Gerima SMA 20 APF-25.L1 User manual

©
SMA 20 APF-25.L1 / 01.01.2020 / V01.00-EN
Operating manual
Hand-held beveling machine
SMA 20 APF-25.L1
Operating manual

2
©
SMA 20 APF-25.L1 / 01.01.2020 / V01.00-EN
Imprint
Operating manual SMA 20 APF-25.L1
GERIMA GmbH
Weimarer Straße 12
D-66606 St. Wendel
Tel.: +49 (0) 6851 / 93951-0
Fax.: +49 (0) 6851 / 93951-21
E-Mail: [email protected]
All rights, including translation, are reserved. No part of this manual may be reproduced in any form (print,
photocopy, microfilm or any other process) without the written permission of GERIMA GmbH, St. Wendel,
reproduced or distributed using electronic systems, duplicated or distributed.
Subject to change.

3
©
SMA 20 APF-25.L1 / 01.01.2020 / V01.00-EN
Directory
1Preface…….…………………………………………. 2
1.1 Imprint…...………………………………………….… 2
1.2 Foreword……………………………………………... 4
1.3 Signs and symbols ..……………………………….. 5
2Technical specification………………….………… 6
2.1 Technical data….…………………………………….. 6
2.2 Shipment….………………………….……………….. 6
2.3 Noise emission value…..………………………….… 7
2.4 Power-on time…………..………………………….… 7
3Safety instructions……….………………………… 8
3.1 Basic safety instructions…………….………………. 8
3.2 Intended use………………………...……………….. 14
4Settings………………...……………………..……… 15
4.1 Replacing guiding roll……………...………………... 15
4.2 Replacing carbide inserts…………………………... 15
4.3 Setting the bevel length..………….………………... 16
4.4 Setting the radius……...…………………………..… 16
4.5 Consumables and accessories…………………..… 16
5Operating mode……………………………………... 17
5.1 Generally……....……………………………………... 17
5.2 Handling…..…..…………………….………………... 17
6Maintenance...……………………………………….. 18
7Disposal…......……………………………………….. 19
8Technical documentation…………………………. 20
9Terms of guarantee……………..………………….. 21
10 EC Declaration of Conformity….……………..….. 22

4
©
SMA 20 APF-25.L1 / 01.01.2020 / V01.00-EN
1. Operating issues
If you have questions regarding the use or
operation of the machine, or if you need our
supportor advice regarding specialized appli-
cations, our team of specialist retailers and
application technicians would be pleased to
offer their assistance.
2. Servicing and repair issues
If you need to make a guarantee claim, if the
machine needs to be repaired or if you need to
order spare parts, please contact our specia-
list retailers for help.
3. Sales
Our specialist retailers are also the people to
contact if you wish to purchase additional
GERIMA machine.
To help us provide quick an efficient assistance,
please always have your machine identification
number to hand.
We hope you enjoy working with your precisionmade
GERIMA machine.
The GERIMA-Team
Foreword
Dear customer,
Congratulations, you have purchased a highperfor-
mance beveling machine that will help you to
achieve high-quality results in your bevelling appli-
cations.
To ensure that the machine is used safely and
effectively, please read this operating manual
carefully in order to become properly acquainted
with the machine.
Please instruct your co-workers and employees to
become acquainted with the machine. Learning to
use the machine properly will save you time and
money, will save your employees time and effort,
and will improve the quality of your products.
Due to our policy of continuous product improve-
ment, the information contained in this manual may
be subject to change without notice.
Please contact GERIMA for the latest product in-
formation.
To verify correct functioning, the machine under-
went acceptance testing in which it processed
sheet metal of a variety of thicknesses.
Should you need to contact us for assistance,
please always have the identification number of
your GERIMA SMA 20 APF-25.L1 available.
The machine identification number is engraved on
the gear box (see red arrow in diagram shown at
top right of page).
Machine identification number

5
©
SMA 20 APF-25.L1 / 01.01.2020 / V01.00-EN
Signs and symbols
Please read the manual before using the ma-
chine !
This manual has been created so that you can
work with your device quickly and safely. Here is a
brief guide on how you should read this manual:
• Read these operating instructions before
working with the machine. Note especially
the safety information.
• This manual is intended for people with
basic technical knowledge in dealing with
devices like the one described here. If you
have no experience with such devices, you
should first obtain the assistance of experi-
enced person.
• Keep all documentation delivered with the
device, so you can get information when
needed. Keep your receipt for any warranty
claims.
• If you lend or sell the machine once please
give all equipment supplied documentation
with.
• For damages which arises because these
operating instructions were not followed, the
manufacturer accepts no responsibility.
The information in this manual are indentified
as follows:
Danger!
Warning of person, machinery or
environmental damage.
Entanglement!
Warning of personal damage by
detection of body parts or clothing.
Restart lock! Secure the machine
against restarting and disconnect
compressed air connection of the
machine. Otherwise there is a
danger of injury due to
unintentional starting the power
tool.
Stop!
Switch on the machine prohibited!
Tip:
Additional information used to
improve the knowledge.
Ear protection!
Operating personnel must wear ear
protection.
Eye protection!
Operating personnel must wear eye
protection.
Hand protection!
The operator must wear protective
gloves.
Safety shoes!
The operator must wear safety
shoes.
Note that the substances / materials
used to handle properly and must
be disposed of according to
regulations and laws.

6
©
SMA 20 APF-25.L1 / 01.01.2020 / V01.00-EN
Technical specification
Technical data SMA 20 APF-25.L1
Dimension and weight
Length 353 mm
Weight approx appr. 3,00 Kg
Connection value / power
Air connection 6-7 bar, 20l/s
Power 670 W
Idle speed 12.000 rpm
Noise emission
Sound power level Lwa / dB (A) 94 dB (A)
Allowed materials and formats
Thickness of workpiece min. 1,5 mm
Bevel width 1-5 mm
Radius 1,2-2,5 mm
(depending on material)
Materials
Steel 1-5 mm
Stainless steel 1-3 mm
Aluminium 1-5 mm
1. Handle
2. Spindle lock
3. Motor
4. Air connection
5. On-/Off-switch
6. Height clamping lever
7. Milling head with guiding roll
8. Guiding plate
9. Vernier scale
Shipment
1x Basic machine SMA 20 APF-25.L1
with milling head
1x Manual
1x Torx wrench T15
2
5
6
4
7
1
8
9
3

7
©
SMA 20 APF-25.L1 / 01.01.2020 / V01.00-EN
Technical manual
Noise emission values in accordance with the DIN
EN 60745-1 standard:
Vibrations:
Note:
The measured values listed above depend on the
materials and operating procedures used and may
therefore be exceeded under other operating
conditions.
Using the machine to create bevels with a width
greater than that permitted will result in a
disproportionally large reduction in the machine’s
on-time and the service life of the indexable carbide
inserts. The vibration and noise emission values
will increase accordingly.
To prevent overloading the machine and to avoid
operator fatigue it is very important to observe the
maximum power-on periods especially when
machining wide bevels or high-strength materials.
Value Un-
certainty
Noise emission [dB (A)]
Emission sound pressure
level LpA 83 3
Peak emission sound pres-
sure level at workplace
(during milling operation)
LpGpeak 101 3
Sound power level LWA 94 3
Total vibration value
(tri-axial vector sum)
Appropriate to
DIN EN 60745:
Measured vibration emission
value
ah = 2,5 m/s²
Work process:
- 45° milling head
- 2 mm bevel width (C) in
12 mm steel sheet S 355 Uncertainty
K = 1,5 m/s²
Power-on time (POT):
To avoid damaging the machine, it is essential to
be monitor how long the machine has been
operating continuously (‘power-on time’).
The compressed air that powers a pneumatic drive
also serves to cool the motor as well. Pneumatic
tools can therefore be operated for longer periods
than electrically powered tools.
However, if the machine is subjected to particularly
extreme loads (e.g. when machining wide bevels or
very hard or tough materials) and/or if the machine is
run for very long periods, the air cooling may still be
insufficient to prevent overheating of the milling drive
unit. If the operator continues to use the machine,
the milling drive unit may overheat and be damaged
as a result
(C=bevel width, POT=power-on time)
The power-on time is always expressed as a
percentage of one hour.
Example:
If the power-on time is specified as 50 %, then you
can use the machine to mill bevels for a maximum of
30 min. in an hour and must then leave the machine
to cool for 30 min.. If the machine is subjected to
heavy loads, the power-on time might be 20 %,
which means it can be used for 12 min. in any hour
and must be left to cool for 48 min.. Before
completely switching off the machine, we
recommend running the machine for one or two
minutes in idle mode (unloaded) so that fan can
continue to draw cool air through the machine.
Do not overload the machine!
The machine can become overloaded if, for
example, it continues to be used even though the
bevel being cut is too large for the material being
milled, or if the cutting inserts have become blunt
and therefore unable to penetrate the material.
Such conditions can lead to large machine vibrations
or even machine breakdown.
To prevent this sort of damage when milling large
bevels and/or hard materials, never try to machine
the bevel in a single pass, always use multiple
passes, and do not forget to change the carbide
inserts before they become blunt or worn.
Material strength C max. POT max.
Aluminium, copper, brass 5mm 80%
Steel up to 400 N/mm² 5mm 60%
Steel up to 600 N/mm² 4mm 50%
Steel up to 900 N/mm² 3mm 40%
Stainless steel 3mm 20%

8
©
SMA 20 APF-25.L1 / 01.01.2020 / V01.00-EN
Basic safety instructions
Duties of the operator
The SMA 20 APF-25.L1 was designed
and built taking into account a risk
analysis and careful selection of the
applicable harmonized standards and
technical specifications. It thus corres-
ponds to the prior art and allows for
maximum safety during operation.
However, the machine safety can only be effec-
tively implemented in practice, if all necessary
measures have been taken. It is the duty of care
and responsibility of the machine operator to plan
these measures and to monitor their execution.
The operator must in particular ensure that:
• the machine must only be used for its intended
use (see chapter intended use).
• the machine must only be operated in perfect
working condition and especially the safety de-
vices must be checked regularly for proper func-
tion.
• the required protective equipment for the opera-
tion, maintenance and repair staff must be
available and must be used.
• the operating instructions must always in a good
condition and fully available at the machine.
• only qualified and authorized staff may operate,
maintain and repair the machine.
• this staff must be instructed regularly about rele-
vant occupational safety and environmental pro-
tection and know the operating instructions and
the safety instructions.
• all safety instructions and warnings attached to
the machine must not be removed and must
remain legible.
The following instructions must be
read carefully in order to avoid ac-
cidents to persons and / or property
damage
• Never attempt to operate the machine before you
have read and understood the content of this ope-
ration manual.
• If you are unsure about any points, please contact
GERIMA for assistance.
• Make sure that all persons who will be operating
or servicing the machine have read and under-
stood all the relevant safety information.
• Before starting the machine, the operator must
ensure that all safety equipment is properly in-
stalled and functioning correctly.
• Never use the machine for purposes other than
those specified in this manual. Never use the ma-
chine to process materials other than those ap-
proved for use by the machine’s manufacturer. If
you are considering using the machine for an un-
approved purpose, please first contact GERIMA
to request approval of your proposed application.
• Check that all air connections are secure and
sound. Never attempt to service or repair the ma-
chine before it has been disconnected from the
power supply.
• Always use genuine GERIMA spare parts and
accessories or those that have been approved for
use by GERIMA.
If you encounter a problem or fault when operat-
ing the machine and you are unable to solve the
issue with the aid of this manual, please contact
GERIMA for rapid assistance.

9
©
SMA 20 APF-25.L1 / 01.01.2020 / V01.00-EN
Basic safety instructions
Operator qualifications and protection of ma-
chine operators:
The term ‘operator’ is used here to mean any per-
son who operates, adjusts, services and/or repairs
the machine.
The employer is obliged to inform the operator
about security relevant standards and to verify
compliance.
To be trained operating personnel may initially
work only under the supervision of an experienced
person on the machine. Successful completion of
training should be confirmed in writing.
All control and safety devices must always be ope-
rated only by trained personnel.
All persons carrying out work on the machine must
read the operating instructions and confirm with
their signature that they have understood the ope-
rating instructions.
The workplace must be well lit and provide suffi-
cient space for safe working.
Before working with or on the ma-
chine, the operator must have
become acquainted with the ma-
chine and must have read and un-
derstood this manual.
The operator must
1. ensure that all guard plates are in place and all
safety mechanisms are functioning correctly
before starting the machine.
2. not wear clothing or accessories
(jewellery etc.) that could be get
trapped in moving machine parts.
3. always wear protective clothing (non-slip
shoes, ear protection, gloves and safety gog-
gles.
4. observe all relevant safety instructions. If a
problem arises, the operator must refer to this
manual before continuing with his or her work.
Protective clothing:
When working on/with the machine always wear:
ear protectors,
safety goggles,
protective gloves,
safety shoes.

10
©
SMA 20 APF-25.L1 / 01.01.2020 / V01.00-EN
Basic safety instructions
Requirements to be met by operating staff:
The machine may only be operated by appropri-
ately trained persons who have been instructed in
the use of the machine and are authorized to oper-
ate it.
Operators must have read and understood this
operating manual and must act in accordance with
it. The functions of the operating personnel, i.e.
what an operator is or is not allowed to do, must be
clearly specified.
Special qualifications are required for the following
activities:
• Commissioning: The machine may only be com-
missioned by the manufacturer.
• Operational training: Training in the use of the
machine must be provided either by the manu-
facturer or by persons who have received appro-
priate instruction.
• Fault elimination: Faults may only be dealt with
by appropriately qualified technical staff or by the
manufacturer’s service personnel.
• Maintenance: Maintenance work may only be
performed by technical staff who have received
appropriate instruction.
• Cleaning: The machine may only be cleaned by
persons who have received appropriate instruc-
tion.
• Servicing: The machine may only be serviced by
appropriately qualified technical staff or by the
manufacturer’s service personnel.
• Repair: The machine may only be repaired by
appropriately qualified technical staff or by the
manufacturer’s service personnel.
• Decommissioning: Decommissioning of the ma-
chine may only be performed by appropriately
qualified technical staff or by the manufacturer’s
service personnel.
Risk of injury from hot metal chips:
• Hot chips are ejected from the
machine at high speed.
Improper use can cause serious injury:
• Make sure you always have a firm
footing when working with the
machine.
• Never touch the milling tool when
the machine is running.
• Never use the machine above head height.
• Ensure the switch is in the off-position before connec-
ting to power source. After use de-energize the machi-
ne by disconnecting it from the power supply!
• Only milling against the rotating direction = upcut mil-
ling
Improper use can damage equipment and property:
• Risk of machine being damaged or
destroyed.
• Never lift or carry the machine by its
air hose.
• Make sure the air hose is directed behind and away
from the machine. Do not lay the air hose over sharp
edges.
• Always use genuine GERIMA spare parts and acces-
sories.

11
©
SMA 20 APF-25.L1 / 01.01.2020 / V01.00-EN
Basic safety instructions
Pneumatically-driven power tools
are generally not insulated in a way
that would allow them to come into
contact with an electrical power
source.
• All work on the machine’s air system must be
performed only by qualified technicians.
• Pneumatically equipment must be checked re-
gularly.
• Any loose connections must be reattached and
any damaged air hoses replaced immediately.
• Avoid hazards associated with vibrating pneu-
matic tubing. Check the condition of the tubing,
tube connectors and tube clamps regularly.
• The machine may only be operated with the prescri-
bed air pressure strength.
Machine hazards :
The machine has been built in accordance with the
latest engineering standards and generally recog-
nized safety principles.
Nevertheless, improper use can result in serious or
fatal injury to the user and/or third parties or cause
damage to the machine or other property.
The machine must only be used:
• For its intended purpose.
• If it is safe and in good repair.
• In compliance with the operating manual and by
persons who are aware of the safety issues and
hazards associated with the machine.
• Faults that could affect the safety of the ma-
chine must be remedied immediately.
Regular pre-start safety precautions
Perform the following pre-start proce-
dures each time you plan to use the
machine:
• Check and ensure that all of the ma-
chine’s safety and protective equipment is in
place and functioning correctly.
• Check the machine for visible signs of damage.
Any defects or deficiencies identified must be
remedied immediately or reported to the supervi-
sor. The machine may only be used if it is safe
and in a state of good repair.
• Check and ensure that only authorized persons
are within the machine’s work area and that no
other persons can be endangered by switching
on the machine.
• All objects and other materials that are not nee-
ded for the operation of the machine must be
removed from the machine’s work area.
• The measures to be taken in an emergency are
known.
Basic Safety Measures for Normal Operation:
• The machine may only be started
from the specified workstation.
• During operation of the machine sa-
fety devices must not be removed or
rendered inoperable.
• The operator may be present only at the spe-
cified workplace during operation of the machine.
• The operator must ensure that no unauthorized
persons are in the working area of the machine.
• After switching off the machine, the operator
must wait until all moving parts have stopped
and the lights are off function.

12
©
SMA 20 APF-25.L1 / 01.01.2020 / V01.00-EN
Basic safety instructions
• If protective guards or other safety devices have
to be removed for servicing or maintenance work,
they must be reinstalled immediately after the
work has been completed.
• Use only listed operating and auxiliary materials.
• Use only genuine spare parts as listed in the
spare parts list.
• Check bolted connections for tightness.
• Before restarting the machine, make sure that no-
body can be endangered by the running machine.
• Any unsafe operation is prohibited!
• Never put safety devices inoperative!
• Never wear hanging or prodruding clothes which could
become trapped in moving machine parts!
• After maintenance check all safety devices for function!
Consequences when nonobservance:
• Injury hazards for personnel!
• Damage to the machine!
• Modifications of the machine can
affect the correct operation and
safety of the machine!
Maintenance:
Maintenance or service work must
only be performed once the machi-
ne’s moving parts have come to
rest. Machine parts may become
very hot during operation.
Restart lock! Secure the machine
against restarting and disconnect
compressed air connection of the
machine. Otherwise there is a dan-
ger of injury due to unintentional
starting the power tool.
Machine hazard points:
Milling head
• Never touch the milling head when
the machine is running.
Safety information for servicing, maintenance
and fault elimination:
• Any person who installs, commissions, opera-
tes, inspects, services or maintains the machi-
ne must have read and understood the opera-
ting manual and in particular the safety infor-
mation contained therein.
• Machine adjustment, maintenance and inspec-
tion work must be carried by appropriately qua-
lified technical staff.
• Servicing and maintenance work must only be
carried out by appropriately qualified technical
staff.
• All operating equipment must be secured
against accidental activation or energization.
• When performing any servicing, maintenance
or repair work de-energize the machine by dis-
connecting it from the supply and ensure that
the machine cannot be switched on again ac-
cidentally. Put up a warning sign prohibiting
reactivation of the machine (lock and tag out
procedure).

13
©
SMA 20 APF-25.L1 / 01.01.2020 / V01.00-EN
Basic safety instructions
Residual risks:
• The machine was plant and constructed with all
suitable devices to guarantee the safety and
health of the operator.
• The machine is covered to prevent the risk of
contact with moving parts.
• However residual risks still exist.
• As already mentioned the cutting area is protected
as far as possible but there is an opening portion
through which the processing material must be
introduced.
• It is possible that the operator reaches in this area
with his hands.
Always keep your hands as far as
possible away from the cutting area!
Always oberserve the safety rules to
minimize the residual risks!
Be aware that the machine may be a
source of residual mechanical or
pneumatically energy. Appropriate
precautions for dealing with these
hazardous energy sources must be
taken when instructing operating
personnel on the use of the machi-
ne.
Modifications to the machine:
The machine may not be modifi-
ed, added to or converted unless
the prior consent of the manufac-
turer has been granted.
Any alterations to the machine
must have been approved by
GERIMA GmbH.
This also applies to the welding of
the component parts.
Cleaning the machine and disposal information:
All substances and materials used
must be handled appropriately and
accordance with all relevant statuto-
ry provisions and legislation.
The machine must only be cleaned
after it has been switched off!
Machine noise:
The continuous sound power level emitted by the
machine at the installation site is greater than > 84
dB (A).
Operating personnel must wear ear
protection!

14
©
SMA 20 APF-25.L1 / 01.01.2020 / V01.00-EN
Intended use
The hand-held beveling machine SMA 20 APF-
25.L1 may only be used for work and materials
des-cribed in the section ‚intended use‘.
Do not use the machine to work
on materials containing asbestos!
The SMA 20 APF-25.L1 is a hand-held, pneumati-
cally powered beveling machine intended:
• For machining workpieces made of steel,
cast steel, fine-grained steel, stainnless
steel, aluminium, aluminium alloy, brass
and plastic.
• For commercial use in industrial settings
and in the skilled-trades.
• For preparing K-, V-, X-, and Y-shaped
welding grooves.
• For creating visible edges in plant and me-
chanical engineering work.
• For rounding off of edges for an optimal
painting preperation or as a scratch and
bump protection.

15
©
SMA 20 APF-25.L1 / 01.01.2020 / V01.00-EN
Settings
Replacing guiding roll / carbide inserts
Before replacing the machine must be
disconnected from the compressed air
supply and secured against reconnec-
tion.
Lock spindle !
Loosen the guiding roll with Torx wrench T15 and
pull out the guide wheel of the milling head.
Then loosen the clamping screws with the Torx
wrench T15 and replace the carbide inserts. The
inserts must be fastened to the mounting seat on
the milling head by means of the original locking
screws (max. tightening torque: 4.0–5.0 Nm).
In order to avoid cuts and burns when
carbide inserts change, carbide inserts
only change to a complete stop of the
machine. Use protective gloves!
1
2
Adjusting the 4-fold insert type MV and the 8 bevel
and radius inserts (type SX and RSX):
The bevel and radius carbide inserts of type SX and RSX
each have 8 cutting edges. By turning and turning, it is
possible to use the cutting edges 8 times and the radius
carbide insert up to 16 times.
The MV carbide insert has 4 cutting edges each. By turn-
ing and turning, it is possible to use the indexable inserts
four times.
Consumables and accessories
milling bodies with special angles and radii
on request
3
nr. name of part order-nr.
1Clamping screw
CS-30-09 0101.203.16-00001
2Bevel-carbide insert
MV4.B12-V1 0101.404.19-00058
3Bevel-carbide insert
SX8.B22-V1 0101.404.19-00075
4Radius-carbide insert
R1.2-SX16.B22-V1 0101.404.19-00063
5Radius-carbide insert
R2.5-SX8.B22-V1 0101.404.19-00076
6Guiding roll (MV)
GR45.M3-SD2.V1 0101.113.19-00003
7Guiding roll (SX)
GR45.S3-SD1.V1 0101.113.19-00002
8Guiding roll (R1.2)
GR45R1.2.S3-LC2.V1 0101.113.19-00004
9Guiding roll (R1.2)
GR45R1.2.S3-SC2.V1 0101.113.19-00005
10 Guiding roll (R2.5)
GR45R2.5.S3-SC2.V1 0101.113.19-00006
11 Torx-wrench
T15 0000.077.14-00001
12 Screwdriver
SW4 0000.077.15-00014

16
©
SMA 20 APF-25.L1 / 01.01.2020 / V01.00-EN
Settings
a leg length = bevel length a
b leg length = bevel length b
C bevel width
α bevel angle
β opposite angle
A bevel size
h bevel height
S residual bridge
t plate thickness
Setting the bevel length:
The bevel length (a) is setting by adjusting the position
of guiding plate (1). The height setting can be read out at
the main scale (2) and the vernier collar (3). Loosen the
clamping lever (4) and rotate the guiding plate (1) until
the required bevel length has been set as shown by the
main scale (2) in combination with the verniere scale on
the collar (3). Retighten the clamping lever (4).
Once the bevel height has been set, a bevel should be
milled on a test sample to check whether further height
adjustments are required. These may be necessary
because the precision of the scale is approx. ± 1 mm.
The values above are experical values, no guarantee
values!
Some materials can harden on the edges of the
workpiece when working with flame cutting, plasma,
laser cutting. This can result in significant deviations
from the specified reference values.
too low
correctly
1
23
4
too high
Adjusting radius:
The procedure for setting the radius and bevel is identi-
cally. Please note that only the position of the upper
edge of the radius can be adjusted by rotating the guid-
ing plate. The lateral position of the radius on the work-
piece end face is determined by the guide wheel fitted
and cannot be altered.
Guiding plate set too low (radius incomplete).
Guiding plate set to high (radius cuts into material).
Guiding plate set correctly (radius fully formed with
smooth transition to workpiece surfaces.)

17
©
SMA 20 APF-25.L1 / 01.01.2020 / V01.00-EN
Operating mode
General:
Two-handed operation:
Whatever the position of the
machine, always use two hands to
control the machine.
When working with the machine, make sure that the
machine is always held with two hands (see red arrows)
and in such a way that both hands are kept away from
the machining point.
Ensure that the workpiece is securely clamped!
• for safety reasons
• to improve the service life of the
carbide inserts
• to prevent damage to the milling
machine
Important!
Before machining a workpiece, make sure that it is
securely clamped so that it cannot slip.
This should be done to ensure safe working so that the
workpiece does not slip or even fly off when being milled
and to prevent unnecessary vibrations in the workpiece
material.
The less vibration generated in the workpiece, the longer
the service life of the carbide inserts.
To became acquainted with the
machine, you must start by
machining a small bevel with a width
of no more than 2 mm and remember
to advance the machine slowly first.
Bevels of maximum width can only
be machined safely and reliably
once you have become used to
handling the machine.
Handling:
Damages caused by wrong power
supply!
• Check values air connection. The air
pressure must correspondend with the
specifications on the type plate of the
machine.
Improper use can cause serious
injury!
• Make sure you always have a firm
footing when working with the
machine!
• Never touch the milling head when the
machine is running!
• Always lead the machine away from
body during working, never use the
machine above head height.
Risk of damage to equipment and
property!
• Working with worn or damaged
carbide inserts or milling heads will
cause the machine to fail!
• Avoid collisions when working with the
machine!
Working with the machine:
Motor starts
Bring the machine slowly into contact with the workpiece
only after the tool speed has been reached.
Machining the workpiece (up-cut milling)
When milling a bevel always move the machine from left
to right against the direction of rotation of the milling head
(up-cut milling).
Switching off the machine
• remove the machine from the workpiece.
• release the on-/off-switch.
• once the motor is switched off, wait for it to come to a
standstill before placing the machine down on a
surface.

18
©
SMA 20 APF-25.L1 / 01.01.2020 / V01.00-EN
Maintenance
Maintenance
Before servicing the machine always
must be disconnected from the
compressed air supply and secured
against reconnection.
Repair must only be carried out by a
GERIMA trained technician!
Improperly repaired machines are
hazzard!
• Increased risk of injury
• Machine does not function correctly!
Hot carbide inserts and milling head!
• Burn hazzard!
• Wear protective gloves when replacing
the carbide inserts!
Maintenance plan:
Blunt tool can cause damage!
• Blunt tool can overload the machine!
• Inspect milling tools regulary for signs
of wear.
• Wear protective gloves when changing
or readjusting the carbide inserts!
Part to be serviced Type of maintenance
work
Service Maintenance
procedure
Materials
required
Order-nr.
Gear box re-grease approx. every
1000 operating hours
certified GERIMA
service agent
disassemble
gear box
lubrication
greaset
0109.007.10-00002
Motor laminations peplace as
necessary
certified GERIMA
service agent
Lamellen
auswechseln
stave-set 0109.113.09-00029
Height adjuster thread clean and lubricate as
necessary
trained technician disassemble guide
plate unit
teflon pray 0109.007.10-00005
Carbide inserts rotate or replace as
necessary
machine operator see page
15
torx-key T15 see page
15
Oil put a drop oil in the
nozzle, daily
machine operator see page
18
spezial-
pneumatic-oil
0109.007.10-00004
Height adjuster thread:
Remove the screw for height clamping, lift the guiding
plate unit, clean the mounting thread, lubricate the
thread with teflon spray and then re-assemble in reverse
order.
Oil:
Before connecting the machine to the compressed air line
put a drop oil in the nozzle, daily.

19
©
SMA 20 APF-25.L1 / 01.01.2020 / V01.00-EN
Disposal
Disposal of components removed from the ma-
chine:
All machine parts, operating and
auxiliary materials must be dis-
posed of in accordance with the
applicable statutory provisions.

20
©
SMA 20 APF-25.L1 / 01.01.2020 / V01.00-EN
Technical documentation
SMA 20 APF-25.L1 0202-02-01-00-00-04
nr. name of part order-nr. pc.
1Spacer wing screw 0101.112.15-00016 1
2Steel bush 0101.112.15-00006 1
3Counter-ring 0101.112.15-00005 1
4Guiding plate 0101.112.15-00004 1
6Spindle with milling head 0109.112.16-00019 1
7Bevel gear 0109.112.16-00005 1
8Disc spring 0109.112.16-00008 1
9Spacer 0109.112.16-00004 1
10 Flange 0109.112.16-00003 1
11 Gear box 0109.112.16-00001 1
12 Distance bush 0101.243.09-00015 1
13 Handle 0101.243.09-00002 1
14 Thread insert 0101.143.09-00023 1
15 Groove ball bearing 0000.012.14-00023 1
16 Flat headed screw M12x20 0000.022.14-00191 2
17 Wing screw M6x15 0000.032.14-00056 1
19 O-ring 0000.042.15-00002 1
20 Countersunk screw M4x12 0000.022.14-00190 4
21 Locking ring 0000.022.15-00256 1
22 Locking ring 0000.022.15-00005 1
23 Plug nipple with external thread 0000.032.14-00083 1
24 Groove ball bearing 0000.012.14-00040 1
25 Cylinder screw M5x12 0000.022.14-00113 4
26 Cylinder screw M4x8 0000.022.16-00097 4
27 Cylinder screw M6x14 0000.022.14-00192 1
28 Fitted washer 0000.022.16-00108 1
29 Drive unit 0101.243.15-00001 1
Table of contents
Other Gerima Power Tools manuals
Popular Power Tools manuals by other brands
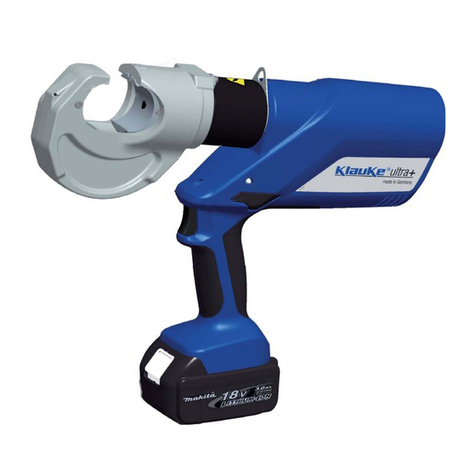
Textron
Textron Klauke Ultra+ EK 120/30-L instruction manual
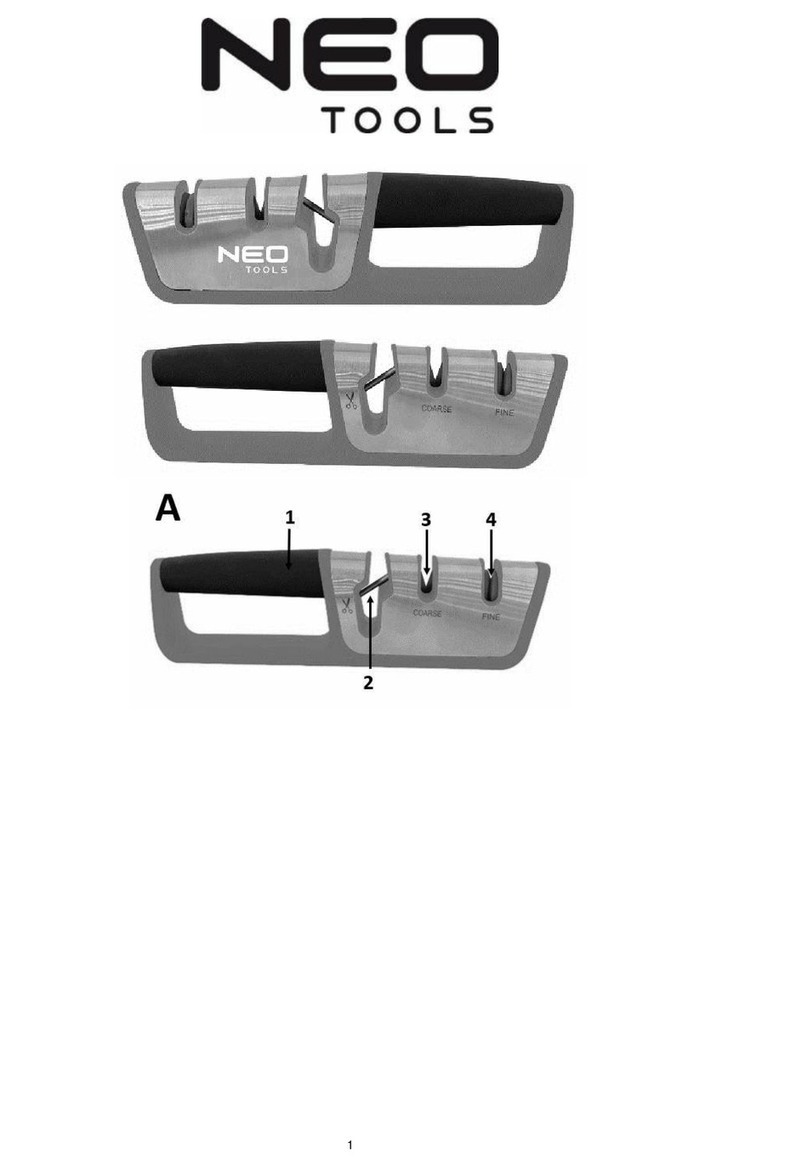
NEO TOOLS
NEO TOOLS 56-053 user manual
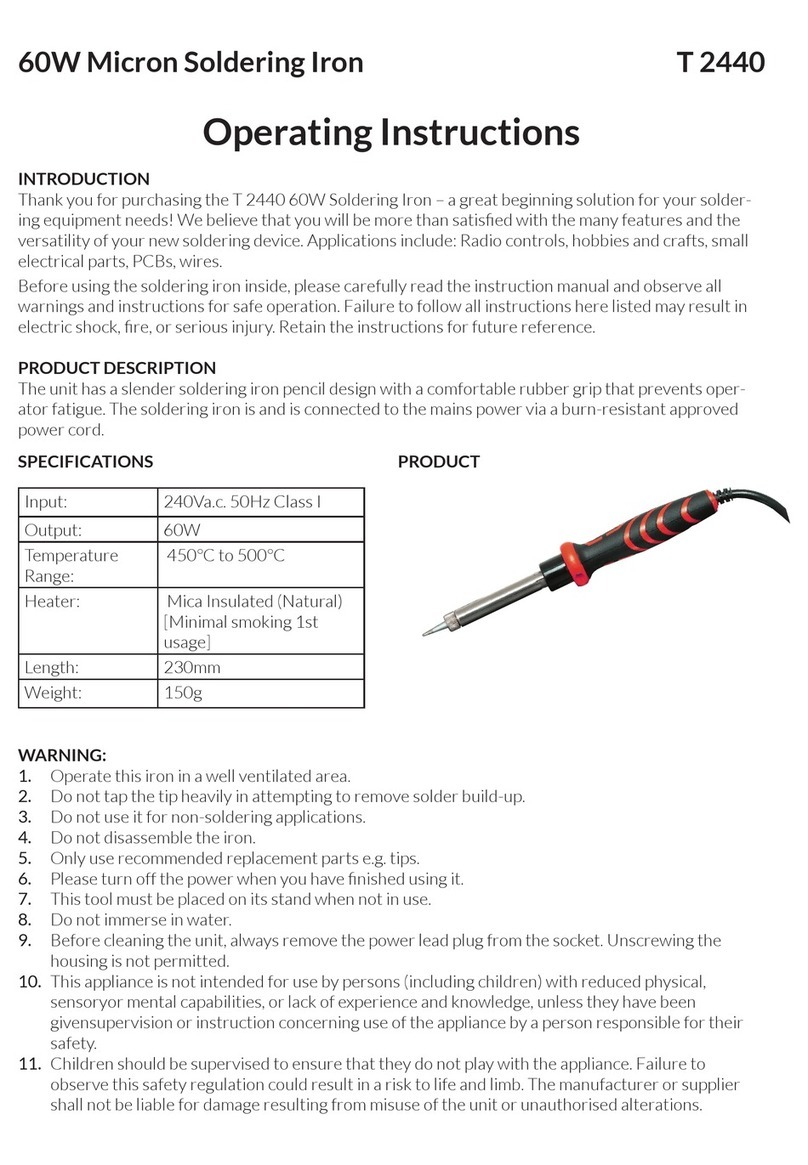
Altronics
Altronics T 2440 operating instructions
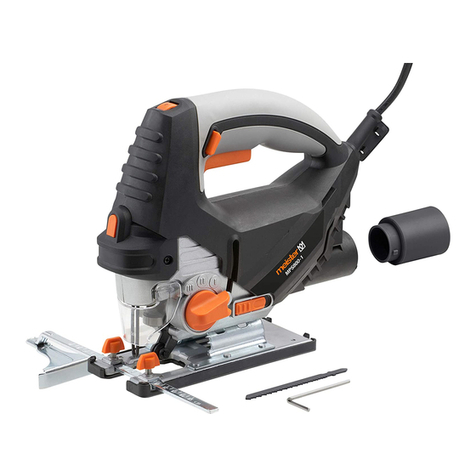
Meister
Meister MPS800-1 Translation of the original instructions
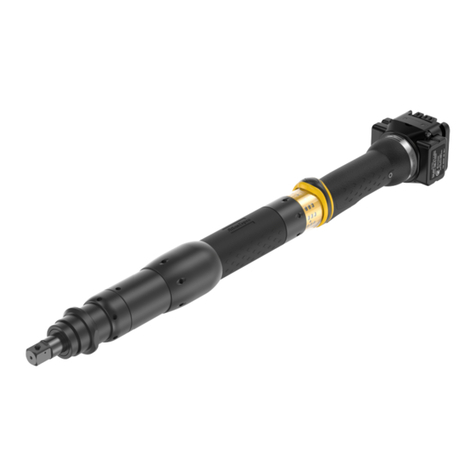
Atlas Copco
Atlas Copco STB64-40-13 Safety information
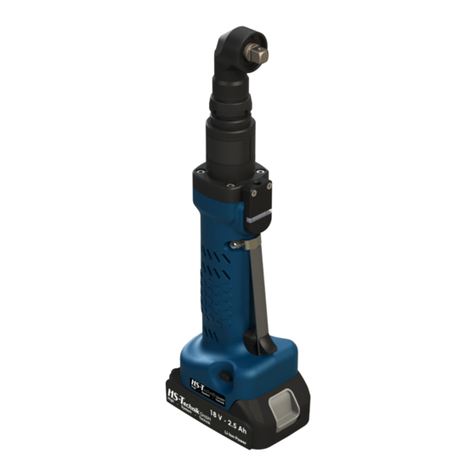
HS-Technik
HS-Technik TorqBee TBASL-5-2 operating instructions
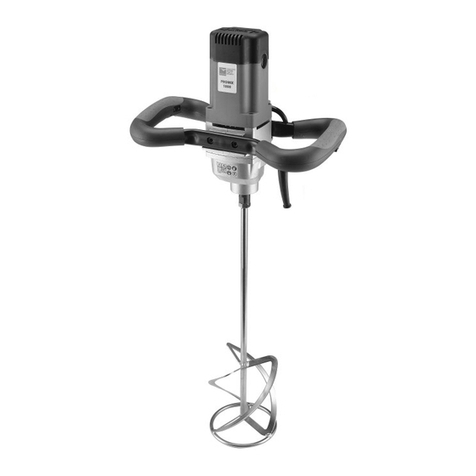
Altrad
Altrad PROMIX 1800 Original instructions, safety instructions, spare parts
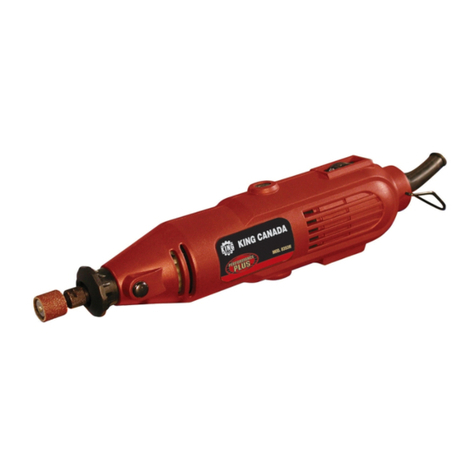
King Canada
King Canada 8353N instruction manual
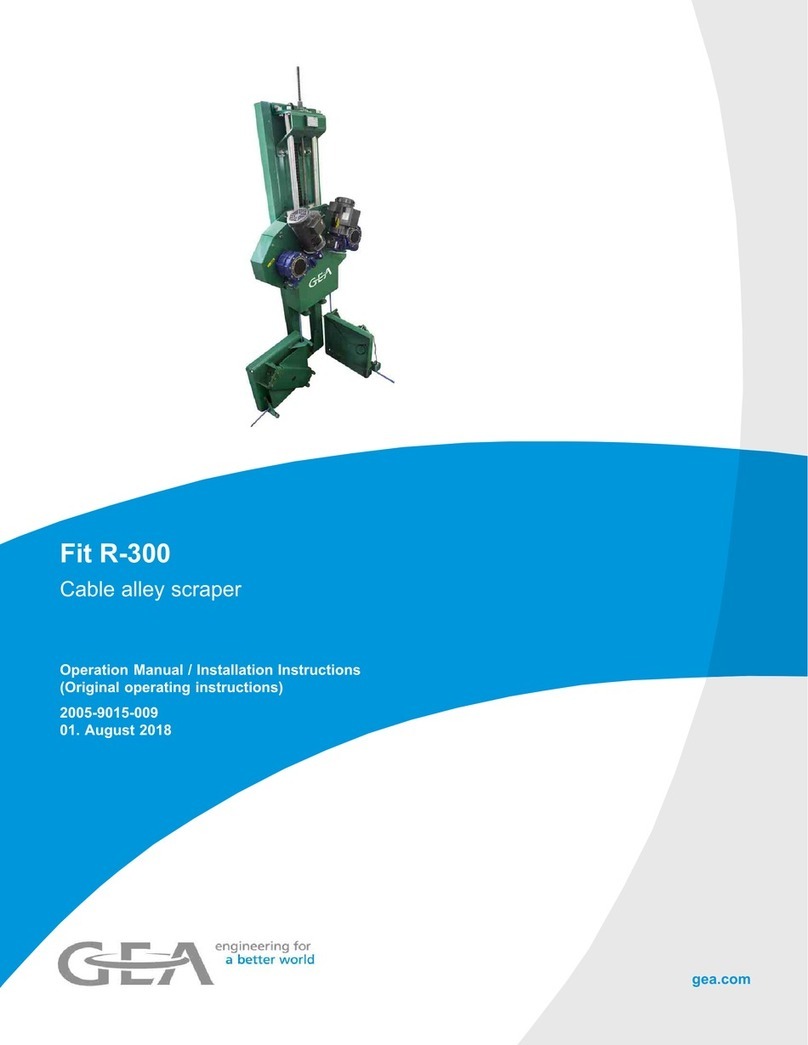
GEA
GEA Fit R-300 Operation manual and installation instructions
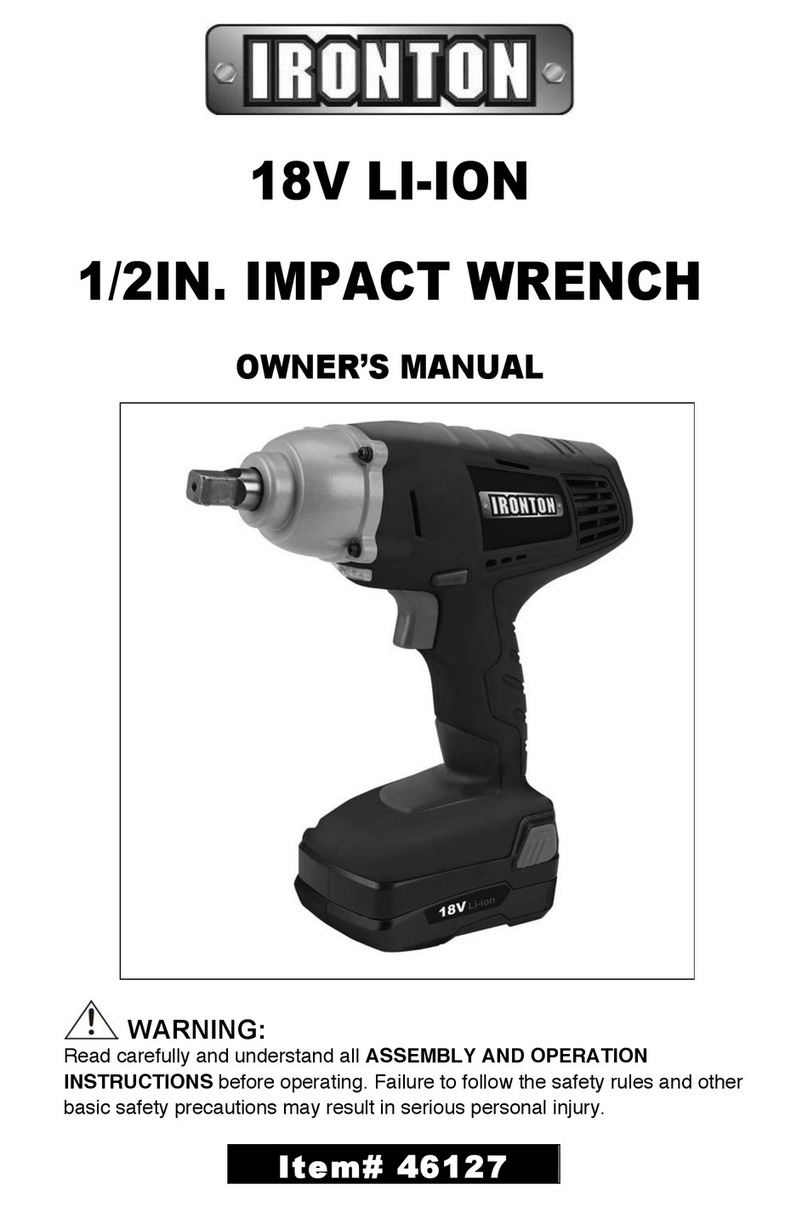
Ironton
Ironton 46127 owner's manual
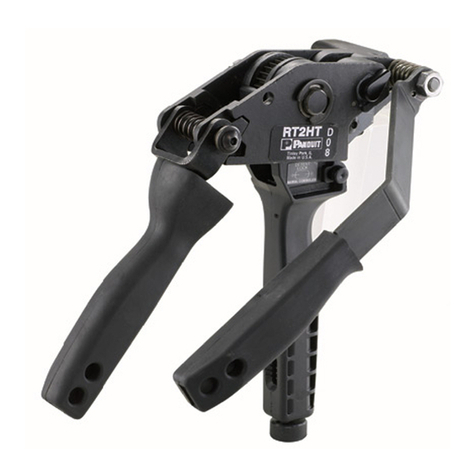
Panduit
Panduit RT2HT Operation instructions
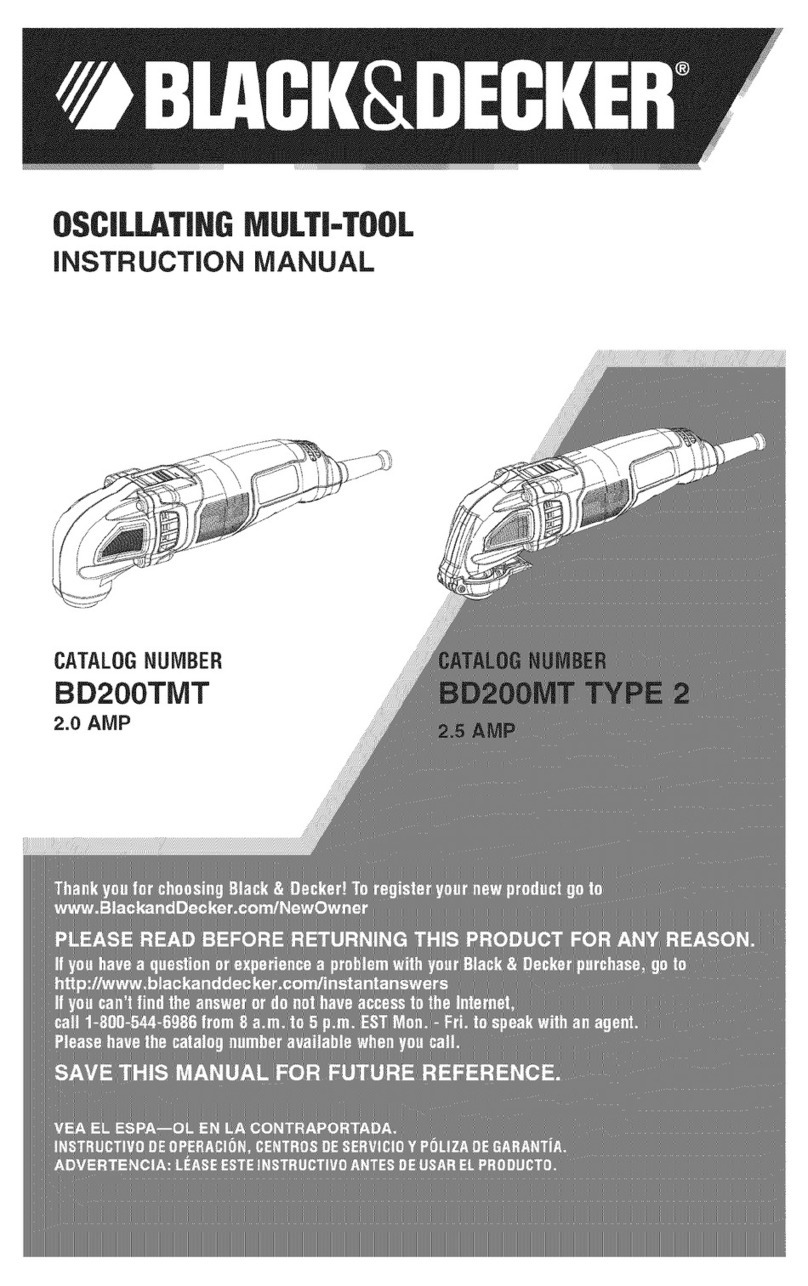
Black & Decker
Black & Decker BD200TMT instruction manual