KONRAD 520 User manual

GENERAL INSTALLATION MANUAL
500 Series Models
KONRAD, INC.
1421 HANLEY ROAD • HUDSON, WI 54016-9376 USA
Phone: 715-386-4203 • Toll Free: 1-800-927-3545 • Fax: 715-386-4219
www.konradmarine.com

All rights reserved. Reproduction or use, without express permission, of editorial or pictorial content, in any manner,
is prohibited. No patent liability is assumed with respect to the use of the information contained herein. While
every precaution has been taken in the preparation of this book, the publisher assumes no responsibility for errors
or omission. Neither is any liability assumed for damages resulting from use of the information contained herein.
All instructions and diagrams have been checked for accuracy and ease of application; however, success and safety
in working with tools depend to a great extent upon individual accuracy, skill and caution. For this reason, the
publishers are not able to guarantee the result of any procedure contained herein. Nor can they assume responsibility
for any damage to property or injury to persons occasioned from the procedures. Persons engaging in the procedure
do so entirely at their own risk.
*Original equipment manufacturer’s names, drawings, colors and part numbers are used for identication purposes only.
We are in no way implying that any of our parts are the original equipment manufacturer’s product.
500 SERIES INSTALLATION MANUAL JULY 2016PAGE II

Version 3
Part # 11-660
KONRAD, INC.
1421 HANLEY ROAD • HUDSON, WI 54016-9376 USA
Phone: 715-386-4203 • Toll Free: 1-800-927-3545 • Fax: 715-386-4219
GENERAL INSTALLATION MANUAL
500 Series Models
*Written/Narrated by Randall J. Soe, January 2007
*Modied by Randall J. Soe, January 2010
500 SERIES INSTALLATION MANUALJULY 2016 PAGE III


TABLE OF CONTENTS
520 Stern Drive Description ........................................................1
540 Stern Drive Description ........................................................2
560 Stern Drive Description ........................................................3
Stern Drive General Information .................................................4
General Operation........................................................................4
Safety Notices ..............................................................................4
Tools Recommended For Installation .......................................5-6
Torque Specications For Selected Fasteners..............................7
Installation Guidelines .................................................................8
Figure A: 500 Series Cutout Template.........................................9
Figure B: 500 Series X-Dimension Guidelines .........................10
KONRAD 500 SERIES DRIVE INSTALLATION
Step 1: Transom Cutout ........................................................11-12
Step 2: Transom Assembly Installation.................................13-14
Step 3: Oil Reservoir Installation..........................................15-17
Step 4: Trim/Lift Pump Installation ......................................18-21
Figure C: Trim System Electrical Drawing 12 Volt...................22
Figure D: Trim System Electrical Drawing 24 Volt...................23
Step 5: Stern Drive Installation.............................................24-27
Figure E: Alignment Specications Chart .................................28
Step 6: Alignment Procedures...............................................29-32
Step 7: Trim Cylinder Installation.........................................33-34
Figure F: Trim Assembly Diagram ............................................35
Figure G: Trim Assembly Individual Components....................36
Step 8(a): 520 / 540 Propeller Installation .................................37
Step 8(b): 560 Propeller Installation..........................................38
Step 9: Stern Drive Lubrication ............................................39-41
Step 10: Trim/Lift Control Module Installation....................42-45
Step 11: Trim/Lift Pump Filling/Bleeding Procedure...........46-47
Step 12: Setting Trim/Lift Limit & Sender Switch...............48-49
Step 13: Manual Hydraulic Steering System Installation.....50-53
Figure H: Routing Diagram 30-462R ........................................54
Step 14: Power Steering System Installation........................55-59
Figure I: Routing Diagram 30-390R..........................................60
Figure J: Hoses for Assembly KM #30-390 ..............................61
Figure K: 30-264 Parts List........................................................62
Figure L: 30-274 Parts List........................................................63
500 SERIES INSTALLATION MANUALJULY 2016 PAGE V

Step 15: Rubber Coupling Extension Shaft(s)......................64-67
Step 16: U-Joint Extension Shaft Installation.......................68-69
Step 17: CV Extension Shaft Installation .............................70-71
Step 18: Drive Shaft Shroud Installation ...................................72
Figure M: Rear Mount/Tailpiece Cutout Template....................73
Step 19: Rear Mount / Tailpiece Installation ........................74-76
Step 20:Installation Review ..................................................77-78
Application Trial Data Forms ...............................................79-81
TABLE OF CONTENTS (Continued)
500 SERIES INSTALLATION MANUAL JULY 2016PAGE VI

Recreational Performance
Maximum Recommendation:
1000 Nm (738 lb. ft.) of torque for
diesel or gas applications. Maximum
operation: 250 hours per year for planing
type hulls of highly intermittent operation.
Gross weight to horsepower less than
15.2 kg/kw (25 lbs./hp). This classification
includes private, non-commercial, non-
charter, sport/leisure activity craft. Long
range pleasure cruisers, sport fishing
charters and commercial service craft
are NOT in this service classification.
Standard warranty.
Commercial/Military
Performance
Maximum recommendation:
755 Nm (557 lb. ft.) of torque for semi
displacement and planing hulls of
intermittentoperation.Maximumoperation:
1000 hours per year and gross weight
to horsepower less than 21.3 kg/kw (35
lbs./hp). This classication includes light
commercial charter/sport activity craft,
patrol and crew boats. Standard warranty.
Medium Duty Performance
Maximum operation:
678 Nm (500 lb. ft.) of torque for semi-
displacement and displacement mono-
hulls of intermittent operation with some
variations in engine rpm and power.
This classication includes charter and
commercial craft. Note: These applications
must be approved by the factory. Standard
warranty.
520 Classications
520 Stern Drive Description
The Konrad 520 stern drive is the hardest working stern
drive in the marine industry today. Designed for high-
use, endurance-type applications, the Konrad 520 is
recognized for its versatility and long-term durability.
It is not a “pleasure” drive. It’s a working drive that
can take you shing all day or patrol harbors 24/7. The
Konrad 520 is the only commercial-rated stern drive
available for diesel applications in the 180-440 hp
(134 - 328 kw) range.
The Konrad 520 stern drive is designed to
accommodate aluminum or stainless steel propellers
with three (3) to ve (5) blades. Propellers are chosen
depending on the application and performance criteria.
The maximum diameter propeller size for the Konrad
520 stern drive is 20 in. (50.8 cm).
500 SERIES INSTALLATION MANUALJULY 2016 PAGE 1

The Konrad 540 is specically designed for high speed
applications, both diesel and gasoline. This versatile
stern drive is manufactured in two variations: Standard
and High Performance. The High Performance model
includes a lower hydrodynamic nose cone, and both
versions have a lightweight design to deliver superior
hole-shot and on-plane performance. The Konrad 540
allows mariners to apply greater power levels, while
still delivering performance and reliability.
The Konrad 540 stern drive is designed to
accommodate aluminum or stainless steel propellers
with three (3) to six (6) blades. Propellers are chosen
depending on the application and performance criteria.
The maximum diameter propeller size for the Konrad
540 stern drive is 16 in. (40.6 cm).
Commercial Performance
Maximum recommendation:
755 Nm (557 lb. ft.) of torque for diesel
or gas applications. Maximum operation:
500 hours per year for planing type
hulls of highly intermittent operation.
Gross weight to horsepower less than
12.2 kg/kw (20 lbs./hp). This clas-
sication includes light commercial
charter/sport activity craft, patrol and
intercept boats. Standard warranty.
High Performance
Maximum operation:
100 hours/year for racing applications at
highly intermittent operation. Gross weight
to horsepower less than 12.2 kg/kw (20
lbs./hp). No warranty.
540 Stern Drive Description
540 Classications
Recreational Performance
Maximum recommendation:
1000 Nm (738 lb. ft.) of torque for diesel
or gas applications. Maximum operation:
250 hours per year for planing type hulls of
highly intermittent operation. Gross weight
to horsepower less than 12.2 kg/kw (20
lbs./hp). This classication includes pri-
vate, non-commercial, non-charter, sport/
leisure activity craft. Long range pleasure
cruisers, sport shing charters and com-
mercial service craft are NOT in this ser-
vice classication. Standard warranty.
500 SERIES INSTALLATION MANUAL JULY 2016PAGE 2

The Konrad 560 Twin Prop System is engineered
to reduce stress on the gears using dual propeller
technology, providing a reliable, durable stern drive
unit. With counter rotating propellers, the 560 reduces
propeller roll, which increases efciency and control.
The Konrad 560 stern drive features two, one
piece propeller shafts that accommodate two
stainless steel propellers. The specially designed
propellers have one blade conguration: 3 blades
on the forward prop and 4 blades on the rear
prop. The propeller pitches are manipulated on
each application to meet the performance criteria.
The maximum diameter of the propellers in the
Konrad 560 is 16 in. (40.6 cm) for the forward
prop, and 15.25 in. (38.7 cm) for the rear prop.
Commercial Performance
Maximum recommendation:
755 Nm (557 lb. ft.) of torque for diesel
or gas applications. Maximum operation:
500 hours per year for planing type
hulls of highly intermittent operation.
Gross weight to horsepower less than
12.2 kg/kw (20 lbs./hp). This clas-
sication includes light commercial
charter/sport activity craft, patrol and
intercept boats. Standard warranty.
560 Stern Drive Description
560 Classications
Recreational Performance
Maximum recommendation:
1000 Nm (738 lb. ft.) of torque for diesel
or gas applications. Maximum operation:
250 hours per year for planing type hulls of
highly intermittent operation. Gross weight
to horsepower less than 12.2 kg/kw (20
lbs./hp). This classication includes pri-
vate, non-commercial, non-charter, sport/
leisure activity craft. Long range pleasure
cruisers, sport shing charters and com-
mercial service craft are NOT in this ser-
vice classication. Standard warranty.
500 SERIES INSTALLATION MANUALJULY 2016 PAGE 3

Stern Drive
General Information
The Konrad 500 Series stern drives are designed
to accommodate engines that generate up to 738 lb.
ft. (1000 Nm) of torque.
There is a sixteen degree (16°) trim range to
optimize vessel performance while underway.
There is an additional 30 degrees (30°) of lift range
that may only be used in an emergency or when the
stern drive is being serviced or transported.
The Konrad 500 Series stern drives are
designed for applications where the vessel transom
angle is 14 degrees (14°). Applications that do not
meet this criteria may require extra equipment or
modications, or may not be possible at all. The
Konrad 520 stern drive is designed to accommodate
propellers (aluminum and stainless steel) with
a maximum diameter of 20 in (50.8 cm). The
Konrad 540 and 560 can accommodate propellers
(aluminum and stainless steel) with a maximum
diameter of 16 in. (40.6 cm).
General Operation
The engine produces power (clockwise or
counterclockwise) that is transmitted through a
reversing transmission. A coaxial planetary-style
reversing transmission is normally used in recre-
ational applications. A twin shaft vertically offset
standard reversing transmission (with coaxial ad-
ditions available) is normally used in commercial
applications. From this point the transmission is
connected via close couple or drive shaft (different
shafts are discussed in detail in Step 6 on pages 29
- 32 in this manual). The power is then transmitted
through a series of shafts and gears and then to the
propeller(s).
Safety Notices
Read and understand all of the safety precau-
tions and warnings before performing any installa-
tion or repair.
This list contains the general safety precautions
and warnings that MUST be followed to provide
personal safety. This list is only a suggested safety
guideline. Working conditions vary greatly and
safety measures will vary upon your individual cir-
cumstances.
ALWAYS USE CAUTION. Make sure the
work area surrounding the product is safe. Be
aware of hazardous conditions that can exist.
ALWAYS wear protective eyewear and
protective footwear when working.
DO NOT wear loose-tting or torn clothing.
Remove all jewelry when working.
DO NOT work on anything that is supported
only by lifting jacks or a hoist.
ALWAYS use blocks or proper stands to
support the product before performing any
service work.
TO AVOID PERSONAL INJURY, use
a hoist or get assistance when lifting stern
drive components. Make sure all lifting de-
vices such as chains, hooks or slings are in
good condition and are of the correct lifting
capacity.
500 SERIES INSTALLATION MANUAL JULY 2016PAGE 4

500 SERIES INSTALLATION MANUALJULY 2016 PAGE 5
Konrad has an installation tool kit available for purchase.
The following is a complete list of all items included in the kit.
Installation Tool Kit
30 – 190
NOTE: Additional tools may be required.
Tool box
3/8 in. Drill
13/64 in. Drill Bit (pilot for lag screws)
Jig Saw
Jig Saw Blades (2)
3/8 in. Drive Ratchet (quick release)
3/8 in. Drive 3 in. Extension
3/8 in. Drive 6 in. Wobble Extension
3/8 in. Drive to 1/4 in. Drive Reducer
1/4 in. Drive 1/4 in. Socket
3/8 in. Drive to 5/16 in. Socket
3/8 in. Drive 7/16 in. Socket
3/8 in. Drive 1/2 in. Deep Socket
3/8 in. Drive 1/2 in. Socket
3/8 in. Drive 9/16 in. Socket
3/8 in. Drive 5/8 in. Deep Socket
3/8 in. Drive 3/4 in. Socket
3/8 in. Drive 3/4 in. Deep Socket
3/8 in. Drive 5/16 in. Allen Head Socket
5/16 in. Combination Wrench
3/8 in. Combination Wrench
7/16 in. Combination Wrench
1/2 in. Combination Wrench
9/16 in. Combination Wrench
5/8 in. Combination Wrench
11/16 in. Combination Wrench
3/4 in. Combination Wrench
1-7/16 in. Combination Wrench
8 in. Adjustable Wrench
4 in. Flat Blade Screwdriver
6 in. Flat Blade Screwdriver
4 in. #2 Phillips Screwdriver
6 in. #3 Phillips Screwdriver
6 in. #2 Phillips Bit
6 in. #3 Phillips Bit
7 in. Vice Grips
6 in. Slip Joint Pliers
12 in. Flat Blade Pry Bar
15 in. Pry Bar
Diagonal Side Cutter
1-1/4 in. Putty Knife
Center Punch/Scratch
100 Grit Sandpaper (5) pcs.
Black Permanent Marker
2 lb. Hammer
Breathing Mask
Rasp File (Flat/Half Round)
Assortment of Cable Clamps (15)
Screws for Cable Clamps (15)
Pilot Drill 4/Cable Clamp Screws 3/32 in.
8 in. Cable Ties (15)
Horseshoe Magnet
Tools Recommended for Installation

500 SERIES INSTALLATION MANUAL JULY 2016PAGE 6
Tools for 30-264 and 30-272
Rubber Coupling Drive Shaft (if applicable)
Tools Recommended for Installation (continued)
TO-066 Adapter, Torque Wrench 12 mm
TO-067 Adapter, Torque Wrench 22 mm.
TO-068 Adapter, Torque Wrench 24 mm.
GO-017, Dial Indicator with Magnetic Stand

500 SERIES INSTALLATION MANUALJULY 2016 PAGE 7
Listed below are the torque specifications for selected fasteners. Additional torque specifications are listed
throughout this manual.
Torque Specications for Selected Fasteners
Description Torque Value
Drive Shaft Flange to Transmission
Output Flange Shaft Nuts/Bolts (if applicable) 70 lb. ft. (95 Nm)
Transom Assembly / Gimbal Housing
Studs to Inner Transom Plate Nuts (8) 25-30 lb. ft. (34-41 Nm)
Drive Shaft Housing to Gear Housing Nuts and Bolts (8) 35 lb. ft. (47 Nm)
Power Trim Cylinder to Anchor Pin, Nuts (4)
Tighten until approx.
two (2) threads show.
Do not over tighten.
Lifting Bracket Top Cover (and Emergency Tiller Arm if applicable) (6) 20 lb. ft. (27 Nm)
Stern Drive Unit to Bell Housing, Nuts (6) 55 lb. ft. (75 Nm)
Gimbal Carrier Bolts (S.H.C.S.) (3) (if applicable) 70 lb. ft. (95 Nm)
520 Propeller Nut (1) 80 lb. ft. (109 Nm)
540 Propeller Nut (1) 55 lb. ft. (75 Nm)
560 Forward Propeller Nut (1) 100 lb.ft. (136 Nm)
560 Rear Propeller Nut (1) 60 ft.lb. (81 Nm)

1) Ensure that the propeller height is performed
according to guidelines detailed in diagrams
10-410 (Figures A and B on pages 9 and 10
in this manual). The height of the propeller
is critical to a successful application. If the
propeller centerline is too low, excessive
drag can occur based on transom assembly
location. Intermediate spacers are available
for special concerns.
2) Ensure that the water ow to the propeller
is clear and consistent without interruptions.
Protrusions on the hull surface create a neg-
ative pressure area and induce turbulence.
Turbulence can cause severe propeller inef-
ciency and excessive torsional vibration.
Common problems are:
• Water pickup
• Sonar transducers
• Retrotted surfaces which are not
properly faired or smoothed
• Any hull shape which does not
provide smooth transition
• In heavy applications, the bow can
produce turbulence if the attitude
of the vessel is weighted forward.
• Improper listing of the vessel due
to weight distribution
Installation Guidelines
3) Ensure that the vessel center of gravity is
properly placed. Excessive weight forward
or aft can signicantly affect performance
and the efciency of the propeller.
4) Ensure that the stern drive is trimmed to
the correct level. While undertrimming can
cause premature u-joint wear, overtrimming
can cause propeller inefciency, porpoising,
and premature gear wear.
500 SERIES INSTALLATION MANUAL JANUARY 2010PAGE 8

in.
in.
in.
in.
in.
in.
in.
in.
in.
in.
in. Note: Drawing not to scale.
FIGURE A: 500 Series CUTOUT TEMPLATE
500 SERIES INSTALLATION MANUALJANUARY 2010 PAGE 9

FIGURE B: 500 Series X-DIMENSION GUIDELINES
Note: Drawings not to scale.
500 SERIES INSTALLATION MANUAL JANUARY 2010PAGE 10

A
B
CD
1.1 Scribe an arc from points A and B to the bottom center of
the transom exterior. Scribe an arc from points C and D to
the top center of the transom exterior. Where the previous
mentioned arcs intersect, scribe a vertical line approxi-
mately 28 in. (71 cm) long. This will represent the center
line of the stern drive.
NOTE: For twin application, measure (to
the port and starboard) off the vessel verti-
cal center line over to the engine crank shaft
center line and scribe a vertical center line
parallel to the vessel vertical center line. See
the lower drawing of Figure B on page 10 in
this manual for explanation.
1.2 After establishing the x-dimension (see Figure B on page
10 in this manual), scribe a horizontal line at least 18 in.
(46 cm) long, perpendicular and centered on the existing
vertical line (scribed in Step 1.1).
NOTE: Specic characteristics of an installation may
change the recommended vertical drive position. Please
contact Konrad with any specic concerns.
ATTENTION: If you are installing the Konrad
“Rear Mount / Tail Piece” assembly, please go
to step 19 (page 73 - 74) in this manual.
Step 1: Transom Cutout
FIGURE 1B
FIGURE 1A
500 SERIES INSTALLATION MANUALJANUARY 2010 PAGE 11

500 SERIES INSTALLATION MANUAL JULY 2016PAGE 12
1.3 Place the cutout template (10-455) on the exterior of the
transom and position it so the scribed horizontal and ver-
tical match up with the scribed center lines on the tem-
plate.
1.4 Trace the cut out area and the eight (8) holes. Remove the
template.
1.5 Center punch the eight (8) holes traced in Step 1.4. Drill
the eight (8) holes through the transom using a 5/8 in. (16
mm) drill bit.
NOTE: Holes must be drilled perpendicular to the tran-
som face.
1.6 Using a reciprocating saw, cut out the area traced in Step
1.4. Use a le or rasp to touch up the cutout area.
NOTE: Cut must be made perpendicular to transom
face.
NOTE: For berglass transoms, it is recommended that
berglass epoxy resin be applied to the cut areas. Verify
that cutout area is correctly sized and shaped before
applying epoxy. Allow proper drying/setup time for epoxy
to cure.
Step 1: Transom Cutout (continued)
FIGURE 1A
FIGURE 1C
FIGURE 1B

500 SERIES INSTALLATION MANUALJULY 2016 PAGE 13
2.1 Grease the transom assembly gasket with marine grade
grease (see Figure 2A).
NOTE: If the gimbal carrier assembly is not mounted
in the gimbal housing bore, it should be done at this time
(see Figure 2B).
NOTE: The gimbal carrier ange may differ from the
one pictured in Figure 2B per application.
1) Lightly grease the carrier assembly and o-ring,
then slide it into the gimbal housing bore.
2) Rotate the carrier assembly to achieve correct
orientation. The brass nipple should be at
approximately two o’clock.
3)
Torque the three (3) fasteners to 70 lb. ft. (95 Nm).
NOTE: The gimbal carrier ange may differ from the
one pictured in Figure 2B per application.
2.2 Guide the transom assembly studs through the eight (8)
holes in the transom.
NOTE: The weight of the transom assembly is 81 lbs.
(36.7 kg). Use caution when lifting.
NOTE: Some installations/applications require an ex-
ternal adapter plate.
NOTE: Proper stud length varies due to hull thickness.
Stud length is also dictated by peripheral equipment that
mounts inside the hull (steering cylinder bracket, inner
transom plate, drive shaft shroud, etc.). Verify correct
stud length before continuing past this step.
Step 2: Transom Assembly Installation
FIGURE 2B
FIGURE 2C
FIGURE 2A

500 SERIES INSTALLATION MANUAL JULY 2016PAGE 14
2.3 Place the inner transom backing plate (10-357) over the
eight (8) studs from the inside of the vessel.
NOTE: If an internal steering cylinder is going to be
used, the bracket can be mounted on the upper one (1) or
two (2) sets of horizontal studs depending on the steering
cylinder style used.
NOTE: The inner transom plate may require modication
or elimination depending on steering cylinder assembly
used.
NOTE: If an inner transom backing plate is not used, the
round washers (10-415) must be replaced with rectangular
washers (10-941).
2.4 Secure the transom assembly to the transom by using
eight (8) nylock nuts (10-334) and eight (8) at washers
(10-415). Torque to 25-30 lb. ft. (34-41 Nm).
NOTE: Place inner transom backing plate continuity
cable between the washer and nylock nut of either of
the top two transom assembly studs before tightening (if
applicable).
NOTE: Connect the tiller arm continuity cable to the
inner transom backing plate by using the small phillips
head screw (if applicable).
NOTE: The two (2) oil lines in this photo will be ran and
attached in a later step.
Step 2: Transom Assembly Installation (continued)
FIGURE 2D
FIGURE 2E
Other manuals for 520
1
This manual suits for next models
2
Table of contents
Other KONRAD Engine manuals
Popular Engine manuals by other brands

Stiga
Stiga TRE 352 Operator's manual
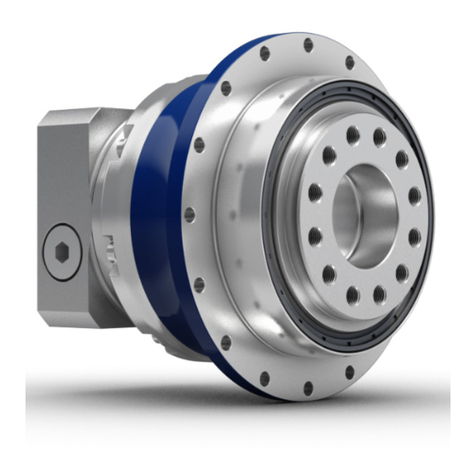
Wittenstein Alpha
Wittenstein Alpha Advanced TP+ Series operating manual
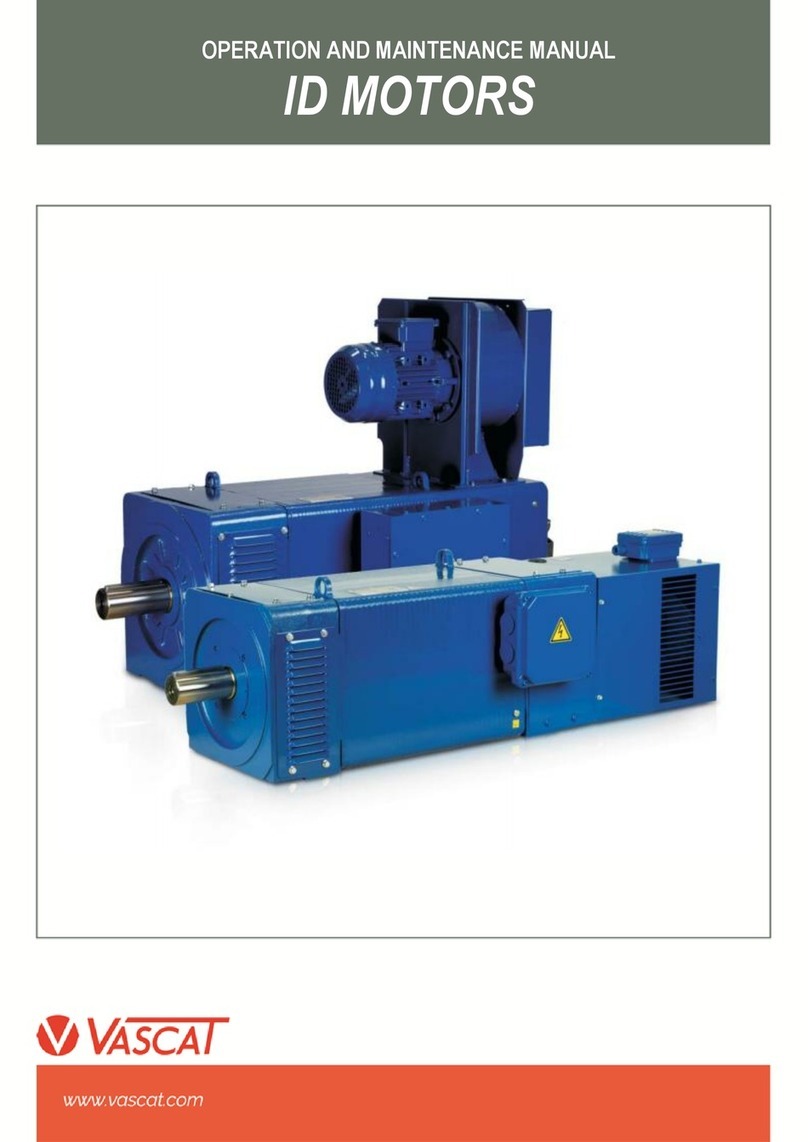
Vascat
Vascat ID Series Operation and maintenance manual
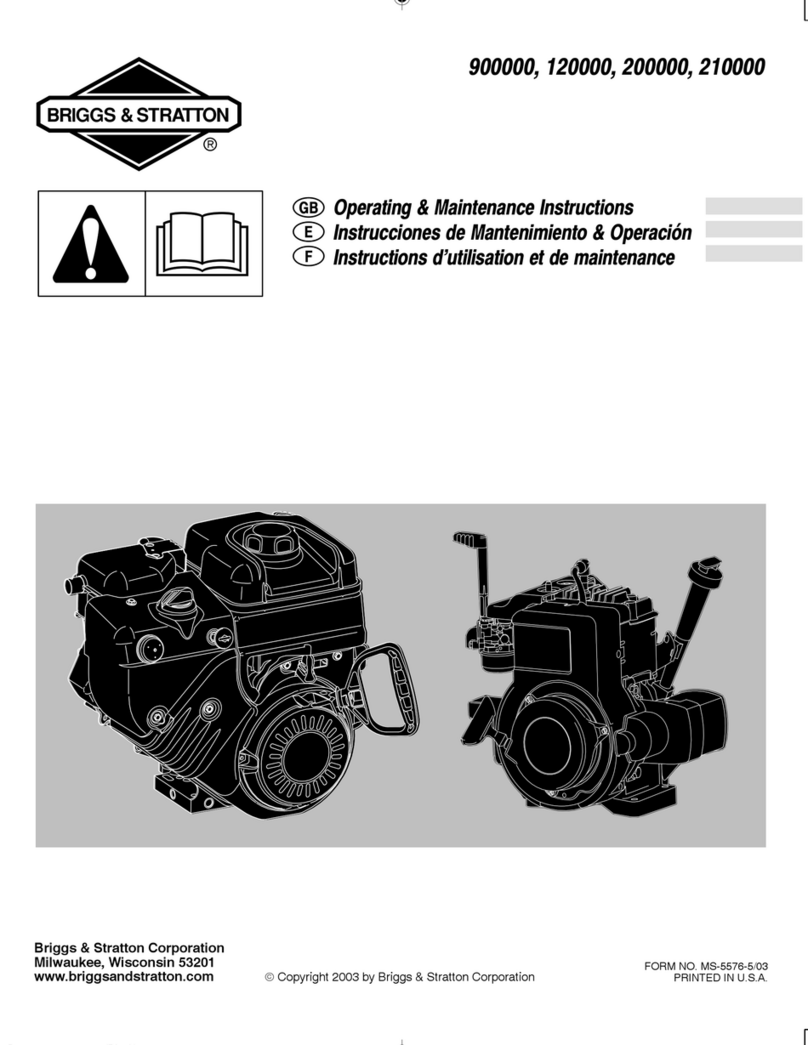
Briggs & Stratton
Briggs & Stratton Intek 200000 Operating & maintenance instructions

Briggs & Stratton
Briggs & Stratton classic 450 series Operating & maintenance instructions
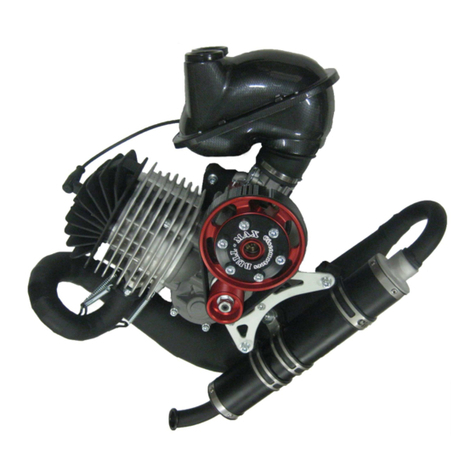
Ciscomotors
Ciscomotors BullMax 250 Simplified maintenance manual