intermountain GP10 Manual

1336 Sherman Dr., Unit C
Longmont, CO 80501-6174
Phone: (303 772-1901
Fax: (303 532-2352
intermountain@intermountain-railway.com www.intermountain-railway.com
OPERATORS GUIDE
Default DCC Address for All Locomotives: 3 ( o leadi g zeros)
Decoder Reset: CV8 = 8
Thank you for your purchase of the InterMountain Railway Company GP10 locomotive. Your locomotive is equipped with either a
LokSound Select Sound decoder or a LokPilot non-sound decoder. Both utilize the 21-Pin MTC system. This guide directs you
through basic operational and decoder functions for DCC operation. More in-depth information is available on our website in the
regularly updated DCC Assistance section. Should you have any questions that are not answered in this guide or online, please
feel free to contact InterMountain at the contact information listed above.
Removi g a d Operati g your GP10 Locomotive
Your locomotive is attached to the black plastic packaging via two Phillips head screws below the fuel tank. Removal of these
screws can be done with a standard sized Phillips screwdriver.
We do not recommend operating your decoder equipped locomotive on analog DC track power. If you operate your locomotives on
DC only and do not want to purchase a DCC system, please contact us to obtain a 21-pin DC plug that will allow the locomotive to
operate properly with DC track power. Note that some lighting functions may not work correctly when the DC plug is used. If you
decide to convert to DCC later, you can easily do so.
DCC No -Sou d Decoder Operatio
The non-sound DCC equipped locomotive responds to address 3 (no leading zeros out of the box. Increase the speed on your
DCC throttle and the locomotive should move in the direction your throttle is set for. The locomotive lighting is controlled by
various function keys. Please see the table on the following page for the functions available in the non-sound decoder. Please
verify that all lighting and motion is working properly before making any programming changes to the decoder. If you should have
any issues, contact us.
DCC Sou d Decoder Operatio
The DCC sound equipped locomotive responds to address 3 (no leading zeros out of the box. Upon placing your
locomotive on the track, you will not hear any sound.
You must press the F8 fu ctio key i order to get the
locomotive's prime mover started
. As the prime mover is starting, your locomotive will not move even if you give it
a speed command. A prototype locomotive cannot move until it is fully started and your model simulates this! After the
prime mover settles into idle (20 seconds , you should be able to give it a speed command, hear the prime mover
throttle up, hear the brakes release and watch it slowly move. If you reduce the speed to 0, you should hear the brake
squeal as the locomotive comes to a stop. Press F8 again while the locomotive is in idle and the prime mover will shut-
down. You'll hear the spitter valve releasing air for 1 minute after shut-down. A prototype locomotive's horn and bell
can be operated when the prime mover is shut down as long as enough air is available. Your GP10 is no exception!
Please see the table on the following page for all of the lighting and sound functions available in the sound decoder.
The F8 function key operation can be changed to allow track power to start the prime mover by setting CV32 to 2
FIRST, and then CV419 to 32.
The 20 second start-up delay can be removed by simply changing CV124 to 0. This will allow the locomotive to start
moving immediately when the throttle is increased during the start-up sound sequence.
Sou d a d No -Sou d Decoder Exte ded Addressi g:
After you have verified that your locomotive operates properly on address 3, you'll want to give it an address other
than 3. Today's DCC Systems give you the option to enter a 3 or 4 Digit Extended (long Address. This is usually the
cab number of the locomotive. Any address from 128 and above is considered by most DCC systems as a long address.
If you want an address between 1-127, set it as a short address. Refer to your DCC System's manual for step-by-step
guidance as to how to do this. Once you have set the new address, verify that all lighting and motion works properly
before proceeding to any other programming.
Full Throttle Features – Sou d U its O ly
Function 9 activates
Drive Hold
, allowing you to throttle the prime mover sound up or down while your locomotive
maintains a constant speed. This helps to simulate pulling heavy “loaded” cars working independent of BEMF which can
only adjust the prime mover sound based on how heavy the model train actually is, not by what is “loaded” in the cars.
Function 10 activates the
I depe de t Brake
. Just be sure to release the brakes before you try to move again!!
Ru 8
and
Coast
are also included in the decoder but are not mapped to a function key. Visit our website's DCC
Assistance section for more information on mapping Run 8 and Coast.
For more information about all of the FULL THROTTLE features visit: http://intermountain-railway.com/fullthrottle.html
HO-GP10-Locomotive-Insert-March-2017.odt

Default DCC Decoder Fu ctio Table
Fu ctio Key
DCC Sou d GP10
DCC No -Sou d GP10
F0 / Headlight Nose Headlight (if equipped / Rear Light [Directional] Nose Headlight (if equipped / Rear Light [Directional]
F1 / Bell
Bell (Steel Bell by Default
N/A
F2 / Horn
Playable Air Horn (Nathan P3 by Default
N/A
F3
Cab Headlight (GYRA Effect / Non-GYRA Effect (if equipped
Cab Headlight (if equipped [Set CV113 = 159 for GYRA Light]*
F4
Marker Lights (if equipped
N/A
F5
Number Board Lights
Number Board Lights
F6
Ditch Lights (if equipped [Directional]
Ditch Lights (if equipped [Directional]
F7
Dimmer
Dimmer
F8
Prime Mover Start-up / Shut-down (mute if moving
Virtual Drive Sound (used when operating with a sound unit
F9
Drive Hold
N/A
F10
Independent Brake
N/A
F11
Rotary Beacon (if equipped
N/A
F12
Coupler
N/A
F13
Slow Spitter Valve
N/A
F15
Radiator Fan
N/A
F16
Spitters on Shutdown OFF
N/A
F17
Brake Set / Brake Release OFF
N/A
F18
Sanding Valve
N/A
F19
Short Air Let Off
N/A
F20
Compressor
N/A
F21
Handbrake Ratchet
N/A
*CV113 = 159 is for NON-SOUND u it o ly to cha ge cab headlight to GYRA light effect.
Sou d Volume CV Defaults Table:
Fu ctio CV # Ra ge GP10
Master Volume Control
63
0-192
180
**** SET CV32 to 1 BEFORE CHANGING CV 257 THROUGH CV 511 ****
Prime Mover
259
0-128
128
Horn
275
0-128
128
Bell
283
0-128
50
Coupler
291
0-128
128
Air Compressor
307
0-128
50
Radiator Fan 315 0-128 50
Independent Brake
339
0-128
20
Brake Set / Brake Release
347
0-128
20
Sanding Valve
355
0-128
128
Short Air Let Off
363
0-128
128
Fast Spitter Valve 371 0-128 50
Slow Spitter Valve
387
0-128
50
Spitters on Shutdown 395 0-128 50
Air Reverse
403
0-128
50
Run 8 411 0-128 128
Coast
419
0-128
128
Handbrake Ratchet
427
0-128
128
Random Sounds
451
0-128
50
Brake Squeal
459
0-128
25
Decoder Reset: CV8 = 8
HO-GP10-Locomotive-Insert-March-2017.odt

CV48 Sou d Selectio Table:
The default horn in the GP10 locomotive is the Nathan P3. There are 12 other horns to choose from if you should prefer a
different horn sound, or your prototype uses a different horn. The bell defaults to the standard EMD Steel Bell, however the
Bronze bell is also included. These can all be changed with your DCC system. The value for CV48 is calculated by adding the
values for the prime mover, the horn, and the bell sounds using the charts below.
As an example, the GP10 default values include: Prime Mover = 0, Horn = 3, Bell = 0 Total = 0 + 3 + 0 = 3 (Default)
Track Power MUST be i terrupted to the locomotive after cha gi g the value of CV48.
The locomotive ca be simply rocked off o e rail briefly to accomplish this task.
DEFAULT 6
Prime Movers GP10
0 4 Exhaust EMD 16 Cyl 567C - (Default)
Hor s GP10
0 Nathan K5LA
1 Nathan K3L
2 Nathan M3
3 Nathan P3 - (Default)
4 Nathan Old Cast P5
5 Leslie S5T
6 Leslie S3L
7 Leslie RS3L
8 Nathan K5H
9 Nathan K5LA
10 Nathan K3L
11 Nathan M3
12 Nathan P3
Bells* GP10
0 Steel Bell - (Default)
64 Bronze Bell
GP10 Locomotive Mi imum Recomme ded Tur Radius: 18”
Decoder Reset: CV8 = 8
Troubleshooti g
DCC equipped locomotives require very reliable electrical connections and contacts. If you are experiencing operating
issues with your locomotive, the track and/or locomotive wheels might be dirty. Both of these items need to be cleaned
thoroughly on a regular basis for reliable operation. Denatured alcohol works very well for these tasks.
DCC in general also requires plenty of power to the rails in all locations. If you have problem areas with any DCC
locomotive, it may be beneficial to add more feeder wires in these locations. It is also recommended that the first
feeder to the rails be within 6 feet of the command station. Items like turnouts and rail joints are never reliable for
passing electrical current. Rail joints can be soldered and extra feeders can be wired to the track around turnouts to
ensure reliable power distribution.
If the above is not improving the operation of your locomotive, check that the wires are properly soldered to the trucks
on both sides. These wires are visible by looking behind the truck side frames. If any wire is detached, it needs to be
soldered back on. You can do this yourself or send the locomotive in to us for the repair.
If you are having programming difficulties using the program track, remember that ESU LokSound decoders DO NOT
require a program track booster! If you have a program track booster such as the PTB-100 or PowerPax in-line between
your DCC system's program track outputs and program track, you must bypass it for programming ESU decoders on
the program track. You should also use Direct Mode (DIR programming. Visit our website's DCC Assistance Section for
more information.
The ESU LokSound Select decoder's address and all CVs may be programmed on the mainline in OPS mode or on the
program track in Direct Mode (DIR . Note that some systems may not be able to program CVs higher than 255. Should
you have this issue, there is an alternate method. You can set CV96 to the hundreds digit of the CV number you're
trying to program, set CV97 to the tens and units digits of the CV number you're trying to program. Set CV99 to the
value that you're trying to program. Visit our website's DCC Assistance page for more information.
HO-GP10-Locomotive-Insert-March-2017.odt

GP10 Locomotive Shell Removal I structio s
1. Place the locomotive on a soft surface or foam cradle. Remove the front and rear Kadee® couplers
from the locomotive by unscrewing the Phillips head screws. Gently slide the coupler box from the shell
and frame. Keep the pieces together for re-assembly. Next remove the two body screws (Phillips head
located just behind the front truck on either edge of the chassis.
2. Pull upward on the shell using a steady controlled pressure. Be gentle and take your time to avoid
damaging any of the locomotive details. Once the die-cast chassis begins to slide out from the shell,
take care to guide the front and rear portions evenly. Do NOT wedge the chassis against the shell.
3. The chassis should slide out of the shell to reveal the mechanism and
electronics. Note that if your locomotive has o e or more rooftop
beaco s, there are wires attachi g the shell to the chassis. Be very
careful ot to pull o these wires!
4. To reassemble the locomotive, place the shell over the drive mechanism and
gently press downward and evenly until the shell snaps into place.
Reassemble the two body screws, then slide the front and rear coupler boxes
back into place and replace the screws.
MAINTENANCE TASKS
Your InterMountain locomotive is designed to provide hours of enjoyment with little or no maintenance. On occasion
the drive gear mechanisms should be lubricated. Utilize a plastic compatible lubricant such as Labelle® 107 Oil. To
lubricate your locomotive place a few drops on the gears of the drive mechanism. Only a small amount is required.
Service Needs: Although rare, at some time you may require service for your locomotive. If you feel the need
to send your locomotive in for repair, you do not need to contact us first. The instructions for sending your
locomotive in for repair are located on our website: intermountain-railway.com under Customer Service and then
Service and Repair.
Decoder related issues may be solvable by checking the links on our website under the DCC Assistance section. We
regularly update this section to help you get the most out of your InterMountain locomotives. If you cannot find the
answer to your specific issue, please contact us at: intermountain@intermountain-railway.com or 303-772-1901.
Resetti g the decoder solves 95% of the decoder
related issues we ha dle. Decoder Reset: CV 8 = 8
HO-GP10-Locomotive-Insert-March-2017.odt
Table of contents
Other intermountain Toy manuals
Popular Toy manuals by other brands
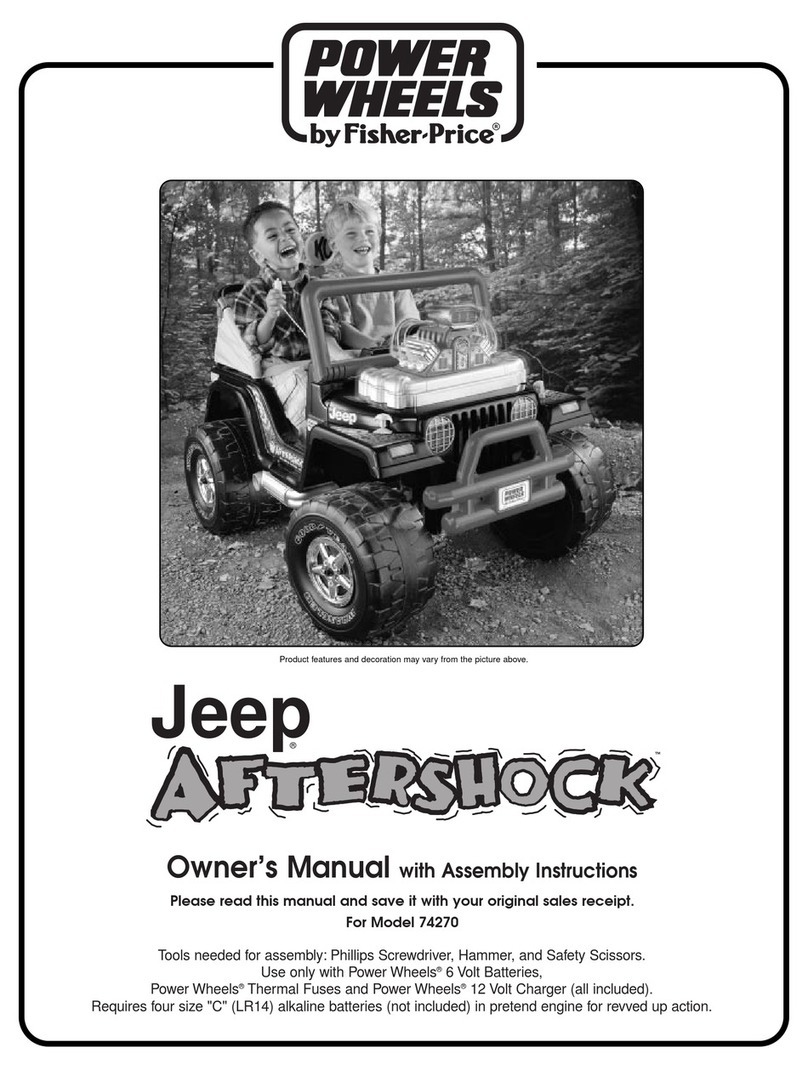
Fisher-Price
Fisher-Price JEEP AFTERSHOCK 74270 Owner's manual & assembly instructions

Faller
Faller 141072 manual
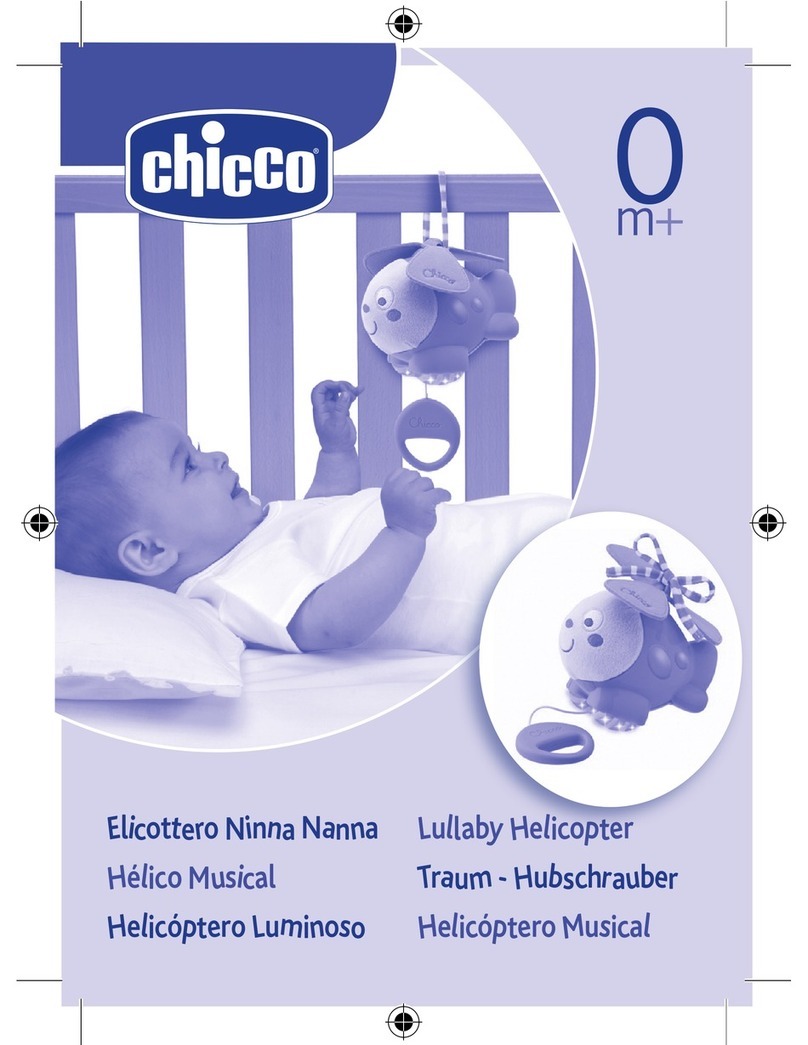
Chicco
Chicco HELICO MUSICAL manual

Rail King
Rail King F-3 Diesel Engine operating instructions

Eduard
Eduard Schürzen Pz.IV Ausf.J manual
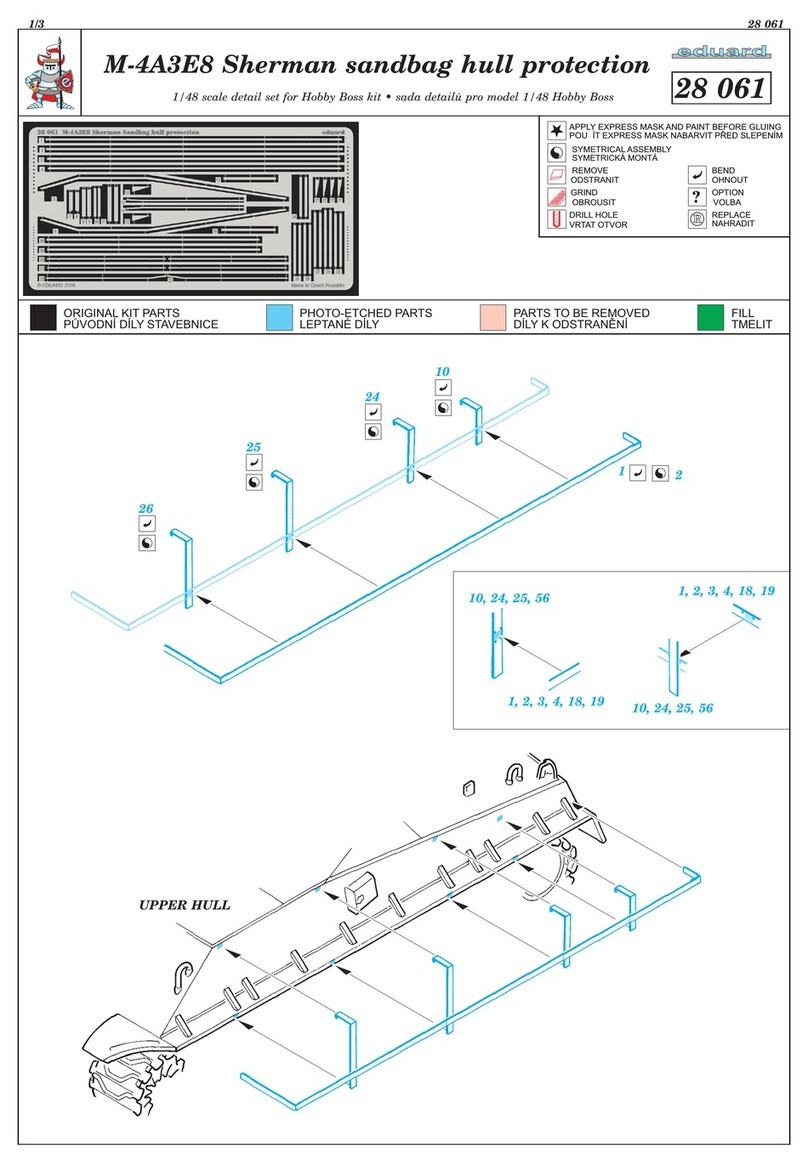
Eduard
Eduard M-4A3E8 Sherman sandbag hull protection manual