HATTAT A90 User manual

1
Service Manual
A90
A100
A110

2

3
A90
A100
A110
Hattat Tarım
April, 2011
Çerkezköy
Aletler
Cab &
Shields
Frame &
Wheels
Front
Axle &
Steering
Brake
System
Power
Transmision
Electrical
System
Engine
General
Hydraulics
Tools
Service Manual

4

5
10. General
11.Layout
12. Maintenance

6
To the reader
The Service Manual for the HATTAT A90, A100, A110 tractors is intended to be a practical reference source to be used in
workshop.
The repair instructions in the manual are based on methods which have been worked out in practice during normal
workshop conditions and which are based on the use of special tools from the manufacturer when stated in the
instructions. The manual also contains descriptions of the design and function of the components.
Detailed maintenance instructions can be found in Operator’s Manual.
The Service Manual will be continually updated with new revised pages which should be inserted in the manual. Alterations
and additions will first appear as service bulletins.
Only genuine Hattat Tarım spare parts should be used to ensure the best possible function of the machine. Certain
operations should be carried out with the aid of special tools designed by Hattat Tarım .
HATTAT Holding
April 2011

7
Layout of Service Manual
1. Division into groups
The manual is divided into groups (10--100) which are based on the make--up of the tractor. The groups are listed on the
firstindexf.
example. 10. General
20. Engine, fuel and cooling systems
30. Electrical system
40. Power transmission
a.s.o.
The number designation for each group is given in the top left box of the respective pages (and the first figure in the code
designation).
2. Division into components or sub—groups
Each group is further divided into components or sub--groups. The number and the name of each component is given in the top
left box on each page (and comprise the two first figures in the code designation).
Example. 41. Clutch
42. Gearbox
44. Low gear
45.Final drives etc.
10. General Model
A90-A100-A110
Page
1

8
10. General Model
A90-A100-A110
Page
2
3. Tractor model
At the top of each page it is indicated for which tractor the page is valid.
4. Page numbers
The instructions for all components are numbered in consecutive order in the right--hand box at the top of the page. The page
numbers begin with page 1 for each component.
5. Additions and amendments of the service manual
New and up--dated pages will be continuously added to the service manual. The new pages should be inserted as indicated by
the code: the first digit (also the first digit on the index leaf) indicates the group:
-- the two first digits indicate the component or sub--group.
-- the third digit indicates the document group for the respective components
-- the page number indicates the definite position of the page within the service manual.
If there are two pages with the same code and page number, it is the page with the later date in the date box and the old date
in the crossed--over box which is valid or which is the current page.
When an entirely new set of repair instructions is issued, it will be accompanied by instructions on where the pages should be
inserted in the file.
41. Clutch Model
A90-A100- A110
Page
1

9
10. General Model
A90-A100-A110
Page
3

10
10. General Model
A90-A100-A110
Page
4
Code designations in the Service Manual
10. General
11 General, lay out
12 Maintenance
20 Engine
Specifications Section
Engine Design
Fuel Injection Lines
Fuel Injection Pump
Fuel Injectors
Fuel Transfer Pump
Lifter Group
Rocker Shaft
Valve Mechanism Cover
Cylinder Head Valves
Cylinder Head
Turbocharger
Exhaust Manifold
Camshaft
Camshaft Bearings
Engine Oil Filter
Engine Oil Cooler
Engine Oil Pump
Engine Oil Pressure
Engine Oil Bypass Valve Engine Oil Pan
Breather Canister
Water Temperature Regulator and Housing
Water Pump
Cylinder Block
Crankshaft
Crankshaft Seals
Connecting Rod Bearing Journal
Main Bearing Journal
Connecting Rod
Piston and Rings
Piston Cooling Jet
Front Housing and Covers
Gear Group (Front)
Flywheel
Flywheel Housing
Crankshaft Pulley
Fan Drive
Engine Lifting Bracket
Alternator
Starter Motor
Glow Plugs
30 Electrical system
31 Electrical system in general
30
General
Safety precautions for the electrical system
Alternator
Battery checks and maintenance
32 Electric system:
Content
32 Electric system
With Cab Models
Cabless models
Standard trailer socket
Headlight adjustment
Electric Diagram of Tractor
Instrument panel
Instrument panel
Front panel of instrument panel (1)
Steering wheel adjustment (2)
Direction indicator flashers and horn (3)
Light switch (4)
Switch for windscreen was− her (5)
Switch for windscreen wiper (6)
Instrument panel (2)
Fuel gauge (3)
Tachometer (4)
Coolant thermometer (1)
Indicator lights for direction indicator (2)
Indicator light for main be−am (5)
Indicator lights on instrument panel
Infoline − instrument panel operating hour meter (2.7)
Right Side panel of instrument panel (3)
Ignition switch (3.1)
Rear window opening and locking device (2)
Roof console
Roof fan (1)
Recirculation control knob (2)
40 Power transmission
41. Clutch
Technical data
Setting values
Tightening torques
Clutch, description
Reconditioning clutch
1. Changing clutch by parting tractor
A. Parting tractor at clutch
B. Removing fitting clutch
C. Assembling tractor at clutch
D. Adjust clutch pedal free travel
E. Adjusting PTO clutch lever free travel
2. Changing clutch without splitting tractor
A. Fitting clutch
B. Reconditioning clutch release bearings
3. Changing propulsion clutch disc and adjusting
clutch
A. Dismantling clutch
B. Assembling and adjusting clutch
50 Brake system
51 . Brake System
Technical data
Brake system
Brake cylinder
Reconditioning brakes
52. Air Brake System
Diaghram of Air Brake System
Twin curcuit hydraulically actuated that controlled from
tractor air brake system
When brake pedal is used that the system working
When hand brake is used in N position
When brake pedal is used in P position that the system
working

11
10. General Model
A90-A100-A110
Page
5
60 Front axle and steering system
61. Steering System
Steering System
Measurement of the steering system, oil pressures
Reconditioning steering valve
Fitting steering valve
62. Powered Front Axle
General information
Disassembly of Hub and Planetary Gear Set
Disassembly of Joint Casing
Assembly of Joint Casing
Disassembly of Steering System
Assembly of Steering System
Disassembly of Drive Shaft
Assembly of Drive Shaft
Disassembly of Differential Unit
Assembly of Differential Unit
Disassembly of Central Housing
Assembly of Central Housing
Conversion Table
Explanation
Tool numbers
70 Frame and wheels
71 Frame:
Front weight support + frame
72 Wheels:
Technical data, technical specifications, training
material
Wheels
Tightening torques, wheel nuts
Tyre pressures and permissible loadings
Track widths
80 Cab And Shield
81 Cab
Cab
Cab Heater
82 Air conditioner
Technical data, technical specifications, training material
Safety precautions
Operating principle
Aır Condıtıoner
Technical data
CIrculation of the refrigerant
Drier
Compressor
Expansion valve
83 Instrument
90 Working Hydraulics, power lift
91.Technical specialities – Valves – Mechanicisms and
Working Principles
Hydraulic Lift Service Guide
Main Relief Valve Operation
Changing of System relief valve
Adjustment of system relief valve
Changing the cylinder relief valve
Changing the LS (Load Sensing) relief valve
92.Disassembling – Assembling – Adjustments
Visual inspection of locking valve and replacement the
parts
Changing of distributor
Dismantling and re-installation of hydraulic lifts
Disassembly, control and re-assembly of hydraulic lifter
arms
Removal, controls and re-assamble of hydraulic cylinders
Setting the operation distance of outer arms of hydraulic
lifter
The principle of power control mechanisms
Setting of hydraulic lifter power control mechanism
Posıtıon Control
Mıxed Control
Auxılıary Cylınder
Electrıcal Autolıft
Electrıcal Autolıft Mechanısm Settıng
Hydraulıc Lıfter Drıve Settıngs

12
General instructions for repairs
Outer oil seals
The Service Manual contains instructions for changing all outer oil seals, (e.g. oil seals on the PTO shaft end, on the output
shaft to the front wheel drive and on the pinion shaft on the powered front axle, and so on).
Sealing compound and glue
If sealing compounds or glue are required for the repair work, the instructions will specify a sealing compound or glue which is
readily available through specialist dealers. Some seals should be greased before fitting and the space between the lips of the
seal should be filled with universal grease. If the seal is to be pushed over splines or sharp edges the seal should be protected
with for example a thin plastic foil.
Tightening torques and setting values
Al necessary tightening torques and setting values for each repair operation are given at the beginning of each repair section
under the heading Technical Data. The most important values can also be found in the repair instructions.
Table 1 later gives the tightening torques in order of dimension, quality and surface treatment. The values given in the table
should be used if the tightening torque is not given in the repair instructions.
Safety
Always bear safety in mind when repairing or servicing the tractor. Use tools and lifting devices in the correct way . When you
are removing tractor components or splitting the tractor, every tractor part must be supported in such a way, that no risk of
accident exists. Avoid working under the supported tractor part if it is not absolutely necessary. When supporting the tractor the
centre of gravity of the frame part must always be checked. For instance the wedges must always be fitted between front axle
and engine to prevent axle oscillation when splitting the front frame of the tractor.
Trouble--shooting
The following procedure, combined with the information contained in the workshop manual will be helpful in tracing faults
accurately. It consists of following a number of logical steps to locate and correct the problem:
a) Determine the problem
b) List possible causes
c) Differentiate the causes
d) Conduct checks in logical order to determine the exact cause
e) Consider approximate remaining service life against cost of parts and labour..
f) Make any necessary repairs.
g) Recheck the parts and functions for correct operation
10. General Model
A90-A100-A110
Page
6

13
Table 1. Tightening torques, metric standard thread (ISO)
1) 1 Nm=0,102 kpm
2) Zne=zinc electroplating
3) Znk=hot galvanized
If the bolts differs from the standard range the values in the table must not be used.
10. General Model
A90-A100-A110
Page
7
Tightening toorques Nm
1
Quality, surface treatment, material and so on
Dim.
8.8
Lubr. tol.± 8.8
Zne
2
) tol.± 8.8
Znk
3
) tol.± 10.9
Lubr. tol.± 12.9
Lubr. tol.±
M4 -
- - - - - - - -
M5 6,4 0,6 5,7 0,5 - 9 1 11 1
M6 11 1 10 1 12 1,2 15 1,5 18 2
M8 25 2 23 2 30 3 35 4 45 5
M10 50 5 45 5 60 5 70 7 90 10
M12 90 10 80 8 100 10 125 10 151 15
M14 140 15 125 10 160 15 200 20 240 20
M16 220 20 195 20 250 25 300 30 370 40
M18 300 30 270 30 350 35 430 40 510 50
M20 430 40 380 40 480 50 600 60 720 70
M22 570 60 500 50 650 65 800 80 970 100
M24 740 70 660 70 830 80 1030 100 1250 120
M27 1100 100 950 100 1200 120 1500 150 1800 180
M30 1500 150 1300 130 1600 160 2040 200 2500 250

14
Conversion table for common units
Quantities and units……………………………………………………………………………… Conversion factors
Overall and detail dimensions millimetres (mm)
……………………………………………….. 100 mm=3,94 inches
1 inch=25,4 mm
Short distances e.g. turning circles metres (m) ………………………………………………..1 m=3,28 ft
1 ft=0,305 m
Travel distances kilometres ………………………………………………………………………1 km=0,62 mile
1 mile=1,61 km
Tractor weights, axle loadings kilograms (kg) ………………………………………………… 1 kg=2,2 lbs
1 lb=0,454 kg
Travel speed kilometres per h (km/h) ……………………………………………………………1 km/h=0,62 mph
1 mph=1,61 km/h
Drawbar pull kilonewtons (kN)……………………………………………………………………1 kN=224,8 lbs
1 lb=4,448 N
Power (identified by such terms as crankshaft power,
………………………………………………..1 kW=1,34 hp
pto power, belt power, drawbar power, indicating
1 hp=0,746 kW
the point at which the measurement was taken)
kilowatts (kW)
Engine torque newton metres (Nm) ………………………………………………………........ 1 Nm=0,74 ft lb
1 ft lb=1,356 Nm
Fuel consumption by weight (kilograms per hr, kg/h)
…………………………………………………1 kg/h=2,2 lb/hr
(by volume) litres per hr (l/h) …………………………………………………………………….. 1 lb=0,454 kg
1 l/h=0,22 gal/hr
1 gal=4,54 l
Fuel economy (specific fuel consumption) ……………………………………………………. 304 g/kWh=0,5 lb/hp hr
grams per kilowatt hr (g/kWh)
Engine displacement litres (l) …………………………………………………………………… 1 l=61,02 m cu in
100 cu in=1,639
Hydraulic pump ……………………………………………………………………………………1 MPa=145 psi
pressure-mecapascal (MPa) ……………………………………………………………………. 1000 psi=6,9 MPa
delivery-millimetres per sec (ml/s) ……………………………………………………………… 100 ml/s=1,32 gpm
Tyrepressure-kilopascal (kPa) ………………………………………………………………….. 1 gpm=75,77 ml/s
100 kPa=14,5 psi
1 psi=6,9 kPa
Area acres-hectare ………………………………………………………………………………. To convert multiply by
0,404686
Volume bushel-litre ………………………………………………………………………............To convert multiply by
39,3687
Quantity pound per acre-kilogram per hectare ……………………………………………….. Multiply by 1,12085
Volume ……………………………………………………………………………………………. Multiply by
superficial foot-cubic metre ……………………………………………………………..............0,002360
10. General Model
A90-A100-A110
Page
8

15
Maintenance
Note! Detailed maintenance procedures are given in the
Operator’s Manual.
When servicing:
-- Always stop the engine before doing any servicing work.
-- Apply the parking brake to ensure the tractor cannot
move.
If the ground is uneven the wheels should be scotched
-- Always observe the utmost cleanliness in al maintenance
work.
--Thoroughly wipe off filter caps and plugs as well as sur-
rounding parts of the tractor before filling up with fuel or oil.
-- Inspect the oil and filters when changing. Large amounts
of dirt (e.g. heavily clogged filters) can point to a fault which
could cause extensive and costly repairs if not corrected in
time.
-- When carrying out checks the tractor should stand on
level ground.
-- Levels should be checked in the morning when the oil is
cold and has had time to run down to the bottom of the unit
concerned.
Lubrication of points provided with grease
nipples
-- Always clean the grease nipples before applying the
grease gun.
-- Pump in grease to the nipples until clean grease is
squeezed out (unless otherwise instructed).
-- Wipe off all surplus grease which has been squeezed
out at the lubricating points.
-- Preferably carry out lubrication with bearing points and
joints unloaded and with the bearings in different position
(e.g. lubricate the steering knuckle bearing on the steering
axle with the wheels at both full left and right lock and with
the front axle lifted up).
Lubrication and maintenance schedule
Al intervals are counted from zero on the hour recorder.
For example, 1000--hour service is carried out every 1000
and 2000 hours according to the hour recorder (yearly or
every other year) even if the operates have been carried
out at the guarantee service.
Example:
The 1000--hour service includes al operates listed under
Daily / every 10 hours, weekly / every 50 hours,250, 500
and 1000 hours.
10. General Model
A90-A100-A110
Page
9

16
10. General Model
A90-A100-A110
Page
10
Maintenance daily/weekly
Daily/every 10 hours
1. Check engine oil level
2. Check coolant level
3. Clean draining hose
Weekly/every 50 hours
4. Lubricate front axle and steering nipples
4--wheel drive
-- universal joints
-- front axle mountings
-- steering knuckles
5. Check propeler shaft, grease nipples for propeller shaft.
(with nipple)
6. Lubricate brake and clutch pedals
7. Lubricate top link and lifting links
8. Lubricate extra lifting cylinder nipples (if fitted)
9. Check fluid level in windscreen washer
10. Check fan and alternator belt
11. Check electrolyte level in battery
12. Drain water from fuel filter, tractors also have a
separate water trap.

17
10. General Model
A90-A100-A110
Page
11
Every 250 hours
13. Clean heating system air filter. Clean air filter of roof
fan.
14. Clean air filter (change if necessary) (filter)
15. Change engine oil and oil filter
16. Change hydraulic system pressure filter. First change
at 100 hours Service inspection. The second change at
250 running hours and the third at 500 hours. After that at
intervals of 250 running hours.
17.Lubricate gear lever joints
18.Check tyre pressures and wheel nuts
Every 500 hours
19. Clean separate water trap
20. Check brake pedal free travel
21.Check propulsion clutch pedal free travel
22. Check PTO lever free travel
23. Check oil level in power transmission
24. Check oil level in differential, 4--wheel drive
25.Check oil level in hub reduction gears, 4--wheel drive
26. Check oil level in hydraulic system
27.Change pressure filter in hydraulic system
28. Change oil filter in transmission
Every 1000 hours/yearly
29. Change oil in hydraulic system
30. Change oil in power transmission
31. Change oil in differential, 4--wheel drive
32. Change oil in hub reduction gears, 4--wheel drive
33. Clean hydraulic pump suction strainer
34. Drain fuel tank
35. Change fuel filter, also change the water trap filter.
36. Change safety filter in air cleaner
37. Check, adjust and lubricate front wheel bearings,
2--wheel drive (only 2wd)
38. Check and adjust front wheel toe--in
39. Lubricate drive axle bearings (2 nipples)
40. Adjust valves
40a. Change air filter of roof fan.
40b. Change breather filter (in filling cap)
Every 2000 hours/every other year
41. Clean cooling system
42. Check alternator
43. Check starter motor
44. Check and clean injectors
Every 4000 hours
45. Turbo unit checked at authorized workshop

18
10. General Model
A90-A100-A110
Page
12
Recommended fuel and lubricants
(All volumes are incl. of filters)
Part of machine SAE / Viscocity API grade Volume when
changing l
Engine
A90, A100, A110
10W- 40
15W- 40
API CF- 4
11
Hydraulic system Tellus 46 ISO HM 30
Power Transmission Valtra HT 200
10W - 30 API GL-4 29
Power front axle (4WD)
- differential 6
- Hubs
80W-90
API GL-5 (LS)
2x0,8
Fuel Tank 70
-with extra tank
The fuel (diesel) must conform to the EN 590
standardstandard 115
Cooling system (ASTM D4985) 15,5
Air Conditioning R134 a 1200 gr
Air Conditioning Compressor oil
ZXL 100 PG 207 ml.
Brake fluid
Brake fluid SAEJ1703 0,5
Front window washer reserv
Washer fluid 1,5
Oil recommendations according to outdoor temperature
When starting the tractor in a warm garage, oil meant for warmer areas may be used.
Note : Please see PERKINS ENGINE catalog for fuel and engine oil quality and maintance. This is the only suggestion.

19
10. General Model
A90-A100-A110
Page
13
Grease
Always use the following greases in Hattat tractors. Each point requires it own type of grease.
Universal grease
Lithium − based universal grease. Is suitable for greasing all heavy machines.
− 30°... +130°C
Universal grease of high quality, lithium based grease for vehicle use. It is recommended for greasing wheel bearings,
chassis water pumps, caterpillar rollers etc. The grease is adhesive, protects against corrosion and resists water and
varying temperatures. Temperature range is
− 30°... +130°C.
Calsium Grease LF
Is suitable for greasing all heavy machines. Long fibre grease. Colour red.
− 20°... +60°C
Calsium LF is of long fibre, high quality and calsium based universal grease for vehicle use. It is recommended for
greasing chassis, water pumps, pins etc.The grease is adhesive, protects against corrosion and resists water and varying
temperatures. Temperature range is − 20°....60°C.
Moly Grease
Is suitable for greasing all heavy machines. Lithium − based universal grease.
− 30°... +130°C
Universal grease of high quality, lithium based grease for vehicle use. It is recommended for greasing wheel bearings,
chassis water pumps, catepillar rollers etc. The grease is adhesive, protects against corrosion and resists
water and varying temperatures. Temperature range is
− 30°... +130°C.
Avoid repeating skin contact.
Protect nature and take care of empty packages
Quality requirements of engine fuel
Property Requirement
Test standard
Specific weight +15ºC. ISO 12185 0,82…0,86 kg/litre ASTM D 4052. EN
Viscosity+40º. ISO 31041 1,2…4,5 mm
2
/s ASTM D
Sulphur content Max. 0,2 p-% ASTM D 4294, ISO 8754
Cetan e number 4737 Min 51 ASTM D
Water content Max. 200 mg/kg ASTM D 1744
The fuel must conform to the EN 590 standard

20
This manual suits for next models
2
Table of contents
Other HATTAT Tractor manuals
Popular Tractor manuals by other brands

Bolens
Bolens nolens 1250 Operator and maintenance manual
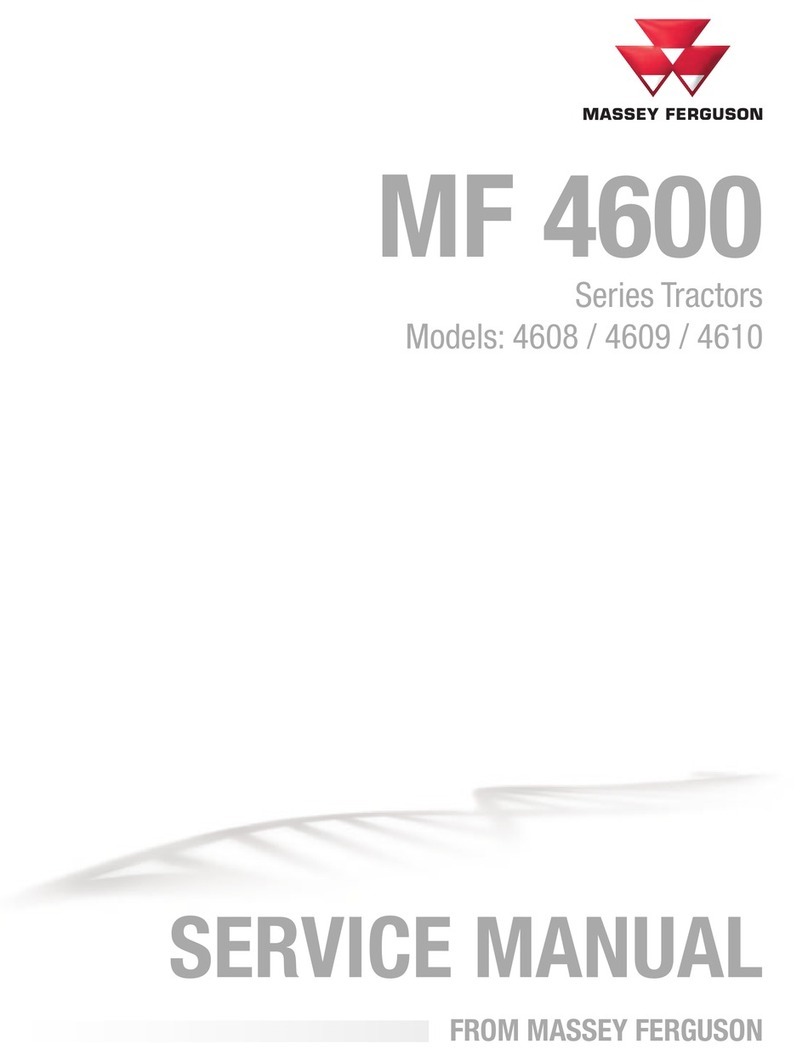
MASSEY FERGUSON
MASSEY FERGUSON 4600 Series Service manual
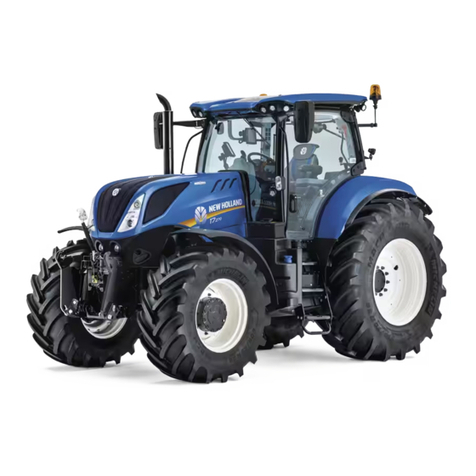
New Holland
New Holland Sidewinder II T7.230 AutoCommand Operator's manual
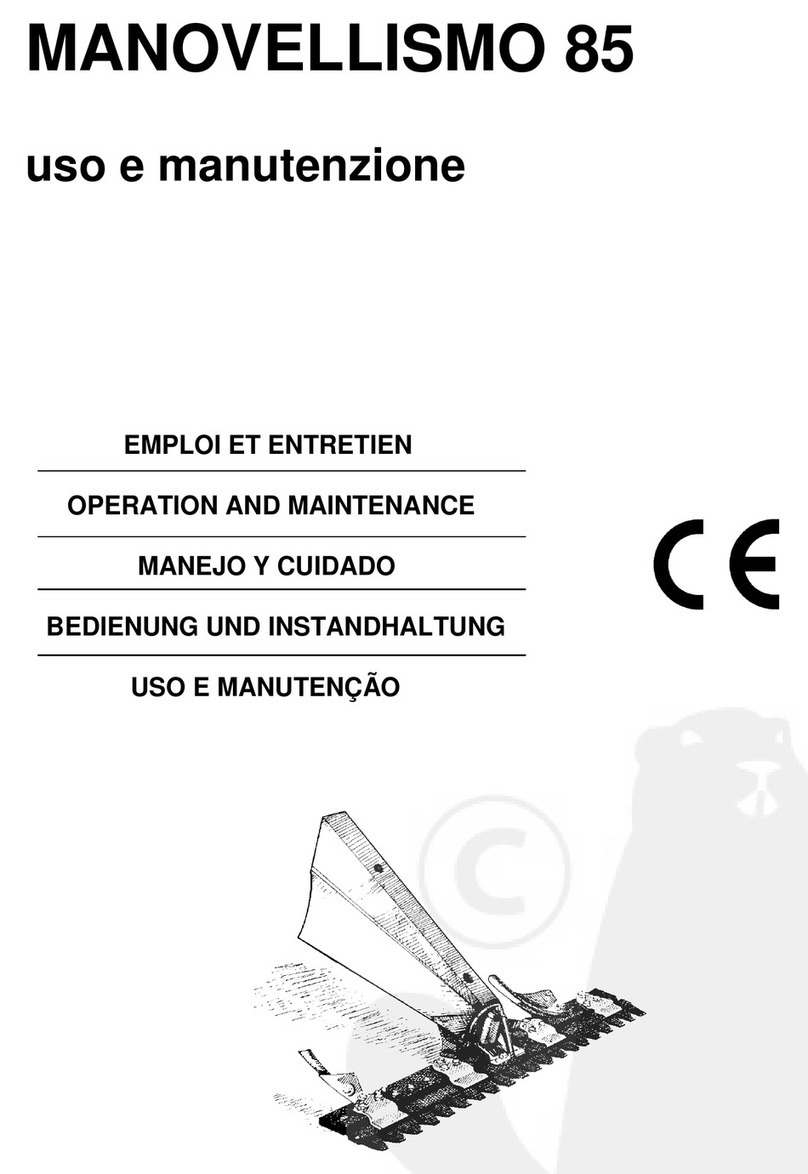
GOLDONI
GOLDONI 85 Operation and maintenance

Mitsubishi
Mitsubishi 1540 FD owner's manual
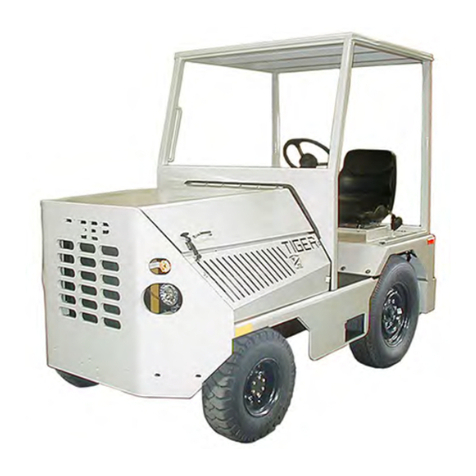
Taylor-Dunn
Taylor-Dunn TC-30 Operator's manual