Micropack FDS300 User guide

FDS300
VISUAL FLAME
DETECTOR
SAFETY & TECHNICAL
MANUAL
Ref: 2401.6000
micro
p
ack.co.uk

HELP US TO HELP YOU
Every effort has been made to ensure the accuracy in the contents of our documents; however,
Micropack (Engineering) Ltd can assume no responsibility for any errors or omissions in our
documents or their consequences.
Micropack (Engineering) Ltd would greatly appreciate being informed of any errors or omissions
that may be found in our documents. To this end we include a form, given in Appendix B, for you
to photocopy, complete and return to us so that we take the appropriate action. Thank you.
CONTENTS
TABLE
OF
This document is strictly private and confidential, reproduction without Micropack approval is prohibited. © Micropack Engineering Ltd, 2015
1
Introduction 4
1.1 Features 4
2
Safety Instructions 5
2.1 Warnings 5
2.2 Cautions 6
2.3 Important Safety Notices 6
3
Installation 8
3.1 Detector Enclosure 8
3.2 Mounting & Orientation 9
3.3 Wiring Procedure 11
3.3.1 4-20mA Output 12
3.3.2 Relay Output 13
3.3.3 Internal Inter-connections 14
3.4 Installation Checklist 15
3.4.1 Mechanical 15
3.4.2 Electrical 15
4
System Design Guidelines 16
4.1 Power Supply 16
4.2 Cable Selection 16
4.2.1 DC Power 16
FDS300 Flame Detector FDS300 Safety and Technical Manual
2
Ref: 2401.6000 Rev: 2.3 ECN: 4436

micro
p
ack.co.uk
5
Application Guidelines 17
5.1 Positioning Requirements 17
5.2 Detection Coverage 18
5.3 Exposure to Flare Radiation 18
5.4 Optical Contamination 18
5.5 Enclosed Areas 19
5.6 Detector Sensitivity 19
6
Maintenance and Commissioning 20
6.1 Procedure 20
6.2 Functional Testing 22
7
Fault Finding 23
7.1 Removal of the Electronics 23
7.2 Replacement of the Electronics 23
7.3 Diagnostics 23
7.4 LED Indication 24
7.5 Power Fault 25
8
Technical Specification 26
8.1 Electrical Specification 26
8.2 Mechanical Specification 26
8.3 Environmental Specification 27
8.4 Certification and Approvals 27
8.5 Operating Specification 27
Appendix A
Acronyms, Terms & Abbreviations 28
Appendix B
Help us to help you 29
Appendix C
Field of View 30
FDS300 Flame Detector FDS300 Safety and Technical Manual
3
Ref: 2401.6000 Rev: 2.3 ECN: 4436

1
Introduction
The MICROPACK FDS300 is a flame detector that has unsur
p
assed false alarm immunit
y
.
The Micro
p
ack flame detection ran
g
e
are the safest and most advanced flame detectors
on the market today, and their track record on the numerous facilities where they are
installed has proven the technology to be robust, even in the harshest of environments.
FDS300 flame detectors identif
y
flame usin
g
certified flame reco
g
nition software. FM
A
pp
rovals ensures that our flame reco
g
nition software is fit for
p
ur
p
ose throu
g
h ri
g
orous
research and testing in a range of difficult environments.
Production losses caused b
y
common sources of alarm from existin
g
flame detection
technologies are addressed by the FDS300 flame detector.
The FDS300 has been desi
g
ned for use in standalone o
p
eration.
1.1
Features
•
The FDS300 has 120° horizontal
x 80° vertical field of view with an increased
range of 60 metres to an n-heptane 0.1m2pan fire.
•
Sin
g
le detection sensitivit
y
settin
g
because
the
FDS300
is
unaffected b
y
the
background radiation experienced in industrial environments.
•
Su
p
erior False
alarm immunit
y
to
common
sources
o
f
unwanted alarms such as
hot process, Hot Work, Hot CO2 emissions and Flare Reflections.
•
Advanced o
p
tical verification test assurin
g
readiness to
p
erform when needed.
•
Out
p
uts include both rela
y
contact
and
4-20
mA.
•
Se
p
arate termination chamber
for
ease
o
f
installation.
•
Flame simulation tester to verif
y
o
p
eration
from
distances
o
f
3-8 metres,
removing the need for scaffolding or ladders.
•
FDS300 can o
p
erate via a standard
3
or
4
wire
termination.
This document is strictly private and confidential, reproduction without Micropack approval is prohibited. © Micropack Engineering Ltd, 2015
FDS300 Flame Detector FDS300 Safety and Technical Manual
4
Ref: 2401.6000 Rev: 2.3 ECN: 4436

2
Safet
y
Instructions
For the correct and effective use of this e
q
ui
p
ment, to maintain safet
y
and avoid hazards
it is essential that you read and understand these instructions fully, act accordingly
BEFORE installing, operating or maintaining the equipment.
2.1
Warnin
g
s
This e
q
ui
p
ment is certified and intended for use in
p
otentiall
y
hazardous areas. Install and
use
the equipment in accordance with the latest regulations.
For Euro
p
ean (ATEX) installations IEC/EN60079-14
‘Electrical
Installations
in Hazardous Areas’
and
ICE/EN60079-17 ‘Inspection and Maintenance in Hazardous Areas’ should be strictly observed.
For installations in North
A
merica the National
Electrical
Code
(NEC)
should be strictl
y
observed.
In other countries the appropriate local or national regulations should be observed.
The e
q
ui
p
ment must be
p
ro
p
erl
y
earthed
to
p
rotect
a
g
ainst
electrical
shoc
k
and minimise
electrical interference.
Do not drill holes in any housing or enclosure as this will invalidate the explosion protection.
Ensure that the enclosure lid is fully tightened and locked into position before energising the
equipment.
Do not o
p
en the enclosure in the
p
resence
o
f
an
ex
p
losive
atmos
p
here.
All
p
ermits and
p
ro
p
er site
p
rocedure and
p
ractises
must
be
followed
and
the e
q
ui
p
ment
must
be isolated from the power supply before opening the enclosure in the field.
O
p
erators must be
p
ro
p
erl
y
trained and aware of what actions to take in the event of a fire bein
g
detected.
Cable to be used for installation is to be selected with a temperature rating of greater than 25
degrees Celsius above the maximum ambient temperature. The metric cable entries are fitted
with an internal stop. This will result in threads of the cable gland being visible. Do not over
tighten.
micro
p
ack.co.uk
PAY ATTENTION TO ALL SAFETY WARNINGS AND CAUTIONS
FDS300 Flame Detector FDS300 Safety and Technical Manual
5
Ref: 2401.6000 Rev: 2.3 ECN: 4436

2.2
Cautions
Use only approved parts and accessories with this equipment.
Do not attempt to replace the window as the glass and the front cover are individually matched
pairs to meet the stringent requirement of the Hazardous area certification.
The threaded portions of the detector are flame paths. These threads and the flame paths
around the window are not to be repaired.
To maintain safet
y
standards, commissionin
g
and re
g
ular maintenance should be
p
erformed b
y
a qualified person.
2.3
Im
p
ortant Safet
y
Notices
Pa
y
attention to the
g
uidelines
g
iven throu
g
hout
this
document.
If in any doubt about the instructions listed within this manual then please contact Micropack
(Engineering) Ltd. Micropack (Engineering) Ltd takes no responsibility for installation and/or use
of its equipment if this it is not in accordance with the appropriate issue and/or amendment of
the manual. Micropack (Engineering) Ltd reserve the right to change or revise the information
contained herein without notice and without obligation to notify any person or organisation of
such action.
Onl
y
those
p
arameters and confi
g
urations
hi
g
hli
g
hted with the FM diamond (
tested and approved by Factory Mutual.
) have been
Warnin
g
Do not open the detector assembly in a hazardous area when power is applied. The detector
contains limited serviceable components and should never be opened except by trained
personnel.
Caution
The wiring procedures in this manual are intended to ensure functionality of the device under
normal conditions. Due to the many variations in wiring codes and regulations, total compliance
to these ordinances cannot be guaranteed. Be certain that all wiring complies with the all local
ordinances. If in doubt, consult the authority having jurisdiction before wiring the system.
Installation must be done by trained personnel.
Caution
To prevent unwanted actuation or alarm, extinguishing devices must be inhibited/isolated prior
to performance testing or maintenance.
This document is strictly private and confidential, reproduction without Micropack approval is prohibited. © Micropack Engineering Ltd, 2015
FDS300 Flame Detector FDS300 Safety and Technical Manual
6
Ref: 2401.6000 Rev: 2.3 ECN: 4436

Detector Orientation
Detectors should be mounted with the earth stud/status led directly below the lens to ensure the
120° horizontal field of view is achieved.
Detector Positionin
g
Detectors should be positioned to provide the best unobstructed view of the area to be
protected.
The followin
g
factors should also be taken
into
consideration:
•
Identif
y
all hi
g
h risk fire i
g
nition sources. Ensure that enou
g
h detectors are used to
adequately cover the hazardous area.
•
Locate and
p
osition the detector so that the fire hazard(s) are within both the field o
f
view and detection range of the device.
•
For best
p
erformance, the detector
should
be
mounted
on
a
ri
g
id surface in a low
vibration area.
•
Extremel
y
dense fo
g
or blizzard
conditions
could
eventuall
y
block the vision o
f
the
detector.
•
For indoor a
pp
lications, if dense
smoke is ex
p
ected to accumulate at the onset of a
fire,
mount the detector on a side wall (approximately 1 metre, 3 feet) down from the ceiling.
•
The FS301 flame simulator can be used to verif
y
correct detector
p
ositionin
g
and
coverage.
•
The FDS300 has
one sensitivit
y
settin
g
,
this
is
factor
y
set,
and
no
chan
g
es can be
made
to set-up except by fully trained Micropack engineers.
•
The detector carries out continuous
internal
hardware
dia
g
nostic testin
g
to ensure
correct operation is relayed to the control system.
•
The FDS300 is not designed to annunciate diagnostic failures of signal returns via
external wiring. Control systems and fire panels generally have fault monitoring for
such an eventuality.
micro
p
ack.co.uk
FDS300 Flame Detector FDS300 Safety and Technical Manual
7
Ref: 2401.6000 Rev: 2.3 ECN: 4436

3
Installation
The FDS300 design has been developed to allow simple installation. The detector comprises
two key components, the detector enclosure and the detector internal assembly. The detector
assembly located in the front of the enclosure should not be removed except by trained
personnel. Unauthorised removal or disassembly of the detector assembly will invalidate the
warranty. Only the rear end cap can be removed for terminal access.
3.1
Detector Enclosure
The detector electronics are housed in an enclosure certified for use in hazardous areas. For
the exact certification and conditions of use see certification label on the device, or the exam
p
le
drawing below:
The enclosure com
p
rises
the front enclosure
cover
(includin
g
the
face
p
late window), the rear
enclosure cover, the enclosure body (with certification label), and the mounting bracket.
This document is strictly private and confidential, reproduction without Micropack approval is prohibited. © Micropack Engineering Ltd, 2015
FDS300 Flame Detector FDS300 Safety and Technical Manual
8
Ref: 2401.6000 Rev: 2.3 ECN: 4436

3.2
Mountin
g
&
Orientation
The mountin
g
bracket allows the detector’s
v
ertical
orientation
to
be
ad
j
usted from 0 to 45°,
and
allows a horizontal rotation of +/-45°.
Fi
g
ure 1: Detector Mountin
g
Bracket
&
Orientation
micro
p
ack.co.uk
FDS300 Flame Detector FDS300 Safety and Technical Manual
9
Ref: 2401.6000 Rev: 2.3 ECN: 4436

Fi
g
ure 2: Ceilin
g
Mount
Fi
g
ure 3: Wall Mount
Firm, vibration free mountings are essential for trouble free operation of optical systems and the
detector should be fixed to a rigid mounting. When mounting on a wall in this orientation allow
for the cable gland and cable as this may restrict the downward rotation of the detector.
This document is strictly private and confidential, reproduction without Micropack approval is prohibited. © Micropack Engineering Ltd, 2015
FDS300 Flame Detector FDS300 Safety and Technical Manual
10
Ref: 2401.6000 Rev: 2.3 ECN: 4436

3.3
Wirin
g
Procedure
The wirin
g
terminals are
located in the rear
section
o
f
the
detector
enclosure and are accessible
by removal of the end cap.
The front section of the enclosure should onl
y
be accessed b
y
trained
p
ersonnel.
The terminal schematic detailed below
shows
the
v
iew
lookin
g
inside
the
detector followin
g
removal of the end cap.
Fi
g
ure 4: Terminal Schematic
The detector has two t
yp
es o
f
alarm out
p
ut
available
simultaneousl
y
•
•
4-20m
A
(source)
Relay (Alarm & Fault)
Listed below are wirin
g
o
p
tions de
p
endant
on
the
functional
re
q
uirements o
f
the detector.
micro
p
ack.co.uk
FDS300 Flame Detector FDS300 Safety and Technical Manual
11
Ref: 2401.6000 Rev: 2.3 ECN: 4436

3.31
4-20mA
Out
p
ut
The followin
g
wirin
g
connection dia
g
ram
shows
wirin
g
the
detector
when
a 4-20m
A
out
p
ut
is
required.
Fi
g
ure 5: 3 Wire Terminations
Table 1: Current Level Out
p
ut Indicators
Factor
y
Fixed Values
This document is strictly private and confidential, reproduction without Micropack approval is prohibited. © Micropack Engineering Ltd, 2015
Current Output Event
0mA Power/Detector Fault
2mA Optical Fault
4mA Healthy
18mA Alarm
21mA Over-range
FDS300 Flame Detector FDS300 Safety and Technical Manual
12
Ref: 2401.6000 Rev: 2.3 ECN: 4436

3.32
Rela
y
Out
p
ut
The followin
g
wirin
g
connection dia
g
rams
shows
wirin
g
the
detector
when
a rela
y
out
p
ut is
required.
Fi
g
ure 6: 2 Pair Termination
NOTE: EOL and Alarm resistors values are defined by the client and the control
system/fire panel which the detectors are being integrated into
micro
p
ack.co.uk
FDS300 Flame Detector FDS300 Safety and Technical Manual
13
Ref: 2401.6000 Rev: 2.3 ECN: 4436

3.33
Internal Inter-connections
The followin
g
dia
g
ram shows the internal
inter-connections
o
f
the
alarm
and fault rela
y
contacts
and jumpers. Each field connection is listed on this diagram for clarity.
Fi
g
ure
7:
FDS300 Internal Inter-connections
This document is strictly private and confidential, reproduction without Micropack approval is prohibited. © Micropack Engineering Ltd, 2015
FDS300 Flame Detector FDS300 Safety and Technical Manual
14
Ref: 2401.6000 Rev: 2.3 ECN: 4436

3.4
Installation Checklist
Ex
p
erience has shown that
p
oor installation
and
commissionin
g
p
ractice
ma
y
result in an
unreliable fire detection system that fails to meet the site performance targets. Before installing
the detector it is important to take into account where it is to be located and how it is to be
mounted. In order to maintain compliance with the EMC regulations it is essential the electrical
installation be engineered correctly.
3.41
Mechanical
3.42
Electrical
micro
p
ack.co.uk
Notes
It is advisable to check the detection locations, prior to fabrication of the mounting supports, as
changes are frequently made during construction at site. Detector cabling must be segregated
from cables carrying high-speed data or high energy and/or high frequency signals and other
forms electrical interference. The detector requires a clear unobstructed view of the local hazard.
In order to avoid local obstructions, such as pipe-work and cable trays, a 2m helix should
be allowed in the detector cabling. The detector should only be fitted just prior to commissioning
the detector. Experience shows that the detector can be damaged due to cable testing
operations (Insulation Tests, etc).
1
Isolate all associated power supplies. Ensure that they remain OFF until required for
commissioning.
2
The threaded flame path of the enclosure cover and body must be protected from damage
during installation. Any such damage can destroy the validity of the enclosure.
3
The electronics subassembly shall be protected from mechanical damage and external sources
of EMI such as X-rays, RFI and electrostatic discharge.
4The enclosures external earth stud should be connected to a local earth point.
5Remove the blanking plug(s) from the enclosure body gland entries.
6Fit approved cable glands.
Notes
When locating the detector consideration should be given to maintenance access to the detector.
The detector mounting should be secure and vibration free.
It is advisable to check the detection locations, prior to fabrication of the mounting supports, as
changes are frequently made during construction at site which can affect detector coverage.
The installation should allow subsequent space for detector removal, for maintenance or repair,
to be easily achieved.
1
The detector should be fixed to a stable supporting structure using the mounting bracket
provided. The supporting structure must allow for horizontal adjustment of the detector
orientation. The support structure should be in place prior to detector installation. Information
on mounting is available from Micropack (Engineering) Limited.
2
The threaded flame path of the enclosure cover and body must be protected from damage
during installation. Any such damage can destroy the validity of the enclosure.
3
The detector electronics shall be protected from mechanical damage and external sources of
EMI such as X-rays, RFI and electrostatic discharge. The detector should not face directly towards
the sun.
4
Fit the mounting bracket to the support structure using 8mm bolts (not provided). The detector
(bracket) should be oriented to provide the desired coverage.
5
The detector enclosure body should be fitted to the mounting bracket. The bolts locate into the
bracket. Twist the enclosure to locate the bolts; these are then tightened using a 6mm Allen key.
6Ensure the detector is orientated such that the status led/earthing stud is directly beneath the lens.
7
Glanding should be carried out by trained personnel. The gland should be fitted in line with
installation standards for potentially explosive atmospheres that is 5 full threads minimum with
the IP seal washer fitted at the bottom of the thread. This sealing arrangement will result in a
number of threads of the cable gland being visible. The gland should be torqued between 15 to
20 NM (11 to 15 lbf·ft).
FDS300 Flame Detector FDS300 Safety and Technical Manual
15
Ref: 2401.6000 Rev: 2.3 ECN: 4436

4
S
y
stem Desi
g
n
Guidelines
The following guidelines are intended to assist with the electrical design and engineering of
systems where it is intended that flame detectors will be used.
4.1
Power
Su
pp
l
y
The detector requires an absolute minimum supply voltage of 18V, as measured at the detector
terminals. The system power supply voltage and power distribution should be arranged such
that on the longest cable run the detector(s) has a supply voltage of greater than 18V.
4.2
Cable Selection
Cable to be used for installation is to be selected with a temperature rating of greater than 25°
Celsius above the maximum ambient temperature.
The metric cable entries are fitted with an internal stop. This will result in threads of the cable
gland being visible. Do not over tighten.
The installation and local regulations and standards determine the overall cable specification.
This section specifies suitable cable characteristics to ensure correct operation of the flame
detector.
4.21 DC Power
NOTE: Table 2 shows absolute maximums for cable lengths; try not to approach these values.
Table 2: Maximum Cable Len
g
ths (24V su
pp
l
y
)
Table 3: AWG Conversions
This document is strictly private and confidential, reproduction without Micropack approval is prohibited. © Micropack Engineering Ltd, 2015
Cross Sectional Area (mm2)
American Wire Gauge (AWG)
Typical Conductor Resistance per
km (3280 ft.) DC Ohms /km @
20°C (approximate)
0.5 22 36
118 19
1.5 16 12
2.5 14 7.6
Installation based
on 24V nominal
supply
Number of Flame
Detectors
Maximum Power
(W)
Maximum Cable
Length (m) with
1.5mm2 Conductors
(12Ω/km)
Maximum Cable
Length (m)with
2.5mm2 Conductors
(7.6Ω/km)
Detector 13 @ 24V 2,000 1,578
FDS300 Flame Detector FDS300 Safety and Technical Manual
16
Ref: 2401.6000 Rev: 2.3 ECN: 4436

5
A
pp
lication
Guidelines
In considering the application of the detector it is important to know of any conditions that may
p
revent the detector from res
p
ondin
g
. The detector
p
rovides reliable res
p
onse to visible flames
within its field of view, and insensitivity to common false alarm sources. Solid obstructions or a
direct view of intense light sources may result in a reduction in the coverage and/or a reduction
in the detector sensitivity. Scaffolding or tarpaulins in the detector’s field of view may reduce
coverage. Contamination of the detector window may result in a reduction in sensitivity.
The detector has a horizontal field of view of 120° and a vertical field of view of 80°. The location
and orientation of the detector in relation to the protected area determines the actual footprint.
Achieving the desired coverage depends on congestion within the protected space, the location
of the detector(s) and the distance of the detector from the hazard. It may be necessary to install
more than one detector within an area in order to achieve adequate coverage.
The detector sensitivity, expressed as fire size at a distance, is determined visually by the
apparent size of the fire. This is a function of the fuel source, how it is released and distance
from the detector to the fire. The detector res
p
onse time is relativel
y
inde
p
endent of fuel t
yp
e
and/or distance.
In common with other forms of flame detection the detector’s sensitivity is reduced and
potentially blinded by dense obscurants such as smoke, fog and other airborne particulates. The
detector is insensitive to arc welding, however this should not be conducted within 5m of the
detector.
5.1
Positionin
g
Re
q
uirements
The following guidelines have been based on operational feedback, reflecting commonly
experienced problems which can be traced to a failure to observe the following:
•
•
•
•
•
•
Ensure the mounting position is free from vibration or movement.
Prevent accidental knocking or forcing out of alignment.
Isolate as far as possible from local electrical interference sources.
Ensure sufficient detection to achieve adequate coverage for all likely hazards.
Minimise exposure to contamination of the detector face plate.
Ensure ease of maintenance access to detector (i.e. direct, ladder or scaffold access).
All these issues are of crucial importance to a successful installation and they should be afforded
great attention during the detailed design, construction and commissioning phases of the work.
micro
p
ack.co.uk
FDS300 Flame Detector FDS300 Safety and Technical Manual
17
Ref: 2401.6000 Rev: 2.3 ECN: 4436

5.2
Detection Covera
g
e
Detector locations can be chosen from computer models or from site surveys. The detectors
should be aligned to view the intended hazard taking into account any obstruction and
congestion. Software analysis of the actual detector coverage may be required to ensure
adequate coverage of the hazards. This analysis can also be used to optimise the number of
detectors and the loop configuration. The cones of vision are detailed in Appendix C.
Fi
g
ure 8: FDS300 Covera
g
e & Field of View
5.3
Ex
p
osure
to Flare Radiation
Flame detectors are frequently used where hydrocarbon fire hazards are expected; these are
quite often processing plants where a flare stack is in use nearby. The detector should not have a
direct view of the flare.
5.4
O
p
tical Contamination
There are many sources of contamination such as oil, water (deluge water, rain and sea-spray),
snow, ice, and internal misting. Excessive contamination of the detector faceplate may result in
an increased maintenance requirement and potentially reduce the detector’s sensitivity. Where
detectors are mounted at low level, care should be taken to avoid contamination (such as water
and oil) from equipment above the detector. Care should be taken in sighting the detector to
minimise the likelihood of such contamination. The detector is designed such that an optical fault
is indicated when half of the detection range remains. This is indicated by the Fault output and
is evident by the yellow colour of the LED on the face of the detector. The optical fault condition
indicates that the detector requires cleaning or service. The optical fault indication is self-clearing.
This document is strictly private and confidential, reproduction without Micropack approval is prohibited. © Micropack Engineering Ltd, 2015
FDS300 Flame Detector FDS300 Safety and Technical Manual
18
Ref: 2401.6000 Rev: 2.3 ECN: 4436

5.5
Enclosed
A
reas
In enclosed areas, if dense smoke is ex
p
ected to accumulate at the onset of the fire, the detector
should be mounted 1 to 2 metres below the ceiling level.
5.6
Detector Sensitivit
y
The detector’s response to a fire is a function of the fuel source and how it is released, fire size
and distance, orientation to the detector and local ambient conditions. The typical figures are
based on in-house tests except where marked with the FM logo these tests were conducted and
certified by Factory Mutual. As with all tests the results must be interpreted according to the
individual application taking into account all possible variables.
The detector sensitivity to different fuel sources is dependent on the a
pp
arent size of the flame,
the detectors typical response is shown below (see table 4).
Table 4: T
yp
ical FDS300 Res
p
onse Characteristics
micro
p
ack.co.uk
Fuel Fire Size Distance
Methane Jet Fire 3ft plume 26m (86 feet)
Ethanol 0.3m x 0.3m pan
30m (100 feet)
Diesel 0.3m x 0.3m pan
50m (165 feet)
Crude Oil (heavy fuel oil) Pan Fire 0.5m x 0.5m pan
50m (165 feet)
Wax Inhibitor (Clear 10) Pan Fire 0.3m x 0.3m pan
50m (165 feet)
Anti-Foam (Surflo AF-300) Pan Fire 0.3m x 0.3m pan
50m (165 feet)
Wood Stack 0.3m x 0.3m crib
50m (165 feet)
n-Heptane Pan Fire 0.3m x 0.3m pan
60m (200 feet)
n-Heptane Pan Fire in direct sunlight 0.3m x 0.3m pan
60m (200 feet)
n-Heptane Pan Fire in modulated sunlight 0.3m x 0.3m pan
60m (200 feet)
n-Heptane Pan Fire in the presence of modulated black
body radiation 0.3m x 0.3m pan
60m (200 feet)
n-Heptane Pan Fire in the presence of Arc welding 0.3m x 0.3m pan
60m (200 feet)
n-Heptane Pan Fire in the presence of a 1000watt lamp 0.3m x 0.3m pan
60m (200 feet)
Gasoline pan Fire 0.3m x 0.3m pan
60m (200 feet)
JP4 0.6m x 0.6m pan
90m (300 feet)
Silane 2ft plume 17m (55 feet)
FDS300 Flame Detector FDS300 Safety and Technical Manual
19
Ref: 2401.6000 Rev: 2.3 ECN: 4436

6
Maintenance
and
Commissionin
g
6.1
Procedure
This maintenance schedule/ commissioning procedure is intended for guidance only. The actual
level of maintenance required will depend on the severity of the operating environment and
the likelihood of damage or the rate of contamination from oil, sea spray, deluge system etc. It
is advisable to regularly review maintenance reports and adapt the maintenance period to the
operating environment.
This document is strictly private and confidential, reproduction without Micropack approval is prohibited. © Micropack Engineering Ltd, 2015
FDS300 Flame Detector FDS300 Safety and Technical Manual
20
Ref: 2401.6000 Rev: 2.3 ECN: 4436
Other manuals for FDS300
1
Table of contents
Popular Smoke Alarm manuals by other brands
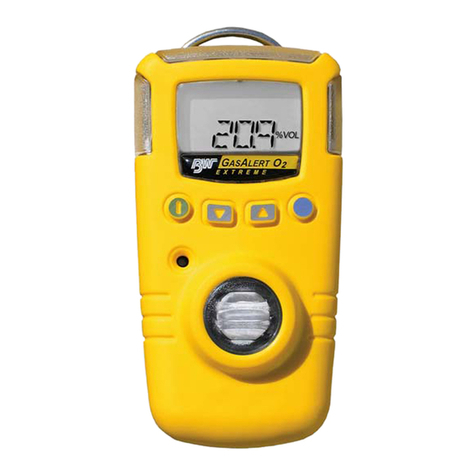
Honeywell
Honeywell GasAlert Extreme user manual
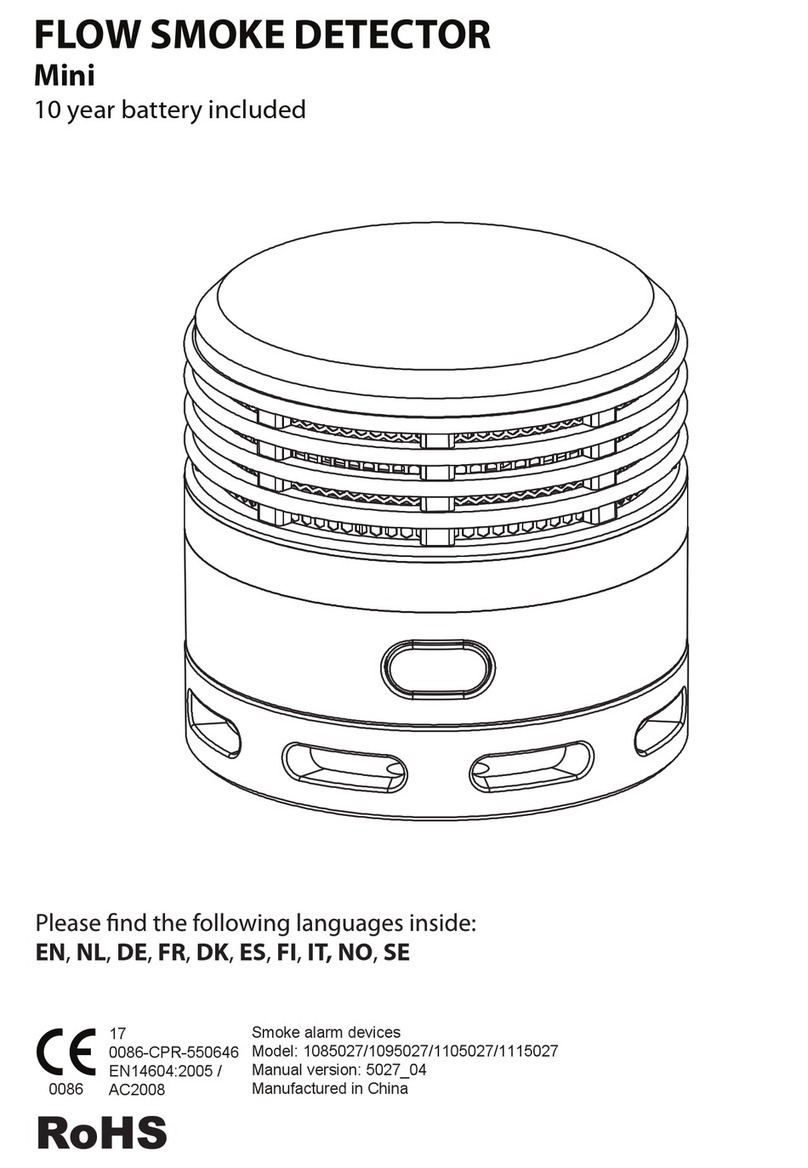
Flow Amsterdam
Flow Amsterdam Mini 1085027 manual
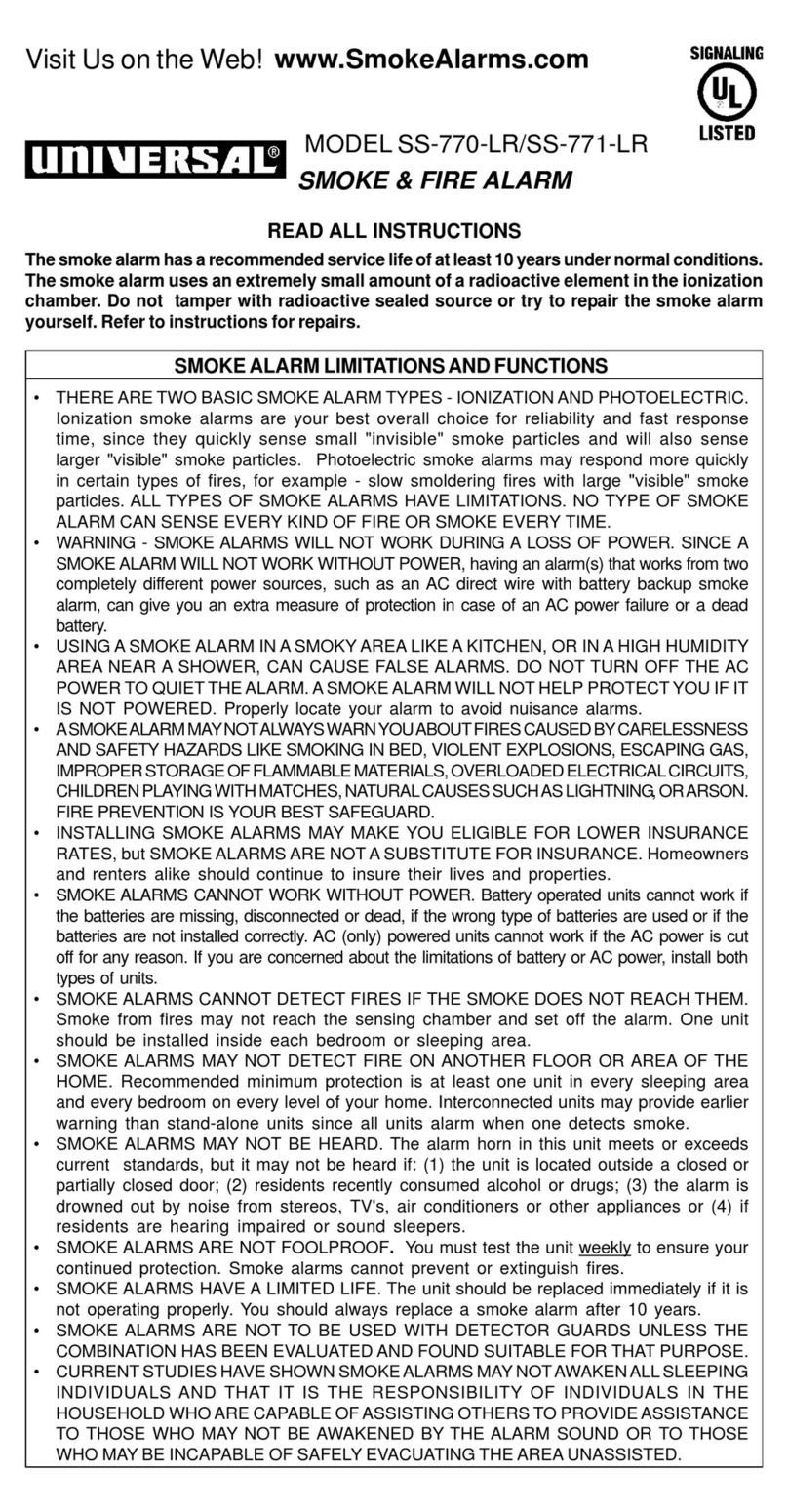
Universal Security Instruments
Universal Security Instruments UNIVERSAL SS-770-LR user manual
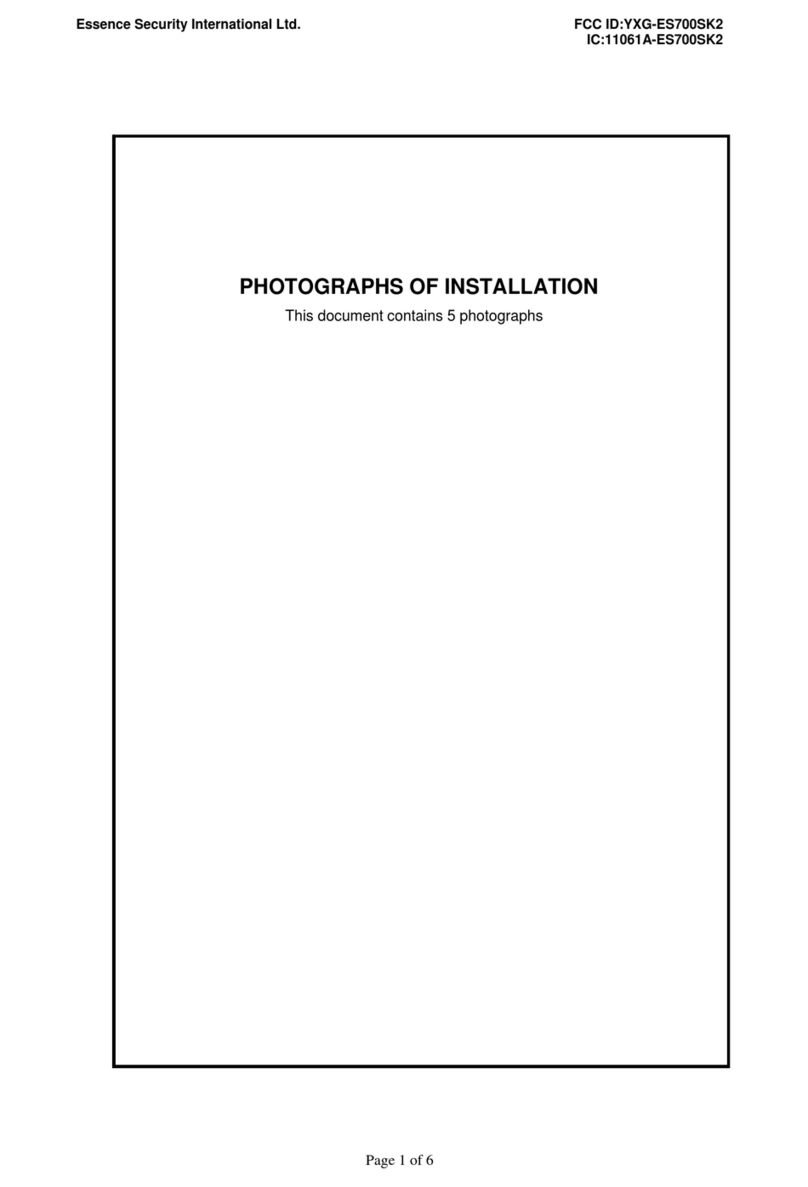
Essence Security
Essence Security ES700SK2 Installation
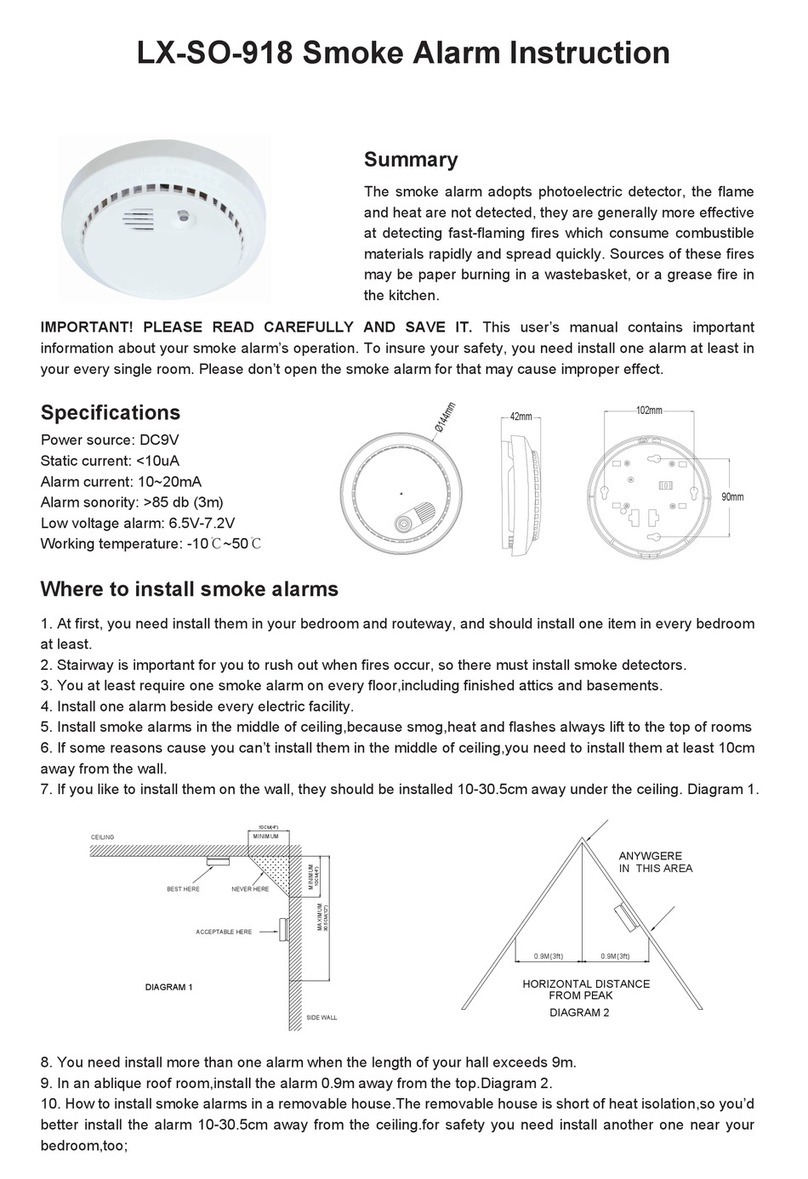
Lexing
Lexing LX-SO-918 Instruction
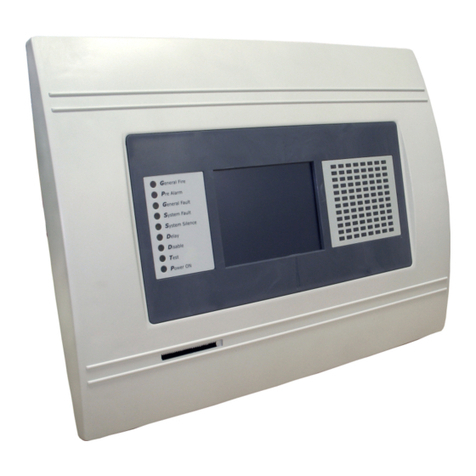
Teletek electronics
Teletek electronics IRIS installation manual