Lutz Easyzon D 100 Guide

(Original Instructions) V1.0 02/20
Easyzon D 100/250 –200/500 g/h
On-site Chlorine Dioxide Generation
Installation, Operation &
Maintenance Instructions
EN

This page is left intentionally blank

Contents Page
Contents
1Notes for the Reader...................................1
1.1 Introduction................................................1
1.2 Explanation of the Signal Words................1
1.3 Explanation of the Warning Signs..............1
1.4 Identification of Warnings ..........................1
1.5 Instruction for Action Identification.............1
1.6 References to Intellectual Property Rights 1
1.7 Details for the Operator .............................1
1.8 Instruction & Training Course Assistance..2
1.9 Example of Training Course Topics...........2
2Safety............................................................4
2.1 Hazards Due to Non-compliance...............4
2.2 Working in a Safety-conscious Manner.....4
2.3 Personal Protective Equipment .................5
2.4 Personnel Qualification..............................5
3Technical Data.............................................6
3.1 System ID ..................................................6
3.2 Dimensions................................................7
3.3 Connections...............................................8
3.4 Electrical Specification...............................8
3.5 Consumption Data.....................................8
3.6 Output Data................................................8
3.7 Precursor Chemical Specification..............8
3.8 Operating Conditions and Limits................8
3.9 Materials in Contact with Media.................9
3.10 Other data..................................................9
4Product Description ................................. 10
4.1 Intended Use........................................... 10
4.2 Design and Function............................... 10
5Delivery...................................................... 11
5.1 Transport & Packaging ........................... 11
5.2 Damages................................................. 11
6Installation................................................. 12
6.1 Components............................................ 12
6.2 Location .................................................. 12
6.3 Cable & Tube Entry System ................... 15
6.4 Hydraulic................................................. 16
6.5 Electrical ................................................. 17
7Commissioning......................................... 21
7.1 Safety Checks......................................... 21
7.2 Initial Start-Up......................................... 21
7.3 Commissioning with Chemicals.............. 23
8Control....................................................... 24
8.1 System Control Elements ....................... 24
8.2 Manual Inhibit.......................................... 24
8.3 Menu Navigation & Hierarchy................. 25
8.4 Display Menu Features & Settings ......... 28
8.5 Service Menu Settings............................ 29
8.6 Factory Settings...................................... 30
9Operation................................................... 31
9.1 Control Function Sequences .................. 31
9.2System Fault States................................ 32
9.3 Shutdown Procedures ............................ 33
10 Maintenance .......................................... 35
10.1 Maintenance Intervals............................. 35
10.2 Maintenance Diagrams........................... 36
10.3 Maintenance Kits .................................... 36
11 Spare Parts............................................ 37
11.1 Recommended Spare Parts ................... 37
12 EC Declaration of Conformity.............. 38
13 Declaration of No Objection ................ 39
14 Warranty Claim...................................... 40
15 Index....................................................... 41

Section 1: Notes for the Reader
P a g e | 1
1 Notes for the Reader
1.1 Introduction
This operating manual provides significant assistance in
the successful and smooth running of the Easyzon D
systems, also referred to, in short, as ‘system’ in the
following instructional text.
The operating manual for the Easyzon must always
be available where the system is located and must be
read and used by every person who is assigned to
working on the system. This includes amongst other
things:
•The installation
•The servicing and repair work
•The maintenance (maintenance, care, repair)
•The transport
1.2 Explanation of the Signal Words
Different signal words in combination with warning signs
are used in this operating manual. Signal words illustrate
the gravity of possible injuries if the risk is ignored.
Signal
Word
Meaning
DANGER!
Refers to imminent danger. Ignoring this
sign may lead to death or the most
serious injuries.
WARNING!
Refers to a potentially hazardous
situation. Failure to follow this
instruction may lead to death or severe
injuries.
CAUTION!
Refers to a potentially hazardous
situation. Failure to follow this
instruction may lead to minor injury or
damage to property.
Note
Refers to a danger which, if ignored,
may lead to risk to the machine and its
function.
1.3 Explanation of the Warning Signs
1.4 Identification of Warnings
Warnings are intended to help personnel recognise risks
and avoid negative consequences.
Warnings are displayed in boxes throughout the manual
as shown below:
Symbol
SIGNAL WORD
Description of danger/hazard/risk
Consequences if ignored
•Bullet points signal a safety precaution to be taken
to eliminate the danger
1.5 Instruction for Action Identification
This is how pre-conditions for action are identified:
✓Pre-condition for action which must be met before
acting.
This is how instructions for action are identified:
•Separate step with no follow-up action.
1. First step in a series of steps.
2. Second step in a series of steps.
✓
Action completed, aim achieved
1.6 References to Intellectual Property
Rights
This operating manual must be treated confidentially.
Only authorised persons should have access to it. It
may only be given to third parties with the written
consent of Lutz Jesco GB Ltd.
All documents are protected in the sense of the copyright
law. It is forbidden to forward on and copy the documents,
even in part, as well as to use and communicate their
contents, insofar as this is not expressly conceded in
writing. Violations are punishable and incur an
obligatory payment of damages. Lutz Jesco GB Ltd
reserves all the rights for the practice of industrial
property rights.
1.7 Details for the Operator
The operating manual is a significant component of the
Easyzon D system. The operator must ensure that the
service personnel learn these guidelines.
The operating manual is to be supplemented by the
operator regarding the operating instructions; national
regulations for Health and Safety at Work and
Environmental Protection, including information on
the responsibilities of supervision and the
observance of operational specifics, e.g.
concerning labour organisations, operational
sequences and appointed personnel.
Besides the operating manual and the
obligatory regulations for Health and Safety at Work
applicable in the country of use, as well as in the
place of use, the recognised specialist technical
regulations for safe and professional work must also be
observed.
Symbol
Meaning
Potential danger zone
Danger of electric shock
Danger of explosion
Danger to health - irritant
Danger of damage to machine or
functional influences

Section 1: Notes for the Reader
P a g e | 2
The operator of the Easyzon D system may not make
any changes, attach fittings or make alterations to
the construction of the system that may impair security,
without the written consent of Lutz Jesco GB Ltd. This
also applies to the installation and setup of safety
devices.
Any replacement parts to be used have to correspond to
the technical requirements specified by Lutz Jesco GB
Ltd. This is always guaranteed in the case of original
spare parts. Only appoint trained or instructed
personnel. Clearly specify the responsibilities of the
personnel for operating, servicing and repairing the
system.
1.8 Instruction & Training Course
Assistance
As a contractor/operator you are obligated to inform
and/or instruct the operating personnel about existing
provisions of law and accident prevention regulations, as
well as existing safety regulations at the plant. In doing
so, the different technical qualifications must be
considered. The operating personnel must have
understood the training and it must be ensured that the
training is adhered to.
Only in this way can you ensure that your personnel work
in a safety conscious and risk aware manner. This should
be controlled on a regular basis. As the
contractor/operator you should therefore obtain
confirmation of each of the employee’s attendance in
writing.
On the following pages, you will find examples of the
training course topics, as well as a main form to copy for
the confirmation of attendance.
If the operating personnel still require further training after
the system has been delivered to the operator,
please contact Lutz Jesco GB Ltd.
1.9 Example of Training Course Topics
For safety:
•COSHH
•Accident prevention regulations
•General safety precautions
•Action to be taken in an emergency
•Safety precautions for operating
•Safety devices
•Definition of symbols and signs
For device operation:
•How to operate the controls
•Elimination of operational disturbances
•Interpretation of fault indications
For maintenance and service instructions:
•Inspection/testing of the system
•Cleaning the system and exchange of
replacement parts

Section 1: Notes for the Reader
P a g e | 3
1.9.1 Confirmation of the Training Instruction
Topic of the training instruction: _______________________________________________________________
Date: _______________________________________________________________________________________
Training instructor: ___________________________________________________________________________
Training instructor’s signature: _________________________________________________________________
No.
Surname
First Name
Signature
1
2
3
4
5
6
7
8
9
10

Section 2: Safety
P a g e | 4
2 Safety
The following warnings are intended to help you to
eliminate the dangers that can arise while handling the
device. Risk prevention measures always apply
regardless of any specific action.
Safety instructions warning against risks arising from
specific activities or situations can be found in the
respective sub-chapters.
DANGER!
Mortal danger from electric shock!
Live parts can inflict fatal injuries.
•Disconnect from the electricity supply before
working on any equipment.
•Secure all devices to prevent it from being
switched on again.
DANGER!
Risk of explosion due to ClO2gas!
The two chemical precursors, hydrochloric acid (HCl)
and sodium chlorite (NaClO2) almost instantly form
large quantities of toxic ClO2gas, which can also
decompose in an explosive manner.
•NEVER mix the two chemical precursors,
hydrochloric acid (HCl) and sodium chlorite
(NaClO2), except within the Easyzon D process.
WARNING!
Risk of contact with toxic ClO2solution!
If system leaks occur, toxic ClO2 solution can escape.
•Under no circumstance must the dosing pump
maximum permissible pressure be exceeded.
•Entire installation must remain leak free in
operation.
CAUTION!
Risk of equipment starting automatically!
Remember the unit and the dosing pump(s) are two
separate pieces of equipment with respect to the
chlorine dioxide treatment/process on site.
•The Easyzon D system operates automatically
when the batch tank is running low.
•The dosing pump(s) will automatically respond
to the treatment/process conditions on site, e.g.
water meter signal input and/or analyser signal
input.
CAUTION!
Damage to the system due to incorrect
maintenance!
Irreversible damage to equipment and treatment
process.
•Adhere to planned maintenance frequency to
system equipment.
2.1 Hazards Due to Non-compliance
Failure to follow the safety instructions leads to:
•Failure of important functions of the device and
of the corresponding system.
•Failure of required maintenance and repair
methods.
•Danger to personnel.
•Danger to the environment .
2.2 Working in a Safety-conscious Manner
Safety rules and regulations not specified in this
manual, which must be adhered to:
•Accident prevention regulations
•Safety and operating provisions
•Environmental protection provisions
•Applicable standards and legislation

Section 2: Safety
P a g e | 5
2.3 Personal Protective Equipment
Based on the dosing medium and precursor
chemicals involved in the Easyzon D process,
appropriate protective equipment must be used to
minimise risk of injury to personnel.
Protective equipment recommended when
performing tasks described in the manual:
•Start Up and Commissioning (see section 7)
•Working on pressurised dosing devices
•Shutdown (see section 9.3)
•Maintenance (see section 10)
•Disposal (see section 9.3.5)
2.3.1 Recommended Protective Equipment
Safety
Sign
Protection
Type
Item
Description
General
protection
Chemical safety
overalls/PVC apron
Hand
protection
PVC/Nitrile disposable
gloves
Foot
protection
PVC safety boots
Eye
protection
Safety goggles
2.4 Personnel Qualification
The device must not be operated by any persons under
the age of 18. Any personnel who work on the device
require certain special knowledge and skills, to ensure
safe and correct operation.
Personnel requirements:
Attendance of all the training courses offered by
the owner
Suitability for the respective activity
Sufficient qualification for the respective activity
Training in handling of the device
Knowledge of safety equipment and the way
this equipment functions
Knowledge of these operating instructions,
particularly of safety instructions and sections
relevant for the activity
Knowledge of fundamental regulations
regarding health and safety and accident
prevention
Minimum qualifications for all personnel:
Training as specialists for unsupervised work
on the device
Sufficient training for working on the device
under the supervision and guidance of a trained
specialist
These operating instructions differentiate between
these user groups:
2.4.1 Specialist Staff
Specialist staff are able, thanks to their professional
training, knowledge and experience as well as
knowledge of the respective provisions, to do the job
allocated to them and recognise and/or eliminate any
possible dangers by themselves.
2.4.2 Trained Electricians
Due to their professional training, knowledge and
experience as well as knowledge of specific standards
and provisions, trained electricians are able to do the
electrical work assigned to them and to recognise and
avoid any potential dangers by themselves.
They are specially trained for their specific working
environment and are familiar with relevant standards and
provisions.
They must comply with the legally binding regulations on
accident prevention.
2.4.3 Trained Persons
Trained persons have received training from the
operator about the tasks they are to perform and about
the dangers stemming from improper behaviour.
Trained persons have attended all trainings offered by
the operator.
2.4.4 Personnel Tasks
In the table below, you can check what personnel
qualifications are the pre-condition for the respective
tasks. Only people with appropriate qualifications are
allowed to perform these tasks!
Personnel
Group
Qualification
Group
Specialist Staff
Technician
•Installation
•Hydraulic installations
•Commissioning
•Taking out of operation
•Fault rectification
•Maintenance
•Repairs
•Disposal
Trained
Electricians
•Electrical installation
•Rectifying electrical faults
•Electrical repairs
Trained Persons
•Control
•Storage
•Transportation

Section 3: Technical Data
P a g e | 6
3 Technical Data
3.1 System ID
3.1.1 Match-code System Build Information
3.1.2 Rating Plate
The rating plate contains information on the safety and
functional method of the product. The rating plate must
be kept legible for the duration of the service life of the
product.
Generator capacity
LJED100g/h chlorine dioxide generator at 2000mg/l ClO₂solution
LJED200g/h chlorine dioxide generator at 2000mg/l ClO₂solution
LJED250g/h chlorine dioxide generator at 2000mg/l ClO₂solution
LJED500g/h chlorine dioxide generator at 2000mg/l ClO₂solution
Cover
C0
Grey cover hood
Power Supply
V1
100-240Vac 50/60Hz
Communication Interface
R0
Without comms
R1
RS485 Modbus RTU
C0
V1
R0
Match code order example
No.
Description
1
Product name
2
Nominal size (g/hr)
3
Label showing conformity with European
directives
4
Supply Voltage
5
AC Frequency
6
Date of manufacture
7
Serial Number
8
Power consumption
9
System part number

Section 3: Technical Data
P a g e | 7
3.2 Dimensions
3.2.1 Easyzon D
Skid dimensions:

Section 3: Technical Data
P a g e | 8
3.3 Connections
3.3.1 Hydraulic
3.3.2 Electrical
3.4 Electrical Specification
3.5 Consumption Data
3.6 Output Data
3.7 Precursor Chemical Specification
In accordance with the Biocidal Products Regulation
(BPR), Regulation (EU) 528/2012, the member states of
the European Union may only use precursors for the
generation of biocidal active substances produced “in
situ” which are authorised under Article 95 of the
regulation. These precursors must be sourced from a
manufacturer or supplier listed in accordance with Article
95 of the BPR. Please ask your supplier to confirm
conformity with the biocide ordinance (certificate or
Letter of Access).
Note:
•Output data is determined by the precursor
quality & concentration. Tolerance is
permissible up to ±10%, however this may affect
the performance specified.
3.8 Operating Conditions and Limits
Connection
Description
Cold water dilution
½” BSPf
Precursor chemical
4mmID x 6mmOD tube
compression
Connection
Description
Mains power input
M20 cable gland
Signal input/output
M12/16 cable gland
Chemical empty switch
input
M12 connector - A code
Description [all models]
Power supply
1Ø, 100-240VAC
Power rating
20W (excluding auxiliary
equipment)
Aux output
1Ø, 100-240VAC, 5A
Enclosure class of
electronic panel
IP64
General system
protection class
IP64
Model:
Low strength
High strength
100
200
250
500
Nominal water
consumption (l/h)
45
90
120
240
Precursor
consumption ratio
1:1
Precursor
consumption, each
(L/h)
2.5
5
2.5
5
Model:
Low strength
High strength
100
200
250
500
Generation capacity
(g/h ClO2)
100
200
250
500
Generation capacity
(L/h)
50
100
125
250
Solution concentration
(mg/L ClO2)
2000
Product tank volume
(L)
80
Model:
100
200
250
500
9.0% HCl (EN939)
✓
✓
7.5% NaClO2 (EN938)
✓
✓
≈15.0% HCl (EN939)
✓
✓
≈14.0% NaClO2 (EN938)
✓
✓
Model:
100
250
200
500
Water supply inlet
pressure (MPa)
0.2-1.6 (Min-Max)
Reduced pressure
value (MPa)
0.05 –0.1
Dilution water
temperature (oC)
5-20
Precursor temperature
(oC)
10-35
Ambient temperature
(oC)
5-35
Dilution Water Quality
Potable

Section 3: Technical Data
P a g e | 9
3.9 Materials in Contact with Media
3.9.1 Cold Water Feed
3.9.2 Chemical Precursor Feed
3.9.3 Dilution Water (Generated Solution)
3.9.4 Dosing Pump(s) Connected to Easyzon D
Dosing pump liquid end assembly material specification
must be chemically resistant to a ClO2solution
concentration ≥2000mg/l.
See below table for asuitable pump liquid end
specification. Consult your equipment supplier for further
guidance.
3.9.5 Precursor Suction Lance Assembly
Any chemical drum/tank suction line assembly
connected to the relevant Easyzon D chemical
precursor tube connection, must be chemically
resistant to the precursor as detailed in section 3.9.
See below table for a suitable suction line assembly
specification. Consult your equipment supplier
for further guidance.
Description
Material
Foot valve housing
PVC / PVDF
Foot valve ball
Ceramic / PTFE
Foot valve seat
PVDF / FPM / PTFE /
Ceramic
Foot valve outer seal/gasket
FPM / PTFE
3.10 Other data
Description
Material
In-line strainer
PP
Flow sensor
PVDF
Solenoid valve
PVDF/FPM
Reactor vessel
PVC
Tubing
PTFE (opaque/violet)
Tube compression fittings
PVDF/FPM
Description
Material
Reactor vessel
PVDF
Venturi device
PVDF
Batch tank
MDPE
Tubing
PTFE (violet)
Tube compression fittings
PVDF/FPM
Tank level switch
PVDF
Description
Material
Pressure regulator
Brass/NBR/SS
Solenoid valve
Brass/FPM/SS
Flow sensor
PVDF
Tubing
LDPE (blue)
Push-fit fittings
PP/SS/EPDM
Description
Material
Pump head
PVC / PVDF
Diaphragm (membrane)
PTFE
Suction/discharge valve
housing
PVC / PVDF
Suction/discharge valve
ball
Ceramic / PTFE
Suction/discharge valve
seat
PVDF / FPM / PTFE /
Ceramic
Suction/discharge valve
housing outer seal/gasket
FPM / PTFE
Description
All models
Empty weight (kg)

Section 4: Product Description
P a g e | 10
4 Product Description
4.1 Intended Use
The Easyzon D on-site chlorine dioxide generation
system is intended for the following purpose: Automatic
generation of a <0.2% diluted chlorine dioxide solution
using sodium chlorite, hydrochloric acid and cool water.
The resulting solution can be used as a disinfection
agent for a wide range of applications.
4.2 Design and Function
The Easyzon D is a fully automated batch skid
system, with the output ranging from 100 to 500g/hr
of ClO2. The system can be configured with a
standalone reaction vessel to produce 100g/hr, or two
vessels in series to produce 200g/hr. Higher
concentration precursors can be used to gain 250g/hr
and 500g/hr respectively.
The system uses a plastic cabinet to mount its
instrumentation and house its reaction vessel/’s, these
are protected by a cover which can be secured shut
by a padlock on a toggle latch.
Chemical precursors are safely drawn into the reaction
vessel/’s [19]at a 1:1 ratio from a drum/tank by the
means of a vacuum created by a venturi [12]. Each
reactant is precisely measured and controlled via
individual flowmeters [6 & 7] and solenoid valves[8 &
9], which allow the reaction toproduce a ≈2 wt% ClO2
solution (Or ≈5 wt% ClO2with higher strength
precursors) . A predefined cycle time enables the
system to batch the necessary number of times to
generate the desired g/hr. After a reaction time of 15
minutes the product enters a level-controlled product
tank [17]. Any excess gas created in the reaction
process passes through the carbon filter [21] and into
the atmosphere. This process continues until the ‘Tank
Full’ level is reached, where the system waits for an
adjustable set time before restarting generation (see
section 8.5.3).
Description
1
Control panel
2
Dilution water solenoid
3
Dilution water flow meter
4
Inline strainer - chlorite (4x6mmOD Connection)
5
Inline strainer - acid (4x6mmOD Connection)
6
Acid flowmeter
7
Chlorite flow meter
8
Acid solenoid valve
9
Chlorite solenoid valve
10
Chlorite drum/tank empty connection
11
Acid drum/tank empty connection
12
Venturi
13
Reactor –Product outlet
14
Dilution water line
15
Product tank level switch
16
Non-return valve
17
Product tank
18
Product tank inlet
19
Reaction vessel
20
Reactor –Chemical inlet
21
Activated carbon filter –Gas scrubber
22
Temperature sensor
23
Diluted chlorine line

Section 5: Delivery
P a g e | 11
5 Delivery
CAUTION!
Damage can occur during incorrect
transportation and delivery procedures
Irreversible damage can occur to the system and
warranty may be affected.
•Use pallet truck cut outs on the Easyzon D to
move it into position.
5.1 Transport & Packaging
Please inspect packaging for damage upon delivery.
Unpack with care and check that all standard contents
from the list below are present.
5.2 Damages
If your package has incurred damages due to improper
transportation and handling, inform your supplier and
follow returns procedure.
Standard Contents
Net
Weight
(kg)
Package
Dimensions
(mm)
Easyzon D
Installation & Operation
Manual
Cable gland insert kit
Water purge suction kit

Section 6: Installation
P a g e | 12
6 Installation
6.1 Components
The standard components supplied with the Eayzon D
system that are required to be installed are as follows:
•Easyzon D Skid
6.2 Location
6.2.1 Requirements
Certain location conditions are to be met prior to
installation, to ensure safe and optimal operation of the
system.
Location conditions:
✓There is access to a permanent water supply
for connection to the Easyzon D
✓The water supply is of a constant pressure of 2
bar or above with minimal fluctuations
✓There is access to the main water line for
product injection
✓Temperature, humidity and water quality are
under the specified limits (seesection 3.8)
✓There is access to a power supply
✓There is a floor drain for flushing away of
chemicals if spillage was to occur
✓There is adequate ventilation and lighting
✓It is safe from unauthorised access
✓It meets all local regulations including fire safety
and accident prevention laws.
✓The floor is made of concrete and is level
✓There is sufficient protection from frost
✓Storage of chemicals has been approved and
there are adequate facilities to do so.
✓Chemical tanks are positioned so suction lines
are <50m.
DANGER
Incorrect installation can compromise safety!
This can expose personnel and the surrounding
environment to hazards.
•Adhere to safety precautions and instructions for
correct installation in this manual.
•Only trained/specialist personnel may perform
installation work/maintenance (see section 2.4)
•It is recommended that stickers/labels/tags are
to be used to notify users of any potential
hazards.

Section 6: Installation
P a g e | 13
6.2.2 Installation Example 1
Standard installation, see 6.2.1 for environment
requirements.
Installation notes:
•Max length of chemical suction line: 50.00m at
4mmID
•Asteadypermanentpressureisrequiredforthe
unit to operate most efficiently, if there isn’t one
it is recommended that a booster
set, or pressure vessel is installed.
•PRV on the skid should always be set between
0.6 –1.0 bar (when the Easyzon D is batching)
(P&ID legend is on the next page)

Section 6: Installation
P a g e | 14

Section 6: Installation
P a g e | 15
6.3 Cable & Tube Entry System
The Easyzon D uses an entry system located on the
right-hand side of the cabinet for routing cables into
the control panel.
New cable routing steps:
1. Insert the cable(s) through the preferred inlay
section [2] of the entry system that is fitted
inside the frame [1].
2. Remove trunking covers and route cable/s
through each section and hole in the cabinet
door.
3. Choose a suitable gland on the control panel to
run the cable/sthrough, use the electrical
diagram to wire in to the correct terminals on
the Easyzon D PCB.
4. Select a seal insert from the kit provided with
the correct number of holes and diameter for
the cable/s(see section 6.3.1). Spread open
the insert [3] and place it around the cable/son
the inside of the cabinet, close to the entry
system.
5. Push the seal insert all the way into the inlay
section.
✓Cable routing complete
6.3.1 Seal Insert Selection
An array of varying diameter seal inserts is supplied
with the Easyzon D, ready to be used with a range of
tubes and cables. Additional inserts can be purchased
if required, see section 11.4 for spares.
Description
1
Entry frame
2
6 –way frame inlay
3
Seal insert

Section 6: Installation
P a g e | 16
6.4 Hydraulic
6.4.1 Water Supply
If the water supplied to the device is not of aconstant
pressure of at least 2.0 bar then it is advised that a break
tank and booster set is installed. This prevents any
possible fault situations from occurring with the
Easyzon D due to low mains/supply water pressure.
When connected to a UK mains water supply the
Easyzon D must be fitted with a fluid category
3 back-flow prevention device (Type EC or ED)
which conforms to local water supply regulations and
plumbing codes. Installation Steps:
1. Connect your water supply to the ½”BSPf
connection which is provided on the left-hand
side of the Easyzon D skid.
Note:
•The Pressure regulating valve should be set
between 0.6-1.0 bar when the unit is batching
(see commissioning section 7), this is vital to the
workings of the system.
6.4.2 Dosing Pumps
Any pump which is suitable for your application and also
for dosing 0.2%wt ClO2solution can be used.
Installation steps:
1.Fit your pumps suction set into the Easyzon product
tank making sure there is an airtight seal.
✓Dosing pump installation complete
6.4.3 Suction Lances
Installation Steps:
1. Refer to the suction lances manual for
installation guidance.
2. Check empty level switch [5] is into the N.C
orientation ( - N.C symbol is on the top face
of the float).
Description
1
G3/8”BSPf to G5/8”BSPm Adapter
2
Adjustable rigid suction lance
3
Tank connection
4
Pre-empty level switch - not active
5
Empty level switch (N.C)
6
Strainer

Section 6: Installation
P a g e | 17
6.5 Electrical
DANGER!
Mortal danger from electric shock!
Live parts can inflict fatal injuries.
•Disconnect from the electricity supply before
working on any equipment.
•Secure all devices to prevent it from being
switched on again.
•Perform mains connection in accordance with
local regulations.
CAUTION!
Damage to the system can occur if wired
incorrectly.
•Isolate power to the Easyzon D before
performing any electrical work.
•Study the electrical diagrams and instructions
provided before beginning work.
•Only trained/specialist personnel may perform
electrical work/maintenance (seesection 2.4).
6.5.1 PCB Terminal Connections
Connections refer to electrical schematics, section 6.5.2
Terminal
I.D.
Terminal
Description
28
+
Not active
29
+
+5VDC Output
30
N.C
Ext Alarm N/C
N.C Ext Alarm
31
-
0V
Digital Inputs
32
+
Site Flowmeter
33
-
0V
34
+
Emergency Stop
35
-
0V
36
+
Chlorite Drum Empty
37
-
0V
38
+
Chemical Bund Switch
39
-
0V
40
+
Acid Drum Empty
41
-
0V
42
+
Batch Tank Run/Stop
43
-
0V
44
+
Not Active
45
-
0V
Digital Inputs
46
+
Batch Tank Low
47
-
0V
48
+
Batch Tank High
49
-
0V
50
*
Spare
51
+
+24Vdc - Acid
Chemical
Solenoids -
Control Output
52
-
0V
53
+
+24Vdc - Chlorite
54
-
0V
55
+
+12VDC
LED
Supply
56
+
Green
57
+
Blue
58
+
Red
59
-
0V
60
+
Chlorite Flowmeter
Signal Inputs
61
+
Acid Flowmeter
62
+
Not Active
Not Active
63
+
Not Active
64
A
TIA-485
Communication
connection
65
B
66
+
Auxiliary Alarm
Digital Inputs
67
-
0V
68
+
Remote Inhibit
69
-
0V
Terminal
I.D.
Terminal
Description
1
L
Mains Out
100-240VAC
2
N
3
E
4
L
Mains In
5
N
6
E
7
N.C
Alarm 2 Relay
Volt Free Alarm
Outputs
(10A max)
8
C
9
N.O
10
N.O
Alarm 1 Relay
11
C
12
N.C
13
C
Solenoid Run Relay
Dilution Water
Solenoid
14
N.O
15
+
+24Vdc
DC Output for
external alarm
(Terminal 30)
16
+
Not active
Not Active
17
-
0V
18
+
Not active
19
-
0V
20
+
Not active
21
+
+24Vdc Output
22
-
0V
23
-
0V
Dilution Water
Flow Meter
24
+
FM Pulse Signal
25
+
+5Vdc Output
26
+
Not active
Not Active
27
-
0V
This manual suits for next models
1
Table of contents
Popular Portable Generator manuals by other brands
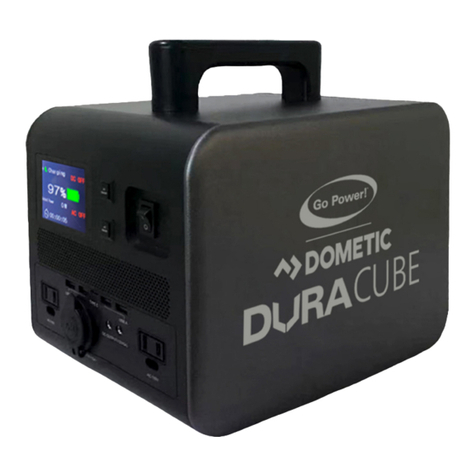
Dometic
Dometic GO POWER DURACUBE-500 user manual
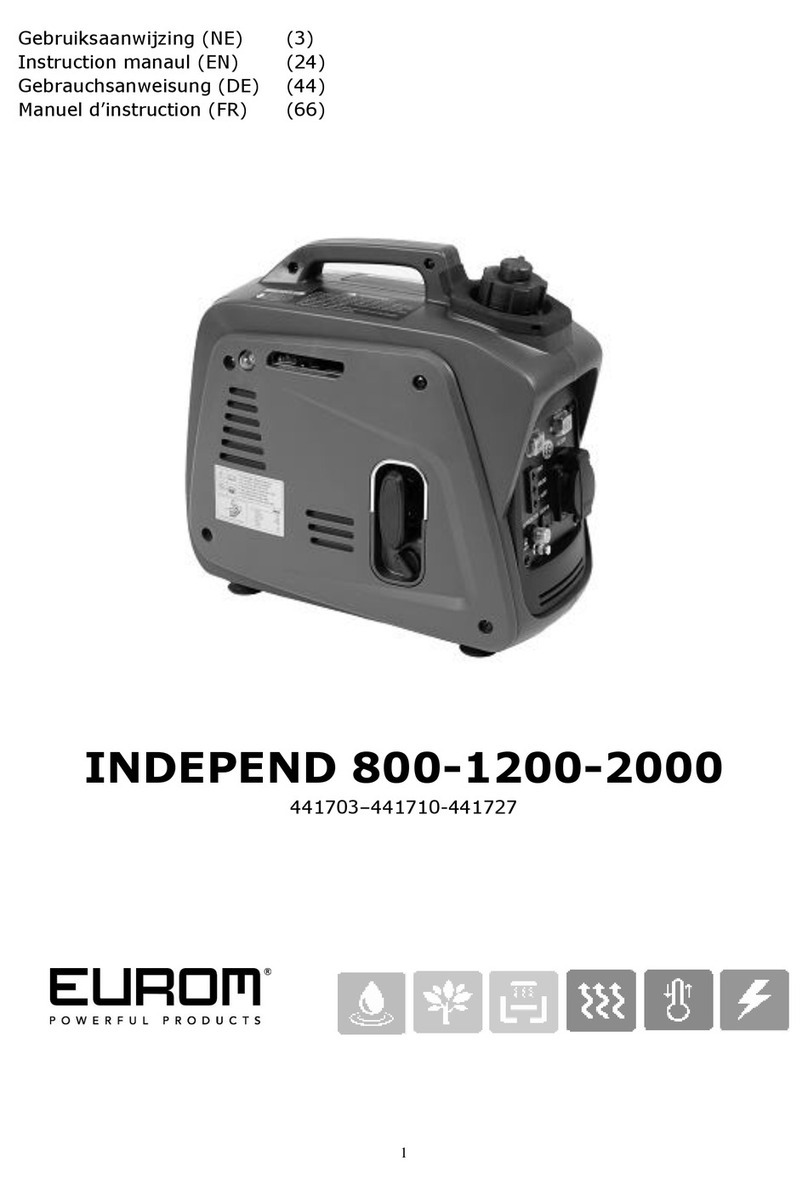
EUROM
EUROM INDEPEND 800 instruction manual

Briggs & Stratton
Briggs & Stratton Vanguard 580000 Operator's manual
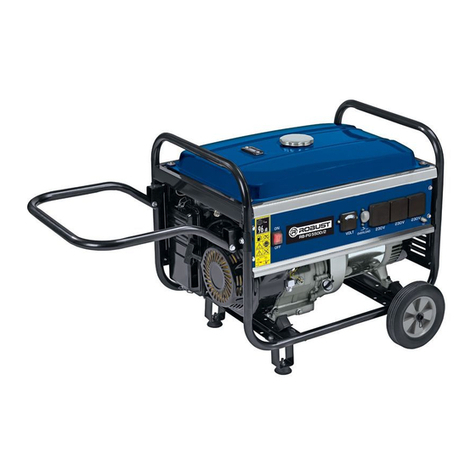
Robust
Robust RB-PG 5500/2 Original operating instructions
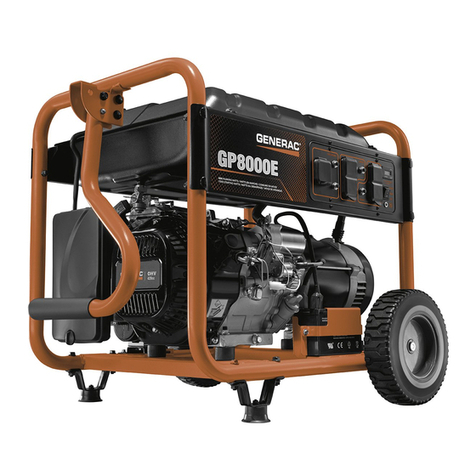
Generac Power Systems
Generac Power Systems 0065141C owner's manual

Arman
Arman PRE4000K owner's manual
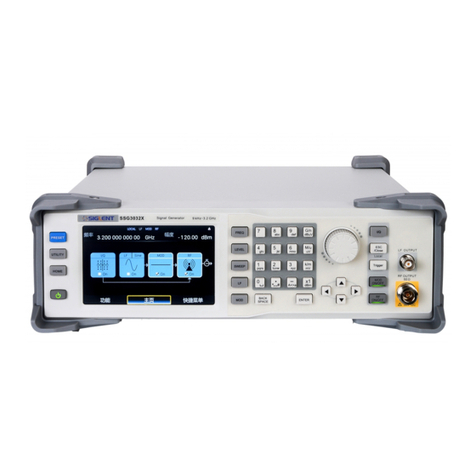
SIGLENT
SIGLENT SSG3032X user manual
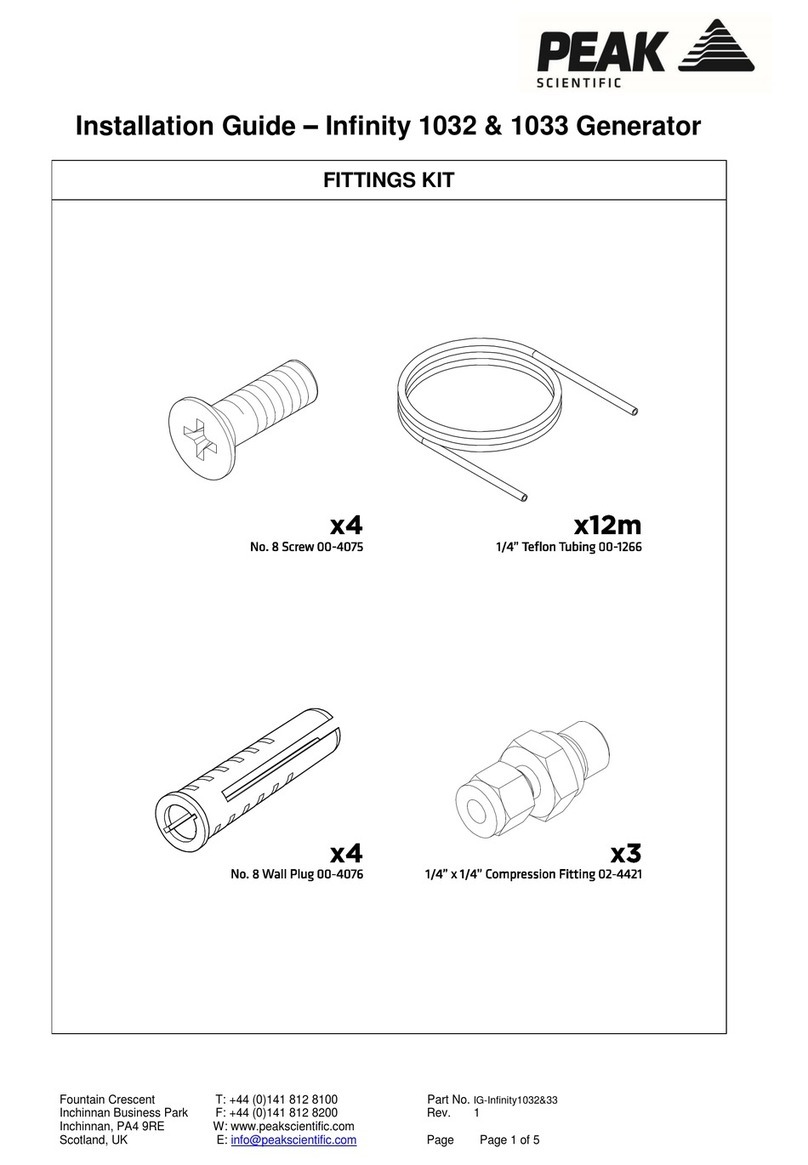
Peak Scientific
Peak Scientific Infinity 1032 installation guide

Chicago Electric
Chicago Electric 65309 Set up, operating, and servicing instructions
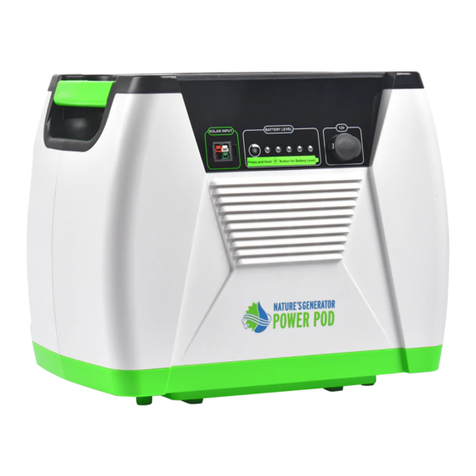
Nature's Generator
Nature's Generator Power Pod user manual
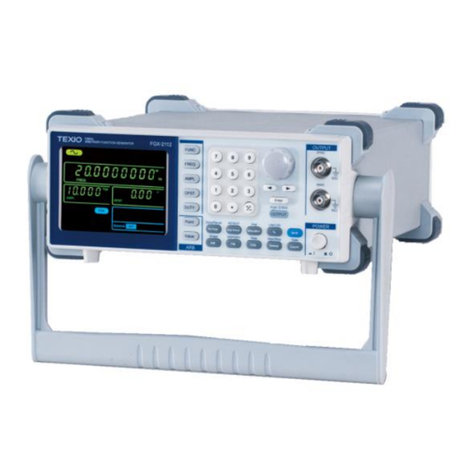
TEXIO
TEXIO FGX-2005 instruction manual
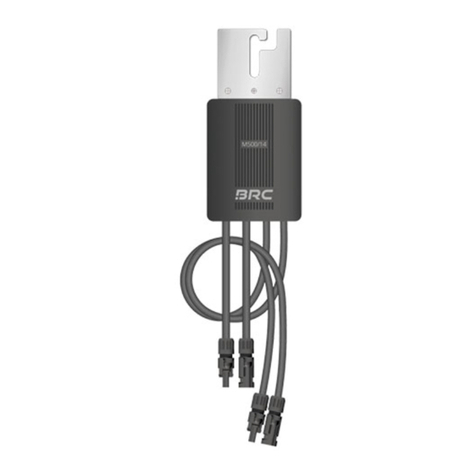
BRC
BRC M500/14 instruction manual