LiftEquip MFC-16 Series User manual

Edition: October 1997 - 1 -
Elevator Drive System MFC - 16
Installation Instruction
1 GENERAL ............................................................................................................... 3
1.1 SAFETY INSTRUCTION.............................................................................................. 3
1.2 INSTALLATION INSTRUCTIONS ................................................................................... 4
1.3 TECHNICAL DATA .................................................................................................... 5
1.3.1 General Specifications ................................................................................... 5
1.3.2 Type-Specific Data.........................................................................................6
1.4 GENERAL INSTRUCTIONS ......................................................................................... 7
1.4.1 Supply Voltage............................................................................................... 7
1.4.2 Supply Form................................................................................................... 7
1.4.3 Supply Connection......................................................................................... 7
1.4.4 Earth Leakage Current................................................................................... 7
1.4.5 Fault Current..................................................................................................7
1.4.6 Insulation Resistance..................................................................................... 7
1.4.7 Discharge Time of the Radio Interference Filter............................................. 7
1.4.8 Electronic Ground .......................................................................................... 8
1.4.9 Motor Contacter ............................................................................................. 8
1.4.10 Internal Fan.................................................................................................. 8
2 INTERFACE ............................................................................................................ 8
2.1 CIRCUIT CONNECTION DIAGRAM............................................................................... 8
2.2 INVERTER CONNECTIONS.......................................................................................... 8
2.2.1 Incoming Power Supply .................................................................................8
2.2.2 Motor.............................................................................................................. 8
2.2.3 Braking Resistor............................................................................................. 9
2.2.4 Internal Voltage.............................................................................................. 9
2.2.5 Extra Motor Cooling Fan................................................................................ 9
2.2.6 Size of Cables................................................................................................ 9
2.3 MOTOR THERMISTOR: CONNECTION ....................................................................... 10
2.4 ENCODER: CONNECTION........................................................................................ 10
2.5 WIRING CIRCUIT FOR THE ELEVATOR CONTROL....................................................... 10
2.5.1 Operational Readiness................................................................................. 10
2.5.2 Digital Input and Output ............................................................................... 10
2.5.3 Switching Sequence Diagramm................................................................... 12

Edition: October 1997 - 2 -
3 LINE FEEDACK, EMV........................................................................................... 13
3.1 GENERAL.............................................................................................................. 13
3.2 FITTING REGULATION............................................................................................. 13
3.3 POWER SUPPLY CHOKE......................................................................................... 14
3.4 POWER SUPPLY FILTER......................................................................................... 14
3.5 INSTALLATION OF OTHER WIRES AND CABLES ........................................................... 14
4 APPENDIX............................................................................................................. 14
4.1 DIMENSIONS DIAGRAM OF MFC 16......................................................................... 15
4.2 FRONT VIEW MFC 16 / 12-26............................................................................... 15
4.3 FRONT VIEW MFC 16 / 40 .................................................................................... 16
4.4 FRONT VIEW MFC 16 / 60 .................................................................................... 17
4.5 CIRCUIT WIRING DIAGRAM..................................................................................... 19
4.6 EXTERNAL UNITS................................................................................................... 20
4.6.1 Part / Order numbers.................................................................................... 20
4.6.2 Dimension Diagrams.................................................................................... 21

Edition: October 1997 - 3 -
1 GENERAL
These Installation Instructions are designed to give Planners of advanced Elevator
control systems the necessary information for installing the MFC 16 series Inverters.
For commissioning, please see the separate Commissioning Instructions.
1.1 Safety Instruction
a) Work on the Frequency Converter may only be carried out by qualified personnel.
All safety rules and regulations as may internationally and locally apply must be
strictly observed and all persons must have been informed of the dangers of electric
current.
b) When installing the Inverter, all relevant laws, safety regulations and procedures
as may apply must be followed, (including VDE 0160).
c) Electrical Energy may still be present in the Converter and the external braking
resistor, even after switching off, because off the charge in the intermediate circuit
condensors. This applies in particular when there is a defect in the system. An
appropriate safety warning is affixed to the unit and must also appear in the
operating instructions of the Elevator control.
d) The heat-sink in the unit may reach a temperature in excess of 60 degrees
Celsius during operation and shortly after switching off, may still retain this
temperature.
e) The housing of the braking resistor unit can exceed a temperature of 80 degrees
Celsius during operation. All necessary precautions must be taken. In particular,
when the unit is wall mounted, care must be taken to ensure that no flammable
material is nearby.
These safety instructions do not claim to be complete and no legal liability shall be
deemed to arise therefrom.

Edition: October 1997 - 4 -
1.2 Installation Instructions
Inverters are defined as build-in units (Safety Precaution IP 20).
The installation dimensions together with the required ventilation clearances are
given in the dimensions tables in the Appendix hereto.
The specified vertical mounting position must be adhered to and free passage of air
to the heat sink unit must be ensured.
If installed in a control cabinet, there must bi suitable ventilation louvres.
In the case of impurities in the cooling air which could affect the functioning of the
Inverter, suitable precautions must be taken, (e.g. provision of a regularly serviced air
filter).
When a control cabinet is used, the individually housed braking resistor, Safety
Precaution IP 20, is to be installed outside the cabinet ((preferably on the top
thereof).
The installation dimensions and ventilation clearances are given in the relevant
dimensions tables in the Appendix.

Edition: October 1997 - 5 -
1.3 Technical Data
1.3.1 General Specifications
Power Supply Rating
Supply Voltage (Nominal) (V) 3 AC 400 without N
Supply Voltage Tolerance (V) 3 AC 380 -10% to 415 +10%
Supply Frequency (Hz) 50 nominal, range 48 ... 63
Power Factor cos ϕ=10.99 at nominal power
Supply Power Factor Lambda 0.94 at nominal power
Safety Precautions and Climatics Conditions
Safety Precautions (°C) IP20
Permitted Ambient Temperature (m NN) 0 ... 45
Maximum Operating Altitude (%) 1000
Maximum Relative Humidity 65
Contamination grade 2(to DIN VDE 0160)
Line Feedback EMV (EMC)
Radio Interference Level as in prEN 12015
Interference Tolerance as in prEN 12016
EN 50082-1
When built into a control
cabinet, using a supply filter
and appropriate wiring.
Current Harmonic Content I5/ I1< 0.3 Value at Nominal power
Total Harmonic Distortion THD-F* 33% approx Value at Nominal power
* [Total Harmonic Distortion (Harmonic Distortion Effective Current) in relation to the
Fundamental Current Oscillation.]
Mode of Operation Characteristics
Alternating load tolerance S 5
Operating Cycles (max) (c/H) 240
Short Circuit Tolerance as required in DIN VDE 0160
The right to amend Technical Specifications is reserved.

Edition: October 1997 - 6 -
1.3.2 Type-Specific Data
Type MFC 16
12 MFC 16
18 MFC 16
26 MFC 16
40 MFC 16
60
Motor Power
at n = 1270 - 1420 rpm
at n = 1420 - 1650 rpm
(kW) up to 6
up to
6.5
6 - 8
6 - 8.5 7 - 10
8 - 11 9 - 16.5
9 - 18 16 -27.5
16 -28.5
Input Data
Input Fusing AFF (A) 25 30 40 50 80
Input Current (Nominal) (A) 13 16 23 34 52
Input Current (Peak) (A) 18.5 26 37 55 88
Output Data
Output Voltage (Nominal) (V) 3 x 0 ... 360
Output power (Nominal) (kVA) 9.5 11 16 25 36
Maximum Output Power for 10
soconds (kVA)13.518264060
Output Current (Nominal) (A) 15.5 18 27 42 60
Maximum Output Current for 10
seconds (A)22304367100
Loss at Nominal Power (W) 480 500 540 620 835
Efficiency 0.96 0.97
Mechanical Data
Dimensions Width (mm) 339 363
Height (mm) 493 658
Depth (mm) 270 285
Minimum clearance above/below (mm) 150 / 100 200 / 100
Ventilation requirements (m3/h) 250 300
Weight (kg) 26 27 27 29 39
Braking Resistor (External) Convection cooling
For use with MFC 16 model: MFC 16
12 MFC 16
18 MFC 16
26 MFC 16
40 MFC 16
60
Resistor value (Ohm) 23 14 14 14 7
Thermal Continuous
Performance PD(kW) 1,5 3 3 4 6,5
Peak Performance for 2 secs. (kW) 4 6 10 12 18
Safety Precaution IP 20
Mimimum Clearance, sides and
above mm 200
Maximum Ambient Temperature (oC) 45
Maximum Operating Altitude (m) 1000
The right to alter Technical Specifications is reserved

Edition: October 1997 - 7 -
1.4 General Instructions
1.4.1 Supply Voltage
When the supply voltage deviates from the authorised Supply Voltage Tolerance
(380V -10% ... 415V + 10%), it is necessary to fit an Autotransformer at the power
supply point.
Because of the fixed voltage motor, suitable adaptation is also necessary where the
supply voltage is too low.
1.4.2 Supply Form
The Inverter and the Power Supply Filter are set up for TN and TT supplies (VDE
0100 part 410).
For other supply types, e.g. IT supply, an Isolating Transformer is necessary at the
power supply point. If this is not done an undefined load can occur at the power
supply filter in the case of an earth fault.
1.4.3 Supply Connection
The Inverter must be connected to the Incoming Power Supply via a permanent
connection.
1.4.4 Earth Leakage Current
To suppress radio interference, Y condensers ar fitted in the Inverter and in the
external circuit between the Phase and the Earth wire. These counteract leakage
corrents each of > 3.5 mA.
Therefore, in accordance with VDE 0160 (6.5.2.1a), the earth wire cross-section of
the power supply must be at least 10mm² Cu.
1.4.5 Fault Current
A D.C. fault current can occur in the inverter by body contact. This fact, with the
existing leakage of the Y condensors, does not allow the use of an fault current (FI)
protection device. to conform with VDE 0160 (5.5.3.4.2), a suitable notice must be
given in the operating instruction manual forbidding the use of a fault current (F1)
protection relay.
1.4.6 Insulation Resistance
Resistors are wired in parallel for the discharge of Y condensors.
It is therefore not possible to measure the insulation resistance on an Inverter and ist
accessories, when installed and operationally ready.
The testing of the insulation resistance is carried out as part of the quality control in
accordance with the Standards of the German Society of Electrical Engineers (VDE
0160 - 7.6.2)
1.4.7 Discharge Time of the Radio Interference Filter
A residual voltage of 60V after 5 seconds, as recommended in the VDE 0113 (part 1)
Standards, is not conformed with.
An appropriate warning notice must be displayed in the control cabinet.

Edition: October 1997 - 8 -
1.4.8 Electronic Ground
The Electronic Ground (Electronic Zero) is galvanically connected to the Line
protection ground wire (PE).
1.4.9 Motor Contacter
The motor current at low rpm and when stationary is almost D.C. (low Hertz)
When Contactors with A.C. contacts are used between the Inverter and the motor, it
is important to ensure, for correct control operation, that when the ‘open’ command is
given, the Inverter is also prevented from operating. (See switching Sequence
Diagram)
The use of contactors with D.C. coils is recommended. A delayed switch-off of the
relay is then achieved.
1.4.10 Internal Fan
The internal fan for cooling the heat-sink is governed by the Inverter control system,
dependant on elevator operation. It runs on for a predetermined time after the end of
a journey.
2 INTERFACE
2.1 Circuit Connection Diagram
The circiut connection diagram, (see Appendix), gives an overview of all connections
necessary for the operation of the Inverter.
2.2 Inverter connections
2.2.1 Incoming Power Supply
Power supply to the Inverter L1, L2, L3, without N, on terminal strip X1, terminals 1,
2, 3.
2.2.2 Motor
The motor is connected to terminal strip X1, terminals 8, 9, 10.
It must be connected via a 4 core screened cable. The screening must be clamped
onto the motor terminal box and on the control cabinet inlet for EMV reasons.
The necessary cable lead-throughs must be allowed for.
The unscreened motor wiring running between the control cabinet cable inlet and the
Inverter exit, must be kept short and be twisted together.
The motor cable should be no longer than 30m. (If a longer cable is necessary,
please first consult). If possible, the cable should not be layed parallel to the
signalling lines.

Edition: October 1997 - 9 -
2.2.3 Braking Resistor
The external Braking resistor unit is connected to terminals 1 and 2 of the terminal
strip X2 and to the adjacent PE terminal.
If mounted on the top of the control and twisted. If mounted separately near the
control cabinet the connecting cable must be screened.
DANGER! When the Inverter is switched on, this external Braking Resistor Unit is
charged with 600 V DC !
Even a long time after switching the Inverter off, a charge may still be
present. This applies particularly when there is some defect in the
system.
An appropriate Warning Notice must be displayed in the control cabinet !
2.2.4 Internal Voltage
The voltage adaptation for the internal fan and for the internal electronic voltage is
made by an appropriate bridge on the terminal strip X3. (L-380V, L-400V or L-415V)
2.2.5 Extra Motor Cooling Fan
If a separate cooling fan on the motor is needed, this is to be switched directly
through the elevator control unit.
2.2.6 Size of Cables
The cross-section of all cables must be proportionate to the various currents in the
unit:
Input Fuse
AFF Line Rated
Current
A
Mains
Cable
∅/ mm²
Motor Rated
Current
A
Motor
Cable Size
∅/ mm²
Branking
Resistor
∅/ mm²
MFC 16 -
12 25 13 2,5 15,5 2,5 1,5
MFC 16 -
18 30 16 2,5 18 2,5 2,5
MFC 16 -
26 40 23 4 27 6 2,5
MFC 16 -
40 50 34 10 42 10 2,5
MFC 16 -
60 80 52 16 60 16 6
The earth wire cross-section for all model types must be an minimum of 10mm² Cu.
(See section 1.4.4 - Earth Current)

Edition: October 1997 - 10 -
2.3 Motor Thermistor: Connection
The Thermistor located in the motor is to be connected to terminal strip X1, terminals
6 and 7. Approximately 30 seconds after an excessive motor temperature is reached,
the Inverter is switched off. The MFC 16 ‘operation-ready’ indication supplied from
terminal strip X1 terminals 4 and 5 is suspended.
After the motor has cooled (readiness again indicated) a new operating instruction
can be given. Where no Thermistor is fitted, terminals 6 and 7 are to be connected
with a wire bridge.
2.4 Encoder: Connection
The encoder for rpm determination is connected to the plug X907 of the FMC printed
circuit board. (9 pin D mini- plug/socket)
The screening of the sensor cable is to be clamped, both on the side of the unit as
well as on the plug housing, for EMV reasons.
The sensor/feed cable length should not exceed 40 metres.
The impulse count of the Encoder is 4096 increments per revolution, for all DKE
motors.
2.5 Wiring Circuit for the Elevator Control
2.5.1 Operational Readiness
On the terminal strip X1 terminals 4 and 5 there is a volt-free contact (Closing
230VAC/3A) to notifiy ‘Inverter Operationally Ready’
2.5.2 Digital Input and Output
The digital inputs and outputs are to be connected via plugs X1, X2 and X3 of the
IPV wiring board.
The screening of these cables should be clamped on the control side.
The input and output signals are electrically isolated by the MFC 16. The control
voltage levels for the digital control signals between the Elevator Control and the
MFC 16 are determined by the Elevator Control.
Control voltage for digital control signals, plug X1 / IPV
0 V (N) Pin 1
+24 V Pin 2

Edition: October 1997 - 11 -
Digital Control SIGNALS from Elevator Control to MFC 16, Plug X1 / IPV
Start and Travel Direction
Signal upwards UP Opto Coupler
Inlet 24 V DC,
50 mA Pin 3
Start and Travel Direction
Signal downwards DOWN ditto 24 V DC
50 mA Pin 4
Nominal Speed vNditto 24 V DC
50 mA Pin 5
Interim Speed v2ditto 24 V DC
50 mA Pin 6
Inspection Speed vIditto 24 V DC
50 mA Pin 7
Levelling Speed voditto 24 V DC
50 mA Pin 8
Main contacter status
acknowledgement
Alternative to QSP
QSP1 ditto 24 V DC
50 mA Pin 10
Output Signals from MFC 16 to Elevator Control, Plug X2 / IPV
Switch on Signal for Supply
overload relay ESP Relay outlet 250 VAC,
5 A Pin 1
Pin 2
Switch on Signal for Brake EBS Relay outlet 250 VAC,
5 A Pin 4
Pin 5
Speed signal from MFC 16 to Elevator Control, Plug X1 / IPV
Speed v <= 0,3 Relay outlet 24 VDC,
1 A Pin 11
Pin 12
Acknowledgement signal from Elevator Control to MFC 16, Plug X3 / IPV
Main Contacter status
acknowledgement
Alternative to QSP 1
QSP Opto Coupler
Inlet 180 - 250 VAC Pin 1
Pin 2
The right to alter technical specifications is reserved.

Edition: October 1997 - 12 -
2.5.3 Switching Sequence Diagramm

Edition: October 1997 - 13 -
3 LINE FEEDACK, EMV
3.1 General
To minimize the line feedback, (Radio Interference or Harmonics), the following
external units are available:
Incomming Power Filter and Power Choke (see Appendix for technical data and
dimensions). The Inverter is to be connected to these additional external units as
shown in the Connection Wiring Diagramm (see 4.5)
3.2 Fitting Regulation
To comply with standards prEN 12015, prEN 12016 and EN 50082/1, the following
measures must be taken:
- The Inverter and the external units must all be mounted on a single galvanised
mounting plate
- Installation of the external units in accordance with the Connection Wiring
Diagramm. This must be displayed in the control cabinet immediately adjacent to
the Inverter Connecting wiring up to 50cm must be twisted.
Longer cables must be screened.
- Screening of the wires and cables to the Motor, Encoder, Thermistor and Braking
Resistor.
- Twisted or screening of the wiring between the Incoming Power Filter, Power
Choke and Inverter.
- Twisting or screening of the wiring between the Inverter and Motor Contactors.
- The screening of all such wires and cables must be clamped to the earthed
mounting plate.
- The screening of the motor cable must also be clamped to the motor housing in
the motor terminal box. (Use suitable PG screw connectors)
- The screening of the Braking Resistor cable must also be clamped to the Resistor
housing.
The user is responsible for compiance with the EMV Guidelines. The Installation
Repulations must be followed.

Edition: October 1997 - 14 -
3.3 Power Supply Choke
The required installation of the 3-phase power choke (in combination with the
integrated DC choke) gives the drive the following advatages:
- An approximation of the Line Current to the Sinesoidal form
- reduced line current harmonics
- a limitation of the commutation effects on the line voltage to a permissable value
3.4 Power Supply Filter
Correct installation of the power supply filter in accordance with regulations will
reduce the radio interference to a permissable level.
3.5 Installation of other wires and cables
Wiring unrelated to the Inverter (e.g. for the Motor Brake) must, for EMV reasons, be
routed seperately from the wires and cables to the Motor, thermistor and encoder.
These should also not be routed through the motor connection box.
4 APPENDIX

Edition: October 1997 - 15 -
4.1 Dimensions Diagram of MFC 16
Mindestfreiräume / minimal free spaces
unten / bottom 100mm
oben / top 150mm MFC16/12-26
200mm MFC16/40-60
Typ A B C D E F
MFC16/12 339 493 270 250 460 7
MFC16/18 339 493 270 250 460 7
MFC16/26 339 493 270 250 460 7
MFC16/40 339 493 270 250 460 7
MFC16/60 363 658 285 280 620 9
alle Maßangaben in mm
all dimensions in mm
4.2 Front View MFC 16 / 12-26

Edition: October 1997 - 16 -
4.3 Front View MFC 16 / 40

Edition: October 1997 - 17 -
4.4 Front View MFC 16 / 60

Edition: October 1997 - 18 -

Edition: October 1997 - 19 -
4.5 Circuit Wiring Diagram

Edition: October 1997 - 20 -
4.6 External Units
4.6.1 Part / Order numbers
Appliance
(order no.) Power Supply
Filter L1
(order no. )
Power Supply
Choke L2
(order no. )
MFC 16 - 12 1 560 445 225 B 84143A 12-R
(00 993 29 100) K 305 - 12/0,82
(1 753 445 007)
MFC 16 - 18 1 560 445 226 B 84143A 16-R
(0 860 000 060) K 305-940
(1 753 445 008)
MFC 16 - 26 1 560 445 227 B 84143A 25-R
(0 860 000 061) K 306-945
(1 753 445 009)
MFC 16 - 40 1 560 445 228 FN 351-36-33
(0 860 000 054) NK 307/34/0,43
(1 753 445 011)
MFC 16 - 60 1 560 445 229 FN 351-50-33
(00 990 37 10 0) NK 308/50/0,29
(00 993 34 10 0)
Braking Resistors
(order no.)
MFC 16 - 12 23 Ohm / 1,5 kW
(00 993 21 20 0)
MFC 16 - 18 14 Ohm / 3 kW
(00 993 22 20 0)
MFC 16 - 26 14 Ohm / 3 kW
(00 993 22 20 0)
MFC 16 - 40 14 Ohm / 4 kW
(00 993 23 20 0)
MFC 16 - 60 7 Ohm / 6,5 kW
(00 993 24 20 0)
This manual suits for next models
5
Table of contents
Popular DC Drive manuals by other brands
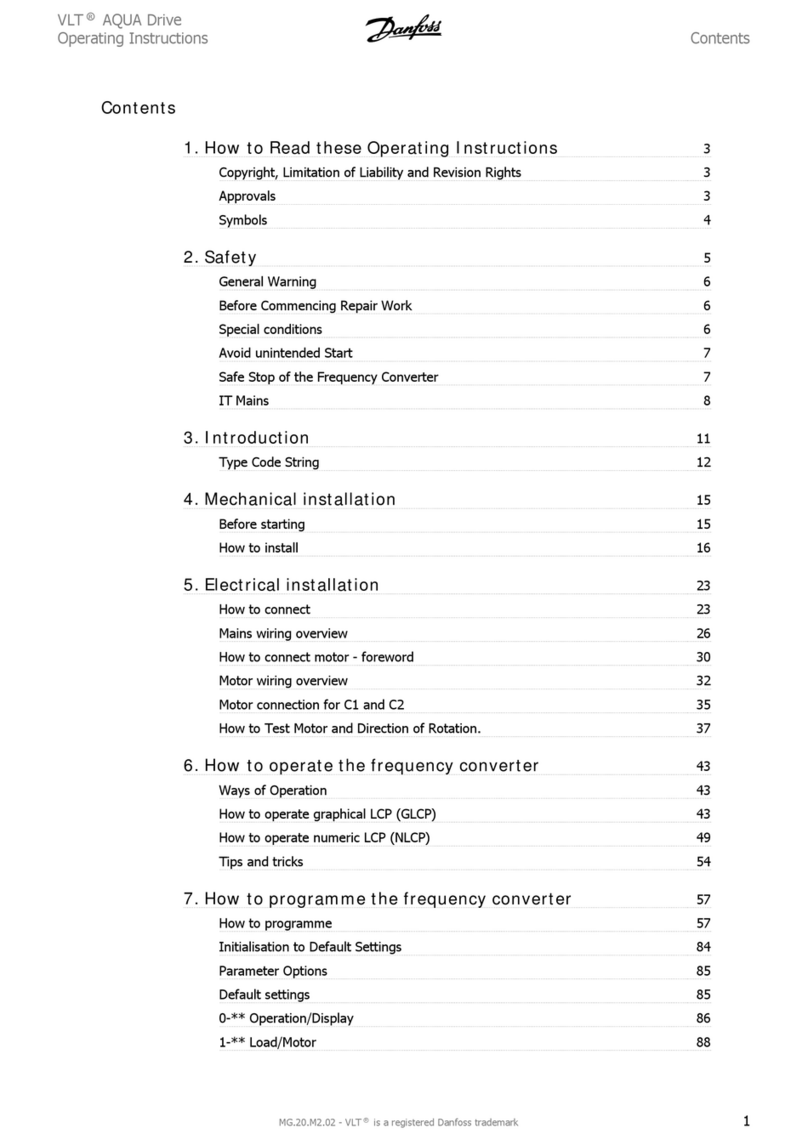
Danfoss
Danfoss VLT AQUA Drive FC 202 operating instructions
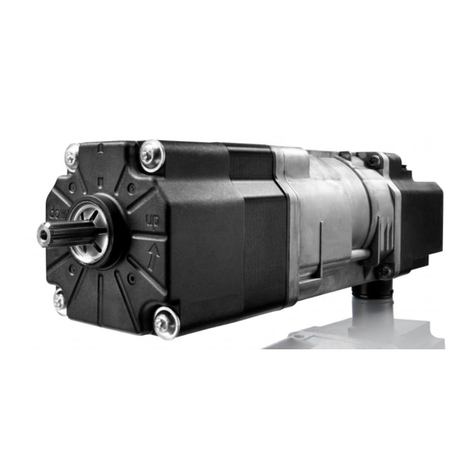
SOMFY
SOMFY J4 WT Operating guidelines
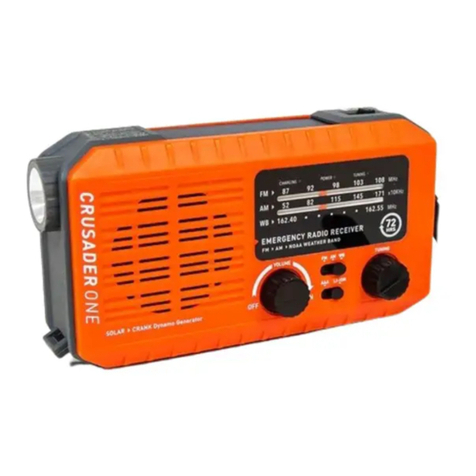
BMG
BMG CRUSADER ONE 72H-033 instruction manual

GFA ELEKTROMATEN
GFA ELEKTROMATEN ELEKTROMAT SI 75.10-55,00 installation instructions
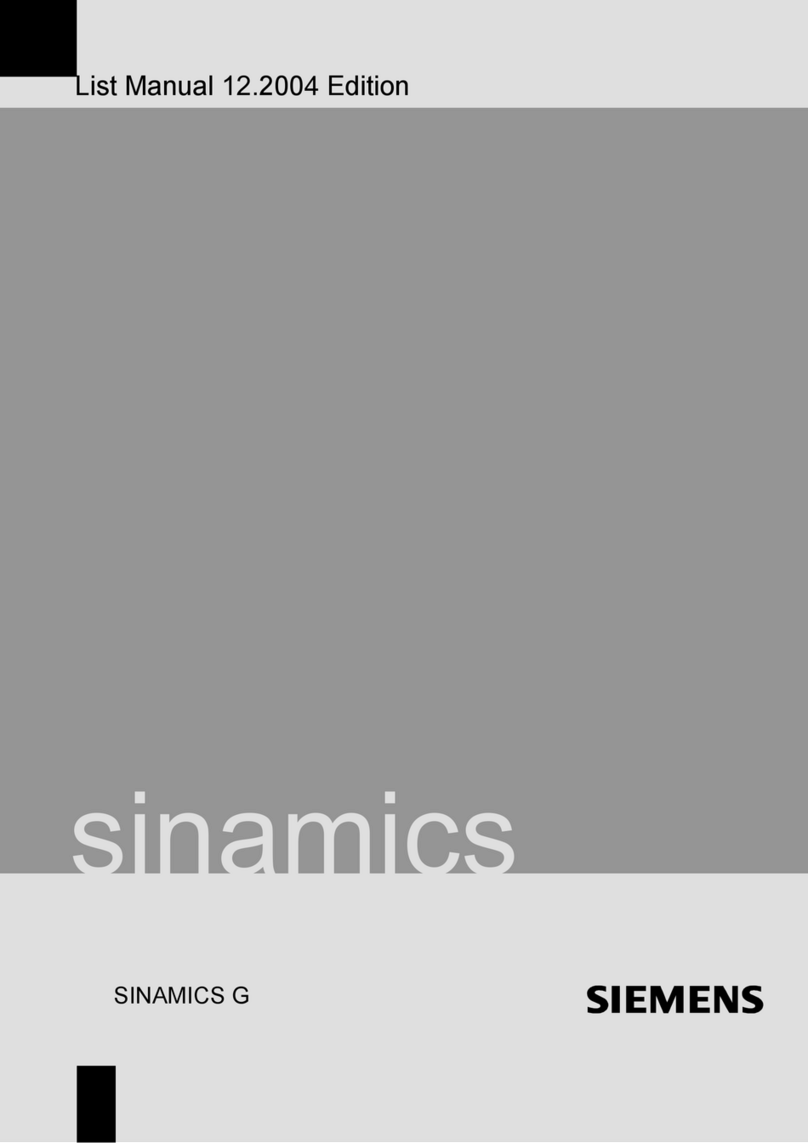
Siemens
Siemens SINAMICS G List manual
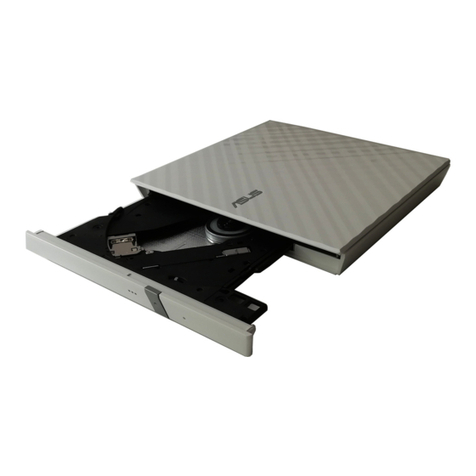
Asus
Asus SDRW-08D2S-U Quick installation guide