Goblin urukay User manual


Goblin URUKAY Manual
Release 1.0 - October 2014
SAB HELI DIVISION
Via San Crispino N. 47
47030 San Mauro Pascoli (FC) ITALY
WORLD DISTRIBUTION
www.goblin-helicopter.com
For sales inquiries, please email:
For info inquiries, please email:
Attention: If you are a consumer and have questions or need of assistance,
please contact in a first time the Goblin retailer where you made the purchase
EUROPEAN DISTRIBUTION
www.sabitaly.it
For sales inquiries, please email:
For info inquiries, please email:
Attention: If you are a consumer and have questions or need of assistance,
please contact in a first time the Goblin retailer where you made the purchase

7 – Assembling The Modules
8 – Installation of Swashplate Servos
9 – Installation of The ESC
10 – Installation of Flybarless Unit and RX
11 – Installation of The Motor
12 – Tail Assembly
1 – Specifications
2 – Important Notes
3 – Components and Box
4 – Carbon frame Assembly
5 – Trasmission Assembly
6 – Main Rotor HPS2/HPS3
INDEX
13 – Installation of the Boom, Canopy
14 – Battery
15 – In flight
16 – Maintenance
17 – Exploded Views
18 – Spare Parts
//www.goblin-helicopter.com
http:
1648 - 1680 mm
394 mm
1440 mm
155 mm
SPECIFICATIONS
It is extremely important that you take a moment to register your helicopter with us. This is the only way to ensure that you are
properly informed about changes to your kit, such as upgrades, retrofits and other important developments. SAB Heli Division
cannot be held responsible for issues arising with your model and will not provide support unless you register your serial
number.
To mount the serial number tag on your helicopter, please refer to page 32.
Thank you for your purchase, we hope you enjoy your new Goblin helicopter!
SAB Heli Division
The Goblin Competition
is the result of all the feedback and experienced gained with the original Goblin.
All the changes incorporated into the Goblin Competition create a model even more reliable and efficient than ever before.
New colors, new composite materials and many upgrades are included in this kit making it the best Goblin ever.
Please read this user manual carefully, it contains instructions for the correct assembly of the model.
Please refer to the web site www.goblin-helicopter.com for updates and other important information.
VERY IMPORTANT
Inside Box 6, you will find Bag 21. This bag contains your serial number tag. Please take a moment to register your kit online
via our web site at:
Main rotor diameter:
* HPS3, 3 Blade main rotor: 1648mm with 730mm blades.
* HPS2, 2 Blade main rotor: 1680mm with 750mm blades.
Main blade length: up to 750mm
Tail rotor diameter: 304mm
Tail blade length: 115mm
Main shaft diameter: 12mm
Tail shaft diameter: 6mm
Spindle diameter: 10mm
Motor size: Maximum 64mm diameter, maximum height 64mm
Battery compartment: 60x58x350mm (adaptable to 75x58x350mm)
Page 1
Chapter 1, Specifications

IMPORTANT NOTES
*This radio controlled helicopter is not a toy.
*This radio controlled helicopter can be very dangerous.
*This radio controlled helicopter is a technically complex device which has to be built and handled very carefully.
*This radio controlled helicopter must be built following these instructions. This manual provides the necessary information
to correctly assemble the model. It is necessary to carefully follow all the instructions.
*Inexperienced pilots must be monitored by expert pilots.
*All operators must wear safety glasses and take appropriate safety precautions.
*A radio controlled helicopter must only be used in open spaces without obstacles, and far enough from people to minimize
the possibility of accidents or of injury to property or persons.
*A radio controlled helicopter can behave in an unexpected manner, causing loss of control of the model, making it very
dangerous.
*Lack of care with assembly or maintenance can result in an unreliable and dangerous model.
*
Neither SAB Heli Division nor its agents have any control over the assembly, maintenance and use of this product.
Therefore, no responsibility can be traced back to the manufacturer. You hereby agree to release SAB Heli Division from
any responsibility or liability arising from the use of this product.
SAFETY GUIDELINES
*Fly only in areas dedicated to the use of model helicopters.
*Follow all control procedures for the radio frequency system.
*It is necessary that you know your radio system well. Check all functions of the transmitter before every flight.
*The blades of the model rotate at a very high speed; be aware of the danger they pose and the damage they may cause.
*Never fly in the vicinity of other people.
NOTES FOR ASSEMBLY
Please refer to this manual for assembly instructions for this model.
Follow the order of assembly indicated. The instructions are divided into chapters, which are structured in a way that
each step is based on the work done in the previous step. Changing the order of assembly may result in additional or
unnecessary steps.
Use thread lockers and retaining compounds as indicated. In general, each bolt or screw that engages with a metal part
requires thread lock.
It is necessary to pay attention to the symbols listed below:
Important
Use retaining
compound
(eg Loctite 648)
Use retaining
compound
(eg Loctite 243)
Use CA Glue
Use Proper
Lubricant
Indicates that for this
assembly phase you need
materials that are in bag xx.
Bag xx
Page 2
Chapter 2, Important Notes

ADDITIONAL COMPONENTS REQUIRED
*Electric Motor: 400 - 560Kv
Maximum diameter 64mm,
Maximum height 64mm,
Pinion shaft diameter 6/8mm
*Speed controller: minimum 120A , suggest 160A
*Batteries: 12S-5000 mAh
*1 flybarless 3 axis control unit
*Radio power system, if not integrated with the ESC
*3 cyclic servos
*1 tail rotor servo
*6 channel radio control system on 2.4 GHz
(See configuration examples on page 18)
The assembly process is described in the following chapters.
Each chapter provides you with the box, bag and/or foam
tray numbers you will need for that chapter. The information
is printed in a green box in the upper right hand corner of the
page at the beginning of every chapter.
TOOLS, LUBRICANTS, ADHESIVES
*Generic pliers
*Hexagonal driver, size 1.5,2,2.5,3,4mm
*4mm T-Wrench
*5.5mm Socket wrench (for M3 nuts)
*8mm Hex fork wrench (for M5 nuts)
*Medium threadlocker (eg. Loctite 243)
*Strong retaining compound (eg. Loctite 648)
*Spray lubricant (eg. Try-Flow Oil)
*Grease ( eg. Microlube GL261 )
*Cyanoacrylate adhesive
*Pitch Gauge (for set-up)
*Soldering equipment (for motor wiring)
Inside the main box:
Box 2: Canopy, Blade Holder, Carbon parts.
Box 3: Boom,Carbon rod.
Box 4: Mechanical parts in 4 trays:
Tray 1: Main rotor.
Tray 2: Carbon frame and tail rotor.
Tray 3: Transmission.
Tray 4: Main structure.
Box 5: Bags, Blades.
Box 6: Bags, Tail Blades.
Inside the main box there are:
Page 3
Chapter 3, Components and Box

4-Carbon Frame
The manufacturing process of the carbon parts
often leaves micro-burrs and sharp edges. We
recommend de-burring the edges to minimize the
risks of electrical wire cuts, etc. Very important in
red line zone.
Page 4
Chapter 4, Carbon Frame

Frame Spacer
(H0003-S)
......x10
Flat Head Cap Screw M2.5x5mm
Flat Head Cap Screw
M2.5x5mm
(HC128-S)
Stop Battery Plate
(H0150-S)
Socket Head Cap Screw
M2.5x8mm
(HC020-S)
Flat Head Cap Screw
M2.5x5mm
(HC128-S)
ESC Support
(H0153-S)
Flat Head Cap Screw
M2.5x5mm
(HC128-S)
Flat Head Cap Screw
M2.5x5mm
(HC128-S)
Flat Head Cap Screw
M2.5x5mm
(HC128-S)
Battery Tray
(H0002-S)
Socket Head Cap Screw M2.5x8mm
......x2
Battery Tray Assembly
Note:
Bag 1.1
Page 5
Chapter 4, Carbon Frame

Frame Spacer
(H0003-S)
Socket Head Cap
Screw M3x10mm
(HC056-S)
Finishing
Washer M3
(H0007-S)
Battery Tray
Assembly
Main Frame
(H0445-S)
Tail Servo Support
(H0436-S)
Socket Head Cap
Screw M3x10mm
(HC056-S)
Finishing
Washer M3
(H0007-S)
Finishing
Washer M2.5
(H0255-S)
Left Main Frame Assembly
Cable Pass
(HA010-S)
Socket Head Cap
Screw M2.5x8mm
(HC020-S)
Canopy
Positioners
(HA106-S)
Washer
3,2x
6x0,5
(HC180-S)
Bag 1.2
Font Position for Battery Support
( Light Batteries < 1500-1600g )
Back Position for Battery Support
( Heavy Batteries > 1600-1700g )
Page 6
Chapter 4, Carbon Frame

Bag 1.2
Socket Head Cap
Screw M3x10mm
(HC056-S)
Finishing Washer M3
..... x4
Socket Head Cap Screw M3x10mm
..... x4
Socket Head Cap
Screw M3x10mm
(HC056-S)
Canopy Positioner
(HA106-S)
Finishing
Washer M3
(H0007-S)
Main Frame
(H0445-S)
Left Main Frame
Assembly
Washer
Ø3,2xØ6x0.5mm
(HC180-S)
Page 7
Chapter 4, Carbon Frame

Note:
You can use Super Glue for block
the nuts in correct position
Note:
Use the lower hole
Socket Head Cap
Screw M3x16mm
(HC068-S)
Finishing
Washer M3
(H0007-S)
Finishing
Washer M3
(H0007-S)
Socket Head Cap
Screw M3x16mm
(HC068-S)
Finishing
Washer M3
(H0007-S)
Socket Head Cap
Screw M3x12mm
(HC062-S)
Socket Head Cap
Screw M3x12mm
(HC062-S)
Finishing Washer M3
Socket Head Cap Screw M3x12mm
Metric Hex
Nylon Nut M3
(HC206-S)
Socket Head Cap Screw M3x10mm
.....x4
.....x4
.....x8
.....x8
Carbon Landing Gear
(H0446-S)
Finishing
Washer M3
(H0007-S)
Socket Head Cap
Screw M3x16mm
(HC068-S)
Finishing
Washer M3
(H0007-S)
Socket Head Cap
Screw M3x16mm
(HC068-S)
Finishing
Washer M3
(H0007-S)
Landing Gear
Support
(H0344-S)
Bag 2
Chapter 4, Carbon Frame
Page 8

Bearing
10x
19x5mm
(HC422-S)
Socket Head Cap
Screw M3x10mm
(HC056-S)
......x1
Finishing
Washer M3
(H0007-S)
Bearing
10x
19x5mm
......x1
Servo Support
(H0010-S)
Bearing
12x
24x6mm
(HC426-S)
Bearing
12x
24x6mm
(HC426-S)
Swash plate
Anti-Rotation Guide
(H0152-S)
Column
(H0018-S)
Socket Head Cap Screw
M3x10mm
......x2
......x1
......x3
Button Head Cap
ScrewM3x4mm
(HC038-S)
Antenna Guide
(H0050-S)
Main Structure
(H0009-S)
Bearing Support Assembly
(H0024-S)
......x1
......x4
Button Head Cap Screw
M3x4mm
......x1
Flat Head Cap Screw
M2.5x5mm
(HC128-S)
Socket Head Cap Screw
M3x8mm
Socket Head Cap
Screw M3x8mm
(HC050-S)
Bearing
12x
24x6mm
......x3
Socket Head Cap
Screw M3x10mm
(HC056-S)
Column
(H0018-S)
Bearing
10x
19x5mm
Bearing
12x
24x6mm
Socket Head Cap Screw
M3x10mm
Flat Head Cap Screw
M2.5x5mm
Bearing
10x
19x5mm
(HC422-S)
Note:
Socket Head Cap
Screw M3x10mm
(HC056-S)
Note:
You must be put strong main gear (H0320-S)
before you put 3 column on main structure
Bag 3
Page 9
Chapter 5, Transmission Assembly

One Way Bearing
10x
14x12mm
(HC442-S)
60T Pulley Assembly
(H0171-S)
Bearing
10x
15x4mm
(HC420-S)
Socket Head Cap Screw
Shouldered M2.5x19mm
(HC033-S)
One Way Bearing
10x
14x12mm
(HC442-S)
Bearing
10x
15x4mm
(HC420-S)
Front Tail Pulley Low
Assembly
(H0172-S)
Main Gear Assembly
(H0405-S)
6.25
4.8
Main Shaft
(H0127-S)
Main Structure
Assembly 1
Note 1:
When you tighten the collar (
H0121-S
) on
the main shaft, ensure there is no axial play.
Push down the main shaft while pulling up the
locking collar. Tighten the screw
M4x22
at this
time.
Note 2:
The pinion and gear are designed to have
zero backlash. This leads to initial “rough”
rotation. After some run in flights (
3-5 flights
) it
will begin to rotate freely, ensuring perfect
contact and the ability to transmit maximum
power.
It is very important to lubricate these two
elements with a lubricant
( Dry Fluids Gear or similar).
Socket Head Cap Screw M4x22mm
......x1
Socket Head Cap Screw
Shouldered M4x24mm
(HC111-S)
Socket Head Cap Screw Shouldered
M2.5x18mm
Socket Head Cap Screw Shouldered
M4x24mm
......x1
......x2
Metric Hex
Nylon Nut
(HC212-S)
Metric Hex Nylon
Nut M4
(HC212-S)
Socket Head Cap
Screw M4x22mm
(HC104-S)
Socket Head Cap
Screw Shouldered
M3x18mm
(HC079-S)
60T Pulley
(H0171-1)
60T Pulley Assembly
(H0171-S)
Metric Hex Nylon Nut M4
......x2
Socket Head Cap
Screw M2x10mm
(HC010-S)
Front Tail Pulley Assembly
(H0172-S)
Bush One Way
(H0110-S)
Note:
Put a small amount of grease
every 30/40 flights on the main
gear (for example Tri- flow
Synthetic grease)
Note 2
The perfect play is 0.5mm
add or remove shim for this
Note:
Correct insertion
of the one-way pulley
Washer
10x
16x0.2mm
(HC232-S)
Check the axial play
See Note 1.
37T Pulley
(H0172-S)
Secondary Shaft
(H0157-S)
M4 Locking Collar
(H0121-S)
Metric Hex Nylon
Nut M2.5
(HC200-S)
Main Gear
(H0405-S)
Metric Hex Nylon
Nut M3
(HC206-S)
19T Drive Pinion
(H0156-S)
eg: Microlube GL261
Bag 4
Main Gear
(H0405-S)
Screw M3x8mm
Page 10
Chapter 5, Transmission Assembly

Spring
de 8 / df0.5 / LL8
(HC315-S)
Flanged Bearing
5x
9x3mm
(HC410-S)
Flanged Bearing
3x
7x3mm
(HC402-S)
......x1
Button Head Cap Screw M3x4mm
......x1
Flanged Bearing
5x
9x3mm
......x2
Flanged Bearing
3x
7x3mm
......x2
Tail Belt Idler
[H0069]
Washer
3x
4x0.5mm
......x1
Belt Tensioner Arm
[H0071]
......x1
Washer
3x
4x0.5mm
(HC176-S)
Belt Tensioner Support
(H0174-S)
Socket Head Cap Screw M3x12mm
Socket Head Cap Screw M3x40mm
Socket Head Cap
Screw M3x12mm
(HC062-S)
Tail Belt Idler Assembly
(H0174-S)
Belt Tensioner Arm
Assembly
(H0174-S)
Washer
3.2x
6x0.5mm
(HC180-S)
Socket Head Cap
Screw M3x40mm
(HC091-S)
Main Structure
Assembly
Tail Belt Idler Assembly
(H0174-S)
Button Head Cap Screw
M3x4mm
(HC038-S)
Belt Tensioner Arm Assembly
(H0174-S)
Note:
Position without preload.
Insert the screw in the hole
through the aluminum
support as in the picture.
Bag 5
Page 11
Chapter 5, Transmission Assembly

Socket Head Cap
Screw M3x10mm
(HC056-S)
Finishing
Washer M3
(H0007-S)
Socket Head Cap
Screw M3x10mm
(HC056-S)
Spring
[HC314]
(HC315-S)
34mm
21mm
6mm
7mm
0.2mm
Set Screw
M4x6mm
(HC153-S)
Button Head Cap
Screw M4x8mm
(HC098-S)
20T Pulley
(H0175-20-S)
Lock motor pulley after locking H0142
(see page 18 for optional pulley selection)
Washer
5.3x
15x1mm
(HC188-S)
Metric Hex Nylon
Nut M5
(HC218-S)
Spring
[HC310]
(HC315-S)
Note
To maximize space for the batteries, it
is advisable to shorten the motor shaft.
Follow the dimensions given in this
drawing. For the cut, you can use an
electric tool like a “Dremel” with a cut-
off disc.
Additionally, ensure the motor shaft
has an appropriate 'flat' for one of the
set screws.
Socket Head Cap
Screw M3x8mm
(HC050-S)
Bearing Support (H0142-S) Lock
H0142 after have locked the motor.
Motor shaft is requires to optimize
the centering.
H0142 can not be
used with motor shaft 8mm.
Bushing
6x
8x18mm
(H0176-S)
Use with 6mm
motor shaft.
Motor Support
(H0143-S)
Set Screw M5x20mm
(HC158-S)
Motor
Flanged Bearing
6x
13x5mm
(HC414-S)
Bag 6
Page 12
Chapter 5, Transmission Assembly

* Clock-wise, counter clock-wise thread
* By turning the linkages you can adjust
tracking. If tracking is adjusted correctly,
you’ll see the metal part line up around
in the center of the opening.
Approx 76mm
A
DETAIL A
Spindle
(H0412-S)
Uniball Radius Arm
Assembly ... x 2
Main Blade Grip Assembly ....x2
Note
: Larger ID Inside
Socket Head Cap Screw M6x10mm
(HC124-S)
Oring
(HA024)
Washer
6x
14 x1mm
(HC194-S)
Washer
10x
16x1mm
(HC230-S)
Thrust Bearing
10x
18x5.5mm
(HC438-S)
Socket Head Cap
Screw M3x16mm
(HC068-S)
Washer
3x4x0.5mm
(HC176-S)
Swashplate Assemly
Center Hub Assembly
Radius Arm
(H0132-S)
Flanged Bearing
3x
7x3mm
(HC402-S)
Flanged Bearing
2.5x
6x2.5mm
(HC400-S)
Spacer Arm
2.5x
4x6.3mm
[H0253]
Spacer Arm
3x
5x2.7mm
[H0134]
Main Blade Grip
Assembly
Bearing
10x
19x5mm
(HC422-S)
Radius Arm
Assembly ... x 2
Swashplate
Assemly
(H0422-S)
Radius Arm
Assembly
Pin 5 mm
(H0413-S)
Damper
(H0426-B)
Uniball
M3H3
(H0065-S)
Socket Head Cap
Screw M4x10mm
(HC102-S)
Uniball Radius Arm
Assembly
Linkage Rod A
[HC230-S]
[HC232-S]
Uniball Radius Arm
(H0205-S)
Socket Head Cap
Screw M2.5x6mm
(HC018-S)
Socket Head Cap
Screw M2.5x18mm
(HC032-S)
The HPS2 head should be assembled with one, 1mm shim
(HC230) and one, 0.2mm shim (HC232) on each side.
The blade grips must move freely, but they should not move just
under their own weight.If the blade grips are too tight, you can
remove the 0.2mm shim (HC232) from each side.
After approximately 10/20 flights, please check preload, you can
add one or two 0.2mm shim (HC232) if preload has changed.
Washer
10x
16x1mm
(HC230-S)
Head HPS2 Assemly
Center Hub
(H0411-S)
Uniball M3H18
(H0063-S)
Bearing
10x
19x5mm
(HC422-S)
Main Blade Grip
(H0182-S)
Blade Grip Arm
(H0183-S)
Uniball M3
(H0437-S)
Socket Head Cap
Screw M3x10mm
(HC056-S)
Linkage Rod A Assembly .....x2
(Initial length for the rods from the
swashplate to the Blade Grip.)
Plastic Ball Link
(H0402-S)
Plastic Ball Link
(H0402-S)
Linkage Rod
M3x50mm
(H0417-S)
Right Side
Left Side
eg: Microlube GL261
Bag 7A
Page 13
Chapter 6, Head HPS2

Center Hub
(H0410-S)
Linkage Rod
M3x50mm
(H0417-S)
Plastic Ball Link
(H0402-S)
Main Blade Grip
(H0182-S)
Bearing
10x
19x5mm
(HC422-S)
Blade Grip Arm
(H0183-S)
Plastic Ball Link
(H0402-S)
Right Side
Left Side
eg: Microlube GL261
A
Spindle
(H0412-S)
Main Blade Grip Assembly ....x2
Note
: Large ID Inside
Socket Head Cap
Screw M6x10mm
(HC124-S)
Oring
(HA024)
Washer
6x
14 x1mm
(HC194-S)
Washer
10x
16x1mm
(HC230-S)
Thrust Bearing
10x
18x5.5mm
(HC438-S)
Center Hub Assembly
Radius Arm
(H0421-S)
Flanged Bearing
3x
7x3mm
(HC402-S)
Flanged Bearing
2.5x
6x2.5mm
(HC400-S)
Spacer Arm
(H0134-S)
Main Blade Grip
Assembly
Bearing
10x
19x5mm
(HC422-S)
Approx. 76mm
Radius Arm
Assembly ... x 2
Uniball M3
(H0063-S)
Swashplate
Assemly
(H0420-S)
Uniball M3
(H0065-S)
Linkage Rod A Assembly . . . .x3
Linkage Rod A
Assembly
Linkage Rod B
Assembly
DETAIL A
(to adjust the tracking,
turn this linkage.)
Socket Head Cap
Screw M3x16mm
(HC068-S)
Pin 5 mm
(H0413-S)
Socket Head Cap
Screw M2.5x6mm
(HC018-S)
Damper Derlin
(H0426-B)
Uniball M3
(H0065-S)
Socket Head Cap
Screw M4x10mm
(HC102-S)
[HC230-S] [HC232-S]
Socket Head Cap
Screw M2.5x10mm
(HC022-S)
Spacer Arm
(H0416-S)
Flanged Bearing
2.5x
6x2.5mm
(HC400-S)
Radius Arm
Assembly
Swashplate Assemly
Uniball Radius Arm
(H0415-S)
Socket Head Cap
Screw M2.5x10mm
(HC022-S)
Socket Head Cap
Screw M3x16mm
(HC068-S)
Radius Arm
Assembly
Socket Head Cap
Screw M3x10mm
(HC056-S)
Washer
3x
4x0.5mm
(HC176-S)
M4x24mm
[HC111-S]
M3x12mm
[HC062-S]
Nut M4
[HC212-S]
[HC176-S]
Note:
The HPS3 head should be assembled with one, 1mm shim
(HC230) and one, 0.2mm shim (HC232) on each side.
The blade grips must move freely, but they should not
move just under their own weight.
If the blade grips are too tight, you can remove the
0.2mm shim (HC232) from each side.
After approximately 10/20 flights, please check preload,
you can add one or two 0.2mm shim (HC232) if preload
has changed.
Bag 7B
(Initial length for the rods from the
swashplate to the Blade Grip.)
* Clock-wise, counter clock-wise thread
* By turning the linkages you can adjust
tracking. If tracking is adjusted correctly,
you’ll see the metal part line up around
in the center of the opening.
Page 14
Chapter 6, Head HPS3

Finishing
Washer M3
(H0007-S)
Socket Head Cap
Screw M3x8mm
(HC050-S)
Canopy
Position
(H0008-S)
Head HPS2
Assembly
Socket Head Cap
Screw M3x8mm
(HC050-S)
[HC212-S]
[HC111-S]
Finishing
Washer M3
(H0007-S)
Swashplate HPS3
Assembly
[H0420-S]
[HC062-S]
Head Cap Screw
M3x12mm
(HC062-S)
Head HPS3
Assembly
[HC062-S]
[HC212-S]
[HC111-S]
Swashplate HPS2
Assembly
[H0422-S]
[HC062-S]
Canopy
Position
(H0008-S)
Head Cap Screw
M3x12mm
(HC062-S)
Washer
3,1x
1,2x1.8
(H0078-S)
Washer
3,1x
1,2x1.8
(H0078-S)
Bag 8
Page 15
Chapter 7, Assembling The Modules

ASSEMBLY OF THE BALL ON THE HORN
The rods going from the servos to the swash plate must be as vertical
as possible. Not all servos are equal, so to better align them you can
choose to use the supplied spacer H0031. Figure 4 illustrates this.
INSTALLATION OF SWASHPLATE SERVOS
The linkage ball must be positioned between
17-19 mm
out on the servo arm (
figure 1
), recommended servo arm SAB
p/n [HA050/HA051]. The 120° placement of the servos inside Goblin means the arms are difficult to access. For this reason it is
advisable to ensure alignment of the servo arms (and sub trim set) before installation of the servos in the model (
figure 2
).
Proceed with installation following the instructions below.
Figure 3
shows a completed installation.
Uniball M2
5H6
(H0064-S)
Socket Head Cap Screw M2x8mm
(HC008-S)
or
Socket Head Cap Screw M2x6mm
(HC004-S) without Uniball Spacer
..... x3
Socket Head Cap Screw
M2.5x8mm
Servo 2
SERVO ASSEMBLY 1, 2, 3
Servo 1
Uniball Spacer
(H0064-S)
Socket Head Cap
Screw M2.5x12mm
(HC026-S)
..... x9
Socket Head Cap Screw
M2.5x12mm
Socket Head Cap Screw M3x6mm
(HC044-S)
Socket Head Cap
Screw M2.5x8mm
(HC020-S)
Servo 1
Servo 3
Servo Spacer
(H0075-S)
Servo 2
Servo 3
17-19mm
Bag 9
Page 16
Chapter 8, Installation Of Swashplate Servos

Plastic ball link
(H0066-S)
Plastic ball link
(H0402-S)
Plastic ball link
(H0402-S)
Initial length for the rods from the servos to the swash plate.
Approx 65 mm
Plastic ball link
(H0066-S)
Initial length for the rods from the swashplate to the blade
grips.
Set Screw M2.5x40mm
(HC242-S)
Linkade Rod B
Aseembly
Head HPS Version Preliminary Setup
Adjust the linkage as shown. The linkage Rod A has thead right/left.
Turning, you can change the tracking without disconnecting the
plastic ball link.
The wire for the front servo must be positioned here. Use zip ties.
Linkade Rod A
Aseembly
Approx
56mm
Linkage Rod B Assembly ... x3
Linkage Rod A Assembly ... x2
Approx
66mm
(to adjust the tracking,
turn this linkage.)
Linkage Rod
M3x50mm
(H0417-S)
Approx 76mm
Page 17
Chapter 8, Installation Of Swashplate Servos

Note: Although the Goblin can fly at high rpm, for safety reasons we suggest to not exceed 2100 rpm.
Some example configurations:
TRANSMISSION SETUP
It is important to choose the right reduction ratio to maximize efficiency based on your required flight performance.
The Goblin has many possible reduction ratios at your disposal. It is possible to optimize any motor and battery combination.
It is recommended to use wiring and connectors appropriate for the currents generated in a helicopter of this class.
If you are using a head speed calculator which requires a main gear and pinion tooth count, use
214
teeth for the main gear
(this takes into account the two stage reduction) and the tooth count of your pulley as the pinion count.
Below is a list of available reduction ratios:
H0175-18-S - 18T Pinion = ratio 11.9:1 H0175-22-S - 22T Pinion = ratio 9.8:1
H0175-19-S - 19T Pinion = ratio 11.3:1 H0175-23-S - 23T Pinion = ratio 9.3:1
H0175-20-S - 20T Pinion = ratio 10.7:1 H0175-24-S - 24T Pinion = ratio 8.9:1
H0175-21-S - 21T Pinion = ratio 10.2:1 H0175-25-S - 25T Pinion = ratio 8.6:1
GOBLIN URUKAY - HPS2 HEAD
GOBLIN URUKAY - HPS3 HEAD
GOBLIN URUKAY CONFIGURATION
Rev:01
Performace
Battery
Motor
ESC
Pinion
RPM
Max (Gov)
Pitch
GENERAL
12S
5000/5500
Kontrionik Pyro
800-480
Edge 160 HV
22T
1950
± 12,5
Jive 120 HV
YGE 160 HV
KOSMIK 160/200
21T
1950
± 12,5
Quantum 4530-500
Scorpion HK 4530-500
Edge 160 HV
21T
1950
± 12,5
Jive 120 HV
YGE 160 HV
KOSMIK 160/200
20T
1950
± 12,5
Scorpion HK 4525-520
Edge 160 HV
20T
1950
± 12,5
Jive 120 HV
YGE 160 HV
KOSMIK 160/200
19T
1950
± 12,5
14S
5000 mAh
Kontrionik Pyro 850-40L
YGE 160 HV
KOSMIK 160/200
22T/23T
2000/2100
± 12,5
Quantum 4530-450
Scorpion HK 4530-450
YGE 160 HV
KOSMIK 160/200
20T/21T
2000/2100
± 12,5
Kontrionik Pyro 800-48
YGE 160 HV
KOSMIK 160/200
19T/20T
2000/2100
± 12,5
Battery
Motor
ESC
Pinion
RPM Max
Pitch
REV 01
12S
5000/5500 mAh
Kontrionik Pyro 800-480
Edge 160 HV
22T
2000 rpm
± 12,5
YGE 160 HV
KOSMIK 160/200
21T
± 12,5
Xnova 4530-500KV
Quantum 4530 - 500
Edge 160 HV
21T
± 12,5
YGE 160 HV
KOSMIK 160/200
20T
± 12,5
Scorpion HK-4526-520KV
F3C Edition
KDE Direct 700XF - 535 - G3
Edge 160 HV
20T
± 12,5
YGE 160 HV
KOSMIK 160/200
19T
± 12,5
12S
5000/5500 mAh
Kontrionik Pyro 800-480
Edge 160 HV
21T
1900 rpm
± 12,5
YGE 160 HV
KOSMIK 160/200
20T
± 12,5
Xnova 4530-500KV
Quantum 4530 - 500
Edge 160 HV
20T
± 12,5
YGE 160 HV
KOSMIK 160/200
19T
± 12,5
Scorpion HK-4526-520KV
F3C Edition
KDE Direct 700XF - 535 - G3
Edge 160 HV
19T
± 12,5
YGE 160 HV
KOSMIK 160/200
18T
± 12,5
Page 18
Chapter 9, Installation Of The Motor
Table of contents
Other Goblin Toy manuals
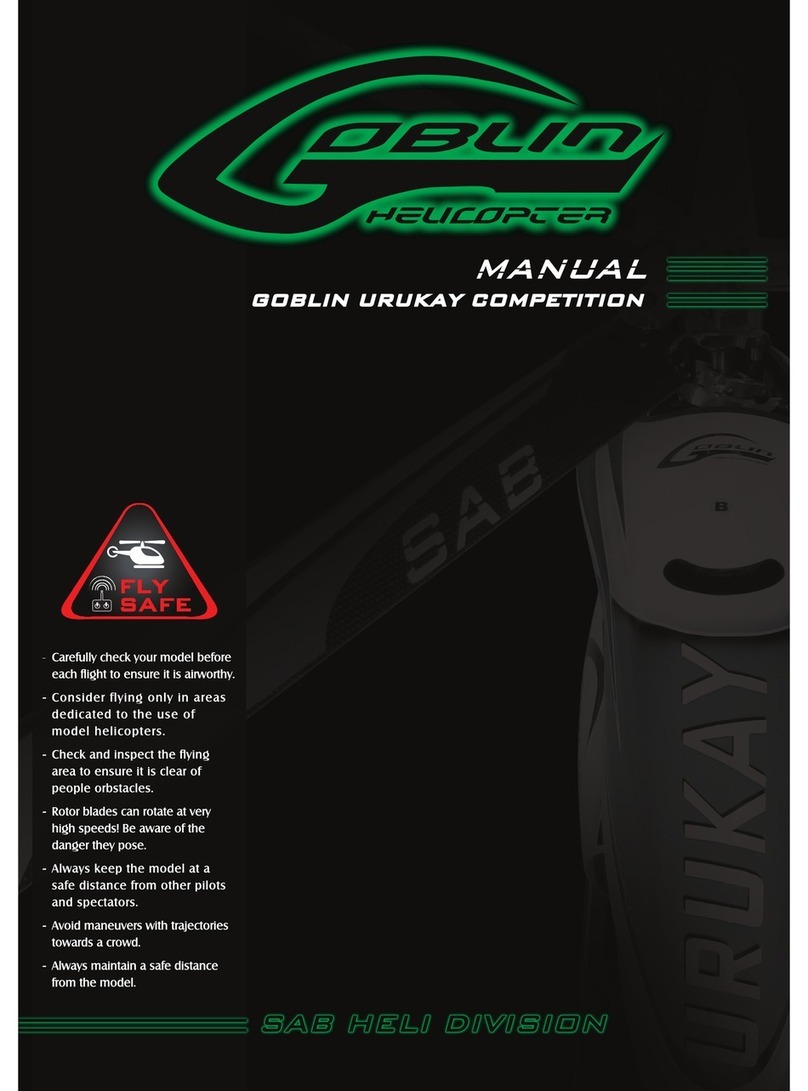
Goblin
Goblin Urukay Competition User manual
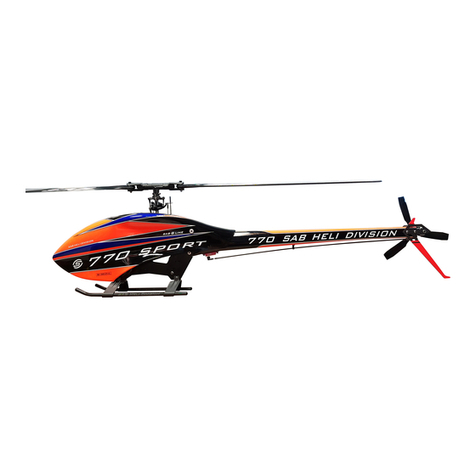
Goblin
Goblin Goblin 770 Sport User manual
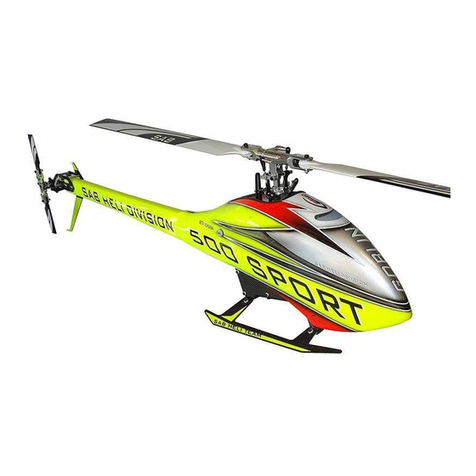
Goblin
Goblin 500S User manual
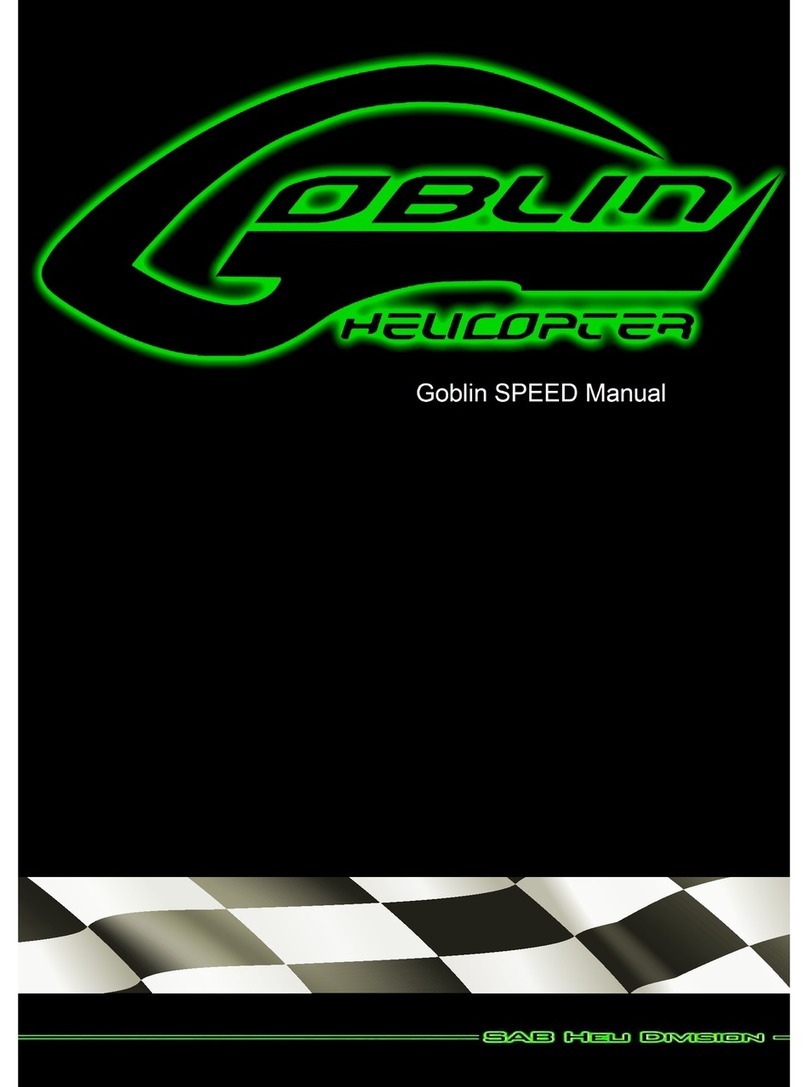
Goblin
Goblin SPEED User manual
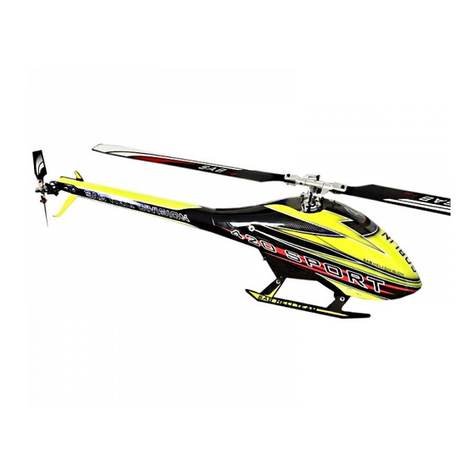
Goblin
Goblin 420 User manual

Goblin
Goblin 380 KYLE STACY EDITION User manual
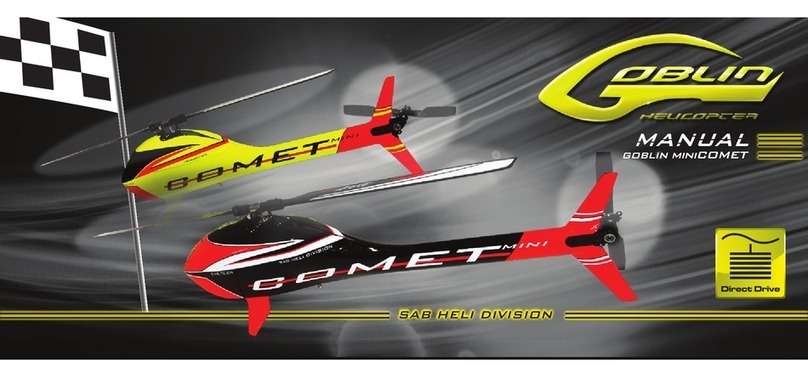
Goblin
Goblin MINI COMET User manual
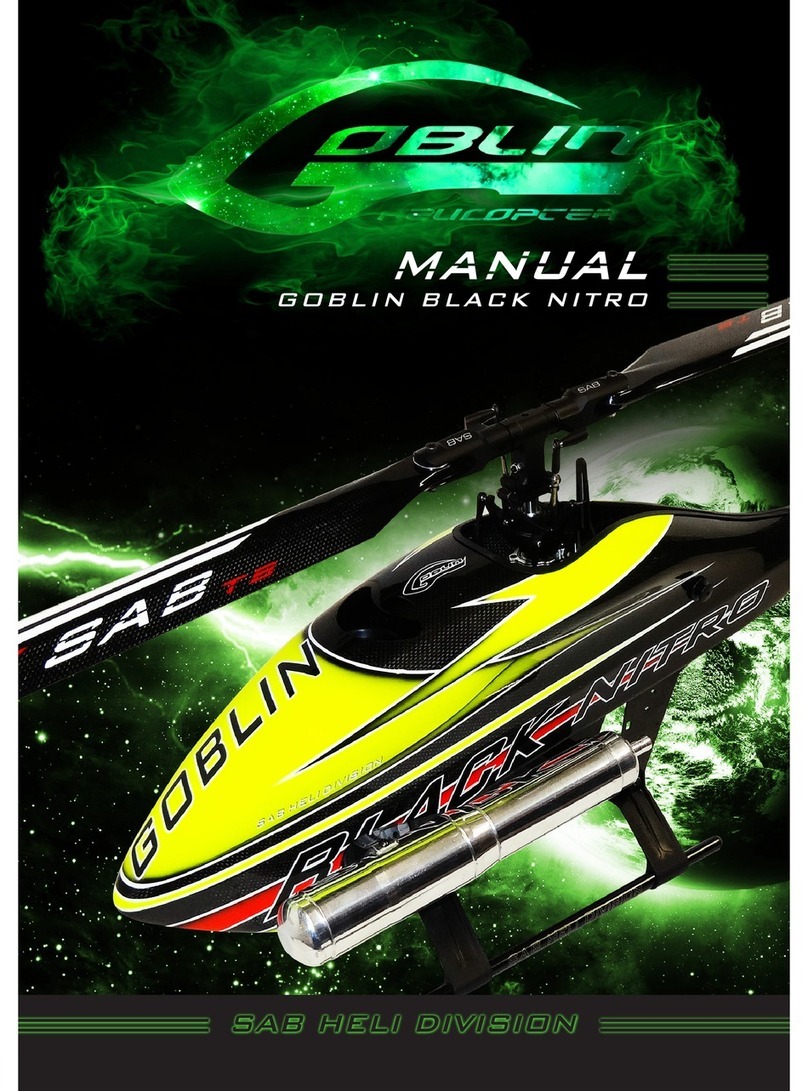
Goblin
Goblin SG651 User manual
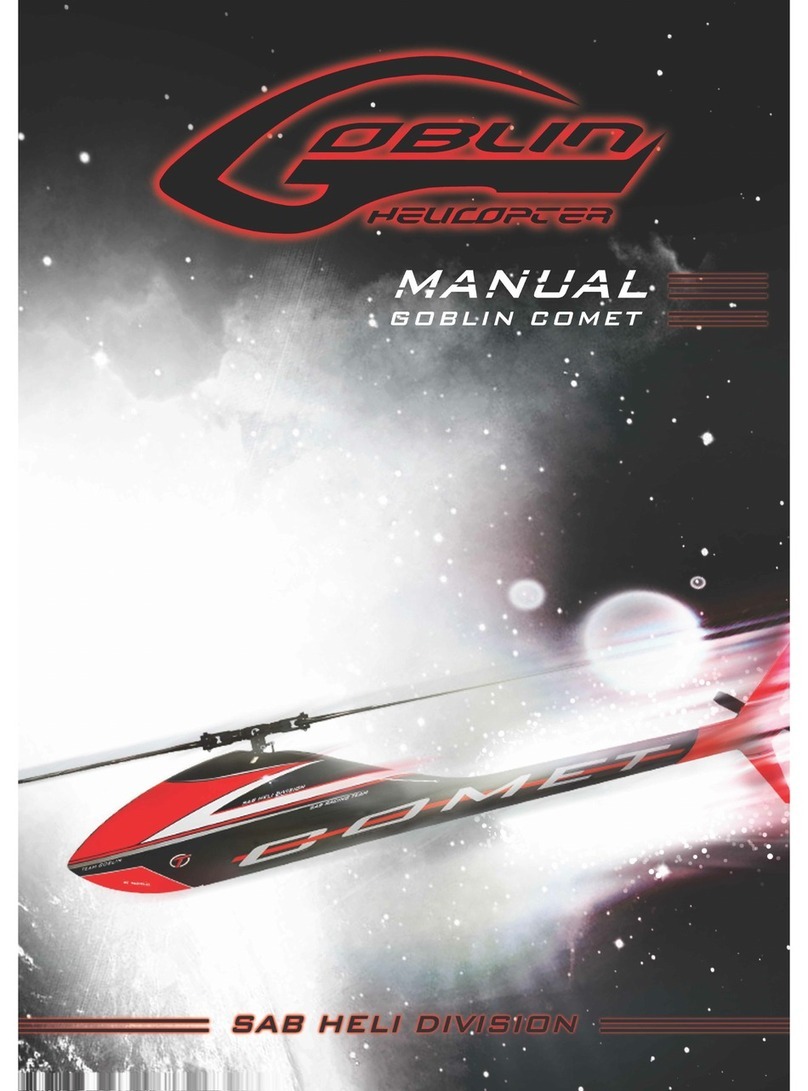
Goblin
Goblin Goblin Comet User manual
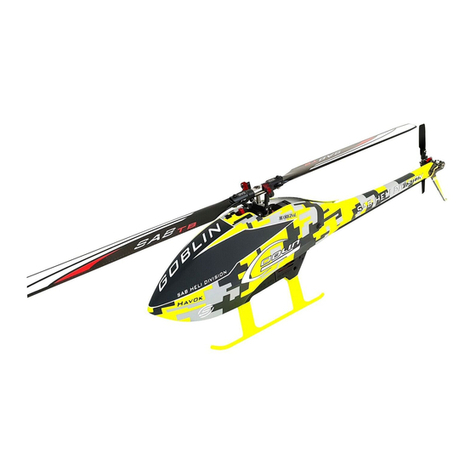
Goblin
Goblin FIREBALL User manual
Popular Toy manuals by other brands
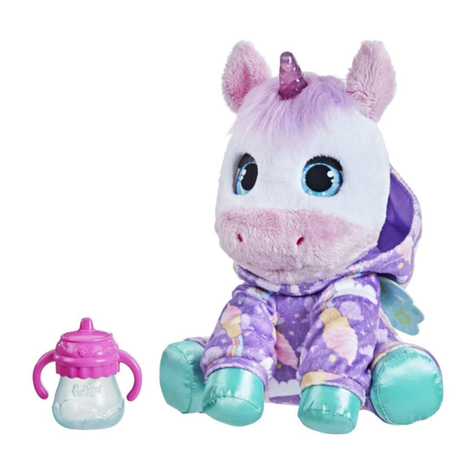
Hasbro
Hasbro furReal F2066 quick start guide
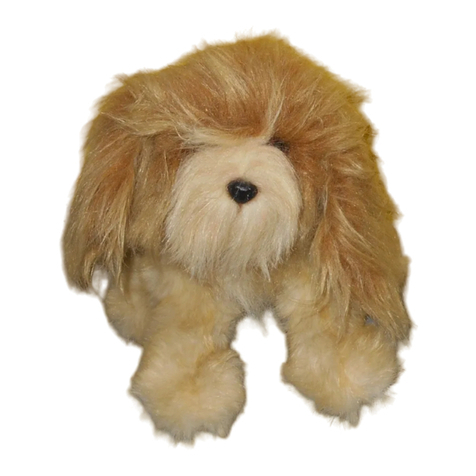
Hasbro
Hasbro Tiger Electronics FurReal Friends My Lost Little... manual
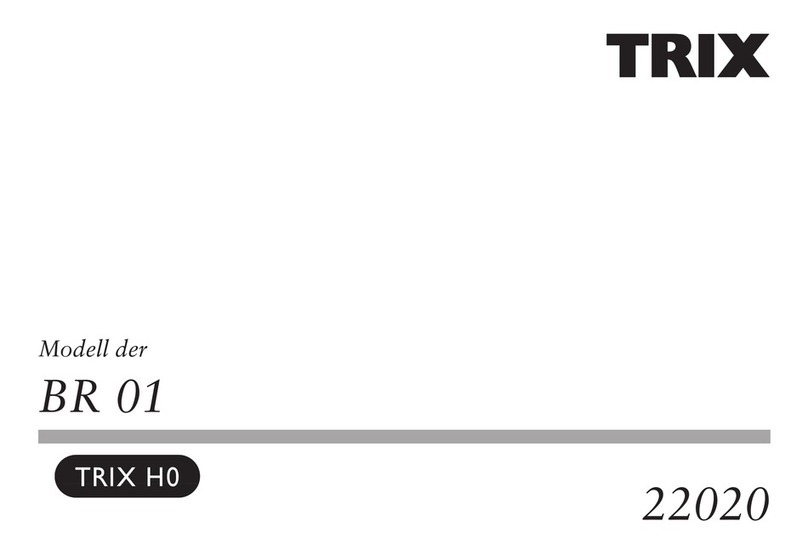
Trix
Trix H0 BR 01 manual
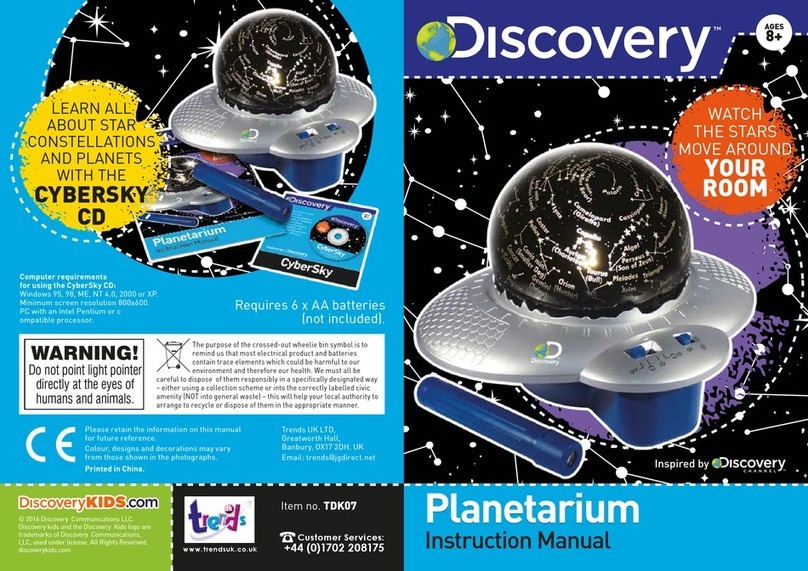
Discovery Telecom
Discovery Telecom Planetarium instruction manual
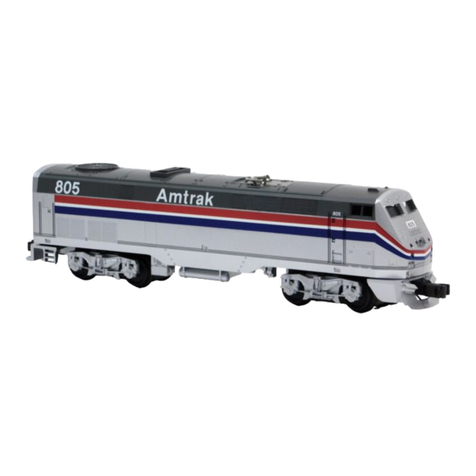
Rail King
Rail King Genesis Diesel Engine operating instructions

RC Factory
RC Factory RS 352 Building instructions