Geca Tecnocontrol RG User manual

English
RGD032-5B-SSV
132
123
4
Gas Regulator with SSV:
RG = Attacchi filettati
RGD=Attacchi flangiati
DIMENSIONI:
032= 1" 1/4
040= 1" 1/2
050= 2”
SSV:
Slam Shut Valve
PRESSIONE di
MASSIMA:
_ = 500mbar
5B = bar
Depending on which model, GAS REGULATOR SSV are marked by laser with
their technical characteristics. (Fig.1):
MARKING
Fig.1
Pe max: 5bar Body: 1"1/4
Pd: 60 I130bar Upso: 30-60mbar
T. amb.: -20 +60°C Opso: 150-250mbar
Group: 2
S/N 188801
RG032-5B-SSV
Any maintenance operation must be performed by qualified personnel.
This device must be installed in accordance with the laws in force.
The GAS REGULATOR SSV is normally installed before the user. It can be installed
in a horizontal position and it must be installed with the arrow on the body towards
the user. (Fig.2).
N.B. Install the GAS REGULATOR SSV away from atmospheric agents.
INSTALLATION AND POSITIONING
4
GENERAL DESCRIPTION
GAS REGULATOR with SSV
Impulse
socket Distance:
Impulse socket /
Gas regulator SSV
Copper Tube
Cod.
5bar
SPY2-15
SPN2-15
SPR2-15
SPBK2-15
SPG2-15
SPBR2-15
Color
YELLOW
NEUTRAL
RED
BLACK
GREEN
BROWN
RANGE SPRING (mbar)
Range (mbar)
6 I22
10 I27
28 I70
60 I130
120 I300
220 I480
Gas Regulator
with Slam Shut Valve integrated
for Over (OPSO) and Under (UPSO) pressure 500mbar/5bar
Mod. RG & RGD
Cod.
SPY2-U
SPN2-U
Color
YELLOW
NEUTRAL
Range (mbar)
5 I14
30 I 60
Cod.
SPB2-O
SPG2-O
SPBR2-O
Color
BLACK
GREEN
BROWN
Range (mbar)
150 I250
300 I500
500 I700
UPSO SPRING (mbar)
OPSO SPRING (mbar)
GAS REGULATOR SSV are single-stage gas regulators with pressure blocking
device.
GAS REGULATOR SSV can be installed in systems with automatic gas burners
and in industrial gas distribution systems.
GAS REGULATOR SSV have three diaphragms fitted inside them: a operating
diaphragm 9, a compensation diaphragm 13 and a safety diaphragm 16
(refer to Fig. 3).
A breather pipe and external discharge is not necessary because the safety
membrane avoids more than 30 dm3 / h, point 3.3.2 of the UNI-EN88-1: 2011
Norms.
The GAS REGULATOR SSV comply with the ATEX Directive 2014/34 / EU as
device of group II, category 2G and as device of group II, category 2D; for this
reason it is suitable for installation in zones 1 and 21 (as well as in zones 2 and
22) as classified in Annex I to Directive 99/92 / EC.
They are NOT suitable for installation in zones 0 and 20 as defined in the Direc-
tive 99/92 / EC.
We recommend checking the CEI EN 60079-10-1 standard to determine the
qualification and extension of hazardous areas.
GAS REGULATOR SSV are equipped with:
• OVER PRESSURE blocking device (SSV) that blocks the pressure flow
when the output pressure of the GAS REGULATOR SSV exceeds the set limit
(OPSO).
• UNDER PRESSURE blocking device that blocks the pressure flow when
the output pressure of the GAS REGULATOR SSV is lower than the set limit
(UPSO).
WARNING: The GAS REGULATOR SSV will remain operated only if the pres-
sure downstream is between the maximum value (OPSO) and the minimum
value (UPSO) set.
Fig.3Fig.2
• Before proceeding with the installation, make sure that the gas supply has been
shut-off.
• Check that the line pressure does NOT EXCEED the maximum pressure stated
on the LABEL OF REGULATOR SSV.
• Make sure to respect the gas flow indicated by the arrow on the body of the
GAS REGULATOR SSV which must always be directed towards the user.
• It is necessary to install an impulse socket for the shut-off valve with G 1/8
“connection and an impulse socket at the output of the GAS REGULATOR SSV
at a distance of 5 times the nominal diameter of the pipe from the output of the
same (Fig.3).
The two impulse sockets must be connected to each other with a copper tube
with G 1/8 “connection.
GAS REGULATOR SSV if installed according all the indications of the following
document it will not constitute a source of danger.
Only in particular fault conditions it will they be able to release flammable sub-
stances into the environment.
If the GAS REGULATOR SSV are installed in critical area (places not protected,
lack of servicing, lacking availability of ventilation) and, especially in presence,
close to the regulator, of potential sources of primer and/or dangerous devices
during the normal working because susceptible to origine electric arcs or sparks,
it is necessary to value before the compatibility between the regulator and these
devices, we recommend removing the protective cap and connecting a tube with
M10X1 connection. Place the other end of the tube outside the room. In this case
the exhaust gas will be expelled into the external environment.
Make sure that debris or scraps have been created inside the network piping.
Carefully check the connections made and check the tightness of the system.
GAS
REGULATOR
Slam Shut Valve
GAS REGULATOR 500mbar/5 bar
SLAM SHUT VALVE
Cod.
500mbar
SPY2-5
SPN2-5
SPR2-5
SPBK2-5
SPG2-5
SPBR2-5

ASSEMBLY OVERVIEW SETTING
1 Seal cap
2 O-Ring
3 Spring compressor
4 Washer
5 Screws
6 Vent cap
7 Upper cover
8 Plastic Washer
9 Safety diaphragm
10 Calibrated nozzle
11 Washer
12 Disc
13 Compensation diaphragm
14 Upper Bush
15 Disc
16 Working diaphragm
17 Lower bush
18 Cap
19 O-Ring
20 Body
21 Sensing Tube
22 Shaft
23 Seal washer
24 Shaft-Insert Assembly
25 Spring
26 Nut
27 Gasket
28 Cover
29 O-Ring
30 Release button
31 Spring
32 Fitting
33 O-Ring
34 Body
35 O-Ring
36 Reset knob
37 Seeger
38 O-Ring
39 Release shaft
40 Levers assembly
41 Spring
42 Shaft-membrane Assembly
43 O-Ring
44 Insert
45 Cap
46 Screws M4
47 Washer
48 Spring UPSO Min
49 Insert
50 Spring OPSO Max
51 Spring compressor UPSO
52 Spring compressor
53 O-Ring
54 Seal Cap
Fig.4
2
13
12
16
1
3
4
5
6
7
8
10
11
5
15
20
21
23
27
9
17
22
29 48 51
53
54
45 47 49 50 52
36 37 34
35
32
30
5
28
25
24
19
18
14
26
223mm
238mm
197mm
415mm
DIMENSION
GAS REGULATOR SSV do not require any specific maintenance. Yearly periodi-
cal inspection of regular working
If necessary, before carrying out any operation with the GAS REGULATOR SSV,
make sure that gas supply has been shut off.
Any maintenance operation must be performed by qualified personnel.
MAINTENANCE
50
48
54
52
49
47 51
53
UPSO adjustment screw
Remove to adjust
OPSO adjustment screw
PRESSURE SETTING
Unscrew the Seal cap 1to access to the Spring compressor 3(Fig.4).
The outlet pressure is regulated by rotating the Spring compressor (Fig.4).
Using a 10mm Allen key, turn the Spring compressor 3in a clockwise direction
to increase the pressure and in an anticlockwise direction to reduce the pressure.
After making the adjustment, replace the Seal cap 1.
1" 1/2
4,52
2"
4,4
DIMENSION
WEIGHT (Kgs)
1" 1/4
4,57
Release button
30
MANUAL RESET
Make sure there is pressure inside the system and proceed as follows:
- Close the tap downstream of the GAS REGULATOR SSV.
- Unscrew and pull down the Reset knob 36 .
For pressures over 2 bar, hold the Reset knob down until the pressure balance is
created inside the system which allows the SSV to be reset (This may also occur
after several seconds). If this is not the case, it means that the outlet pressure of
the GAS REGULATOR SSV is lower than the minimum set pressure (UPSO).
RELEASE BUTTON
To stop the gas flow, firmly press the RELEASE button 30 .
36
REGULATOR GAS SSV
The manufacturer reserves the right make any aesthetic or functional change without notice and at any time.
dis.8034095 Cod.2.710.XXXX MADE IN ITALY
GECA Srl
Via E. Fermi, n°98 25064 Gussago (BS)
Italy Tel. +39 030 3730218
www.gecasrl.it
Tecnocontrol Srl
Via Miglioli, n°47 20090 Segrate (MI)
Italy Tel. +39 02 26922890
www.tecnocontrol.it
TECHNICAL SPECIFICATIONS
Pmax: inlet max – 500 mbar or 5bar.
Setting outlet: available from 6 to 480mbar - choose the appropriate spring.
UPSO available from 5 to 60mbar - choose the appropriate spring.
OPSO available from 150 to 700mbar - choose the appropriate spring.
Others configuration on request
Inlet - Outlet Connection:
Thread gas 1"1⁄4 , 1"1⁄2 , 2"- ISO 228 connection
DN32 DN40 DN50 - Sliding Aluminium flange PN10
Test point: Inlet / outlet on request – Test point 1/8” NPT
Working Temperature: - 20 °C ... + 60 °C
Use: Not aggressive gases of three families – Natural Gas – LPG –Town Gas
Approval: UNI EN 88-1:2008 / PED
MATERIALS:
Complete Body: Die – Cast Aluminium Gd – AlSi12Cu - EN AB 46100
Diaphragms: NBR 60Sh – DvGW EN 549
Plastic components: White POM / Pa 66 + 25% Gf
This manual suits for next models
2
Popular Controllers manuals by other brands
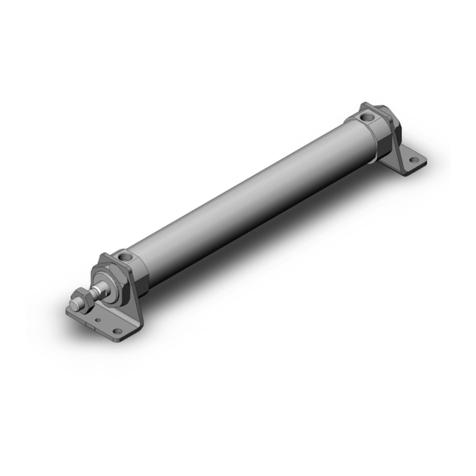
SMC Networks
SMC Networks C M2 Z Series Operation manual

Jäger
Jäger OPUS RADIO PLUS Installation and operating instructions
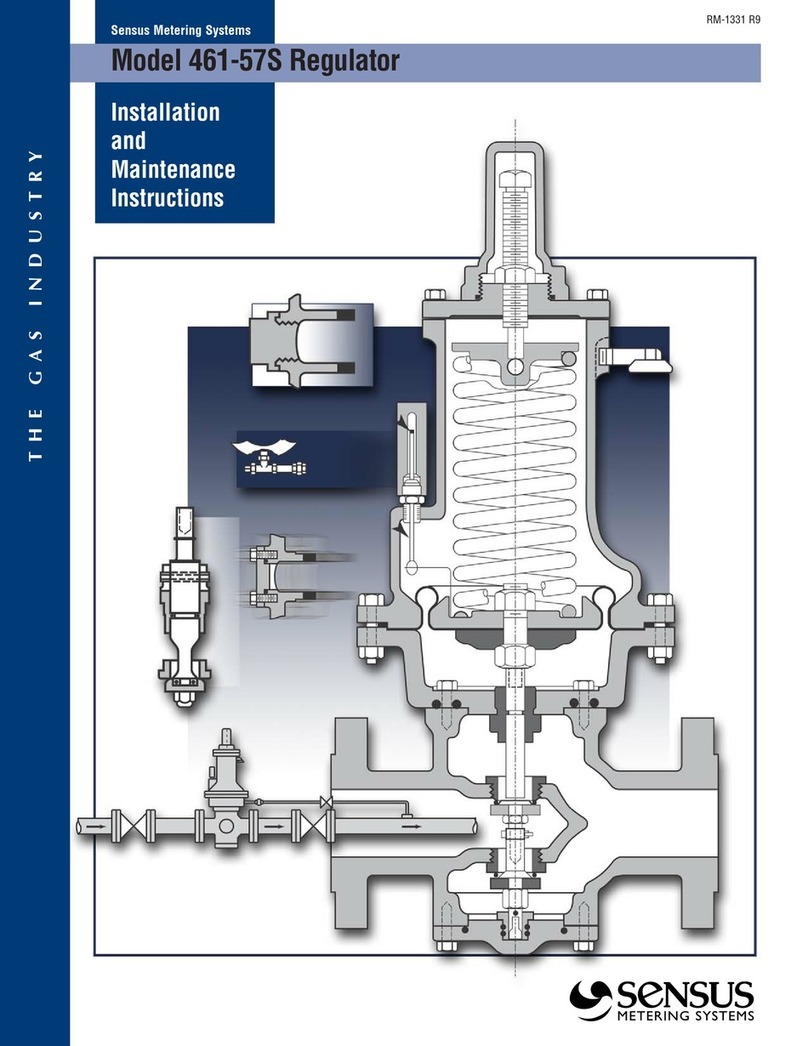
Sensus
Sensus 461-57S Installation and maintenance instructions
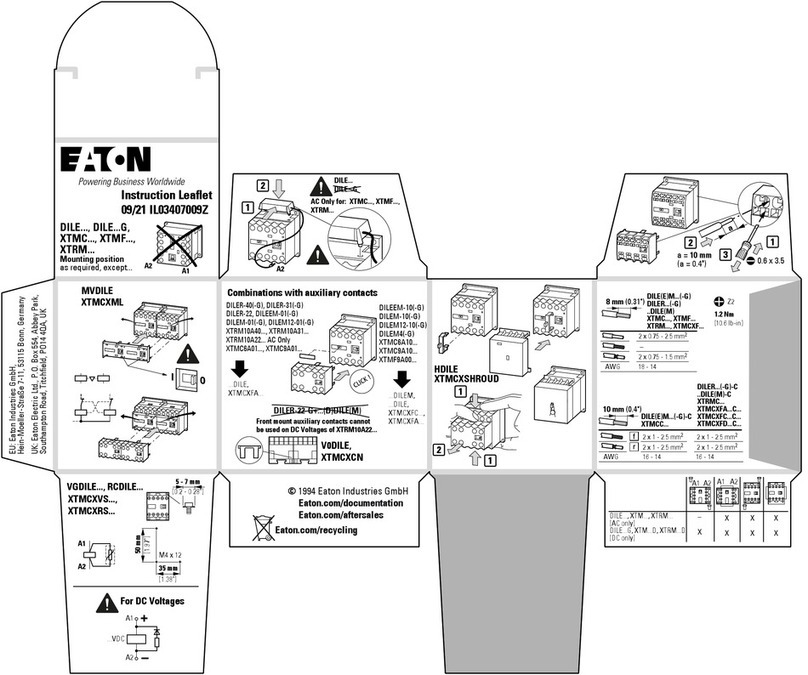
Eaton
Eaton DILE Series instruction manual

RIB
RIB T2-CRX Simplified instructions
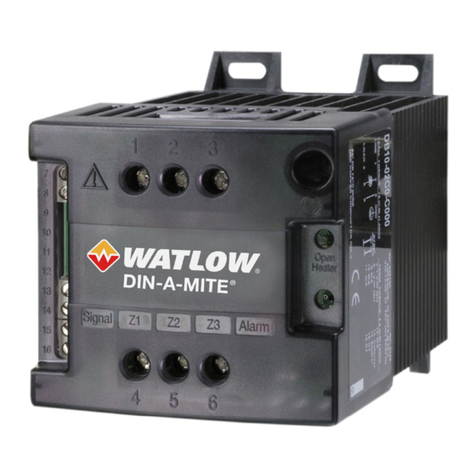
Watlow
Watlow DIN-A-MITE Style B user manual