Gehl FB 86 Building instructions

<Mfr

INTRODUCTION (g)
1
Mr. Owner:
Gehl Bros. Manufacturing Company, America's leading line of Forage Harvesting, Handling and Feed Making
Equipment, sincerely believes you have made the best choice in selecting this unit. Experience of many years
of farm implement development has made available this quality machinery. Its performance and economy will
exceed that which is required. As avaluable addition to your purchase and to maintain satisfied service, this
warranty is presented:
)oooooooono( inoooonooooo
The Gehl Warranty
alEHL BROS. MANUFACTURING COMPANY (INCORPORATED) AS MANUFACTURERS OF QUAL-
ITY FARM IMPLEMENTS SINCE 1859, WARRANTS GEHL MACHINERY TO DO GOOD WORK.
TO BE WELL-MADE OF GOOD MATERIALS AND DURABLE IF USED WITH PROPER CARE.
THE OBLIGATION OF THE COMPANY UNDER THIS WARRANTY IS LIMITED TO FURNISHING
NEW PARTS FOR THOSE PARTS THAT PROVE, IN THE COMPANY'S JUDGMENT, TO BE DE-
FECTIVE IN MATERIAL OR WORKMANSHIP WITHIN 90 DAYS FROM DATE OF SALE ON MA-
CHINES USED FOR CUSTOM WORK OR WITHIN ONE YEAR FROM DATE OF SALE ON OTHER
MACHINES. NEW PARTS WILL BE FURNISHED FREE OF CHARGE DELIVERED TO THE GEHL
DEALER'S PLACE OF BUSINESS.
THIS WARRANTY IS NOT APPLICABLE TO ENGINES, CLUTCHES. UNIVERSAL JOINTS.
KNIVES, BEARINGS. TIRES. BELTS OR OTHER TRADE ACCESSORIES. AS THEY ARE SUB-
JECT TO THE WARRANTIES OF THEIR RESPECTIVE MANUFACTURERS.
TO MAKE THIS WARRANTY EFFECTIVE. THE OWNER'S REGISTRATION CARD FURNISHED
WITH EACH UNIT MUST BE SENT TO GEHL BROS. MANUFACTURING COMPANY, OR ITS
AUTHORIZED DISTRIBUTORS.
Gehl Bros Manufacturing Co west bend Wisconsin u.s.a.
Over 2500 Implement Dealers are authorized to service your Gehl Equipment. They maintain genuine Gehl ser-
vice parts. This Operation and Parts Manual will assist you and your dealer in gaining valuable Maintenance and
service information. We suggest that you study this manual before putting your unit in operation. This manual
is aready reference. Keep it handy.
All service parts should be obtained from or ordered through your Gehl dealer. Give complete information when
ordering service parts. The model number and serial number should always be given. The numbers for this
unit are located on the Right Side of the Main Frame just above the wheel.
Whenever the terms "Right" and "Left" are used it should be understood to mean from aposition looking toward
the Hopper looking into the Blower Fan Housing opening. The Blower Outlet would then be on the "Left" side.
Gehl Bros. Manufacturing Company reserves the right to make changes or improvements in the design or con-
struction of any part without incurring the obligation to install such changes on any unit previously delivered.
TABLE OF CONTENTS Page
Introduction 2
Assembling Instructions 3-4
Operating Instructions 4-8
Lubrication 8
Parts Illustration and List -Blower Rim, Disc and Outlet 9
-Frame and Hopper 10-11
-Conveyor and Drive 12-13
-Universal Drives 14
-Blower Pipe and Accessories 15

®ASSEMBLING INSTRUCTIONS
ASSEMBLING THE DRAWBAR
Place the Right and Left Drawbars on the Blower
Frame and Fasten with 1/2" x1-1/4" hexagon head
bolts. Attach the Drawbar Hitch Support to the Right
and Left Drawbars with 1/2" x1" hexagon head
bolts. The Drawbars are to be inside of the Draw-
bar Hitch Support. The Drawbar Hitch -Upper and
Drawbar Hitch -Lower are to be attached so the
blower will be level when hooked to the tractor.
ASSEMBLING THE UNIVERSAL DRIVE GUARD
Remove the lock nuts from the Rear Main Bearing
Bolts. Attach the Drive Guard to the bolts and re-
assemble nuts.
Lightly grease the Blower Main Shaft spline and
attach the Universal Drive. The end of the Univer-
sal Drive Assembly with the short spline is the
Blower Shaft end.
ASSEMBLING THE AXLES
Remove the cotter pins from the ends of both axles.
Slide axles through Blower Frame Brackets. The
short axle is to be on the right when looking toward
the drawbar. Insert and spread cotter pins next to
Frame Brackets. Slide Axle Washer on axles next
to cotter pin. Slide wheels on axles and put other
axle washers against wheel bearings. Insert and
spread cotter pins to keep wheels in place.
CAUTION
UNIVERSAL JOINT LOCKING PIN MUST BE
SEATED IN BLOWER SHAFT GROOVE BEFORE
PUTTING MACHINE IN OPERATION.
Check the entire machine carefully. Be sure all
bolts and other fasteners are tight. Lubricate ma-
chine completely as indicated in the lubrication
section of this manual. Run machine ashort time
as apartial break- in and as acheck that all parts
are assembled correctly and functioning properly.
SAFETY
FIRST
KEEP ALL SHIELDS IN PLACE.
STOP MACHINE TO ADJUST AND OIL.
WHEN MECHANISM BECOMES CLOGGED, DIS-
CONNECT POWER BEFORE CLEANING.
KEEP HANDS, FEET AND CLOTHING AWAY
FROM POWER-DRIVEN PARTS.
KEEP OFF IMPLEMENT UNLESS SEAT OR PLAT-
FORM IS PROVIDED.
KEEP OTHERS OFF. NATIONAL SAFETY COUNCIL
4
J

ASSEMBLING INSTRUCTIONS
MOUNTING THE D3008A DEFLECTOR
1. Bolt Deflectors together with 5/16" x5/8MBolts
provided with the Bolt Heads on inside of De-
flectors.
2. Bolt Braces together with 5/16Mx2-1/2" Bolts.
Position Braces as shown and Drill thru eight
11/32 holes. Bolt Braces to Deflector with
5/16" x5/8" Bolts with the Bolt Heads on inside
of Deflector.
3. Bolt Cap to End Deflector with 5/16" Wing Nuts.
Attach Chain to End Deflector with 1/4 Nut and
Washers.
4. Bolt Deflector Brace to Deflector Strap with
1/2" x1" Bolts. See illustration for positions
for 17 Foot and 20 Foot Harvestores.
5. Bolt Deflector Bracket to Harvestore. Be care-
ful -Bolts in Harvestore are not secure. They
can fall in when Nuts are removed if they are
not held.
6. Bolt Deflector to Bracket on Harvestore with
1/2" x1" Bolts.
Bolt Lateral Braces to Deflector and to top of
Harvestore. Braces to be fastened to the seventh
Bolt each side of center of Deflector.
NOTE: IT IS IMPORTANT THAT
DEFLECTOR CAP IS AS CLOSE
TO THIS EDGE AS POSSIBLE.
OPERATING INSTRUCTIONS @
SETTING UP THE BLOWER
GENERAL OPERATION
1. Place the Blower in level position. Block base
of Blower if necessary to maintain level position.
2. Place the Blower to allow astraight drive connec-
tion, for minimum pipe requirements and ample
operating area for Uriloaders and Self- Unloading
Forage Boxes.
3. Use agood Tractor with sufficient power. Light-
er material requires less power to maintain good
capacity. Heavier material requires more steady
power.
4. Tractor PTO speed must be maintained at no less
than 540 RPM under load .Ordinary conditions
do not demand higher speed but if higher RPM
from the Tractor PTO is available it can be used
for increasing capacity. Do not operate Blower
Fan in excess of 750 RPM.
5. Capacity and ease of operation will depend upon
the set-up for operation and uniformity of feed-
ing. Use of Gehl Unloading Devices or Self Un-
loading Forage boxes will allow completely syn-
chronized operation, thereby increasing capacity,
reducing operating time and assuring even feed-
ing.
GRASS SILAGE IN UPRIGHT SILO
1. The pipe should be bolted or clamped together
starting at the Defiector Elbow. The telescoping
section should be at the lower end setting on the
Blower Outlet. The pipe and outlet should be in
aperpendicular position for best results. The
telescoping section can be adjusted up or down
to correct pipe length for each individual Silo.
2. Never install an Elbow at the Blower Outlet.
Such installation will reduce capacity. Serious
plugging can result. Available however is a
short section of pipe with aswivel top which can
be used where slight pipe angularity is necessary.
See Table of Contents for Pipe Accessories.
3. IMPORTANT: When placing the Deflector into
the Silo, Do Not allow it to rest on the ledge of
the opening. Raise the Deflector ten inches or
more to allow air to escape.

m> OPERATING INSTRUCTIONS
Set the Blower Fan down within 1/16" of rim. Shift
the Fan to the Outlet side so Fan Tip is within
1/16" of rim at the Outlet. The Cut-off is not im-
portant in grass silage unless moisture content is
below 25%. See Blower Fan Adjustment on page 7.
MOW STORAGE OF DRY OR SEMI-WILTED HAY
Generally for Mow storage the Blower Outlet will
be positioned at an angle up to 45° either side
from perpendicular. This will eliminate any
need for an Elbow at the Outlet. The pipe can be
set up as described in this illustration. Do not
exceed 45° angle.
1/16"
1/16"
The Blower Rim and Fans must be kept clean of
any waxes, gums and trash accumulations. In-
variably capacity will decrease as these accumu-
lations increase. When the cut crop is generally
in acritical moisture content stage (60% to 40%)
it has atendency to loose its waxes and gums.
To remove this from the Blower, apply apail of
water or the spray from ahose into the Fan
Housing after each load. Turn the Fan at Slow
PTO speed to loosen the accumulations. Increase
PTO speed to discharge the water.
2. Always keep doors or windows open to allow air
and dust to escape.
Set the Blower Fan up to the Cut-off. The Cut-off
is the short piece of the Rim that protrudes inside
the Blower Outlet. Shift the Fan up and to the
side to keep the Fan as close as possible to the
Cut-off. If this is not done correctly hay will
6. IMPORTANT: Keep the Blower Rim tight. If
cut feed gets between the Rim and the Blower
sides, it must be cleaned out. See Rim Adjust-
ment on page 7
.
wedge between the Fan Tips and the Rim. This
wedging will cause the Rim to heat where the Fan
is close to the Rim. Prevent wedging and the
heating will stop.
7. Always relieve the air pressure from aroofed
Silo. Set the Deflector as described in No. 3
above. In Harvestore Silos provide another open-
ing to allow air to escape and be sure Deflector
is set in the opening as described on page 4.
4. IMPORTANT: Keep the Blower Rim tight. If
cut feed gets between the Rim and the Blower
sides, it must be cleaned out. See Rim Adjust-
ment on page 7.

OPERATING INSTRUCTIONS @
DIAGRAM OF BLOWER PIPE
Pipe can be placed horizontal for areasonable distance. Horizontal Pipe should slope downward, having a
drop of about one foot for every twelve feet of length.
45° ELBOW
IMPORTANT
BLOWER MUST RUN
AT 540 R. P. M.
UNDER LOAD
USE D3009A TOP SEC-
TION AND D3040 DIS-
TRIBUTOR PIPE WITH
D3008 STATIONARY DE-
FLECTOR AS SHOWN.
SEE PAGE 7FOR ADJUSTABLE
DEFLECTOR SET-UP.
WHEN USING AFLEXIBLE ELBOW
OR SWIVEL ELBOW, INSTALL SO
JOINT OPENINGS FACE OPPOSITE
FROM THE DIRECTION OF FLOW
OF MATERIAL. THIS IS NECES-
SARY TO ELIMINATE OBSTRUC-
TIONS WHICH CAUSE SLOWING OF
FLOW AND PLUGGING OF THE
PIPES.
CORN SILAGE IN UPRIGHT SILO
1. The pipe should be bolted or clamped together
starting at the Deflector Elbow. The telescoping
section should be at the lower end setting on the
Blower Outlet. The pipe and outlet should be in
aperpendicular position for best results. The
telescoping section can be adjusted up or down
to correct pipe length for each individual Silo.
2. Never install an Elbow at the Blower Outlet.
Such installation will reduce capacity. Serious
plugging can result. Available however is a
short section of pipe with aswivel top which can
be used where slight pipe angularity is necessary.
See Table of Contents for Pipe Accessories.
3. IMPORTANT: When placing the Deflector into
the Silo, Do Not allow it to rest on the ledge of
the opening. Raise the Deflector ten inches or
more to allow air to escape.
4. IMPORTANT: Keep the Blower Rim tight. If
cut feed gets between the Rim and the Blower
sides, it must be cleaned out. See Rim Adjust-
ment below.
BLOWING SMALL GRAINS
Maintain Tractor PTO at aspeed only sufficient
to raise grain to the storage area. Excessive
speeds will have atendency to damage the grain.

@OPERATING INSTRUCTIONS
POSITIONING BLOWER OUTLET
Loosen Nuts on both Hooks and slide Rim around to
the desired position. Be sure you have tightened
Nuts securely before you operate machine again.
IMPORTANT
Keep the Blower Rim tight. If cut feed gets between
the Rim and the Blower side, it must be cleaned out.
Loosen the Bolts that hold the Rim and Outlet to-
gether, clean out the Rim grooves and clear the
edges of the Blower sides. Reassemble Rim and
Outlet making sure it is drawn up tight.
BLOWER FAN ADJUSTMENT
The Blower Fan is set at the factory, 1/8' rfrom the
Rim at the bottom and 5/32Mfrom the Rim at the
point where the Outlet is bolted to the Rim. This
setting is for most operations. When blowing dry
hay or straw, the Fans must come close to the Out-
let cut-off point.
To position Fan in Housing, loosen Bearing Bolts
and adjust set screws as necessary. If necessary,
add or remove shims from underneath the Bearing
Housings. Be sure all nuts are tightened after ad-
justment is made.
Avoid the use of any Elbows at the Blower Outlet.
Turn Outlet when necessary to obtain sufficient op-
erating area.
IMPORTANT
Do not set outlet lower than 37 inches from bottom
of tire of left wheel.

OPERATING INSTRUCTIONS <S
CONVEYOR DRIVE TAKE-UP
To keep chain in proper tension, loosen nut and move
Idler Sprocket and Stud. Do not tighten chain so
tight that undue strain is on shafts and sprockets.
DEFLECTOR ADJUSTMENT
To change direction of flow of material out of the
Adjustable Deflector, remove the wing nuts from
the bolts in the Adjusting Straps and position De-
flector to get desired flow. After adjustment is
made, be sure to replace and tighten wing nuts.
Use D3009B Top Section
If D3040 Distributor -
Pipe Is To Be Used U
LUBRICATION (pfc
Before starting, see that the entire unit is properly lubricated. It is well to remember that too much oil and
grease will do no harm but not enough might ruin it. All fittings are of standard style commonly found on farm
implements and automotive equipment. Units before Serial #5155 have 8fittings. Units after Serial #5154 have
4fittings. Check below for their locations. We recommend frequent lubrication if unit is operated continuously
for along period of time.
Lubricate Machine at Frequent Intervals
at Least Once aDay During Steady Operation Use aGood Grade of
Pressure Gun Grease
Conveyor Drive Shaft
Bearing —
Before Serial #5155
Idler Sprocket
Before Serial #5155
Conveyor Bearings
Before Serial #5155
Wheel Hub
Universal Joints
Wheel Hub

mBLOWER DISC, RIM and OUTLET
WARNING -Order By Part Number -Do
Not Use Illustration Reference Numbers
Ref. Part
No. No.
1}
1H58D
BB89
D300H
D303G
D305E
D307E
Part Name
Cover Lock Bolt
Frame Spacer
Blower Disc Assembled
Blower Disc Hub
Soc. Hd. Set Screw 1/2 x1/2
Soc. Hd. Set Screw 1/2 x3/4
Blower Arm
Blower Fan Plate
Rd. Hd. Rivet 3/8x13/16
No.
Req.
6
6
24
Ref. Part
No. No.
7D324B
8D351
9D353C
10 D362F
11 D401D
12 D402G
13 D9092
14 D9092A

FRAME and HOPPER
WARNING -Order By Part Number -Do
Not Use Illustration Reference Numbers
10
ALWAYS GIVE MODEL AND SERIAL NUMBER WHEN ORDERING SERVICE PARTS

FRAME and HOPPER
Ref.
No.
11
12
13
14
15
16
Part
No.
118H16
218H19A
318H20A
4D400G
A464
Q656
7D905B
8D906B
9D912H
10 D957F
D984C
D988E
D998A
D998B
D999A
D999B
FS5927
D9042A
D9042B
17 D9045B
D9045C
18

CONVEYOR and DRIVE ®
WARNING -Order By Part Number -Do
Not Use Illustration Reference Numbers
PARTS USED AFTER SERIAL NO. 2204
AND BEFORE SERIAL NO. 5155
ALWAYS GIVE MODEL AND SERIAL NUMBER WHEN ORDERING SERVICE PARTS
12

@CONVEYOR and DRIVE
Ref. Part
No. No. Part Name
1OST30 Bearing Bushing
(One Req'd After Serial #2204
and Before Serial #5155. Three
Req'd Before Serial #2205)
2H242A Chain Tightener Stud
(Used Before Serial #2205)
D9102B Idler Journal
(Used After Serial #2204 and
Before Serial #5155)
3D312E MainShaft 1-5/8x22-1/4
Machine Key 7/16 x3
4D313 Bearing Housing
5D320E Drive Sprocket (8 T)
Soc.Hd. Set Screw 5/16x5/16
6D366D Bearing Shim -Thick
D366E Bearing Shim -Medium
D366F Bearing Shim -Thin
7D915H Conveyor Drive Shaft
1x30-1/4
Woodruff Key 5/16 x1
8D962B Universal Drive Guard
9D967F Conveyor Drive Sprocket (48 T)
(Used Before Serial #2205)
Soc. Hd. Set Screw 5/16x5/16
D967G Conveyor Drive Sprocket (48T)
(Used After Serial #2204)
Soc. Hd. Set Screw 5/16 x1/4
Thrust Washer
(Used Before Serial #2205)
Thrust Washer
(Used After Serial #2204)
Bearing Bushing
(Used After Serial #3604
and Before Serial #5155)
Bearing Collar
(Used After Serial #5154)
Bearing Collar
(Used After Serial #5154)
Main Shaft Bearing
Bearing Collar
Blower Universal Drive
(Used Before Serial #2364)
Blower Universal Drive
(Used After Serial #2363)
Chain Tightener Sprocket (16 T)
(Used Before Serial #5155)
Grease Fitting 1612B
Chain Tightener Sprocket (17 T)
(Used After Serial #5154)
Bearing (Includes OST30)
(One Req'd After Serial #2204
and Before Serial #51 55. Three
Req'd Before Serial #2205)
Grease Fitting 1610B
Grease Fitting 161 IB
RA100NPPB Bearing
(Used After Serial #5154)
10

UNIVERSAL DRIVES m
SNAP RING TYPE 24
JL
(Q 0)U^^^
56716 19 19 16 23 684
T
29 \27
—6
Ref.

BEtit) BLOWER PIPE and ACCESSORIES

CO
00
r-
5
1L
5a&A ouwL Qvwiu,
-i
<
D
Z
<
(0
h
ft:
<
a.
Q
Z
<
UJ
o
>
a.
w
(0 GEHL BROS. MANUFACTURING CO.
WEST BEND WISCONSIN U.S.A.
AMERICAS LEADING LINE OF FORAGE HARVESTING,
HANDLING, AND FEED MAKING EQUIPMENT
Form 1831D 7M1P962 Printed in U. S. A.
Table of contents
Popular Blower manuals by other brands

Kress Elektrowerkzeuge
Kress Elektrowerkzeuge KU085.9 manual

GreenWorks Pro
GreenWorks Pro ULTRAPOWER 60X RANGE BLC402 Operator's manual
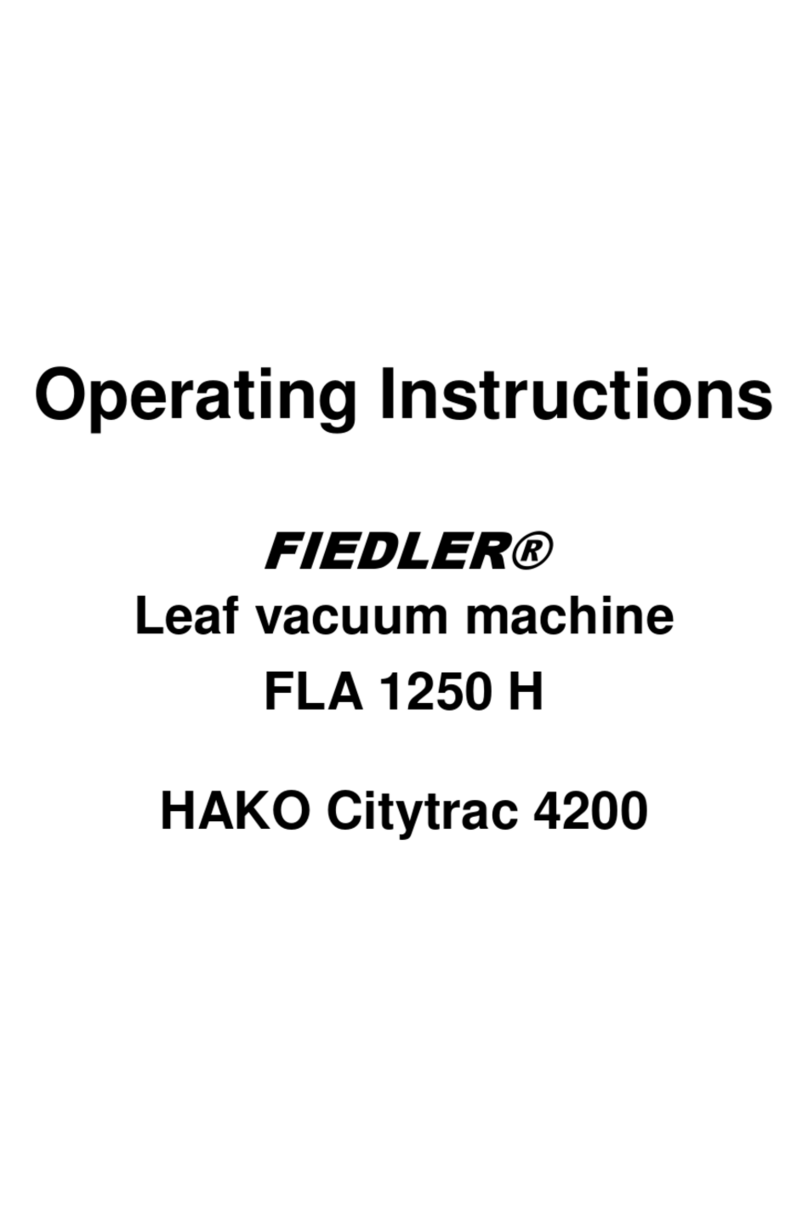
FIEDLER
FIEDLER FLA 1250 H operating instructions
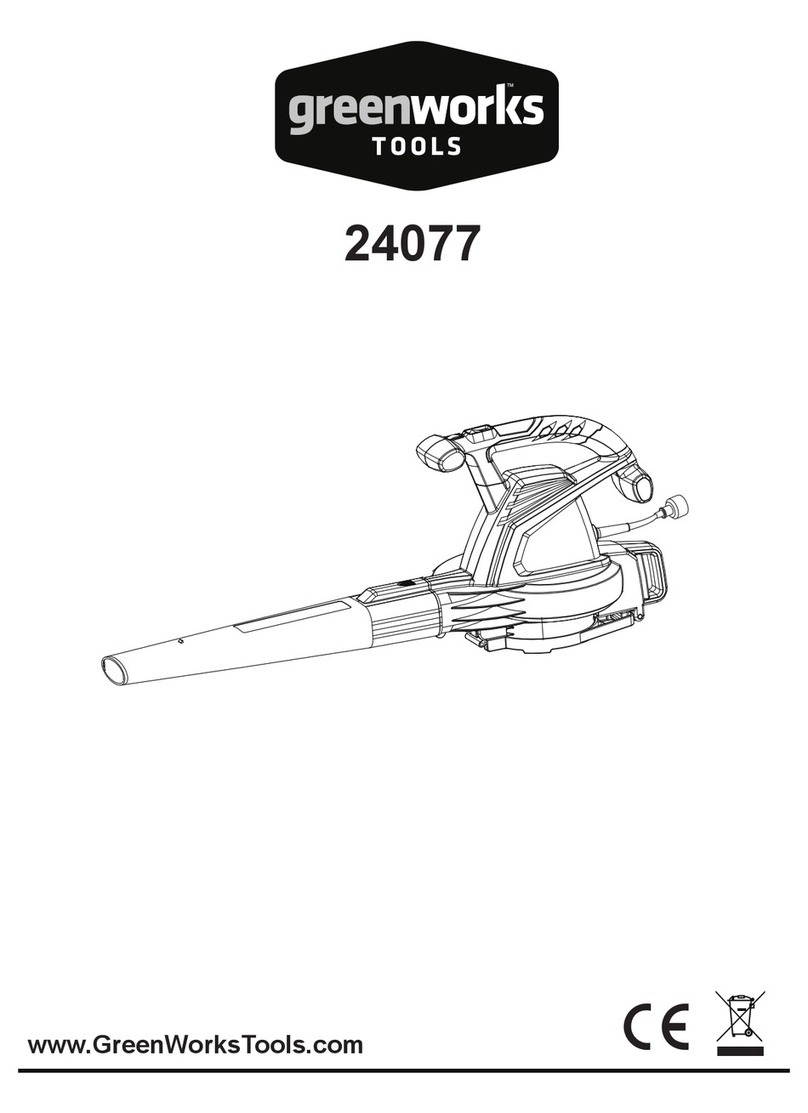
GreenWorks Tools
GreenWorks Tools 24077 Original instructions

Toro
Toro Ultra 350 Operator's manual
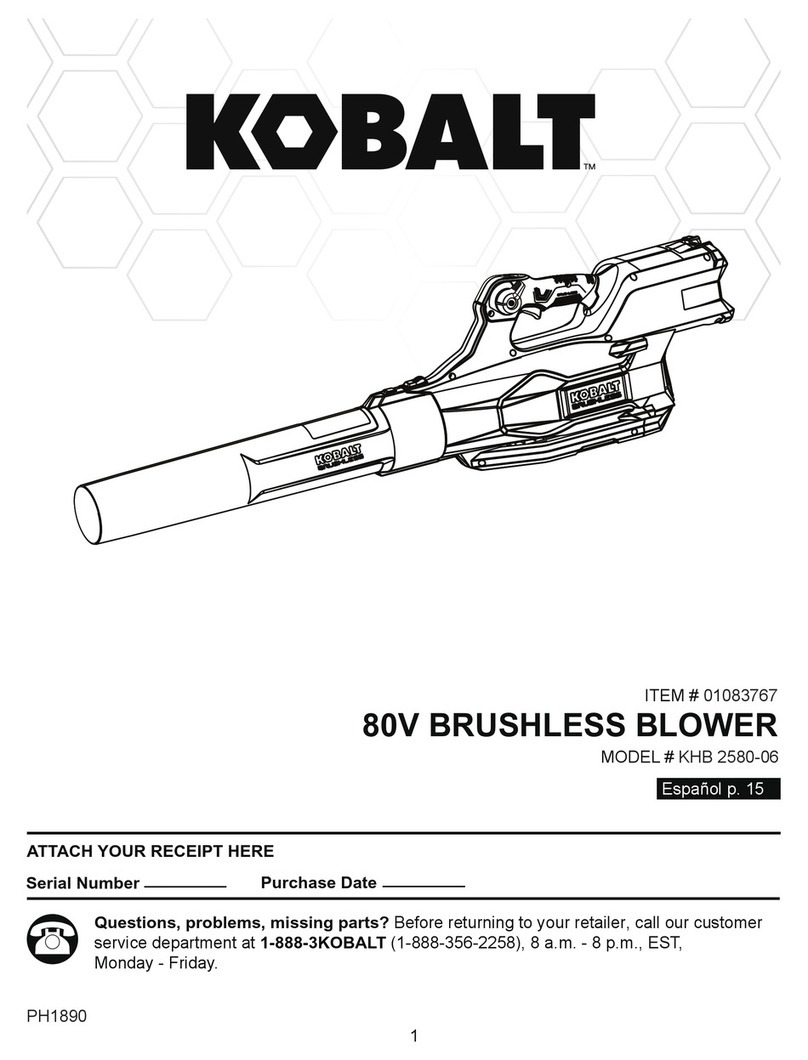
Kobalt
Kobalt KHB 2580-06 manual