Kia Carnival 2009 Configuration guide

Engine Electrical System
General Information
Engine ,SLJ[YPcal System

2009 > G 2.7 DOHC >
THE MICRO 570 ANALYZER
The MICRO 570 Analyzer provides the ability to test the charging and starting systems, including the battery, starter
and generator.
Because of the possibility of personal injury, always use extreme caution and appropriate eye protection when
working with batteries.
KEYPAD
The MICRO570 button on the key pad provides the following functions :
BATTERY TEST PROCEDURE
1. Connect the tester to the battery.
A. Red clamp to battery positive (+) terminal.
B. Black clamp to battery negative (-) terminal.
Connect clamps securely. If "CHECK CONNECTION" message is displayed on the screen, reconnect clamps
securely.

2. The tester will ask if the battery is connected "IN A VEHICLE" or "OUT OF A VEHICLE". Make your selection by
pressing the arrow buttons; then press ENTER.
3. Choose either CCA or CCP and press the ENTER button.
• CCA : Cold cranking amps, is an SAE specification for cranking batteries at -18°C (0°F).
• CCP : Cold cranking amps, is an SAE specification for korean manufacturer's for cranking batteries at -
18°C (0°F).
4. Set the CCA value displayed on the screen to the CCA value marked on the battery label by pressing up and
down buttons and press ENTER.
The battery ratings(CCA) displayed on the tester must be identical to the ratings marked on battery label.
5. The tester (Micro570) displays battery test results including voltage and battery ratings.
A relevant action must be given according to the test results by referring to the battery test results as shown in the
table below.

The battery ratings (CCA) displayed on the tester must be identical to the ratings marked on battery label.
6. To conduct starter test, press ENTER.
BATTERY TEST RESULTS
RESULT ON PRINTER REMEDY
Good battery No action is required
Good recharge Battery is in a good state
Recharge the battery and use
Charge & Retest
Battery is not charged properly
=> Charge and test the battery again (Failure to charge
the battery fully may read incorrect measurement value)
Replace battery
=> Replace battery and recheck the charging system.
(Improper connection between battery and vehicle cables
may cause "REPLACE BATTERY", retest the battery
after removing cables and connecting the tester to the
battery terminal directly prior to replacing the battery)
Bad cell-replace
=> Charge and retest the battery. And then, test results
may cause "REPLACE BATTERY", replace battery and
recheck the charging system
Whenever filing a claim for battery, the print out of the battery test results must be attached.
STARTER TEST PROCEDURE
1. After the battery test, press ENTER immediately for the starter test.

2. After pressing ENTER key, start the engine.
3. Cranking voltage and starter test results will be displayed on the screen.
Take a relevant action according to the test results by referring to the starter test results as given below.
4. To continue charging system test, press ENTER.
STARTER TEST RESULTS
RESULT ON PRINTER REMEDY
Cranking voltage normal System shows a normal starter draw
Cranking voltage low Cranking voltage is lower than normal level
=> Check starter
Charge battery
The state of battery charge is too low to test
=>Charge the battery and
retest
Replace battery
=> Replace battery
=> If the vehicle is not started though the battery
condition of "Good and fully charged" is displayed.
=> Check wiring for open circuit, battery cable connection,
starter and repair or replace as necessary.
CHARGING SYSTEM TEST PROCEDURE
1. Press ENTER to begin charging system test.

2. ENTER button is pressed, the tester displays the actual voltage of generator.
Press ENTER to test the charging system.
3. The MICRO 570 will prompt you to rev the engine until the rev detected. It will then collect the data.
4. Press ENTER.
5. The MICRO 570 will analyze the charging system output at idle for comparison to other readings.

6. The MICRO 570 will detect the amount of ripple from the charging system to the battery. Excessive ripple usually
means the stator is damaged or that one or more generator diodes have failed.
7. The MICRO 570 will prompt you to turn on accessary loads. It will then test at idle and prompt you to rev the
engine. The analyzer will determine if the charging system can provide enough current for the demands of the
vehicle's electrical system.
When asked to turn of the accessory loads, turn of the blower to high(heater), the high beam beadlights, and
rear defogger. DO NOT use cyclical loads such as air conditioning or wind-shield wipers.
8. After the test, the MICRO 570 will display the idle voltage, load voltage and the state results.

CHARGING SYSTEM TEST RESULTS
RESULT ON PRINTER REMEDY
Charging system normal/Diode ripple normal Charging system is normal
No charging voltage
Generator does not supply charging current to battery
=> Check belts, connection between generator and battery
Replace belts or cable or generator as necessary
Low charging voltage
Generator does not supply charging current to battery and electrical
load to system fully
=> Check belts and generator and replace as necessary
High charging voltage
The voltage from generator to battery is higher than normal limit
during voltage regulating.
=> Check connection and ground and replace regulator as necessary
=> Check electrolyte level in the
battery
Excess ripple detected One or more diodes in the generator is not functioning properly
=> Check generator mounting and belts and replace as necessary

2009 > G 2.7 DOHC >
SPECIAL SERVICE TOOL
Tool (Number and name) Illustration Use
Alternator pulley remover wrench
(09373-27000)
Removal and installation of alternator
pulley
REFERENCE SERVICE TOOLS
Tool (Number and name) Illustration Use
Micro-570
Battery checker
- Check the battery condition
- Check the charging and starting
system

2009 > G 2.7 DOHC >
TROUBLE SHOOTING
IGNITION SYSTEM
Symptom Suspect area Remedy
Engine will not start or
is hard to start
(Cranks OK)
Ignition lock switch Inspect ignition lock switch, or replace as required
Ignition coil Inspect ignition coil, or replace as required
Spark plugs Inspect spark plugs, or replace as required
Ignition wiring disconnected or broken Repair wiring, or replace as required
Rough idle or stalls Ignition wiring Repair wiring, or replace as required
Ignition coil Inspect ignition coil, or replace as required
Engine hesitates/poor
acceleration
Spark plugs and spark plug cables Inspect spark plugs / cable, or replace as required
Ignition wiring Repair wiring, or replace as required
Poor mileage Spark plugs and spark plug cables Inspect spark plugs / cable, or replace as required
CHARGING SYSTEM
Symptom Suspect area Remedy
Charging warning
indicator does not
light with ignition
switch "ON" and
engine off.
Fuse blown Check fuses
Light burned out Replace light
Wiring connection loose Tighten loose connection
Electronic voltage regulator Replace voltage regulator
Charging warning
indicator does not go
out with engine
running. (Battery
requires frequent
recharging)
Drive belt loose or worn Adjust belt tension or replace belt
Battery cable loose, corroded or worn Inspect cable connection, repair or replace
cable
Electronic voltage regulator or alternator Replace voltage regulator or alternator
Wiring Repair or replace wiring
Overcharge Electronic voltage regulator Replace voltage regulator
Voltage sensing wire Repair or replace wiring
Discharge Drive belt loose or worn Adjust belt tension or replace belt
Wiring connection loose or short circuit Inspect wiring connection, repair or replace
wiring
Electronic voltage regulator or alternator Replace voltage regulator or alternator
Poor grounding Inspect ground or repair
Worn battery Replace battery
STARTING SYSTEM
Symptom Suspect area Remedy
Engine will not crank Battery charge low Charge or replace battery
Battery cables loose, corroded or
worn out Repair or replace cables
Transaxle range switch (Vehicle with
automatic transaxle only) Refer to TR group-automatic transaxle

Fuse blown Replace fuse
Starter motor faulty Replace
Ignition switch faulty Replace
Engine cranks slowly Battery charge low Charge or replace battery
Battery cables loose, corroded or
worn out Repair or replace cables
Starter motor faulty Replace
Starter keeps running Starter motor Replace
Ignition switch Replace
Starter spins but engine will not
crank
Short in wiring Repair wiring
Pinion gear teeth broken or starter
motor Replace
Ring gear teeth broken Replace fly wheel or torque converter

2009 > G 2.7 DOHC >
SPECIFICATION
IGNITION SYSTEM
Items Specification
Ignition coil
Primary resistance 0.715 ± 0.015 !
Secondary
resistance -
Spark plugs NGK ILFR5B11
Plugs Gap 1.0 ~ 1.1 mm (0.0394 ~ 0.0433 in)
STARTING SYSTEM
Items Specification
Starter
Rated voltage 12 V, 1.2 kW
No. of pinion teeth 8
No-load
characteristics
Voltage 11.5 V
Ampere 90A, MAX
Speed 2,600 rpm, MIN
CHARGING SYSTEM
Items Specification
Alternator
Type Battery voltage sensing
Rate voltage 13.5 V, 110A
Speed in use 1,000 ~ 18,000 rpm
Voltage regulator Electronic built-in type
Regulator setting voltage 14.2 ~ 14.8V
Battery
Type MF 68AH
Cold cranking amperage [at -18°C(-
0.4°F)] 600 A
Reserve capacity 110 min
Specific gravity [at 20°C(68°F)] 1.280 ± 0.01
- COLD CRANKING AMPERAGE is the amperage a battery can deliver for 30 seconds and maintain a terminal
voltage of 7.2V or greater at a specified temperature.
- RESERVE CAPACITY RATING is amount of time a battery can deliver 25A and maintain a minimum terminal
voltage of 10.5V at 26.7°C(80.1°F).

Engine Electrical System
Ignition System
Engine Electrical System

2009 > G 2.7 DOHC >
DESCRITION
Ignition timing is controlled by the electronic control ignition timing system. The standard reference ignition timing data
for the engine operating conditions are preprogrammed in the memory of the ECM (Engine Control Module).
The engine operating conditions (speed, load, warm-up condition, etc.) are detected by the various sensors. Based on
these sensor signals and the ignition timing data, signals to interrupt the primary current are sent to the ECM. The
ignition coil is activated, and timing is controlled.

2009 > G 2.7 DOHC >
REMOVAL
IGNITION COIL
1. Remove the engine cover.
2. Remove the ignition coil (A).
3. Remove the ignition coil.
4. Installation is the reverse of removal.
REPLACEMENT
SPARK PLUG
1. Remove the ignition coil connector(A).
2. Remove the ignition coil.
3. Using a spark plug socket, remove the spark plug.
Be careful that no contaminates enter through the spark plug holes
4. When replacing the spark plug, always use the long reach type spark plug.
(1) Color Marking (Tip)
A. [2.7L]
Unleaded : Yellow Marking
Leaded : Green Marking
(2) Length(Tip-Tip / PT Length)
A. [2.7L]
B. 83.2mm/ 26.5mm
C. Others: The length is different from the specification above.
(3) Part ID

A. [U2.7]
L nleaded : ILFR5B11
Leaded : LFR5A
ON-VEHICLE INSPECTION
SPARK TEST
1. Remove the ignition coil connector(A).
Disconnect the iguition coil connector while pulling up tre connector lock.
2. Remove the ignition coil.
3. Using a spark plug socket, remove the spark plug.
4. Install the spark plug to the ignition coil.
5. Ground the spark plug to the engine.
6. Check is spark occurs while engine is being cranked.
To prevent fuel being injected from injectors while the engine is being cranked, remove the fuel pump(A) relay
from the fuse box.
Crank the engine for no more than 5 ~ 10 seconds.
7. Inspect all the spark plugs.
8. Using a spark plug socket, install the spark plug.
9. Install the ignition coil.
10. Reconnect the ignition coil connector.

INSPECT SPARK PLUG
1. Inspect the electrodes(A) an ceramic insulator(B).
INSPECTION OF ELECTRODES
Condition Dark deposits White deposits
Description - Fuel mixture too rich
- Low air intake
- Fuel mixture too lean
- Advanced ignition timing
- Insufficient plug tightening torque
2. Check the electrode gap (A).
Standard : 1.0 ~ 1.1 mm (0.0394 ~ 0.0433 in.)

INSPECT IGNITION COIL
1.
Standard : 0.0715 ± 0.015!
Mesure the resistance between the terminals No.1 and No.3.

Engine Electrical System
Charging System
Engine ,SLJ[YPcal System

2009 > G 2.7 DOHC >
DESCRIPTION
The charging system included a battery, an alternator with a built-in regulator, and the charging indicator light and
wire.
The Alternator has built-in diodes, each rectifying AC current to DC current.
Therefore, DC current appears at alternator "B" terminal.
In addition, the charging voltage of this alternator is regulated by the battery voltage detection system.
The alternator is regulated by the battery voltage detection system. The main components of the alternator are the
rotor, stator, rectifier, capacitor brushes, bearings and V-ribbed belt pulley. The brush holder contains a built-in
electronic voltage regulator.
Table of contents
Other Kia Automobile manuals
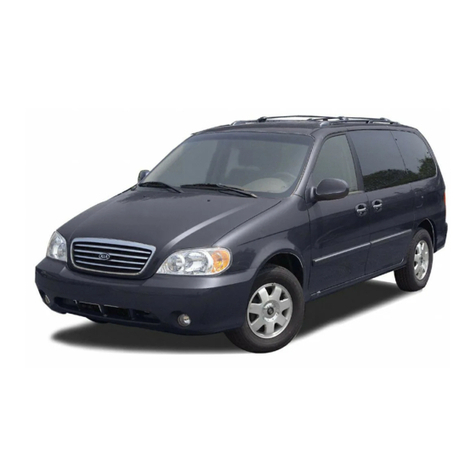
Kia
Kia Sedona User manual
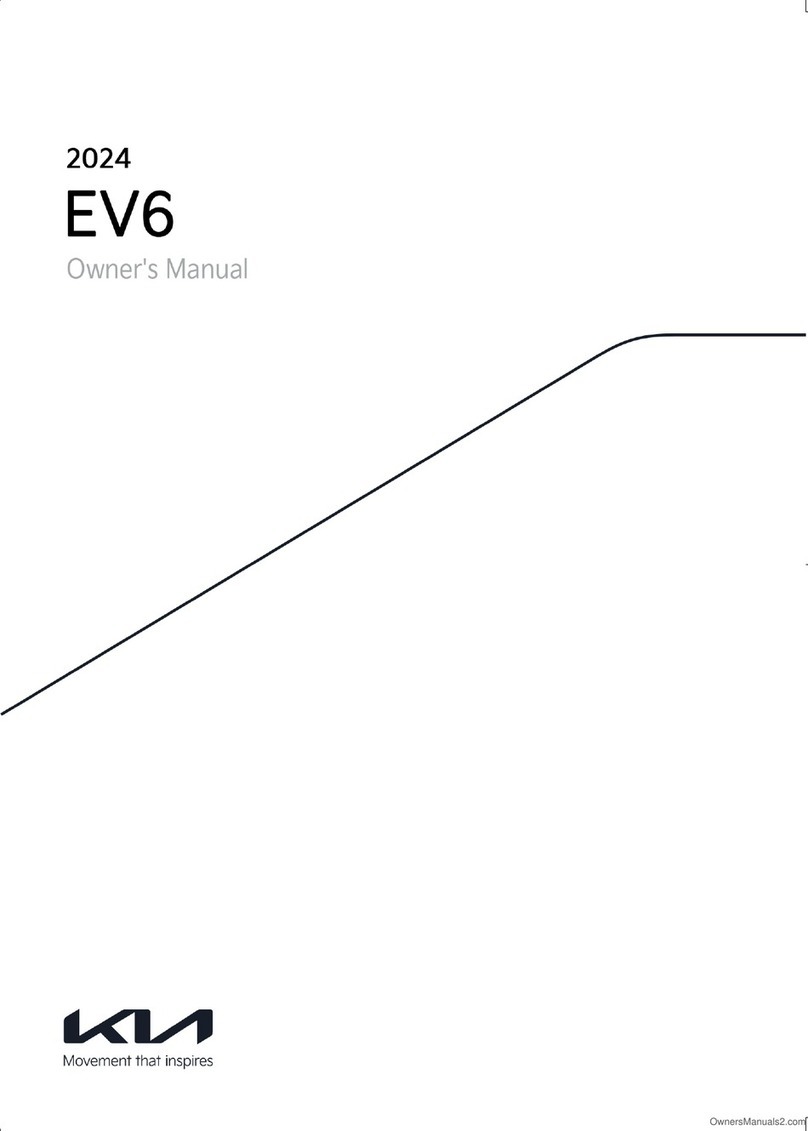
Kia
Kia EV6 2024 User manual

Kia
Kia Picanto User manual
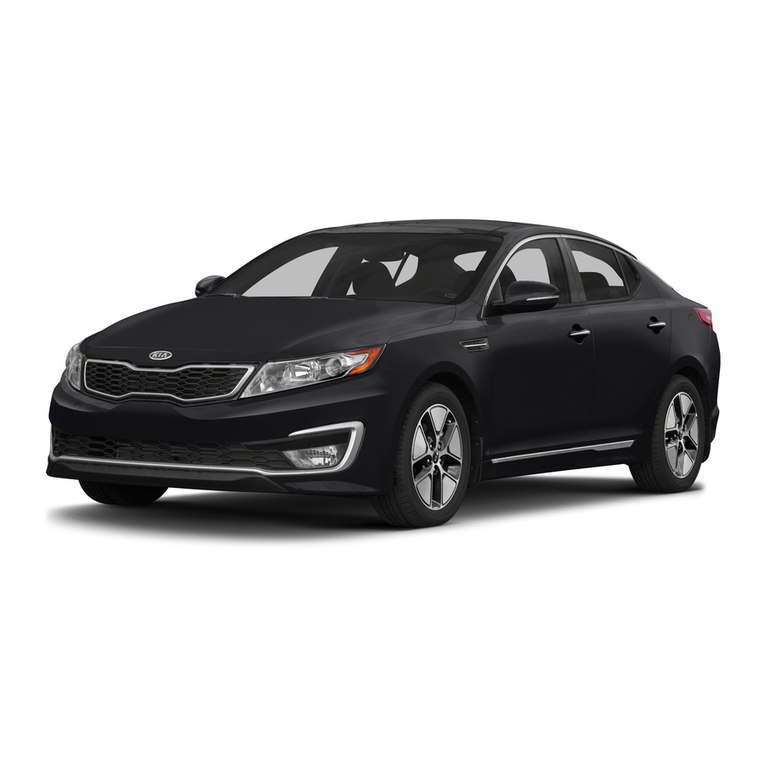
Kia
Kia Optima Hybrid 2013 User manual
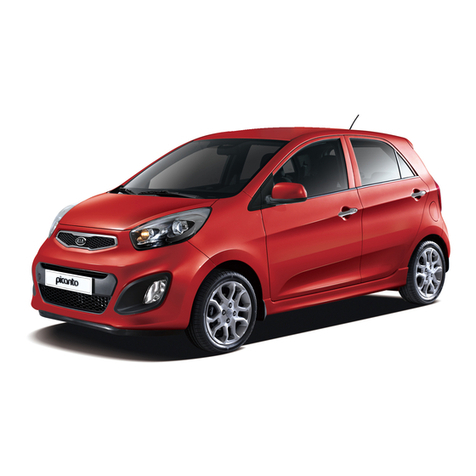
Kia
Kia picanto 2014 User manual

Kia
Kia Sportage 2022 User manual

Kia
Kia Amanti 2009 User manual

Kia
Kia Soul 2010 User manual

Kia
Kia Carnival MPV 2024 User manual
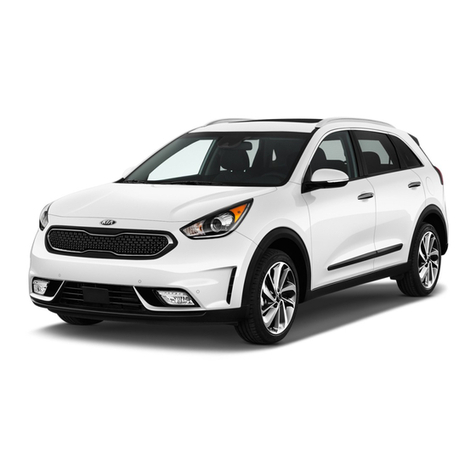
Kia
Kia Niro 2017 User manual