SMC Networks Thermo-con HEF002-A6 manual
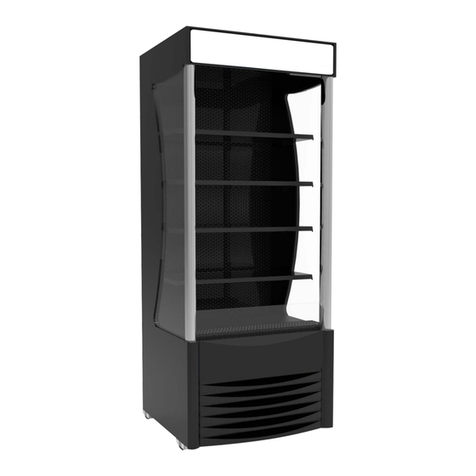
KoolMore
KoolMore OF-500 Instructions for use
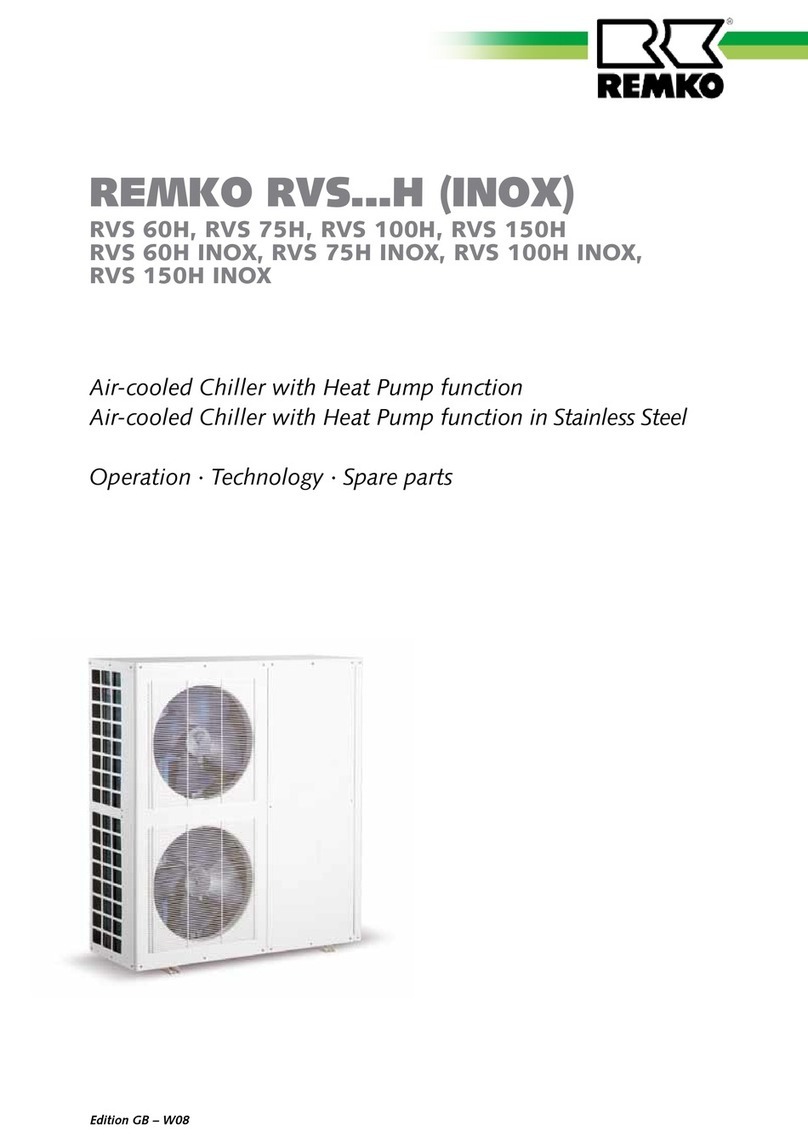
REMKO
REMKO RVS***H Series Operation manual
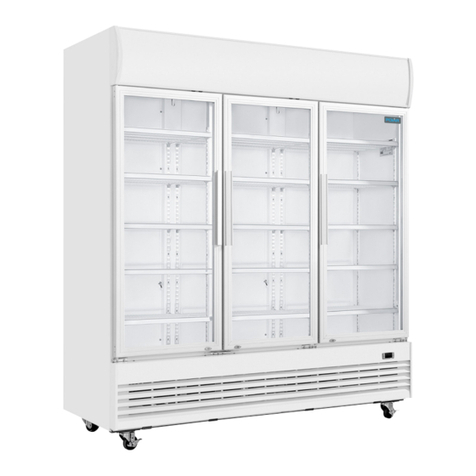
Polar Electro
Polar Electro GE769 instruction manual
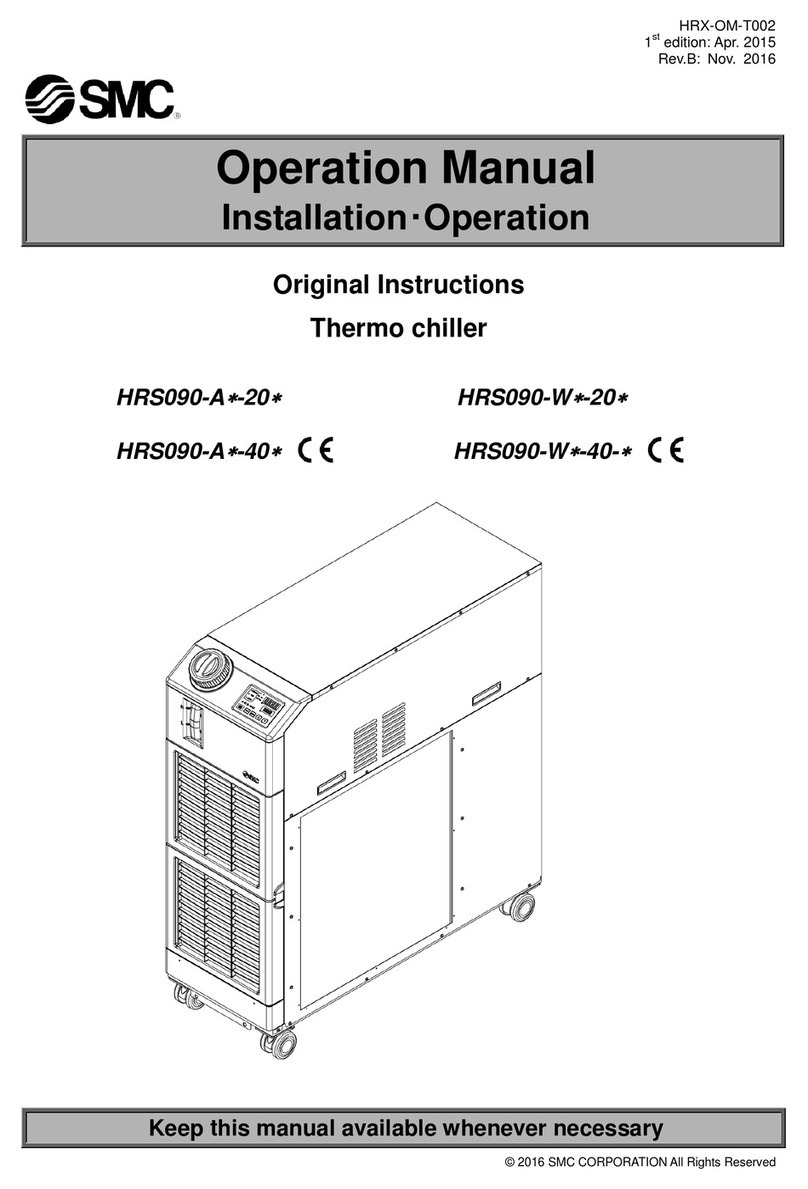
SMC Networks
SMC Networks HRS090-A...-20 Series Original instructions

Hydrofarm
Hydrofarm ACTIVE AQUA AACH50 instructions