Inxpect LBK System BUS User manual

Original instructions
LBK System BUS
Instruction manual
v1.0 - EN
SRE - Safety Radar Equipment
WARNING! Any who uses this system must read the instruction manual to ensure safety. Read
and adhere to the "Safety information" chapter in its entirety before using the system for the first
time.

Copyright © 2020, Inxpect SpA
All rights reserved in all countries.
Any distribution, alteration, translation or reproduction, partial or total, of this
document is strictly prohibited unless with prior authorization in writing from
Inxpect SpA, with the following exceptions:
lPrinting the document in its original format, totally or partially.
lTransferring the document on websites or other electronic systems.
lCopying contents without any modification and stating Inxpect SpA as
copyright owner.
Inxpect SpA reserves the right to make modifications or improvements to the
relative documentation without prior notice.
Requests for authorizations, additional copies of this manual or technical
information about this manual must be addressed to:
Inxpect SpA
Via Serpente, 91
25131 Brescia (BS)
Italy
safety-support@inxpect.com
+39 030 5785105

Contents
Glossary of terms iv
1. This manual 6
1.1 Information on this manual 6
2. Safety 7
2.1 Safety information 7
2.2 Conformity 9
2.3 National restrictions 9
3. Get to know LBK System BUS 11
3.1 LBK System BUS 11
3.2 Controller ISC-B01 13
3.3 Sensors LBK-S01 16
3.4 Inxpect Safety application 17
3.5 Fieldbus communication 18
3.6 System configuration 19
4. Functioning principles 22
4.1 Sensor functioning principles 22
4.2 System category (according to EN ISO 13849) 23
4.3 Safety working modes and safety functions 25
4.4 Safety working mode: Both (default) 29
4.5 Safety working mode: Always access detection 30
4.6 Safety working mode: Always restart prevention 30
4.7 Features of the restart prevention function 30
4.8 Muting 32
4.9 Anti-tampering functions:anti-rotation around axes (accelerometer) 33
4.10 Anti-tampering functions:anti-masking 34
4.11 Multi-controller Synchronization 35
5. Sensor position 37
5.1 Basic concepts 37
5.2 Sensor field of view 38
5.3 Dangerous area calculation 39
5.4 Calculation of position for sensor height ≤ 1 m 40
5.5 Calculation of position for sensor height > 1 m 45
5.6 Outdoor installations 46
6. Installation and use procedures 48
6.1 Before installation 48
6.2 Install and configure LBK System BUS 49
6.3 Validate the safety functions 54
6.4 Manage the configuration 56
6.5 Other functions 57
7. Maintenance and troubleshooting 58
7.1 Troubleshooting 58
7.2 System log 60
7.3 Cleaning and spare parts 63
7.4 Updates 63
8. Technical references 64
8.1 Technical data 65
8.2 Terminal blocks and connector pin-outs 67
8.3 Electrical connections 69
8.4 Parameters 74
8.5 Digital input signals 75
9. Appendix 78
9.1 Disposal 78
9.2 Service and warranty 78
LBK System BUS| Instruction manual v1.0 SEP 2020 |LBK-System-BUS_instructions_en v1.0|© 2020 Inxpect SpA iii

iv LBK System BUS| Instruction manual v1.0 SEP 2020 |LBK-System-BUS_instructions_en v1.0|© 2020 Inxpect SpA
Glossary of terms
1
1oo2
(one out of two) Type of multi-channel architecture where one area is monitored by two sensors at the
same time.
A
Activated output (ON-state)
Output that switches from OFF to ON-state.
Angular coverage
Property of the field of view that corresponds to the coverage of 110° or 50° on the horizontal plane.
D
Dangerous area
Area to be monitored because it is dangerous for people.
Deactivated output (OFF-state)
Output that switches from ON to OFF-state.
Detection distance 1
Depth of the field of view configured for detection field 1.
Detection distance 2
Depth of the field of view configured for detection field 2.
Detection field 1
Area of the fieldset closer to the sensor. In the absence of detection field 2, it corresponds to the
whole fieldset.
Detection field 2
Area of the fieldset that follows detection field 1.
Detection signal 1
Output signal that describes the monitoring status of detection field 1.
Detection signal 2
Output signal that describes the monitoring status of detection field 2.
Glossary of terms

E
ESPE (Electro-Sensitive Protective Equipment)
Device or system of devices used for the safety-related detection of people or parts of the body. ESPEs
provide personal protection at machines and plants/systems where there is a risk of physical injury.
These devices/systems cause the machine or plant/system to switch over to a safe status before a
person is exposed to a dangerous situation.
F
Field of view
Sensor area of vision characterized by a specific angular coverage.
Fieldset
Structure of the field of view which can be composed of one or two detection fields.
FMCW
Frequency Modulated Continuous Wave
I
Inclination
Sensor rotation around the transverse axis. The sensor inclination is the angle between the center of
the field of view of the sensor and a line parallel to the ground.
M
Machinery
The system for which the dangerous area is monitored.
Monitored area
Area that is monitored by the system. It is composed of detection field 1 (e.g. used as alarm area) and
detection field 2 (e.g. used as warning area) of all the sensors.
O
OSSD
Output Signal Switching Device
T
Tolerance area
Area of the field of view where detection or not of an object depends on the characteristics of the same
object.
Glossary of terms
LBK System BUS| Instruction manual v1.0 SEP 2020 |LBK-System-BUS_instructions_en v1.0|© 2020 Inxpect SpA v

1. This manual
1.1 Information on this manual
1.1.1 Objectives of this instruction manual
This manual explains how to integrate LBK System BUS for safeguarding machinery operators and how to
install it, use it and maintain it safely.
The functioning and safety of the machinery to which LBK System BUS is connected is out of the scope of this
document.
1.1.2 Obligations with regard to this manual
NOTICE: this manual is an integral part of the product and must be kept for its entire working life.
It must be consulted for all situations related to the life cycle of the product, from its delivery to
decommissioning.
It must be stored so that it is accessible to operators, in a clean location and in good condition.
In the event of manual loss or damage, contact Customer Assistance Service.
Always enclose the manual when the equipment is sold.
1.1.3 Provided documentation
Document Code Date Distribution format
Instruction manual (this
manual)
LBK-System-BUS_
instructions_en v1.0
SEP
2020
online PDF
PDF downloadable from the site
www.inxpect.com/industrial/tools
Instruction manual to interact
with Inxpect Safety
LBK-app_instructions_
en v1.4
JAN
2020
the online help accessible from the
application Inxpect Safety
1.1.4 Instruction manual updates
Publication
date Code Hardware
version
Firmware
version Updates
SEP 2020 LBK-System-BUS_instructions_en
v1.0
lISC-B01: 2.1
lLBK-S01: 1.2
lISC-B01:
1.1.0
lLBK-S01:
2.10
First
publication
1.1.5 Intended users of this instruction manual
The recipients of the instruction manual are:
lThe machinery manufacturer onto which the system will be installed
lSystem installer
lMachinery maintenance technician
6LBK System BUS| Instruction manual v1.0 SEP 2020 |LBK-System-BUS_instructions_en v1.0|© 2020 Inxpect SpA

LBK System BUS| Instruction manual v1.0 SEP 2020 |LBK-System-BUS_instructions_en v1.0|© 2020 Inxpect SpA 7
2. SAFETY
2.1 Safety information
2.1.1 SAFETY MESSAGES
Warnings related to safety of the user and equipment as envisaged in this document are as follows:
WARNING! indicates a hazardous situation which, if not avoided, may cause death or serious
injury.
NOTICE: indicates obligations that if not observed may cause harm to the equipment.
2.1.2 Safety symbols on the product
This symbol marked on the product indicates that the manual must be consulted. In particular, pay
attention to the following activities:
lwiring of the connections (see "Terminal blocks and connector pin-outs" on page67 and "Electrical
connections" on page69)
lcable operating temperature (see "Terminal blocks and connector pin-outs" on page67)
lcontroller cover, which was subjected to an impact test at low energy (see "Technical data" on
page65)
2.1.3 PERSONNEL SKILLS
The recipients of this manual and the skills required for each activity presented herein are as follows:
Recipient Assignments Skills
Machinery
manufacturer
lDefines which protective devices
should be installed and installation
specifications
lKnowledge of significant hazards of the
machinery that must be reduced based on
risk assessment.
lKnowledge of the entire machinery safety
system and the system on which it is
installed.
Protection
system installer
lInstalls the system
lConfigures the system
lPrints configuration report
lAdvanced technical knowledge in the
electrical and industrial safety fields
lKnowledge of the dimensions of the
dangerous area of the machinery to be
monitored
lReceives instructions from the machinery
manufacturer
Machinery
maintenance
technician
lPerforms maintenance on the system lAdvanced technical knowledge in the
electrical and industrial safety fields
2.1.4 INTENDED USE
LBK System BUS is certified SIL 2 according to IEC/EN 62061 and PL d in accordance with EN ISO 13849-1.
Performs the following safety functions:
laccess detection function: prevents access to a dangerous area. Access to the area deactivates the
safety outputs to stop the moving parts of the machinery.
lrestart prevention function: prevents unexpected starting or restarting of the machinery. Detection of
motion within the dangerous area maintains the safety outputs deactivated to prevent machinery
starting.
LBK System BUS is suitable for protecting the entire body.
LBK System BUS has been designed to monitor dangerous areas in industrial environments. Thanks to IP67
protection grade, the sensors are suitable for indoor and outdoor installations. The sensor LBK-S01 is also a
type 3 enclosure, according to UL 50E.

8LBK System BUS| Instruction manual v1.0 SEP 2020 |LBK-System-BUS_instructions_en v1.0|© 2020 Inxpect SpA
2.1.5 GENERAL WARNINGS
lIncorrect installation and configuration of the system decreases or inhibits the protective function of the
system. Follow the instructions provided in this manual for correct installation, configuration and validation
of the system.
lChanges to the system configuration may compromise the protective function of the system. After any
changes made to the configuration, validate correct functioning of the system by following the instructions
provided in this manual.
lIf the system configuration allows access to the dangerous area without detection, implement additional
safety measures (e.g. guards).
lThe presence of static objects, in particular metallic objects, within the field of view may limit the efficiency
of sensor detection. Keep the sensor field of view unobstructed.
lThe system protection level (SIL 2, PL d) must be compatible with the requirements set forth in the risk
assessment.
lCheck that the temperature of the areas where the system is stored and installed is compatible with the
storage and operating temperatures indicated in the technical data of this manual.
2.1.6 WARNINGS FOR THE RESTART PREVENTION FUNCTION
lThe restart prevention function is not guaranteed in blind spots. If required by the risk assessment,
implement adequate safety measures in those areas.
lMachinery restarting must be enabled only in safe conditions. The restart enable button must be installed:
ooutside of the dangerous area
onot accessible from the dangerous area
oin a point where the dangerous area is fully visible
2.1.7 RESPONSIBILITY
The machinery manufacturer and system installer are responsible for the operations listed below:
lProviding adequate integration of the safety output signals of the system.
lChecking the monitored area of the system and validating it based on the needs of the application and
risk assessment. Following the instructions provided in this manual.
2.1.8 LIMITS
lThe system cannot detect the presence of people who are immobile and not breathing or objects within the
dangerous area.
lThe system does not offer protection from pieces ejected from the machinery, from radiation, and objects
falling from above.
lThe machinery command must be electronically controlled.

LBK System BUS| Instruction manual v1.0 SEP 2020 |LBK-System-BUS_instructions_en v1.0|© 2020 Inxpect SpA 9
2.2 Conformity
2.2.1 STANDARDS AND DIRECTIVES
Directives 2006/42/EC (MD - Machinery)
2014/53/EU (RED - Radio equipment)
Standards IEC/EN 62061: 2005 SIL 2
EN ISO 13849-1: 2015 PL d
EN ISO 13849-2: 2012
IEC/EN 61496-1: 2013
IEC/EN 61508: 2010 Part 1-7 SIL 2
ETSI EN 300 440 v2.1.1
ETSI EN 301 489-1 v2.2.0 (only emissions)
ETSI EN 301 489-3 v2.1.1 (only emissions)
IEC/EN 61326-3-1:2017
IEC/EN 61010-1: 2010
EN 61784-3-3 for the PROFIsafe Fieldbus
Note: no type of failure has been excluded during the system analysis and design phase.
The EUDeclaration of Conformity can be downloaded from www.inxpect.com.
2.3 National restrictions
2.3.1 FRANCE AND THE UNITED KINGDOM
LBK System BUS is a short-range device in class 2 in accordance with the directive 2014/53/EU (RED - Radio
equipment) and is subject to the following restrictions:
FR UK
en Restrictions in UK. In the United Kingdom, the national allocation of frequencies does not allow the
free use of the whole band 24-24.25 GHz. Set the country correctly in the Inxpect Safety application and the
authorized band 24.05-24.25 GHz will be automatically selected.
fr Restrictions en FR. En France, la répartition nationale des fréquences ne permet pas l'utilisation libre
de la totalité de la bande 24-24,25 GHz. Définissez correctement le pays dans l'application Inxpect Safety et la
bande autorisée 24,05-24,25 GHz sera automatiquement sélectionnée.
2.3.2 JAPAN
en Restrictions in Japan. In Japan, the national allocation of frequencies does not allow the free use of
the whole band 24-24.25 GHz. Set the country correctly in the Inxpect Safety application and the authorized
band 24.05-24.25 GHz will be automatically selected.
ja 日 本 における制 限 。日 本 では、全 国 的 な周 波 数 割 り当 てでは、24〜24.25 GHzの全帯域を自由に使用
することはできません。Inxpect Safetyアプリケーションで国 を正 しく設 定 すると、許 可 された帯 域 24.05-24.25 GHzが
自 動 的 に選 択 されます。

10 LBK System BUS| Instruction manual v1.0 SEP 2020 |LBK-System-BUS_instructions_en v1.0|© 2020 Inxpect SpA
2.3.3 SOUTH KOREA
en Restrictions in South Korea. In South Korea, the national allocation of frequencies does not allow the
free use of the whole band 24-24.25 GHz. Set the country correctly in the Inxpect Safety application and the
authorized band 24.05-24.25 GHz will be automatically selected.
ko 한국의 제한.한국에서는 국가의 주파수 할당 규정에 따라 24-24.25 GHz 전체 주파수 대역을 무료로 사용하
는 것을 허용하지 않는다. Inxpect Safety 응용프로그램에서 올바른 국가를 설정하면 승인된 대역 24.05-24.25 GHz
가 자동으로 선택된다.
2.3.4 ARGENTINA
en Restrictions in Argentina. In Argentina, the national allocation of frequencies does not allow the free
use of the whole band 24-24.25 GHz. Set the country correctly in the Inxpect Safety application and the
authorized band 24.05-24.25 GHz will be automatically selected.
es-AR Restricciones en Argentina. La atribución de las bandas de frecuencia en la República Argentina no
permite el uso libre de toda la banda de 24-24,25 GHz. Configure correctamente el país en la aplicación
Inxpect Safety y la banda autorizada 24,05-24,25 GHz se seleccionará automáticamente.
2.3.5 MEXICO
en Restrictions in Mexico. In Mexico, the national allocation of frequencies does not allow the free use of
the whole band 24-24.25 GHz. Set the country correctly in the Inxpect Safety application and the authorized
band 24.05-24.25 GHz will be automatically selected.
es-MX Restricciones en México. La atribución de las bandas de frecuencia en México no permite el uso libre
de toda la banda de 24-24,25 GHz. Configure correctamente el país en la aplicación Inxpect Safety y la banda
autorizada 24,05-24,25 GHz se seleccionará automáticamente.
2.3.6 CHINA
en Restrictions in China. Use in China is strictly linked to compliance with the temperature range of
operation, which can not fall below 0° C or 32° F.
zh-CN 中国的限制。在中国使用须严格符合操作温度范围,不能低于0°C或32°F。

3. Get to know LBK System BUS
Contents
This section includes the following topics:
3.1 LBK System BUS 11
3.2 Controller ISC-B01 13
3.3 Sensors LBK-S01 16
3.4 Inxpect Safety application 17
3.5 Fieldbus communication 18
3.6 System configuration 19
3.0.1 Product label description
The following table describes the information contained in the product label:
Part Description
DC "yy/ww" : year and week of the product manufacture
SRE Safety Radar Equipment
Model Model of the product (e.g. LBK-S01, ISC-B01)
Type Product variant, used for commercial purposes only
S/N Serial number
3.1 LBK System BUS
3.1.1 Definition
LBK System BUS is an active protection radar system that monitors the dangerous areas of machinery.
3.1.2 Special features
Some of the special features of this protection system are the following:
limmunity to dust and smoke
lreduction of undesired alarms caused by the presence of water or processing waste
lpossibility to configure a second safe detection field (e.g. used as warning area) to signal proximity or
prepare the machinery for stopping
lthree configurable sensitivity levels
lmuting on the entire system or only on some sensors
lEthernet safety Fieldbus to safely communicate with the PLC of the machinery (only if the controller
supports the safety communication on the Fieldbus interface)
LBK System BUS| Instruction manual v1.0 SEP 2020 |LBK-System-BUS_instructions_en v1.0|© 2020 Inxpect SpA 11

12 LBK System BUS| Instruction manual v1.0 SEP 2020 |LBK-System-BUS_instructions_en v1.0|© 2020 Inxpect SpA
3.1.3 Main components
LBK System BUS is composed of a controller and up to six sensors. The Inxpect Safety software application
allows system operation configuration and checks.
3.1.4 Controller - sensors communication
The sensors communicate with the controller via CAN bus using diagnostic mechanisms in compliance with
standard EN 50325-5 to guarantee SIL 2 and PL d.
For correct functioning, each sensor must be assigned an identification (Node ID).
Sensors on the same bus must have different Node IDs. By default, the sensor does not have a pre-assigned
Node ID.
3.1.5 Controller - machinery communication
Starting from firmware version 1.2.0, the controller is provided with a safety communication on a Fieldbus
interface. The Fieldbus interface allows the ISC-B01 controller to communicate in real-time with the PLC of the
machinery in order to do what follows:
lsend information about the system to the PLC (e.g. the position of the detected target)
lreceive information from the PLC to change the configuration dynamically
See "Fieldbus communication" on page18.
3.1.6 Applications
LBK System BUS integrates with the machinery control system: when performing safety functions or detecting
failures, LBK System BUS deactivates the safety outputs and keeps them deactivated, so the control system
can put the area into a safe condition and/or prevent restarting of the machinery.
In the absence of other control systems, LBK System BUS can be connected to the devices that control the
power supply or machinery start-up.
LBK System BUS does not perform normal machinery control functions.
For connection examples, see "Electrical connections" on page69.
3. Get to know LBK System BUS

3.2 Controller ISC-B01
3.2.1 Functions
The controller performs the following functions:
lCollects information from all the sensors via CAN bus.
lCompares the position of detected motion with the set thresholds.
lDeactivates the safety output when at least one sensor detects motion in the detection field.
lDeactivates the safety output if a failure is detected in one of the sensors or the controller.
lManages the inputs and outputs.
lCommunicates with the Inxpect Safety application for all configuration and diagnostic functions.
lAllows dynamically switching between different configurations.
lCommunicates with a safety PLC through Fieldbus connection*
Note*: only if the controller supports the safety communication on the Fieldbus interface. For details, see "Safety Fieldbus
support" on page18.
3.2.2 Structure
Part Description
AI/O terminal block
BSensor status LEDs
CNetwork parameter reset button
DOutput reset button
EMicro-USB port for connecting the PC and communicating with the Inxpect Safety
application
FMicro-USB port (reserved)
GFieldbus status LEDs (Ethernet)
HEthernet port with LEDs for connecting the PC and communicating with the Inxpect Safety
application
IPower supply terminal block
JError LEDs
KSensor CAN bus terminal block
LDIP switch for turn on/off the termination
MCPU LEDs
3. Get to know LBK System BUS
LBK System BUS| Instruction manual v1.0 SEP 2020 |LBK-System-BUS_instructions_en v1.0|© 2020 Inxpect SpA 13

14 LBK System BUS| Instruction manual v1.0 SEP 2020 |LBK-System-BUS_instructions_en v1.0|© 2020 Inxpect SpA
Part Description
NEthernet Fieldbus port n. 1 with LEDs
OEthernet Fieldbus port n. 2 with LEDs
3.2.3 Sensor status LEDs
The LEDs are each dedicated to a sensor, and can display the following statuses:
Status Meaning
Steady green Normal sensor function and no motion detected in the monitored area
Orange Normal sensor function and some motion detected in the monitored area
Flashing red Sensor in error. See "Controller LED" on page58
Steady red System error. See "Controller LED" on page58
Flashing green Sensor in boot status. See "Controller LED" on page58
3.2.4 Fieldbus status LEDs (Ethernet)
Note: only if the controller supports the safety communication on the Fieldbus interface. For details, see "Safety Fieldbus
support" on page18.
The meaning of the LEDs depends on the protocol in use. For details, refer to the proper safety Fieldbus
manual.
3.2.5 Inputs
The system has two digital inputs type3 (according to EN 61131-2). Each digital input is dual channel, and the
ground reference is common for all the inputs (for details, see "Technical references" on page64).
When using digital inputs, it is mandatory that the additional SNS input "V+ (SNS)" is connected to 24 V dc and
that the GND input "V- (SNS)" is connected to the ground in order to:
lperform the correct input diagnostic
lassure the system safety level
The function of each digital input must be programmed through the Inxpect Safety application. The available
functions are the following:
lStop signal: manages a specific signal to force all the safety outputs (detection signal 1 and detection signal
2, if present) to OFF-state.
lRestart signal: manages a specific signal which enables the controller to switch the safety outputs related
to all the detection fields that are free of movements to ON-state.
lMuting group “N”: manages a specific signal which allows the controller to ignore the information coming
from a selected group of sensors.
lActivate dynamic configuration: allows the controller to select a specific dynamic configuration.
lFieldbus controlled*: monitors the input status through Fieldbus communication. A generic ESPE can be
connected to the input, respecting electrical specifications.
lAcquisition Trigger**: manages a specific signal which allows to use the Multi-controller Synchronization
(for details, see "Multi-controller Synchronization" on page35).
Note*: only if the controller supports the safety communication on the Fieldbus interface. For details, see "Safety Fieldbus
support" on page18.
Note**: only if the Inxpect Safety application supports the functionality.
For details about digital input signals, see "Digital input signals" on page75.
3.2.6 SNS input
The controller also has an SNS input (high logic level (1) = 24 V) to check the correct functioning of the chip
that detects the status of the inputs.
NOTICE: if at least one input is connected, the SNS input "V+ (SNS)" and the GND input "V- (SNS)" must also
be connected.
3.2.7 Outputs
The system has four digital OSSD short-circuit protected outputs that can be used individually (non safe) or
can be programmed as dual channel safety outputs (safe) in order to ensure the system safety level.
3. Get to know LBK System BUS

An output is activated when it switches from OFF to ON-state and it is deactivated when it switches from ON to
OFF-state.
The function of each digital output must be programmed through the Inxpect Safety application.
The available functions are the following:
lSystem diagnostic signal: switches the selected output to OFF-state when a system fault is detected.
lMuting enable feedback signal: switches the selected output to ON-state in the following cases:
owhen a muting signal is received over the configured input and at least one group is in muting
owhen a muting command is received through Fieldbus communication* and at least one group is in
muting
lDetection signal 1: (e.g. alarm signal) switches the selected output to OFF-state when a sensor detects
motion in detection field 1, or when a stop signal is received from the related input. The selected output
remains in OFF-state for at least 100 ms.
Note: when an OSSD is configured as detection signal 1, a second OSSD is automatically assigned to it to provide a safe
signal.
lDetection signal 2: (e.g. warning signal) switches the selected output to OFF-state when a sensor detects a
motion in detection field 2, or when a stop signal is received from the related input. The selected output
remains in OFF-state for at least 100 ms.
Note: when an OSSD is configured as detection signal 2, a second OSSD is automatically assigned to it to provide a safe
signal.
lFieldbus controlled: allows setting the specific output through the Fieldbus communication*.
lRestart Feedback signal: switches the selected output to ON-state when it is possible to restart the system
safely using the dedicated input (Restart signal). In case of:
oautomatic restart prevention, the dedicated output is always in OFF-state;
omanual restart prevention, the dedicated output remains in OFF-state as long as a movement is detected
in the monitored area; then it is activated (ON-state) and the ON-state lasts as long as the entire
monitored area is free of movements and until the Restart Signal is activated on the dedicated input;
osafe manual restart prevention, the dedicated output remains in OFF-state as long as a movement is
detected in the monitored area; then it is activated (ON-state) if the entire monitored area is free of
movements (each detection field for its consecutive Restart timeout). The ON-state lasts as long as the
area remains free of movements and until the Restart Signal is activated on the dedicated input.
Each output status can be retrieved by Fieldbus communication*.
Note*: only if the controller supports the safety communication on the Fieldbus interface. For details, see "Safety Fieldbus
support" on page18.
The system installer can decide to configure the system as follows:
ltwo dual channel safety outputs (e.g. detection signal 1 and detection signal 2, usually alarm and warning
signals), or
lone dual channel safety output (e.g. detection signal 1) and two single channel output (e.g. system
diagnostic and muting enable feedback), or
leach output as a single output (e.g. system diagnostic, muting enable feedback and two Fieldbus controlled
outputs).
The dual channel safety output is automatically obtained by the Inxpect Safety application and it matches the
single OSSD outputs only as follows:
lOSSD 1 with OSSD 2
lOSSD 3 with OSSD 4
In the dual channel safety output, the output status is the following:
lactivated output (24 V dc): no motion detected and normal functioning
ldeactivated output (0 V dc): motion detected in the detection field or failure detected in the system
Idle signal is 24 V dc, periodically shortly pulsed to 0 V (pulses are not synchronous) for the receiver to detect
shortcut to either 0 V or 24 V.
3. Get to know LBK System BUS
LBK System BUS| Instruction manual v1.0 SEP 2020 |LBK-System-BUS_instructions_en v1.0|© 2020 Inxpect SpA 15

16 LBK System BUS| Instruction manual v1.0 SEP 2020 |LBK-System-BUS_instructions_en v1.0|© 2020 Inxpect SpA
For details, see "Technical references" on page64.
3.3 Sensors LBK-S01
3.3.1 Functions
The sensors perform the following functions:
lDetect motion in their field of view.
lSend the motion detection signal to the controller through CAN bus.
lSignal to the controller through CAN bus the failures or faults detected on the sensor during diagnostics.
3.3.2 Structure
Part Description
ASensor
BScrews for fastening the sensor at a specific inclination
CPerforated bracket for installing the sensor on the ground or on the machinery
DStatus LED
EConnectors for connecting the sensors in a chain and to the controller
3. Get to know LBK System BUS

3.3.3 Status LED
Status Meaning
Steady on Normal functioning and no motion detected
Rapid flashing on (100 ms) Normal functioning and motion detected
Other conditions Error. See "Sensor LED" on page58
3.4 Inxpect Safety application
3.4.1 Functions
The application permits the following main functions to be performed:
lConfigure the system.
lCreate the configuration report.
lCheck system functioning.
lDownload system log.
WARNING! The Inxpect Safety application must be used only for the system configuration and
for the first validation. It cannot be used for monitoring the system continuously during the
regular operation of the machinery.
3.4.2 Access
The application can be downloaded free of charge at www.inxpect.com/industrial/tools.
To use the application, the computer must be connected to a ISC-B01 controller using a data micro-USB cable
or an Ethernet cable.
Some functions are password protected. The admin password can be set through the application and then
saved on the controller. The available functions according to access type are presented as follows:
Available functions Access type
lDisplay the system status (Dashboard)
lDisplay the sensors configuration (Configuration)
lRestore factory default settings, if not using Ethernet connection (Configuration >
Settings >General)
lBack up the configuration (Configuration >Settings >General)
without password
lValidate the system (Validation)
lRestore factory default settings, if using Ethernet connection (Configuration >
Settings >General)
lDownload the system log and display reports (Configuration >Settings >Activity
History)
lConfigure the system (Configuration)
lLoad a configuration (Configuration >Settings >General)
lChange the admin password (Configuration >Settings >Account)
lUpdate the firmware (Configuration >Settings >General)
lShow and change the network parameters (Configuration >Network Parameters)
lShow and change the Fieldbus parameters (Configuration >Fieldbus Parameters)
with password
3. Get to know LBK System BUS
LBK System BUS| Instruction manual v1.0 SEP 2020 |LBK-System-BUS_instructions_en v1.0|© 2020 Inxpect SpA 17

18 LBK System BUS| Instruction manual v1.0 SEP 2020 |LBK-System-BUS_instructions_en v1.0|© 2020 Inxpect SpA
3.4.3 Main menu
Page Function
Dashboard Display main information on the configured system.
Configuration Define the configuration of the sensors and monitored area.
Start the validation procedure.
Configure the sensors.
Configure the inputs and outputs function.
Update the firmware.
Perform the configuration backup and load a configuration.
Configure network parameters.
Configure Fieldbus parameters.
Download the log.
Show and change the network parameters.
Show and change the Fieldbus parameters.
Other general functions.
REFRESH
CONFIGURATION
Refresh configuration or ignore unsaved changes.
User Enable access to the configuration functions. Admin password required.
Disconnect Close the connection with the device and allow to connect to another device.
Change the language.
3.5 Fieldbus communication
3.5.1 Safety Fieldbus support
The safety communication on the Fieldbus interface is supported from controller firmware version 1.2.0.
If the controller firmware version is 1.1.0, the controller can manage the system safety functions only through
digital inputs and outputs.
Please refer to the Inxpect Safety application to check the controller firmware version.
3.5.2 Communication with the machinery
The Fieldbus makes the following actions possible:
lto choose from 1 to 32 preset configurations dynamically
lto read the status of the inputs
lto control the outputs
lto mute the sensors
3.5.3 Data exchanged through Fieldbus
The following table details the data exchanged through the Fieldbus communication:
3. Get to know LBK System BUS

Data
type Description Communication
direction
Safe SYSTEM STATUS DATA
ISC-B01 controller:
linternal status, used to check for errors on the controller
lreal time status of each of the four outputs
lreal time status of each of the two inputs
LBK-S01 sensor:
lstatus of each detection field (target detected or not) or error status
lmuting status
from the
controller
Safe SYSTEM SETTING COMMAND
ISC-B01 controller:
lset the ID of the dynamic configuration that shall be activated
lset the status of each of the four outputs
lfix the current accelerometer information
LBK-S01 sensor:
lset the muting status
to the controller
Safe DYNAMIC CONFIGURATION STATUS
lID of the dynamic configuration currently active
lsignature (CRC32) of the dynamic configuration ID currently active
from the
controller
Safe TARGET DATA
Current distance of the targets detected by each sensor connected to the
controller. For each sensor, only the closest target to the sensor is considered.
from the
controller
Unsafe SYSTEM EXTENDED STATUS
ISC-B01 controller:
linternal status with an extended description of the error condition
LBK-S01 sensor:
linternal status with an extended description of the error condition
from the
controller
3.6 System configuration
3.6.1 System configuration
The controller parameters have their own default values that can be modified via the Inxpect Safety
application (see "Parameters" on page74).
3.6.2 Dynamic system configuration
LBK System BUS allows a real-time adjustment of the most important system parameters, providing the
means to switch dynamically among different preset configurations. Via the Inxpect Safety application, once
the first system configuration (default configuration) has been set, it is possible to set up to 31 alternative
presets to allow a dynamic real-time reconfiguration of the monitored area.
The following parameters are part of each of these alternative presets:
ldetection field 1 and 2, for each sensor
langular coverage (50° or 110° on the horizontal plane), for each sensor
lrestart timeout, for each detection field of each sensor
lsafety working mode (Both (default),Always access detection or Always restart prevention), for each
detection field, for each sensor (see "Safety working modes and safety functions" on page25)
All the remaining system parameters cannot be changed dynamically and are considered static.
3.6.3 Dynamic system configuration activation
The dynamic system configuration can be activated through the digital inputs or the safety Fieldbus (from
3. Get to know LBK System BUS
LBK System BUS| Instruction manual v1.0 SEP 2020 |LBK-System-BUS_instructions_en v1.0|© 2020 Inxpect SpA 19

20 LBK System BUS| Instruction manual v1.0 SEP 2020 |LBK-System-BUS_instructions_en v1.0|© 2020 Inxpect SpA
1.2.0 firmware version). Depending on this choice, it will be possible to switch dynamically among two, four or
32 alternative preset configurations.
3.6.4 Inxpect Safety application usage
To use the application, the controller must be connected to a computer with a data micro-USB cable or an
Ethernet cable. The USB cable allows to configure the system locally, whereas the Ethernet cable allows to do
it remotely.
The Ethernet communication between the ISC-B01 and the Inxpect Safety application is secured by the most
advanced security protocols (TLS).
3.6.5 Dynamic configuration through the digital inputs
To activate the dynamic system configuration, one or both the digital inputs of the ISC-B01 controller can be
used. The result is the following:
If... Then it is possible to dynamically switch
between...
only one digital input is used for the dynamic
configuration
two preset configurations (see "Example 1" below
and "Example 2" below)
both digital inputs are used for the dynamic
configuration
four preset configurations (see "Example 3" below)
Example 1
The first digital input has been linked to the dynamic configuration.
Configuration Input 1 Input 2
Dynamic configuration #1 0-
Dynamic configuration #2 1-
0 = signal deactivated; 1 = signal activated
Example 2
The second digital input has been linked to the dynamic configuration.
Configuration Input 1 Input 2
Dynamic configuration #1 - 0
Dynamic configuration #2 - 1
0 = signal deactivated; 1 = signal activated
Example 3
Both digital inputs have been linked to the dynamic configuration.
Configuration Input 1 Input 2
Dynamic configuration #1 0 0
Dynamic configuration #2 1 0
Dynamic configuration #3 0 1
Dynamic configuration #4 1 1
0 = signal deactivated; 1 = signal activated
3.6.6 Dynamic configuration through the safety Fieldbus
To activate the dynamic system configuration, connect an external safety PLC that communicates through the
safety Fieldbus to the ISC-B01 controller. This makes it possible to dynamically switch between all the preset
configurations, therefore up to 32 different configurations. For all the parameters used for each configuration,
see "Dynamic system configuration" on the previous page.
For details about the supported protocol, please refer to the Fieldbus manual.
3. Get to know LBK System BUS
Table of contents
Other Inxpect Security Sensor manuals
Popular Security Sensor manuals by other brands
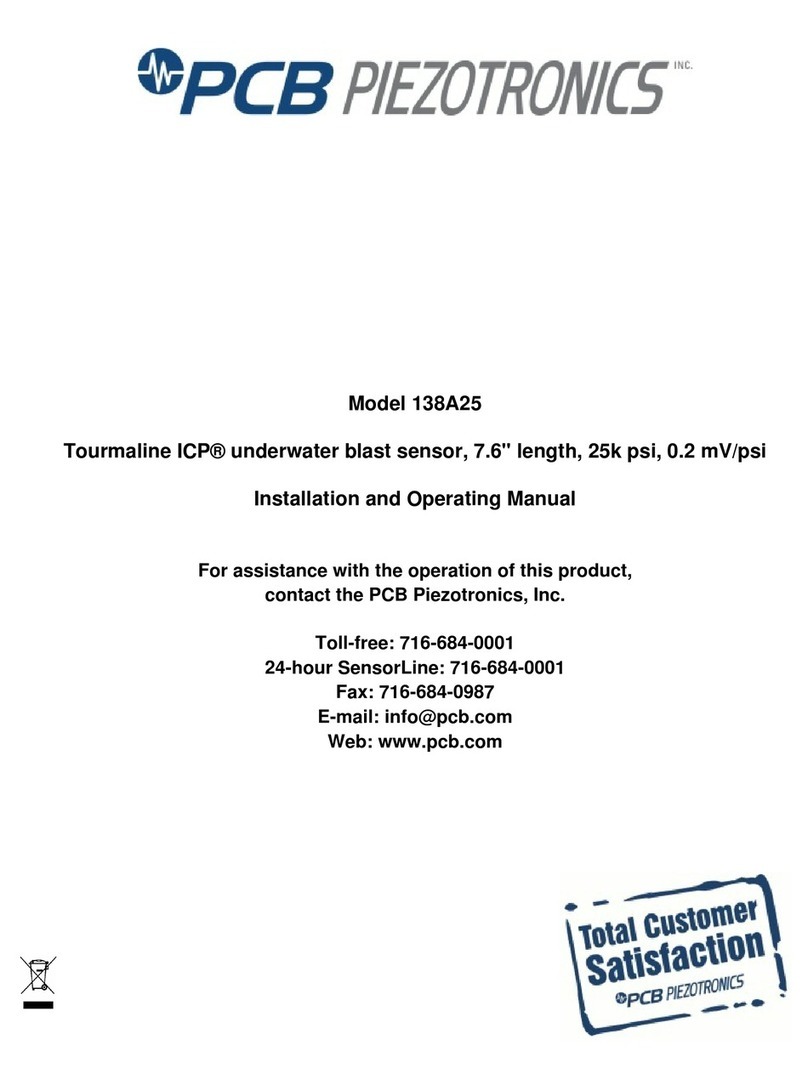
PCB Piezotronics
PCB Piezotronics 138A25 Installation and operating manual
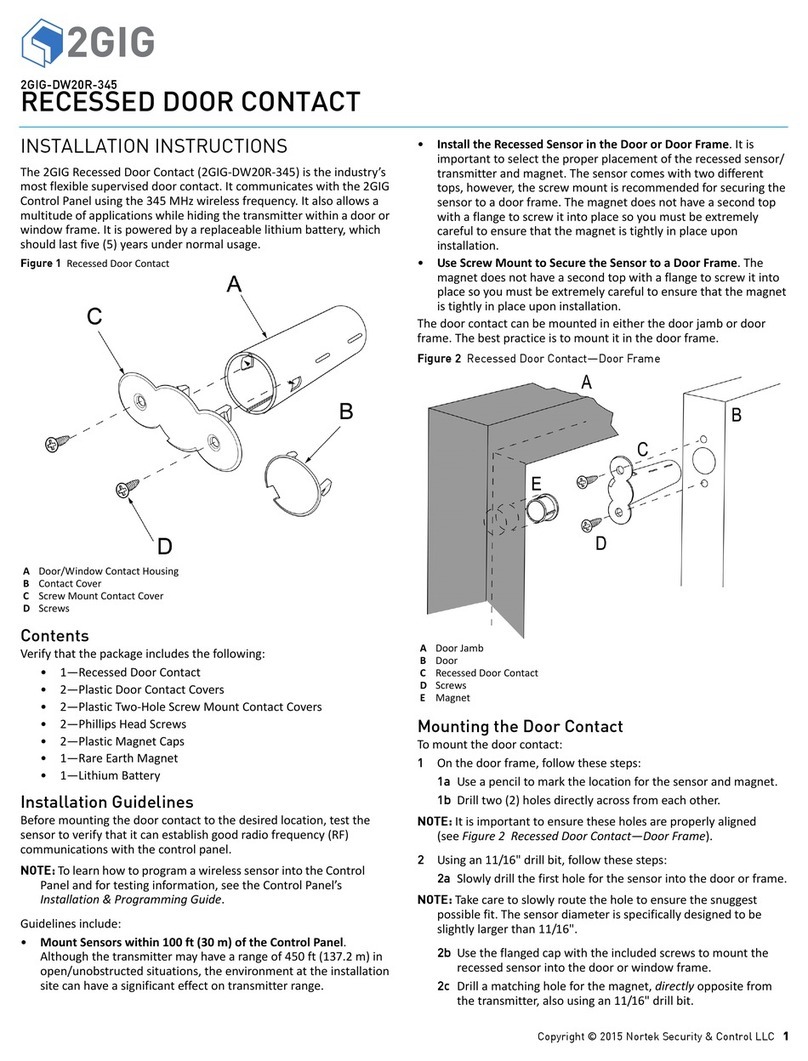
Nortek Security & Control
Nortek Security & Control 2GIG-DW20R-345 installation instructions
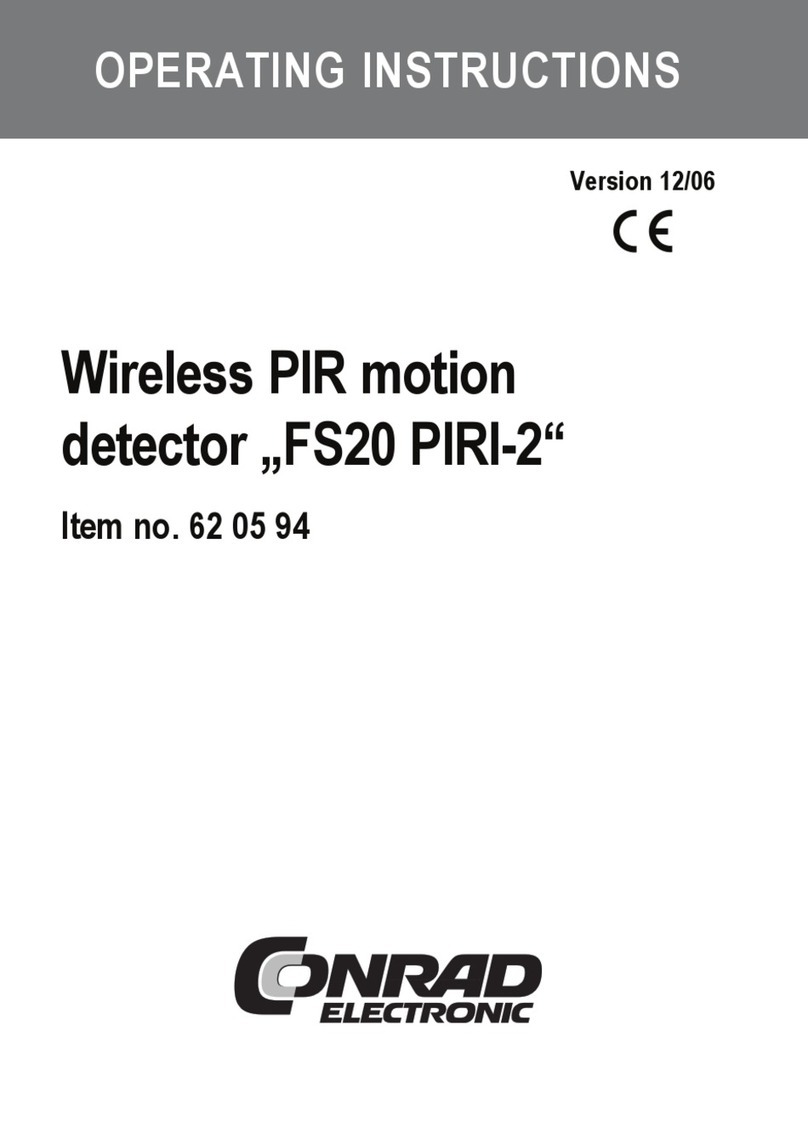
Conrad Electronic
Conrad Electronic FS20 PIRI-2 operating instructions

Eagle Eye Power Solutions
Eagle Eye Power Solutions GFL-1000 user manual
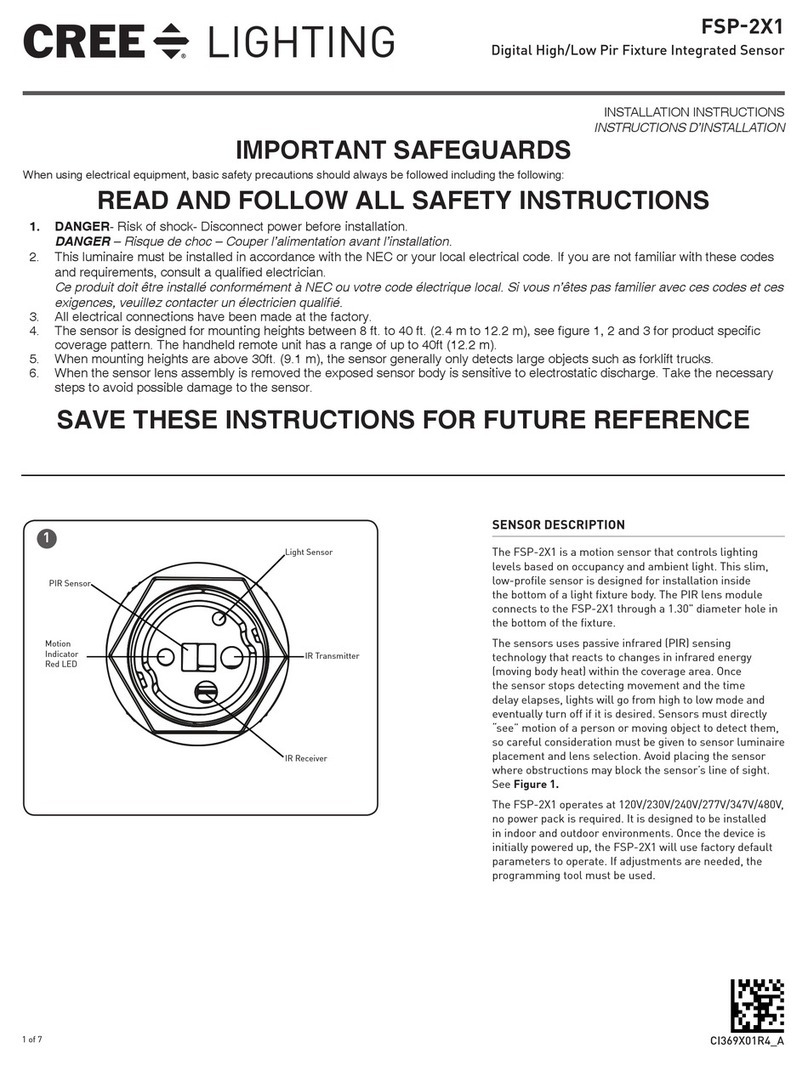
CREE LIGHTING
CREE LIGHTING FSP-2X1 installation instructions
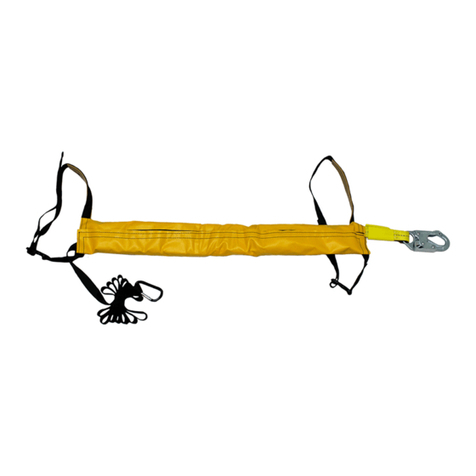
Buckingham
Buckingham 102SR Series Instructions & warnings