KRUEGER KLPS Dimensions and installation guide

WWW.KRUEGER-HVAC.COM
Models: KLPS, KLPS-D, KLPP, KQFS,
KQFS-FA, KQFP, QFC, QFV
FAN POWERED
TERMINAL UNITS
INSTALLATION, START-UP, AND
SERVICE INSTRUCTIONS FOR
KRUEGER TERMINAL UNITS

Fan Powered Terminal Units IOM
SAFETY NOTE.............................................................................................4
PRE-INSTALLATION...................................................................................4
General ...............................................................................................................4
Control Offerings .............................................................................................4
Storage And Handling.....................................................................................4
Initial Inspection...............................................................................................7
Unit Identification............................................................................................7
Installation Precaution....................................................................................7
Codes ..................................................................................................................7
Unit Suspension................................................................................................7
Warranty............................................................................................................7
CONTROL OPTIONS...................................................................................7
Analog Electronic Controls.............................................................................8
Direct Digital Controls (By Others) .............................................................8
Pneumatic Controls.........................................................................................8
No Control Units...............................................................................................8
INSTALLATION ...........................................................................................9
Step 1 - Install Fan - Powered Box...............................................................9
Step 2 - Make Duct Connections..................................................................11
Step 3 - Power Wiring ....................................................................................11
Step 4 - System Setup And Calibration......................................................12
START-UP ................................................................................................14
General ...............................................................................................................14
Initial Start-Up Procedures............................................................................14
Balancing Krueger Fan Terminals.................................................................15
Speed Controller...............................................................................................20
Setting Fan Air Flow With EC Motors..........................................................21
PNEUMATIC CONTROLS ...........................................................................41
General ...............................................................................................................41
TABLE OF CONTENTS

Fan Powered Terminal Units IOM
ANALOG CONTROLS .................................................................................44
Installation And Balancing Procedures.......................................................44
WATER VALVE INSTALLATION ..................................................................46
Service................................................................................................................46
TROUBLESHOOTING .................................................................................48
TABLE OF CONTENTS

4
Fan Powered Terminal Units IOM
PRE-INSTALLATION
GENERAL
The KLPS, KLPS-D, KQFS, KQFS-FA & QFC constant volume
(series) and KLPP, KQFP & QFV variable volume (parallel) fan
powered boxes (see Figure 1 & 2) are equipped to provide
pressure independent, variable volume (VAV). The units can
also be equipped with factory-installed Analog, Pneumatic,
or eld supplied direct digital controls. Units are available
with factory-installed electric or hot water heat.
CONTROL OFFERINGS
Each KLPS, KLPS-D, KLPP, KQFS, KQFS-FA, KQFP, QFC &
QFV unit is supplied with four quadrant multi-point center
averaging airow sensor as a standard feature. These
sensors oer airow averaging capability that results in an
airow sensing capacity equal to any competitive unit.
Control options include pressure independent pneumatic,
analog electronic and eld supplied direct digital. Pneumatic
controls are available with linear actuators and single-
function or multi-function controllers. The multi-function
controller provides a simple switchover from normally open
to normally closed applications. Electronic control units
feature a factory-installed enclosure that provides easy
access for eld connections.
STORAGE AND HANDLING
Inspect for damage upon receipt. Shipping damage claims
should be led with shipper at time of delivery. Store in a
clean, dry, and covered location. Do not stack units. When
unpacking units, care should be taken that the inlet collars
and externally mounted components do not become
damaged. Do not lift units using collars, sensors, or externally
mounted components as handles. If a unit is supplied with
electric or hot water heat, care should be taken to prevent
damage to these devices. Do not lay uncrated units on end
or sides. Do not stack uncrated units over 6 ft high. Do
not handle control boxes by tubing connections or other
external attachments. Table 1 shows component weights.
Air-handling equipment will provide safe and reliable service
when operated within design specifications. The equipment
should be operated and serviced only by authorized
personnel who have a thorough knowledge of system
operation, safety devices, and emergency procedures. Good
judgment should be used in applying any manufacturer’s
instructions to avoid injury to personnel or damage to
equipment and property.
WARNING: Disconnect all power to the unit before
performing maintenance or service. Unit may
automatically start if power is not disconnected.
Electrical shock and personal injury could result.
WARNING: If it is necessary to remove and dispose of
mercury contactors in electric heat section, follow
all local, state, and federal laws regarding disposal of
equipment containing hazardous materials.
SAFETY NOTE
Figure 1 - Series Fan Powered Terminal Unit (KQFS)
Figure 2 - Series DOAS Fan Powered Terminal Unit (KLPS-D)

5
Fan Powered Terminal Units IOM
QFC (lbs.)
UNIT
SIZE
UNIT
WEIGHT
PNEUMATIC CONTROLS
ADD
DDC OR ANALOG
CONTROLS ADD
ELECTRIC
HEAT ADD
HOT WATER ADD
1-ROW 2-ROW
270 4 9 30 19 21
370 4 9 30 20 22
485 4 9 32 22 25
585 4 9 32 24 28
6100 4 9 35 25 30
7140 4 9 40 35 43
QFV (lbs.)
UNIT
SIZE
UNIT
WEIGHT
PNEUMATIC CONTROLS
ADD
DDC OR ANALOG
CONTROLS ADD
ELECTRIC
HEAT ADD
HOT WATER ADD
1-ROW 2-ROW
2114 4 9 30 19 21
3114 4 9 30 19 21
4115 4 9 32 19 21
5122 4 9 32 12 14
6123 4 9 32 12 14
7127 4 9 40 12 14
KQFS (lbs.)
UNIT
SIZE
UNIT
WEIGHT
PNEUMATIC CONTROLS
ADD
DDC OR ANALOG
CONTROLS ADD
ELECTRIC
HEAT ADD
HOT WATER ADD
1-ROW 2-ROW
2185 4 9 93 912
3200 4 9 80 912
4200 4 9 32 912
5225 4 9 32 12 17
6250 4 9 35 12 17
7260 4 9 40 12 17
KQFP (lbs.)
UNIT
SIZE
UNIT
WEIGHT
PNEUMATIC CONTROLS
ADD
DDC OR ANALOG
CONTROLS ADD
ELECTRIC
HEAT ADD
HOT WATER ADD
1-ROW 2-ROW
2185 4 9 34 912
3200 4 9 30 912
4200 4 9 37 912
5225 4 9 32 12 17
6250 4 9 34 12 17
7260 4 9 44 12 17

6
Fan Powered Terminal Units IOM
KLPP (lbs.)
UNIT
SIZE
UNIT
WEIGHT
PNEUMATIC CONTROLS
ADD
DDC OR ANALOG
CONTROLS ADD
ELECTRIC
HEAT ADD
HOT WATER ADD
1-ROW 2-ROW
280 4 9 25 810
490 4 9 25 810
KLPS (lbs.)
UNIT
SIZE
UNIT
WEIGHT
PNEUMATIC CONTROLS
ADD
DDC OR ANALOG
CONTROLS ADD
ELECTRIC
HEAT ADD
HOT WATER ADD
1-ROW 2-ROW
180 N/A 925 810
280 N/A 930 810
375 4 9 30 10 12
4120 4 9 35 12 14
5100 4 9 35 12 14
KLPS-D (lbs.)
UNIT
SIZE
UNIT WEIGHT WITH COOLING COIL DDC CONTROLS
ADD
ELECTRIC
HEAT ADD
HOT WATER ADD
2-ROW 4-ROW 6-ROW 1-ROW 2-ROW
1100 107 115 925 810
2100 108 120 925 810
397 106 120 930 10 12
5130 145 160 935 12 14
TABLE 1 - Unit Weights

7
Fan Powered Terminal Units IOM
INITIAL INSPECTION
Once items have been removed from packing, check
carefully for damage to duct connections, coils, or controls.
File damage claims immediately with transportation agency
and notify Krueger.
NOTE: Remove all packaging material and foreign
material from unit and ensure the blower wheel moves
freely before installation. Every fan terminal unit is
shipped with cardboard ring in one side of the fan inlet
that MUST be removed. This ring is accessible from the
unit’s plenum.
UNIT IDENTIFICATION
Each unit has 2 main labels attached to the casing. The
FAN UNIT label (Figure 3) lists the model number, supply
voltage requirements, motor horsepower and overcurrent
protection requirements. The AIRFLOW label (Figure 4)
lists the model number, unit size, factory order number
and location. The location “tag” indicates where the unit is
intended for installation. There may be other labels attached
to the unit, as options or codes may require. Read all labels
on a typical unit before attempting installation. Control
boxes are assembled as indicated on the identication label.
Contact your local Krueger representative for more
information.
INSTALLATION PRECAUTION
Check that construction debris does not enter unit or
ductwork. Do not operate the central-station air-handling
fan without nal or construction lters in place. Accumulated
dust and construction debris distributed through the
ductwork can adversely aect unit operation.
SERVICE ACCESS
Provide service clearance for unit access (see Installation
section for details).
CODES
Install units in compliance with all applicable code
requirements.
UNIT SUSPENSION
See Installation section for unit suspension details.
WARRANTY
All Krueger-furnished items carry the standard Krueger
warranty.
FAN UNIT
FAN UNIT KQFP - 5 - 12 CODE - 10 - 579600 - C 014 REV:
MOTOR VOLT 277 PHASE 1HZ 60
HP 1/2 FLA(EA) 3.110
HEAT VOLT 480 PHASE 3 HZ 60
KW 12.0 AMPS 14.43
TAG: FPB - 313
MOTOR(S) ARE THERMALLY PROTECTED
MIN. SUPPLY CIRCUIT AMPS 21.920 REPLACEMENT LINE FUSE
MAX. FUSE OR HACR CIRCUIT BREAKERS 25.000 AMPS 25 AMP 600V
MAX. OUTLET AIR TEMPERATURE 200 F
UNIT DESIGNED TO OPERATE AT NO LESS THAN 0.2 IWG STATIC PRESSURE.
ZERO CLERANCE FROM UNIT. CONNECTED DUCT AND/OR PLENUM.
TO COMBUSTIBLE MATERIAL.
For operation & Maintenance manual see
WWW.KRUEGER - HVAC.COM
FIGURE 3 - Fan Unit Label
CONTROL OPTIONS
The units are oered with a wide variety of factory-mounted
controls that regulate the volume of air delivery from the
unit and respond to cooling and heating load requirements
of the conditioned space. All control packages can operate
stand-alone and will fulll the thermal requirements of a
given control space. These devices are available in both
pneumatic and electronic arrangements. A number of DDC
control packages by others are available for consignment
mounting as indicated. Each control approach oers a
variety of operating functions; a control package number
identies combinations of control functions. Because of the
variety of functions available, circuit diagrams, operating
sequences, and function descriptions are contained in
separate Application Data publications. These publications
are available from the Krueger website, www.krueger-hvac.
com, within the submittal icon.
DUCT HEATER
UP
AIR
FLOW
ORDER : 599049 ITEM: 010 REV: SN: C - 599049 - 10
MODEL: QFC DUCT SIZE: 12 X 10 MIN FPM: 0375
LINE VLT: 480 PH: 03 HZ: 60 KW: 2.50 AMP: 3.00
STEP : 01 CTL VOLT: 24 CTL VA: 50
MIN CIR AMP: 5.60 15 AMP 600V INTERNAL FUSE
MAX FUSE OR HACR CIRCUIT BREAKERS 15.00 AMP
MIN WIRE SIZE (COPPER CONDUCTORS ONLY): 12AWG
(SUITABLE FOR AT LEAST 75 DEGREES CENT.)
TAG: VAV- 05-01
For operation & Maintenance manual see
WWW.KRUEGER - HVAC.COM
FIGURE 4 - Air Flow Label

8
Fan Powered Terminal Units IOM
ANALOG ELECTRONIC CONTROLS
Pressure independent control packages are available with
or without hot water or electric heat, automatic or remote
night shutdown, and automatic night setback. All control
arrangements include a standard inlet airow sensor, control
enclosure, SCR fan speed controller, 24-volt transformer, fan
relay, and wall thermostat to match the control type. See
Tables 2A and 2B.
DIRECT DIGITAL CONTROLS (By Others)
Control sequences are available for factory installation
of numerous eld-supplied controls from various
manufacturers including: Andover, Automated Logic,
Invensys (Siebe), Siemens (Landis), Johnson, and others. All
packages include a standard inlet airow sensor, control
enclosure, SCR fan speed controller, 24-volt transformer,
and fan relay. Contact Krueger for information on mounting
eld-supplied controls.
PNEUMATIC CONTROLS
Pressure independent control packages are available with
or without hot water or electric heat, night shutdown and/
or unoccupied heating. All control arrangements include a
standard inlet airow sensor and SCR fan speed controller.
See Tables 3A and 3B.
Single function controller: Provides single function, i.e., DA-
NO.
Multi-function controller: Capable of providing DA-NO, DA-
NC, RA-NC or RA-NO functions.
NO CONTROL UNITS
Control sequences are also available to provide a control
box on units supplied with no factory-installed controls.
These arrangements include a standard inlet airow
sensor, control enclosure, SCR fan speed control, 24-volt
transformer, and fan relay. See Table 4.
PACKAGE NO. DESCRIPTION
2200 Cooling Only
2201 Cooling Only With Automatic Night Shutdown
2203 Cooling Only With Automatic Night Shutdown
2204 Cooling With On/O Hot Water Heat
2205 Cooling With On/O Hot Water Heat With Automatic Night Shutdown
2207 Cooling With On/O Hot Water Heat With Automatic Night Shutdown
2208 Cooling With Proportional Hot Water Heat
2209 Cooling With Proportional Hot Water Heat With Automatic Night Shutdown
2211 Cooling With Proportional Hot Water Heat With Automatic Night Shutdown
2212 Cooling With Up To 3 Stages Of Electric Heat
2213 Cooling With Up To 3 Stages Of Electric Heat W/ Automatic Night Shutdown
2215 Cooling With Up To 2 Stages Of Electric Heat W/ Automatic Night Shutdown
2217 Cooling/Heating with Automatic Changeover
2218 Cooling with Solid State LineaHeat Proportional Heat
PACKAGE NO. DESCRIPTION
2300 Cooling With Sequenced Fan
2301 Cooling With Sequenced Fan & Automatic Night Shutdown
2302 Cooling With Sequenced Fan & Automatic Night Setback
2303 Cooling With Sequenced Fan & On/O Hot Water Heat
2304 Cooling With Sequenced Fan & On/O Hot Water Heat & Automatic Night
Shutdown
2305 Cooling With Sequenced Fan & On/O HotWater Heat & Automatic Night
Setback
2306 Cooling With Sequenced Fan & Proportional Hot Water Heat
2307 Cooling With Sequenced Fan & Proportional Hot Water Heat & Automatic
Night Shutdown
2308 Cooling With Sequenced Fan & Proportional Hot Water Heat & Automatic
Night Setback
2309 Cooling With Sequenced Fan & Up To 2 Stages Of Electric Heat
2310 Cooling With Sequenced Fan & Up To 2 Stages Of Electric Heat & Automatic
Night Shutdown
2311 Cooling With Sequenced Fan & Up To 2 Stages Of Electric Heat & Automatic
Night Setback
2313 Cooling with Solid State LineaHeat Proportional Heat
2314 Cooling with Solid State LineaHeat Proportional Heat and Automatic Night
Shutdown On Loss Of Primary Air
TABLE 2A – Analog Electronic Control Arrangements –KLPS,
KQFS, QFC
TABLE 2B – Analog Electronic Control Arrangements – KLPP,
KQFP, QFV

9
Fan Powered Terminal Units IOM
PACKAGE NO. DESCRIPTION
1300 Single Function Controller; DA-NO With or Without Auxiliary Heat
1301 Single Function Controller; DA-NO With or Without Auxiliary Heat And With
Night Shutdown
1302 Single Function Controller; DA-NO With or Without Auxiliary Heat,With
Night Shutdown And Unoccupied Heating
1303 Single Function Controller; RA-NC With or Without Auxiliary Heat
1304 Single Function Controller; RA-NC With or Without Auxiliary Heat And With
Night Shutdown
1305 Single Function Controller; RA-NC With or Without Auxiliary Heat,With
Night Shutdown And Unoccupied Heating
1306 Multi-Function Controller; DA-NO With or Without Auxiliary Heat
1307 Multi-Function Controller; DA-NO With or Without Auxiliary Heat And With
Night Shutdown
1308 Multi-Function Controller; DA-NO With or Without Auxiliary Heat,With Night
Shutdown And Unoccupied Heating
1309 Multi-Function Controller; DA-NC With or Without Auxiliary Heat
1310 Multi-Function Controller; DA-NC With or Without Auxiliary Heat And With
Night Shutdown
1311 Multi-Function Controller; DA-NC With or Without Auxiliary Heat, With
Night Shutdown And Unoccupied Heating
1312 Multi-Function Controller; RA-NC With or Without Auxiliary Heat
1313 Multi-Function Controller; RA-NC With or Without Auxiliary Heat And With
Night Shutdown
1314 Multi-Function Controller; RA-NC With or Without Auxiliary Heat,With Night
Shutdown And Unoccupied Heating
1315 Multi-Function Controller; RA-NO With or Without Auxiliary Heat
1316 Multi-Function Controller; RA-NO With or Without Auxiliary Heat And With
Night Shutdown
1317 Multi-Function Controller; RA-NO With or Without Auxiliary Heat,With Night
Shutdown And Unoccupied Heating
PACKAGE NO. DESCRIPTION
1400 Single Function Controller; DA-NO With or Without Auxiliary Heat
1401 Single Function Controller; RA-NC With or Without Auxiliary Heat
1402 Multi-Function Controller; DA-NO With or Without Auxiliary Heat
1403 Multi-Function Controller; RA-NO With or Without Auxiliary Heat
1404 Multi-Function Controller; DA-NC With or Without Auxiliary Heat And With
Night Shutdown
1405 Multi-Function Controller; RA-NC With or Without Auxiliary Heat,With Night
Shutdown And Unoccupied Heating
PACKAGE NO. DESCRIPTION
D000 Field Supplied And Mounted Controls By Others On Units Without Electric
Heat
D001 Field Supplied And Mounted Controls By Others On Units With Electric Heat
TABLE 3A – Pneumatic Control Arrangements KLPS, KQFS & QFC
TABLE 3B – Pneumatic Control Arrangements KLPP, KQFP, QFV
TABLE 4 – No Control Unit Options
INSTALLATION
STEP 1 - INSTALL FAN - POWERED BOX
SELECT LOCATION
1. Units should be installed so that they do not come in
contact with obstacles such as rigid conduit, sprinkler
piping, Greeneld exible metal covering, or rigid
pneumatic tubing; such contact can transmit vibration
to the building structure, causing objectionable low
frequency noise.
2. Units should never be installed tight against concrete
slabs or columns, as vibration transmission is amplied
in this condition.
3. Fan powered terminals require sucient clearance for
servicing the blower/motor assembly from the bottom
of the unit, low voltage controls from the side and line
voltage motor controls or electric heat (if equipped) from
the rear (discharge end) of the unit.
Bottom access panel removal requires a minimum of 3”
minimum clearance, plus substantial horizontal clearance
to slide the access panel out of the way for service. Actual
horizontal dimensions will vary due to varying access
panels for dierent sized units. See the specic unit’s
submittal drawings for more detail.
NOTE: Be certain appropriate accommodations for
panel removal of most unit casings are large enough
to allow adequate internal service room once the
panels are removed.
A minimum clearance of 18”* is recommended for
control enclosure access. Unit control enclosure will vary
depending on which control package is used. Control
enclosure location is specied on unit submittals. Low
voltage enclosure covers are removable, not hinged.
A clearance of 36”* is recommended for line voltage motor
controls and electric heat control access. High- voltage
motor controls or electric heat control access is supplied
with hinged access doors for units with fused disconnect.
Specic location is indicated on the unit submittal.
NOTE: These recommendations do not supersede
NEC (National Electrical Code) or local codes that
may be applicable, which are the responsibility of the
installing contractor.
4. Whenever possible, fan-powered boxes should be
installed over halls or passageways (rather than over
occupied spaces) in order to limit the sound reaching
occupants.
POSITION UNIT
1. When moving boxes, use appropriate material handling
equipment and avoid contact with shaft extensions,
controls, wiring, piping, heaters, and control boxes.
2. Raise unit to position using safe mechanical equipment
and support until hanging means are attached and box
is level.

10
Fan Powered Terminal Units IOM
INSTALL UNIT
1. Install eld-supplied eyebolts, straphangers or bolt rod
supports as desired. Figure 5 illustrates possible unit
suspension methods. A typical installation is shown in
Figure 6.
2. Care should be taken to use hanging materials of
sucient stiness and strength, rigidly attached to the
unit. Straps should not be located on coil anges, electric
heat sections, or control boxes. When using trapeze
FIGURE 5 – Typical Unit Suspension Methods (KQFS Shown)
OPTIONAL
ACCESSORY
HANGER
FIELD-SUPPLIED
HANGING STRAPS
DO NOT suspend unit by trapeze
hangers that intefere with the unit
access panal.
FIELD-SUPPLIED
HANGER
BRACKET
supports, avoid areas where access is required to side
mounted controls, or side or bottom access doors.
For best installation with trapeze supports, provide
elastomeric material between unit and supports.
3. Hangers should be securely attached to bar joist or
mounting anchors properly secured to building structure
with lugs or poured-in-place hangers. Percussion nails
are not considered adequate anchors.

11
Fan Powered Terminal Units IOM
FIGURE 6 – Typical Perimeter Installation – Constant Volume Fan-Powered Box
DISTRIBUTION DUCT
LINED DISCHARGE DUCT
CONSTANT VOLUME FAN BOX W/
ELECTRIC HEAT
PRIMARY AIR
INLET
ROOM
SENSOR
CONTROL
ENCLOSURE
PTBS LINEAR BOOT DIFFUSER
3. Fan boxes should not be attached to octopus sections
immediately downstream of the unit.
4. Install optional return-air lters before operating the
unit.
5. Where construction lters were supplied with the box,
leave lters in place until installation is complete and
building is cleaned for occupancy.
STEP 3 - POWER WIRING (see Figure 7.)
1. All power wiring must comply with local codes and with
the NEC (National Electrical Code) ANSI/NFPA (American
National Standards Institute/National Fire Protection
Association) 70-1981. Disconnect switches are optional
equipment. Electrical, control and piping diagrams are
shown on the exterior labeling or on a diagram inside
the control and high-voltage enclosure covers, unless
otherwise specied in the order write-up. All units are
wired for a single point electrical connection to the
fan and electric heater (if equipped). Electric heaters
provided by Krueger are balanced by kW per stage. The
installing electrician should rotate incoming electric
service by phase to help balance overall building load.
2. All eld wiring must be provided with a safety disconnect
per NEC 424-19, 20, and 21.
3. Disconnect all incoming power before wiring or servicing
STEP 2 - MAKE DUCT CONNECTIONS
1. Install supply ductwork on each of the unit inlet collars.
It is recommended that 3 duct diameters of straight duct
are supplied to the inlet of the unit. An elbow put at the
inlet of the unit will create turbulence at the inlet making
it dicult for the ow sensor to accurately measure
the airow. Check that the pressure pick-up in primary
air collar is located properly and that air supply duct
connections are airtight. Install supply ductwork on unit
inlet collar, following all accepted medium-pressure duct
installation procedures. Seal joints against leakage.
NOTE: For maximum eciency in controlling radiated
noise in critical applications, inlet ducts should be
fabricated of 24-gauge minimum sheet metal in place
of ex connections. Flex duct is extremely transparent
to radiated sound; consequently high inlet static’s (Ps)
or sharp bends with excessive pressure drop can cause
a radiated noise problem in the space. If ex duct is
used, it should be limited to the connection between
the distribution duct and the boot diuser.
2. Install the discharge duct. On units with electric heat, the
recommended minimum distance of straight duct before
any transitions, elbows or branch connections is 48”. It is
strongly recommended that lined discharge duct be used
downstream of the unit. Insulate duct as required.

12
Fan Powered Terminal Units IOM
FIGURE 7 – Typical Power Connections for Fan Powered Units with 3-Stage Electric Heat
unit. All disconnect switches on the terminal (if equipped)
should be in the OFF position while making power
connections.
4. Units with electric heat should use copper wires rated at
least 125% of rating plate amperage. Refer to the unit’s
rating label and minimum supply circuit amps.
5. Observe wiring diagram and instructions attached to the
unit. 480-v, 3-phase units require a Wye power source
with a 4th (neutral) wire in addition to the full sized
ground wire. All units must be grounded as required by
NEC 424-14 and 250.
STEP 4 - SYSTEM SETUP AND CALIBRATION
GENERAL
The parallel fan powered terminals (KLPP, KQFP and QFV) are
designed to provide varying quantities of cold primary air
to a space in response to a thermostat demand for cooling.
For a heating demand, the fan will operate to supply ceiling
plenum air to the space. For units equipped with a heating
coil, the heater will operate as required to meet a heating
demand.
The series fan powered terminals (KLPS, KQFS and QFC) are
designed to provide a constant airow to the space. The air
supplied to the space is a mixture of primary air and ceiling
plenum air. The fan speed is adjusted to provide the required
airow to the space. In response to a cooling demand from
a thermostat, the damper will increase the amount of cold
primary air while reducing the amount of ceiling plenum air
to decrease the temperature of the air being delivered to the
space.
Most terminal control packages provide pressure
compensation to allow pressure independent operation of
the primary air damper, regardless of changes to the available
static pressure in the supply ductwork. To balance the unit it
is necessary to set both the minimum and maximum airow
set points of the controller. The many types of control
options available each have specic procedures required
for balancing. Refer to the submittal information for these
requirements.
SET POINTS
Maximum and minimum airow set points are normally
specied for the job and specic for each unit on the job.
Default set point values are provided by the factory and can
be reset to the specic requirements in the eld. The fan
speed must be eld adjusted after all discharge ductwork
and diusers have been installed.
FIELD ADJUSTMENT OF THE MAXIMUM AND MINIMUM
AIRFLOW SET POINTS
Each fan powered terminal unit is equipped with an airow
sensor installed in the primary air inlet that measures a
dierential pressure. The relationship between the airow
probe pressure and the corresponding airow is shown in
the airow sensor graph. See Figure 8. The corresponding
chart for specic probe is attached to each unit.
Power
Supply 120/277V
L1
N
G
Term Block or
Optional Disc Switch
Line Fuse
(Optional)
< Brown >
Brown
Brown
Brown
Green
Green
Brown
< White >
< White >
< White >
Thermal Hi-Limit
Auto-Reset (Typ)
White #18
Red
Fan Relay
Orange #18
Crimp
Cap
Red
SCR 2
5
1
4
3
6
CAP
MOTOR
MOTOR
CAP
Dual Motor Option
2 OR 3
2
OR 3
1
1
Whi te #12
< Brown >
< Brown > < Brown >
(Opt)
Motor
Fuse
(Opt)
Manual
Reset
Black #18
Black #18
Black #12
Black #12
Transformer
Yellow #18
Yellow #18
Yellow #12
Brown #18
Brown #12
Brown #12
White #18
Red #18
Red #18
Red #12
Orange #18
Blue #18
Blue #18
Black #18
Black #18
Black #18
Black #18
Black #18
Blk #18
Blk #12
Blk #12
Wht #12
Black #18
COM
N.O.
AFS
To
Controller
24 VAC
STEP 1
HEAT CONTACTOR
STEP 2
HEAT CONTACTOR
STEP 3
HEAT CONTACTOR
Wht #18
B 059606 BM 5/96
C119728 CS 11/97
DT01119 BR 5/01
ET01874 MF 7/02
Notes:
1. Use Thermostat with Isolating Contacts to
prvent Interconnection of class 2 outputs.
2. Use Copper conductors only suitable for 75
degrees C.
3. This Heater has integral limit control.
4. The Air ow must be in the direction indicated
on the unit. Air ow should not be less than
indicated on the label.
5. The Inlet temperature should not exceed 77
degrees fahrenheit.
6. This Unit has 1 Circuit.
7. Wire colors in < > to be sized by unit amps.
Caution:
Electrical shock may result.
Disconnect power prior to
servicing unit.
THIS DOCUMENT AND ITS CONTENT REMAIN THE EXCLUSIVE PROPERTY OF AIR SYSTEM COMPONENTS NO REPRODUCTION, USE OR DISCLOSURE OF THIS
DOCUMENT OR ITS CONTENTS IS AUTHORIZED WITHOUT THE WRITTEN CONSENT OF A DULY AUTHORIZED REPRESENTATIVE OF AIR SYSTEM COMPONENTS
NOTES: LEGEND
FACTORY WIRING
FACTORY PIPING
FIELD WIRING
FIELD PIPING
* PIGGY BACK CONNECTOR
DRAWN BY
FN
DATE
2/14/92
WIRING DIAGRAM
CKD
APPVD
UNLESS OTHERWISE
SPECIFIED
ALL DIMESIONS IN INCHES
[ ] = MILLIMETERS
TOLERANCES
FRACTIONAL = 1/32 [.794]
DECIMAL = 010 [.254]
ANGULAR = 10
REMOVE BURRS AND
SHARP EDGES
TITLE
120/277V 1 1Ø
3 STAGE, 3 ELEMENT
DO NOT SCALE THIS DRAWING SCALE
N/A
SIZE
C
DRAWING NO
00-713776
REV
E
SHEET
4/99
-04

13
Fan Powered Terminal Units IOM
INLET SNSOR ΔP INCHES
W.G. (PASCALS)
VOLTS (DC), ANALOG CONTROLS
CFM ()L/s
1.0 (248.8) 11
.8 (199.0) 9.7
.6 (149.3) 8.2
.4 (99.5) 6.8
.3 (74.6) 5.8
.2 (49.8) 4.6
.1 (24.9) 3.4
.07 (17.4) 2.6
.05 (12.4) 2.0
.04 (10.0)
.03 (7.5) 1.4
1.5
40
(19)
50
(24)
70
(33)
100
(47)
200
(94)
300
(142)
(108)
229
(169)
358
(243)
515
(331)
702
(432)
916
(547)
1160
(676)
1432
(973)
2062
(1324)
2806
(1730)
3665
(3303)
7000
500
(236)
700
(330)
1000
(472)
2000
(944)
3000
(1437)
5000
(2360)
7000
(3303)
45678910 12 14 16 22
FIGURE 8 – Inlet Airflow Sensor CFM vs. Signal Chart

14
Fan Powered Terminal Units IOM
GENERAL
Before balancing the system, the air handlers must be
operating in accordance with the specications for air
capacity, static pressure, and temperature. Record data on a
unit performance sheet (Figure 9). The following items must
be checked:
1. All fans must be running at calculated and specied rpm.
2. Permanent or temporary lters must be clean and in-
stalled where required.
3. All central station dampers must be adjusted and
operating properly.
4. All thermostats must be calibrated and at the desired
settings.
5. All ductwork must be tight.
6. All dirt or loose lining must be removed from inside
ductwork.
7. Pumps and sprays, when used, must be in operation.
INLET DIAMETER INLET AREA CFM @ 1 IN. WG
4” 0.087 ft2230
5” 0.136 ft2360
6” 0.196 ft2515
8” 0.349 ft2920
10” 0.545 ft21430
12” 0.785 ft22060
14” 1.069 ft22800
16” 1.396 ft23660
TABLE 7 – Inlet Areas
START-UP
SYSTEM CALIBRATION OF THE INLET AIRFLOW SENSOR
To achieve ecient pressure independent operation, the
velocity sensor and averaging ow probe must be calibrated
to the controller. This will ensure that airow will be accurate
for all terminals at system start-up.
System calibration is accomplished by calculating a ow
coecient that adjusts the pressure fpm characteristics.
The ow coecient is determined by dividing the ow for a
given unit (design air volume in cfm), at a dierent velocity
pressure of 1.0 in. wg, by the standard pitot tube coecient
of 4005. This ratio is the same for all sizes, if the standard
averaging probe is used.
Determine the design air velocity by dividing the design air
volume (the ow at 1.0-in. wg) by the nominal inlet area (sq.
ft). This factor is the K factor.
Krueger inlet areas are shown in the table. The design air
volume is shown in this table. It can be determined from
Table 7 that the average design air velocity for units is equal
to 2660 fpm at 1.0-in. wg.
8. Connections to the coil, when used, must be checked.
9. Water control valve, if used, must be checked.
NOTE: All KQF* & QF* Series terminal units are shipped
with cardboard packaging rings placed in one side of
the blower housing internal to the blower/motor. These
rings are provided to prevent damage to the motor
during shipment. The rings MUST BE REMOVED prior to
operation. The packing rings are accessible through the
terminal’s plenum. Turn the fan wheel by hand to insure
that blower is free spinning. Krueger will not accept
responsibility for any additional costs for removal of
this packaging material.
IMPORTANT: Before proceeding with start-up, be
certain that voltage, frequency, and phase correspond
to unit specications. Unless noted, all fan motors are
60 Hz, 115, 208/240, or 277 v, single-phase ac. electric
heat, the electric heat voltage may exceed the blower
motor voltage requirement. Excessive voltage to the
fan box may seriously damage it. Verify that the DDC (if
equipped) are receiving 24-v ac, –15%, +20%
INITIAL START-UP PROCEDURES
NOTE: The following steps MUST be followed in order to
properly operate and service this unit.
1. Disconnect all electrical power to the unit. Failure to
disconnect the power to the fan box prior to checking
and/or servicing the fan box could result in a serious
injury.
2. Verify that the fan box is installed level, and that adequate
mounting support has been provided.
3. Remove motor access panel from the bottom of the fan
box, and also remove the control panel cover.
4. Test the fan motor setscrew. The setscrew should t
tightly, but it may have come loose during shipment or
installation.
5. Rotate the blower by hand to ensure proper clearance
between the blower and the blower housing.
6. Check the fan box for loose berglass insulation,
especially on the electric heater elements or the hot
water coils (if these accessories are installed).
7. Check the control enclosure and remove any debris.
8. Check the induced air inlet lter (if provided) for
obstructions, and verify the lter is securely in place.
9. Verify the main power supply to the connection to the
fan box for proper voltage. If the fan box is installed with
electric heat, the electric heat voltage may exceed the
blower motor voltage requirement. Excessive voltage to
the fan box may seriously damage it. Verify that the DDC
(if equipped) are receiving 24v-ac, –15%, +20%.Identify
the control system supplied.
10. Check all control connections (and/or electric) for proper
installation.
11. Connect electrical power.

15
Fan Powered Terminal Units IOM
BALANCING KRUEGER FAN TERMINALS
Krueger fan terminal units contain primary air dampers,
which, under the control of a volume controller, regulate the
amount of cold air distributed to the space.
BALANCING SERIES FLOW UNITS
KLPS, KQFS & QFC series ow terminals direct all primary
air through the unit fan. The terminal is designed to operate
with the fan supplying airow equal to or greater than the
airow supplied by the VAV damper. To balance the unit,
therefore, it is necessary to rst set the fan ow, and then
the VAV damper (primary) ow.
Each control option has specic procedures required for
balancing the unit, but some steps are common to all KLPS,
KQFS & QFC units. The fan box adjustments described
below must be made in conjunction with the adjustments
described in the Speed Controller section, and Control
Adjustments section. The VAV damper airow may be set
at the factory, but the fan airow must be set in the eld as
described below.
SETTING FAN AIRFLOW
NOTE: If the unit has electric heat or hot water heat,
temporarily disable these functions before balancing
the fan. If unit has optional electric heat disconnect
downstream of fan motor connections to power, open
disconnect. If unit does not have optional electric
heat disconnect, remove one electric heat power line
connection. Be sure to insulate loose line from ground
wire or other wires.
1. Set the controller to provide heating airow demand only.
Typically, this is accomplished by setting the thermostat
to the highest possible temperature setting. NOTE: A
minimum of 0.1” w.g. downstream static pressure is
required in the duct to ensure proper heater operation.
2. Determine that the VAV valve is fully closed and that the
fan is rotating in the proper direction. (If the VAV damper
is open when the fan is started and there is primary air in
the system, the fan may start and run backward.)
3. Using a ow hood or duct traverse, determine the
delivered fan airow (cfm). NOTE: Both ow hood and
duct traverse are subject to measurement errors. Be sure
that all applicable measurement precautions are taken.
4. Compare the actual cfm in heating mode to the designed
airow. If there is a minimum setting for the VAV damper
in heating mode (as recommended by ASHRAE [American
Society of Heating, Refrigeration, and Air Conditioning
Engineers] Standard 62), this quantity is included in
the total measured heating airow to determine if the
desired induction airow level has been met.
5. Adjust the fan SCR at unit control box to achieve the
desired airow rate. Refer to the performance data
tables (Tables 8 and 9) to ensure airow through electric
heaters meets the requirements before operating the
heater. Setting of VAV (Primary) Airow
ADJUSTMENT OF SET POINTS
Each KLPS, KQFS and QFC unit, supplied with controls, is
equipped with a pneumatic or electronic volume controller
which regulates the quantity of cold primary air entering the
terminal and the conditioned space. If required airow levels
are specied with the job order, the minimum and maximum
cfm levels will be set at the factory where applicable. If
minimum and maximum levels are not specied, a default
value of 0 is used for minimum setting at the factory. Other
settings of minimum and maximum primary airow must
be set in the eld. Airow (cfm) ranges for the primary
air damper are shown in Tables 8 and 9. The minimum
primary airow (other than zero) is the minimum ow rate
controllable by the unit volume controller. The primary air
damper can be set at zero for shuto or at the minimum
cfm listed.
FIELD ADJUSTMENT OF MINIMUM AND MAXIMUM AIRFLOW
SET POINTS
Each KLPS, KQFS and QFC unit is equipped with a centerpoint
averaging airow sensor, which provides an amplied
dierential pressure that is proportional to the unit airow.
Output from this sensor is used to provide a ow signal to
both pneumatic and electronic controls. Unit airow (cfm)
can be read directly from the airow sensor labels on the
unit (refer to Figure 8, Flow Chart).
1. With the unit airow from the fan set, turn on primary
(VAV) air supply.
2. To set cfm in the eld, connect a gage to the ow probe at
the provided ‘T’ taps, and check the dierential pressure.
(Alternately, the total ow may be measured, and the
previously determined fan induction ow rate may be
subtracted from the total ow to determine VAV ow.
However, for low primary settings, this may not be as
accurate as the ow tap method.)
3. If a minimum VAV ow is required in heating mode, adjust
the volume until the dierential pressure corresponds to
the cfm required.
4. Set the controller to provide maximum cooling demand.
This is typically accomplished by rst setting the
thermostat to the lowest possible temperature setting.
a. In most series fan boxes, the primary airow rate is
set so the maximum primary CFM is equal to the fan
CFM; in these cases, adjust the volume controller until
a balance is achieved between fan-induced airow
and primary airow. When a balance exists, a strip of
paper hung at the induction port should hang straight
down, and neither be blown in or out of the unit.
b. Primary CFM airow is less than the fan induction ow
cfm, adjust the volume controller until the dierential
pressure (measured through the ow probe as
described above) corresponds to the cfm required.
Verify that induction exists through the inlet ports,
using the paper strips as described above. When
induction exists, the paper strip should be pulled into
the unit.
5. Return all reheat options to normal connections.

16
Fan Powered Terminal Units IOM
6. Cap the ‘T’ taps.
7. Reset the thermostat to a normal setting.
NOTE: It is normal for the total airow to the room to
increase slightly in full cooling mode.
TABLE 8 – KQFS Series Fan Terminal Unit
UNIT SIZE INLET SIZE
PRIMARY AIR FLOW PCS MOTOR EC MOTOR
MAX MIN MOTOR HP MAX FAN MIN FAN MOTOR HP MAX FAN MIN FAN
2
6515 90
1/10 530 50 N/A
8530 160
3
6515 90
1/4 1110 200 1/2 1050 250
8920 160
10 1110 250
12 1110 360
4
8920 160
1/4 1400 500 N/A10 1400 250
12 1400 360
5
10 1425 250
1/2 1850 800 N/A12 1850 360
14 1850 480
6
10 1425 250
3/4 2600 1200 12000 500
12 2060 360
14 2600 480
16 2600 630
7
10 1425 250
13000 1250 12500 600
12 2060 360
14 2800 480
16 3000 630
TABLE 8 – KQFS Series Fan Terminal Unit

17
Fan Powered Terminal Units IOM
TABLE 9 – QFC Series Fan Terminal Unit
UNIT SIZE INLET SIZE
PRIMARY AIR FLOW PCS MOTOR ECM MOTOR
MAX MIN MOTOR HP MAX FAN MIN FAN MOTOR HP MAX FAN MIN FAN
2 6 515 90 1/10 560 100 N/A
3
6515 90
1/4 990 300 1/2 1100 275
8920 160
4
8920 160
1/4 1440 550 N/A10 1430 250
12 1440 360
5
10 1430 250
1/2 2140 1100 N/A
12 2060 360
6
12 2060 360
3/4 2530 1200 12550 650
14 2530 480
716 3660 630 (2)3/4 3900 2100 (2)1 4550 1125
TABLE 10 – KLPS Series Fan Terminal Unit
UNIT SIZE INLET SIZE
PRIMARY AIR FLOW PCS MOTOR ECM MOTOR
MAX MIN MOTOR HP MAX FAN MIN FAN MOTOR HP MAX FAN MIN FAN
1
4230 40
N/A 1/3 850 1255350 62
6515 90
2
6515 90
N/A 1/3 925 140
8860 160
3
8920 160
1/4 1075 460 1/3 1125 170
10 1075 250
4
10 1425 250
(2)1/6 1650 805 (2)1/3 1900 285
8X14 1650 360
5
8920 160
1/2 1970 840 1/3 1790 265
10 1425 250
12 1970 360
14 1970 480
TABLE 9 – QFC Series Fan Terminal Unit
TABLE 10 – KLPS Series Fan Terminal Unit

18
Fan Powered Terminal Units IOM
TABLE 10A – KLPS-D Series Fan Terminal Unit
UNIT SIZE INLET SIZE
PRIMARY AIR FLOW ECM MOTOR
MAX MIN MOTOR HP MAX FAN MIN FAN
1
4230 40
1/3 775 1055350 62
6515 90
2
4230 40
1/3 875 1355350 62
6515 90
3
6515 90
1/3 1000 150
8920 160
5
6515 90
1/2 11625 2508920 160
10 1430 250
Note: Minimum Primary airow may be 0 cfm.
BALANCING PARALLEL FLOW UNITS
The KLPP, KQFP, and QFV parallel fan terminals are designed
to operate with the fan supplying air equal to 40 to 60% of
the VAV damper maximum primary air setting. Adjustments
to the parallel units fan should be made with the primary
air closed o. Refer to unit capacity tables to ensure
airow through the electric heater meets the minimum
requirements before operating heater.
Each control option has specic procedures required for
balancing the unit, but some steps are common to all parallel
fan units, as described below.
To balance parallel fan unit:
SETTING FAN AIRFLOW
NOTE: If the unit has electric heat or hot water heat,
temporarily disable these functions before balancing
the fan.
If unit has optional electric heat disconnect downstream of
fan motor connections to power, open disconnect. If unit
does not have optional electric heat disconnect, re-move
one electric heat power line connection. Be sure to insulate
loose line from ground wire or other wires.
1. Set the controller to provide heating airow demand only.
Typically, this is accomplished by setting the thermostat
to the highest possible temperature setting.
NOTE: A minimum of 0.1” w.g. downstream static
pressure is required in the duct to ensure proper
heater operation.
2. Determine that the VAV damper is fully closed. This may
require a temporary override of the VAV controller. Do
not adjust minimum and maximum cfm set points at this
time.
3. Using a ow hood or duct traverse, determine the
delivered fan airow (cfm).
NOTE: Both ow hood and duct traverse are subject
to measurement errors. Be sure that all applicable
measurement precautions are taken.
4. Compare the required design cfm in heating mode to the
actual delivered airow. If there is a minimum setting for
the VAV damper in heating mode (as recommended by
ASHRAE [American Society of Heating, Refrigeration, and
Air Conditioning Engineers] Standard 62), this quantity is
included in the total measured airow.
5. Adjust the fan SCR at unit control box to achieve the
desired airow rate.
SETTING OF VAV (PRIMARY) AIRFLOW
ADJUSTMENT OF SET POINTS
Each parallel fan unit is equipped with a pneumatic or
electronic volume controller that regulates the quantity of
cold primary air entering the terminal and the conditioned
space. If required airow levels are specied with the job
order, the minimum and maximum cfm levels will be set
at the factory. If minimum and maximum levels are not
specied, a default value is used. Other settings of minimum
and maximum primary airow must be set in the eld.
Airow (cfm) ranges for the primary air damper are shown
in Tables 11, 12 and 13 for KQFP, QFV and KLPP units. The
minimum primary airow (other than zero) is the minimum
ow rate controllable by the unit volume controller. The
primary air damper can be set at zero for shuto or at the
minimum cfm listed.
TABLE 10A – KLPS-D Series Fan Terminal Unit

19
Fan Powered Terminal Units IOM
FIELD ADJUSTMENT OF MINIMUM AND MAXIMUM AIRFLOW
SET POINTS
Each parallel fan unit is equipped with a four quadrant
multi-point center averaging airow sensor that provides
an amplied dierential pressure that is proportional to
the unit airow. Output from this probe is used to provide a
ow signal to both pneumatic and electronic controls. Unit
airow (cfm) can be read directly from the ow probe on the
unit.
1. After the unit airow from the fan has been set, turn on
primary (VAV) air supply and turn o the fan.
2. To set cfm in the eld, connect a gage to the ow probe
and check the dierential pressure.
3. If a minimum VAV ow is required in heating mode, adjust
the volume controller until the dierential pressure
corresponds to the cfm required.
4. Some control sequences allow the fan to start before the
VAV damper reaches minimum setting, for an overlapping
of fan and VAV ow. For these sequences, after controller
min airow has been adjusted, the total airow with
both fan and primary airow should be checked. For
sequences that call for the fan to start as the rst stage
of heat, the cooling minimum cfm can be veried at the
diuser. Setting the minimum control point will typically
require careful adjustment of the thermostat to create a
minimum cooling demand signal.
a. Set the controller to provide maximum cooling
demand. This is typically accomplished by setting
the thermostat to the lowest possible temperature
setting. For most control sequences, this will cause
the fan to shut o.
b. Adjust the volume controller until the dierential
pressure (measured through the ow probe as
described above) corresponds to the cfm required.
6. Return all reheat options to normal connections.
7. Cap the ends of the inlet ow sensors.
8. Reset the thermostat to a normal setting.
5.
TABLE 11 - KQFP Parallel Fan Terminal Unit
UNIT SIZE INLET SIZE
PRIMARY AIR FLOW PCS MOTOR ECM MOTOR
MAX MIN MOTOR HP MAX FAN MIN FAN MOTOR HP MAX FAN MIN FAN
2
6515 90
1/4 500 150 N/A
8920 16
3
6515 90
1/4 800 160 N/A8920 160
10 1430 250
4
6515 90
1/4 900 190 1/2 1000 250
8920 160
10 1430 250
12 2060 360
5
10 1430 250
1/2 1700 480 N/A12 2060 360
14 2800 480
6
10 1430 250
1/2 1700 500 N/A
12 2060 360
14 2800 480
16 3660 630
7
10 1430 250
3/4 2000 780 11600 400
12 2060 360
14 2800 480
16 3660 630
TABLE 11 - KQFP Parallel Fan Terminal Unit

20
Fan Powered Terminal Units IOM
HI
LO
RJ
MXF-544002-001
FLA
III V
1005-33-01
TABLE 13 – KLPP Parallel Fan Terminal Unit
UNIT SIZE INLET SIZE
PRIMARY AIR FLOW PCS MOTOR ECM MOTOR
MAX MIN MOTOR HP MAX FAN MIN FAN MOTOR HP MAX FAN MIN FAN
2
6515 90
1/6 665 350 1/3 820 1658920 160
10 1430 250
4
8920 160
1/4 855 420 1/3 885 17510 1430 250
8X14 2060 360
TABLE 12 – QFV Parallel Fan Terminal Unit
UNIT SIZE INLET SIZE
PRIMARY AIR FLOW ECM MOTOR
MAX MIN MOTOR HP MAX FAN MIN FAN
2
6515 90
1/10 400 200
8920 160
3
8920 160
1/10 600 300
10 1430 250
4
10 1430 250
1/4 1050 480
12 2060 360
5
12 2060 360
1/2 1500 860
14 2800 480
6
14 2800 480
1/2 1800 930
16 3660 630
716 3660 630 3/4 2200 1140
SPEED CONTROLLER
Each Krueger fan powered air terminal unit is equipped with
a fan SCR speed controller, located on the bottom of the
control box. The SCR can be adjusted in the eld. (The QFC,
size 7 unit has 2 SCR speed controllers, one for each fan. One
SCR is located in the standard position at the bottom of the
control box; the other is at the top of the control box.)
CAUTION: The minimum stop on the speed controller
is factory set at an internal minimum stop to prevent
damage to the motor. Do not attempt to override this
minimum stop or electrical damage to the fan motor
may result.
The fan airow output is dependent on the setting of the
controller and the downstream static resistance.
TO INCREASE THE FAN SPEED (RPM)
Turn the slotted adjustment on the controller clockwise
toward the “HI” marking printed on the controller faceplate.
(Refer to Figure 9.)
TO DECREASE THE FAN SPEED (RPM)
Turn the slotted adjustment on the controller clockwise
toward the “LO” marking. (Refer to Figure 9.)
FIGURE 9 – Fan Speed Controller
TABLE 12 – QFV Parallel Fan Terminal Unit
TABLE 13 – KLPP Parallel Fan Terminal Unit
This manual suits for next models
7
Table of contents
Other KRUEGER Fan manuals
Popular Fan manuals by other brands

Euramco Safety
Euramco Safety UB20 Series owner's manual

Hunter
Hunter Astwood installation manual
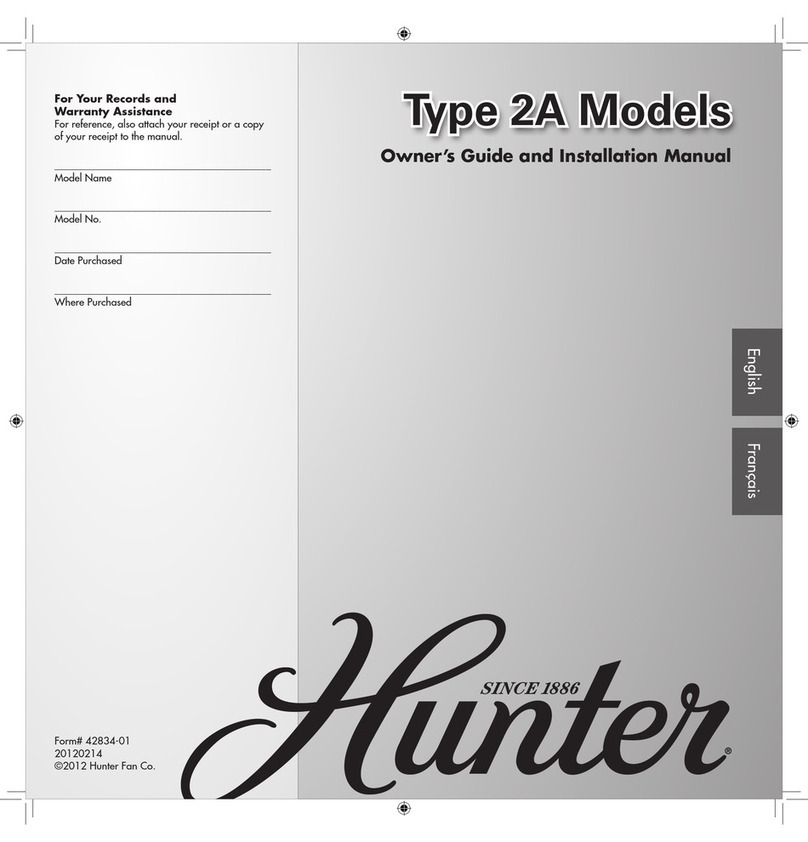
Hunter
Hunter Type 2A Models Owner's guide and installation manual
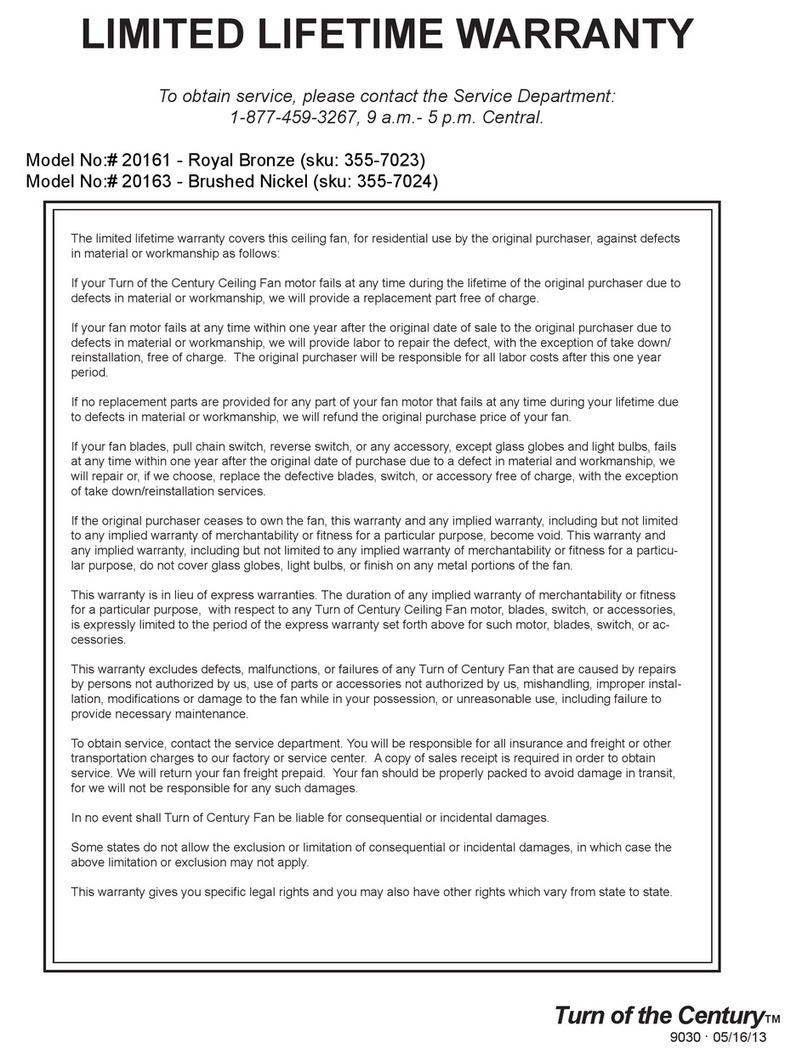
Turn of the century
Turn of the century 20161 installation guide

Ebmpapst
Ebmpapst M3G150-NA02-52 operating instructions
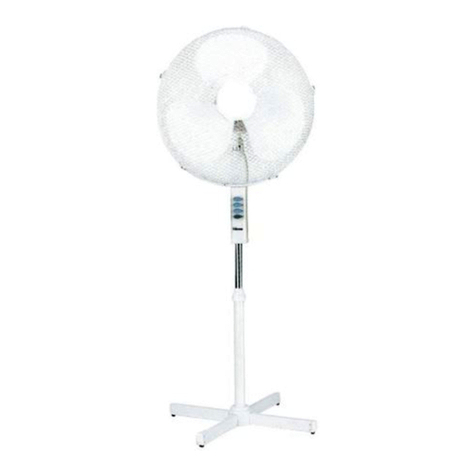
TriStar
TriStar VE-5939 instruction manual
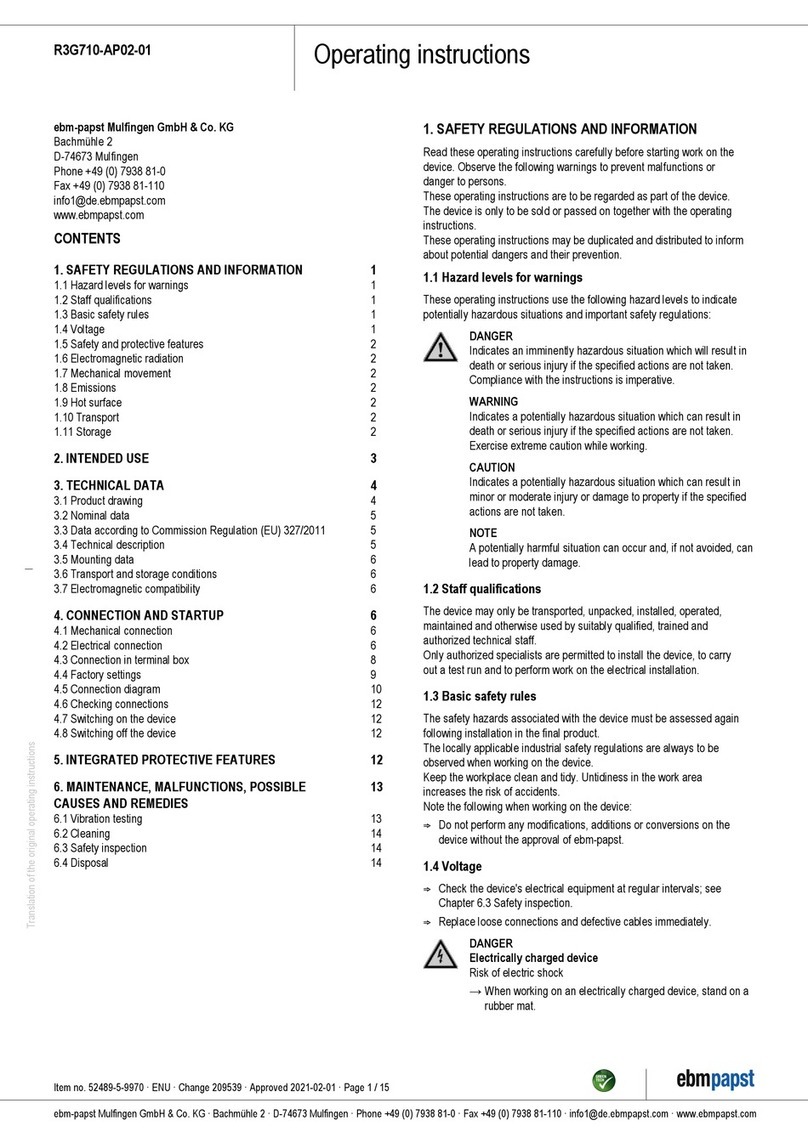
Ebmpapst
Ebmpapst R3G710-AP02-01 operating instructions
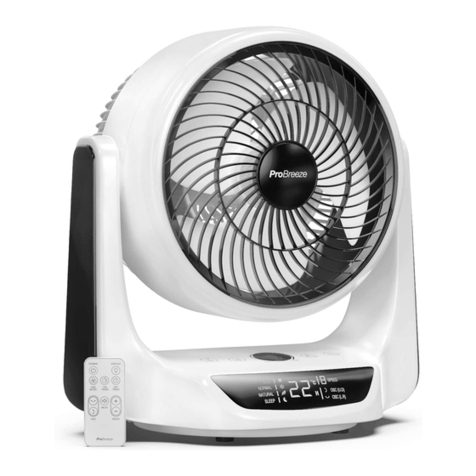
Pro Breeze
Pro Breeze PB-F09 instruction manual
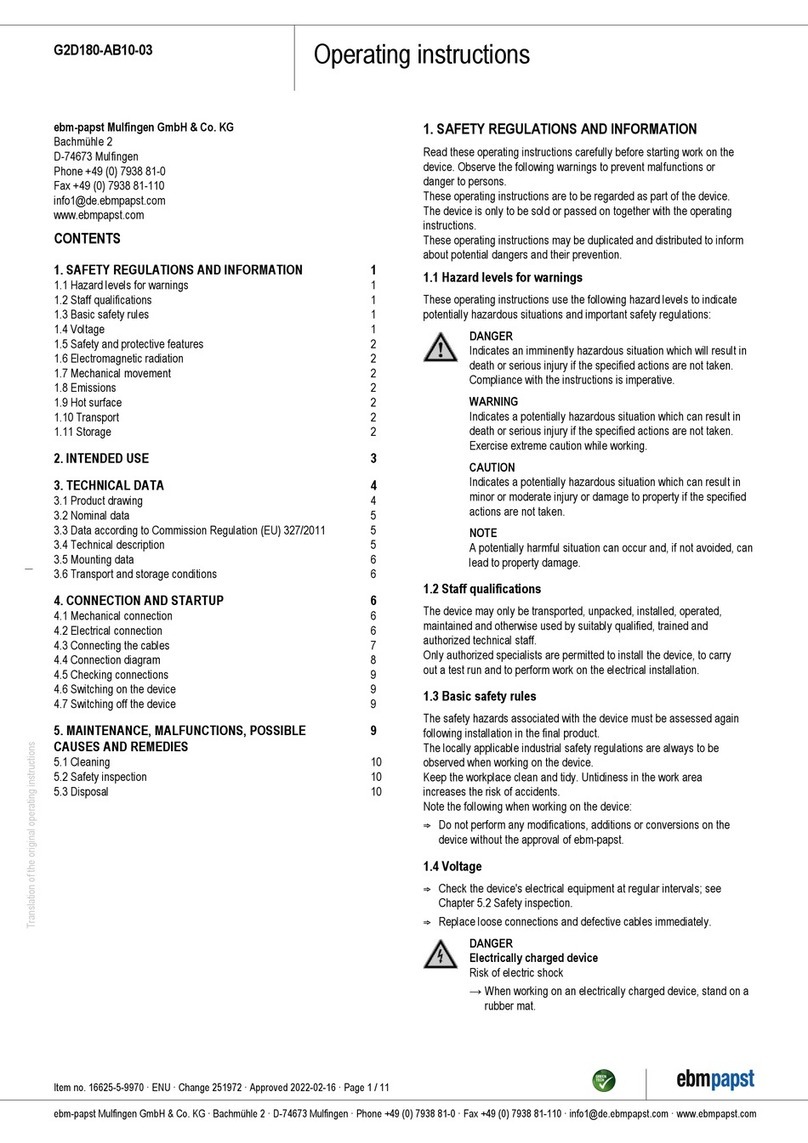
Ebmpapst
Ebmpapst G2D180-AB10-03 operating instructions
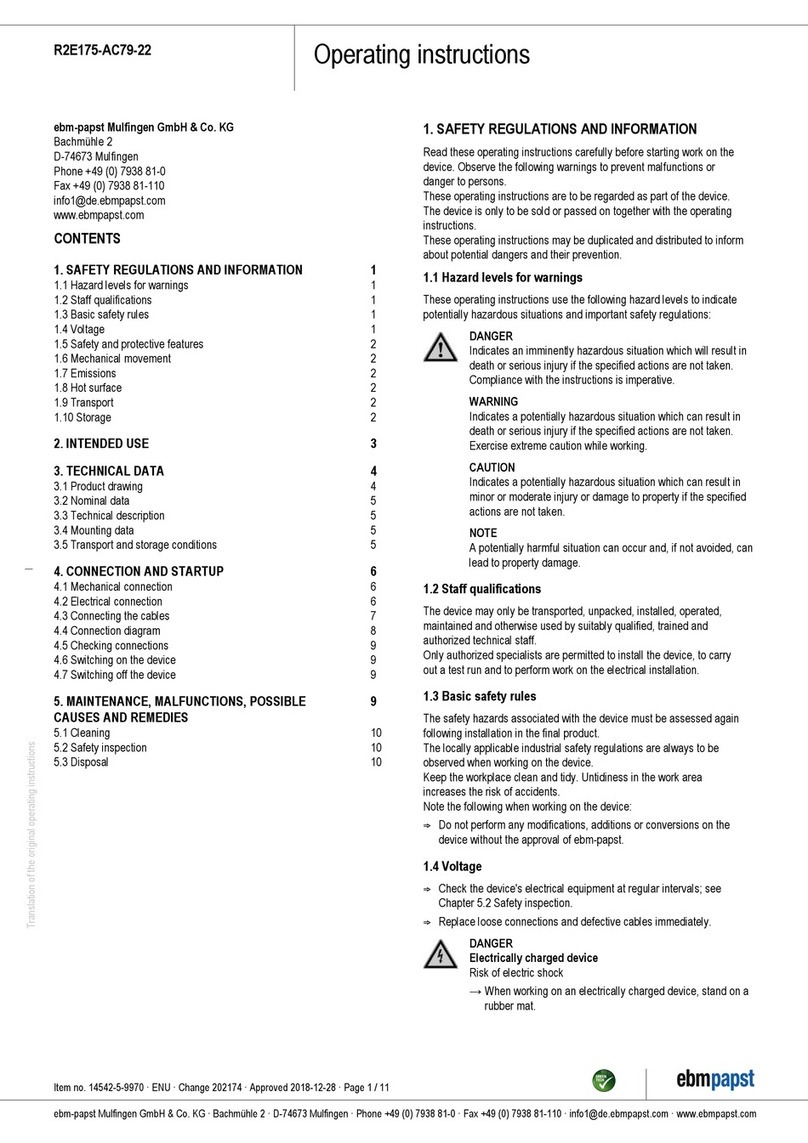
Ebmpapst
Ebmpapst R2E175-AC79-22 operating instructions

HAMPTON BAY
HAMPTON BAY FANELEE Use and care guide

Ebmpapst
Ebmpapst D3G283-AB37-01 operating instructions