HYT TC-618 User manual


TC-618/626 Service Manual
1
Contents
Introduction ..........................................................................................................................................2
Safety Information ................................................................................................................................3
Radio Overview ....................................................................................................................................4
Software Specifications .......................................................................................................................7
Circuit Description ............................................................................................................................. 11
CPU Pins ............................................................................................................................................. 19
TC-618/626 Parts List 1 ......................................................................................................................22
Adjustment Description ..................................................................................................................... 71
Troubleshooting Flow Chart ..............................................................................................................83
Disassembly and Assembly for Repair ............................................................................................86
Exploded View ....................................................................................................................................89
TC-618/626 Parts List 2 ......................................................................................................................91
Packing ................................................................................................................................................ 94
TC-618/626 PCB View .........................................................................................................................95
TC-618/626 Level Diagram .................................................................................................................99
TC-618/626 Block Diagram .............................................................................................................. 100
TC-618/626 Schematic Diagram ......................................................................................................102
Specifications ...................................................................................................................................103

TC-618/626 Service Manual
2
Introduction
Manual Scope
This manual is intended for use by experienced technicians familiar with similar types of communication
equipment. It contains all service information required for the equipment and is current as of the
publication date.

TC-618/626 Service Manual
3
Safety Information
The following safety precautions shall always be observed during operation, service and repair of this
radio.
◇This radio shall be serviced by qualified technicians only.
◇Only use HYT supplied or approved batteries and chargers.
◇To avoid electromagnetic interference and/or compatibility conflicts, turn off your radio in any
area where posted notices instruct you to do so. Turn off your radio before boarding an aircraft.
Any use of the radio must be in accordance with airline regulations or crew instructions.
◇For vehicles with an air bag, do not place a radio in the area over an air bag or in the air bag
deployment area.
◇Turn off your radio prior to entering any area with explosive and flammable materials.
◇Do not charge or replace your battery in a location with explosive and flammable materials.
◇Turn off your radio before entering a blasting area.
◇Do not use any portable radio that has a damaged antenna. If a damaged antenna comes into
contact with your skin, a minor burn may result.
◇Do not expose the radio to direct sunlight for a long time, nor place it close to a heating source.
◇During transmission, hold the radio in a vertical position with its microphone 2.5 to 5.0
centimeters (1-2 inches) away from your lips, and keep the antenna at least 2.5 centimeters
(approximately 1 inch) away from your head.
◇If you wear a portable radio on your body, ensure that the antenna is at least 2.5 centimeters
(approximately 1 inch) away from your body when transmitting.

TC-618/626 Service Manual
4
Radio Overview
TC-618
(1) PTT (Push-to-Talk)
Key (2) SK1 (Side Key
1) (3) SK2 (Side Key 2) (4) Speaker
(5) Microphone (6) Antenna (7) LED Indicator (8) Channel Selector Knob
(9) Radio On-Off/Volume
Control Knob (10) Battery Latch (11) Accessory Jack (12) Accessory Jack Cover
(13) Belt Clip (14) Battery (15) Screw of Belt Clip (16) Charging Piece

TC-618/626 Service Manual
5
TC-626
(1) PTT (Push-to-Talk)
Key (2) SK1 (Side Key 1) (3) SK2 (Side Key 2) (4) Speaker
(5) Microphone (6) Antenna (7) LED Indicator (8) Channel Selector
Knob
(9) Radio On-Off/Volume
Control Knob (10) Battery Latch (11) Accessory Jack (12) Accessory Jack
Cover
(13) Belt Clip (14) Battery (15) Screw of Belt Clip (16) Charging Piece
PTT (Push-to-Talk) Key
Press and hold down the PTT key to transmit, and release it to receive.
SK1 (Side Key 1)
SK1 is a programmable key that can be assigned with long/short press function by your dealer.
SK2 (Side Key 2)
SK2 is a programmable key that can be assigned with long/short press function by your dealer.
Note: Short Press means key press shorter than 1.5s, while Long Press means key press not shorter
than 1.5s.
LED Indicator

TC-618/626 Service Manual
6
Status indications and alert tones are shown in the table below:
Operations/Functions LED Indications and Alert Tones
To enter Wired Clone mode
(For the source radio, hold down
SK2 while powering it on; for the
target radio, turn it on directly)
The LED on the source radio flashes orange once
upon power-on.
Status of the source radio
(After the target radio is turned
on and the cloning cable is
connected, press SK2 of the
source radio to begin cloning.)
The LED flashes red during the cloning process;
The red LED goes out once cloning succeeds;
The red LED goes out once cloning fails.
Wired
Clone
Status of the target radio The LED flashes green during the cloning process;
The green LED goes out once cloning is completed.
Power On (to enter User Mode)
When the radio is turned on, it sounds the power-on
alert.
When the radio is currently on a blank channel, it
sounds beep tones continuously.
Low Battery Alert The LED flashes red, and a low-pitched tone sounds
every 10 seconds.
Transmitting
The LED solidly glows red.
When the TOT timer expires, the radio sounds beep
tones continuously.
A TOT pre-alert tone sounds before the TOT timer
expires.
Receiving The LED glows green when carrier is present.
Scanning
The LED flashes green once every second during the
scanning process.
Scan Start Alert (programmable by the dealer): one
beep.
Scan End Alert (programmable by the dealer): one
beep.
Priority Scan Alert (programmable by the dealer): one
beep if the radio is currently on a priority channel.
Writing/Reading The LED flashes red during reading.
The LED flashes green during writing.
Adjust Power Level
A low-pitched tone is heard when the radio switches
from high power to low power.
A high-pitched tone is heard when the radio switches
from low power to high power.
VOX
A high-pitched tone is heard when the VOX function is
enabled.
A high-pitched tone is heard when the VOX function is
disabled.
Channel Selector knob
Rotate the knob to select your desired channel.
Radio On-Off/Volume Control Knob
Rotate the knob clockwise to turn the radio on, or counter-clockwise to turn it off (a “click”will be heard).
After the radio is powered on, rotate the knob clockwise to increase the volume, or counter-clockwise to
decrease the volume.
Accessory Jack
Use the jack to connect accessories such as speaker, microphone, external PTT, earpiece, PC
programming cable and wired cloning cable, etc.

TC-618/626 Service Manual
7
Software Specifications
Description of Features
1. Channel Capacity: 16
2. Channel Spacing: 25KHz/12.5KHz
3. Channel Step: 5/6.25/10/12.5KHz
4. Channel Scan
5. Tx/Rx Status Indication (red/green LED)
6. CTCSS/CDCSS Encode & Decode (38 groups of standard CTCSS; 83 groups of standard
CDCSS; optional CTCSS Tail Revert of 180/120 degrees, and supporting non-standard
CTCSS/CDCSS).
7. Low Battery Alert
8. Auto Battery Save
9. Unlock Detection and Emergency Alarm
10. Nine Selectable Squelch Levels
11. Monitor
12. Time-out Timer (TOT)
13. Squelch Tail Elimination
14. PC Programming (manual/automatic adjustment)
15. High/Low Power Switch (2.0/5.0W)
16. Wide & Narrow Bandwidth Compatibility
17. Busy Channel Lockout (transmission prohibited in busy status)
18. Wired Clone
19. Battery Strength Indication
20. Manual Adjustment
21. VOX and Five Selectable Sensitivity Levels
Mode Description
User Mode
It is a conventional communication mode. After the radio is turned on, it enters the User Mode.
PC Programming Mode
The radio in User Mode enters PC Programming Mode through specific protocol based communication.
Wired Clone Mode
1. Description
Wired Clone Mode is an independent mode. To access other modes, you must restart the radio.
Wired Clone Mode includes User Clone Mode and Factory Clone Mode.
1) User Clone Mode:
Connect two radios using a cloning cable. Then hold down SK2 on the source radio while

TC-618/626 Service Manual
8
powering it on, and the radio enters User Clone Mode in 2 seconds. The target radio can be
directly turned on to enter the mode. In this mode, parameter data stored in EEPROM of the
source radio will be cloned to EEPROM of the target radio. The data transferred only covers
channel data and common parameters, excluding adjustment data, version and serial No. of the
model.
2) Factory Clone Mode:
Short the SELF pin of the source radio's MCU, and connect the two radios using a cloning
cable. Then hold down SK2 on the source radio while powering it on, and the radio enters
Factory Clone Mode in 2 seconds. The target radio can be directly turned on to enter the mode.
Data transferred covers all data in EEPROM other than the Serial No., with the flag of Tune
Switch included.
2. Process
Process of Wired Clone:
1) The LED flashes orange once after the source radio enters Wired Clone Mode. Press SK2
again to clone data to the target radio.
2) During cloning, the LED on the source radio flashes red, and the LED on the target radio
flashes green. When cloning ends, both the red LED on the source radio and the green LED on
the target radio go out, indicating both radios are ready for another cloning operation.
3) If any abnormal situation occurs during cloning, the source radio will stop cloning and the red
LED on it will go out, indicating both radios are ready for another cloning operation.
4) When cloning ends, the source radio goes back to the standby status. Press SK2 again to
begin another cloning operation.
Manual Adjust Mode
Hold down PTT and SK2 on a radio while powering it on, and the radio enters Manual Adjust Mode.
(Note: This operation is subject to the option Tune Switch in the programming software.) When this
option is unchecked, the radio is unable to enter the adjustment mode, which helps avoid change of
parameters and degradation of radio performance caused by user’s misoperations. )
Keep this option unchecked after values are well adjusted from factory, to avoid any unexpected change
of values. The adjustment values can be reset and changed in Factory Mode only.
Description of adjustment:
1) To enter Manual Adjust Mode
Hold down PTT and SK2 on the radio over two seconds while powering it on, and then the LED
glows orange, indicating entry into Manual Adjust Mode. When the keys are released, the radio will
enter item N of Tx group (N depends on the position where the Channel Selector knob locates).
The radio enters an item of Tx group by default, and the LED glows red. (CH16 is used to switch
between Tx group and Rx group. When the Channel Selector knob locates on this channel, there is
no LED indication.)
2) To switch between Tx group and Rx group
Rotate the Channel Selector knob to CH16 and long press PTT to switch between Tx group and Rx

TC-618/626 Service Manual
9
group. If the LED glows red, Tx group is entered; if the LED glows green, Rx group is entered.
The LED solidly glows red for adjustment of Tx group items.
The LED solidly glows green for adjustment of Rx group items.
3) To switch between items of Tx group/Rx group
This operation is done through the Channel Selector knob.
Tx group: CH1~Ch15 respectively stand for Tx Preset Power, Tx Low Power, Tx Medium Power, Tx
High Power, CDCSS Deviation, CTCSS Deviation (low), CTCSS Deviation (medium),
CTCSS Deviation (high), MSK Deviation, VOX Level 1, VOX Level 2, VOX Level 3, VOX
Level 4, VOX Level 5 and Tx Low Voltage Threshold. (Note: Tx Medium Power is not
required to be adjusted and can be skipped. For radios without the ATIS function, MSK
Deviation is not required to be adjusted and can be skipped. )
The LED solidly glows red during adjustment of CH1~CH15.
Rx group: CH1~CH8 respectively stand for SQL On 1, SQL On 5, SQL On 9, SQL Off 1, SQL Off 5,
SQL Off 9, Rx Low Voltage Threshold and Rx Bandpass Filter.
The LED solidly glows green during adjustment of CH1~CH8.
CH9~CH15 are invalid, and the green LED goes out when the Channel Selector knob
locates on one of these channels.
4) To switch between wide and narrow bandwidth
When adjusting a certain item, long press PTT (orange LED flashes indicating valid press) to switch
between wide/narrow bandwidth. And the first frequency of the current bandwidth is the frequency
for adjustment by default.
5) To switch between frequencies
Short press PTT (orange LED flashes indicating valid press) to switch between frequencies orderly
under certain bandwidth and certain adjustment item.
6) To adjust the value
Short press SK1 under certain bandwidth and certain adjustment item to increase the adjustment
value in steps of 1; hold down the key to increase the value continuously in steps of 1. The
adjustment value will remain unchanged once it reaches the allowed maximum value.
Short press SK2 under certain bandwidth and certain adjustment item to decrease the adjustment
value in steps of 1; hold down the key to decrease the value continuously in steps of 1. The
adjustment value will remain unchanged once it reaches the allowed minimum value.
7) Measures on special items:
Tx group: CH10~CH15 respectively stand for VOX Level 1, VOX Level 2, VOX Level 3, VOX Level 4,
VOX Level 5 and Tx Low Voltage Threshold. These adjustment items are related to AD
sampling. Press SK1 or SK2 after entering the above items, to activate AD sampling
(including calculation) once. Rotate the Channel Selector knob to save the current AD
sampling value. If neither of SK1 or SK2 is pressed, the adjustment value will not be
updated, and AD sampling will not be activated.

TC-618/626 Service Manual
10
Rx group: CH1~CH7 respectively stand for SQL On 1, SQL On 5, SQL On 9, SQL Off 1, SQL Off 5,
SQL Off 9 and Rx Low Voltage Threshold. These adjustment items are related to AD
sampling. Press SK1 or SK2 after entering the above items, to activate AD sampling
(including calculation) once. Rotate the Channel Selector knob to save the current AD
sampling value. If neither of SK1 or SK2 is pressed, the adjustment value will not be
updated, and AD sampling will not be activated.
8) Description of key-press:
Short press: key press shorter than 1.5s;
Long press: key press not shorter than 1.5s.

TC-618/626 Service Manual
11
Circuit Description
Realization Methods of Basic Functional Modules
1. PLL Frequency Synthesizer
The PLL circuit mainly provides the local oscillator signal for Rx and RF carrier signal for Tx. It
is composed of VCO and baseband processor, allowing frequency tracking and channel
switching under the control of MCU signals.
1) PLL
MB95F108AK
WPFV-GE1
U605
1/2
17bitDIV
32/33
OSC
1/2
21bitDIV
U202
CP
RX-VCO
L102
D103
L101
APC/TUNE
T/R-SW
CLK
DATA
EN
Q101
2SK508NV
D102
BUFFER
Q6
1
23
D104
D101
D100
Q100
2SK508NV
12.8MHZ
TX-VCO
LPF
Q5 1
23
Figure 1
The step frequency of the PLL circuit is 5.0KHz, 6.25KHz, 10.0KHz or 12.5KHz (selectable). Therefore,
the 38.4MHz reference oscillator signal is divided into 5.0KHz, 6.25 KHz, 10.0 KHz or 12.5 KHz
reference frequencies via a fixed counter in the PLL (at U202). Meantime, the signal from the VCO goes
through the buffer Q102 and amplifier Q103, and then it feeds to the PLL (at U202), where it is divided by
a variable frequency divider. In the phase detector (PD) of PLL, the new signal derived from frequency
division is compared with the reference frequencies. After passing through a low-pass filter, the signal
from the phase detector goes to the varactors (D100, D101, D102 and D103) of VCO so as to control its
output frequency.
2) VCO
The VCO section is realized by the oscillator circuit of three-point capacitance.
In Tx mode, the oscillator frequency of VCO is generated by Q100; in Rx mode, it is generated by Q101.
U202 generates, via the phase detector, a control voltage to control varactors (D100 and D101 in Tx
mode; D102 and D103 in Rx mode), making the oscillator frequency of VCO consistent with the preset
frequency of MCU within a wide frequency range.

TC-618/626 Service Manual
12
The switching diode Q652 performs switching between transmission and reception under the control of
T/R: in Tx mode, T/R is set to low level and Q653 becomes conductive, making Q100 operate; in Rx
mode, T/R is set to high level and Q653 is cut off, making Q101 operate. The output from Q100 and
Q101 is amplified by Q102 and then feeds to the buffer amplifier for further processing.
If the PLL is unlocked, the LD pin of U202 outputs low level. If the microprocessor detects such situation,
Tx/Rx operation is prohibited, and the alarm alert sounds.
2. RF Power Amplifier Circuit (Tx Section)
The block diagram of the RF power amplifier circuit is shown in the figure below:
R/TSW
L453
1u
RX
RQA0002
2
13
3 Amplifier
Q401
2SC4988
1
23
APC
LPF
2SK3475
2
13
Q400
2SC5108
1
23
Q104
2SC51081
23
MATCH
ANTENNA
Q402
0
RF PA
Q403
Figure 2
To obtain the required RF power, the RF signal from VCO goes to the buffer Q104 and to the driver
amplifiers Q400 and Q401. Then the amplified RF signal feeds to the driver Q402, which pre-amplifies
power of the input signal to drive the final-stage power amplifier Q403. The input RF signal is then further
amplified by Q403, and feeds to the LC low-pass filter (LPF) through the Tx/Rx switching diode D401.
Finally, it is transmitted from the antenna after ultroharmonics are removed.
3. Rx LNA and Mixer Circuit (Rx Section)
1) Rx LNA and RF BPF
To allow better frequency range selectivity, the Rx bandpass filter adopts the multi-stage electrically
tunable circuit, as shown in Figure 3.
C505
LNA
TUNE BPF
TUNE FROM MCU
C504
C523
L508 L506
Q500
D503
L507
D506
1
23
L501
C526
C519
C524
L502
C521
C506
TUNE FROM MCU
D504
D505D507
TUNE BPF
Figure 3
After out-of band signals are removed by the electrically tunable bandpass circuit (D503, D504, L501,
L502, C503, C505 and C507), the signals from the antenna go to the low-noise amplifier (LNA) Q500 for

TC-618/626 Service Manual
13
amplification. Then the amplified signals feed to the three-stage bandpass circuit (mainly composed of
D505, D506, D507 and peripheral components) to effectively reject out-of-band interference and to
obtain pure RF signals. Finally, the signals go to the mixer circuit.
MCU provides the electrically tunable control signal (its level can be obtained via table lookup or
calculation), making the varactor operate within an appropriate voltage range. It forms a bandpass filter
with the peripheral inductors/capacitors. The capacitance of the varactor changes along with the control
voltage of MCU, making the center frequency of the bandpass filter circuit change. In this way, the
requirements of preset Rx sensitivity and out-of-band rejection are satisfied.
2) Mixer Circuit and BPF Circuit
The block diagram of the mixer circuit is shown in the figure below:
L53022nH
C533
C534 C532
C531
XF1
Q501
38.85MHZ
1stIF BPF
RF MIXER
AN29160
C528
Figure 4
The mixer circuit mainly mixes the local oscillator signal from VCO with the received RF signal, to
provide the first IF signal for frequency discrimination by the demodulator chip (active mixer is applied).
The mixer Q501 uses a dual-gate MOSFET (3SK318), and is characterized by good noise characteristic,
square-law characteristic, and high isolation degree between the first local oscillator signal and the Rx
signal. In addition, it also has a gain value (adjustable via offset), so as to assure sufficient sensitivity.
After residual spurious signals are removed by the inductor L509, the signals from the mixer go to the
first IF filter (first-class crystal filter assuring sufficient bandwidth and good selectivity). Then the signals
feed to the baseband processor chip (AN29160) for demodulation.
4. APC/TUNE Circuit
The block diagram of the APC/TUNE circuit is shown in the figure below:
R430
R421 Q431
DTA114YE
R437
C441
R422
R441
R433
R434
from MCU
V_BAT
TX_VCC
R432
R440
C435C437
R438
C436
R442
C438
-+
+-
U430
NJM2904
1
3
4
2
5
7
8
6
R436
Q430
DTC114EE
2
31
R431
R420
R439
R500
C440C439
to RF PA(APC)
C434
R435
to BPF(TUNE)
Figure 5

TC-618/626 Service Manual
14
MCU outputs appropriate PWM waveform according to the selected channel. The waveform is then
rectified by the RC filter circuit (R441, R442, C440 and C441) to generate level of APC/TUNE control
signal. One flow of APC/TUNE control signals go to R500 to be used as control voltage of the Rx
electrically tunable circuit. In Tx mode, the signals go to R439 and R440 for voltage division, and the
APC reference voltage is derived.
The error detect voltage is derived after the Tx current goes through R420, R421 and R422. Then the
voltage is compared and amplified by the operational amplifier U430, and further compared with the APC
reference voltage. After these operations, the APC control voltage is output, and the close-loop negative
feedback control power is generated when the Tx current changes.
5. Audio and Signaling Processing Circuit
The baseband processor (AN29160) is highly integrated and allows multiple functions (e.g. VOX Level
Detect & Output, SQ Level Detect & Output, Rx/Tx Audio Process & Convert, Audio Amplify, etc.) to be
realized in it. In addition, it can be used for both transmission and reception.
1) Block diagram of Tx audio & signaling processing circuit
0
sp Amp
SF
AMP(TX)
Tone
AFMOD
Mic amp
U200
AN29160AA
PROCESSER
signalling input
AF
HPF
5th-HPF
Pre
Emphasis mic
M IC3
AF
mute
volume
mic mute
LIM
(TX)
AUDIO OUT
CPU
TX VCO
Figure 6
a) Tx Audio Process: The audio signals from MIC are converted to electrical signals via acoustoelectric
conversion of MIC. After pre-emphasized, the audio signals are processed by a limiting amplifier (at
U200). Then the processed signals go to the low-pass filter circuit to remove frequencies over 3KHz.
Finally, the signal goes to the potentiometer VR200 and then to VCO for direct frequency
modulation.
b) Tx Signaling Process: MCU outputs, via the QTO port, signaling encoded waveform, which is
divided via the RC circuit into two flows. One flow modulates the reference frequency oscillator of
PLL directly, while the other flow modulates VCO.
Note: VR260 adjusts the amplitude proportion between the two flows, to optimize the signaling
waveform modulated on the carrier.

TC-618/626 Service Manual
15
2)Block diagram of Rx audio & signaling processing circuit
U201
AF
AMP
16ΩIW
RX
1
sp Amp
SF
AMP(TX)
VOX
Ton e
AGC
tone-LPF
DET
BGR
EN
RSSI
DATA
Mic amp
VCO
0
U200
AN29160AA
PROCESSER
IFAMP2
5th-LPF
CLK
AF
HPF
PE
5th-HPF
signalling output
IFAmp1
SW
To MCU
IC
CF302
450KHz+/4.5K
OUT IN
VREF
TX
De
Emphasis
LATCH
AF
mute
SPVCC
volume
To MCU
CDC/CTC
MCU
POWERREG
mix2
mic mute
LIM
(TX)
VCC
SQ
AUDIO OUT
Figure 7
After demodulating the received signal, U200 outputs initial audio signal containing noise, signaling and
voice components. Therefore, audio signal is processed via three flows.
1) Rx Voice Process: One flow of audio signals from U200 goes back to U200 after passing through the
RC low-pass filter and de-emphasis circuit. This flow of audio signals are amplified at U200, and
restored after frequencies below 300Hz are removed. Then the restored audio signals are adjusted
by the potentiometer and feed to the audio power amplifier U201, which performs power
amplification to drive the speaker directly. To obtain larger power, the BTL bridge dual-end output is
adopted.
2) Rx Signaling Process: One flow of audio signals from U200 goes to the 300Hz low-pass filter circuit
(U640). After audio signals over 300Hz are removed, signaling signals (CTCSS or CDCSS) go to the
QTIN pin of CPU, and then are decoded by CPU.
3) Noise Signal Process: One flow of audio signals from U200 goes back to U200. After they are
filtered, amplified and rectified at U200, a DC voltage signal (SQ) corresponding to the noise
component is derived and is sent to the BUSY pin of MCU via the ND pin of U200. Then MCU
processes the input signal.

TC-618/626 Service Manual
16
6. MCU Control Circuit
The block diagram of the MCU control circuit is shown in the figure below. MCU operates on the clock
frequency of 7.3728MHz.
/LIGHTING
X601
MB95F108AK
WPFV-GE1
AT24 C6 4
APC/TUNE
U605
U610
Reset
IC
U609
MON2
BAT
7.3728M cry stal oscillator
PTT2
PLL
1.VOX
2.BUSY_DET
3.BEEF/CALL
4.T/R
5.SAVE
6.DC/CTC
7.W/N
8.UART
9.BAT_BAT
10.PLL_LD
CHANNEL SW
Figure 8
The MCU control circuit is mainly composed of MCU, EEPROM, reset IC, keys, knobs, etc. Main
functions realized by this circuit are:
1) Signal Control:
To control Battery Save Mode;
To control high/low power switch;
To control wide/narrow bandwidth switch;
To control Tx/Rx switch;
To control APC/TUNE output voltage;
To control Tx power supply and power supply of audio amplifier;
To control SQL OFF detection.
2) Signal Detect:
To detect startup of external PTT, MONI and VOX;
To detect unlocking of PLL;

TC-618/626 Service Manual
17
To detect VOX ON level;
To detect low voltage alarm;
To detect enabling and distinguishing of external earpiece.
3) Data Transmission and Processing:
To initiate EEPROM data;
To transmit programming data;
To process the code of Channel Selector knob.
To encode and decode signaling;
To transmit data of baseband processor (PLL).
7. Power Supply Processing Circuit
The block diagram is shown in the figure below:
SW
Q611
power management
Vin
VSS
Vout
---
7.2V
U606
L604
601s
SAVE
FMMT717FMMT717
Q612
5V
UPA572T
Q610
TXC
V-TX POWER-SAVE
Figure 9
After power-on, one flow of battery voltage is filtered by L604 and C682, and then feeds to the RF power
amplifier and audio power amplifier for amplification. Another flow goes to the 5V regulator (U606). After
regulated, the VCC_5V voltage is output for use by MCU and baseband processor chip. As the radio
operates at half-duplex mode, the Tx and Rx power supplies need to be controlled alternately. In addition,
to meet requirements of battery save mode, MCU needs to output a pulse signal (SAVE control signal)
with fixed duty ratio. If the SAVE control signal is at high level, Q610 becomes conductive and provides
the 5V voltage (V_SAVE) for the operating circuit (PLL and Rx circuit). If the SAVE control signal is a
pulse signal, the radio will enter Battery Save Mode. During transmission, CPU control signal (TXC) is at
high level. Then Q611 becomes conductive and provides 5V voltage (TX_VCC) for the operating circuit
(Tx circuit).
The power supplies of the Tx and Rx circuits are protected by symmetrical voltage regulation measures.
When output voltage/current changes along with the change of load, the close-loop feedback circuit
operates, limiting the output voltage to 5V.

TC-618/626 Service Manual
18
8. VOX Realization Circuit
The block diagram is shown in the figure below:
Q202
2SA1832
1
2 3
Q201
2SK1824
2
31
J4
MICJACK
2431
VCC_5V
R251
1M
MIC_EN
EXPTT
C260
220P
RXD
mic
X1
-
2
+
1
R201
2.2K
C201
470P
C200
4.7u/10V
R203
4.7K
VCC_5V
R200
470
C213
1U
C212
0.1U
R205
47K
C202
0.1U
L200 1UH
R202 100
TP200
R208
100K
R207
56K
R206 1K
R204 470
C274
0.01U
Figure 10
Press and hold down the programmed VOX key, and the radio enters the VOX status. The VOX function
can be enabled only when MIC_EN and EXT-PTT are detected by MCU to switch from low level to high
level within several hundred milliseconds. Otherwise, the earpiece will be deemed as one without VOX
and the VOX function cannot be enabled.
1) When a VOX earpiece is plugged into the accessory jack, Q201 is cut off, and MIC_EN switches
from low level to high level. Meantime, Q202 and R204 form a closed circuit with the external
earpiece (Q202 is conductive), and EXT-PTT switches from low level to high level. In this case, the
VOX earpiece is determined by MCU, and the VOX function is enabled. When the VOX level (5
levels, adjustable) reaches the preset value, voice operated transmission is being made, and the
voice signals enter the baseband processor (AN29160) via the processing path.
2) If a non-VOX earpiece (namely an earpiece with PTT), Q201 is cut off, and MIC_EN switches from
low level to high level. However, Q202 does not form a closed circuit (maintaining the cut-off status)
and EXT-PTT is still at low level. In this case, a non-VOX earpiece is determined by MCU. The
radio will return to normal mode, and will transmit if the PTT key on the earpiece is held down.

TC-618/626 Service Manual
19
CPU Pins
Pin No. Port Name TC-618 TC-626 I/O Function
1 AVcc Vcc Vcc I For input from the A/D power supply;
connected with the power supply.
2 AVR Vcc Vcc I For input of A/D reference signal;
connected with the power supply.
3 PE3/INT13 PTT PTT I For input from PTT (connected with
pull-up resistor) (valid at low level).
4 PE2/INT12 A_KEY A_KEY I For input from SK1 (connected with
pull-up resistor) (valid at low level).
5 PE1/INT11 EXT-PTT EXT-PTT I For input from earpiece PTT
(connected with pull-down resistor)
(valid at high level).
6 PE0/INT10 B_KEY B_KEY I For SK2 input (connected with pull-up
resistor) (valid at low level).
7 P83 ENC3 ENC3 I For input from the Channel Selector
Knob (connected with pull-up resistor).
8 P82 ENC2 ENC2 I For input from the Channel Selector
Knob (connected with pull-up resistor).
9 P81 ENC1 ENC1 I For input from the Channel Selector
Knob (connected with pull-up resistor).
10 P80 ENC0 ENC0 I For input from the Channel Selector
Knob (connected with pull-up resistor).
11 P71/TI0 T/R T/R O To control Tx/Rx switch: H(Rx)/L(Tx).
12 P70/TO0 Reserve Reserve O Reserved.
13 MOD For
programmi
ng
For
programmi
ng
IFor operating mode indication; during
programming, it is connected with VCC
and a 47K resistor is connected
between the pin and the grounded Vss;
during non-programming period, only a
47K resistor is connected between the
pin and the grounded Vss.
14 X0 OSC0 OSC0 O
15 X1 OSC1 OSC1 I
Pin for the 7.3728MHz main crystal
oscillator.
16 Vss GND GND GND (connected the GND
programming port during
programming).
17 Vcc VCC VCC I 5V (connected the VCC programming
port during programming).
18 PG0 C C Not used as I/O; a capacitor is
connected between the pin and the
grounded Vss.
19 PG2/X1A OSC32K OSC32K O Pin for the auxiliary crystal (reserved)
20 PG1/X0A OSC32K OSC32K O Pin for the auxiliary crystal (reserved)
21 /RST RESET RESET I Reset (connected the RSTX
programming port during
programming).
22 P00/INT00 Reserve Reserve O Reserved.
23 P01/INT01 Reserve Reserve O Reserved.
24 P02/INT02 Reserve Reserve O Reserved.
25 P03/INT03 Reserve Reserve O Reserved.
This manual suits for next models
1
Table of contents
Other HYT Two-way Radio manuals
Popular Two-way Radio manuals by other brands
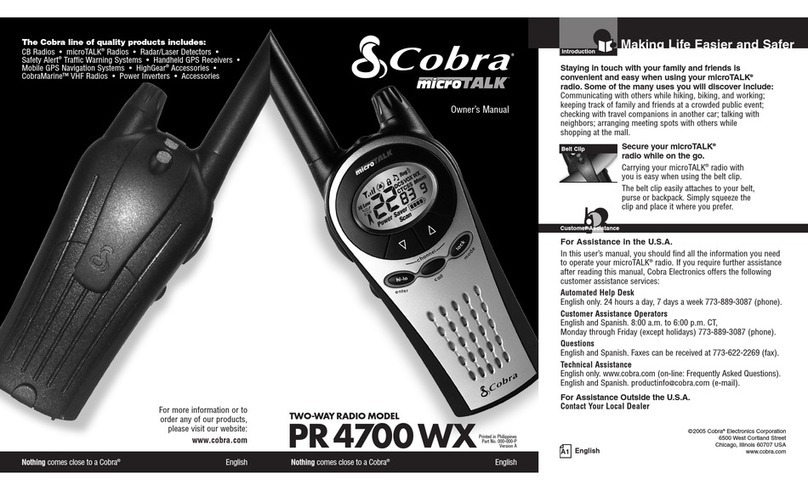
Cobra
Cobra microTALK PR4700 WX owner's manual

Alecto
Alecto FR-09 quick start guide

Vertex Standard
Vertex Standard VZ-30-G6-4 user guide
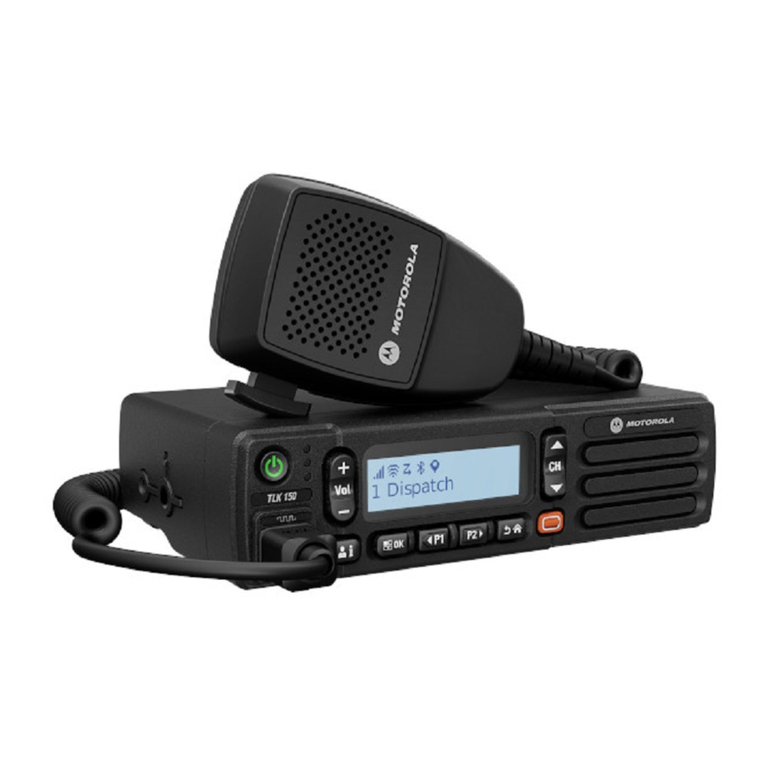
Motorola solutions
Motorola solutions WAVE TLK 150 user guide

eKids
eKids MARVEL SPIDEY and his SPIDEY AMAZING FRIENDS... manual

Bresser
Bresser NATIONAL GEOGRAPHIC 9111400 operating instructions