Haehne DCX User manual

HAEHNE Elektronische Messgeräte GmbH · Heinrich-Hertz-Str. 29 · D-40699 Erkrath Germany · Telefon 0211/9 25 91-0 · Fax 0211/9 25 91-20
DCX EA EN 04_20 Technical modications reserved
Modularer Digital Controller DCX
Quick Start Guide

HAEHNE Elektronische Messgeräte GmbH · Heinrich-Hertz-Str. 29 · D-40699 Erkrath Germany · Telefon 0211/9 25 91-0 · Fax 0211/9 25 91-20
HAEHNE Elektronische Messgeräte GmbH · Heinrich-Hertz-Str. 29 · D-40699 Erkrath Germany · Telefon 0211/9 25 91-0 · Fax 0211/9 25 91-20
DCX
Content
1. System Description ..................................................3
2. Hardware Design....................................................4
3. Terminal Assignment .................................................6
4. Software Design ....................................................8
4.1. Function Blocks ...............................................9
4.2. DCX Operation ............................................... 11
4.2.1.ModicationofDisplayedValues .......................... 11
4.2.2.PeakValueMode ......................................13
4.2.3. Quick Function ........................................14
4.2.4. Adjustment Mode ......................................16
5. Operating Instruction
5.1. Sensor Adjustment ............................................19
5.2. Controller Adjustment ..........................................20
5.3. Fieldbus and Master Adjustment .................................21
6. Description of Parameters
6.1.ParametersDisplayedValues ...................................23
6.2. Parameters Level 1 ...........................................25
6.2.1. General Display Adjustment (Function Block 0)...............25
6.3. Parameters Level 3 and 4 ......................................26
6.3.2. Anybus Inputs (Block 1) .................................26
6.3.3. Analog Inputs (Block 4) .................................28
6.3.4.Amplier(Block5) .....................................31
6.3.5. Mathematical functions (Block 6) ..........................34
6.3.8. Analog Outputs (Block 9) ................................36
6.3.9. Anybus Outputs (Block A) ...............................38
6.4. Parameters Level 7 ...........................................39
6.4.1. Anybus (Function Block 1) ...............................39
7. Parameter Table ...................................................40
8. Tabular Overview of Signal Sources ....................................43
This quick reference guide covers primarily the function of the DCX as an amplier.
The digital inputs and outputs as well as the other parameters and settings are ex-
plained in more detail in the Reference Manual.
2 Content

HAEHNE Elektronische Messgeräte GmbH · Heinrich-Hertz-Str. 29 · D-40699 Erkrath Germany · Telefon 0211/9 25 91-0 · Fax 0211/9 25 91-20
Several Applications of Web Tension Measurement
1. System Description
The DCX is a multi-functional amplier system that can be congured through its modular design to customized in-
dustrial application. The individual modules, options and specications can be individually tailored to t the specic
applications.
Up to eight force measurement channels can be operate with the amplier inputs and can be processed with ad-
ditional process variables.
Averaging, dierence calculation or wrap angle correction can be assigned separately to each channel. The signal
processor of the DCX also calculates complex functions in a very short time, eg. the evaluation of the X-Y signals.
The DCX can also be used as a multi-channel web tension controller. Various controller models can be congured
and the control behavior can be modied by winding diameter or the strip speed.
There are analog and digital interfaces available for the signal outputs. On the analog side there are up to eight
voltage outputs available and in addition eight current outputs. On the digital side this is either a eldbus interface,
such as Probus or either an Ethernet interface, such as Pronet.
With digital control inputs and outputs, the controller settings can be changed or limit switches can be set.
With the menu-driven touch-panel display, the set up and the use of the DCX is very user friendly.
System Description
Blown Film Lines
CalanderTissue Machine
3

HAEHNE Elektronische Messgeräte GmbH · Heinrich-Hertz-Str. 29 · D-40699 Erkrath Germany · Telefon 0211/9 25 91-0 · Fax 0211/9 25 91-20
HAEHNE Elektronische Messgeräte GmbH · Heinrich-Hertz-Str. 29 · D-40699 Erkrath Germany · Telefon 0211/9 25 91-0 · Fax 0211/9 25 91-20
DCX
4
2. Hardware Design
The DCX is a user-oriented combination of functional units which are arranged around the core: the Digital Signal
Processor. This runs synchronously to the A / D converter with a cycle time of 0.52 ms. In one clock cycle every
eight converter signals, present in the A / D, are read, processed and issued again with 16 bit resolution.
Parallel to this, in the same clock cycle, occurs the conversion of the eight analog input signals into digital signals
in the 24 bit sigma-delta converter. These are available in the next clock cycle for further processing.
Analog Inputs
The eight inputs are designed either as a measuring amplifier differential inputs to connect to strain gauge
sensors or at the option of the customer as ±10 V signal input voltages. The differential inputs are normalized
to ± 20 mV.
Signals up to max. ± 40 mV can be analyzed. The normalized ± 10 V analog inputs can process signals
up to 13.5 V.
Analog Outputs
The eight optional analog outputs are normalized to ± 10 V. The maximum voltage is ± 12 V. They are fully
configurable in terms of operating range and assignment. To each voltage output a current output can be option-
ally assigned. The current range 4-20 mA corresponds to the standard signal 0-10 V.
8 Channel
A/D-
Converter
24-Bit
Sigma-Delta
2-8Strain gauge input
Nominal voltage ±20mV
max.±40 mV
6-0Voltage inputs
Nominal voltage ±10V
max.±13.5 V
Processor
with Flash
0.52 ms
Cycle time 4 Channel
D/A-
Converter
16-Bit
2x4Digital inputs
(Photocoupler /24V)0-8Digital outputs
(Reed relays /NO/24 VDC/ 300 mA /1ms optional
single pole double throw (AEM) 230 VAC/1A/10ms)
Nominal voltage ±10V
max.±12V
U/I-
Converter (0)4-20mA
Bridge supply voltage
every two channels
10V/160 mA
Value
storage
Display
160x104
Touch Panel
Reference voltage
10V/10mA
every
Channel
Anybusinterface
2x
Hardware Design

HAEHNE Elektronische Messgeräte GmbH · Heinrich-Hertz-Str. 29 · D-40699 Erkrath Germany · Telefon 0211/9 25 91-0 · Fax 0211/9 25 91-20
Bridge Power Supply And Reference Voltage
For the supply of the strain gauge sensors a bridge supply of 10 V / 160 mA is available. Optional up to
4 x 160 mA are possible. One output with 10 V / 10 mA is provided as a reference voltage. This output can
also be used for external potentiometers.
Digital Inputs
For control functions there are eight galvanically isolated 24 V inputs.
Digital outputs
As digital outputs up to eight Reed type relays are available as normally open contacts (SPNO) or as PCB relays
double throw contacts (SPDT) are available. DC voltage up to 24 V / 300 mA with a response time of max. 1 ms
can be switched with the normally open relay. With the double throw relay an AC voltage to 230 V / 1 mA with a
response time of 10 ms can be switched.
Anybus Interface
At the Anybus interface the following fieldbus versions can be connected: BACNet MS/TP, CANopen,
CC-Link, ControlNet, Modbus RTU and Profibus. With Ethernet modules, the versions BACNet/IP, EtherCAT,
Ethernet/IP, Modbus TCP, Profinet and SERCOS III can be connected.
Hardware Design 5

HAEHNE Elektronische Messgeräte GmbH · Heinrich-Hertz-Str. 29 · D-40699 Erkrath Germany · Telefon 0211/9 25 91-0 · Fax 0211/9 25 91-20
HAEHNE Elektronische Messgeräte GmbH · Heinrich-Hertz-Str. 29 · D-40699 Erkrath Germany · Telefon 0211/9 25 91-0 · Fax 0211/9 25 91-20
DCX
3. Terminal Assignment
The terminal assignments shown here are for use of DCX without digital inputs and outputs. The terminal assign-
ment for the DCX with digital inputs and outputs is described in the Reference Manual.
UBr-/#
USig- /GND
UBr+/#
789101112 12345613141516232425262728 171819202122
USig+ /U+
AI1
UBr-/#
USig- /GND
UBr+/#
USig+ /U+
AI2
UBr-/#
USig- /GND
UBr+/#
USig+ /U+
AI3
UBr-/#
USig- /GND
UBr+/#
USig+ /U+
AI4
UBr-/#
USig- /GND
UBr+/#
USig+ /U+
AI5
UBr-/#
USig- /GND
UBr+/#
USig+ /U+
AI6
UBr-/#
USig- /GND
UBr+/#
USig+ /U+
AI7UBr2 UBr1
UBr3
UBr4
UBr5
UBr6
UBr7
GND
3130
U+
URef
2928272625242322212019181716151413121110987654321
GND
U+
AO8
I+
GND
U+
AO7
I+
GND
U+
AO6
I+
GND
U+
AO5
I+
GND
U+
AO4
I+
GND
U+
AO3
I+
GND
U+
AO2
I+
GND
U+
AO1
I+
PE
24V
0V
29303132
UBr-/#
USig- /GND
UBr+/#
USig+ /U+
AI8UBr8
DCX
PH30
Optionales
Netzteil bei
Spannungs-
versorgung:
110-240 VAC
-
+
24V
N
L
VAC
PE
X5
Anybus
X1
X2
With the optional power supply of 110-240 V AC and the housings G1 to G4, the 24 V supply is pre-wired
for the power supply PH30 (X1: terminal 1 and 3).
The power supply voltage must be grounded. In the power supply loop the current of the supply voltage should
not be exceed 500 mA.
Optional:
PH30 Power
Supply with
voltage supply
110-240 V AC
6Terminal Assignment

HAEHNE Elektronische Messgeräte GmbH · Heinrich-Hertz-Str. 29 · D-40699 Erkrath Germany · Telefon 0211/9 25 91-0 · Fax 0211/9 25 91-20
Terminal Block X1
Terminal No. Description
1 and 2 24 V Supply voltage +
3 and 4 0 V Supply voltage -
5PE-connection
6Reference voltage 10 V
7GND
8Voltage output AO1
9GND
10 Current output AO1
11 Voltage output AO2
12 GND
13 Current output AO2
14 Voltage output AO3
15 GND
16 Current output AO3
17 Voltage output AO4
18 GND
19 Current output AO4
20 Current output AO5
21 GND
22 Current output AO5
23 Voltage output AO6
24 GND
25 Current output AO6
26 Voltage output AO7
27 GND
28 Current output AO7
29 Voltage output AO8
30 GND
31 Current output AO8
Terminal Block X2
Terminal No. Description
1Bridge supply voltage UBR1 +
2Bridge supply voltage UBR1 -
3Signal voltage AI1 +
3Signal voltage AI1- / GND
5Bridge supply voltage UBR2 +
6Bridge supply voltage UBR2 -
7Signal voltage AI2 +
8Signal voltage AI2- / GND
9Bridge supply voltage UBR3 +
10 Bridge supply voltage UBR3 -
11 Signal voltage AI3 +
12 Signal voltage AI3- / GND
13 Bridge supply voltage UBR4 +
14 Bridge supply voltage UBR4 -
15 Signal voltage AI4 +
16 Signal voltage AI4- / GND
17 Bridge supply voltage UBR5 +
18 Bridge supply voltage UBR5 -
19 Signal voltage AI5 +
20 Signal voltage AI5- / GND
21 Bridge supply voltage UBR6 +
22 Bridge supply voltage UBR6 -
23 Signal voltage AI6 +
24 Signal voltage AI6- / GND
25 Bridge supply voltage UBR7 +
26 Bridge supply voltage UBR7 -
27 Signal voltage AI7 +
28 Signal voltage AI7- / GND
29 Bridge supply voltage UBR8 +
30 Bridge supply voltage UBR8 -
31 Signal voltage AI8 +
32 Signal voltage AI8- / GND
The terminal assignments shown here represent the complete version of the DCX.
In a partial version only the required terminals are connected. Corresponding inputs are
defined as strain gauge sensor inputs. Also in this case the signal inputs are
designed as differential inputs.
Terminal Assignment 7

HAEHNE Elektronische Messgeräte GmbH · Heinrich-Hertz-Str. 29 · D-40699 Erkrath Germany · Telefon 0211/9 25 91-0 · Fax 0211/9 25 91-20
HAEHNE Elektronische Messgeräte GmbH · Heinrich-Hertz-Str. 29 · D-40699 Erkrath Germany · Telefon 0211/9 25 91-0 · Fax 0211/9 25 91-20
DCX
The software of the DCX is divided into blocks. These blocks are independently operating functional units can
therefore be independently congured.
8 Software Design
4. Software Design
Up to 8 analog values from the data matrix can be displayed. All block outputs are scheduled as a source.
This simplies troubleshooting in customer systems, eg. the raw data of the sensor signals can be checked with-
out a measuring device.
Depending on the application, the inputs of the blocks can be selected exibly from the data matrix.
The matrix is supplied from the outputs of the blocks 0-9.
In the blocks 0, A and C all values from the data matrix can be processed.
For block 5 (*) applies the following: the amplier input can process values only from the strain gauge sensor
inputs. The inputs of the wrap angle correction can be linked only with values from the blocks 0 ... 4.
Blocks 6, 7, 8 and 9 (**) can be linked only with values from the "smaller" blocks.
This guarantees the processing of data in a cycle of 0,52 ms.
Blocks 2,3 and B are not shown because they are currently not used, but are reserved for further use.
Block 5
8 Amplifier
Block 7
8Controller
Block 8
8Adder
Relays
8 NO or
SPDT
Block 1
Anybus
8Analog
Inputs
Block 0
8Buffer
Digital Inputs
8 Photocoupler Inputs DI01...DI08
8 Anybus Digital Inputs DI11 ...18
(Analog values) data matrix
-> 1 cycle ->
selectable via block/channel
11...18
01...08
all
Block 6
Math
8 channel
*
51...58
Block 9
8 Analog
Outputs
Block C
8 Limit
Switches
Display
max.8values
8 DI and 8DO „LEDs“
all
61...68
71...78
81...88
91...98
all
**
**
**
**
LS01..08
Block A
Anybus
8Analog
Outputs
Block 4
8Analog
Inputs
41...48
all
Limit Switch and status
Anybus
8Digital
output

HAEHNE Elektronische Messgeräte GmbH · Heinrich-Hertz-Str. 29 · D-40699 Erkrath Germany · Telefon 0211/9 25 91-0 · Fax 0211/9 25 91-20
4.1. Function Blocks
Each block consists of 8 channels with identical parameters. Blocks that are not necessary for the specic
application can be disabled. Therefore the operation need not be considered in more detail at this point.
Block 0 - Temporary Storage
the selected signals of the data matrix from the previous cycle are scaled and ltered here.
This allows, for example, the use of the analog output values again as inputs for the controller block.
Block 1 - Anybus Analog Inputs
The incoming "analog data" via the Anybus module are scaled here and can optionally also be ltered.
Block 4 - Analog Inputs
The lter behavior and the scaling of each analog input is adjustable independently.
This way very noisy signals can be better processed. The correction factors for multi-axis sensors are also
entered here.
Block 5 - Ampliers
In this block, the virtual amplier inputs are adapted to the dierent sensors. Each amplier is associated with
one or more sensor outputs. In the latter case it is possible choose between an average or a summation.
The usual settings, such as zero point and gain are made here. A correction of the wrap angle can be activated
here for each channel and can be individually congured. To simplify conguration, a coupling of the ampliers
is possible. The calibration functions can be triggered by external signals.
Block 6 - Mathematical Functions
In this block, special calculations can be performed.
The block can be used for various calculations. These are for example the averaging of separately evaluated
sensor signals, the dierence calculation for detecting a defective sensor or the winding diameter projection for
the control function. The signal analysis of the multi-axis sensors is also done in this block.
Block 7 - Controller
This block describes the PID controller with additional functions.
For more details see the Reference Manual.
Block 8 - Adder
The sum of up to 8 signals is calculates here. Due to the separate adjustment of the scaling, which also allows
an inversion, a separate evaluation of the signals is possible.
Software Design 9

HAEHNE Elektronische Messgeräte GmbH · Heinrich-Hertz-Str. 29 · D-40699 Erkrath Germany · Telefon 0211/9 25 91-0 · Fax 0211/9 25 91-20
HAEHNE Elektronische Messgeräte GmbH · Heinrich-Hertz-Str. 29 · D-40699 Erkrath Germany · Telefon 0211/9 25 91-0 · Fax 0211/9 25 91-20
DCX
Block 9 - Analog Outputs
Here the analog voltage outputs are congured independently.
The outputs are exibly allocatable. The signals are ltered dierently depending on the use.
The output voltage range is also set in this block. The signal can be limited to positive values only. For devices that
may cause problems during further processing, the value can be set to a certain maximum voltage.
It is possible to activate an analog peak value storage per channel. This can be reset via the digital interfaces.
The output range of -10 V to 10 V can be compressed to the range of 0 to 10 V. This is useful when positive and
negative signals are to be processed, but only one current input or one 0 to 10 V input is available.
In addition, a switching function is integrated. This enables switching the output to an alternative signal by using a
digital input.
Block A - Anybus Analog Outputs
The "analog data" sent to the Anybus module, are scaled and ltered here on request.
Block C - Limit Switch
The selectable assignment to external or internal signals enables the a monitoring of a limit switch with adjustable
characteristics.
Digital Inputs
The digital inputs DI01 to DI18 are control inputs intended for activatable special functions (eg external zeroing,
controller lockout, peak level reset, output signal switching)
Digital Outputs
Through the digital outputs, the switching states of the limit switches or their status messages, such as adjustment
function or voltage limitation, are issued. The signals are routed either to the Anybus as 8bit value or they switch
the relays.
10 Software Design

HAEHNE Elektronische Messgeräte GmbH · Heinrich-Hertz-Str. 29 · D-40699 Erkrath Germany · Telefon 0211/9 25 91-0 · Fax 0211/9 25 91-20
11Operation
4.2. DCX Operation
After applying power on the DCX starts with the start screen.
4.2.1. Modication of Displayed Values
The displayed values are changed by directly pressing the corresponding eld
By pressing the rst display position, as an example,
the following parameter selection screen can appear:
The values for the data source, the lter setting, scaling and unit are presented here.
The eld "y" displays the number of changed parameters. If no parameter is changed, then this value is 0.
By pressing the start screen always appears.
Menu Min Max Func ? x
51: xxxxxxxx
52: xxxxxxxx
53: xxxxxxxx
54: xxxxxxxx
55: xxxxxxxx
56: xxxxxxxx
57: xxxxxxxx
58: xxxxxxxx
y
Position 1 (001..)
Source: 51
Scale: xxxxx
Filter: xxxx
Unit: xx
Actual Value: xxxxxxx
DO
DI
Menu Min Max Func ? x
„Digital“ Inputs „Digital“ Outputs
Display range of values/
congurated as 2, 4, 6
or 8 display
Adjustment mode/
By selecting Level, Block,
channel and parameter
number the desired
parameter is set
Activating peak value display Activating quick function

HAEHNE Elektronische Messgeräte GmbH · Heinrich-Hertz-Str. 29 · D-40699 Erkrath Germany · Telefon 0211/9 25 91-0 · Fax 0211/9 25 91-20
HAEHNE Elektronische Messgeräte GmbH · Heinrich-Hertz-Str. 29 · D-40699 Erkrath Germany · Telefon 0211/9 25 91-0 · Fax 0211/9 25 91-20
DCX
12 Operation12
By pressing a parameter eld, the page for the change of values is displayed, in which the respective parameter values
can be set. (Allparameteraredescribedinchapter6.1.„ParameterofdisplayedValues“)
For the data source, for example this is the following page:
This values are not saved permanently. This is especially useful in cases in which
dierent parameter values should be tried only. With restart the old parameter values are restored without
resetting each parameter.
The following page appears:
By pressing "Save", the modied values are transferred to the long-term storage.
In contrast, the page is exited by pressing "Esc" without saving any changes.
With "<" resp. ">" the position in the value eld is selected.
With "˄" resp. "˅" the corresponding digit is increased or de-
creased.
To exit the page without change, use „Esc“
In case of modied values "OK" appears. By pressing it, the
modied values are saved.
< > Esc ^v OK
Position 1 Source (00101)
Actual Value: xxxxxxx
XX
y
Actual Value: xxxxxxx
Position 1 (001..)
Source: 51
Scale: xxxxx
Filter: xxxx
Unit: xx
Esc y
Position 1 (001..)
Save
Thus, the modied values even after a restart are still
present, the eld designated here as "y",must be
pressed in the parameter selection page.

HAEHNE Elektronische Messgeräte GmbH · Heinrich-Hertz-Str. 29 · D-40699 Erkrath Germany · Telefon 0211/9 25 91-0 · Fax 0211/9 25 91-20
Operation 1313
Following page appears:
By pressing "Clear" the peak values are reset to
the current value.
Leave this page with "Esc".
4.2.2. Peak Value Mode
By pressing „Min“- resp. „Max“ on the start screen the peak value mode is activated.
If only individual peak values are to be reset, the corresponding eld must be pressed
directly.
All peak values reset to the actual value with "Clear".
"Esc" to exit the page without resetting.
Min Clear x
51: xxxxxxxx
52: xxxxxxxx
53: xxxxxxxx
54: xxxxxxxx
55: xxxxxxxx
56: xxxxxxxx
57: xxxxxxxx
58: xxxxxxxx
Max Clear x
51: xxxxxxxx
52: xxxxxxxx
53: xxxxxxxx
54: xxxxxxxx
55: xxxxxxxx
56. xxxxxxxx
57: xxxxxxxx
58: xxxxxxxx
Min Clear x
51: xxxxxxxx
52: xxxxxxxx
53: xxxxxxxx
54: xxxxxxxx
55: xxxxxxxx
56: xxxxxxxx
57: xxxxxxxx
58: xxxxxxxx
Esc Clear x
Minimum Position: 1
51: xxxxxxxx
To reset all values, "Clear" must be pressed. Following page appears:
Esc x
Minimum values
Clear

HAEHNE Elektronische Messgeräte GmbH · Heinrich-Hertz-Str. 29 · D-40699 Erkrath Germany · Telefon 0211/9 25 91-0 · Fax 0211/9 25 91-20
HAEHNE Elektronische Messgeräte GmbH · Heinrich-Hertz-Str. 29 · D-40699 Erkrath Germany · Telefon 0211/9 25 91-0 · Fax 0211/9 25 91-20
DCX
14 Operation
Press "Func." on the initial screen, quick functions are called. These are the calibration functions for the zero
point (tare) and the gain for each amplier separately selectable.
4.2.3. Quick Function
Page numbering (current page / number of pages "1/3")
"P <" and "P>" switches between the sides.
By selecting an amplier the following page is displayed:
Values of Level 3 are "Zero" (zero adjustment
value) and "Gain" (adjustment value for a dened
load)
Here, too, shows the as "y" designated eld the number of changed parameters.
If no adjustments were made, this value is 0.
With "Activate" the appropriate activation page is called.
(This additional step is used to avoid incorrect entries.)
Actual value
With "Activate", the corresponding adjustment process
is started.
"Esc" to exit the page without adjustment.
Esc
Calibrate Amplier 1 Zero
Actual Value: xxxxxx
Activate
P< P> x
Function
Calibrate Amplier 1
Calibrate Amplier 2
Calibrate Amplier 3
1/3
Esc y x
Calibrate Amplier 1
Zero
35111: xxxxxx
Activate
Gain
35121: xxxxxx
Activate
xxxx Actual value

HAEHNE Elektronische Messgeräte GmbH · Heinrich-Hertz-Str. 29 · D-40699 Erkrath Germany · Telefon 0211/9 25 91-0 · Fax 0211/9 25 91-20
Operation 15
*) The zero adjust function respectively the amplier adjustment is activated by pressing "Activate".
In order to nd the optimal adjustment value, the calculation of averages is activated for 200 msec.
The input signal should not be changed at this time.
At the amplier adjustment 3 fault conditions are possible:
"GainH": calculated amplication is too high
"GainL": calculated amplication is too low
"Zero": actual calibration weight is too low
Following page appears:
By pressing "Save" the changed parameter values are transferred to the long-term memory. In contrast,
the page is exited by pressing "Esc" without saving the entries.
To assure that the modied values even after a restart are still present, the eld labeled "y" must be pressed
in the amplier overview page.
Esc y x
Calibrate Amplier 1
Zero
35111: xxxxxx
Activate
Gain
35121: xxxxxx
Activate
xxxx
Esc y x
Calibrate Amplier 1
Save
1/3
In this concrete example "y" is the number 1

HAEHNE Elektronische Messgeräte GmbH · Heinrich-Hertz-Str. 29 · D-40699 Erkrath Germany · Telefon 0211/9 25 91-0 · Fax 0211/9 25 91-20
HAEHNE Elektronische Messgeräte GmbH · Heinrich-Hertz-Str. 29 · D-40699 Erkrath Germany · Telefon 0211/9 25 91-0 · Fax 0211/9 25 91-20
DCX
16 Operation
4.2.4. Adjustment Mode
With the gain setting of the rst amplier channel to 1000, the procedure is illustrated by an example:
1. Level Selection
2. Password Input
Additional protection regarding faulty input. In level 1 to 7 the password corresponds to the level.
The eld will be selected by simply pressing the
respective eld.
By pressing the elds "^" or "v" the respective
digit increases or decreases.
With "OK" the password is conrmed.
y x
Level 1
Level 2
Level 3
Level 4
Level 5
Level 6
Level 7
Level 8
y x
Level 1
Level 2
Level 3
Level 4
Level 5
Level 6
Level 7
Level 8
Esc ˄vOK
Level 3 Password
0 0 0 3
By pressing the "Menu" eld in the start screen, select the parameter to be adjusted by selecting the level,
block, channel and the parameter number.
The procedure is similar for all parameters. The parameters are explained in more detail in chapter 6
"Description of Parameters".
Currently, the following levels are assigned:
Level 1: - A display setting such as 2, 4, 6 or 8 display
- Conguration of the Anybus digital outputs
- Relay settings
Level 3 Continuous parameter values such as
Scaling, ltering and amplication
Level 4 Basic settings and combinations of the blocks
Level 7 basic settings of the Anybus, such as the
Slave address
Level 8 HAEHNE basic settings for the hardware
(Only set by HAEHNE)

HAEHNE Elektronische Messgeräte GmbH · Heinrich-Hertz-Str. 29 · D-40699 Erkrath Germany · Telefon 0211/9 25 91-0 · Fax 0211/9 25 91-20
Operation 17
Page numbering (current page / number of pages "1/2")
"P<" and "P>" switches between the pages.
3. Block Selection
Page numbering (current page / number of pages "1/2")
To access more channels, with the "P<" and "P>"
switch between the pages.
4. Channel Selection
5. Parameter Selection
Page numbering (current page / number of pages "1/3")
In order to access additional parameters, "P<" and "P>"
switches between the pages.
6. Parameter Value Mode
Here in parentheses is the complete parameter number,
as listed in the parameter table (chapter 7. Level / block /
channel / 2-digit number)
The elds "<" or ">" the digit position is selected within
the value.
The elds "^" or "˅" each digit is increased or decreased.
With "Esc" exit the page without a change.
The "OK" eld appears only, when a value has been
modied. If the page is left on the eld, the modied
value is adopted.
P< P> Esc 0 x
Level 3 (3...)
Buer
Anybus Inputs
USB Inputs
Analog Inputs
Amplier
1/2
P< P> Esc 0 x
Amplier (35...)
Channel 1
Channel 2
Channel 3
Channel 4
Channel 5
Channel 6
1/2
< > Esc ^v OK x
Amplier Channel 1 (35122)
1000
P< P> Esc 0 x
Amplier Channel 1 (351..)
11: xxxxxxxX
12: xxxxxxxx
21: xxxxxxxx
22: xxxxxxx
31: xxxxxxxx
32: xxxxxxx
1/3
P< P> Esc 0 x

HAEHNE Elektronische Messgeräte GmbH · Heinrich-Hertz-Str. 29 · D-40699 Erkrath Germany · Telefon 0211/9 25 91-0 · Fax 0211/9 25 91-20
HAEHNE Elektronische Messgeräte GmbH · Heinrich-Hertz-Str. 29 · D-40699 Erkrath Germany · Telefon 0211/9 25 91-0 · Fax 0211/9 25 91-20
DCX
18 Operation
In this example one parameter has been changed.
The following page appears:
By pressing the "Save" eld the changed param-
eter values of the amplier channel (Level / Block /
Channel) are stored in the long term memory.
But pressing the eld "Esc" results in leaving this
page without storing the changed value.
As a general rule, pressing the "Esc" eld in leaving the present position
Pressing the eld, results in leaving all previous steps with the immediate return to the
start screen.
P< P> Esc y x
Amplier Channel 1 (351..)
11: xxxxxxxx
12: xxxxxxxx
21: xxxxxxxx
22: 1000
31: xxxxxxxx
32: xxxxxxxx
1/3
Esc 1 x
Amplier Channel 1 (351...)
Save
In order maintain changed values after a new start, it is necessary to press the eld "y" in the parameter selec-
tion page. This eld shows the number of modied parameters.
7. Storing in the Long Term Memory

HAEHNE Elektronische Messgeräte GmbH · Heinrich-Hertz-Str. 29 · D-40699 Erkrath Germany · Telefon 0211/9 25 91-0 · Fax 0211/9 25 91-20
Operating Instruction 19
The following adjustments are necessary only if the amplication cannot be calculated:
Step by step instruction:
1. Wire the system according to the application under consideration.
2. Apply power and wait until operating temperature has been reached.
3. Adjust parameters which deviate from the standard adjustment.
4. If the sensor signal is very volatile then it is possible to use lter adjustment 34x11 to lter the signal.
5. Ensure that the sensor is free of any additional load such as production material webs of foil, paper etc.
Only the initial pre-load consisting of the measuring roll including bearings and possibly other accessories
should be acting on the sensors.
6. Use the "Quick Function" for adjusting the zero point (s. chapter 4.2.3 Quick Function).
After the adjustment the present pre-load, the amplier output shows a voltage of 0 V. If a dierent
voltage is necessary, then it must be adjusted in advance in the menu with parameter 35×11.
5. Operating Instruction
7. Model the web geometry with a belt or rope in
the middle of the measuring roll.
Please ensure that the Web geometry in front
and back of the measuring roll is identical to
the operating conditions. The wrapped rolls must
turn easily (e.g. not driven rolls).
Please pay attention so as to not touch any
machinery components.
8. Connect one end of the rope to a fixed point.
Apply a precisely determined reference weight
at the other end of the roll. The weight force
should be 70 to 100% of the nominal force.
9. Under parameter 35x21 (s. chapter 4.2.4. Adjustment Mode) the percent value of the reference weight
in relation to the maximum force. Use the "Quick Function for adjusting the amplication" (refer to 4.2.3
Quick Functions). After adjustment a voltage is available at the amplier output which is proportional to the
percent value. In case of 100 % of the utilized maximum force the voltage is 10 V.
10000 [mV] *Sensor nominal force [N]
Nominal rating of sensor * 10 [V] * Maximum used sensor force [N]
[ ]
mV
V
33x22 =
As a rule the HAEHNE measuring systems do not need calibration. The measuring amplier is factory calibrated to
the specic sensitivity of the HAEHNE sensors. If the actually used maximum sensor force is less then the nominal
force of the sensor, then it is possible to adjust the amplication with parameter 35x22.(Level 3 / Block 5 (amplier)
/ channel x / 22 (manuel amplier adjustment))
In case the actually used maximum sensor force is not known, then it is possible to calculate the amplication
automatically with parameters 35x21. A reference weight is necessary for this task. In case of web tension mea-
surement an additional rope or cable is necessary to simulate the web geometry.
5.1. Sensor adjustment
Alternatively to positions 7. to 9.
If the amplication factor known then this value can be entered
under parameter 35x22.
Calibration weight
Measuring
roll Amplier
Cable or
rope

HAEHNE Elektronische Messgeräte GmbH · Heinrich-Hertz-Str. 29 · D-40699 Erkrath Germany · Telefon 0211/9 25 91-0 · Fax 0211/9 25 91-20
HAEHNE Elektronische Messgeräte GmbH · Heinrich-Hertz-Str. 29 · D-40699 Erkrath Germany · Telefon 0211/9 25 91-0 · Fax 0211/9 25 91-20
DCX
5.1. Sensor adjustment
Example 1
Sensor data: Nominal rating 1,5 mV/V
Bridge supply voltage: 10 V
(therefore the output signal is 15 mV = 0,015 V at nominal force)
Amplier output: 10 V at nominal web tension
0 V at zero web tension
If the sensor is operating below its nominal force then the amplication must be increased.
Example 2
The maximum sensor load is only 75% of nominal force
.
The output signal is therefore only:
This leads to
:
10. With parameters of Block 9 (analog outputs) or Block A (Anybus analog outputs) the signal of
downstream systems, e.g. a PLC or a display, can be adjusted.
Gain = 10 V = 888,88 ≈ 888,9
0,01125 V
Gain = 10 V = 666,66 ≈ 666,7
0,015 V
15 mV • 75 % = 11,25 mV
100 %
20 Operating Instruction
The settings for the controller are described in the Reference Manual..
5.2. Controller Adjustment
Table of contents
Popular Controllers manuals by other brands

industrie technik
industrie technik TH-xxxSx1 Series user manual
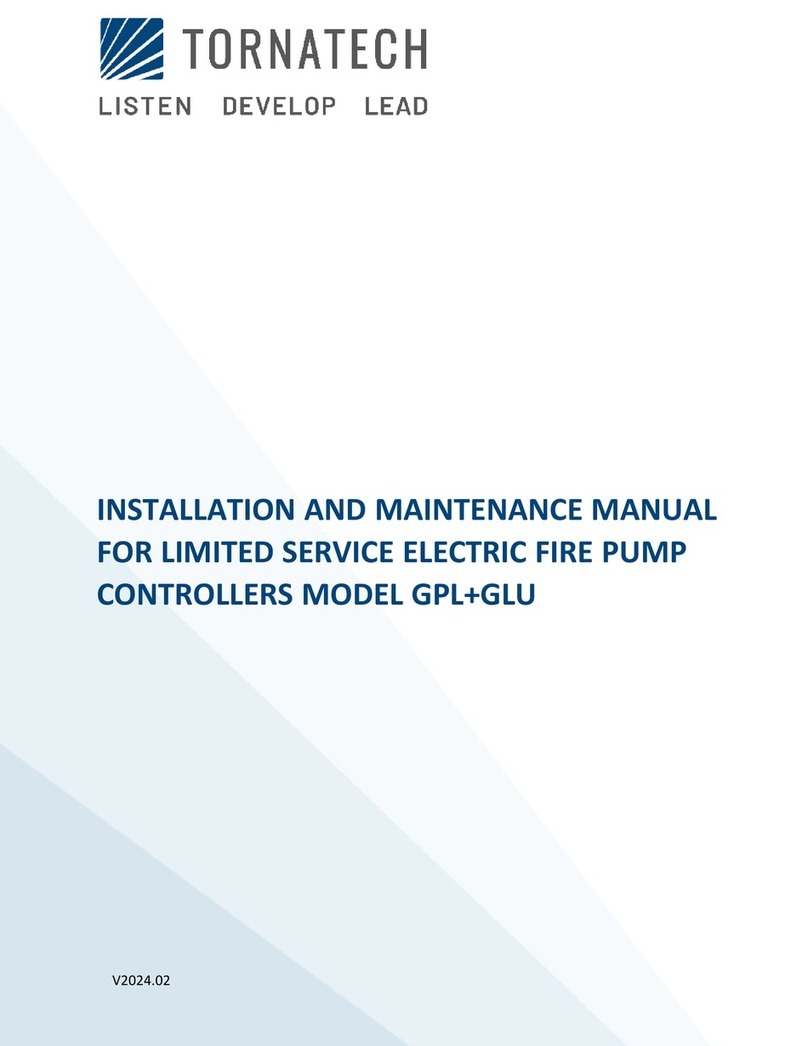
Tornatech
Tornatech GPL Installation and maintenance manual
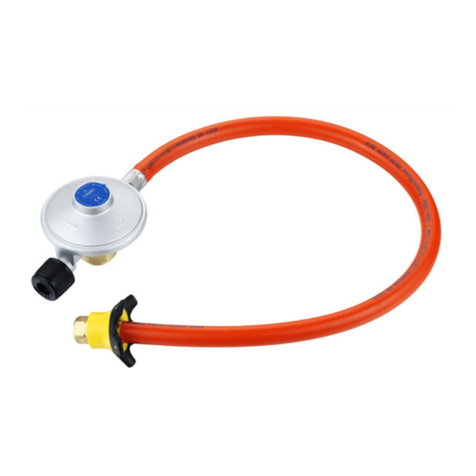
Cadac
Cadac 343 User instructions
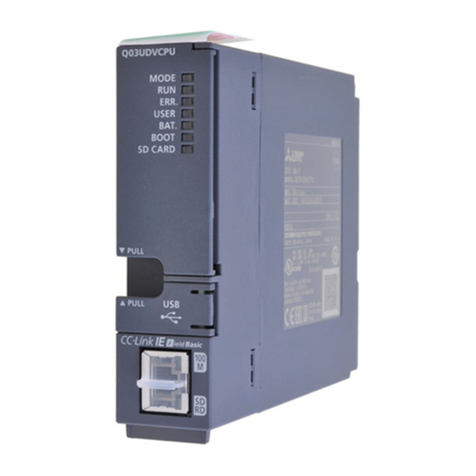
Mitsubishi Electric
Mitsubishi Electric Q03UDVCPU user manual
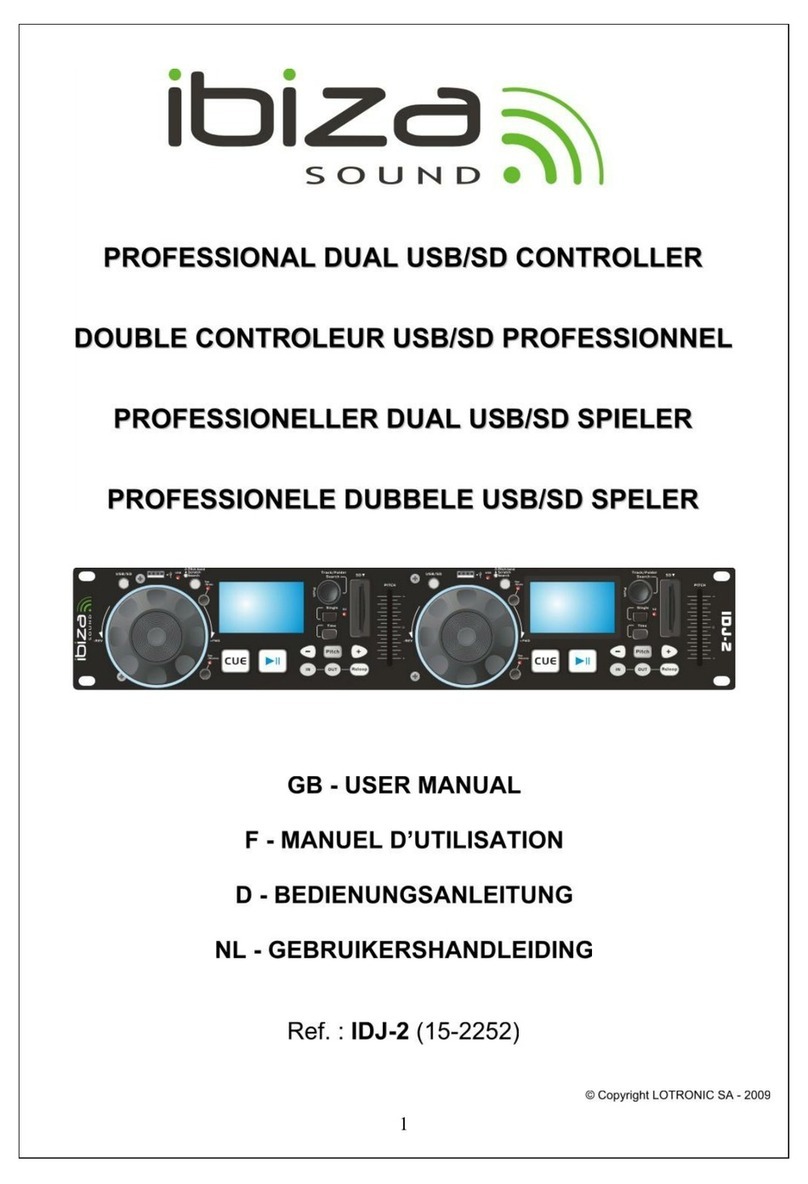
Ibiza sound
Ibiza sound IDJ-2 user manual
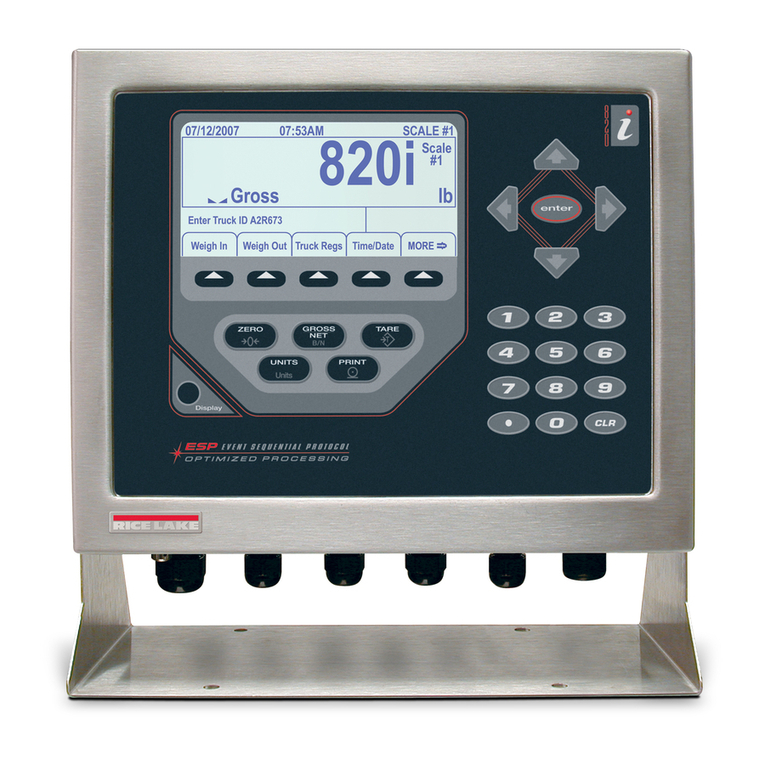
Rice Lake
Rice Lake 820i installation instructions
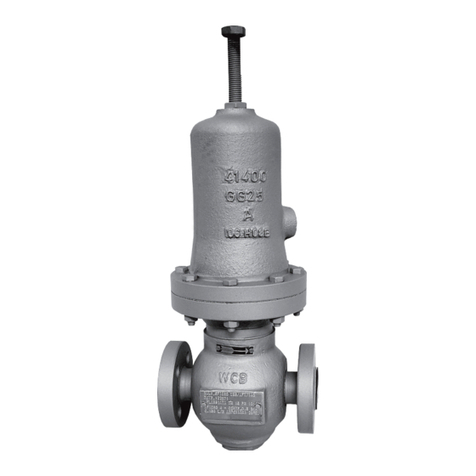
GE
GE Masoneilan 173 Series instruction manual
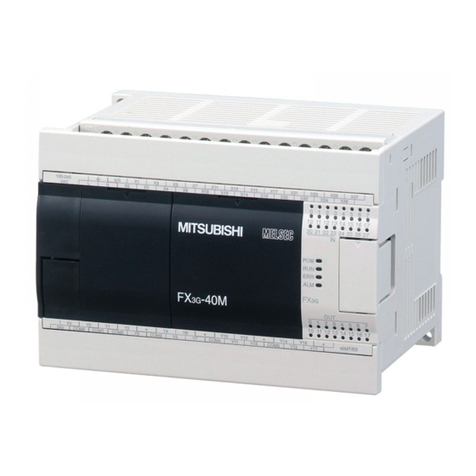
Mitsubishi Electric
Mitsubishi Electric FX3G SERIES user manual

OpenSprinkler
OpenSprinkler OpenSprinkler v3 user manual
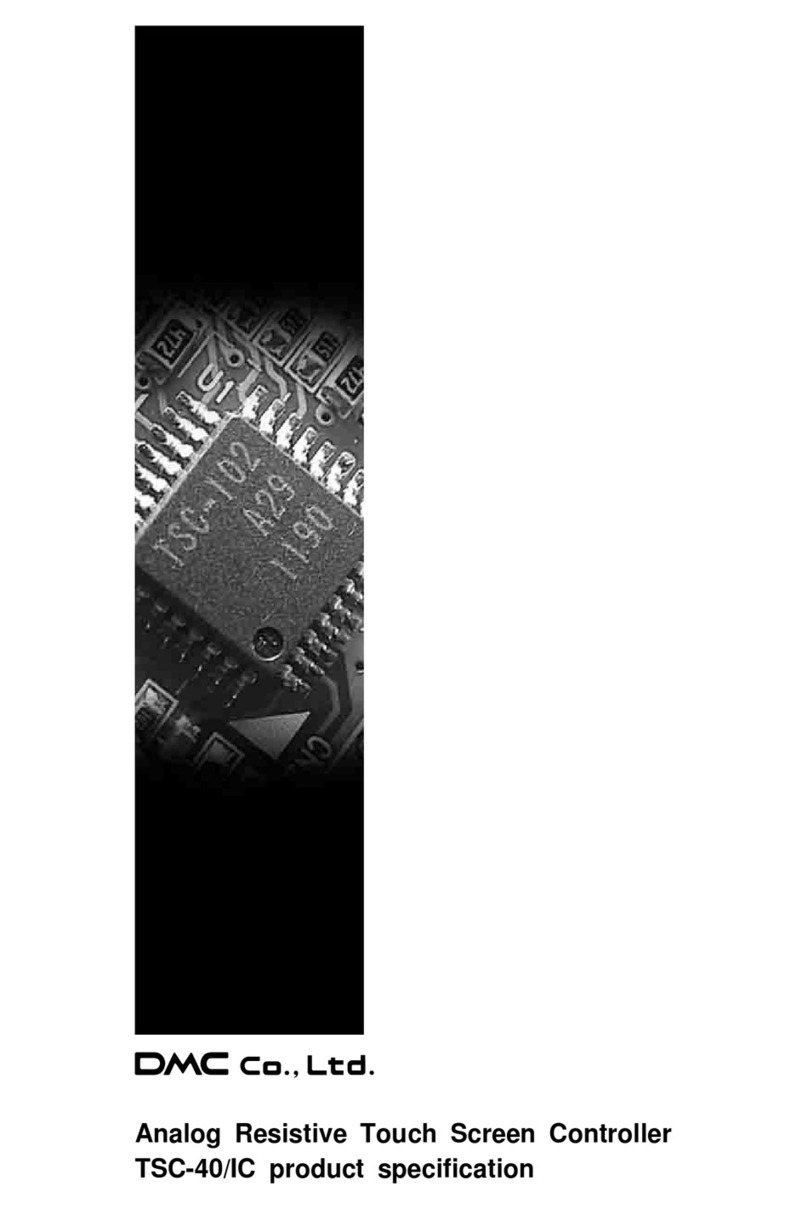
DMC
DMC TSC-40/IC Product specifications
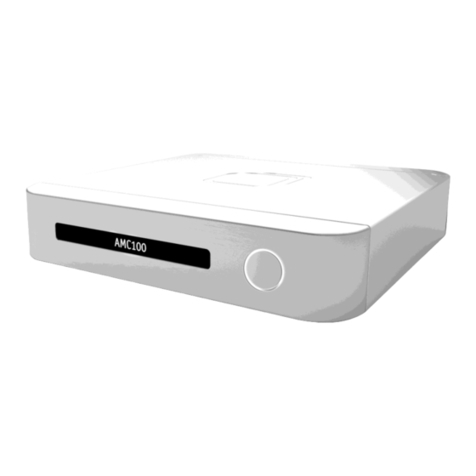
Wittenstein
Wittenstein attocube AMC100 user manual
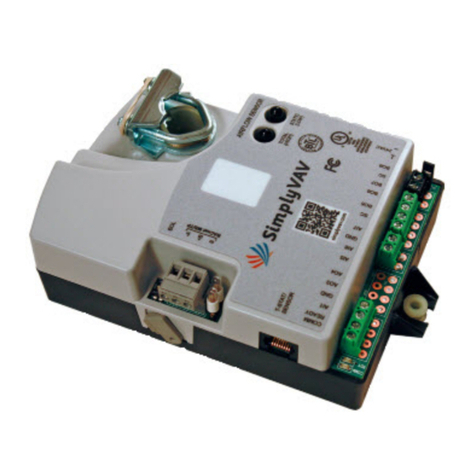
KMC Controls
KMC Controls SimplyVAV BAC-8001 installation guide