LAFERT AMBY Series User manual

SAFETY, INSTALLATION AND MAINTENANCE INSTRUCTIONS FOR BRAKE MOTORS AMBY – 3007/12 en Ed. 02.2012
SAFETY, INSTALLATION AND MAINTENANCE INSTRUCTIONS FOR BRAKE MOTORS - AMBY SERIES
HIGH-TORQUE D.C. BRAKE
GENERAL SAFETY INSTRUCTIONS
Danger: electric rotating machine have dangerous rotating and conductive parts, as well as possibly hot surfaces.
The commissioning of electric motor is forbidden until the machine on which it has been incorporated has been declared conform to
2006/42/EC directive (Machine Directive).
All transportation, storage, installation, commissioning, inspection, maintenance and repair works have to be carried out exclusively
by qualified personnel (definition according to IEC 364) according to EN 60204-1.
Improper use may cause major damage to persons and objects.
Motors meet the requirements of Low Voltage Directive 2006/95/EC and are therefore CE marked on name plate.
Operating conditions have to be according to EN 60034-1.
BRAKE MOTORS INSTALLATION
The responsibility of the correct brake functionality is completely of the installer, who has to:
comply with the connection scheme placed inside the terminal box
supply the rectifier / brake according to the data on the nameplate / connection scheme
check the correct brake functionality
check that the brake torque satisfies the application needs
supply in a correct way auxiliary equipments, if any (see specific documentation)
Earthing has always to be carried out (according to local regulations) before the connection to the mains.
The supply of motor, rectifier/brake, auxiliary equipments (if any) has to be made using cables of suitable section in order to avoid
overheating and/or too high voltage drop.
Pay attention not to alter the protection degree (use only original gaskets).
In case of brake motor inverter supply follow correctly the wiring instructions of the inverter manufacturer and separately supply
(directly from the main) the rectifier/brake.
For any special design see specific documentation.
The good brake running in time depends on a correct periodical maintenance.
MAIN COMPONENTS LIST
A) V-ring (for IP55 only for size 80 … 112, 160)
B) Braking flange1)
C) Dragging hub
D) Anti-vibration spring/O-ring
E) Key
F) Hand release (on request)
G) V-ring (for IP55 only)
H) Fan
I.1) Braking spring
I.2) Magnet casing (with brake coil inside)
I.3) Fastening screw2) I.4) Contrast spring
I.5) Guiding pipe I.6) Mobile anchor
I.7) Fastening nut
J) Protection gasket (for IP55 only)
K) Brake disk
L) Fan cover (with slot in case of hand release)
M)Flywheel (on request)
SPARE PARTS LIST
B) Braking flange1)
C+D) Dragging hub with anti-vibration spring/O-ring
F) Hand release
H) Fan
I) Preassembled part
J) Protection gasket
K) Brake disk
L) Fan cover (with slot in case of hand release)
M)Flywheel
1) for sizes 63 and 71 only
2) fastening stud bolt for sizes 63 and 71 only
I.2
I.1
M
ABCD EF
H
G
LK I.5
t
S min
I.7
J I.6 I.4 I.3

SAFETY, INSTALLATION AND MAINTENANCE INSTRUCTIONS FOR BRAKE MOTORS AMBY – 3007/12 en Ed. 02.2012
PERIODICAL MAINTENANCE OF BRAKE MOTORS
Every maintenance work on brake motors should only be carried out by qualified personnel, always with the machine out of
operation, disconnected and previously secured against starting.
Brake motors with high-torque D.C. brake (with electromagnetic brake braking in case of failure supply) have got braking torque already preset
at rated plate value, according to catalogue (braking torque adjustment upon braking springs number up to 250Nm3)) that means that the
periodical maintenance consists on checking that the air-gap “t”, the minimum friction surface thickness “Smin” and hand release backlash “x” (if
any) are according the following table:
Brake
size4) Motor
size t5)
[mm] Smin6)
[mm] x
12MV 63, 71 0,25 …0,5 1 0,6
53MV, 13MV 71, 80 0,25 …0,5 1 0,8
04MV, 14MV 80, 90 0,3 …0,55 1 1
05MV, 15MV 90, 100, 112 0,3 …0,55 1 1
56SMV, 16SMV 100, 112,132 0,35 …0,6 1 1,2
07MV, 17MV 132,160 0,4 …0,8 1 1,2
08MV 1607) 0,5 …0,9 1 1,2
3) For higher braking torque consult us
4) Always present on the preassembled part label
5) Refer to minimum value
6) Minimum thickness of friction surface on each side of the brake disk (for lower values it is necessary to
replace the brake disk)
7) For bigger sizes consult us
Too high air-gap values could produce a noisy operation and even cause the brake not to be released; excessive air-gap values can reduce the
braking torque to zero due to the clearance taking up of the release lever tie rods.
AIR-GAP ADJUSTMENT
To adjust the air gap value release the fixing nuts I.7 and screw the fastening screws I.3 to reach the minimum value of air gap t according to
above table (measure the air gap in 3 positions at 120° next to the guiding pipe); tighten the fixing nuts I.7 keeping in position the fastening
screws I.3.
Occasionally we recommend to use an air jet to eliminate dust or other particles that may have settled on the braking surface.
After several air-gap adjustments verify that the thickness of the friction surface on each side of the brake disk is no lower the minimum value
stated in the above table; if needed replace the brake disk.
Any repair work within the guarantee period is subject to the motor manufacturer approval.
For any brake motors repair use only original spare parts.
Popular Engine manuals by other brands

Perkins
Perkins 1204F-E44TA Systems operation testing and adjusting

Motorline professional
Motorline professional TUB10R User& installer's manual
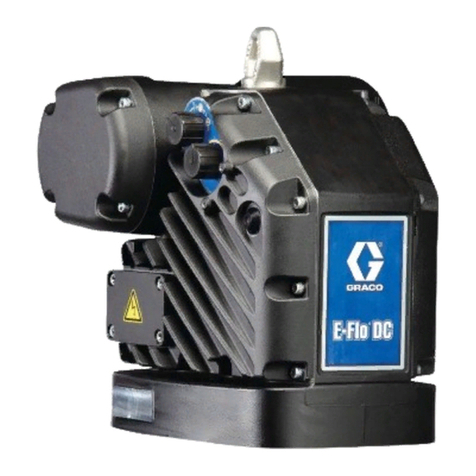
Graco
Graco E-Flo EM0011 Instructions & installation
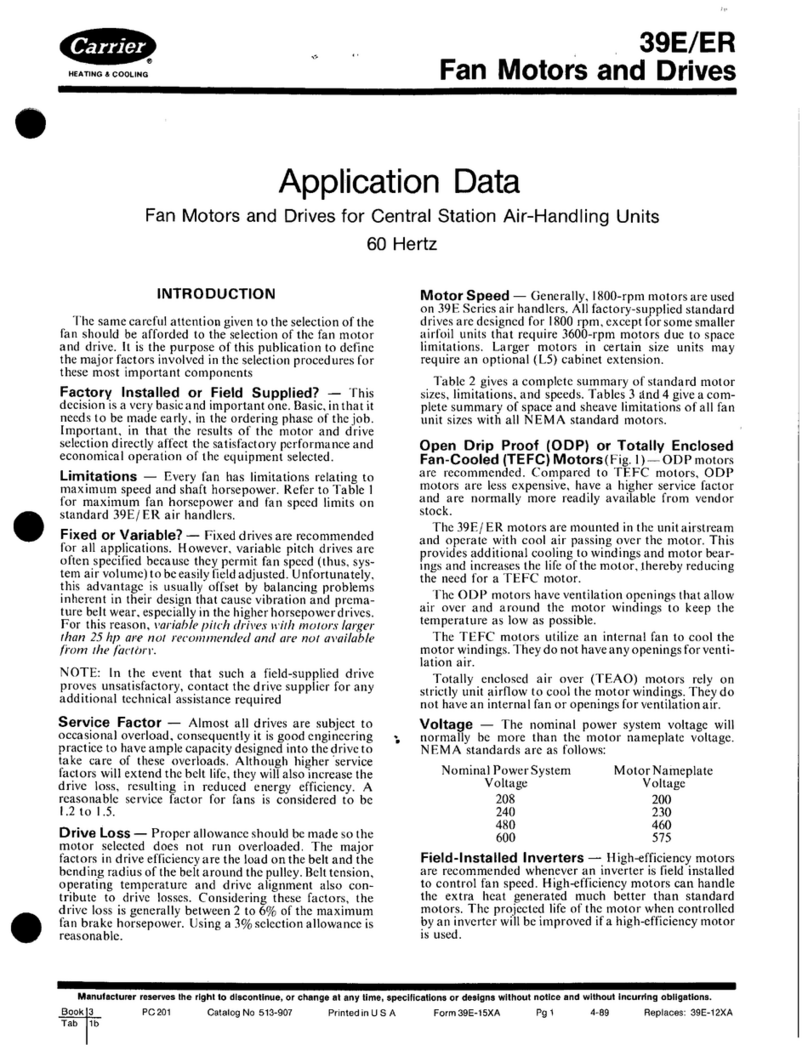
Carrier
Carrier 39E/ER Application data
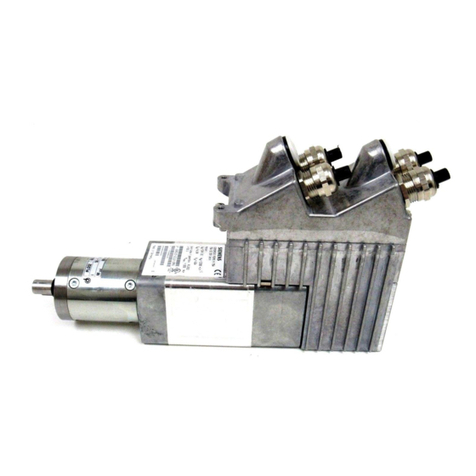
Siemens
Siemens SIMODRIVE POSMO A Function manual
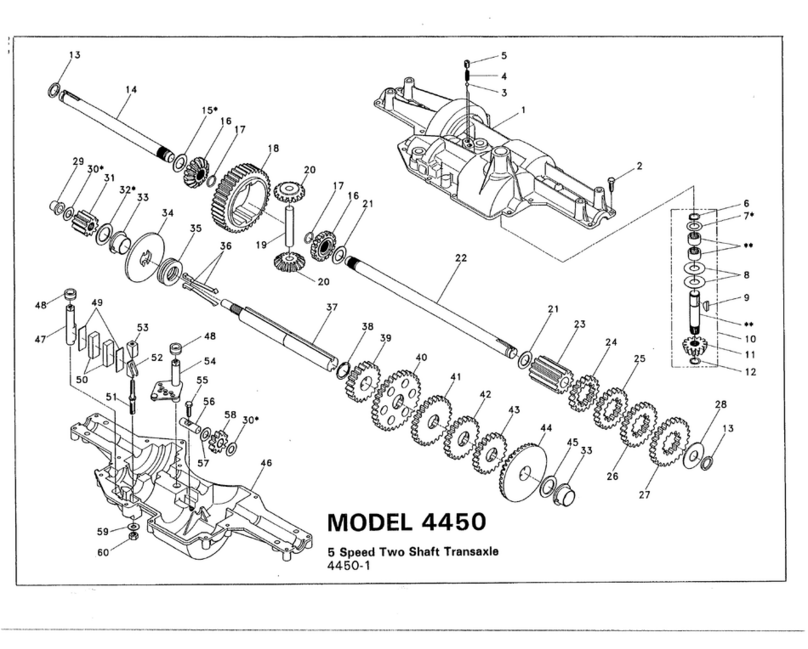
DANA
DANA 4450-1 parts list