KOJA Future Series Installation instructions

Instructions for operation and maintenance
www.koja.fi
Air handling unit
Future


AIR HANDLING UNIT FUTURE
INSTRUCTIONS FOR OPERATION AND MAINTENANCE
2017-02-13 V. 2.0 3
TABLE OF CONTENTS
1. General ................................................................................................................................................... 5
1.1. Operangcondions............................................................................................................................ 5
1.2. CENstandardclassicaon................................................................................................................... 5
1.3. Soundlevel ........................................................................................................................................... 5
1.4. Safety.................................................................................................................................................... 5
1.4.1. CEmarking............................................................................................................................ 7
1.4.2. Safetyequipment ................................................................................................................. 7
1.4.3. Fire........................................................................................................................................ 7
1.5. Safetydevices....................................................................................................................................... 8
1.5.1. An-freezingthermostat ...................................................................................................... 8
1.5.2. Filterindicator(dierenalpressuregauge) ........................................................................ 8
1.5.3. Firethermostat ..................................................................................................................... 8
1.5.4. Flowcontroller...................................................................................................................... 8
1.6. Manufacturer’sdeclaraon.................................................................................................................. 9
2. Commissioning and maintenance.......................................................................................................... 10
2.1. Commissioning ................................................................................................................................... 10
2.2. Maintenance ...................................................................................................................................... 11
3. Damper,mixingandreturnairsecons
FPTP, FPTA, FPTB AND FPTC ................................................................................................................... 12
3.1. Operangcondions.......................................................................................................................... 12
3.2. Commissioning ................................................................................................................................... 12
3.3. Maintenance ...................................................................................................................................... 12
4. FilterseconFSTF ................................................................................................................................. 13
4.1. Construcon....................................................................................................................................... 13
4.2. Operangcondions.......................................................................................................................... 13
4.3. Installaon.......................................................................................................................................... 13
4.4. Commissioning ................................................................................................................................... 13
4.5. Maintenance ...................................................................................................................................... 14
4.6. Replacementoflters ........................................................................................................................ 14
4.7. Replacementofgasket ....................................................................................................................... 15
5. Coilsecons.......................................................................................................................................... 16
5.1. Operangcondions.......................................................................................................................... 16
5.2. Installaon.......................................................................................................................................... 17
5.3. Dimensioninginstruconsforwatertrap........................................................................................... 17
5.4. Commissioning ................................................................................................................................... 18
5.5. Maintenance ...................................................................................................................................... 19
6. Heatrecoverysecon,rotorFRTR ......................................................................................................... 20
6.1. Operangcondions.......................................................................................................................... 20
6.2. Commissioning ................................................................................................................................... 20
6.3. Firstaconsincaseofanalarm,whenthemotorhasstopped......................................................... 21
6.4. Maintenance ...................................................................................................................................... 21
6.5. Cleaning.............................................................................................................................................. 22
6.6. Rotoradjustment ............................................................................................................................... 23
7. Heatrecoverysecon,plateFRTL.......................................................................................................... 25
7.1. Operangcondions.......................................................................................................................... 25
7.2. Installaon.......................................................................................................................................... 25
7.3. Dimensioninginstruconsforwatertrap........................................................................................... 26
7.4. Commissioningandmaintenance ...................................................................................................... 27

AIR HANDLING UNIT FUTURE
INSTRUCTIONS FOR OPERATION AND MAINTENANCE
4 V. 2.0 2017-02-13
8. Heangsecon,electricalFLTE.............................................................................................................. 28
8.1. Operangcondions.......................................................................................................................... 28
8.2. Operaon ........................................................................................................................................... 28
8.3. Commissioning ................................................................................................................................... 28
8.4. Maintenance ...................................................................................................................................... 28
9. Drop separator, FPTE............................................................................................................................. 29
9.1. Operangcondions.......................................................................................................................... 29
9.2. Commissioning ................................................................................................................................... 29
9.3. Maintenance ...................................................................................................................................... 29
10. Humidifyingsecon,evaporaonFKTK ................................................................................................. 30
10.1. Operangcondions.......................................................................................................................... 30
10.2. Commissioning ................................................................................................................................... 30
10.3. Maintenance ...................................................................................................................................... 31
11. Humidifyingsecon,steamFKTH .......................................................................................................... 32
11.1. Installaon.......................................................................................................................................... 32
11.2. Commissioning ................................................................................................................................... 32
11.3. Maintenance ...................................................................................................................................... 32
12. Fansecon,motorsandfrequencyconverters ...................................................................................... 33
12.1. Shortcircuitmotors............................................................................................................................ 34
12.2. Conneconofelectricmotorandfrequencyconverter..................................................................... 36
12.3. PMmotors.......................................................................................................................................... 37
12.4. ECmotors ........................................................................................................................................... 39
12.5. ConneconoftheEBM/FläktECmotor ........................................................................................... 39
12.6. ConneconoftheZiehlECmotor ...................................................................................................... 40
12.7. Maintenance,sparepartsandwarranty ............................................................................................ 41
13. Fansecon,FFTSandFFTK.................................................................................................................... 42
13.1. Operangcondions.......................................................................................................................... 42
13.2. Fansecon ......................................................................................................................................... 42
13.3. Safety.................................................................................................................................................. 43
13.4. Safetyequipment ............................................................................................................................... 43
13.5. Commissioning ................................................................................................................................... 43
13.6. Maintenance ...................................................................................................................................... 44
14. AirowmeterFIZM .............................................................................................................................. 45
14.1. Fanmalfunconsandtheirpossiblecauses ...................................................................................... 46
14.1.1. Casingfans(AC,EC,PM) ..................................................................................................... 46
14.1.2. Belt-drivenfans................................................................................................................... 47
15. CasingmoduleFMOD............................................................................................................................ 48
15.1. Maintenance ...................................................................................................................................... 48
16. SoundaenuatorseconFVTK ............................................................................................................. 49
16.1. Commissioning ................................................................................................................................... 49
16.2. Maintenance ...................................................................................................................................... 49

AIR HANDLING UNIT FUTURE
INSTRUCTIONS FOR OPERATION AND MAINTENANCE
General
2017-02-13 V. 2.0 5
1. GENERAL
For efficient and economical air-conditioning, the operation of the equipment must be monitored on a regular
basis, and the operation and maintenance instructions must be followed.
The instructions for the operation and maintenance of the air-conditioning plant contain the operating princi-
ples of the plant and its subsystems, operating programs, connection and control diagrams, location and layout
drawings, and adjustment values and operation and maintenance instructions for the equipment. (The National
Building Code of Finland, Section D2 Indoor climate and ventilation of buildings.)
1.1. Operating conditions
The standard unit is designed for indoor installation. The ambient temperature must be over 0 oC The air to be
handled must not be corrosive or poisonous, warmer than 70 oC or contain significant amounts of water vapour
or large particles.
CAUTION
The permitted operating conditions and any limitations must be checked from the section-
specific instructions.
1.2. CEN standard classification
Air handling unit Future complies with the CEN standard EN 1886 classification as follows:
• L2 leakage class for casing
• T3 heat transfer coefficient for casing.
1.3. Sound level
For the unit’s sound data, please refer to the design calculations supplied with the acknowledgment of order.
1.4. Safety
WARNING
The component manufacturer’s installation and operating instructions must be followed.
In case of a discrepancy between these instructions and the component manufacturer’s
instructions, follow the component manufacturer’s instructions. For the detailed
component manufacturer’s operating and maintenance instructions, please refer to our
website at
http://www.koja.fi/fi/rakennukset/tukimateriaalit/ilmankaesittelykoneet
WARNING
Do not keep extra objects on top of or inside the unit. Do not climb or walk on top of the
unit.
WARNING
Before switching on the fan, make sure that the inlet and outlet of the fan section have
been connected to the ductwork or that the access to the rotating fan parts, such as
the impeller, through an inlet, outlet or access door has been prevented with protective
screens or by other appropriate manner. The service switch of the air handling unit must be
installed and in service when the unit is switched on. The damper section of the unit must
open before the fan starts.

AIR HANDLING UNIT FUTURE
INSTRUCTIONS FOR OPERATION AND MAINTENANCE
General
6 V. 2.0 2017-02-13
WARNING
Electrical installations must comply with EMC requirements. For EMC-compliant
connections, refer to the instructions in the frequency converter manufacturers’ installation
guides. Connections made at the Koja factory comply with these requirements. Koja is not
responsible for damages, if the connections made by the customer do not comply with
general EMC requirements. Such damages include, for example, motor bearing damage due
to bearing currents.
WARNING
The frame of the ventilation unit must be connected to the building’s earthing system
before operation.
WARNING
The fans have a supply frequency for the maximum rotation speed stated in the fan
plate. When using a frequency converter, make sure that the maximum frequency is not
exceeded.
WARNING
The motor and/or frequency converter supply cables must be equipped with a service
switch. If the service switch is installed between the motor and frequency converter, the
switch must be EMC approved and connected in compliance with the EMC regulations. Pay
special attention to the screened 360 degree connection and protective ground continuity.
WARNING
The earth leakage current from the frequency converters exceeds 3.5 mA. According to
standard EN61800-5-1, the frequency converter connection must, therefore, be fixed and
the cross-section of the protective earth conductor of the supply must be at least 10 mm2
(Cu) or 16 mm2(Al). Alternatively, the frequency converter supply can be equipped with an
additional protective earth conductor of the same cross-section than the actual protective
earth conductor. Local regulations must also be followed. The earth leakage current from
the integrated control unit of the EC motors is no more than 3.5 mA.
WARNING
The electric motors and frequency converter are serviced according to the manufacturer’s
instructions. The components must be de-energized and the impeller stopped for the
duration of the maintenance. Once opened, the rotors and stators of the permanent
magnet motors (EC and PM motors) may cause interference in electrical devices, such as
phones and payment cards. Being in close proximity to opened permanent magnet motors
constitutes a danger to people with pacemakers.
WARNING
Permanent magnet motors rotating freely in air flow operate as generators. To prevent the
risk of electric shock, the axles of permanent magnet motors must, therefore, be locked for
the duration of the maintenance.
WARNING
Electrical connections must be made by a qualified and authorized electrician only. Before
starting any installation and maintenance work on the electrical device, make absolutely
sure that the device is de-energized. After switching off the power, wait at least five
minutes to allow dangerous voltages to discharge from the devices. Electrical devices
should be inspected every six months. Any deficiencies and faults must be rectified
immediately.
WARNING
Due to functional reasons, fans/motors may start and stop automatically without warning.
This may happen, for example, after a power outage or malfunction.

AIR HANDLING UNIT FUTURE
INSTRUCTIONS FOR OPERATION AND MAINTENANCE
General
2017-02-13 V. 2.0 7
CAUTION
If the unit is installed in a place where it is easily accessible to persons other than service
personnel, the handles of the access doors must be removed and locked in a safe place.
CAUTION
The ventilation system and its maintenance routes must be designed and constructed
so that the ventilation unit can be serviced and repaired easily and safely. The National
Building Code of Finland D2, section 3.8.6.
CAUTION
The filter pressure difference values must under no circumstances exceed the dimensioning
pressure drop in the filter by more than two times. If the pressure difference is exceeded,
the components or structure of the unit may become damaged. The warranty does not
cover damages due to negligence in replacing the filters.
CAUTION
If the unit is equipped with drainages for washing water, these must be plugged. If the
drainages are sewered, they must be equipped with a water trap.
CAUTION
The fan models are not designed to be disassembled. If the fan has to be disassembled, due
to, for example, narrow hauling routes, the fan-motor assembly must be balanced and a
certificate of balancing must be presented, in order to retain the warranty. If the motor has
to be removed or the fan disassembled due to maintenance or repair work, permission is
needed from Koja Ltd’s Warranty Handler. Otherwise, the fan warranty will be voided.
CAUTION
If the fan has to be replaced, the faulty fan is to be returned with a length of the wire
attached to the motor.
1.4.1. CE marking
The unit has been CE marked at the factory, and the CE mark has been attached to the machine plate. A decla-
ration of conformity is supplied with the unit.
The person responsible for taking the unit into use must ensure that all procedures mentioned in these in-
structions have been performed before using the unit. Electrical installations and their installation inspections
and measurements must be performed in accordance with standards SFS-EN 60204-1 and SFS 6000-6, and the
person responsible for installing the unit must compile the testing and installation documents.
1.4.2. Safety equipment
Service/safety switch installed in the fan section functions also as an unit emergency switch.
(not included in delivery).
The protective devices for the electric components must be dimensioned correctly in order to guarantee safe
use of the unit.
1.4.3. Fire
In case of fire in the unit, do not use water, but a powder extinguisher or such. The materials used in the unit do
not produce harmful amounts of any hazardous gases when burning.

AIR HANDLING UNIT FUTURE
INSTRUCTIONS FOR OPERATION AND MAINTENANCE
General
8 V. 2.0 2017-02-13
1.5. Safety devices
1.5.1. Anti-freezing thermostat
An anti-freezing thermostat (not included in delivery) is installed in the water space of the heat exchanger, or
on a heat transfer surface of the heat exchanger. The thermostat gives an alarm and stops the unit if the water
temperature in the heat exchanger drops below the set point (e.g., +8 oC). Always determine the reason for the
tripping of the thermostat. The unit can be restarted by pressing the reset button of the anti-freezing thermo-
stat.
1.5.2. Filter indicator (differential pressure gauge)
A filter indicator (not included in delivery) is installed in the filter section, so that it can measure the pressure
difference across the filter. It indicates the pressure difference and/or gives an alarm. For the purpose of the
filter indicator, please refer to the section covering the filters.
1.5.3. Fire thermostat
A fire thermostat (not included in delivery) is installed in the inlet or outlet duct of the unit. It gives an alarm
(and stops the unit) if the supply air temperature exceeds the set point (e.g., +50 oC). Always determine the
cause for the tripping of the thermostat, and also check if the fire dampers (if applicable) have been actuated.
The unit can be restarted by pressing the reset button of the fire thermostat.
1.5.4. Flow controller
A flow controller (not included in delivery) is installed in the inlet or outlet duct of the unit. It gives an alarm if
the sensor does not detect air flow. Always determine the cause for the alarm immediately.
CAUTION
Instructions for the operation and maintenance of safety devices are supplied by the
device manufacturers.

AIR HANDLING UNIT FUTURE
INSTRUCTIONS FOR OPERATION AND MAINTENANCE
General
2017-02-13 V. 2.0 9
1.6. Manufacturer’s declaration
Tampere
Lentokentänkatu 7, PO Box 351
FI-33101 TAMPERE, FINLAND
Tel. +358 3 282 5111
Fax +358 3 282 5401
Vantaa
Vantaankoskentie 14
FI-01670 VANTAA, FINLAND
Tel. +358 9 777 1750
Fax +358 9 878 6087
Jalasjärvi
Vaasantie 255, PO Box 72
FI-61601 JALASJÄRVI, FINLAND
Tel. +358 6 456 7600
Fax +358 6 456 7610
DECLARATION OF CONFORMITY
Manufacturer Koja Oy
Address Lentokentänkatu 7
FI-33900 Tampere
Finland
Hereby declares that
Products
Future air handling unit series
Type
FUTURE 0603…3630
Serial number
a) conforms with the essential requirements of the directives listed below,
provided that the said products are installed in accordance with the
instructions supplied with the unit.
Consolidated Machinery Directive 2006/42/EC
Consolidated EMC Directive 2004/108/EC
Consolidated Low Voltage Directive 2006/95/EC
Consolidated Ecodesign Directive 2009/125/EC
If any changes are made to the products, this declaration will no longer be in
effect.
b) has been manufactured according to the following harmonised standards.
SFS-EN ISO 12100, SFS-EN ISO 13857, SFS-EN 60204-1, EN 61000-6-1, EN
61000-6-3, EN 61000-6-4
Technical file compiled by: Taru Lähteenmäki
Product Development Manager, air handling units
Address: Lentokentänkatu 7, FI-33900 Tampere, Finland
Date 10 October 2016.
Signature Joonas Lius
Position Director, Production and Procurement

AIR HANDLING UNIT FUTURE
INSTRUCTIONS FOR OPERATION AND MAINTENANCE
Commissioning and maintenance
10 V. 2.0 2017-02-13
2. COMMISSIONING AND MAINTENANCE
2.1. Commissioning
Before commissioning the air handling unit, make sure that the unit has been installed and cleaned according to
the instructions, that the components and safety devices essential for the safe operation of the unit have been
installed properly, and that the flow rates have been adjusted.
The commissioning of the air handling unit and the training of the operating personnel are usually carried out
by the supplier of the air-conditioning plant in question.
WARNING
Observe general and section-specific safety instructions.
Earthing of the access doors
CAUTION
Earthing of the access doors must be checked visually after closing the access doors.
In access doors without hinges the earthing conductor must be connected to a quick
disconnect connector after attaching the door (see picture Earthing of access doors).
CAUTION
The motor of the fan FFTK-xx-AF may become overloaded, if the air volume flow exceeds the
designed level. This may happen if, for example, the air handling unit is switched on before all the
sections of the unit and the ductwork are installed, if the fan is switched on with the access door
open, or if the access door is opened during operation of the fan.
CAUTION
The FFTS casing fan models are not designed to be disassembled. If the fan has to be
disassembled, due to, for example, narrow hauling routes, the fan-motor assembly must
be balanced and the certificate of balancing must be presented, in order to retain the
warranty. If the motor has to be removed or the fan disassembled due to maintenance or
repair work, permission is needed from Koja Ltd’s Warranty Handler. Otherwise, the fan
warranty will be voided.

AIR HANDLING UNIT FUTURE
INSTRUCTIONS FOR OPERATION AND MAINTENANCE
Commissioning and maintenance
2017-02-13 V. 2.0 11
2.2. Maintenance
WARNING
Observe general and section-specific safety instructions.
WARNING
Preventing start-up before starting the maintenance work
CAUTION
Earthing of the access doors must be checked visually after closing the access doors.
In access doors without hinges the earthing conductor must be connected to a quick
disconnect connector after attaching the door (see picture Earthing of access doors).
Before starting any maintenance and/or repair work, make sure that the work will not cause unnecessary
disturbance to other activities in the building. Stop the unit and turn the service switch to the zero position.
Remove the fuses of both speeds of 2-speed motors (all fuses in case of 3-speed motors) and make sure (via a
written notice, for example) that the unit will not be started accidentally during the maintenance.
After completing the maintenance and/or repair work, start the unit and make sure that all shut-off and control
devices, instruments and the signal lamp are functioning.
The stated maintenance intervals are only guidelines. The intervals are determined by the utilisation rate of the
air-conditioning plant and the ambient conditions. The given intervals apply when the plant is used 8 hours a
day in city air environment. The maintenance intervals are longer in cleaner environments (like the countryside)
and shorter in dirtier environments (like industrial areas).
It is advisable to have the unit serviced at the beginning (autumn) and at the end (spring) of the heating season.
Maintenance activities that can be performed by the plant’s own service personnel are cleaning, the replace-
ment of filters, belts and pulleys, and the lubrication of joints and bearings.
Repairs on unit sections, replacement of bearings, and all installation and adjustment operations related to
electricity or automation require special expertise. Clean the unit with an ordinary detergent. Solvents must not
be used in cleaning sections that include aluminium parts (heat exchangers).
Spare parts mentioned in these instructions are available at Koja or the manufacturer in question. (Koja Ltd
reserves the right to changes without prior notice.)

AIR HANDLING UNIT FUTURE
INSTRUCTIONS FOR OPERATION AND MAINTENANCE
Damper, mixing and return air secons FPTP, FPTA, FPTB AND FPTC
12 V. 2.0 2017-02-13
3. DAMPER, MIXING AND RETURN AIR SECTIONS
FPTP, FPTA, FPTB AND FPTC
FPTP FPTA FPTB FPTC
CAUTION
The pressure rise of the fan can be higher than the maximum permissible pressure
difference of the damper. The damper should open before the fan starts, and close after
the fan has stopped.
3.1. Operating conditions
• The operating temperature range is –40…+80 °C.
• The maximum permissible pressure difference across the damper is 1,200 Pa.
3.2. Commissioning
• Make sure that the dampers of the sections open and close fully and that the actuator works according
to the control.
3.3. Maintenance
• The maintenance interval is 6 months.
• Make sure that the leafs open and close unhindered up to the set limits.
• Make sure that the lever mechanisms between the leafs and between the actuators and shafts are not
loose or worn.
• Lubricate the joints in lever mechanisms with light oil.
• Tighten screws, if necessary, and replace worn parts.
• Make sure that the leaf and end plate gaskets are intact. Replace damaged and worn gaskets.
• Clean the section, if necessary.

AIR HANDLING UNIT FUTURE
INSTRUCTIONS FOR OPERATION AND MAINTENANCE
Filter secon FSTF
2017-02-13 V. 2.0 13
4. FILTER SECTION FSTF
4.1. Construction
The filter section FSTF is available in four lengths. The hygiene type Future Clean can be equipped with a pull-
out filter frame up to unit size 1209.
The filter section has a thermally insulated casing. The particle filters used are disposable filter cassettes of the
module’s length. The cassettes are pushed into the mounting frame and pressed against the rubber strips made
of EPDM. The activated carbon filters have carbon cylinders fixed to the connection plate.
The section has connections for a differential pressure gauge and filter indicator.
4.2. Operating conditions
• The operating temperature range is –40…+80 °C.
4.3. Installation
Filter section FSTF is installed in the upright position (see figure above) or in the horizontal position, in which
case the air flow can be directed upwards or downwards when using coarse-grain filters G3 and G4 or wide-area
filter F7. With other filter grades, the air flow direction is downwards only. The air flow direction is marked on
the filter section and on the filters. If there are no markings, the filter section must be installed so that the air
must enter the filter from the filter groove side.
4.4. Commissioning
The filters must be installed before test-running the unit. The filters are placed in the mounting grooves with
the folds in upright position, and then clamped against the gasket.
• Check that the filters are intact and of the correct type.
• Check that the filters are tight against the frame gasket and that there are no leaks.
• Check that the filters are clamped in place.
• Check that the differential pressure gauge is intact and reset.
• Check that the differential pressure hoses of the filter section are intact and in their places.
At the installation stage, the pressure difference limits for the filter indicators must be set according to the Fu-
ture dimensioning program documentation. The filter pressure difference values must under no circumstances
exceed the dimensioning pressure drop in the filter by more than two times. If the pressure difference is ex-
ceeded, the components or structure of the unit may become damaged. The warranty does not cover damages
due to negligence in replacing the filters.

AIR HANDLING UNIT FUTURE
INSTRUCTIONS FOR OPERATION AND MAINTENANCE
Filter secon FSTF
14 V. 2.0 2017-02-13
4.5. Maintenance
The filter section is to be serviced and cleaned twice a year, normally in the autumn and spring. The replace-
ment interval of the filters is usually determined by the maximum permissible decrease in the air flow due to
increased pressure drop across the filter (normally 10% of the design air flow).
To measure the pressure drop, a filter indicator indicating the pressure difference across the filter (shows the
pressure difference or gives an alarm) has been installed on the filter section. When the pressure difference
across the filter exceeds the set limit, the filter must be replaced. Refer to the unit design documentation for
the recommended filter-specific final pressure drop with design air flow.
The filter pressure difference values must under no circumstances exceed the dimensioning pressure drop in
the filter by more than two times. If the pressure difference is exceeded, the components or structure of the
unit may become damaged. The warranty does not cover damages due to negligence in replacing the filters.
Replace the filters if the pressure difference limit in the filters has been exceeded, or if the filters are dirty or
damaged.
• Check that the filters are intact and of the correct type.
• Check that the filters are tight against the frame gasket and that there are no leaks.
• Check that the filters are clamped in place.
• Check that the differential pressure gauge is intact and reset.
• Check that the differential pressure hoses of the filter section are intact and in their places.
• Check that the differential pressure transmitter operates properly and has been calibrated according
to the manufacturer’s instructions. Check also that a pressure difference limit, which must not exceed
the dimensioning pressure drop by more than two times, has been set in accordance with the Future
dimensioning program documentation.
4.6. Replacement of filters
1. Open the access door and the clamping mechanism. Pull the filter (filters) out of the casing.
2. Clean the casing, if necessary.
3. Check the condition of the gaskets. Replace worn and damaged gaskets. NOTE! Gaskets are not need-
ed between filters that are mounted parallel to each other.
4. Place new filters in the mounting grooves with the folds in upright position. Clamp the filters against
the gasket.
5. Close the access door.
6. Check the operation of the filter indicator once the fan has been restarted.
Filter cassee sizes / number of cassees
Unit size Width, mm Height, mm 287 x 592 592 x 287 592 x 592 592 x 490
0603 790 470 1
0605 790 670 1
0606 790 790 1
0906 1,070 790 1 1
0909 1,070 1,070 1 1 1
1206 1,350 790 2
1208 1,350 990 2 2
1209 1,350 1,070 2 2
1210 1,350 1,190 4
1212 1,350 1,350 4
1506 1,670 790 1 2
1509 1,670 1,070 1 2 2
1512 1,670 1,350 24
1515 1,670 1,670 2 2 4
1809 1,990 1,070 3 3
1810 1,990 1,190 6
1812 1,990 1,350 6
1815 1,990 1,670 3 6
1818 1,990 1,990 9
2409 2,550 1,070 4 4

AIR HANDLING UNIT FUTURE
INSTRUCTIONS FOR OPERATION AND MAINTENANCE
Filter secon FSTF
2017-02-13 V. 2.0 15
Filter cassee sizes / number of cassees
Unit size Width, mm Height, mm 287 x 592 592 x 287 592 x 592 592 x 490
2412 2,550 1,350 8
2415 2,550 1,670 4 8
2418 2,550 190 12
2421 2,550 2,310 4 12
2424 2,550 2,550 16
3015 3,190 1,670 5 10
3018 3,190 1,990 15
3021 3,190 2,310 5 15
3024 3,190 2,550 20
3624 3,790 2,550 24
3627 3,790 2,870 624
3630 3,790 3,190 30
The thickness of the mounting frame is 25 ±1 mm.
4.7. Replacement of gasket
Dimensions of the mounting groove and filter cassette frame
A new gasket is mounted, starting from the middle of
the frame bottom. Press the gasket against the edge
of the plate by hand or carefully with a hammer or
some other tool. Use, for example, a 20-mm pipe to
bend the corners appropriately. Cut the gasket to a
length of about 5 mm too long. Force the ends to-
gether and apply sealant between them.
A. With the clamp closed: 35 ± 1.0
B. Lower frame
C. With the clamp closed: 35 ± 1.0
D. Middle frame

AIR HANDLING UNIT FUTURE
INSTRUCTIONS FOR OPERATION AND MAINTENANCE
Coil secons
16 V. 2.0 2017-02-13
5. COIL SECTIONS
Heat recovery section, FRTG
Heating section, fluid FLTV
Cooling section, fluid FTVJ
Heat recovery section,
coil FRTG
A. Outlet pipe for condensation
water
B. Ductwork for heat transfer agent
Heating section, FLTV Cooling section, FJTV
5.1. Operating conditions
• The maximum operating temperature is +150 °C.
• The maximum operating pressure is 1.0 MPa.
CAUTION
The coils of large units have been split in two. The condensation water drain of the coil has
to be piped to the sewer, also from behind the unit. Make sure that the water traps and
piping have been mounted according to the instructions.
CAUTION
Due to the construction, the heat exchanger will never drain completely. If the cooling
medium used is water, the heat exchanger may freeze up and become damaged at
temperatures below 0 °C.

AIR HANDLING UNIT FUTURE
INSTRUCTIONS FOR OPERATION AND MAINTENANCE
Coil secons
2017-02-13 V. 2.0 17
5.2. Installation
CAUTION
The coils are always connected, so that the fluid flow runs against the direction of the air
flow. There is an adhesive label on the coils describing the connection.
The right-handed heating section is connected according to the figure Right-handed connection, and the
left-handed according to the figure Left-handed connection (the heat exchanger must be bled carefully in order
to ensure proper fluid circulation in the piping).
The connection principle for the left-handed and right-handed heating sections is the same. The heat exchanger
has inlet and outlet connections and connections for coil bleeding, draining and the anti-freezing thermostat
sensor.
Right-handed connection Left-handed connection
5.3. Dimensioning instructions for water trap
Coil at the inlet side of the fan
Δp = P0- p1 (Pa)
Amin = Δp/10 + 30 (mm)
Bmin = A/2 + 20 (mm)

AIR HANDLING UNIT FUTURE
INSTRUCTIONS FOR OPERATION AND MAINTENANCE
Coil secons
18 V. 2.0 2017-02-13
Coil at the outlet side of the fan
Δp = P0- p1 (Pa)
Amin = 20 (mm)
Bmin = Δp/10 + 30 (mm)
CAUTION
The water trap must be installed in
the position shown in the picture.
5.4. Commissioning
• Make sure that the heat transfer surfaces of the coil are clean and intact.
• Open the line control valves to fill the coil with fluid.
• Bleed the coil.
• Make sure that the water side connections of the coil do not leak.
• Check the rotation direction of the circulating pump (do not run the pump dry).
• If necessary, check the operation of the anti-freezing thermostat.
• Make sure that the control valve functions, and adjust the line control valves, according to the plan.
Refer to the manufacturer’s manual for further adjustment instructions.
• Check the condensation water discharge system, i.e., drip tray, piping and water trap.
• Flush the piping and fill the water trap.

AIR HANDLING UNIT FUTURE
INSTRUCTIONS FOR OPERATION AND MAINTENANCE
Coil secons
2017-02-13 V. 2.0 19
5.5. Maintenance
• Make sure that the water side connections of the coil do not leak.
• Make sure that the heat transfer surfaces of the coil are clean and intact.
• Clean the coil gently with a brush, compressed air or a vacuum cleaner. If the unit has water drains, the
coil can be cleaned with water and a mild detergent. NOTE! Do not use pressure cleaning.
• Bleed the coil and check the operation of the anti-freezing thermostat at the beginning of each heating
season.
• Check and clean the condensation water discharge system, i.e., drip tray, piping and water trap (traps).
• A damaged coil must be repaired in place, sent to the manufacturer to be repaired or replaced.
CAUTION
If the coil is not used during the heating season, water must be drained from it or it has to
be filled with a water-glycol mixture to avoid freezing. The coil does not drain fully through
the drain screw; 20 to 30% of the total water volume remains in the coil. To fully drain
water from the coil, you can, for example, blow compressed air through the bleed screw,
observing the maximum permissible operating pressure.
CAUTION
The HR circuit must be bled again after 2–4 weeks of heating in order for the energy
efficiency in heat recovery to be the best possible.

AIR HANDLING UNIT FUTURE
INSTRUCTIONS FOR OPERATION AND MAINTENANCE
Heat recovery secon, rotor FRTR
20 V. 2.0 2017-02-13
6. HEAT RECOVERY SECTION, ROTOR FRTR
6.1. Operating conditions
• The maximum permissible operating temperature is +70 °C.
6.2. Commissioning
• The units should not be started during the construction phase. If this cannot be avoided, the fan must
not be used without the heat exchanger in operation. Make sure that the filters are in place.
• Make sure that the inlet or outlet ducts are free from foreign objects that could damage the faces of
the heat exchanger.
• Use a spirit level on the face of the heat exchanger to ensure that the rotor is upright, and adjust it, if
necessary.
• Make sure that the rotor rotates freely.
• Make sure that the rotor belt is tight and running freely in its proper place. Check the tightness of the
belt after two weeks of use, and shorten the belt according to the tightening instructions so that the
belt will have allowance for stretch with respect to the limit switch, if necessary.
• If necessary, adjust the brush seals on the circumference of the rotor, so that they touch the surface
of the heat exchanger. Also check the brush seals on the lower surface of the rotor mid-beams and, if
necessary, adjust them so that they touch the surface of the exchanger.
• Check that the rotation guard magnet and sensor are installed correctly.
• Make sure that the seals of the access door are in place and intact. Close the access door and make
sure that each latch tightens properly.
• Go through the section-specific instructions, check that the access doors are shut, and then start the unit.
• Looking from the exhaust air side, check that the heat exchanger rotates from the exhaust air side to
the supply air side through the purging sector.
• After two weeks of use, check the bolts and belt of the sectorised rotor periphery plates for tightness.
Tighten, if necessary.
CAUTION
If the unit is installed in a place where it is accessible to persons other than service
personnel, the handles of the access doors must be removed and locked in a safe place.
This manual suits for next models
32
Table of contents
Other KOJA Air Handler manuals
Popular Air Handler manuals by other brands
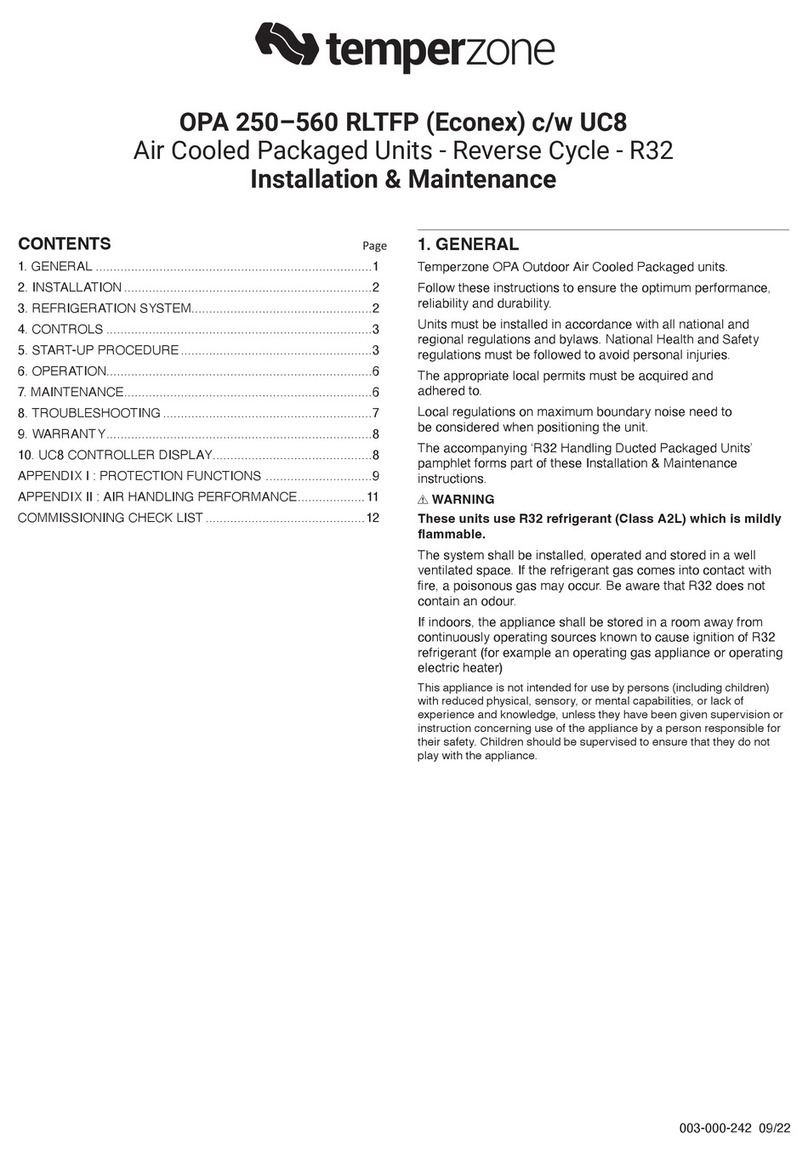
TemperZone
TemperZone Econex OPA 250RLTFP Installation & maintenance
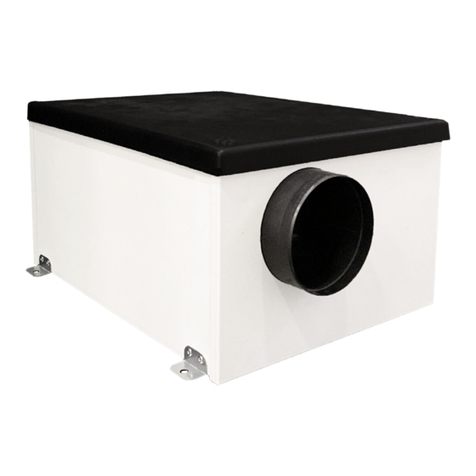
aerauliqa
aerauliqa AIRQURE P1 Installation, use and maintenance manual
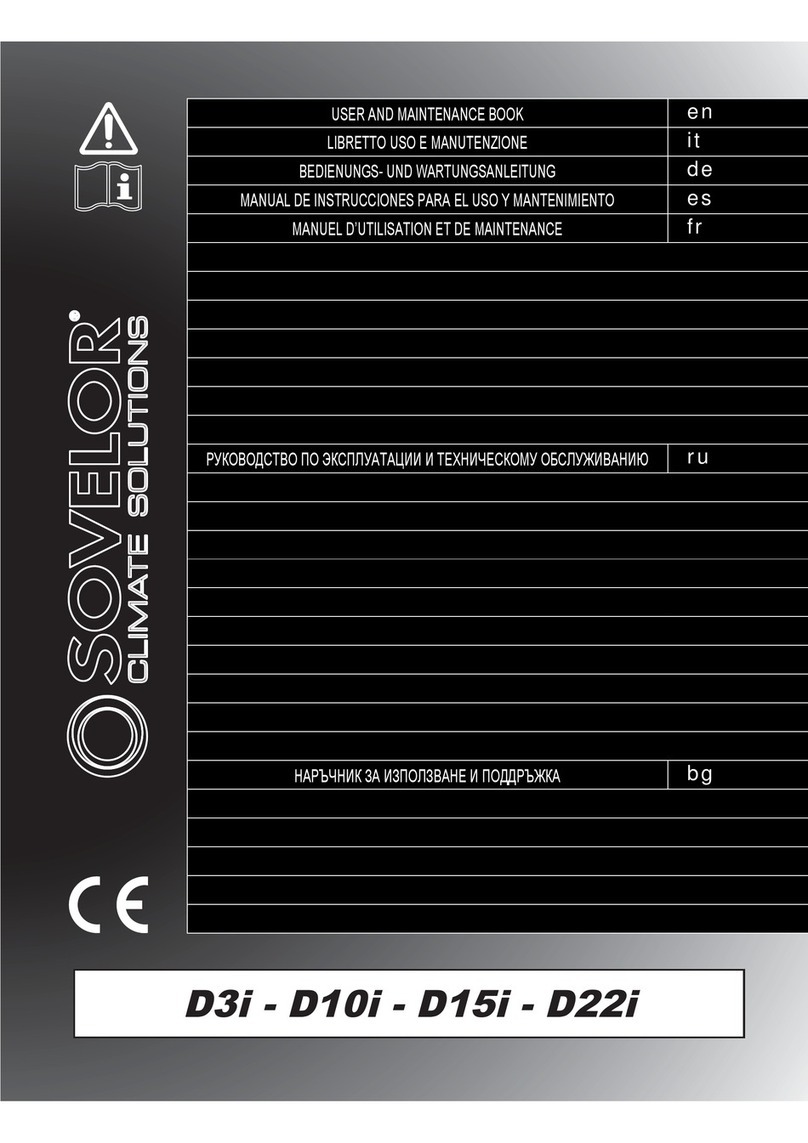
Dantherm
Dantherm Sovelor D3i User and Maintenance Book
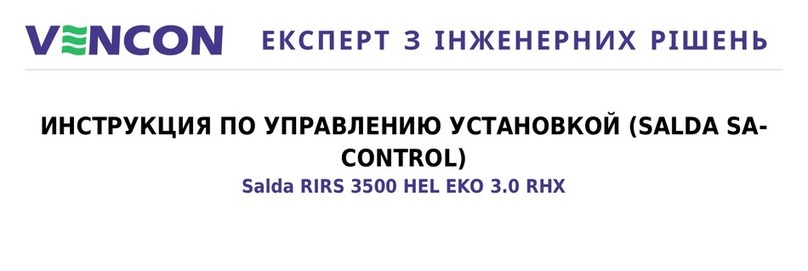
Salda
Salda RIRS 3500 HEL EKO 3.0 RHX QUICK LAUNCH GUIDE
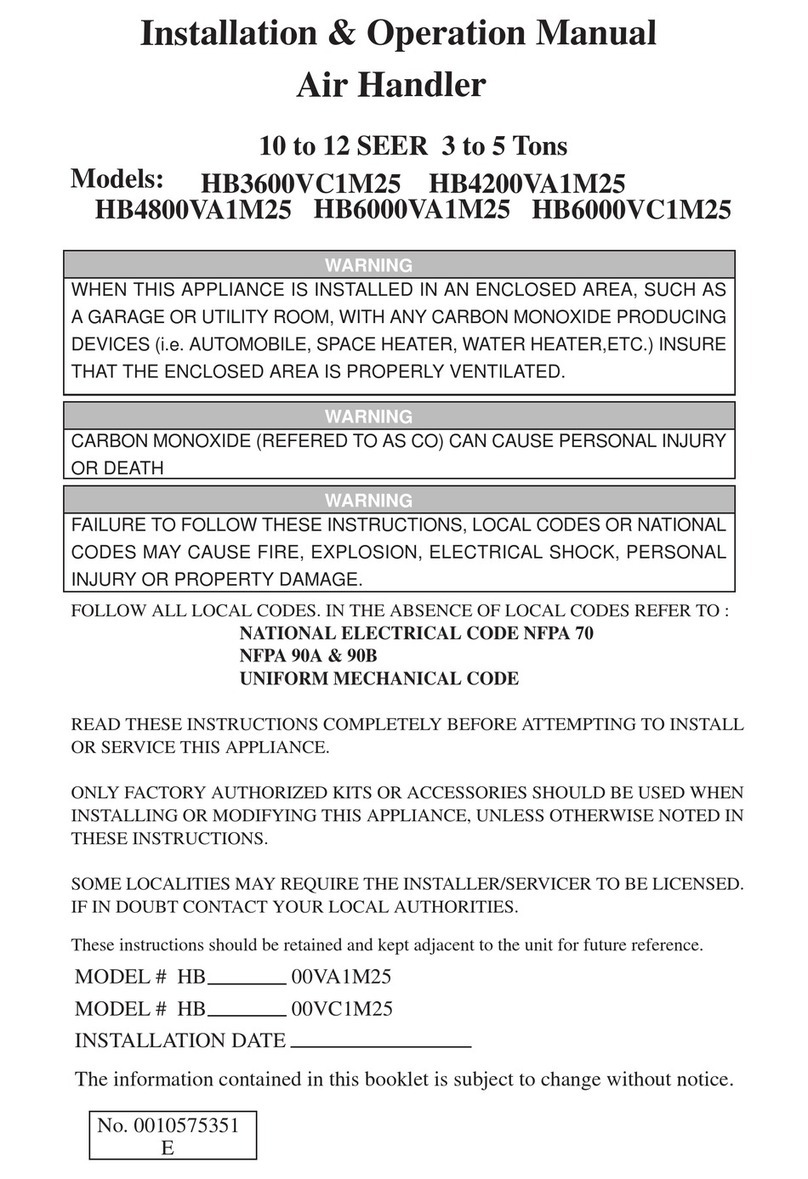
Haier
Haier HB3600VC1M25 Installation & operation manual
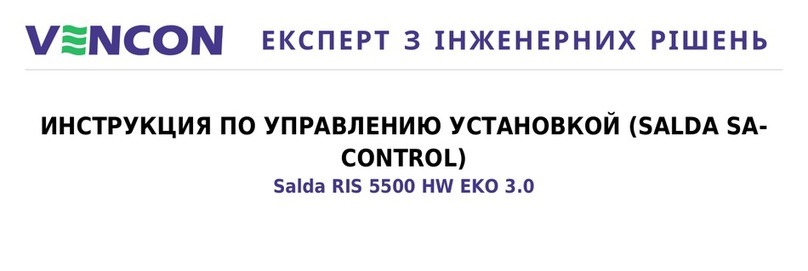
Salda
Salda RIS 5500 HW EKO 3.0 QUICK LAUNCH GUIDE

Trane Technologies
Trane Technologies THERMO KING UT-1290 installation manual
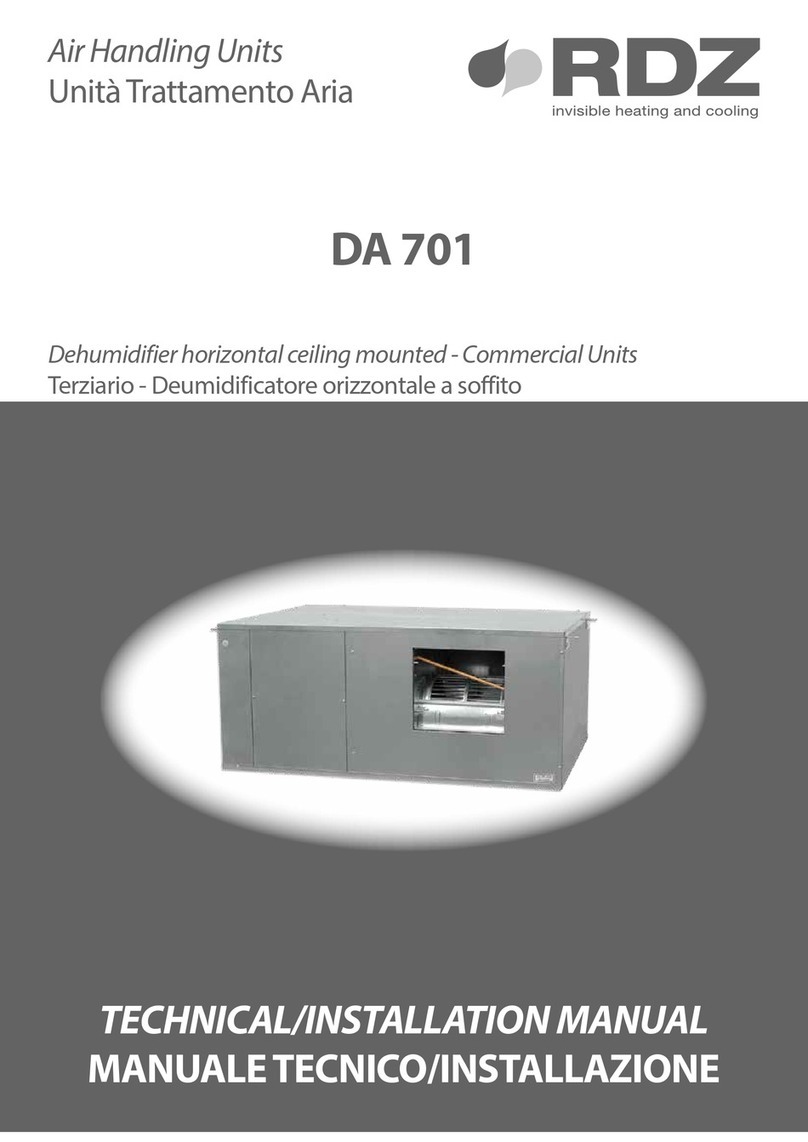
RDZ
RDZ DA 701 Technical installation manual
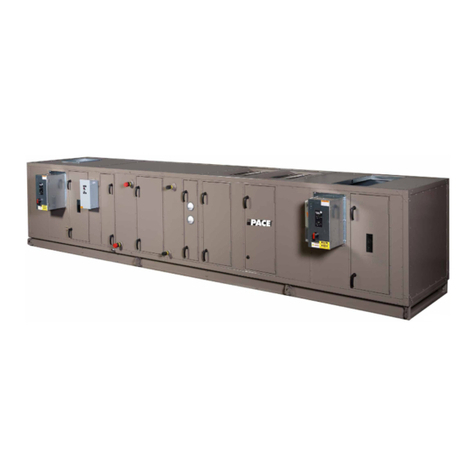
Pace
Pace PAI Installation and assembly manual
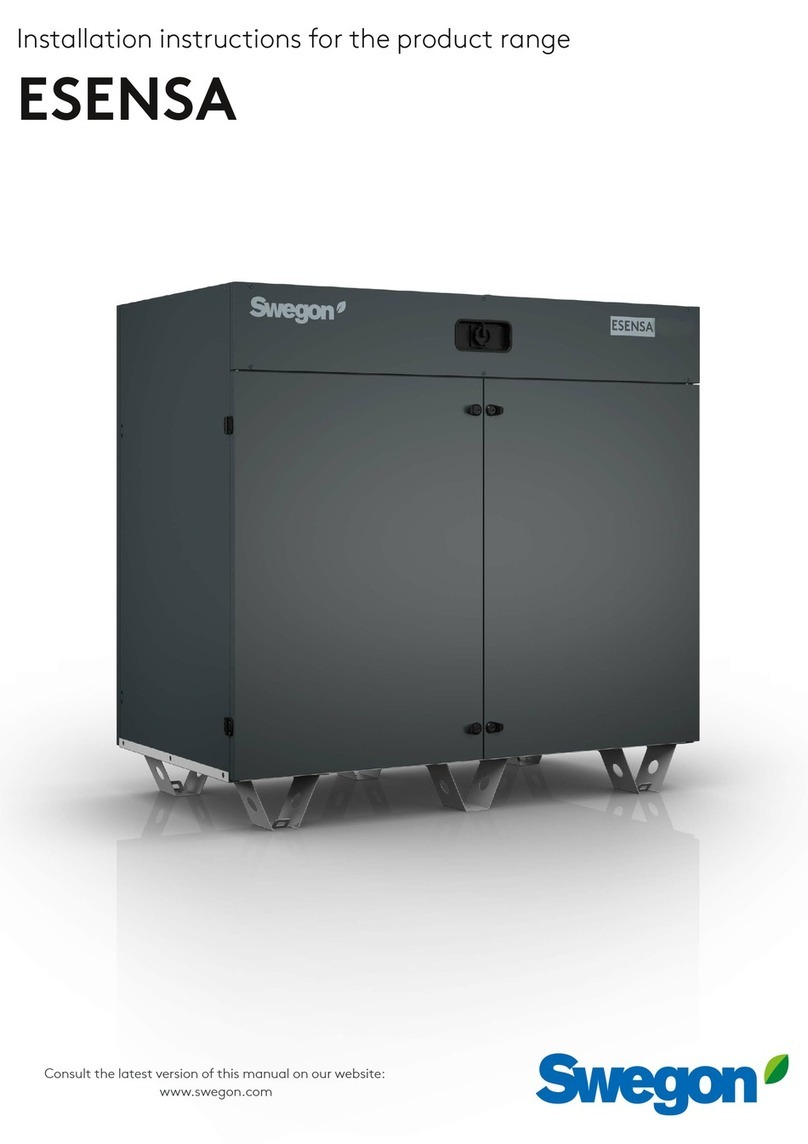
Swegon
Swegon ESENSA PX TOP 05 installation instructions
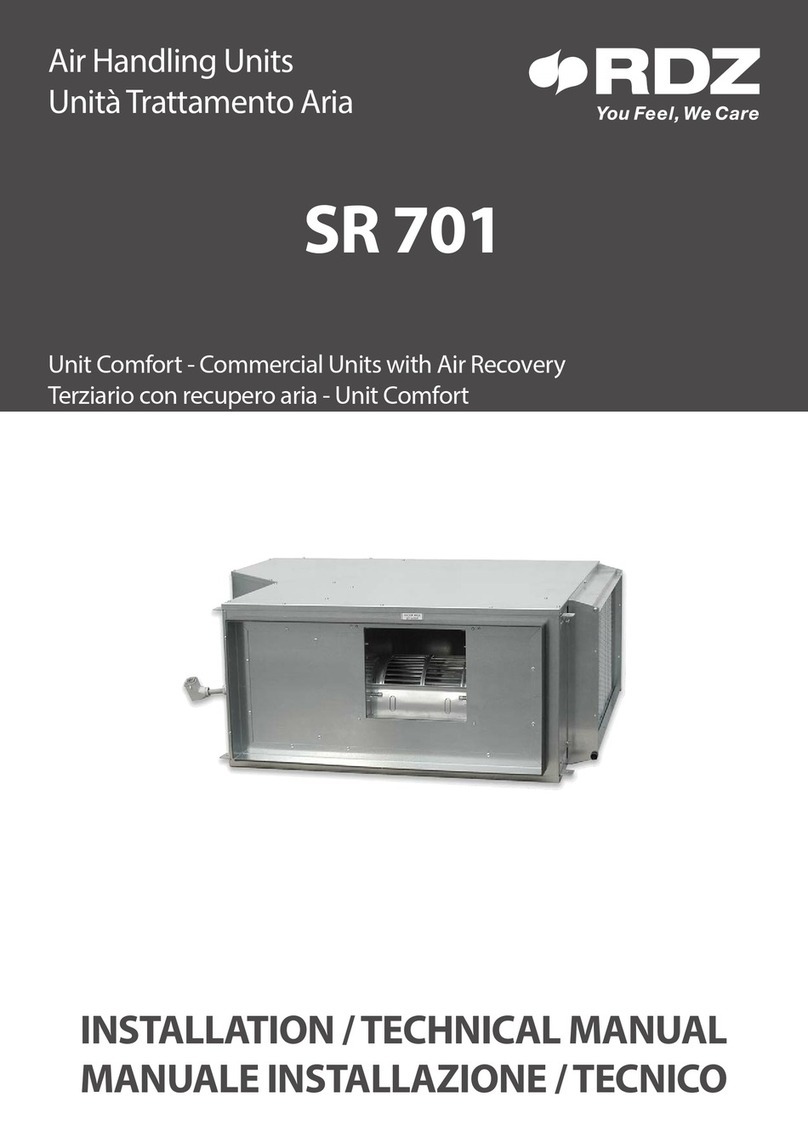
RDZ
RDZ SR 701 Installation & technical manual

Carrier
Carrier 61AF operating instructions