GRIGGIO GC 95/1 User manual

GC ?5/1 l GC 95/2RR r GC 95/2RRT
GC 110/1 - GC 1'10/2RR r GC 110/2RRT
WIDE BELT SANDING MACHINE
TNSTRUCTIONS SPARE PARTS
((
GRIGGIO
WOODW.ORKING MACHINERY
7\
\,.,r Vio Co' Brion, 40 - 3501 1 Reschigliono (PD) ITALY
'lel.049/9200920 FoxO49l920l433
f,ìtp:l¡*w..griggio.com E-moil:info@griggio'cc

c!

Table of Contents:
1. General lnformation...'......-..
1.1. WarrantY
1.2- Application of Operating Manual """
1.3. General safety information..'.'.."""
1.4. Machine application ..........'
'1.5. ldentification of the machine..'.""""
'1.6. Applicable documentation..-....
1.7. Specifications.........
1.8. Possible machine configurations.""""
1.9. Standard machine accessories """"""'
1.10. Customequipment.'......'....'
5
5
5
6
7
7
7
I
I
I
I
0
0
2. Technical description of the machine"
2.1. Emergency equþrnent description """"""'
2.2. Description of the safety equipment"""""'
3. Safety information....'.........
3.1. Safety rules for moving the machine
3.2. Safety rules for set-up and operation
....... 1
1
of the machine.....
3.3. Safety,rulesformaintenance..""
4. lnstallation .............
4.1 Transportation .........
Unpacking and cleaning the
4.2
4.3. Placement of the machine...
4.7.
4.8.
machine.
4.4. lnstalling the machine.
4.5. Power connection..-.....
4.6. Connecting compressed air '
Connecting suction....
Working conditions...'
4.9. Operators
5. Machine adjustments.........."'
5.1. Replacing the sanding belt"""'
5.2. Replacing the pad ...."......"1'
5.3. Adjustingthe height of working rollers"""
5.4. Controlling and aã¡usting oscillation of the sanding belt....
5.5. Adjusting the sanding belt tension""
5.6. Centering the loading conveyor"""""""'
6. Operation of the machine
6.1. Contro-l Panel'......
6.2. Calibration of tab'le lifting read-out"""
6.2.1
6-2.2
6.3.
6.4.
6.5.
6.6.
6.7.
6.8. Automatic control of the Pad""'
Maintenance and rePairs
Cleaning the machine '.."'
Maintenance schedule ...'......."
1. Conveyor
Zero setting......'- "..'.
Changing the system unit of measurement '
Automatic positioning of the table
Manualwheel
Starting the machine .'..
Stopping the machine .......'...
Catinraäng and sanding of solid wood on the RT machine .
Calibrating, presanding, and sanding on the RRT machine
6.9
7.
8.
8.1
8.1 3

8.1.2.
8.1.3.
8.1.4.
8.1.5.
8.1.5.1.
8.1.5.2.
8.1.6.
8.1.7_
Tightening the chain of table 1if.t.........
Gearbox of loading and table |ift........
Greasing bolts on the table lift...........
Belts
lnspection and adjustment of belts.
Replacing the belts ....
Storing sanding belts ........
lnspection of emergency
Moving the machjne.......... and safety devices
period.
8.2.
8.3.
8.4.
8.5.
9.
9:1.
9.2.
1A.
Laying up the machine for an extended
Liquidating the machine .............
Dangerous situations
Remedies of defects
Possible defects
Quality of work deterioration
Spare parts.
..23
..23
..24
..24
..25
,.25
,,25
.25
.26
.26
.27
.28
4

f . General lnformation
I .1 . Warrantv
a) The product has been tested priorto shipment. The manufacturer warants that the
product shall maintain declared properties while the warranty remains in force.
b) Warranty applies to all defects preventing the use of the product due to faulty
material or workmanship
c) Warranty doesn't apply to defects caused by improper haridling, disregard of
operation instructions, unauthorized intrusion, or force major, such as damage
during transport or forces of nature.
d) Should the machine be installed improperly, we shall not be responsible for any
consequential darnages or injuries.
e) File all warranty claims dJrect$ with the manufacturer. Repairs outside warranty
may be performed by any professional repair shop.
f) Warranty shall be extended by the time for which the product remained under
warranty repair.
g) A duly completed Warranty Card must accompany a submitted warranty claim.
Model
Serial Number Manufacturcls seal and signature
Date of sale:
1.2. Application of Operatinq Manual
Tlris manual has been compiled by the manufacturer of the equipment and is part of the
delivered goods. lt contains basic infiormation for qualified operators. lt describes the
environment and manner in which the machine should be used, including all
information for correct and safe service. Furthermore, it includes the text of regulations
for a safe and economical operation during the planned service life of the machine.
The manual is organized in Chapters pertaining to details of particular subþct matters,
for easy orientation.
Please read it carefully before you start using the machine, and file it for firture
reference.
Some information and drawings may not be applicable specifically to the pur,chased
model, since the Manual includes information for all manufactured models.
The manufacturer reviews the Manual continuously and updates it with modifications
incorporated in new models.
Operations and applications not listed here require the manufacturer's prior approval in
writing.
Notice that recommends to proceed exclusively according
to the following regulation. Should the regulation be not
adhered to, serious injury or death to the operator may be
the consequence.
5

dWarning that improper procedures or application of the
machine may cause injury, machine breakdown,
environmental, or economical damages.
Warning demanding due considerations during work.
Non-adherence may cause minor injuries and/or damage
to the machine. -
1.3. Gnnara I safet i.n rmati(ln
vfo
The machine has been designed to guaran-tee outmost safety and optimal performance.
Safety, horuever, depends to a great degree on you.
Non-adherence to the following safety regulations represents danger of injury to
yourself as well as other oeople.
The use of any kind of machine represents certain risks that have to be kept in
mind at all times.
Be extra careful wtren getting ready for any work
Prior to starting the machine read carefulty the Operating Manual.
Prior to any work, install and check all safety elements in their functíonal
readiness.
Prior to maintenance and clean up, make sure the machine is at a complete stop
befrore you deactivate safety elements.
For switching the machine off for set-up or dismantling of any part, switch the
main switch to 0 position, shut off cornpressed air, and lock.,
General cleanliness of the machine and the floor around is an important safety
precept.
From experience we found that personal items like rings, watches, bracelets,
etc., ate often causes of injuries. Therefiore, remove them before you start
working" button up your sleeves, remove your necktie so that it doesn't enter the
gears, tie up your free flowing hair, and wear work shoes prescribed by
international safety rules.
Always use goggles or eye protectors.
Never work with too small or too large pieces.
Never start the machine, unless all safiety elements have been properly activated.
6

BS is a semi-automatic machine used for finishing work, calibration, surface treatment
of lacquer, and sanding of pieces made of solid wood, wood-particle boards, planks,
and similar materials. lt may also be used for whetting lacquered boards between
operations.
1.4, Me appl[c R
1.5. ldentific ion of the
1.6. Applicable documentation
Parts of the Operating Manual are
- electrical schematic
- pneurnatic circuit schematic
e
The macfiine may be identified by the manuúacturing label
attached to the stand.in the rear of the machine.
)
@
ìf*
m sfmr
ProÍM
wr}@t ilP
¡4
túff
æ
ffi
ffi
IL
((
7

1.7. Specifications
Max. working width
Min. working width
Max. working width
Diameter of working rollers
Length of the sanding belt
Speed of the sanding belt
Speed of the forwarding belt
Nominalvoltage
Main electric motor power
Forwarding electric motor power
Table lifting electric motor power
Pneumatic circuit pressur€
Air intake
Min. suction air speed
Min. suction capacity
Diameter of suction hose
Machine dimensions L x W x H
Weight (as to selected configuration
and appoíntment)
Level of noise
Level of acoustic pressure
Dust emanation
Certificate
mm
mm
mm
m.m
mm
m.s-r
m.min-1
Vl\z
KW
KW
KW
bar (MPa)
dm3.min-r
m.sec-1
m3.hod-r
mm
rnm
kg
dB (A)
dB (A)-?
mg.m'
950 1100
33
160 160
180 180
1900 1900
18 18
4,519 4,519
400/50 400t50
7.5 7.5
0.3/0.55 a,55t1
0,25 0,25
6(0,6) 6 (0,6)
20-30 20-30
28 zB
3100 3500
120 120
f 395x1 320x1950 1395x1 470x1 9S0
730-890
95
81
0,57
930-
96
82
0,64
1120
The listed values are emission values and are not necessarily safe working values.
Although there is correlation between emission and ""porré values, such values
cannot be used for reliabb determination of possible required further steps. Factors that
affect real exposure vatues to the workers include conditions of the rorLrrláp, ;pr*
sources of noise, such as the nurnber of machines, etc.
I

GC 12 RR GC /1 RT GC /2 RRT
1.9. Standard machine accessories
- Rubberized working roller
- 80 Sh - ca[ibrating roller
- 50 Sh - sanding roHer
- Motorized table lift
- Rubberized Pressing rollers
- SafetY gate at the machine inPut
- Two feeding sPeeds
.Pneumaticcontrolledoscillationofthesandingbelt
- Brake of working units
- Start star-delta õonnection (manua¡y controlled)
- Mechanical gauging of table elevation
- Ampermeter
_ såiåðtabte s,bft or semi-hard pad - for RT and RRT configuration
- Working units set r-rp by sanding belts
- Holderlor the hose to êuction opening connection
- ópét"ting, Maintenance, and Set-up Manual.. . ^-
- Construction ;;l-"Opoin'tment in line with valid CE standards'
Possible machine confiqurations
uipme
1.8
1.10. Gustom eq
lncreased motor power 11 kW, 15kW, 18'5 kW
Extended table *iti'rói1"rc on 'oearings at the input and output to the machine
f iectr¡cal sta rt.étar-delta, autom ati cal ly co ntro lled
Electronic table positioning display
Àutomatic table positioning to tfte thickness of material
Pad controlled PneumaticallY
Padcontrolledpneumaticallywithautomaticcontrol
Soft pneumatic pad with adjustable firmness
etowing of sanding belts for longer life
Automãtic centeriñg of the feeding belt
I

2.Tech nic
2.1. Emer
al desc ript on of the machi ne
encv eouiþme td tion
escrip
Emergency equipment for stopping the machine in case of danger.
Push button for emergency stopping of the machine. All systems of the machine
stop' Two such buttonsãre instatted oñ tne machine - one ;"iË front control paner,
and one on the cover at the rear of the machin". in" shaped button is red.
2.2.
The safety equipment protects the operator and the machine against dangerous
situations
a) Folding gate at the mate¡:ial entry to the machine.
b) Lockable main switch. Prevents unauthorized starting. Lock the main switch w*h
the padlock dur.ing repair.s!
c) Blocking of doois ón the electrical box. The door may be opened only with the
main sr,vitch in the,,ofif" position. rrrqv ve vp
d) Door switches' Accídeñtal opening of side doors stops the running machine.
e) Automatic brake. stops the'macñin "y.t rs w¡th¡ir a fime lim¡t. lt is activated by
the emergency stop búüon, efectricat power inier,ruption, drop ¡n ä¡i'pi"JJr;ff"Ë;
limit, and some other safety devices.
fl -sanding belt tension "*¡'t"tl prevents the machine from being started with the belt
loose, and stops the machine, åhourd ttre oeit Ëreat.
g) sanding belt position switch stops the machine when the vibrating belt exceeds
set limits.
h) umit switch .of table position limits extreme top and bottom positions of the table
during its positioning by the motor. It blocks rurtner moyement towards the end limit
Position, ¡rwvtrrvrrr rL'Yr
¡) switch blocked by lock allows for..tenporary release of door contacts dur:ing
specific set-up or maintenance operations.'lnsert key in the switch lock and twn it
cw' The switches are out of service in this póéition io r."ðtiuåì" turn the key ccw,
remove and store safely. The deactivation oi swiicher r"y Àê ¿ãne only by a trained
worker, well versed in the operation and funciion of trí" rããn¡ne. ¡te may also
activate the switch in its original positio" pri"i iå start. The switch is located inside
the electrical box.
3. Sa-f-etv information
Read the operating Manuat carefutly before starting the machine, its set-up or repair.
3.1. Safetv rules for movinq the mach_ine
Lifting and moving the machine may g9 d.ole ysing only such proper and technically
suitable equipment that has been specified ror tÀis'[rrpo.", and by trained and skilled
workers.
ftlg ger¡on -may be present underneath a lifted machine or in íts vicinity, and near the
hoist, the lift t'uck, or any other rifting or moving equipment.
10

3.2. Safetv rules for t-up and operation of the ma!hi¡e
It is strictly forbidden to perform other work on the machine than specified and listed in
Section 1.3.
The operator must be adept physically and mentally. Only a person trained in the field of
wood machining or a person instructed by him may operate the machine Strch workers
must be older than 18 years.
The operator must comply with all safety regulations and rules established for the given
territory of work.
Operate the machine only in accordance with recommendations of the Operating
Manual.
Prior to startingthe machine check the vicinity of the machine.
Never place your hands or other objects near the moving parts.
Obserue proper illumination of the work area.
When working, prevent unauthorized personnel frorn entering near the machine.
Unless all protective and safety devices are functional, do not use the machine.
Prior to starting the machine make sure that no objects have been lefr in machine.
Prior to starting the machine, make sure that machined pieces have been removed from
the working sections. lnsert them frst after the machine has reached its full operating
speed.
It is not allowed to interfere with the electrical circuitry by untrained people.
Do not touch runníng sanding belt and pressing rollers. Be extremely careful when
working on heavy pieces.
d
Å*,
mln990 m
60% å ks(mln)
3.3. Safetv rules for maintena.nce
Do not tet unqualified personnel perform maintenance or repairs. Read the
Manual before you start working. Never lubricate or clean a running
machine.-Prior to workn make sure that the main swiúch is locked.
4. lnstallation
4.1. Transportation
Unload the machine from the platform with a crane or a
high-lift truck to avoid danger of injury or damage to the
machine. Only trained and skilled persons may lift and
handle the machine. Only equipment designed for lifting,
of required strength, and properly maintained may be
used. The needed length and strength of the cables is
illustrated.
11

4.2. Unpackinq and cleanin the rnac I ne.
Unpack the machine.
check for possible damage sustained during hansportation.
Remove wooden pads.
Wash off conservation .film using technical gasoline or other organic solvents. Use
protective means and obey rules for handling such chemicals. Deétroy soiled rags as
prescribed
4.3. Placement of the machine
L max
*flr5 mrì
L max
1,5 mm
w
î
ln placing the machine, observe that minimal distances as
illustrated are maintained.
Make all connections of power, compr€ssed air, and suction
available at the site, to be connected to fixtures on the upper
side of the machine.
The site should be illuminated by at reast sOo LUX intensity.
The best floor material is concrete; asphalt is not well suiied.
should the machine be focated on an elevatcd floor, make
sure of loading characteristics of the floor.
4.4. lnstallinq the machine :
The machine must be perfectly level; required accuracy of operations is not guaranteed
otherwise.
- Open the side door and attach supplied bolts to bushings in the bottom cross-
piece.
- Place supporting pads underneath the bolts
- Place a water level on the table of the machine, and level the machine in both
directions, using maximum care.
4.5. Power connection
Power may be connected by a skitled person
Prior to connecting the machine, make sure that voltage and frequency of
the power supply corresponds to data shown on the label, and that fusing
and conductors diameter satisff power inputto the motors
Guide the cable through the opening in the upper part of the machine, and connect
wires to terminals L1, L2 and L3, the blue conductor to N, and the yellow-green
conductor to PE. Close the door of the electric box, switch power on, switch the main
switch, push the button "Start',, and start the loading conveyor. Should the conveyor
travel in the opposite direction, switch main switch off, disconneet
conductors on terminals L1 aL2.
Attention, do not replace the blue or the yellow-gr.een conductors!
12
power, and change

4.6. Connectinq essed air
n-õ Check that ther:e is no condensed water or dirt in the pipes. The reliabitity
It;ff and life of pneumatic elements would be jeopardized.
Connect the 3/8" hose to the input valve in the upper section of the machine, and
secure it with a clamp.
Admit compressed air and open input valve by turning the lever vertically. Pull the
control of the reduction valve on frontal panel and by turning it adjust pressure on the
manometer to 6 bar. Push the valve pin closed.
4.7. Connectinq sn
It is absolutely necessary to connect the suction system. lt is
forbidden use rnachine without suction. Suction system .must fill
94l9lEC directive and have minimal capacifywritten in chapter 1.7.
We recommend to connect it so that the machine cannot be started if the
system is not activated.
The openings of working elements have a diameter of 120 mm.
Hoses leading from the openinç tothe suction system must be clamped
4.8. Workinc condítions
The machine is intended to be operated in covered areas under following conditions
- air temperature between +5'C and +40'C
- relative humidity between 30% and 90Vo, with no condensation
- elevation above sea level to 1000 m
- dusty environment in woodworking shops
The machine and its operation have no adverse effect on the environment.
Transportation and storage at -25 to +50"C (for a short time of less than 24 hours,
temperature may be up to 70"C).
4.9. Operators
Operators must be older than 18 years, and rnay be of both
sexes.
/'('\
\.o-l
1J
13

5. Machine adiustments
5.1. Replacinq the sandino belt
Æ> ilff :,ir"fäg#',i J:,ï:""oins bert' use protective s toves'
4
3
By pushing button 3 release the belt.
By turning crank handte ccw release the foot of the working
unit, move it towards you, and remove.
Rernove the belt.
Replace with new sanding belt, The arrows on the inside of
the belt must turn in the same direction as the rollers.
\tvatch that the belt is close to the center of the rofler. The
edge of the belt must not touch any of the end switches.
trnsert support foot and tþhten crank handle to firm up the
body of the working unit.
By pulling button 3 tighten the belt. Close the door.
Every time you replace the belt clean the area of the
working unit and the internal side of the belts of colTected
dust. clean also the optical sensor that contrors oscilation
of the belts.
Store the betts as described in Ghapter g.1.6. to prevent
their deterioration and to extend their service life.
5
6
5.2. Replacine the pad
The machine may be provided with a stiff ora semi-stiff pad. Replace as follows
By pressíng button 3 release belt tension.
Loosen the rose, grasp the pad by the ball, and pull it out.
lnsert another pad
Tighten the rose.
By putling out button 3 tighten the belt.
14

5.3. Adiustinq the heiqht of workinq rollers
when a new sanding belt is installed, the position of sanding rollers
must be adjusted.
Measure the thickness of belts and adjust this value on scale s as
follows:
- To move the indicator ccw, loosen rose 4 and turn the lower rose.
- Value n,0" on the scale represents belt thickness of 0 mm, i.e., the
roller without the belt touches the loading conveyor. This value is
preset by the manufacturer.
ln time, the rubberized surface of the roller wears off and the ,,0,,
must be reset. check thís set-up regularly and if necessary, readjust
it by loosening bolt 6 and resetting the indicator.
5.4. Controlli¡
4
5
o
q and adiustinq íllation of the sandinq belt.
Oscillations of the belt are controlled by a
pneumatic system and its optical sensor.
Should the sensor fail, the system is
protected by end stop.switches on both
sides of the belt. The centering of the
oscillating belt is done by eccentric device
no. l, or if the lift of the eccentric device is
not sufficient, by moving the holder of the
pneumatic cylinder. The speed of the
piston movement may be adjusted by flow
regutators no. 3 at the input to the
pneumatic cylinders.
Attention - adjust the eccentric devices only with the machi,ne stopped.
The adjustment of oscillations requires some experience. Let a Service
shop do this adjustment.
u
Z
rs
15

5.5. Adiusfino tha sandindbeltt nston
The working unit is equipped with a pneumatic cylinder, which keeps the sanding belt
taut' The tightening force may be adjusted by the reduction valve on machine fiontal
panel' Pull the valve pin, adjust required pressure, and push it back locked. The
pressure is indicated on manometer. Adjust pressure lo 4 - 5 bars.
5.6. Centerinq the loadino convevor
Check occasionally, whether guiding pulteys in the lower part of the table are turning. lf
are, the conveyor must be centered by turning bolts on the face of the table from -the
side of material entry to the machine. Center the belt so that it doesn't touch the guiding
pulleys. Start loading at the lowest speed and watch whether the belt is not-sliãinf,
sideways.
F./- Do not over tighten the belt not to decrease its service life.
lJgHif ":ï,ii:ï$1"?;å5g; ;#i::i'"î,*E:î3ji^.j'Jåffi onu"vo'
lf the machine has automatic centering of the loading conveyor, it is not necessary to
a{ust it manually.
-6. Operation of the mach ine
6.1 . Control panel
lrlext chapter describes all control elements installed on the machine. Some are not
standard and are custom instalted. You rnay not find them all on your machine.
START
- Main switch. Switches on and off electrical power.
- Emergency push-button. with the button depressed the machine
stops. The button is locked in its depressed position automatically. To
restart the machine the button must be turned in the direction of the
arow
- Push-button ,nstart*. As long as all emergency and limiting switches
are deactivated and the pneumatic loop is under sufficient pressure, the
button lights up white when depressed. All other'control elements are
activated and the electric motor's brake is off.
- Ammeter indicates the current flowing through the motor.
- The Star-delta switch starts the main motor. Starting with this switch
lowers the peak current during starting
EMP
l
16

I
-Push-button,,start,ostartsthemainelectricmotor,ifthemachinehas
equipped "rtotnät' rá'iJårt" s*iiór'. lt replaces the above-mentioned
_ ËTlTllo"tton ,nstop,, stops ail working units when depressed.
-LoadingGonveyorspeedswitchallowsturningonandselectionof
E
loading sPeed
- Push'button ,,UP" when pressed' the table moves up'
- Push-button ,,Down", when pressed' moves the table down
-Electroniccl-isplayshowsthepresetthicknessofworkedmaterial
- Main compressed air inPut
- Sanding belt tension unit R
- Sanding belt tension unit RT
-Timingrelayscontrolsthepadinautomaticmode,anda]lowsforthe
äi;;ñ';nt ót *t" moment of extension'
.Switch.,Manual-Automatic,,selectsthemodeofthepneumatically
controlled Pad'
, - position n,0" - the pad is not in working position.
- position ,,Manuãi" - The p"O- "XãtìOt to the lower working
Ë:iil,:i',,Aurornatic,, - The pad extends automaticalrv in rine with
the starting position of the *åtáüál and its leading edge' The
timing relaysñust be adjusted beforehand'
Jã E
too
I
\
I
1
17

- Move pad force
- lnside press of pad (for pneumatic or segmented pad)
6.2, Cati
By pushing -
to inches and
message.
6.3. Auto
table
ino
tionof lifti
off
nqr -ô
le
ut
6,2.1. Zero settinq
lf it should be necessary to reset the erectronic read out act as forows:
- set the tabre to.zero-degr""r by means of a checking rure
- Push + and set buttont-"ìrrl"'n"9u:ly, tú Ji+i;y wiil show an intermittent ZER'
with a numeric,value that you must change.
- Push + and - buttons tò rÇËt.
- Pr¡sh the set button to memlize the vafue.
- Push esc to quit the ,"rái rááã.
6.2.2. e
üHilt#:ifr3:.Iîl".."ttomaticallv the prosrammins mode, if no buttons are pushed
button for 3 seconds, the unit of measurement is changed from mi¡imetres
vice versa. rnches counting is shown o¡r a reo l"o-;n"r,t to the mm/inch
ff:iirrt;in mirimerres is set automaticaty, after switching the dispfay
maÍiCD ¡r¡ ta
IP :qry.pment provides for automatic positioning of the
table to the thickness of workeã: materiar and the intenoeo
amount of finishing. rt eriminates incorrect manuar set-up of
the table due to incorrect r"árrr"rent of the materiar,
incor¡ect carcuration of the inienà"0 finish, or inaccurate
setting of the position.
- 9lop the loading conveyor
- slide the tabre õrigr,flvló;er than the thickness of materiar
- Place materiar onlne tabre "nJ.r¡0" ii Ët*;;ää"rrr¡ng feerers.
-Adjust the intendeo matàr¡*irinËr, on.the.."i" ov'fl.," crank handle. Values from
zero in the "+" direction indicate distance ;t";å the material, and below zero
towards "-" indicate amount of Rnan. ni;o;Ú'Jãå-pr"v shows the real thickness of
the material when engaged.
;""Tii"fush-button ,!p-', and the table will stop automaticaltyr in the correct
18

6.4. Manual wheel
Serves the accurate engagement of the required table position. To lift the table turn the
wheel ccw and observe the display.
Attention! Do not adjust while working.
The wheel may be used also for releasing the table should the material become wedged
in the machine-
6.5. Startinq the mach
Prior to starting the machine check the area around for neglec-ted unwanted objects
S1ÀRT E
Switch the main switch to "Or'ì".
Depress push-buton ,,Start" - the push-button lights up vuhite. Control; circuits
are ready and the break is off. If the push-button doesn't light up, the control
cil'cuits are not connected because of a disconnected safety .''ú¡tcn. Check
whether sufficient air pressure is present in the loop, the sandiñg belts are tight
in the correct position, the side door is closed, and emergency buttons are not
locked. The switches "star-delta" and "Loading conveyor épeed" must be in ,,0f,
position.
D_epress push-button ,UP" or ,,Down" and adjust table elevation according to
display, or use automatic engagement.
Start working units - switch "Star-delta" to 1tt position and after a few seconds
when the current drops lo 2nd position. lt is not possible to operate the machine
continu,ally in the 1"r position. lt is there only for easier start-up. lf the machine is
equipped with automatic starter, press only the green button "start".
Start loading in thefirst or second speed.
6.6. Stoppinq the mac ine
To sûop the machi-ne shift speed gear to position ,,0"
To stop completely the machine switch phase shift Star-delta to positiorì "0" without
delay in the Star position.
lf the machine has the automatic starter Star-delta, depress only the red push-button
,,Stop" (not the emergency stop push-button).
19
M
+I

o
Always wait for the machine to cotrre to a complete stop, and then switch the main
switch to position "Off', and "Loading conveyor speed" to ,,ô,,.
6.7. calibratinq and sândins of solid wood on the RT machine
- lnstall sanding belt suitable for the operation, such as 60
grain, on the working unit.
- lnsert foot and fix with lever.
- Tighten belt by pulling button 3.
- Switch main switch and push button',Start".
- Measure thickness of material and move the table to
required position.
- Turn hand.le 6 and extend pad to top position.
- Start the woking unit.
- Start the loading conveyor.
- Make a pencil mark on the surface of il're material and
insert it ínto the machine.
- Check that the mark disappeared. lf not, move the table
up until it disappears.
- Make a pencil mark on the just calibrated surface; lower
the pad position by handle 6, and after the rnaterial passed
through eheck that the mark disappeared. tf not, lower the
pad position untilthe mark disappears.
The machine is ready for calibrating and finishing work.
6.8. Galibratino- andino. an sandino on the RRT machine.
- lnstall sanding belts on the
working unit suitable for the
operation, such as 80 grain on a
twin-cylinder or 150 grain on a
trþle-cylinder.
- Measure thickness of the
sanding belt on each unit, and
by turning handle 4 set this
value on scale 5. Set a slightly
higher value on the other unit to
keep the eylinder away from the
material. Loosen crank handle,
and lift the pad as well by
turning handle 6 higher.
- lnsert a pad and fix the unit by
he handle.
- Tighten the belts by pulling
button 3, and close the door.
switch the main switch on, and push-button ,,start" (white líght appears).
Measure materialthickness and move the table into the required position.
Start the unit and the conveyor.
Make a pencil mark on the materialsurface and insert into the machine.
Check that the mark disappeared. If not move the table higher up until the mark
disappears.
4
3
5
6
z
4
4
a
5
E
5
6
20
This manual suits for next models
5
Table of contents
Popular Sander manuals by other brands

Hitachi
Hitachi SP18VA Handling instructions
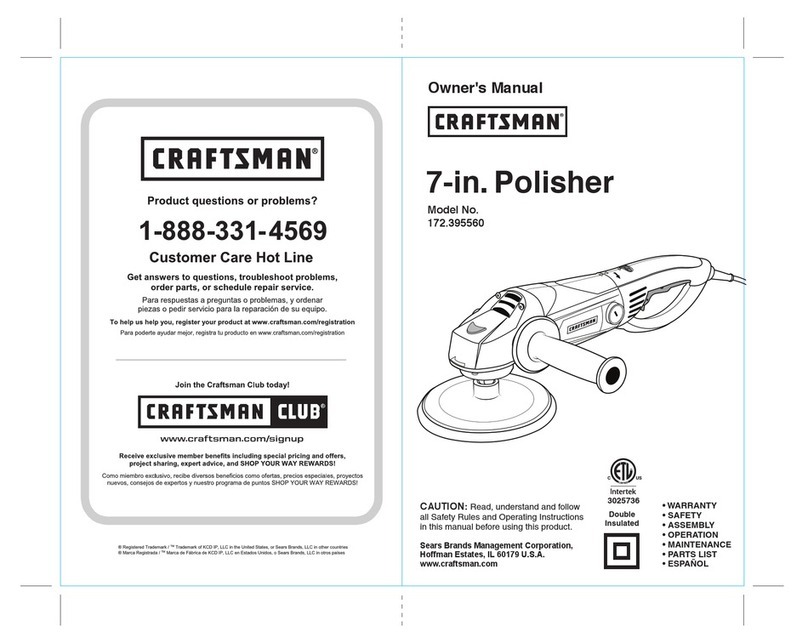
Craftsman
Craftsman 172.395560 owner's manual

Chicago Electric
Chicago Electric 90045 Assembly and operating instructions
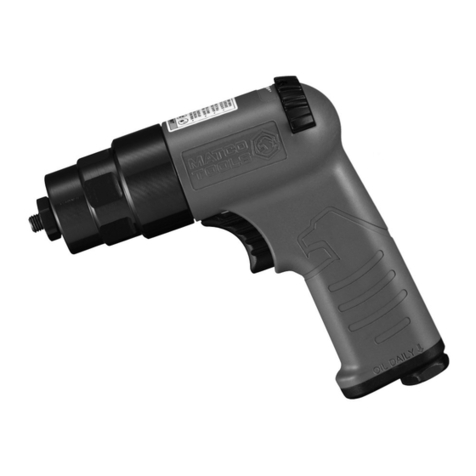
Matco Tools
Matco Tools MT1630 operating instructions

KNECHT
KNECHT B 600 operating instructions
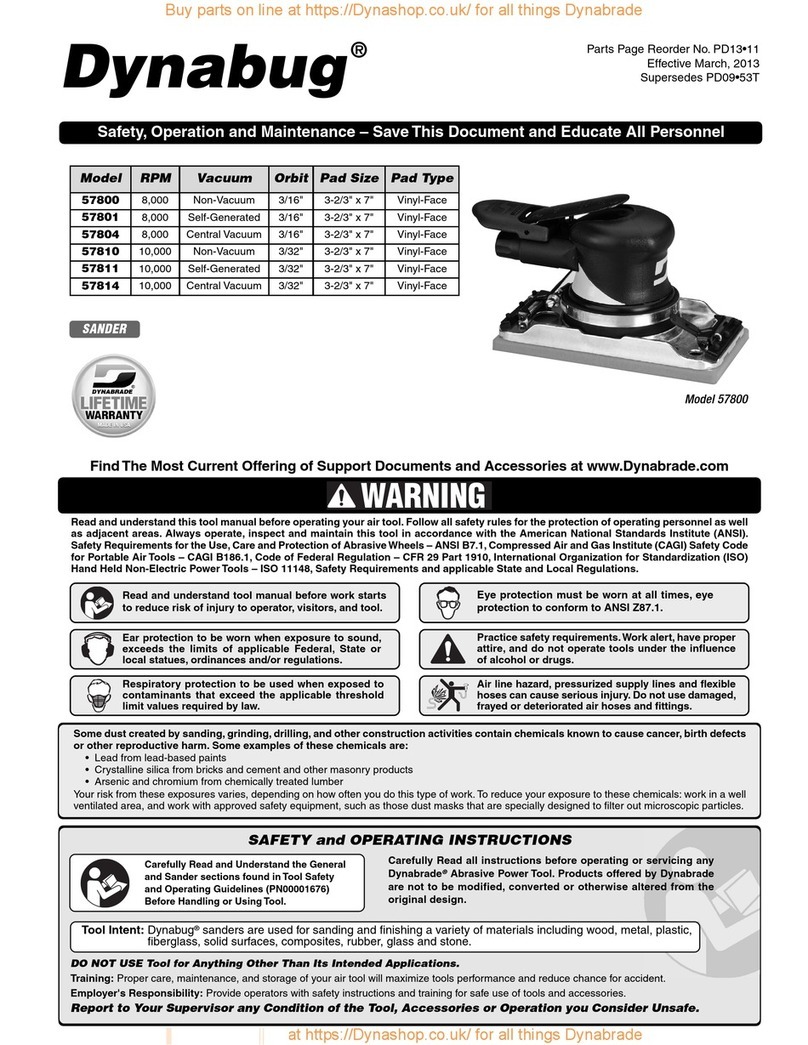
dynabug
dynabug 57800 Safety, operation and maintenance