Heathkit XO-1 Guide

Assembling
and Using Your...
Heathkit
ELECTRONIC
CROSSOVER
MODEL XO-1
595-130

STANDARD COLOR CODE —RESISTORS AND CAPACITORS
AXIAl LEAD RESISTOR
lr*wn —Insulated
Hack— Nan*ins«lated
Taltrnnce
Multiplier
ist and 2nd Significont Figures
Wire weund resisters have
1st digit band deuble width
INSULATED FIRST BING SECOND BING THIRD RING
UNINSUIATED BODY COLOR END COLOR DOT COLOR
Color First Figure Second Figure Multiplier
BIACK 00None
BROWN 110
RKD 2200
ORANGE 33,000
YELLOW 440,000
GREEN 5500,000
BLUE 66000,000
VIOLET 770,000,000
GRAY 8800,000,000
whut: 99000,000,000
DISC CERAMIC RMA CODE
S-Dot 3-Dot
Capacity
MultipKer ~
^Telerance
Temp. Ceeff.
RADIAL LEAD DOT RESISTOR
Multiplier
Ist Figure
’2nd Figure
5-DOT RADIAL LEAD CERAMIC CAPACITOR
-Capacity
Multiplier Tolerance
EXTENDED RANGE TC CERAMIC HICAP
Temp-Ceell. nvCopacity
TC Multiplier Multiplier t<«'^nce
RADIAL LEAD (BAND) RESISTOR
•Multiplier
i-2nd Figure
BY-PASS COUPLING CERAMIC CAPACITOR
Capacity
f-f
AXIAl LEAD CERAMIC lAPAaTOR
Temp. Ceeff. —i•—iCopecity
Multiplier Tolerance c..1)
Telerance
Tolerance 1st Figure
The standard color code provides all necessary information re-
quired to properly identify color coded resistors and capacitors.
Refer to the color code for numerical values and the zeroes or
multipliers assi^^ned to the colors used. Afourth color band on
resistors determines* tolerance rating as follows: Gold =5%,
silver =10%. Absence of the fourth band indicates a20%
tolerance rating. MOLDED MICA TYPE CAPACITORS
The physical size of carbon resistors is determined by their
wattage rating. Carbon resistors most commonly us(‘d in Heath-
kits are 3^ watt. Higher wattage rated resistors when specified
are progressively larger in physical size. Small wire wound
resistors }/2 watt, 1or 2 watt may be color coded but the fi^’s!
band will be double width. ^
White (RMA)
Hock (JAN)
CURRENT STANDARD CODE
2iid [
Figure
Class
-Multiplier
Telei
JAN C
1948
RMA
CODE
RMA 3-DOT (OBSOLETE)
RATED 500 W.V.D.C. ±20% TOL.
Multiplier
Figure
BUTTON SILVER MICA
CAPACITOR
class
Toleronce
Multiplier
3rd digit
RMA (5-DOT OBSOLETE CODE)
7n6 [
Figure Voltage
Multiplier
Front
-Working Voltage
sRear
—Telerance
Ist 2nd
Working
Voltage
Telerance
Multiplier
Significant Figure
—Multiplier
Toleronce
'flank
RMA 6-DOT (OBSOLETE)
‘1st
I
-2nd ^Significant Figures
-3rdj
Multiplier
Tderance
Working Voltage
RMA 4-DOT (OBSOLETE)
-Working Voltage
-Multiplier
h
I
Significant Figure
MOLDED PAPER TYPE CAPACITORS
TUBULAR CAPACITOR 1Significant Figure
Multiplier
-1st}
-2ndC
1
1
Telerance
Normolly
stomped for
value
Significont
Veltoge Figure
MOLDED FLAT CAPACITOR
Commercial Cede
Hack
ledy
JAN. CODE CAPACITOR
1st /Significant
A2digit voltage rating indicates mere than 900 V.
Add 2zeros to end of 2digit number.
The tolerance rating of capacitors is determined by the color
code. For example: red =2%. green =5%, etc. The voltage
rating of capacitors is obtained by multiplying the color value
by 100. For example: orange =3X100 or 300 volts. Blue =
6X100 or 600 volts.
IWerking Veits
Multiplier
I"
^I
Significont Figure
S2nd CFigure
-Multiplier
Tolerance
In the design of Heathkits, the temperature coefficient of ceramic
or mica capacitors is not giuierally acritical factor and there-
fore Heathkit manuals avoid reference to temperature coeffi-
cient specifications.
Courtosy of Centrolob

HEATHKIT ELECTRONIC CROSSOVER
MODEL XO-1
SPECIFICATIONS
Input: ITigh impedance.
Outputs: (1). Low-frequency.
(2)
.High-frequency.
(3)
.By-pass. (Input signal may be transferred
•to this output jack by means of switch pro-
vided. )
(Low and high-frequency outputs are low im-
pedance from cathode-followers.
)
Cutoff Frequencies: 100, 200, 400, 700, 1200, 2000 and 3500 cycles.
The high and the low-frequency channels can be
individually adjusted to any of these frequencies
by means of two rotary switches.
Total Hum and Noise, Each Channel: 70 db below« 1.5 volts out.
Tubes: Two 12AX7.
One 6X4 rectifier.
9*’ wide, 53/4” high, 43/4” deep.
105 -125 volts, 50-60 cycles AC. 5watts.
6lbs.
Dimensions:
Power Requirements:
Kit Shipping Weight: .

HEATHKIT ELECTRONIC CROSSOVER
MODEL XO-1
Page 2

Maximum Gain of Each Channel:
Normal Operating Level:
Maximum Recommended Operating Level: ..
Frequency Response:
Low-Frequency Channel:
High-Frequency Channel:
Unity.
2.0 volts rms or less.
5.0 volts rms.
±1.2 db from 10 cycles to cutoff frequency.
±1.2 db from cutoff frequency to 20,000 cycles.
FREQUENCY- C.P.S.
Figure 1
FREQUENCY- C.P.S.
Figure 2
Distortion: Distortion introduced bytheXO-1 is extremely low, and can be considered negligi-
ble. It was not possible to measure intermodulation distortion with laboratory equipment ordin-
arily available, owing to the frequency characteristics of the XO-1; distortion figures so obtained
would not be valid. For this reason, harmonic distortion tests were relied upon to furnish in-
formation as to linearity of the XO-1 circuits.
Page 3

Harmonic Distortion:
Low-Frequency Channel: Less than .1 of 1% at2 volts out at anyfrequency
up to approximately one-half the cutoff frequen-
cy. See curve (Figure 3) for further data on dis-
tortion vs. frequency.
High-Frequency Channel: Less than .25 of 1% when measured at the cut-
off frequency; drops rapidly at higher frequen-
cies, to less than .1 of 1% (see curve of Figure 4).
FREQUENCY
LOW FREQ. CHANNEL
HARMONIC DISTORTION VS. FREO.
Figure 3
100 FREQUENCY 1000
OB
HI. FREO. CHANNEL
HARMONIC DISTORTION VS. FREO.
Figure 4
NOTE: The proper interpretation of these harmonic distortion vs. frequency curves is com-
plicated by the fact that the response is far from flat. In other words, the relative levels of the
fundamental frequency and the total harmonic content are upset by the inherent sloping response
which is an essential characteristic of the XO-1. Thus, the harmonic content measured is not
atrue ’’percentage distortion” under the normal interpretation.
Nevertheless the curves indicate the relationship between harmonic content and the fundamen-
tal at various frequencies in the region of cutoff, which would hold under actual operating con-
ditions; it is NOT aTRUE measure of distortion introduced by non-linearity of the XO-1 itself.
Since the measurements were made by the method which shows ’’total harmonic content”, it is
difficult to accurately correct the curves in order to gain atrue distortion figure for the XO-1.
However, if this were done, it would be found that the distortion would not rise appreciably with
decreasing frequency as appears to be the case in Figure 4. In Figure 3the corrected distortion
figure would be somewhat higher at frequencies close to Fc and would tend to level off above Fc
instead of dropping. However, these corrected distortion figures are of little value anyway in
the case of Figure 3since harmonic products of frequencies approaching Fc are rapidly atten-
uated. From this it can be concluded that distortion introduced by the XO-1, at normal oper-
ating levels, can be considered negligible.
Page 4

NOTE; The performance specifications given are based on careful measurements made on a
typical unit, and kits constructed in exact accordance with the instructions can be expected to
conform to these specifications to areasonable degree. We cannot guarantee, however, that
measurements made on completed kits will be in exact agreement with the specifications, owing
to factors beyond our reasonable control. Such factors include placement of critical leads, nor-
mal variation of components and tube characteristics.
INTRODUCTION
It is generally appreciated that to satisfactorily reproduce the spectrum of audio frequencies
from approximately 30 cycles to 15,000 cycles requires arelatively large speaker or "woofer"
to reproduce the low frequencies, say from 30 to 1000 cycles and acomparitively small speaker
or "tweeter" to reproduce the higher range, in this example, from 1000 to 15,000 cycles. Such
asystem requires anelectrical dividing network or "crossover" to divide the total audio spect-
rum into the proper ranges, in order that only the high frequencies will be fed to the tweeter
and only the low frequencies to the woofer. (Many 2-way speakers built as an integral unit with
separate cones for the high and the low frequencies have abuilt-in or "mechanical" crossover
and are not considered here. Best results and greatest flexibility are generally achieved by the
use of aseparate woofer and tweeter and an electrical, rather than amechanical crossover.
Figure 5shows, in block diagram form, the connection of aconventional electrical crossover
unit of the type which has come into general use. Note that the crossover unit is connected be-
tween the output of the power amplifier and the speakers.
TO PROGRAM
SOURCE
;
(TUNER, PREAMPLIFIER.
ETC. )
TWEETER
WOOFER
Figure 5
The Heathkit XO-1 Electronic Crossover is designed to operate in conjunction with atwo-way
speaker system where separate power amplifiers are used for the high and the low frequencies
as shown in the block diagram of Figure 6. This has several important advantages over the
conventional method of Figure 5.
Figure 6
(1) Since the crossover unit operates at the input of the power amplifiers rather than at the out-
put, no output power is dissipated and therefore wasted in the crossover unit itself. In con-
trast, it is to be noted that aconventional type crossover with an insertion loss of only 1
db would reduce the power capability of a20 watt amplifier to 16 watts and a50 watt ampli-
fier to 40 watts.
Page 5

(2) In an electronic crossover device, it is practical to vary the crossover frequency over a
wide range to accommodate almost countless woofer-tweeter combinations and acoustic en-
vironments. Changing speakers in your hi-fi system will not obsolete the XO-1. Also,
there are no complex impedance matching problems in assembling your own speaker cross-
over system.
(3) It is possible to achieve anear ideal crossover characteristic by means of electronic cir-
cuitry, without significant peaks or valleys in the overall response. Also, the response and
crossover characteristics are unaffected by differences in speakers and enclosures.
(4) Amplifier damping factor is not altered by the crossover device.
(5) The possibility of intermodulation distortion (modulation of the high frequencies by high-
amplitude low frequencies) in the amplifiers is reduced, particularly at high power levels.
(6) No reactive-load conditions, sometimes caused by conventional crossover units, are im-
posed on the power amplifier. Such load conditions can result in instability (oscillation)
in amplifiers with heavy feedback.
It should be noted that while the above discussion is confined to two-way speaker systems, the
XO-1 may be used to good advantage in three or four- way systems. Anumber of suggested
arrangements are given in the section entitled ’’Installation and Operation”.
CIRCUIT DESCRIPTION
The circuitry of the XO-1 is quite simple and straightforward. Refer to the Schematic. It con-
sists basically of ahigh-frequency channel and alow-frequency channel. A12AX7 dual triode is
used in each channel. A6X4 rectifier tube is used in aconventional full wave power supply with
atwo-section RC filter.
The high-frequency channel is actually ahigh- pass filter; it passes only those frequencies above
the cutoff frequency, as shown in the curves of Figure 1. It will be noted that the cutoff fre-
quency may be adjusted to 100, 200, 400, 700, 1200, 2000 or 3500 cycles by means of arotary
switch. Similarly, the low-frequency channel is alow-pass filter which will pass only frequen-
cies below the cutoff frequency, as shown in Figure 2. The cutoff frequency of this channel is
adjustable over the same range by means of another switch. The input signal is applied through
the high and low-frequency LEVEL controls, through suitable isolating resistors to the input of
both channels. The 12AX7 dual triode in each channel is utilized so that one section functions
as again stage and the other as an output cathode follower. Each channel employs two RC net-
works in order to achieve acutoff slope of 12 db per octave since each network contributes 6db
per octave. In each channel the 12AX7 gain stage serves to separate the two RC networks. Ap-
proximately 14 db negative feedback is applied around each channel from the cathode-follower
output back to the grid of the gain stage. The function of this negative feedback is three-fold:
(1) It modifies the shape of the response curves in the region near the cutoff frequency, so that
amuch sharper ’’knee” is imparted to the curve than if feedback were not used. This makes it
possible to maintain essentially flat response up to and including the cutoff frequency, with as
much as 12 db attenuation at twice and one-half this frequency for the low and high-frequency
channel, respectively. (2) Any harmonic distortion developed is reduced by feedback, at fre-
quencies within the passband of either channel. (3) The amount of feedback used reduces the
overall gain to unity since gain is not required in the unit.
The cutoff frequency is varied by switching different values of capacity in both RC networks of
each channel. Although this could be accomplished by switching resistors instead, the level in
the ’’flat” region would vary appreciably with the cutoff frequency due to the finite values of resis-
tance already in the circuit. Aunique method of switching capacitors has been devised whereby
each capacitor (with exceptions) serves for two successive cutoff frequencies. This greatly re-
duces the number of components required and is made possible by ’’staggering” the turnover
frequencies of the two RC networks in each channel.
Page 6

NOTES ON ASSEMBLY AND WIRING
Agreat deal of enginnering has gone into the design of your Heathkit Electronic Crossover to
ensure highest performance and the components have been carefully selected for quality and
long life. We urge you to proceed with the utmost care in construction, follow the instructions
exactly and perform each step in the most workmanlike manner possible. By so doing you will
protect your investment in time and money and be rewarded with the fine performance of which
your Electronic Crossover is capable as well as the deep feeling of satisfaction that comes from
ajob well done.
This manual is supplied to assist you in everyway to complete the instrument with the least pos-
sible chance for error. The detailed instructions are specifically written to allow either the
experienced or inexperienced constructor to construct the unit with aminimum of difficulty.
Only avery small percentage of Heathkit assemblers encounter any difficulty whatsoever in com-
pleting kits of this kind. The large fold-in pictorial diagrams included in this manual are in-
tended to be attached to the wall above your work space, for convenient reference. The dia-
grams are repeated in smaller form within the manual proper.
UNPACK THE KIT CAREFULLY AND CHECK EACH PART AGAINST THE PARTS LIST. DO
NOT DISCARD ANY PACKING MATERIAL UNTIL THIS HAS BEEN DONE. In so doing you will
become acquainted with each part. Full size sketches of the various type parts will be found on
Page 28 to help you identify any questionable components. If aparts shortage is found, please
notify us promptly and return the inspection slip to us with your letter. Hardware items are
counted by weight and if afew are missing, we suggest that to save time, you obtain them locally
if at all possible.
Resistors and controls generally have atolerance rating of ±20% unless otherwise stated in the
parts list. Thus a100 KQ resistor may test anywhere from 80 KQ to 120 KQ and still be ac-
ceptable. Tolerances on electrolytic condensers may be even wider and commonly run from
±100% to -50%. The parts furnished with your Heathkit have been specified so as to meet the
performance specifications given. Refer to the color code information given on the inside front
cover of this manual when in doubt as to the value or tolerance of aresistor or capacitor.
In order to expedite delivery to you, we are occasionally forced to make minor substitutions of
parts. Such substitutions are very carefully checked before they are approved and the parts sup-
plied will work satisfactorily in your kit. For example, if your kit is short a15 K12 resistor
and an 18 K^2 resistor is furnished which is not on the parts list, you will understand that such
asubstitution has been made. This fact is mentioned here only to prevent any confusion in check-
ing the contents of your kit.
CAUTION* We strongly urge that you follow exactly the wiring and parts layout shown in this
manual. The position of certain leads and components in this instrument is quite critical and
changes may seriously affect the characteristics of the circuit.
STEP-BY-STEP ASSEMBLY INSTRUCTIONS
First attach the large fold- in pictorials to the wall above your work space. Then we suggest
that you carefully read through the entire assembly and wiring instructions. This will famili-
arize you with the construction procedure and will tend to prevent errors before they occur.
WE URGE YOU TO FOLLOW THE STEP-BY-STEP INSTRUCTIONS IN THE EXACT ORDER
GIVEN. Read through each step carefully then perform the operation indicated. Place acheck
mark in the space provided ( ) as each step is completed.
In assembling the kit, use lockwashers under all nuts unless otherwise specified. Tube sockets
are mounted inside the chassis; the filter condenser mounting wafer is mounted on top of the
chassis. Other details of construction are included where pertinent in the instructions.
Page 7

Page 8
PICTORIAL
1

(^) Place the chassis with its open side up in front of you on your workbench. Be sure the front
apron (with the lettering on the outside) is away from you. The chassis will then be in the
position shown in Pictorial 1.
(^)Install aphono connector socket at location AA. Be sure lug 2is away from the end of the
chassis. Mount with two 6-32 screws through the chassis and the holes in the socket.
Place a#6 lockwasher directly under each nut.
(i)In the same manner, install aphono connector socket at location AB. As before, be sure
lug 2is away from the end of the chassis.
(^) Likewise, install the two remaining phono connector sockets at AC and AD, observing lug
orientation as before.
(^)
(J)
(*)
(V)
(>/)
(>)
(>)
(')
Mount the four spring catch clips at Bl, B2, B3 and B4. Secure each clip on the under side
of the chassis, with two 4-40 pan head screws inserted from the top of the chassis. Use a
#4 lockwasher under each nut.
Install the fiber mounting wafer for the electrolytic filter condenser at C. IMPORTANT:
Make sure this wafer is installed with the triangular hole positioned as shown in Pictorial
1. Secure with 6-32 hardware.
Mount a9-pin wafer tube socket at D. Be sure to observe lug orientation shown with the
blank space (between lugs 1and 9) to the right away from the end of the chassis. See Fig-
ure 7. Secure socket with two 3-48 s
3-48 hardware.
Mount a9-pin wafer tube socket at E
observing the same lug orientation as
before.
Install the 7-pin wafer tube socket at
Fwith the blank space (between lugs
1and 7) to the right toward this end
of the chassis.
Mount a2-lug terminal strip at Gob-
serving orientation shown in Pictorial
1. Use 6-32 hardware.
In the same manner, mount a3-lug terminal strip at H. Be sure terminal 1is nearest the
rear chassis apron.
Install a2-lug terminal strip at J.
Mount a1-lug terminal strip at K.
screws and nuts. Lockwashers are not required with
9-PIN
SOCKET
Figure 7
NOTE: The 2-lug terminal strip at Lwill be mounted later.
(J )Install a100 control at M. Orient so that the lugs are toward the open side of the chas-
sis. Refer to Figure 8for control mounting details. Use a3/8” lockwasher between the
control and the chassis. Place acontrol washer under the 3/8”-32 nut used to secure the
control.
(4)In the same manner install a100 K^2 control at R.
()Using 6-32 hardware, mount the S. P. D. T. slide switch at Pwith the switch handle protrud-
ing through the rectangular opening in the front chassis apron. Observe orientation shown
with the three lugs away from the open side of the chassis. Page 9

(^) Install a1/2” rubber grommet at T.
(i )Install a3/8” rubber grommet at U.
(\|) Install the power transformer on top of the
chassis, by first pulling its seven leads
through rul?ber grommet Tall the way. Make
sure no part of any lead remains coiled be-
tween the bottom of the transformer and the
top of the chassis, which could result in a
short circuit of serious consequences. Se-
cure the transformer to the chassis by means
of 8-32 hardware.
)Install the electrolytic filter condenser on it,
at C. Insert this condenser from the top of the chassis with the three metal tabs protruding
through the three slots in the wafer. IMPORTANT: Be sure to orient the condenser as
shown in Pictorial 1. Note that two of these metal tabs have holes through them, while one
does not. The tab with no hole goes toward the upper left-hand corner of the chassis, when
viewed as in Pictorial 1. With the condenser in this position and tight against the wafer,
twist each of the mounting tabs 1/8 turn with apair of pliers.
This completes preliminary assembly of parts on the chassis with the exception of the two ro-
tary switches and terminal strip L, which will be mounted later. At this point we suggest that
you carefully compare your work with Pictorial 1and correct any errors in parts mounting be-
fore proceeding with the wiring. Any mistakes at this point are much more difficult to correct
after wiring has been started.
PROPER SOLDERING PROCEDURE
Only asmall percentage of Heathkit purchasers find it necessary to return an instrument for
factory service. Of these, by far the largest proportion function improperly due to poor or
improper soldering.
Correct soldering technique is extremely important. Good solder joints are essential if the
performance engineered into the kit is to be fully realized. If you are abeginner with no ex-
perience in soldering, ahalf-hour’s practice with odd lengths of wire and atube socket will be
aworthwhile investment.
High quality solder of the proper grade is most important. There are several different brands
of solder on the market, each clearly marked ’’Rosin Core Radio Solder.” Such solders consist
of an alloy of tin and lead, usually in the proportion of 50:50. Minor variations exist in the mix-
ture such as 40:60, 45:55, etc. with the first figure indicating the tin content. Radio solders are
formed with one or more tubular holes through the center. These holes are filled with arosin
compound which acts as aflux or cleaning agent during the soldering operation.
NO SEPARATE FLUX OR PASTE OF ANY KIND SHOULD BE USED. We specifically caution
against the use of so-called ’’non-corrosive” pastes. Such compounds, although not corrosive
at room temperatures, will form residues when heated. The residue is deposited on surround-
ing surfaces and attracts moisture. The resulting compound is not only corrosive but actually
destroys the insulation value of non-conductors. Dust and dirt will tend to accumulate on these
’’bridges” and eventually will create erratic or degraded performance of the instrument.
NOTE: ALL GUARANTEES ARE VOIDED AND WE WILL NOT REPAIR OR SERVICE
INSTRUMENTS IN WHICH ACID CORE SOLDER OR PASTE FLUXES HAVE BEEN
USED. WHEN IN DOUBT ABOUT SOLDER, IT IS RECOMMENDED THAT ANEW
ROLL PLAINLY MARKED ’’ROSIN CORE RADIO SOLDER” BE PURCHASED.
smounting wafer which was previously mounted
Page 10

If terminals are bright and clean and wires free of wax, frayed insulation and other foreign sub-
stances, no difficulty will be experienced in soldering. Crimp or otherwise secure the wire (or
wires) to the terminal, so agood joint is made without relying on solder for physical strength.
To make agood solder joint, the clean tip of the soldering iron should be placed against the joint
to be soldered so that the terminal is heated sufficiently to melt solder. The solder is then
placed against both the terminal and the tip of the iron and will immediately flow out over the
joint. Refer to the sketch below. Use only enough solder to cover wires at the junction; it is
not necessary to fill the entire hole in the terminal with solder. Excess solder may flow into
tube socket contacts, ruining the socket, or it may creep into switch contacts and destroy their
spring action. Position the work so that gravity tends to keep the solder where you want it.
Apoor solder joint will usually be indicated by its appearance.
The solder will stand up in ablob on top of the connection,
with no evidence of flowing out caused by actual "wetting" of
the contact. Acrystalline or grainy texture on the solder
surface, caused by movement of the joint before it solidified
is another evidence of a"cold" connection. In either event,
reheat the joint until the solder flows smoothly over the en-
tire junction, cooling to asmooth, bright appearance. Photo-
graphs in the adjoining picture clearly indicate these two
characteristics.
Agood, clean well-tinned soldering iron is also important to obtain consistently perfect con-
nectionL For most wiring, a60 or 100 watt iron, or the equivalent in asoldering gun, is very
satisfactory. Smaller irons generally will not heat the connections enough to flow the solder
smoothly over the joint and are recommended only for light work, such as on etched circuit
boards, tec. Keep the iron tip clean and bright. Apad of steel wool may be used to wipe the
tip occasionally during use.
Take these precautions and use reasonable care during assembly of the kit. This will insure the
wonderful satisfaction of having the instrument operate perfectly the first time it is turned on.
Page 11

STEP-BY-STEP WIRING INSTRUCTIONS
Pictorial 2represents a wired XO-1 crossover unit (complete except for parts to be installed
later, as indicated in Pictorial 3. )We again suggest that you attach the large fold-in versions
of these pictorials to the wall above your work space for aready reference during wiring.
/
Note that the letter designations of parts in Pictorial 1have been retained in Pictorial 2and that
the terminals on each component are numbered.
When the instructions read, ’’Connect one end of a.l capacitor to D3 (NS). ”,it will be under-
stood that the connection is to be made to pin 3of tube socket D. The abbreviation (NS) indicates
that the connection should not be soldered as yet as other leads will be added to the same termi-
nal later. When the last wire is connected, the terminal should be soldered and the abbrevia-
tion (S) is used to indicate this.
Unless otherwise indicated, all wire used is insulated. Whenever there is apossibility of the
bare leads on resistors and condensers shorting to other parts or to the chassis, the leads
should be covered with insulated sleeving. This is indicated in the instructions by the phrase
(use sleeving). Bare wire is used where the lead lengths are short and the possibility of short
circuits non-existent. Use small diameter bare wire except where otherwise specified.
If awire-stripping tool is not at hand, we suggest the following method of stripping insulation
from the end of hook-up wire: Crush about 1/4” of insulation at the end of the wire by squeez-
ing with longnose pliers. The wire should be placed as far back in the jaws as possible for
maximum leverage. The insulation thus broken away may then be trimmed off close with di-
agonal cutters.
Leads on capacitors, resistors, and transformers are generally much longer than they need to
be to make the indicated connections. In these cases, the excess leads should be cut off
before the part is added to the chassis. In general, the leads should be just long enough to
reach their terminating points. Not only does this make the wiring much neater but in many
cases excessively long leads will actually impair the operation of the instrument.
The pictorials indicate actual chassis wiring, designate values of the component parts and show
color coding of leads where pertinent. We very strongly urge that the chassis layout, lead place-
ment and grounding connections be followed exactly as shown. While the arrangement shown is
probably not the only satisfactory layout, it is the result of considerable experimentation and
trial. If followed carefully it will result in astable instrument operating at ahigh degree of
dependability.
(')Twist together the two green leads coming from grommet T. Connect the longer of these
two leads to F3 (NS) and the shorter lead to F4 (NS).
(v/) Twist together the two red leads coming from the same grommet,
lead to Fl (S) and the shorter red lead to F6 (S).
Connect the longer red
(r )Connect the red and yellow striped wire coming from the same grommet to C2 (S) (twisted
mounting tab of the electrolytic capacitor). Run this wire between terminal strip Kand
the front apron of the chassis.
(/) Connect a47 resistor (yellow-violet-black) between F3 (NS) and J2 (NS).
(^Connect another 47 Qresistor between F4 (NS) and J2 (NS).
(J)Cut awire to alength of 51/4”. Strip approximately 1/4” of insulation from each end and
connect one end to F3 (S). Leave the other end free temporarily.
(i) Cut another length of wire 41/2" long. Strip both ends as before and connect one end to
F4 (S).
Page 12

Page 13
PICTORIAL
2

(V )Run this wire under the two 47 Qresistors and twist it together with the wire coming from
F3. Twist up to 11/4” from the end of the shorter wire. Connect the shorter wire to E9
(NS). Dress the twisted pair of wires snugly along the bend at the rear of the chassis.
Leave the longer wire unconnected for now.
(\l) Cut awire to alength of 6” and after stripping both ends connect one end to E9 (S). Run this
wire toward the rear of the chassis along beside the wire previously connected to E9. At
the rear bend of the chassis twist this wire with the unconnected wire coming from the twisted
pair previously installed. Twist for alength of 1”, then connect the shorter wire to E4 (NS).
(J) Cut awire 51/4” long and strip 1/2” of insulation from both ends. Pass one end through
E4 and connect to E5 (S). Now solder E4. Run this wire toward the rear of the chassis
along with the other wire connected to E4. At the rear bend of the chassis run this wire to
the left and twist with the wire coming from the pair previously twisted. Twist for alength
of 21/4”.
(J
)
Connect the shorter end to D9 (S).
(J )Pass the longer end through D4 and connect to D5 (S). Now solder D4. Dress these twisted
wires snugly in the rear bend of the chassis. Be sure all of these wires clear the unused
socket terminals.
(J) Prepare an 8” length of wire and connect one end to F7 (S). Connect the other end to the
terminal marked aon the electrolytic capacitor C(NS). Route this wire as shown in Pic-
torial 2.
(J)Run a3” length of wire between J2 (NS) and C3 (NS).
(-I) Run a31/2” length of wire between C3 (NS) and H2 (NS).
(j) Connect a31/2” length of wire between H2 (NS) and G2 (NS).
(>1) Dress the three preceeding wires close to chassis.
(Bend the ground lug 2of phono connector socket AA down against the front apron of the
chassis.
('i )Do the same on socket AB.
(J)Prepare awire 51/2” long and connect one end to AAl (S). Run this wire over the mount-
ing bushing of control Mand connect the other end to P2 (S). Dress this wire close to the
front chassis apron. Be sure this wire is at least 1/4” above hole N(viewed in the wiring
position) so it will not interfere with the installation of the switch that mounts in this hole.
(>|) In asimilar manner, prepare awire 51/4” long and connect one end to ABl (S). Run this
wire over the mounting bushing of control Rand connect the other end to P3 (S). Be sure
the wire clears hole Q.
(J)Connect a21/4” length of wire between G2 (NS) and Ml (NS). Dress this wire close to the
rear c'^ver of the control.
(4) Connect ashort bare wire between Ml (S) and AD2 (NS).
(i)Run a23/4” length of wire between M3 (S) and PI (NS).
(^ )Connect one end of a51/2” length of wire to Cb (NS). Run this wire between socket Eand
terminal strip Haround to El (NS). Dress close to chassis.
Page 14

('^) Connect a43/4” length of wire between El (NS) and Dl (NS).
(v/) Connect one end of an 8” length of wire to K1 (NS). Run this wire between terminal strip J
and socket Fand connect to E3 (NS). Dress this wire close to chassis.
(V) Connect a1500 Qresistor (brown-green-red) between J2 (NS) and E8 (NS).
Connect a10 jif tubular electrolytic capacitor between C3 (NS) and E8 (S). IMPORTANT:
Be sure the positive (+) end of this capacitor connects to E8. Before soldering, rotate this
capacitor so that the positive lead goes straight to E8 and avoids E7.
(^) Connect a100 K5% resistor (brown-black-yellow-gold) between C3 (S) and E7 (NS). Let
the resistor rest lightly against the 10 iif electrolytic capacitor.
(v) Connect another 10 ^f tubular electrolytic capacitor between G2 (NS) and D8 (NS). Observe
polarity as before with the positive (+) lead going to D8.
(Connect a1500 ^2 resistor (brown-gre }n-red) between G2 (NS) and D8 (S).
(^) Connect a100 K5% resistor (brown-black- yellow-gold) between G1 (NS) and D7 (NS).
(/) Install a10 K5% resistor (brown-black-orange-gold) between G2 (S) and G1 (NS).
(Connect a150 K5% resistor (brown-green-yellow-gold) between G1 (NS) and ADl (NS).
(/) Connect a100 K5% resistor (brown-black-yellow-gold) between G1 (S) and M2 (S) (use
sleeving on the end going to M2).
(/) Install a4700 resistor (yellow-violet-red) between Ca (S) and Cb (S). Note the position
of this resistor in the pictorial.
(V) Install a100 K5% resistor (brown-black-yellow-gold) between Dl (S) and D6 (NS).
(y)Install a100 K5% resistor between El (S) and E6 (NS).
(>/) Slip a13/8” length of insulated sleeving on each lead of a.1 fif capacitor and connect the
capacitor between ADl (S) and D3 (NS). Dress this capacitor close to the chassis end plate.
(/) a.01 /if A04'"<-8) .Note: Do not use capacitor marked
’"5%” here.
(y) Connect a11/2” length of wire from AC2 (S) to Rl (NS).
)Install a47 Kresistor (yellow-violet-orange) from Jl (NS) to J2 (S).
(w)Install another 47 Kresistor from Hi (NS) to H2 (S).
(J) Install a.1 /if capacitor between H3 (NS) and D2 (NS). Position this capacitor as shown in
the pictorial and cover the lead going to D2 with a1” length of insulated sleeving.
(J) Connect a1megohm 5% resistor (brown-black-green-gold) between H3 (S) and D6 (S). Use
a3/4” length of sleeving on the lead to D6 and position as shown.
(>/) Connect a1megohm 5% resistor (brown-black-green-gold) between Hi (NS) and D2 (NS)
(use sleeving on the lead to D2).
(J) Install a1Kresistor (brown-black-red) between Hi (S) and D3 (S) (use 1/2” of sleeving on
the lead to D3).
(4 )Connect a22 Kresistor from Jl (NS) to E2 (NS) (use 3/8” of sleeving on the lead to E2).
Page 15

(^ )Connect a1Kresistor (brown-black-red) between Jl (S) and E3 (S) (use 1/2” of sleeving on
the lead to E3.
(•^ )Now mount a2-lug terminal strip at L. Use 6-32 hardware.
(/) Twist together the two black leads coming from rubber grommet T. Connect the shorter
black lead to L2 (NS) and the longer one to Ll (NS). Dress these twisted leads as near as
possible to the chassis end plate.
(/) Bring the end of the line cord in through rubber grommet U. Tie aknot in the line cord in-
side the chassis for strain relief. Leave about 1” between the knot and the end of the cord.
Connect one line cord wire to L2 (S) and the other to Ll (S).
Lay the chassis aside temporarily.
WIRING OF THE ROTARY-SELECTOR SWITCHES
You are now ready to mount the capacitors on the two rotary-selector switches, after which
these switches will be mounted on the chassis. Only two of these capacitors are of the molded-
paper type (the .04 juf and the .01 4!). The rest are of the molded-mica type; the values may
be printed directly on these capacitors or may be in the form of color code, depending on the
manufacturer. Values printed on may be in micro-farads (^f) whereas the values referred to
in the step-by-step instructions are in micro-micro-farads, for the molded-mica capacitors.
To convert from (if to 4/if, move the decimal point six places to the right. Thus, acapacitor
marked .00U39 4!is the same value as one marked 390 44!. If the mica capacitors in your kit are
color-coded, refer to Figure 9, which shows the coding system currently in use. In the follow-
ing step-by-step instructions, the colors given for aparticular capacitor are given in this order;
1st significant figure, 2nd significant figure, multiplier.
(^)
1ST SIGNIFICANT FIGURE
2no significant figure
MULTIPLIER
TOLERANCE
Identify the low-frequency cutoff selector switch which has nine con- fog
tact lugs on the front deck and ten lugs on the rear deck. This I®?^
switch is shown in Figure 10 with the capacitors installed. Each lug |
on the front deck, as well as each lug on the rear deck, has been
assigned an identifying number. Carefully compare the switch with Figure 9
Figure 10 so that you will have no difficulty in identifying any of the
lugs. Remember that any mistakes made in wiring the capacitors to the switch will be quite
difficult to correct after the connections have been soldered. The capacitors in the Figure
are shown widely separated for clarity. On the actual switch, all leads should be perfectly
straight and no longer than necessary to make the connections. Otherwise, it may be dif-
ficult to place the completed switch in the chassis. The capacitors should be positioned as
shown in Figure 11 like the spokes of awheel. In addition, they should be approximately
centered between the front and rear switch decks.
Figure 11
Page 16

(Connect a47 ju/if mica capacitor (yellow -violet-black) between lug 2(S) on the front deck
and lug 3(S) on the rear deck.
( ) Connect a180 ii(ii mica capacitor (brown-gray-brown) between lug 3(S) on the front deck
and lug 4(S) on the rear deck.
('' )Connect a1000 {ijif mica capacitor (brown-black-red) between lug 4(S) on the front deck
and lug 5(S) on the rear deck.
(v) Connect a500 ii^if mica capacitor (green-black-brown) between lug 5(S) on the front deck
and lug 6(S) on the rear deck.
(Connect a3000 iifif mica capacitor (orange-black-red) between lug 6(S) on the front deck
and lug 7(S) on the rear deck.
(Connect a2000 ujuf mica capacitor (red-black-red) between lug 7(S) on the front deck and
lug 8(S) on the rear deck.
(Connect a.01 /xf ^molded tubular paper capacitor between lug 8(S) on the front deck and
lug 9(S) on the rear deck.
('/) Connect a.04 jitf ^molded paper tubular capacitor between lug 9(S) on the front deck and
lug 10 (S) on the rear deck.
()Connect one end of a21/2” length of wire to lug 1(S) on the front deck. Leave the other
end free.
()Connect one end of a13/4” length of wire to lug 1(S) on the rear deck.
()Connect one end of a21/2” length of wire to lug 2(S) on the rear deck.
Lay this switch aside temporarily.
The high-frequency cutoff switch will now be prepared in the same manner. This switch is
shown in Figure 12.
(v/) Connect a43 p,af mica capacitor (yellow-
orange-black) between lug 1(NS) on the front
deck and lug 1(S) on the rear deck.
( ) Connect a220 /i /if mica capacitor (red-red-
brown) between lug 2(S) on the front deck
and lug 3(NS) on the rear deck.
( ) Connect a330 fifif mica capacitor (orange-
orange-brown) between lug 4(S) on the front
deck and lug 4(NS) on the rear deck.
(\l
)
Connect a120 /i/xf mica capacitor (brown-
red-brown) between lug 5(NS) on the front
deck and lug 5(S) on the rear deck.
(J) Connect a910 /x/xf mica capacitor (white-
brown-brown) between lug 6(S) on the front
deck and lug 6(NS) on the rear deck.
(J) Connect a390 /x/xf mica capacitor (orange-white-brown) between lug 7(NS) on the front deck
and lug 7(S) on the rear deck.
Page 17

(Connect a4000 4/if mica capacitor (yellow-black- red) between lug 8(S) on the front deck and
lug 8(NS) on the rear deck.
(v/) Connect a1300 /i/if mica capacitor (brown-orange-red) between lug9 (NS) on the frontdeck
and lug 9(S) on the rear deck.
(V) Connect a27 /luf mica capacitor (red-violet-black) between lug 10 (NS) on the front deck
and lug 10 (S) on the rear deck.
('^) On the front deck connect lugs 5, 7, 9, 10 and 1together with asingle length of bare wire.
(These are the five dummy lugs on the front side of this deck or the side toward the threaded
mounting bushing). Solder the bare wire at lugs 5, 7, 9and 10. Use a5/16” length of sleev-
ing on the wire between lugs 10 and 1.
(.)Connect one end of a33/8” length of wire to lug 1(S) on the front deck. Leave the other
end free.
(J )Connect lugs 3, 4, 6and 8on the rear deck together with alength of bare wire. (These are
the four dummy lugs on the rear side of this deck). Leave 11/4” of bare wire protruding
from lug 8.Use sleeving on the wire between lugs 4and 6.Solder the connections on these
four lugs.
(\/) Connect one end of a21/2” length of wire to lug 2(S) on the rear deck. Leave the other
end free.
This completes the installation of capacitors on the switches and they are ready to be mounted
on the chassis.
(y) Install the low-frequency cutoff switch in chassis hole Nof Pictorial 1. Use a3/8” lock-
washer inside the chassis and acontrol washer under the nut as shown in Figure 8.
IMPORTANT: Before tightening the nut, orient the switch as shown in Pictorial 3. The
two switch posts should lie horizontally. Note that lugs 1and 10 are to the left. Refer to
Pictorial 3in making the following connections.
(/f Connect the wire coming from lug 1on the front deck to AD2 (S). Run this wire between
control Mand the front chassis apron and dress close to apron.
(1/) Connect the wire from lug 1on the rear deck to D7 (S).
(v/) Connect the wire from lug 2on the rear deck to D2 (S).
(y/j Install the high-frequency cutoff switch in hole Q, using a3/8” lockwasher, control washer
and nut as before. The switch posts should lie horizontally and lugs 1and 10 should be to
the left.
(^) Connect the wire coming from lug 1on the front deck to E6(S). Dress this wire as shown,
(/) Connect the wire from lug 2on the rear deck to E2 (S).
(n/) Slip a1” length of sleeving on the bare wire coming from lug 8on the rear deck and connect
to E7 (S).
(
I/O '
^9-
(blue--grayTyollow-gold) between lug 3on the frontdeck (NS) and
(use sleeving on the lead to switch lug 8).
(\J) Connect a100 K5% resistor (brown-black-yellow-gold) from lug 3on the frontdeck (NS) to
R1 (S).
Page 18
Other manuals for XO-1
1
Other Heathkit Crossover manuals
Popular Crossover manuals by other brands
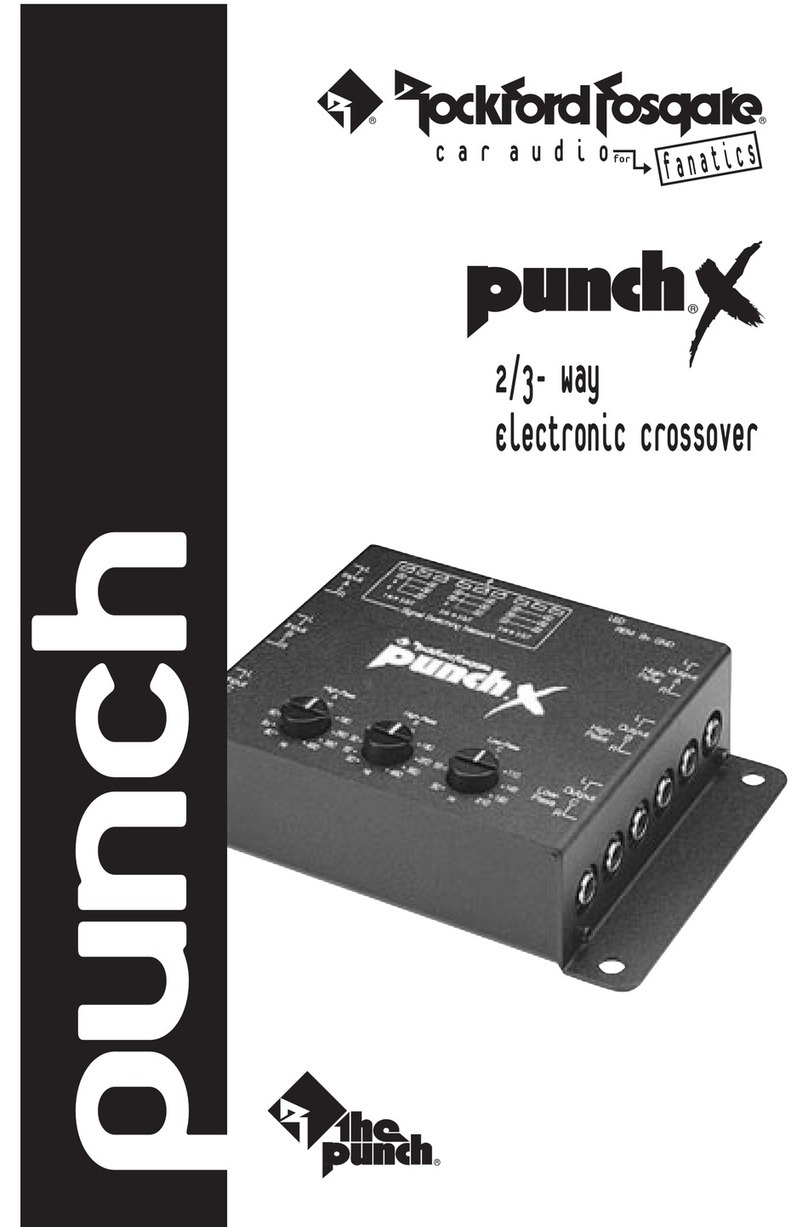
Rockford Fosgate
Rockford Fosgate PunchX user manual
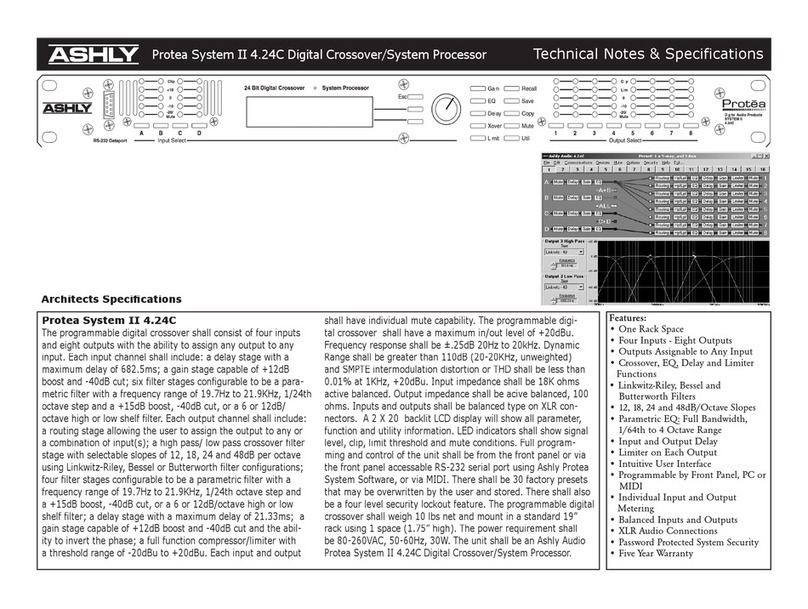
Ashly
Ashly PROTEA SYSTEM II 4.24C Technical notes & specifications

Monacor
Monacor MCX-200/SW instruction manual
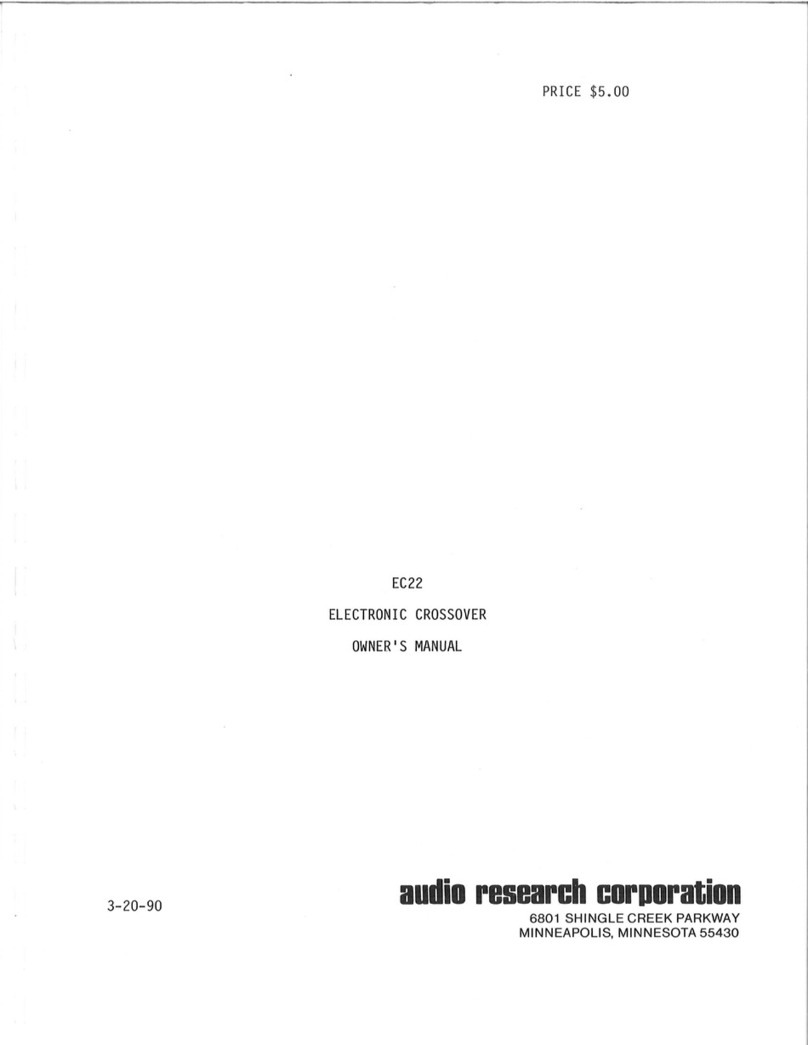
Audio Research
Audio Research EC22 owner's manual

PowerAcoustik
PowerAcoustik C-3184 owner's manual
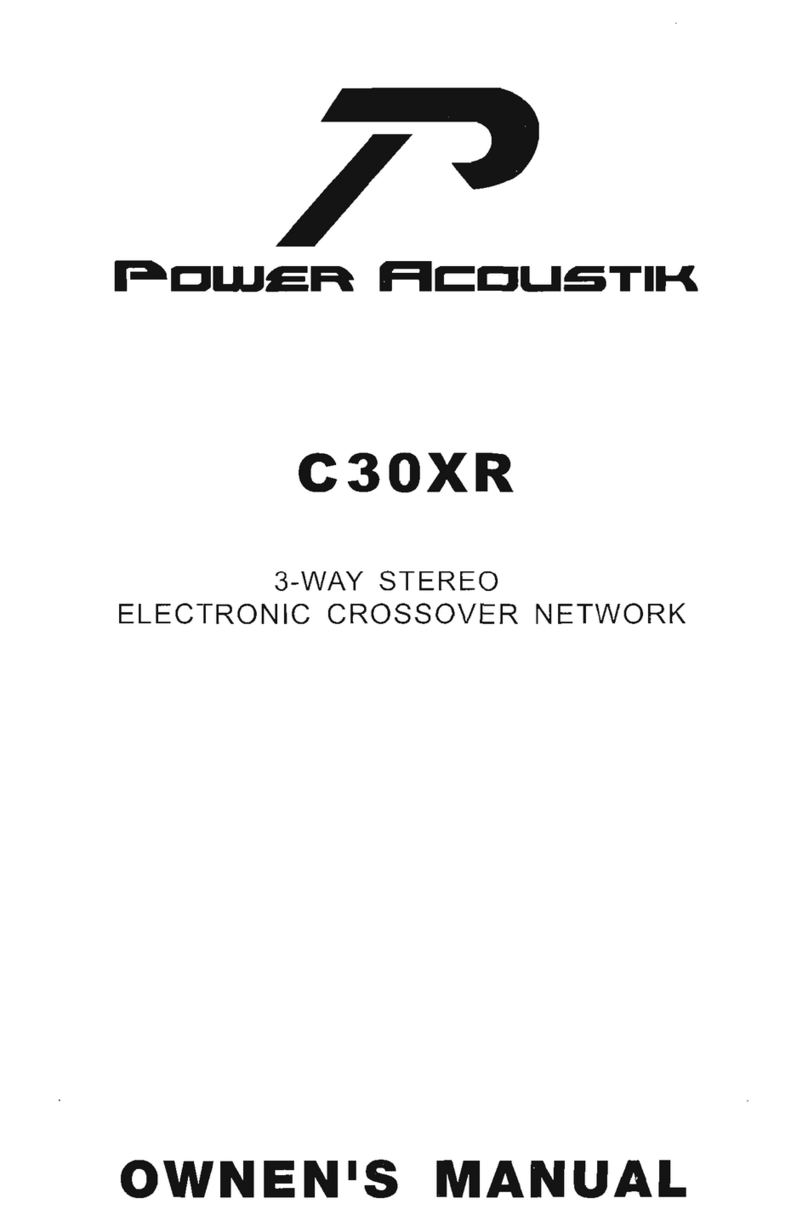
PowerAcoustik
PowerAcoustik C30XR owner's manual