Global AcuDrill User manual

USER MANUAL
DRILLING MACHINE
FOR UNDER PRESSURE MAINS
MODEL AcuDrill
Revision No. 4 - June 2016
Publication: MU-41-14E

DATOS DEL FABRICANTE
MANUFACTURER DATA
ACUSTER GLOBAL, S.L.
Ctra. Montcada, 608
08223 Terrassa (Barcelona) - SPAIN
Tel. (+34) 93 736 18 80
e-mail: [email protected]
DATOS DEL DISTRIBUIDOR Y SAT
DISTRIBUTOR AND SERVICE DATA
STP Acuster Internacional
Crta. Montcada, 608
08223 Terrassa (Barcelona) - SPAIN
hello @stpacuster.com
+34937361880
STP Acuster North Europe
Ind. terrein de Wildeman, hof 4
Bossekamp 12
5301 LZ Zaltbommel - The Netherlands
+31418840003
STP Acuster Central Europe
2, Kvetna 685, Areal Salvia
736 61 Napajedla - Czech Republic
+420577913065
STP Acuster Baltics
Bullu str. 45
Riga, LV1067 - Latvia
+37167815281
STP Acuster South Africa
54 Richard Road, Industria North
PO BOX 2203 Wilro Park
1731 Roodepoort - South Africa
+27315397451
Agru Acuster Chile
Lo Echevers 891,
Bodegas 11 y 12, Quilicura,
Santiago - Chile
+56229493910
Agru Acuster Brasil
Rua Saburo Sumiya, 211
Aldeia, Barueri, SP
CEP: 06440-110 – Brasil
+55114138088
NOTES !
The modifications carried out against the previous revision of this
publication are indicated with 2on the right margin.

USER MANUAL
AcuDrill DRILLING MACHINE
Edition: June 2016
Revision: No. 4 GENERAL CONTENTS - 3
CONTENTS:Page:
CHAPTER 1: INTRODUCTION............................................................................ 5
1.1 Introduction........................................................................ 5
1.2 General information............................................................. 5
1.3 “CE” declaration of conformity............................................... 6
1.4 Guarantee.......................................................................... 7
CHAPTER 2: MACHINE DESCRIPTION................................................................. 8
2.1 Components of the drilling machine....................................... 8
2.2 Machine accessories............................................................ 10
2.3 Hole saws diameters and characteristics................................. 11
CHAPTER 3: MODE OF OPERATION.................................................................... 12
3.1 Drilling under pressure over AcuStop-R branch connections..... 12
3.1.1 Initial operations....................................................... 12
3.1.2 Branch connection installation..................................... 12
3.1.3 Assembly of the drilling machine................................. 12
3.1.4 Pressure test............................................................ 13
3.1.5 Drilling the mains...................................................... 14
3.1.6 Plugging the branch connection................................... 15
3.1.7 Disassembly of the machine and accessories................. 15
3.1.8 Connecting the branch connection............................... 16
3.2 Pressureless drilling over CA-R branch connections................. 17
3.2.1 Initial operations....................................................... 17
3.2.2 Branch connection installation..................................... 17
3.2.3 Assembly of the drilling machine................................. 17
3.2.4 Drilling the mains...................................................... 18
3.2.5 Disassembly of the machine and accessories................. 19
3.2.6 Connecting the branch connection............................... 19
3.3 Drilling under pressure over CA-R branch connections............. 20
3.3.1 Initial operations....................................................... 20
3.3.2 Branch connection installation..................................... 20
3.3.3 Assembly of the cutoff valve....................................... 20
3.3.4 Assembly of the drilling machine................................. 21
3.3.5 Pressure test............................................................ 22
3.3.6 Drilling the mains...................................................... 22
3.3.7 Disassembly of the machine and accessories................. 23
3.3.8 Connecting the branch connection............................... 23
3.4 Pressureless drilling over ACUFLEX/BH525 branch connections. 24
3.4.1 Initial operations....................................................... 24
3.4.2 Branch connection installation..................................... 24
3.4.3 Assembly of the drilling machine................................. 24
3.4.4 Drilling the mains...................................................... 25
3.4.5 Disassembly of the machine and accessories................. 26
3.4.6 Connecting the branch connection............................... 26

USER MANUAL
AcuDrill DRILLING MACHINE
Edition: June 2016
- GENERAL CONTENTS Revision: No. 44
Page:
3.5 Drilling under pressure fittings for gas: 3-Way Tees 1½”&2"..... 27
3.5.1 Initial operations....................................................... 27
3.5.2 Fitting mains installation............................................ 27
3.5.3 Sandwich valve installation......................................... 27
3.5.4 Assembly of the drilling machine................................. 27
3.5.5 Pressure test............................................................ 28
3.5.6 Drilling the mains...................................................... 29
3.5.7 Plugging the fitting.................................................... 30
3.5.8 Disassembly of the machine and accessories................. 30
3.5.9 Installation of the fitting internal plug.......................... 30
NEW ! 3.6 Drilling under pressure fittings for gas: 3-Way Tees 1"............. 32
3.6.1 Initial operations....................................................... 32
3.6.2 Fitting mains installation............................................ 32
3.6.3 Sandwich valve installation......................................... 32
3.6.4 Assembly of the drilling machine................................. 33
3.6.5 Pressure test............................................................ 33
3.6.6 Drilling the mains...................................................... 34
3.6.7 Plugging the fitting.................................................... 34
3.6.8 Disassembly of the machine and accessories................. 35
3.6.9 Installation of the fitting internal plug.......................... 35
CHAPTER 4: MAINTENANCE.............................................................................. 37
4.1 General information............................................................. 37
CHAPTER 5: TECHNICAL CHARACTERISTICS....................................................... 38

USER MANUAL
AcuDrill DRILLING MACHINE
Edition: June 2016
Revision: No. 4
INTRODUCTION - 5
SECTION 1: INTRODUCTION
1.1 INTRODUCTION
The AcuDrill dri ing machine is especia y designed to dri on mains, under pressure or
pressure ess, on any type of materia : gray-iron casting, ducti e casting, PVC, PE, PP,
asbestos cement, po yester, c ay, stee , etc. It is especia y designed to be used on branch
connections or threaded accessories.
The machine dome is connected to the threaded out ets of sadd es through threaded
adapters. The sizes of the avai ab e adapters are 3/4", 1", 1¼”, 1½” and 2" BSP. It a ows
ho es of up to 48 mm diameter to be dri ed, using standard ho e saws of high-speed stee
or tungsten carbide tipped ho e saws with coupon retainer-equipped pi ot dri . The
chuckshaft can be fixed in three different positions according to the position of the
accessories to be dri ed.
It can be operated manua y by means of a ratchet wrench provided with a revo ving
hand e, a though it is designed to be used through a swive gear with either an e ectric,
pneumatic or hydrau ic actuator.
For dri ing mains under pressure, the maximum a owab e pressure is 16 bar (for water
mains) and 5 bar (for gas mains).
The machine is equipped with an absorbing mechanism that ensures a soft and regu ar
operation system of the dri and ho e saw over the pipe during dri ing, absorbing
excessive feed that cou d ead to b ocking of the ho e saw, a owing continuous dri ing.
The set inc udes a dome with bui t-in spind e, a machine body, chuckshaft, two arbor ho e
saws with pi ot dri (with coupon retainer system), an spanner for the dome adapters,
a 3 mm A en key, a ½” ratchet wrench with revo ving hand e, in addition to a carrying
case and User Manual.
The technica information provided in this Manual is pure y informative, and subject to
change without prior notification. ACUSTER GLOBAL, SL. sha not be responsib e for any
c aims derived from misuse of this pub ication or any errors and/or omissions that cou d
be detected in it fo owing its pub ication.
1.2 GENERAL INFORMATION
The deve opment, documentation, production, testing and shipping of the products
described have been performed:
C in comp iance with the app icab e safety ru es, and
C in accordance with the Acuster G oba , SL. qua ity assurance requirements.
WARNING !
On y qua ified personne are authorized to perform dri ing work with the
AcuDrill dri ing machine. Qua ified personne must be fami iar with a safety
measures, potentia hazards and maintenance ru es described in this
Manual.
The safe usage of the products described herein requires appropriate
transport, storage, insta ation and use, carefu treatment and comp iance
with the pre-estab ished regu ar maintenance.

USER MANUAL
AcuDrill DRILLING MACHINE
Edition: June 2016
- INTRODUCTION
Revision: No. 4
6
1.3 “CE” DECLARATION OF CONFORMITY
ACUSTER GLOBAL, S.L.
Ctra. Montcada, 608
08223 Terrassa (Barce ona)
SPAIN
we dec are, under our so e responsibi ity that the AcuDrill dri ing machine
has been manufactured in comp iance with the fo owing specifications:
Directive Related specificatio Model
2006/42/CE
Machine safety Directive
EN-ISO 12100
EN 60204-1
AcuDrill
Sant Just Desvern, 13
th
May 2005
Jaume Puig
Genera Manager

USER MANUAL
AcuDrill DRILLING MACHINE
Edition: June 2016
Revision: No. 4
INTRODUCTION - 7
1.4 GUARANTEE
Guara tee declaratio :
A AcuDrill dri ing machines are manufactured from high qua ity materia and
have been subjected to rigorous tests for resistance and working order as we
as passing a the qua ity contro tests required by the app icab e normative (see
"CE" Dec aration of conformity).
Regard ess of whether an incident might occur during the period of guarantee,
we recommend a carefu reading of the fo owing genera guarantee conditions.
Ge eral co ditio s of Guara tee:
1. ACUSTER GLOBAL S.L. guarantees that this product has no
manufacturing defect at the time of its purchase and extends this
guarantee for the period of TWO years.
2. If the product proves defective during this period, due to the materia s or
its assemb y, it wi be repaired free of charge, inc uding the cost of
materia s and abour at Acuster G oba , SL.'s Technica Service.
3. The Guarantee is not va id in the fo owing cases:
When the fau t in the product is a resu t of:
! Usua wear and tear due to usage.
! Abuse or incorrect use of the unit
! Repairs carried out without authority from Acuster G oba , S.L..
! Accidents, natura disasters (inc uding ightning, water action etc) as
we as any cause beyond Acuster G oba , S.L.'s contro .
4. In a c aims against this guarantee, information re ating to the mode ,
date of purchase, Seria number and any other additiona information
must at a times be stated.

USER MANUAL
AcuDrill DRILLING MACHINE
Edition: June 2016
- MACHINE DESCRIPTION
Revision: No. 4
8
SECTION 2: MACHINE DESCRIPTION
2.1 COMPONENTS OF THE RILLING MACHINE
The AcuDrill drilling machine assembly is made of the following components:
Figure 1
1Carrying case with die cut foam
2rilling machine
3ome adapter spanner
4Ratchet wrench with revolving handle
53mm Allen key
6Arbor hole saws (14 to 30 mm) featuring pilot drill with coupon retainer
7Arbor hole saws (32 to 46 mm) featuring pilot drill with coupon retainer

USER MANUAL
AcuDrill DRILLING MACHINE
Edition: June 2016
Revision: No. 4
MACHINE DESCRIPTION - 9
Main parts of the AcuDrill drilling machine:
1ome with spindle
2" BSP threaded with i er O-ri g to
screw threaded adapters of the saddle or
accessory to be drilled.
2Venting valve
PN16 valve for depressurizi g a d
pressurizi g test operatio s.
3Machine body
I cludes e d travel mecha ism a d
absorbi g mecha ism to optimize drilli g
power.
4 CE identification plate
Marki g pursua t to Machi ery Safety
Directive.
5End travel mechanism
Blocks the machi e’s e d travel but
allows a ma ual release through the
retractable ha dle.
6Chuckshaft
Features three faste i g ope i gs to
select the most appropriate le gth for
drilli g.
7Chuckshaft fastening bush
This is the eleme t that joi s the
chuckshaft with the absorbi g
mecha ism. It features a mark i dicati g
the maximum feed limit.
8Chuckshaft fastening mechanism
This allows quick a d safe faste i g of
the chuckshaft to the faste i g bush.
Figure 2

USER MANUAL
AcuDrill DRILLING MACHINE
Edition: June 2016
- MACHINE DESCRIPTION
Revision: No. 4
10
2.2 MACHINE ACCESSORIES
The AcuDrill drilling machine also features the following accessories:
Figure 3a: Sta dard accessories Figure 3b: Drilli g kit 1" (#141143)
1Saddle adapter kit of 3/4", 1", 1-
1/4", 1-1/2" and 2" (optional kit
of 2-3/4").
1a Saddle adapter.
1b Metal-rubber washer.
1c Variable pitch hole saws of 19,
22, 30, 33 and 46 mm,
respectively.
I additio to the hole saws
sizes i dicated above, other
optio al sizes ca be ordered.
There are special hole saws for
drilli g PE pipes.
For additional information, refer
to clause 2.3 of this Ma ual.
2½" Arbor hole saw with drill (for
hole saws of 14 to 30 mm) and
arbor hole saws of 5/8" with drill
(for hole saws of 32 to 46 mm).
2a Arbor hole saws without drill.
2b Pilot drill of 6.35 mm diameter,
with coupon retainer (optionally
6.25 HSS pilot drills with or
without coupon retainer are also
available).
3Chuckshaft adapter to an electric
drilling machine. Two options: 1)
female square drive of ½" x ½"
thread and 2) female square
drive of ½" x 5/8" thread.
4Ch u ck sh a ft ad a pt er to
pneumatic machine. Female
square drive of ½".
The kit 1" is composed of:
1ome adapter 1"
2Sandwich valve 1" (with driven key)
3Arbor hole saw with drill 10 mm.
4Tool for inside plug installation.
52½” sandwich valve with 1½” and 2"
adapters for 3-way tees and TOR-
threaded O-rings.
62"-2½” drilling machine dome-
sandwich valve adapter.
7Tool for inside plug installation.

USER MANUAL
AcuDrill DRILLING MACHINE
Edition: June 2016
Revision: No. 4
MACHINE DESCRIPTION - 11
2.3 HOLE SAW IAMETERS AN CHARACTERISTICS FOR ACU RILL & ACU RILL PLUS
ADAPTER
SIZE
ADAPTER
INSIDE
DIAMETER
HOLE SAW DIAMETER (MA *)
APPLICATION
Bi-metal
HSS
Tungsten
Carbide Grit
For plastic
pipes
3/4" 20 19 19 19 Acu rill
1" 24,5 22 22 22 Acu rill
1¼” 32,5 30 29 30 Acu rill
1½” 37,5 33 32 35 Acu rill
2" 49 46 44 48 Acu rill+Acudrill Plus
2½” 65 60 60 60 Acu rill Plus
3” 78 76 76 76 Acu rill Plus
N65/80 78 60 / 76 60 / 76 62/76 Acu rill Plus
N100/125 125,8 95 / 121 95 / 121 98/114 Acu rill Plus
N150 160,3 146 146 146 Acu rill Plus
N200 184,7 177 152 160 Acu rill Plus
GENERAL CHARACTERISTICS
Bi-metal HSS:
Hole saw made of speed steel type M3.
Sizes: from 14 to 210 mm; cutting depth of 35 mm.
Long series: request information (cutting depth of 48 mm).
Application: standard pipelines made of ductile iron, steel and asbestos
cement.
Tungsten carbide:
Hole saw made from tungsten carbide tooth welded on a solid body of
special steel.
Sizes: from 19 to 152 mm; cutting depth of 38 mm.
Application: pipelines made of ductile iron and steel.
For plastic pipes:
Hole saw made of tungsten carbide tooth welded on a sheet body.
Sizes: from 16 to 210 mm; cutting depth of 50-55 mm.
Application: plastic pipelines, such as PE, PP, PVC, etc.
(MAX*) The indicated hole saw diameter is the one recommended based on:
CAvailable diameters according to the hole saw supplier.
CMaximum diameter depending on the drilling machine adapter used.
CMaximum diameter depending on the saddle, T-clamp, valve (full bore), connecting
accessories, etc., of the N used.

USER MANUAL
AcuDrill DRILLING MACHINE
Edition: June 2016
- MODE OF USE
Revision: No. 4
12
SECTION 3: MODE OF OPERATION
3.1 DRILLING UNDER PRESSURE O ER ACUSTOP-R BRANCH CONNECTIONS
3.1.1 Initial operations:
Before performing the drilling operations, ensure that you have all
the necessary material and that it is in good condition.
CComplete drilling machine.
CArbor hole saw (with pilot drill installed) matching the size of
the hole saw to be used.
CHole saw of the diameter to be used.
CAdapter (with washer) of the diameter of the thread matching
the saddle to be installed.
CTools: 3 mm Allen key, adapter spanner, 17 mm open-end
spanner, ½” ratchet wrench (manual drilling) and electrical
or pneumatic swivel gear with chuckshaft adaptation
elements (if applicable).
3.1.2 ranch connection installation:
The installation of the AcuStop-R branch connection is performed
placing the saddle and sealing gasket on the pipe. Next, fasten the
clamp between the saddle and mains (the hinge joints should remain
above the saddle), equally tightening the two fastening bolts to
ensure tightness.
For more information, refer to the Fitting Instructions
included with the accessory.
Figure 4
3.1.3 Assembly of the drilling machine:
CSet up the arbor hole saws with the pilot drill in the chuckshaft. Screw the hole
saw matching the threaded outlet of the branch connection into the arbor hole
saw. See Figure 5.
CChoose the adapter that matches the thread of the saddle and screw it into the
machine dome. See Figure 6.
This operation can be performed manually. If necessary, use the dome
adapter spanner included with the equipment.
CFor this type of branch connection, position the retention mechanism in the lowest
of the three anchoring openings on the chuckshaft. See Figure 7.

USER MANUAL
AcuDrill DRILLING MACHINE
Edition: June 2016
Revision: No. 4
MODE OF USE - 13
Figure 5 Figure 6 Figure 7
CPlace the body of the machine in its upper position (unscrew it until the end travel
mechanism is released). Now install the AcuDrill drilling machine by screwing it
onto the saddle of the branch connection. The adapter must have the washer
installed.
WARNING !
If the support face of the saddle is not flat enough, apply Teflon tape to
the adapter thread to achieve tightness.
Manually tighten the machine body. If necessary, retighten using the
dome adapter spanner included with the equipment.
3.1.4 Pressure test:
Once the drilling machine set and accessories are installed on
the saddle of the branch connection, perform a pressure test.
To do so, apply compressed air through the venting valve to
check tightness of the assembly (see Figure 8).
Once the interior is pressurized, and with the venting valve
closed, check for leaks in the threaded connections or the
gasket at the mains head seat gasket using a spray detector or
soapy water. Correct in case of leaks.
Once the check is complete, open the venting valve to
depressurize, then leaving it in the “closed” position.
Figure 8

USER MANUAL
AcuDrill DRILLING MACHINE
Edition: June 2016
- MODE OF USE
Revision: No. 4
14
3.1.5 Drilling the mains:
Once the pressure test is complete, lower the chuckshaft by rotating the machine body
(with your hand in the knurled area), until the pilot drill makes contact with the pipe (the
chuckshaft will have risen depending on the contact force: see measurement a of Figure
9). At this point, withdraw the tip of the drill from the pipe by approximately one turn.
Now begin drilling the mains by activating the chuckshaft using the ratchet wrench, if
drilling is manual, or through the electrical or pneumatic swivel gear.
SWI EL GEAR
If an electrical actuation swivel gear (drilling machine) or pneumatic
swivel gear (pneumatic, non-impact tool) is used, the following
considerations must be taken into account:
C The rotation speed must be that indicated by the hole saw
manufacturer.
C The adapter components may be supplied by Acuster Global, SL.
C The usage and safety recommendations given by the manufacturer
must be followed.
The feed is achieved by making the machine body rotate
(with the hand placed in the knurled area). The
recommended distance produced by the feed is a = 1 or 2
mm (see Figure 9) when drilling with the pilot drill. Once
perforated with the drill, remember that distance a will be
increased by the internal driving pressure. The feed limit is
indicated by a mechanized line on the fastening bush shaft.
If due to an excess of compression (feed + internal
pressure) this line becomes visible (see Figure 9), turn
slightly in the opposite direction to return to the previously-
recommended distance.
Ensure that the drilling is complete by making one or two
additional turns.
Figure 9
WARNING !
It is recommended to avoid excess feed, especially in the pilot drill work
phase, given that the drill could break specially at low revolutions.

USER MANUAL
AcuDrill DRILLING MACHINE
Edition: June 2016
Revision: No. 4
MODE OF USE - 15
3.1.6 Plugging the branch connection:
Once the mains has been perforated, move the chuckshaft up by turning the machine
body counterclockwise until the hole saw is positioned in the upper part of the dome.
Carefully open the venting valve to remove chip residues. Next, close the valve again.
Now carry out the plugging to facilitate disassembly of the machine and the subsequent
connection to the branch connection.
Figure 10 Figure 11
To do so, the slot in the saddle for the introduction of the spatula must be fully
accessible. Slightly raise the clamp-gasket assembly of the saddle closure to keep it from
interfering with the handle of the spatula during the introduction. See Figure 10.
The clamp-gasket assembly is delivered flush with the upper face of the
saddle and with the fastening bolt untightened.
Place the pivoting shaft of the spatula in the opening of the saddle (use the small spatula
to plug branch connections with threaded outlets of 3/4” to 1½” and the large spatula
for branch connections with 2” threaded outlet). Insert the spatula all the way to the
bottom through the slot of the saddle. See Figure 11.
3.1.7 Disassembly of the machine and accessories:
Before carrying out the disassembly of the drilling machine, check the tightness of the
spatula by opening the venting valve. There should not be any fluid overflow, unless it
is the amount remaining in the interior before fitting the spatula. Correct the position of
the spatula in case of leak or determine the causes of any possible loss.
Once the check is complete, return the venting valve to the closed position.
Disassemble the saddle adapter and drilling machine using the spanner designed for this
purpose.

USER MANUAL
AcuDrill DRILLING MACHINE
Edition: June 2016
- MODE OF USE
Revision: No. 4
16
The coupon resulting from drilling the main will have remained trapped by the pilot drill’s
coupon retainer mechanism. To extract the coupon, disassemble the drill by loosening the
Allen fastening stud. Remove the coupon through the upper part of the drill and fit it to
the arbor hole saw again. See Figure 12.
Figure 12 Figure 13
3.1.8 Connecting the branch connection:
Make the proper connections at the threaded outlet of the saddle. If necessary, perform
a pressure test on the new section.
Completely withdraw the spatula (to allow fluid flow). Next slide the exterior clamp-
gasket assembly all the way down. Tighten the fastening bolt of the exterior clamp-gasket
assembly to its end travel. See Figure 13.
The tightening bolt must remain positioned on the opposite side from the
spatula insertion slot, as it is delivered stock.
Retighten the fastening bolts of the branch connection.

USER MANUAL
AcuDrill DRILLING MACHINE
Edition: June 2016
Revision: No. 4
MODE OF USE - 17
3.2 PRESSURELESS DRILLING VER CA-R BRANCH C NNECTI NS
3.2.1 Initial operations:
Before performing the drilling operations, ensure that you have all
the necessary material and that it is in good condition.
CComplete drilling machine.
CArbor hole saw (with pilot drill installed) matching the size of
the hole saw to be used.
CHole saw of the diameter to be used.
CAdapter (with washer) of the diameter of the thread matching
the saddle to be installed.
CTools: 3 mm Allen key, adapter spanner, 17mm open-end
spanner, ½" ratchet wrench (manual drilling) and electrical
or pneumatic swivel gear with chuckshaft adaptation
elements (if applicable).
3.2.2 Branch connection installation:
The installation of the CA-R branch connection is performed placing
the saddle and gasket on the pipe. Next, fasten the clamp between
the saddle and mains (the hinge joints should remain above the
saddle), equally tightening the two fastening bolts to ensure
tightness.
For more information, refer to the Fitting Instructions
included with the accessory.
Figure 14
3.2.3 Assembly of the rilling machine:
CSet up the arbor hole saws with the pilot drill in the chuckshaft. Screw the hole
saw matching the threaded outlet of the branch connection into the arbor hole
saw. See Figure 15.
CChoose the adapter that matches the thread of the saddle and screw it into the
machine dome. See Figure 16.
This operation can be performed manually. If necessary, use the dome
adapter spanner included with the equipment.

USER MANUAL
AcuDrill DRILLING MACHINE
Edition: June 2016
- MODE OF USE
Revision: No. 4
18
Figure 15 Figure 16 Figure 17
CFor this type of branch connection and intervention, position the retention
mechanism in the lowest of the three anchoring openings on the chuckshaft. See
Figure 17.
CPlace the body of the machine in its upper position (unscrew it until the end travel
mechanism is released). Now install the AcuDrill drilling machine screwing it onto
the saddle of the branch connection. The adapter must have the washer installed.
WARNING !
If the support face of the saddle is not flat enough, apply Teflon tape to
the adapter thread to achieve tightness.
Manually tighten the machine body. If necessary, retighten using the
dome adapter spanner included with the equipment.
3.2.4 Drilling the mains:
nce the machine set and saddle accessories are assembled, lower the chuckshaft by
rotating the machine body (with your hand in the knurled area), until the pilot drill makes
contact with the pipe (the chuckshaft will have risen depending on the contact force: see
measurement a of Figure 18). At this point, withdraw the tip of the drill from the pipe by
approximately one turn.
Now begin drilling the mains by activating the chuckshaft using the ratchet wrench, if
drilling is manual, or through the electrical or pneumatic swivel gear.

USER MANUAL
AcuDrill DRILLING MACHINE
Edition: June 2016
Revision: No. 4
MODE OF USE - 19
SWIVEL GEAR
If an electrical actuation swivel gear (drilling machine) or pneumatic
swivel gear (pneumatic, non-impact tool) is used, the following
considerations must be taken into account:
C The rotation speed must be that indicated by the hole saw
manufacturer.
C The adapter components may be supplied by Acuster Global, S.L.
C The usage and safety recommendations given by the manufacturer
must be followed.
The feed is achieved by making the machine body rotate (with
the hand placed in the knurled area). The recommended
distance produced by the feed is a = 1 or 2 mm (see Figure
18). The feed limit is indicated by a mechanized line on the
fastening bush shaft. If due to an excess of compression (feed
+ internal pressure) this line becomes visible (see Figure 18),
turn slightly in the opposite direction to return to the
previously-recommended distance.
WARNING !
It is recommended to avoid excess feed,
especially in the pilot drill work phase, given
that the drill could break specially at low
revolutions.
Figure 18
3.2.5 Disassembly of the machine an accessories:
nce the mains has been perforated, move the chuckshaft up by
turning the machine body counterclockwise.
Disassemble the saddle adapter and drilling machine using the
spanner designed for this purpose.
The coupon resulting from drilling the main will have remained
trapped by the pilot drill’s coupon retainer mechanism. To extract
the coupon, disassemble the drill by loosening the Allen fastening
stud. Remove the coupon through the upper part of the drill and
fit it to the arbor hole saw again. See Figure 19.
WARNING !
Do not touch the coupon following drilling,
especially if an electrical or pneumatic swivel gear
has been used. Hot surfaces.
Figure 19
3.2.6 Connecting the branch connection:
Connect the branch connection to the threaded outlet of the saddle. Retighten the branch
connection fasteners.

USER MANUAL
AcuDrill DRILLING MACHINE
Edition: June 2016
- MODE OF USE
Revision: No. 4
20
3.3 DRILLING UNDER PRESSURE O ER CA-R BRANCH CONNECTIONS
3.3.1 Initial operations:
Before performing the drilling operations, ensure that you have all
the necessary material and that it is in good condition.
CComplete drilling machine.
CArbor hole saw (with pilot drill installed) matching the size of
the hole saw to be used.
CHole saw of the diameter to be used.
CAdapter (with washer) of the diameter of the thread matching
the saddle to be installed.
CIntermediate full bore valve, of the size corresponding to the
saddle’s threaded outlet. Adapter fitting (if necessary).
CTools: 3 mm Allen key, adapter spanner, 17 mm open-end
spanner, ½” ratchet wrench (manual drilling) and electrical or
pneumatic swivel gear with chuckshaft adaptation elements
(if applicable).
3.3.2 Branch connection installation:
The installation of the CA-R branch connection is performed placing
the saddle and gasket on the pipe. Next, fasten the clamp between
the saddle and mains (the hinge joints should remain above the
saddle), equally tightening the two fastening bolts to ensure
tightness.
For more information, refer to the Fitting Instructions
included with the accessory.
3.3.3 Assembly of the c toff valve: Figure 20
Install an intermediate valve (not supplied with the equipment).
Screw it directly (or through an adapter fitting) over the CA-R
branch connection previously installed on the line. Put the valve
actuation lever in OPEN position.
WARNING !
The total height (h) of the branch connection saddle +
selected intermediate valve and fitting (once
assembled) must not exceed 210 mm. See Figure 21.
Figure 21
Table of contents
Other Global Drill manuals
Popular Drill manuals by other brands
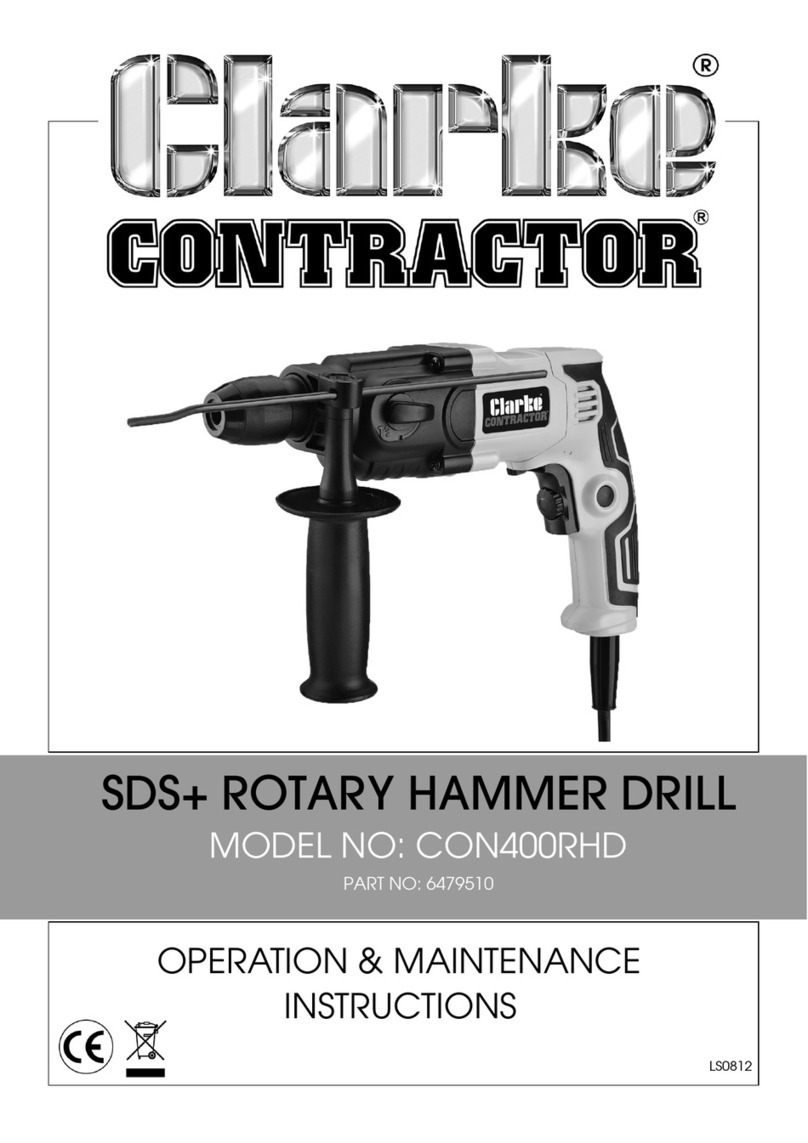
Clarke
Clarke CONTRACTOR CON400RHD Operation & maintenance instructions
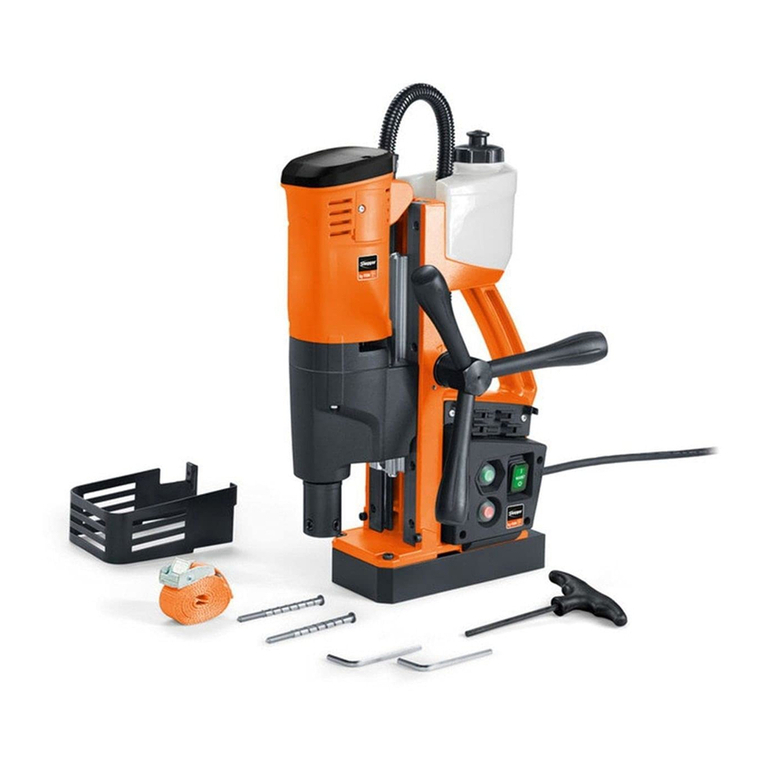
Fein
Fein Slugger JME Holemaker III instruction manual

Craftsman
Craftsman 28129 - Panasonic 21.6V Li-ion Hammer Drill Operator's manual
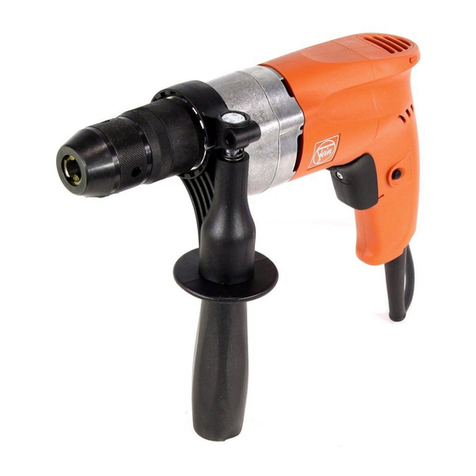
Fein
Fein BOP6 instruction manual

Westfalia
Westfalia CT 2408 instruction manual

Milwaukee
Milwaukee Hammer-Drill Operator's manual