Milnor TP1607 Series Manual

Published Manual Number/ECN: MAPTP16XAE/9713A@
• Publishing System: TPAS
• Access date: 11/24/1999
• Document ECN's: Latest Available
Installation and Service—
TP1607xx Single Stage
Press
PELLERIN MILNOR CORPORATION POST OFFICE BOX 400, KENNER, LOUISIANA 70063-0400, U.S.A.

Please Read
About the Manual Identifying Information on the Cover
The front cover displays pertinent identifying information for this manual. Most important, are
the published manual number (part number) /ECN (date code). Generally, when a replacement
manual is furnished, it will have the same published manual number, but the latest available
ECN. This provides the user with the latest information applicable to his machine. Similarly all
documents comprising the manual will be the latest available as of the date the manual was
printed, even though older ECN dates for those documents may be listed in the table of
contents.
When communicating with the Milnor factory regarding this manual, please also provide the
other identifying information shown on the cover, including the publishing system, access date,
and whether the document ECN’s are the latest available or exact.
References to Yellow Troubleshooting Pages
This manual may contain references to “yellow pages.” Although the pages containing
troubleshooting procedures are no longer printed on yellow paper, troubleshooting instructions, if
any, will be contained in the easily located “Troubleshooting” chapter or section. See the table of
contents.
Trademarks of Pellerin Milnor Corporation
The following, some of which may be used in this manual, are trademarks of Pellerin Milnor
Corporation:
Ampsaver®CBW®Gear Guardian®Milnet®Staph-Guard®
Autolint®Dye-Extractor®Hands-Off®Milnor®System 4®
Auto-Purge®Dyextractor®Hydro-Cushion®Miltrac System 7®
Autovac E-P Plus®Mildata®Miltron Totaltrol®
Comments and Suggestions
Help us to improve this manual by sending your comments to:
Pellerin Milnor Corporation
Attn: Technical Publications
P. O. Box 400
Kenner, LA 70063-0400
Fax: (504) 469-1849

Table of Contents
for MAPTP16XAE/9713A@
TP1607xx Single Stage Press
Page Description Document/ECN
1 About This Manual MHPTP16XAE/9702AV
3 Chapter 1: Installation
5 Installation„TP1607xx Press MSIN0908AE/9713AV
17 Chapter 2: Functional Description
19 How the TP1607xx Press Works MSSM0947AE/9613AV
29 Chapter 3: Service and Maintenance
31 TP1607xx Press Preventive Maintenance MSSM0945AE/9710AV
36 TP1607xx Press Diaphragm Replacement MSSM0946AE/9638AV
40 Single Stage Press TP1607xx Spare Parts List BMP970003/98191V
41 Chapter 4: Dimensional Drawings
43 Dimensions: TP1607 Single Stage Press BDTP60SSAE/97087D
44 Dimensions: TP1607 Options BDTP60SSAB/97151D
45 Dimensions: TP1607 Single Stage Press Left/Right Unload BDTP60LRAE/97087D
46 Dimensions: TP1607 Interface BDTP60INAE/97026D


MHPTP16XAE/9702AV (1 of 1)
ABOUT THIS MANUAL
Scope—This instruction manual is intended to provide preventive maintenance, service procedures, and
mechanical parts identification for all Milnor®microprocessor-controlled presses.
See the safety manual before installing, servicing, or operating this machine. See the installation manual
for facility requirements and machine installation procedures. See the operator guide for operating instruc-
tions. See the reference manual for programming, operating, and troubleshooting the control system. See the
schematic manual for electrical parts identification and electrical troubleshooting.
Manual Number/Date Code (When To Discard or Save)—The manual number/date code
is located on the inside front cover, upper right corner just above the manual name. Whenever the manual is
reprinted with new information, part of this number changes. If thedate code after the “/” changes, the new
version applies to all machines covered by the old version, but is improved— thus the old version can
be discarded. If the manualnumber before the “/” changes, the new manual covers only new machines.
Example: Discard MATMODELAE/8739CV when MATMODELAE/8739DV is received (minor improve-
ments). Also, discard MATMODELAE/8739DV when MATMODELAE/8746AV is received (major im-
provements). But keep MATMODELAE/8746FV when MATMODELBE/8815AV is received, since the
new manual no longer applies to machines originally shipped with the old manual.
Documents and Change Bars—The individual documents comprising this manual use the same
revision criteria as the manual. Text documents also display change bars. Example: When section
MSOP0599AE/9135BV becomes MSOP0599AE/9135CV, change bars with the letter “C” appear next to all
changes for this revision. For a major rewrite (e.g., MSOP0599AE/9226AV), all change bars are deleted.
Trademarks of Pellerin Milnor Corporation—The following, some of which may be used in
this publication, are trademarks of Pellerin Milnor Corporation:
Ampsaver®
Autolint®
Auto-Purge®
Autovac
CBW®
Dye-Extractor®
Dyextractor®
E-P Plus®
Gear Guardian®
Hands-Off®
Hydro-Cushion®
Mildata®
Milnet®
Milnor®
Miltrac
Miltron
Staph-Guard®
System 4®
System 7®
Totaltrol®
For Assistance—Please call:
Pellerin Milnor Corporation
Attn: Service Department
P. O. Box 400
Kenner, LA 70063-0400
Phone: (504) 467-9591
Fax: (504) 467-9777
1

2

Chapter 1
Installation
3

4

<B8=('04(& "0E
9>CD1<<1D9?>±D@!& 'hh@B5CC
The procedures herein are to be performed only by service personnel experienced in heavy
equipment handling, general mechanics, three-phase power wiring, and control wiring. The procedures
assume this expertise. General tasks are as follows:
NOff-load and locate the press
NAlign, level, and set the press
NInstall assemblies that were removed for shipment
NConnect utilities
NPrepare the press for operation
?VV<_QTQ^T<_SQdUdXU@bUcc
The press is shipped with certain assemblies temporarily removed to reduce overall size during
transit. Corridors and openings must be large enough to accommodate the main body of the press (but
not the fully assembled press) and the equipment used to move it. Refer to the dimensional drawing
(see table of contents) for overall dimensions of the main body and fully assembled press. The
instructions for lifting, aligning, leveling, and setting apply to the main body of the press.
<YVd Refer to the dimensional drawing (see table of contents) for press weight.
"
G1B>9>7* 3becX Q^T =QSXY^U 4Q]QWU 8QjQbTc
CWT _aTbb Xb WTPeXTa cWP] \^bc X]SdbcaXP[ [Pd]Sah T`dX_\T]c ^U R^\_PaPQ[T bXiT
8]PST`dPcT \^eX]V T`dX_\T]c RP] TPbX[h R^[[P_bT P]S^a UP[[ ^eTa X]YdaX]V
_Tab^]]T[ P]S STbca^hX]V T`dX_\T]c
☞
3^ ]^c PccT\_c c^ ^UU[^PS ^a \^eT cWT _aTbb d][Tbb `dP[XUXTS P]S PdcW^aXiTS
☞
4]bdaT cWPc [XUcX]V P]S \^eX]V T`dX_\T]c Xb PST`dPcT fXcW P aTPb^]PQ[T
bPUTch \PaVX]
☞
0[fPhb bTc cWT \PX] Q^Sh ^U cWT _aTbb X] Xcb UX]P[ _^bXcX^] QTU^aT X]bcP[[X]V cWT
_aTeX^db[h aT\^eTS PbbT\Q[XTb CWTbT PbbT\Q[XTb bXV]XUXRP]c[h aPXbT cWT
RT]cTa ^U VaPeXch P]S X]cTaUTaT fXcW aXVVX]V
3bQ^U<YVdY^W—Lift from the eye bolts
installed on top of the four frame posts using four
point lifting and a long harness.
6_b[<YVdY^W—The press rests on anX-shaped
footing. Lift with a fork lift under the notched ends
of the footing, just enough to block up the pressfor
fork blade clearance, then lift the entire press from
underthefootingasshowninFIGURE1.Liftfrom
the rear (discharge-end) or side without the control
box. Use care not to damage adjacent sheet metal.
586DA4 )
6_b[ <YVdY^W
5

1\YW^<UfU\Q^TCUddXU@bUcc
Support the press on shims placed under the outer ends of the X-shaped footing while aligning
and leveling.
1\YW^
Locate the press with respect to the Milnor
CBW®tunnel washer or the Milnor Cobuc
conveyor it receives goods from, as shown in the
interface drawing (see Table of Contents). Verify
that the tunnel exit ring or Cobuc bucket when in
the discharge position is centered in the press
scupper or load door (see FIGURE 2). Reposition
the press slightly, if required.
<UfU\
Level the press right to left and front to rear
using a carpenter’s level placed on the press bed.
Reposition the press slightly, if required.
CUd The press must be supported under the entire length of its X-shaped footing and anchored to
prevent creeping. To accomplish both objectives, form and pour a grout bed that imbeds one to two
inches of the footing, as shown in FIGURE 3. Use Sonneborn 14K or equivalent high flow, high
precision (fills all voids), non-shrinking, non-metalic, cementious grout.
586DA4 !)
1\YW^Y^W dXU @bUcc GYdX dXU <_QTY^W 4UfYSU
586DA4 ")
7b_edY^W dXU @bUcc
9>CD1<<1D9?>±D@!& 'hh @B5CC =C9> ) (15)'!#1F " _V !!
6

9^cdQ\\1ccU]R\YUcDXQd
GUbUBU]_fUTV_bCXY`]U^d
Once the main body of the press is installed (and not before), install the following assemblies
that were removed for shipment:
Ncylinder assembly (ram)
Nhydraulic assembly
Nproximity switch mounting post
Npress water return pump
Nlevel float
Most fasteners used on the press are metric. Some metric tools are required for assembly.
9^cdQ\\dXU3i\Y^TUb1ccU]R\iBQ]
Thecylinderassembly(ram)isshippeddismountedandlowered,asshowninFIGURE4.Mount
the cylinder assembly as follows:
The cylinder flange is held firmly between two nuts on each of three threaded rods. Run the top nut
on each rod all the way up (see FIGURE 4) so the cylinder can be raised almost its full distance.
The cylinder will be raised in this step. As it is raised, the shaft, platten, and membrane (hidden
inside the can) will remain resting on the press bed. Use one of the following methods for raising
the cylinder:
IMethod 1: Crane lifting—This method requires a crane or come-along with a minimum
capacity of one ton, positioned directly over the cylinder. Remove the lifting eyes from two
frame posts and install them on the cylinder as shown in FIGURE 5. Lift with the crane or
come-along from both lifting eyes, stopping about every two inches or 50 mm to run up the
lower nuts on the threaded rods.
JMethod 2: Hand cranking—Use the lower nuts on the rods to crank the cylinder up, as shown
in FIGURE 6.Alternate between nutsso that none ofthe lowernuts isever morethan twoinches
or 50 mm below the flange.
586DA4 #)
3i\Y^TUb 1ccU]R\i
BQ] <_gUbUT V_b CXY`]U^d
586DA4 $)
<YVdY^W 5iUc 9^cdQ\\UT _^
3i\Y^TUb V_b SbQ^U <YVdY^W =UdX_T !
586DA4 %)
8Q^TSbQ^[Y^W dXU 3i\
Y^TUb Y^d_ @_cYdY_^ =UdX_T "
9>CD1<<1D9?>±D@!& 'hh @B5CC =C9> ) (15)'!#1F # _V !!
7

Each threaded rod now has two nuts above the cylinder
flange which interfere with raising the cylinder
completely. The uppermost nut locks the rod in place.
When the cylinder assembly is within three inches or 75
mm of its final position and the assembly is supported by
all three threaded rods and lower nuts, remove one
threaded rod, as shown in FIGURE 7, remove both top
nuts then replace the rod and lower nut. Repeat for each
of the other two rods,ensuring that the cylinder assembly
is always supported by at least two rods/nuts.
Carefully crank the assembly up the remaining distance
using the nutson the threaded rods, guiding the machined
lipof thecylinder assemblyinto theholeand fullyseating
the assembly. Six hex head (30 mm) mounting bolts are
furnished. Install three mounting bolts in the three empty
mounting holes, then remove the three threaded rods, and
replace with the three remaining mounting bolts. Torque
all bolts to 550 foot-pounds (76 Nm).
9^cdQ\\dXU8iTbQe\YS1ccU]R\i
Thehydraulic powerunitwas removedfrom thepress
and skidded separately.
=_e^ddXU1ccU]R\i—Anchor the hydraulic
assembly to the mounting frame on top of the press using the
bolts, nuts and washers furnished on the mounting frame.
Four integral lifting eyes are provided on the hydraulic
assembly for crane lifting.
CUddXU@bUVY\\FQ\fU9^@_cYdY_^Q^T
3_^^USddXU@bUVY\\@Y`U—as follows:
Remove the cylinder protective cover, taking care not to
permit debris from entering the cylinder.
Place the pre-fill valve over the opening, oriented as
shown in FIGURE 8.
Clip the tie wrap securing the pre-fill pipe on the
hydraulic assembly, then lift and rotate it into position
over the pre-fill valve (see FIGURE 9).
Eight Allen head bolts (19 mm) are furnished. Install
these as shown in FIGURE 9 and torque to 250
foot-pounds (35 Nm).
Tighten the hose clamps on the rubber boot on the tank side of the prefill pipe.
586DA4 &)
DU]`_bQbY\i BU]_fY^W Q
DXbUQTUT B_T d_ BU]_fU dXU D_` >edc
586DA4 ')
@bUVY\\ FQ\fU CUd Y^ @_cYdY_^
586DA4 ()
@bUVY\\ @Y`U 9^cdQ\\UT
9>CD1<<1D9?>±D@!& 'hh @B5CC =C9> ) (15)'!#1F $ _V !!
8

3_^^USd8iTbQe\YS<Y^Uc—as follows:
Install hard piping. FIGURE 10 shows the hydraulic pipe assemblies (pipe with flare type fittings,
both ends) furnished and their general location when installed. Most connection points can be easily
matched up because the pipe is shaped to fit. However, if any questions arise, refer to the hydraulic
schematic, elsewhere in the manual. Use two wrenches to fully tighten all connections.
#
31ED9?>* =Q\Ve^SdY_^ 8QjQbT
CWT _aTbb dbTb P WXVW _aTbbdaT WhSaPd[XR bhbcT\ 8U P]h R^]]TRcX^]b PaT ]^c Ud[[h
cXVWcT]TS ^X[ fX[[ `dXRZ[h [TPZ ^dc cWT UXabc cX\T cWT bhbcT\ Xb _aTbbdaXiTS
☞
4]bdaT cWPc P[[ WhSaPd[XR R^]]TRcX^]b PaT Ud[[h cXVWcT]TS QTU^aT ^_TaPcX]V
Connect the prefill valve actuator tube to the prefill valve, as shown in FIGURE 10. This flexible
tube will be found on the hydraulic assembly.
Connect the pressure sensing tube at the location shown in FIGURE 10. This flexible tube will be
found on the press top plate.
586DA4 )
9^cdQ\\Y^W 8iTbQe\YS <Y^Uc
9>CD1<<1D9?>±D@!& 'hh @B5CC =C9> ) (15)'!#1F % _V !!
9

GYbUdXU8iTbQe\YS@e]`—The hydraulic motor power cable from the press control box
will be found on the press top plate. Make the appropriate electrical connections in the motor junction
box. Proper motor rotation (phasing) will be verified later.
GYbUdXU8iTbQe\YS3_^db_\c—A plastic conduit
containingonemulti-conductorcableandonetwo-conductorcablethat
terminates with a solenoid will be found on top of the press near the
junction box on the front of the hydraulic assembly. Refer to FIGURE
11 and make the following connections:
Snap the conduit into the plastic clips on the hydraulic unit.
Install the solenoid on the valve indicated.
Feed the multi-conductor cable into the junction box. Wire
numbers are printed on the wire insulation. Match wires to pins as
shown in table A. Connect the yellow/green wire (ground) to
pin 3.
9^cdQ\\dXU@b_hY]YdiCgYdSX=_e^dY^W@_cd
As the ram travels up and down, its guide rod actuates proximity switches on an adjacent post,
which is bolted to the press top plate. The base of this post is shimmed with washers to make the post
parallel to the guide rod. The post is dismounted and laid on the press top plate for shipment and the
bolts and washers are replaced in their respective mounting holes, as shown in FIGURE 12. Note
carefully the washer locations before removing the bolts, then install the post, placing any large flat
washers under the base of the post and the small flat washers and lock washers on top.
#
31ED9?>* 3_]`_^U^d 4Q]QWU Q^T =Q\Ve^SdY_^ 8QjQbTc
CWT VdXST a^S RP] bcaXZT P]S STbca^h cWT _a^gX\Xch bfXcRWTb ^a cWT bfXcRWTb \Ph
UPX[ c^ Ud]RcX^] XU cWT _^bc Xb ]^c _PaP[[T[ c^ cWT _PcW ^U cWT VdXST a^S
☞
4]bdaT cWPc cWT \^d]cX]V _^bc Xb _PaP[[T[ c^ cWT VdXST a^S _PcW Qh aT_[PRX]V
cWT bWX\\X]V fPbWTab X] cWTXa ^aXVX]P[ [^RPcX^]b d]STa cWT _^bc QPbT _[PcT
586DA4 )
9^cdQ\\Y^W 3QR\Uc 6b_] @bUcc 3_^db_\ 2_h
586DA4 !)
2_\dc V_b =_e^dY^W dXU @b_hY]Ydi CgYdSX
=_e^dY^W @_cd
C01;4 0) 2^]]TRcX^]b X]
7hSaPd[XR D]Xc 9d]RcX^] 1^g
Wire # Pin # Wire # Pin #
14756
250857
31958
4 2 10 59
5 541160
655
9>CD1<<1D9?>±D@!& 'hh @B5CC =C9> ) (15)'!#1F & _V !!
10

9^cdQ\\dXU@bUccGQdUbBUdeb^@e]`
This pump sends reuse water from the press water tank to the CBW®flush tank. Piping and
power cables are not furnished because the pump location and distance to the CBW®flush tank can
vary.
=_e^dQ^T@\e]RdXU@e]`—Locate the pump at the right front or left front corner of the
press, whichever side the press control box is on. The pump assembly (pump, motor, and base may be
set on the floor or mounted to the machine by welding the stainless steel brackets (furnished with the
pump) to the press water tank, as shown in FIGURE 13.
Connect the pump inlet to the closest 1 1/2" NPTmale connection on the front of the press water
tank, similar to the arrangement shown in FIGURE 13. When adjusting the system, it is sometimes
helpful to reduce the flow into the pump, therefore an in-line valve, as shown in FIGURE 13 is
recommended. Refer to “Connect Utilities” elsewhere in this section for the pump-to-CBW®flush tank
connection.
GYbUdXU@e]`—Pump power is supplied by the press control box. Run 14 gauge, 3 conductor
cable (for three-phase motor) in conduit. Connection points are as shown in FIGURE 14. Proper motor
rotation (phasing) will be verified later.
586DA4 ")
@bUcc GQdUb BUdeb^ @e]`
=_e^dUT d_ @bUcc
586DA4 #)
3_^^USdY^W @e]` @_gUb Q^T <UfU\ CgYdSX
9^`edc Y^ dXU @bUcc 3_^db_\ 2_h
9>CD1<<1D9?>±D@!& 'hh @B5CC =C9> ) (15)'!#1F ' _V !!
11

9^cdQ\\dXU<UfU\6\_Qd1ccU]R\i
This assembly turns the press water return pump on when the press water tank level rises above
high and off when the level falls below low. The assembly may be installed within the frame of the
machine, thus savingspace, or outsidethe framewhere it ismore accessable. Ineither case, the assembly
must be mounted on the opposite side of the machine from the press water return pump. Piping and
control wiring are not furnished because the location of the level float assembly can vary.
=_e^dQ^T@\e]RdXU6\_QdDeRU—Once the location has been determined, mark and
drill four holes in the press corner panel and mount the float tube using the hardware provided.
<^d]cX]V8]bXSTcWT5aP\T—Let the float tube rest on the bottom of the press water tank.
The float tube will sit in the press water tank and not need a hose connection (see FIGURE 15).
<^d]cX]V>dcbXSTcWT5aP\T—For outside mounting, connect the 3/4" (19mm) hose
conection on the float tube to the closest 1/2" NPT male conection on the front of the tank.
Provide a 3/4" to 1/2"NPT reducer, 3/4" pipe nipple, 3/4" (19 mm) hose and hose clamps (see
FIGURE 16).
3_^^USdY^W<UfU\CgYdSXUc—The two level switches are inputs to the press controller.
Wire these as shown in FIGURE 14.
586DA4 $)
<UfU\ 6\_Qd =_e^dUT 9^cYTU dXU =Q
SXY^U 6bQ]U
586DA4 %)
<UfU\ 6\_Qd =_e^dUT ?edcYTU dXU =QSXY^U
6bQ]U
9>CD1<<1D9?>±D@!& 'hh @B5CC =C9> ) (15)'!#1F ( _V !!
12

3_^^USdEdY\YdYUc
The following service connections are needed:
NPiped utilities: compressed air in, press water to CBW®reuse tank, and overflow to sewer
NElectric utilities: electric power in and electronic interface with system controller
3_^^USd@Y`UTEdY\YdYUc
Piped utility connection locations and sizes are shown on the dimensional drawing (see Table
of Contents). Utility requirements and other information are given in TABLE B.
#
31ED9?>* 3_]`_^U^d 4Q]QWU Q^T =Q\Ve^SdY_^ 8QjQbTc
8\_a^_Ta _[d\QX]V fX[[ RPdbT \PRWX]T SP\PVT P]S^a X]TUUXRXT]c ^_TaPcX^]
☞
4]bdaT cWPc X][Tc _aTbbdaTb PaT fXcWX] cWT b_TRXUXTS aP]VT
☞
FWT] R^]]TRcX]V c^ P] P__PaPcdb bdRW Pb P eP[eT ^a _d\_ W^[S cWT
R^]]TRcX^] bXST ^U cWT P__PaPcdb fXcW P faT]RW c^ Pe^XS SXbc^acX]V cWT
P__PaPcdb
C01;4 1) ?X_TS DcX[XcXTb
Description Utility Requirements Comments
Piped Inlets
Compressed air in 85 PSI minimum
100 PSI maximum Recommend 1" NPT minimum piping from
compressor
Piped Outlets
Press water return
pump to CBW®
reuse tank
No valves or other line
restrictions between pump and
CBW®reuse tank
2" (51 mm) ID reinforced rubber hose
normally supplied with CBW®
Overflow to sewer No valves or other line
restrictions between outlet and
sewer
Recommend 4" (approx. 100 mm) PVC or
similar pipe connected to 100 mm integral
stainless steel pipe fitting (unflanged) on press
water tank with rubber hose/hose clamps.
9>CD1<<1D9?>±D@!& 'hh @B5CC =C9> ) (15)'!#1F ) _V !!
13

3_^^USd5\USdbYSEdY\YdYUc
The general location for electrical connections is shown on the dimensional drawing (see Table
of Contents). Electric utility requirements (or where to look for requirements) and other information
are given in TABLE C.
!
41>75B* 5\USdb_SedY_^ Q^T 5\USdbYSQ\ 2eb^ 8QjQbTc
2^]cPRc fXcW WXVW e^[cPVT fX[[ T[TRca^RdcT ^a Qda] h^d
☞
3^ ]^c PccT\_c c^ R^]]TRc \PRWX]T c^ T[TRcaXR _^fTa d][Tbb `dP[XUXTS P]S
PdcW^aXiTS
#
31ED9?>* E^cQVU ?`UbQdY_^ Q^T =QSXY^U 4Q]QWU 8QjQbTc
8\_a^_Ta T[TRcaXR _^fTa R^]]TRcX^]b fX[[ RPdbT d]bPUT ^_TaPcX^] P]S^a \PRWX]T
SP\PVT
☞
3^ ]^c R^]]TRc \PRWX]T c^ T[TRcaXR _^fTa d][Tbb `dP[XUXTS P]S PdcW^aXiTS
☞
3^ ]^c _^fTa d_ \PRWX]T d]cX[ P[[ aT`dXaTS Va^d]Sb _^fTa P]S R^]ca^[ PaT
R^]]TRcTS P]S WhSaPd[XR cP]Z WPb QTT] UX[[TS
☞
FWT] \PZX]V _^fTa R^]]TRcX^]b R^]]TRc bcX]VTa [TV XU P]h c^ cTa\X]P[ ;"
^][h ]^c c^ ; ^a ;!
☞
2^\_[h fXcW P[[ b_TRXUXRPcX^]b
C01;4 2) 4[TRcaXR DcX[XcXTb
Description Utility Requirement Comments
Machine electric
power Three phase power, as specified on the
machine nameplate See the Electrical manual and the system
documentation (such as the power
conductors drawing) for connection
points and additional specifications.
Remotely mounted disconnect switch
box with lag type fuses or circuit
breakers
See External Fuse and Wire manual for
specifications.
Zero potential earth ground Connect between ground lug on machine
and external disconnect box or other
reliable earth ground.
Control interface Interface to Miltrac or Allied
(non-Milnor) controller as specified in
the system documentation. Several
types of connections, each with their
own specifications, may be required.
See the Electrical manual and the system
documentation (such as the control
conductors drawing) for connection
points and additional specifications.
9>CD1<<1D9?>±D@!& 'hh @B5CC =C9> ) (15)'!#1F ! _V !!
14

@bU`QbUdXU@bUccV_b?`UbQdY_^
Refer to the Reference manual for press operating procedures. The following tasks are required
before commissioning the press:
Fill the hydraulic tank as explained in preventive maintenance (see Table of Contents).
Verify proper phasing. If power legs L1, L2, and L3 were identified and properly matched with
incoming power conductors, motorswill operate properly. Verify proper motor rotation and correct
if required, by interchanging the connections to L1 and L2.
#
31ED9?>* =QSXY^U 4Q]QWU 8QjQbTc
8\_a^_Ta bcX]VTa [TV R^]]TRcX^] RP] `dXRZ[h STbca^h \^c^a
☞
X]cTaRWP]VT cWT fXaTb R^]]TRcTS c^ ; P]S ;! =TeTa \^eT ;" XU ;" Xb P bcX]VTa
[TV
Install the membrane (if shipped separate) as explained in press diaphragm replacement (see
Table of Contents).
Set press water level. The press water tank is the pan in which the press bed sits. This tank, which
collects extracted water for return to the CBW®reuse tank, has two levels—high and low, as set on
the level float assembly. When the level rises above high, the press water return pump runs, sending
water to the reuse tank. The pump continues to run until the levelfalls below low, shutting off the pump.
Prior to commissioning, it may be convenient to fill the press water tank with a hose, to set the levels.
Levels are set by adjusting the position of the clips on the float rod (bottom clip sets high level and top
clip sets low level). The clips must be kept at least 1" (25mm) apart to prevent binding. Factors to
consider when setting levels are:
NDetermine the needs of the reuse tank.
NKeep high level below the overflow to prevent wasting water.
NKeep low level above the top of the outlet to the pump to prevent the pump from sucking air.
NReduce the flow to the pump (using the in-line valve, if installed) to lengthen pump cycle time.
Verify proper PXSM proximity switch setting.This switch determines when during descent, the
ram transitions from free fall to power, (see "HOW THE TP1607xx PRESS WORKS"). This switch
must be set as stated in the following caution.
#
31ED9?>* =QSXY^U 4Q]QWU 8QjQbTc
8U cWT STbRT]SX]V aP\ caP]bXcX^]b Ua^\ UaTT UP[[ c^ _^fTa QTU^aT cWT \T\QaP]T
Ud[[h T]cTab cWT RP] _aTbb SP\PVT fX[[ aTbd[c XU cWT \T\QaP]T T]R^d]cTab P]
^QbcadRcX^] bdRW Pb V^^Sb RPdVWc X] cWT [^PS RWdcT
☞
ETaXUh cWPc _a^gX\Xch bfXcRW ?GB< QaTPZb R^]cPRc fWT] cWT [^fTa TSVT ^U cWT
\T\QaP]T Xb Pc [TPbc % X]RWTb $!\\ QT[^f cWT [^fTbc _^X]c ^U cWT [^PS
RWdcT
9>CD1<<1D9?>±D@!& 'hh @B5CC =C9> ) (15)'!#1F !! _V !!
15

16
Table of contents
Other Milnor Power Tools manuals
Popular Power Tools manuals by other brands
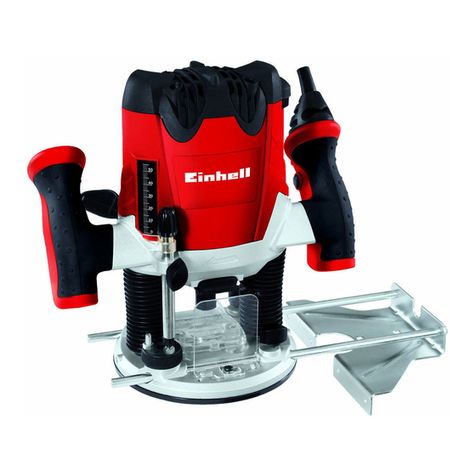
EINHELL
EINHELL RT-RO 55 operating instructions
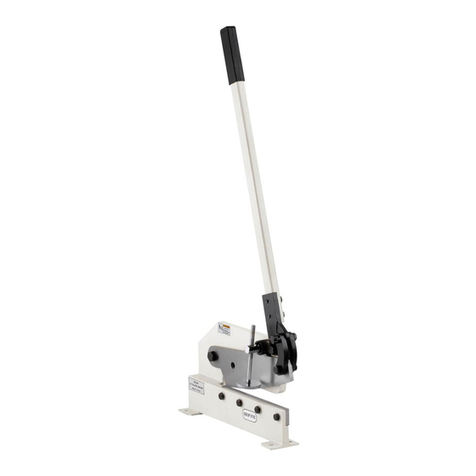
Woodstock
Woodstock SHOP FOX M1040 instruction sheet
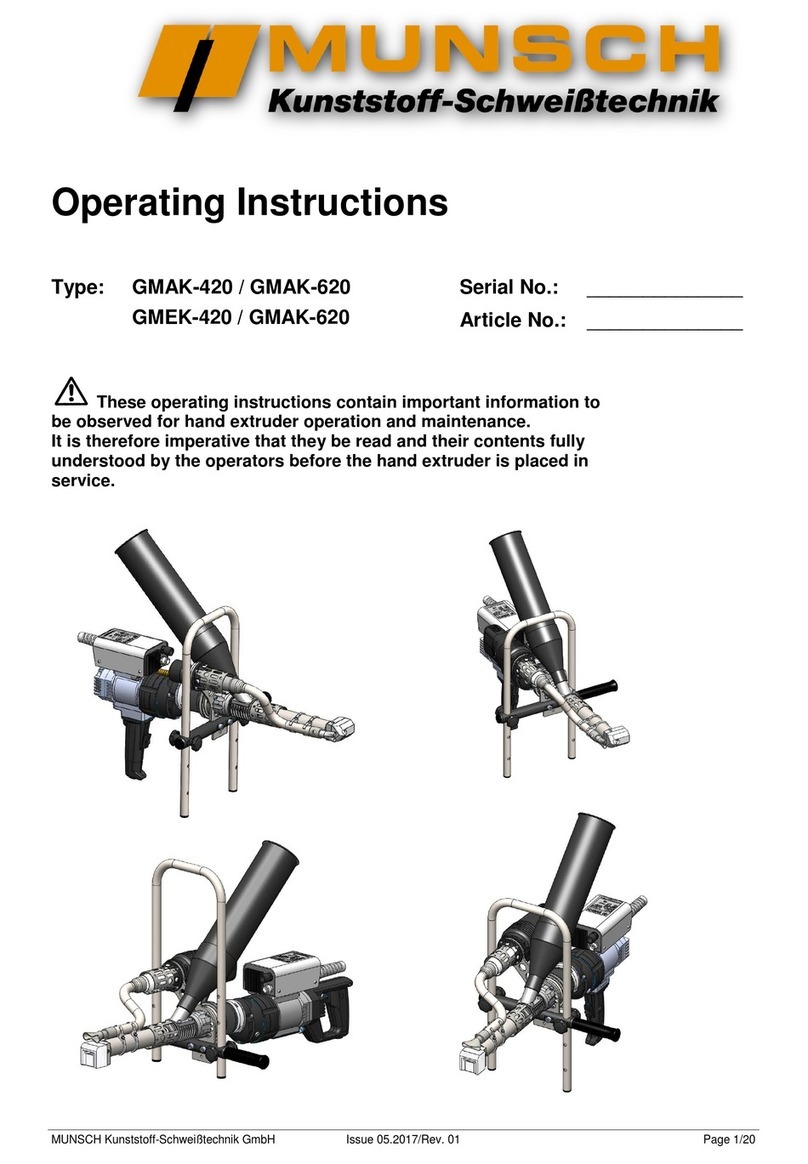
Munsch
Munsch GMAK-420 operating instructions
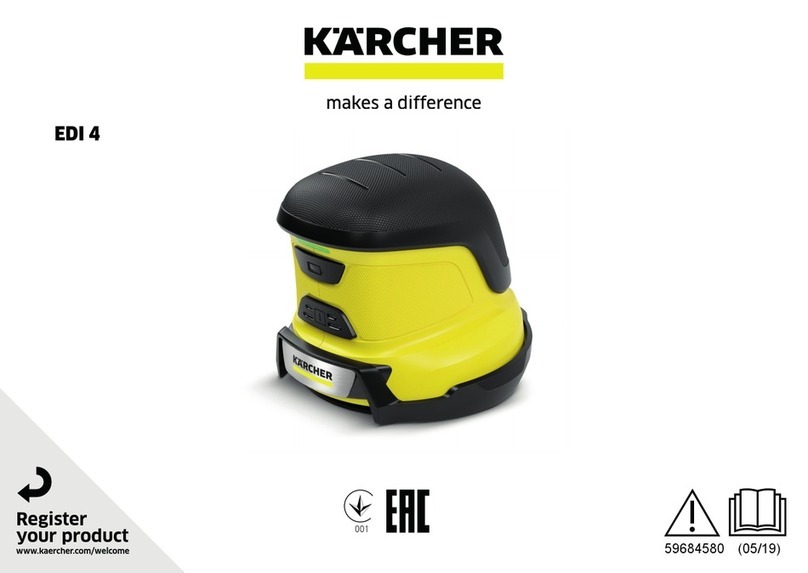
Kärcher
Kärcher EDI 4 Original operating instructions

Central Pneumatic Professional
Central Pneumatic Professional 42248 Set up and operating instructions
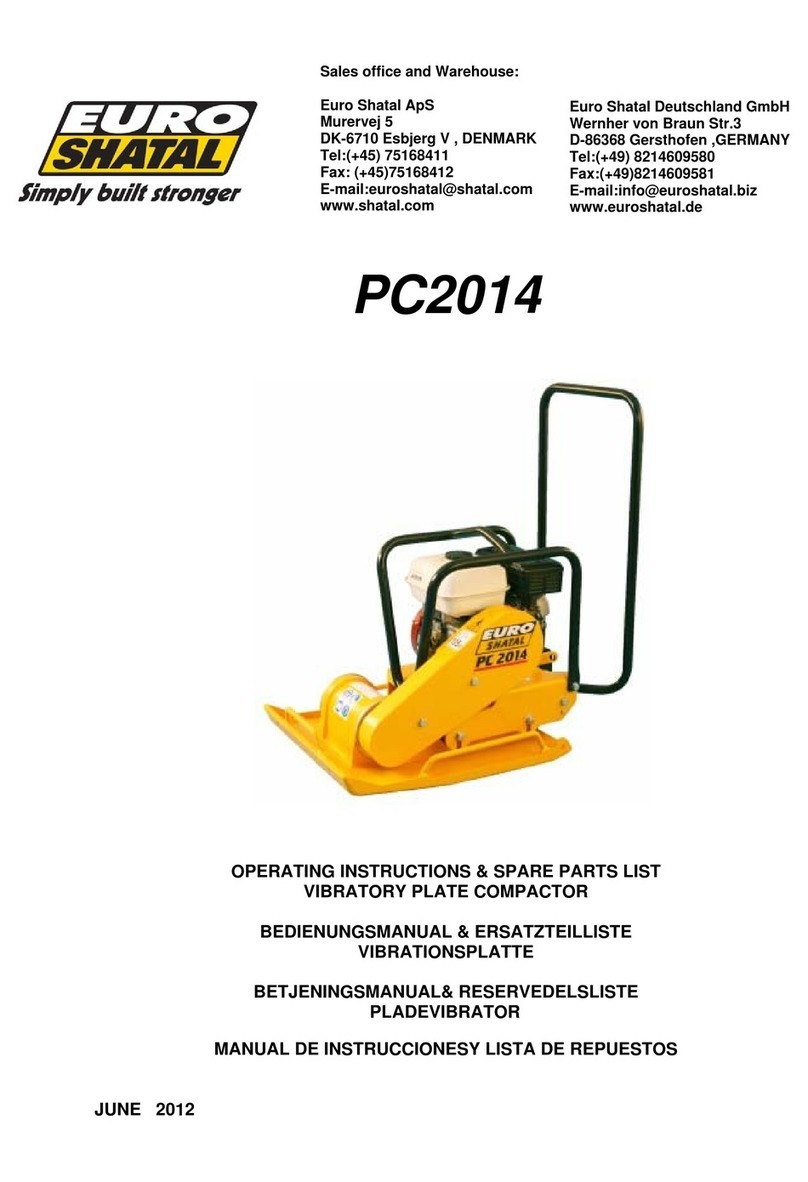
Euro Shatal
Euro Shatal PC2014 Operating instructions/spare parts list