Lumberjack DP16-1050B User manual

DP16-1050B
SAFETY AND OPERATING MANUAL
16mm Bench Top Drill Press
DP16-1050B
ORIGINAL INSTRUCTIONS

DP16-1050B
TABLE OF CONTENTS
Welcome to Lumber
j
ack!
Dear customer, Congratulations on your purchase. Before using the
product for the first time please be sure to read these instructions for use.
They provide you with all information necessary for using the product safely and to
ensure its long service life.
Closely observe all safety information in these instructions!
General Power Tool Safety Warnings………………………………….…......
Symbols & Cable Rating Chart ……….…………………………………….………
Machine Details and Product Features……….…………………………….….
Assembly……………………………………………………………………………………..
Adjustments………………………………………………………………………………..
Operation, Maintenance and Service…………………………………………..
Lumberjack Guarantee………….…………………………………………………….
Declaration of Conformity……………………………………………………………
Parts List…………..………………………………………………………………………...
Parts Diagram………………………………………………………………………………
01
05
06
08
12
15
17
19
20
22

DP16-1050B 01
GENERAL POWER TOOL SAFETY WARNINGS
WARNING Read all safety warnings and
all instructions.
Failure to follow the warnings
and instructions may result in electric shock, fire
and/or serious injury.
Save all warnings and instructions for
future reference.
The term "power tool" in
the warnings refers to your electric (corded)
power tool or battery-operated (cordless) power
tool.
1. Work area safety
a)Keep work area clean and well lit. Cluttered
or dark areas invite accidents.
b) Do not operate power tools in explosive
atmospheres, such as in the presence of
flammable liquids, gases or dust. Power tools
create sparks which may ignite the dust or
fumes.
c) Keep children and bystanders away while
operating a power tool. Distractions can cause
you to lose control.
2. Electrical safety
a) Power tool plugs must match the outlet.
Never modify the plug in any way. Do not use
any adapter plugs with grounded power tools.
Unmodified plugs and matching outlets will
reduce risk of electric shock.
b) Avoid body contact with grounded surfaces,
such as pipes, radiators, ranges and
refrigerators
.
There is an increased risk of electric
shock if your body is grounded.
c) Do not expose power tools to rain or wet
conditions. Water entering a power tool will
increase the risk of electric shock.
d) Do not abuse the cord. Never use the cord for
carrying, pulling or unplugging the power tool.
Keep cord away from heat, oil, sharp edges or
moving parts. Damaged or entangled cords
increase the risk of electric shock.
e) When operating a power tool outdoors, use an
extension cord suitable for outdoor use. Use of a
cord suitable for outdoor use reduces the risk of
electric shock.
f) If operating a power tool in a damp location is
unavoidable, use a residual current device (RCD)
protected supply. Use of an RCD reduces the risk
of electric shock.
3. Personal safety
a) Stay alert, watch what you are doing and use
common sense when operating a power tool. Do
not use a power tool while you are tired or under
the influence of drugs, alcohol or medication. A
moment of inattention while operating power
tools may result in serious personal injury.
b) Use personal protective equipment. Always
wear eye protection. Protective equipment such
as dust mask, non-skid safety shoes, hard hat, or
hearing protection used for appropriate conditions
will reduce personal injuries.
c) Prevent unintentional starting. Ensure the
switch is in the off position before connecting to
power source and/or battery pack, picking up or
carrying the tool. Carrying power tools with your
finger on the switch or energising power tools that
have the switch on invites accidents.
d) Remove any adjusting key or wrench before
turning the power tool on. A wrench or a key left
attached to a rotating part of the power tool may
result in personal injury.

DP16-1050B 02
GENERAL POWER TOOL SAFETY WARNINGS
e) Do not overreach. Keep proper footing and
balance at all times. This enables better control
of the power tool in unexpected situations.
f) Dress properly. Do not wear loose clothing or
jewellery. Keep your hair, clothing and gloves
away from moving parts. Loose clothes,
jewellery or long hair can be caught in moving
parts.
g) If devices are provided for the connection of
dust extraction and collection facilities, ensure
these are connected and properly used. Use of
dust collection can reduce dust-related hazards.
4. Power tool use and care
a) Do not force the power tool. Use the correct
power tool for your application. The correct
power tool will do the job better and safer at the
rate for which it was designed.
b) Do not use the power tool if the switch does
not turn it on and off. Any power tool that
cannot be controlled with the switch is
dangerous and must be repaired.
c) Disconnect the plug from the power source
and/or the battery pack from the power tool
before making any adjustments, changing
accessories, or storing power tools. Such
preventive safety measures reduce the risk of
starting the power tool accidentally.
d) Store idle power tools out of the reach of
children and do not allow persons unfamiliar
with the power tool or these instructions to
operate the power tool. Power tools are
dangerous in the hands of untrained users.
e) Maintain power tools. Check for misalignment
or binding of moving parts, breakage of parts and
any other condition that may affect the power
tool’s operation. If damaged, have the power tool
repaired before use. Many accidents are caused
by poorly maintained power tools.
f) Keep cutting tools sharp and clean. Properly
maintained cutting tools with sharp cutting edges
are less likely to bind and are easier to control.
g) Use the power tool, accessories and tool bits
etc. in accordance with these instructions, taking
into account the working conditions and the work
to be performed. Use of the power tool for
operations different from those intended could
result in a hazardous situation.
5. Service
a) Have your power tool serviced by a qualified
repair person using only identical replacement
parts. This will ensure that the safety of the power
tool is maintained.
b) If the replacement of the supply cord is
necessary, this has to be done by the
manufacturer or its agent in order to avoid a
safety hazard.
6. Battery Tool Use and Care
a) Recharge only with the charger specified by
the manufacturer. A charger that is suitable for
one type of battery pack may create a risk of fire
when used with another battery pack.
b) Use power tools only with specifically
designated battery packs. Use of any other
battery packs may create a risk of injury or fire.

DP16-1050B 03
GENERAL POWER TOOL SAFETY WARNINGS
c) When Battery pack is not in use, keep it away
from other metal objects, like paper clips, coins,
keys, nails, screws or other small metal object
that can make a connection from one terminal
to another. Shorting the battery terminals
together may cause burns or a fire.
D) User abusive conditions, liquid may be
ejected from the battery; Avoid contact. If
contact accidentally occurs, flush with copious
amounts of water. If liquid contacts eyes, seek
medical help immediately. Liquid ejected from
the batter may cause irritation or burns.
7. Additional Safety and working
Instructions
7.1. Dust from materials such as lead-containing
coatings, some wood types, minerals and
metals can be harmful to one’s health and
cause allergic reactions, leading to respiratory
infections and/or cancer. Materials containing
asbestos may only be worked by specialists.
Observe the relevant regulations in your country
for the materials to be worked.
7.2. Prevent dust accumulation at the
workplace. Dust can easily ignite.
8 Additional Safety Warning for Bench
Drills
8.1 Always wear hairnet for long hair, and
make sure you are wearing safety goggles.
8.2 Do not wear gloves, ties or loose clothing.
8.3 while drilling make sure the piece is
secured with a vice; never hold the workpiece
by hand! Never keep your fingers near where
they could touch the drill in case the piece
moves suddenly.
8.4Do not use the machine until it has been
properly installed in accordance with the
instructions provided.
8.5Do not switch on the machine until all pieces
have been firmly tightened together.
8.6Do not use the machine if it is damaged or
functioning badly.
8.7 Perform all adjustments before switching
on the machine, make sure to set table height
or depth stop to prevent the drill entering the
table.
8.8(If Applicable) Always make sure chick key is
removed before use.
8.9Before switching on the machine check the
chuck has been mounted correctly and
securely, and that the safety guard is engaged.
8.10In operations stick to recommended
speeds for the drilling accessories and material
being used.
8.11 Switch off the power before handling the
drill or chuck. Once finished remove drill and
clean the table before leaving the machine.
8.12 Always lock the on/off switch when
leaving the machine.

DP16-1050B 04
GENERAL POWER TOOL SAFETY WARNINGS
9. Using an Extension Cable
.
9.1. If an extension cable is required, use an
approved triple core extension cable suitable
for the power input of the tool.
9.2. Grounded tools always require a three wire
extension cable.
9.3. As the distance from the supply outlet
increases you must use a heavier gauge
extension cable. Using extension cables with
inadequately sized wire causes a serious drop in
voltage, resulting in loss of power and possible
tool damage.
9.4. The smaller the gauge number of the wire
the greater the capacity of the cord.
9.5. When using a cable reel, always unwind the
cable completely.

DP16-1050B 05
SYMBOLS AND POWER RATING CHART
Danger!
–
Read the operating
instructions to reduce the risk of
injury.
Caution! Wear safety goggles.
Caution! Wear ear defenders. The
impact of noise can cause damage
to hearing.
Amperes 7.5M 15M 25M 30M 45M 60M
0 – 2.0 6 6 6 6 6 6
2.1 – 3.4 6 6 6 6 6 6
3.5 - 5.0 6 6 6 6 10 15
5.1 – 7.1 10 10 10 10 15 15
7.1 – 12.0 15 15 15 15 20 20
12.1 – 20.0 20 20 20 20 25 -
Caution! Risk of Injury! Do
not reach into the running
saw blade
.
Caution! Wear a dust mask.

AIR6V 01AIR6V 01AIR6V 01AIR6V 01
DP16-1050B 06
MACHINE DETAILS AND PRODUCT FEATURES
Machine Details
Usage
Your bench drill has been designed for the
drilling of holes in metal, plastics and wood.
It has not been designed for commercial use.
Specifications:
Mains Voltage - 230V/50Hz
Power – 600W
Motor Speed – 1400min
-1
Speed Range – 12
(180/250/300/400/480/580/970/
1280/1410/1540/2270/2740RPM)
Swing –330mm
Spindle Taper – MT2
Max. Spindle Travel – 80mm
Drill Capacity – 16mm
Chuck Capacity – 16mm
Max. Distance From Chuck to the table –
430mm
Max. Distance From Chuck to the base –
630mm
Table Size – 254X254mm
Base Size – 450X270mm
Over all Height – 580mm
Nett Weight - 50Kgs
Gross Weight – 52Kgs
Package Contents:
A Table x 1
B Column Support Asm x 1
C Owner’s Manual x 1
D Box of loose parts x 1
E Bag of loose parts x 1
F Base x1
G Head Asm x 1
H Chuck guard Asm x 1
Loose parts list:
Hex M10 head screw x 4
M5 Hex “L” Wrench x 1
M3 Hex “L” Wrench x 1
Clamp-column lock x 1
Crank(with set screw) x 1
Feed handle x 3
Chuck x 1
Chuck Key x 1
Idler pulley assembly x 1
Belt “V” M24 x 1
Key-drift x 1
The design of the model may be different
depending on manufacturing changes.
H

DP16-1050B 07
MACHINE DETAILS AND PRODUCT FEATURES
Features
1. Belt Guard
2. Belt Tension Lock Handle
3. Belt Tension Handle
4. Head LOCK
5. Feed Handle
6. Column Collar
7. Table Support
8. Table Crank
9. Rack
10. Base
11. Column Support
12. Column
13. Table
14. Depth Scale
15. Depth Scale Indicator
16. Depth Scale Lock
17.Spring Cap
18. Chuck
19. Arm
20. Table Bevel Lock(Under Table)
21. Table Lock
22. Bevel Scale
23. Support Lock
24. Chuck Key
25. Chuck guard
Unpacking Instructions
1. Separate all parts from packaging materials and check all items are accounted for.
2. Remove the protective oil that is applied to the table and column. Any ordinary grease and spot
remover will do.
3. Apply a coat of paste wax to the table and column to prevent rust. Wipe all parts thoroughly with clean
dry cloth.

DP16-1050B 08
Assembly
Avoid unintentional starting of the machine.
During assembly and for all work on the
machine, the power plug must not be
connected to the mains supply.
Carefully remove all parts included in the
delivery from their packaging.
Remove all packaging material from the machine
and the accessories provided.
Before starting the operation of the machine for
the first time, check if all parts listed in the box
content section have been supplied
Note: Check the power tool for possible damage.
Before further use of the machine, check that all
protective devices are fully functional. Any
lightly damaged parts must be carefully checked
to ensure flawless operation of the tool. All parts
must be properly mounted and all conditions
fulfilled that ensure faultless operation.
Damaged protective devices and parts must be
immediately replaced by an authorised service
centre.
Base and column & table assembly
1. Position the base (A) on the floor. Remove the
protective covering and discard.
2. Remove protective sleeve from the column (B)
and discard. Place the column assembly on the
base, align the holes in the column support (C)
with the holes in the base.
3. Locate three long bolts from the parts bag.
4. Install a bolt in each hole through the column
support (C) and the base and tighten with the
ajustable wrench.
5.Loosen set screw (A) in column collar (B) with
3mm hex. Key (C) and remove collar and rack (D)
from the column.
6.Find the elevation worm gear shaft (A) in the
loose parts bag. Insert the elevation shaft into the
table support (B) and extend the shaft through the
opening as far as possible. The crank handle (C) is
to be installed on the elevation shaft, the set
screw (D) is to be aligned with the flat portion of
the shaft. The crank is to be positioned as close to
the arm support as possible, then tighten the set
screw.
7.With the long smooth end of the rack (A)
pointing upwards, slide rack down through the
large round opening in the table support (B).
Engage rack in gear mechanism found inside the
opening of the table support.
ASSEMBLY INSTRUCTIONS

DP16-1050B 09
8.While holding the rack (A) and table support
(B) in an engaged position, slide both down over
the column (C). Slide rack down the column until
the rack is positioned against the lower column
support (D).
9.Replace column collar (A) and position it bevel
side down over the rack (B). Tighten set screw
(C) in collar with 3mm hex. key (D). To let the
rack slide when the table is swung to the left or
right around the column, the collar must sit
loosely over the rack and should not be angled
on the column. Only tighten set screw enough to
keep the collar in place, otherwise the collar may
break due to excessive pressure.
NOTE: To avoid column or collar damage, do not
overtighten set screw.
10. Locate the support lock handle (A) in loose
parts bag and tighten by hand.
11. To minimize crank backlash; tighten the
support lock handle and rotate the elevation
worm shaft clockwise with the crank handle.
Loosen the set screw in the crank and reposition
it as close to the table support as possible.
Tighten set screw in the crank handle.
Installation the head
1. Remove the protective covering from the head
assembly.
2. Carefully lift the head above the column and
slide it down on the column as far as it will go.
Align the head with the table and the base.
3. Using a 4mm hex. Key, tighten the head set
screws on the right side of the head.
Installing pulley cover knob or locking
pulley cover
1.Install the knob (A) Fig.13B to the pulley cover
(B) using a small pan head screw (C) as shown in
Option #1.
2.For safety reasons, user may be required to lock
the pulley cover to prevent easy access to the
pulleys. This can be done by only using the small
pan head screw (C). Close the pulley cover and
screw panhead screw through the cover and into
the tab (D) as shown in Option #2.
ASSEMBLY INSTRUCTIONS

DP16-1050B 10
Installation the chuck & arbor
1. Locate the chuck in the box of parts.
2. Tighten Philip’s head screws of the chuck
guard to quill shaft.
3. Clean out the tapered hole in the chuck, also
clean the spindle nose with a clean cloth. Make
sure there are no foreign particles sticking tothe
surfaces. The slightest piece of dirt on the
spindle nose or thechuck will prevent the chuck
from seating properly. This will cause the drill to
“wobble .
NOTE: If the tapered hole in the chuck is
extremely dirty, use a cleaning solvent on a clean
cloth.
4. Tight philip’s head screws of the chuck guard
to quill shaft.
5.Push the chuck up on the spindle nose as far as
it will go.
6. Turn the chuck sleeve clockwise and open the
chuck jaws completely.
7. Lightly tap the nose of the chuck with a piece
of wood to insure the proper seating of the
chuck on the spindle.
Installation the feed handles
1. Locate the three feed handles among the loose
parts.
2. Screw the feed handle tightly into the threaded
holes in the hub.
Installing the belt guard knob
1.To attach the belt guard knob, use the knob and
a pan head screw from the loose parts bag. Insert
the pan head screw into the belt guard and screw
knob. Tighten.
WARNING!: To avoid possible injury, keep the
guard in place and in proper working order while
operating.
Tensioning the belt
NOTE: The drill press is shipped with the belt
installed, but it should be properly tensioned
before use.
1. Lift the guard (A) from the right side and keep it
opened.
2. Release the belt tension lock knobs (B) located
on the both side of the drill press head. Release
tension to the belt tension handle (C) clockwise.
Tighten the belt tension lock knobs (B).
ASSEMBLY INSTRUCTIONS

DP16-1050B 11
ASSEMBLY INSTRUCTIONS
3. Choose the desired speed for your drilling
operation, and move the belts (D) to the
indicated position on the pulleys (E). Refer to the
chart on the inside of the belt guard.
4. Loosen the belt tension lock knobs and turn
the belt tension handle (C) counterclockwise to
apply tension to the belts.
5. Tighten the belt tension lock knobs.
NOTE: The belt should deflect approximately
1/2” by applying finger pressure at the mid-point
of the belt between the pulleys.
6. Close the belt guard.
7. If the belt slips while drilling, readjust the belt
tension.
Installing drill bits
Insert the drill bit into the chuck far enough to
obtain the maximum gripping of the chuck jaws.
The chuck jaws are approximately 1” long. When
using a small drill bit, do not insert it so far that
the jaws touch the flutes (spiral grooves) of the
bit.
Make sure the drill bit is centered in the chuck
before tightening the chuck with the key. Tighten
the drill bit well, so that it doesn’t slip while
drilling. Turn the chuck key clockwise to tighten,
counter clockwise to loosen.

DP16-1050B 12
Adjustments
WARNING!
For your own safety, turn the switch
OFF and remove the plug from the power source
before making any adjustements. To avoid injury
from thrown parts due to the spring release,
follow instructions carefully and wear safety
glasses.
Drilling to a specific depth
To drill a blind hole (not all the way through) to a
given depth, proceed as follows.
1. Mark the depth of the hole on the workpiece.
2. Loosen the depth scale lock knob (A) Fig.19.
3. With the switch OFF, bring the drill bit down
until the tip of the lips of the drill bit are even
with the mark (B).
4. Turn the depth scale (C) counterclockwise
until it stops moving.
5. Tighten the depth scale lock knob.
The drill bit will stop at this depth until the depth
scale is readjusted.
Another way-depth scale
1. With the power OFF, loosen the depth scale
lock knob (A) Fig.19.
2. Place workpiece on table. Adjust table until
the tip of the drill is just a little above the top of
the workpiece.
3. Turn the depth scale (C) clockwise until the
depth scale indicator (D) points to the desired
drilling depth on the scale.
4. Tighten the depth scale lock knob.
5. The chuck or drill will now be stopped after
traveling downward the distance selected on the
depth scale.
Quill return spring
NOTE: The return spring tension is set at the
factory and should not require further
adjustment.
1. With the chuck at its highest possible position,
turn the depth scale (C) clockwise until it stops and
tighten the depth scale lock knob (A). This will
prevent the quill from dropping while tensioning
the spring.
2. Lower the table for additional clearance.
3. Work from the left side of the drill press.
4. Place screwdriver in the lower front notch (A)
of the spring cap (B), and hold it in place while
loosening and removing the outer nut (C) (only).
5. With screwdriver remaining in the notch, loosen
inner nut (D) (approx. 1/8”) until the notch
disengages from the boss on the head. Do not
remove this nut.
6. Carefully turn screwdriver counterclockwise and
engage the next notch (E) in the boss. Do not
remove screwdriver.
7. Tighten nut with wrench only enough to engage
boss. Do not over tighten as this will restrict quill
movement.
8. Check tension while turning feed handles.
9.If there is not enough tension on the spring,
repeat steps 4-8 moving only one notch each time
and checking tension after each repetition.
ADJUSTMENTS

DP16-1050B 13
Removing the chuck
1. Align key holes in spindle and quill (A ) by rotating
the chuck (C) by hand.
2. Insert drift key (B) into key holes in the quill.
3.Tap key drift key lightly until the chuck and arbour
fall out of the spindle.
NOTE: Place one hand below the chuck to catch it
when it falls out.
Adjusting the table square to the head
1. Insert a precision round steel rod (A)
approximately 3” long into the chuck and tighten.
2. With the table (B) raised to working height and
locked into position, place a combination square (C)
flat on the table beside the rod .
3. If an adjustment is necessary, loosen the table
bevel lock bolt (D) with an adjustable wrench and
loosen the set screw (E) below the table bevel lock
bolt. These adjustments are located under the table.
4. Align the table square to the rod by tilting the
table.
5. Retighten the table bevel lock bolt. Retighten set
screw.
Tilting the table
To use the table in a bevel position, loosen the bevel
lock bolt (D) with an adjustable wrench. Tilt the table
to the desired angle by reading the bevel scale on the
table support. Retighten the bevel lock bolt.
Feeding
Pull down the feed handles (A) with only enough effort
to allow the drill to cut. Feeding too slowly might cause
the drill to burn...feeding too rapidly might stop the
motor...cause the belt or drill to slip... tear the
workpiece loose or break the drill bit.
Hole location
Make an indentation in the workpiece where you want
the to drill a hole using a centre punch or a sharp nail.
Before turning the switch ON, bring the drill bit down
to the workpiece, lining it up with the hole location.
ADJUSTMENTS

DP16-1050B 14
Positioning the table and workpiece
Lock the table to the column in a position so that the
tip of the drill is just a little above the top of the
workpiece. Always place a piece of back-up material
(wood, plywood) on the table underneath the
workpiece. This will prevent splintering or making a
heavy burr on the underside of the workpiece as the
drill breaks through. To keep the back-up material
from spinning out of control, it must come in contact
with the left side of the column, as illustrated in
picture.
WARNING! To prevent the workpiece or the back-up
material from being tornfrom your hand while
drilling, position them against the left side of the
column. If the workpiece or the back-up material are
not not long enough to reach the column, clamp
them to the table. Failure to do this could result in
personal injury.
ADJUSTMENTS

DP16-1050B 15
OPERATION & MAINTENANCE AND SERVICE
Operation
–Practise on waste material first to learn how to
operating the machine.
–When drilling all the way through a piece of
material, adjust the table so the drill is aligned
with the centre of the table. Secure the work
piece securely an unsecured work piece results
in a rough drilling hole and increases the risk of
the drill bit breaking.
–Use a piece of waste wood beneath your
workpiece to reduce the risk of the work piece
splinting and protect the drill tip.
–Use the lift handles to slowly bring the drill
downwards and slowly feed the drill into the
workpiece.
–Drill extra slowly when the drill bit is about to
break through the workpiece to prevent
splintering.
Switching on
Lift the safety stop case and engage the green
start button.
Simply press the Red button to stop the machine
Switching on
Lift the safety stop case and engage the green
start button.
Simply press the Red button to stop the machine
Cleaning And Maintenance
Before performing any work on the equipment,
pull the power plug.
Regularly clean the ventilation slots, dust build
up can damage the motor.
Grease every three months by turning the drill
to maximum drill depth and greasing the shaft
with oil.
No repairs should be carried out without first
contacting the supplier as this will void your
warranty.
Storage
thoroughly cleans the whole machine and
accessories before storing to keep the machine
in good running condition.
Store out of reach of children in a stable cool
temperature dry place and avoid too high or too
low temperatures.

Trouble Probable cause Remedy
Noisy Operation 1. Incorrect belt tension
2. Dry spindle
3. Loose spindle pulley
4. Loose motor pulley
1. Adjust tension
2. Lubricate spindle
3. Tighten the retaining nut on
the pulley as needed
4. Tighten the set screws which
hold the pulleys in place
Drill Bit Burns 1. Incorrect speed
2. Chips not coming out of
the hole
3. Dull drill bit
4. Feeding too slow
5. Not lubricated
1. Change the speed
2. Retract drill bit frequently to
clear the chips
3. Resharpen the drill bit
4. Feeding too fast …allow the
drill bit to cut.
5. Lubricate the drill bit with
cutting or motor oil.
Wood Splinters On Underside Of
Workpiece.
1. No “back up material”
under workpiece
1. Use “back up material”
Workpiece Torn Loose From Hand. 1. Not supported or
clamped properly
1. Support the workpiece or
clamp it.
Drill Bits Binds To Workpiece 1. Workpiece is pinching
the drill bit or there is an
excessive feeding
pressure.
2. Improper belt tension
1. Support the workpiece or
clamp it
2. Adjust the tension of the belt.
Excessive drill bit wobbling. 1. Bent drill bit
2. Worn spindle bearings
3. Drill bit is not properly
installed in the chuck
4. Chuck not properly
installed.
1. Use a straight drill bit.
2. Replace the bearings
3. Install drill bit properly
4. Install chuck properly
Quill returns too fast or too slow. 1. Spring has improper
tension.
1. Adjust the spring tension.
Chuck will not stay attached to the
spindle. It falls off when trying to
install it.
1. Dirt, grease or oil on the
tapered inside surface of
chuck or on the spindles
tapered surface
1. Using household detergent
clean the tapered surface of
the chuck and the spindle to
remove the dirt, grease and
oil.
DP16-1050B 16
MAINTENANCE AND SERVICE

DP16-1050B 17
LUMBERJACK GUARANTEE
1. Guarantee
1.1 Lumberjack guarantees that for a period of
12 months from the date of purchase the
components of qualifying products (see clauses
1.2.1 to 1.2.8) will be free from defects caused
by faulty construction or manufacture.
1.2. During this period Lumberjack, will repair or
replace free of charge any parts which are
proved to be faulty in accordance with
paragraph 1.1 providing that:
1.2.1 You follow the claims procedure set out in
clause 2
1.2.2 Lumberjack and its authorised dealers are
given reasonable opportunity after receiving
notice of the claim to examine the product
1.2.3 If asked to do so by Lumberjack or its
Authorised dealer, you return the product at
your own cost to Lumberjack’s or supplying
Authorised Dealer’s premises, for the
examination to take place clearly stating the
Returns Material Authorisation number given by
Lumberjack or an Authorised Dealer.
1.2.4 The fault in question is not caused by
industrial use, accidental damage, fair wear and
tear, wilful damage, neglect, incorrect electrical
connection, misuse, or alteration or repair of the
product without approval.
1.2.5 The product has been used in a domestic
environment only
1.2.6 The fault does not relate to consumable
items such as blades, bearings, drive belts, or
other wearing parts which can reasonably be
expected to wear at different rates depending
on usage.
1.2.7 The product has not been used for hire
purposes.
1.2.8 The product has been purchased by you as
the guarantee is not transferable from a private
sale.
2. Claims Procedure
2.1 In the first instance please contact the
Authorised Dealer who supplied the product to
you. In our experience many initial problems with
machines that are thought to be faulty due to
faulty parts are actually solved by correct setting
up or adjustment of the machine. A good
Authorised Dealer should be able to resolve the
majority of these issues much more quickly than
processing a claim under the guarantee. If a
return is requested by the Authorised Dealer or
Lumberjack, you will be provided with a Returns
Material Authorisation number which must be
clearly stated on the returned package, and any
accompanying correspondence. Failure to provide
a Returns Material Authorisation number may
result in item being refused delivery at Authorised
Dealer.
2.2 Any issues with the product resulting in a
potential claim under the guarantee must be
reported to the Authorised Dealer from which it
was purchased within 48 hours of Receipt.
2.3 If the Authorised Dealer who supplied the
product to you has been unable to satisfy your
query, any claims made under this Guarantee
should be made directly to Lumberjack. The Claim
itself should be made in a letter setting out the
date and place of purchase, giving a brief
explanation of the problem which has led to the
claim. This letter should be then sent with proof

DP16-1050B 18
LUMBERJACK GUARANTEE
of purchase to Lumberjack. If you include a
contact number with this it will speed your claim
up.
2.4 Please note that it is essential that the letter
of claim reaches Lumberjack on the last day of
this Guarantee at the latest. Late claims will not
be considered.
3. Limitation of Liability
3.1 We only supply products for domestic and
private use. You agree not to use the product for
any commercial, business or resale purposes and
we have no liability to you for any loss of profit,
loss of business, business interruption or loss of
business opportunity.
3.2 This Guarantee does not confer any rights
other than these expressly set out above and
does not cover any claims for consequential loss
or damage. This Guarantee is offered as an extra
benefit and does not affect your statutory rights
as a consumer.
4. Notice
This Guarantee applies to all product purchased
from an Authorised Dealer of Lumberjack within
the United Kingdom. Terms of Guarantee may
vary in other countries.
Table of contents
Other Lumberjack Power Tools manuals
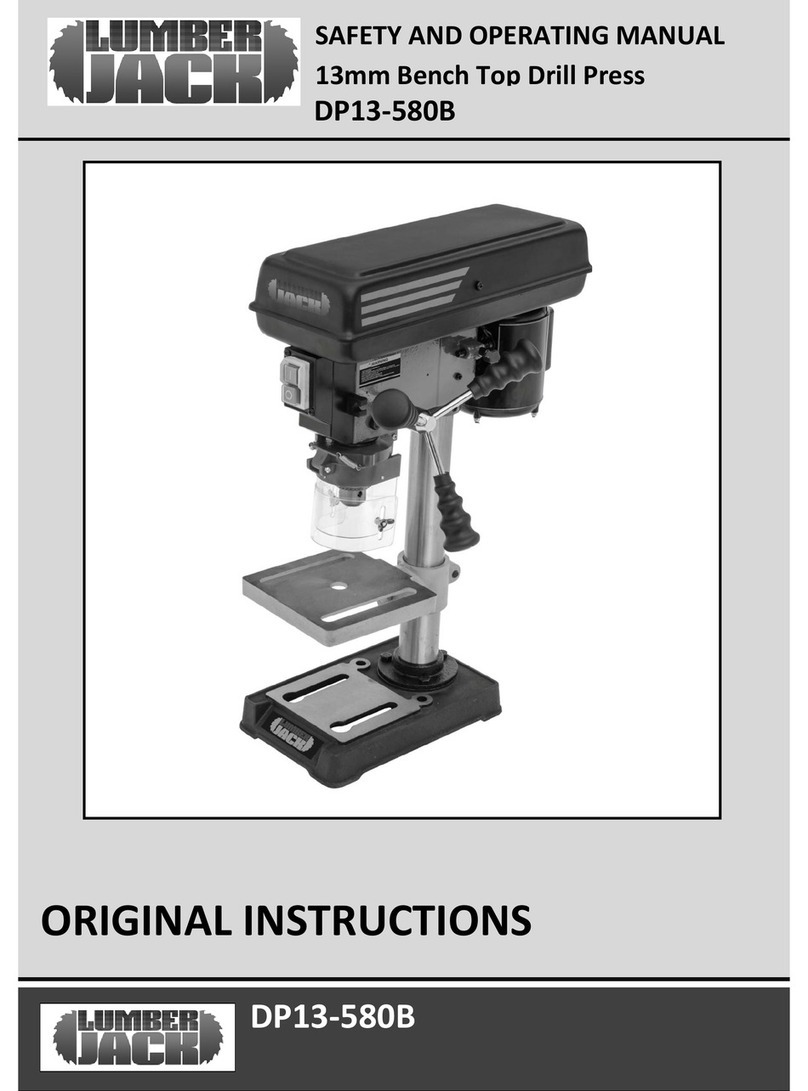
Lumberjack
Lumberjack DP13-580B Installation manual

Lumberjack
Lumberjack TTA-MULTI User manual
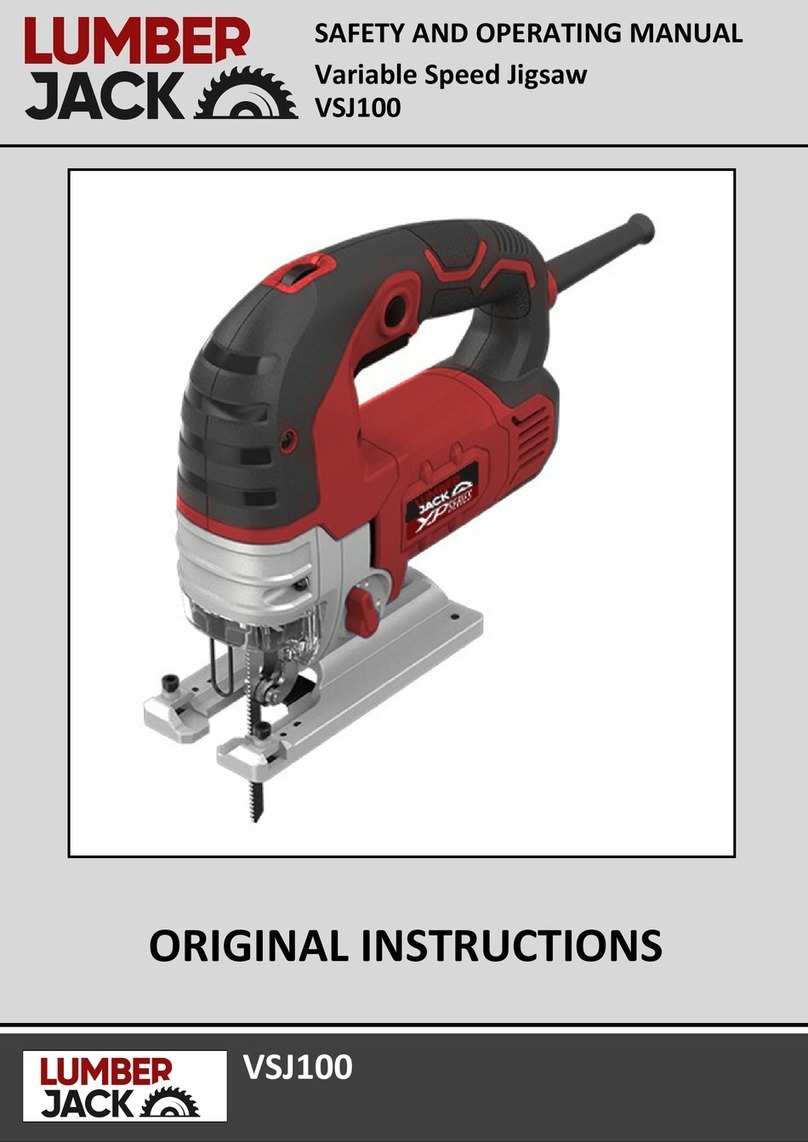
Lumberjack
Lumberjack VSJ100 Installation manual

Lumberjack
Lumberjack MT250 Installation manual
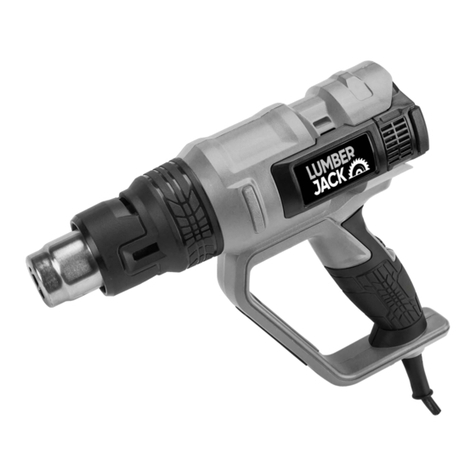
Lumberjack
Lumberjack HG2000P Installation manual

Lumberjack
Lumberjack BM16 User manual

Lumberjack
Lumberjack ST2000-15 User manual
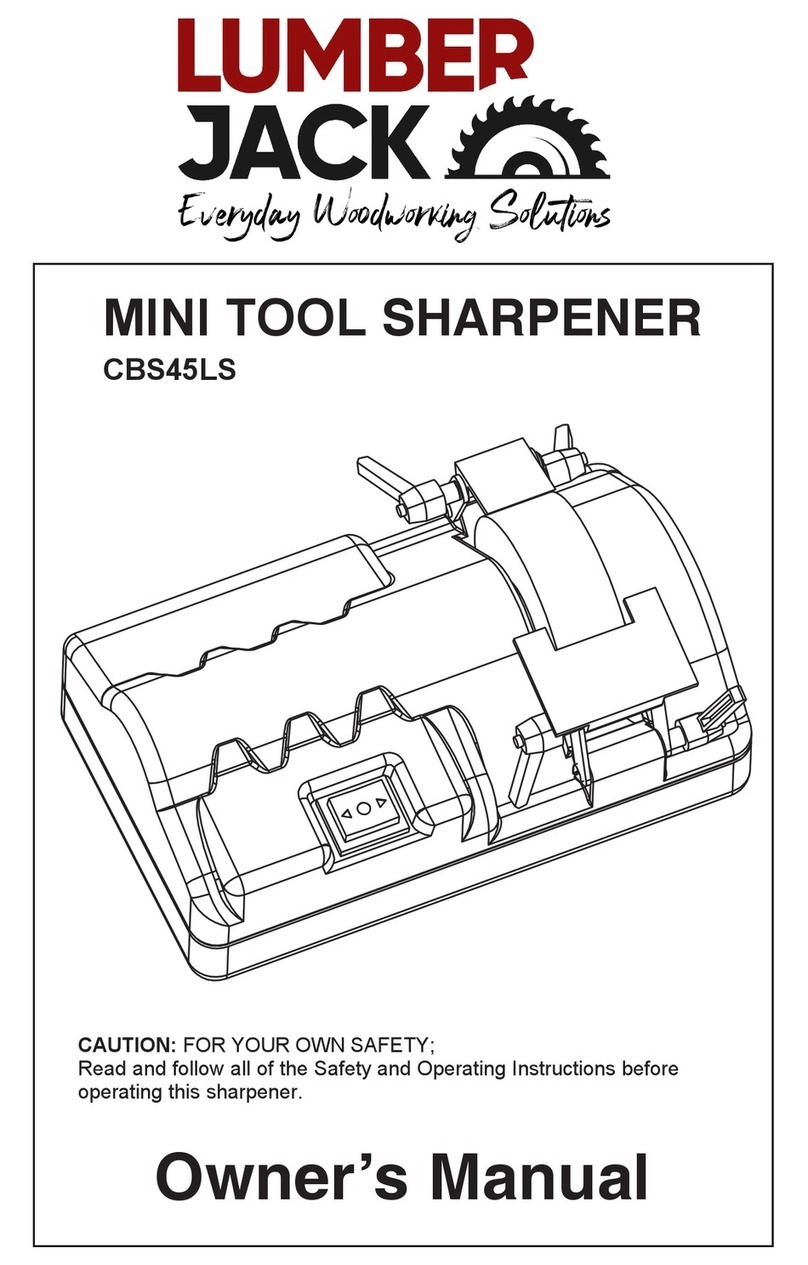
Lumberjack
Lumberjack CBS45LS User manual

Lumberjack
Lumberjack DRT170/120 Installation manual
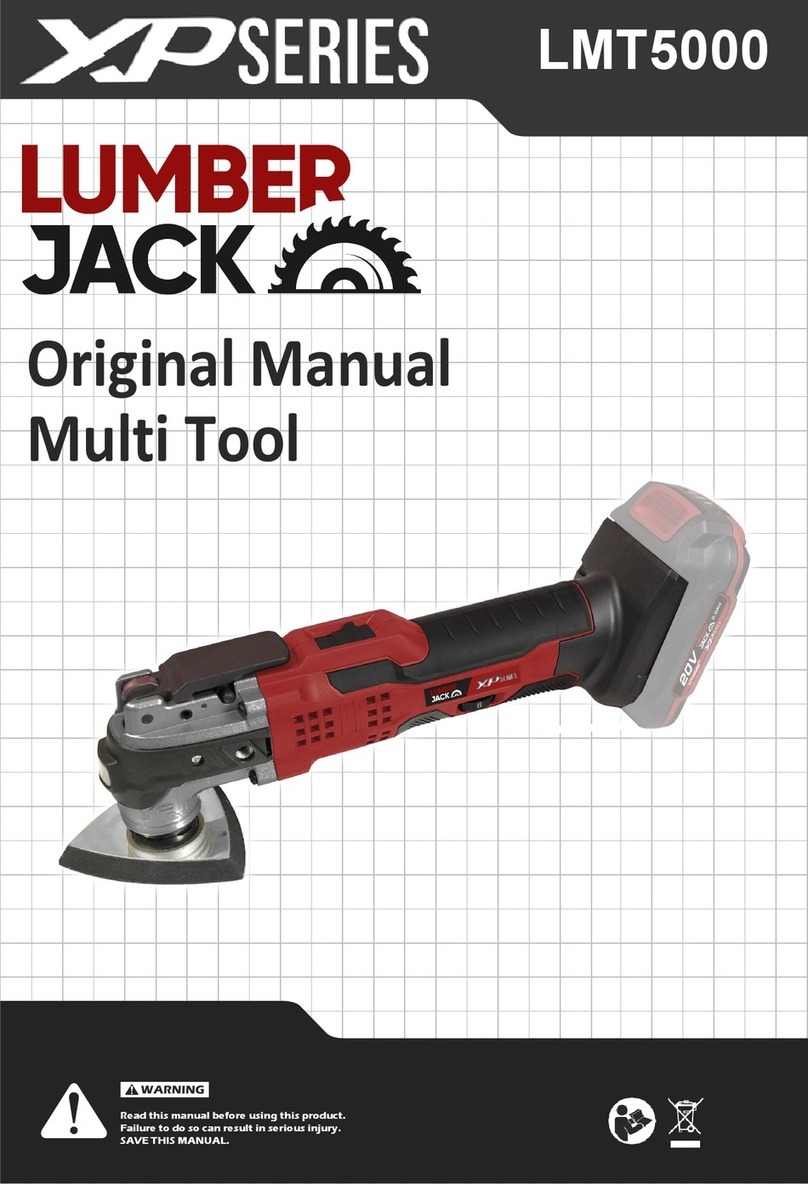
Lumberjack
Lumberjack XP Series Operation instructions