Magus BASIKA rho NS 2 Assembly instructions

150331_IOM_GS_PE-LMD_BASIKA_rho_gb 1 von 30
BASIKA rho
Grease Separator
with integrated sludge trap made of Polyethylen (PE-LMD)
in oval design
NS 2 / 4 / 7,5 / 10
Indoor installation in rooms protected
from frost
Installation,
Operating and
Maintenance Instructions
Subject to modifications in terms of technical further development!

150331_IOM_GS_PE-LMD_BASIKA_rho_gb 2 von 30
Table of Contents
Page
1. General Advice 4
1.1 Purpose of Use 4
1.2 Technical Data 5
2. Safety 5
2.1 Identification of Advice in the Operating Manual 5
2.2 Staff Qualification 6
2.3 Risks if Safety Instructions are Ignored 6
2.4 Safety-Conscious Working 6
2.5 Safety Instructions for the Operator 6
2.6 Safety Instructions for Maintenance, Inspection and Assembly Work 6
2.7 Modifications and Manufacture of Spare Parts on One’s Own Authority 7
2.8 Illegal Operating Methods 7
3. Transportation 7
4. Description of the grease separators 7
4.1 Design Alternatives 8
4.1.1 Manual semi-automatic disposal device 8
4.1.2 Fully-automatic disposal device 8
5. Set-up and Installation 8
5.1 Choice of Set-up Area 8
5.2 Preparation of Set-up Area 9
6. Installation 9
6.1 Sanitary Installation 9
6.2 Electric Installation 10
7. Commissioning 11

150331_IOM_GS_PE-LMD_BASIKA_rho_gb 3 von 30
8. Operation 12
8.1 Work bench signalling unit "Maximum grease storage capacity reached" 13
8.2 Disposal 13
8.2.1 Manual semi-automatic disposal device 13
8.2.2 Fully-automatic disposal device 15
8.3 Default settings for LOGO! 17 - 23
9. Maintenance 24 - 25
10. Faults during Operation 26
Declaration of performance 28 - 29
Declaration of Conformity 30
Subject to modifications in terms of technical further development!

150331_IOM_GS_PE-LMD_BASIKA_rho_gb 4 von 30
1. General Advice
(excerpt DIN EN 1825-2)
•Only waste water containing fat and grease of plant and animal origin may enter the
grease separator.
•The adequate connecting height of the existing drains needs to be checked.
•The materials of the inlet and outlet pipes need to correspond with DIN EN 12056 and
must be resistant against the waste water according to DIN EN 1825-2. The required
cross section of the pipes which depends on the nominal size of the grease separator
needs to be observed.
•The effluent needs to enter the grease separator in gravity fall. If the rest water level is
below the backflow level (see EN 752-2) a lifting plant needs to be installed.
•In order to avoid grease settlement in the inlet pipes they need to be laid with a slope
of at least 2% (1 : 50) and they should be easy to clean.
Technical regulations to be observed:
•DIN 1986 draining plants for buildings and estates, section 30, 100
•DIN EN 752 draining systems outside of buildings, section 1-7
•DIN EN 1825 grease separators for fatty matters, section 2
•draft DIN 4040, section 100
•DIN EN 12056 draining plants by means of gravity in buildings, section 1-5
•DIN 1988 technical rules for tap water installation
WARNING
The valid standards for the installation and connection to the draining system need to be
observed.
1.1 Purpose of Use
Grease separators separate fatty matters and grease of vegetable and animal origin from
waste water by means of gravity.
The following liquids may never enter grease separators:
•foul water („dirty water“)
•rain water
•waste water containing light liquids, e.g. fatty matters and grease of mineral origin

150331_IOM_GS_PE-LMD_BASIKA_rho_gb 5 von 30
1.2 Technical Data
(see data sheet for installation, operating and maintenance instructions)
2. Safety
(according to the VDMA-sheet 24292)
These operating instructions include basic advice to be followed during installation,
operation and maintenance of the plant. Therefore, it is essential that the technician and
operator read the operating instructions prior to installation and commissioning. The
operating instructions must always be available at the installation site of the system.
Not only that the general safety advice mentioned under the headline „safety“ need to be
followed, but all other special safety advice given under other headlines as well.
2.1 Identification of Advice in the Operating Manual
All safety advice given in this operating manual which may be hazardous if being ignored
are identified with a general risk symbol, safety symbol according to DIN 4844-W 9.
Warnings because of electric voltage are identified with a safety symbol according to DIN
4844-W 8.
WARNING stands whenever the device and its function is at risk if the safety
instructions are ignored.
Any advice, e.g.
•markings
•lables
attached to the plant must always be readable and strictly observed.

150331_IOM_GS_PE-LMD_BASIKA_rho_gb 6 von 30
2.2 Staff Qualification
Staff responsible for operation, maintenance and commissioning of the plant needs to be
qualified accordingly and must be familiar with the installation, operating and maintenance
instructions, especially with the instructions regarding occupational safety and prevention
of accidents.
2.3 Risks if Safety Instructions are Ignored
If safety instructions are ignored people as well as the environment or the plant can be at
risk. If safety instructions are ignored this may occur the loss of claim for damages.
If safety instructions are ignored this may cause e.g. the following risks:
•essential functions of the plant may fail
•people are in danger because of electric, mechanical and chemical impacts
•the environment is endangered because of leakage of hazardous substances
2.4 Safety-conscious Working
The safety advice, the existing national prescriptions regarding prevention of accidents as
well as the operator’s internal occupational, operating and safety prescriptions need to be
observed.
2.5 Safety Instructions for the Operator
Any risks by electric energy need to be avoided (for details see e.g. prescriptions of the
VDE and the local electric utility).
2.6 Safety Instructions for Maintenance, Inspection and
Assembly Work
The operator needs to make sure that only authorized and qualified personnel who is
familiar with the operating manual executes the maintenance, inspection and assembly
work.
The plant needs to be switched “OFF” and secured against restart whenever any work is
being conducted on the plant.

150331_IOM_GS_PE-LMD_BASIKA_rho_gb 7 von 30
As soon as the work has been finished all safety and protective devices need to be
reactivated.
Prior to commissioning the plant again, please observe the advice mentioned under the
headline “Commissioning”.
2.7 Modification and Manufacture of Spare Parts on One’s Own
Authority
Any modifications to the plant require the manufacturer’s approval. Safety is only
guaranteed if genuine spare parts and accessories approved by the manufacturer are
used. If different parts are used the liability may become void.
2.8 Illegal Operating Methods
The perfect performance of the supplied plant is guaranteed only if the plant is used as
intended according to section 1 – General Advice – of the operating manual.
The limit values indicated in the data sheet may not be exceeded at all.
This installation and operating manual does not suspend any general prescriptions which
are not mentioned hereunder!
VDMA = Association of German Engineering and Plant Construction e.V.
3 Transportation
Do not throw the grease separators during transportation!
4. Description of the Grease Separators
Grease separators consist of a water- and odour-proof container (polyethylene HDPE)
according to EN 1825-1 and DIN 4040-100, either in oval shape, for indoor installation in
rooms protected from frost. Equipped with integrated sludge trap or sludge trap connected
in series, volume 100 x NS in litres. The container lids are water- and odour tight by means
of O-seal ring and clamping rings. Equipped with inlet and outlet pipe connection DN 100
for nominal size NS 2 and 4, DN 150 for nominal size NS 7,5 and 10.

150331_IOM_GS_PE-LMD_BASIKA_rho_gb 8 von 30
Depending on the construction, as an option and for easy cleaning purposes the
separators are either equipped with a suction pipe leaving the container at the bottom and
leading to the top (up to the container upper rim) and a flange PN 10 at the end. In addition
the grease separators are equipped with a screw connection to connect a filling unit if
required later-on.
4.1 Design Alternatives
4.1.1 Manual semi-automatic disposal device
The separator can be supplied with the following options: inspection window; agitator(s)
allowing that the hardened grease layers as well as the settled sludge become a
homogeneous slurry which is easy to be sucked off from the disposal car without opening
the lid; filling unit, solenoid valve to refill the separator, signalling unit “max. grease storage
capacity reached”.
4.1.2 Fully Automatic Disposal Device
Equipped with inspection window, agitator(s), filling unit with solenoid valve to refill the
separator automatically, pressure sensor to monitor the level and disposal pump.
5. Set- up and Installation
An authorized and competent company has to do the installation.
Any national prescriptions regarding prevention of accidents as well as existing
internal occupational and safety prescriptions need to be followed.
First of all check whether all parts of the plant were supplied and whether these are
in perfect condition (never assemble any defective parts).
5.1 Choice of Set-up Area
•Separators should be set-up close to the area where the waste water is produced. In
addition the suction connection for disposal vehicles should be easily accessible
(excerpt DIN EN 1825-2).

150331_IOM_GS_PE-LMD_BASIKA_rho_gb 9 von 30
5.2 Preparation of Set-up Area
Prior to the set-up of the grease separator please check the following conditions :
•The room is protected from frost
•The room can be illuminated
•The room allows self-ventilation
•The surface of the floor is protected and has a drain
•The floor must be even and have a good bearing capacity [observe stability (floor
loading)] and needs to provide sufficient space for the erection of the plant.
•The area must be big enough to allow for operation, maintenance and inspection of the
separator
•Water supply for filling and cleaning purposes as well as the respective electric
installation need to be available.
6. Installation
6.1 Sanitary Installation
•The grease separator needs to be set-up horizontally and in flow direction. The outlet
suction connection points to the front.
For grease separators in oval shape which are supplied on disposal pallets with
suction pipe first of all the disposal pallet is erected horizontally and in flow direction
(the outlet suction connection points to the front).
Then the grease separator with the connection piece at the bottom of the container is
placed on the pallet.
Finally the connecting sleeve of the suction pipe is attached to the connection piece
and screwed to the disposal pallet (see attached mounting sketch).
Please ensure the stability of the plant.
For plants having horizontal flanges it is essential to make sure that the connections
between the container components (see marking), the O-ring seal and the clamping
ring / screwed flange are perfect (also see attached mounting sketch).
•Prior to connecting all pipes the container is to be filled with water in order to ensure
that the container is fixed correctly and a leakage test can be run.
•Inlet and outlet pipes need to be laid according to DIN EN 752 and DIN EN 12 056 or
DIN EN 1610 and DIN EN 1825-2 respectively, as well as DIN EN 4040 section 100.
•We recommend to connect the vent pipe DN 100 of the grease separator to a separate
vent pipe (constantly rising) which leads via the roof.

150331_IOM_GS_PE-LMD_BASIKA_rho_gb 10 von 30
ADVICE:
All lines need to be stress-free and equipped with isolated distance clamps. Loads of pipes
(also if made of plastic) and fittings must be supported at site!
•If a tap water system is used to fill the container the connection to ensure filling in
gravity fall needs to comply with DIN 1988-4. If a Basika filling unit is used a stop valve
and a throttle which has to be pre-adjusted needs to be placed in front of the filling unit.
6.2 Electric Installation
When the sanitary installation has been finished an electrician will connect the electric line
(if available) in the control panel.
Only a competent electrician may do the electric connection.
Supply line: Three phase current = 400 V, 3 phases, N, PE, 50 cycles
Required Fuse: (see data sheet for installation, operation and maintenance)
Prior to commissioning an expert needs to make sure that one of the necessary electric
protective measures is available. Grounding, protective multiple earthing, differential
current-switching, etc. need to comply with the prescriptions of the local electric utility
(EVU) and operate perfectly when the electrician runs the function test.
WARNING!
Cross section and voltage drop of the power line need to comply with the VDE
prescriptions.
The voltage mentioned in the electric documentation needs to comply with the existing
power line. The electrician needs to connect the feeder as well as the cables of the
individual devices to the terminals of the control panel according to the wiring diagram (in
the control panel) of the individual control panel.
The feeder needs to be protected by a sufficiently dimensioned and slow-blowing fuse
(according to the nominal power of the total wattage).
ADVICE
The motor overload switches in the control panel are pre-adjusted correctly. Please ask
the responsible electrician at your site.

150331_IOM_GS_PE-LMD_BASIKA_rho_gb 11 von 30
When the electric connection has been finished please check the phase sequence (turning
to the right) of the power line prior to commissioning. If the phase sequence of the power
line is not correct two phases of the power line need to be swapped.
Only a competent electrician may swap the two phases of the power line under stress-free
conditions.
7. Commissioning
Prior to commissioning the grease separator is to be filled with water.
•Main switch at the control panel is turned to “ OFF“ and secured against restart by
means of a padlock.
•Check whether the cover of the grease separator fits and is closed perfectly by means
of the snap buckles (clamping rings).
•Check whole plant for tightness (especially the flanges when the plant was
disassembled at site). Condition: Grease separator is filled with fresh water until it
drains.
•Check whether the electric connection was made according to the valid prescriptions.
•If necessary have the power supply be added-on from the sub distribution to the
control panel of the plant.
•Open the control panel of the grease separator and check the phase sequence (must
be turning to the right) at the feeder.
•Are all power supply leads of the devices connected correctly?
•Turn main switch at the control panel to position “ON“.

150331_IOM_GS_PE-LMD_BASIKA_rho_gb 12 von 30
•Check sense of rotation and electric switching functions of all devices.
ADVICE
When the preparation work at site has been finished our after-sales service can do the
commissioning which will be charged separately.
Please arrange a date for commissioning at least 2 weeks in advance.
After-Sales Service: Drecker Industrie Electronic GmbH
Westfalenweg 279
42111 Wuppertal, Germany
Tel.: +49 (0) 202-704090
Fax: +49 (0) 202-704060
e-mail: DreckerGmbH@aol.com
8. Operation
•Detergents, including washing-up powders and liquids may neither contain nor release
chlorine and should be used sparingly. If they are used before entering the separator
the separation effect may not be affected and they may not form stable emulsions (EN
1825-2).
•According to EN 1825-2 the use of biological additives (bacteria, enzymes etc.) for so-
called self-cleaning purposes is not allowed in separators.
•Disposal needs to take place in regular intervals in order to avoid that the storage
capacity of the sludge trap (half of the sludge trap volume) and of the separator (max.
grease storage capacity) is exceeded.
•Sludge trap and separator need to be emptied completely and cleaned at least once a
month, preferably every 2 weeks.
•Finally the plant is to be refilled with fresh water.
•Register the disposal process in the journal and file away the disposal proof.

150331_IOM_GS_PE-LMD_BASIKA_rho_gb 13 von 30
8.1 Option Signalling Unit
„Max. Grease Storage Capacity Reached“
The maximum grease storage capacity in the grease separator may not be exceeded
since otherwise limit values cannot be observed and fatty waste water may affect the
devices following the separator. If very fatty kitchen swills enter the separator the
maximum storage capacity may be reached before the monthly disposal interval is run out.
Then the grease separator needs to be emptied earlier.
In order to recognize the maximum grease capacity all grease separators – option only
with inspection window – can be equipped with a detection device to measure the max.
grease storage capacity. A sensor (B1) will be mounted onto the inspection window at the
same level where the maximum grease storage capacity is reached. When the limit is
reached the control panel releases a message. This message can also be retrieved in a
potential-free manner via an in-house alarm signal processing system BMS/GLT.
8.2 Disposal of the Grease Separator Content
8.2.1 Manual semi-automatic disposal device
Key Assignment at the Control Panel
Acknowledge
General Fault
Agitator
ON / OFF
Reserved
Option
Solenoid Valve
ON / OFF
Operational Sequence:
•First of all the suction pipe needs to be connected firmly to the disposal car, e.g. by
means of a B-coupling.
•
The agitators are activated manually by pushing the button „Agitator ON / OFF“ – The
text display says “Stirring ON”.
•After a certain stirring time (see table page 14) the container content is being pumped
off into the disposal car.
•When the plant has been emptied completely the agitator is switched off manually by
pushing the button „ON / OFF“.
•Option:
The electrically driven solenoid valve at the filling unit is activated manually by pushing
the button „Solenoid Valve ON/OFF“. The text display says “Solenoid Valve on”. The
solenoid valve switches off automatically as soon as the refill process is over.

150331_IOM_GS_PE-LMD_BASIKA_rho_gb 14 von 30
•Option:
Message „Max. Grease Storage Capacity Reached“
In order measure properly the grease separator needs to be ready for operation and
refilled. As soon as the main switch is turned to position „ON“ the measuring process
starts. When the max. grease storage capacity is reached an alarm light immediately
indicates “Acknowledge General Fault” which means that the disposal process is
pending. The display says “Max. Grease Storage Capacity Reached”. At the same time
the in-house alarm signal processing system (BMS / GLT) is / can be activated via a
floating contact.
By pushing the button “Acknowledge General Fault” the BMS/GLT message can be
confirmed. While the alarm light switches off the message in the text display “Max.
Grease Storage Capacity Reached” remains on until the container of the grease
separator is emptied. The message disappears automatically as soon as water is
recognized.
Nominal Size NS
Stirring Time in Min.
2 5
4 8
7,5 12
10 12

150331_IOM_GS_PE-LMD_BASIKA_rho_gb 15 von 30
8.2.2 Fully Automatic Disposal Device
Key Assignment at the Control Panel
Acknowledge
General Fault
Reserved
Disposal
ON / OFF
Manual Pump
ON / OFF
Operational Sequence:
•First of all the suction pipe needs to be connected firmly to the disposal car, e.g. by
means of a B-coupling.
•The disposal process is activated by pushing the button „Disposal ON-OFF“. The fully
automatic programme control which operates in connection with the pressure sensor
starts.
•The agitators switch on automatically. The text display says “Stirring ON”.
•After a programmed stirring time, depending on the nominal size, the disposal pump
switches on automatically and the content of the container is pumped off into the
disposal car. The text display says “Pump ON”. If the distance from the separator to
the disposal car is quite long the device to accelerate the pump off process can now be
activated at the disposal car.
•The agitators switch off automatically. When the containers are completely empty the
solenoid valve at the filling unit opens. Since the disposal pump continues to operate
for a predefined time the fresh water flushes out any residues which are still in the
sludge trap or grease separator.
•As soon as the disposal pump switches off automatically the solenoid valve at the
filling unit remains open for refilling purposes. The text display says “Solenoid Valve
ON”.
The disposal process is finished and the suction pipe connection (B-coupling) can be
disconnected from the disposal car.
•The pressure sensor indicates the container filling level „Full“, the solenoid valve
closes and the plant is in „stand by“ mode until the next disposal process starts.

150331_IOM_GS_PE-LMD_BASIKA_rho_gb 16 von 30
•Option:
Message „Max. Grease Storage Capacity Reached“
In order to measure properly the grease separator needs to be ready for operation and
refilled. As soon as the main switch is turned to position „ON“ the measuring process
starts. When the max. grease storage capacity is reached an alarm light immediately
indicates “Acknowledge General Fault” which means that the disposal process is
pending. The display says “Max. Grease Storage Capacity Reached”. At the same time
the in-house alarm signal processing system (BMS / GLT) is / can be activated via a
floating contact.
By pushing the button “Acknowledge General Fault” the BMS/GLT message can be
confirmed. While the alarm light switches off the message in the text display “Max.
Grease Storage Capacity Reached” remains on until the container of the grease
separator is emptied. The message disappears automatically as soon as water is
recognized.
Our service personnel can optimise and adapt all predefined and control times to your
requirements.

150331_IOM_GS_PE-LMD_BASIKA_rho_gb 17 von 30
8.3 Default settings for LOGO!
The following default settings can be laid down for LOGO:
Clock settings
You can determine the default settings for time and date, summer/winter time changeover
and synchronisation:
•In the parameterization operation mode under the "Set" menu item.” (Menu item -
“Clock”)
•In the programming operation mode under the "Setup" menu item.” (Menu item -
“Clock”)
For time and date see Chapter 8.3.1
Summer/Winter time changeover
The automatic summer/winter time changeover can be activated/deactivated:
•In the parameterization operation mode under the "Set" menu item.”
•In the programming operation mode under the "Setup" menu item”.
Activating/deactivating summer/winter time changeover in the programming
operation mode:
1. Switch LOGO! to the programming operation mode.
2. You are now in the main menu and want to pre-select the ’Setup’ menu: Keys ▲or ▼
3. Accept ’Setup’: Key OK
4. Move ’>’ to ’Clock’ : Keys ▲or ▼
5. Accept ’Clock’: Key OK
6. Move ’>’ to ’S/W Time’ : Keys ▲or ▼
7. Move ’S/W Time’: Key OK
LOGO! reveals the following display:
The ongoing setting of the automatic summer/winter time changeover is shown in the
bottom line. In the as-delivered condition this setting is shut down
(’Off’: deactivated).
Activating/deactivating summer/winter time changeover in the parameterization
operation mode:
If wanting to activate/deactivate the summer/winter time changeover in the
parameterization operation mode, then select ’Set..’ in the parameterization menu –
followed by the ’Clock’ and ’S/W Time’ menus. The summer/winter time changeover can
now be activated / deactivated:

150331_IOM_GS_PE-LMD_BASIKA_rho_gb 18 von 30
Activate summer/winter time changeover
You now want to activate this changeover and set and/or define your parameters:
1. Move ’>’ to ’On’: Keys ▲or ▼
2. Confirm ’On’: Key OK
The display shows:
3. Select desired changeover: Keys or explanation of the display:
•’EU’ is equivalent to the beginning and end of summer time in Europe.
•’UK’ is equivalent to the beginning and end of summer time in Great Britain.
•’US’ is equivalent to the beginning and end of summer time in the Unites States.
•’AUS’ is equivalent to the beginning and end of summer time in Australia.
•’AUS-TAS ’ is equivalent to the beginning and end of summer time in
Australia/Tasmania.
•’NZ’ is equivalent to the beginning and end of summer time in New Zealand.
•. . : any month, day and time difference can be set here.
The pre-programmed settings are in the following
Tables:
A. German / B. English
A. German

150331_IOM_GS_PE-LMD_BASIKA_rho_gb 19 von 30
B. English
Start of summer time End of summer time Time
difference
EU Last Sunday in March:
02:00am—>03:00am
Last Sunday in
October: 03:00am—
>02:00am
60 min
UK Last Sunday in March:
01:00am—>02:00am
Last Sunday in
October: 02:00am—
01:00am
60 min
US First Sunday in April:
02:00am—>03:00am
Last Sunday in
October: 02:00am—
>01:00am
60 min
AUS Last Sunday in
October: 02:00am—
>03:00am
Last Sunday in March:
03:00am—>02:00am
60 min
Start of summer time End of summer time Time
difference
AUS-
TAS
First Sunday in
October: 02:00am—
>03:00am
Last Sunday in March:
03:00am—>02:00am
60 min
NZ First Sunday in
October: 02:00am—
>03:00am
Third Sunday in March
03:00am—>02:00am
60 min
Set month and day at
will: 02:00—> 02:00 +
time difference
Set month and day at
will: 03:00—> 03:00 -
time difference
Determined
by yourself
(precisely - to
the minute)
Caution:
The time difference ∆can be determined within a range of 0 to 180 minutes.
Let us assume you want to start the European summer/winter time changeover:
4. Move ’>’ to ’EU’: Keys ▲or ▼
5. Confirm ’EU’: Key OK
LOGO! reveals the following display:
LOGO! then shows that the European summer/winter time changeover has switched on.

150331_IOM_GS_PE-LMD_BASIKA_rho_gb 20 von 30
Setting one's own parameters
All parameters/changeovers which do not conform to your country can be defined at will
under menu item ’. .’ . Proceed as follows:
1. Confirm ’On’ once again: Key OK
2. Move ’>’ to’. .’: Keys ▲or ▼
3. Accept menu item ’. .’: Key OK
The display shows:
Month (MM) and (DD)
Start of summer time
End of summer time
Time difference wanted in min.
Let us assume you want to enter the following parameters: Start of summer time 31
March, end of summer time 1 November and a time difference of 120 minutes
(two hours).
You can enter your data in the following manner:
•Keys ◄and ►move the cursor/filled-in square to and fro.
•Keys ▲and ▼change the value at the cursor position.
•
The display shows:
31 March
1. November
Time difference of 120 min.
When you have entered all the values, then press Key OK.
In this way you have entered your personal summer/winter time changeover.
LOGO! then displays the following:
LOGO! shows that the summer/winter time changeover is switched on and that the
parameters have been freely set ( ’..’ ).
Caution:
The only thing you need to do to deactivate the summer/winter time changeover is to
confirm ’Off’ with key OK in this menu.
This manual suits for next models
3
Table of contents
Popular Water Filtration System manuals by other brands
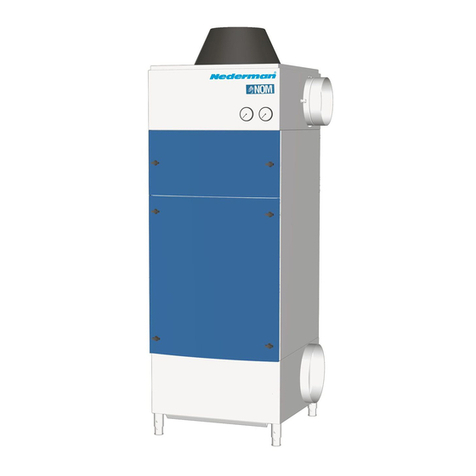
Nederman
Nederman NOM 18 instruction manual
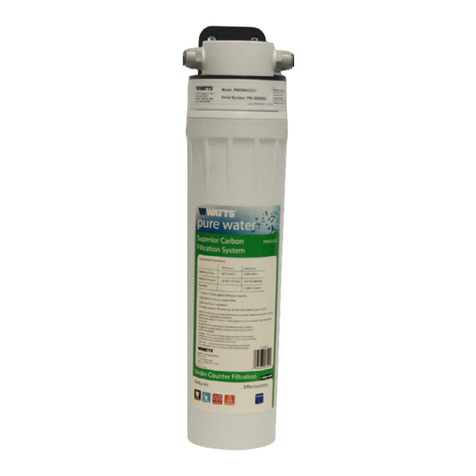
Watts
Watts PWDWHCUC1 Installation, operation and maintenance manual

Kärcher
Kärcher WPC 120 UF manual

Cintropur
Cintropur NW 18 Instructions for installation, use and maintenance
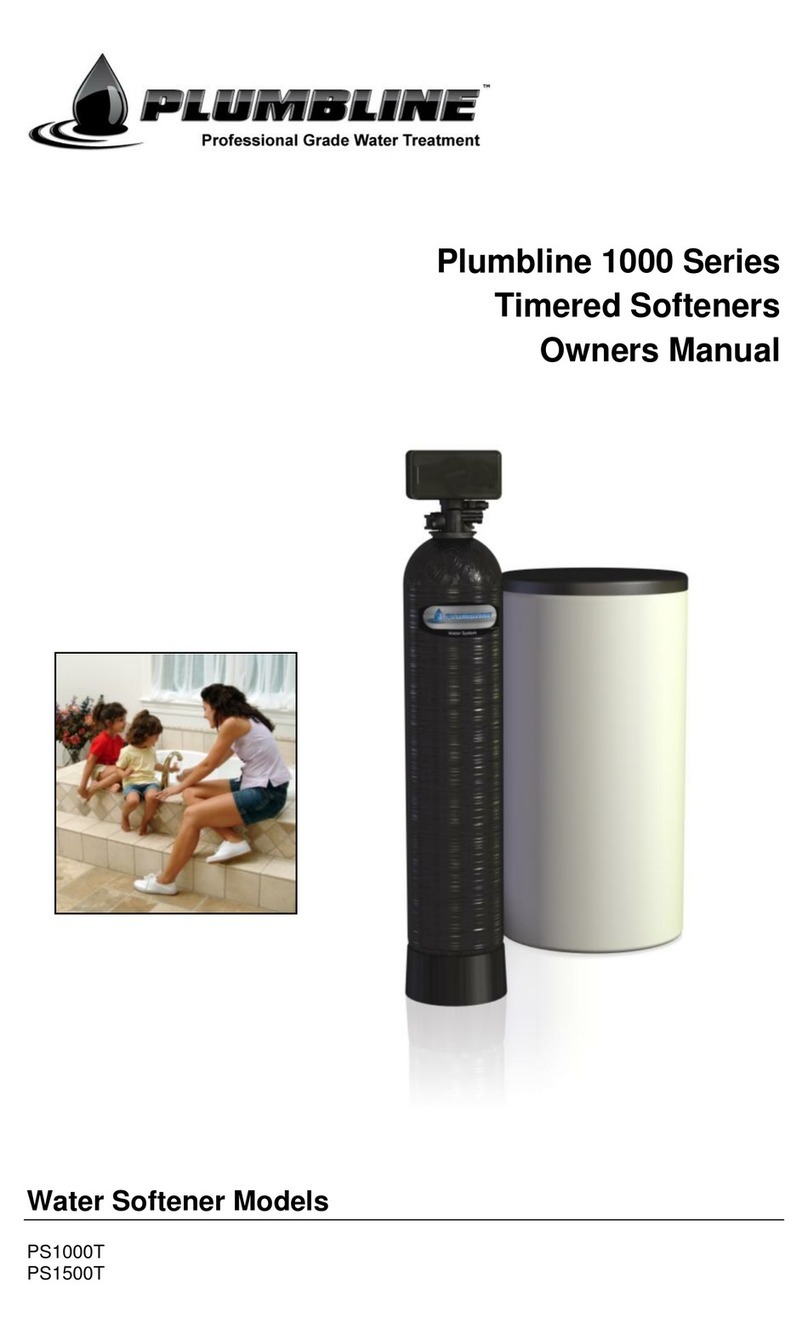
Plumbline
Plumbline PS1000T owner's manual

LG
LG Premium 5231JA2002A-S installation and replacement